change time DATSUN 610 1969 Workshop Manual
[x] Cancel search | Manufacturer: DATSUN, Model Year: 1969, Model line: 610, Model: DATSUN 610 1969Pages: 171, PDF Size: 10.63 MB
Page 34 of 171
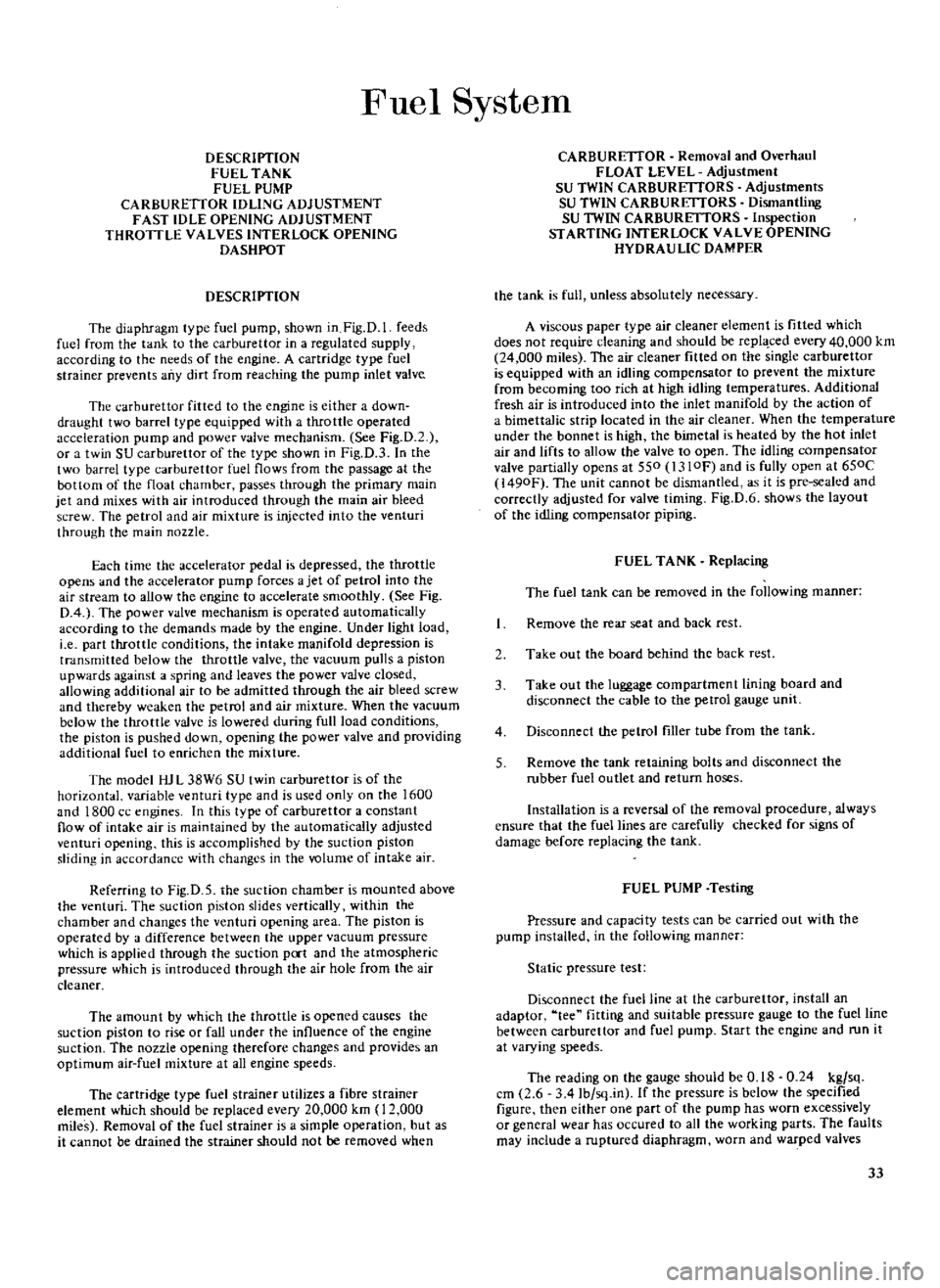
Fuel
System
DESCRIPTION
FUEL
TANK
FUEL
PUMP
CARBURETTOR
IDLING
ADJUSTMENT
FAST
IDLE
OPENING
ADJUSTMENT
THROTTLE
VALVES
INTERLOCK
OPENING
DASHPOT
DESCRIPTION
The
diaphragm
type
fuel
pump
shown
in
Fig
D
1
feeds
fuel
from
the
tank
to
the
carburettor
in
a
regulated
supply
according
to
the
needs
of
the
engine
A
cartridge
type
fuel
strainer
prevents
any
dirt
from
reaching
the
pump
inlet
valve
The
carburettor
fitted
to
the
engine
is
either
a
down
draught
two
barrel
type
equipped
with
a
throttle
operated
acceleration
pump
and
power
valve
mechanism
See
Fig
D
2
or
a
twin
SU
carburettor
of
the
type
shown
in
Fig
D
3
In
the
two
barrel
type
carburettor
fuel
flows
from
the
passage
at
the
bottom
of
the
float
chamber
passes
through
the
primary
main
jet
and
mixes
with
air
introduced
through
the
main
air
bleed
screw
The
petrol
and
air
mixture
is
injected
into
the
venturi
through
the
main
nozzle
Each
time
the
accelerator
pedal
is
depressed
the
throttle
opens
and
the
accelerator
pump
forces
a
jet
of
petrol
into
the
air
stream
to
allow
the
engine
to
accelerate
smoothly
See
Fig
0
4
The
power
valve
mechanism
is
operated
automatically
according
to
the
demands
made
by
the
engine
Under
light
load
i
e
part
throttle
conditions
the
intake
manifold
depression
is
transmitted
below
the
throttle
valve
the
vacuum
pulls
a
piston
upwards
against
a
spring
and
leaves
the
power
valve
closed
allowing
additional
air
to
be
admitted
through
the
air
bleed
screw
and
thereby
weaken
the
petrol
and
air
mixture
When
the
vacuum
below
the
throttle
vaJve
is
lowered
during
full
load
conditions
the
piston
is
pushed
down
opening
the
power
valve
and
providing
additional
fuel
to
enrichen
the
mixture
The
model
HJ
L
38W6
SU
twin
carburettor
is
of
the
horizontal
variable
venturi
type
and
is
used
only
on
the
1600
and
1800
cc
engines
In
this
type
of
carburettor
a
constant
flow
of
intake
air
is
maintained
by
the
automatically
adjusted
venturi
opening
this
is
accomplished
by
the
suction
piston
sliding
in
accordance
with
changes
in
the
volume
of
intake
air
Referring
to
Fig
D
5
the
suction
chamber
is
mounted
above
the
venturi
The
suction
piston
slides
vertically
within
the
chamber
and
changes
the
venturi
opening
area
The
piston
is
operated
by
a
difference
between
the
upper
vacuum
pressure
which
is
applied
through
the
suction
poct
and
the
atmospheric
pressure
which
is
introduced
through
the
air
hole
from
the
air
cleaner
The
amount
by
which
the
throttle
is
opened
causes
the
suction
piston
to
rise
or
fall
under
the
intluence
of
the
engine
suction
The
pozzle
opening
therefore
changes
and
provides
an
optimum
air
fuel
mixture
at
all
engine
speeds
The
cartridge
type
fuel
strainer
utilizes
a
fibre
strainer
element
which
should
be
replaced
every
20
000
km
12
000
miles
Removal
of
the
fuel
strainer
is
a
simple
operation
but
as
it
cannot
be
drained
the
strainer
should
not
be
removed
when
CARBURETIOR
Removal
and
Overhaul
FLOAT
LEVEL
Adjustment
SU
TWIN
CARBURmORS
Adjustments
SU
TWIN
CARBURmORS
Dismantling
SU
TWIN
CARBURETTORS
Inspection
STARTING
INTERLOCK
VALVE
OPENING
HYDRAULIC
DAMPER
the
tank
is
full
unless
absolutely
necessary
A
viscous
paper
type
air
cleaner
element
is
fitted
which
does
not
require
cleaning
and
should
be
repl
ced
every
40
000
km
24
000
miles
The
air
cleaner
fitted
on
the
single
carburettor
is
equipped
with
an
idling
compensator
to
prevent
the
mixture
from
becoming
too
rich
at
high
idling
temperatures
Additional
fresh
air
is
introduced
into
the
inlet
manifold
by
the
action
of
a
bimettalic
strip
located
in
the
air
cleaner
When
the
temperature
under
the
bonnet
is
high
the
bimetal
is
heated
by
the
hot
inlet
air
and
lifts
to
allow
the
valve
to
open
The
idling
compensator
valve
partially
opens
at
550
I310F
and
is
fully
open
at
650C
l490F
The
unit
cannot
be
dismantled
as
it
is
pre
sealed
and
correctly
adjusted
for
valve
timing
Fig
D
6
shows
the
layout
of
the
idling
compensator
piping
FUEL
TANK
Replacing
The
fuel
tank
can
be
removed
in
the
following
manner
Remove
the
rear
seat
and
back
rest
2
Take
out
the
board
behind
the
back
rest
3
Take
out
the
luggage
compartment
lining
board
and
disconnect
the
cable
to
the
petrol
gauge
unit
4
Disconnect
the
petrol
filler
tube
from
the
tank
5
Remove
the
tank
retaining
bolts
and
disconnect
the
rubber
fuel
outlet
and
return
hoses
Installation
is
a
reversal
of
the
removal
procedure
always
ensure
that
the
fuel
lines
arc
carefully
checked
for
signs
of
damage
before
replacing
the
tank
FUEL
PUMP
Testing
Pressure
and
capacity
tests
can
be
carried
out
with
the
pump
installed
in
the
following
manner
Static
pressure
test
Disconnect
the
fuel
line
at
the
carburettor
install
an
adaptor
tee
fitting
and
suitable
pressure
gauge
to
the
fuel
line
between
carburettor
and
fuel
pump
Start
the
engine
and
run
it
at
varying
speeds
The
reading
on
the
gauge
should
be
0
18
0
24
kg
sq
cm
2
6
34
Ib
sq
in
If
the
pressure
is
below
the
specified
figure
then
either
one
part
of
the
pump
has
worn
excessively
or
general
wear
has
occured
to
all
the
working
parts
The
faults
may
include
a
ruptured
diaphragm
worn
and
warped
valves
33
Page 40 of 171
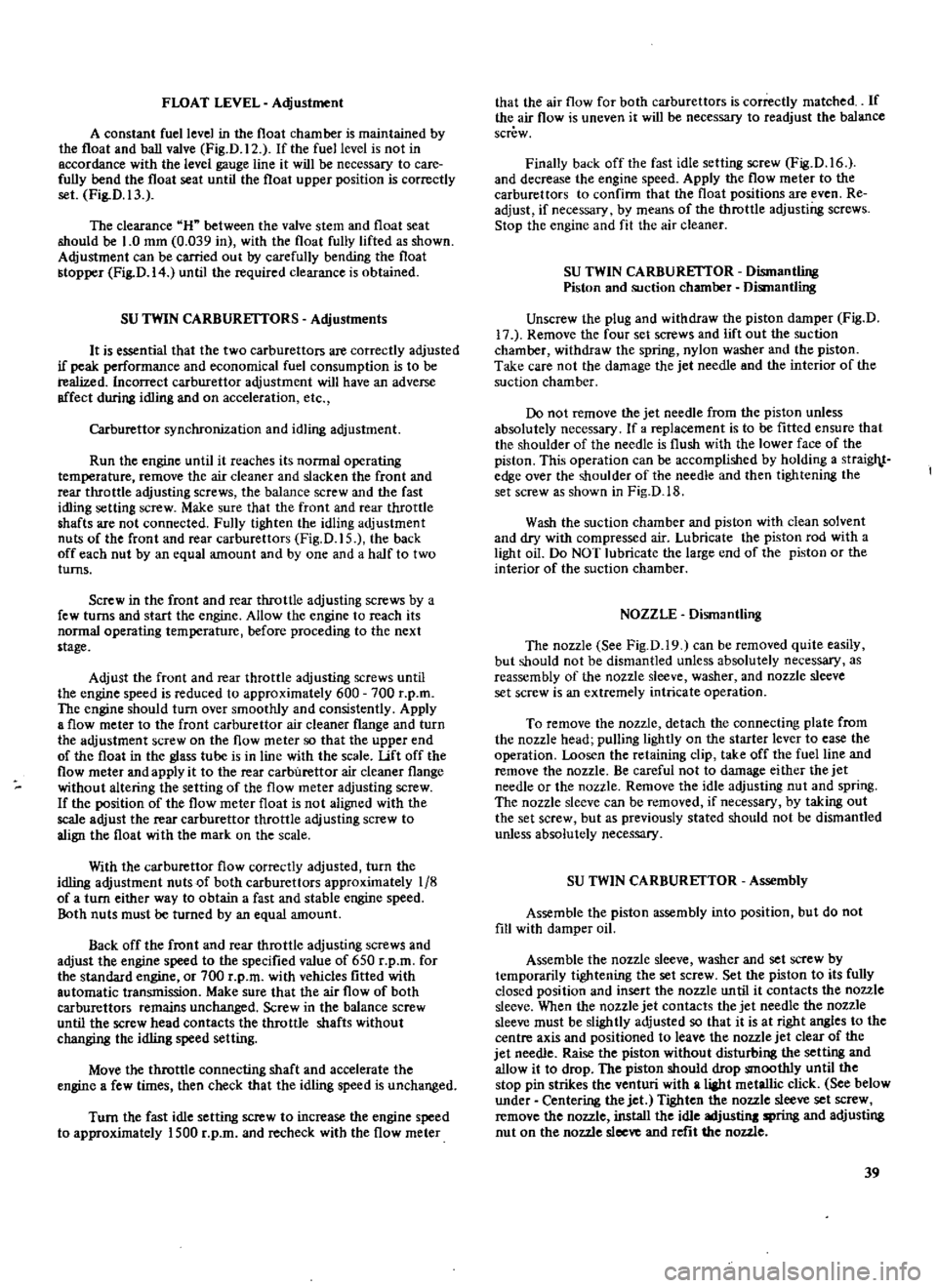
FLOAT
LEVEL
Adjustment
A
constant
fuel
level
in
the
float
chamber
is
maintained
by
the
float
and
ball
valve
Fig
D
12
If
the
fuel
level
is
not
in
accordance
with
the
level
gauge
line
it
will
be
necessary
to
care
fully
bend
the
float
seat
until
the
float
upper
position
is
correctly
set
Fig
D
13
The
clearance
H
between
the
valve
stem
and
float
seat
should
be
1
0
mm
0
039
in
with
the
float
fully
lifted
as
shown
Adjustment
can
be
carried
out
by
carefully
bending
the
float
stopper
Fig
D
14
until
the
required
clearance
is
obtained
SU
TWIN
CARBURETTORS
Adjustments
It
is
essential
that
the
two
carburettors
are
correctly
adjusted
if
peak
m3l1ce
and
economical
fuel
consumption
is
to
be
realized
Incorrect
carburettor
a
ljustment
will
have
an
adverse
affect
during
idling
and
on
acceleration
etc
Carburettor
synchronization
and
idling
adjustment
Run
the
engine
until
it
reaches
its
normal
operating
temperature
remove
the
air
cleaner
and
slacken
the
front
and
rear
throttle
adjusting
screws
the
balance
screw
and
the
fast
idling
setting
screw
Make
sure
that
the
front
and
rear
throttle
shafts
are
not
connected
Fully
tighten
the
idling
adjustment
nuts
of
the
front
and
rear
carburettors
Fig
D
15
the
back
off
each
nut
by
an
equal
amount
and
by
one
and
a
half
to
two
tUrns
Screw
in
the
front
and
rear
throttle
adjusting
screws
by
a
few
turns
and
start
the
engine
Allow
the
engine
to
reach
its
normal
operating
temperature
before
proceding
to
the
next
stage
Adjust
the
front
and
rear
throttle
adjusting
screws
until
the
engine
speed
is
reduced
to
approximately
600
700
r
p
m
The
engine
should
turn
over
smoothly
and
consistently
Apply
a
flow
meter
to
the
front
carburettor
air
cleaner
flange
and
turn
the
adjustment
screw
on
the
flow
meter
so
that
the
upper
end
of
the
float
in
the
glass
tube
is
in
line
with
the
scale
Uft
off
the
flow
meter
and
apply
it
to
the
rear
carburettor
air
cleaner
flange
without
altering
the
setting
of
the
flow
meter
adjusting
screw
If
the
position
of
the
flow
meter
float
is
not
aligned
with
the
scale
adjust
the
rear
carburettor
throttle
adjusting
screw
to
align
the
float
with
the
mark
on
the
scale
With
the
carburettor
flow
correctly
adjusted
turn
the
idling
adjustment
nuts
of
both
carburettors
approximately
1
8
of
a
turn
either
way
to
obtain
a
fast
and
stable
engine
speed
Both
nuts
must
be
turned
by
an
equal
amount
Back
off
the
front
and
rear
throttle
adjusting
screws
and
adjust
the
engine
speed
to
the
specified
value
of
650
r
p
m
for
the
standard
engine
or
700
r
p
m
with
vehicles
fitted
with
automatic
transmission
Make
sure
that
the
air
flow
of
both
carburettors
remains
unchanged
Screw
in
the
balance
screw
until
the
screw
head
contacts
the
throttle
shafts
without
changing
the
idling
speed
setting
Move
the
throttle
connecting
shaft
and
accelerate
the
engine
a
few
times
then
check
that
the
idling
speed
is
unchanged
Turn
the
fast
idle
setting
screw
to
increase
the
engine
speed
to
approximately
1500
r
p
m
and
recheck
with
the
flow
meter
that
the
air
flow
for
both
carburettors
is
correctly
matched
If
the
air
flow
is
uneven
it
will
be
necessary
to
readjust
the
balance
screw
Finally
back
off
the
fast
idle
setting
screw
Fig
D
16
and
decrease
the
engine
speed
Apply
the
flow
meter
to
the
carburettors
to
confirm
that
the
float
positions
are
even
Re
adjust
if
necessary
by
means
of
the
throttle
adjusting
screws
Stop
the
engine
and
fit
the
air
cleaner
SU
TWIN
CARBURETTOR
Dismantling
Piston
and
suction
chamber
Dismantling
Unscrew
the
plug
and
withdraw
the
piston
damper
Fig
D
17
Remove
the
four
set
screws
and
lift
out
the
suction
chamber
withdraw
the
spring
nylon
washer
and
the
piston
Take
care
not
the
damage
the
jet
needle
and
the
interior
of
the
suction
chamber
Do
not
remove
the
jet
needle
from
the
piston
unless
absolutely
necessary
If
a
replacement
is
to
be
fitted
ensure
that
the
shoulder
of
the
needle
is
flush
with
the
lower
face
of
the
piston
This
operation
can
be
accomplished
by
holding
a
strai
edge
over
the
shoulder
of
the
needle
and
then
tightening
the
set
screw
as
shown
in
Fig
D
18
Wash
the
suction
chamber
and
piston
with
dean
solvent
and
dry
with
compressed
air
Lubricate
the
piston
rod
with
a
light
oil
Do
NOT
lubricate
the
large
end
of
the
piston
or
the
interior
of
the
suction
chamber
NOZZLE
Dismantling
The
nozzle
See
Fig
D
19
can
be
removed
quite
easily
but
should
not
be
dismantled
unless
absolutely
necessary
as
reassembly
of
the
nozzle
sleeve
washer
and
nozzle
sleeve
set
screw
is
an
extremely
intricate
operation
To
remove
the
nozzle
detach
the
connecting
plate
from
the
nozzle
head
pulling
lightly
on
the
starter
lever
to
ease
the
operation
Loosen
the
retaining
clip
take
off
the
fuel
line
and
remove
the
nozzle
Be
careful
not
to
damage
either
the
jet
needle
oc
the
nozzle
Remove
the
idle
adjusting
nut
and
spring
The
nozzle
sleeve
can
be
removed
if
necessary
by
taking
out
the
set
screw
but
as
previously
stated
should
not
be
dismantled
unless
absolutely
necessary
SU
TWIN
CARBUREfTOR
Assembly
Assemble
the
piston
assembly
into
position
but
do
not
fill
with
damper
oil
Assemble
the
nozzle
sleeve
washec
and
set
screw
by
temporarily
tightening
the
set
screw
Set
the
piston
to
its
fully
closed
position
and
insert
the
nozzle
until
it
contacts
the
nozzle
sleeve
When
the
nozzle
jet
contacts
the
jet
needle
the
nozzle
sleeve
must
be
slightly
adjusted
so
that
it
is
at
right
angles
to
the
centre
axis
and
positioned
to
leave
the
nozzle
jet
clear
of
the
jet
needle
Raise
the
piston
without
disturbing
the
setting
and
allow
it
to
drop
The
piston
should
drop
smoothly
until
the
stop
pin
strikes
the
venturi
with
a
liaht
metallic
click
See
below
under
Centering
the
jet
Tighten
the
nozzle
sleeve
set
screw
remove
the
nozzle
install
the
idle
adjustinJ
spring
and
adjusting
nut
on
the
nozzle
sleeve
and
refit
the
nozzle
39
Page 118 of 171
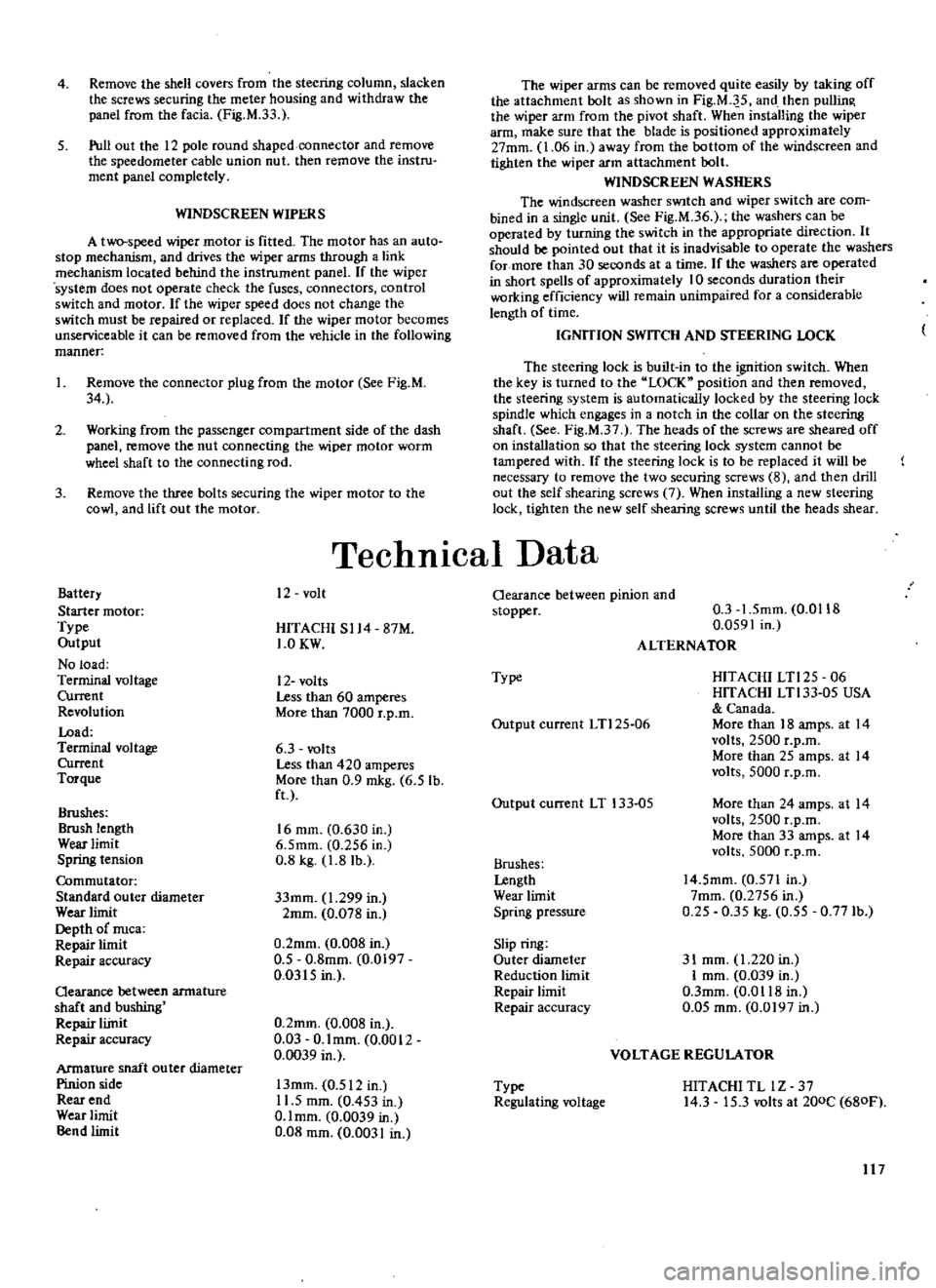
4
Remove
the
shell
covers
from
the
steering
column
slacken
the
screws
securing
the
meter
housing
and
withdraw
the
panel
from
the
facia
Fig
M
33
5
Pull
out
the
12
pole
round
shaped
connector
and
remove
the
speedometer
cable
union
nut
then
remove
the
instru
ment
panel
completely
WINDSCREEN
WIPERS
A
two
speed
wiper
motor
is
fitted
The
motor
has
an
auto
stop
mechanism
and
drives
the
wiper
arms
through
a
link
mechanism
located
behind
the
instrument
panel
If
the
wiper
system
does
not
operate
check
the
fuses
connectors
control
switch
and
motor
If
the
wiper
speed
does
not
change
the
switch
must
be
repaired
or
replaced
If
the
wiper
motor
becomes
unserviceable
it
can
be
removed
from
the
vehicle
in
the
fOllowing
manner
I
Remove
the
connector
plug
from
the
motor
See
Fig
M
34
2
Working
from
the
passenger
compartment
side
of
the
dash
panel
remove
the
nut
connecting
the
wiper
motor
worm
wheel
shaft
to
the
connecting
rod
3
Remove
the
three
bolts
securing
the
wiper
motor
to
the
cowl
and
lift
out
the
motor
Battery
Starter
motor
Type
Output
No
load
Terminal
voltage
Current
Revolution
Load
Terminal
voltage
Current
Torque
Brushes
Brush
length
Wear
limit
Spring
tension
Commutator
Standard
outer
diameter
Wear
limit
Depth
of
nuca
Repair
limit
Repair
accuracy
Qearance
between
armature
shaft
and
bushing
Repair
liinit
Repair
accuracy
Armature
shaft
ou
ter
diameter
Pinion
side
Rear
end
Wear
limit
Bend
limit
The
wiper
arms
can
be
removed
quite
easily
by
taking
off
the
attachment
bolt
as
shown
in
Fig
M
J
5
and
then
pullin
the
wiper
arm
from
the
pivot
shaft
When
installing
the
wiper
arm
make
sure
that
the
blade
is
positioned
approximately
27mm
1
06
in
away
from
the
bottom
of
the
windscreen
and
tighten
the
wiper
arm
attachment
bolt
WINDSCREEN
WASHERS
The
windscreen
washer
SWItch
and
wiper
switch
are
com
bined
in
a
single
unit
See
Fig
M
36
the
washers
can
be
operated
by
turning
the
switch
in
the
appropriate
direction
It
should
be
pointed
out
that
it
is
inadvisable
to
operate
the
washers
for
more
than
30
seconds
at
a
time
If
the
washers
are
operated
in
short
spells
of
approximately
10
seconds
duration
their
working
efficiency
will
remain
unimpaired
for
a
considerable
length
of
time
IGNITION
SWITCH
AND
STEERING
LOCK
The
steering
lock
is
built
in
to
the
goition
switch
When
the
key
is
turned
to
the
LOCK
position
and
then
removed
the
steering
system
is
automatically
locked
by
the
steering
lock
spindle
which
engages
in
a
notch
in
the
collar
on
the
steering
shaft
See
Fig
M
37
The
heads
of
the
screws
are
sheared
off
on
installation
so
that
the
steering
lock
system
cannot
be
tampered
with
If
the
steering
lock
is
to
be
replaced
it
will
be
necessary
to
remove
the
two
securing
screws
8
and
then
drill
out
the
self
shearing
screws
7
When
installing
a
new
steering
lock
tighten
the
new
self
shearing
screws
until
the
heads
shear
TechnICal
Data
12
volt
HITACHI
S114
87M
1
0KW
12
volts
Less
than
60
amperes
More
than
7000
r
p
m
6
3
volts
Less
than
420
amperes
More
than
0
9
mkg
6
5
lb
ft
16
mm
0
630
in
6
5mm
0
256
in
0
8
kg
1
8
lb
33mm
1
299
in
2mm
0
078
in
0
2mm
0
008
in
0
5
0
8mm
0
0197
0
0315
in
0
2mm
0
008
in
0
03
O
lmm
0
0012
0
0039
in
13mm
0
512
in
11
5
mm
0
453
in
O
lmm
0
0039
in
0
08
mm
0
0031
in
Oearance
between
pinion
and
stopper
0
3
1
5mm
0
0118
0
0591
in
ALTERNATOR
Type
HITACHI
LTl25
06
HITACHI
LTl33
05
USA
Canada
More
than
18
amps
at
14
volts
2500
r
p
m
More
than
25
amps
at
14
volts
5000
r
p
m
Output
current
LTl25
06
Output
current
LT
133
05
More
than
24
amps
at
14
volts
2500
r
p
m
More
than
33
amps
at
14
volts
5000
r
p
m
Brushes
Lengtb
Wear
limit
Spring
pressure
14
5mm
0
571
In
7mm
0
2756
in
0
25
0
35
kg
0
55
0
771b
Slip
ring
Outer
diameter
Reduction
limit
Repair
limit
Repair
accuracy
31
mm
1
220
in
I
mm
0
039
in
O
3mm
0
0118
in
0
05
mm
0
0197
in
VOLTAGE
REGULATOR
Type
Regulating
voltage
HITACHI
TL
lZ
37
14
3
15
3
volts
at
200C
680F
117
Page 156 of 171
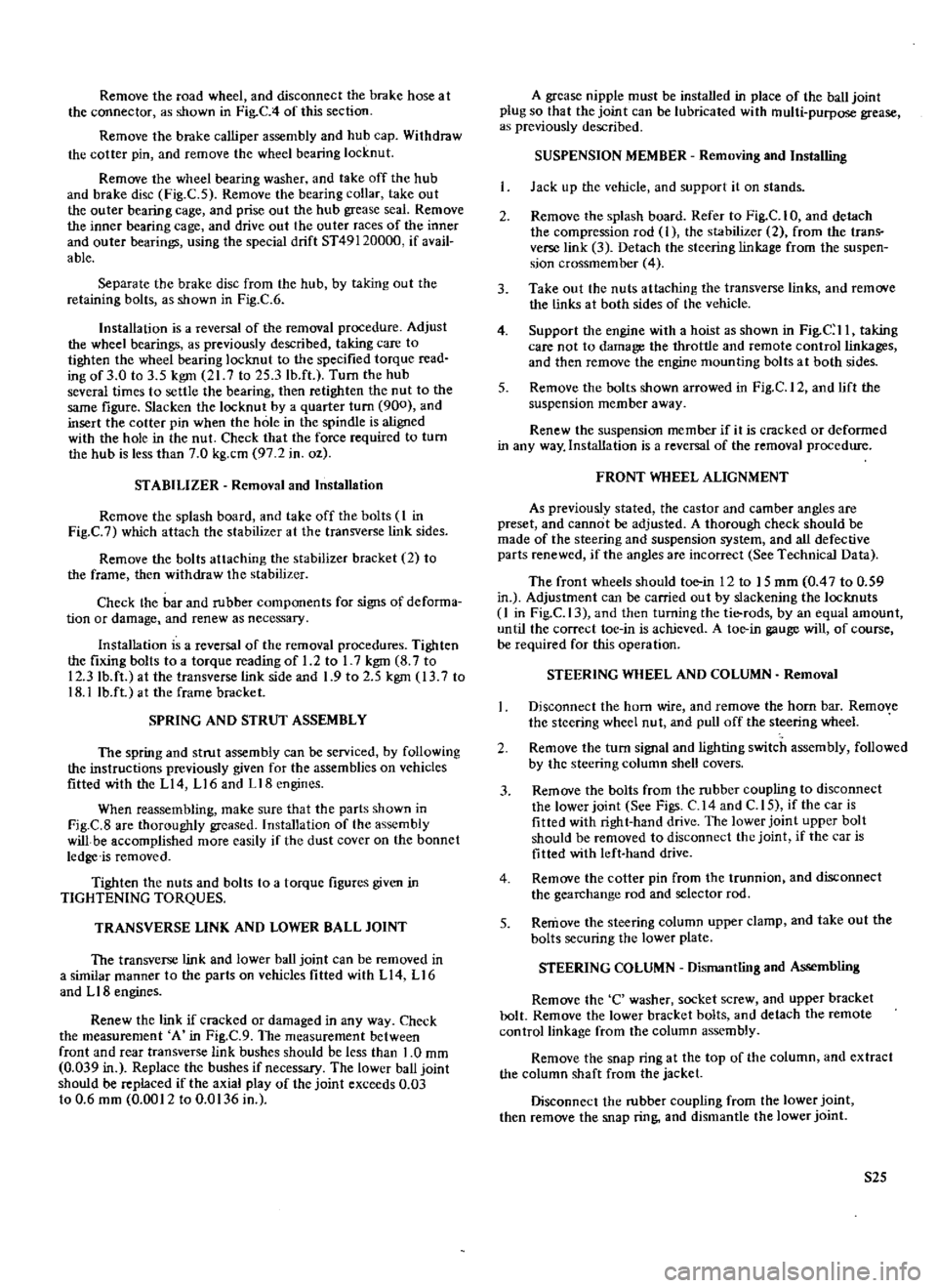
Remove
the
road
wheel
and
disconnect
the
brake
hose
at
the
connector
as
shown
in
Fig
C
4
of
this
section
Remove
the
brake
calliper
assembly
and
hub
cap
Withdraw
the
cotter
pin
and
remove
the
wheel
bearing
locknut
Remove
the
wheel
bearing
washer
and
take
off
the
hub
and
brake
disc
Fig
C
5
Remove
the
bearing
collar
take
out
the
outer
bearing
cage
and
prise
out
the
hub
grease
seal
Remove
the
inner
bearing
cage
and
drive
out
the
outer
races
of
the
inner
and
outer
bearings
using
the
special
drift
ST49120000
if
avail
able
Separate
the
brake
disc
from
the
hub
by
taking
out
the
retaining
bolts
as
shown
in
Fig
C
6
Installation
is
a
reversal
of
the
removal
procedure
Adjust
the
wheel
bearings
as
previously
described
taking
care
to
tighten
the
wheel
bearing
locknut
to
the
specified
torque
read
ing
of
3
0
to
3
5
kgm
21
7
to
25
3lb
ft
Turn
the
hub
several
times
to
settle
the
bearing
then
retighten
the
nut
to
the
same
figure
Slacken
the
locknut
by
a
quarter
turn
900
and
insert
the
cotter
pin
when
the
hole
in
the
spindle
is
aligned
with
the
hole
in
the
nut
Check
that
the
force
required
to
turn
the
hub
is
less
than
7
0
kg
cm
97
2
in
oz
STABILIZER
Removal
and
Installation
Remove
the
splash
board
and
take
off
the
bolts
I
in
Fig
C
7
which
attach
the
stabilizer
at
the
transverse
link
sides
Remove
the
bolts
attaching
the
stabilizer
bracket
2
to
the
frame
then
withdraw
the
stabilizer
Check
the
bar
and
rubber
components
for
signs
of
deforma
tion
or
damage
and
renew
as
necessary
Installation
is
a
reversal
of
the
removal
procedures
Tighten
the
fixing
bolts
to
a
torque
reading
of
1
2
to
I
7
kgm
8
7
to
12
3
lb
ft
at
the
transverse
link
side
and
1
9
to
2
5
kgm
13
7
to
18
llb
ft
at
the
frame
bracket
SPRING
AND
STRUT
ASSEMBLY
The
spring
and
strut
assembly
can
be
serviced
by
following
the
instructions
previously
given
for
the
assemblies
on
vehicles
fitted
with
the
L14
L16
and
Ll8engines
When
reassembling
make
sure
that
the
parts
shown
in
Fig
C
8
are
thomughly
greased
Installation
of
the
assembly
will
be
accomplished
more
easily
if
the
dust
cover
on
the
bonnet
ledge
is
removed
Tighten
the
nuts
and
bolts
to
a
torque
figures
given
in
TIGHTENING
TORQUES
TRANSVERSE
LINK
AND
LOWER
BALL
JOINT
The
transverse
link
and
lower
ball
joint
can
be
removed
in
a
similar
manner
to
the
parts
on
vehicles
fitted
with
L
14
L
16
and
L
18
engines
Renew
the
link
if
cracked
or
damaged
in
any
way
Check
the
measurement
A
in
Fig
C
9
The
measurement
between
front
and
rear
transverse
link
bushes
should
be
less
than
1
0
mm
0
039
in
Replace
the
bushes
if
necessary
The
lower
ball
joint
should
be
replaced
if
the
axial
play
of
the
joint
exceeds
0
03
to
0
6
mm
0
0012
to
0
0136
in
A
grease
nipple
must
be
installed
in
place
of
the
ball
joint
plug
so
that
the
joint
can
be
lubricated
with
multi
purpose
grease
as
previously
described
SUSPENSION
MEMBER
Removing
and
Installing
Jack
up
the
vehicle
and
support
it
on
stands
2
Remove
the
splash
board
Refer
to
Fig
C
I
0
and
detach
the
compression
rod
I
the
stabilizer
2
from
the
trans
verse
link
3
Detach
the
steering
linkage
from
the
suspen
sion
crossmember
4
3
Take
out
the
nuts
attaching
the
transverse
links
and
remove
the
links
at
both
sides
of
the
vehicle
4
Support
the
engine
with
a
hoist
as
shown
in
Fig
C
II
taking
care
not
to
damage
the
throttle
and
remote
control
linkages
and
then
remove
the
engine
mounting
bolts
at
both
sides
5
Remove
the
bolts
shown
arrowed
in
Fig
C
12
and
lift
the
suspension
member
away
Renew
the
suspension
member
if
it
is
cracked
or
deformed
in
any
way
Installation
is
a
reversal
of
the
removal
procedure
FRONT
WHEEL
ALIGNMENT
As
previously
stated
the
castor
and
camber
angles
are
preset
and
cannot
be
adjusted
A
thorough
check
should
be
made
of
the
steering
and
suspension
system
and
all
defective
parts
renewed
if
the
angles
are
incorrect
See
Technical
Data
The
front
wheels
should
toe
in
12
to
15
mm
0
4
7
to
0
59
in
Adjustment
can
be
carried
out
by
slackening
the
locknuts
1
in
Fig
C
13
and
then
turning
the
tie
rods
by
an
equal
amount
until
the
correct
toe
in
is
achieved
A
toe
in
gauge
will
of
course
be
required
for
this
operation
STEERING
WHEEL
AND
COLUMN
Removal
Disconnect
the
horn
wire
and
remove
the
horn
bar
Remove
the
steering
wheel
nut
and
pull
off
the
steering
wheel
2
Remove
the
turn
signal
and
lighting
switch
assembly
followed
by
the
steering
column
shell
covers
3
Remove
the
bolts
from
the
rubber
coupling
to
disconnect
the
lower
joint
See
Figs
C
14
and
C
I
5
if
the
car
is
fitted
with
right
hand
drive
The
lower
joint
upper
bolt
should
be
removed
to
disconnect
the
joint
if
the
car
is
fitted
with
left
hand
drive
4
Remove
the
cotter
pin
from
the
trunnion
and
disconnect
the
gearchange
rod
and
selector
rod
5
Remove
the
steering
column
upper
clamp
and
take
out
the
bolts
securing
the
lower
plate
STEERING
COLUMN
Dismantling
and
Assembling
Remove
the
C
washer
socket
screw
and
upper
bracket
bolt
Remove
the
lower
bracket
bolts
and
detach
the
remote
control
linkage
from
the
column
assembly
Remove
the
snap
ring
at
the
top
of
the
column
and
extract
the
column
shaft
from
the
jacket
Disconnect
the
rubber
coupling
from
the
lower
joint
then
remove
the
snap
ring
and
dismantle
the
lower
joint
S25