lug pattern DATSUN 610 1969 Workshop Manual
[x] Cancel search | Manufacturer: DATSUN, Model Year: 1969, Model line: 610, Model: DATSUN 610 1969Pages: 171, PDF Size: 10.63 MB
Page 18 of 171
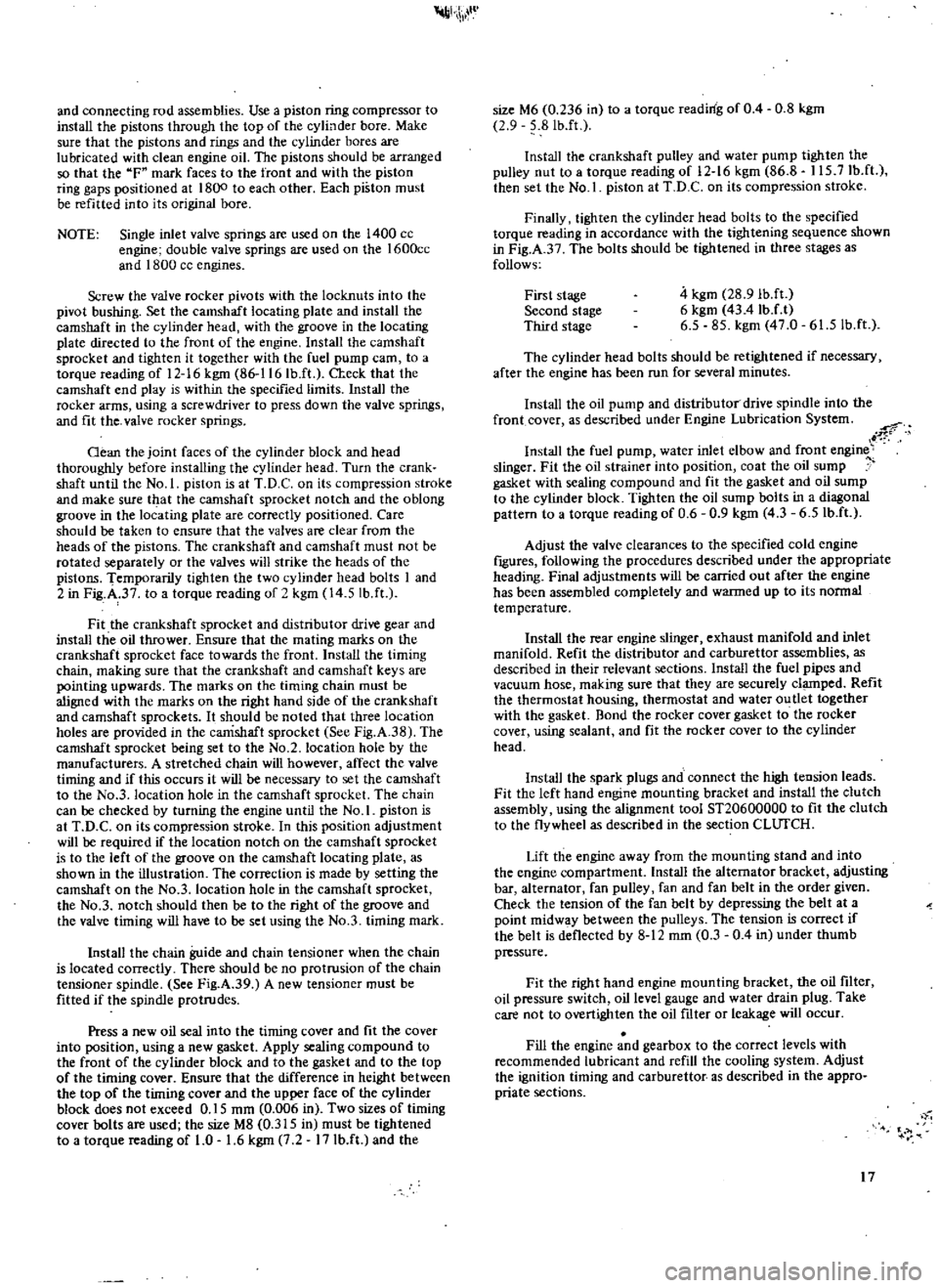
h
W
and
connecting
rod
assemblies
Use
a
piston
ring
compressor
to
install
the
pistons
through
the
top
of
the
cylbder
bore
Make
sure
that
the
pistons
and
rings
and
the
cylinder
bores
are
lubricated
with
clean
engine
oil
The
pistons
should
be
arranged
so
that
the
F
mark
faces
to
the
front
and
with
the
piston
ring
gaps
positioned
at
1800
to
each
other
Each
piston
must
be
refitted
into
its
original
bore
NOTE
Single
inlet
valve
springs
are
used
on
the
1400
cc
engine
double
valve
springs
are
used
on
the
1600cc
and
1800
cc
engines
Screw
the
valve
rocker
pivots
with
the
locknuts
into
the
pivot
bushing
Set
the
camshaft
locating
plate
and
install
the
camshaft
in
the
cylinder
head
with
the
groove
in
the
locating
plate
directed
to
the
front
of
the
engine
Install
the
camshaft
sprocket
and
tighten
it
together
with
the
fuel
pump
earn
to
a
torque
reading
of
12
16
kgm
86
116
IbJt
a
eck
that
the
camshaft
end
play
is
within
the
specified
limits
Install
the
rocker
arms
using
a
screwdriver
to
press
down
the
valve
springs
and
fit
the
valve
rocker
springs
Gean
the
joint
faces
of
the
cylinder
block
and
head
thoroughly
before
installing
the
cylinder
head
Turn
the
crank
shaft
until
the
No
1
piston
is
at
T
D
C
on
its
compression
stroke
and
make
sure
that
the
camshaft
sprocket
notch
and
the
oblong
groove
in
the
locating
plate
are
correctly
positioned
Care
should
be
taken
to
ensure
that
the
valves
are
clear
from
the
heads
of
the
pistons
The
crankshaft
and
camshaft
must
not
be
rotated
separately
or
the
valves
will
strike
the
heads
of
the
pistons
Temporarily
tighten
the
two
cylinder
head
bolts
1
and
2
in
Fig
A
37
to
a
torque
reading
of
2
kgm
14
5
lb
ft
Fit
the
crankshaft
sprocket
and
distributor
drive
gear
and
install
the
oil
thrower
Ensure
that
the
mating
marks
on
the
crankshaft
sprocket
face
towards
the
front
Install
the
timing
chain
making
sure
that
the
crankshaft
and
camshaft
keys
are
XJinting
upwards
The
marks
on
the
timing
chain
must
be
aligned
with
the
marks
on
the
right
hand
side
of
the
crankshaft
and
camshaft
sprockets
It
should
be
noted
that
three
location
holes
are
provided
in
the
camshaft
sprocket
See
Fig
A
38
The
camshaft
sprocket
being
set
to
the
No
2
location
hole
by
the
manufacturers
A
stretched
chain
will
however
affect
the
valve
timing
and
if
this
occurs
it
will
be
necessary
to
set
the
camshaft
to
the
No
3
location
hole
in
the
camshaft
sprocket
The
chain
can
be
checked
by
turning
the
engine
until
the
No
1
piston
is
at
T
D
C
on
its
compression
stroke
In
this
position
adjustment
will
be
required
if
the
location
notch
on
the
camshaft
sprocket
is
to
the
left
of
the
groove
on
the
camshaft
locating
plate
as
shown
in
the
illustration
The
correction
is
made
by
setting
the
camshaft
on
the
No
3
location
hole
in
the
camshaft
sprocket
the
No
3
notch
should
then
be
to
the
right
of
the
groove
and
the
valve
timing
will
have
to
be
set
using
the
No
3
timing
mark
Install
the
chain
guide
and
chain
tensioner
when
the
chain
is
located
correctly
There
should
be
no
protrusion
of
the
chain
tensioner
spindle
See
Fig
A
39
A
new
tensioner
must
be
fitted
if
the
spindle
protrudes
Press
a
new
oil
seal
into
the
timing
cover
and
fit
the
cover
into
position
using
a
new
gasket
Apply
sealing
compound
to
the
front
of
the
cylinder
block
and
to
the
gasket
and
to
the
top
of
the
timing
cover
Ensure
that
the
difference
in
height
between
the
top
of
the
timing
cover
and
the
upper
face
of
the
cylinder
block
does
not
exceed
0
15
mm
0
006
in
Two
sizes
of
timing
cover
bolts
are
used
the
size
M8
0
315
in
must
be
tightened
to
a
torque
reading
of
1
0
1
6
kgm
7
2
17
Ib
ft
and
the
size
M6
0
236
in
to
a
torque
reading
of
0
4
0
8
kgm
2
9
81b
ft
Install
the
crankshaft
pulley
and
water
pump
tighten
the
pulley
nut
to
a
torque
reading
of
12
16
kgm
86
8
115
7Ib
ft
then
set
the
No
1
piston
at
T
D
C
on
its
compression
stroke
Finally
tighten
the
cylinder
head
bolts
to
the
specified
torque
reading
in
accordance
with
the
tightening
sequence
shown
in
Fig
A
3
The
bolts
should
be
tightened
in
three
stages
as
follows
First
stage
Second
stage
Third
stage
4
kgm
28
9
lbJt
6
kgm
43
4
IbJ
t
6
5
85
kgm
47
0
61
5lb
ft
The
cylinder
head
bolts
should
be
retightened
if
necessary
after
the
engine
has
been
run
for
several
minutes
Install
the
oil
pump
and
distributor
drive
spindle
into
the
front
cover
as
described
under
Engine
Lubrication
System
r
rf
i
Install
the
fuel
pump
water
inlet
elbow
and
front
engine
slinger
Fit
the
oil
strainer
into
position
coat
the
oil
sump
gasket
with
sealing
compound
and
fit
the
gasket
and
oil
sump
to
the
cylinder
block
Tighten
the
oil
sump
bolts
in
a
diagonal
pattern
to
a
torque
reading
of
0
6
0
9
kgm
4
3
6
5
IbJt
Adjust
the
valve
clearances
to
the
specified
cold
engine
ftgures
following
the
procedures
described
under
the
appropriate
heading
Final
adjustments
will
be
carried
out
after
the
engine
has
been
assembled
completely
and
warmed
up
to
its
nonnal
temperature
Install
the
rear
engine
slinger
exhaust
manifold
and
inlet
manifold
Refit
the
distributor
and
carburettor
assemblies
as
described
in
their
relevant
sections
Install
the
fuel
pipes
and
vacuum
hose
making
sure
that
they
are
securely
cl
ped
Refit
the
thermostat
housing
thermostat
and
water
outlet
together
with
the
gasket
Bond
the
rocker
cover
gasket
to
the
rocker
cover
using
sealant
and
fit
the
rocker
cover
to
the
cylinder
head
Install
the
spark
plugs
and
connect
the
high
tension
leads
Fit
the
left
hand
engine
mounting
bracket
and
install
the
clutch
assembly
using
the
alignment
tool
ST20600000
to
fit
the
clutch
to
the
flywheel
as
described
in
the
section
ClUfCR
Lift
the
engine
away
from
the
mounting
stand
and
into
the
engine
compartment
Install
the
alternator
bracket
adjusting
bar
alternator
fan
pulley
fan
and
fan
belt
in
the
order
given
Check
the
tension
of
the
fan
belt
by
depressing
the
belt
at
a
point
midw
y
between
the
pulleys
The
tension
is
correct
if
the
belt
is
deflected
by
8
12
mm
0
3
0
4
in
under
thumb
pressure
Fit
the
right
hand
engine
mounting
bracket
the
oil
filter
oil
pressure
switch
oil
level
gauge
and
water
drain
plug
Take
care
not
to
overtighten
the
oil
nIter
or
leakage
will
occur
Fill
the
engine
and
gearbox
to
the
correct
levels
with
recommended
lubricant
and
refill
the
cooling
system
Adjust
the
ignition
timing
and
carburettor
as
described
in
the
appro
priate
sections
17
Page 44 of 171
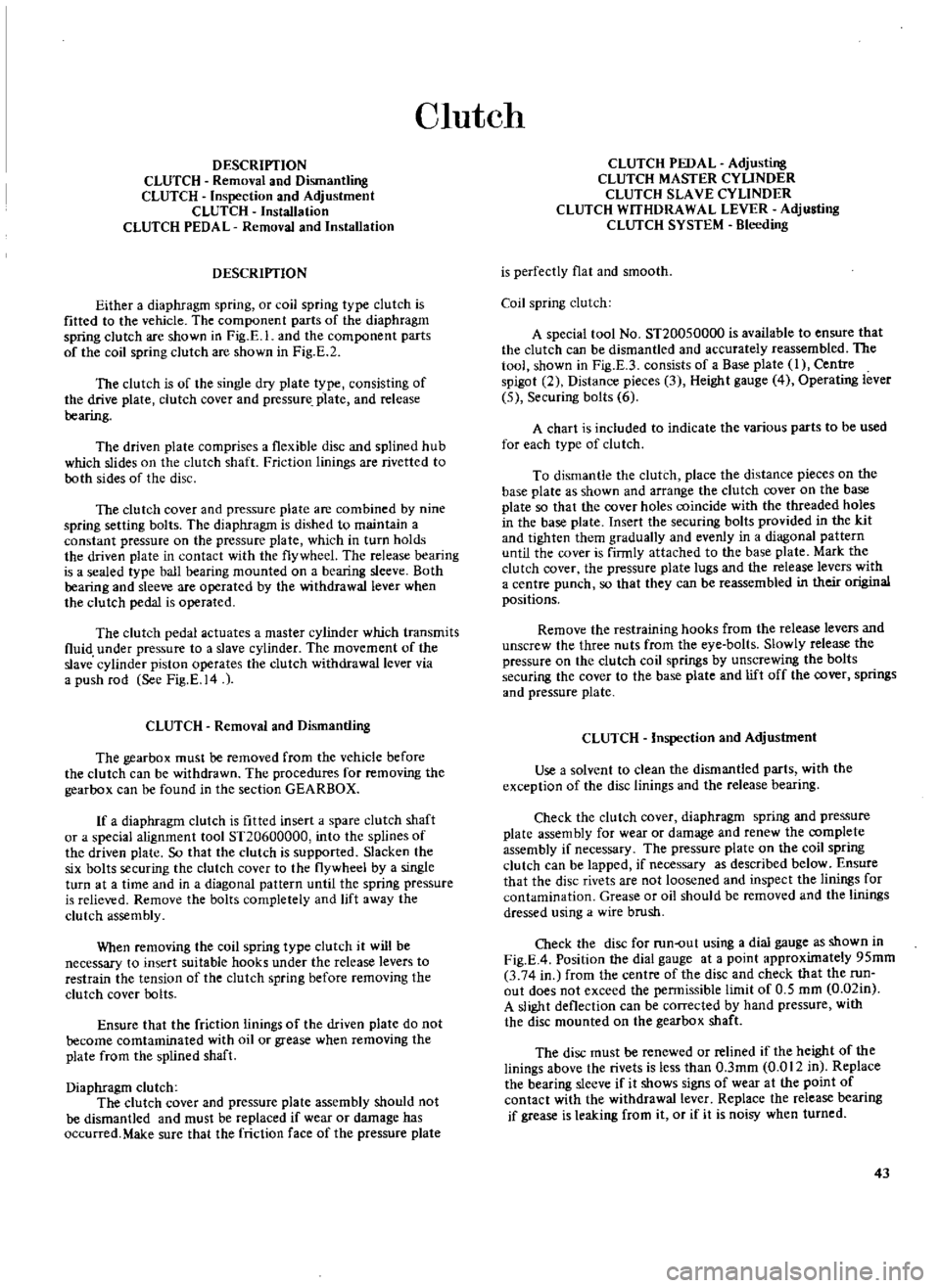
Clutch
DESCRIPTION
CLUTCH
Removal
and
Dismantling
CLUTCH
Inspection
and
Adjustment
CLUTCH
Installation
CLUTCH
PEDAL
Removal
and
Installation
DESCRIPTION
Either
a
diaphragm
spring
or
coil
spring
type
clutch
is
fitted
to
the
vehicle
The
component
parts
of
the
diaphragm
spring
clutch
are
shown
in
Fig
E
l
and
the
component
parts
of
the
coil
spring
clutch
are
shown
in
Fig
E
2
The
clutch
is
of
the
single
dry
plate
type
consisting
of
the
drive
plate
clutch
coveT
and
pressure
plate
and
release
bearing
The
driven
plate
comprises
a
flexible
disc
and
splined
hub
which
slides
on
the
clutch
shaft
Friction
linings
are
rivetted
to
both
sides
of
the
disc
The
clutch
cover
and
pressure
plate
are
combined
by
nine
spring
setting
bolts
The
diaphragm
is
dished
to
maintain
a
constant
pressure
on
the
pressure
plate
which
in
turn
holds
the
driven
plate
in
contact
with
the
flywheel
The
release
bearing
is
a
sealed
type
ball
bearing
mounted
on
a
bearing
sleeve
Both
bearing
and
sleeve
are
operated
by
the
withdrawalleveT
when
the
clutch
pedal
is
operated
The
clutch
pedal
actuates
a
master
cylinder
which
transmits
fluid
under
pressure
to
a
slave
cylinder
The
movement
of
the
slave
cylinder
piston
operates
the
clutch
withdrawal
lever
via
a
push
rod
See
Fig
E
14
CLUTCH
Removal
and
Dismantling
The
gearbox
must
be
removed
from
the
vehicle
before
the
clutch
can
be
withdrawn
The
procedures
for
removing
the
gearbox
can
be
found
in
the
section
GEARBOX
If
a
diaphragm
clutch
is
fitted
insert
a
spare
clutch
shaft
or
a
special
alignment
tool
ST20600000
into
the
splines
of
the
driven
plate
So
that
the
dutch
is
supported
Slacken
the
six
bolts
securing
the
clutch
cover
to
the
flywheel
by
a
single
turn
at
a
time
and
in
a
diagonal
pattern
until
the
spring
pressure
is
relieved
Remove
the
bolts
completely
and
lift
away
the
clutch
assembly
When
removing
the
coil
spring
type
clutch
it
will
be
necessary
to
insert
suitable
hooks
under
the
release
levers
to
restrain
the
tension
of
the
clutch
spring
before
removing
the
clutch
cover
lx
llts
Ensure
that
the
friction
linings
of
the
driven
plate
do
not
become
comtaminated
with
oil
or
grease
when
removing
the
plate
from
the
splined
shaft
Diaphragm
clutch
The
clutch
cover
and
pressure
plate
assembly
should
not
be
dismantled
and
must
be
replaced
if
wear
or
damage
has
occurred
Make
sure
that
the
friction
face
of
the
pressure
plate
CLUTCH
PEDAL
Adjusting
CLUTCH
MASTER
CYLINDER
CLUTCH
SLAVE
CYLINDER
CLUTCH
WITHDRAWAL
LEVER
Adjusting
CLUTCH
SYSTEM
Bleeding
is
perfectly
flat
and
smooth
Coil
spring
clutch
A
special
tool
No
ST200S0000
is
available
to
ensure
that
the
clutch
can
be
dismantled
and
accurately
reassembled
The
tool
shown
in
Fig
E
3
consists
of
a
Base
plate
I
Centre
spigot
2
Distance
pieces
3
Height
gauge
4
Operating
lever
5
Securing
bolts
6
A
chart
is
included
to
indicate
the
various
parts
to
be
used
for
each
type
of
clutch
To
dismantle
the
clutch
place
the
distance
pieces
on
the
base
plate
as
shown
and
arrange
the
clutch
cover
on
the
base
plate
so
that
the
cover
holes
coincide
with
the
threaded
holes
in
the
base
plate
Insert
the
securing
bolts
provided
in
the
kit
and
tighten
them
gradually
and
evenly
in
a
diagonal
pattern
until
the
cover
is
firmly
attached
to
the
base
plate
Mark
the
clutch
cover
the
pressure
plate
lugs
and
the
release
levers
with
a
centre
punch
so
that
they
can
be
reassembled
in
their
original
positions
Remove
the
restraining
hooks
from
the
release
levers
and
unscrew
the
three
nuts
from
the
eye
bolts
Slowly
release
the
pressure
on
the
clutch
coil
springs
by
unscrewing
the
bolts
securing
the
cover
to
the
base
plate
and
lift
off
the
cover
springs
and
pressure
plate
CLUTCH
Inspection
and
Adjustment
Use
a
solvent
to
clean
the
dismantled
parts
with
the
exception
of
the
disc
linings
and
the
release
bearing
Check
the
clutch
cover
diaphragm
spring
and
pressure
plate
assembly
for
wear
or
damage
and
renew
the
complete
assembly
if
necessary
The
pressure
plate
on
the
coil
spring
clutch
can
be
lapped
if
necessary
as
described
below
Ensure
that
the
disc
rivets
are
not
loosened
and
inspect
the
linings
for
contamination
Grease
or
oil
should
be
removed
and
the
linings
dressed
using
a
wire
brush
Check
the
disc
for
run
ut
using
a
dial
gauge
as
shown
in
Fig
E
4
Position
the
dial
gauge
at
a
point
approximately
9Smm
3
74
in
from
the
centre
of
the
disc
and
check
that
the
run
out
does
not
exceed
the
permissible
limit
of
0
5
mm
0
02in
A
slight
deflection
can
be
corrected
by
hand
pressure
with
the
disc
mounted
on
the
gearbox
shaft
The
disc
must
be
renewed
or
relined
if
the
height
of
the
linings
above
the
rivets
is
less
than
0
3mm
0
012
in
Replace
the
bearing
sleeve
if
it
shows
signs
of
wear
at
the
point
of
contact
with
the
withdrawal
lever
Replace
the
release
bearing
if
grease
is
leaking
from
it
or
if
it
is
noisy
when
turned
43
Page 46 of 171
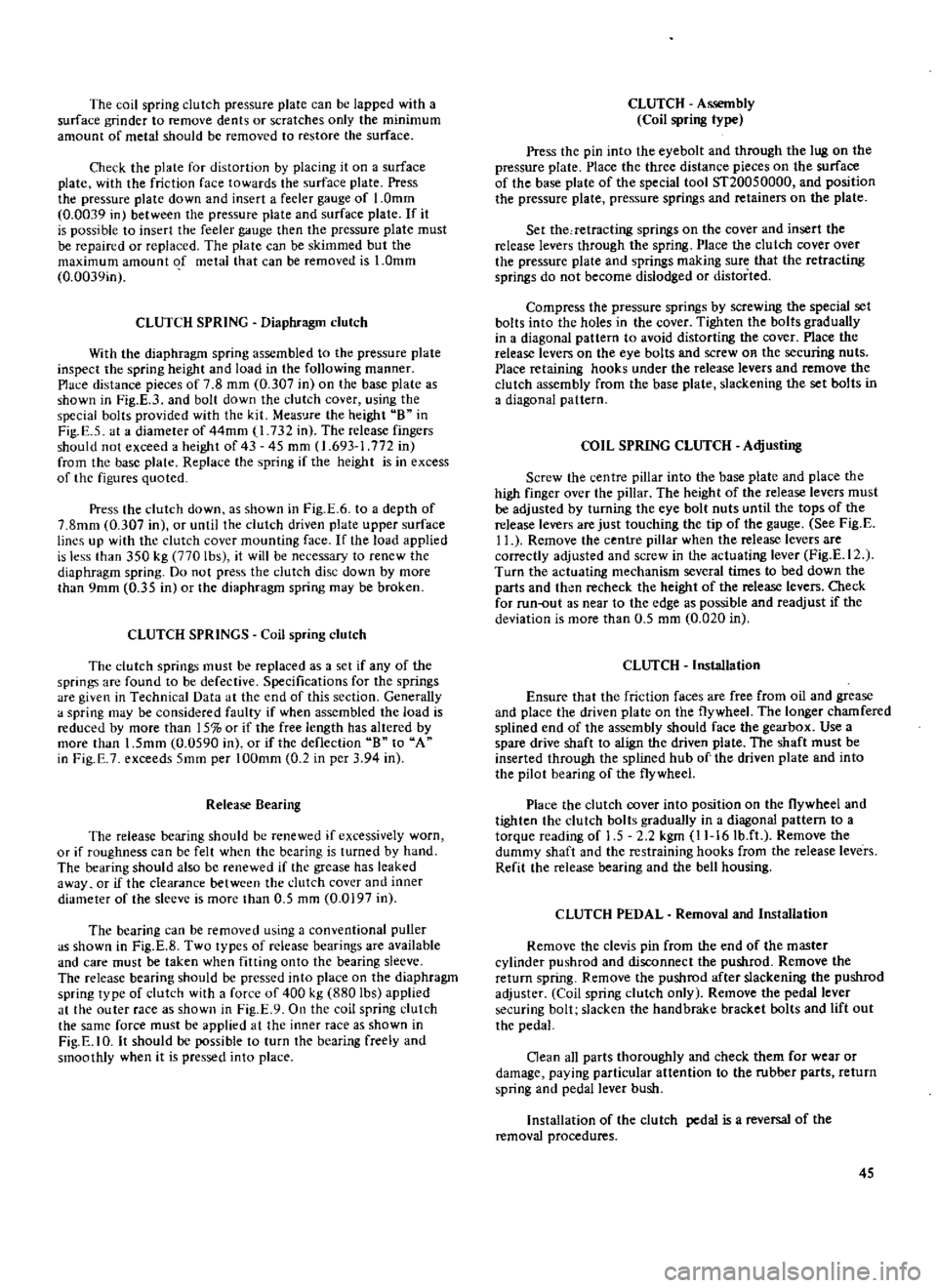
The
coil
spring
clutch
pressure
plate
can
be
lapped
with
a
surface
grinder
to
remove
dents
or
scratches
only
the
minimum
amount
of
metal
should
be
removed
to
restore
the
surface
Check
the
plate
for
distortion
by
placing
it
on
a
surface
plate
with
the
friction
face
towards
the
surface
plate
Press
the
pressure
plate
down
and
insert
a
feeler
gauge
of
1
0mm
0
0039
in
between
the
pressure
plate
and
surface
plate
If
it
is
possible
to
insert
the
feeler
gauge
then
the
pressure
plate
must
be
repaired
or
replaced
The
plate
can
be
skimmed
but
the
maximum
amount
of
metal
that
can
be
removed
is
1
0mm
0
0039in
CLUTCH
SPRING
Diaphragm
clutch
With
the
diaphragm
spring
assembled
to
the
pressure
plate
inspect
the
spring
height
and
load
in
the
following
manner
Place
distance
pieces
of
7
8
mm
0
307
in
on
the
base
plate
as
shown
in
Fig
E
3
and
bolt
down
the
clutch
cover
using
the
special
bolts
provided
with
the
kit
Meas
Jre
the
height
B
in
Fig
E
5
at
a
diameter
of
44mm
1
732
in
The
release
fingers
should
not
exceed
a
height
of
43
45
mm
1
693
1
772
in
from
the
base
plate
Replace
the
spring
if
the
height
is
in
excess
of
the
figures
quoted
Press
the
dutch
down
as
shown
in
Fig
E
6
to
a
depth
of
7
8mm
0
307
in
or
until
the
clutch
driven
plate
upper
surface
lines
up
with
the
clutch
cover
mounting
face
If
the
load
applied
is
less
than
350
kg
770
lbs
it
will
be
necessary
to
renew
the
diaphragm
spring
Do
not
press
the
clutch
disc
down
by
more
than
9mm
0
35
in
or
the
diaphragm
spring
may
be
broken
CLUTCH
SPRINGS
Coil
spring
clutch
The
clutch
springs
must
be
replaced
as
a
set
if
any
of
the
springs
are
found
to
be
defective
Specifications
for
the
springs
are
given
in
Technical
Data
at
the
end
of
this
section
Generally
a
spring
may
be
considered
faulty
if
when
assembled
the
load
is
reduced
by
more
than
15
or
if
the
free
length
has
altered
by
more
than
1
5mm
0
0590
in
or
if
the
deflection
B
to
A
in
Fig
E
7
exceeds
5mm
per
100mm
0
2
in
per
3
94
in
Release
Bearing
The
release
bearing
should
be
renewed
if
excessively
worn
or
if
roughness
can
be
felt
when
the
bearing
is
turned
by
hand
The
bearing
should
also
be
renewed
if
the
grease
has
leaked
away
or
if
the
clearance
between
the
clutch
cover
and
inner
diameter
of
the
sleeve
is
more
than
0
5
mm
0
0197
in
The
bearing
can
be
removed
using
a
conventional
puller
as
shown
in
Fig
E
8
Two
types
of
release
bearings
are
available
and
care
must
be
taken
when
fitting
onto
the
bearing
sleeve
The
release
bearing
should
be
pressed
into
place
on
the
diaphragm
spring
type
of
clutch
with
a
force
of
400
kg
880
lbs
applied
at
the
outer
race
as
shown
in
Fig
E
9
On
the
coil
spring
clutch
the
same
force
must
be
applied
at
the
inner
race
as
shown
in
Fig
E
IO
It
should
be
possible
to
turn
the
bearing
freely
and
smoothly
when
it
is
pressed
into
place
CLUTCH
Assembly
Coil
spring
type
Press
the
pin
into
the
eyebolt
and
through
the
lug
on
the
pressure
plate
Place
the
three
distance
pieces
on
the
surface
of
the
base
plate
of
the
special
tool
ST20050000
and
position
the
pressure
plate
pressure
springs
and
retainers
on
the
plate
Set
the
retracting
springs
on
the
cover
and
insert
the
release
levers
through
the
spring
Place
the
clutch
cover
over
the
pressure
plate
and
springs
making
sure
that
the
retracting
springs
do
not
become
dislodged
or
distorted
Compress
the
pressure
springs
by
screwing
the
special
set
bolts
into
the
holes
in
the
cover
Tighten
the
bolts
gradually
in
a
diagonal
pattern
to
avoid
distorting
the
cover
Place
the
release
levers
on
the
eye
bolts
and
screw
OR
the
securing
nuts
Place
retaining
hooks
under
the
release
levers
and
remove
the
clutch
assembly
from
the
base
plate
slackening
the
set
bolts
in
a
diagonal
pattern
COIL
SPRING
CLUTCH
Adjusting
Screw
the
centre
pillar
into
the
base
plate
and
place
the
high
finger
over
the
pillar
The
height
of
the
release
levers
must
be
adjusted
by
turning
the
eye
bolt
nuts
until
the
tops
of
the
release
levers
are
just
touching
the
tip
of
the
gauge
See
Fig
E
11
Remove
the
centre
pillar
when
the
release
levers
are
correctly
adjusted
and
screw
in
the
actuating
lever
Fig
E
12
Turn
the
actuating
mechanism
several
times
to
bed
down
the
parts
and
then
recheck
the
height
of
the
release
levers
Check
for
run
out
as
near
to
the
edge
as
possible
and
readjust
if
the
deviation
is
more
than
0
5
mrn
0
020
in
CLUTCH
InsWlation
Ensure
that
the
friction
faces
are
free
from
oil
and
grease
and
place
the
driven
plate
on
the
flywheel
The
longer
chamfered
splined
end
of
the
assembly
should
face
the
gearbox
Use
a
spare
drive
shaft
to
align
the
driven
plate
The
shaft
must
be
inserted
through
the
splined
hub
of
the
driven
plate
and
into
the
pilot
bearing
of
the
flywheel
Place
the
clutch
cover
into
position
on
the
flywheel
and
tighten
the
dutch
bolts
gradually
in
a
diagonal
pattern
to
a
torque
reading
of
1
5
2
2
kgm
11
16Ib
ft
Remove
the
dummy
shaft
and
the
restraining
hooks
from
the
release
levers
Refit
the
release
bearing
and
the
bell
housing
CLUTCH
PEDAL
Removal
and
Installation
Remove
the
clevis
pin
from
the
end
of
the
master
cylinder
pushrod
and
disconnect
the
pushrod
Remove
the
return
spring
Remove
the
pushrod
after
slackening
the
pushrod
adjuster
Coil
spring
clutch
only
Remove
the
pedal
lever
securing
bolt
slacken
the
handbrake
bracket
bolts
and
lift
out
the
pedal
Clean
all
parts
thoroughly
and
check
them
for
wear
or
damage
paying
particular
attention
to
the
rubber
parts
return
spring
and
pedal
lever
bush
Installation
of
the
clutch
pedal
is
a
reversal
of
the
removal
procedures
45
Page 64 of 171
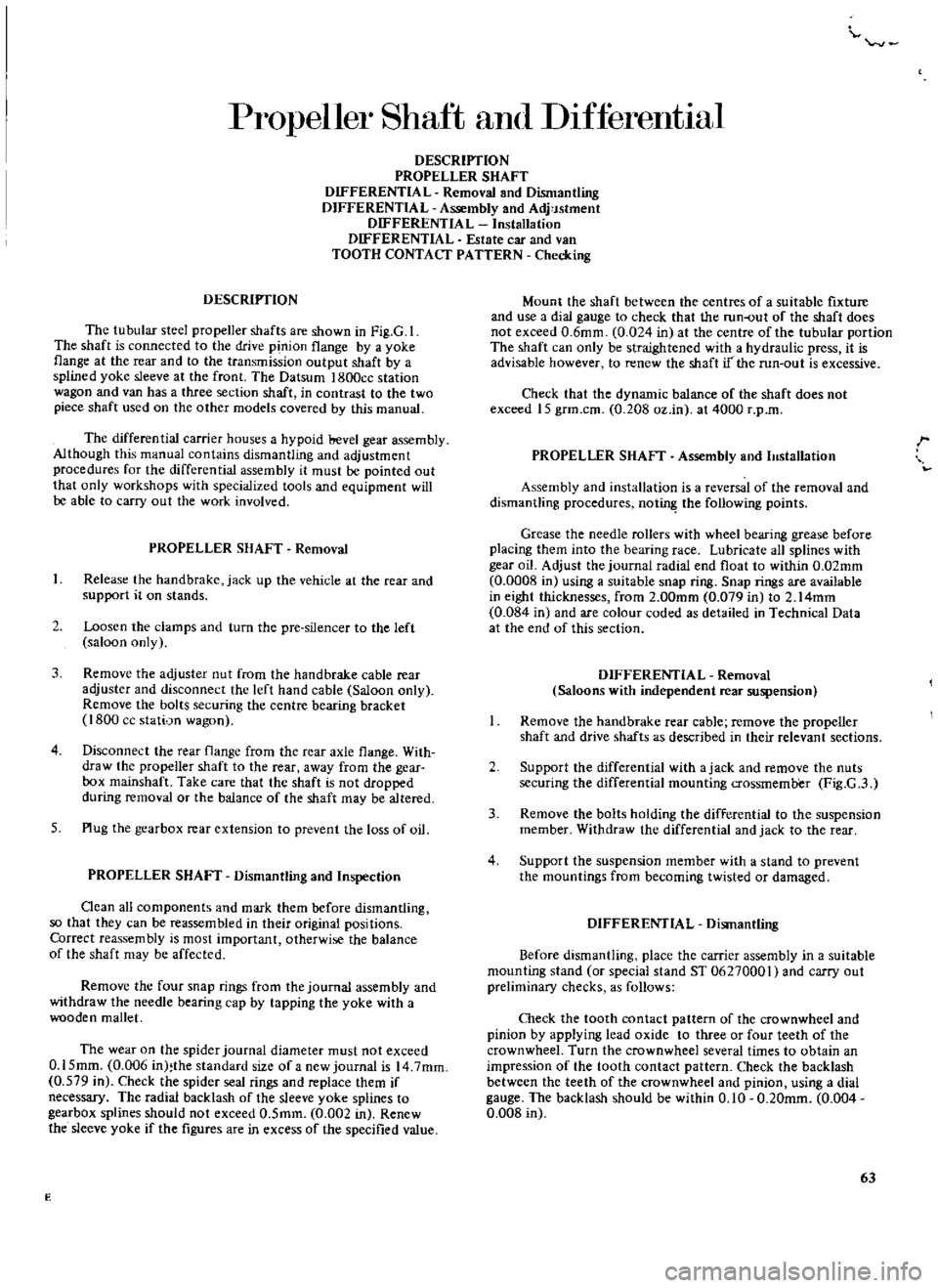
Propeller
Shaft
and
DIfferentIaJ
DESCRIPTION
PROPELLER
SHAFT
DIFFERENTIAL
Removal
and
Dismantling
DIFFERENTIAL
Assembly
and
Adj
Jstment
DIFFERENTIAL
Installation
DIFFERENTIAL
Estate
car
and
van
TOOTH
CONTACT
PATTERN
Checking
DESCRIPTION
The
tubular
steel
propeller
shafts
are
shown
in
Fig
G
1
The
shaft
is
connected
to
the
drive
pinion
flange
by
a
yoke
flange
at
the
rear
and
to
the
transmission
output
shaft
by
a
splined
yoke
sleeve
at
the
front
The
Datsum
I800ce
station
wagon
and
van
has
a
three
section
shaft
in
contrast
to
the
two
piece
shaft
used
on
the
other
models
covered
by
this
manual
The
differential
carrier
houses
a
hypoid
bevel
gear
assembly
Although
this
manual
contains
dismantling
and
adjustment
procedures
for
the
differential
assembly
it
must
be
pointed
out
that
only
workshops
with
specialized
tools
and
equipment
will
be
able
to
carry
out
the
work
involved
PROPELLER
SHAFT
Removal
1
Release
the
hand
brake
jack
up
the
vehicle
at
the
fear
and
support
it
on
stands
2
Loosen
the
clamps
and
turn
the
pre
silencer
to
the
left
saloon
only
3
Remove
the
adjuster
nut
from
the
handbrake
cable
rear
adjuster
and
disconnect
the
left
hand
cable
Saloon
only
Remove
the
bolts
securing
the
centre
bearing
bracket
1800
cc
stati
n
wagon
4
Disconnect
the
fear
flange
from
the
rear
axle
flange
With
draw
the
propeller
shaft
to
the
rear
away
from
the
gear
box
mainshaft
Take
care
that
the
shaft
is
not
dropped
during
removal
or
the
balance
of
the
shaft
may
be
altered
5
Plug
the
gearbox
rear
extension
to
prevent
the
loss
of
oil
PROPELLER
SHAFT
Dismantling
and
Inspection
Oean
all
components
and
mark
them
before
dismantling
so
that
they
can
be
reassembled
in
their
original
positions
Correct
reassembly
is
most
important
otherwise
the
balance
of
the
shaft
may
be
affected
Remove
the
four
snap
rings
from
the
journal
assembly
and
withdraw
the
needle
bearing
cap
by
tapping
the
yoke
with
a
wooden
mallet
The
wear
on
the
spider
journal
diameter
must
not
exceed
0
15mm
0
006
in
the
standard
size
of
a
new
journal
is
14
7mm
0
579
in
Check
the
spider
seal
rings
and
replace
them
if
necessary
The
radial
backlash
of
the
sleeve
yoke
splines
to
gearbox
splines
should
not
exceed
0
5mm
0
002
in
Renew
the
sleeve
yoke
if
the
figures
are
in
excess
of
the
specified
value
E
Mount
the
shaft
between
the
centres
of
a
suitable
fixture
and
use
a
dial
gauge
to
check
that
the
run
out
of
the
shaft
does
not
exceed
0
6mm
0
024
in
at
the
centre
of
the
tubular
portion
The
shaft
can
only
be
straightened
with
a
hydraulic
press
it
is
advisable
however
to
renew
the
shaft
if
the
run
out
is
excessive
Check
that
the
dynamic
balance
of
the
shaft
does
not
exceed
15
grm
cm
0
208
oz
in
at
4000
r
p
m
PROPELLER
SHAFT
Assembly
and
11Istallation
r
Assembly
and
installation
is
a
reversal
of
the
removal
and
dismantling
procedures
not
the
following
points
Grease
the
needle
rollers
with
wheel
bearing
grease
before
placing
them
into
the
bearing
race
Lubricate
all
splines
with
gear
oil
Adjust
the
journal
radial
end
float
to
within
0
02mm
0
0008
in
using
a
suitable
snap
ring
Snap
rings
are
available
in
eight
thicknesses
from
2
00mm
0
079
in
to
2
14mm
0
084
in
and
are
colour
coded
as
detailed
in
Technical
Data
at
the
end
of
this
section
DIFFERENTIAL
Removal
Saloons
with
independent
rear
suspension
Remove
the
hand
brake
rear
cable
remove
the
propeller
shaft
and
drive
shafts
as
described
in
their
relevant
sections
2
Support
the
differential
with
ajack
and
remove
the
nuts
securing
the
differential
mounting
crossmemb
er
Fig
G
3
3
Remove
the
bolts
holding
the
differential
to
the
suspension
member
Withdraw
the
differential
and
jack
to
the
rear
4
Support
the
suspension
member
with
a
stand
to
prevent
the
mountings
from
becoming
twisted
or
damaged
DIFFERENTIAL
Dismantling
Before
dismantling
place
the
carrier
assembly
in
a
suitable
mounting
stand
or
special
stand
ST
06270001
and
carry
out
preliminary
checks
as
follows
Check
the
tooth
contact
pattern
of
the
crownwheel
and
pinion
by
applying
lead
oxide
to
three
or
four
teeth
of
the
crownwheel
Turn
the
crownwheel
several
times
to
obtain
an
impression
of
the
tooth
contact
pattern
Check
the
backlash
between
the
teeth
of
the
crownwheel
and
pinion
using
a
dial
gauge
The
backlash
should
be
within
0
10
0
20mm
0
004
0
008
in
63
Page 82 of 171
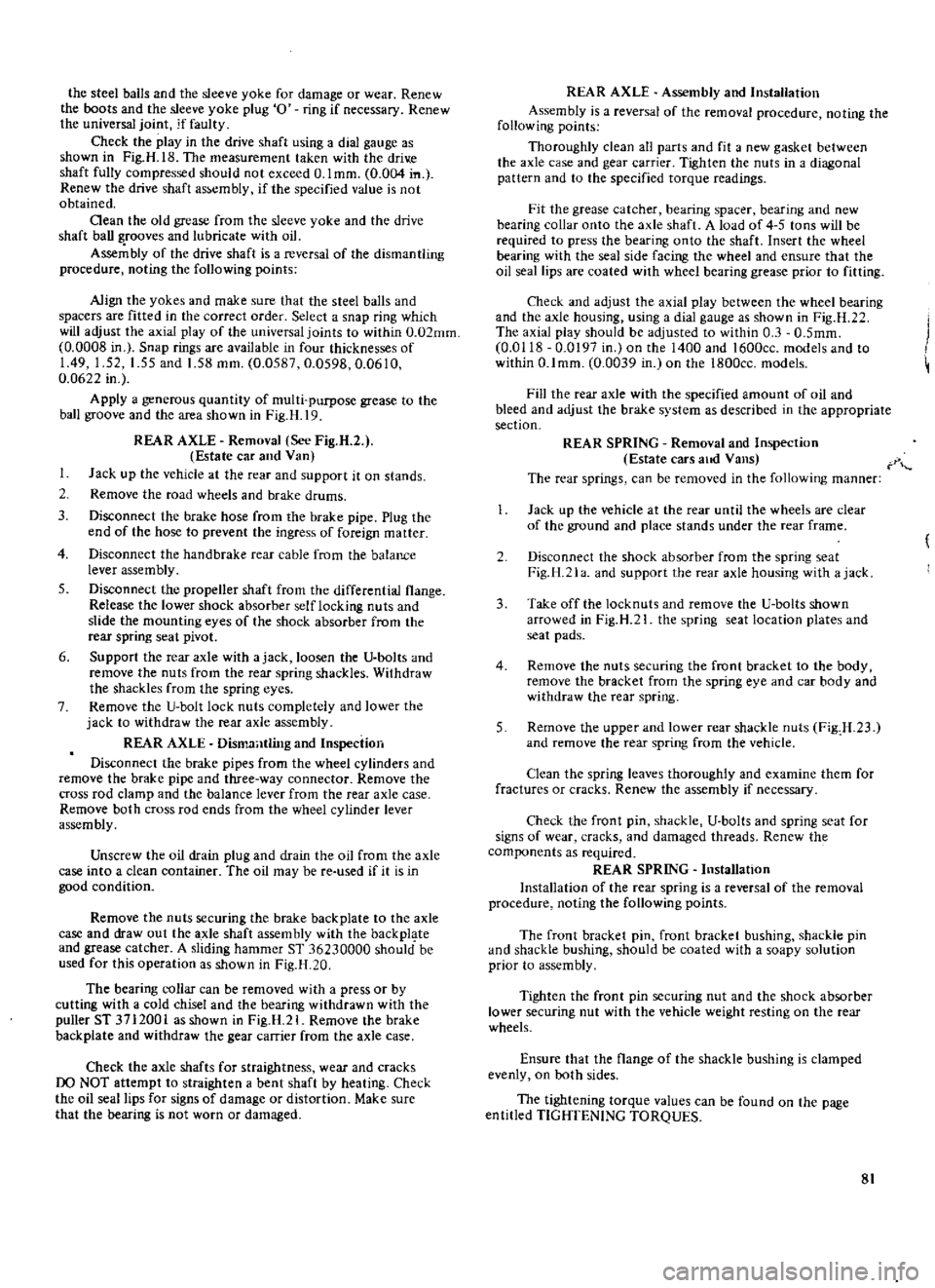
the
steel
balls
and
the
sleeve
yoke
for
damage
or
wear
Renew
the
boots
and
the
sleeve
yoke
plug
0
ring
if
necessary
Renew
the
universal
joint
jf
faulty
Check
the
play
in
the
drive
shaft
using
a
dial
gauge
as
shown
in
Fig
H
18
The
measurement
taken
with
the
dri
le
shaft
fully
compressed
should
not
exceed
O
lmm
0
004
in
Renew
the
drive
shaft
as
embly
if
the
specified
value
is
not
obtained
Oean
the
old
grease
from
the
sleeve
yoke
and
the
drive
shaft
ball
grooves
and
lubricate
with
oil
Asse
bly
of
the
drive
shaft
is
a
reversal
of
the
dismantling
procedure
noting
the
following
points
Align
the
yokes
and
make
sure
that
the
steel
balls
and
spacers
are
fitted
in
the
correct
order
Select
a
snap
ring
which
will
adjust
the
axial
play
of
the
universaIjoints
to
within
0
02mm
0
0008
in
Snap
rings
are
available
in
four
thicknesses
of
1
49
1
52
1
55
and
1
58
mm
0
0587
0
0598
0
0610
0
0622
in
Apply
a
generous
quantity
of
multi
purpose
grease
to
the
ball
groove
and
the
area
shown
in
Fig
H
19
REAR
AXLE
Removal
See
Fig
H
2
Estate
car
and
Van
Jack
up
the
vehicle
at
the
rear
and
support
it
on
stands
Remove
the
road
wheels
and
brake
drums
I
3
Disconnect
the
brake
hose
from
the
brake
pipe
Plug
the
end
of
the
hose
to
prevent
the
ingress
of
foreign
matter
4
Disconnect
the
handbrake
rear
cable
from
the
balance
lever
assembly
5
Disconnect
the
propeller
shaft
from
the
differential
flange
Release
the
lower
shock
absorber
self
locking
nuts
and
slide
the
mounting
eyes
of
the
shock
absorber
from
the
rear
spring
seat
pivot
6
Support
the
rear
axle
with
ajack
loosen
the
U
bolts
and
remove
the
nuts
from
the
rear
spring
shackles
Withdraw
the
shackles
from
the
spring
eyes
7
Remove
the
V
bolt
lock
nuts
completely
and
lower
the
jack
to
withdraw
the
rear
axle
assembly
REAR
AXLE
Dismailtling
and
Inspection
Disconnect
the
brake
pipes
from
the
wheel
cylinders
and
remove
the
brake
pipe
and
three
way
connector
Remove
the
cross
rod
clamp
and
the
balance
lever
from
the
rear
axle
case
Remove
both
cross
rod
ends
from
the
wheel
cylinder
lever
assembly
Unscrew
the
oil
drain
plug
and
drain
the
oil
from
the
axle
case
into
a
clean
container
The
oil
may
be
re
used
if
it
is
in
good
condition
Remove
the
nuts
securing
the
brake
backplate
to
the
axle
case
and
draw
out
the
axle
shaft
assembly
with
the
backpl
te
and
grease
catcher
A
sliding
hammer
ST
36230000
should
be
used
for
this
operation
as
shown
in
Fig
H
2Q
The
bearing
collar
can
be
removed
with
a
press
or
by
cutting
with
a
cold
chisel
and
the
bearing
withdrawn
with
the
puller
ST
3712001
as
shown
in
Fig
H
2t
Remove
the
brake
backplate
and
withdraw
the
gear
carrier
from
the
axle
case
Check
the
axle
shafts
for
straightness
wear
and
cracks
00
NOT
attempt
to
straighten
a
bent
shaft
by
heating
Check
the
oil
seal
lips
for
signs
of
damage
or
distortion
Make
sure
that
the
bearing
is
not
worn
or
damaged
REAR
AXLE
Assembly
and
Installation
Assembly
is
a
reversal
of
the
removal
procedure
noting
the
following
points
Thoroughly
clean
all
parts
and
fit
a
new
gasket
between
the
axle
case
and
gear
carrier
Tighten
the
nuts
in
a
diagonal
pattern
and
to
the
specified
torque
readings
Fit
the
grease
catcher
bearing
spacer
bearing
and
new
bearing
collar
onto
the
axle
shaft
A
load
of
4
5
tons
will
be
required
to
press
the
bearing
onto
the
shaft
Insert
the
wheel
bearing
with
the
seal
side
facing
the
wheel
and
ensure
that
the
oil
seal
lips
are
coated
with
wheel
bearing
grease
prior
to
fitting
Check
and
adjust
the
axial
play
between
the
wheel
bearing
and
the
axle
housing
using
a
dial
gauge
as
shown
in
Fig
H
22
The
axial
play
should
be
adjusted
to
within
0
3
0
5mm
0
0118
0
0197
in
on
the
1400
and
1600cc
models
and
to
within
O
lmm
0
0039
in
on
the
1800cc
models
Fill
the
rear
axle
with
the
specified
amount
of
oil
and
bleed
and
adjust
the
brake
system
as
described
in
the
appropriate
section
REAR
SPRING
Removal
and
Inspection
Estate
cars
aud
Vans
The
rear
springs
can
be
removed
in
the
following
manner
Jack
up
the
vehicle
at
the
rear
until
the
wheels
are
clear
of
the
ground
and
place
stands
under
the
rear
frame
Disconnect
the
shock
absorber
from
the
spring
seat
Fig
H
21a
and
support
the
rear
axle
housing
with
ajack
3
Take
off
the
locknuts
and
remove
the
U
bolts
shown
arrowed
in
Fig
H
2t
the
spring
seat
location
plates
and
seat
pads
4
Remove
the
nuts
securing
the
front
bracket
to
the
body
remove
the
bracket
from
the
spring
eye
and
car
body
and
withdraw
the
rear
spring
5
Remove
the
upper
and
lower
rear
shackle
nuts
Fig
H
23
and
remove
the
rear
spring
from
the
vehicle
Clean
the
spring
leaves
thoroughly
and
examine
them
for
fractures
or
cracks
Renew
the
assembly
if
necessary
Check
the
front
pin
shackle
U
boIts
and
spring
seat
for
signs
of
wear
cracks
and
damaged
threads
Renew
the
components
as
required
REAR
SPRING
Installation
Installation
of
the
rear
spring
is
a
reversal
of
the
removal
procedure
noting
the
following
points
The
front
bracket
pin
front
bracket
bushing
shackle
pin
and
shackle
bushing
should
be
coated
with
a
soapy
solution
prior
to
assembly
Tighten
the
front
pin
securing
nut
and
the
shock
absorber
lower
securing
nut
with
the
vehicle
weight
resting
on
the
rear
wheels
Ensure
that
the
flange
of
the
shackle
bushing
is
clamped
evenly
on
both
sides
The
tightening
torque
values
can
be
found
on
the
page
entitled
TIGHTENING
TORQUES
81