tow CHRYSLER VOYAGER 2005 Workshop Manual
[x] Cancel search | Manufacturer: CHRYSLER, Model Year: 2005, Model line: VOYAGER, Model: CHRYSLER VOYAGER 2005Pages: 2339, PDF Size: 59.69 MB
Page 475 of 2339
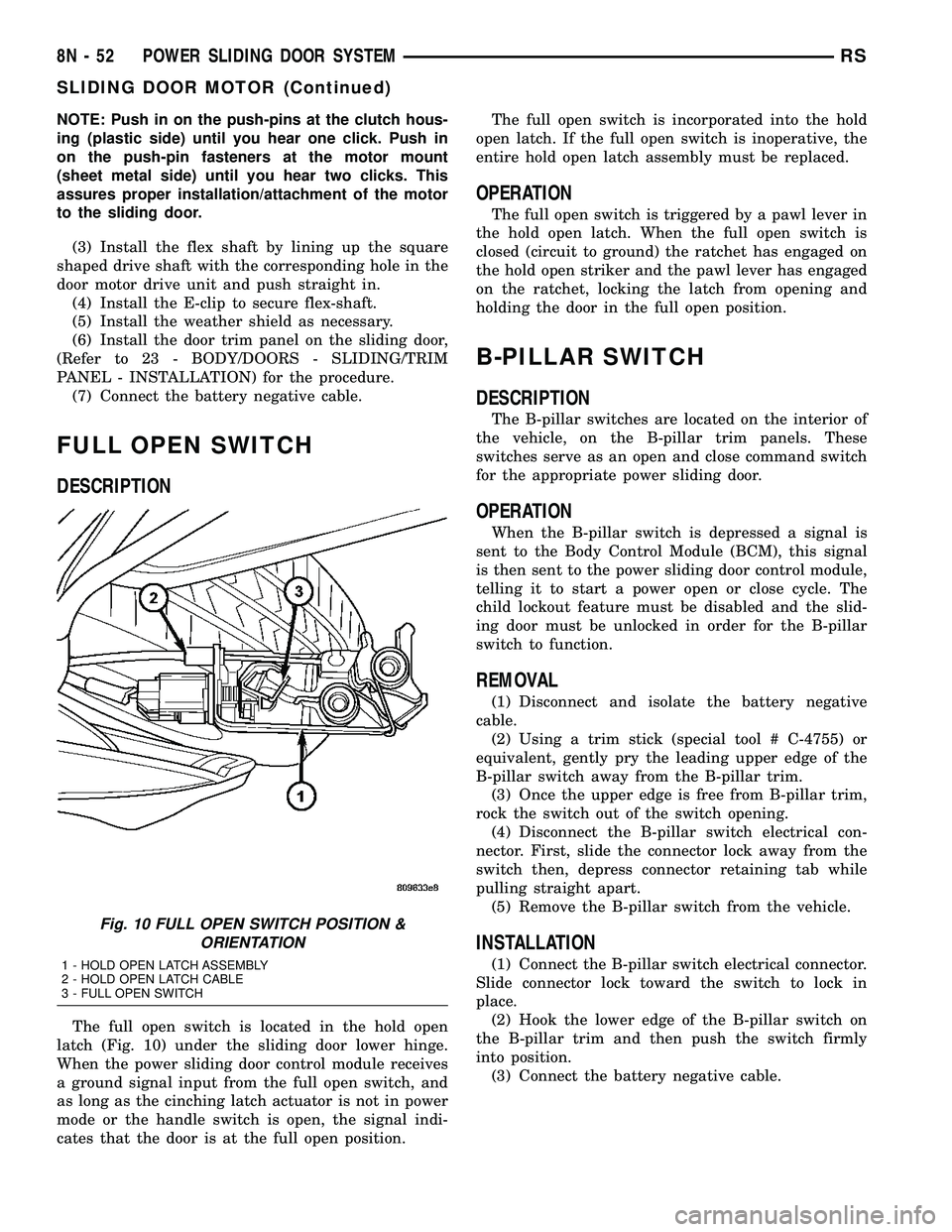
NOTE: Push in on the push-pins at the clutch hous-
ing (plastic side) until you hear one click. Push in
on the push-pin fasteners at the motor mount
(sheet metal side) until you hear two clicks. This
assures proper installation/attachment of the motor
to the sliding door.
(3) Install the flex shaft by lining up the square
shaped drive shaft with the corresponding hole in the
door motor drive unit and push straight in.
(4) Install the E-clip to secure flex-shaft.
(5) Install the weather shield as necessary.
(6) Install the door trim panel on the sliding door,
(Refer to 23 - BODY/DOORS - SLIDING/TRIM
PANEL - INSTALLATION) for the procedure.
(7) Connect the battery negative cable.
FULL OPEN SWITCH
DESCRIPTION
The full open switch is located in the hold open
latch (Fig. 10) under the sliding door lower hinge.
When the power sliding door control module receives
a ground signal input from the full open switch, and
as long as the cinching latch actuator is not in power
mode or the handle switch is open, the signal indi-
cates that the door is at the full open position.The full open switch is incorporated into the hold
open latch. If the full open switch is inoperative, the
entire hold open latch assembly must be replaced.
OPERATION
The full open switch is triggered by a pawl lever in
the hold open latch. When the full open switch is
closed (circuit to ground) the ratchet has engaged on
the hold open striker and the pawl lever has engaged
on the ratchet, locking the latch from opening and
holding the door in the full open position.
B-PILLAR SWITCH
DESCRIPTION
The B-pillar switches are located on the interior of
the vehicle, on the B-pillar trim panels. These
switches serve as an open and close command switch
for the appropriate power sliding door.
OPERATION
When the B-pillar switch is depressed a signal is
sent to the Body Control Module (BCM), this signal
is then sent to the power sliding door control module,
telling it to start a power open or close cycle. The
child lockout feature must be disabled and the slid-
ing door must be unlocked in order for the B-pillar
switch to function.
REMOVAL
(1) Disconnect and isolate the battery negative
cable.
(2) Using a trim stick (special tool # C-4755) or
equivalent, gently pry the leading upper edge of the
B-pillar switch away from the B-pillar trim.
(3) Once the upper edge is free from B-pillar trim,
rock the switch out of the switch opening.
(4) Disconnect the B-pillar switch electrical con-
nector. First, slide the connector lock away from the
switch then, depress connector retaining tab while
pulling straight apart.
(5) Remove the B-pillar switch from the vehicle.
INSTALLATION
(1) Connect the B-pillar switch electrical connector.
Slide connector lock toward the switch to lock in
place.
(2) Hook the lower edge of the B-pillar switch on
the B-pillar trim and then push the switch firmly
into position.
(3) Connect the battery negative cable.
Fig. 10 FULL OPEN SWITCH POSITION &
ORIENTATION
1 - HOLD OPEN LATCH ASSEMBLY
2 - HOLD OPEN LATCH CABLE
3 - FULL OPEN SWITCH
8N - 52 POWER SLIDING DOOR SYSTEMRS
SLIDING DOOR MOTOR (Continued)
Page 492 of 2339
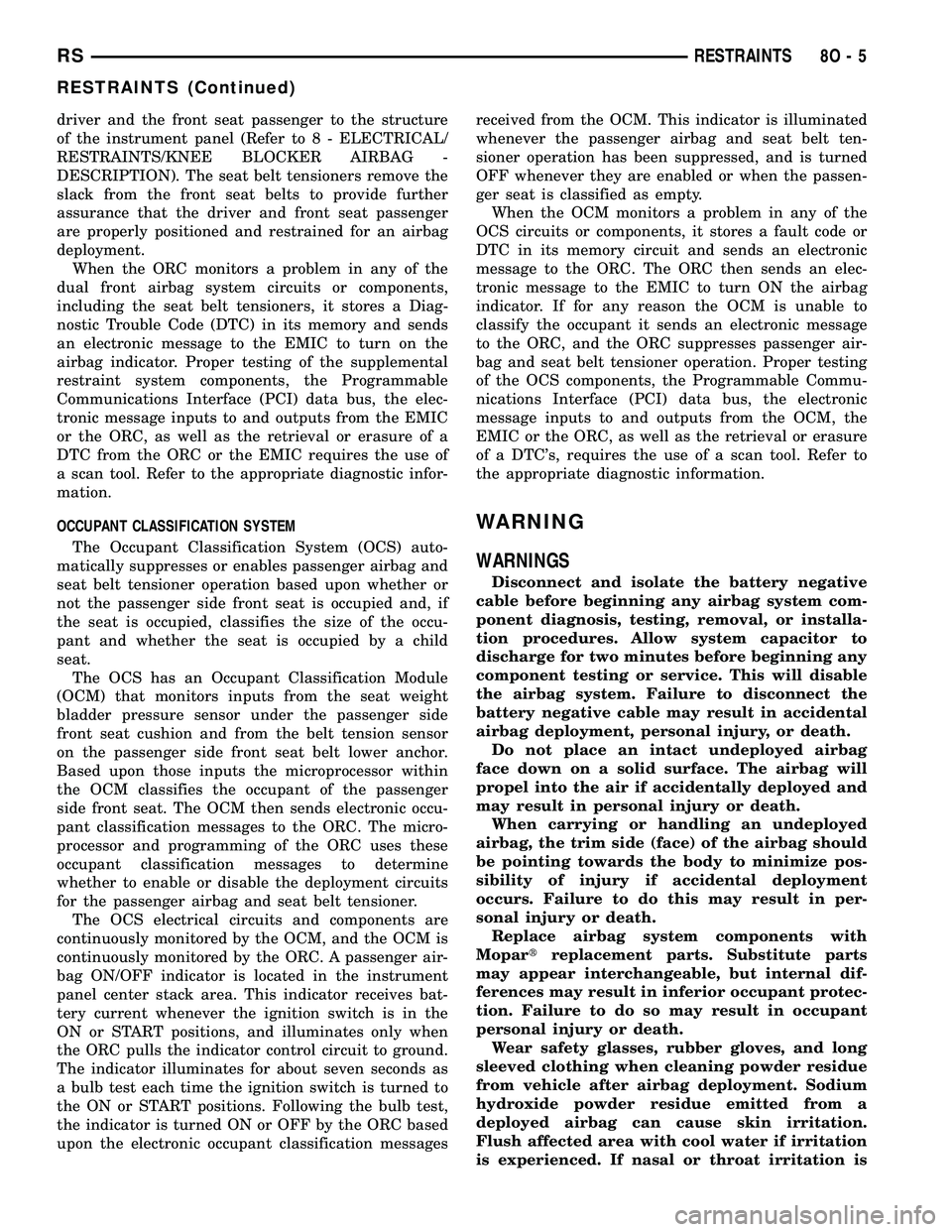
driver and the front seat passenger to the structure
of the instrument panel (Refer to 8 - ELECTRICAL/
RESTRAINTS/KNEE BLOCKER AIRBAG -
DESCRIPTION). The seat belt tensioners remove the
slack from the front seat belts to provide further
assurance that the driver and front seat passenger
are properly positioned and restrained for an airbag
deployment.
When the ORC monitors a problem in any of the
dual front airbag system circuits or components,
including the seat belt tensioners, it stores a Diag-
nostic Trouble Code (DTC) in its memory and sends
an electronic message to the EMIC to turn on the
airbag indicator. Proper testing of the supplemental
restraint system components, the Programmable
Communications Interface (PCI) data bus, the elec-
tronic message inputs to and outputs from the EMIC
or the ORC, as well as the retrieval or erasure of a
DTC from the ORC or the EMIC requires the use of
a scan tool. Refer to the appropriate diagnostic infor-
mation.
OCCUPANT CLASSIFICATION SYSTEM
The Occupant Classification System (OCS) auto-
matically suppresses or enables passenger airbag and
seat belt tensioner operation based upon whether or
not the passenger side front seat is occupied and, if
the seat is occupied, classifies the size of the occu-
pant and whether the seat is occupied by a child
seat.
The OCS has an Occupant Classification Module
(OCM) that monitors inputs from the seat weight
bladder pressure sensor under the passenger side
front seat cushion and from the belt tension sensor
on the passenger side front seat belt lower anchor.
Based upon those inputs the microprocessor within
the OCM classifies the occupant of the passenger
side front seat. The OCM then sends electronic occu-
pant classification messages to the ORC. The micro-
processor and programming of the ORC uses these
occupant classification messages to determine
whether to enable or disable the deployment circuits
for the passenger airbag and seat belt tensioner.
The OCS electrical circuits and components are
continuously monitored by the OCM, and the OCM is
continuously monitored by the ORC. A passenger air-
bag ON/OFF indicator is located in the instrument
panel center stack area. This indicator receives bat-
tery current whenever the ignition switch is in the
ON or START positions, and illuminates only when
the ORC pulls the indicator control circuit to ground.
The indicator illuminates for about seven seconds as
a bulb test each time the ignition switch is turned to
the ON or START positions. Following the bulb test,
the indicator is turned ON or OFF by the ORC based
upon the electronic occupant classification messagesreceived from the OCM. This indicator is illuminated
whenever the passenger airbag and seat belt ten-
sioner operation has been suppressed, and is turned
OFF whenever they are enabled or when the passen-
ger seat is classified as empty.
When the OCM monitors a problem in any of the
OCS circuits or components, it stores a fault code or
DTC in its memory circuit and sends an electronic
message to the ORC. The ORC then sends an elec-
tronic message to the EMIC to turn ON the airbag
indicator. If for any reason the OCM is unable to
classify the occupant it sends an electronic message
to the ORC, and the ORC suppresses passenger air-
bag and seat belt tensioner operation. Proper testing
of the OCS components, the Programmable Commu-
nications Interface (PCI) data bus, the electronic
message inputs to and outputs from the OCM, the
EMIC or the ORC, as well as the retrieval or erasure
of a DTC's, requires the use of a scan tool. Refer to
the appropriate diagnostic information.
WARNING
WARNINGS
Disconnect and isolate the battery negative
cable before beginning any airbag system com-
ponent diagnosis, testing, removal, or installa-
tion procedures. Allow system capacitor to
discharge for two minutes before beginning any
component testing or service. This will disable
the airbag system. Failure to disconnect the
battery negative cable may result in accidental
airbag deployment, personal injury, or death.
Do not place an intact undeployed airbag
face down on a solid surface. The airbag will
propel into the air if accidentally deployed and
may result in personal injury or death.
When carrying or handling an undeployed
airbag, the trim side (face) of the airbag should
be pointing towards the body to minimize pos-
sibility of injury if accidental deployment
occurs. Failure to do this may result in per-
sonal injury or death.
Replace airbag system components with
Mopartreplacement parts. Substitute parts
may appear interchangeable, but internal dif-
ferences may result in inferior occupant protec-
tion. Failure to do so may result in occupant
personal injury or death.
Wear safety glasses, rubber gloves, and long
sleeved clothing when cleaning powder residue
from vehicle after airbag deployment. Sodium
hydroxide powder residue emitted from a
deployed airbag can cause skin irritation.
Flush affected area with cool water if irritation
is experienced. If nasal or throat irritation is
RSRESTRAINTS8O-5
RESTRAINTS (Continued)
Page 494 of 2339
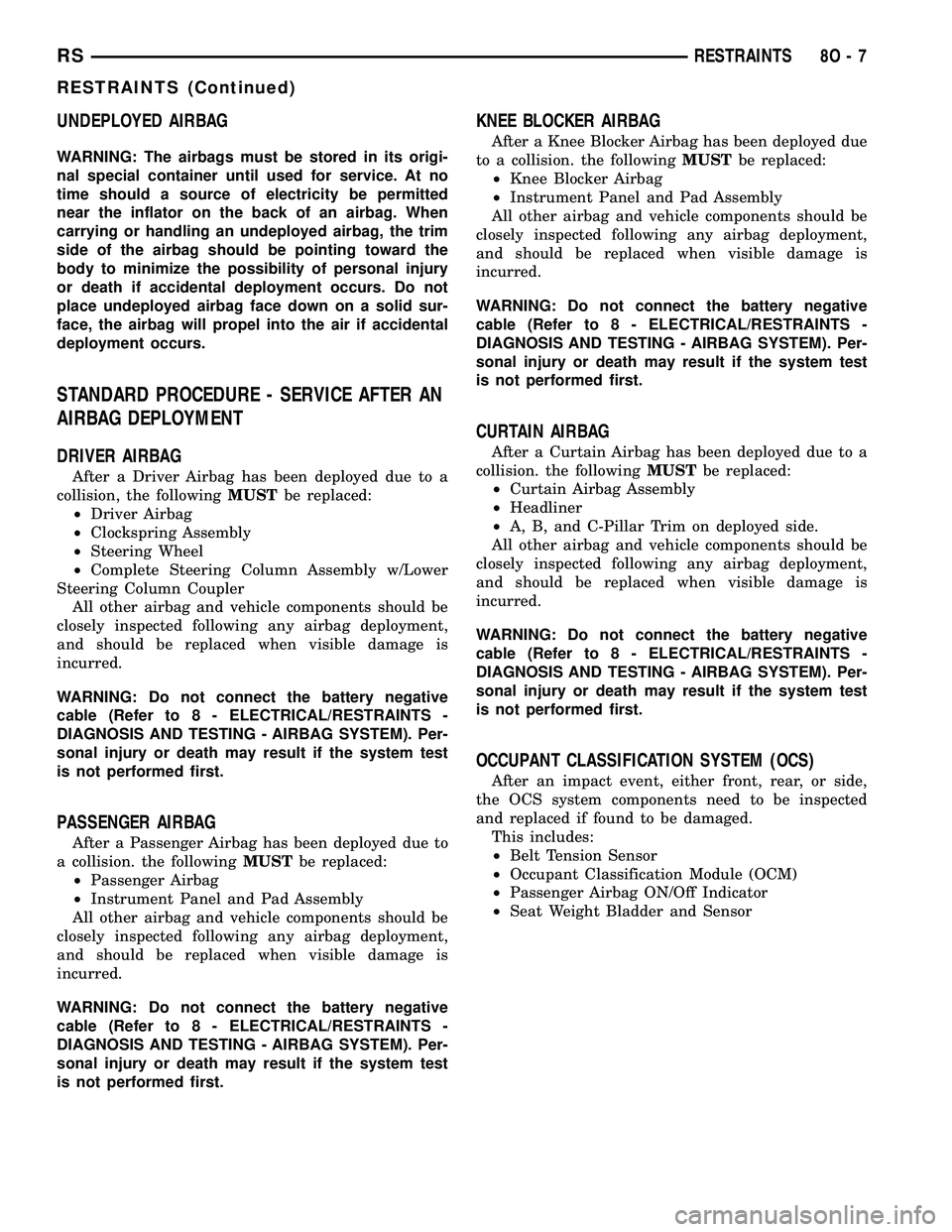
UNDEPLOYED AIRBAG
WARNING: The airbags must be stored in its origi-
nal special container until used for service. At no
time should a source of electricity be permitted
near the inflator on the back of an airbag. When
carrying or handling an undeployed airbag, the trim
side of the airbag should be pointing toward the
body to minimize the possibility of personal injury
or death if accidental deployment occurs. Do not
place undeployed airbag face down on a solid sur-
face, the airbag will propel into the air if accidental
deployment occurs.
STANDARD PROCEDURE - SERVICE AFTER AN
AIRBAG DEPLOYMENT
DRIVER AIRBAG
After a Driver Airbag has been deployed due to a
collision, the followingMUSTbe replaced:
²Driver Airbag
²Clockspring Assembly
²Steering Wheel
²Complete Steering Column Assembly w/Lower
Steering Column Coupler
All other airbag and vehicle components should be
closely inspected following any airbag deployment,
and should be replaced when visible damage is
incurred.
WARNING: Do not connect the battery negative
cable (Refer to 8 - ELECTRICAL/RESTRAINTS -
DIAGNOSIS AND TESTING - AIRBAG SYSTEM). Per-
sonal injury or death may result if the system test
is not performed first.
PASSENGER AIRBAG
After a Passenger Airbag has been deployed due to
a collision. the followingMUSTbe replaced:
²Passenger Airbag
²Instrument Panel and Pad Assembly
All other airbag and vehicle components should be
closely inspected following any airbag deployment,
and should be replaced when visible damage is
incurred.
WARNING: Do not connect the battery negative
cable (Refer to 8 - ELECTRICAL/RESTRAINTS -
DIAGNOSIS AND TESTING - AIRBAG SYSTEM). Per-
sonal injury or death may result if the system test
is not performed first.
KNEE BLOCKER AIRBAG
After a Knee Blocker Airbag has been deployed due
to a collision. the followingMUSTbe replaced:
²Knee Blocker Airbag
²Instrument Panel and Pad Assembly
All other airbag and vehicle components should be
closely inspected following any airbag deployment,
and should be replaced when visible damage is
incurred.
WARNING: Do not connect the battery negative
cable (Refer to 8 - ELECTRICAL/RESTRAINTS -
DIAGNOSIS AND TESTING - AIRBAG SYSTEM). Per-
sonal injury or death may result if the system test
is not performed first.
CURTAIN AIRBAG
After a Curtain Airbag has been deployed due to a
collision. the followingMUSTbe replaced:
²Curtain Airbag Assembly
²Headliner
²A, B, and C-Pillar Trim on deployed side.
All other airbag and vehicle components should be
closely inspected following any airbag deployment,
and should be replaced when visible damage is
incurred.
WARNING: Do not connect the battery negative
cable (Refer to 8 - ELECTRICAL/RESTRAINTS -
DIAGNOSIS AND TESTING - AIRBAG SYSTEM). Per-
sonal injury or death may result if the system test
is not performed first.
OCCUPANT CLASSIFICATION SYSTEM (OCS)
After an impact event, either front, rear, or side,
the OCS system components need to be inspected
and replaced if found to be damaged.
This includes:
²Belt Tension Sensor
²Occupant Classification Module (OCM)
²Passenger Airbag ON/Off Indicator
²Seat Weight Bladder and Sensor
RSRESTRAINTS8O-7
RESTRAINTS (Continued)
Page 495 of 2339
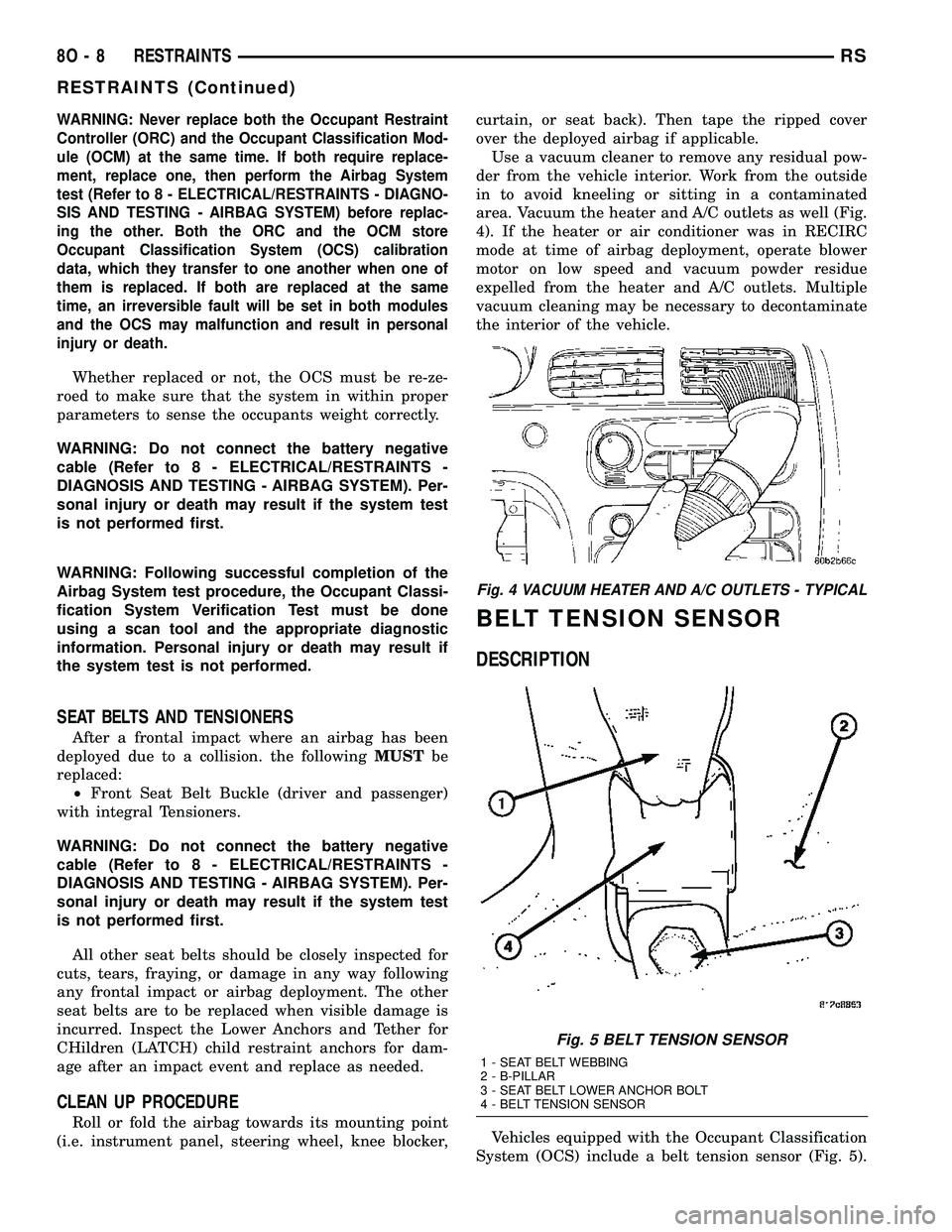
WARNING: Never replace both the Occupant Restraint
Controller (ORC) and the Occupant Classification Mod-
ule (OCM) at the same time. If both require replace-
ment, replace one, then perform the Airbag System
test (Refer to 8 - ELECTRICAL/RESTRAINTS - DIAGNO-
SIS AND TESTING - AIRBAG SYSTEM) before replac-
ing the other. Both the ORC and the OCM store
Occupant Classification System (OCS) calibration
data, which they transfer to one another when one of
them is replaced. If both are replaced at the same
time, an irreversible fault will be set in both modules
and the OCS may malfunction and result in personal
injury or death.
Whether replaced or not, the OCS must be re-ze-
roed to make sure that the system in within proper
parameters to sense the occupants weight correctly.
WARNING: Do not connect the battery negative
cable (Refer to 8 - ELECTRICAL/RESTRAINTS -
DIAGNOSIS AND TESTING - AIRBAG SYSTEM). Per-
sonal injury or death may result if the system test
is not performed first.
WARNING: Following successful completion of the
Airbag System test procedure, the Occupant Classi-
fication System Verification Test must be done
using a scan tool and the appropriate diagnostic
information. Personal injury or death may result if
the system test is not performed.
SEAT BELTS AND TENSIONERS
After a frontal impact where an airbag has been
deployed due to a collision. the followingMUSTbe
replaced:
²Front Seat Belt Buckle (driver and passenger)
with integral Tensioners.
WARNING: Do not connect the battery negative
cable (Refer to 8 - ELECTRICAL/RESTRAINTS -
DIAGNOSIS AND TESTING - AIRBAG SYSTEM). Per-
sonal injury or death may result if the system test
is not performed first.
All other seat belts should be closely inspected for
cuts, tears, fraying, or damage in any way following
any frontal impact or airbag deployment. The other
seat belts are to be replaced when visible damage is
incurred. Inspect the Lower Anchors and Tether for
CHildren (LATCH) child restraint anchors for dam-
age after an impact event and replace as needed.
CLEAN UP PROCEDURE
Roll or fold the airbag towards its mounting point
(i.e. instrument panel, steering wheel, knee blocker,curtain, or seat back). Then tape the ripped cover
over the deployed airbag if applicable.
Use a vacuum cleaner to remove any residual pow-
der from the vehicle interior. Work from the outside
in to avoid kneeling or sitting in a contaminated
area. Vacuum the heater and A/C outlets as well (Fig.
4). If the heater or air conditioner was in RECIRC
mode at time of airbag deployment, operate blower
motor on low speed and vacuum powder residue
expelled from the heater and A/C outlets. Multiple
vacuum cleaning may be necessary to decontaminate
the interior of the vehicle.
BELT TENSION SENSOR
DESCRIPTION
Vehicles equipped with the Occupant Classification
System (OCS) include a belt tension sensor (Fig. 5).
Fig. 4 VACUUM HEATER AND A/C OUTLETS - TYPICAL
Fig. 5 BELT TENSION SENSOR
1 - SEAT BELT WEBBING
2 - B-PILLAR
3 - SEAT BELT LOWER ANCHOR BOLT
4 - BELT TENSION SENSOR
8O - 8 RESTRAINTSRS
RESTRAINTS (Continued)
Page 497 of 2339
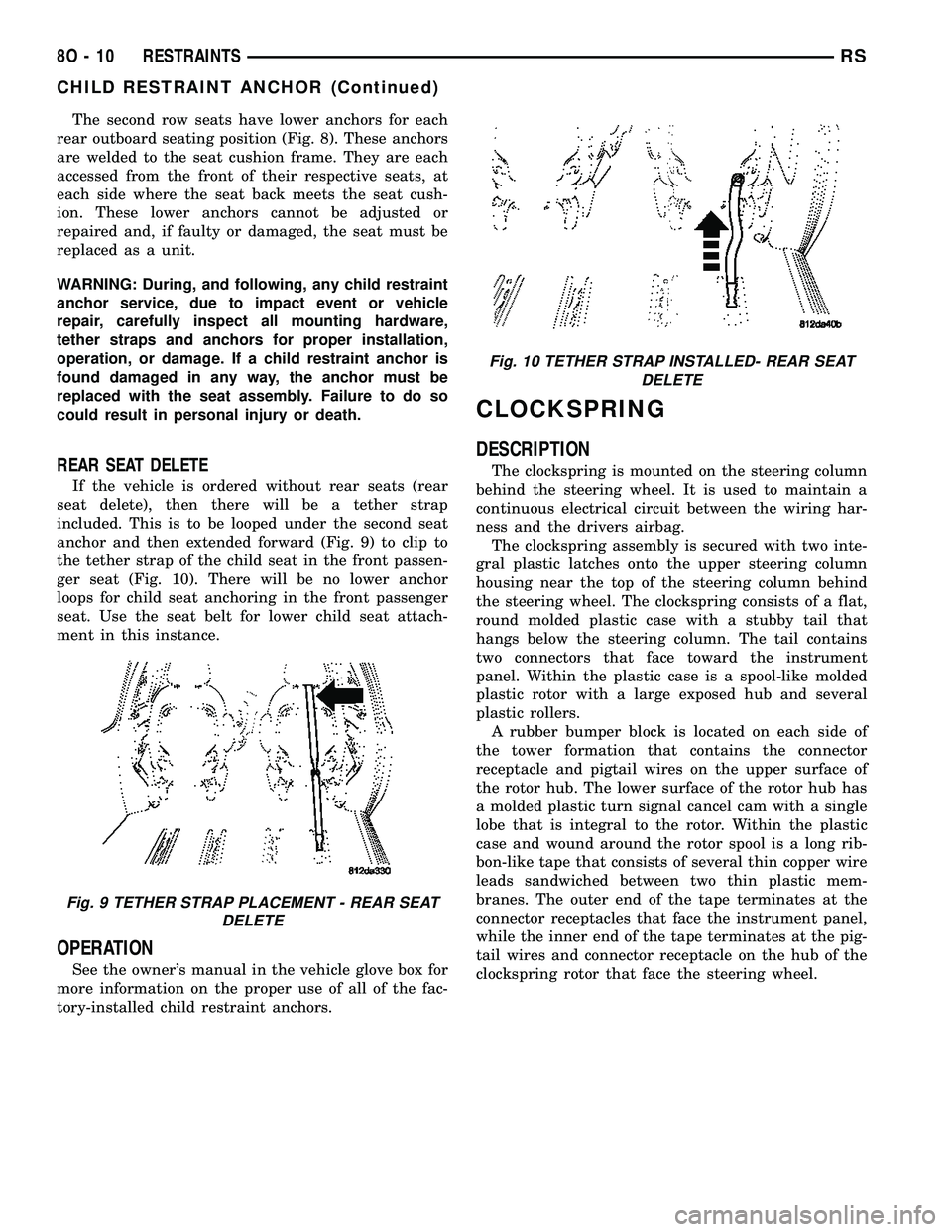
The second row seats have lower anchors for each
rear outboard seating position (Fig. 8). These anchors
are welded to the seat cushion frame. They are each
accessed from the front of their respective seats, at
each side where the seat back meets the seat cush-
ion. These lower anchors cannot be adjusted or
repaired and, if faulty or damaged, the seat must be
replaced as a unit.
WARNING: During, and following, any child restraint
anchor service, due to impact event or vehicle
repair, carefully inspect all mounting hardware,
tether straps and anchors for proper installation,
operation, or damage. If a child restraint anchor is
found damaged in any way, the anchor must be
replaced with the seat assembly. Failure to do so
could result in personal injury or death.
REAR SEAT DELETE
If the vehicle is ordered without rear seats (rear
seat delete), then there will be a tether strap
included. This is to be looped under the second seat
anchor and then extended forward (Fig. 9) to clip to
the tether strap of the child seat in the front passen-
ger seat (Fig. 10). There will be no lower anchor
loops for child seat anchoring in the front passenger
seat. Use the seat belt for lower child seat attach-
ment in this instance.
OPERATION
See the owner's manual in the vehicle glove box for
more information on the proper use of all of the fac-
tory-installed child restraint anchors.
CLOCKSPRING
DESCRIPTION
The clockspring is mounted on the steering column
behind the steering wheel. It is used to maintain a
continuous electrical circuit between the wiring har-
ness and the drivers airbag.
The clockspring assembly is secured with two inte-
gral plastic latches onto the upper steering column
housing near the top of the steering column behind
the steering wheel. The clockspring consists of a flat,
round molded plastic case with a stubby tail that
hangs below the steering column. The tail contains
two connectors that face toward the instrument
panel. Within the plastic case is a spool-like molded
plastic rotor with a large exposed hub and several
plastic rollers.
A rubber bumper block is located on each side of
the tower formation that contains the connector
receptacle and pigtail wires on the upper surface of
the rotor hub. The lower surface of the rotor hub has
a molded plastic turn signal cancel cam with a single
lobe that is integral to the rotor. Within the plastic
case and wound around the rotor spool is a long rib-
bon-like tape that consists of several thin copper wire
leads sandwiched between two thin plastic mem-
branes. The outer end of the tape terminates at the
connector receptacles that face the instrument panel,
while the inner end of the tape terminates at the pig-
tail wires and connector receptacle on the hub of the
clockspring rotor that face the steering wheel.
Fig. 9 TETHER STRAP PLACEMENT - REAR SEAT
DELETE
Fig. 10 TETHER STRAP INSTALLED- REAR SEAT
DELETE
8O - 10 RESTRAINTSRS
CHILD RESTRAINT ANCHOR (Continued)
Page 498 of 2339
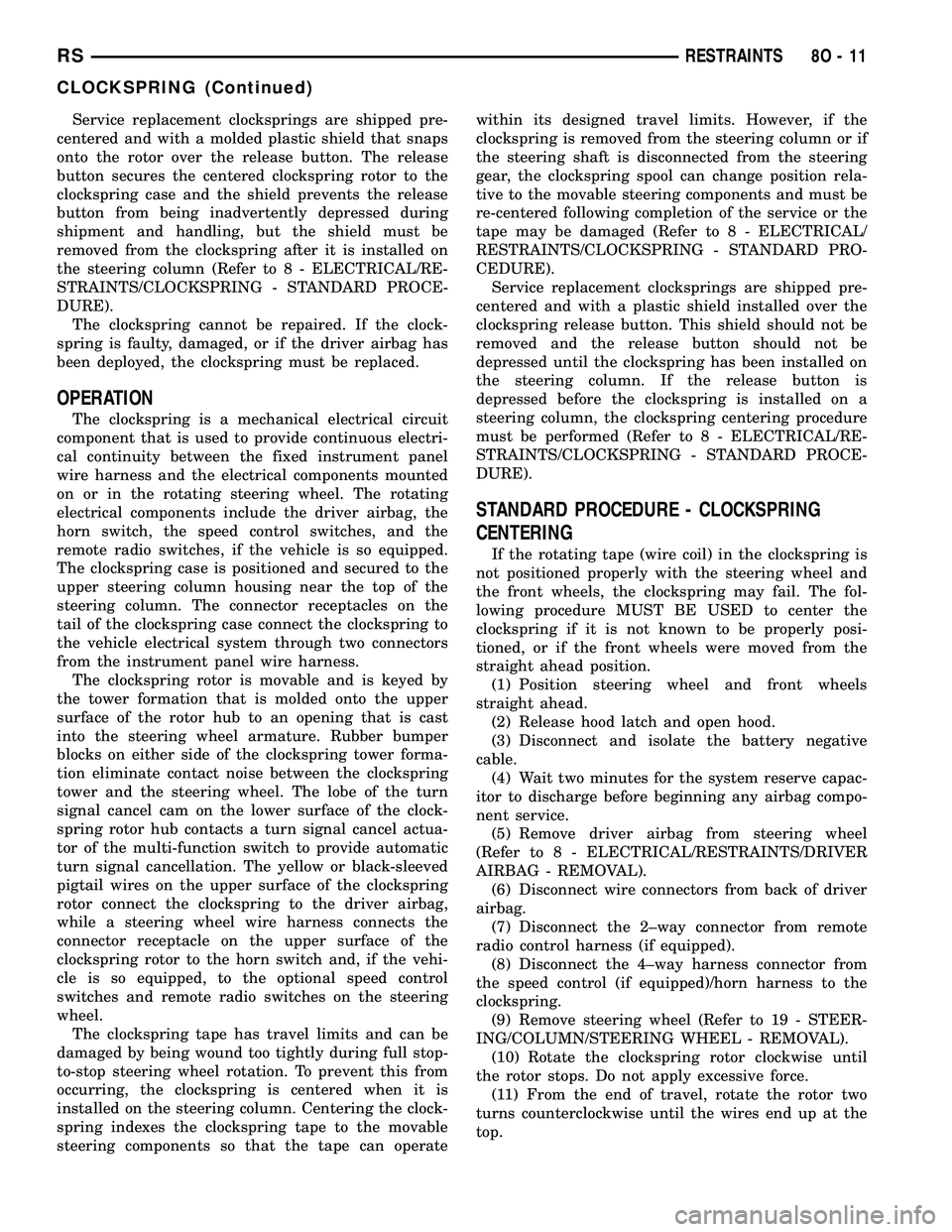
Service replacement clocksprings are shipped pre-
centered and with a molded plastic shield that snaps
onto the rotor over the release button. The release
button secures the centered clockspring rotor to the
clockspring case and the shield prevents the release
button from being inadvertently depressed during
shipment and handling, but the shield must be
removed from the clockspring after it is installed on
the steering column (Refer to 8 - ELECTRICAL/RE-
STRAINTS/CLOCKSPRING - STANDARD PROCE-
DURE).
The clockspring cannot be repaired. If the clock-
spring is faulty, damaged, or if the driver airbag has
been deployed, the clockspring must be replaced.
OPERATION
The clockspring is a mechanical electrical circuit
component that is used to provide continuous electri-
cal continuity between the fixed instrument panel
wire harness and the electrical components mounted
on or in the rotating steering wheel. The rotating
electrical components include the driver airbag, the
horn switch, the speed control switches, and the
remote radio switches, if the vehicle is so equipped.
The clockspring case is positioned and secured to the
upper steering column housing near the top of the
steering column. The connector receptacles on the
tail of the clockspring case connect the clockspring to
the vehicle electrical system through two connectors
from the instrument panel wire harness.
The clockspring rotor is movable and is keyed by
the tower formation that is molded onto the upper
surface of the rotor hub to an opening that is cast
into the steering wheel armature. Rubber bumper
blocks on either side of the clockspring tower forma-
tion eliminate contact noise between the clockspring
tower and the steering wheel. The lobe of the turn
signal cancel cam on the lower surface of the clock-
spring rotor hub contacts a turn signal cancel actua-
tor of the multi-function switch to provide automatic
turn signal cancellation. The yellow or black-sleeved
pigtail wires on the upper surface of the clockspring
rotor connect the clockspring to the driver airbag,
while a steering wheel wire harness connects the
connector receptacle on the upper surface of the
clockspring rotor to the horn switch and, if the vehi-
cle is so equipped, to the optional speed control
switches and remote radio switches on the steering
wheel.
The clockspring tape has travel limits and can be
damaged by being wound too tightly during full stop-
to-stop steering wheel rotation. To prevent this from
occurring, the clockspring is centered when it is
installed on the steering column. Centering the clock-
spring indexes the clockspring tape to the movable
steering components so that the tape can operatewithin its designed travel limits. However, if the
clockspring is removed from the steering column or if
the steering shaft is disconnected from the steering
gear, the clockspring spool can change position rela-
tive to the movable steering components and must be
re-centered following completion of the service or the
tape may be damaged (Refer to 8 - ELECTRICAL/
RESTRAINTS/CLOCKSPRING - STANDARD PRO-
CEDURE).
Service replacement clocksprings are shipped pre-
centered and with a plastic shield installed over the
clockspring release button. This shield should not be
removed and the release button should not be
depressed until the clockspring has been installed on
the steering column. If the release button is
depressed before the clockspring is installed on a
steering column, the clockspring centering procedure
must be performed (Refer to 8 - ELECTRICAL/RE-
STRAINTS/CLOCKSPRING - STANDARD PROCE-
DURE).
STANDARD PROCEDURE - CLOCKSPRING
CENTERING
If the rotating tape (wire coil) in the clockspring is
not positioned properly with the steering wheel and
the front wheels, the clockspring may fail. The fol-
lowing procedure MUST BE USED to center the
clockspring if it is not known to be properly posi-
tioned, or if the front wheels were moved from the
straight ahead position.
(1) Position steering wheel and front wheels
straight ahead.
(2) Release hood latch and open hood.
(3) Disconnect and isolate the battery negative
cable.
(4) Wait two minutes for the system reserve capac-
itor to discharge before beginning any airbag compo-
nent service.
(5) Remove driver airbag from steering wheel
(Refer to 8 - ELECTRICAL/RESTRAINTS/DRIVER
AIRBAG - REMOVAL).
(6) Disconnect wire connectors from back of driver
airbag.
(7) Disconnect the 2±way connector from remote
radio control harness (if equipped).
(8) Disconnect the 4±way harness connector from
the speed control (if equipped)/horn harness to the
clockspring.
(9) Remove steering wheel (Refer to 19 - STEER-
ING/COLUMN/STEERING WHEEL - REMOVAL).
(10) Rotate the clockspring rotor clockwise until
the rotor stops. Do not apply excessive force.
(11) From the end of travel, rotate the rotor two
turns counterclockwise until the wires end up at the
top.
RSRESTRAINTS8O-11
CLOCKSPRING (Continued)
Page 504 of 2339
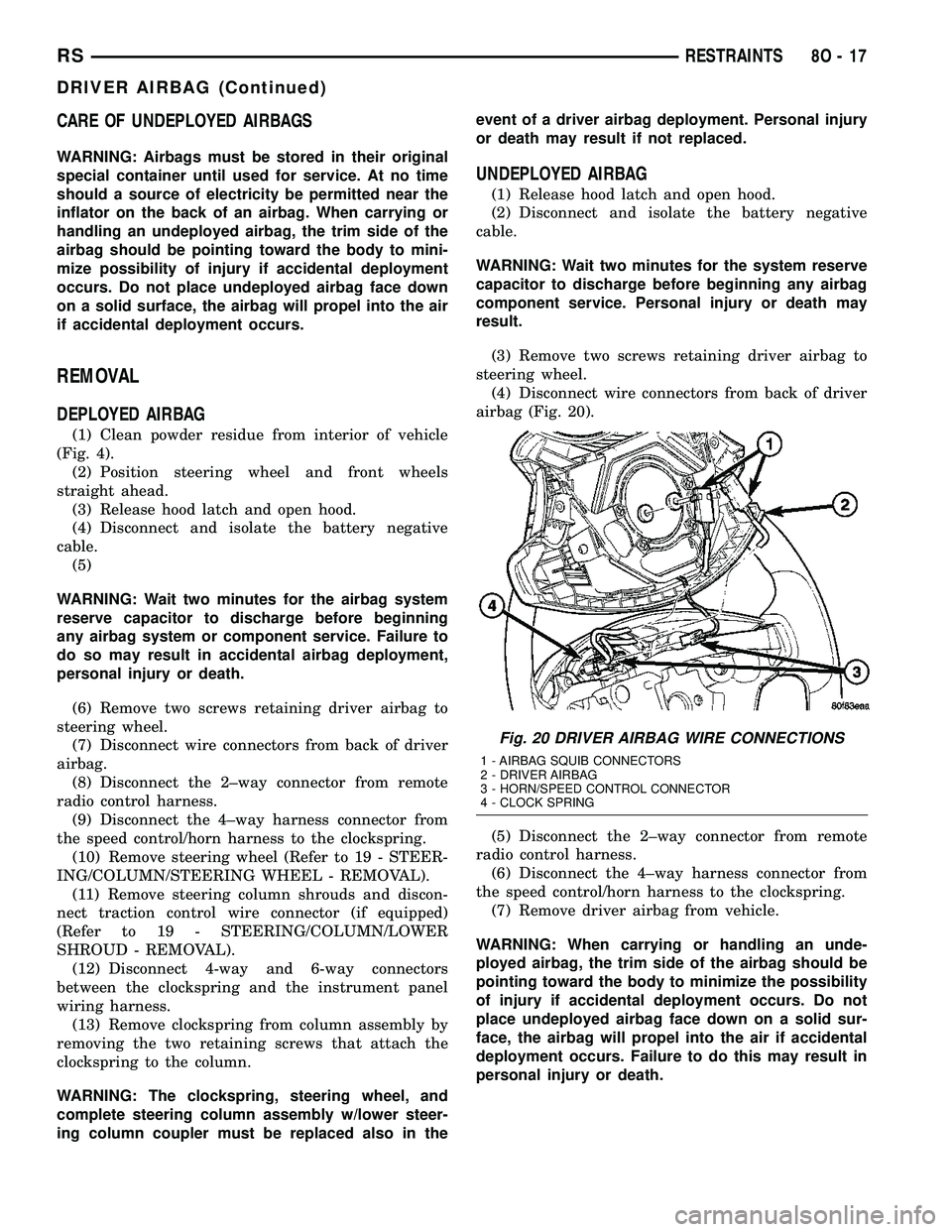
CARE OF UNDEPLOYED AIRBAGS
WARNING: Airbags must be stored in their original
special container until used for service. At no time
should a source of electricity be permitted near the
inflator on the back of an airbag. When carrying or
handling an undeployed airbag, the trim side of the
airbag should be pointing toward the body to mini-
mize possibility of injury if accidental deployment
occurs. Do not place undeployed airbag face down
on a solid surface, the airbag will propel into the air
if accidental deployment occurs.
REMOVAL
DEPLOYED AIRBAG
(1) Clean powder residue from interior of vehicle
(Fig. 4).
(2) Position steering wheel and front wheels
straight ahead.
(3) Release hood latch and open hood.
(4) Disconnect and isolate the battery negative
cable.
(5)
WARNING: Wait two minutes for the airbag system
reserve capacitor to discharge before beginning
any airbag system or component service. Failure to
do so may result in accidental airbag deployment,
personal injury or death.
(6) Remove two screws retaining driver airbag to
steering wheel.
(7) Disconnect wire connectors from back of driver
airbag.
(8) Disconnect the 2±way connector from remote
radio control harness.
(9) Disconnect the 4±way harness connector from
the speed control/horn harness to the clockspring.
(10) Remove steering wheel (Refer to 19 - STEER-
ING/COLUMN/STEERING WHEEL - REMOVAL).
(11) Remove steering column shrouds and discon-
nect traction control wire connector (if equipped)
(Refer to 19 - STEERING/COLUMN/LOWER
SHROUD - REMOVAL).
(12) Disconnect 4-way and 6-way connectors
between the clockspring and the instrument panel
wiring harness.
(13) Remove clockspring from column assembly by
removing the two retaining screws that attach the
clockspring to the column.
WARNING: The clockspring, steering wheel, and
complete steering column assembly w/lower steer-
ing column coupler must be replaced also in theevent of a driver airbag deployment. Personal injury
or death may result if not replaced.
UNDEPLOYED AIRBAG
(1) Release hood latch and open hood.
(2) Disconnect and isolate the battery negative
cable.
WARNING: Wait two minutes for the system reserve
capacitor to discharge before beginning any airbag
component service. Personal injury or death may
result.
(3) Remove two screws retaining driver airbag to
steering wheel.
(4) Disconnect wire connectors from back of driver
airbag (Fig. 20).
(5) Disconnect the 2±way connector from remote
radio control harness.
(6) Disconnect the 4±way harness connector from
the speed control/horn harness to the clockspring.
(7) Remove driver airbag from vehicle.
WARNING: When carrying or handling an unde-
ployed airbag, the trim side of the airbag should be
pointing toward the body to minimize the possibility
of injury if accidental deployment occurs. Do not
place undeployed airbag face down on a solid sur-
face, the airbag will propel into the air if accidental
deployment occurs. Failure to do this may result in
personal injury or death.
Fig. 20 DRIVER AIRBAG WIRE CONNECTIONS
1 - AIRBAG SQUIB CONNECTORS
2 - DRIVER AIRBAG
3 - HORN/SPEED CONTROL CONNECTOR
4 - CLOCK SPRING
RSRESTRAINTS8O-17
DRIVER AIRBAG (Continued)
Page 509 of 2339
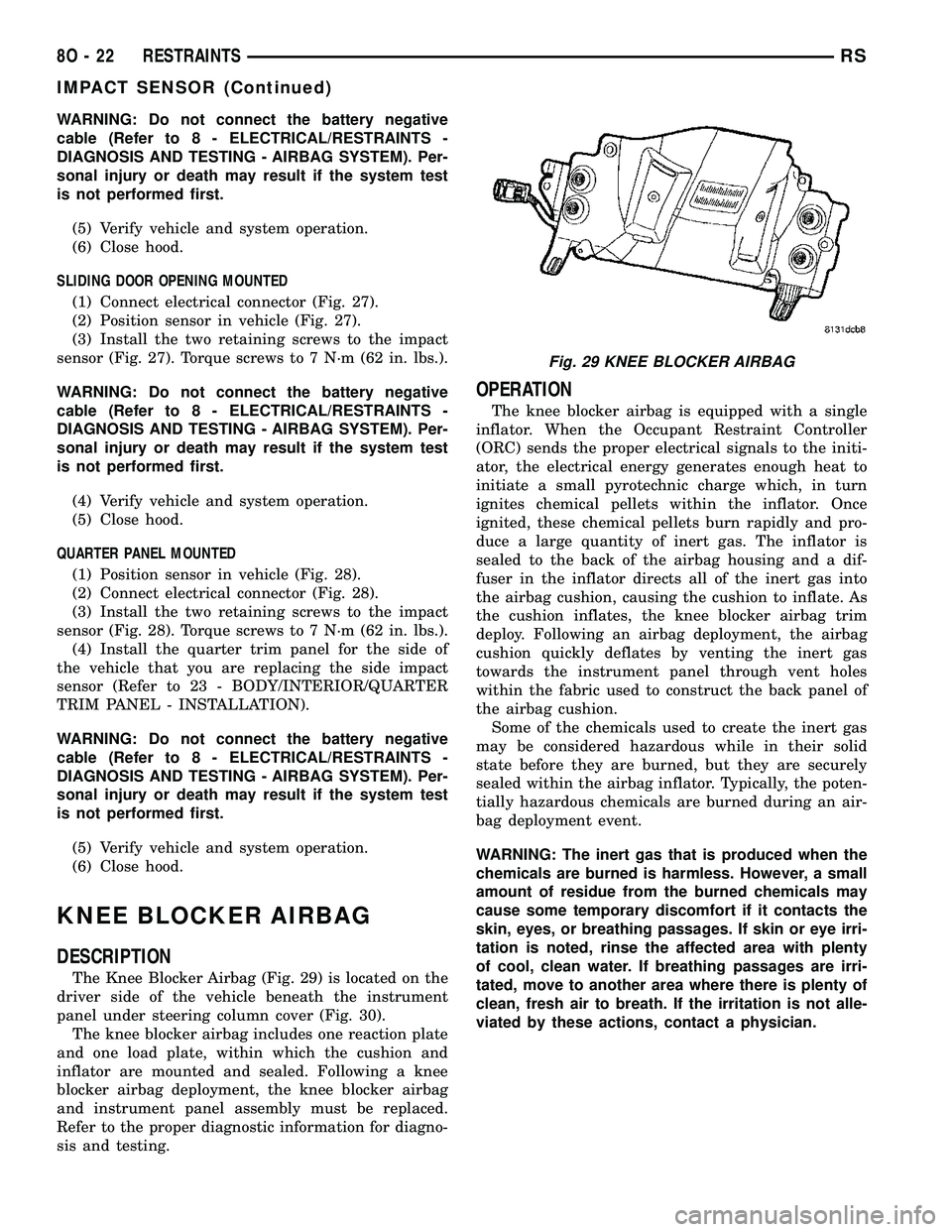
WARNING: Do not connect the battery negative
cable (Refer to 8 - ELECTRICAL/RESTRAINTS -
DIAGNOSIS AND TESTING - AIRBAG SYSTEM). Per-
sonal injury or death may result if the system test
is not performed first.
(5) Verify vehicle and system operation.
(6) Close hood.
SLIDING DOOR OPENING MOUNTED
(1) Connect electrical connector (Fig. 27).
(2) Position sensor in vehicle (Fig. 27).
(3) Install the two retaining screws to the impact
sensor (Fig. 27). Torque screws to 7 N´m (62 in. lbs.).
WARNING: Do not connect the battery negative
cable (Refer to 8 - ELECTRICAL/RESTRAINTS -
DIAGNOSIS AND TESTING - AIRBAG SYSTEM). Per-
sonal injury or death may result if the system test
is not performed first.
(4) Verify vehicle and system operation.
(5) Close hood.
QUARTER PANEL MOUNTED
(1) Position sensor in vehicle (Fig. 28).
(2) Connect electrical connector (Fig. 28).
(3) Install the two retaining screws to the impact
sensor (Fig. 28). Torque screws to 7 N´m (62 in. lbs.).
(4) Install the quarter trim panel for the side of
the vehicle that you are replacing the side impact
sensor (Refer to 23 - BODY/INTERIOR/QUARTER
TRIM PANEL - INSTALLATION).
WARNING: Do not connect the battery negative
cable (Refer to 8 - ELECTRICAL/RESTRAINTS -
DIAGNOSIS AND TESTING - AIRBAG SYSTEM). Per-
sonal injury or death may result if the system test
is not performed first.
(5) Verify vehicle and system operation.
(6) Close hood.
KNEE BLOCKER AIRBAG
DESCRIPTION
The Knee Blocker Airbag (Fig. 29) is located on the
driver side of the vehicle beneath the instrument
panel under steering column cover (Fig. 30).
The knee blocker airbag includes one reaction plate
and one load plate, within which the cushion and
inflator are mounted and sealed. Following a knee
blocker airbag deployment, the knee blocker airbag
and instrument panel assembly must be replaced.
Refer to the proper diagnostic information for diagno-
sis and testing.
OPERATION
The knee blocker airbag is equipped with a single
inflator. When the Occupant Restraint Controller
(ORC) sends the proper electrical signals to the initi-
ator, the electrical energy generates enough heat to
initiate a small pyrotechnic charge which, in turn
ignites chemical pellets within the inflator. Once
ignited, these chemical pellets burn rapidly and pro-
duce a large quantity of inert gas. The inflator is
sealed to the back of the airbag housing and a dif-
fuser in the inflator directs all of the inert gas into
the airbag cushion, causing the cushion to inflate. As
the cushion inflates, the knee blocker airbag trim
deploy. Following an airbag deployment, the airbag
cushion quickly deflates by venting the inert gas
towards the instrument panel through vent holes
within the fabric used to construct the back panel of
the airbag cushion.
Some of the chemicals used to create the inert gas
may be considered hazardous while in their solid
state before they are burned, but they are securely
sealed within the airbag inflator. Typically, the poten-
tially hazardous chemicals are burned during an air-
bag deployment event.
WARNING: The inert gas that is produced when the
chemicals are burned is harmless. However, a small
amount of residue from the burned chemicals may
cause some temporary discomfort if it contacts the
skin, eyes, or breathing passages. If skin or eye irri-
tation is noted, rinse the affected area with plenty
of cool, clean water. If breathing passages are irri-
tated, move to another area where there is plenty of
clean, fresh air to breath. If the irritation is not alle-
viated by these actions, contact a physician.
Fig. 29 KNEE BLOCKER AIRBAG
8O - 22 RESTRAINTSRS
IMPACT SENSOR (Continued)
Page 512 of 2339
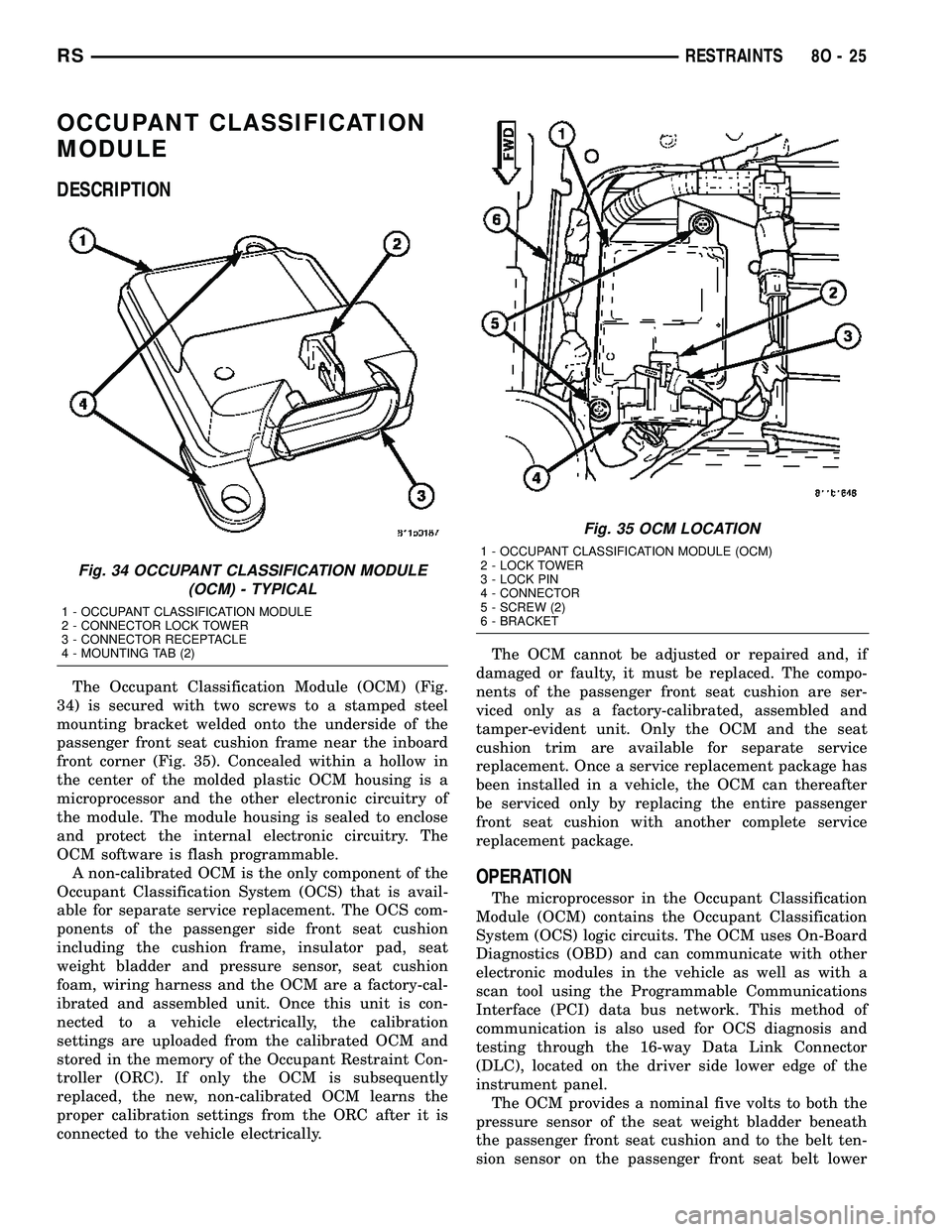
OCCUPANT CLASSIFICATION
MODULE
DESCRIPTION
The Occupant Classification Module (OCM) (Fig.
34) is secured with two screws to a stamped steel
mounting bracket welded onto the underside of the
passenger front seat cushion frame near the inboard
front corner (Fig. 35). Concealed within a hollow in
the center of the molded plastic OCM housing is a
microprocessor and the other electronic circuitry of
the module. The module housing is sealed to enclose
and protect the internal electronic circuitry. The
OCM software is flash programmable.
A non-calibrated OCM is the only component of the
Occupant Classification System (OCS) that is avail-
able for separate service replacement. The OCS com-
ponents of the passenger side front seat cushion
including the cushion frame, insulator pad, seat
weight bladder and pressure sensor, seat cushion
foam, wiring harness and the OCM are a factory-cal-
ibrated and assembled unit. Once this unit is con-
nected to a vehicle electrically, the calibration
settings are uploaded from the calibrated OCM and
stored in the memory of the Occupant Restraint Con-
troller (ORC). If only the OCM is subsequently
replaced, the new, non-calibrated OCM learns the
proper calibration settings from the ORC after it is
connected to the vehicle electrically.The OCM cannot be adjusted or repaired and, if
damaged or faulty, it must be replaced. The compo-
nents of the passenger front seat cushion are ser-
viced only as a factory-calibrated, assembled and
tamper-evident unit. Only the OCM and the seat
cushion trim are available for separate service
replacement. Once a service replacement package has
been installed in a vehicle, the OCM can thereafter
be serviced only by replacing the entire passenger
front seat cushion with another complete service
replacement package.
OPERATION
The microprocessor in the Occupant Classification
Module (OCM) contains the Occupant Classification
System (OCS) logic circuits. The OCM uses On-Board
Diagnostics (OBD) and can communicate with other
electronic modules in the vehicle as well as with a
scan tool using the Programmable Communications
Interface (PCI) data bus network. This method of
communication is also used for OCS diagnosis and
testing through the 16-way Data Link Connector
(DLC), located on the driver side lower edge of the
instrument panel.
The OCM provides a nominal five volts to both the
pressure sensor of the seat weight bladder beneath
the passenger front seat cushion and to the belt ten-
sion sensor on the passenger front seat belt lower
Fig. 34 OCCUPANT CLASSIFICATION MODULE
(OCM) - TYPICAL
1 - OCCUPANT CLASSIFICATION MODULE
2 - CONNECTOR LOCK TOWER
3 - CONNECTOR RECEPTACLE
4 - MOUNTING TAB (2)
Fig. 35 OCM LOCATION
1 - OCCUPANT CLASSIFICATION MODULE (OCM)
2 - LOCK TOWER
3 - LOCK PIN
4 - CONNECTOR
5 - SCREW (2)
6 - BRACKET
RSRESTRAINTS8O-25
Page 513 of 2339
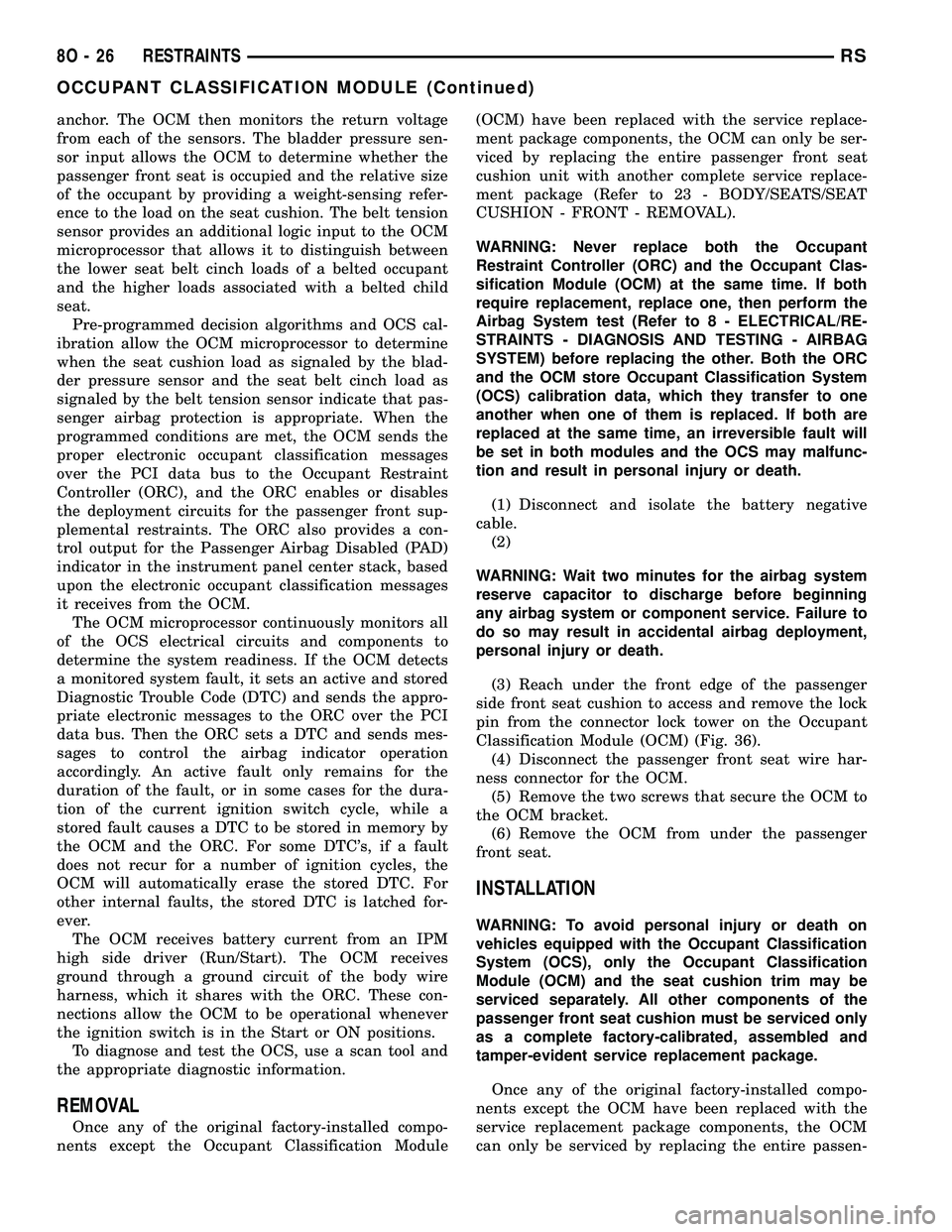
anchor. The OCM then monitors the return voltage
from each of the sensors. The bladder pressure sen-
sor input allows the OCM to determine whether the
passenger front seat is occupied and the relative size
of the occupant by providing a weight-sensing refer-
ence to the load on the seat cushion. The belt tension
sensor provides an additional logic input to the OCM
microprocessor that allows it to distinguish between
the lower seat belt cinch loads of a belted occupant
and the higher loads associated with a belted child
seat.
Pre-programmed decision algorithms and OCS cal-
ibration allow the OCM microprocessor to determine
when the seat cushion load as signaled by the blad-
der pressure sensor and the seat belt cinch load as
signaled by the belt tension sensor indicate that pas-
senger airbag protection is appropriate. When the
programmed conditions are met, the OCM sends the
proper electronic occupant classification messages
over the PCI data bus to the Occupant Restraint
Controller (ORC), and the ORC enables or disables
the deployment circuits for the passenger front sup-
plemental restraints. The ORC also provides a con-
trol output for the Passenger Airbag Disabled (PAD)
indicator in the instrument panel center stack, based
upon the electronic occupant classification messages
it receives from the OCM.
The OCM microprocessor continuously monitors all
of the OCS electrical circuits and components to
determine the system readiness. If the OCM detects
a monitored system fault, it sets an active and stored
Diagnostic Trouble Code (DTC) and sends the appro-
priate electronic messages to the ORC over the PCI
data bus. Then the ORC sets a DTC and sends mes-
sages to control the airbag indicator operation
accordingly. An active fault only remains for the
duration of the fault, or in some cases for the dura-
tion of the current ignition switch cycle, while a
stored fault causes a DTC to be stored in memory by
the OCM and the ORC. For some DTC's, if a fault
does not recur for a number of ignition cycles, the
OCM will automatically erase the stored DTC. For
other internal faults, the stored DTC is latched for-
ever.
The OCM receives battery current from an IPM
high side driver (Run/Start). The OCM receives
ground through a ground circuit of the body wire
harness, which it shares with the ORC. These con-
nections allow the OCM to be operational whenever
the ignition switch is in the Start or ON positions.
To diagnose and test the OCS, use a scan tool and
the appropriate diagnostic information.
REMOVAL
Once any of the original factory-installed compo-
nents except the Occupant Classification Module(OCM) have been replaced with the service replace-
ment package components, the OCM can only be ser-
viced by replacing the entire passenger front seat
cushion unit with another complete service replace-
ment package (Refer to 23 - BODY/SEATS/SEAT
CUSHION - FRONT - REMOVAL).
WARNING: Never replace both the Occupant
Restraint Controller (ORC) and the Occupant Clas-
sification Module (OCM) at the same time. If both
require replacement, replace one, then perform the
Airbag System test (Refer to 8 - ELECTRICAL/RE-
STRAINTS - DIAGNOSIS AND TESTING - AIRBAG
SYSTEM) before replacing the other. Both the ORC
and the OCM store Occupant Classification System
(OCS) calibration data, which they transfer to one
another when one of them is replaced. If both are
replaced at the same time, an irreversible fault will
be set in both modules and the OCS may malfunc-
tion and result in personal injury or death.
(1) Disconnect and isolate the battery negative
cable.
(2)
WARNING: Wait two minutes for the airbag system
reserve capacitor to discharge before beginning
any airbag system or component service. Failure to
do so may result in accidental airbag deployment,
personal injury or death.
(3) Reach under the front edge of the passenger
side front seat cushion to access and remove the lock
pin from the connector lock tower on the Occupant
Classification Module (OCM) (Fig. 36).
(4) Disconnect the passenger front seat wire har-
ness connector for the OCM.
(5) Remove the two screws that secure the OCM to
the OCM bracket.
(6) Remove the OCM from under the passenger
front seat.
INSTALLATION
WARNING: To avoid personal injury or death on
vehicles equipped with the Occupant Classification
System (OCS), only the Occupant Classification
Module (OCM) and the seat cushion trim may be
serviced separately. All other components of the
passenger front seat cushion must be serviced only
as a complete factory-calibrated, assembled and
tamper-evident service replacement package.
Once any of the original factory-installed compo-
nents except the OCM have been replaced with the
service replacement package components, the OCM
can only be serviced by replacing the entire passen-
8O - 26 RESTRAINTSRS
OCCUPANT CLASSIFICATION MODULE (Continued)