DODGE RAM 1500 1998 2.G Workshop Manual
Manufacturer: DODGE, Model Year: 1998, Model line: RAM 1500, Model: DODGE RAM 1500 1998 2.GPages: 2627
Page 1861 of 2627
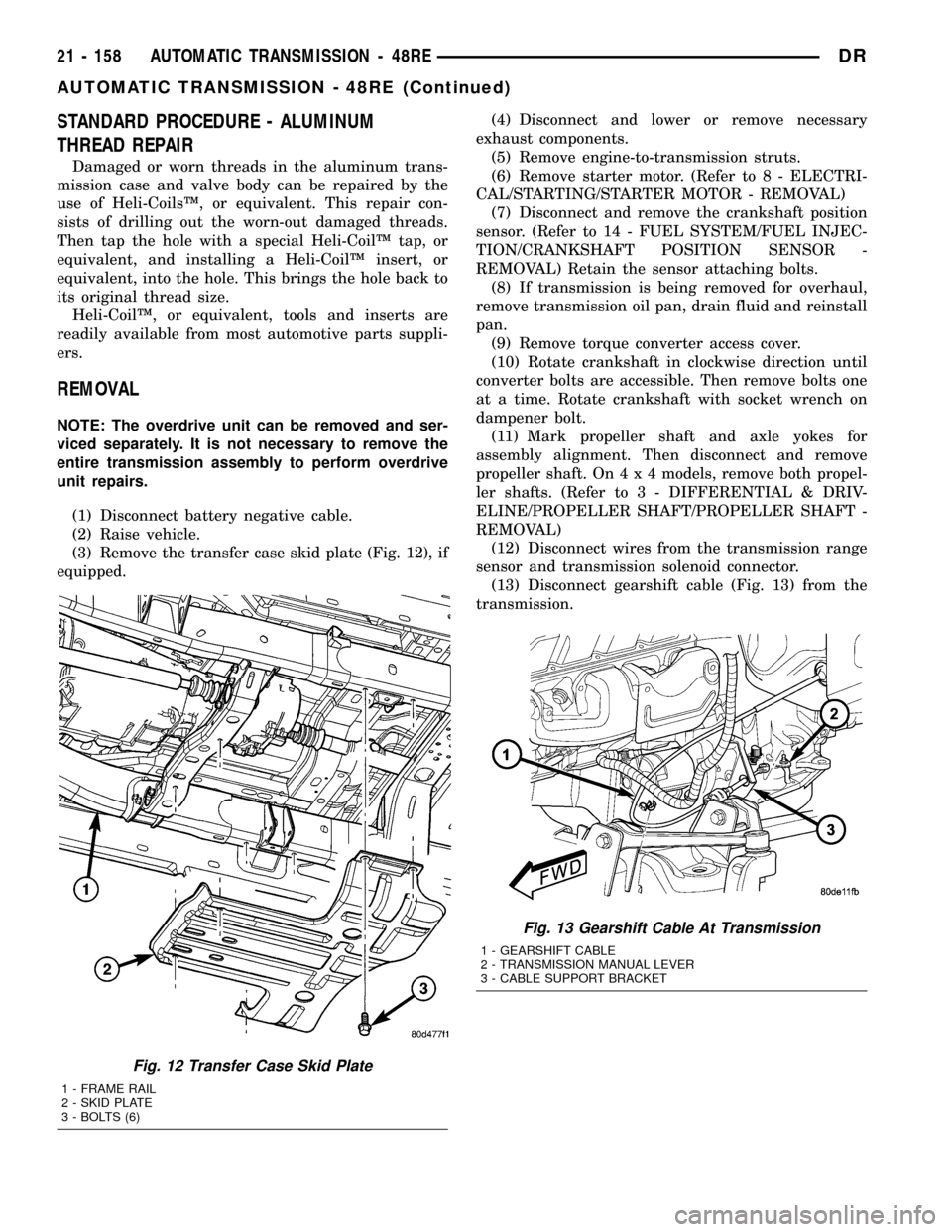
STANDARD PROCEDURE - ALUMINUM
THREAD REPAIR
Damaged or worn threads in the aluminum trans-
mission case and valve body can be repaired by the
use of Heli-CoilsŸ, or equivalent. This repair con-
sists of drilling out the worn-out damaged threads.
Then tap the hole with a special Heli-CoilŸ tap, or
equivalent, and installing a Heli-CoilŸ insert, or
equivalent, into the hole. This brings the hole back to
its original thread size.
Heli-CoilŸ, or equivalent, tools and inserts are
readily available from most automotive parts suppli-
ers.
REMOVAL
NOTE: The overdrive unit can be removed and ser-
viced separately. It is not necessary to remove the
entire transmission assembly to perform overdrive
unit repairs.
(1) Disconnect battery negative cable.
(2) Raise vehicle.
(3) Remove the transfer case skid plate (Fig. 12), if
equipped.(4) Disconnect and lower or remove necessary
exhaust components.
(5) Remove engine-to-transmission struts.
(6) Remove starter motor. (Refer to 8 - ELECTRI-
CAL/STARTING/STARTER MOTOR - REMOVAL)
(7) Disconnect and remove the crankshaft position
sensor. (Refer to 14 - FUEL SYSTEM/FUEL INJEC-
TION/CRANKSHAFT POSITION SENSOR -
REMOVAL) Retain the sensor attaching bolts.
(8) If transmission is being removed for overhaul,
remove transmission oil pan, drain fluid and reinstall
pan.
(9) Remove torque converter access cover.
(10) Rotate crankshaft in clockwise direction until
converter bolts are accessible. Then remove bolts one
at a time. Rotate crankshaft with socket wrench on
dampener bolt.
(11) Mark propeller shaft and axle yokes for
assembly alignment. Then disconnect and remove
propeller shaft. On4x4models, remove both propel-
ler shafts. (Refer to 3 - DIFFERENTIAL & DRIV-
ELINE/PROPELLER SHAFT/PROPELLER SHAFT -
REMOVAL)
(12) Disconnect wires from the transmission range
sensor and transmission solenoid connector.
(13) Disconnect gearshift cable (Fig. 13) from the
transmission.
Fig. 12 Transfer Case Skid Plate
1 - FRAME RAIL
2 - SKID PLATE
3 - BOLTS (6)
Fig. 13 Gearshift Cable At Transmission
1 - GEARSHIFT CABLE
2 - TRANSMISSION MANUAL LEVER
3 - CABLE SUPPORT BRACKET
21 - 158 AUTOMATIC TRANSMISSION - 48REDR
AUTOMATIC TRANSMISSION - 48RE (Continued)
Page 1862 of 2627

(14) Disconnect throttle valve cable from transmis-
sion bracket and throttle valve lever.
(15) On 4X4 models, disconnect shift rod from
transfer case shift lever.
(16) Support rear of engine with safety stand or
jack.
(17) Raise transmission slightly with service jack
to relieve load on crossmember and supports.
(18) Remove bolts securing rear support and cush-
ion (Fig. 14) and (Fig. 15) to transmission and cross-
member and remove rear support.
(19) Remove bolts attaching crossmember to frame
and remove crossmember.
(20) On 4X4 models, remove transfer case with
transmission jack or aid of helper.
(21) Disconnect fluid cooler lines at transmission.
(22) Remove fill tube bracket bolts and pull tube
out of transmission. Retain fill tube seal. On 4X4
models, it will also be necessary to remove bolt
attaching transfer case vent tube to converter hous-
ing (Fig. 16).
(23) Remove all converter housing bolts.
(24) Carefully work transmission and torque con-
verter assembly rearward off engine block dowels.
(25) Lower transmission and remove assembly
from under the vehicle.
(26) To remove torque converter, remove C-clamp
from edge of bell housing and carefully slide torque
converter out of the transmission.
Fig. 14 Engine Rear Mount - 4X2 Automatic
Transmission
1 - ENGINE REAR MOUNT
2 - BOLT
3 - NUT
4 - THROUGH BOLT NUT
5 - TRANSMISSION
Fig. 15 Engine Rear Mount - 4X4 Automatic
Transmission
1 - TRANSMISSION
2 - ENGINE REAR MOUNT
3 - BOLT
Fig. 16 Fill Tube Attachment
1 - TRANSFER CASE VENT TUBE
2 - FILL TUBE (V8)
3 - TUBE SEAL
4 - FILL TUBE (V6)
DRAUTOMATIC TRANSMISSION - 48RE 21 - 159
AUTOMATIC TRANSMISSION - 48RE (Continued)
Page 1863 of 2627
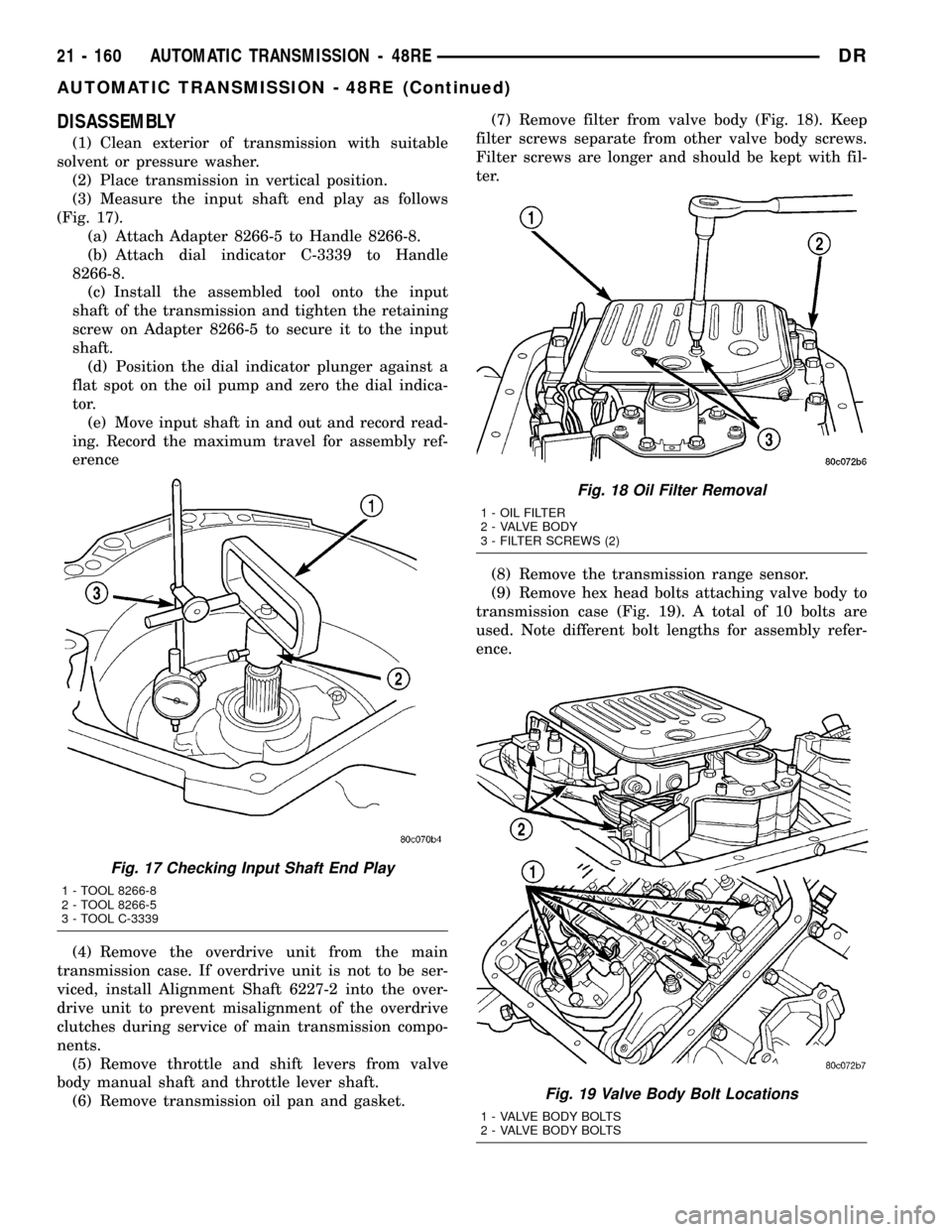
DISASSEMBLY
(1) Clean exterior of transmission with suitable
solvent or pressure washer.
(2) Place transmission in vertical position.
(3) Measure the input shaft end play as follows
(Fig. 17).
(a) Attach Adapter 8266-5 to Handle 8266-8.
(b) Attach dial indicator C-3339 to Handle
8266-8.
(c) Install the assembled tool onto the input
shaft of the transmission and tighten the retaining
screw on Adapter 8266-5 to secure it to the input
shaft.
(d) Position the dial indicator plunger against a
flat spot on the oil pump and zero the dial indica-
tor.
(e) Move input shaft in and out and record read-
ing. Record the maximum travel for assembly ref-
erence
(4) Remove the overdrive unit from the main
transmission case. If overdrive unit is not to be ser-
viced, install Alignment Shaft 6227-2 into the over-
drive unit to prevent misalignment of the overdrive
clutches during service of main transmission compo-
nents.
(5) Remove throttle and shift levers from valve
body manual shaft and throttle lever shaft.
(6) Remove transmission oil pan and gasket.(7) Remove filter from valve body (Fig. 18). Keep
filter screws separate from other valve body screws.
Filter screws are longer and should be kept with fil-
ter.
(8) Remove the transmission range sensor.
(9) Remove hex head bolts attaching valve body to
transmission case (Fig. 19). A total of 10 bolts are
used. Note different bolt lengths for assembly refer-
ence.
Fig. 19 Valve Body Bolt Locations
1 - VALVE BODY BOLTS
2 - VALVE BODY BOLTS
Fig. 17 Checking Input Shaft End Play
1 - TOOL 8266-8
2 - TOOL 8266-5
3 - TOOL C-3339
Fig. 18 Oil Filter Removal
1 - OIL FILTER
2 - VALVE BODY
3 - FILTER SCREWS (2)
21 - 160 AUTOMATIC TRANSMISSION - 48REDR
AUTOMATIC TRANSMISSION - 48RE (Continued)
Page 1864 of 2627
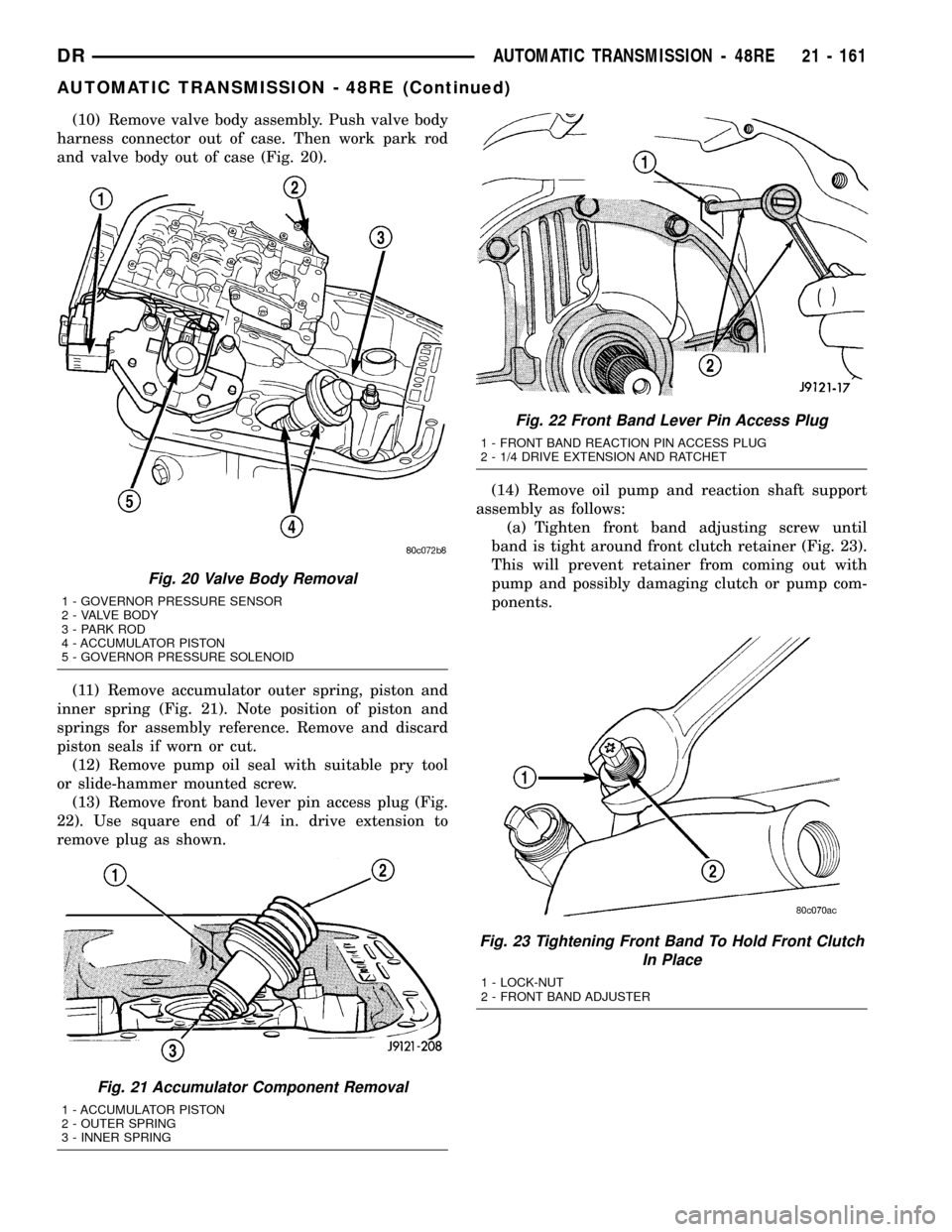
(10) Remove valve body assembly. Push valve body
harness connector out of case. Then work park rod
and valve body out of case (Fig. 20).
(11) Remove accumulator outer spring, piston and
inner spring (Fig. 21). Note position of piston and
springs for assembly reference. Remove and discard
piston seals if worn or cut.
(12) Remove pump oil seal with suitable pry tool
or slide-hammer mounted screw.
(13) Remove front band lever pin access plug (Fig.
22). Use square end of 1/4 in. drive extension to
remove plug as shown.(14) Remove oil pump and reaction shaft support
assembly as follows:
(a) Tighten front band adjusting screw until
band is tight around front clutch retainer (Fig. 23).
This will prevent retainer from coming out with
pump and possibly damaging clutch or pump com-
ponents.
Fig. 23 Tightening Front Band To Hold Front Clutch
In Place
1 - LOCK-NUT
2 - FRONT BAND ADJUSTER
Fig. 20 Valve Body Removal
1 - GOVERNOR PRESSURE SENSOR
2 - VALVE BODY
3 - PARK ROD
4 - ACCUMULATOR PISTON
5 - GOVERNOR PRESSURE SOLENOID
Fig. 21 Accumulator Component Removal
1 - ACCUMULATOR PISTON
2 - OUTER SPRING
3 - INNER SPRING
Fig. 22 Front Band Lever Pin Access Plug
1 - FRONT BAND REACTION PIN ACCESS PLUG
2 - 1/4 DRIVE EXTENSION AND RATCHET
DRAUTOMATIC TRANSMISSION - 48RE 21 - 161
AUTOMATIC TRANSMISSION - 48RE (Continued)
Page 1865 of 2627

(b) Remove oil pump bolts.
(c) Thread Slide Hammer Tools C-3752 into
threaded holes in flange of oil pump housing (Fig.
24).
(d) Remove oil pump and reaction shaft support
by bumping slide hammers outward alternately to
pull pump from case (Fig. 25).
(15) Remove oil pump gasket (Fig. 26). Note gas-
ket position in case for assembly reference.(16) Loosen front band adjusting screw until band
is completely loose.
(17) Remove front band strut and anchor (Fig. 27).
Fig. 24 Oil Pump Removal Tools
1 - PUMP HOUSING
2 - SLIDE HAMMER TOOLS (THREAD INTO PUMP HOUSING)
Fig. 25 Oil Pump Removal
1 - OIL PUMP AND REACTION SHAFT SUPPORT
Fig. 26 Oil Pump Gasket
1 - OIL PUMP GASKET
Fig. 27 Front Band Linkage
1 - LEVER
2 - STRUT
3 - ANCHOR
4 - FRONT BAND
21 - 162 AUTOMATIC TRANSMISSION - 48REDR
AUTOMATIC TRANSMISSION - 48RE (Continued)
Page 1866 of 2627
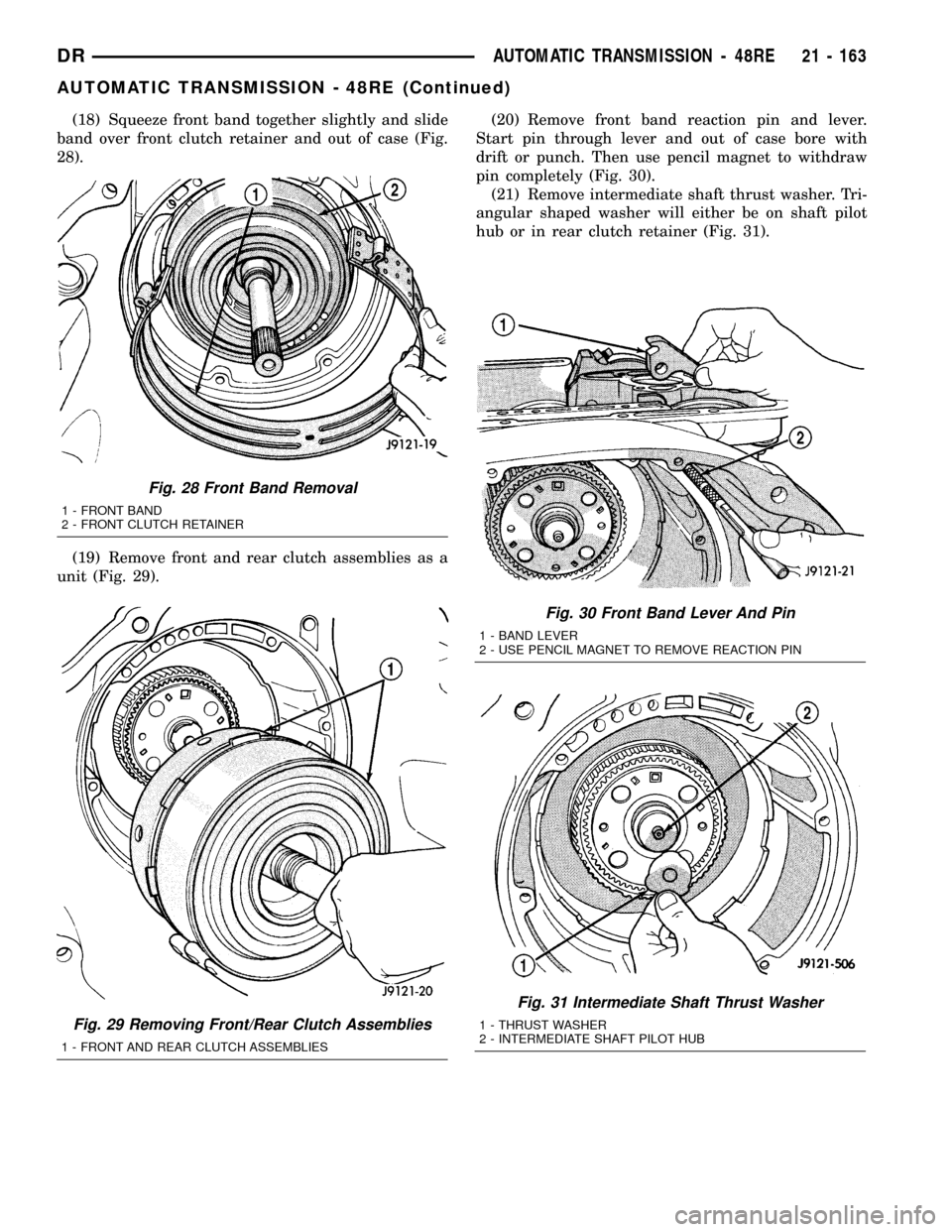
(18) Squeeze front band together slightly and slide
band over front clutch retainer and out of case (Fig.
28).
(19) Remove front and rear clutch assemblies as a
unit (Fig. 29).(20) Remove front band reaction pin and lever.
Start pin through lever and out of case bore with
drift or punch. Then use pencil magnet to withdraw
pin completely (Fig. 30).
(21) Remove intermediate shaft thrust washer. Tri-
angular shaped washer will either be on shaft pilot
hub or in rear clutch retainer (Fig. 31).
Fig. 29 Removing Front/Rear Clutch Assemblies
1 - FRONT AND REAR CLUTCH ASSEMBLIES
Fig. 30 Front Band Lever And Pin
1 - BAND LEVER
2 - USE PENCIL MAGNET TO REMOVE REACTION PIN
Fig. 31 Intermediate Shaft Thrust Washer
1 - THRUST WASHER
2 - INTERMEDIATE SHAFT PILOT HUB
Fig. 28 Front Band Removal
1 - FRONT BAND
2 - FRONT CLUTCH RETAINER
DRAUTOMATIC TRANSMISSION - 48RE 21 - 163
AUTOMATIC TRANSMISSION - 48RE (Continued)
Page 1867 of 2627
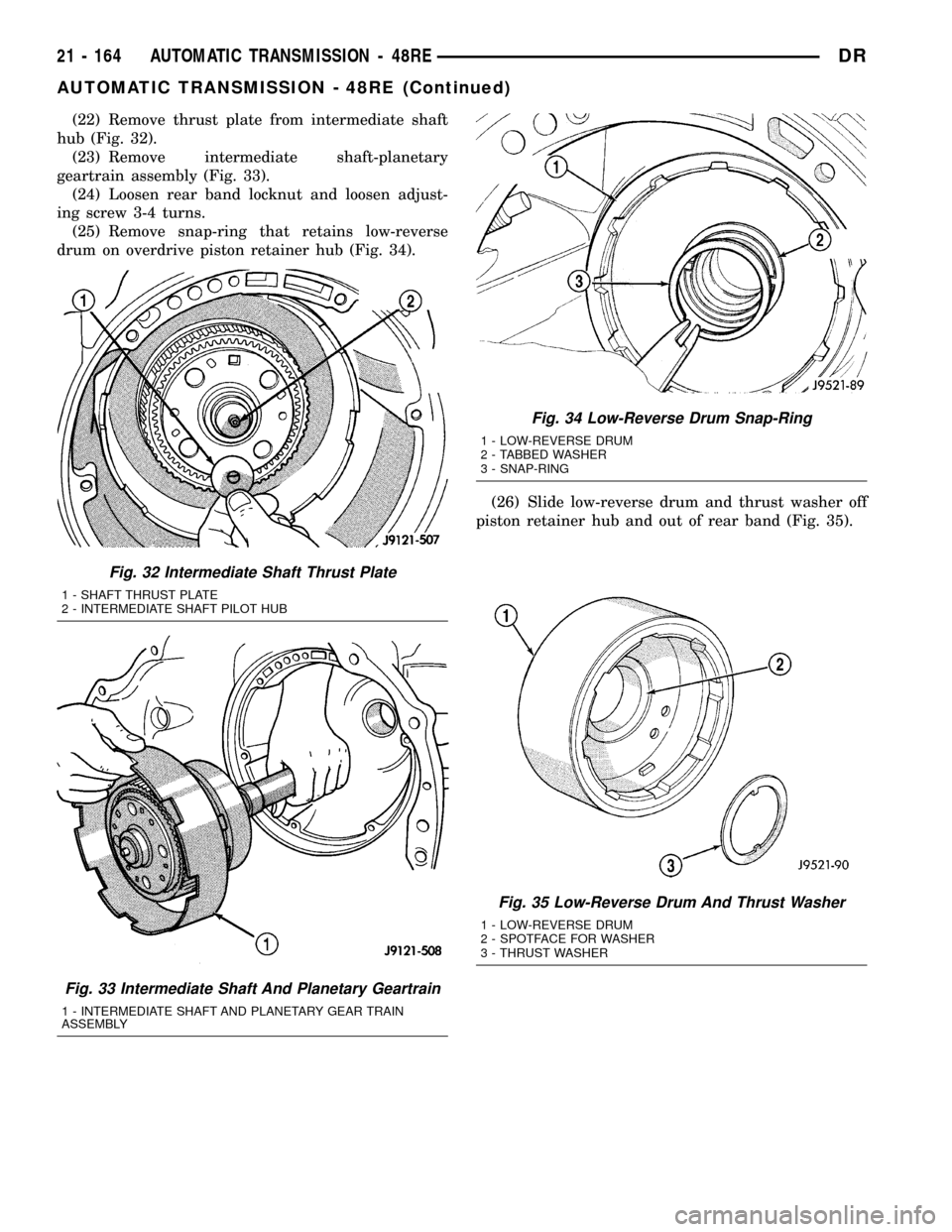
(22) Remove thrust plate from intermediate shaft
hub (Fig. 32).
(23) Remove intermediate shaft-planetary
geartrain assembly (Fig. 33).
(24) Loosen rear band locknut and loosen adjust-
ing screw 3-4 turns.
(25) Remove snap-ring that retains low-reverse
drum on overdrive piston retainer hub (Fig. 34).
(26) Slide low-reverse drum and thrust washer off
piston retainer hub and out of rear band (Fig. 35).
Fig. 35 Low-Reverse Drum And Thrust Washer
1 - LOW-REVERSE DRUM
2 - SPOTFACE FOR WASHER
3 - THRUST WASHER
Fig. 32 Intermediate Shaft Thrust Plate
1 - SHAFT THRUST PLATE
2 - INTERMEDIATE SHAFT PILOT HUB
Fig. 33 Intermediate Shaft And Planetary Geartrain
1 - INTERMEDIATE SHAFT AND PLANETARY GEAR TRAIN
ASSEMBLY
Fig. 34 Low-Reverse Drum Snap-Ring
1 - LOW-REVERSE DRUM
2 - TABBED WASHER
3 - SNAP-RING
21 - 164 AUTOMATIC TRANSMISSION - 48REDR
AUTOMATIC TRANSMISSION - 48RE (Continued)
Page 1868 of 2627
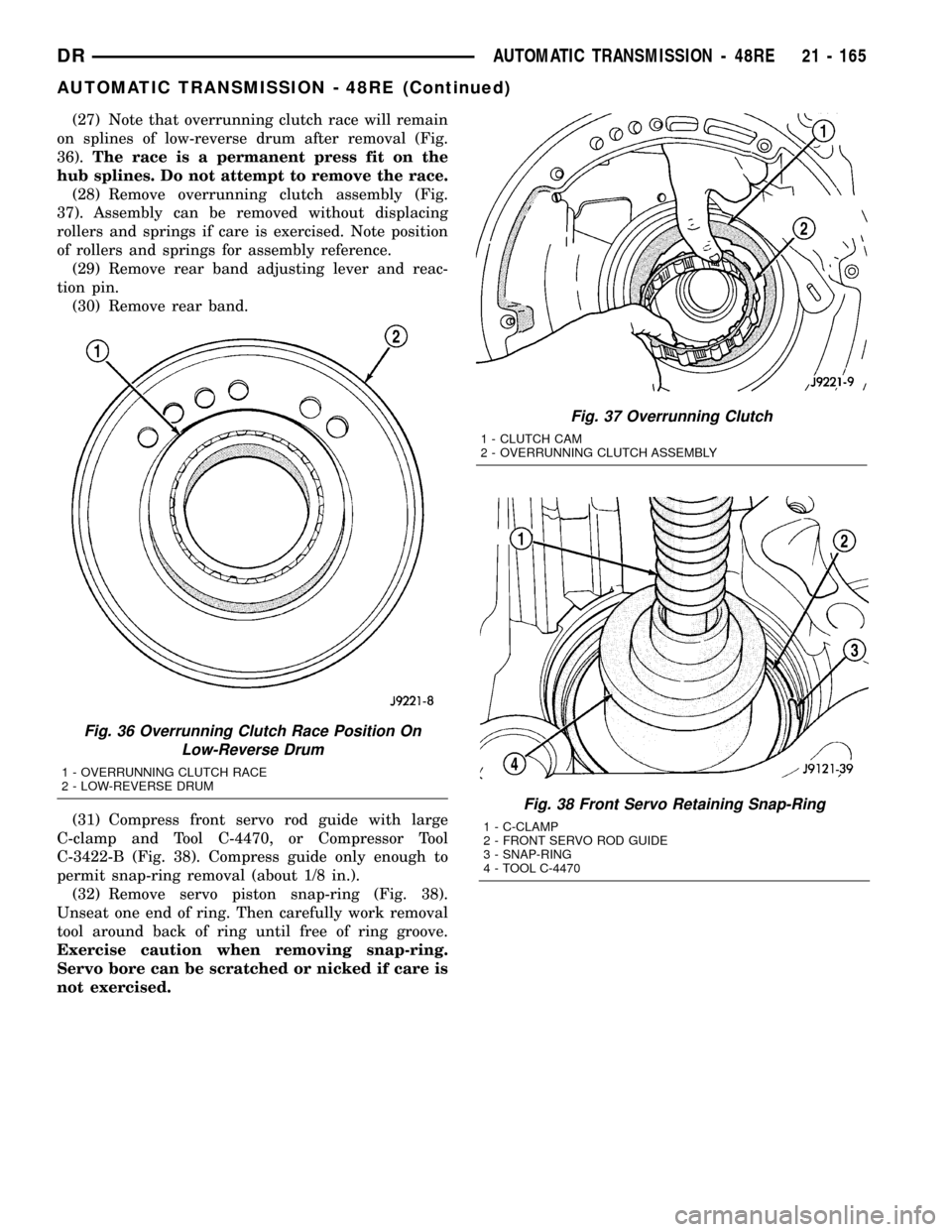
(27) Note that overrunning clutch race will remain
on splines of low-reverse drum after removal (Fig.
36).The race is a permanent press fit on the
hub splines. Do not attempt to remove the race.
(28) Remove overrunning clutch assembly (Fig.
37). Assembly can be removed without displacing
rollers and springs if care is exercised. Note position
of rollers and springs for assembly reference.
(29) Remove rear band adjusting lever and reac-
tion pin.
(30) Remove rear band.
(31) Compress front servo rod guide with large
C-clamp and Tool C-4470, or Compressor Tool
C-3422-B (Fig. 38). Compress guide only enough to
permit snap-ring removal (about 1/8 in.).
(32) Remove servo piston snap-ring (Fig. 38).
Unseat one end of ring. Then carefully work removal
tool around back of ring until free of ring groove.
Exercise caution when removing snap-ring.
Servo bore can be scratched or nicked if care is
not exercised.
Fig. 38 Front Servo Retaining Snap-Ring
1 - C-CLAMP
2 - FRONT SERVO ROD GUIDE
3 - SNAP-RING
4 - TOOL C-4470
Fig. 36 Overrunning Clutch Race Position On
Low-Reverse Drum
1 - OVERRUNNING CLUTCH RACE
2 - LOW-REVERSE DRUM
Fig. 37 Overrunning Clutch
1 - CLUTCH CAM
2 - OVERRUNNING CLUTCH ASSEMBLY
DRAUTOMATIC TRANSMISSION - 48RE 21 - 165
AUTOMATIC TRANSMISSION - 48RE (Continued)
Page 1869 of 2627
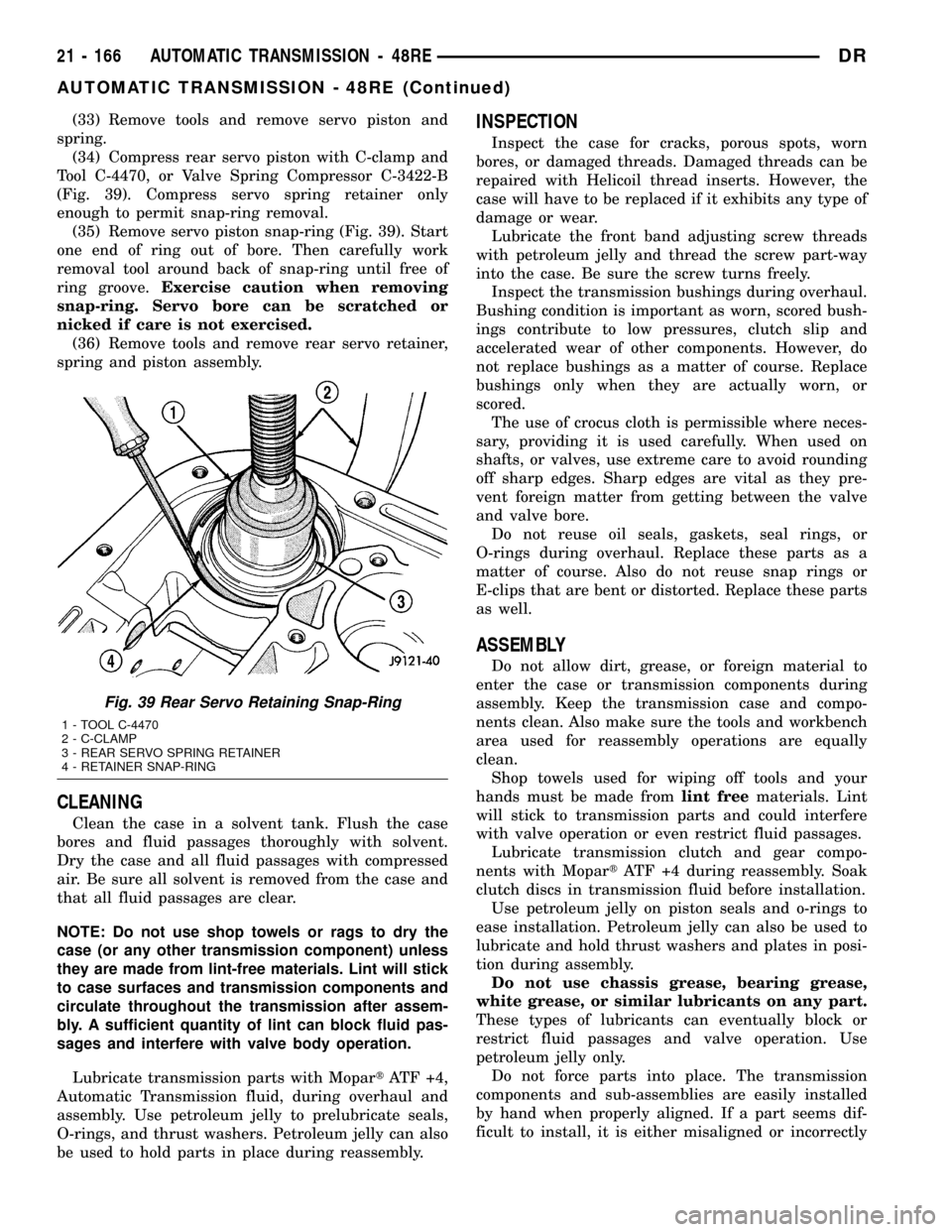
(33) Remove tools and remove servo piston and
spring.
(34) Compress rear servo piston with C-clamp and
Tool C-4470, or Valve Spring Compressor C-3422-B
(Fig. 39). Compress servo spring retainer only
enough to permit snap-ring removal.
(35) Remove servo piston snap-ring (Fig. 39). Start
one end of ring out of bore. Then carefully work
removal tool around back of snap-ring until free of
ring groove.Exercise caution when removing
snap-ring. Servo bore can be scratched or
nicked if care is not exercised.
(36) Remove tools and remove rear servo retainer,
spring and piston assembly.
CLEANING
Clean the case in a solvent tank. Flush the case
bores and fluid passages thoroughly with solvent.
Dry the case and all fluid passages with compressed
air. Be sure all solvent is removed from the case and
that all fluid passages are clear.
NOTE: Do not use shop towels or rags to dry the
case (or any other transmission component) unless
they are made from lint-free materials. Lint will stick
to case surfaces and transmission components and
circulate throughout the transmission after assem-
bly. A sufficient quantity of lint can block fluid pas-
sages and interfere with valve body operation.
Lubricate transmission parts with MopartATF +4,
Automatic Transmission fluid, during overhaul and
assembly. Use petroleum jelly to prelubricate seals,
O-rings, and thrust washers. Petroleum jelly can also
be used to hold parts in place during reassembly.
INSPECTION
Inspect the case for cracks, porous spots, worn
bores, or damaged threads. Damaged threads can be
repaired with Helicoil thread inserts. However, the
case will have to be replaced if it exhibits any type of
damage or wear.
Lubricate the front band adjusting screw threads
with petroleum jelly and thread the screw part-way
into the case. Be sure the screw turns freely.
Inspect the transmission bushings during overhaul.
Bushing condition is important as worn, scored bush-
ings contribute to low pressures, clutch slip and
accelerated wear of other components. However, do
not replace bushings as a matter of course. Replace
bushings only when they are actually worn, or
scored.
The use of crocus cloth is permissible where neces-
sary, providing it is used carefully. When used on
shafts, or valves, use extreme care to avoid rounding
off sharp edges. Sharp edges are vital as they pre-
vent foreign matter from getting between the valve
and valve bore.
Do not reuse oil seals, gaskets, seal rings, or
O-rings during overhaul. Replace these parts as a
matter of course. Also do not reuse snap rings or
E-clips that are bent or distorted. Replace these parts
as well.
ASSEMBLY
Do not allow dirt, grease, or foreign material to
enter the case or transmission components during
assembly. Keep the transmission case and compo-
nents clean. Also make sure the tools and workbench
area used for reassembly operations are equally
clean.
Shop towels used for wiping off tools and your
hands must be made fromlint freematerials. Lint
will stick to transmission parts and could interfere
with valve operation or even restrict fluid passages.
Lubricate transmission clutch and gear compo-
nents with MopartATF +4 during reassembly. Soak
clutch discs in transmission fluid before installation.
Use petroleum jelly on piston seals and o-rings to
ease installation. Petroleum jelly can also be used to
lubricate and hold thrust washers and plates in posi-
tion during assembly.
Do not use chassis grease, bearing grease,
white grease, or similar lubricants on any part.
These types of lubricants can eventually block or
restrict fluid passages and valve operation. Use
petroleum jelly only.
Do not force parts into place. The transmission
components and sub-assemblies are easily installed
by hand when properly aligned. If a part seems dif-
ficult to install, it is either misaligned or incorrectly
Fig. 39 Rear Servo Retaining Snap-Ring
1 - TOOL C-4470
2 - C-CLAMP
3 - REAR SERVO SPRING RETAINER
4 - RETAINER SNAP-RING
21 - 166 AUTOMATIC TRANSMISSION - 48REDR
AUTOMATIC TRANSMISSION - 48RE (Continued)
Page 1870 of 2627

assembled. Verify that thrust washers, thrust plates
and seal rings are correctly positioned.
The planetary geartrain, front/rear clutch assem-
blies and oil pump are all much easier to install
when the transmission case is upright. Either tilt the
case upward with wood blocks, or cut a hole in the
bench large enough for the intermediate shaft and
rear support. Then lower the shaft and support into
the hole and support the rear of the case directly on
the bench.
FRONT/REAR SERVO
(1) Lubricate rear servo piston seal with ATF +4.
Lubricate servo bore in case with ATF +4.
(2) Install rear servo piston in case. Position piston
at slight angle to bore and insert piston with twisting
motion (Fig. 40).
(3) Install rear servo spring and retainer in case
bore (Fig. 41). Be sure spring is seated on piston.
(4) Compress rear servo piston with C-clamp or
Valve Spring Compressor C-3422-B and install servo
piston snap-ring (Fig. 42).
(5) Lubricate front servo piston components and
servo bore in case with transmission fluid.
(6) Install front servo piston in bore. Carefully
ªrunº small, suitable tool around piston ring to press
it back into groove and ease installation (Fig. 43).
Rotate piston into bore at same time. Rock piston
slightly to ease piston ring past snap-ring groove and
into bore.
Fig. 40 Rear Servo Piston
1 - REAR SERVO PISTON
Fig. 41 Rear Servo Piston Spring And Retainer
1 - PISTON SPRING
2 - REAR SERVO PISTON
3 - SPRING RETAINER
Fig. 42 Rear Servo Snap Ring
1 - TOOL C-4470
2 - C-CLAMP
3 - REAR SERVO SPRING RETAINER
4 - RETAINER SNAP-RING
DRAUTOMATIC TRANSMISSION - 48RE 21 - 167
AUTOMATIC TRANSMISSION - 48RE (Continued)