check engine CHRYSLER VOYAGER 2001 Service Manual
[x] Cancel search | Manufacturer: CHRYSLER, Model Year: 2001, Model line: VOYAGER, Model: CHRYSLER VOYAGER 2001Pages: 4284, PDF Size: 83.53 MB
Page 4074 of 4284
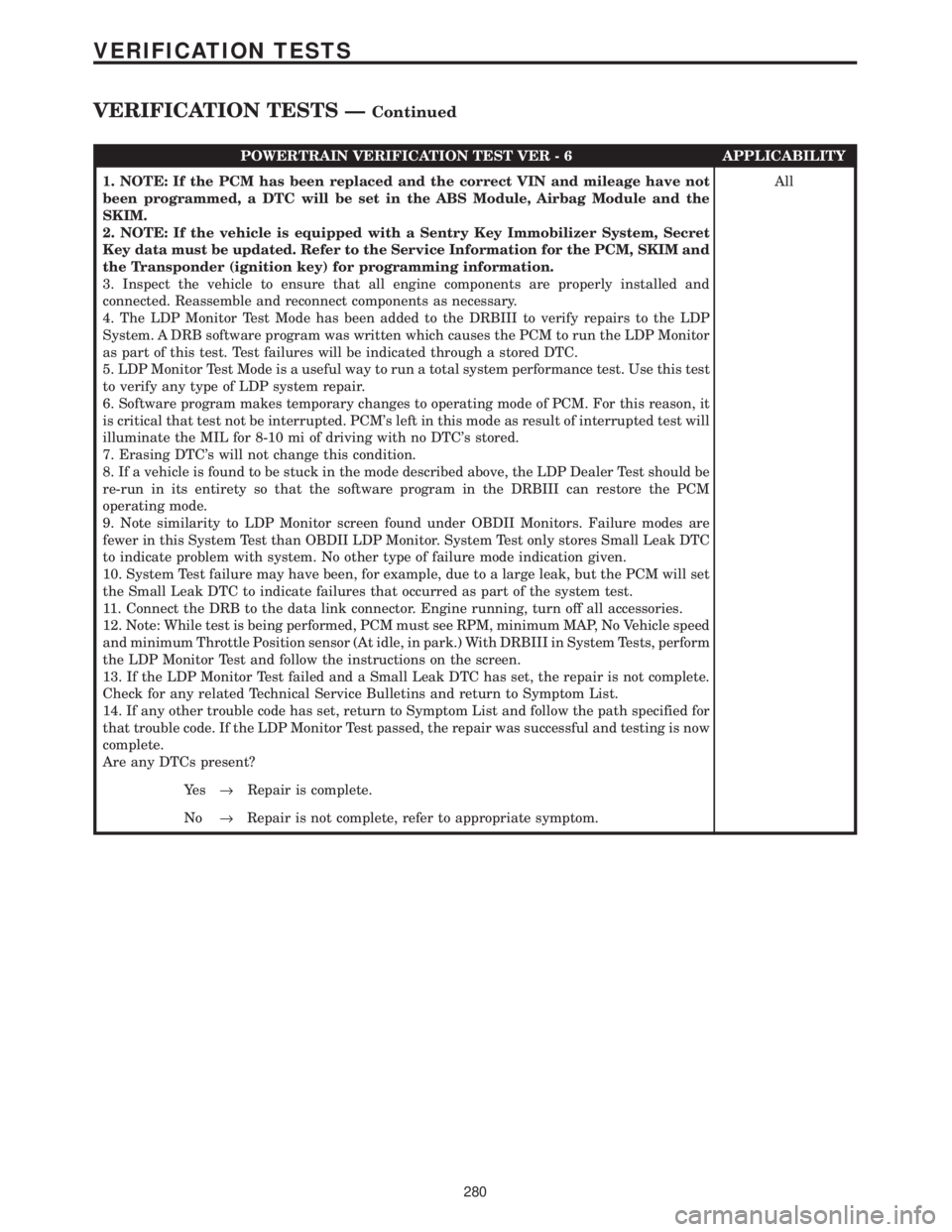
POWERTRAIN VERIFICATION TEST VER - 6 APPLICABILITY
1. NOTE: If the PCM has been replaced and the correct VIN and mileage have not
been programmed, a DTC will be set in the ABS Module, Airbag Module and the
SKIM.
2. NOTE: If the vehicle is equipped with a Sentry Key Immobilizer System, Secret
Key data must be updated. Refer to the Service Information for the PCM, SKIM and
the Transponder (ignition key) for programming information.
3. Inspect the vehicle to ensure that all engine components are properly installed and
connected. Reassemble and reconnect components as necessary.
4. The LDP Monitor Test Mode has been added to the DRBIII to verify repairs to the LDP
System. A DRB software program was written which causes the PCM to run the LDP Monitor
as part of this test. Test failures will be indicated through a stored DTC.
5. LDP Monitor Test Mode is a useful way to run a total system performance test. Use this test
to verify any type of LDP system repair.
6. Software program makes temporary changes to operating mode of PCM. For this reason, it
is critical that test not be interrupted. PCM's left in this mode as result of interrupted test will
illuminate the MIL for 8-10 mi of driving with no DTC's stored.
7. Erasing DTC's will not change this condition.
8. If a vehicle is found to be stuck in the mode described above, the LDP Dealer Test should be
re-run in its entirety so that the software program in the DRBIII can restore the PCM
operating mode.
9. Note similarity to LDP Monitor screen found under OBDII Monitors. Failure modes are
fewer in this System Test than OBDII LDP Monitor. System Test only stores Small Leak DTC
to indicate problem with system. No other type of failure mode indication given.
10. System Test failure may have been, for example, due to a large leak, but the PCM will set
the Small Leak DTC to indicate failures that occurred as part of the system test.
11. Connect the DRB to the data link connector. Engine running, turn off all accessories.
12. Note: While test is being performed, PCM must see RPM, minimum MAP, No Vehicle speed
and minimum Throttle Position sensor (At idle, in park.) With DRBIII in System Tests, perform
the LDP Monitor Test and follow the instructions on the screen.
13. If the LDP Monitor Test failed and a Small Leak DTC has set, the repair is not complete.
Check for any related Technical Service Bulletins and return to Symptom List.
14. If any other trouble code has set, return to Symptom List and follow the path specified for
that trouble code. If the LDP Monitor Test passed, the repair was successful and testing is now
complete.
Are any DTCs present?All
Ye s®Repair is complete.
No®Repair is not complete, refer to appropriate symptom.
280
VERIFICATION TESTS
VERIFICATION TESTS ÐContinued
Page 4102 of 4284
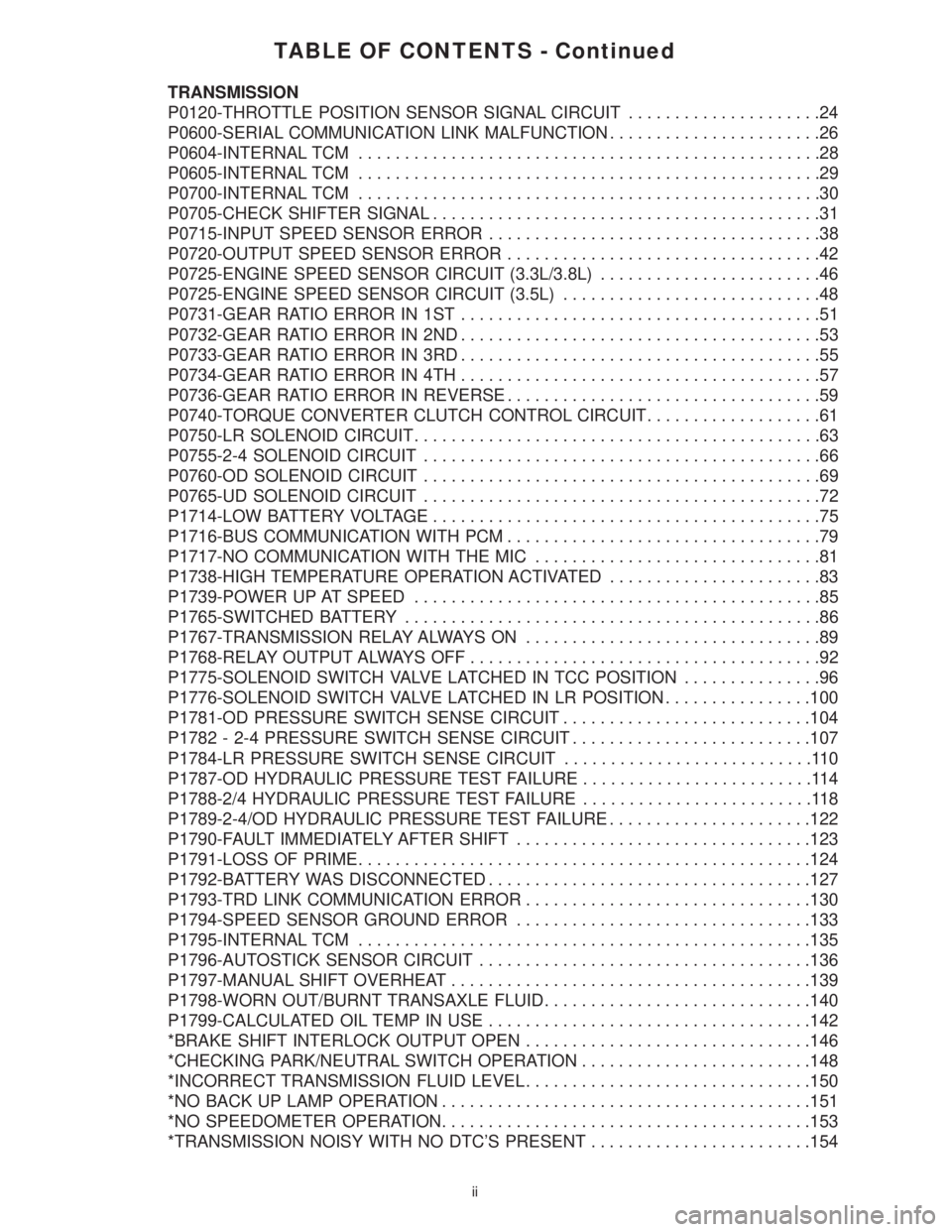
TABLE OF CONTENTS - Continued
TRANSMISSION
P0120-THROTTLE POSITION SENSOR SIGNAL CIRCUIT.....................24
P0600-SERIAL COMMUNICATION LINK MALFUNCTION.......................26
P0604-INTERNAL TCM..................................................28
P0605-INTERNAL TCM..................................................29
P0700-INTERNAL TCM..................................................30
P0705-CHECK SHIFTER SIGNAL..........................................31
P0715-INPUT SPEED SENSOR ERROR....................................38
P0720-OUTPUT SPEED SENSOR ERROR..................................42
P0725-ENGINE SPEED SENSOR CIRCUIT (3.3L/3.8L)........................46
P0725-ENGINE SPEED SENSOR CIRCUIT (3.5L)............................48
P0731-GEAR RATIO ERROR IN 1ST.......................................51
P0732-GEAR RATIO ERROR IN 2ND.......................................53
P0733-GEAR RATIO ERROR IN 3RD.......................................55
P0734-GEAR RATIO ERROR IN 4TH.......................................57
P0736-GEAR RATIO ERROR IN REVERSE..................................59
P0740-TORQUE CONVERTER CLUTCH CONTROL CIRCUIT...................61
P0750-LR SOLENOID CIRCUIT............................................63
P0755-2-4 SOLENOID CIRCUIT...........................................66
P0760-OD SOLENOID CIRCUIT...........................................69
P0765-UD SOLENOID CIRCUIT...........................................72
P1714-LOW BATTERY VOLTAGE..........................................75
P1716-BUS COMMUNICATION WITH PCM..................................79
P1717-NO COMMUNICATION WITH THE MIC...............................81
P1738-HIGH TEMPERATURE OPERATION ACTIVATED.......................83
P1739-POWER UP AT SPEED............................................85
P1765-SWITCHED BATTERY.............................................86
P1767-TRANSMISSION RELAY ALWAYS ON................................89
P1768-RELAY OUTPUT ALWAYS OFF......................................92
P1775-SOLENOID SWITCH VALVE LATCHED IN TCC POSITION...............96
P1776-SOLENOID SWITCH VALVE LATCHED IN LR POSITION................100
P1781-OD PRESSURE SWITCH SENSE CIRCUIT...........................104
P1782 - 2-4 PRESSURE SWITCH SENSE CIRCUIT..........................107
P1784-LR PRESSURE SWITCH SENSE CIRCUIT...........................110
P1787-OD HYDRAULIC PRESSURE TEST FAILURE.........................114
P1788-2/4 HYDRAULIC PRESSURE TEST FAILURE.........................118
P1789-2-4/OD HYDRAULIC PRESSURE TEST FAILURE......................122
P1790-FAULT IMMEDIATELY AFTER SHIFT................................123
P1791-LOSS OF PRIME.................................................124
P1792-BATTERY WAS DISCONNECTED...................................127
P1793-TRD LINK COMMUNICATION ERROR...............................130
P1794-SPEED SENSOR GROUND ERROR................................133
P1795-INTERNAL TCM.................................................135
P1796-AUTOSTICK SENSOR CIRCUIT....................................136
P1797-MANUAL SHIFT OVERHEAT.......................................139
P1798-WORN OUT/BURNT TRANSAXLE FLUID.............................140
P1799-CALCULATED OIL TEMP IN USE...................................142
*BRAKE SHIFT INTERLOCK OUTPUT OPEN...............................146
*CHECKING PARK/NEUTRAL SWITCH OPERATION.........................148
*INCORRECT TRANSMISSION FLUID LEVEL...............................150
*NO BACK UP LAMP OPERATION........................................151
*NO SPEEDOMETER OPERATION........................................153
*TRANSMISSION NOISY WITH NO DTC'S PRESENT........................154
ii
Page 4105 of 4284
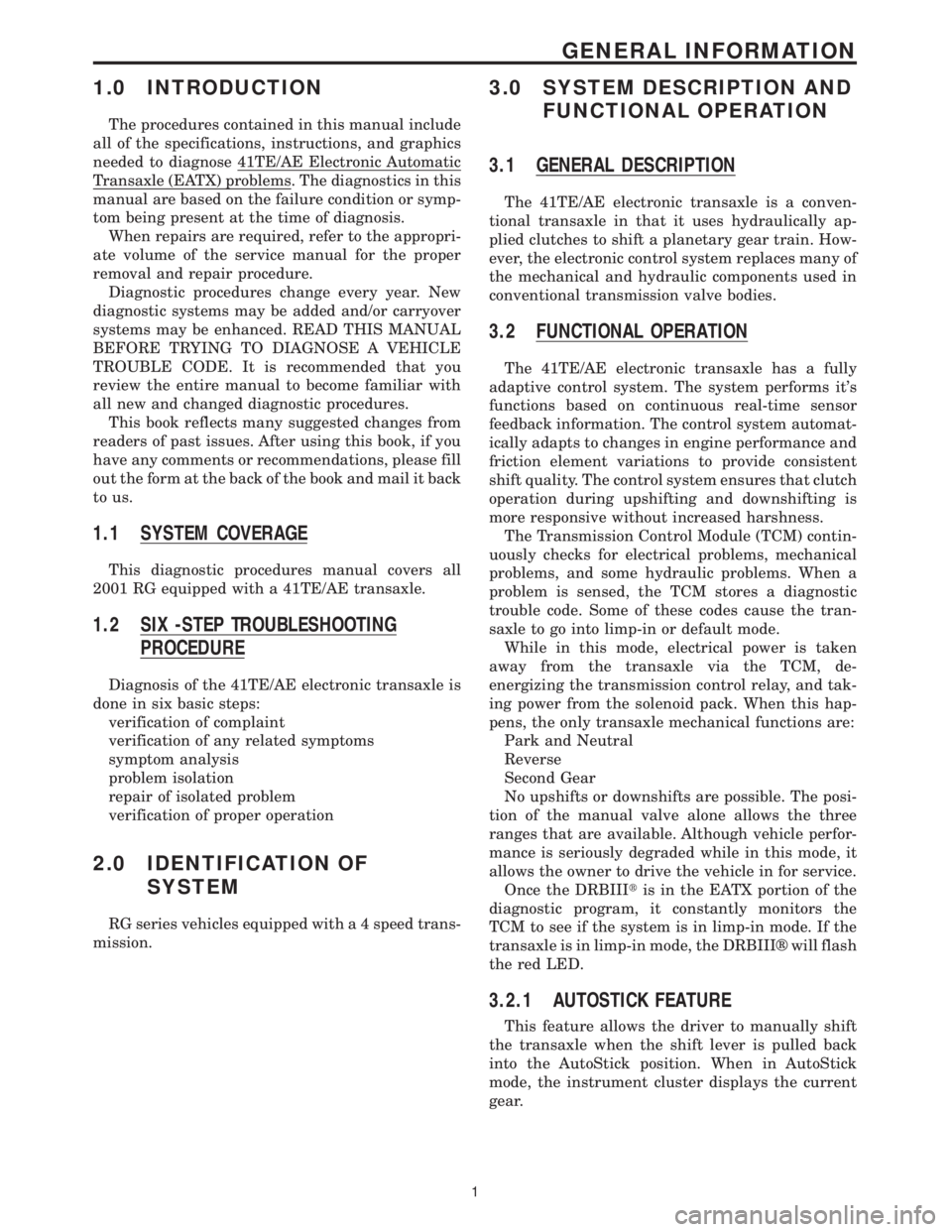
1.0 INTRODUCTION
The procedures contained in this manual include
all of the specifications, instructions, and graphics
needed to diagnose 41TE/AE Electronic Automatic
Transaxle (EATX) problems. The diagnostics in this
manual are based on the failure condition or symp-
tom being present at the time of diagnosis.
When repairs are required, refer to the appropri-
ate volume of the service manual for the proper
removal and repair procedure.
Diagnostic procedures change every year. New
diagnostic systems may be added and/or carryover
systems may be enhanced. READ THIS MANUAL
BEFORE TRYING TO DIAGNOSE A VEHICLE
TROUBLE CODE. It is recommended that you
review the entire manual to become familiar with
all new and changed diagnostic procedures.
This book reflects many suggested changes from
readers of past issues. After using this book, if you
have any comments or recommendations, please fill
out the form at the back of the book and mail it back
to us.
1.1 SYSTEM COVERAGE
This diagnostic procedures manual covers all
2001 RG equipped with a 41TE/AE transaxle.
1.2 SIX -STEP TROUBLESHOOTING
PROCEDURE
Diagnosis of the 41TE/AE electronic transaxle is
done in six basic steps:
verification of complaint
verification of any related symptoms
symptom analysis
problem isolation
repair of isolated problem
verification of proper operation
2.0 IDENTIFICATION OF
SYSTEM
RG series vehicles equipped with a 4 speed trans-
mission.
3.0 SYSTEM DESCRIPTION AND
FUNCTIONAL OPERATION
3.1 GENERAL DESCRIPTION
The 41TE/AE electronic transaxle is a conven-
tional transaxle in that it uses hydraulically ap-
plied clutches to shift a planetary gear train. How-
ever, the electronic control system replaces many of
the mechanical and hydraulic components used in
conventional transmission valve bodies.
3.2 FUNCTIONAL OPERATION
The 41TE/AE electronic transaxle has a fully
adaptive control system. The system performs it's
functions based on continuous real-time sensor
feedback information. The control system automat-
ically adapts to changes in engine performance and
friction element variations to provide consistent
shift quality. The control system ensures that clutch
operation during upshifting and downshifting is
more responsive without increased harshness.
The Transmission Control Module (TCM) contin-
uously checks for electrical problems, mechanical
problems, and some hydraulic problems. When a
problem is sensed, the TCM stores a diagnostic
trouble code. Some of these codes cause the tran-
saxle to go into limp-in or default mode.
While in this mode, electrical power is taken
away from the transaxle via the TCM, de-
energizing the transmission control relay, and tak-
ing power from the solenoid pack. When this hap-
pens, the only transaxle mechanical functions are:
Park and Neutral
Reverse
Second Gear
No upshifts or downshifts are possible. The posi-
tion of the manual valve alone allows the three
ranges that are available. Although vehicle perfor-
mance is seriously degraded while in this mode, it
allows the owner to drive the vehicle in for service.
Once the DRBIIItis in the EATX portion of the
diagnostic program, it constantly monitors the
TCM to see if the system is in limp-in mode. If the
transaxle is in limp-in mode, the DRBIIIž will flash
the red LED.
3.2.1 AUTOSTICK FEATURE
This feature allows the driver to manually shift
the transaxle when the shift lever is pulled back
into the AutoStick position. When in AutoStick
mode, the instrument cluster displays the current
gear.
1
GENERAL INFORMATION
Page 4107 of 4284
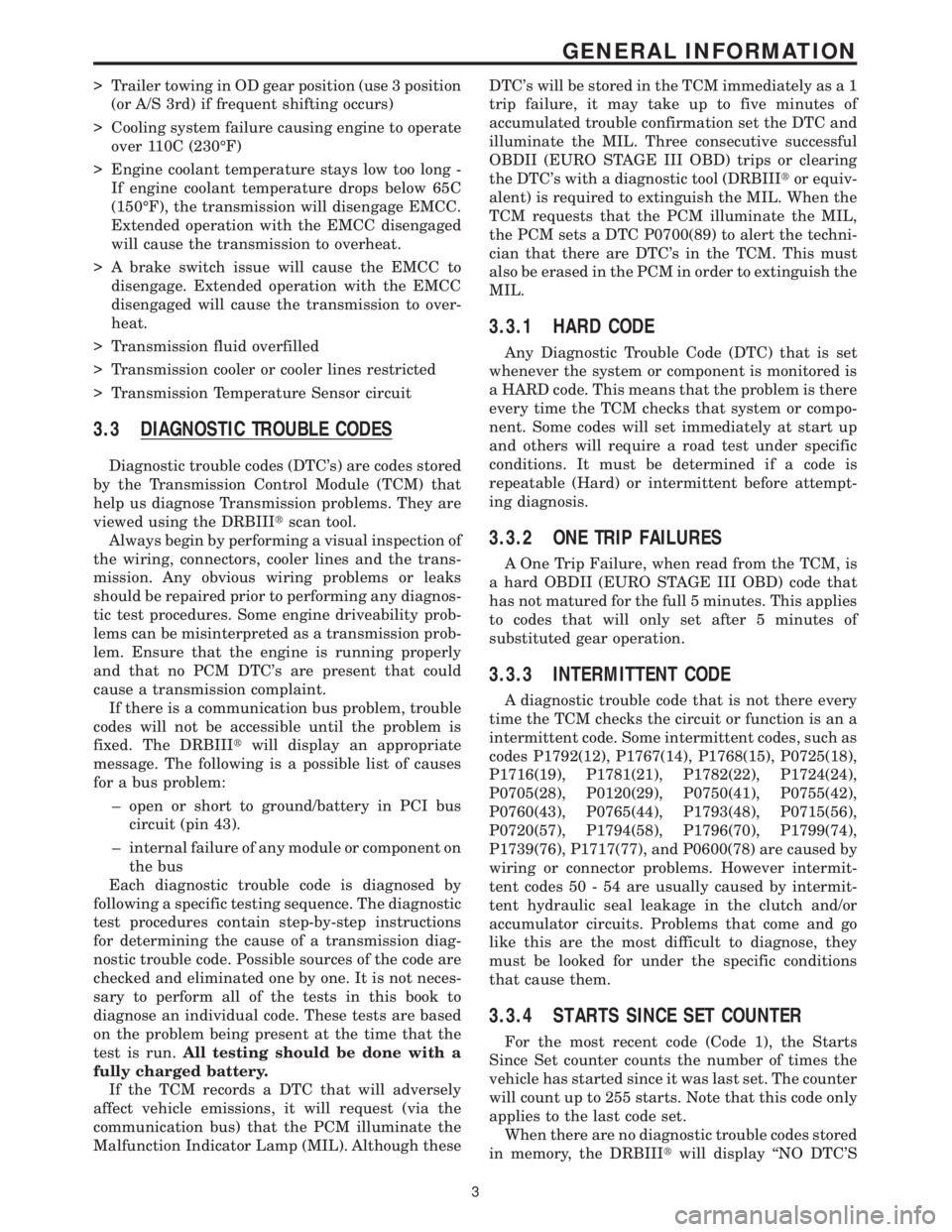
> Trailer towing in OD gear position (use 3 position
(or A/S 3rd) if frequent shifting occurs)
> Cooling system failure causing engine to operate
over 110C (230ÉF)
> Engine coolant temperature stays low too long -
If engine coolant temperature drops below 65C
(150ÉF), the transmission will disengage EMCC.
Extended operation with the EMCC disengaged
will cause the transmission to overheat.
> A brake switch issue will cause the EMCC to
disengage. Extended operation with the EMCC
disengaged will cause the transmission to over-
heat.
> Transmission fluid overfilled
> Transmission cooler or cooler lines restricted
> Transmission Temperature Sensor circuit
3.3 DIAGNOSTIC TROUBLE CODES
Diagnostic trouble codes (DTC's) are codes stored
by the Transmission Control Module (TCM) that
help us diagnose Transmission problems. They are
viewed using the DRBIIItscan tool.
Always begin by performing a visual inspection of
the wiring, connectors, cooler lines and the trans-
mission. Any obvious wiring problems or leaks
should be repaired prior to performing any diagnos-
tic test procedures. Some engine driveability prob-
lems can be misinterpreted as a transmission prob-
lem. Ensure that the engine is running properly
and that no PCM DTC's are present that could
cause a transmission complaint.
If there is a communication bus problem, trouble
codes will not be accessible until the problem is
fixed. The DRBIIItwill display an appropriate
message. The following is a possible list of causes
for a bus problem:
± open or short to ground/battery in PCI bus
circuit (pin 43).
± internal failure of any module or component on
the bus
Each diagnostic trouble code is diagnosed by
following a specific testing sequence. The diagnostic
test procedures contain step-by-step instructions
for determining the cause of a transmission diag-
nostic trouble code. Possible sources of the code are
checked and eliminated one by one. It is not neces-
sary to perform all of the tests in this book to
diagnose an individual code. These tests are based
on the problem being present at the time that the
test is run.All testing should be done with a
fully charged battery.
If the TCM records a DTC that will adversely
affect vehicle emissions, it will request (via the
communication bus) that the PCM illuminate the
Malfunction Indicator Lamp (MIL). Although theseDTC's will be stored in the TCM immediately as a 1
trip failure, it may take up to five minutes of
accumulated trouble confirmation set the DTC and
illuminate the MIL. Three consecutive successful
OBDII (EURO STAGE III OBD) trips or clearing
the DTC's with a diagnostic tool (DRBIIItor equiv-
alent) is required to extinguish the MIL. When the
TCM requests that the PCM illuminate the MIL,
the PCM sets a DTC P0700(89) to alert the techni-
cian that there are DTC's in the TCM. This must
also be erased in the PCM in order to extinguish the
MIL.
3.3.1 HARD CODE
Any Diagnostic Trouble Code (DTC) that is set
whenever the system or component is monitored is
a HARD code. This means that the problem is there
every time the TCM checks that system or compo-
nent. Some codes will set immediately at start up
and others will require a road test under specific
conditions. It must be determined if a code is
repeatable (Hard) or intermittent before attempt-
ing diagnosis.
3.3.2 ONE TRIP FAILURES
A One Trip Failure, when read from the TCM, is
a hard OBDII (EURO STAGE III OBD) code that
has not matured for the full 5 minutes. This applies
to codes that will only set after 5 minutes of
substituted gear operation.
3.3.3 INTERMITTENT CODE
A diagnostic trouble code that is not there every
time the TCM checks the circuit or function is an a
intermittent code. Some intermittent codes, such as
codes P1792(12), P1767(14), P1768(15), P0725(18),
P1716(19), P1781(21), P1782(22), P1724(24),
P0705(28), P0120(29), P0750(41), P0755(42),
P0760(43), P0765(44), P1793(48), P0715(56),
P0720(57), P1794(58), P1796(70), P1799(74),
P1739(76), P1717(77), and P0600(78) are caused by
wiring or connector problems. However intermit-
tent codes 50 - 54 are usually caused by intermit-
tent hydraulic seal leakage in the clutch and/or
accumulator circuits. Problems that come and go
like this are the most difficult to diagnose, they
must be looked for under the specific conditions
that cause them.
3.3.4 STARTS SINCE SET COUNTER
For the most recent code (Code 1), the Starts
Since Set counter counts the number of times the
vehicle has started since it was last set. The counter
will count up to 255 starts. Note that this code only
applies to the last code set.
When there are no diagnostic trouble codes stored
in memory, the DRBIIItwill display ``NO DTC'S
3
GENERAL INFORMATION
Page 4108 of 4284
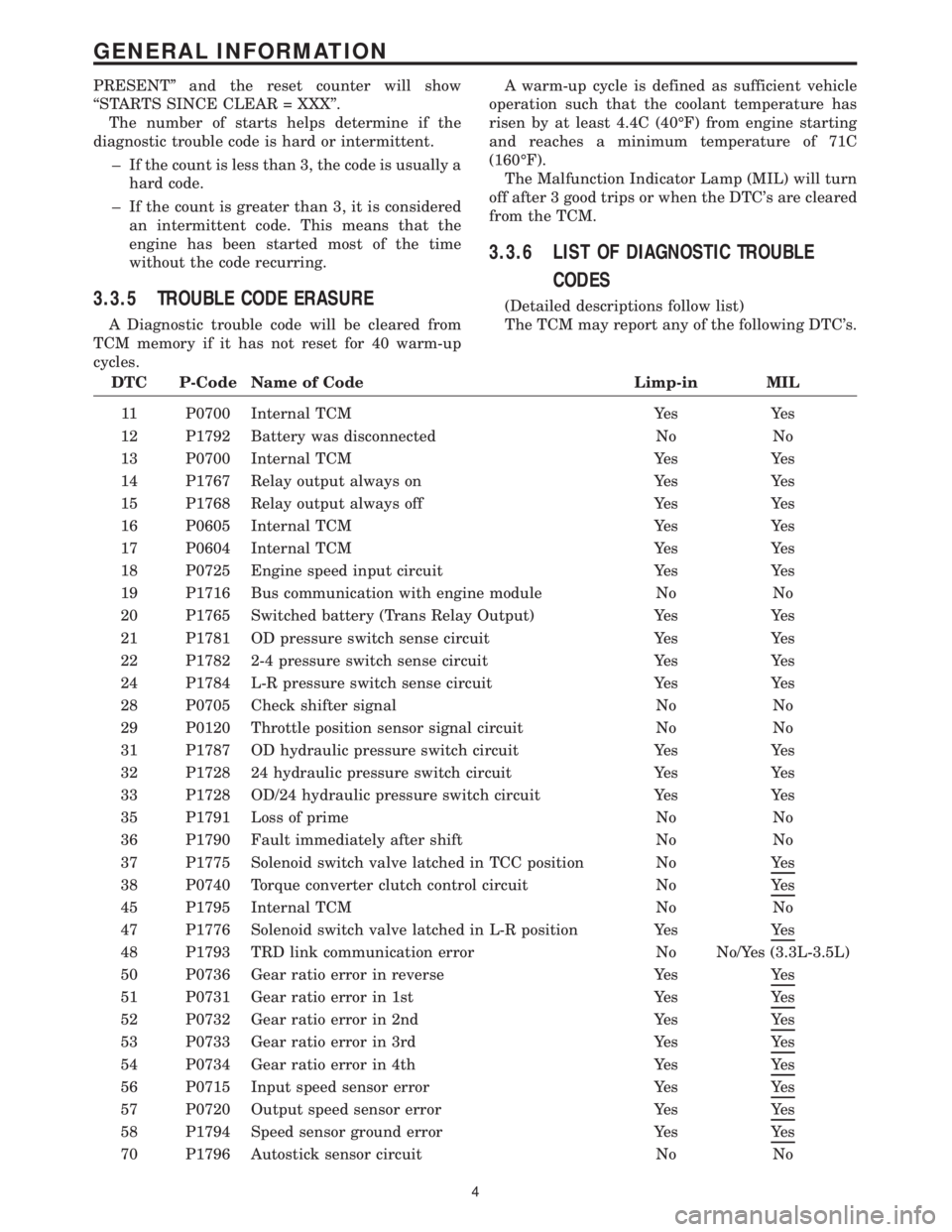
PRESENT'' and the reset counter will show
``STARTS SINCE CLEAR = XXX''.
The number of starts helps determine if the
diagnostic trouble code is hard or intermittent.
± If the count is less than 3, the code is usually a
hard code.
± If the count is greater than 3, it is considered
an intermittent code. This means that the
engine has been started most of the time
without the code recurring.
3.3.5 TROUBLE CODE ERASURE
A Diagnostic trouble code will be cleared from
TCM memory if it has not reset for 40 warm-up
cycles.A warm-up cycle is defined as sufficient vehicle
operation such that the coolant temperature has
risen by at least 4.4C (40ÉF) from engine starting
and reaches a minimum temperature of 71C
(160ÉF).
The Malfunction Indicator Lamp (MIL) will turn
off after 3 good trips or when the DTC's are cleared
from the TCM.
3.3.6 LIST OF DIAGNOSTIC TROUBLE
CODES
(Detailed descriptions follow list)
The TCM may report any of the following DTC's.
DTC P-Code Name of Code Limp-in MIL
11 P0700 Internal TCM Yes Yes
12 P1792 Battery was disconnected No No
13 P0700 Internal TCM Yes Yes
14 P1767 Relay output always on Yes Yes
15 P1768 Relay output always off Yes Yes
16 P0605 Internal TCM Yes Yes
17 P0604 Internal TCM Yes Yes
18 P0725 Engine speed input circuit Yes Yes
19 P1716 Bus communication with engine module No No
20 P1765 Switched battery (Trans Relay Output) Yes Yes
21 P1781 OD pressure switch sense circuit Yes Yes
22 P1782 2-4 pressure switch sense circuit Yes Yes
24 P1784 L-R pressure switch sense circuit Yes Yes
28 P0705 Check shifter signal No No
29 P0120 Throttle position sensor signal circuit No No
31 P1787 OD hydraulic pressure switch circuit Yes Yes
32 P1728 24 hydraulic pressure switch circuit Yes Yes
33 P1728 OD/24 hydraulic pressure switch circuit Yes Yes
35 P1791 Loss of prime No No
36 P1790 Fault immediately after shift No No
37 P1775 Solenoid switch valve latched in TCC position No Yes
38 P0740 Torque converter clutch control circuit No Yes
45 P1795 Internal TCM No No
47 P1776 Solenoid switch valve latched in L-R position Yes Yes
48 P1793 TRD link communication error No No/Yes (3.3L-3.5L)
50 P0736 Gear ratio error in reverse Yes Yes
51 P0731 Gear ratio error in 1st Yes Yes
52 P0732 Gear ratio error in 2nd Yes Yes
53 P0733 Gear ratio error in 3rd Yes Yes
54 P0734 Gear ratio error in 4th Yes Yes
56 P0715 Input speed sensor error Yes Yes
57 P0720 Output speed sensor error Yes Yes
58 P1794 Speed sensor ground error Yes Yes
70 P1796 Autostick sensor circuit No No
4
GENERAL INFORMATION
Page 4110 of 4284
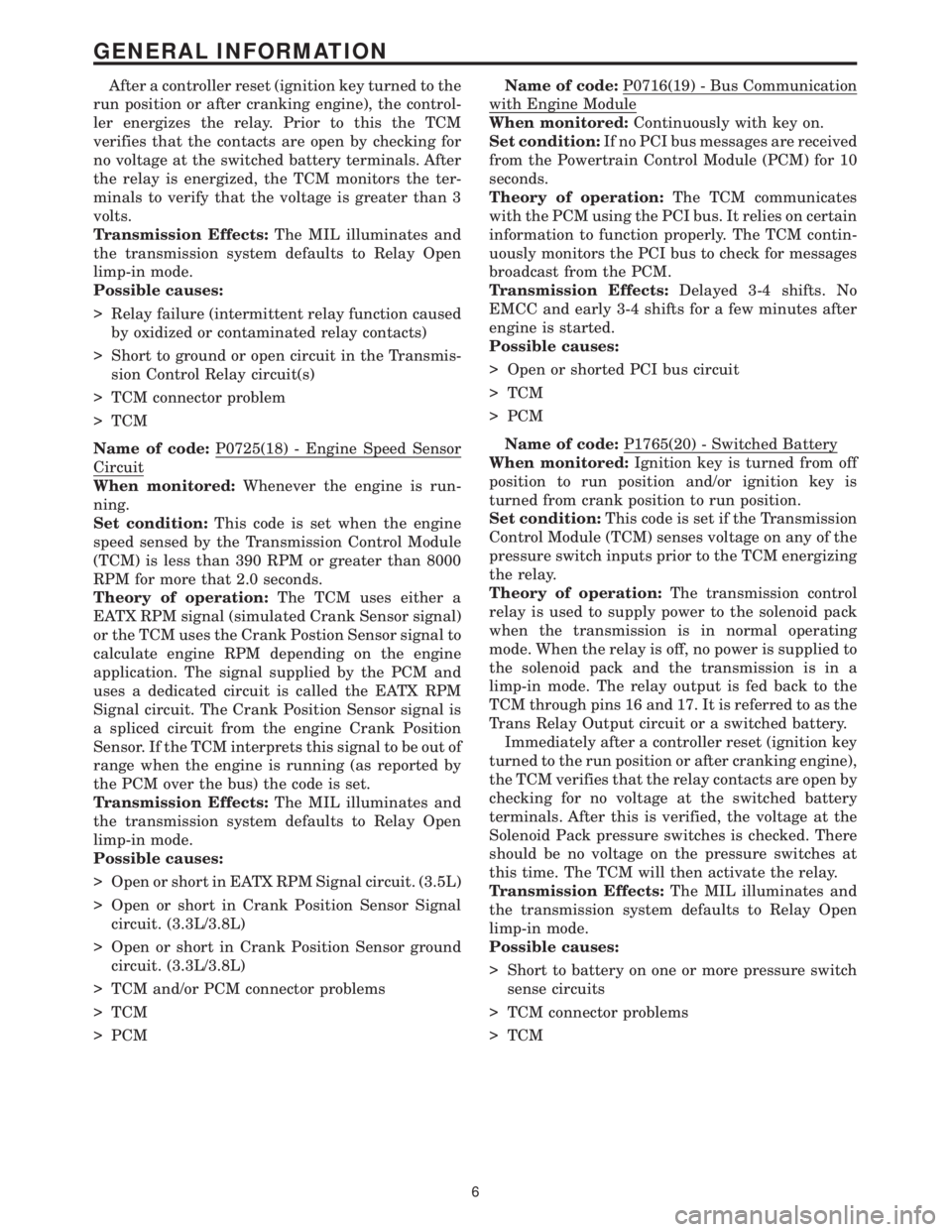
After a controller reset (ignition key turned to the
run position or after cranking engine), the control-
ler energizes the relay. Prior to this the TCM
verifies that the contacts are open by checking for
no voltage at the switched battery terminals. After
the relay is energized, the TCM monitors the ter-
minals to verify that the voltage is greater than 3
volts.
Transmission Effects:The MIL illuminates and
the transmission system defaults to Relay Open
limp-in mode.
Possible causes:
> Relay failure (intermittent relay function caused
by oxidized or contaminated relay contacts)
> Short to ground or open circuit in the Transmis-
sion Control Relay circuit(s)
> TCM connector problem
> TCM
Name of code:P0725(18) - Engine Speed Sensor
Circuit
When monitored:Whenever the engine is run-
ning.
Set condition:This code is set when the engine
speed sensed by the Transmission Control Module
(TCM) is less than 390 RPM or greater than 8000
RPM for more that 2.0 seconds.
Theory of operation:The TCM uses either a
EATX RPM signal (simulated Crank Sensor signal)
or the TCM uses the Crank Postion Sensor signal to
calculate engine RPM depending on the engine
application. The signal supplied by the PCM and
uses a dedicated circuit is called the EATX RPM
Signal circuit. The Crank Position Sensor signal is
a spliced circuit from the engine Crank Position
Sensor. If the TCM interprets this signal to be out of
range when the engine is running (as reported by
the PCM over the bus) the code is set.
Transmission Effects:The MIL illuminates and
the transmission system defaults to Relay Open
limp-in mode.
Possible causes:
> Open or short in EATX RPM Signal circuit. (3.5L)
> Open or short in Crank Position Sensor Signal
circuit. (3.3L/3.8L)
> Open or short in Crank Position Sensor ground
circuit. (3.3L/3.8L)
> TCM and/or PCM connector problems
> TCM
> PCMName of code:P0716(19) - Bus Communication
with Engine Module
When monitored:Continuously with key on.
Set condition:If no PCI bus messages are received
from the Powertrain Control Module (PCM) for 10
seconds.
Theory of operation:The TCM communicates
with the PCM using the PCI bus. It relies on certain
information to function properly. The TCM contin-
uously monitors the PCI bus to check for messages
broadcast from the PCM.
Transmission Effects:Delayed 3-4 shifts. No
EMCC and early 3-4 shifts for a few minutes after
engine is started.
Possible causes:
> Open or shorted PCI bus circuit
> TCM
> PCM
Name of code:P1765(20) - Switched Battery
When monitored:Ignition key is turned from off
position to run position and/or ignition key is
turned from crank position to run position.
Set condition:This code is set if the Transmission
Control Module (TCM) senses voltage on any of the
pressure switch inputs prior to the TCM energizing
the relay.
Theory of operation:The transmission control
relay is used to supply power to the solenoid pack
when the transmission is in normal operating
mode. When the relay is off, no power is supplied to
the solenoid pack and the transmission is in a
limp-in mode. The relay output is fed back to the
TCM through pins 16 and 17. It is referred to as the
Trans Relay Output circuit or a switched battery.
Immediately after a controller reset (ignition key
turned to the run position or after cranking engine),
the TCM verifies that the relay contacts are open by
checking for no voltage at the switched battery
terminals. After this is verified, the voltage at the
Solenoid Pack pressure switches is checked. There
should be no voltage on the pressure switches at
this time. The TCM will then activate the relay.
Transmission Effects:The MIL illuminates and
the transmission system defaults to Relay Open
limp-in mode.
Possible causes:
> Short to battery on one or more pressure switch
sense circuits
> TCM connector problems
> TCM
6
GENERAL INFORMATION
Page 4112 of 4284
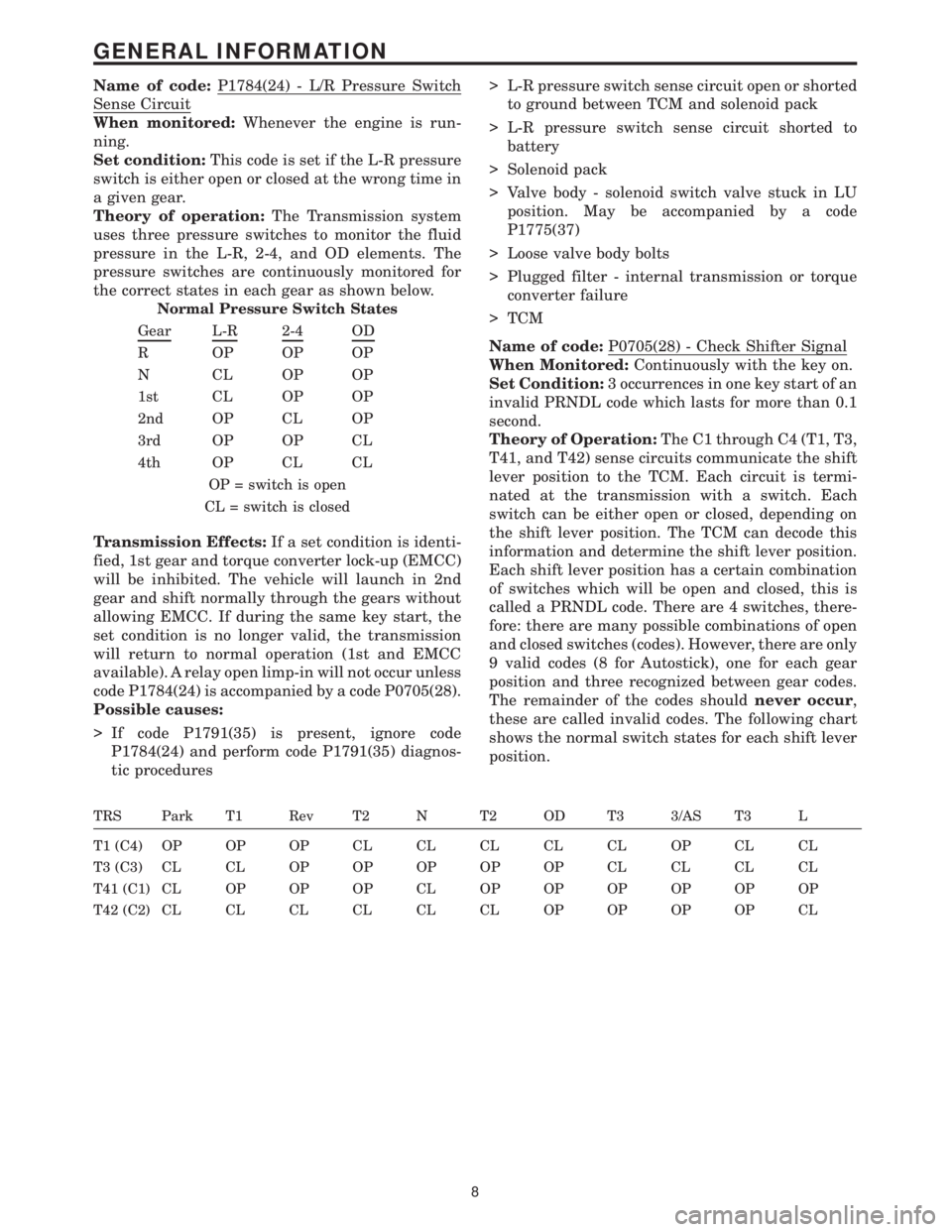
Name of code:P1784(24) - L/R Pressure Switch
Sense Circuit
When monitored:Whenever the engine is run-
ning.
Set condition:This code is set if the L-R pressure
switch is either open or closed at the wrong time in
a given gear.
Theory of operation:The Transmission system
uses three pressure switches to monitor the fluid
pressure in the L-R, 2-4, and OD elements. The
pressure switches are continuously monitored for
the correct states in each gear as shown below.
Normal Pressure Switch States
Gear
L-R2-4OD
R OPOPOP
NCLOPOP
1st CL OP OP
2nd OP CL OP
3rd OP OP CL
4th OP CL CL
OP = switch is open
CL = switch is closed
Transmission Effects:If a set condition is identi-
fied, 1st gear and torque converter lock-up (EMCC)
will be inhibited. The vehicle will launch in 2nd
gear and shift normally through the gears without
allowing EMCC. If during the same key start, the
set condition is no longer valid, the transmission
will return to normal operation (1st and EMCC
available). A relay open limp-in will not occur unless
code P1784(24) is accompanied by a code P0705(28).
Possible causes:
> If code P1791(35) is present, ignore code
P1784(24) and perform code P1791(35) diagnos-
tic procedures> L-R pressure switch sense circuit open or shorted
to ground between TCM and solenoid pack
> L-R pressure switch sense circuit shorted to
battery
> Solenoid pack
> Valve body - solenoid switch valve stuck in LU
position. May be accompanied by a code
P1775(37)
> Loose valve body bolts
> Plugged filter - internal transmission or torque
converter failure
> TCM
Name of code:P0705(28) - Check Shifter Signal
When Monitored:Continuously with the key on.
Set Condition:3 occurrences in one key start of an
invalid PRNDL code which lasts for more than 0.1
second.
Theory of Operation:The C1 through C4 (T1, T3,
T41, and T42) sense circuits communicate the shift
lever position to the TCM. Each circuit is termi-
nated at the transmission with a switch. Each
switch can be either open or closed, depending on
the shift lever position. The TCM can decode this
information and determine the shift lever position.
Each shift lever position has a certain combination
of switches which will be open and closed, this is
called a PRNDL code. There are 4 switches, there-
fore: there are many possible combinations of open
and closed switches (codes). However, there are only
9 valid codes (8 for Autostick), one for each gear
position and three recognized between gear codes.
The remainder of the codes shouldnever occur,
these are called invalid codes. The following chart
shows the normal switch states for each shift lever
position.
TRS Park T1 Rev T2 N T2 OD T3 3/AS T3 L
T1 (C4) OP OP OP CL CL CL CL CL OP CL CL
T3 (C3) CL CL OP OP OP OP OP CL CL CL CL
T41 (C1) CL OP OP OP CL OP OP OP OP OP OP
T42 (C2) CL CL CL CL CL CL OP OP OP OP CL
8
GENERAL INFORMATION
Page 4113 of 4284
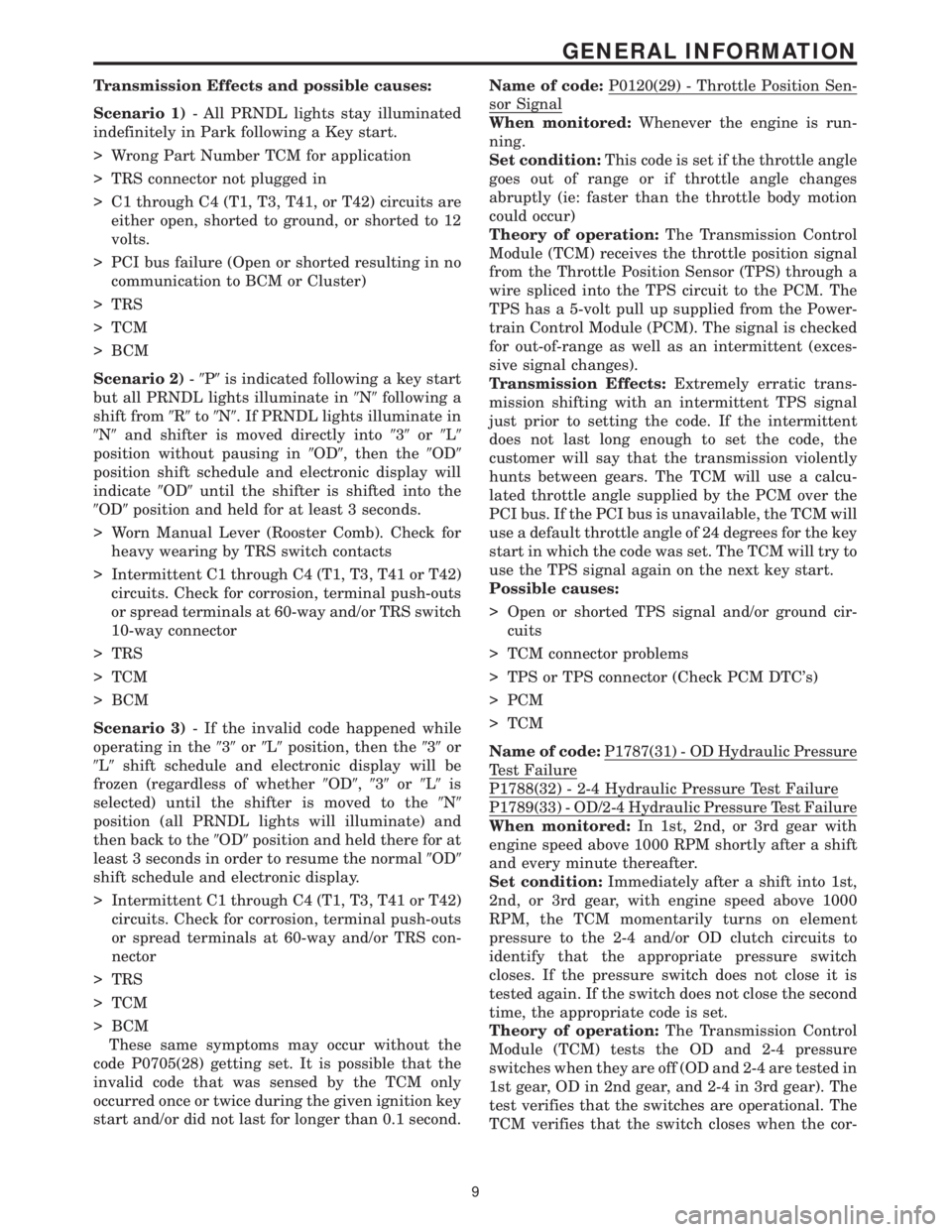
Transmission Effects and possible causes:
Scenario 1)- All PRNDL lights stay illuminated
indefinitely in Park following a Key start.
> Wrong Part Number TCM for application
> TRS connector not plugged in
> C1 through C4 (T1, T3, T41, or T42) circuits are
either open, shorted to ground, or shorted to 12
volts.
> PCI bus failure (Open or shorted resulting in no
communication to BCM or Cluster)
> TRS
> TCM
> BCM
Scenario 2)-9P9is indicated following a key start
but all PRNDL lights illuminate in9N9following a
shift from9R9to9N9. If PRNDL lights illuminate in
9N9and shifter is moved directly into939or9L9
position without pausing in9OD9, then the9OD9
position shift schedule and electronic display will
indicate9OD9until the shifter is shifted into the
9OD9position and held for at least 3 seconds.
> Worn Manual Lever (Rooster Comb). Check for
heavy wearing by TRS switch contacts
> Intermittent C1 through C4 (T1, T3, T41 or T42)
circuits. Check for corrosion, terminal push-outs
or spread terminals at 60-way and/or TRS switch
10-way connector
> TRS
> TCM
> BCM
Scenario 3)- If the invalid code happened while
operating in the939or9L9position, then the939or
9L9shift schedule and electronic display will be
frozen (regardless of whether9OD9,939or9L9is
selected) until the shifter is moved to the9N9
position (all PRNDL lights will illuminate) and
then back to the9OD9position and held there for at
least 3 seconds in order to resume the normal9OD9
shift schedule and electronic display.
> Intermittent C1 through C4 (T1, T3, T41 or T42)
circuits. Check for corrosion, terminal push-outs
or spread terminals at 60-way and/or TRS con-
nector
> TRS
> TCM
> BCM
These same symptoms may occur without the
code P0705(28) getting set. It is possible that the
invalid code that was sensed by the TCM only
occurred once or twice during the given ignition key
start and/or did not last for longer than 0.1 second.Name of code:P0120(29) - Throttle Position Sen-
sor Signal
When monitored:Whenever the engine is run-
ning.
Set condition:This code is set if the throttle angle
goes out of range or if throttle angle changes
abruptly (ie: faster than the throttle body motion
could occur)
Theory of operation:The Transmission Control
Module (TCM) receives the throttle position signal
from the Throttle Position Sensor (TPS) through a
wire spliced into the TPS circuit to the PCM. The
TPS has a 5-volt pull up supplied from the Power-
train Control Module (PCM). The signal is checked
for out-of-range as well as an intermittent (exces-
sive signal changes).
Transmission Effects:Extremely erratic trans-
mission shifting with an intermittent TPS signal
just prior to setting the code. If the intermittent
does not last long enough to set the code, the
customer will say that the transmission violently
hunts between gears. The TCM will use a calcu-
lated throttle angle supplied by the PCM over the
PCI bus. If the PCI bus is unavailable, the TCM will
use a default throttle angle of 24 degrees for the key
start in which the code was set. The TCM will try to
use the TPS signal again on the next key start.
Possible causes:
> Open or shorted TPS signal and/or ground cir-
cuits
> TCM connector problems
> TPS or TPS connector (Check PCM DTC's)
> PCM
> TCM
Name of code:P1787(31) - OD Hydraulic Pressure
Test Failure
P1788(32) - 2-4 Hydraulic Pressure Test Failure
P1789(33) - OD/2-4 Hydraulic Pressure Test Failure
When monitored:In 1st, 2nd, or 3rd gear with
engine speed above 1000 RPM shortly after a shift
and every minute thereafter.
Set condition:Immediately after a shift into 1st,
2nd, or 3rd gear, with engine speed above 1000
RPM, the TCM momentarily turns on element
pressure to the 2-4 and/or OD clutch circuits to
identify that the appropriate pressure switch
closes. If the pressure switch does not close it is
tested again. If the switch does not close the second
time, the appropriate code is set.
Theory of operation:The Transmission Control
Module (TCM) tests the OD and 2-4 pressure
switches when they are off (OD and 2-4 are tested in
1st gear, OD in 2nd gear, and 2-4 in 3rd gear). The
test verifies that the switches are operational. The
TCM verifies that the switch closes when the cor-
9
GENERAL INFORMATION
Page 4115 of 4284
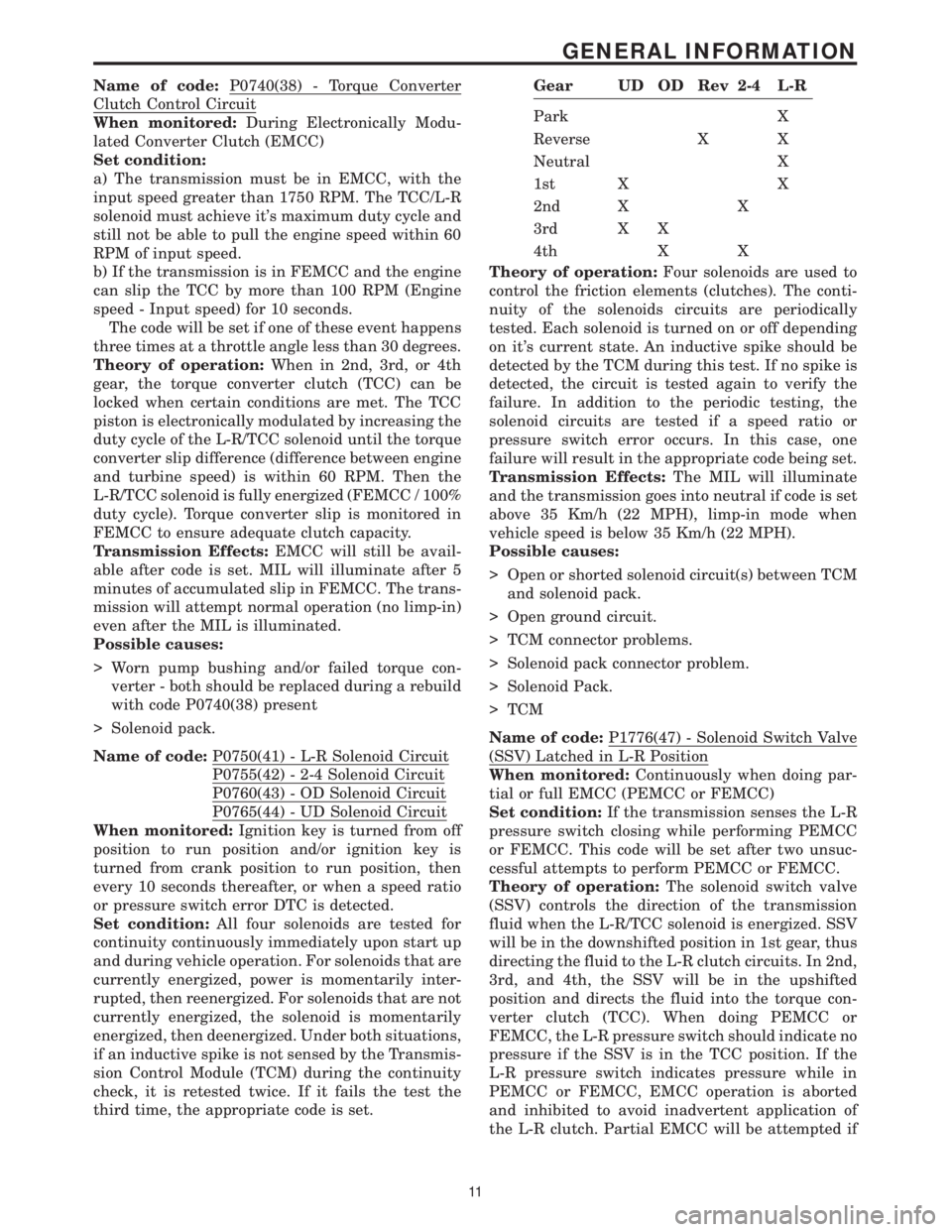
Name of code:P0740(38) - Torque Converter
Clutch Control Circuit
When monitored:During Electronically Modu-
lated Converter Clutch (EMCC)
Set condition:
a) The transmission must be in EMCC, with the
input speed greater than 1750 RPM. The TCC/L-R
solenoid must achieve it's maximum duty cycle and
still not be able to pull the engine speed within 60
RPM of input speed.
b) If the transmission is in FEMCC and the engine
can slip the TCC by more than 100 RPM (Engine
speed - Input speed) for 10 seconds.
The code will be set if one of these event happens
three times at a throttle angle less than 30 degrees.
Theory of operation:When in 2nd, 3rd, or 4th
gear, the torque converter clutch (TCC) can be
locked when certain conditions are met. The TCC
piston is electronically modulated by increasing the
duty cycle of the L-R/TCC solenoid until the torque
converter slip difference (difference between engine
and turbine speed) is within 60 RPM. Then the
L-R/TCC solenoid is fully energized (FEMCC / 100%
duty cycle). Torque converter slip is monitored in
FEMCC to ensure adequate clutch capacity.
Transmission Effects:EMCC will still be avail-
able after code is set. MIL will illuminate after 5
minutes of accumulated slip in FEMCC. The trans-
mission will attempt normal operation (no limp-in)
even after the MIL is illuminated.
Possible causes:
> Worn pump bushing and/or failed torque con-
verter - both should be replaced during a rebuild
with code P0740(38) present
> Solenoid pack.
Name of code:P0750(41) - L-R Solenoid Circuit
P0755(42) - 2-4 Solenoid Circuit
P0760(43) - OD Solenoid Circuit
P0765(44) - UD Solenoid Circuit
When monitored:Ignition key is turned from off
position to run position and/or ignition key is
turned from crank position to run position, then
every 10 seconds thereafter, or when a speed ratio
or pressure switch error DTC is detected.
Set condition:All four solenoids are tested for
continuity continuously immediately upon start up
and during vehicle operation. For solenoids that are
currently energized, power is momentarily inter-
rupted, then reenergized. For solenoids that are not
currently energized, the solenoid is momentarily
energized, then deenergized. Under both situations,
if an inductive spike is not sensed by the Transmis-
sion Control Module (TCM) during the continuity
check, it is retested twice. If it fails the test the
third time, the appropriate code is set.
Gear UD OD Rev 2-4 L-R
Park X
Reverse X X
Neutral X
1st X X
2nd X X
3rd X X
4th X X
Theory of operation:Four solenoids are used to
control the friction elements (clutches). The conti-
nuity of the solenoids circuits are periodically
tested. Each solenoid is turned on or off depending
on it's current state. An inductive spike should be
detected by the TCM during this test. If no spike is
detected, the circuit is tested again to verify the
failure. In addition to the periodic testing, the
solenoid circuits are tested if a speed ratio or
pressure switch error occurs. In this case, one
failure will result in the appropriate code being set.
Transmission Effects:The MIL will illuminate
and the transmission goes into neutral if code is set
above 35 Km/h (22 MPH), limp-in mode when
vehicle speed is below 35 Km/h (22 MPH).
Possible causes:
> Open or shorted solenoid circuit(s) between TCM
and solenoid pack.
> Open ground circuit.
> TCM connector problems.
> Solenoid pack connector problem.
> Solenoid Pack.
> TCM
Name of code:P1776(47) - Solenoid Switch Valve
(SSV) Latched in L-R Position
When monitored:Continuously when doing par-
tial or full EMCC (PEMCC or FEMCC)
Set condition:If the transmission senses the L-R
pressure switch closing while performing PEMCC
or FEMCC. This code will be set after two unsuc-
cessful attempts to perform PEMCC or FEMCC.
Theory of operation:The solenoid switch valve
(SSV) controls the direction of the transmission
fluid when the L-R/TCC solenoid is energized. SSV
will be in the downshifted position in 1st gear, thus
directing the fluid to the L-R clutch circuits. In 2nd,
3rd, and 4th, the SSV will be in the upshifted
position and directs the fluid into the torque con-
verter clutch (TCC). When doing PEMCC or
FEMCC, the L-R pressure switch should indicate no
pressure if the SSV is in the TCC position. If the
L-R pressure switch indicates pressure while in
PEMCC or FEMCC, EMCC operation is aborted
and inhibited to avoid inadvertent application of
the L-R clutch. Partial EMCC will be attempted if
11
GENERAL INFORMATION
Page 4116 of 4284
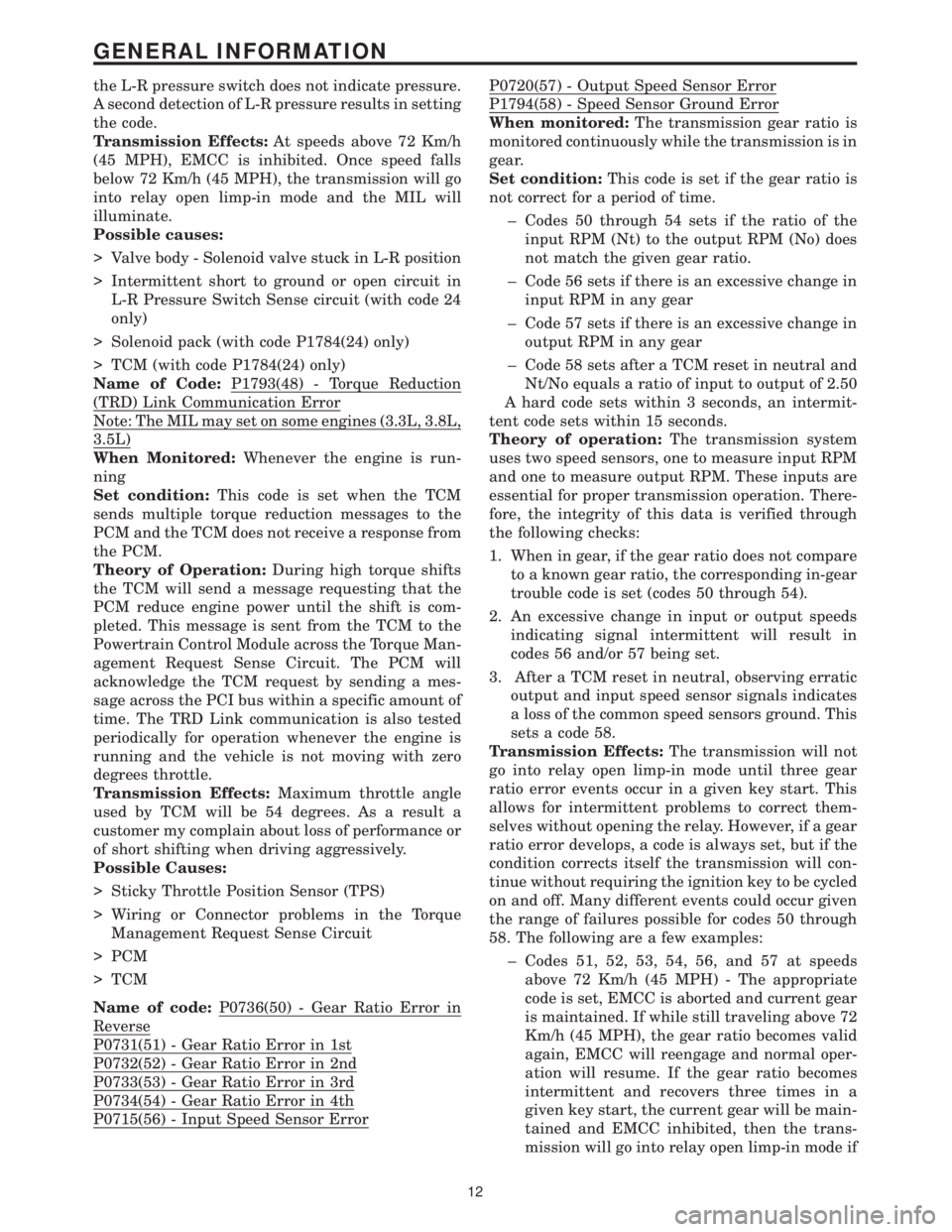
the L-R pressure switch does not indicate pressure.
A second detection of L-R pressure results in setting
the code.
Transmission Effects:At speeds above 72 Km/h
(45 MPH), EMCC is inhibited. Once speed falls
below 72 Km/h (45 MPH), the transmission will go
into relay open limp-in mode and the MIL will
illuminate.
Possible causes:
> Valve body - Solenoid valve stuck in L-R position
> Intermittent short to ground or open circuit in
L-R Pressure Switch Sense circuit (with code 24
only)
> Solenoid pack (with code P1784(24) only)
> TCM (with code P1784(24) only)
Name of Code:P1793(48) - Torque Reduction
(TRD) Link Communication Error
Note: The MIL may set on some engines (3.3L, 3.8L,
3.5L)
When Monitored:Whenever the engine is run-
ning
Set condition:This code is set when the TCM
sends multiple torque reduction messages to the
PCM and the TCM does not receive a response from
the PCM.
Theory of Operation:During high torque shifts
the TCM will send a message requesting that the
PCM reduce engine power until the shift is com-
pleted. This message is sent from the TCM to the
Powertrain Control Module across the Torque Man-
agement Request Sense Circuit. The PCM will
acknowledge the TCM request by sending a mes-
sage across the PCI bus within a specific amount of
time. The TRD Link communication is also tested
periodically for operation whenever the engine is
running and the vehicle is not moving with zero
degrees throttle.
Transmission Effects:Maximum throttle angle
used by TCM will be 54 degrees. As a result a
customer my complain about loss of performance or
of short shifting when driving aggressively.
Possible Causes:
> Sticky Throttle Position Sensor (TPS)
> Wiring or Connector problems in the Torque
Management Request Sense Circuit
> PCM
> TCM
Name of code:P0736(50) - Gear Ratio Error in
Reverse
P0731(51) - Gear Ratio Error in 1st
P0732(52) - Gear Ratio Error in 2nd
P0733(53) - Gear Ratio Error in 3rd
P0734(54) - Gear Ratio Error in 4th
P0715(56) - Input Speed Sensor Error
P0720(57) - Output Speed Sensor Error
P1794(58) - Speed Sensor Ground Error
When monitored:The transmission gear ratio is
monitored continuously while the transmission is in
gear.
Set condition:This code is set if the gear ratio is
not correct for a period of time.
± Codes 50 through 54 sets if the ratio of the
input RPM (Nt) to the output RPM (No) does
not match the given gear ratio.
± Code 56 sets if there is an excessive change in
input RPM in any gear
± Code 57 sets if there is an excessive change in
output RPM in any gear
± Code 58 sets after a TCM reset in neutral and
Nt/No equals a ratio of input to output of 2.50
A hard code sets within 3 seconds, an intermit-
tent code sets within 15 seconds.
Theory of operation:The transmission system
uses two speed sensors, one to measure input RPM
and one to measure output RPM. These inputs are
essential for proper transmission operation. There-
fore, the integrity of this data is verified through
the following checks:
1. When in gear, if the gear ratio does not compare
to a known gear ratio, the corresponding in-gear
trouble code is set (codes 50 through 54).
2. An excessive change in input or output speeds
indicating signal intermittent will result in
codes 56 and/or 57 being set.
3. After a TCM reset in neutral, observing erratic
output and input speed sensor signals indicates
a loss of the common speed sensors ground. This
sets a code 58.
Transmission Effects:The transmission will not
go into relay open limp-in mode until three gear
ratio error events occur in a given key start. This
allows for intermittent problems to correct them-
selves without opening the relay. However, if a gear
ratio error develops, a code is always set, but if the
condition corrects itself the transmission will con-
tinue without requiring the ignition key to be cycled
on and off. Many different events could occur given
the range of failures possible for codes 50 through
58. The following are a few examples:
± Codes 51, 52, 53, 54, 56, and 57 at speeds
above 72 Km/h (45 MPH) - The appropriate
code is set, EMCC is aborted and current gear
is maintained. If while still traveling above 72
Km/h (45 MPH), the gear ratio becomes valid
again, EMCC will reengage and normal oper-
ation will resume. If the gear ratio becomes
intermittent and recovers three times in a
given key start, the current gear will be main-
tained and EMCC inhibited, then the trans-
mission will go into relay open limp-in mode if
12
GENERAL INFORMATION