sensor CHRYSLER VOYAGER 2004 Service Manual
[x] Cancel search | Manufacturer: CHRYSLER, Model Year: 2004, Model line: VOYAGER, Model: CHRYSLER VOYAGER 2004Pages: 2585, PDF Size: 62.54 MB
Page 2012 of 2585
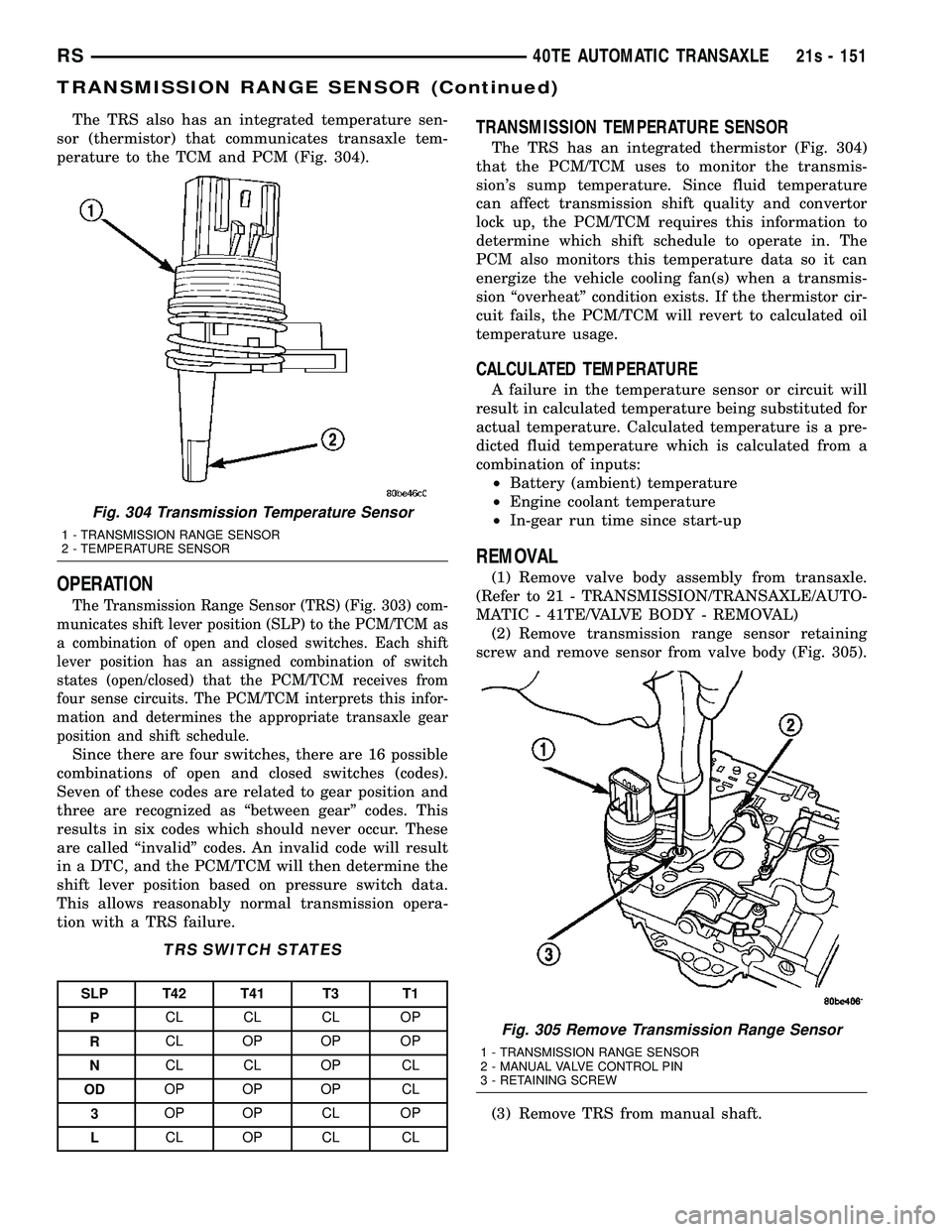
The TRS also has an integrated temperature sen-
sor (thermistor) that communicates transaxle tem-
perature to the TCM and PCM (Fig. 304).
OPERATION
The Transmission Range Sensor (TRS) (Fig. 303) com-
municates shift lever position (SLP) to the PCM/TCM as
a combination of open and closed switches. Each shift
lever position has an assigned combination of switch
states (open/closed) that the PCM/TCM receives from
four sense circuits. The PCM/TCM interprets this infor-
mation and determines the appropriate transaxle gear
position and shift schedule.
Since there are four switches, there are 16 possible
combinations of open and closed switches (codes).
Seven of these codes are related to gear position and
three are recognized as ªbetween gearº codes. This
results in six codes which should never occur. These
are called ªinvalidº codes. An invalid code will result
in a DTC, and the PCM/TCM will then determine the
shift lever position based on pressure switch data.
This allows reasonably normal transmission opera-
tion with a TRS failure.
TRS SWITCH STATES
SLP T42 T41 T3 T1
P CL CL CL OP
R CL OP OP OP
N CL CL OP CL
OD OP OP OP CL
3 OP OP CL OP
L CL OP CL CL
TRANSMISSION TEMPERATURE SENSOR
The TRS has an integrated thermistor (Fig. 304)
that the PCM/TCM uses to monitor the transmis-
sion's sump temperature. Since fluid temperature
can affect transmission shift quality and convertor
lock up, the PCM/TCM requires this information to
determine which shift schedule to operate in. The
PCM also monitors this temperature data so it can
energize the vehicle cooling fan(s) when a transmis-
sion ªoverheatº condition exists. If the thermistor cir-
cuit fails, the PCM/TCM will revert to calculated oil
temperature usage.
CALCULATED TEMPERATURE
A failure in the temperature sensor or circuit will
result in calculated temperature being substituted for
actual temperature. Calculated temperature is a pre-
dicted fluid temperature which is calculated from a
combination of inputs: ² Battery (ambient) temperature
² Engine coolant temperature
² In-gear run time since start-up
REMOVAL
(1) Remove valve body assembly from transaxle.
(Refer to 21 - TRANSMISSION/TRANSAXLE/AUTO-
MATIC - 41TE/VALVE BODY - REMOVAL) (2) Remove transmission range sensor retaining
screw and remove sensor from valve body (Fig. 305).
(3) Remove TRS from manual shaft.
Fig. 304 Transmission Temperature Sensor
1 - TRANSMISSION RANGE SENSOR
2 - TEMPERATURE SENSOR
Fig. 305 Remove Transmission Range Sensor
1 - TRANSMISSION RANGE SENSOR
2 - MANUAL VALVE CONTROL PIN
3 - RETAINING SCREW
RS 40TE AUTOMATIC TRANSAXLE21s - 151
TRANSMISSION RANGE SENSOR (Continued)
Page 2013 of 2585
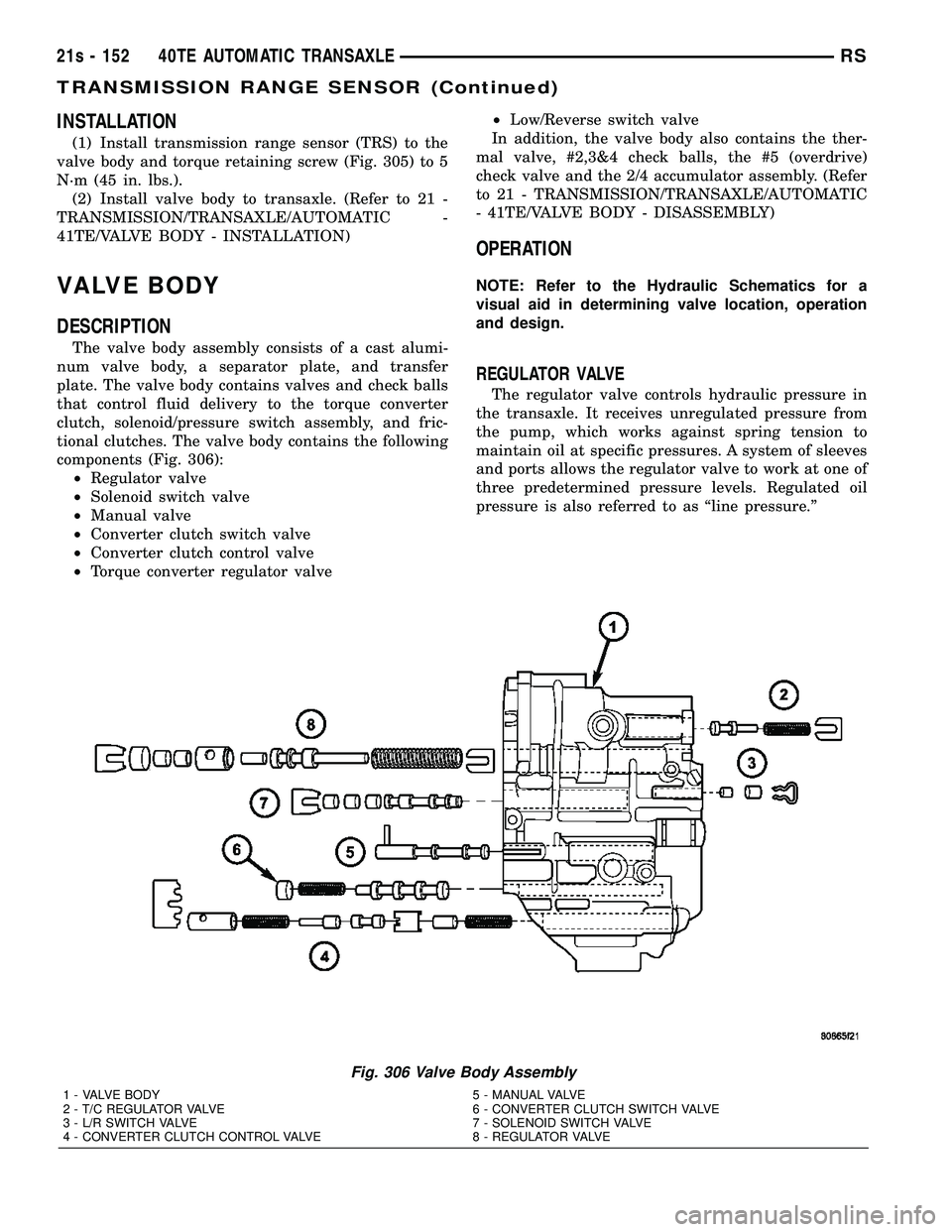
INSTALLATION
(1) Install transmission range sensor (TRS) to the
valve body and torque retaining screw (Fig. 305) to 5
N´m (45 in. lbs.). (2) Install valve body to transaxle. (Refer to 21 -
TRANSMISSION/TRANSAXLE/AUTOMATIC -
41TE/VALVE BODY - INSTALLATION)
VALVE BODY
DESCRIPTION
The valve body assembly consists of a cast alumi-
num valve body, a separator plate, and transfer
plate. The valve body contains valves and check balls
that control fluid delivery to the torque converter
clutch, solenoid/pressure switch assembly, and fric-
tional clutches. The valve body contains the following
components (Fig. 306): ² Regulator valve
² Solenoid switch valve
² Manual valve
² Converter clutch switch valve
² Converter clutch control valve
² Torque converter regulator valve ²
Low/Reverse switch valve
In addition, the valve body also contains the ther-
mal valve, #2,3&4 check balls, the #5 (overdrive)
check valve and the 2/4 accumulator assembly. (Refer
to 21 - TRANSMISSION/TRANSAXLE/AUTOMATIC
- 41TE/VALVE BODY - DISASSEMBLY)
OPERATION
NOTE: Refer to the Hydraulic Schematics for a
visual aid in determining valve location, operation
and design.
REGULATOR VALVE
The regulator valve controls hydraulic pressure in
the transaxle. It receives unregulated pressure from
the pump, which works against spring tension to
maintain oil at specific pressures. A system of sleeves
and ports allows the regulator valve to work at one of
three predetermined pressure levels. Regulated oil
pressure is also referred to as ªline pressure.º
Fig. 306 Valve Body Assembly
1 - VALVE BODY 5 - MANUAL VALVE
2 - T/C REGULATOR VALVE 6 - CONVERTER CLUTCH SWITCH VALVE
3 - L/R SWITCH VALVE 7 - SOLENOID SWITCH VALVE
4 - CONVERTER CLUTCH CONTROL VALVE 8 - REGULATOR VALVE
21s - 152 40TE AUTOMATIC TRANSAXLERS
TRANSMISSION RANGE SENSOR (Continued)
Page 2016 of 2585
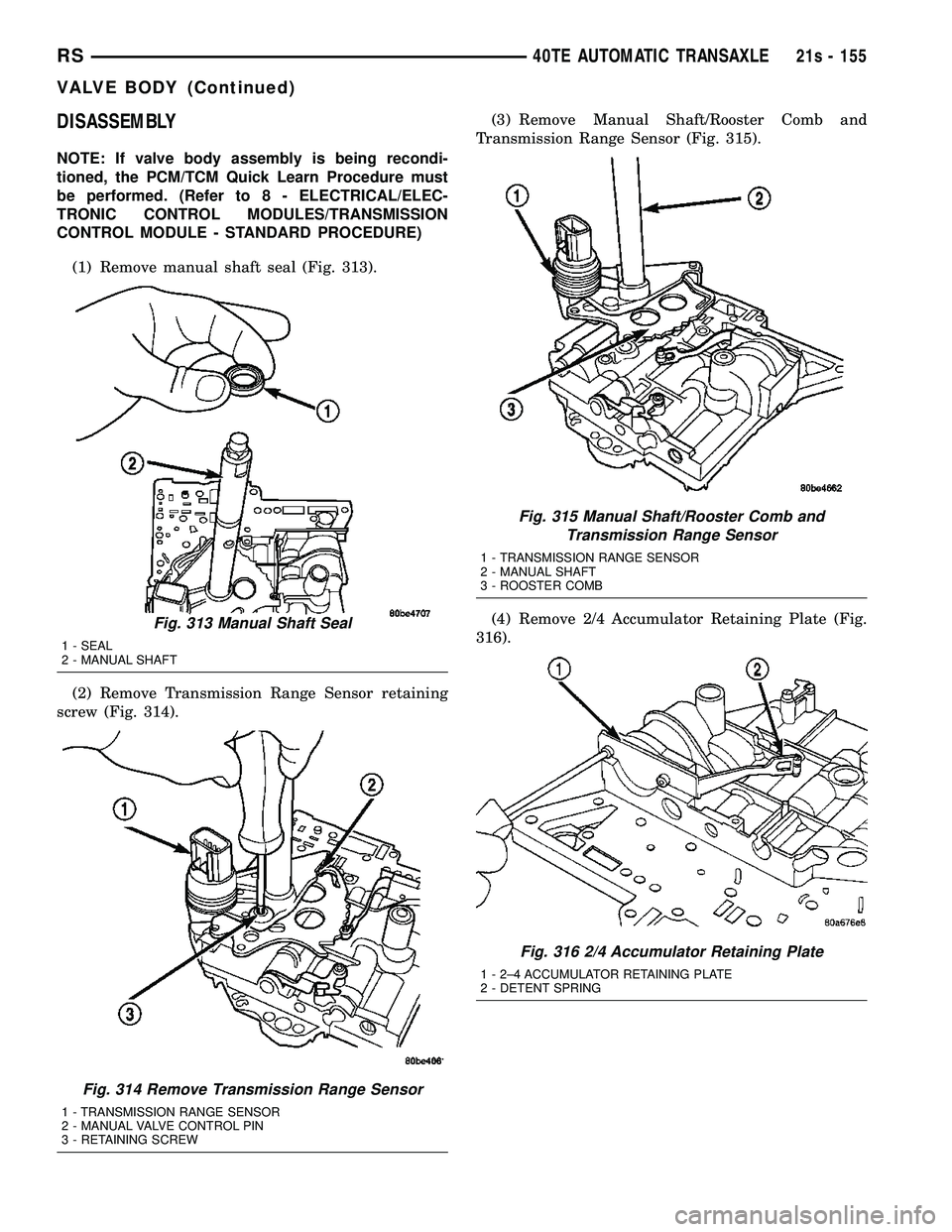
DISASSEMBLY
NOTE: If valve body assembly is being recondi-
tioned, the PCM/TCM Quick Learn Procedure must
be performed. (Refer to 8 - ELECTRICAL/ELEC-
TRONIC CONTROL MODULES/TRANSMISSION
CONTROL MODULE - STANDARD PROCEDURE)
(1) Remove manual shaft seal (Fig. 313).
(2) Remove Transmission Range Sensor retaining
screw (Fig. 314). (3) Remove Manual Shaft/Rooster Comb and
Transmission Range Sensor (Fig. 315).
(4) Remove 2/4 Accumulator Retaining Plate (Fig.
316).
Fig. 313 Manual Shaft Seal
1 - SEAL
2 - MANUAL SHAFT
Fig. 314 Remove Transmission Range Sensor
1 - TRANSMISSION RANGE SENSOR
2 - MANUAL VALVE CONTROL PIN
3 - RETAINING SCREW
Fig. 315 Manual Shaft/Rooster Comb and Transmission Range Sensor
1 - TRANSMISSION RANGE SENSOR
2 - MANUAL SHAFT
3 - ROOSTER COMB
Fig. 316 2/4 Accumulator Retaining Plate
1 - 2±4 ACCUMULATOR RETAINING PLATE
2 - DETENT SPRING
RS 40TE AUTOMATIC TRANSAXLE21s - 155
VALVE BODY (Continued)
Page 2024 of 2585
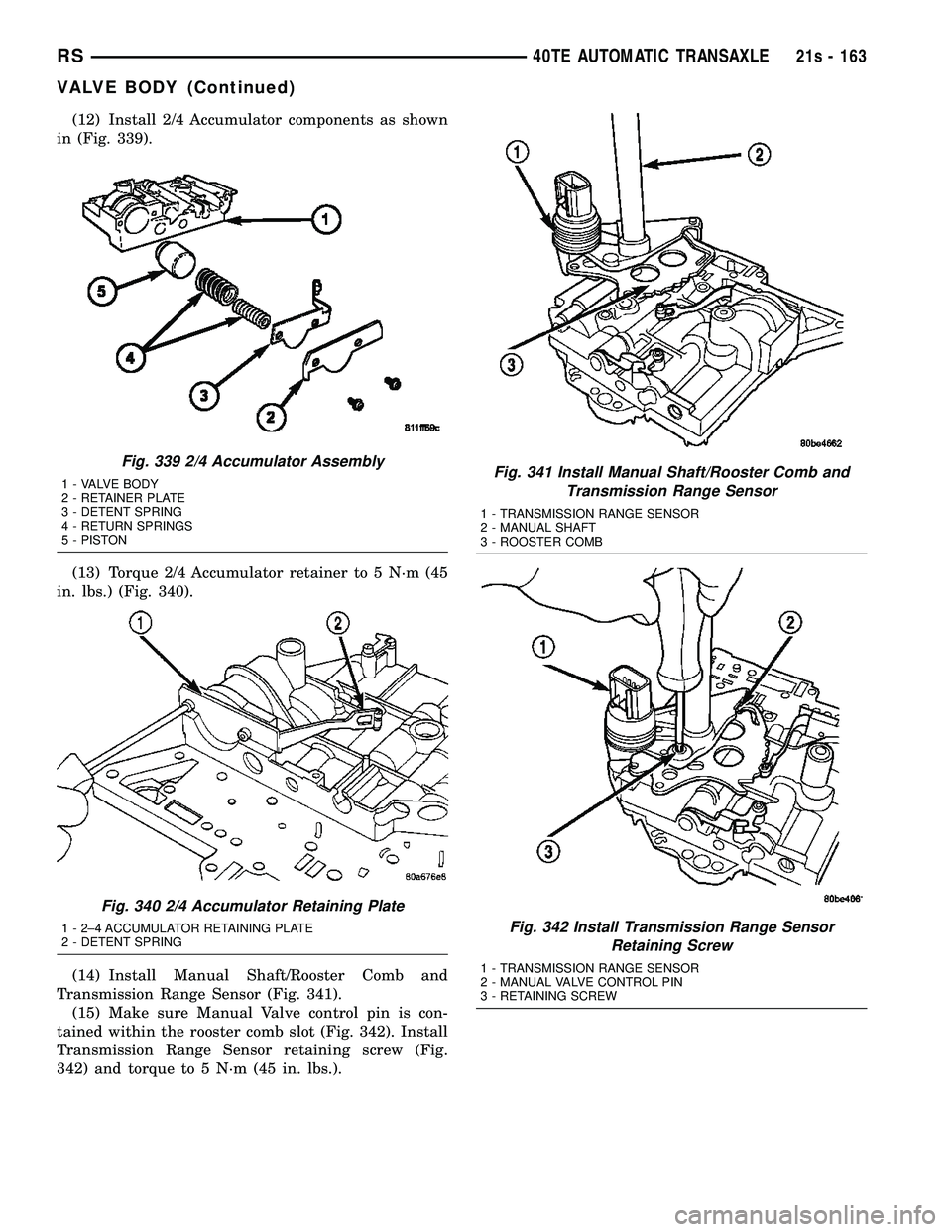
(12) Install 2/4 Accumulator components as shown
in (Fig. 339).
(13) Torque 2/4 Accumulator retainer to 5 N´m (45
in. lbs.) (Fig. 340).
(14) Install Manual Shaft/Rooster Comb and
Transmission Range Sensor (Fig. 341). (15) Make sure Manual Valve control pin is con-
tained within the rooster comb slot (Fig. 342). Install
Transmission Range Sensor retaining screw (Fig.
342) and torque to 5 N´m (45 in. lbs.).
Fig. 339 2/4 Accumulator Assembly
1 - VALVE BODY
2 - RETAINER PLATE
3 - DETENT SPRING
4 - RETURN SPRINGS
5 - PISTON
Fig. 340 2/4 Accumulator Retaining Plate
1 - 2±4 ACCUMULATOR RETAINING PLATE
2 - DETENT SPRING
Fig. 341 Install Manual Shaft/Rooster Comb and Transmission Range Sensor
1 - TRANSMISSION RANGE SENSOR
2 - MANUAL SHAFT
3 - ROOSTER COMB
Fig. 342 Install Transmission Range Sensor Retaining Screw
1 - TRANSMISSION RANGE SENSOR
2 - MANUAL VALVE CONTROL PIN
3 - RETAINING SCREW
RS 40TE AUTOMATIC TRANSAXLE21s - 163
VALVE BODY (Continued)
Page 2026 of 2585
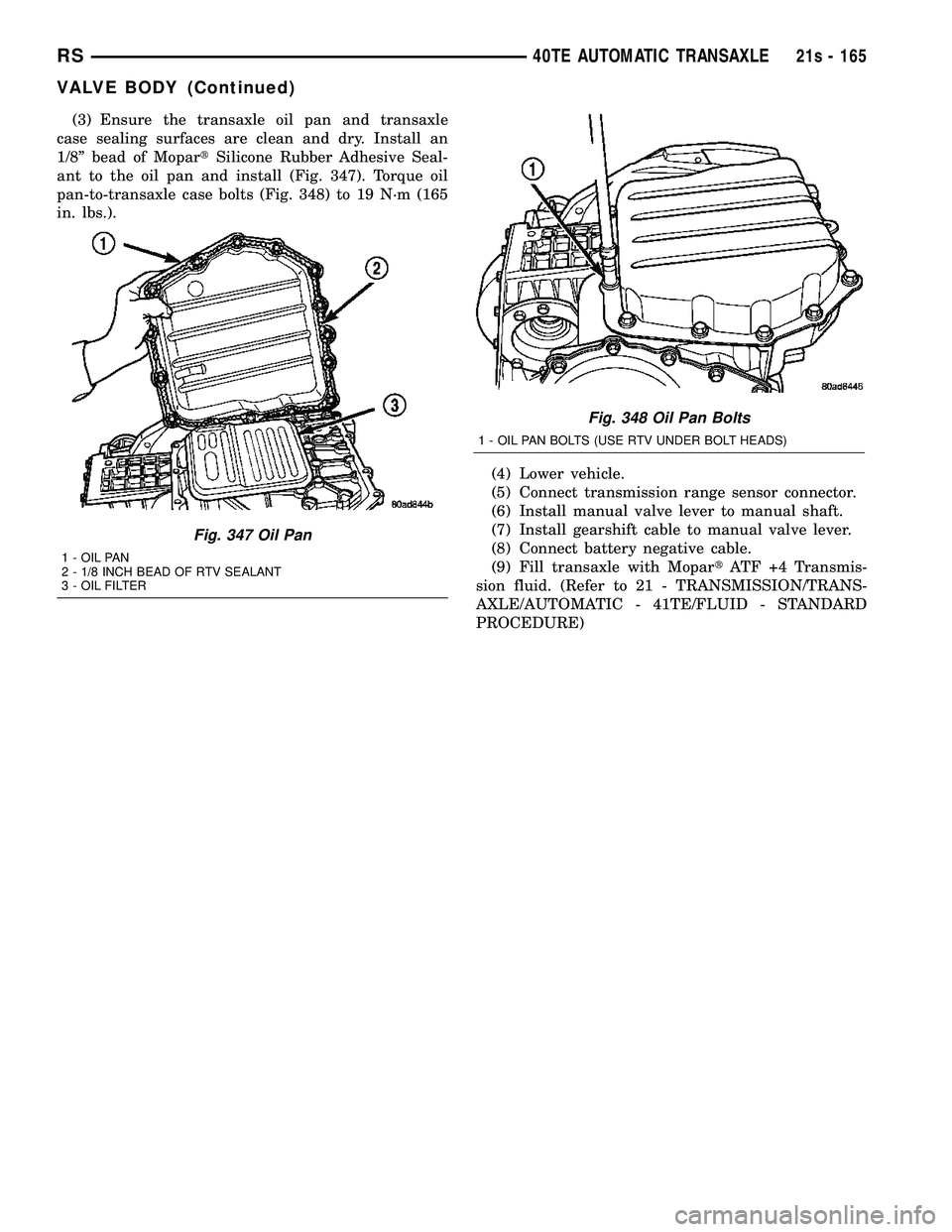
(3) Ensure the transaxle oil pan and transaxle
case sealing surfaces are clean and dry. Install an
1/8º bead of Mopar tSilicone Rubber Adhesive Seal-
ant to the oil pan and install (Fig. 347). Torque oil
pan-to-transaxle case bolts (Fig. 348) to 19 N´m (165
in. lbs.).
(4) Lower vehicle.
(5) Connect transmission range sensor connector.
(6) Install manual valve lever to manual shaft.
(7) Install gearshift cable to manual valve lever.
(8) Connect battery negative cable.
(9) Fill transaxle with MopartATF +4 Transmis-
sion fluid. (Refer to 21 - TRANSMISSION/TRANS-
AXLE/AUTOMATIC - 41TE/FLUID - STANDARD
PROCEDURE)
Fig. 348 Oil Pan Bolts
1 - OIL PAN BOLTS (USE RTV UNDER BOLT HEADS)
Fig. 347 Oil Pan
1 - OIL PAN
2 - 1/8 INCH BEAD OF RTV SEALANT
3 - OIL FILTER
RS 40TE AUTOMATIC TRANSAXLE21s - 165
VALVE BODY (Continued)
Page 2027 of 2585
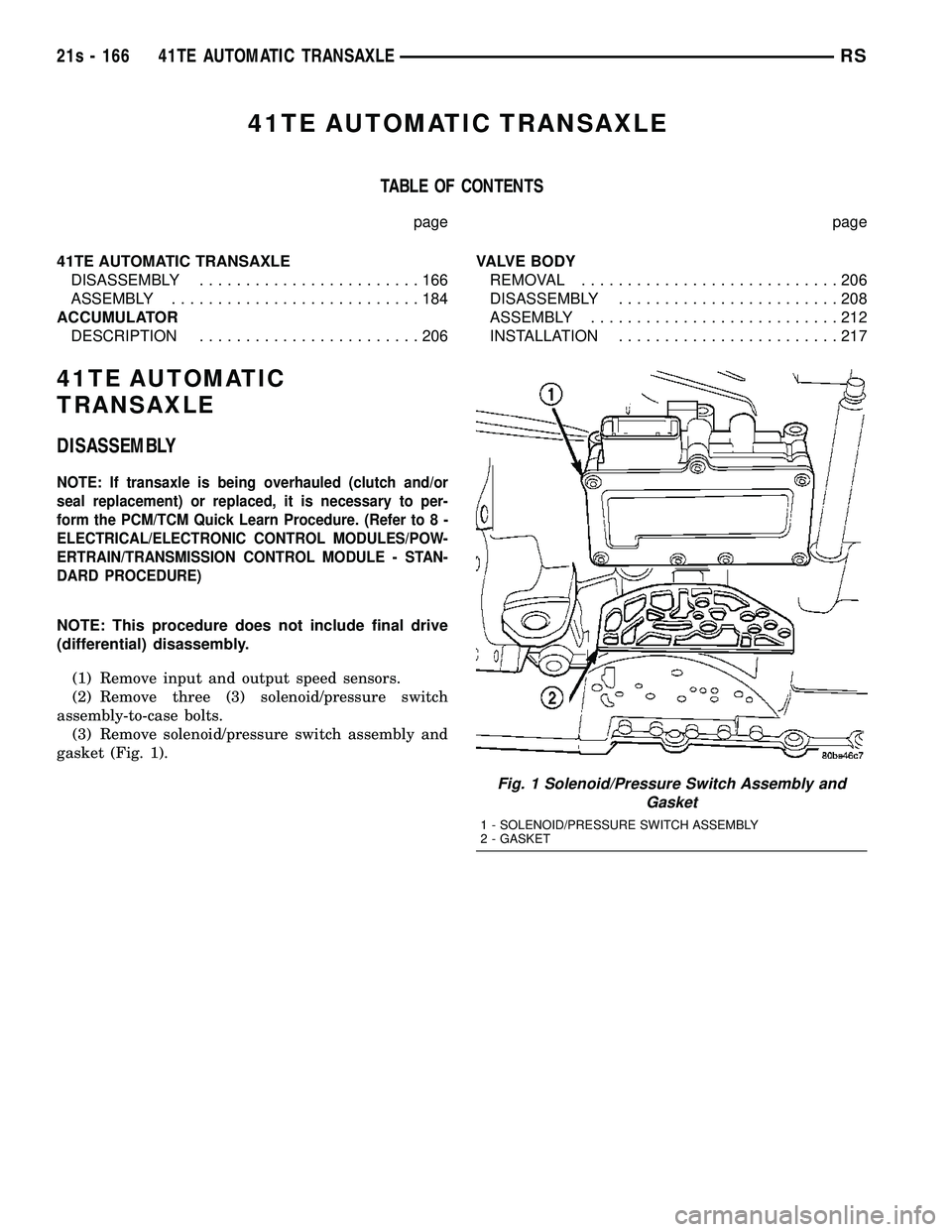
41TE AUTOMATIC TRANSAXLE
TABLE OF CONTENTS
page page
41TE AUTOMATIC TRANSAXLE DISASSEMBLY ........................166
ASSEMBLY ...........................184
ACCUMULATOR DESCRIPTION ........................206 VALVE BODY
REMOVAL ............................206
DISASSEMBLY ........................208
ASSEMBLY ...........................212
INSTALLATION ........................217
41TE AUTOMATIC
TRANSAXLE
DISASSEMBLY
NOTE: If transaxle is being overhauled (clutch and/or
seal replacement) or replaced, it is necessary to per-
form the PCM/TCM Quick Learn Procedure. (Refer to 8 -
ELECTRICAL/ELECTRONIC CONTROL MODULES/POW-
ERTRAIN/TRANSMISSION CONTROL MODULE - STAN-
DARD PROCEDURE)
NOTE: This procedure does not include final drive
(differential) disassembly.
(1) Remove input and output speed sensors.
(2) Remove three (3) solenoid/pressure switch
assembly-to-case bolts. (3) Remove solenoid/pressure switch assembly and
gasket (Fig. 1).
Fig. 1 Solenoid/Pressure Switch Assembly and Gasket
1 - SOLENOID/PRESSURE SWITCH ASSEMBLY
2 - GASKET
21s - 166 41TE AUTOMATIC TRANSAXLERS
Page 2031 of 2585
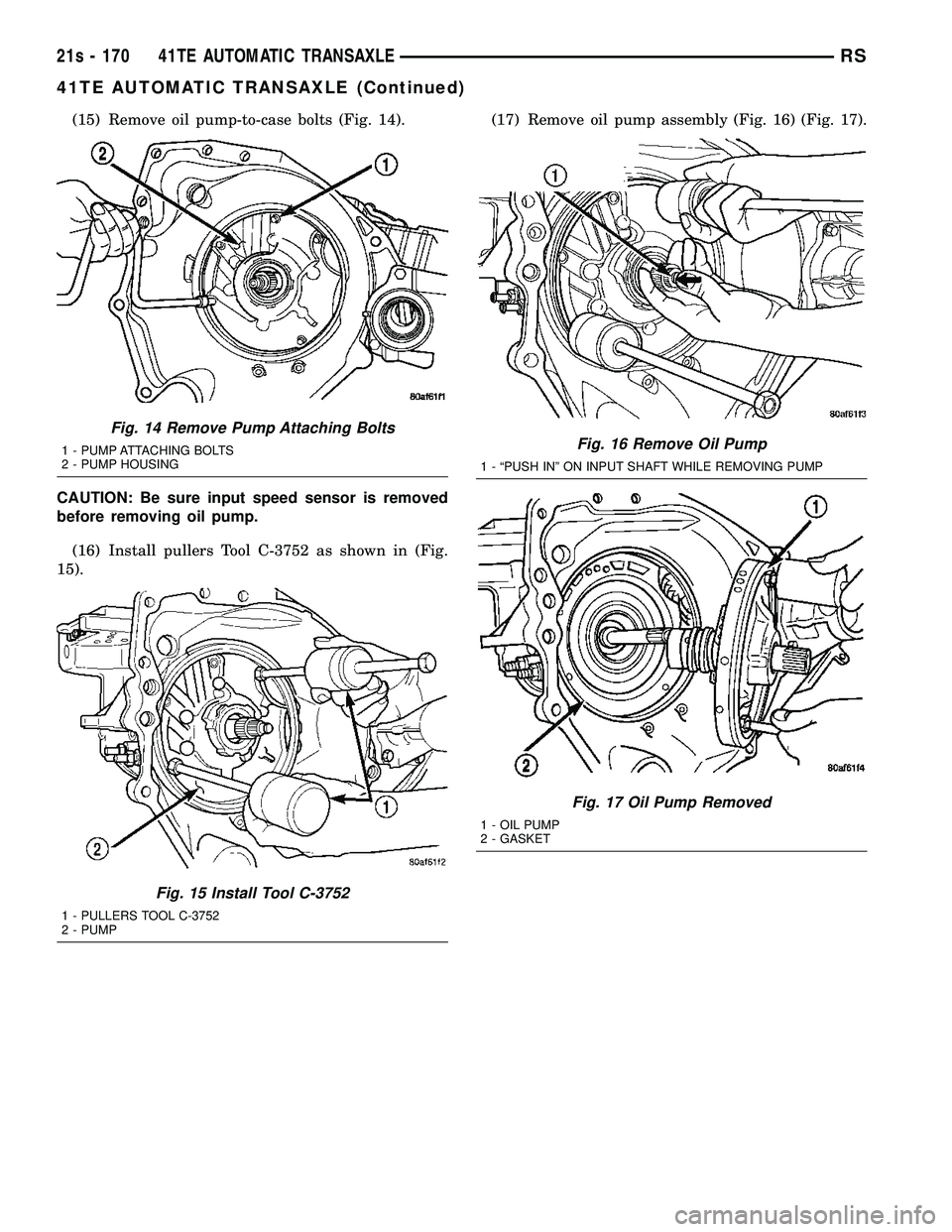
(15) Remove oil pump-to-case bolts (Fig. 14).
CAUTION: Be sure input speed sensor is removed
before removing oil pump. (16) Install pullers Tool C-3752 as shown in (Fig.
15). (17) Remove oil pump assembly (Fig. 16) (Fig. 17).
Fig. 14 Remove Pump Attaching Bolts
1 - PUMP ATTACHING BOLTS
2 - PUMP HOUSING
Fig. 15 Install Tool C-3752
1 - PULLERS TOOL C-3752
2 - PUMP
Fig. 16 Remove Oil Pump
1 - ªPUSH INº ON INPUT SHAFT WHILE REMOVING PUMP
Fig. 17 Oil Pump Removed
1 - OIL PUMP
2 - GASKET
21s - 170 41TE AUTOMATIC TRANSAXLERS
41TE AUTOMATIC TRANSAXLE (Continued)
Page 2062 of 2585
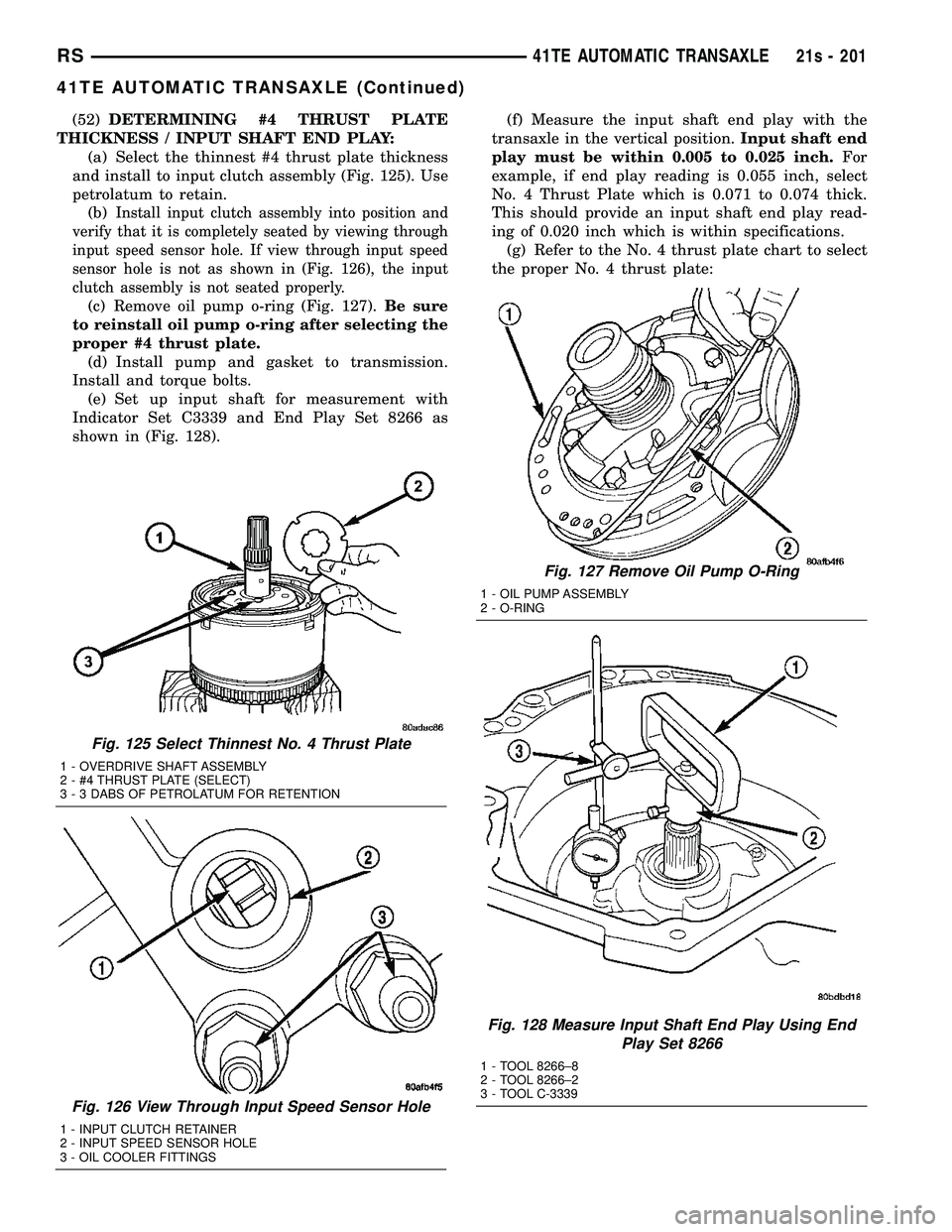
(52)DETERMINING #4 THRUST PLATE
THICKNESS / INPUT SHAFT END PLAY: (a) Select the thinnest #4 thrust plate thickness
and install to input clutch assembly (Fig. 125). Use
petrolatum to retain. (b)
Install input clutch assembly into position and
verify that it is completely seated by viewing through
input speed sensor hole. If view through input speed
sensor hole is not as shown in (Fig. 126), the input
clutch assembly is not seated properly.
(c) Remove oil pump o-ring (Fig. 127). Be sure
to reinstall oil pump o-ring after selecting the
proper #4 thrust plate. (d) Install pump and gasket to transmission.
Install and torque bolts. (e) Set up input shaft for measurement with
Indicator Set C3339 and End Play Set 8266 as
shown in (Fig. 128). (f) Measure the input shaft end play with the
transaxle in the vertical position. Input shaft end
play must be within 0.005 to 0.025 inch. For
example, if end play reading is 0.055 inch, select
No. 4 Thrust Plate which is 0.071 to 0.074 thick.
This should provide an input shaft end play read-
ing of 0.020 inch which is within specifications. (g) Refer to the No. 4 thrust plate chart to select
the proper No. 4 thrust plate:
Fig. 125 Select Thinnest No. 4 Thrust Plate
1 - OVERDRIVE SHAFT ASSEMBLY
2 - #4 THRUST PLATE (SELECT)
3 - 3 DABS OF PETROLATUM FOR RETENTION
Fig. 126 View Through Input Speed Sensor Hole
1 - INPUT CLUTCH RETAINER
2 - INPUT SPEED SENSOR HOLE
3 - OIL COOLER FITTINGS
Fig. 127 Remove Oil Pump O-Ring
1 - OIL PUMP ASSEMBLY
2 - O-RING
Fig. 128 Measure Input Shaft End Play Using End Play Set 8266
1 - TOOL 8266±8
2 - TOOL 8266±2
3 - TOOL C-3339
RS 41TE AUTOMATIC TRANSAXLE21s - 201
41TE AUTOMATIC TRANSAXLE (Continued)
Page 2066 of 2585
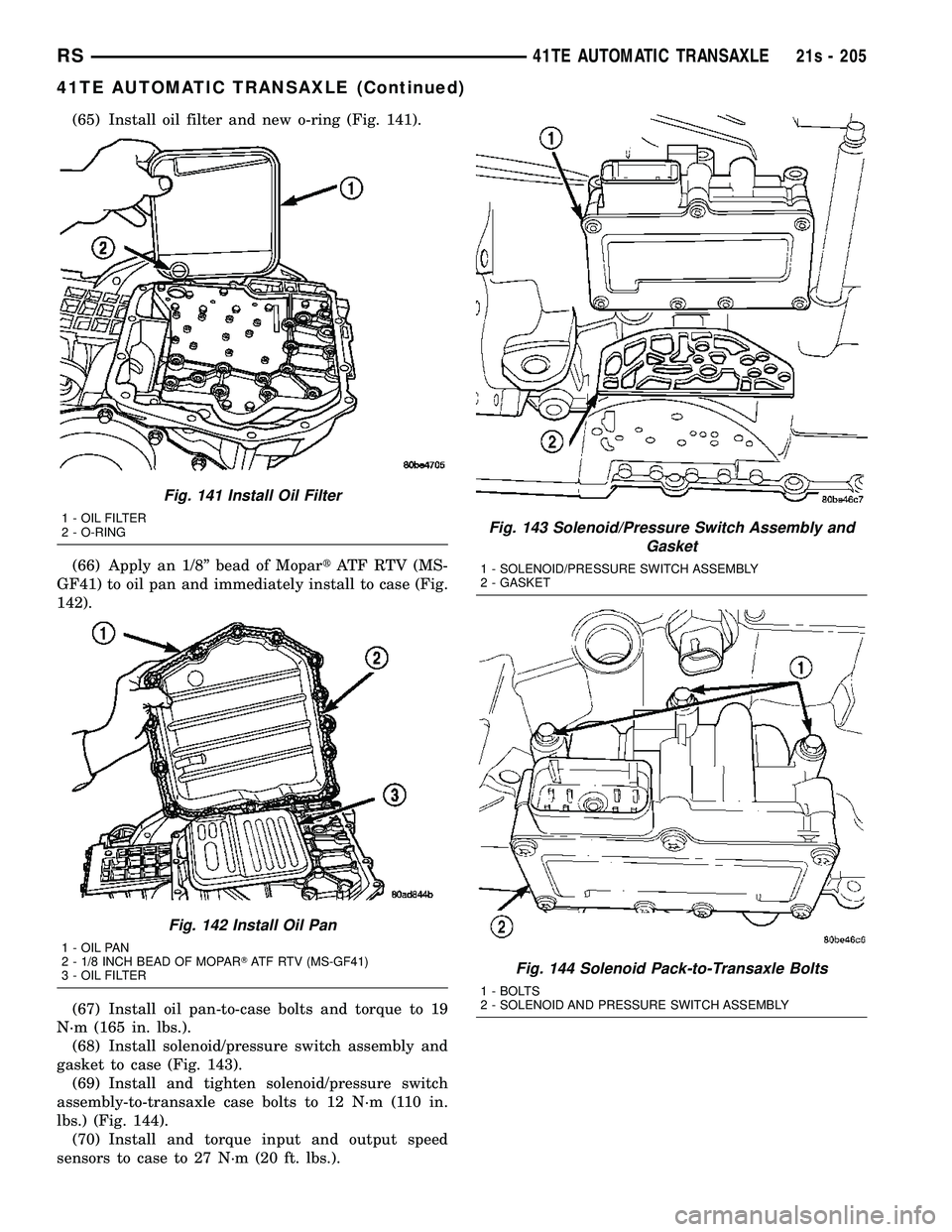
(65) Install oil filter and new o-ring (Fig. 141).
(66) Apply an 1/8º bead of MopartATF RTV (MS-
GF41) to oil pan and immediately install to case (Fig.
142).
(67) Install oil pan-to-case bolts and torque to 19
N´m (165 in. lbs.). (68) Install solenoid/pressure switch assembly and
gasket to case (Fig. 143). (69) Install and tighten solenoid/pressure switch
assembly-to-transaxle case bolts to 12 N´m (110 in.
lbs.) (Fig. 144). (70) Install and torque input and output speed
sensors to case to 27 N´m (20 ft. lbs.).
Fig. 141 Install Oil Filter
1 - OIL FILTER
2 - O-RING
Fig. 142 Install Oil Pan
1 - OIL PAN
2 - 1/8 INCH BEAD OF MOPAR TATF RTV (MS-GF41)
3 - OIL FILTER
Fig. 143 Solenoid/Pressure Switch Assembly and
Gasket
1 - SOLENOID/PRESSURE SWITCH ASSEMBLY
2 - GASKET
Fig. 144 Solenoid Pack-to-Transaxle Bolts
1 - BOLTS
2 - SOLENOID AND PRESSURE SWITCH ASSEMBLY
RS 41TE AUTOMATIC TRANSAXLE21s - 205
41TE AUTOMATIC TRANSAXLE (Continued)
Page 2069 of 2585
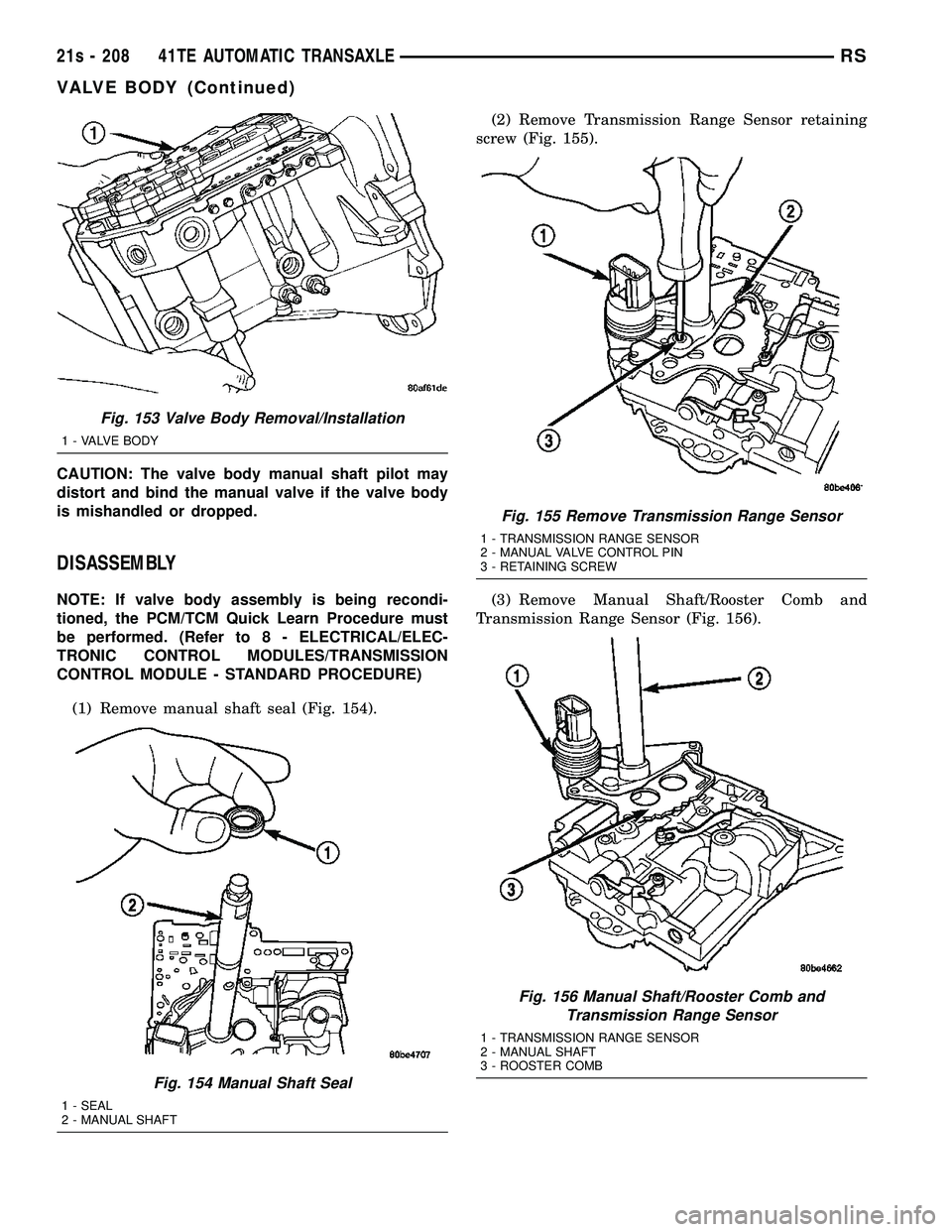
CAUTION: The valve body manual shaft pilot may
distort and bind the manual valve if the valve body
is mishandled or dropped.
DISASSEMBLY
NOTE: If valve body assembly is being recondi-
tioned, the PCM/TCM Quick Learn Procedure must
be performed. (Refer to 8 - ELECTRICAL/ELEC-
TRONIC CONTROL MODULES/TRANSMISSION
CONTROL MODULE - STANDARD PROCEDURE)
(1) Remove manual shaft seal (Fig. 154). (2) Remove Transmission Range Sensor retaining
screw (Fig. 155).
(3) Remove Manual Shaft/Rooster Comb and
Transmission Range Sensor (Fig. 156).
Fig. 153 Valve Body Removal/Installation
1 - VALVE BODY
Fig. 154 Manual Shaft Seal
1 - SEAL
2 - MANUAL SHAFT
Fig. 155 Remove Transmission Range Sensor
1 - TRANSMISSION RANGE SENSOR
2 - MANUAL VALVE CONTROL PIN
3 - RETAINING SCREW
Fig. 156 Manual Shaft/Rooster Comb and Transmission Range Sensor
1 - TRANSMISSION RANGE SENSOR
2 - MANUAL SHAFT
3 - ROOSTER COMB
21s - 208 41TE AUTOMATIC TRANSAXLERS
VALVE BODY (Continued)