fuel filter DATSUN 610 1969 Workshop Manual
[x] Cancel search | Manufacturer: DATSUN, Model Year: 1969, Model line: 610, Model: DATSUN 610 1969Pages: 171, PDF Size: 10.63 MB
Page 6 of 171
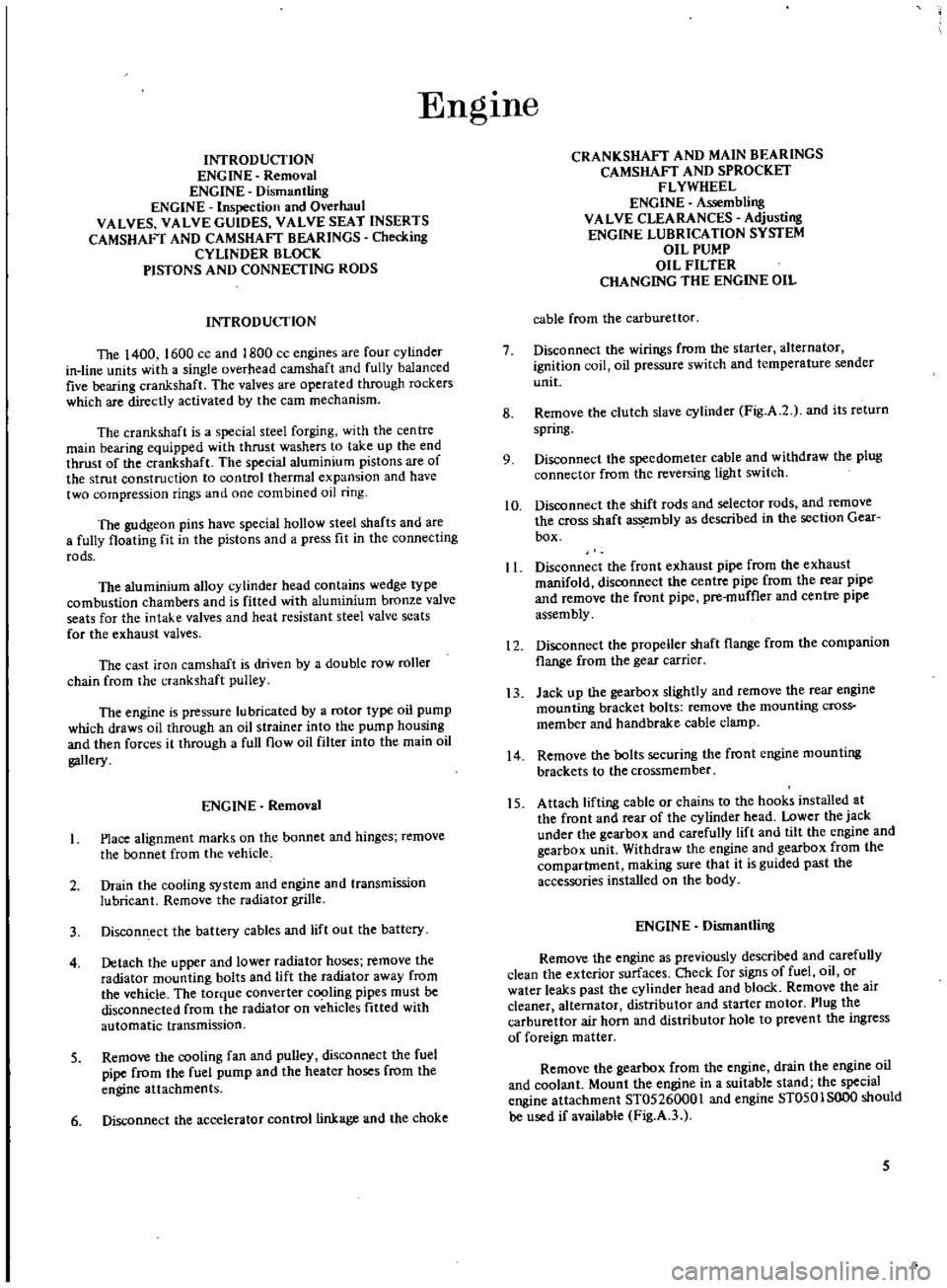
EngIne
INTRODUCTION
ENGINE
Removal
ENGINE
DismantUng
ENGINE
Inspection
and
Overhaul
VALVES
VALVE
GUIDES
VALVE
SEAT
INSERTS
CAMSHAFT
AND
CAMSHAFT
BEARINGS
Checking
CYliNDER
BLOCK
PtSTONS
AND
CONNECTING
RODS
INTRODUCTION
The
1400
1600
cc
and
1800
cc
engines
are
four
cylinder
in
line
units
with
a
single
overhead
camshaft
and
fully
balanced
five
bearing
crankshaft
The
valves
are
operated
through
rockers
which
are
directly
activated
by
the
earn
mechanism
The
crankshaft
is
a
special
steel
forging
with
the
centre
main
bearing
equipped
with
thrust
washers
to
take
up
the
end
thrust
of
the
crankshaft
The
special
aluminium
pistons
are
of
the
strut
construction
to
control
thermal
expansion
and
have
two
compression
rings
and
one
combined
oil
ring
The
gudgeon
pins
have
special
hollow
steel
shafts
and
are
a
fully
floating
fit
in
the
pistons
and
a
press
fit
in
the
connecting
rods
The
aluminium
alloy
cylinder
head
contains
wedge
type
combustion
chambers
and
is
fitted
with
aluminium
bronze
valve
seats
for
the
intake
valves
and
heat
resistant
steel
valve
seats
for
the
exhaust
valves
The
cast
iron
camshaft
is
driven
by
a
double
row
roller
chain
from
the
crankshaft
pulley
The
engine
is
pressure
lubricated
by
a
rotor
type
oil
pump
which
draws
oil
through
an
oil
strainer
into
the
pump
housing
and
then
forces
it
through
a
full
flow
oil
filter
into
the
main
oil
gallery
ENGINE
Removal
Place
alignment
marks
on
the
bonnet
and
hinges
remove
the
bonnet
from
the
vehicle
2
Drain
the
cooling
system
and
engine
and
transmission
lubricant
Remove
the
radiator
grille
3
Discon
ect
the
battery
cables
and
lift
out
the
battery
4
Detach
the
upper
and
lower
radiator
hoses
remove
the
radiator
mounting
bolts
and
lift
the
radiator
away
from
the
vehicle
The
torque
converter
c
jng
pipes
must
be
disconnected
from
the
radiator
on
vehicles
fitted
with
automatic
transmission
S
Remove
the
COOling
fan
and
pulley
disconnect
the
fuel
pipe
from
the
fuel
pump
and
the
heater
hoses
from
the
engine
attachments
6
Disconnect
the
accelerator
control
linkage
and
the
choke
CRANKSHAFT
AND
MAIN
BEARINGS
CAMSHAFT
AND
SPROCKET
FLYWHEEL
ENGINE
Assembling
VALVE
CLEARANCES
Adjusting
ENGINE
LUBRICATION
SYSTEM
OIL
PUMP
OIL
FILTER
CHANGING
THE
ENGINE
OIL
cable
from
the
carburettor
7
Disconnect
the
wirings
from
the
starter
alternator
ignition
coil
oil
pressure
switch
and
temperature
sender
unit
8
Remove
the
clutch
slave
cylinder
Fig
A
2
and
its
return
spring
9
Disconnect
the
speedometer
cable
and
withdraw
the
plug
connector
from
the
reversing
light
switch
10
Disconnect
the
shift
rods
and
seJector
rods
and
remove
the
cross
shaft
assembly
as
described
in
the
section
Gear
box
II
Disconnect
the
front
exhaust
pipe
from
the
exhaust
manifold
disconnect
the
centre
pipe
from
the
rear
pipe
and
remove
the
front
pipe
pre
muffler
and
centre
pipe
assembly
12
Disconnect
the
propeUer
shaft
flange
from
the
companion
flange
from
the
gear
carrier
13
Jack
up
the
gearbox
slightly
and
remove
the
rear
engine
mounting
bracket
bolts
remove
the
mounting
cross
member
and
handbrake
cable
c1amp
14
Remove
the
bolts
securing
the
front
engine
mounting
brackets
to
the
crossmember
15
Attach
lifting
cable
or
chains
to
the
hooks
installed
at
the
front
and
rear
of
the
cylinder
head
Lower
the
jack
under
the
gearbox
and
carefully
lift
and
tilt
the
engine
and
gearbox
unit
Withdraw
the
engine
and
gearbox
from
the
compartment
making
sure
that
it
is
guided
past
the
accessories
installed
on
the
body
ENGINE
Dismantling
Remove
the
engine
as
previously
described
and
carefully
clean
the
exterior
surfaces
Cbeck
for
signs
of
fuel
oil
or
water
leaks
past
the
cylinder
head
and
block
Remove
the
air
cleaner
alternator
distributor
and
starter
motor
Plug
the
carburettor
air
horn
and
distributor
hole
to
prevent
the
ingress
of
foreign
matter
Remove
the
gearbox
from
the
engine
drain
the
engine
oil
and
coolant
Mount
the
engine
in
a
suitable
stand
the
special
engine
attachment
ST05260001
and
engine
ST0501SOO0
should
be
used
if
available
Fig
A
3
5
Page 10 of 171
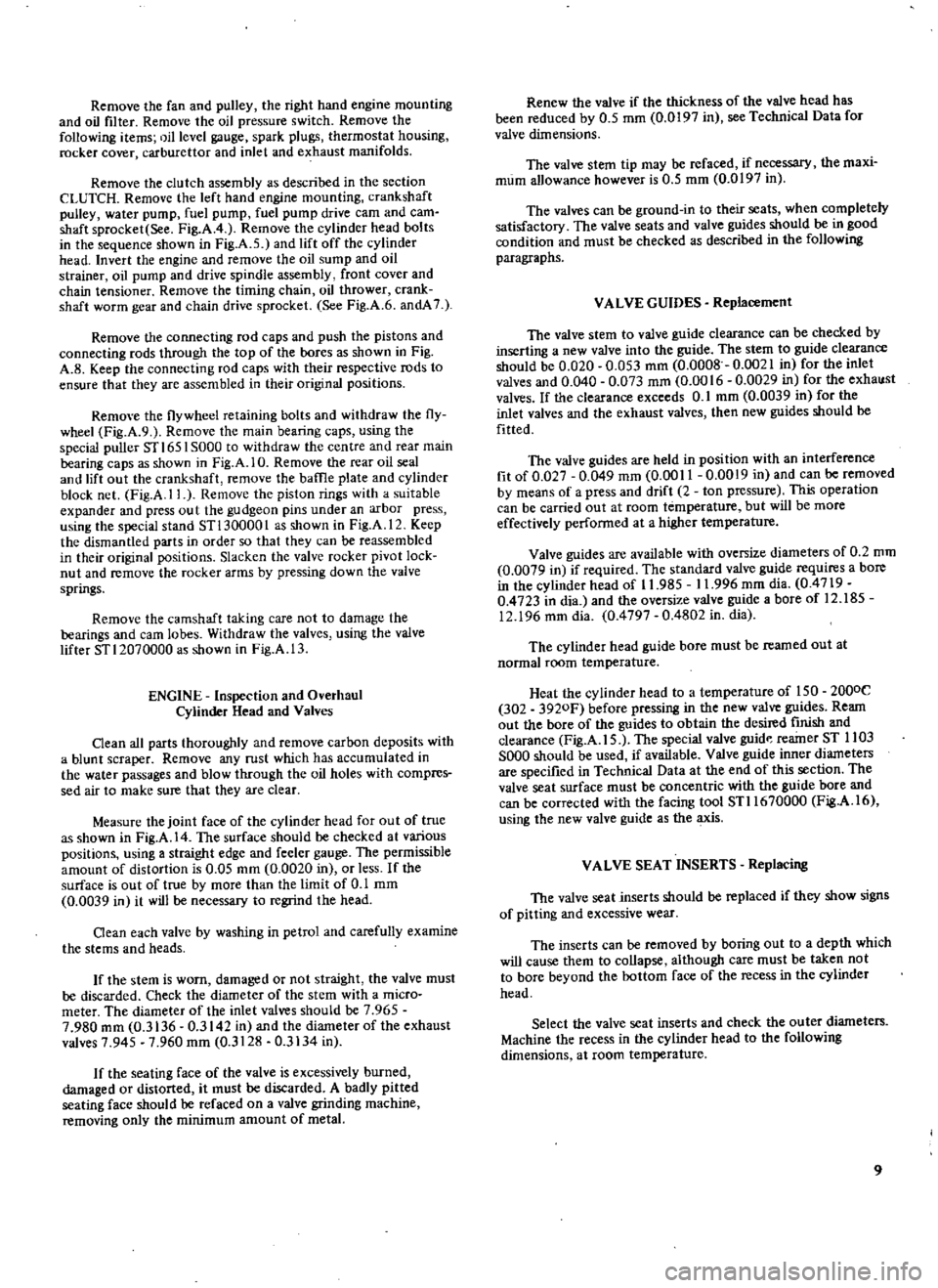
Remove
the
fan
and
pulley
the
right
hand
engine
mounting
and
oil
filter
Remove
the
oil
pressure
switch
Remove
the
following
items
oil
level
gauge
spark
plugs
thermostat
housing
rocker
cover
carburettor
and
inlet
and
exhaust
manifolds
Remove
the
clutch
assembly
as
described
in
the
section
CLUTCH
Remove
the
left
hand
engine
mounting
crankshaft
pulley
water
pump
fuel
pump
fuel
pump
drive
earn
and
cam
shaft
sprocket
See
Fig
A
4
Remove
the
cylinder
head
bolts
in
the
sequence
shown
in
Fig
A
5
and
lift
off
the
cylinder
head
Invert
the
engine
and
remove
the
oil
sump
and
oil
strainer
oil
pump
and
drive
spindle
assembly
front
cover
and
chain
tensioner
Remove
the
timing
chain
oil
thrower
crank
shaft
worm
gear
and
chain
drive
sprocket
See
Fig
A
6
andA
7
Remove
the
connecting
rod
caps
and
push
the
pistons
and
connecting
rods
through
the
top
of
the
bores
as
shown
in
Fig
A
B
Keep
the
connecting
rod
caps
with
their
respective
rods
to
ensure
that
they
are
assembled
in
their
original
positions
Remove
the
flywheel
retaining
bolts
and
withdraw
the
fly
wheel
Fig
A
9
Remove
the
main
bearing
caps
using
the
special
puller
ST
1651
SOOO
to
withdraw
the
centre
and
rear
main
bearing
caps
as
shown
in
Fig
A
l
O
Remove
the
rear
oil
seal
and
lift
out
the
crankshaft
remove
the
baffie
plate
and
cylinder
block
net
Fig
A
II
Remove
the
piston
rings
with
a
suitable
expander
and
press
out
the
gudgeon
pins
under
an
arbor
press
using
the
special
stand
STl300001
as
shown
in
Fig
A
12
Keep
the
dismantled
parts
in
order
so
that
they
can
be
reassembled
in
their
original
positions
Slacken
the
valve
rocker
pivot
lock
nut
and
remove
the
rocker
arms
by
pressing
down
the
valve
springs
Remove
the
camshaft
taking
care
not
to
damage
the
bearings
and
earn
lobes
Withdraw
the
valves
using
the
valve
lifter
STl2070000
as
shown
in
Fig
A
13
ENGINE
Inspection
and
Overhaul
Cylinder
Head
and
Valves
Clean
all
parts
thoroughly
and
remove
carbon
deposits
with
a
blunt
scraper
Remove
any
rust
which
has
accumulated
in
the
water
passages
and
blow
through
the
oil
holes
with
compres
sed
air
to
make
sure
that
they
are
clear
Measure
the
joint
face
of
the
cylinder
head
for
out
of
true
as
shown
in
Fig
A
14
The
surface
should
be
checked
at
various
positions
using
a
straight
edge
and
feeler
gauge
The
permissible
amount
of
distortion
is
0
05
mm
0
0020
in
or
less
If
the
surface
is
out
of
true
by
more
than
the
limit
of
0
1
mm
0
0039
in
it
will
be
necessary
to
regrind
the
head
Clean
each
valve
by
washing
in
petrol
and
carefully
examine
the
stems
and
heads
If
the
stem
is
worn
damaged
or
not
straight
the
valve
must
be
discarded
Check
the
diameter
of
the
stem
with
a
micro
meter
The
diameter
of
the
inlet
valves
should
be
7
965
7
980
mm
0
3136
0
3142
in
and
the
diameter
of
the
exhaust
valves
7
945
7
960
mm
0
3128
0
3134
in
If
the
seating
face
of
the
valve
is
excessively
burned
damaged
or
distorted
it
must
be
discarded
A
badly
pitted
seating
face
should
be
refaced
on
a
valve
grinding
machine
removing
only
the
minimum
amount
of
metal
Renew
the
valve
if
the
thickness
of
the
valve
head
has
been
reduced
by
0
5
mm
0
0197
in
see
Technical
Data
for
valve
dimensions
The
valve
stem
tip
may
be
refaced
if
necessary
the
maxi
mum
allowance
however
is
0
5
mm
0
0197
in
The
valves
can
be
ground
in
to
their
seats
when
completely
satisfactory
The
valve
seats
and
valve
guides
should
be
in
good
condition
and
must
be
checked
as
described
in
the
following
paragraphs
VALVE
GUIDES
Replacement
The
valve
stem
to
valve
guide
clearance
can
be
checked
by
inserting
a
new
valve
into
the
guide
The
stem
to
guide
clearance
should
be
0
020
0
053
mm
0
0008
0
0021
in
for
the
inlet
valves
and
0
040
0
073
mm
0
0016
0
0029
in
for
the
exhaust
valves
If
the
clearance
exceeds
0
1
mm
0
0039
in
for
the
inlet
valves
and
the
exhaust
valves
then
new
guides
should
be
fitted
The
valve
guides
are
held
in
position
with
an
interference
fit
of
0
027
0
049
mm
0
0011
0
0019
in
and
can
be
removed
by
means
of
a
press
and
drift
2
ton
pressure
This
operation
can
be
carried
out
at
room
temperature
but
will
be
more
effectively
performed
at
a
higher
temperature
Valve
guides
are
available
with
oversize
diameters
of
0
2
mm
0
0079
in
if
required
The
standard
valve
guide
requires
a
bore
in
the
cylinder
head
of
11
985
11
996
mm
dia
0
4719
0
4723
in
dia
and
the
oversize
valve
guide
a
bore
of
12
185
12
196
mm
dia
0
4797
0
4802
in
dial
The
cylinder
head
guide
bore
must
be
reamed
out
at
normal
room
temperature
Heat
the
cylinder
head
to
a
temperature
of
150
2000e
302
3920F
before
pressing
in
the
new
valve
guides
Ream
out
the
bore
of
the
guides
to
obtain
the
desired
fInish
and
clearance
Fig
A
IS
The
special
valve
guid
reamer
ST
1103
SOOO
should
be
used
if
available
Valve
guide
inner
diameters
are
specified
in
Technical
Data
at
the
end
of
this
section
The
valve
seat
surface
must
be
concentric
with
the
guide
bore
and
can
be
corrected
with
the
facing
tool
STll670000
Fig
A
16
using
the
new
valve
guide
as
the
axis
VALVE
SEAT
INSERTS
Replacing
The
valve
seat
inserts
should
be
replaced
if
they
show
signs
of
pitting
and
excessive
wear
The
inserts
can
be
removed
by
boring
out
to
a
depth
which
will
cause
them
to
collapse
although
care
must
be
taken
not
to
bore
beyond
the
bottom
face
of
the
recess
in
the
cylinder
head
Select
the
valve
seat
inserts
and
check
the
outer
diameters
Machine
the
recess
in
the
cylinder
head
to
the
following
dimensions
at
room
temperature
9
Page 18 of 171
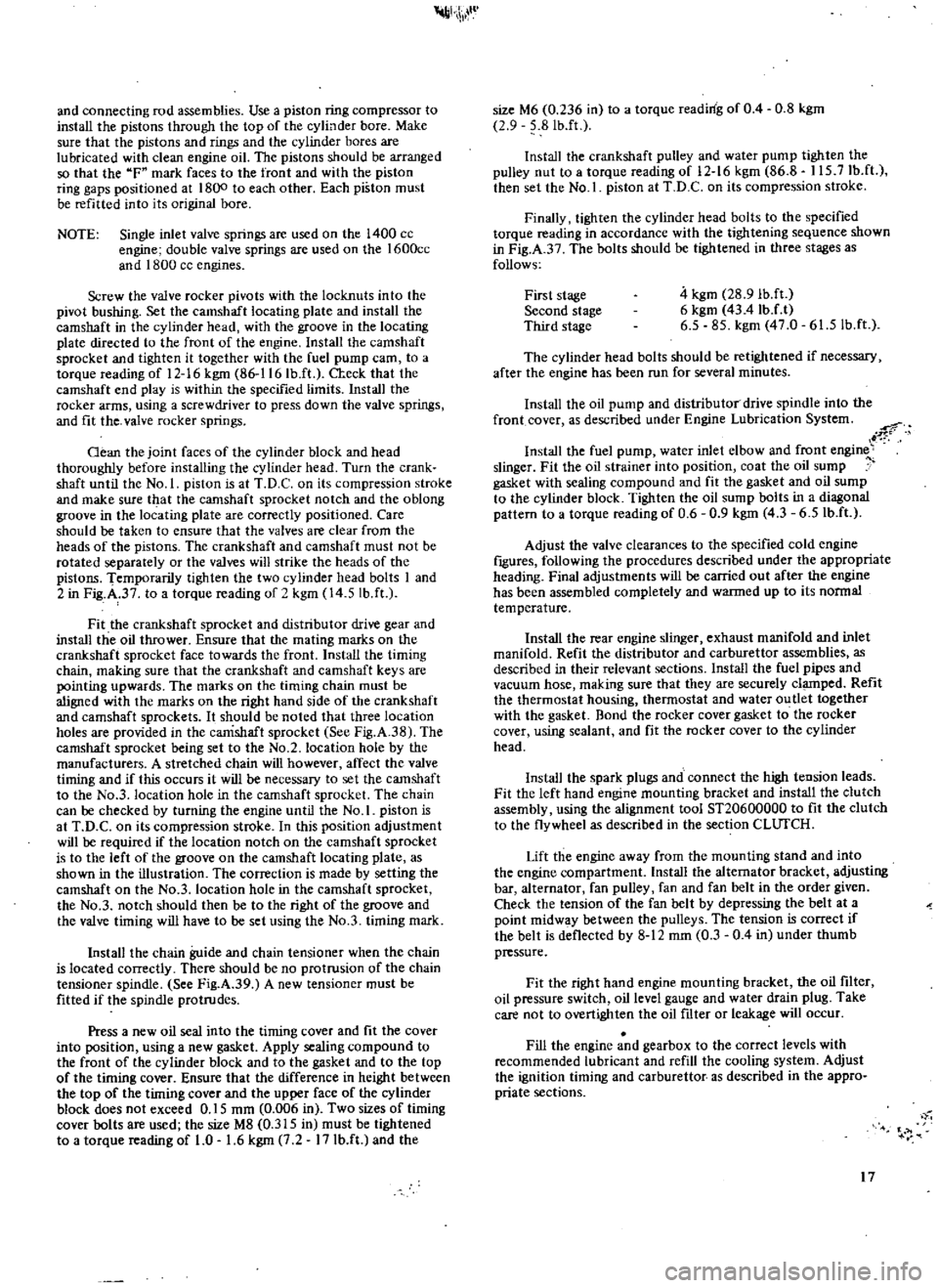
h
W
and
connecting
rod
assemblies
Use
a
piston
ring
compressor
to
install
the
pistons
through
the
top
of
the
cylbder
bore
Make
sure
that
the
pistons
and
rings
and
the
cylinder
bores
are
lubricated
with
clean
engine
oil
The
pistons
should
be
arranged
so
that
the
F
mark
faces
to
the
front
and
with
the
piston
ring
gaps
positioned
at
1800
to
each
other
Each
piston
must
be
refitted
into
its
original
bore
NOTE
Single
inlet
valve
springs
are
used
on
the
1400
cc
engine
double
valve
springs
are
used
on
the
1600cc
and
1800
cc
engines
Screw
the
valve
rocker
pivots
with
the
locknuts
into
the
pivot
bushing
Set
the
camshaft
locating
plate
and
install
the
camshaft
in
the
cylinder
head
with
the
groove
in
the
locating
plate
directed
to
the
front
of
the
engine
Install
the
camshaft
sprocket
and
tighten
it
together
with
the
fuel
pump
earn
to
a
torque
reading
of
12
16
kgm
86
116
IbJt
a
eck
that
the
camshaft
end
play
is
within
the
specified
limits
Install
the
rocker
arms
using
a
screwdriver
to
press
down
the
valve
springs
and
fit
the
valve
rocker
springs
Gean
the
joint
faces
of
the
cylinder
block
and
head
thoroughly
before
installing
the
cylinder
head
Turn
the
crank
shaft
until
the
No
1
piston
is
at
T
D
C
on
its
compression
stroke
and
make
sure
that
the
camshaft
sprocket
notch
and
the
oblong
groove
in
the
locating
plate
are
correctly
positioned
Care
should
be
taken
to
ensure
that
the
valves
are
clear
from
the
heads
of
the
pistons
The
crankshaft
and
camshaft
must
not
be
rotated
separately
or
the
valves
will
strike
the
heads
of
the
pistons
Temporarily
tighten
the
two
cylinder
head
bolts
1
and
2
in
Fig
A
37
to
a
torque
reading
of
2
kgm
14
5
lb
ft
Fit
the
crankshaft
sprocket
and
distributor
drive
gear
and
install
the
oil
thrower
Ensure
that
the
mating
marks
on
the
crankshaft
sprocket
face
towards
the
front
Install
the
timing
chain
making
sure
that
the
crankshaft
and
camshaft
keys
are
XJinting
upwards
The
marks
on
the
timing
chain
must
be
aligned
with
the
marks
on
the
right
hand
side
of
the
crankshaft
and
camshaft
sprockets
It
should
be
noted
that
three
location
holes
are
provided
in
the
camshaft
sprocket
See
Fig
A
38
The
camshaft
sprocket
being
set
to
the
No
2
location
hole
by
the
manufacturers
A
stretched
chain
will
however
affect
the
valve
timing
and
if
this
occurs
it
will
be
necessary
to
set
the
camshaft
to
the
No
3
location
hole
in
the
camshaft
sprocket
The
chain
can
be
checked
by
turning
the
engine
until
the
No
1
piston
is
at
T
D
C
on
its
compression
stroke
In
this
position
adjustment
will
be
required
if
the
location
notch
on
the
camshaft
sprocket
is
to
the
left
of
the
groove
on
the
camshaft
locating
plate
as
shown
in
the
illustration
The
correction
is
made
by
setting
the
camshaft
on
the
No
3
location
hole
in
the
camshaft
sprocket
the
No
3
notch
should
then
be
to
the
right
of
the
groove
and
the
valve
timing
will
have
to
be
set
using
the
No
3
timing
mark
Install
the
chain
guide
and
chain
tensioner
when
the
chain
is
located
correctly
There
should
be
no
protrusion
of
the
chain
tensioner
spindle
See
Fig
A
39
A
new
tensioner
must
be
fitted
if
the
spindle
protrudes
Press
a
new
oil
seal
into
the
timing
cover
and
fit
the
cover
into
position
using
a
new
gasket
Apply
sealing
compound
to
the
front
of
the
cylinder
block
and
to
the
gasket
and
to
the
top
of
the
timing
cover
Ensure
that
the
difference
in
height
between
the
top
of
the
timing
cover
and
the
upper
face
of
the
cylinder
block
does
not
exceed
0
15
mm
0
006
in
Two
sizes
of
timing
cover
bolts
are
used
the
size
M8
0
315
in
must
be
tightened
to
a
torque
reading
of
1
0
1
6
kgm
7
2
17
Ib
ft
and
the
size
M6
0
236
in
to
a
torque
reading
of
0
4
0
8
kgm
2
9
81b
ft
Install
the
crankshaft
pulley
and
water
pump
tighten
the
pulley
nut
to
a
torque
reading
of
12
16
kgm
86
8
115
7Ib
ft
then
set
the
No
1
piston
at
T
D
C
on
its
compression
stroke
Finally
tighten
the
cylinder
head
bolts
to
the
specified
torque
reading
in
accordance
with
the
tightening
sequence
shown
in
Fig
A
3
The
bolts
should
be
tightened
in
three
stages
as
follows
First
stage
Second
stage
Third
stage
4
kgm
28
9
lbJt
6
kgm
43
4
IbJ
t
6
5
85
kgm
47
0
61
5lb
ft
The
cylinder
head
bolts
should
be
retightened
if
necessary
after
the
engine
has
been
run
for
several
minutes
Install
the
oil
pump
and
distributor
drive
spindle
into
the
front
cover
as
described
under
Engine
Lubrication
System
r
rf
i
Install
the
fuel
pump
water
inlet
elbow
and
front
engine
slinger
Fit
the
oil
strainer
into
position
coat
the
oil
sump
gasket
with
sealing
compound
and
fit
the
gasket
and
oil
sump
to
the
cylinder
block
Tighten
the
oil
sump
bolts
in
a
diagonal
pattern
to
a
torque
reading
of
0
6
0
9
kgm
4
3
6
5
IbJt
Adjust
the
valve
clearances
to
the
specified
cold
engine
ftgures
following
the
procedures
described
under
the
appropriate
heading
Final
adjustments
will
be
carried
out
after
the
engine
has
been
assembled
completely
and
warmed
up
to
its
nonnal
temperature
Install
the
rear
engine
slinger
exhaust
manifold
and
inlet
manifold
Refit
the
distributor
and
carburettor
assemblies
as
described
in
their
relevant
sections
Install
the
fuel
pipes
and
vacuum
hose
making
sure
that
they
are
securely
cl
ped
Refit
the
thermostat
housing
thermostat
and
water
outlet
together
with
the
gasket
Bond
the
rocker
cover
gasket
to
the
rocker
cover
using
sealant
and
fit
the
rocker
cover
to
the
cylinder
head
Install
the
spark
plugs
and
connect
the
high
tension
leads
Fit
the
left
hand
engine
mounting
bracket
and
install
the
clutch
assembly
using
the
alignment
tool
ST20600000
to
fit
the
clutch
to
the
flywheel
as
described
in
the
section
ClUfCR
Lift
the
engine
away
from
the
mounting
stand
and
into
the
engine
compartment
Install
the
alternator
bracket
adjusting
bar
alternator
fan
pulley
fan
and
fan
belt
in
the
order
given
Check
the
tension
of
the
fan
belt
by
depressing
the
belt
at
a
point
midw
y
between
the
pulleys
The
tension
is
correct
if
the
belt
is
deflected
by
8
12
mm
0
3
0
4
in
under
thumb
pressure
Fit
the
right
hand
engine
mounting
bracket
the
oil
filter
oil
pressure
switch
oil
level
gauge
and
water
drain
plug
Take
care
not
to
overtighten
the
oil
nIter
or
leakage
will
occur
Fill
the
engine
and
gearbox
to
the
correct
levels
with
recommended
lubricant
and
refill
the
cooling
system
Adjust
the
ignition
timing
and
carburettor
as
described
in
the
appro
priate
sections
17
Page 38 of 171
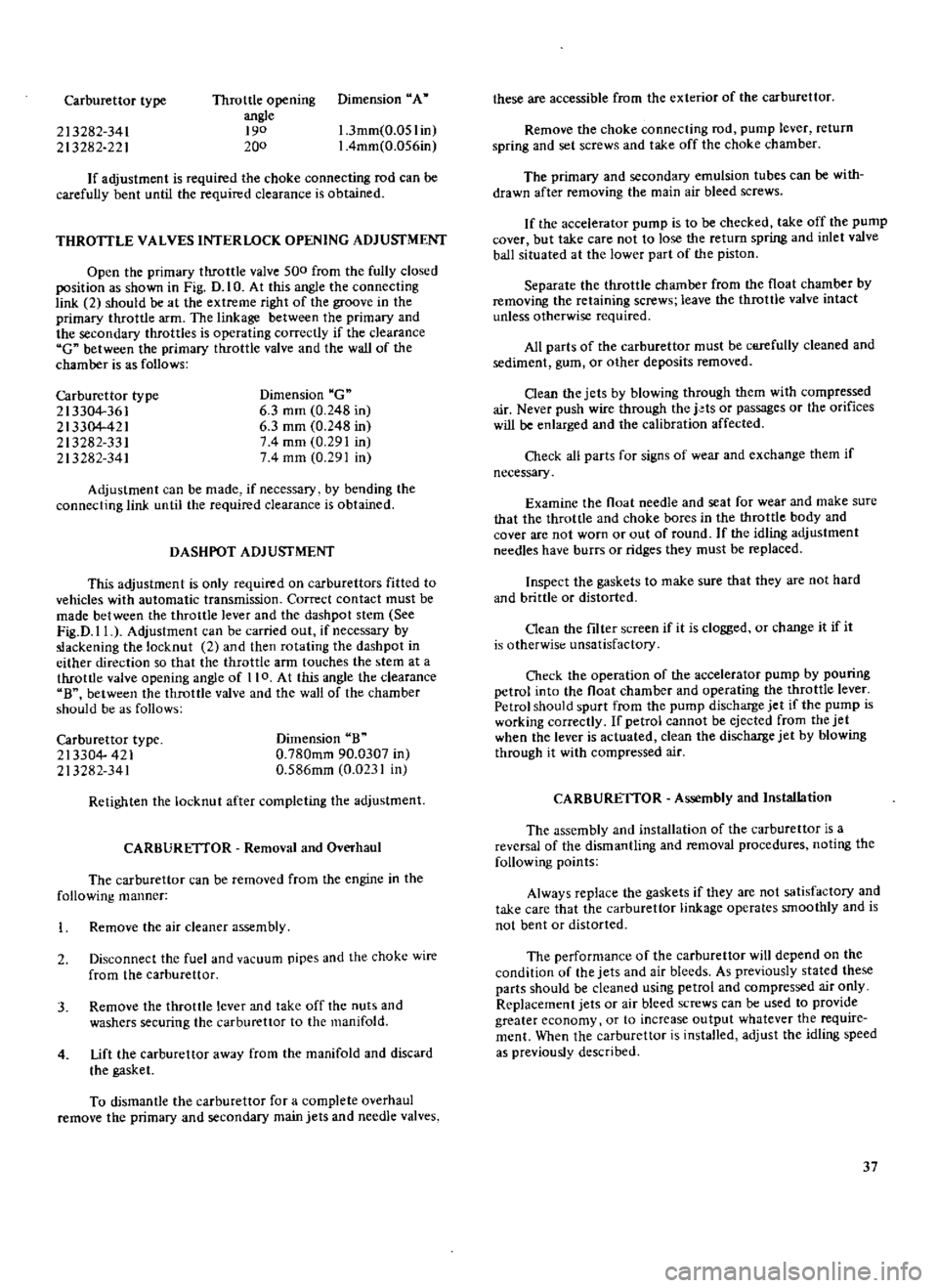
Carburettor
type
Throttle
opening
angle
190
200
Dimension
A
213282
341
213282
221
l
3mm
0
051
in
I
4mm
0
056in
If
adjustment
is
required
the
choke
connecting
rod
can
be
carefully
bent
until
the
required
clearance
is
obtained
THROTTLE
VALVES
INTERLOCK
OPENING
ADJUSfMENT
Open
the
primary
throttle
valve
500
from
the
fully
closed
position
as
shown
in
Fig
D
I
O
At
this
angle
the
connecting
link
2
should
be
at
the
extreme
right
of
the
groove
in
the
primary
throttle
arm
The
linkage
between
the
primary
and
the
secondary
throttles
is
operating
correctly
if
the
clearance
C
between
the
primary
throttle
valve
and
the
wall
of
the
chamber
is
as
follows
Carburettor
type
213304
361
213304
421
213282
331
213282
341
Dimension
C
6
3
mm
0
248
in
6
3
mm
0
248
in
74
mm
0
291
in
74
mm
0
291
in
Adjustment
can
be
made
if
necessary
by
bending
the
connecting
link
until
the
required
clearance
is
obtained
DASHPOT
ADJUSfMENT
This
adjustment
is
only
required
on
carburettors
fitted
to
vehicles
with
automatic
transmission
Correct
contact
must
be
made
between
the
throttle
lever
and
the
dashpot
stem
See
Fig
D
II
Adjustment
can
be
carried
out
if
necessary
by
slackening
the
locknut
2
and
then
rotating
the
dashpot
in
either
direction
so
that
the
throttle
ann
touches
the
stem
at
a
throttle
valve
opening
angle
of
110
At
this
angle
the
clearance
B
between
the
throttle
valve
and
the
wall
of
the
chamber
should
be
as
follows
Carburettor
type
213304
421
213282
341
Dimension
B
0
780mm
90
0307
in
0
586mm
0
0231
in
Retighten
the
locknut
after
completing
the
adjustment
CARBURETTOR
Removal
and
Overhaul
The
carburettor
can
be
removed
from
the
engine
in
the
following
manner
Remove
the
air
cleaner
assembly
2
Disconnect
the
fuel
and
vacuum
pipes
and
the
choke
wire
from
the
carburettor
3
Remove
the
throttle
lever
and
take
off
the
nuts
and
washers
securing
the
carburettor
to
the
manifold
4
Lift
the
carburettor
away
from
the
manifold
and
discard
the
gasket
To
dismantle
the
carburettor
for
a
complete
overhaul
remove
the
primary
and
secondary
main
jets
and
needle
valves
these
are
accessible
from
the
exterior
of
the
carburettor
Remove
the
choke
connecting
rod
pump
lever
return
spring
and
set
screws
and
take
off
the
choke
chamber
The
primary
and
secondary
emulsion
tubes
can
be
with
drawn
after
removing
the
main
air
bleed
screws
If
the
accelerator
pump
is
to
be
checked
take
off
the
pump
cover
but
take
care
not
to
lose
the
return
spring
and
inlet
valve
ball
situated
at
the
lower
part
of
the
piston
Separate
the
throttle
chamber
from
the
float
chamber
by
removing
the
retaining
screws
leave
the
throttle
valve
intact
unless
otherwise
required
All
parts
of
the
carburettor
must
be
ctifefully
cleaned
and
sediment
gum
or
other
deposits
removed
Clean
the
jets
by
blowing
through
them
with
compressed
air
Never
push
wire
through
the
j
ts
or
passages
or
the
orifices
will
be
enlarged
and
the
calibration
affected
Check
all
parts
for
signs
of
wear
and
exchange
them
if
necessary
Examine
the
float
needle
and
seat
for
wear
and
make
sure
that
the
throttle
and
choke
bores
in
the
throttle
body
and
cover
are
not
worn
or
out
of
round
If
the
idling
adjustment
needles
have
burrs
or
ridges
they
must
be
replaced
Inspect
the
gaskets
to
make
sure
that
they
are
not
hard
and
brittle
or
distorted
Oean
the
filter
screen
if
it
is
clogged
or
change
it
if
it
is
otherwist
unsatisfactory
Check
the
operation
of
the
accelerator
pump
by
pouring
petrol
into
the
float
chamber
and
operating
the
throttle
lever
Petrol
should
spurt
from
the
pump
discharge
jet
if
the
pump
is
working
correctly
If
petrol
cannot
be
ejected
from
the
jet
when
the
lever
is
actuated
clean
the
discharge
jet
by
blowing
through
it
with
compressed
air
CARBURETTOR
Assembly
and
Installation
The
assembly
and
installation
of
the
carburettor
is
a
reversal
of
the
dismantling
and
removal
procedures
noting
the
following
points
Always
replace
the
gaskets
if
they
are
not
satisfactory
and
take
care
that
the
carburettor
linkage
operates
smoothly
and
is
not
bent
or
distorted
The
performance
of
the
carburettor
will
depend
on
the
condition
of
the
jets
and
air
bleeds
As
previously
stated
these
pacts
should
be
cleaned
using
petrol
and
compressed
air
only
Replacement
jets
or
air
bleed
screws
can
be
used
to
provide
greater
economy
or
to
increase
output
whatever
the
require
ment
When
the
carburettor
is
installed
adjust
the
idling
speed
as
previously
described
37
Page 134 of 171
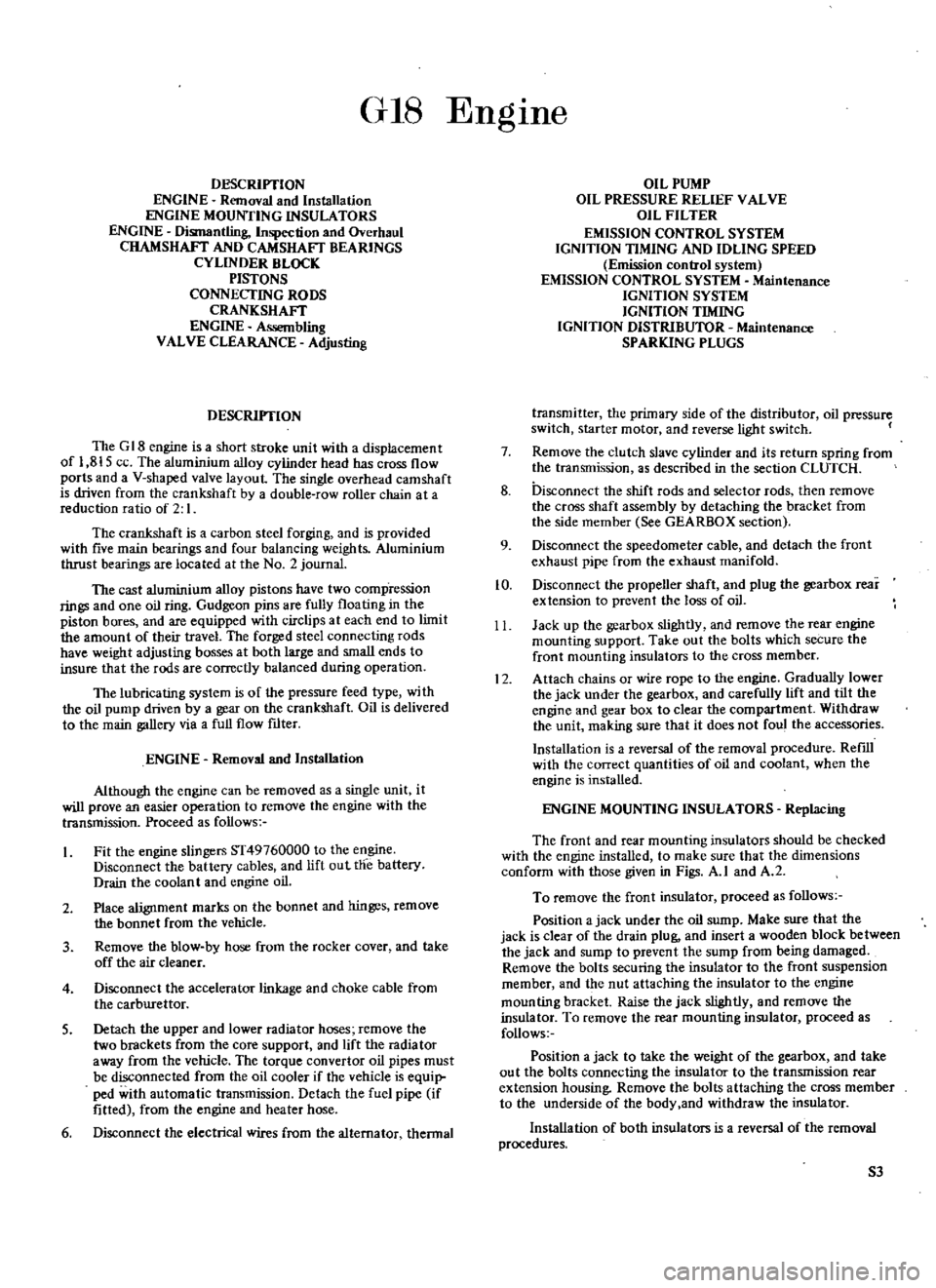
GIS
DESCRIYfION
ENGINE
Removal
and
Installation
ENGINE
MOUNTING
INSULATORS
ENGINE
Dismantling
Inspection
and
Overhaul
CHAMSHAFT
AND
CAMSHAFT
BEARINGS
CYLINDER
BLOCK
PISTONS
CONNECTING
RODS
CRANKSHAFT
ENGINE
Assembling
VALVE
CLEARANCE
Adjusting
DESCRIYfION
The
G
18
engine
is
a
short
stroke
unit
with
a
displacement
of
1
815
ce
The
aluminium
alloy
cylinder
head
has
cross
flow
ports
and
a
V
shaped
valve
layout
The
single
overhead
camshaft
is
driven
from
the
crankshaft
by
a
double
row
roller
chain
at
a
reduction
ratio
of
2
I
The
crankshaft
is
a
carbon
steel
forging
and
is
provided
with
five
main
bearings
and
four
balancing
weights
Aluminium
thrust
bearings
are
located
at
the
No
2
journal
The
cast
aluminium
alloy
pistons
have
two
comp
ression
rings
and
one
oil
ring
Gudgeon
pins
are
fully
floating
in
the
piston
bores
and
are
equipped
with
circlips
at
each
end
to
limit
the
amount
of
their
travel
The
forged
steel
connecting
rods
have
weight
adjusting
bosses
at
both
large
and
small
ends
to
insure
that
the
rods
are
correctly
balanced
during
operation
The
lubricating
system
is
of
the
pressure
feed
type
with
the
oil
pump
driven
by
a
gear
on
the
crankshaft
Oil
is
delivered
to
the
main
gallery
via
a
full
flow
ftlter
ENGINE
Removal
and
Installation
Although
the
engine
can
be
removed
as
a
single
unit
it
will
prove
an
easier
operation
to
remove
the
engine
with
the
transmission
Proceed
as
follows
Fit
the
engine
slingers
ST49760000
to
the
engine
Disconnect
the
battery
cables
and
lift
out
the
battery
Drain
the
coolant
and
engine
oil
2
Place
alignment
marks
on
the
bonnet
and
hinges
remove
the
bonnet
from
the
vehicle
3
Remove
the
blow
by
hose
from
the
rocker
cover
and
take
off
the
air
cleaner
4
Disconnect
the
accelerator
linkage
and
choke
cable
from
the
carburettor
S
Detach
the
upper
and
lower
radiator
hoses
remove
the
two
brackets
from
the
core
support
and
lift
the
radia
tor
away
from
the
vehicle
The
torque
convertor
oil
pipes
must
be
disconnected
from
the
oil
cooler
if
the
vehicle
is
equip
ped
with
automatic
transmission
Detach
the
fuel
pipe
if
fitted
from
the
engine
and
heater
hose
6
Disconnect
the
electrical
wires
from
the
alternator
thennal
EngIne
OIL
PUMP
OIL
PRESSURE
RELIEF
VALVE
OIL
FILTER
EMISSION
CONTROL
SYSTEM
IGNITION
TIMING
AND
IDLING
SPEED
Emission
control
system
EMISSION
CONTROL
SYSTEM
Maintenance
IGNITION
SYSTEM
IGNITION
TIMING
IGNITION
DISTRIBUTOR
Maintenance
SPARKING
PLUGS
transmitter
the
primary
side
of
the
distributor
oil
pressure
switch
starter
motor
and
reverse
light
switch
7
Remove
the
clutch
slave
cylinder
and
its
return
spring
from
the
transmission
as
described
in
the
section
CLUTCH
8
Disconnect
the
shift
rods
and
selector
rods
then
remove
the
cross
shaft
assembly
by
detaching
the
bracket
from
the
side
member
See
GEARBOX
section
9
Disconnect
the
speedometer
cable
and
detach
the
front
exhaust
pipe
from
the
exhaust
manifold
10
Disconnect
the
propeller
shaft
and
plug
the
gearbox
rear
extension
to
prevent
the
loss
of
oil
11
Jack
up
the
gearbox
slightly
and
remove
the
rear
engine
mounting
support
Take
out
the
bolts
which
secure
the
front
mounting
insulators
to
the
cross
member
12
Attach
chains
or
wire
rope
to
the
engine
Gradually
lower
the
jack
under
the
gearbox
and
carefully
lift
and
tilt
the
engine
and
gear
box
to
clear
the
compartment
Withdraw
the
unit
making
sure
that
it
does
not
foul
the
accessories
Installation
is
a
reversal
of
the
removal
procedure
RefIll
with
the
correct
quantities
of
oil
and
coolant
when
the
engine
is
installed
ENGINE
MOUNTING
INSULATORS
Replacing
The
front
and
rear
mounting
insulators
should
be
checked
with
the
engine
installed
to
make
sure
that
the
dimensions
conform
with
those
given
in
Figs
A
I
and
A
2
To
remove
the
front
insulator
proceed
as
follows
Position
a
jack
under
the
oil
sump
Make
sure
that
the
jack
is
clear
of
the
drain
plug
and
insert
a
wooden
block
between
the
jack
and
sump
to
prevent
the
sump
from
being
damaged
Remove
the
bolts
securing
the
insulator
to
the
front
suspension
member
and
the
nut
attaching
the
insulator
to
the
engine
mounting
bracket
Raise
the
jack
slightly
and
remove
the
insulator
To
remove
the
rear
mounting
insulator
proceed
as
follows
Position
a
jack
to
take
the
weight
of
the
gearbox
and
take
out
the
bolts
connecting
the
insulator
to
the
transmission
rear
extension
housing
Remove
the
bolts
attaching
the
cross
member
to
the
underside
of
the
body
and
withdraw
the
insulator
Installation
of
both
insulators
is
a
reversal
of
the
removal
procedures
S3
Page 150 of 171
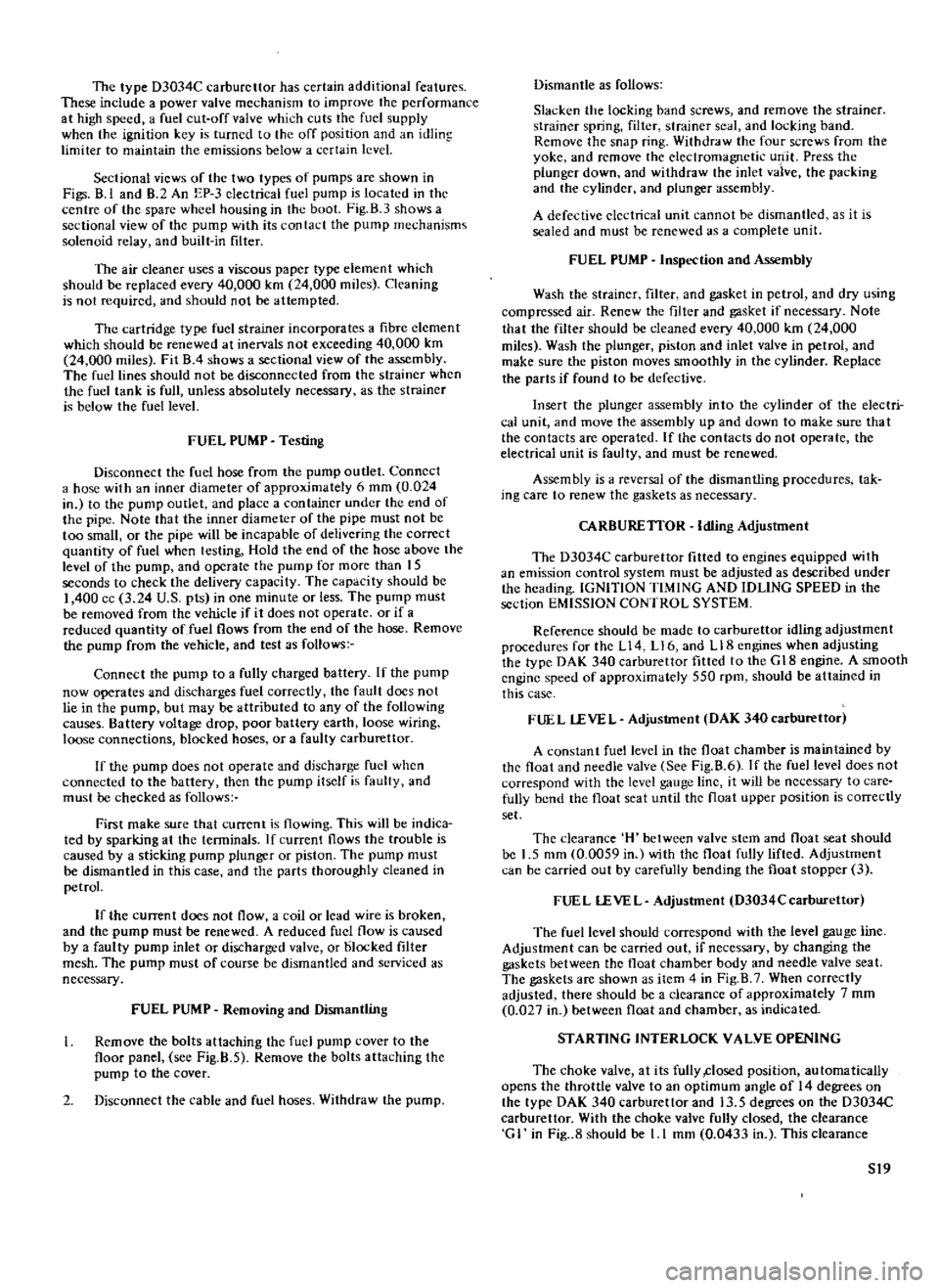
The
type
D3034C
carburettor
has
certain
additional
features
These
include
a
power
valve
mechanism
to
improve
the
performance
at
high
speed
a
fuel
cut
off
valve
which
cuts
the
fuel
supply
when
the
ignition
key
is
turned
to
the
off
position
and
an
idling
limiter
to
maintain
the
emissions
below
a
certain
level
Sectional
views
of
the
two
types
of
pumps
are
shown
in
Figs
8
1
and
B
2
An
EP
3
electrical
fuel
pump
is
located
in
the
centre
of
the
spare
wheel
housing
in
the
boot
Fig
B
3
shows
a
sectional
view
of
the
pump
with
its
contact
the
pump
mechanisms
solenoid
relay
and
built
in
filter
The
air
cleaner
uses
a
viscous
paper
type
element
which
should
be
replaced
every
40
000
km
24
000
miles
Cleaning
is
not
required
and
should
not
be
attempted
The
cartridge
type
fuel
strainer
incorporates
a
fibre
clement
which
should
be
renewed
at
inervals
not
exceeding
40
000
km
24
000
miles
Fit
B
4
shows
a
sectional
view
of
the
assembly
The
fuel
lines
should
not
be
disconnected
from
the
strainer
when
the
fuel
tank
is
full
unless
absolutely
necessary
as
the
strainer
is
below
the
fuel
level
FUEL
PUMP
Testing
Disconnect
the
fuel
hose
from
the
pump
outlet
Connect
a
hose
with
an
inner
diameter
of
approximately
6
mm
0
024
in
to
the
pump
outlet
and
place
a
container
under
the
end
of
the
pipe
Note
that
the
inner
diameter
of
the
pipe
must
not
be
too
small
or
the
pipe
will
be
incapable
of
delivering
the
correct
quantity
of
fuel
when
testing
Hold
the
end
of
the
hose
above
the
level
of
the
pump
and
operate
the
pump
for
more
than
IS
seconds
to
check
the
delivery
capacity
The
capacity
should
be
I
400
cc
3
24
U
S
pts
in
one
minute
or
less
The
pump
must
be
removed
from
the
vehicle
if
it
does
not
operate
or
if
a
reduced
quantity
of
fuel
flows
from
the
end
of
the
hose
Remove
the
pump
from
the
vehicle
and
test
as
follows
Connect
the
pump
to
a
fully
charged
battery
If
the
pump
now
operates
and
discharges
fuel
correctly
the
fault
does
not
lie
in
the
pump
but
may
be
attributed
to
any
of
the
following
causes
Battery
voltage
drop
poor
battery
earth
loose
wiring
loose
connections
blocked
hoses
or
a
faulty
carburettor
If
the
pump
does
not
operate
and
discharge
fuel
when
connected
to
the
battery
then
the
pump
itself
is
faulty
and
must
be
checked
as
follows
First
make
sure
that
current
is
flowing
This
will
be
indica
ted
by
sparking
at
the
tenninals
If
current
flows
the
trouble
is
caused
by
a
sticking
pump
plunger
or
piston
The
pump
must
be
dismantled
in
this
case
and
the
parts
thoroughly
cleaned
in
petrol
If
the
current
does
not
flow
a
coil
or
lead
wire
is
broken
and
the
pump
must
be
renewed
A
reduced
fuel
flow
is
caused
by
a
faulty
pump
inlet
or
discharged
valve
or
blocked
filter
mesh
The
pump
must
of
course
be
dismantled
and
serviced
as
necessary
FUEL
PUMP
Removing
and
Dismantling
Remove
the
bolts
attaching
the
fuel
pump
cover
to
the
floor
panel
see
Fig
B
S
Remove
the
bolts
attaching
the
pump
to
the
cover
2
Disconnect
the
cable
and
fuel
hoses
Withdraw
the
pump
Dismantle
as
follows
Slacken
the
locking
band
screws
and
remove
the
strainer
strainer
spring
filter
strainer
seal
and
locking
band
Remove
the
snap
ring
Withdraw
the
four
screws
from
the
yoke
and
remove
the
electromagnetic
ulJ
it
Press
the
plunger
down
and
withdraw
the
inlet
vaive
the
packing
and
the
cylinder
and
plunger
assembly
A
defective
eledrical
unit
cannot
be
dismantled
as
it
is
sealed
and
must
be
renewed
as
a
complete
unit
FUEL
PUMP
Inspection
and
Assembly
Wash
the
strainer
filter
and
gasket
in
petrol
and
dry
using
compressed
air
Renew
the
filter
and
gasket
if
necessary
Note
that
the
filter
should
be
cleaned
every
40
000
km
24
000
miles
Wash
the
plunger
piston
and
inlet
valve
in
petrol
and
make
sure
the
piston
moves
smoothly
in
the
cylinder
Replace
the
parts
if
found
to
be
defective
Insert
the
plunger
assembly
into
the
cylinder
of
the
electri
cal
unit
and
move
the
assembly
up
and
down
to
make
sure
tha
t
the
contacts
are
operated
If
the
contacts
do
not
operate
the
electrical
unit
is
faulty
and
must
be
renewed
Assembly
is
a
reversal
of
the
dismantling
procedures
tak
ing
care
to
renew
the
gaskets
as
necessary
CARBURETIOR
Idling
Adjustment
The
D3034C
carburettor
fitted
to
engines
equipped
with
an
emission
control
system
must
be
adjusted
as
described
under
the
heading
IGNITION
TIMING
AND
IDLING
SPEED
in
the
section
EMISSION
CONTROL
SYSTEM
Reference
should
be
made
to
carburettor
idling
adjustment
procedures
for
the
L14
L16
and
LI8
engines
when
adjusting
the
type
DAK
340
carburettor
fitted
to
the
G
18
engine
A
smooth
engine
speed
of
approximately
550
rpm
should
be
attained
in
this
case
FUEL
lEVEL
Adjustment
DAK
340earburettor
A
constant
fuellevcl
in
the
float
chamber
is
maintained
by
the
float
and
needle
valve
See
Fig
8
6
If
the
fuel
level
does
not
correspond
with
the
level
gauge
line
it
will
be
necessary
to
care
fully
bend
the
float
seat
until
the
float
upper
position
is
correctly
set
The
clearance
H
between
valve
stem
and
float
seat
should
be
I
5
mm
0
0059
in
with
the
float
fully
lifted
Adjustment
can
be
carried
out
by
carefully
bending
the
float
stopper
3
FUEL
lEVEL
Adjustment
D3034Ccarburettnr
The
fuel
level
should
correspond
with
the
level
gauge
line
Adjustment
can
be
carried
out
if
necessary
by
changing
the
gaskets
between
the
float
chamber
body
and
needle
valve
seat
The
gaskets
are
shown
as
item
4
in
Fig
B
7
When
correctly
adjusted
there
should
be
a
clearance
of
approximately
7
mm
0
027
in
between
float
and
chamber
as
indicated
STARTING
INTERLOCK
VALVE
OPENING
The
choke
valve
at
its
fully
closed
position
automatically
opens
the
throttle
valve
to
an
optimum
angle
of
14
degrees
on
the
type
DAK
340
carburettor
and
13
5
degrees
on
the
D3034C
carburettor
With
the
choke
valve
fully
closed
the
clearance
G
I
in
Fig
8
should
be
1
I
mm
0
0433
in
This
clearance
S19
Page 152 of 171
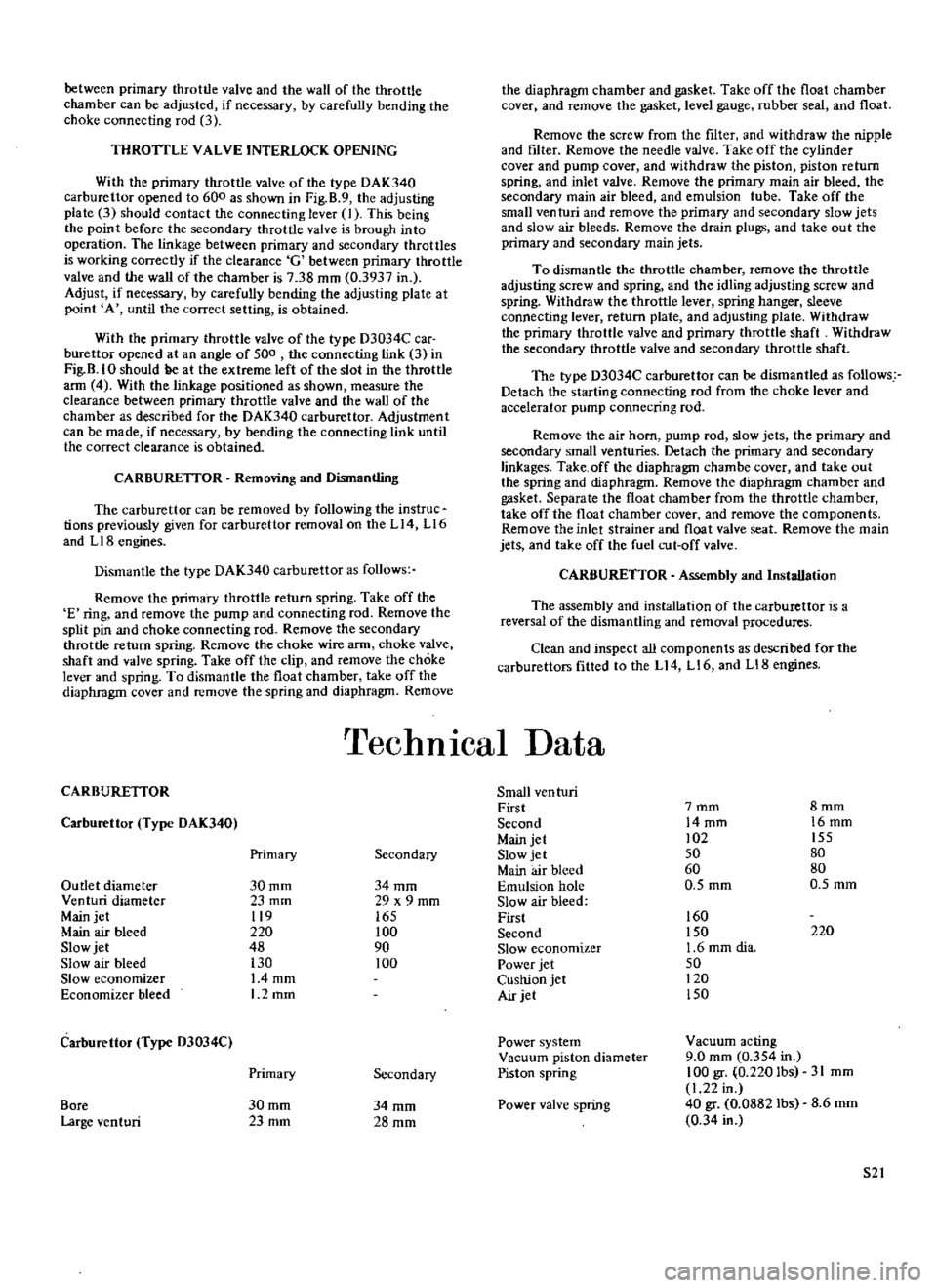
between
primary
throttle
valve
and
the
wall
of
the
throttle
chamber
can
be
adjusted
if
necessary
by
carefully
bending
the
choke
connecting
rod
3
THROTILE
VALVE
INTERLOCK
OPENING
With
the
primary
throttle
valve
of
the
type
DAK340
carburettor
opened
to
600
as
shown
in
Fig
B
9
the
adjusting
plate
3
should
contact
the
connecting
lever
J
This
being
the
point
before
the
secondary
throttle
valve
is
brough
into
operation
The
linkage
between
primary
and
secondary
throttles
is
working
correctly
if
the
clearance
G
between
primary
throttle
valve
and
the
wall
of
the
chamber
is
738
mm
0
3937
in
Adjust
if
necessary
by
carefully
bending
the
adjusting
plate
at
point
A
until
the
correct
setting
is
obtained
With
the
primary
throttle
valve
of
the
type
D3034C
car
burettor
opened
at
an
angle
of
500
the
connecting
link
3
in
Fig
B
IO
should
ge
at
the
extreme
left
of
the
slot
in
the
throttle
ann
4
With
the
linkage
positioned
as
shown
measure
the
clearance
between
primary
throttle
valve
and
the
wall
of
the
chamber
as
described
for
the
DAK340
carburettor
Adjustment
can
be
made
if
necessary
by
bending
the
connecting
link
until
the
correct
clearance
is
obtained
CARBURElTOR
Removing
and
Dismantling
The
carburettor
can
be
removed
by
following
the
instruc
tions
previously
given
for
carburettor
removal
on
the
Ll4
L16
and
LIB
engines
Dismantle
the
type
DAK340
carburettor
as
follows
Remove
the
primary
throttle
return
spring
Take
off
the
E
ring
and
remove
the
pump
and
connecting
rod
Remove
the
split
pin
and
choke
connecting
rod
Remove
the
secondary
throttle
return
spring
Remove
the
choke
wire
arm
choke
valve
shaft
and
valve
spring
Take
off
the
clip
and
remove
the
choke
lever
and
spring
To
dismantle
the
float
chamber
take
off
the
diaphragm
cover
and
remove
the
spring
and
diaphragm
Remove
the
diaphragm
chamber
and
gasket
Take
off
the
float
chamber
cover
and
remove
the
gasket
level
gauge
rubber
seal
and
float
Remove
the
screw
from
the
filter
and
withdraw
the
nipple
and
filter
Remove
the
needle
valve
Take
off
the
cylinder
cover
and
pump
cover
and
withdraw
the
piston
piston
return
spring
and
inlet
valve
Remove
the
primary
main
air
bleed
the
secondary
main
air
bleed
and
emulsion
tube
Take
off
the
small
venturi
and
remove
the
primary
and
secondary
slow
jets
and
slow
air
bleeds
Remove
the
drain
plugs
and
take
out
the
primary
and
secondary
main
jets
To
dismantle
the
throttle
chamber
remove
the
throttle
adjusting
screw
and
spring
and
the
idling
adjusting
screw
and
spring
Withdraw
the
throttle
lever
spring
hanger
sleeve
connecting
lever
return
plate
and
adjusting
plate
Withdraw
the
primary
throttle
valve
and
primary
throttle
shaft
Withdraw
the
secondary
throttle
valve
and
secondary
throttle
shaft
The
type
D3034C
carburettor
can
be
dismantled
as
follows
Detach
the
starting
connecting
rod
from
the
choke
lever
and
accelerator
pump
connecting
rod
Remove
the
air
horn
pump
rod
slow
jets
the
primary
and
secondary
small
venturies
Detach
the
primary
and
secondary
linkages
Take
off
the
diaphragm
chambe
cover
and
take
out
the
spring
and
diaphragm
Remove
the
diaphragm
chamber
and
gasket
Separate
the
float
chamber
from
the
throttle
chamber
take
off
the
float
chamber
cover
and
remove
the
components
Remove
the
inlet
strainer
and
float
valve
seat
Remove
the
main
jets
and
take
off
the
fuel
cut
off
valve
CARBURETTOR
Assembly
and
Installation
The
assembly
and
installation
of
the
carburettor
is
a
reversal
of
the
dismantling
and
removal
procedures
Clean
and
inspect
all
components
as
described
for
the
carburettors
fitted
to
the
Ll4
Ll6
and
LI8
engines
TechnIcal
Data
CARBURETIOR
Small
ven
turi
First
7mm
8mm
Carburettor
Type
DAK340
Second
14mm
16mm
Main
jet
02
155
Primary
Secondary
Slow
jet
50
80
Main
air
bleed
60
80
Outlet
diameter
30mm
34mm
Emulsion
hole
0
5
mm
O
5mm
Venturi
diameter
23
mm
29
x
9
mm
Slow
air
bleed
Main
jet
119
165
First
160
Main
air
bleed
220
100
Second
150
220
Slow
jet
48
90
Slow
economizer
1
6
mm
dia
Slow
air
bleed
130
100
Power
jet
50
Slow
economizer
L4mm
Cushion
jet
120
Economizer
bleed
1
2mm
Air
jet
150
Carburettor
Type
D3034C
Power
system
Vacllum
acting
Vacuum
piston
diameter
9
0
mm
0
354
in
Primary
Secondary
Piston
spring
100
gr
0
220
Ibs
31
mm
1
22
in
Bore
30mm
34mm
Power
valve
spring
40
gr
0
0882
lbs
8
6mm
Large
venturi
23mm
28mm
0
34
in
52
Page 168 of 171
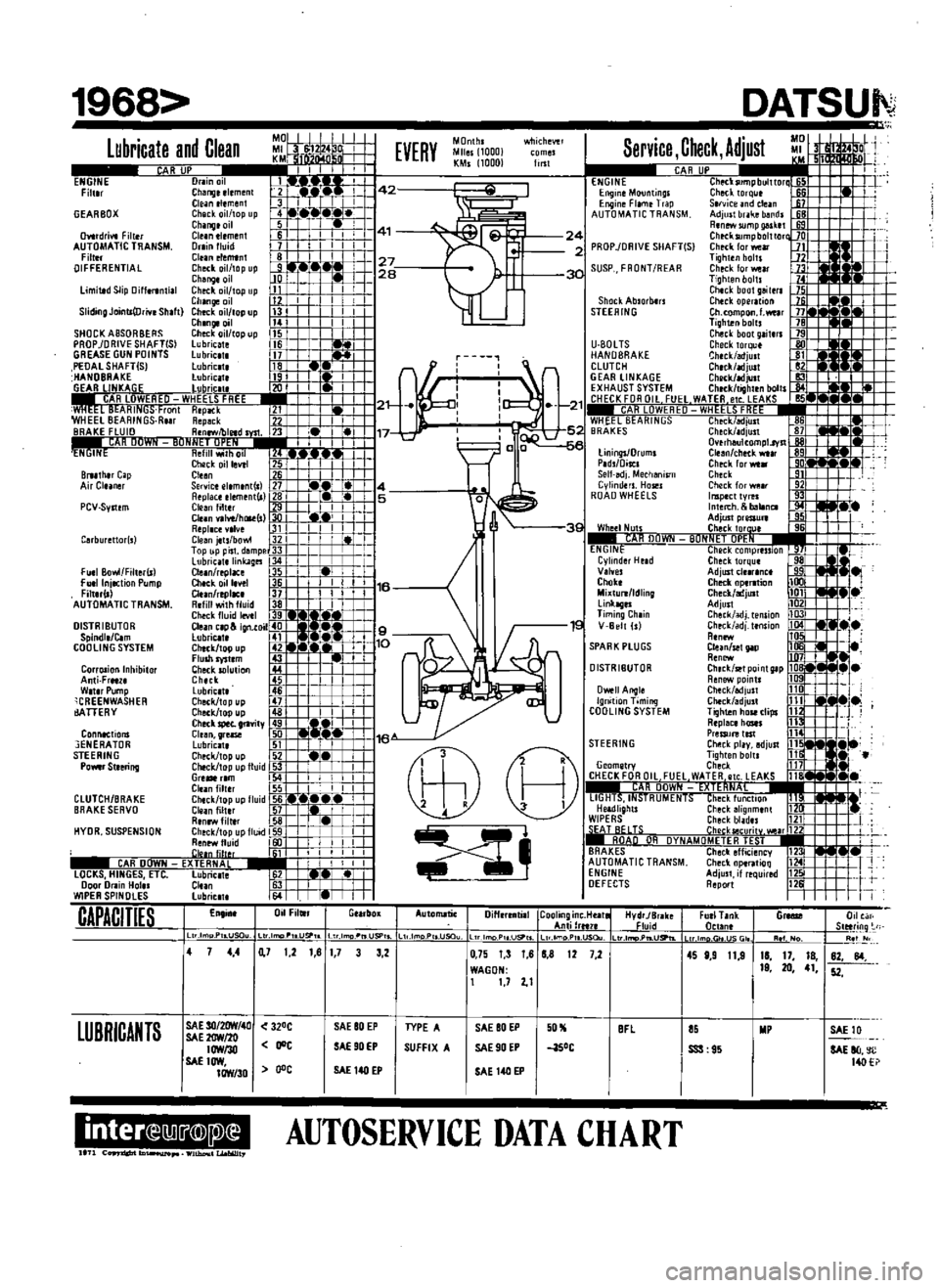
MO
MI
1224
D
I
KM
f
fMn
n
r
A
A
JP
I
I
T
I
I
I
Drain
ill
Changeelemenl
I
42
Cleantlement
3
I
II
r
I
Check
il
topup
4
I
Chinnloil
511
1
11
41
Gle
nelern
n
Ii
I
Orainlluid
7
I
I
I
I
Clunertmtn
81
1
I
I
I
I
I
27
Check
ailltop
up
Jf71
r
I
JIO
WI
28
Change
il
I
ill
limittdSlip
DiHlranti
1
Clleck
ilftopup
1J
I
I
I
Changelil
11
i
ill
ShdmgJolntt
Df
YlShlft
Check
11IIOpup
n
II
I
I
ChangeDl1
1
I
I
I
I
SHOCKASSORBERS
Check
Il
topup
5
PROP
DRIVESHAFTISI
lubncate
Hi
1
GREASE
GUN
POINTS
lubnCIl
it
PEOAlSHAFT
Sj
Lubrlc
te
18
HANDBHAKE
lubnc
1t
I
I
r
1
t
R
IINKAl
iF
luhncll
2u
I
I
i
I
ARlUWIORED
WHEELS
FREE
1m
I
I
i
1121
wHEE
L
tll
AHINli
ronl
HepitCk
211
t
f
WHEEl
BEARINGS
Rur
Repack
77
U
I
BRAKE
FLUID
R
nfWfbletd
1
I
lf
13
117
I
t
I
AH
UUWI
f
t1UN
11Itl
ih1tl
1
i
lcl
Check
oillevtl
B
l
r1i
BI1I1I1
r
Cap
Cleen
1ifj
j
I
Air
Cluner
Service
el
m
nt
l
J7
4
Replace
element
l
l
B
L
5
Cteenfilter
1
C
l
I
I
I
4
Clun
va
vellllR
I
I1
I
I
I
Repl
cH
lve
1
I
I
I
I
Cleen
jets
bOM
R
t
I
Top
liP
pisl
dempe
l
I
r
L
LlIbncatelinkages
I
I
L
Ctean
replace
5
j
I
Ch
ckoill
ve1
Ei
l
j
16
Clun
replac
n
11
R
fill
witll
fluid
38
I
Check
fluid
levll
IlL
t
I
CI
ign
toil
t
i
I
t
1
l
9
CheCk
top
u
p
10
Flulhryst
m
y
Cllecksolullon
44
Chltk
45
Lubrlc
tt
46
i
Clleck
top
up
L
L
Check
topup
4
aJdM
Cllltkspet
gl1vity
i
CI
en
gr
1S
liD
116
Lubriclt
1il
If
I
II
Clleck
topup
52
1
i
Chtck
topuplluid
3
I
I
Gre
rlm
4
I
1
I
I
I
Clunfiltlr
55
L
I
I
I
Chick
top
up
fluid
I6
w
W
e
I
ofi
Ldtir
1
Renewfiltlr
58
I
Check
topupflu
d
i91
i
I
i
Renrwfluid
I
I
I
I
I
ilinlil1r
11
I
I
I
I
I
I
CAR
DOWN
E
TERNAL
j
II
1
I
1
lOCKS
HINGES
Ell
Lubrictt
S21
r
1
el
L
Door
Dram
Hol
l
Clun
f
J
I
I
WIPER
SPINDLES
lubrictt
64
W
I
I
En
in
Dil
Filwr
GttrbOK
1968
Lubricate
and
Clean
ENGINE
Filt
r
GEARBOX
Dvttdrivt
Filt
r
AUTOMATIC
TRANSM
Filt
r
DIFFERENTIAL
PCV
Syllem
rburettor
s
FUll
Bowl
Filter
S1
Fu
llnjectionPump
Fittll
ll
AUTOMATIC
TRANSM
DISTRIBUTOR
Spindl
Ctm
COOLING
SYSTEM
CorrDlionlnllibitor
Anti
Frltl
W
t
rPump
CREENWASHER
ArrERY
Connections
3ENERATOR
STEERING
POMrStlering
CLUTCH
BRAKE
BRAKE
SERVO
HYDR
SUSPENSION
CAPACITIES
LUBRICANTS
Il
D
P
LUSClu
Service
Check
Adjust
CAR
UP
I
l
lletksumpbulttortM
1
Clled
rque
i6
ServiceJndclean
J1
Adjult
brake
bandl
tB
RtnMsumpgal
tt
fiS
Check
llJmpbnlttort
PROP
lOAIVE
SHAFT
S
Check
lor
wear
JJ
Tiglltenbolu
Jl
Check
tor
wear
n
Tiglltenboltl
Clllckbootgeiltrl
Clleckoperltion
Ch
CQmpon
l
welr
Tighten
bolts
Clleclbootgaiterl
Checktorqu
Gheck
edjult
Clllck
ljust
CIIRCk
adjult
Clleck
tighltnbolts
W
M
KSI
1
t
heCklMliiili
86
Check
ldjust
81
Overllllulcompl
rvll
Cleen
chltkwtlr
R9
Check
for
wear
0
Check
9
Checkforwp
lr
192
Il1Ipecttyrel
1IJ
Illte
II
blIl1nCl
Adjultpres
lure
Cllecktorul
liON
ET
OPE
l
heckcompression
Checktorqul
AdjUltclttr
nc
CheckoptTltion
Check
lIljLllt
AdjUlI
Clleck
alIj
tension
adj
t
nsion
I
Clun
selpp
jt1
Renew
Chetk
tPoint
tp
Renew
pointl
Check
6djult
110
J
Check
edjult
ill
i
ii
j
Tiglltenhoseclips
112
R
plece
lIastl
ill
PreSSIJ
test
114
1
STEERING
Clleek
play
adjust
ill
j
i
itl
e
Ti9htenboltl
ill
ii
Geometry
Check
U1L
H
CHECK
FOR
Oil
FUEL
WATER
etc
LEAKS
1181
I
I
R
DOWN
FXIE
HNA
11
1
1
lIGHTS
If
isfHUMt
NTS
Check
flll
C
lOn
f
3
Headlights
Checkllhgnmlnt
112Cr
WIPERS
Checkbladu
11111
J
TS
r
h
kIl
CII
I
Jrl7
iI
An
UH
OVNAUOMFTER
I
ST
I
BRAKES
CheCkemCienCY
1
I
AUTOMATIC
TRANSM
Clleek
op
rttioQ
T
ENGINE
Adjust
if
required
12
DEFECTS
Report
12
EVERY
MOnthl
Miles
1000
KMs
1000
lIBt
wtJichewl
ENGINE
EngmlMountings
Engine
Film
Trap
AUTOMATIC
TRANSM
24
2
30
SUSP
FRONT
REAR
Shock
Ablorb
rs
STEERING
1
21
5
1
c
e
U
80lTS
HANDBRAKE
CLUTCH
GEAR
LINKAGE
EXHAUST
SYSTEM
f
HFf
K
FOR
Oil
FllE
1
CAH
LUWI
RI
If
WHEEL
BEARINGS
BRAKES
UningsJDruml
Plds
Discl
Selhdj
Meclleni5l11
Cylinders
Hosel
ROAD
WHEELS
3S
Whe
1
Nun
AHllIIWN
ENGINE
Cyllnd
r
Held
Vllyes
Clloke
MiKtulli
ldling
linkagel
Timing
Ch
in
16
V
Belt
Is
SPARK
PLUGS
OISTRIBUTOR
Owell
Angle
Ignition
Timing
COOLING
SYSTEM
8
X
Automatic
Diffrrrntill
ICoolinginc
Ht
lltel
AntilrH1f
Ltr
lmoP
Ugo
IL
dmo
PII
U
Ou
HydrJBrak
Fluid
4
7
1
21
81
7
ULlma
II
USP
ULlmD
USP
L
L
tmoP
USQu
127
2
4
4
SAE
3O
2OW
411
SAE
lfrN
2fJ
IOWI3O
SAE1OW
IOW
30
320C
JOe
o
e
SAE80
EP
SAE90EP
SAE
140
EP
mmDIIIII
Ifn
c
ID
WIthDv
1
LI
obWt7
3
LtrJ
PtLUSPtL
3
2
0
75
T
3
1
8
B
8
WAGON
1
1
72
1
TYPE
A
SUFFIX
A
SAE80
EP
SAE90EP
SAE
140EP
0
aSoC
BFl
AUTOSERVICE
DATA
CHART
DATSUI
D
FurlT
nk
n
tln
G
0
Slltring
Re
I
lm
r
JSGI
11
1
No
4S
8
9
11
9
11
17
18
19
20
41
82
84
52
SSS
95
SAElll
SAE
80
c
14O