DODGE RAM 1500 1998 2.G Workshop Manual
Manufacturer: DODGE, Model Year: 1998, Model line: RAM 1500, Model: DODGE RAM 1500 1998 2.GPages: 2627
Page 1701 of 2627
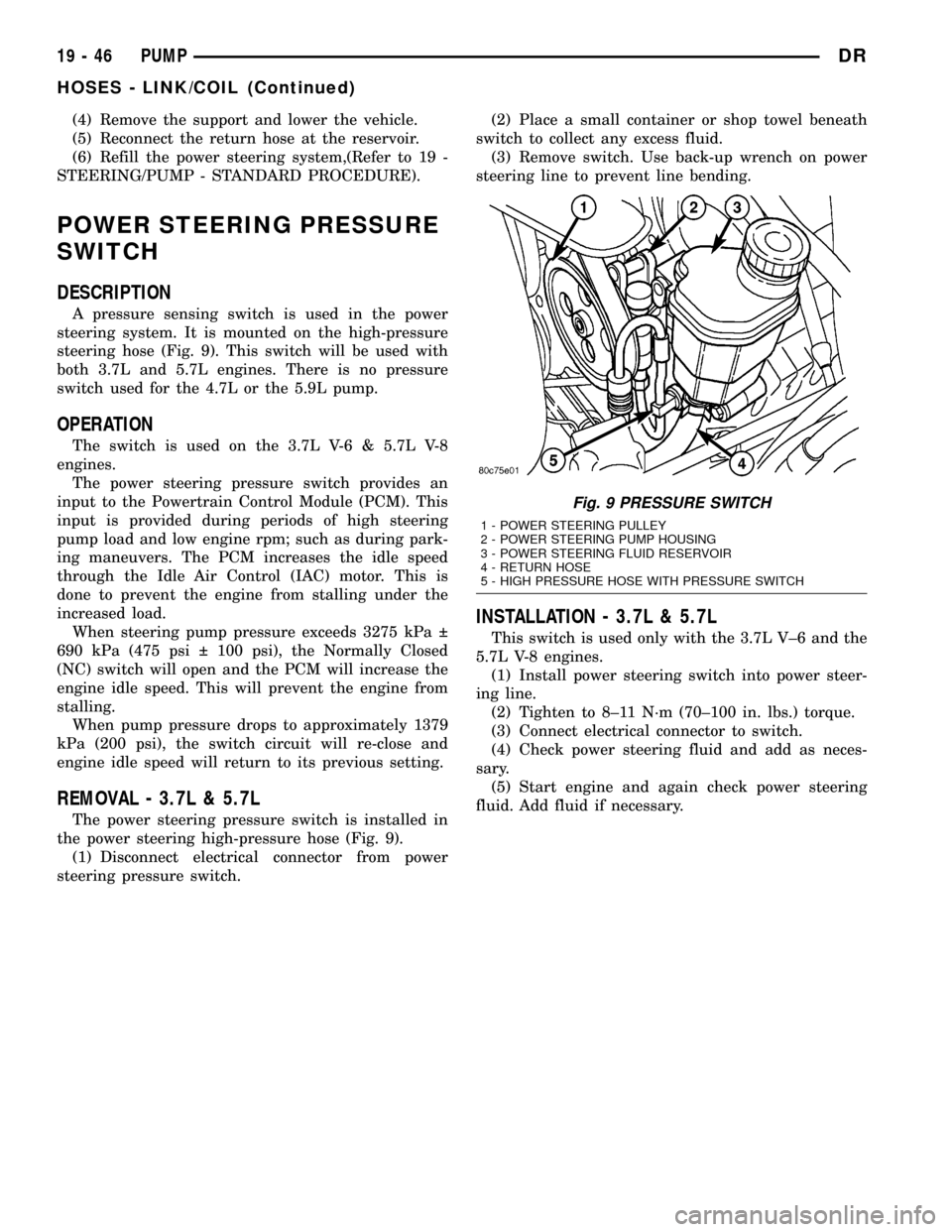
(4) Remove the support and lower the vehicle.
(5) Reconnect the return hose at the reservoir.
(6) Refill the power steering system,(Refer to 19 -
STEERING/PUMP - STANDARD PROCEDURE).
POWER STEERING PRESSURE
SWITCH
DESCRIPTION
A pressure sensing switch is used in the power
steering system. It is mounted on the high-pressure
steering hose (Fig. 9). This switch will be used with
both 3.7L and 5.7L engines. There is no pressure
switch used for the 4.7L or the 5.9L pump.
OPERATION
The switch is used on the 3.7L V-6 & 5.7L V-8
engines.
The power steering pressure switch provides an
input to the Powertrain Control Module (PCM). This
input is provided during periods of high steering
pump load and low engine rpm; such as during park-
ing maneuvers. The PCM increases the idle speed
through the Idle Air Control (IAC) motor. This is
done to prevent the engine from stalling under the
increased load.
When steering pump pressure exceeds 3275 kPa
690 kPa (475 psi 100 psi), the Normally Closed
(NC) switch will open and the PCM will increase the
engine idle speed. This will prevent the engine from
stalling.
When pump pressure drops to approximately 1379
kPa (200 psi), the switch circuit will re-close and
engine idle speed will return to its previous setting.
REMOVAL - 3.7L & 5.7L
The power steering pressure switch is installed in
the power steering high-pressure hose (Fig. 9).
(1) Disconnect electrical connector from power
steering pressure switch.(2) Place a small container or shop towel beneath
switch to collect any excess fluid.
(3) Remove switch. Use back-up wrench on power
steering line to prevent line bending.
INSTALLATION - 3.7L & 5.7L
This switch is used only with the 3.7L V±6 and the
5.7L V-8 engines.
(1) Install power steering switch into power steer-
ing line.
(2) Tighten to 8±11 N´m (70±100 in. lbs.) torque.
(3) Connect electrical connector to switch.
(4) Check power steering fluid and add as neces-
sary.
(5) Start engine and again check power steering
fluid. Add fluid if necessary.
Fig. 9 PRESSURE SWITCH
1 - POWER STEERING PULLEY
2 - POWER STEERING PUMP HOUSING
3 - POWER STEERING FLUID RESERVOIR
4 - RETURN HOSE
5 - HIGH PRESSURE HOSE WITH PRESSURE SWITCH
19 - 46 PUMPDR
HOSES - LINK/COIL (Continued)
Page 1702 of 2627
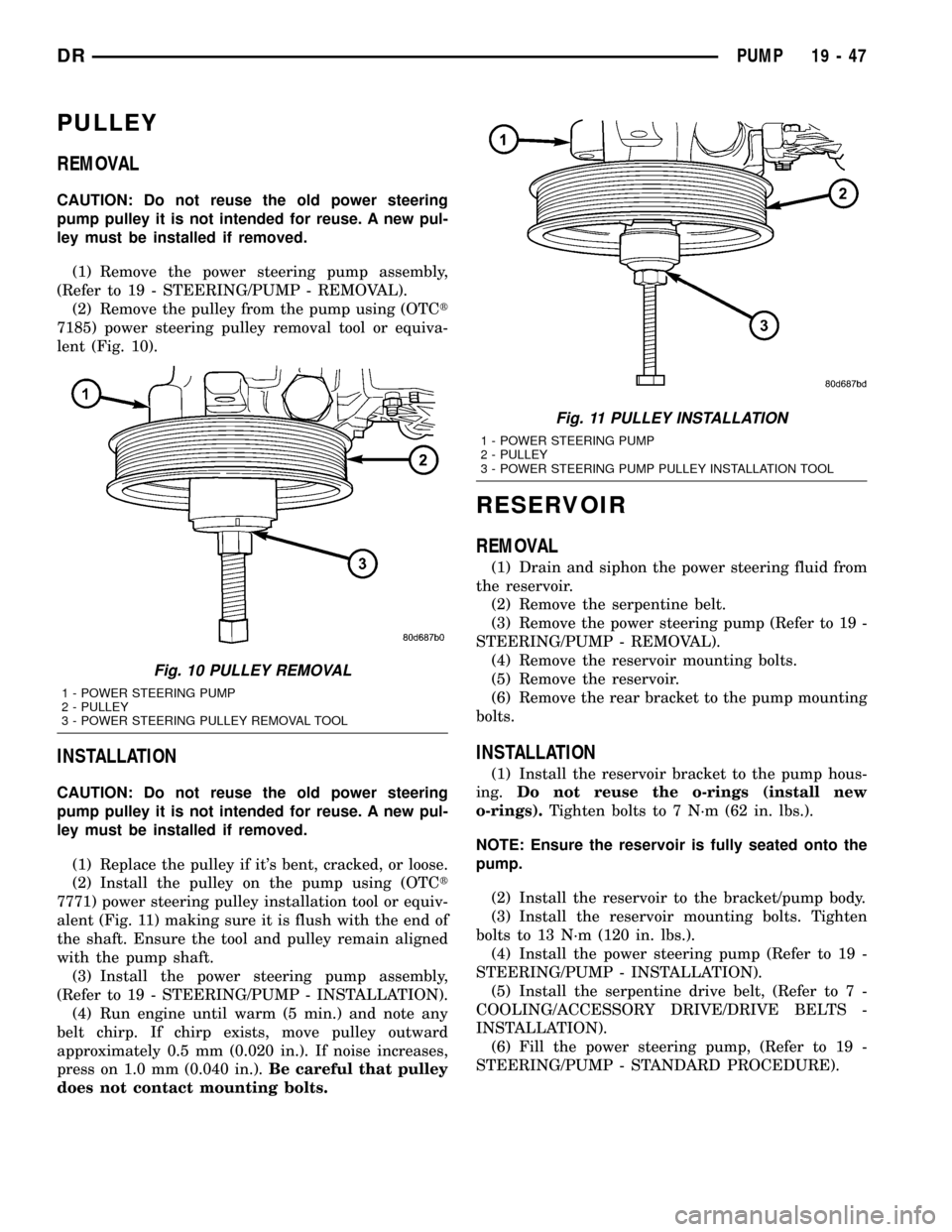
PULLEY
REMOVAL
CAUTION: Do not reuse the old power steering
pump pulley it is not intended for reuse. A new pul-
ley must be installed if removed.
(1) Remove the power steering pump assembly,
(Refer to 19 - STEERING/PUMP - REMOVAL).
(2) Remove the pulley from the pump using (OTCt
7185) power steering pulley removal tool or equiva-
lent (Fig. 10).
INSTALLATION
CAUTION: Do not reuse the old power steering
pump pulley it is not intended for reuse. A new pul-
ley must be installed if removed.
(1) Replace the pulley if it's bent, cracked, or loose.
(2) Install the pulley on the pump using (OTCt
7771) power steering pulley installation tool or equiv-
alent (Fig. 11) making sure it is flush with the end of
the shaft. Ensure the tool and pulley remain aligned
with the pump shaft.
(3) Install the power steering pump assembly,
(Refer to 19 - STEERING/PUMP - INSTALLATION).
(4) Run engine until warm (5 min.) and note any
belt chirp. If chirp exists, move pulley outward
approximately 0.5 mm (0.020 in.). If noise increases,
press on 1.0 mm (0.040 in.).Be careful that pulley
does not contact mounting bolts.
RESERVOIR
REMOVAL
(1) Drain and siphon the power steering fluid from
the reservoir.
(2) Remove the serpentine belt.
(3) Remove the power steering pump (Refer to 19 -
STEERING/PUMP - REMOVAL).
(4) Remove the reservoir mounting bolts.
(5) Remove the reservoir.
(6) Remove the rear bracket to the pump mounting
bolts.
INSTALLATION
(1) Install the reservoir bracket to the pump hous-
ing.Do not reuse the o-rings (install new
o-rings).Tighten bolts to 7 N´m (62 in. lbs.).
NOTE: Ensure the reservoir is fully seated onto the
pump.
(2) Install the reservoir to the bracket/pump body.
(3) Install the reservoir mounting bolts. Tighten
bolts to 13 N´m (120 in. lbs.).
(4) Install the power steering pump (Refer to 19 -
STEERING/PUMP - INSTALLATION).
(5) Install the serpentine drive belt, (Refer to 7 -
COOLING/ACCESSORY DRIVE/DRIVE BELTS -
INSTALLATION).
(6) Fill the power steering pump, (Refer to 19 -
STEERING/PUMP - STANDARD PROCEDURE).
Fig. 10 PULLEY REMOVAL
1 - POWER STEERING PUMP
2 - PULLEY
3 - POWER STEERING PULLEY REMOVAL TOOL
Fig. 11 PULLEY INSTALLATION
1 - POWER STEERING PUMP
2 - PULLEY
3 - POWER STEERING PUMP PULLEY INSTALLATION TOOL
DRPUMP 19 - 47
Page 1703 of 2627
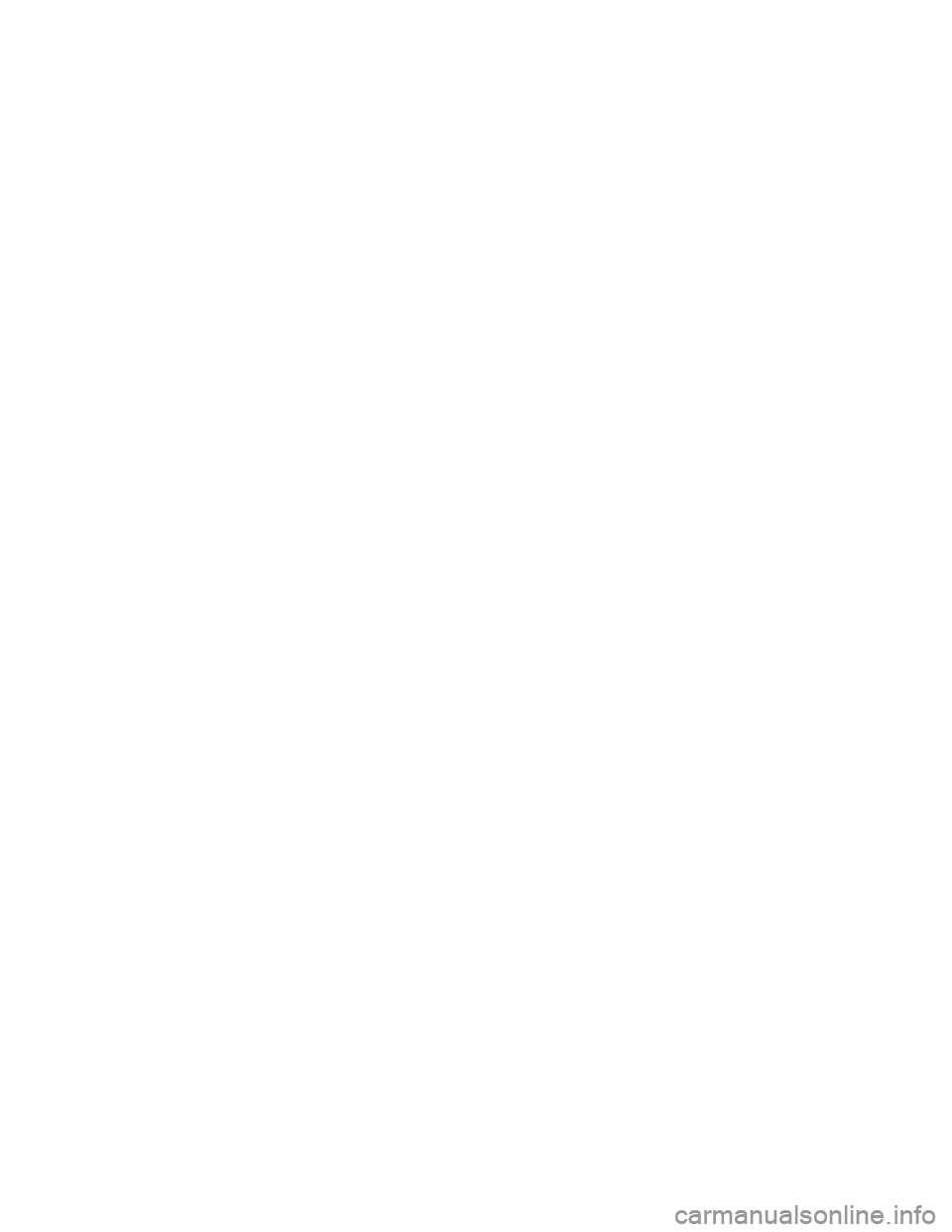
Page 1704 of 2627
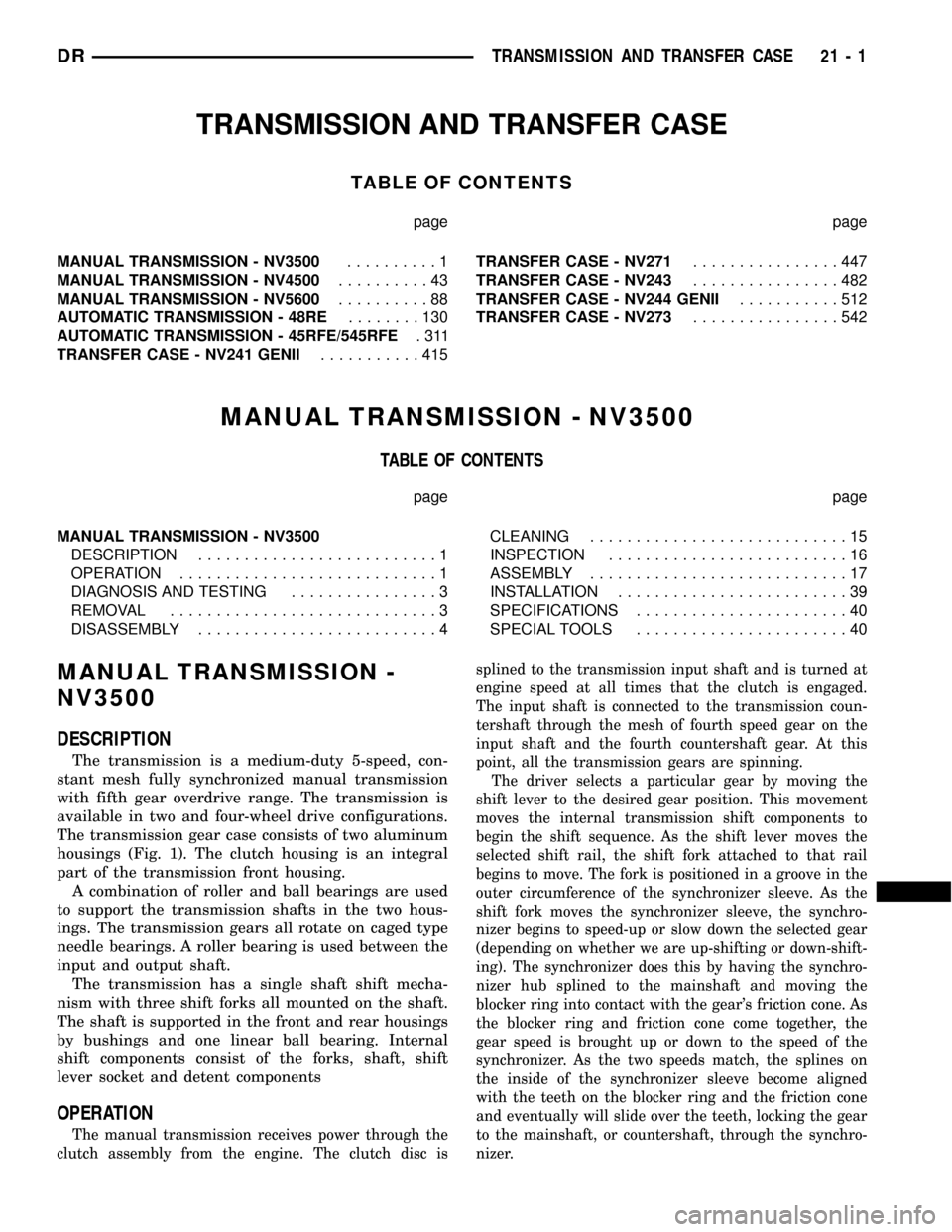
TRANSMISSION AND TRANSFER CASE
TABLE OF CONTENTS
page page
MANUAL TRANSMISSION - NV3500..........1
MANUAL TRANSMISSION - NV4500..........43
MANUAL TRANSMISSION - NV5600..........88
AUTOMATIC TRANSMISSION - 48RE........130
AUTOMATIC TRANSMISSION - 45RFE/545RFE.311
TRANSFER CASE - NV241 GENII...........415TRANSFER CASE - NV271................447
TRANSFER CASE - NV243................482
TRANSFER CASE - NV244 GENII...........512
TRANSFER CASE - NV273................542
MANUAL TRANSMISSION - NV3500
TABLE OF CONTENTS
page page
MANUAL TRANSMISSION - NV3500
DESCRIPTION..........................1
OPERATION............................1
DIAGNOSIS AND TESTING................3
REMOVAL.............................3
DISASSEMBLY..........................4CLEANING............................15
INSPECTION..........................16
ASSEMBLY............................17
INSTALLATION.........................39
SPECIFICATIONS.......................40
SPECIAL TOOLS.......................40
MANUAL TRANSMISSION -
NV3500
DESCRIPTION
The transmission is a medium-duty 5-speed, con-
stant mesh fully synchronized manual transmission
with fifth gear overdrive range. The transmission is
available in two and four-wheel drive configurations.
The transmission gear case consists of two aluminum
housings (Fig. 1). The clutch housing is an integral
part of the transmission front housing.
A combination of roller and ball bearings are used
to support the transmission shafts in the two hous-
ings. The transmission gears all rotate on caged type
needle bearings. A roller bearing is used between the
input and output shaft.
The transmission has a single shaft shift mecha-
nism with three shift forks all mounted on the shaft.
The shaft is supported in the front and rear housings
by bushings and one linear ball bearing. Internal
shift components consist of the forks, shaft, shift
lever socket and detent components
OPERATION
The manual transmission receives power through the
clutch assembly from the engine. The clutch disc issplined to the transmission input shaft and is turned at
engine speed at all times that the clutch is engaged.
The input shaft is connected to the transmission coun-
tershaft through the mesh of fourth speed gear on the
input shaft and the fourth countershaft gear. At this
point, all the transmission gears are spinning.
The driver selects a particular gear by moving the
shift lever to the desired gear position. This movement
moves the internal transmission shift components to
begin the shift sequence. As the shift lever moves the
selected shift rail, the shift fork attached to that rail
begins to move. The fork is positioned in a groove in the
outer circumference of the synchronizer sleeve. As the
shift fork moves the synchronizer sleeve, the synchro-
nizer begins to speed-up or slow down the selected gear
(depending on whether we are up-shifting or down-shift-
ing). The synchronizer does this by having the synchro-
nizer hub splined to the mainshaft and moving the
blocker ring into contact with the gear's friction cone. As
the blocker ring and friction cone come together, the
gear speed is brought up or down to the speed of the
synchronizer. As the two speeds match, the splines on
the inside of the synchronizer sleeve become aligned
with the teeth on the blocker ring and the friction cone
and eventually will slide over the teeth, locking the gear
to the mainshaft, or countershaft, through the synchro-
nizer.
DRTRANSMISSION AND TRANSFER CASE 21 - 1
Page 1705 of 2627
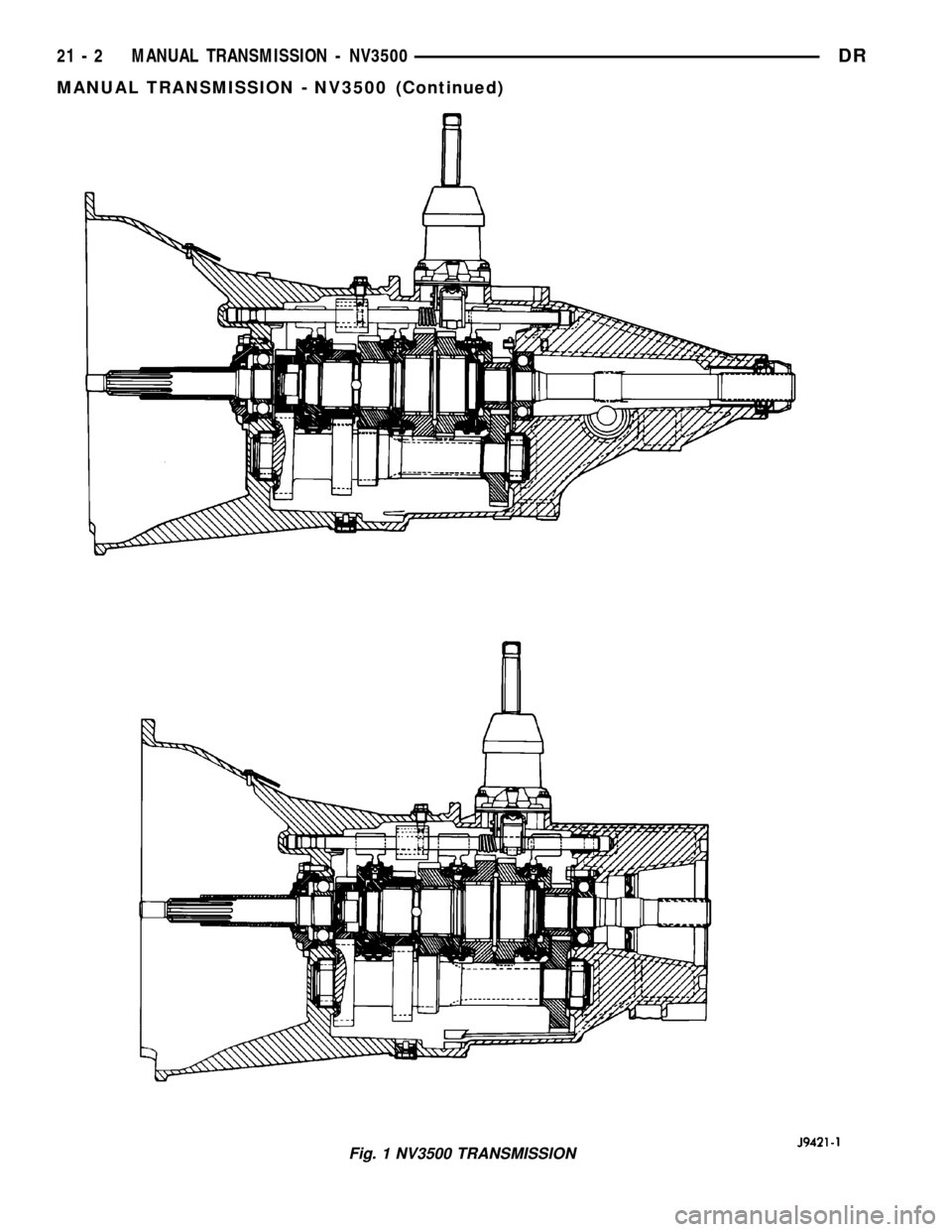
Fig. 1 NV3500 TRANSMISSION
21 - 2 MANUAL TRANSMISSION - NV3500DR
MANUAL TRANSMISSION - NV3500 (Continued)
Page 1706 of 2627
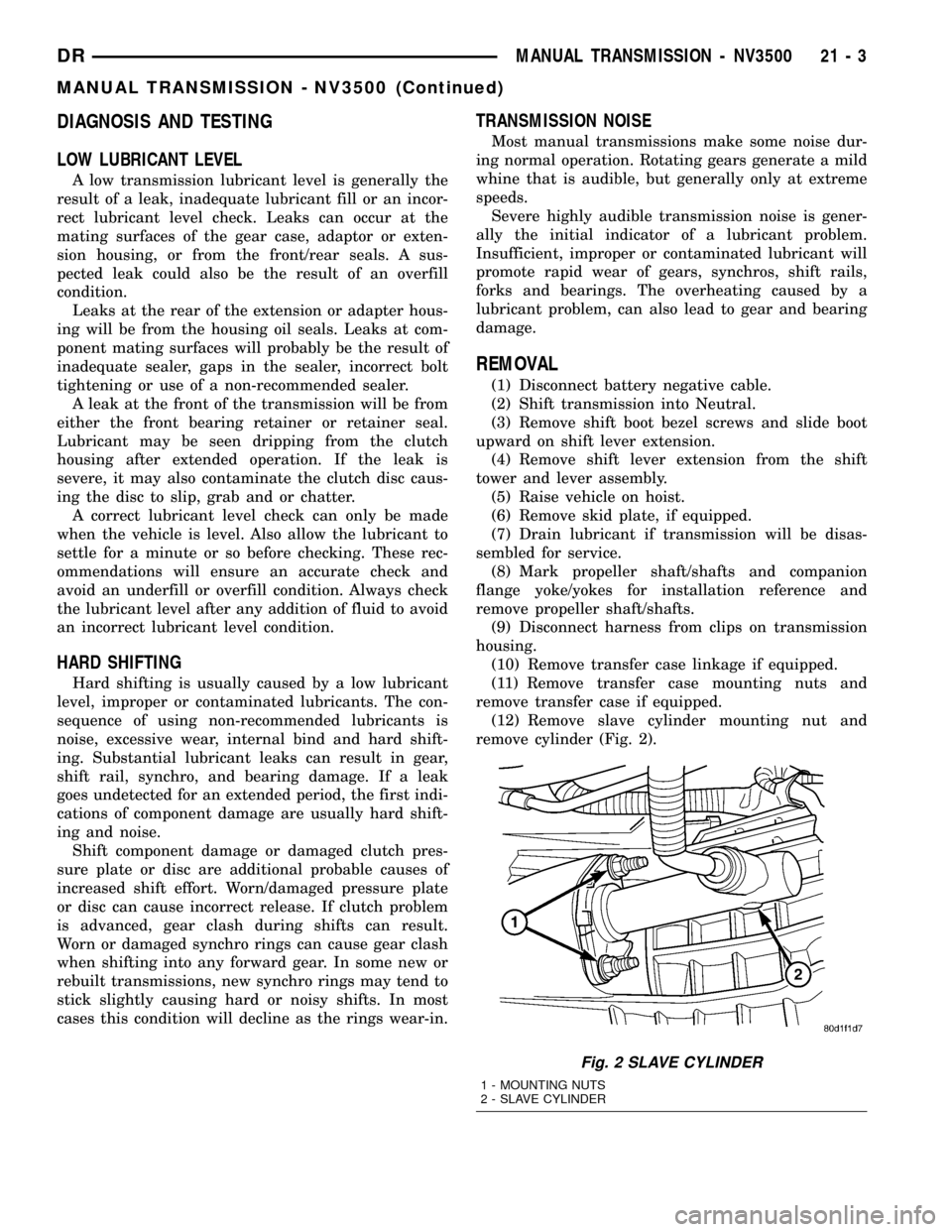
DIAGNOSIS AND TESTING
LOW LUBRICANT LEVEL
A low transmission lubricant level is generally the
result of a leak, inadequate lubricant fill or an incor-
rect lubricant level check. Leaks can occur at the
mating surfaces of the gear case, adaptor or exten-
sion housing, or from the front/rear seals. A sus-
pected leak could also be the result of an overfill
condition.
Leaks at the rear of the extension or adapter hous-
ing will be from the housing oil seals. Leaks at com-
ponent mating surfaces will probably be the result of
inadequate sealer, gaps in the sealer, incorrect bolt
tightening or use of a non-recommended sealer.
A leak at the front of the transmission will be from
either the front bearing retainer or retainer seal.
Lubricant may be seen dripping from the clutch
housing after extended operation. If the leak is
severe, it may also contaminate the clutch disc caus-
ing the disc to slip, grab and or chatter.
A correct lubricant level check can only be made
when the vehicle is level. Also allow the lubricant to
settle for a minute or so before checking. These rec-
ommendations will ensure an accurate check and
avoid an underfill or overfill condition. Always check
the lubricant level after any addition of fluid to avoid
an incorrect lubricant level condition.
HARD SHIFTING
Hard shifting is usually caused by a low lubricant
level, improper or contaminated lubricants. The con-
sequence of using non-recommended lubricants is
noise, excessive wear, internal bind and hard shift-
ing. Substantial lubricant leaks can result in gear,
shift rail, synchro, and bearing damage. If a leak
goes undetected for an extended period, the first indi-
cations of component damage are usually hard shift-
ing and noise.
Shift component damage or damaged clutch pres-
sure plate or disc are additional probable causes of
increased shift effort. Worn/damaged pressure plate
or disc can cause incorrect release. If clutch problem
is advanced, gear clash during shifts can result.
Worn or damaged synchro rings can cause gear clash
when shifting into any forward gear. In some new or
rebuilt transmissions, new synchro rings may tend to
stick slightly causing hard or noisy shifts. In most
cases this condition will decline as the rings wear-in.
TRANSMISSION NOISE
Most manual transmissions make some noise dur-
ing normal operation. Rotating gears generate a mild
whine that is audible, but generally only at extreme
speeds.
Severe highly audible transmission noise is gener-
ally the initial indicator of a lubricant problem.
Insufficient, improper or contaminated lubricant will
promote rapid wear of gears, synchros, shift rails,
forks and bearings. The overheating caused by a
lubricant problem, can also lead to gear and bearing
damage.
REMOVAL
(1) Disconnect battery negative cable.
(2) Shift transmission into Neutral.
(3) Remove shift boot bezel screws and slide boot
upward on shift lever extension.
(4) Remove shift lever extension from the shift
tower and lever assembly.
(5) Raise vehicle on hoist.
(6) Remove skid plate, if equipped.
(7) Drain lubricant if transmission will be disas-
sembled for service.
(8) Mark propeller shaft/shafts and companion
flange yoke/yokes for installation reference and
remove propeller shaft/shafts.
(9) Disconnect harness from clips on transmission
housing.
(10) Remove transfer case linkage if equipped.
(11) Remove transfer case mounting nuts and
remove transfer case if equipped.
(12) Remove slave cylinder mounting nut and
remove cylinder (Fig. 2).
Fig. 2 SLAVE CYLINDER
1 - MOUNTING NUTS
2 - SLAVE CYLINDER
DRMANUAL TRANSMISSION - NV3500 21 - 3
MANUAL TRANSMISSION - NV3500 (Continued)
Page 1707 of 2627
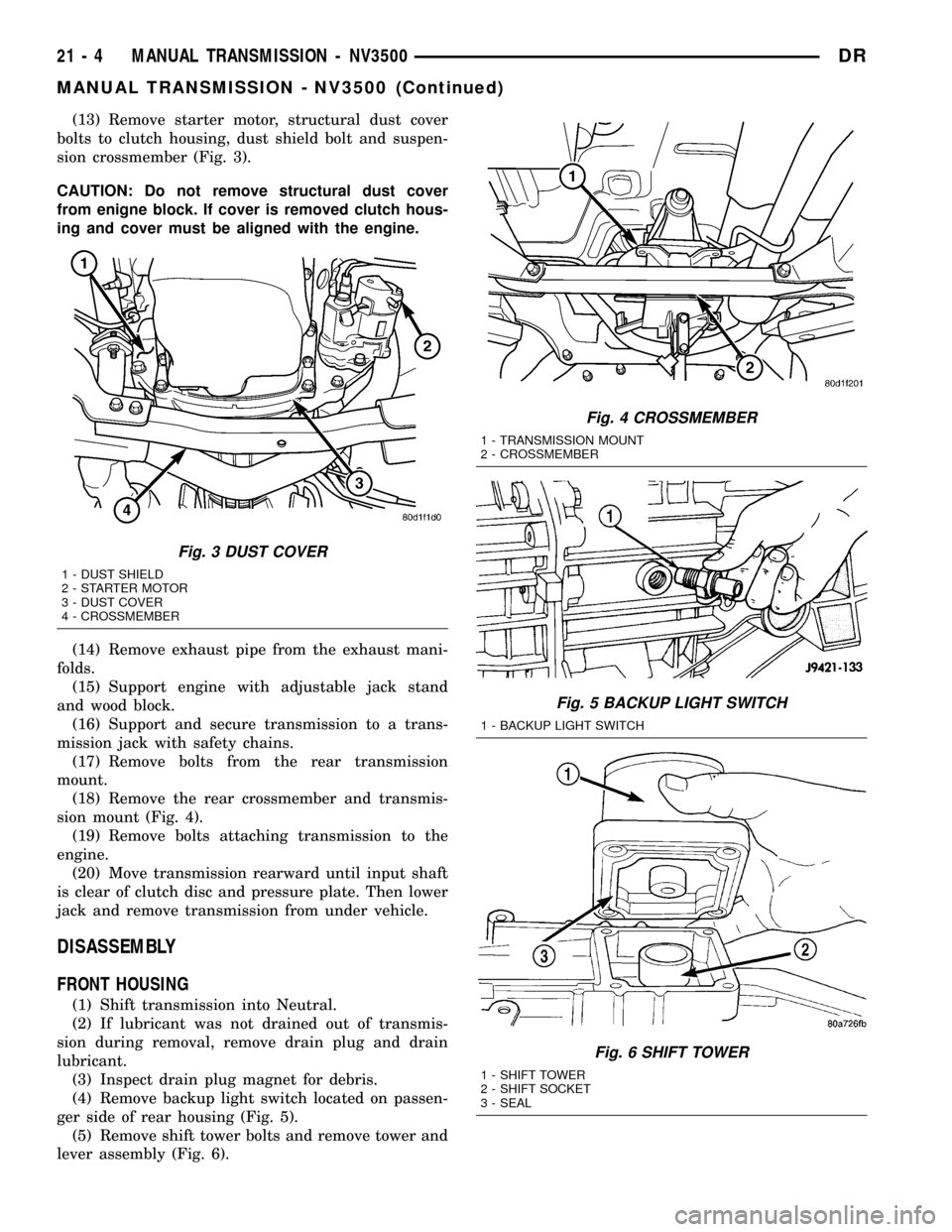
(13) Remove starter motor, structural dust cover
bolts to clutch housing, dust shield bolt and suspen-
sion crossmember (Fig. 3).
CAUTION: Do not remove structural dust cover
from enigne block. If cover is removed clutch hous-
ing and cover must be aligned with the engine.
(14) Remove exhaust pipe from the exhaust mani-
folds.
(15) Support engine with adjustable jack stand
and wood block.
(16) Support and secure transmission to a trans-
mission jack with safety chains.
(17) Remove bolts from the rear transmission
mount.
(18) Remove the rear crossmember and transmis-
sion mount (Fig. 4).
(19) Remove bolts attaching transmission to the
engine.
(20) Move transmission rearward until input shaft
is clear of clutch disc and pressure plate. Then lower
jack and remove transmission from under vehicle.
DISASSEMBLY
FRONT HOUSING
(1) Shift transmission into Neutral.
(2) If lubricant was not drained out of transmis-
sion during removal, remove drain plug and drain
lubricant.
(3) Inspect drain plug magnet for debris.
(4) Remove backup light switch located on passen-
ger side of rear housing (Fig. 5).
(5) Remove shift tower bolts and remove tower and
lever assembly (Fig. 6).
Fig. 3 DUST COVER
1 - DUST SHIELD
2 - STARTER MOTOR
3 - DUST COVER
4 - CROSSMEMBER
Fig. 4 CROSSMEMBER
1 - TRANSMISSION MOUNT
2 - CROSSMEMBER
Fig. 5 BACKUP LIGHT SWITCH
1 - BACKUP LIGHT SWITCH
Fig. 6 SHIFT TOWER
1 - SHIFT TOWER
2 - SHIFT SOCKET
3 - SEAL
21 - 4 MANUAL TRANSMISSION - NV3500DR
MANUAL TRANSMISSION - NV3500 (Continued)
Page 1708 of 2627
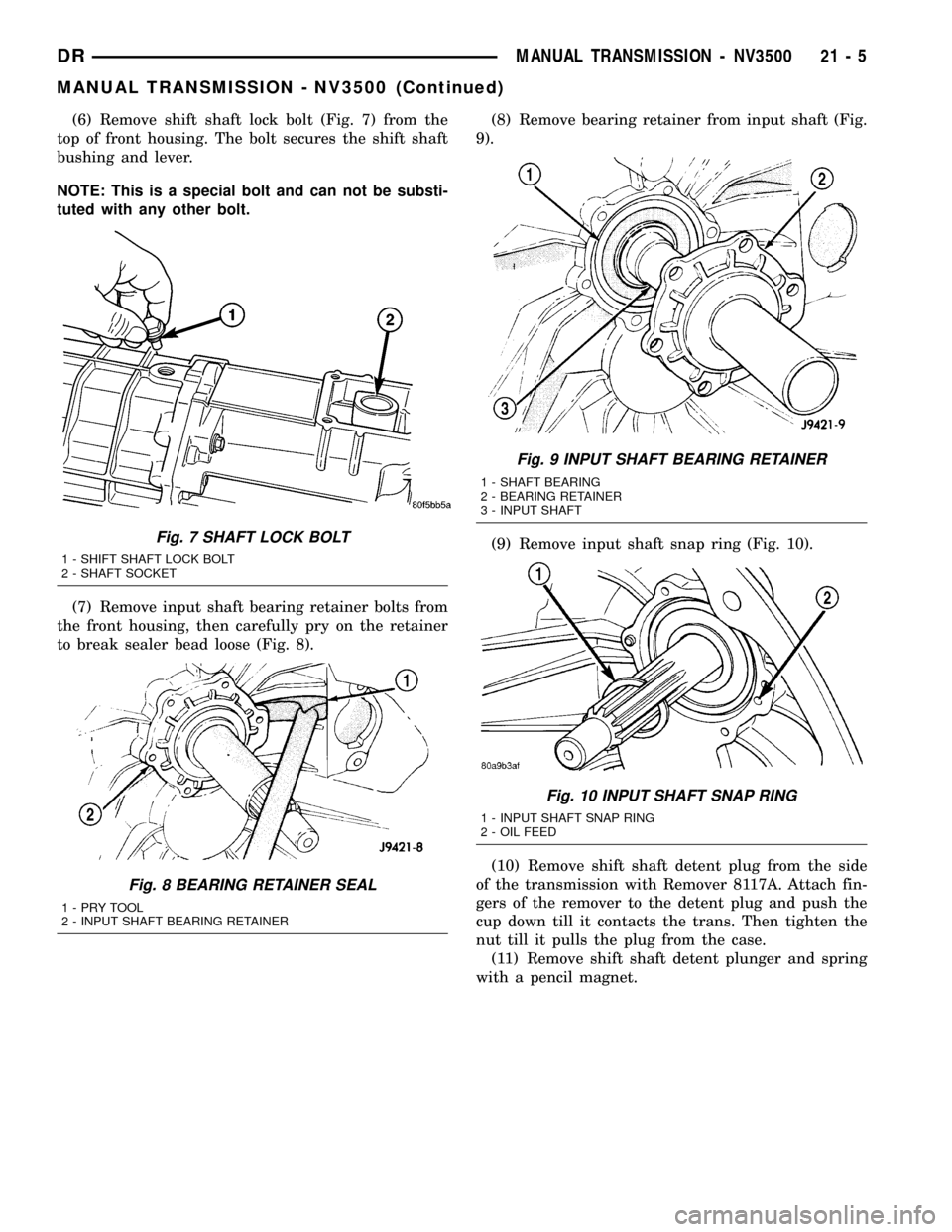
(6) Remove shift shaft lock bolt (Fig. 7) from the
top of front housing. The bolt secures the shift shaft
bushing and lever.
NOTE: This is a special bolt and can not be substi-
tuted with any other bolt.
(7) Remove input shaft bearing retainer bolts from
the front housing, then carefully pry on the retainer
to break sealer bead loose (Fig. 8).(8) Remove bearing retainer from input shaft (Fig.
9).
(9) Remove input shaft snap ring (Fig. 10).
(10) Remove shift shaft detent plug from the side
of the transmission with Remover 8117A. Attach fin-
gers of the remover to the detent plug and push the
cup down till it contacts the trans. Then tighten the
nut till it pulls the plug from the case.
(11) Remove shift shaft detent plunger and spring
with a pencil magnet.
Fig. 7 SHAFT LOCK BOLT
1 - SHIFT SHAFT LOCK BOLT
2 - SHAFT SOCKET
Fig. 8 BEARING RETAINER SEAL
1-PRYTOOL
2 - INPUT SHAFT BEARING RETAINER
Fig. 9 INPUT SHAFT BEARING RETAINER
1 - SHAFT BEARING
2 - BEARING RETAINER
3 - INPUT SHAFT
Fig. 10 INPUT SHAFT SNAP RING
1 - INPUT SHAFT SNAP RING
2 - OIL FEED
DRMANUAL TRANSMISSION - NV3500 21 - 5
MANUAL TRANSMISSION - NV3500 (Continued)
Page 1709 of 2627
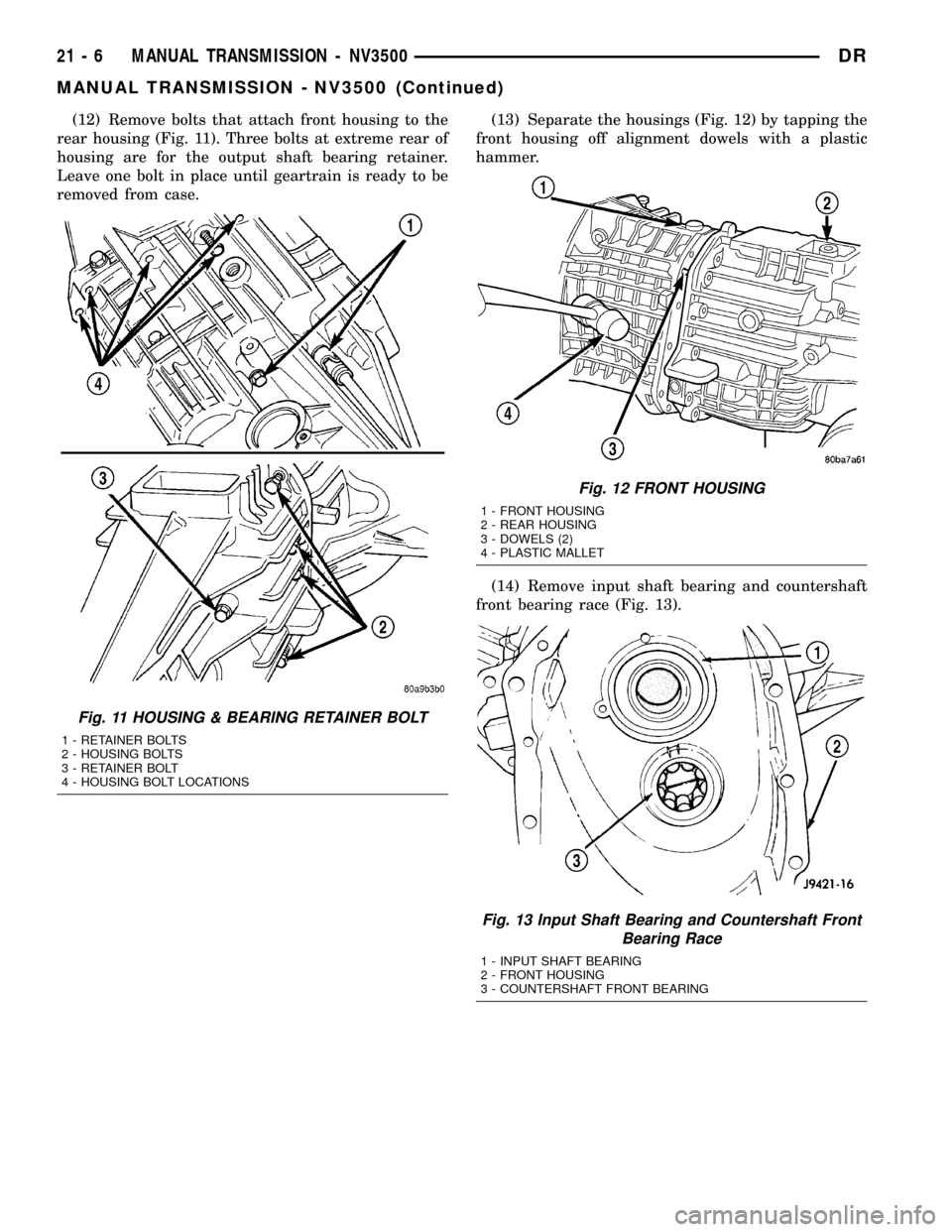
(12) Remove bolts that attach front housing to the
rear housing (Fig. 11). Three bolts at extreme rear of
housing are for the output shaft bearing retainer.
Leave one bolt in place until geartrain is ready to be
removed from case.(13) Separate the housings (Fig. 12) by tapping the
front housing off alignment dowels with a plastic
hammer.
(14) Remove input shaft bearing and countershaft
front bearing race (Fig. 13).
Fig. 11 HOUSING & BEARING RETAINER BOLT
1 - RETAINER BOLTS
2 - HOUSING BOLTS
3 - RETAINER BOLT
4 - HOUSING BOLT LOCATIONS
Fig. 12 FRONT HOUSING
1 - FRONT HOUSING
2 - REAR HOUSING
3 - DOWELS (2)
4 - PLASTIC MALLET
Fig. 13 Input Shaft Bearing and Countershaft Front
Bearing Race
1 - INPUT SHAFT BEARING
2 - FRONT HOUSING
3 - COUNTERSHAFT FRONT BEARING
21 - 6 MANUAL TRANSMISSION - NV3500DR
MANUAL TRANSMISSION - NV3500 (Continued)
Page 1710 of 2627
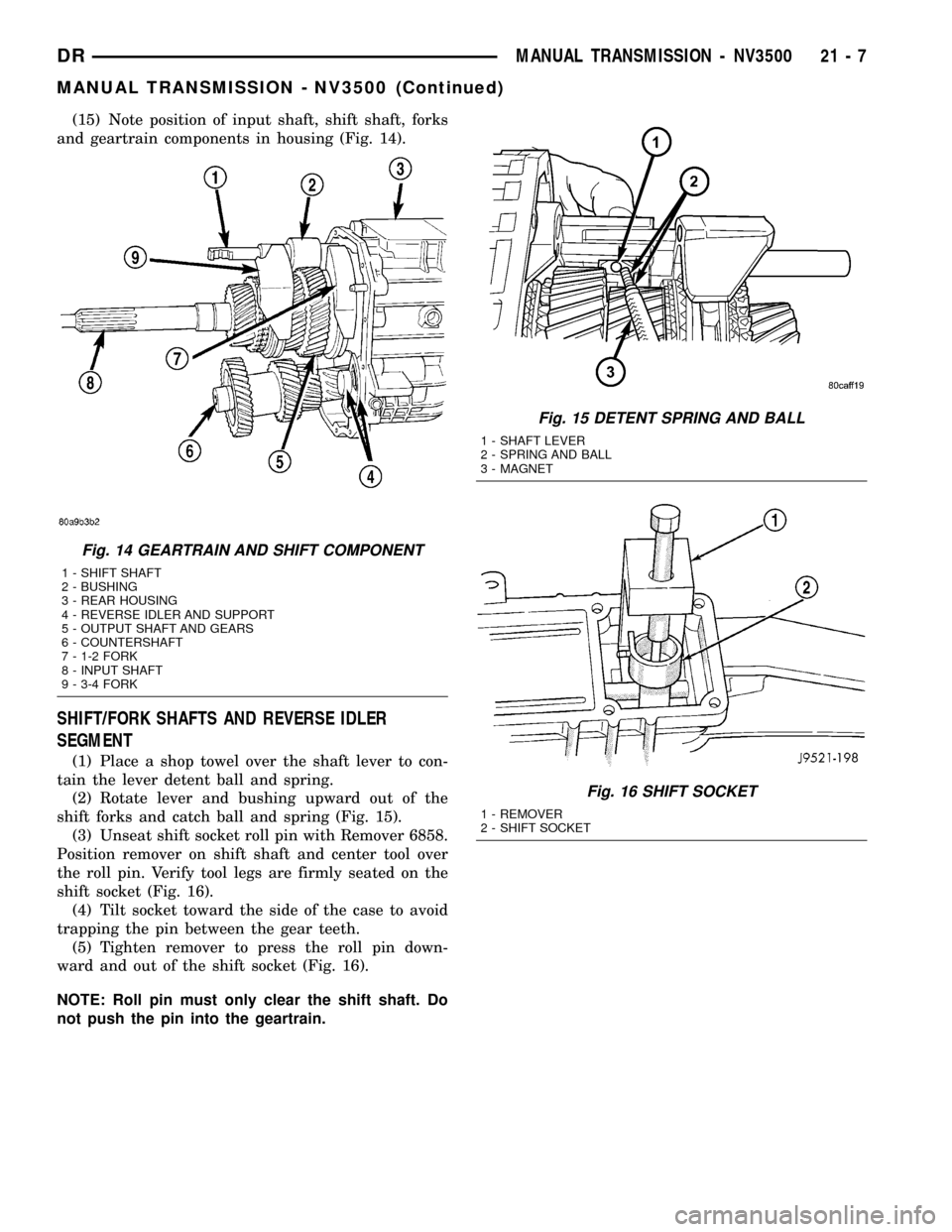
(15) Note position of input shaft, shift shaft, forks
and geartrain components in housing (Fig. 14).
SHIFT/FORK SHAFTS AND REVERSE IDLER
SEGMENT
(1) Place a shop towel over the shaft lever to con-
tain the lever detent ball and spring.
(2) Rotate lever and bushing upward out of the
shift forks and catch ball and spring (Fig. 15).
(3) Unseat shift socket roll pin with Remover 6858.
Position remover on shift shaft and center tool over
the roll pin. Verify tool legs are firmly seated on the
shift socket (Fig. 16).
(4) Tilt socket toward the side of the case to avoid
trapping the pin between the gear teeth.
(5) Tighten remover to press the roll pin down-
ward and out of the shift socket (Fig. 16).
NOTE: Roll pin must only clear the shift shaft. Do
not push the pin into the geartrain.
Fig. 14 GEARTRAIN AND SHIFT COMPONENT
1 - SHIFT SHAFT
2 - BUSHING
3 - REAR HOUSING
4 - REVERSE IDLER AND SUPPORT
5 - OUTPUT SHAFT AND GEARS
6 - COUNTERSHAFT
7 - 1-2 FORK
8 - INPUT SHAFT
9 - 3-4 FORK
Fig. 15 DETENT SPRING AND BALL
1 - SHAFT LEVER
2 - SPRING AND BALL
3 - MAGNET
Fig. 16 SHIFT SOCKET
1 - REMOVER
2 - SHIFT SOCKET
DRMANUAL TRANSMISSION - NV3500 21 - 7
MANUAL TRANSMISSION - NV3500 (Continued)