warning light DATSUN 610 1969 Workshop Manual
[x] Cancel search | Manufacturer: DATSUN, Model Year: 1969, Model line: 610, Model: DATSUN 610 1969Pages: 171, PDF Size: 10.63 MB
Page 99 of 171
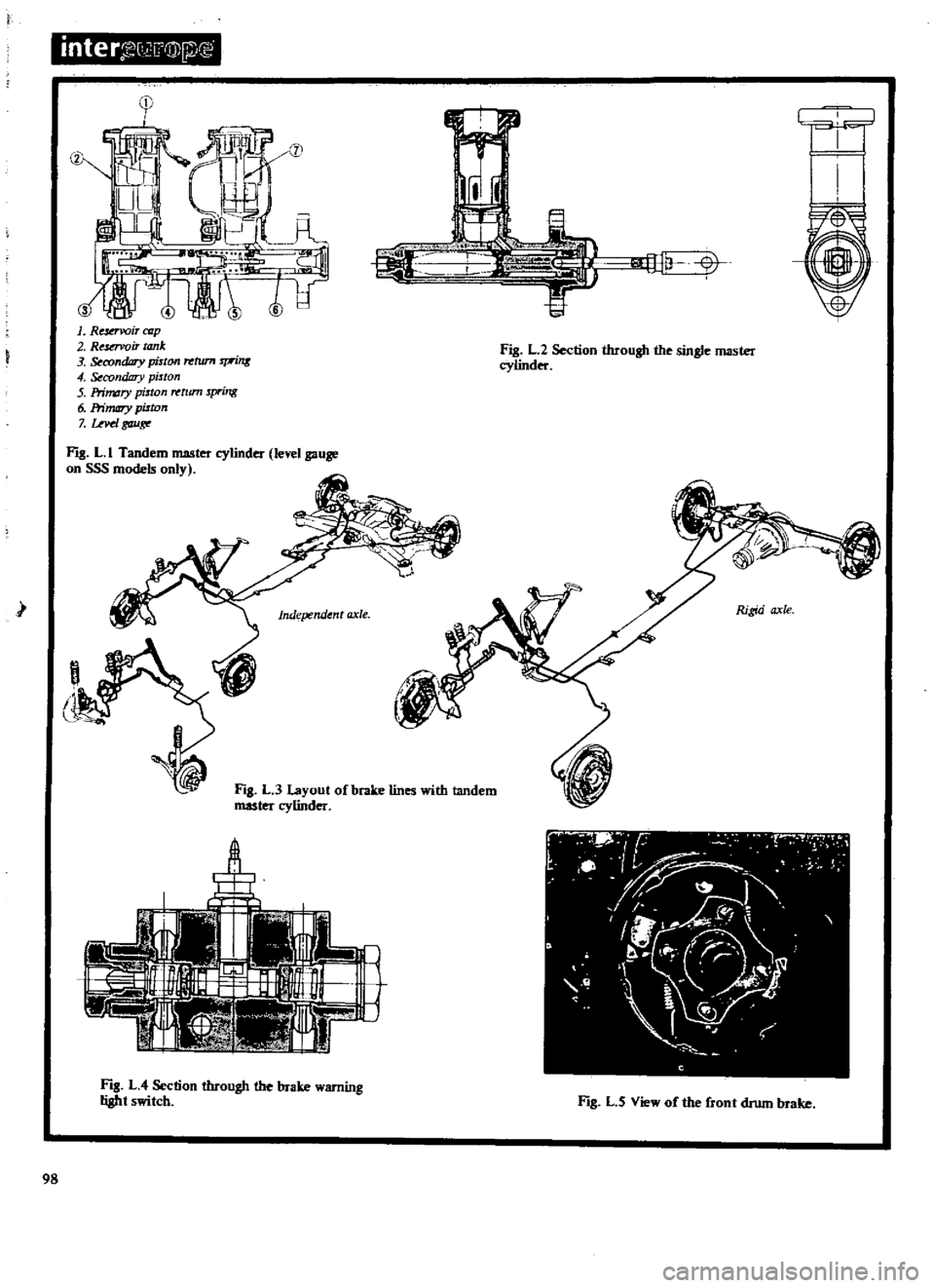
inter
G
@lfi
r
OIl
ll
V
V
1
Re
rvoir
azp
2
Resovoir
tank
3
condDry
piston
rrtrun
rprins
4
Secondary
pitton
5
Primary
piston
tum
spring
6
Primary
piston
7
uvd
gau
Fl
L
I
Tandem
master
cylinder
level
gauge
on
SSS
models
only
Fig
L
2
Section
through
the
single
master
cylinder
I
Independent
axle
Rigid
axle
Fig
L
3
Layout
of
brake
lines
with
tandem
master
cylinder
A
Ji
I
I
f
tf
A1
r
Fig
L
4
Section
through
the
brake
warning
light
switch
Fl
L
5
View
of
the
front
drum
brake
98
Page 100 of 171
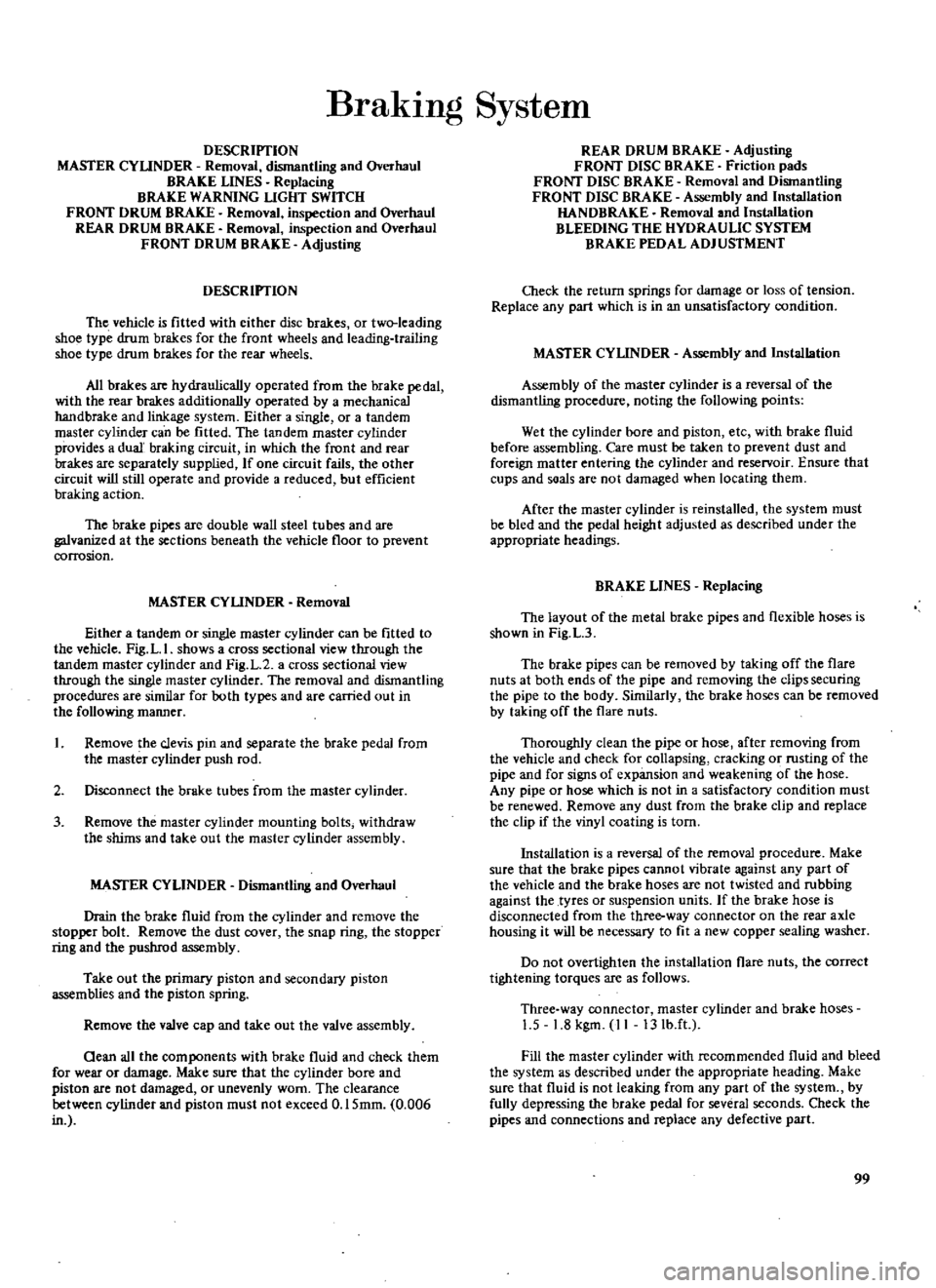
BrakIng
System
DESCRIPTION
MASTER
CYLINDER
Removal
dismantling
and
Overhaul
BRAKE
LINES
Replacing
BRAKE
WARNING
LIGHT
SWITCH
FRONT
DRUM
BRAKE
Removal
inspection
and
Overhaul
REAR
DRUM
BRAKE
Removal
inspection
and
Overhaul
FRONT
DRUM
BRAKE
Adjusting
DESCRIPTION
The
vehicle
is
fitted
with
either
disc
brakes
or
two
leading
shoe
type
drum
brakes
for
the
front
wheels
and
leading
trailing
shoe
type
drum
brakes
for
the
rear
wheels
All
brakes
are
hydraulically
operated
from
the
brake
pedal
with
the
rear
brakes
additionally
operated
by
a
mechanical
handbrake
and
linkage
system
Either
a
single
or
a
tandem
master
cylinder
can
be
fitted
The
tandem
master
cylinder
provides
a
dual
braking
circuit
in
which
the
front
and
rear
brakes
are
separately
supplied
If
ODe
circuit
fails
the
other
circuit
will
still
operate
and
provide
a
reduced
but
efficient
braking
action
The
brake
pipes
are
double
wall
steel
tubes
and
are
galvanized
at
the
sections
beneath
the
vehicle
floor
to
prevent
corrosion
MASTER
CYLINDER
Removal
Either
a
tandem
or
single
master
cylinder
can
be
fitted
to
the
vehicle
Fig
L
I
shows
a
cross
sectional
view
through
the
tandem
master
cylinder
and
Fig
L
2
a
cross
sectional
view
through
the
single
master
cylinder
The
removal
and
dismantling
procedures
are
similar
for
both
types
and
are
carried
out
in
the
following
manner
1
Remove
the
clevis
pin
and
separate
the
brake
pedal
from
the
master
cylinder
push
rod
2
Disconnect
the
brake
tubes
from
the
master
cylinder
3
Remove
the
master
cylinder
mounting
bolts
withdraw
the
shims
and
take
out
the
master
cylinder
assembly
MASfER
CYLINDER
Dismantling
and
Overhaul
Drain
the
brake
fluid
from
the
cylinder
and
remove
the
stopper
bolt
Remove
the
dust
cover
the
snap
ring
the
stopper
ring
and
the
pusbrod
assembly
Take
out
the
primary
piston
and
secondary
piston
assemblies
and
the
piston
spring
Remove
the
valve
cap
and
take
out
the
valve
assembly
Oean
all
the
components
with
brake
fluid
and
check
them
for
wear
or
damage
Make
sure
that
the
cylinder
bore
and
piston
are
not
damaged
or
unevenly
worn
The
clearance
between
cylinder
and
piston
must
not
exceed
0
15mm
0
006
in
REAR
DRUM
BRAKE
Adjusting
FRONT
DISC
BRAKE
Friction
pads
FRONT
DISC
BRAKE
Removal
and
Dismantling
FRONT
DISC
BRAKE
Assembly
and
Installation
HANDBRAKE
Removal
and
Installation
BLEEDING
THE
HYDRAULIC
SYSTEM
BRAKE
PEDAL
ADJUSTMENT
Check
the
return
springs
for
damage
or
loss
of
tension
Replace
any
part
which
is
in
an
unsatisfactory
condition
MASfER
CYLINDER
Assembly
and
Installation
Assembly
of
the
master
cylinder
is
a
reversal
of
the
dismantling
procedure
noting
the
following
points
Wet
the
cylinder
bore
and
piston
etc
with
brake
fluid
before
assembling
Care
must
be
taken
to
prevent
dust
and
foreign
matter
entering
the
cylinder
and
reservoir
Ensure
that
cups
and
soals
are
not
damaged
when
locating
them
After
the
master
cylinder
is
reinstalled
the
system
must
be
bled
and
the
pedal
height
adjusted
as
described
under
the
appropriate
headings
BRAKE
LINES
Replacing
The
layout
of
the
metal
brake
pipes
and
flexible
hoses
is
shown
in
Fig
L
3
The
brake
pipes
can
be
removed
by
taking
off
the
flare
nuts
at
both
ends
of
the
pipe
and
removing
the
clips
securing
the
pipe
to
the
body
Similarly
the
brake
hoses
can
be
removed
by
taking
off
the
flare
nuts
Thoroughly
clean
the
pipe
or
hose
after
removing
from
the
vehicle
and
check
for
collapsing
cracking
or
rusting
of
the
pipe
and
for
signs
of
expansion
and
weakening
of
the
hose
Any
pipe
or
hose
which
is
not
in
a
satisfactory
condition
must
be
renewed
Remove
any
dust
from
the
brake
clip
and
replace
the
clip
if
the
vinyl
coating
is
torn
Installation
is
a
reversal
of
the
removal
procedure
Make
sure
that
the
brake
pipes
cannot
vibrate
against
any
part
of
the
vehicle
and
the
brake
hoses
are
not
twisted
and
rubbing
against
the
tyres
or
suspension
units
If
the
brake
hose
is
disconnected
from
the
three
way
connector
on
the
rear
axle
housing
it
will
be
necessary
to
fit
a
new
copper
sealing
washer
Do
not
overtighten
the
installation
flare
nuts
the
correct
tightening
torques
are
as
follows
Three
way
connector
master
cylinder
and
brake
hoses
1
5
1
8
kgm
II
13Ib
ft
Fill
the
master
cylinder
with
recommended
fluid
and
bleed
the
system
as
described
under
the
appropriate
heading
Make
sure
that
fluid
is
not
leaking
from
any
part
of
the
system
by
fully
depressing
the
brake
pedal
for
several
seconds
Check
the
pipes
and
connections
and
replace
any
defective
part
99
Page 102 of 171
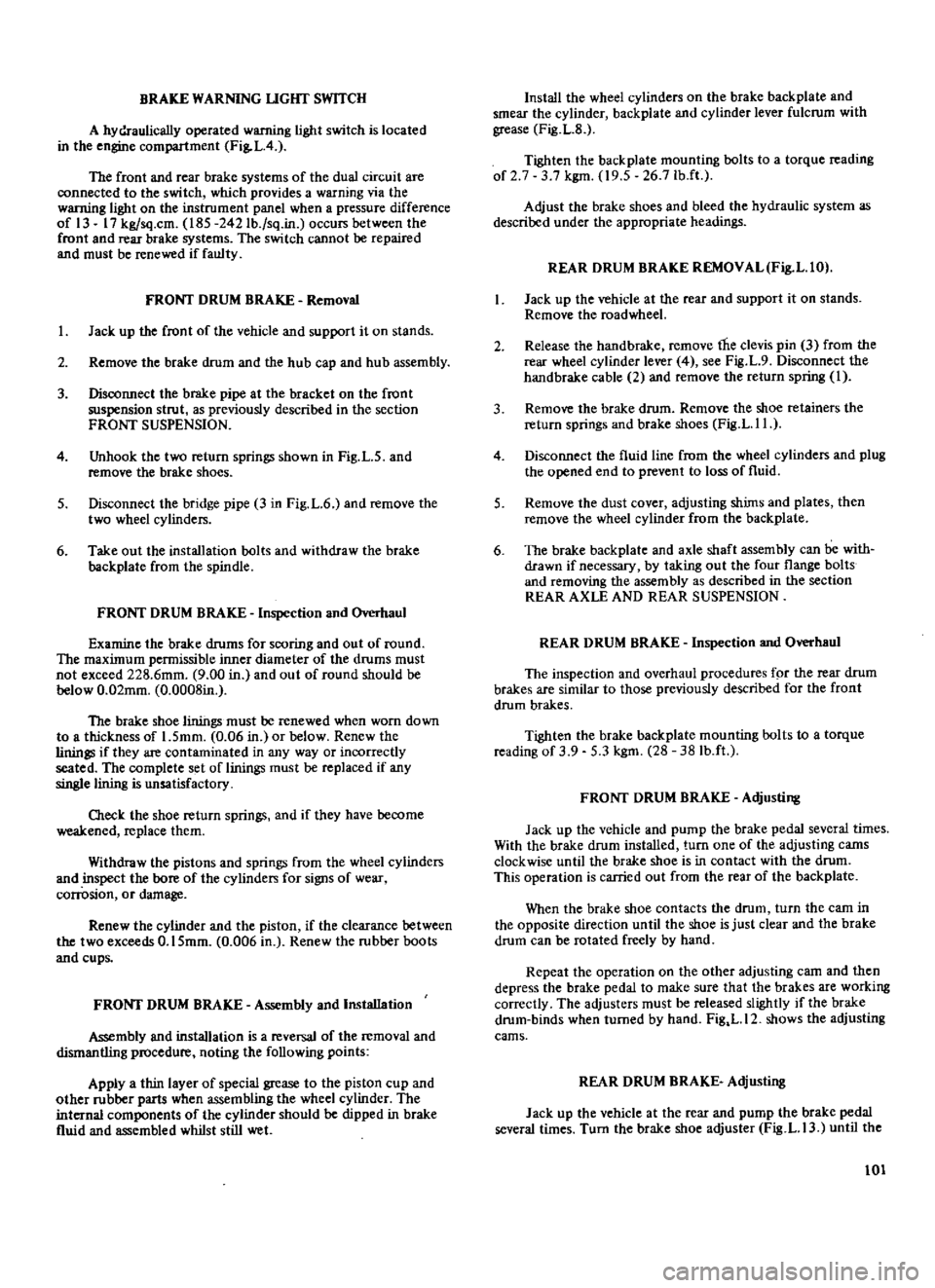
BRAKE
WARNING
UGHT
SWITCH
A
hydraulically
operated
warning
light
switch
is
located
in
the
engine
compartment
Fig
LA
The
front
and
rear
brake
systems
of
the
dual
circuit
are
connected
to
the
switch
which
provides
a
warning
via
the
warning
light
on
the
instrument
panel
when
a
pressure
difference
of
13
17
kg
sq
cm
185
242Ib
sq
in
occurs
between
the
front
and
rear
brake
systems
The
switch
cannot
be
repaired
and
must
be
renewed
if
faulty
FRONT
DRUM
BRAKE
Removal
1
Jack
up
the
front
of
the
vehicle
and
support
it
on
stands
2
Remove
the
brake
drum
and
the
hub
cap
and
hub
assembly
3
Disconnect
the
brake
pipe
at
the
bracket
on
the
front
suspension
strut
as
previously
described
in
the
section
FRONT
SUSPENSION
4
Unhook
the
two
return
springs
shown
in
Fig
L
5
and
remove
the
brake
shoes
5
Disconnect
the
bridge
pipe
3
in
Fig
L
6
and
remove
the
two
wheel
cylinders
6
Take
out
the
installation
bolts
and
withdraw
the
brake
backplate
from
the
spindle
FRONT
DRUM
BRAKE
Inspection
and
Overhaul
Examine
the
brake
drums
for
scoring
and
out
of
round
The
maximum
permissible
inner
diameter
of
the
drums
must
not
exceed
228
6mm
9
00
in
and
out
of
round
should
be
below
0
02mm
0
0008in
The
brake
shoe
linings
must
re
renewed
when
worn
down
to
a
thickness
of
1
5mm
0
06
in
or
below
Renew
the
linings
if
they
are
contaminated
in
any
way
or
incorrectly
seated
The
complete
set
of
linings
must
be
replaced
if
any
single
lining
is
unsatisfactory
O1eck
the
shoe
return
springs
and
if
they
have
become
weakened
replace
them
Withdraw
the
pistons
and
springs
from
the
wheel
cylinders
and
inspect
the
bore
of
the
cylinders
for
signs
of
wear
corrosion
or
damage
Renew
the
cylinder
and
the
piston
if
the
clearance
between
the
two
exceeds
O
15mm
0
006
in
Renew
the
rubber
boots
and
cups
FRONT
DRUM
BRAKE
Assembly
and
Installation
Assembly
and
installation
is
a
reversal
of
the
removal
and
dismantling
procedure
noting
the
fOllowing
points
Apply
a
thin
layer
of
special
grease
to
the
piston
cup
and
other
rubber
parts
when
assembling
the
wheel
cylinder
The
internal
components
of
the
cylinder
should
be
dipped
in
brake
fluid
and
assembled
whilst
still
wet
Install
the
wheel
cylinders
on
the
brake
backplate
and
smear
the
cylinder
backplate
and
cylinder
lever
fulcrum
with
grease
Fig
L
8
Tighten
the
backplate
mounting
bolts
to
a
torque
reading
of
2
7
3
7
kgm
19
5
26
71b
ft
Adjust
the
brake
shoes
and
bleed
the
hydraulic
system
as
described
under
the
appropriate
headings
REAR
DRUM
BRAKE
REMOVAL
Fig
L
IO
Jack
up
the
vehicle
at
the
rear
and
support
it
on
stands
Remove
the
road
wheel
2
Release
the
handbrake
remove
the
clevis
pin
3
from
the
rear
wheel
cylinder
lever
4
see
Fig
L
9
Disconnect
the
handbrake
cable
2
and
remove
the
return
spring
I
3
Remove
the
brake
drum
Remove
the
shoe
retainers
the
return
springs
and
brake
shoes
Fig
L
II
4
Disconnect
the
fluid
line
from
the
wheel
cylinders
and
plug
the
opened
end
to
prevent
to
loss
of
fluid
5
Remove
the
dust
cover
adjusting
shims
and
plates
then
remove
the
wheel
cylinder
from
the
backplate
6
The
brake
backplate
and
axle
shaft
assembly
can
be
with
drawn
if
necessary
by
taking
out
the
four
flange
bolts
and
removing
the
assembly
as
described
in
the
section
REAR
AXLE
AND
REAR
SUSPENSION
REAR
DRUM
BRAKE
Inspection
and
Overhaul
The
inspection
and
overhaul
procedures
fpr
the
rear
drum
brakes
are
similar
to
those
previously
described
for
the
front
drum
brakes
Tighten
the
brake
backplate
mounting
bolts
to
a
torque
reading
of
3
9
5
3
kgm
28
38Ib
ft
FRONT
DRUM
BRAKE
Adjusting
Jack
up
the
vehicle
and
pump
the
brake
pedal
several
times
With
the
brake
drum
installed
turn
one
of
the
adjusting
cams
clockwise
until
the
brake
shoe
is
in
contact
with
the
drum
This
operation
is
carried
out
from
the
rear
of
the
backplate
When
the
brake
shoe
contacts
the
drum
turn
the
cam
in
the
opposite
direction
until
the
shoe
is
just
clear
and
the
brake
drum
can
be
rotated
freely
by
hand
Repeat
the
operation
on
the
other
adjusting
cam
and
then
depress
the
brake
pedal
to
make
sure
that
the
brakes
are
working
correctly
The
adjusters
must
be
released
slightly
if
the
brake
drum
binds
when
turned
by
hand
Fig
L
12
shows
the
adjusting
cams
REAR
DRUM
BRAKE
Adjusting
Jack
up
the
vehicle
at
the
rear
and
pump
the
brake
pedal
several
times
Turn
the
brake
shoe
adjuster
Fig
L
13
until
the
101
Page 162 of 171
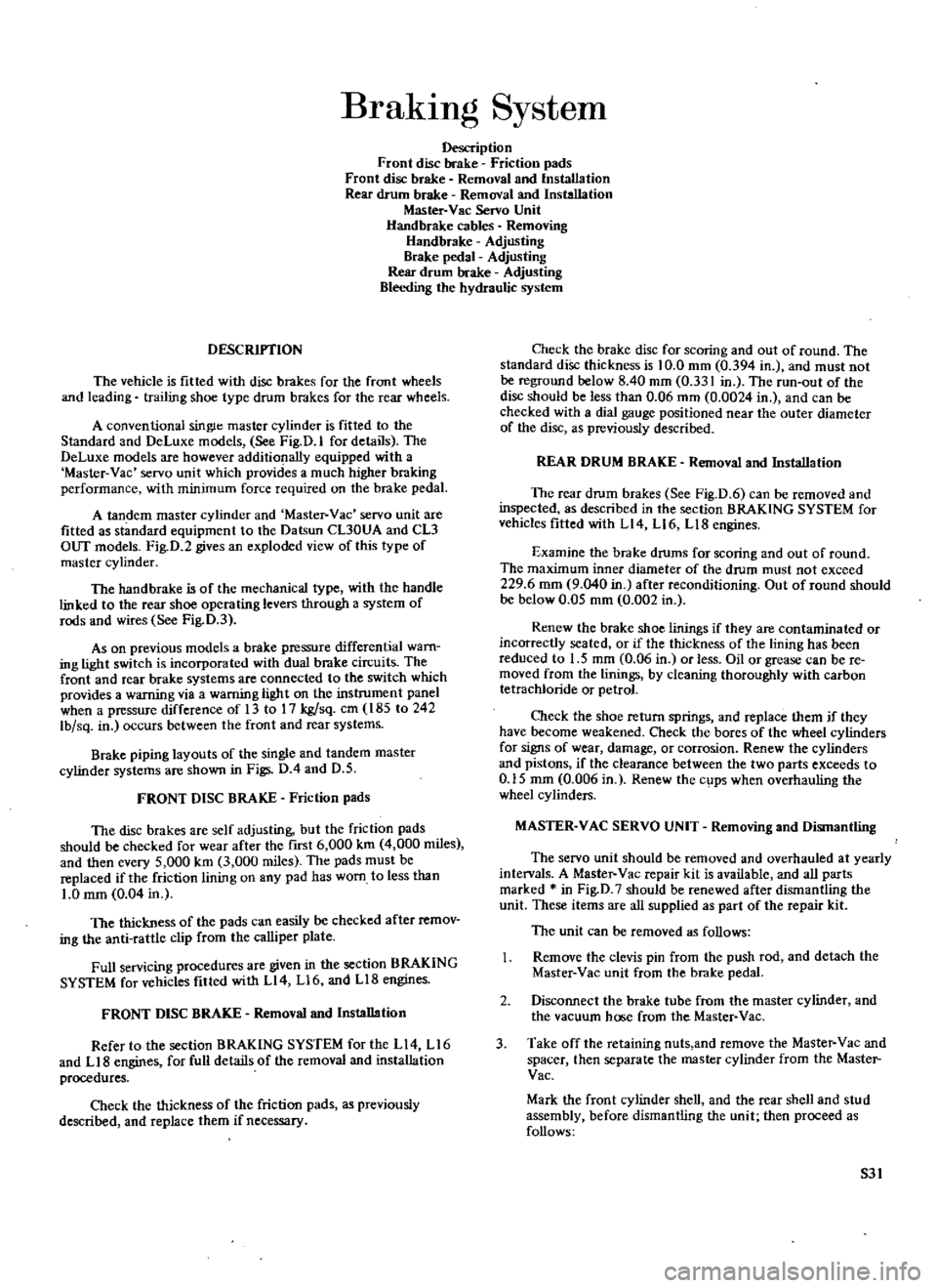
BrakIng
System
Description
Front
disc
brake
Friction
pads
Front
disc
brake
Removal
and
Installation
Rear
drum
brake
Removal
and
Installation
Master
Vac
Servo
Unit
Handbrake
cables
Removing
Handbrake
Adjusting
Brake
pedal
Adjusting
Rear
drum
brake
Adjusting
Bleeding
the
hydraulic
system
DESCRIPTION
The
vehicle
is
fitted
with
disc
brakes
for
the
front
wheels
and
leading
trailing
shoe
type
drum
brakes
for
the
rear
wheels
A
conventional
single
master
cylinder
is
fitted
to
the
Standard
and
DeLuxe
models
See
Fig
D
I
for
details
The
DeLuxe
models
are
however
additio
ally
equipped
with
a
Master
Vae
servo
unit
which
provides
a
much
higher
braking
performance
with
minimum
force
required
on
the
brake
pedal
A
tandem
master
cylinder
and
Master
Vac
servo
unit
are
fitted
as
standard
equipment
to
the
Datsun
CL30UA
and
CL3
OUT
models
Fig
D
2
gives
an
exploded
view
of
this
type
of
master
cylinder
The
handbrake
is
of
the
mechanical
type
with
the
handle
linked
to
the
rear
shoe
operating
lever
through
a
system
of
rods
and
wires
See
Fig
D
3
As
on
previous
models
a
brake
pressure
differential
warn
ing
light
switch
is
incorporated
with
dual
brake
circuits
The
front
and
rear
brake
systems
are
connected
to
the
switch
which
provides
a
warning
via
a
warning
light
on
the
instnllnent
panel
when
a
pressure
difference
of
13
to
17
kg
sq
cm
IB5
to
242
lb
sq
in
occurs
between
the
front
and
rear
systems
Brake
piping
layouts
of
the
single
and
tandem
master
cylinder
systems
are
shown
in
Figs
D
4
and
0
5
FRONT
DISC
BRAKE
Friction
pads
The
disc
brakes
are
self
adjusting
but
the
friction
pads
should
be
checked
for
wear
after
the
fIrst
6
000
un
4
000
miles
and
then
every
5
000
km
3
000
miles
The
pads
must
be
replaced
if
the
friction
lining
on
any
pad
has
worn
to
less
than
1
0
mm
0
04
in
The
thickness
of
the
pads
can
easily
be
checked
after
remov
ing
the
anti
rattle
clip
from
the
calliper
plate
Full
servicing
procedures
are
given
in
the
section
BRAKING
SYSTEM
for
vehicles
fitted
with
Ll4
Ll6
and
Ll8
engines
FRONT
DISC
BRAKE
Removal
and
Installation
Refer
to
the
section
BRAKING
SYSTEM
for
the
Ll4
L16
and
LIB
engines
for
full
details
of
the
removal
and
installation
procedures
Check
the
thickness
of
the
friction
pads
as
previously
described
and
replace
them
if
necessary
Check
the
brake
disc
for
scoring
and
out
of
round
The
standard
diSc
thickness
is
10
0
mm
0
394
in
and
must
not
be
reground
below
8
40
mm
0
331
in
The
run
out
of
the
disc
should
be
less
than
0
06
mm
0
0024
in
and
can
be
checked
with
a
dial
gauge
positioned
near
the
outer
diameter
of
the
disc
as
previously
described
REAR
DRUM
BRAKE
Removal
and
Installation
The
rear
drum
brakes
See
Fig
D
6
can
be
removed
and
inspected
as
described
in
the
section
BRAKING
SYSTEM
for
vehicles
fItted
with
L14
L16
LIB
engines
Examine
the
brake
drums
for
scoring
and
out
of
round
The
maximum
inner
diameter
of
the
drum
must
not
exceed
229
6
mm
9
040
in
after
reconditioning
Out
of
round
should
be
below
0
05
mm
0
002
in
Renew
the
brake
shoe
linings
if
they
are
contaminated
or
incorrectly
seated
or
if
the
thickness
of
the
lining
has
been
reduced
to
1
5
mm
0
06
in
or
less
Oil
or
grease
can
be
re
moved
from
the
linings
by
cleaning
thoroughly
with
carbon
tetrachloride
or
petrol
Check
the
shoe
return
springs
and
replace
them
if
they
have
become
weakened
Check
the
bores
of
the
wheel
cylinders
for
signs
of
wear
damage
or
corrosion
Renew
the
cylinders
and
pistons
if
the
clearance
between
the
two
parts
exceeds
to
0
15
mm
0
006
in
Renew
the
c
ps
when
overhauling
the
wheel
cylinders
MASTER
V
AC
SERVO
UNIT
Removing
and
Dismantling
The
servo
unit
should
be
removed
and
overhauled
at
yearly
intervals
A
Master
Vac
repair
kit
is
available
and
all
parts
marked
in
Fig
D
7
should
be
renewed
after
dismantling
the
unit
These
items
are
all
supplied
as
part
of
the
repair
kit
The
unit
can
be
removed
as
follows
Remove
the
clevis
pin
from
the
push
rod
and
detach
the
Master
V
ac
unit
from
the
brake
pedal
2
Disconnect
the
brake
tube
from
the
master
cylinder
and
the
vacuum
hooe
from
the
Master
Vac
3
Take
off
the
retaining
nuts
and
remove
the
Master
Vac
and
spacer
then
separate
the
master
cylinder
from
the
Master
Vac
Mark
the
front
cylinder
shell
and
the
rear
shell
and
stud
assembly
before
dismantling
the
unit
then
proceed
as
follows
S31