relay DATSUN 610 1969 Workshop Manual
[x] Cancel search | Manufacturer: DATSUN, Model Year: 1969, Model line: 610, Model: DATSUN 610 1969Pages: 171, PDF Size: 10.63 MB
Page 110 of 171
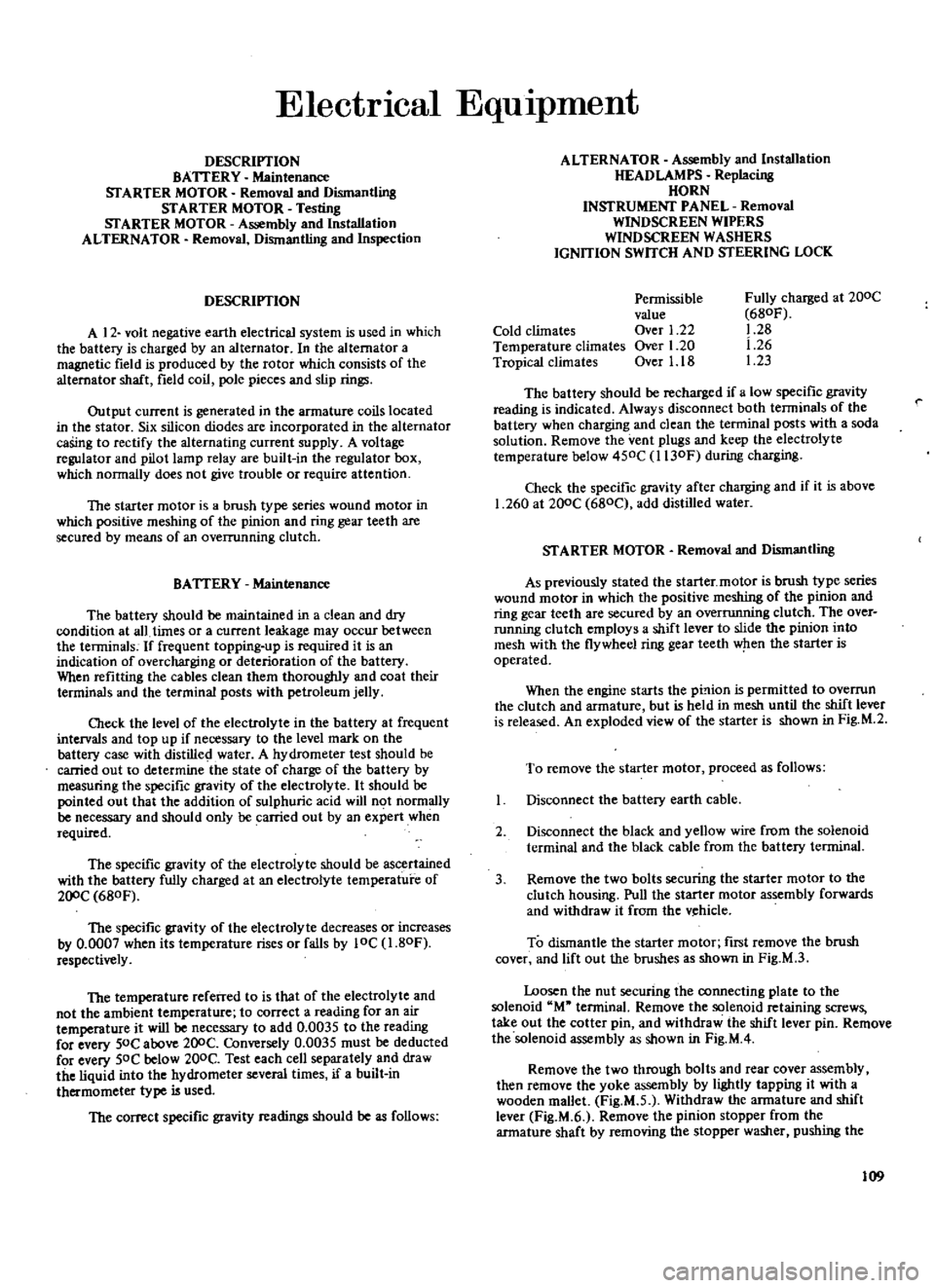
ElectrIcal
EquIpment
DESCRIPTION
BATTERY
Maintenance
STARTER
MOTOR
Removal
and
Dismantling
STARTER
MOTOR
Testing
STARTER
MOTOR
Assembly
and
Installation
ALTERNATOR
Removal
Dismantling
and
Inspection
DESCRIPTION
A
12
volt
negative
earth
electrical
system
is
used
in
which
the
battery
is
charged
by
an
alternator
In
the
alternator
a
magnetic
field
is
produced
by
the
rotor
which
consists
of
the
alternator
shaft
field
coil
p
le
pieces
and
slip
rings
Output
current
is
generated
in
the
armature
coils
located
in
the
stator
Six
silicon
diodes
are
incorporated
in
the
alternator
caSing
to
rectify
the
alternating
current
supply
A
voltage
regulator
and
pilot
lamp
relay
are
built
in
the
regulator
box
which
nonnally
does
not
give
trouble
or
require
attention
The
starter
motor
is
a
brush
type
series
wound
motor
in
which
positive
meshing
of
the
pinion
and
ring
gear
teeth
are
secured
by
means
of
an
overrunning
clutch
BATTERY
Maintenance
The
battery
should
be
maintained
in
a
clean
and
dry
condition
at
all
times
or
a
current
leakage
may
occur
between
the
terminals
If
frequent
topping
up
is
required
it
is
an
indication
of
overcharging
or
deterioration
of
the
battery
When
refitting
the
cables
clean
them
thoroughly
and
coat
their
terminals
and
the
terminal
posts
with
petroleum
jelly
Check
the
level
of
the
electrolyte
in
the
battery
at
frequent
intervals
and
top
up
if
necessary
to
the
level
mark
on
the
battery
case
with
distilled
water
A
hydrometer
test
should
be
carried
out
to
determine
the
state
of
charge
of
the
battery
by
measuring
the
specific
gravity
of
the
electrolyte
It
should
be
pointed
out
that
the
addition
of
sulphuric
acid
will
not
normally
be
necessary
and
should
only
be
carried
out
by
an
expert
when
required
The
specific
gravity
of
the
electrolyte
should
be
ascertained
with
the
battery
fully
charged
at
an
electrolyte
temperature
of
200C
680F
The
specific
gravity
of
the
electrolyte
decreases
or
increases
by
0
0007
when
its
temperature
rises
or
falls
by
10C
1
80F
respectively
The
temperature
referred
to
is
that
of
the
electrolyte
and
not
the
ambient
temperature
to
correct
a
reading
for
an
air
temperature
it
will
be
necessary
to
add
0
0035
to
the
reading
for
every
50C
above
200C
Conversely
0
0035
must
be
deducted
for
every
SOC
below
200C
Test
each
cell
separately
and
draw
the
liquid
into
the
hydrometer
several
times
if
a
built
in
thermometer
type
is
used
The
correct
specific
gravity
readings
should
be
as
follows
ALTERNATOR
Assembly
and
Installation
HEAD
LAMPS
Replacing
HORN
INSTRUMENT
PANEL
Removal
WINDSCREEN
WIPERS
WINDSCREEN
WASHERS
IGNITION
SWITCH
AND
STEERING
LOCK
Cold
climates
Temperature
climates
Tropical
climates
Permissible
value
Over
1
22
Over
1
20
Over
1
18
Fully
charged
at
200C
680F
1
28
1
26
1
23
The
battery
should
be
recharged
if
a
low
specific
gravity
reading
is
indicated
Always
disconnect
both
terminals
of
the
battery
when
charging
and
clean
the
terminal
posts
with
a
soda
solution
Remove
the
vent
plugs
and
keep
the
electrolyte
temperature
below
450C
l130F
during
charging
Check
the
specific
gravity
after
charging
and
if
it
is
above
1
260
at
200C
680C
add
distilled
water
STARTER
MOTOR
Removal
and
Dismantling
As
previously
stated
the
starter
motor
is
brush
type
series
wound
motor
in
which
the
positive
meshing
of
the
pinion
and
ring
gear
teeth
are
secured
by
an
overrunning
clutch
The
over
running
clutch
employs
a
shift
lever
to
slide
the
pinion
into
mesh
with
the
flywheel
ring
gear
teeth
when
the
starter
is
operated
When
the
engine
starts
the
pL
lion
is
permitted
to
overrun
the
clutch
and
armature
but
is
held
in
mesh
until
the
shift
lever
is
released
An
exploded
view
of
the
starter
is
shown
in
Fig
M
2
To
remove
the
starter
motor
proceed
as
follows
Disconnect
the
battery
earth
cable
2
Disconnect
the
black
and
yellow
wire
from
the
solenoid
terminal
and
the
black
cable
from
the
battery
terminal
3
Remove
the
two
bolts
securing
the
starter
motor
to
the
clutch
housing
Pull
the
starter
motor
assembly
forwards
and
withdraw
it
from
the
v
hicle
To
dismantle
the
starter
motor
ftrst
remove
the
brush
cover
and
lift
out
the
brushes
as
shown
in
Fig
M
3
Loosen
the
nut
securing
the
connecting
plate
to
the
solenoid
M
terminal
Remove
the
solenoid
retaining
screws
take
out
the
cotter
pin
and
withdraw
the
shift
lever
pin
Remove
the
solenoid
assembly
as
shown
in
Fig
M
4
Remove
the
two
through
bolts
and
rear
cover
assembly
then
remove
the
yoke
assembly
by
lightly
tapping
it
with
a
wooden
mallet
Fig
M
S
Withdraw
the
armature
and
shift
lever
Fig
M
6
Remove
the
pinion
stopper
from
the
armature
shaft
by
removing
the
stopper
washer
pushing
the
109
Page 115 of 171
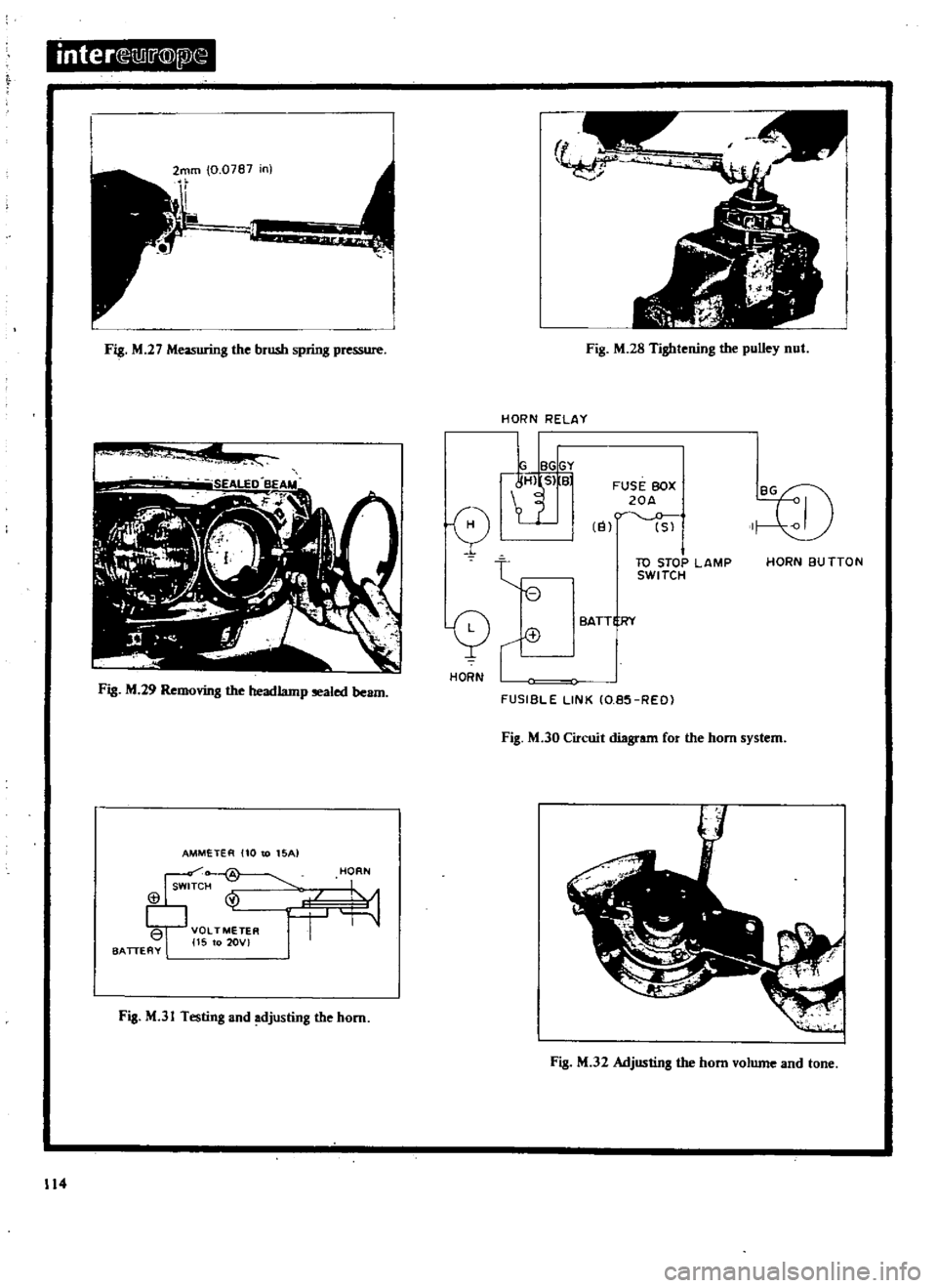
inter
ill
1
@
fl@
2mm
O
07e7
in
l
r
Fig
M
27
Measuring
the
brush
spring
pressure
oo
fI
f
Fig
M
29
R
h
the
headlamp
Ied
beam
AMM
E
iER
HO
to
SA
HO
N
SWITCH
1
VOLTMETER
115
to
2OV
I
I
Fig
M
31
Testing
and
adjusting
the
horn
114
J
GJ
Fig
M
28
Tightening
the
puUey
nut
HORN
RELAY
L
IBGIGY
tt
t
e
q
HO
N
r
FUSIBLE
LINK
IO
e5
REO
FUS
E
BOX
20A
El
Sl
I
10
STOP
LAMP
SWITCH
HORN
eu
TTON
eATT
RY
Fig
M
JO
Circuit
diagram
for
the
horn
system
Fig
M
32
Adjusting
the
horn
volume
and
tone
Page 150 of 171
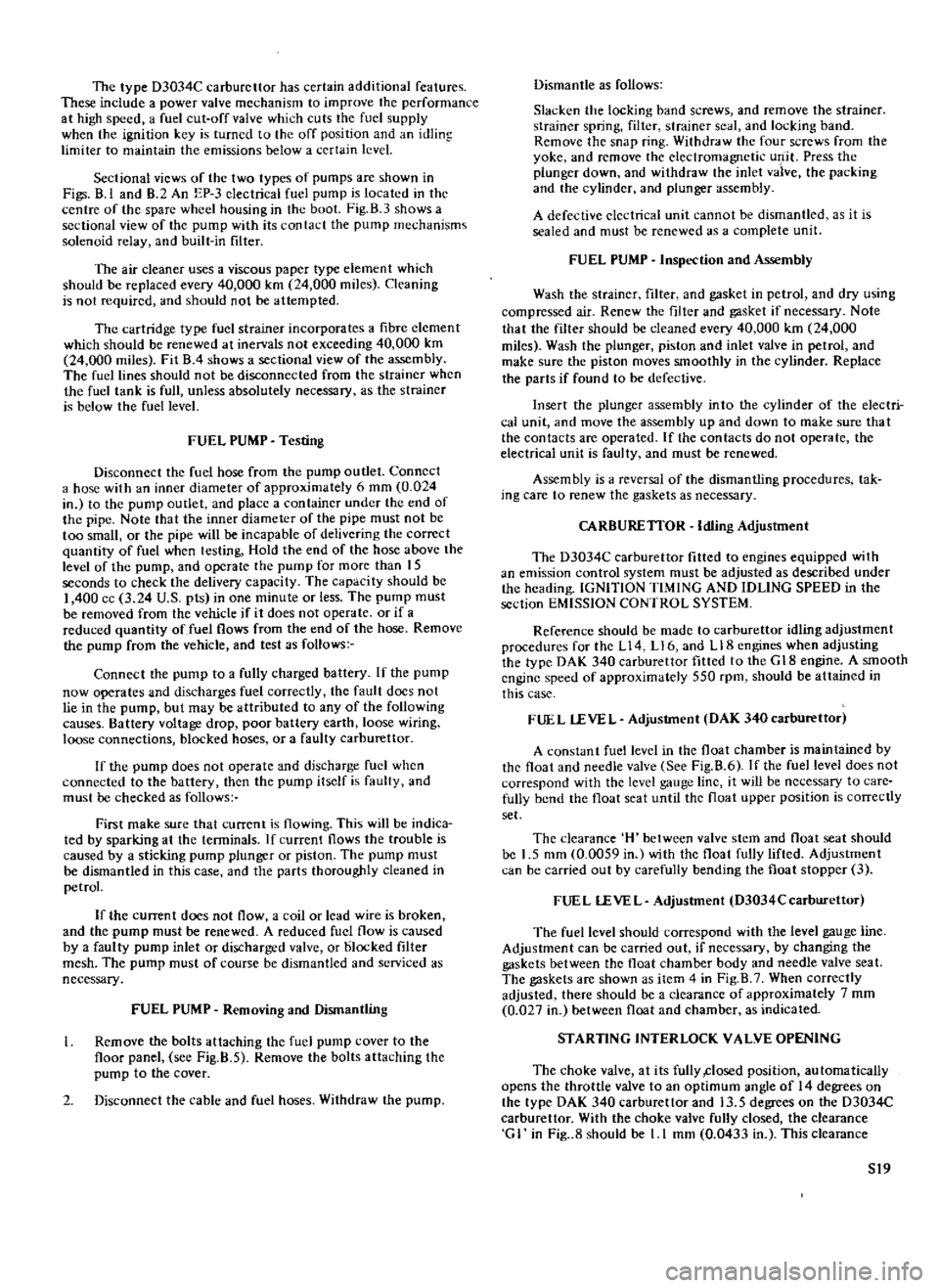
The
type
D3034C
carburettor
has
certain
additional
features
These
include
a
power
valve
mechanism
to
improve
the
performance
at
high
speed
a
fuel
cut
off
valve
which
cuts
the
fuel
supply
when
the
ignition
key
is
turned
to
the
off
position
and
an
idling
limiter
to
maintain
the
emissions
below
a
certain
level
Sectional
views
of
the
two
types
of
pumps
are
shown
in
Figs
8
1
and
B
2
An
EP
3
electrical
fuel
pump
is
located
in
the
centre
of
the
spare
wheel
housing
in
the
boot
Fig
B
3
shows
a
sectional
view
of
the
pump
with
its
contact
the
pump
mechanisms
solenoid
relay
and
built
in
filter
The
air
cleaner
uses
a
viscous
paper
type
element
which
should
be
replaced
every
40
000
km
24
000
miles
Cleaning
is
not
required
and
should
not
be
attempted
The
cartridge
type
fuel
strainer
incorporates
a
fibre
clement
which
should
be
renewed
at
inervals
not
exceeding
40
000
km
24
000
miles
Fit
B
4
shows
a
sectional
view
of
the
assembly
The
fuel
lines
should
not
be
disconnected
from
the
strainer
when
the
fuel
tank
is
full
unless
absolutely
necessary
as
the
strainer
is
below
the
fuel
level
FUEL
PUMP
Testing
Disconnect
the
fuel
hose
from
the
pump
outlet
Connect
a
hose
with
an
inner
diameter
of
approximately
6
mm
0
024
in
to
the
pump
outlet
and
place
a
container
under
the
end
of
the
pipe
Note
that
the
inner
diameter
of
the
pipe
must
not
be
too
small
or
the
pipe
will
be
incapable
of
delivering
the
correct
quantity
of
fuel
when
testing
Hold
the
end
of
the
hose
above
the
level
of
the
pump
and
operate
the
pump
for
more
than
IS
seconds
to
check
the
delivery
capacity
The
capacity
should
be
I
400
cc
3
24
U
S
pts
in
one
minute
or
less
The
pump
must
be
removed
from
the
vehicle
if
it
does
not
operate
or
if
a
reduced
quantity
of
fuel
flows
from
the
end
of
the
hose
Remove
the
pump
from
the
vehicle
and
test
as
follows
Connect
the
pump
to
a
fully
charged
battery
If
the
pump
now
operates
and
discharges
fuel
correctly
the
fault
does
not
lie
in
the
pump
but
may
be
attributed
to
any
of
the
following
causes
Battery
voltage
drop
poor
battery
earth
loose
wiring
loose
connections
blocked
hoses
or
a
faulty
carburettor
If
the
pump
does
not
operate
and
discharge
fuel
when
connected
to
the
battery
then
the
pump
itself
is
faulty
and
must
be
checked
as
follows
First
make
sure
that
current
is
flowing
This
will
be
indica
ted
by
sparking
at
the
tenninals
If
current
flows
the
trouble
is
caused
by
a
sticking
pump
plunger
or
piston
The
pump
must
be
dismantled
in
this
case
and
the
parts
thoroughly
cleaned
in
petrol
If
the
current
does
not
flow
a
coil
or
lead
wire
is
broken
and
the
pump
must
be
renewed
A
reduced
fuel
flow
is
caused
by
a
faulty
pump
inlet
or
discharged
valve
or
blocked
filter
mesh
The
pump
must
of
course
be
dismantled
and
serviced
as
necessary
FUEL
PUMP
Removing
and
Dismantling
Remove
the
bolts
attaching
the
fuel
pump
cover
to
the
floor
panel
see
Fig
B
S
Remove
the
bolts
attaching
the
pump
to
the
cover
2
Disconnect
the
cable
and
fuel
hoses
Withdraw
the
pump
Dismantle
as
follows
Slacken
the
locking
band
screws
and
remove
the
strainer
strainer
spring
filter
strainer
seal
and
locking
band
Remove
the
snap
ring
Withdraw
the
four
screws
from
the
yoke
and
remove
the
electromagnetic
ulJ
it
Press
the
plunger
down
and
withdraw
the
inlet
vaive
the
packing
and
the
cylinder
and
plunger
assembly
A
defective
eledrical
unit
cannot
be
dismantled
as
it
is
sealed
and
must
be
renewed
as
a
complete
unit
FUEL
PUMP
Inspection
and
Assembly
Wash
the
strainer
filter
and
gasket
in
petrol
and
dry
using
compressed
air
Renew
the
filter
and
gasket
if
necessary
Note
that
the
filter
should
be
cleaned
every
40
000
km
24
000
miles
Wash
the
plunger
piston
and
inlet
valve
in
petrol
and
make
sure
the
piston
moves
smoothly
in
the
cylinder
Replace
the
parts
if
found
to
be
defective
Insert
the
plunger
assembly
into
the
cylinder
of
the
electri
cal
unit
and
move
the
assembly
up
and
down
to
make
sure
tha
t
the
contacts
are
operated
If
the
contacts
do
not
operate
the
electrical
unit
is
faulty
and
must
be
renewed
Assembly
is
a
reversal
of
the
dismantling
procedures
tak
ing
care
to
renew
the
gaskets
as
necessary
CARBURETIOR
Idling
Adjustment
The
D3034C
carburettor
fitted
to
engines
equipped
with
an
emission
control
system
must
be
adjusted
as
described
under
the
heading
IGNITION
TIMING
AND
IDLING
SPEED
in
the
section
EMISSION
CONTROL
SYSTEM
Reference
should
be
made
to
carburettor
idling
adjustment
procedures
for
the
L14
L16
and
LI8
engines
when
adjusting
the
type
DAK
340
carburettor
fitted
to
the
G
18
engine
A
smooth
engine
speed
of
approximately
550
rpm
should
be
attained
in
this
case
FUEL
lEVEL
Adjustment
DAK
340earburettor
A
constant
fuellevcl
in
the
float
chamber
is
maintained
by
the
float
and
needle
valve
See
Fig
8
6
If
the
fuel
level
does
not
correspond
with
the
level
gauge
line
it
will
be
necessary
to
care
fully
bend
the
float
seat
until
the
float
upper
position
is
correctly
set
The
clearance
H
between
valve
stem
and
float
seat
should
be
I
5
mm
0
0059
in
with
the
float
fully
lifted
Adjustment
can
be
carried
out
by
carefully
bending
the
float
stopper
3
FUEL
lEVEL
Adjustment
D3034Ccarburettnr
The
fuel
level
should
correspond
with
the
level
gauge
line
Adjustment
can
be
carried
out
if
necessary
by
changing
the
gaskets
between
the
float
chamber
body
and
needle
valve
seat
The
gaskets
are
shown
as
item
4
in
Fig
B
7
When
correctly
adjusted
there
should
be
a
clearance
of
approximately
7
mm
0
027
in
between
float
and
chamber
as
indicated
STARTING
INTERLOCK
VALVE
OPENING
The
choke
valve
at
its
fully
closed
position
automatically
opens
the
throttle
valve
to
an
optimum
angle
of
14
degrees
on
the
type
DAK
340
carburettor
and
13
5
degrees
on
the
D3034C
carburettor
With
the
choke
valve
fully
closed
the
clearance
G
I
in
Fig
8
should
be
1
I
mm
0
0433
in
This
clearance
S19