DAEWOO LACETTI 2004 Service Repair Manual
Manufacturer: DAEWOO, Model Year: 2004, Model line: LACETTI, Model: DAEWOO LACETTI 2004Pages: 2643, PDF Size: 80.54 MB
Page 111 of 2643
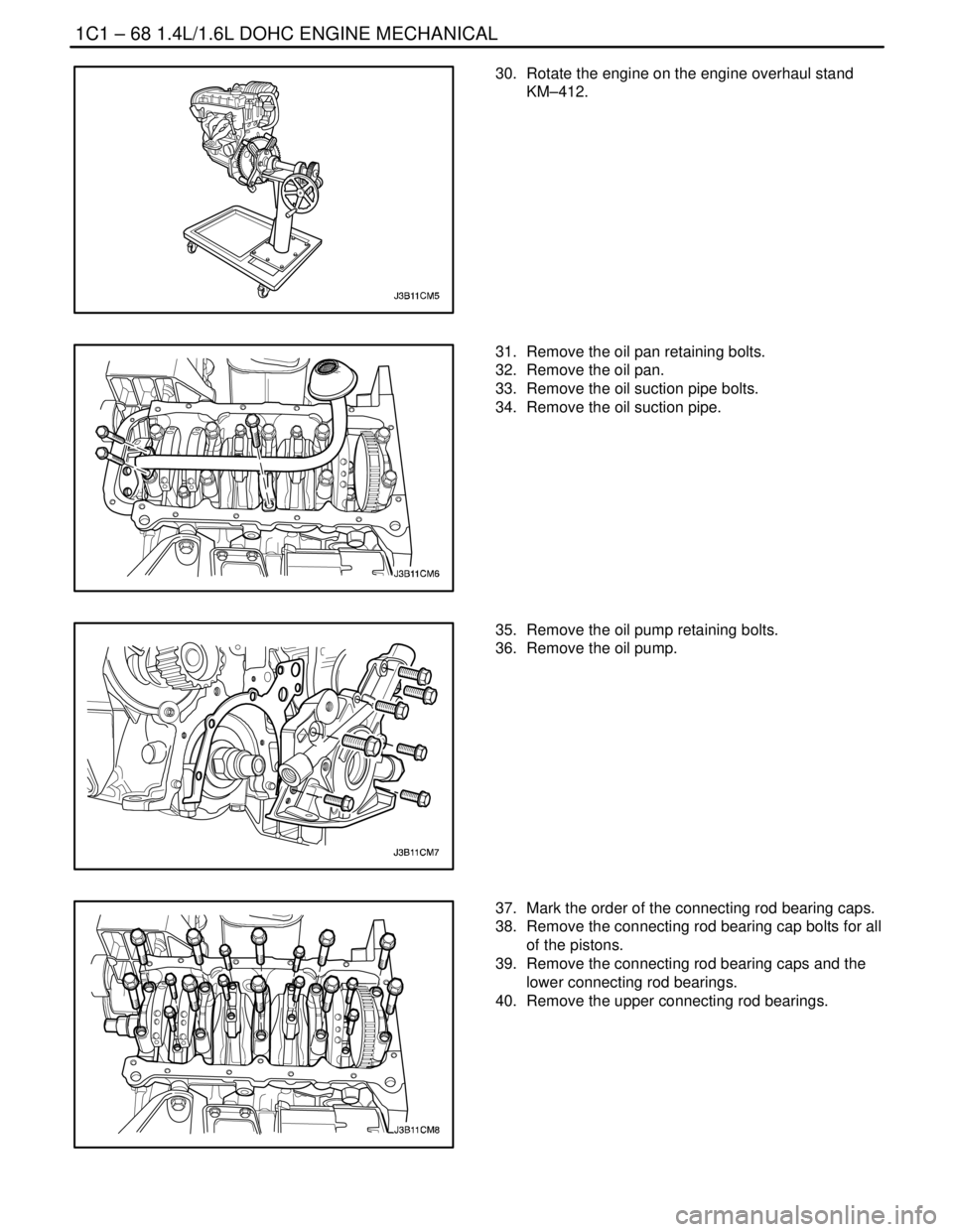
1C1 – 68I1.4L/1.6L DOHC ENGINE MECHANICAL
DAEWOO V–121 BL4
30. Rotate the engine on the engine overhaul stand
KM–412.
31. Remove the oil pan retaining bolts.
32. Remove the oil pan.
33. Remove the oil suction pipe bolts.
34. Remove the oil suction pipe.
35. Remove the oil pump retaining bolts.
36. Remove the oil pump.
37. Mark the order of the connecting rod bearing caps.
38. Remove the connecting rod bearing cap bolts for all
of the pistons.
39. Remove the connecting rod bearing caps and the
lower connecting rod bearings.
40. Remove the upper connecting rod bearings.
Page 112 of 2643
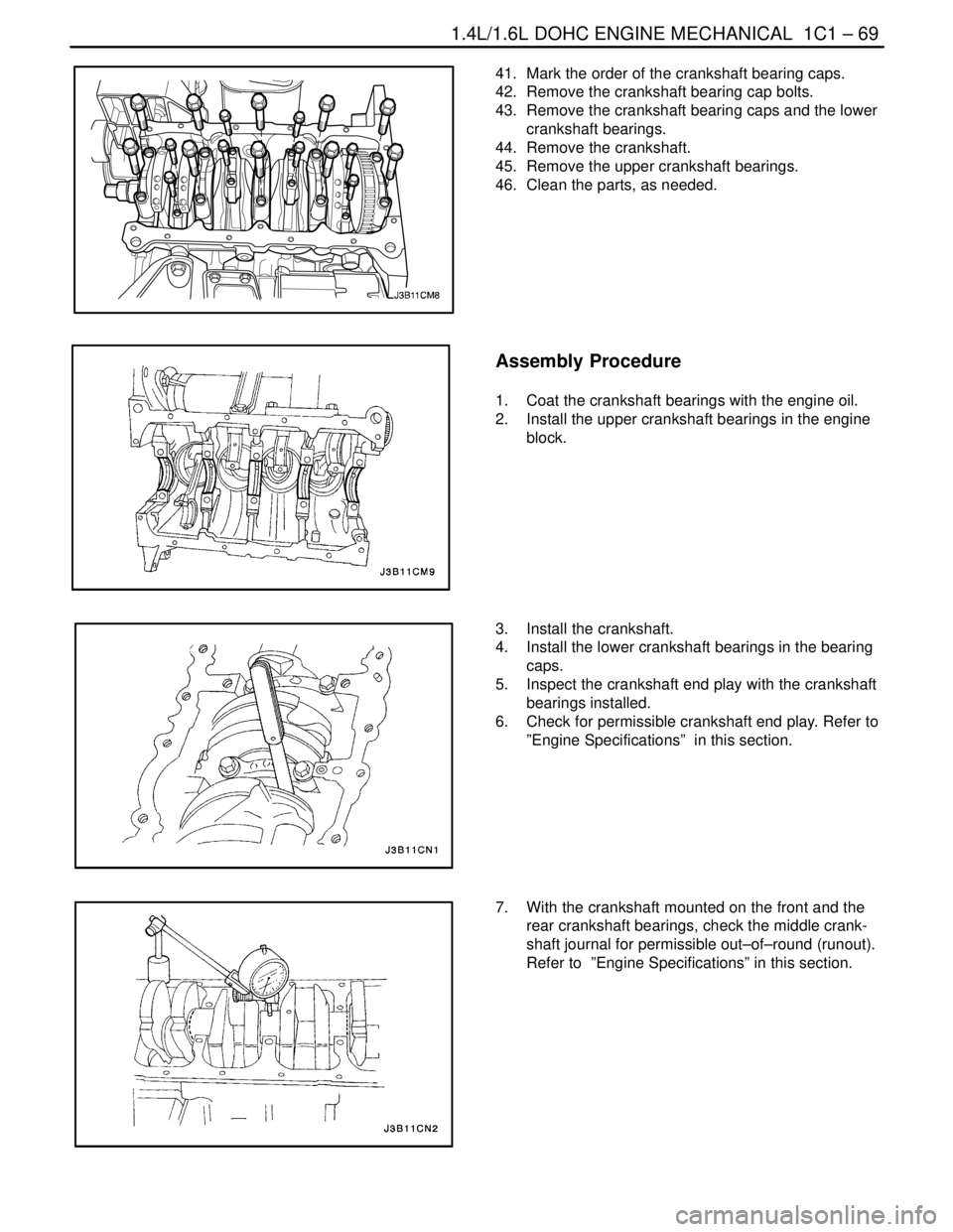
1.4L/1.6L DOHC ENGINE MECHANICAL 1C1 – 69
DAEWOO V–121 BL4
41. Mark the order of the crankshaft bearing caps.
42. Remove the crankshaft bearing cap bolts.
43. Remove the crankshaft bearing caps and the lower
crankshaft bearings.
44. Remove the crankshaft.
45. Remove the upper crankshaft bearings.
46. Clean the parts, as needed.
Assembly Procedure
1. Coat the crankshaft bearings with the engine oil.
2. Install the upper crankshaft bearings in the engine
block.
3. Install the crankshaft.
4. Install the lower crankshaft bearings in the bearing
caps.
5. Inspect the crankshaft end play with the crankshaft
bearings installed.
6. Check for permissible crankshaft end play. Refer to
”Engine Specifications” in this section.
7. With the crankshaft mounted on the front and the
rear crankshaft bearings, check the middle crank-
shaft journal for permissible out–of–round (runout).
Refer to ”Engine Specifications” in this section.
Page 113 of 2643

1C1 – 70I1.4L/1.6L DOHC ENGINE MECHANICAL
DAEWOO V–121 BL4
Important : Grease the crankshaft journals and lubri–cate
the crankshaft bearings slightly so that the plastic gauging
thread does not tear when the crankshaft bearing caps are
removed.
8. Inspect all of the crankshaft bearing clearances us-
ing a commercially available plastic gauging (ductile
plastic threads).
9. Cut the plastic gauging threads to the length of the
bearing width. Lay them axially between the crank-
shaft journals and the crankshaft bearings.
10. Install the crankshaft bearing caps and the bolts.
Tighten
Tighten the crankshaft bearing cap bolts to 50 NSm
(37 lb–ft) plus 45 degrees plus 15 degrees.
11. Remove the crankshaft bearing cap bolts and the
caps.
12. Measure the width of the flattened plastic thread of
the plastic gauging using a ruler. (Plastic gauging is
available for different tolerance ranges.)
13. Inspect the bearing clearance for permissible toler-
ance ranges. Refer to ”Engine Specifications” in
this section.
14. Apply a bead of adhesive sealing compound to the
grooves of the crankshaft bearing caps.
15. Install the crankshaft bearing caps to the engine
block.
16. Tighten the crankshaft bearing caps using new
bolts.
Tighten
Tighten the crankshaft bearing cap bolts to 50 NSm
(37 lb–ft) using a torque wrench. Use the angular
torque gauge KM–470–B to tighten the crankshaft
bearings 45 degrees plus 15 degrees.
Important : Grease the connecting rod journals and lubri-
cate the connecting rod bearings slightly so that the plastic
gauging thread does not tear when the connecting rod
bearing caps are removed.
17. Inspect all of the connecting rod bearing clearances
using a commercially available plastic gauging
(ductile plastic threads).
18. Cut the plastic gauging threads to the length of the
connecting rod bearing width. Lay them axially be-
tween the connecting rod journals and the connect-
ing rod bearings.
19. Install the connecting rod bearing caps.
Page 114 of 2643
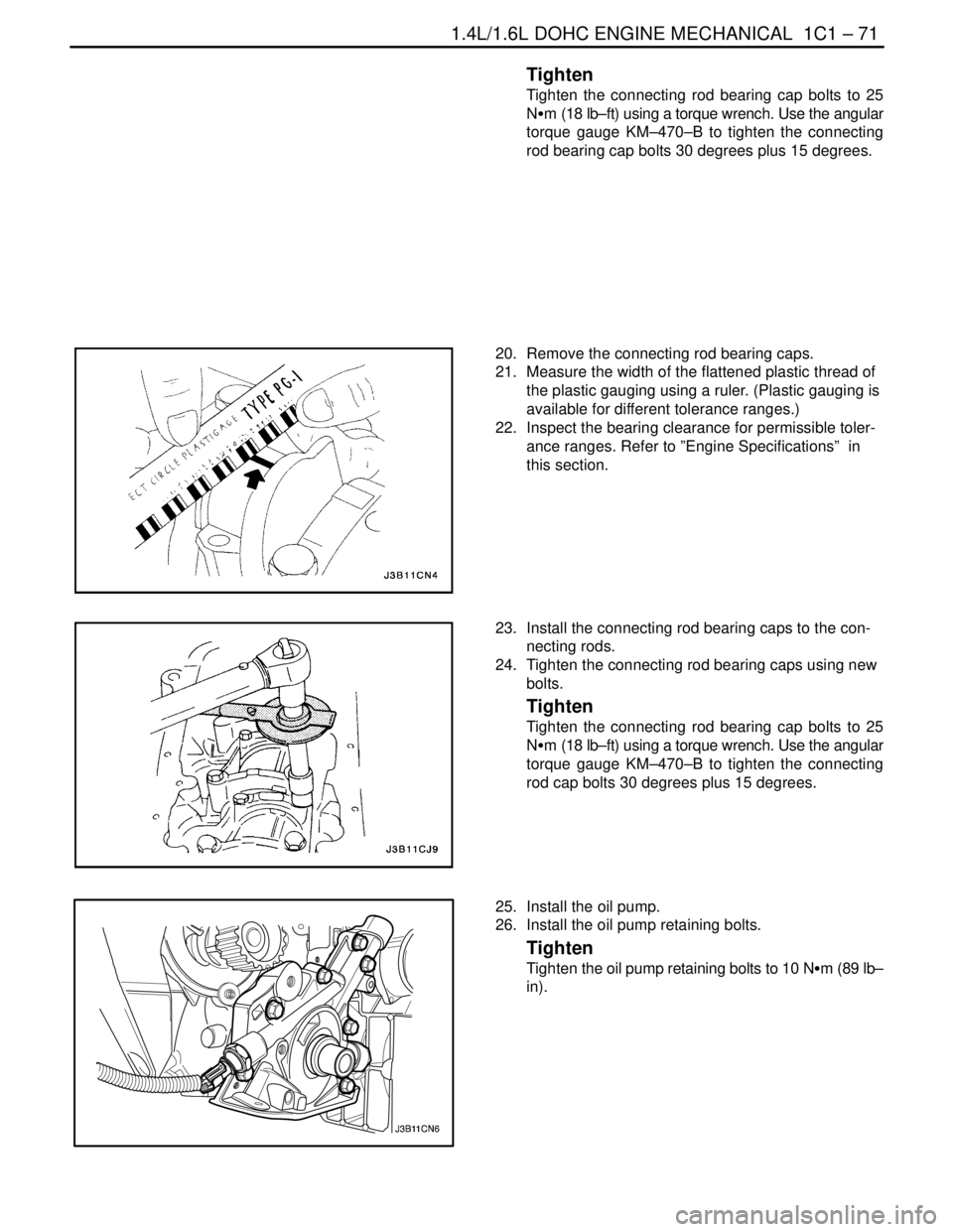
1.4L/1.6L DOHC ENGINE MECHANICAL 1C1 – 71
DAEWOO V–121 BL4
Tighten
Tighten the connecting rod bearing cap bolts to 25
NSm (18 lb–ft) using a torque wrench. Use the angular
torque gauge KM–470–B to tighten the connecting
rod bearing cap bolts 30 degrees plus 15 degrees.
20. Remove the connecting rod bearing caps.
21. Measure the width of the flattened plastic thread of
the plastic gauging using a ruler. (Plastic gauging is
available for different tolerance ranges.)
22. Inspect the bearing clearance for permissible toler-
ance ranges. Refer to ”Engine Specifications” in
this section.
23. Install the connecting rod bearing caps to the con-
necting rods.
24. Tighten the connecting rod bearing caps using new
bolts.
Tighten
Tighten the connecting rod bearing cap bolts to 25
NSm (18 lb–ft) using a torque wrench. Use the angular
torque gauge KM–470–B to tighten the connecting
rod cap bolts 30 degrees plus 15 degrees.
25. Install the oil pump.
26. Install the oil pump retaining bolts.
Tighten
Tighten the oil pump retaining bolts to 10 NSm (89 lb–
in).
Page 115 of 2643
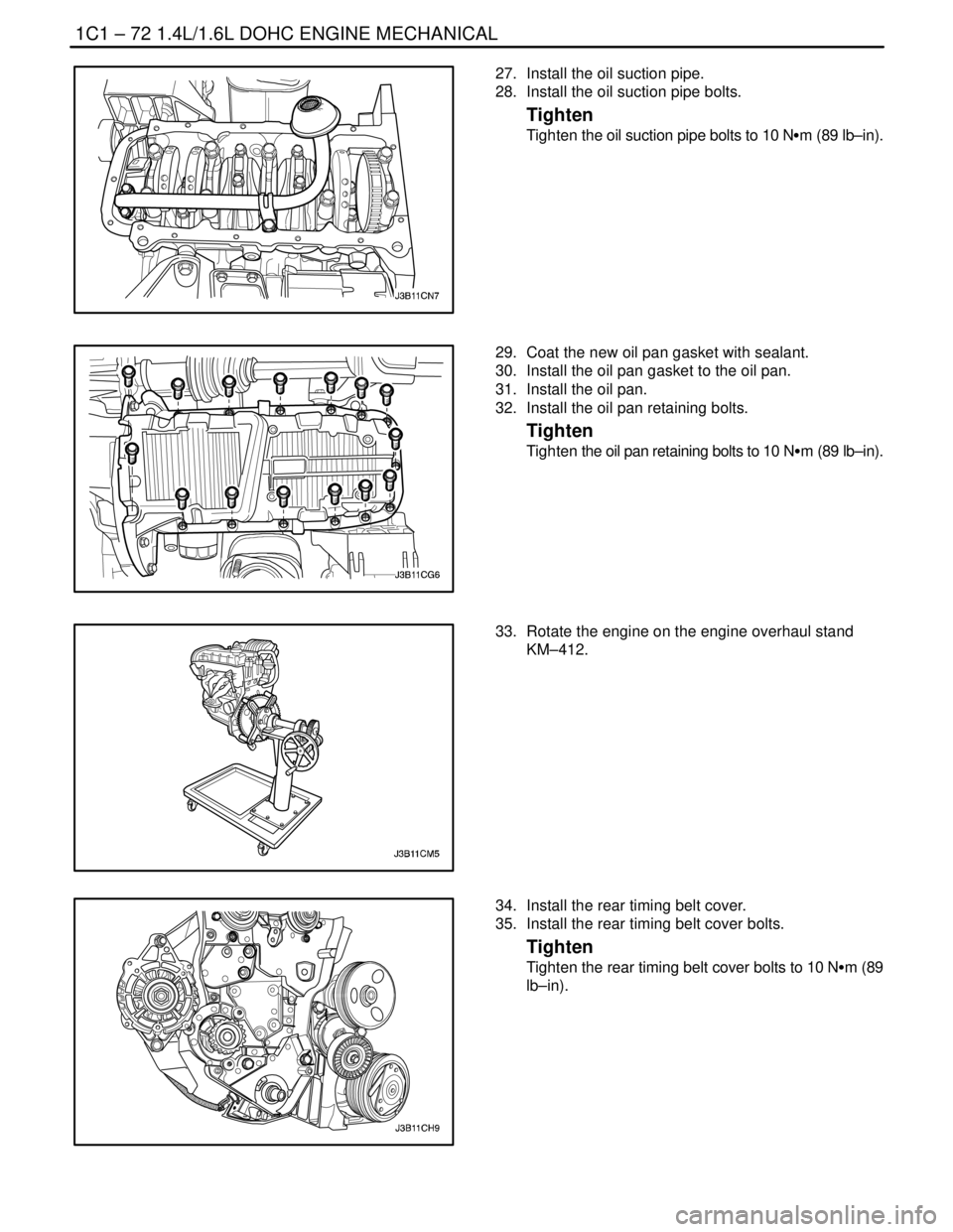
1C1 – 72I1.4L/1.6L DOHC ENGINE MECHANICAL
DAEWOO V–121 BL4
27. Install the oil suction pipe.
28. Install the oil suction pipe bolts.
Tighten
Tighten the oil suction pipe bolts to 10 NSm (89 lb–in).
29. Coat the new oil pan gasket with sealant.
30. Install the oil pan gasket to the oil pan.
31. Install the oil pan.
32. Install the oil pan retaining bolts.
Tighten
Tighten the oil pan retaining bolts to 10 NSm (89 lb–in).
33. Rotate the engine on the engine overhaul stand
KM–412.
34. Install the rear timing belt cover.
35. Install the rear timing belt cover bolts.
Tighten
Tighten the rear timing belt cover bolts to 10 NSm (89
lb–in).
Page 116 of 2643
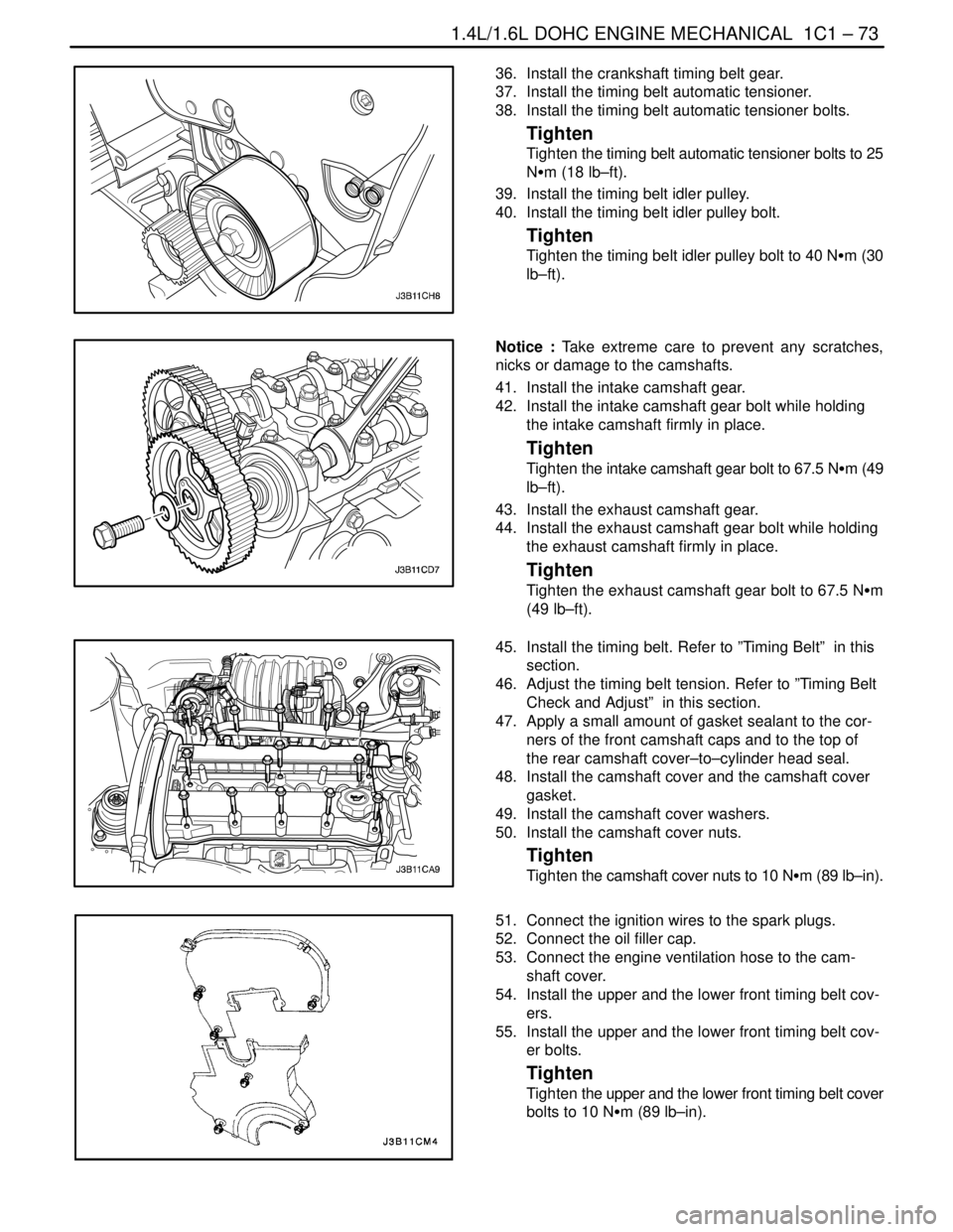
1.4L/1.6L DOHC ENGINE MECHANICAL 1C1 – 73
DAEWOO V–121 BL4
36. Install the crankshaft timing belt gear.
37. Install the timing belt automatic tensioner.
38. Install the timing belt automatic tensioner bolts.
Tighten
Tighten the timing belt automatic tensioner bolts to 25
NSm (18 lb–ft).
39. Install the timing belt idler pulley.
40. Install the timing belt idler pulley bolt.
Tighten
Tighten the timing belt idler pulley bolt to 40 NSm (30
lb–ft).
Notice : Take extreme care to prevent any scratches,
nicks or damage to the camshafts.
41. Install the intake camshaft gear.
42. Install the intake camshaft gear bolt while holding
the intake camshaft firmly in place.
Tighten
Tighten the intake camshaft gear bolt to 67.5 NSm (49
lb–ft).
43. Install the exhaust camshaft gear.
44. Install the exhaust camshaft gear bolt while holding
the exhaust camshaft firmly in place.
Tighten
Tighten the exhaust camshaft gear bolt to 67.5 NSm
(49 lb–ft).
45. Install the timing belt. Refer to ”Timing Belt” in this
section.
46. Adjust the timing belt tension. Refer to ”Timing Belt
Check and Adjust” in this section.
47. Apply a small amount of gasket sealant to the cor-
ners of the front camshaft caps and to the top of
the rear camshaft cover–to–cylinder head seal.
48. Install the camshaft cover and the camshaft cover
gasket.
49. Install the camshaft cover washers.
50. Install the camshaft cover nuts.
Tighten
Tighten the camshaft cover nuts to 10 NSm (89 lb–in).
51. Connect the ignition wires to the spark plugs.
52. Connect the oil filler cap.
53. Connect the engine ventilation hose to the cam-
shaft cover.
54. Install the upper and the lower front timing belt cov-
ers.
55. Install the upper and the lower front timing belt cov-
er bolts.
Tighten
Tighten the upper and the lower front timing belt cover
bolts to 10 NSm (89 lb–in).
Page 117 of 2643
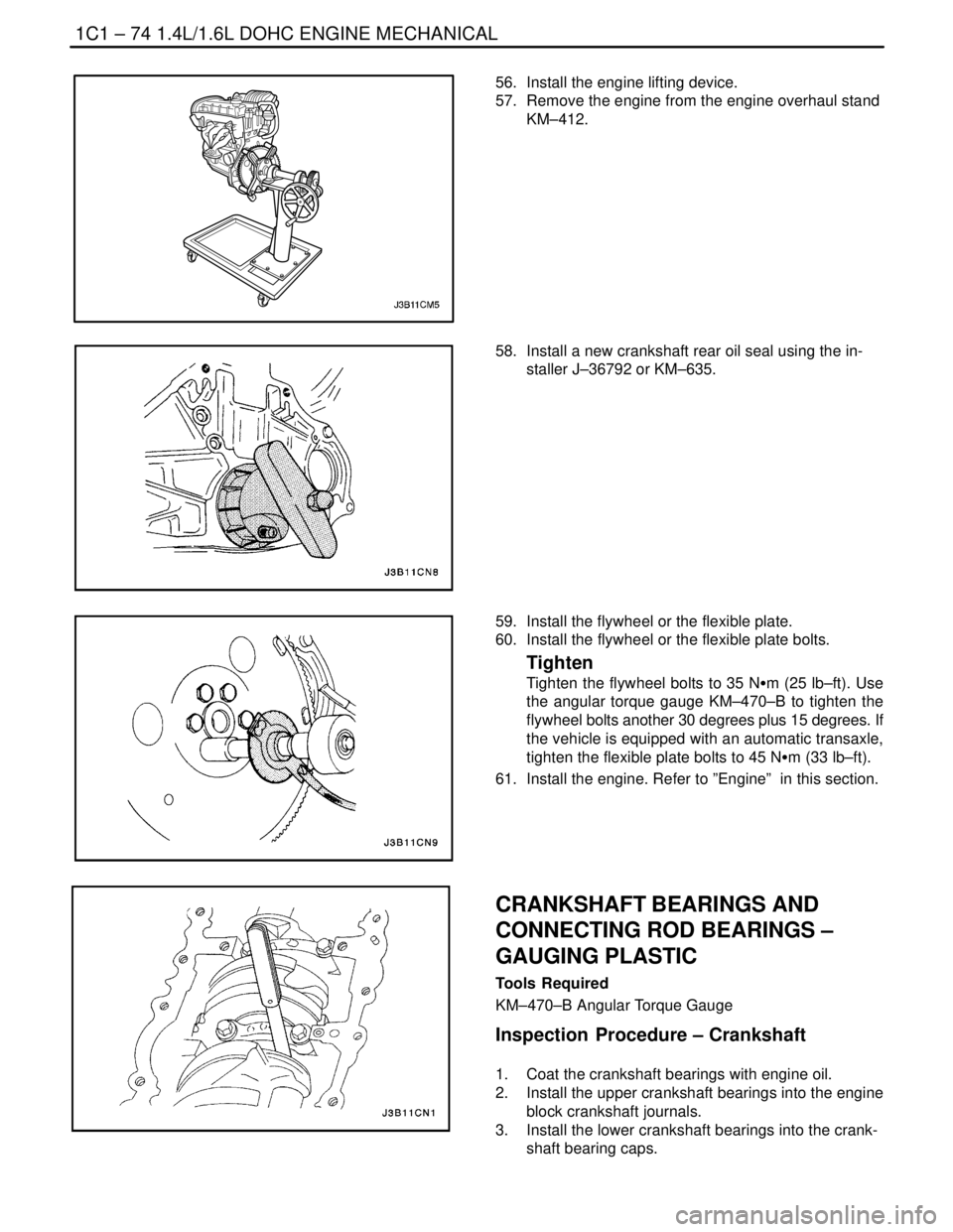
1C1 – 74I1.4L/1.6L DOHC ENGINE MECHANICAL
DAEWOO V–121 BL4
56. Install the engine lifting device.
57. Remove the engine from the engine overhaul stand
KM–412.
58. Install a new crankshaft rear oil seal using the in-
staller J–36792 or KM–635.
59. Install the flywheel or the flexible plate.
60. Install the flywheel or the flexible plate bolts.
Tighten
Tighten the flywheel bolts to 35 NSm (25 lb–ft). Use
the angular torque gauge KM–470–B to tighten the
flywheel bolts another 30 degrees plus 15 degrees. If
the vehicle is equipped with an automatic transaxle,
tighten the flexible plate bolts to 45 NSm (33 lb–ft).
61. Install the engine. Refer to ”Engine” in this section.
CRANKSHAFT BEARINGS AND
CONNECTING ROD BEARINGS –
GAUGING PLASTIC
Tools Required
KM–470–B Angular Torque Gauge
Inspection Procedure – Crankshaft
1. Coat the crankshaft bearings with engine oil.
2. Install the upper crankshaft bearings into the engine
block crankshaft journals.
3. Install the lower crankshaft bearings into the crank-
shaft bearing caps.
Page 118 of 2643
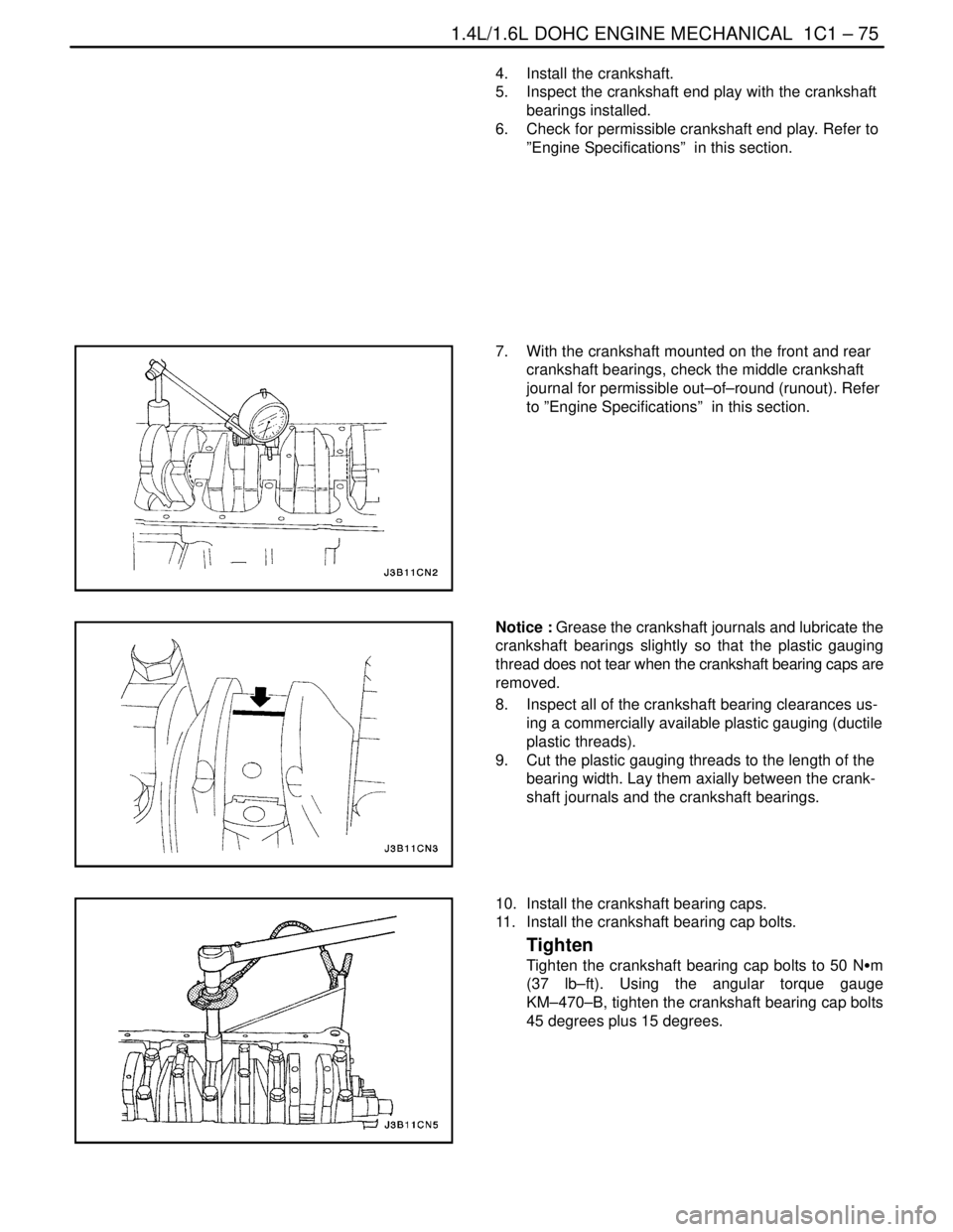
1.4L/1.6L DOHC ENGINE MECHANICAL 1C1 – 75
DAEWOO V–121 BL4
4. Install the crankshaft.
5. Inspect the crankshaft end play with the crankshaft
bearings installed.
6. Check for permissible crankshaft end play. Refer to
”Engine Specifications” in this section.
7. With the crankshaft mounted on the front and rear
crankshaft bearings, check the middle crankshaft
journal for permissible out–of–round (runout). Refer
to ”Engine Specifications” in this section.
Notice : Grease the crankshaft journals and lubricate the
crankshaft bearings slightly so that the plastic gauging
thread does not tear when the crankshaft bearing caps are
removed.
8. Inspect all of the crankshaft bearing clearances us-
ing a commercially available plastic gauging (ductile
plastic threads).
9. Cut the plastic gauging threads to the length of the
bearing width. Lay them axially between the crank-
shaft journals and the crankshaft bearings.
10. Install the crankshaft bearing caps.
11. Install the crankshaft bearing cap bolts.
Tighten
Tighten the crankshaft bearing cap bolts to 50 NSm
(37 lb–ft). Using the angular torque gauge
KM–470–B, tighten the crankshaft bearing cap bolts
45 degrees plus 15 degrees.
Page 119 of 2643
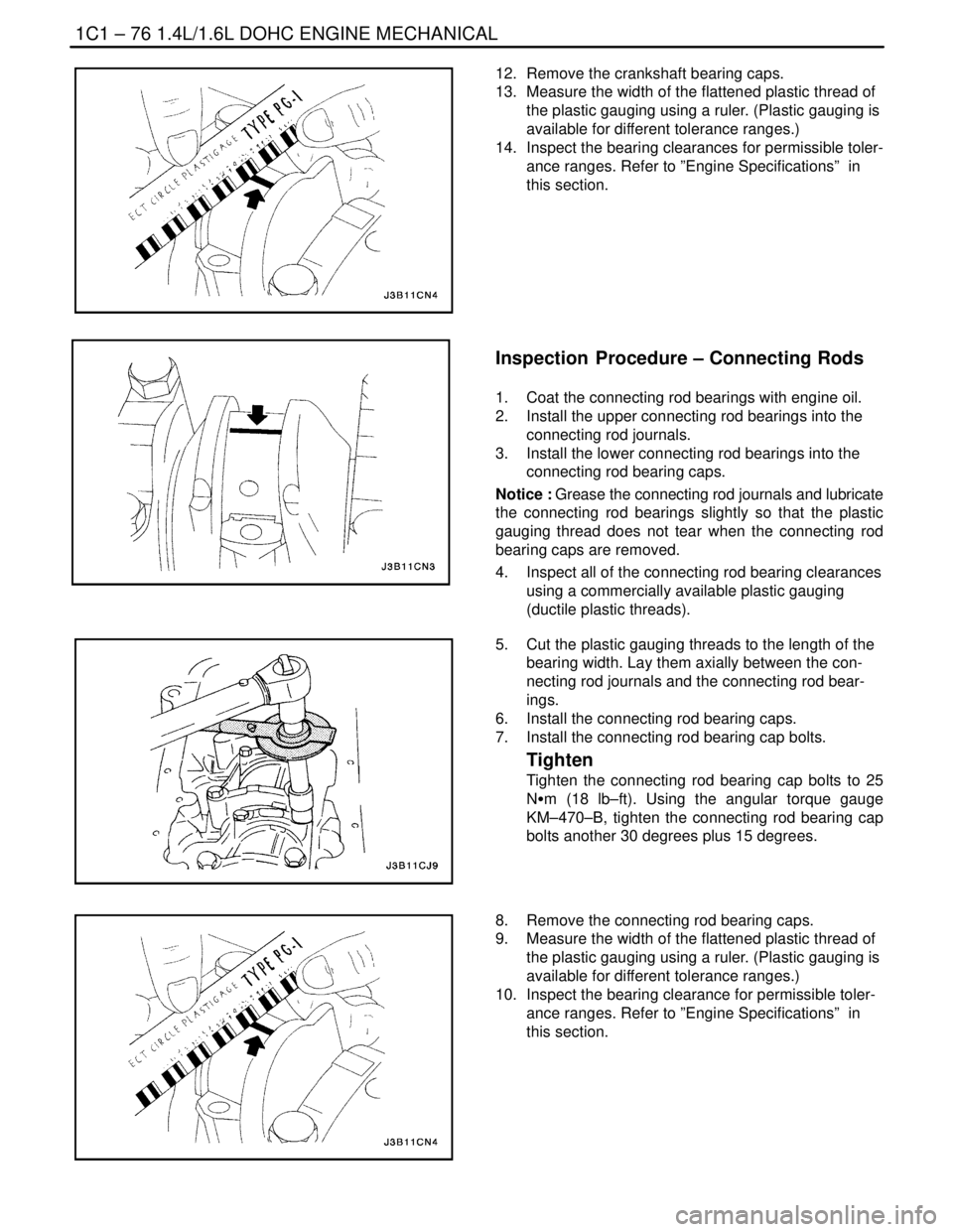
1C1 – 76I1.4L/1.6L DOHC ENGINE MECHANICAL
DAEWOO V–121 BL4
12. Remove the crankshaft bearing caps.
13. Measure the width of the flattened plastic thread of
the plastic gauging using a ruler. (Plastic gauging is
available for different tolerance ranges.)
14. Inspect the bearing clearances for permissible toler-
ance ranges. Refer to ”Engine Specifications” in
this section.
Inspection Procedure – Connecting Rods
1. Coat the connecting rod bearings with engine oil.
2. Install the upper connecting rod bearings into the
connecting rod journals.
3. Install the lower connecting rod bearings into the
connecting rod bearing caps.
Notice : Grease the connecting rod journals and lubricate
the connecting rod bearings slightly so that the plastic
gauging thread does not tear when the connecting rod
bearing caps are removed.
4. Inspect all of the connecting rod bearing clearances
using a commercially available plastic gauging
(ductile plastic threads).
5. Cut the plastic gauging threads to the length of the
bearing width. Lay them axially between the con-
necting rod journals and the connecting rod bear-
ings.
6. Install the connecting rod bearing caps.
7. Install the connecting rod bearing cap bolts.
Tighten
Tighten the connecting rod bearing cap bolts to 25
NSm (18 lb–ft). Using the angular torque gauge
KM–470–B, tighten the connecting rod bearing cap
bolts another 30 degrees plus 15 degrees.
8. Remove the connecting rod bearing caps.
9. Measure the width of the flattened plastic thread of
the plastic gauging using a ruler. (Plastic gauging is
available for different tolerance ranges.)
10. Inspect the bearing clearance for permissible toler-
ance ranges. Refer to ”Engine Specifications” in
this section.
Page 120 of 2643
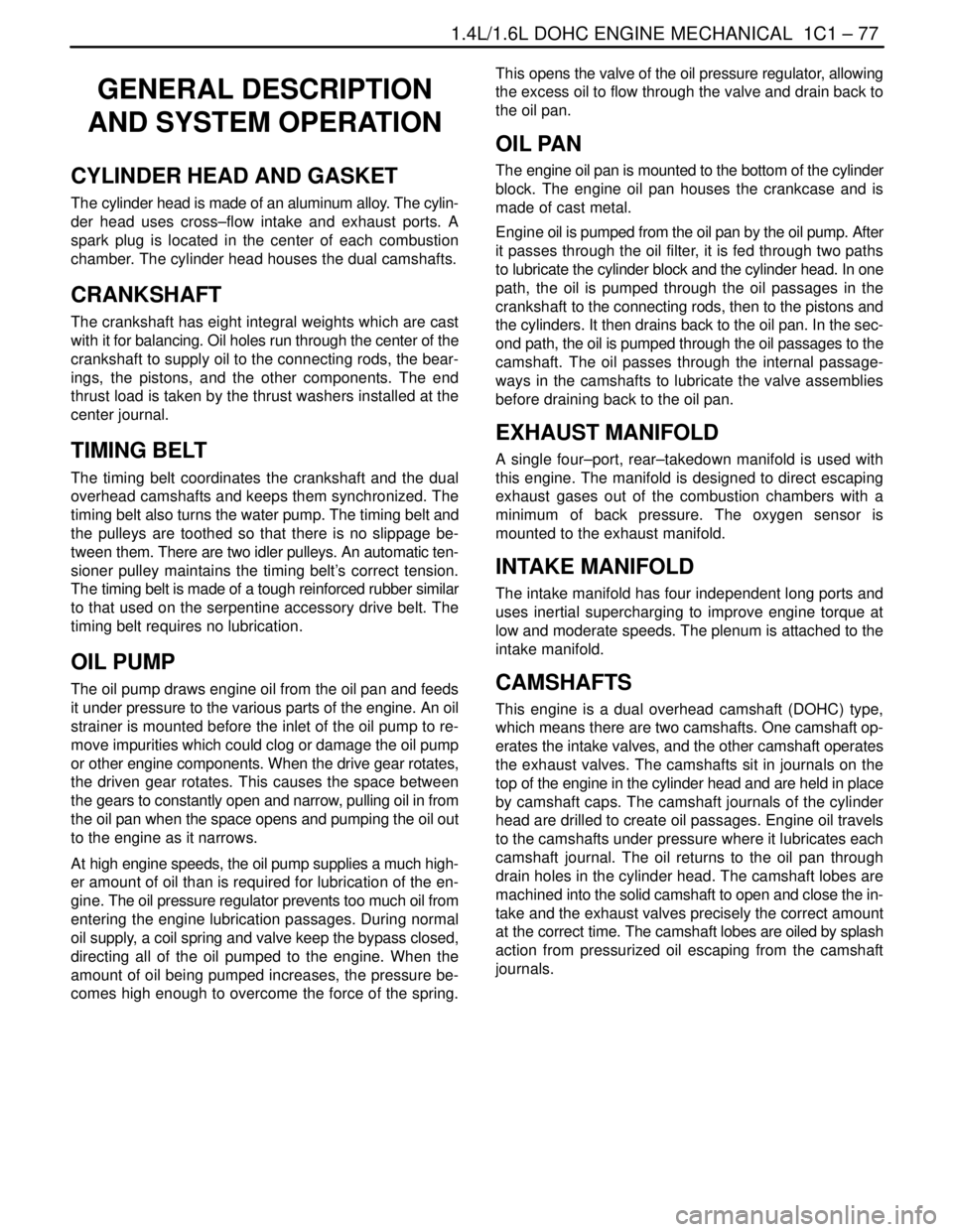
1.4L/1.6L DOHC ENGINE MECHANICAL 1C1 – 77
DAEWOO V–121 BL4
GENERAL DESCRIPTION
AND SYSTEM OPERATION
CYLINDER HEAD AND GASKET
The cylinder head is made of an aluminum alloy. The cylin-
der head uses cross–flow intake and exhaust ports. A
spark plug is located in the center of each combustion
chamber. The cylinder head houses the dual camshafts.
CRANKSHAFT
The crankshaft has eight integral weights which are cast
with it for balancing. Oil holes run through the center of the
crankshaft to supply oil to the connecting rods, the bear-
ings, the pistons, and the other components. The end
thrust load is taken by the thrust washers installed at the
center journal.
TIMING BELT
The timing belt coordinates the crankshaft and the dual
overhead camshafts and keeps them synchronized. The
timing belt also turns the water pump. The timing belt and
the pulleys are toothed so that there is no slippage be-
tween them. There are two idler pulleys. An automatic ten-
sioner pulley maintains the timing belt’s correct tension.
The timing belt is made of a tough reinforced rubber similar
to that used on the serpentine accessory drive belt. The
timing belt requires no lubrication.
OIL PUMP
The oil pump draws engine oil from the oil pan and feeds
it under pressure to the various parts of the engine. An oil
strainer is mounted before the inlet of the oil pump to re-
move impurities which could clog or damage the oil pump
or other engine components. When the drive gear rotates,
the driven gear rotates. This causes the space between
the gears to constantly open and narrow, pulling oil in from
the oil pan when the space opens and pumping the oil out
to the engine as it narrows.
At high engine speeds, the oil pump supplies a much high-
er amount of oil than is required for lubrication of the en-
gine. The oil pressure regulator prevents too much oil from
entering the engine lubrication passages. During normal
oil supply, a coil spring and valve keep the bypass closed,
directing all of the oil pumped to the engine. When the
amount of oil being pumped increases, the pressure be-
comes high enough to overcome the force of the spring.This opens the valve of the oil pressure regulator, allowing
the excess oil to flow through the valve and drain back to
the oil pan.
OIL PAN
The engine oil pan is mounted to the bottom of the cylinder
block. The engine oil pan houses the crankcase and is
made of cast metal.
Engine oil is pumped from the oil pan by the oil pump. After
it passes through the oil filter, it is fed through two paths
to lubricate the cylinder block and the cylinder head. In one
path, the oil is pumped through the oil passages in the
crankshaft to the connecting rods, then to the pistons and
the cylinders. It then drains back to the oil pan. In the sec-
ond path, the oil is pumped through the oil passages to the
camshaft. The oil passes through the internal passage-
ways in the camshafts to lubricate the valve assemblies
before draining back to the oil pan.
EXHAUST MANIFOLD
A single four–port, rear–takedown manifold is used with
this engine. The manifold is designed to direct escaping
exhaust gases out of the combustion chambers with a
minimum of back pressure. The oxygen sensor is
mounted to the exhaust manifold.
INTAKE MANIFOLD
The intake manifold has four independent long ports and
uses inertial supercharging to improve engine torque at
low and moderate speeds. The plenum is attached to the
intake manifold.
CAMSHAFTS
This engine is a dual overhead camshaft (DOHC) type,
which means there are two camshafts. One camshaft op-
erates the intake valves, and the other camshaft operates
the exhaust valves. The camshafts sit in journals on the
top of the engine in the cylinder head and are held in place
by camshaft caps. The camshaft journals of the cylinder
head are drilled to create oil passages. Engine oil travels
to the camshafts under pressure where it lubricates each
camshaft journal. The oil returns to the oil pan through
drain holes in the cylinder head. The camshaft lobes are
machined into the solid camshaft to open and close the in-
take and the exhaust valves precisely the correct amount
at the correct time. The camshaft lobes are oiled by splash
action from pressurized oil escaping from the camshaft
journals.