DODGE RAM 1500 1998 2.G Workshop Manual
Manufacturer: DODGE, Model Year: 1998, Model line: RAM 1500, Model: DODGE RAM 1500 1998 2.GPages: 2627
Page 1831 of 2627
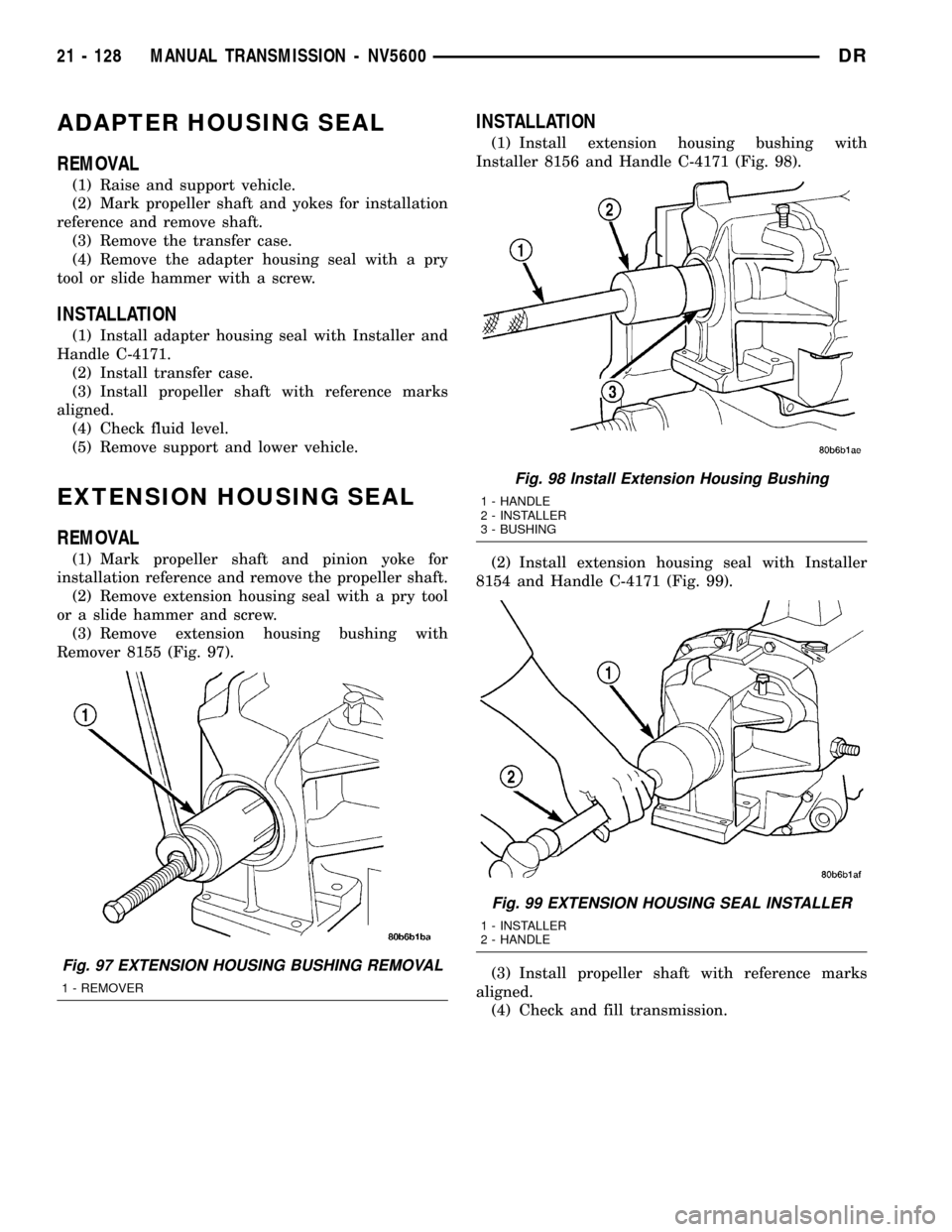
ADAPTER HOUSING SEAL
REMOVAL
(1) Raise and support vehicle.
(2) Mark propeller shaft and yokes for installation
reference and remove shaft.
(3) Remove the transfer case.
(4) Remove the adapter housing seal with a pry
tool or slide hammer with a screw.
INSTALLATION
(1) Install adapter housing seal with Installer and
Handle C-4171.
(2) Install transfer case.
(3) Install propeller shaft with reference marks
aligned.
(4) Check fluid level.
(5) Remove support and lower vehicle.
EXTENSION HOUSING SEAL
REMOVAL
(1) Mark propeller shaft and pinion yoke for
installation reference and remove the propeller shaft.
(2) Remove extension housing seal with a pry tool
or a slide hammer and screw.
(3) Remove extension housing bushing with
Remover 8155 (Fig. 97).
INSTALLATION
(1) Install extension housing bushing with
Installer 8156 and Handle C-4171 (Fig. 98).
(2) Install extension housing seal with Installer
8154 and Handle C-4171 (Fig. 99).
(3) Install propeller shaft with reference marks
aligned.
(4) Check and fill transmission.
Fig. 97 EXTENSION HOUSING BUSHING REMOVAL
1 - REMOVER
Fig. 98 Install Extension Housing Bushing
1 - HANDLE
2 - INSTALLER
3 - BUSHING
Fig. 99 EXTENSION HOUSING SEAL INSTALLER
1 - INSTALLER
2 - HANDLE
21 - 128 MANUAL TRANSMISSION - NV5600DR
Page 1832 of 2627
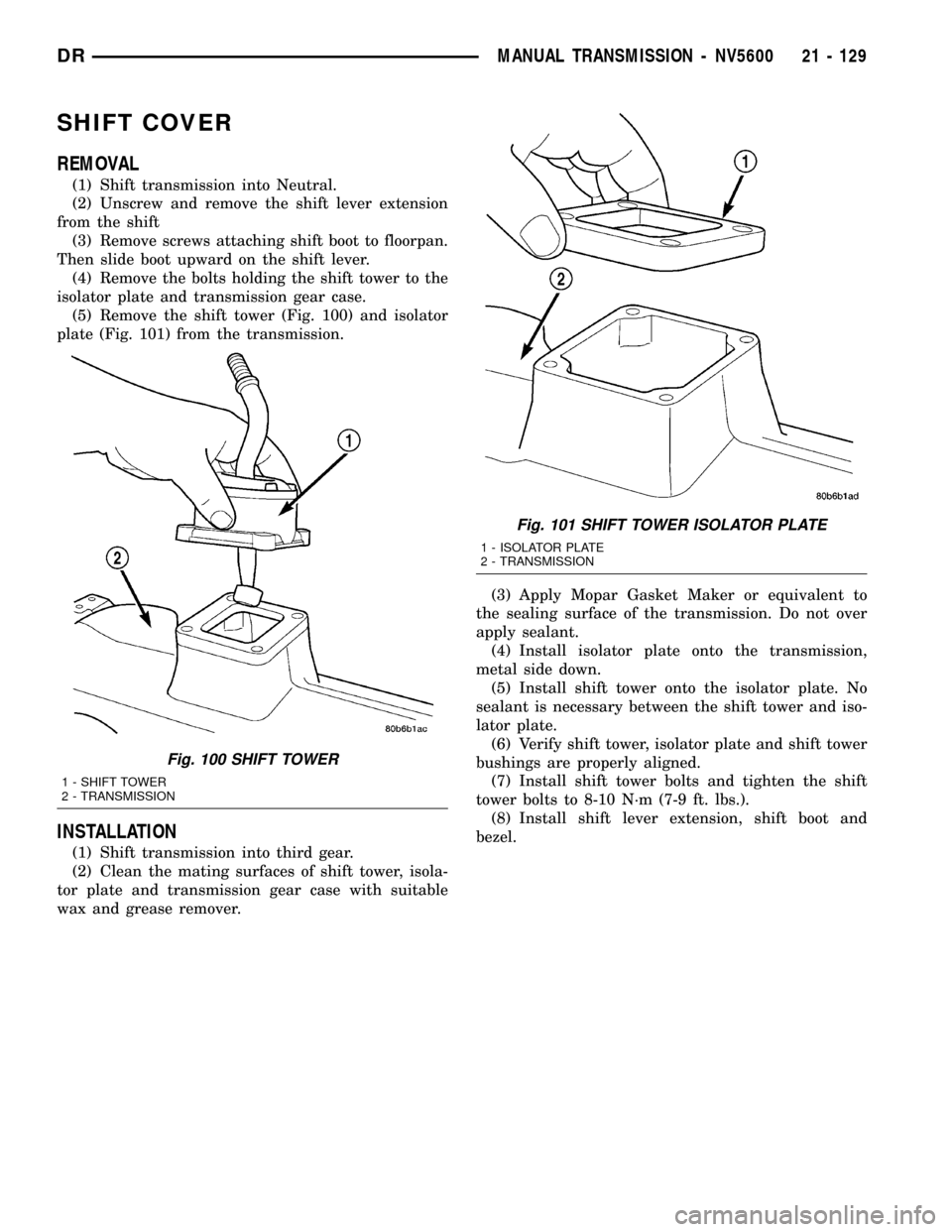
SHIFT COVER
REMOVAL
(1) Shift transmission into Neutral.
(2) Unscrew and remove the shift lever extension
from the shift
(3) Remove screws attaching shift boot to floorpan.
Then slide boot upward on the shift lever.
(4) Remove the bolts holding the shift tower to the
isolator plate and transmission gear case.
(5) Remove the shift tower (Fig. 100) and isolator
plate (Fig. 101) from the transmission.
INSTALLATION
(1) Shift transmission into third gear.
(2) Clean the mating surfaces of shift tower, isola-
tor plate and transmission gear case with suitable
wax and grease remover.(3) Apply Mopar Gasket Maker or equivalent to
the sealing surface of the transmission. Do not over
apply sealant.
(4) Install isolator plate onto the transmission,
metal side down.
(5) Install shift tower onto the isolator plate. No
sealant is necessary between the shift tower and iso-
lator plate.
(6) Verify shift tower, isolator plate and shift tower
bushings are properly aligned.
(7) Install shift tower bolts and tighten the shift
tower bolts to 8-10 N´m (7-9 ft. lbs.).
(8) Install shift lever extension, shift boot and
bezel.
Fig. 100 SHIFT TOWER
1 - SHIFT TOWER
2 - TRANSMISSION
Fig. 101 SHIFT TOWER ISOLATOR PLATE
1 - ISOLATOR PLATE
2 - TRANSMISSION
DRMANUAL TRANSMISSION - NV5600 21 - 129
Page 1833 of 2627
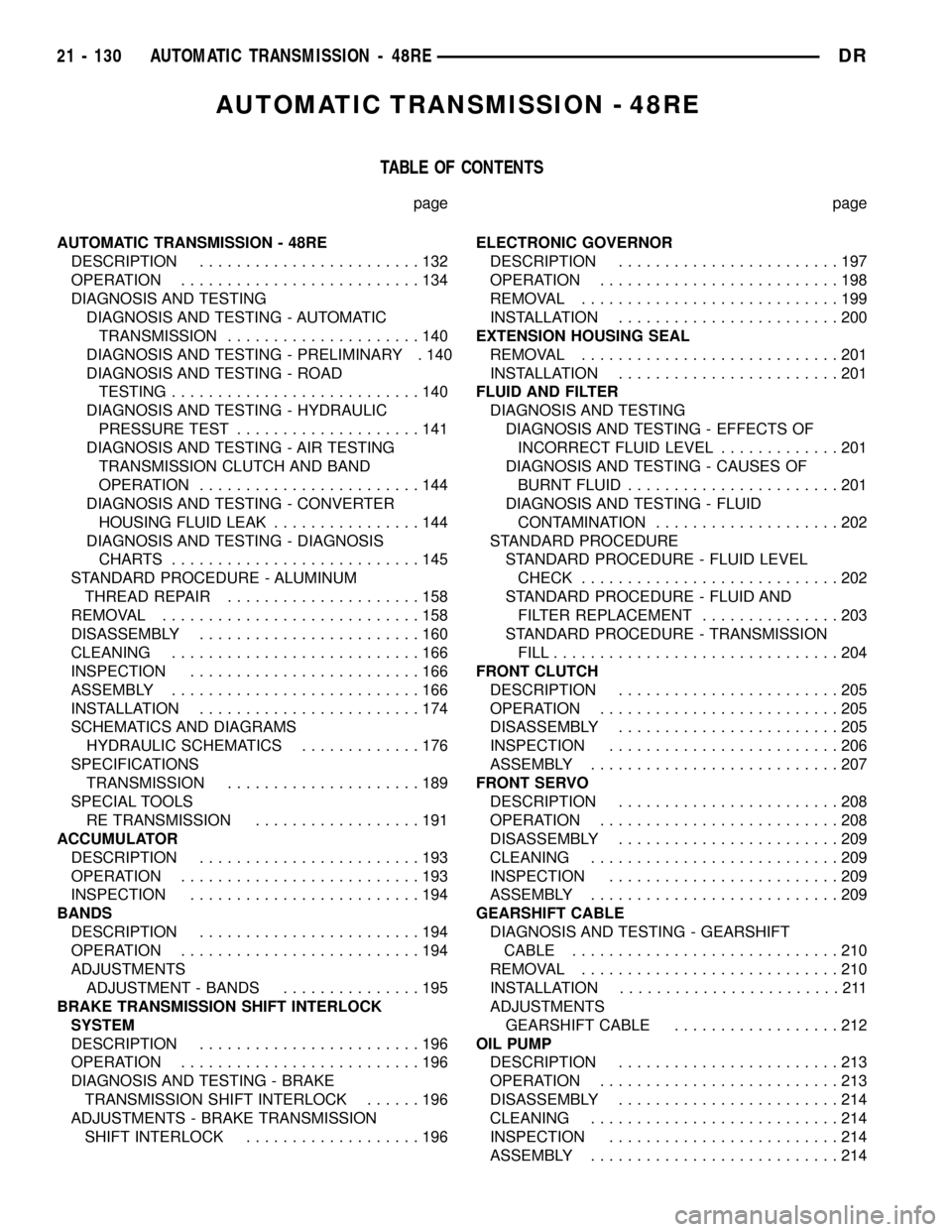
AUTOMATIC TRANSMISSION - 48RE
TABLE OF CONTENTS
page page
AUTOMATIC TRANSMISSION - 48RE
DESCRIPTION........................132
OPERATION..........................134
DIAGNOSIS AND TESTING
DIAGNOSIS AND TESTING - AUTOMATIC
TRANSMISSION.....................140
DIAGNOSIS AND TESTING - PRELIMINARY . 140
DIAGNOSIS AND TESTING - ROAD
TESTING...........................140
DIAGNOSIS AND TESTING - HYDRAULIC
PRESSURE TEST....................141
DIAGNOSIS AND TESTING - AIR TESTING
TRANSMISSION CLUTCH AND BAND
OPERATION........................144
DIAGNOSIS AND TESTING - CONVERTER
HOUSING FLUID LEAK................144
DIAGNOSIS AND TESTING - DIAGNOSIS
CHARTS...........................145
STANDARD PROCEDURE - ALUMINUM
THREAD REPAIR.....................158
REMOVAL............................158
DISASSEMBLY........................160
CLEANING...........................166
INSPECTION.........................166
ASSEMBLY...........................166
INSTALLATION........................174
SCHEMATICS AND DIAGRAMS
HYDRAULIC SCHEMATICS.............176
SPECIFICATIONS
TRANSMISSION.....................189
SPECIAL TOOLS
RE TRANSMISSION..................191
ACCUMULATOR
DESCRIPTION........................193
OPERATION..........................193
INSPECTION.........................194
BANDS
DESCRIPTION........................194
OPERATION..........................194
ADJUSTMENTS
ADJUSTMENT - BANDS...............195
BRAKE TRANSMISSION SHIFT INTERLOCK
SYSTEM
DESCRIPTION........................196
OPERATION..........................196
DIAGNOSIS AND TESTING - BRAKE
TRANSMISSION SHIFT INTERLOCK......196
ADJUSTMENTS - BRAKE TRANSMISSION
SHIFT INTERLOCK...................196ELECTRONIC GOVERNOR
DESCRIPTION........................197
OPERATION..........................198
REMOVAL............................199
INSTALLATION........................200
EXTENSION HOUSING SEAL
REMOVAL............................201
INSTALLATION........................201
FLUID AND FILTER
DIAGNOSIS AND TESTING
DIAGNOSIS AND TESTING - EFFECTS OF
INCORRECT FLUID LEVEL.............201
DIAGNOSIS AND TESTING - CAUSES OF
BURNT FLUID.......................201
DIAGNOSIS AND TESTING - FLUID
CONTAMINATION....................202
STANDARD PROCEDURE
STANDARD PROCEDURE - FLUID LEVEL
CHECK............................202
STANDARD PROCEDURE - FLUID AND
FILTER REPLACEMENT...............203
STANDARD PROCEDURE - TRANSMISSION
FILL...............................204
FRONT CLUTCH
DESCRIPTION........................205
OPERATION..........................205
DISASSEMBLY........................205
INSPECTION.........................206
ASSEMBLY...........................207
FRONT SERVO
DESCRIPTION........................208
OPERATION..........................208
DISASSEMBLY........................209
CLEANING...........................209
INSPECTION.........................209
ASSEMBLY...........................209
GEARSHIFT CABLE
DIAGNOSIS AND TESTING - GEARSHIFT
CABLE.............................210
REMOVAL............................210
INSTALLATION........................211
ADJUSTMENTS
GEARSHIFT CABLE..................212
OIL PUMP
DESCRIPTION........................213
OPERATION..........................213
DISASSEMBLY........................214
CLEANING...........................214
INSPECTION.........................214
ASSEMBLY...........................214
21 - 130 AUTOMATIC TRANSMISSION - 48REDR
Page 1834 of 2627
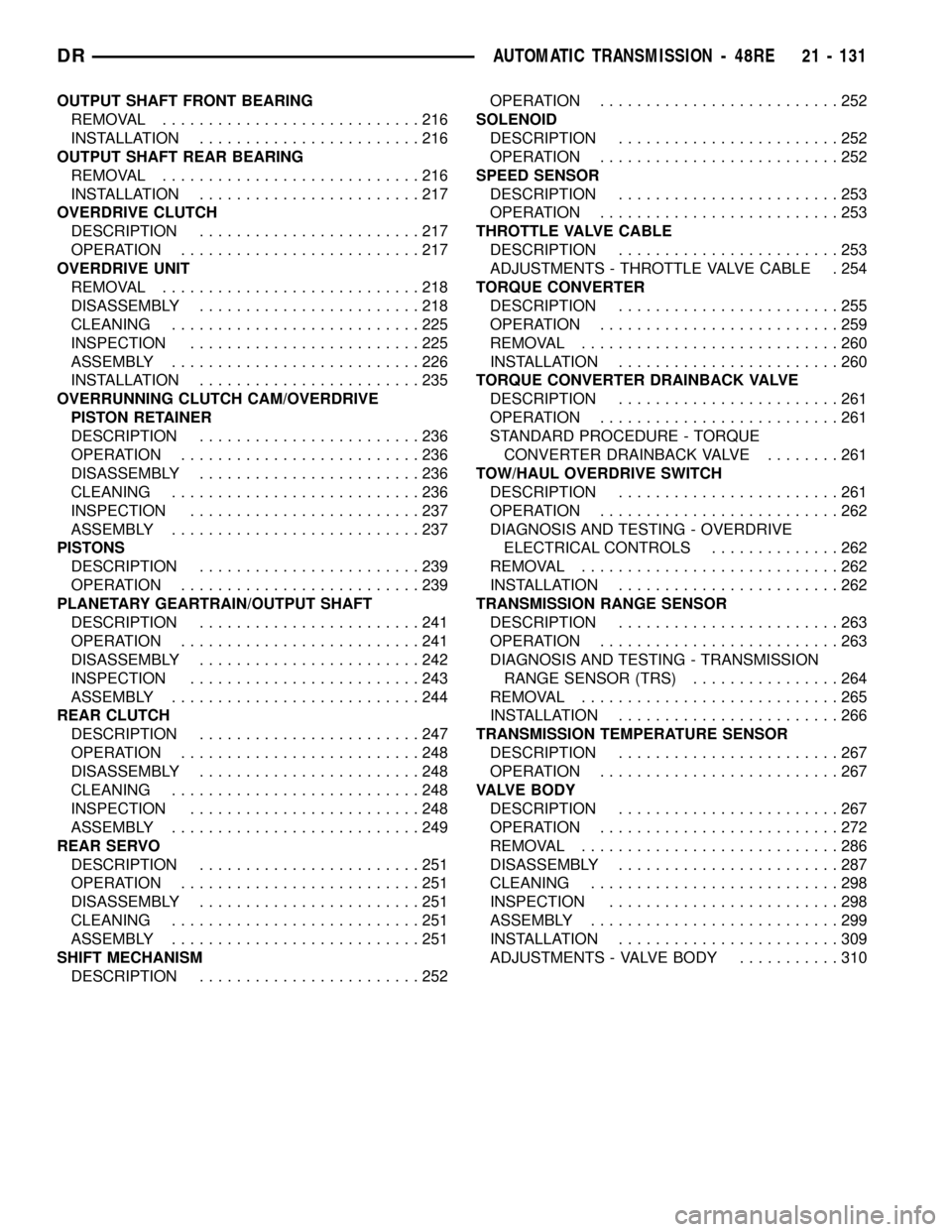
OUTPUT SHAFT FRONT BEARING
REMOVAL............................216
INSTALLATION........................216
OUTPUT SHAFT REAR BEARING
REMOVAL............................216
INSTALLATION........................217
OVERDRIVE CLUTCH
DESCRIPTION........................217
OPERATION..........................217
OVERDRIVE UNIT
REMOVAL............................218
DISASSEMBLY........................218
CLEANING...........................225
INSPECTION.........................225
ASSEMBLY...........................226
INSTALLATION........................235
OVERRUNNING CLUTCH CAM/OVERDRIVE
PISTON RETAINER
DESCRIPTION........................236
OPERATION..........................236
DISASSEMBLY........................236
CLEANING...........................236
INSPECTION.........................237
ASSEMBLY...........................237
PISTONS
DESCRIPTION........................239
OPERATION..........................239
PLANETARY GEARTRAIN/OUTPUT SHAFT
DESCRIPTION........................241
OPERATION..........................241
DISASSEMBLY........................242
INSPECTION.........................243
ASSEMBLY...........................244
REAR CLUTCH
DESCRIPTION........................247
OPERATION..........................248
DISASSEMBLY........................248
CLEANING...........................248
INSPECTION.........................248
ASSEMBLY...........................249
REAR SERVO
DESCRIPTION........................251
OPERATION..........................251
DISASSEMBLY........................251
CLEANING...........................251
ASSEMBLY...........................251
SHIFT MECHANISM
DESCRIPTION........................252OPERATION..........................252
SOLENOID
DESCRIPTION........................252
OPERATION..........................252
SPEED SENSOR
DESCRIPTION........................253
OPERATION..........................253
THROTTLE VALVE CABLE
DESCRIPTION........................253
ADJUSTMENTS - THROTTLE VALVE CABLE . 254
TORQUE CONVERTER
DESCRIPTION........................255
OPERATION..........................259
REMOVAL............................260
INSTALLATION........................260
TORQUE CONVERTER DRAINBACK VALVE
DESCRIPTION........................261
OPERATION..........................261
STANDARD PROCEDURE - TORQUE
CONVERTER DRAINBACK VALVE........261
TOW/HAUL OVERDRIVE SWITCH
DESCRIPTION........................261
OPERATION..........................262
DIAGNOSIS AND TESTING - OVERDRIVE
ELECTRICAL CONTROLS..............262
REMOVAL............................262
INSTALLATION........................262
TRANSMISSION RANGE SENSOR
DESCRIPTION........................263
OPERATION..........................263
DIAGNOSIS AND TESTING - TRANSMISSION
RANGE SENSOR (TRS)................264
REMOVAL............................265
INSTALLATION........................266
TRANSMISSION TEMPERATURE SENSOR
DESCRIPTION........................267
OPERATION..........................267
VALVE BODY
DESCRIPTION........................267
OPERATION..........................272
REMOVAL............................286
DISASSEMBLY........................287
CLEANING...........................298
INSPECTION.........................298
ASSEMBLY...........................299
INSTALLATION........................309
ADJUSTMENTS - VALVE BODY...........310
DRAUTOMATIC TRANSMISSION - 48RE 21 - 131
Page 1835 of 2627
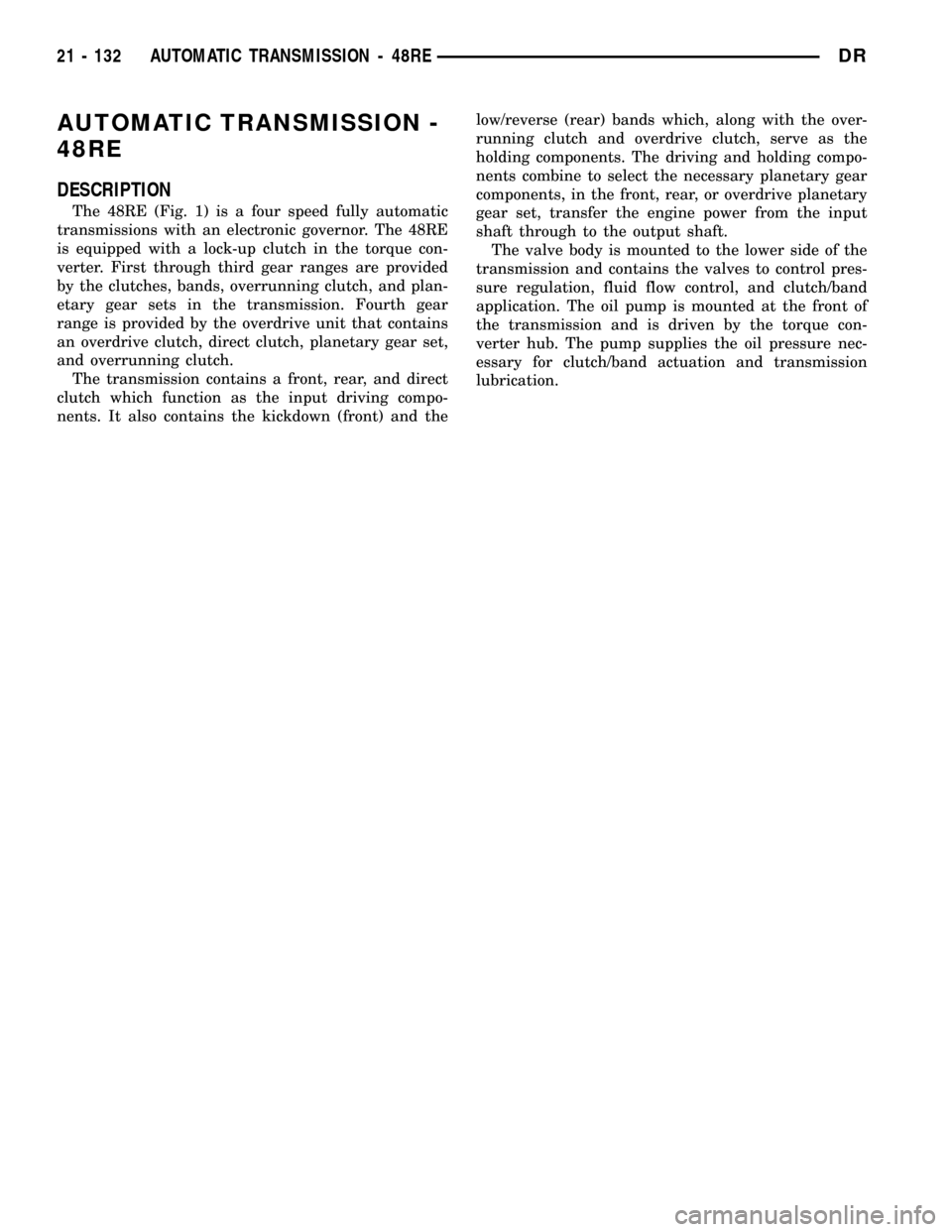
AUTOMATIC TRANSMISSION -
48RE
DESCRIPTION
The 48RE (Fig. 1) is a four speed fully automatic
transmissions with an electronic governor. The 48RE
is equipped with a lock-up clutch in the torque con-
verter. First through third gear ranges are provided
by the clutches, bands, overrunning clutch, and plan-
etary gear sets in the transmission. Fourth gear
range is provided by the overdrive unit that contains
an overdrive clutch, direct clutch, planetary gear set,
and overrunning clutch.
The transmission contains a front, rear, and direct
clutch which function as the input driving compo-
nents. It also contains the kickdown (front) and thelow/reverse (rear) bands which, along with the over-
running clutch and overdrive clutch, serve as the
holding components. The driving and holding compo-
nents combine to select the necessary planetary gear
components, in the front, rear, or overdrive planetary
gear set, transfer the engine power from the input
shaft through to the output shaft.
The valve body is mounted to the lower side of the
transmission and contains the valves to control pres-
sure regulation, fluid flow control, and clutch/band
application. The oil pump is mounted at the front of
the transmission and is driven by the torque con-
verter hub. The pump supplies the oil pressure nec-
essary for clutch/band actuation and transmission
lubrication.
21 - 132 AUTOMATIC TRANSMISSION - 48REDR
Page 1836 of 2627
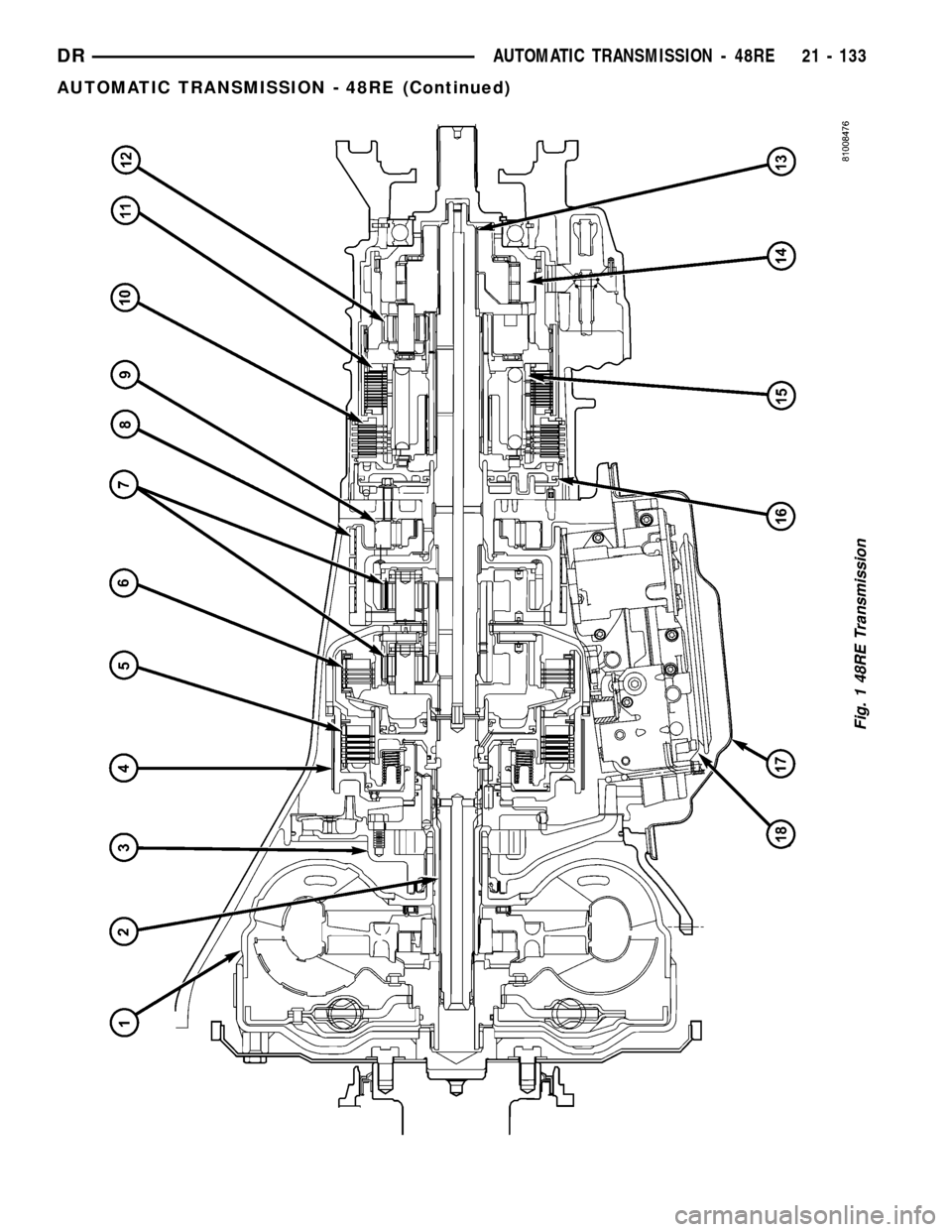
Fig. 1 48RE Transmission
DRAUTOMATIC TRANSMISSION - 48RE 21 - 133
AUTOMATIC TRANSMISSION - 48RE (Continued)
Page 1837 of 2627
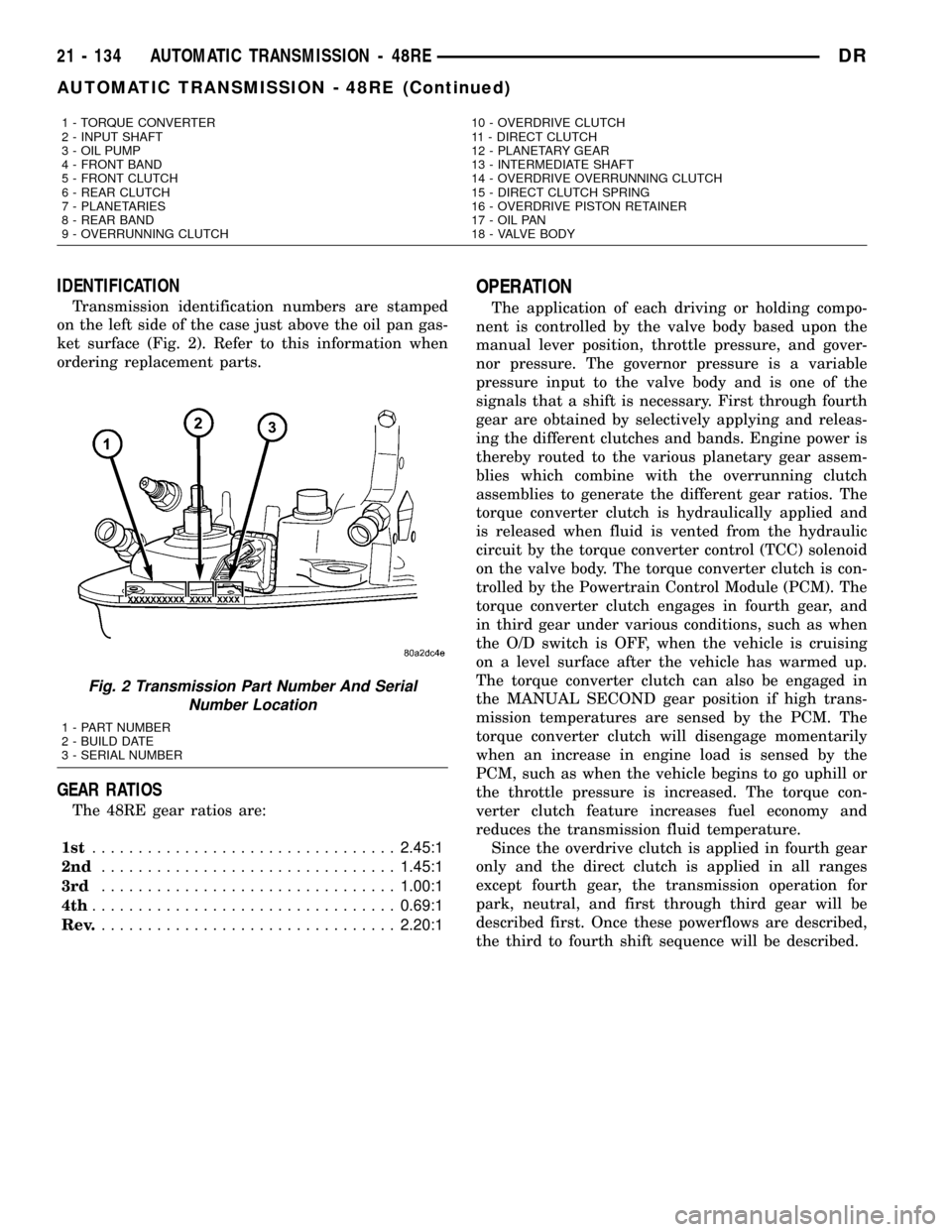
IDENTIFICATION
Transmission identification numbers are stamped
on the left side of the case just above the oil pan gas-
ket surface (Fig. 2). Refer to this information when
ordering replacement parts.
GEAR RATIOS
The 48RE gear ratios are:
1st.................................2.45:1
2nd................................1.45:1
3rd................................1.00:1
4th.................................0.69:1
Rev.................................2.20:1
OPERATION
The application of each driving or holding compo-
nent is controlled by the valve body based upon the
manual lever position, throttle pressure, and gover-
nor pressure. The governor pressure is a variable
pressure input to the valve body and is one of the
signals that a shift is necessary. First through fourth
gear are obtained by selectively applying and releas-
ing the different clutches and bands. Engine power is
thereby routed to the various planetary gear assem-
blies which combine with the overrunning clutch
assemblies to generate the different gear ratios. The
torque converter clutch is hydraulically applied and
is released when fluid is vented from the hydraulic
circuit by the torque converter control (TCC) solenoid
on the valve body. The torque converter clutch is con-
trolled by the Powertrain Control Module (PCM). The
torque converter clutch engages in fourth gear, and
in third gear under various conditions, such as when
the O/D switch is OFF, when the vehicle is cruising
on a level surface after the vehicle has warmed up.
The torque converter clutch can also be engaged in
the MANUAL SECOND gear position if high trans-
mission temperatures are sensed by the PCM. The
torque converter clutch will disengage momentarily
when an increase in engine load is sensed by the
PCM, such as when the vehicle begins to go uphill or
the throttle pressure is increased. The torque con-
verter clutch feature increases fuel economy and
reduces the transmission fluid temperature.
Since the overdrive clutch is applied in fourth gear
only and the direct clutch is applied in all ranges
except fourth gear, the transmission operation for
park, neutral, and first through third gear will be
described first. Once these powerflows are described,
the third to fourth shift sequence will be described.
1 - TORQUE CONVERTER 10 - OVERDRIVE CLUTCH
2 - INPUT SHAFT 11 - DIRECT CLUTCH
3 - OIL PUMP 12 - PLANETARY GEAR
4 - FRONT BAND 13 - INTERMEDIATE SHAFT
5 - FRONT CLUTCH 14 - OVERDRIVE OVERRUNNING CLUTCH
6 - REAR CLUTCH 15 - DIRECT CLUTCH SPRING
7 - PLANETARIES 16 - OVERDRIVE PISTON RETAINER
8 - REAR BAND 17 - OIL PAN
9 - OVERRUNNING CLUTCH 18 - VALVE BODY
Fig. 2 Transmission Part Number And Serial
Number Location
1 - PART NUMBER
2 - BUILD DATE
3 - SERIAL NUMBER
21 - 134 AUTOMATIC TRANSMISSION - 48REDR
AUTOMATIC TRANSMISSION - 48RE (Continued)
Page 1838 of 2627
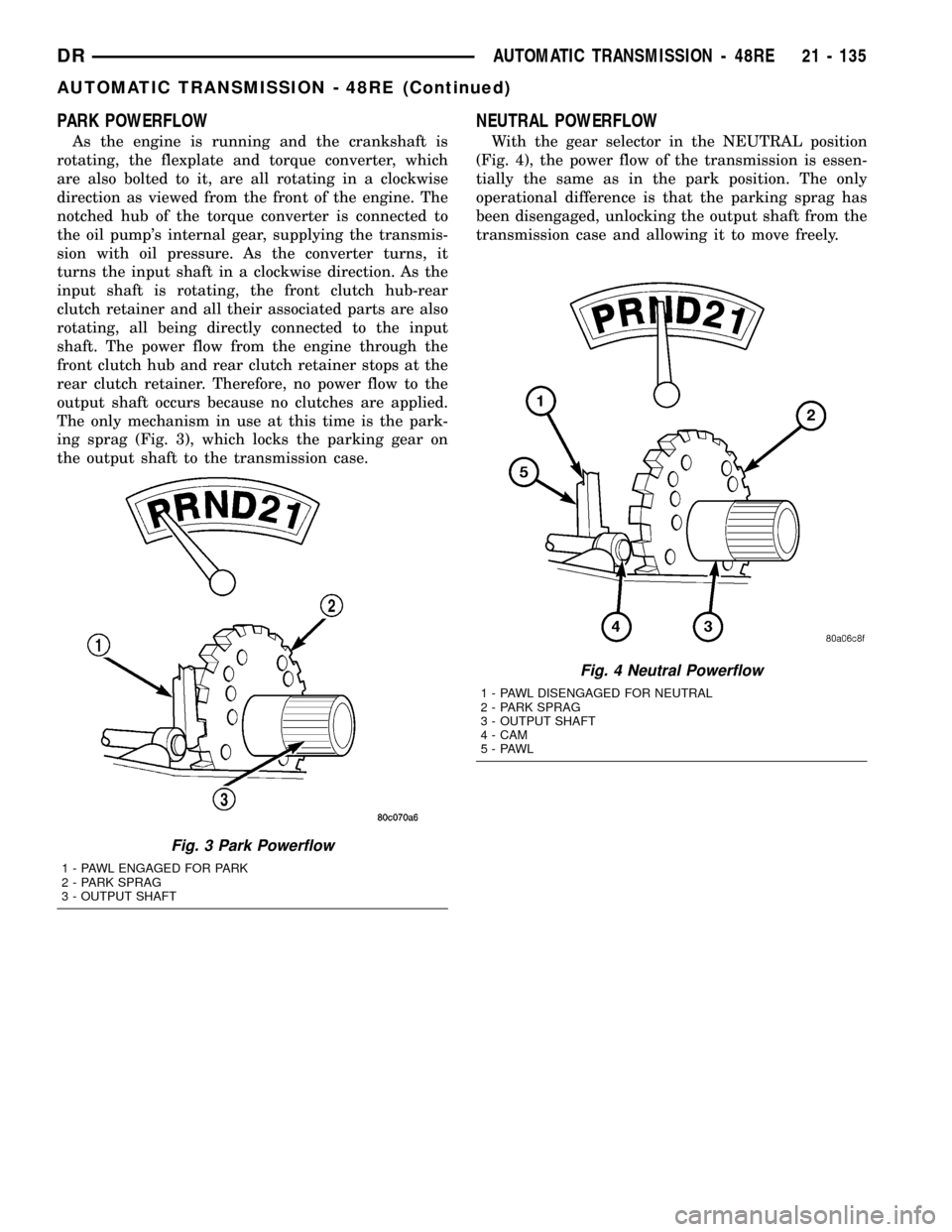
PARK POWERFLOW
As the engine is running and the crankshaft is
rotating, the flexplate and torque converter, which
are also bolted to it, are all rotating in a clockwise
direction as viewed from the front of the engine. The
notched hub of the torque converter is connected to
the oil pump's internal gear, supplying the transmis-
sion with oil pressure. As the converter turns, it
turns the input shaft in a clockwise direction. As the
input shaft is rotating, the front clutch hub-rear
clutch retainer and all their associated parts are also
rotating, all being directly connected to the input
shaft. The power flow from the engine through the
front clutch hub and rear clutch retainer stops at the
rear clutch retainer. Therefore, no power flow to the
output shaft occurs because no clutches are applied.
The only mechanism in use at this time is the park-
ing sprag (Fig. 3), which locks the parking gear on
the output shaft to the transmission case.
NEUTRAL POWERFLOW
With the gear selector in the NEUTRAL position
(Fig. 4), the power flow of the transmission is essen-
tially the same as in the park position. The only
operational difference is that the parking sprag has
been disengaged, unlocking the output shaft from the
transmission case and allowing it to move freely.
Fig. 3 Park Powerflow
1 - PAWL ENGAGED FOR PARK
2 - PARK SPRAG
3 - OUTPUT SHAFT
Fig. 4 Neutral Powerflow
1 - PAWL DISENGAGED FOR NEUTRAL
2 - PARK SPRAG
3 - OUTPUT SHAFT
4 - CAM
5-PAWL
DRAUTOMATIC TRANSMISSION - 48RE 21 - 135
AUTOMATIC TRANSMISSION - 48RE (Continued)
Page 1839 of 2627
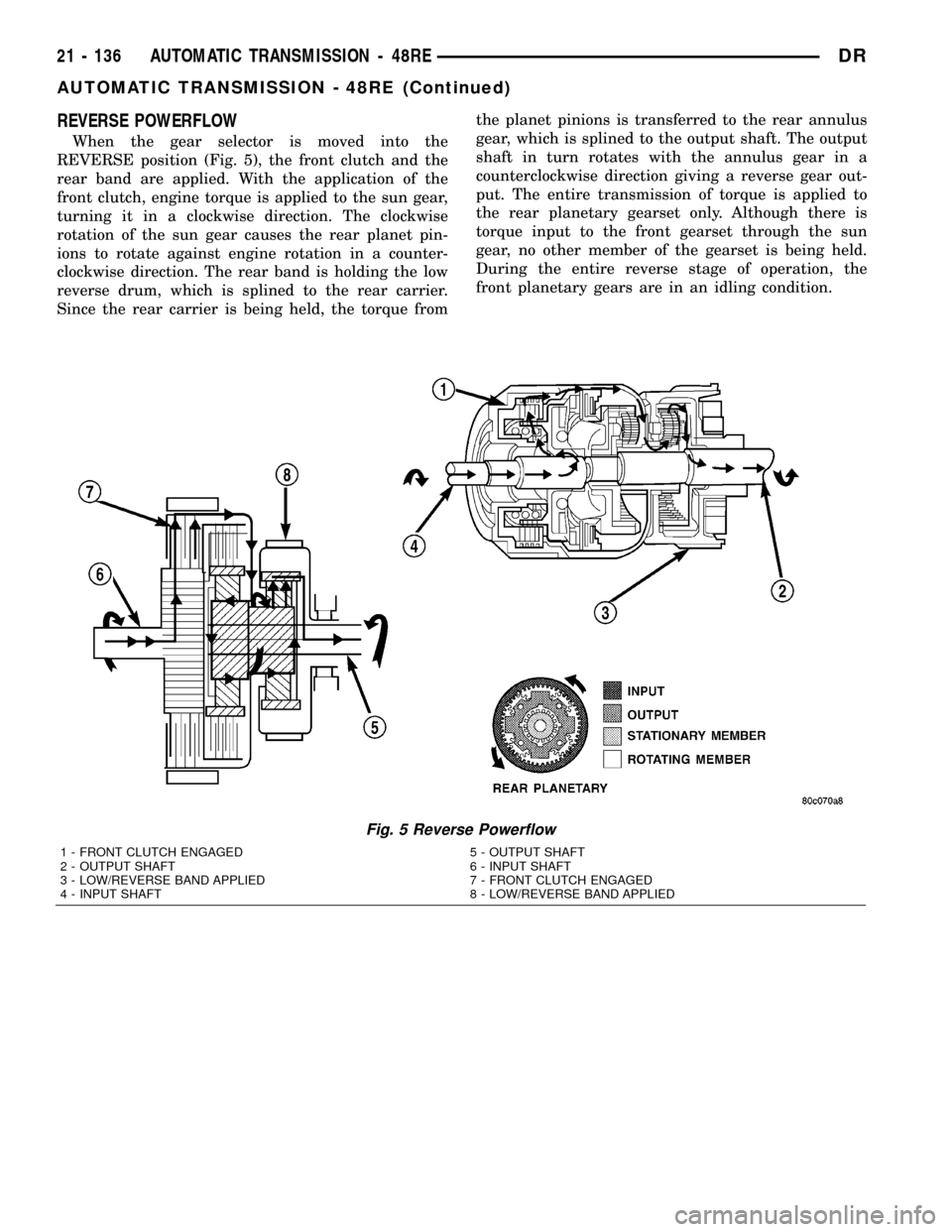
REVERSE POWERFLOW
When the gear selector is moved into the
REVERSE position (Fig. 5), the front clutch and the
rear band are applied. With the application of the
front clutch, engine torque is applied to the sun gear,
turning it in a clockwise direction. The clockwise
rotation of the sun gear causes the rear planet pin-
ions to rotate against engine rotation in a counter-
clockwise direction. The rear band is holding the low
reverse drum, which is splined to the rear carrier.
Since the rear carrier is being held, the torque fromthe planet pinions is transferred to the rear annulus
gear, which is splined to the output shaft. The output
shaft in turn rotates with the annulus gear in a
counterclockwise direction giving a reverse gear out-
put. The entire transmission of torque is applied to
the rear planetary gearset only. Although there is
torque input to the front gearset through the sun
gear, no other member of the gearset is being held.
During the entire reverse stage of operation, the
front planetary gears are in an idling condition.
Fig. 5 Reverse Powerflow
1 - FRONT CLUTCH ENGAGED 5 - OUTPUT SHAFT
2 - OUTPUT SHAFT 6 - INPUT SHAFT
3 - LOW/REVERSE BAND APPLIED 7 - FRONT CLUTCH ENGAGED
4 - INPUT SHAFT 8 - LOW/REVERSE BAND APPLIED
21 - 136 AUTOMATIC TRANSMISSION - 48REDR
AUTOMATIC TRANSMISSION - 48RE (Continued)
Page 1840 of 2627
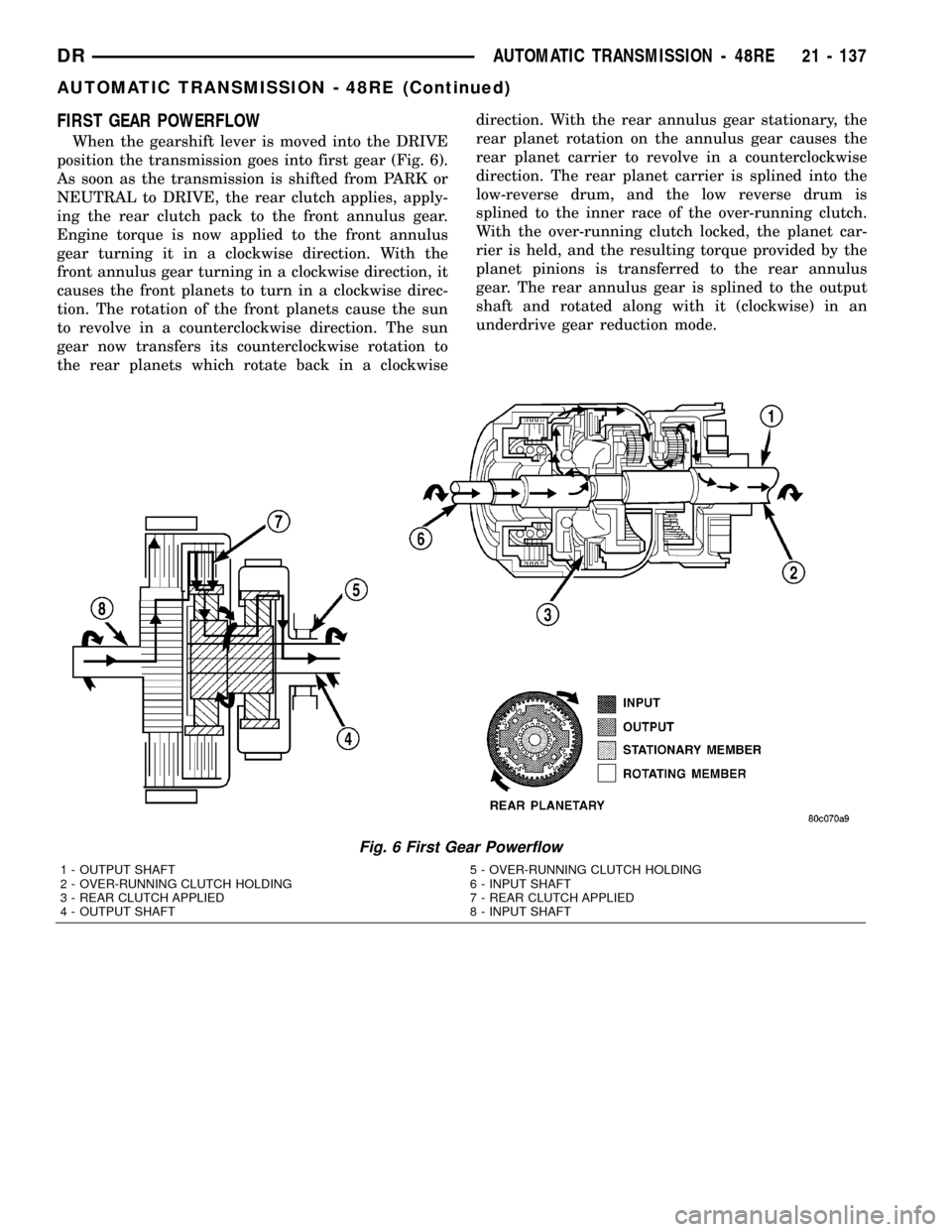
FIRST GEAR POWERFLOW
When the gearshift lever is moved into the DRIVE
position the transmission goes into first gear (Fig. 6).
As soon as the transmission is shifted from PARK or
NEUTRAL to DRIVE, the rear clutch applies, apply-
ing the rear clutch pack to the front annulus gear.
Engine torque is now applied to the front annulus
gear turning it in a clockwise direction. With the
front annulus gear turning in a clockwise direction, it
causes the front planets to turn in a clockwise direc-
tion. The rotation of the front planets cause the sun
to revolve in a counterclockwise direction. The sun
gear now transfers its counterclockwise rotation to
the rear planets which rotate back in a clockwisedirection. With the rear annulus gear stationary, the
rear planet rotation on the annulus gear causes the
rear planet carrier to revolve in a counterclockwise
direction. The rear planet carrier is splined into the
low-reverse drum, and the low reverse drum is
splined to the inner race of the over-running clutch.
With the over-running clutch locked, the planet car-
rier is held, and the resulting torque provided by the
planet pinions is transferred to the rear annulus
gear. The rear annulus gear is splined to the output
shaft and rotated along with it (clockwise) in an
underdrive gear reduction mode.
Fig. 6 First Gear Powerflow
1 - OUTPUT SHAFT 5 - OVER-RUNNING CLUTCH HOLDING
2 - OVER-RUNNING CLUTCH HOLDING 6 - INPUT SHAFT
3 - REAR CLUTCH APPLIED 7 - REAR CLUTCH APPLIED
4 - OUTPUT SHAFT 8 - INPUT SHAFT
DRAUTOMATIC TRANSMISSION - 48RE 21 - 137
AUTOMATIC TRANSMISSION - 48RE (Continued)