check engine Citroen CX 1977 1.G Service Manual
[x] Cancel search | Manufacturer: CITROEN, Model Year: 1977, Model line: CX, Model: Citroen CX 1977 1.GPages: 394
Page 165 of 394
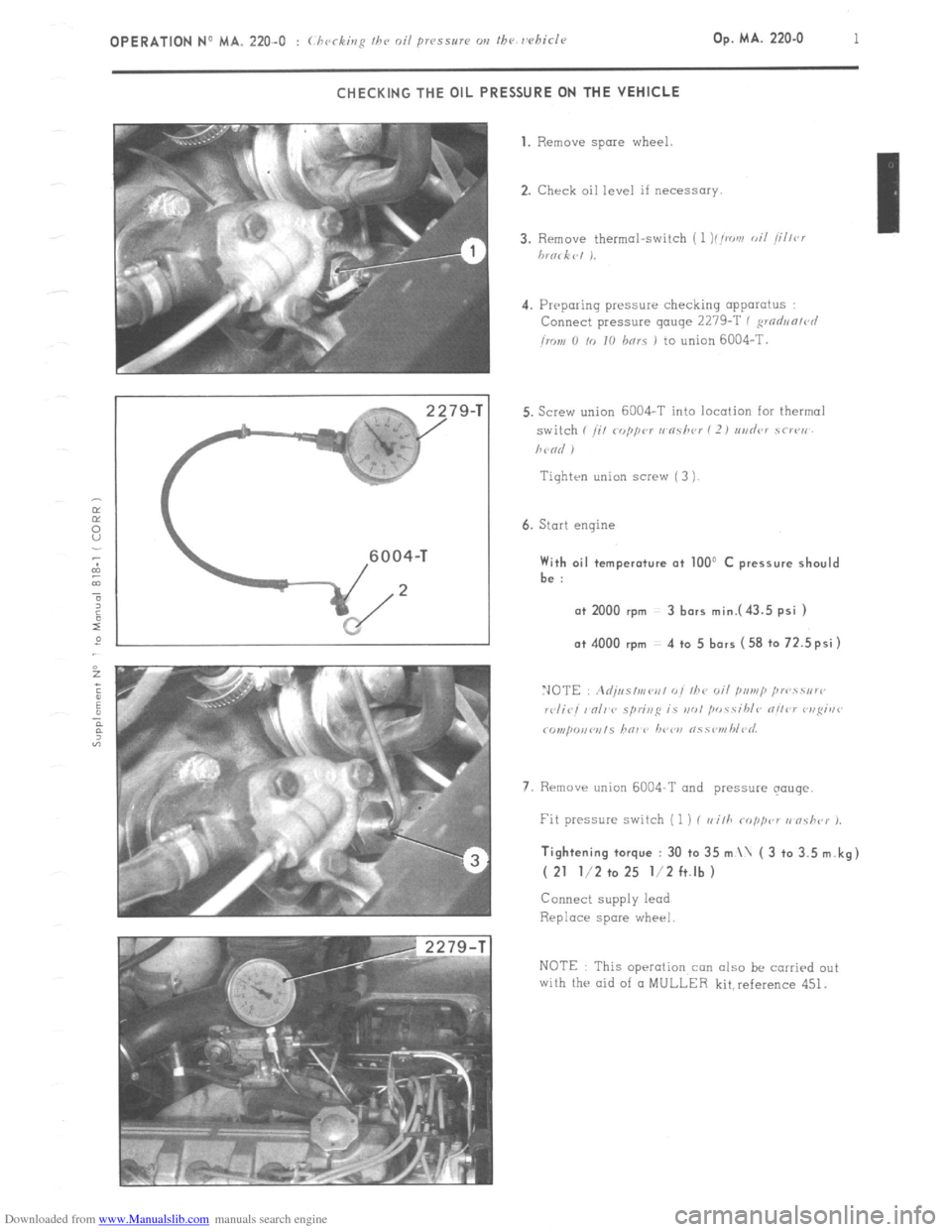
Downloaded from www.Manualslib.com manuals search engine OPERATION No MA. 220-O : (.hrrkinfi Ih e oil pr~ssrrrc m the rehicle Op. MA. 220.0 1
CHECKING THE OIL PRESSURE ON THE VEHICLE
79-T 1. Remove spare
wheel.
2. Check oil level if necessary.
4. Preparing pressure checking apparatus
Connect pressure gauge 2279-T ( ,wdun/r~l
imn 0 /o IO hnrs 1 to union 6004-T.
Tiqhten union screw ( 3 )
6. Start engine With oil temperature at 100’ C pressure should
be :
a+ 2000 rpm 3 bars mini43.5 psi ) o+ 4000 rpm 4 to 5 bars (58 to 72.5psi)
7. Rrmave union 6004-T and pressure qouqe. Tightening torque : 30 to 35 m \ ( 3 to 3.5 m.kg)
( 21 l/2 to 25 l/2 ft.lb )
Connect supply lead
Replace spare wheel
NOTE This operation con also be carried out
with the aid of CI MULLER kit,reference 451.
Page 166 of 394
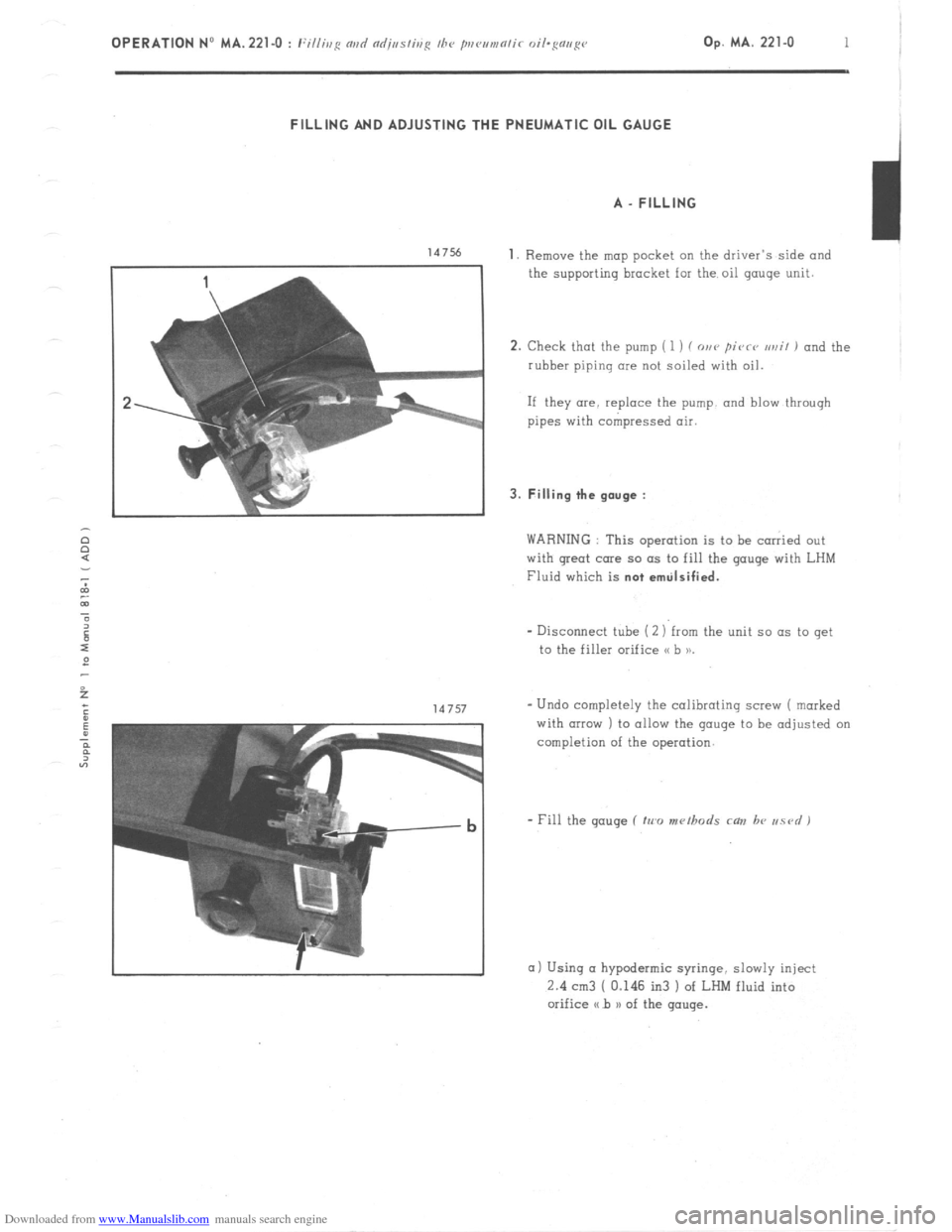
Downloaded from www.Manualslib.com manuals search engine Op. MA. 221-O I
FILLING AND ADJUSTING THE PNEUMATIC OIL GAUGE
A _ FILLING
147% 1. Remove the map pocket on the driver’s side and
the supporting bracket for the oil gauge unit.
2. Check that the pump ( 1 ) f o,,v pivrv ur,il 1 and the
rubber piping clue not soiled with oil.
If they are. replace the pump. and blow through
pipes with compressed air. 3. Filling the gauge :
WARNING : This operation is to be carried out
with great care so as to fill the gauge with LHM
Fluid which is not emtilsified.
- Disconnect tube (2 ) from the unit so as to get
to the filler orifice o b 11.
- Undo completely the calibrating screw ( marked
with (IIPXJ ) to allow the gauge to be adjusted on
completion of the operation.
a) Using CI hypodermic syringe. slowly inject
2.4 cm3 [ 0.146 in3 ) of LHM fluid into
orifice a b n of the gauge.
Page 168 of 394
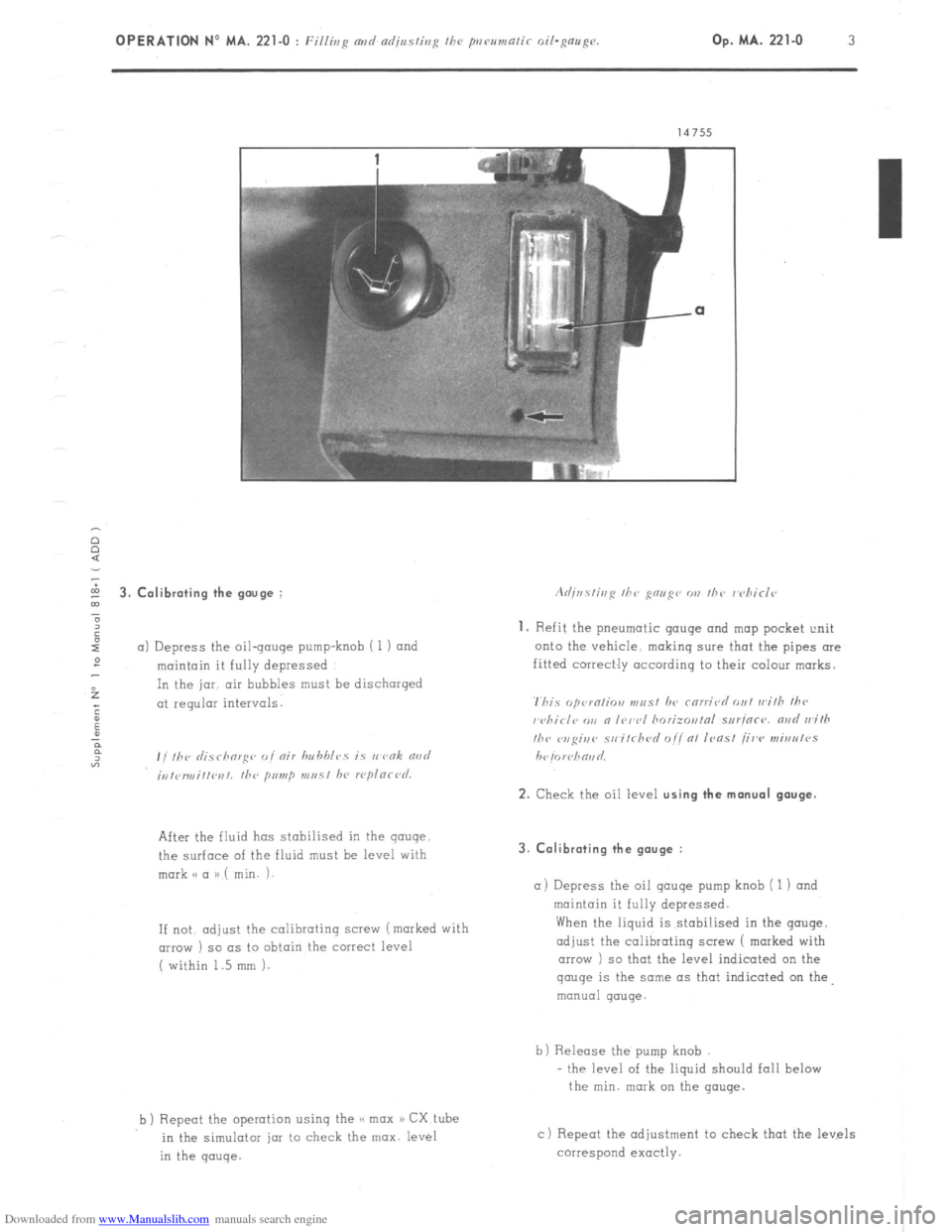
Downloaded from www.Manualslib.com manuals search engine Op. MA. 221-O 3 -
5 3. Calibrating the gouge :
”
6
I
a) Depress the oil-gouge pump-knob i 1) and
:
maintain it fully depressed
f In the jar. air bubbles must be discharged
; at regular intervals.
:
u
P
F
“3 , , ,hr ,I;.7 rhorg<~ ,, I nir hn hhlcs is I, vnk rind
;,,,<,r,,,i,,l~r,,. the primp m,, 51 hl, rcplnrl~d.
After the fluid has stabilised in the gauge
the surface of the fluid must be level with
mark o a a) ( min. i-
If not. adjust
the calibrating screw (marked with
(IIIOW ) so as to obtain the correct level
( within 1.5 mm 1.
b ) Repeot the operation using the << max a) CX tube
in the simulotar jar to check the max. level
in the gauge. 3. Calibrating the gauge :
a) Depress
the oil qauqe pump knob ( 1 1 and
maintain it fully depressed.
When the liquid is stabi!ised in the gouge,
adjust the calibrating screw 1 marked with
arrow ) so that the level indicated on the gauge
is the same as that indicated on the
manual gauge.
b) Release the pump knob
- the level of the liquid should fall below
the min. mark on the gauge.
c) Repeat the adjustment to check that the levels
correspond exactly.
Page 179 of 394
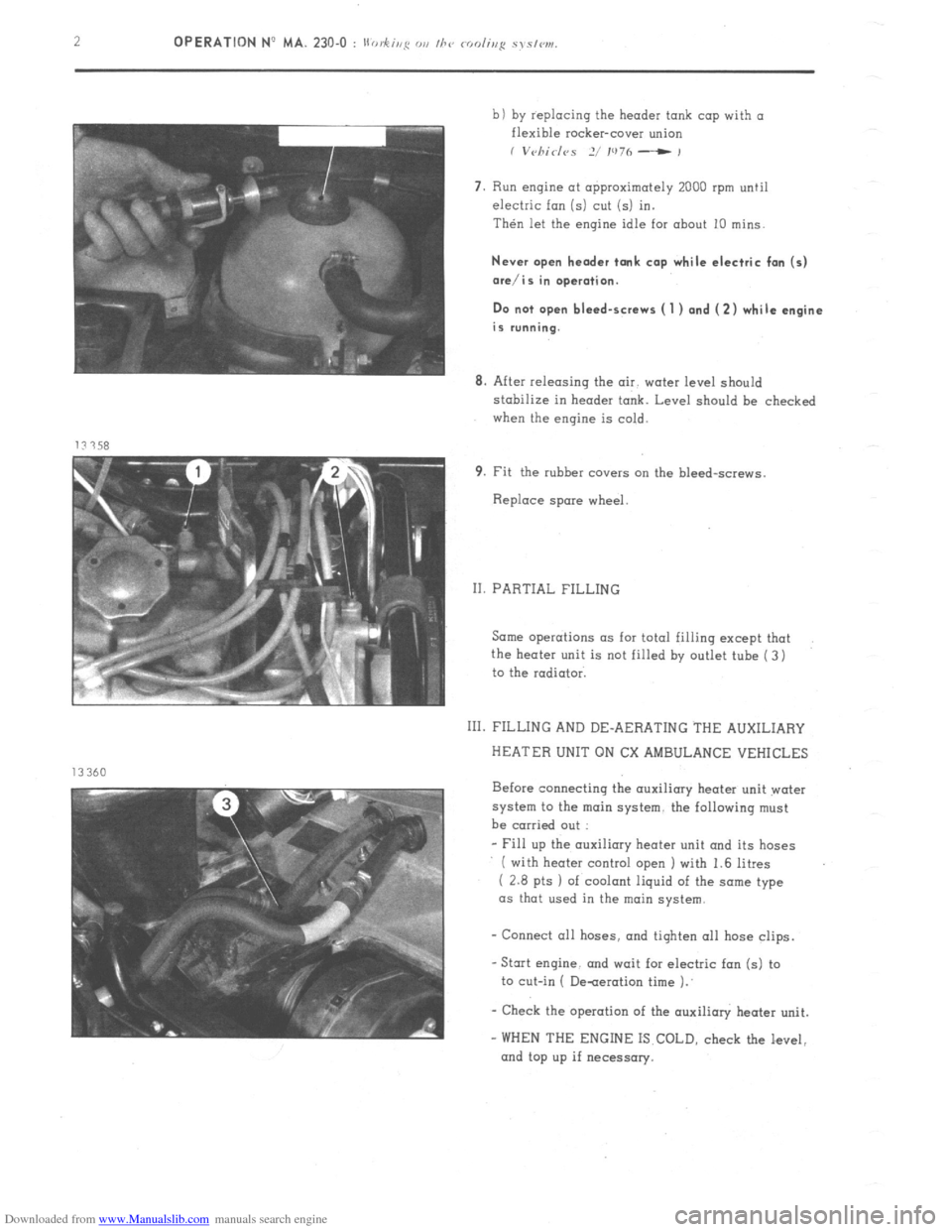
Downloaded from www.Manualslib.com manuals search engine 2 OPERATION No MA. 230-O : II .h’ 0, fug Ol, I/7‘, rodir,p sys/w1.
b) by replacing the header tank cap with a
flexible rocker-cover union
I V~~/7id<~S 2/ IU7h - ,
7. Run engine at approximately 2000 rpm until
electric fan (5) cut (5) in.
Then let the engine idle for about 10 mins.
Never open header tank cap while electric fan (5)
ore/is in operation.
Do not open bleed-screws ( 1 ) and (2) while engine
is running.
8. After releasing the air. water level should
stabilize in header tank. Level should be checked
when the engine is cold.
9. Fit the rubber covers cm the bleed-screws.
Replace spare wheel.
II. PARTIAL FILLING
Same operations as for total filling except that
the heater unit is not filled by outlet tube ( 3)
to the radiator.
111. FILLING AND DE-AERATING THE AUXILIARY
HEATER UNIT ON CX AMBULANCE VEHICLES
Before connecting the auxiliary heater unit water
system to the main system. the following must
be carried out :
- Fill up the auxiliary heater unit and its hoses
( with heater control open I with 1.6 litres
( 2.8 pts 1 of coolant liquid of the some type
as that used in the main
system.
- Connect all hoses. and tiqhten 011 hose clips.
-Stat engine. and wait for electric fan (5) to
to cut-in ( De-aeration time 1.’
- Check the operation of the auxilioly heater unit.
- WHEN THE ENGINE IS COLD, check the level,
and top up if necessary.
Page 189 of 394
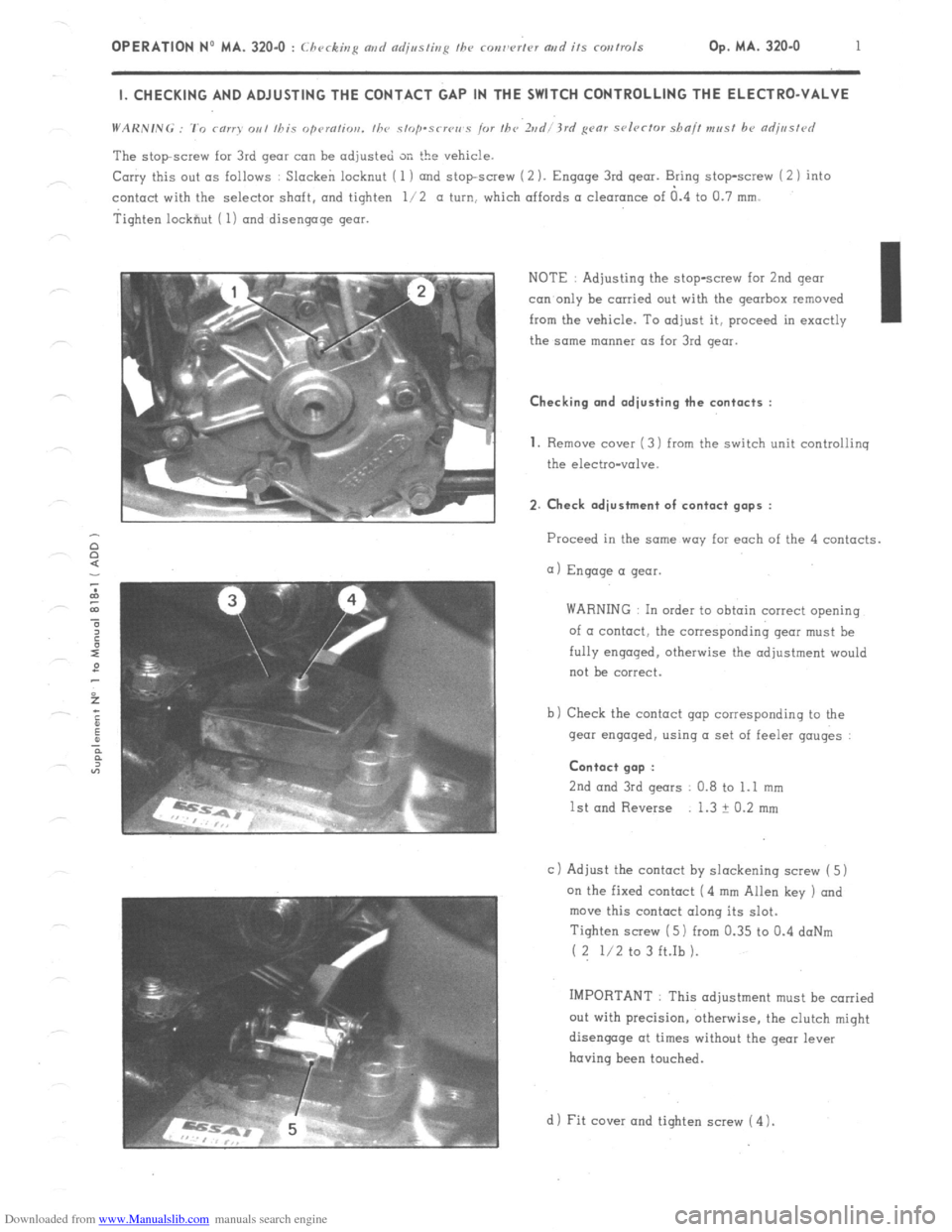
Downloaded from www.Manualslib.com manuals search engine OPERATION No MA. 320-O : Checking md czdjssting fhe ronw’rtcv artd its corrtrols Op. MA. 320.0 1 I. CHECKING AND ADJUSTING THE CONTACT GAP IN THE SWITCH CONTROLLING THE ELECTRO-VALVE
The stopscrew for 3rd gear can be adjusted SK the vehicle.
Carry this out as follows : Slacken locknut ( 1 ) and stopscrew (2 ). Engage 3rd gear. Bring stop-screw i 2 1 into
contact with the selector shaft. and tighten l/2 a turn, which affords a clearance of a.4 to Cl.7 mm.
Tighten lockfiut ( 1) and disengage gear.
NOTE : Adjusting the stop-screw for 2nd gear
con only be carried out with the gearbox removed
from the vehicle. To adjust it, proceed in exactly I
the same manner as for 3rd gear. Checking and adjusting the contacts :
1.
Remove cover ( 3) from the switch unit controliinq
the electro-valve. 2. Check adjustment of contact gaps :
Proceed in the same way far each of the 4 contacts.
a) Engage a gear.
WARNING In order to obtain correct opening
of a contact, the corresponding gear must be
fully engaged. otherwise the adjustment would
not be correct.
b) Check the contact gap corresponding to the
gear engaged, using a set of feeler gauges : Contact gap :
2nd
and 3rd gears 0.8 to 1.1 mm
1st and Reverse 1.3 ? 0.2 mm
c 1 Adjust the contact by slackening screw ( 5)
on the fixed contact (4 mm Allen key ) and
move this contact along its slot.
Tighten screw ( 5) from 0.35 to 0.4 doNm
( 2 l/2 to 3 ft.Ib ).
IMPORTANT : This adjustment must be carried
out with precision, otherwise, the clutch might
disengage at times without the gear lever
having been touched.
d 1 Fit cover and tighten screw ( 4 1.
Page 201 of 394
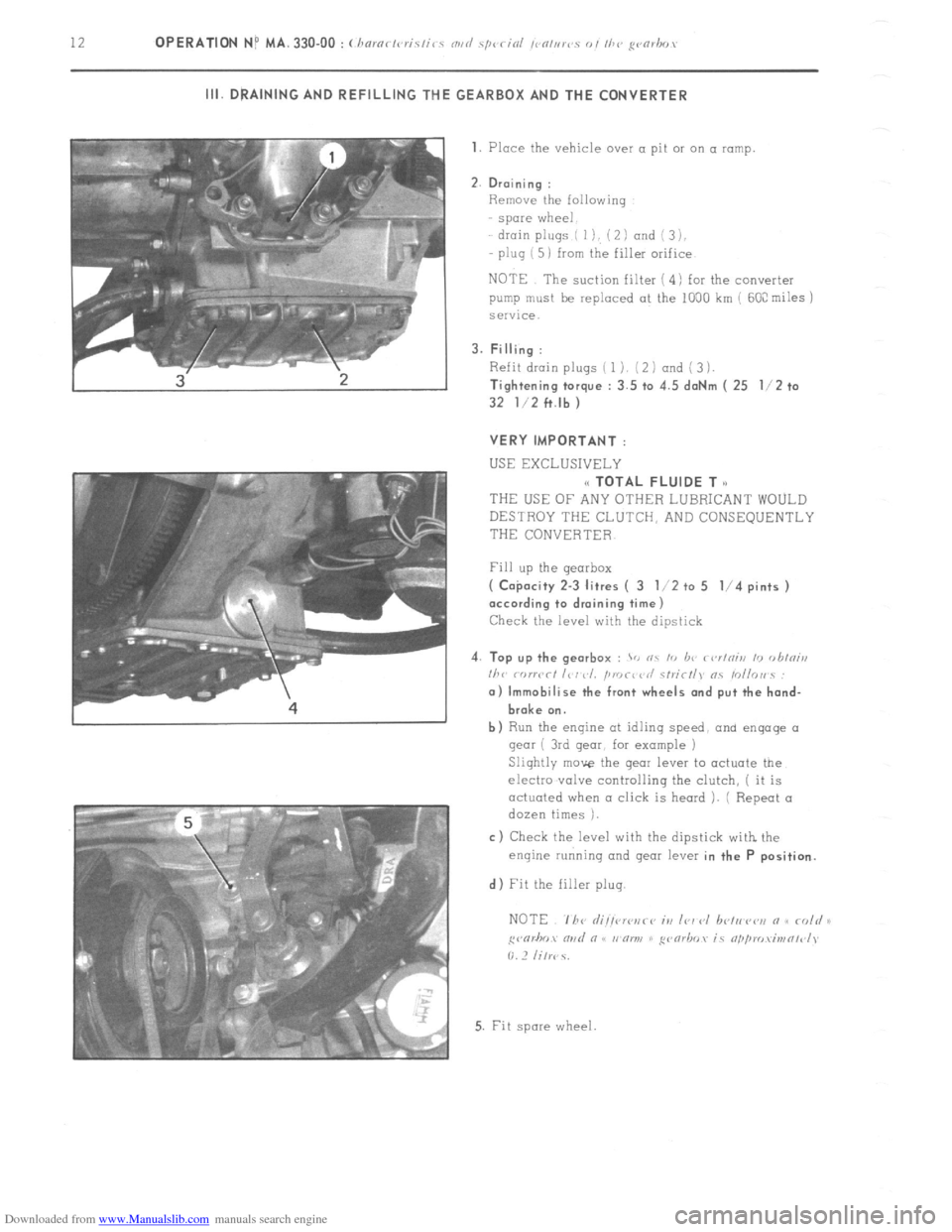
Downloaded from www.Manualslib.com manuals search engine 12 OPERATION NP MA. 330.00 : (haro? gvmhr,, III. DRAINING AND REFILLING THE GEARBOX AND THE CONVERTER
1. Place the vehicle over a pit 01 on a ramp
2. Draining :
Remove the following
spare wheel
drain plugs ( I), ( 2 I and i 3 ),
plug ( 5) from the filler orifice
NOTE The suction filter ( 4) for the converter
pump must be replaced at the 1000 km ( 60C miles j
service.
3. Filling :
Refit drain plugs ( 1). (2 1 and ( 3 1.
Tightening torque : 3.5 to 4.5 daNm ( 25 l/2 to
32 l/2 ft.lb )
VERY IMPORTANT :
USE EXCLUSIVELY
(< TOTAL FLUIDE T o
THEUSEOFANYOTHERLUBRICANTWOULD
DESTROY THE CLUTCH, AND CONSEQUENTLY
THE CONVERTER
Fill up the gearbox
( Co$acity 2-3 litres ( 3 l/2 to 5 l/4 pints )
according to draining time)
Check the level with the dipstick
4. Top up the gearbox :
> nc I<, b<’ r<,r/niii 10 <,hini,,
I/><,
broke on.
b) Run the engine at idlinq speed, and engage 01
gear ( 3rd gear, for example )
Slightly move the gear lever to actuate the
electro .valve controlling the clutch, ( it is
actuated when a click is heard ). ( Repeat a
dozen times ).
c) Check the level with the dipstick with the
enqine running and gear lever in the P position.
d) Fit the filler plug.
5. Fit spore wheel
Page 214 of 394
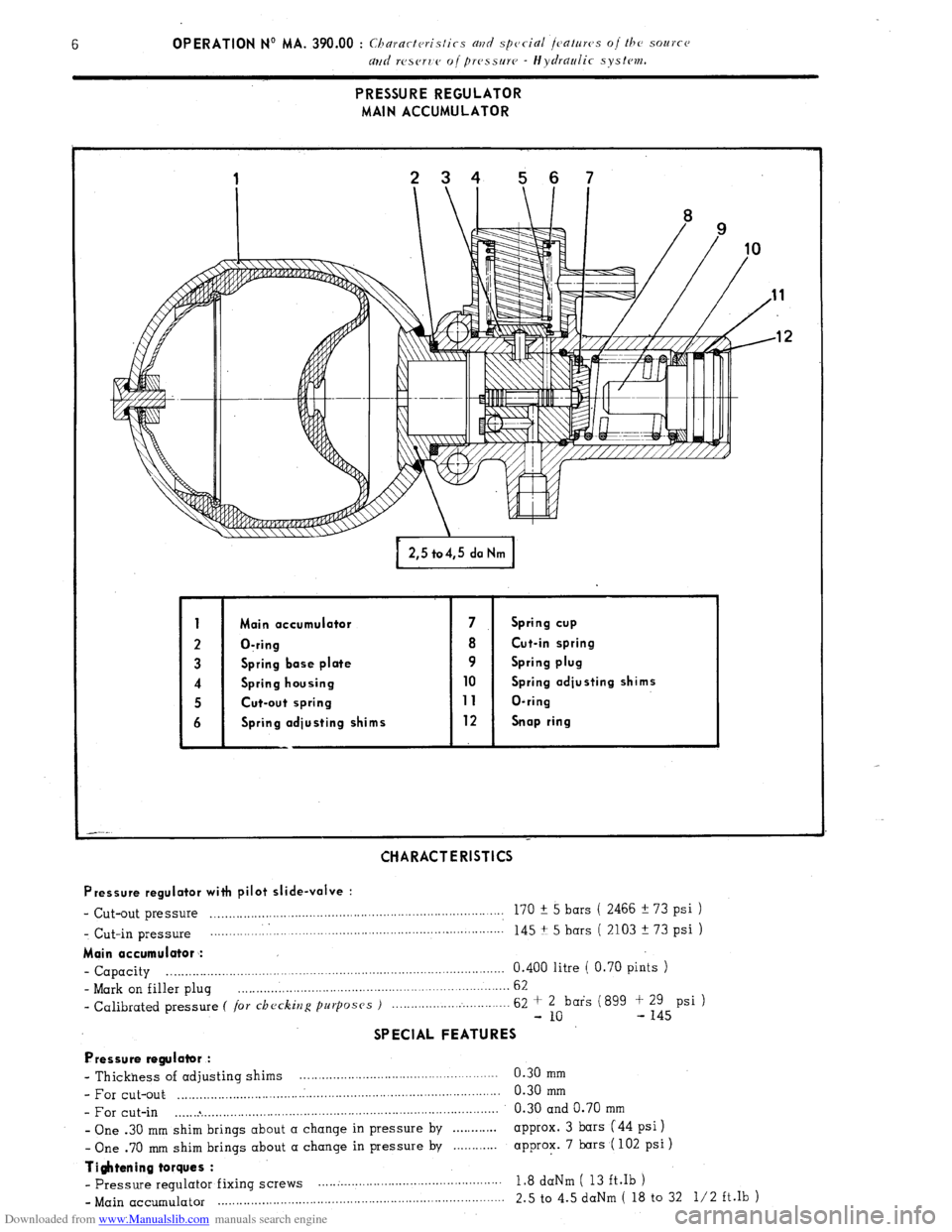
Downloaded from www.Manualslib.com manuals search engine 6 OPERATION No MA, 390.00 : C1 ,ararteristics
ad special fratuws oj the source
apfd rescr7,e o/ pressur(~ - Hydraulic system.
PRESSURE REGULATOR
MAIN ACCUMULATOR
Main occumulotor 7 Spring cup
O-ring 8 Cut-in spring
Spring base plate 9 Spring plug
Spring housing 10 Spring adjusting shims
Cut-out spring 11 O-ring
Spring odjusting shims 12 Snap ring
CHARACTERISTICS
Pressure regulator with pilot slide-valve :
- Cut-out pressure . .._......,_....____.............,.,......................................... 170 f 5 bars ( 2466 !I 73 psi ) _ Cut-in pressure __.....___.__.,..,.....,..,................,,...................................
145 + 5 bars ( 2103 + 73 psi )
Main accumulator :
- Capacity . . . . 0.400 litre ( 0.70 pints )
- Mark on filler plug . . , 62
- Calibrated pressure C /or checking purposes ) 62 + 2 bars (899 f 29 psi )
- 10 - 145
SPECIAL FEATURES
Pressure regulator :
- Thickness of adjusting shims . 0.30 mm
- For cut-out ..I.._......._..... .._. ,. .._. .:.. ,. ,. ..__.. ,. ..__ ,. ,. ._ ._.. .___ 0.30
mm
- For cut-in .._.... * .__....._._.,.,.,._.,....................................... 0.30 and 0.70 mm
- One .30 mm shim brings about a change in pressure by . . . . . . . . . . , approx. 3 bars (44 psi 1
- One .70 mm shim brings about a change in pressure by . . . . . . . . . approx. 7 bars ( 102 psi )
Ti$ttening torques :
- pressure regulator fixing Screws . . . . .._.__.....__._............................... 1.8 daNm ( 13 ft.Ib )
- Main accumulator ..,.. ,. . . ,. __ . . . . .._. ., ,__. ._ __ 2.5 to 4.5 daNm ( 18 to 32 l/2 ft.lb )
Page 217 of 394
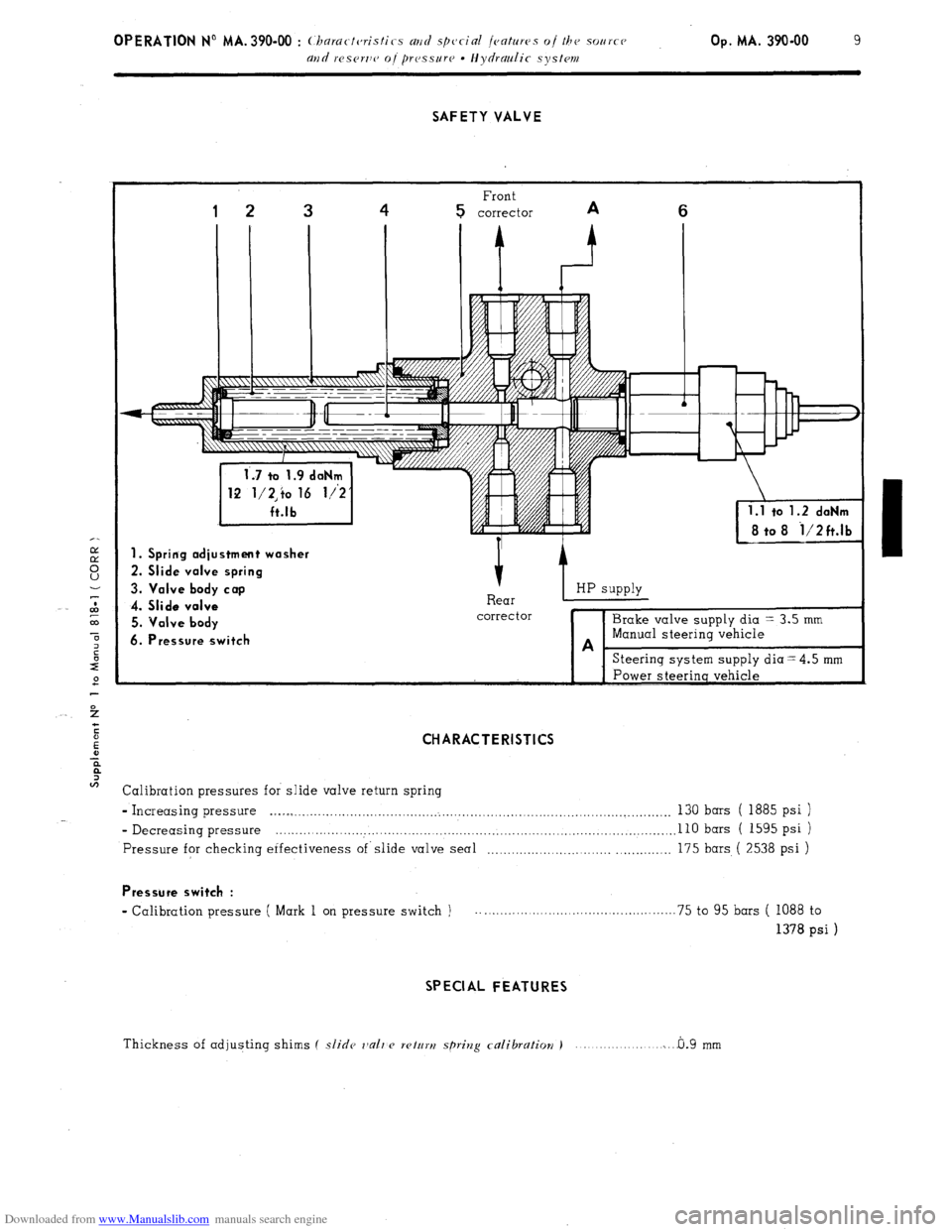
Downloaded from www.Manualslib.com manuals search engine Op. MA. 390.00 9
SAFETY VALVE
Front
1 2 3 4 5 corrector A 6
i 8 to 8 i/2ft.lb
1. Spring adjustment washer
2. Slide valve spring
3. Valve body cap
4. Slide valve
5. Valve body
6. Pressure switch 1 HP SWP~Y I-
corrector
Steering system supply diaz4.5 mm
CHARACTERISTICS
Calibration pressures for slide valve return spring
- Increasing pressure .l~lOs _._..........__...._,..__._....,..__..__.__.,...___........._...._...,__..._.._.,,.._.,...,.... 130 bars ( 1885 psi )
- Decreasing pressure . . . . . . . . . .._.. I ~...~~~....~.~.....~.~.~.~.~.~~~.~.~....~.~~~~.....~~~..~..~....~~.~~...~.~.. 110 bars ( 1595 psi )
Pressure for checking erfectiveness of’slide valve seal .,_._._.,__._._...,._._.,....__ _,..,..,_.___. 175 bars ( 2538 psi )
Pressure switch :
- Calibration pressure ( Mark 1 on pressure switch ) .._.............._.............._............. 75 to 95 bars ( 1088 to
1378 psi )
SPECIAL FEATURES
Thickness of adjusting shims ( slide rlalrzc wturtj spriv2g calibration i 0.9 mm ...._.__..._....,..._.i___
Page 227 of 394
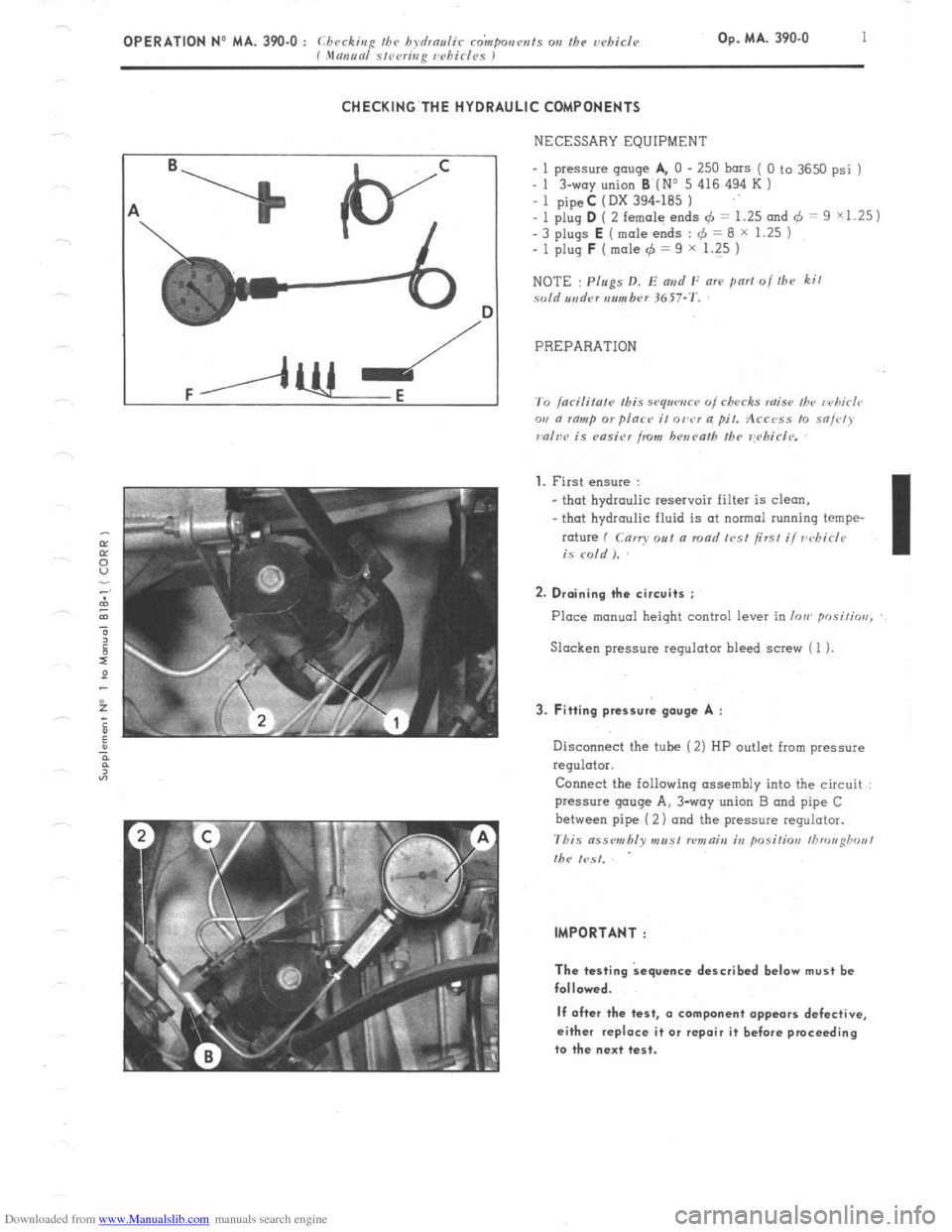
Downloaded from www.Manualslib.com manuals search engine OPERATION No MA. 390-O : ChrckinR thr bydraalir co’mponcnts on the u&i& f Manual stcprine r~ebidos t Op. MA. 390.0 1
CHECKING’THE HYDRAULIC COMPONENTS
NECESSARY EQUIPMENT
- 1 pressure gauge A,
0 - 250 bars ( 0 to 3650 psi )
_ 1 3-way union B (No 5 416 494 K 1
- 1 pipeC (DX 394-185 ) ..
- 1 plug D ( 2 female ends 4 1.25 and 6 9 X1.25) = =
- 3 plugs E (mole ends : r$ 8 X 1.25 ) =
- 1 plug F (
mole 4 = 9 x 1.25 1
NOTE
: Plugs D, E md F are part 01 fhe kit
sold snder number 3657-T.
PREPARATION 1.
First ensure :
- that hydraulic reservoir filter is clean.
- that hydraulic fluid is ot normal running tempe-
rature ( Carry 0~1 a road lent first i/ vt4icie
is
mid ). 8 2. Draining the circuits :
Place manual height control lever in ion, posirios,
Slacken pressure regulator bleed screw ( 1 ). 3. Fitting pressure gouge A :
Disconnect the tube (2) HP outlet from pressure
regulator.
Connect the following assembly into the circuit :
pressure gaoge A, 3way union B and pipe C
between pipe ( 2) and the pressure regulator.
This ass~nzhly mrtst remain in positioa /brougbo~~l
the test. IMPORTANT :
The testing kquance described below must be
followed.
If after the test, a component appears defective,
either replace it or repair it before proceeding
to the next test.
Page 228 of 394
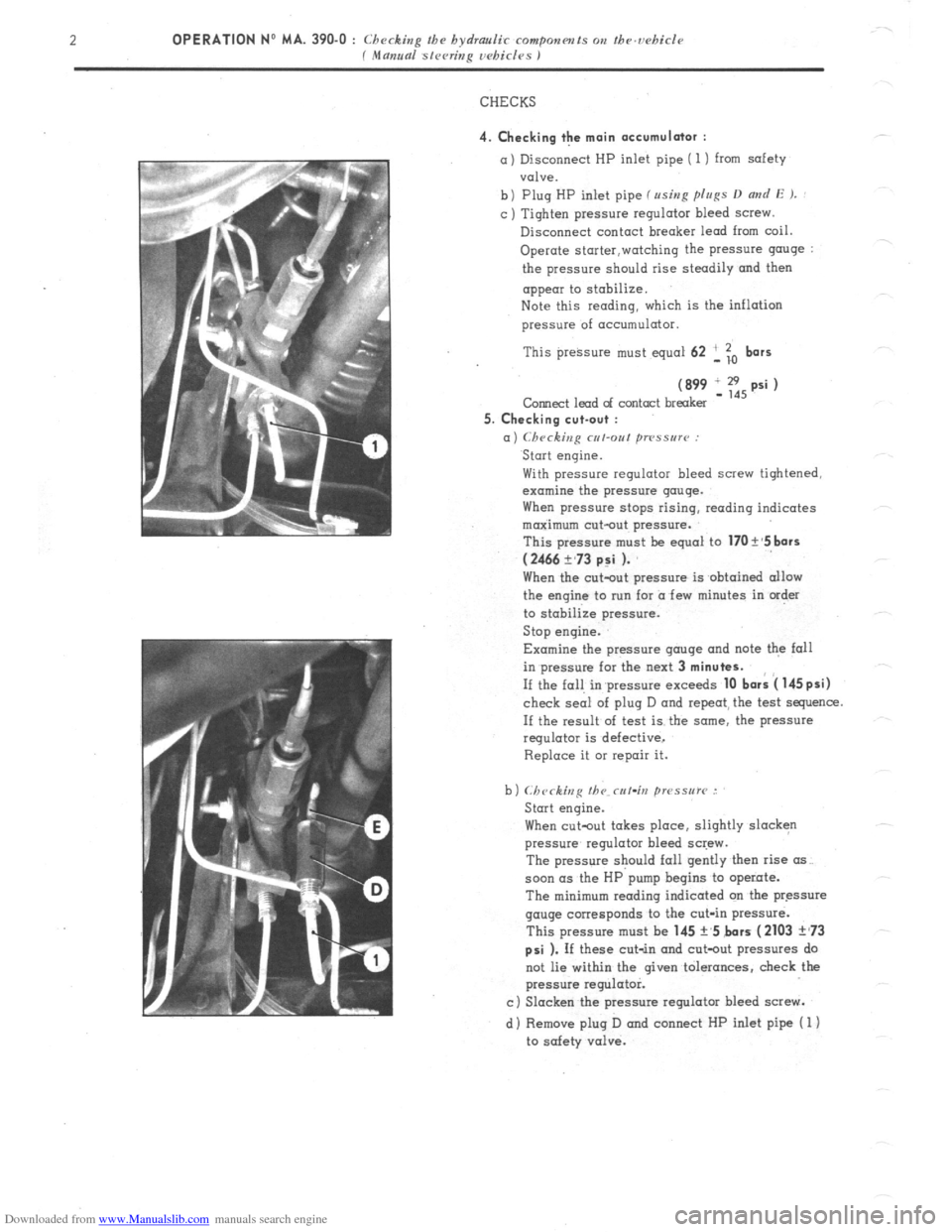
Downloaded from www.Manualslib.com manuals search engine 2 OPERATION No MA. 390-O : Checking the hydra&c conponmts on the.uehicle
f Mnnual sirrrin~ uehicles J CHECKS
4. Checking the main accumulator : a) Disconnect HP inlet pipe ( 1) from safety
valve.
b) Plug HP inlet pipe fusing p[u~s D
and E ). : c ) Tighten pressure regulator bleed screw.
Disconnect contact breaker lead from coil.
Operate storter,watching the pressure g”“ge :
the pressure should rise steadily and then
appear to stobilize.
Note this reading, which is the inflation
pressure of acc”mulator.
This preksure must equal 62 ‘, To
bars
(899 IE,psi) Corned lead of contact breaker
5. Checking cut-out :
a) Checking cut-out ~TPSSU~~~ : Start engine.
With pressure regulator bleed screw tightened,
examine the pressure gauge.
When pressure stops rising, reading indicates
maximum cut-out pressure.
This pressure m”st be equal to
170 t’5 bars
(2466 ?,73 p:i ). When the c”t-o”t pressure is obtained allow
the engine to nrn for a few minutes in order
to stabilize pressure.
Stop engine.
Examine the pressure gauge and note the fall
in pressure for the next 3
minutes. If the fall in’pressure exceeds
10 bark 4 145psi) check seai of plug D and repeat, the test sequence.
If the result of test is the some, the pressure
regulator is defective,
Replace it 01 repair it.
When cutout takes place, slightly slacken
pressure regulator bleed screw.
The pressure should fall gently then rise (IS~.
soon (IS the HP pump begins to operate.
The minimum reading indicated on tbe pressure
gauge corresponds to the cut-in pressure.
This pressure must be 145 +,5 bars
(2103 ?,73
psi ). If these cut-in and cot-out pressures do
not lie within the given tolerances, check the
pressure regulator.
c) Slacken the pressure regulator bleed screw.
d) Remove plug D and connect HP inlet pipe ( 1)
to safety valve.