Engine diagram DODGE RAM 1500 1998 2.G User Guide
[x] Cancel search | Manufacturer: DODGE, Model Year: 1998, Model line: RAM 1500, Model: DODGE RAM 1500 1998 2.GPages: 2627
Page 595 of 2627
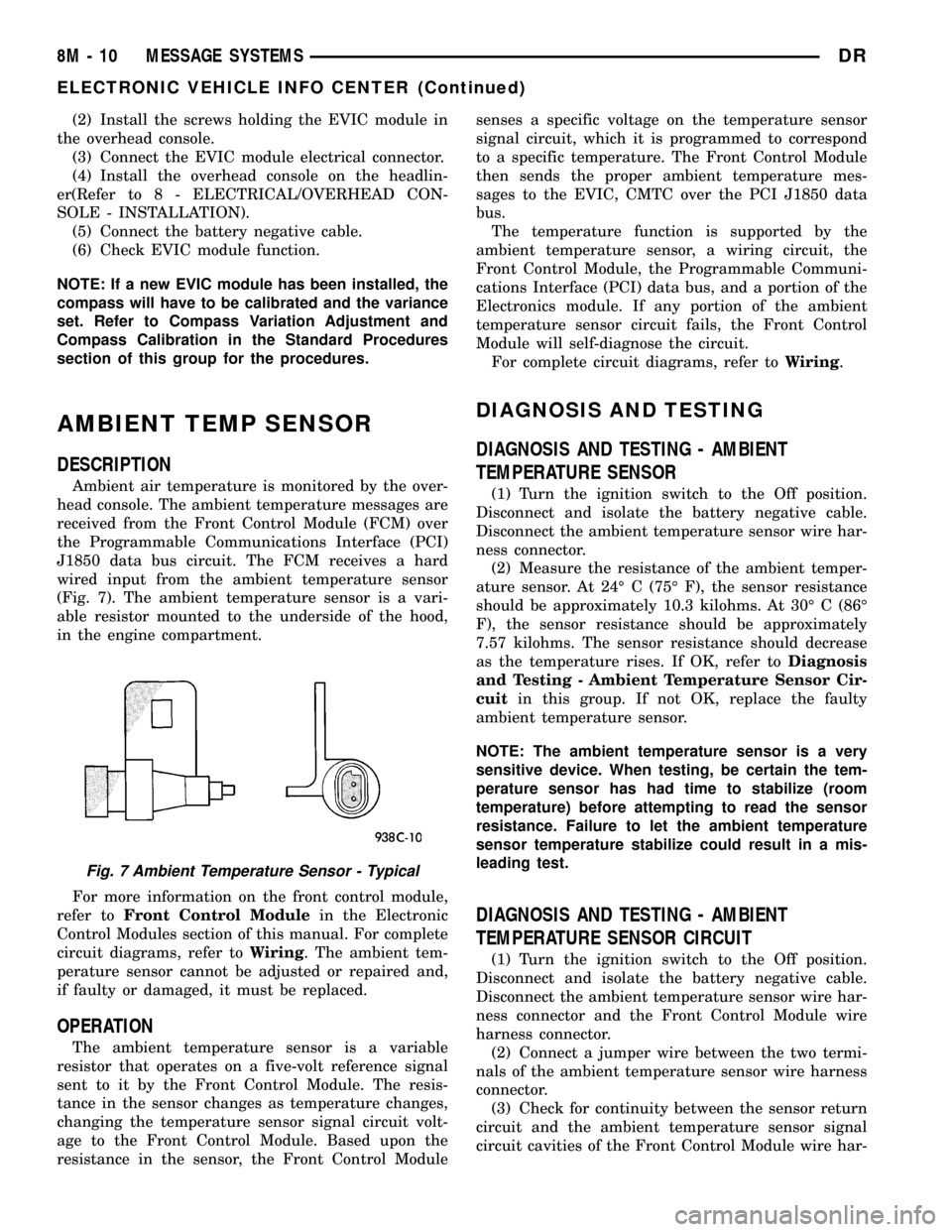
(2) Install the screws holding the EVIC module in
the overhead console.
(3) Connect the EVIC module electrical connector.
(4) Install the overhead console on the headlin-
er(Refer to 8 - ELECTRICAL/OVERHEAD CON-
SOLE - INSTALLATION).
(5) Connect the battery negative cable.
(6) Check EVIC module function.
NOTE: If a new EVIC module has been installed, the
compass will have to be calibrated and the variance
set. Refer to Compass Variation Adjustment and
Compass Calibration in the Standard Procedures
section of this group for the procedures.
AMBIENT TEMP SENSOR
DESCRIPTION
Ambient air temperature is monitored by the over-
head console. The ambient temperature messages are
received from the Front Control Module (FCM) over
the Programmable Communications Interface (PCI)
J1850 data bus circuit. The FCM receives a hard
wired input from the ambient temperature sensor
(Fig. 7). The ambient temperature sensor is a vari-
able resistor mounted to the underside of the hood,
in the engine compartment.
For more information on the front control module,
refer toFront Control Modulein the Electronic
Control Modules section of this manual. For complete
circuit diagrams, refer toWiring. The ambient tem-
perature sensor cannot be adjusted or repaired and,
if faulty or damaged, it must be replaced.
OPERATION
The ambient temperature sensor is a variable
resistor that operates on a five-volt reference signal
sent to it by the Front Control Module. The resis-
tance in the sensor changes as temperature changes,
changing the temperature sensor signal circuit volt-
age to the Front Control Module. Based upon the
resistance in the sensor, the Front Control Modulesenses a specific voltage on the temperature sensor
signal circuit, which it is programmed to correspond
to a specific temperature. The Front Control Module
then sends the proper ambient temperature mes-
sages to the EVIC, CMTC over the PCI J1850 data
bus.
The temperature function is supported by the
ambient temperature sensor, a wiring circuit, the
Front Control Module, the Programmable Communi-
cations Interface (PCI) data bus, and a portion of the
Electronics module. If any portion of the ambient
temperature sensor circuit fails, the Front Control
Module will self-diagnose the circuit.
For complete circuit diagrams, refer toWiring.
DIAGNOSIS AND TESTING
DIAGNOSIS AND TESTING - AMBIENT
TEMPERATURE SENSOR
(1) Turn the ignition switch to the Off position.
Disconnect and isolate the battery negative cable.
Disconnect the ambient temperature sensor wire har-
ness connector.
(2) Measure the resistance of the ambient temper-
ature sensor. At 24É C (75É F), the sensor resistance
should be approximately 10.3 kilohms. At 30É C (86É
F), the sensor resistance should be approximately
7.57 kilohms. The sensor resistance should decrease
as the temperature rises. If OK, refer toDiagnosis
and Testing - Ambient Temperature Sensor Cir-
cuitin this group. If not OK, replace the faulty
ambient temperature sensor.
NOTE: The ambient temperature sensor is a very
sensitive device. When testing, be certain the tem-
perature sensor has had time to stabilize (room
temperature) before attempting to read the sensor
resistance. Failure to let the ambient temperature
sensor temperature stabilize could result in a mis-
leading test.
DIAGNOSIS AND TESTING - AMBIENT
TEMPERATURE SENSOR CIRCUIT
(1) Turn the ignition switch to the Off position.
Disconnect and isolate the battery negative cable.
Disconnect the ambient temperature sensor wire har-
ness connector and the Front Control Module wire
harness connector.
(2) Connect a jumper wire between the two termi-
nals of the ambient temperature sensor wire harness
connector.
(3) Check for continuity between the sensor return
circuit and the ambient temperature sensor signal
circuit cavities of the Front Control Module wire har-
Fig. 7 Ambient Temperature Sensor - Typical
8M - 10 MESSAGE SYSTEMSDR
ELECTRONIC VEHICLE INFO CENTER (Continued)
Page 718 of 2627
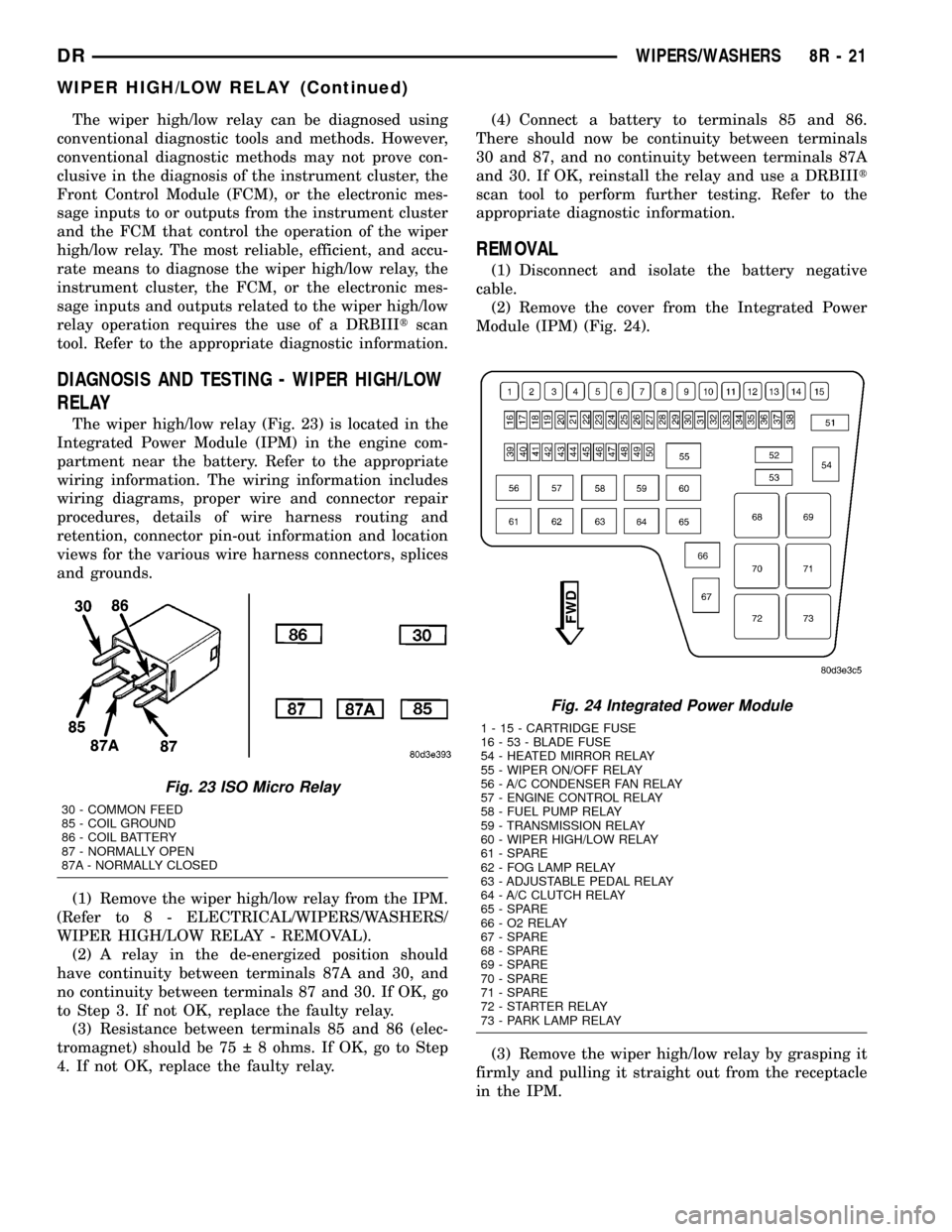
The wiper high/low relay can be diagnosed using
conventional diagnostic tools and methods. However,
conventional diagnostic methods may not prove con-
clusive in the diagnosis of the instrument cluster, the
Front Control Module (FCM), or the electronic mes-
sage inputs to or outputs from the instrument cluster
and the FCM that control the operation of the wiper
high/low relay. The most reliable, efficient, and accu-
rate means to diagnose the wiper high/low relay, the
instrument cluster, the FCM, or the electronic mes-
sage inputs and outputs related to the wiper high/low
relay operation requires the use of a DRBIIItscan
tool. Refer to the appropriate diagnostic information.
DIAGNOSIS AND TESTING - WIPER HIGH/LOW
RELAY
The wiper high/low relay (Fig. 23) is located in the
Integrated Power Module (IPM) in the engine com-
partment near the battery. Refer to the appropriate
wiring information. The wiring information includes
wiring diagrams, proper wire and connector repair
procedures, details of wire harness routing and
retention, connector pin-out information and location
views for the various wire harness connectors, splices
and grounds.
(1) Remove the wiper high/low relay from the IPM.
(Refer to 8 - ELECTRICAL/WIPERS/WASHERS/
WIPER HIGH/LOW RELAY - REMOVAL).
(2) A relay in the de-energized position should
have continuity between terminals 87A and 30, and
no continuity between terminals 87 and 30. If OK, go
to Step 3. If not OK, replace the faulty relay.
(3) Resistance between terminals 85 and 86 (elec-
tromagnet) should be 75 8 ohms. If OK, go to Step
4. If not OK, replace the faulty relay.(4) Connect a battery to terminals 85 and 86.
There should now be continuity between terminals
30 and 87, and no continuity between terminals 87A
and 30. If OK, reinstall the relay and use a DRBIIIt
scan tool to perform further testing. Refer to the
appropriate diagnostic information.
REMOVAL
(1) Disconnect and isolate the battery negative
cable.
(2) Remove the cover from the Integrated Power
Module (IPM) (Fig. 24).
(3) Remove the wiper high/low relay by grasping it
firmly and pulling it straight out from the receptacle
in the IPM.
Fig. 23 ISO Micro Relay
30 - COMMON FEED
85 - COIL GROUND
86 - COIL BATTERY
87 - NORMALLY OPEN
87A - NORMALLY CLOSED
Fig. 24 Integrated Power Module
1 - 15 - CARTRIDGE FUSE
16 - 53 - BLADE FUSE
54 - HEATED MIRROR RELAY
55 - WIPER ON/OFF RELAY
56 - A/C CONDENSER FAN RELAY
57 - ENGINE CONTROL RELAY
58 - FUEL PUMP RELAY
59 - TRANSMISSION RELAY
60 - WIPER HIGH/LOW RELAY
61 - SPARE
62 - FOG LAMP RELAY
63 - ADJUSTABLE PEDAL RELAY
64 - A/C CLUTCH RELAY
65 - SPARE
66 - O2 RELAY
67 - SPARE
68 - SPARE
69 - SPARE
70 - SPARE
71 - SPARE
72 - STARTER RELAY
73 - PARK LAMP RELAY
DRWIPERS/WASHERS 8R - 21
WIPER HIGH/LOW RELAY (Continued)
Page 722 of 2627
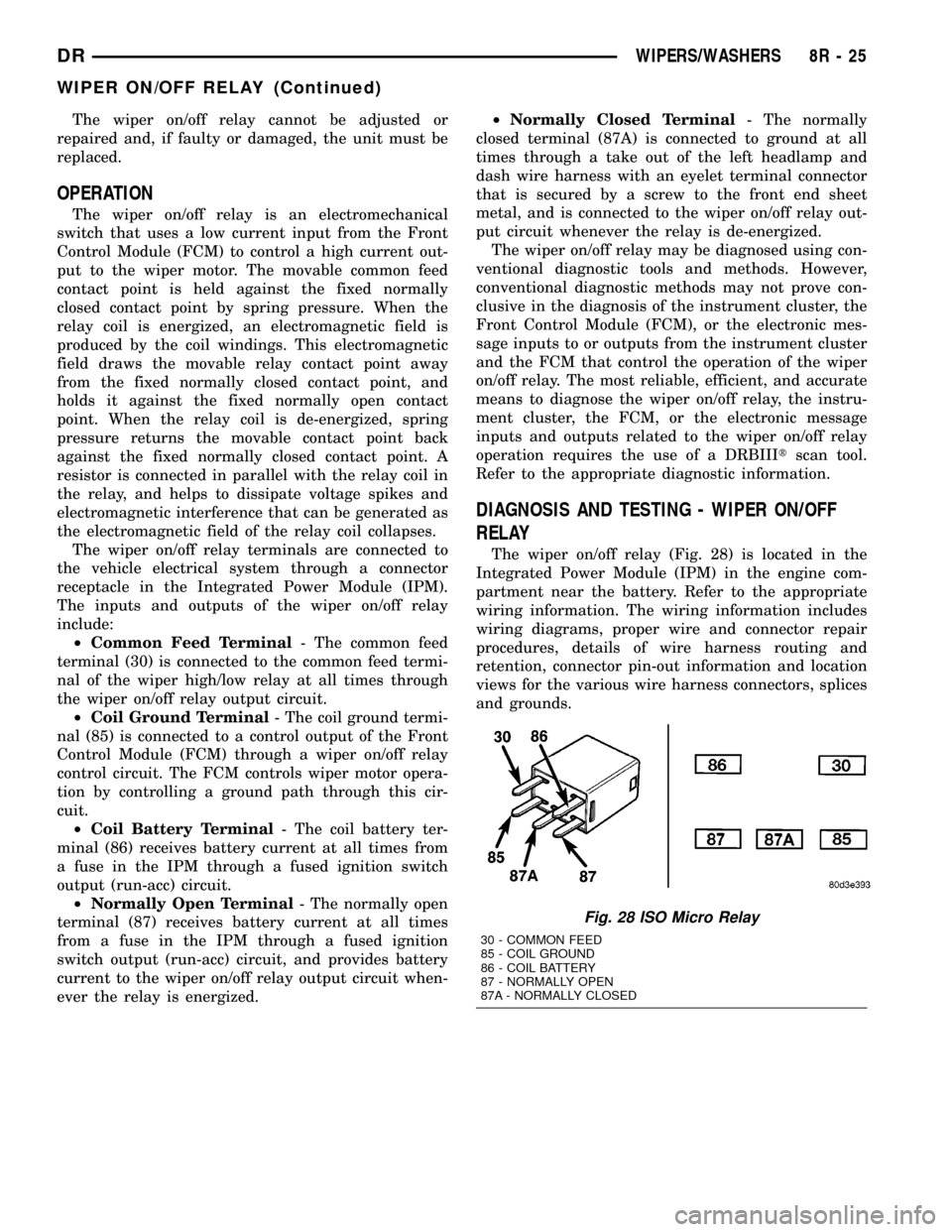
The wiper on/off relay cannot be adjusted or
repaired and, if faulty or damaged, the unit must be
replaced.
OPERATION
The wiper on/off relay is an electromechanical
switch that uses a low current input from the Front
Control Module (FCM) to control a high current out-
put to the wiper motor. The movable common feed
contact point is held against the fixed normally
closed contact point by spring pressure. When the
relay coil is energized, an electromagnetic field is
produced by the coil windings. This electromagnetic
field draws the movable relay contact point away
from the fixed normally closed contact point, and
holds it against the fixed normally open contact
point. When the relay coil is de-energized, spring
pressure returns the movable contact point back
against the fixed normally closed contact point. A
resistor is connected in parallel with the relay coil in
the relay, and helps to dissipate voltage spikes and
electromagnetic interference that can be generated as
the electromagnetic field of the relay coil collapses.
The wiper on/off relay terminals are connected to
the vehicle electrical system through a connector
receptacle in the Integrated Power Module (IPM).
The inputs and outputs of the wiper on/off relay
include:
²Common Feed Terminal- The common feed
terminal (30) is connected to the common feed termi-
nal of the wiper high/low relay at all times through
the wiper on/off relay output circuit.
²Coil Ground Terminal- The coil ground termi-
nal (85) is connected to a control output of the Front
Control Module (FCM) through a wiper on/off relay
control circuit. The FCM controls wiper motor opera-
tion by controlling a ground path through this cir-
cuit.
²Coil Battery Terminal- The coil battery ter-
minal (86) receives battery current at all times from
a fuse in the IPM through a fused ignition switch
output (run-acc) circuit.
²Normally Open Terminal- The normally open
terminal (87) receives battery current at all times
from a fuse in the IPM through a fused ignition
switch output (run-acc) circuit, and provides battery
current to the wiper on/off relay output circuit when-
ever the relay is energized.²Normally Closed Terminal- The normally
closed terminal (87A) is connected to ground at all
times through a take out of the left headlamp and
dash wire harness with an eyelet terminal connector
that is secured by a screw to the front end sheet
metal, and is connected to the wiper on/off relay out-
put circuit whenever the relay is de-energized.
The wiper on/off relay may be diagnosed using con-
ventional diagnostic tools and methods. However,
conventional diagnostic methods may not prove con-
clusive in the diagnosis of the instrument cluster, the
Front Control Module (FCM), or the electronic mes-
sage inputs to or outputs from the instrument cluster
and the FCM that control the operation of the wiper
on/off relay. The most reliable, efficient, and accurate
means to diagnose the wiper on/off relay, the instru-
ment cluster, the FCM, or the electronic message
inputs and outputs related to the wiper on/off relay
operation requires the use of a DRBIIItscan tool.
Refer to the appropriate diagnostic information.
DIAGNOSIS AND TESTING - WIPER ON/OFF
RELAY
The wiper on/off relay (Fig. 28) is located in the
Integrated Power Module (IPM) in the engine com-
partment near the battery. Refer to the appropriate
wiring information. The wiring information includes
wiring diagrams, proper wire and connector repair
procedures, details of wire harness routing and
retention, connector pin-out information and location
views for the various wire harness connectors, splices
and grounds.
Fig. 28 ISO Micro Relay
30 - COMMON FEED
85 - COIL GROUND
86 - COIL BATTERY
87 - NORMALLY OPEN
87A - NORMALLY CLOSED
DRWIPERS/WASHERS 8R - 25
WIPER ON/OFF RELAY (Continued)
Page 732 of 2627
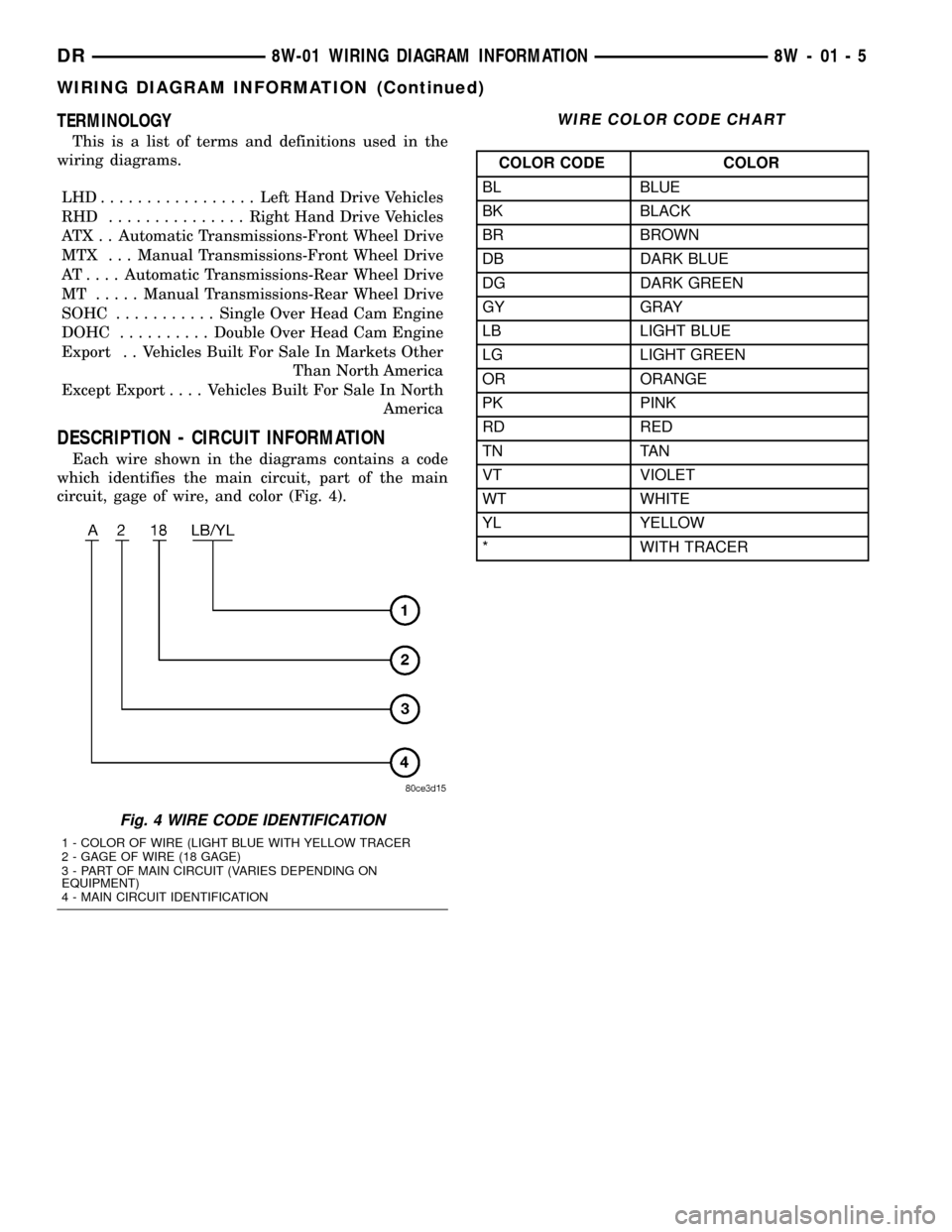
TERMINOLOGY
This is a list of terms and definitions used in the
wiring diagrams.
LHD.................Left Hand Drive Vehicles
RHD ...............Right Hand Drive Vehicles
ATX . . Automatic Transmissions-Front Wheel Drive
MTX . . . Manual Transmissions-Front Wheel Drive
AT....Automatic Transmissions-Rear Wheel Drive
MT .....Manual Transmissions-Rear Wheel Drive
SOHC...........Single Over Head Cam Engine
DOHC..........Double Over Head Cam Engine
Export . . Vehicles Built For Sale In Markets Other
Than North America
Except Export.... Vehicles Built For Sale In North
America
DESCRIPTION - CIRCUIT INFORMATION
Each wire shown in the diagrams contains a code
which identifies the main circuit, part of the main
circuit, gage of wire, and color (Fig. 4).
WIRE COLOR CODE CHART
COLOR CODE COLOR
BL BLUE
BK BLACK
BR BROWN
DB DARK BLUE
DG DARK GREEN
GY GRAY
LB LIGHT BLUE
LG LIGHT GREEN
OR ORANGE
PK PINK
RD RED
TN TAN
VT VIOLET
WT WHITE
YL YELLOW
* WITH TRACER
Fig. 4 WIRE CODE IDENTIFICATION
1 - COLOR OF WIRE (LIGHT BLUE WITH YELLOW TRACER
2 - GAGE OF WIRE (18 GAGE)
3 - PART OF MAIN CIRCUIT (VARIES DEPENDING ON
EQUIPMENT)
4 - MAIN CIRCUIT IDENTIFICATION
DR8W-01 WIRING DIAGRAM INFORMATION 8W - 01 - 5
WIRING DIAGRAM INFORMATION (Continued)
Page 734 of 2627
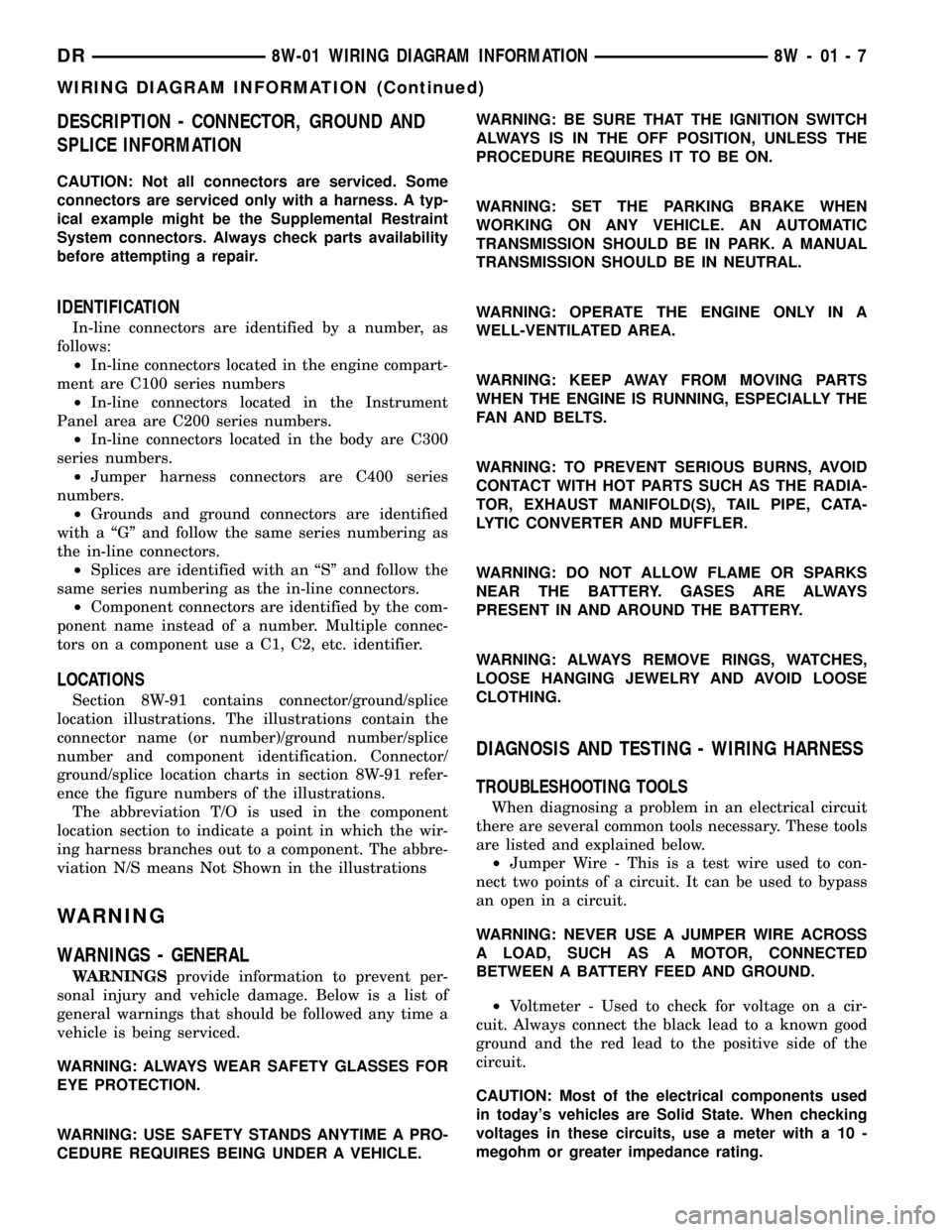
DESCRIPTION - CONNECTOR, GROUND AND
SPLICE INFORMATION
CAUTION: Not all connectors are serviced. Some
connectors are serviced only with a harness. A typ-
ical example might be the Supplemental Restraint
System connectors. Always check parts availability
before attempting a repair.
IDENTIFICATION
In-line connectors are identified by a number, as
follows:
²In-line connectors located in the engine compart-
ment are C100 series numbers
²In-line connectors located in the Instrument
Panel area are C200 series numbers.
²In-line connectors located in the body are C300
series numbers.
²Jumper harness connectors are C400 series
numbers.
²Grounds and ground connectors are identified
with a ªGº and follow the same series numbering as
the in-line connectors.
²Splices are identified with an ªSº and follow the
same series numbering as the in-line connectors.
²Component connectors are identified by the com-
ponent name instead of a number. Multiple connec-
tors on a component use a C1, C2, etc. identifier.
LOCATIONS
Section 8W-91 contains connector/ground/splice
location illustrations. The illustrations contain the
connector name (or number)/ground number/splice
number and component identification. Connector/
ground/splice location charts in section 8W-91 refer-
ence the figure numbers of the illustrations.
The abbreviation T/O is used in the component
location section to indicate a point in which the wir-
ing harness branches out to a component. The abbre-
viation N/S means Not Shown in the illustrations
WARNING
WARNINGS - GENERAL
WARNINGSprovide information to prevent per-
sonal injury and vehicle damage. Below is a list of
general warnings that should be followed any time a
vehicle is being serviced.
WARNING: ALWAYS WEAR SAFETY GLASSES FOR
EYE PROTECTION.
WARNING: USE SAFETY STANDS ANYTIME A PRO-
CEDURE REQUIRES BEING UNDER A VEHICLE.WARNING: BE SURE THAT THE IGNITION SWITCH
ALWAYS IS IN THE OFF POSITION, UNLESS THE
PROCEDURE REQUIRES IT TO BE ON.
WARNING: SET THE PARKING BRAKE WHEN
WORKING ON ANY VEHICLE. AN AUTOMATIC
TRANSMISSION SHOULD BE IN PARK. A MANUAL
TRANSMISSION SHOULD BE IN NEUTRAL.
WARNING: OPERATE THE ENGINE ONLY IN A
WELL-VENTILATED AREA.
WARNING: KEEP AWAY FROM MOVING PARTS
WHEN THE ENGINE IS RUNNING, ESPECIALLY THE
FAN AND BELTS.
WARNING: TO PREVENT SERIOUS BURNS, AVOID
CONTACT WITH HOT PARTS SUCH AS THE RADIA-
TOR, EXHAUST MANIFOLD(S), TAIL PIPE, CATA-
LYTIC CONVERTER AND MUFFLER.
WARNING: DO NOT ALLOW FLAME OR SPARKS
NEAR THE BATTERY. GASES ARE ALWAYS
PRESENT IN AND AROUND THE BATTERY.
WARNING: ALWAYS REMOVE RINGS, WATCHES,
LOOSE HANGING JEWELRY AND AVOID LOOSE
CLOTHING.
DIAGNOSIS AND TESTING - WIRING HARNESS
TROUBLESHOOTING TOOLS
When diagnosing a problem in an electrical circuit
there are several common tools necessary. These tools
are listed and explained below.
²Jumper Wire - This is a test wire used to con-
nect two points of a circuit. It can be used to bypass
an open in a circuit.
WARNING: NEVER USE A JUMPER WIRE ACROSS
A LOAD, SUCH AS A MOTOR, CONNECTED
BETWEEN A BATTERY FEED AND GROUND.
²Voltmeter - Used to check for voltage on a cir-
cuit. Always connect the black lead to a known good
ground and the red lead to the positive side of the
circuit.
CAUTION: Most of the electrical components used
in today's vehicles are Solid State. When checking
voltages in these circuits, use a meter with a 10 -
megohm or greater impedance rating.
DR8W-01 WIRING DIAGRAM INFORMATION 8W - 01 - 7
WIRING DIAGRAM INFORMATION (Continued)
Page 1465 of 2627
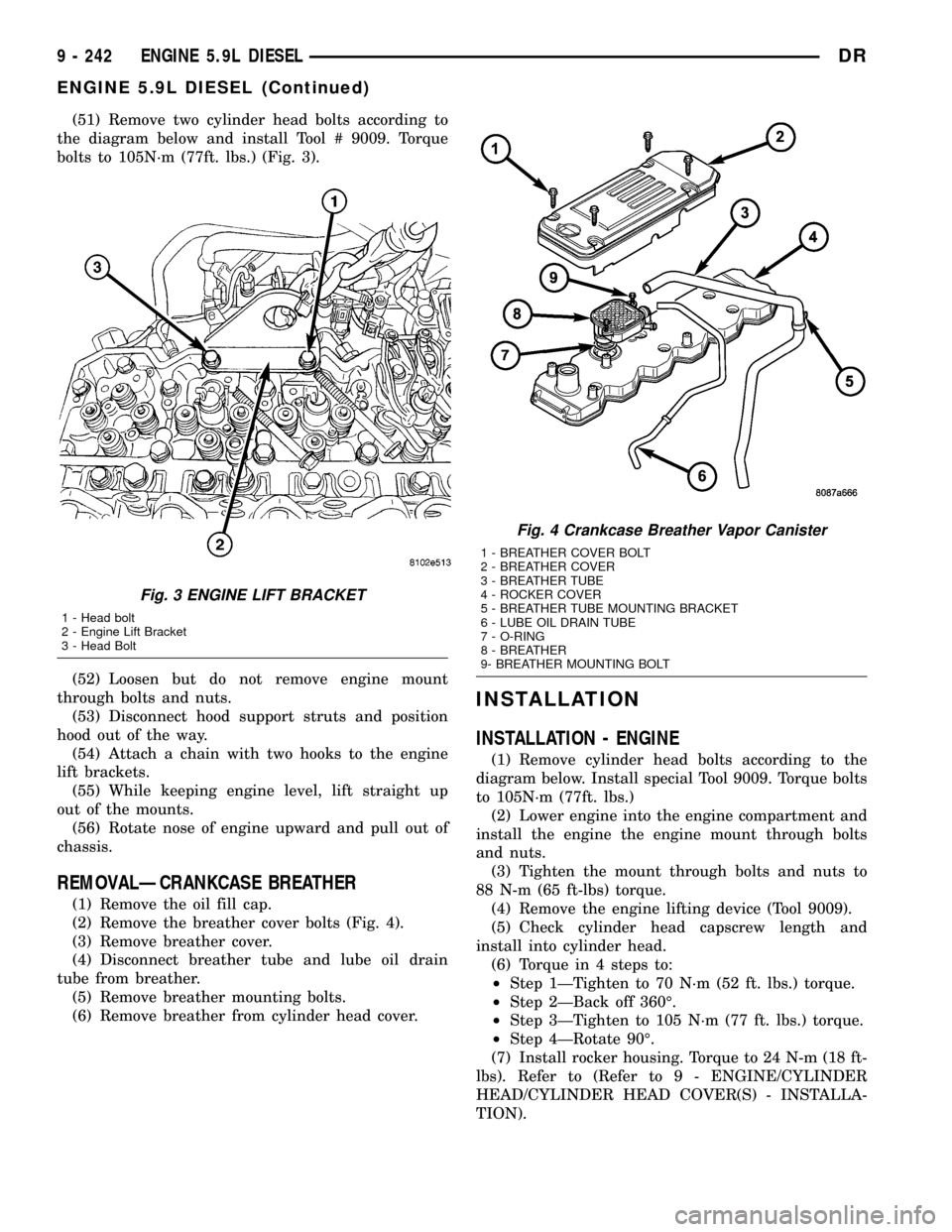
(51) Remove two cylinder head bolts according to
the diagram below and install Tool # 9009. Torque
bolts to 105N´m (77ft. lbs.) (Fig. 3).
(52) Loosen but do not remove engine mount
through bolts and nuts.
(53) Disconnect hood support struts and position
hood out of the way.
(54) Attach a chain with two hooks to the engine
lift brackets.
(55) While keeping engine level, lift straight up
out of the mounts.
(56) Rotate nose of engine upward and pull out of
chassis.
REMOVALÐCRANKCASE BREATHER
(1) Remove the oil fill cap.
(2) Remove the breather cover bolts (Fig. 4).
(3) Remove breather cover.
(4) Disconnect breather tube and lube oil drain
tube from breather.
(5) Remove breather mounting bolts.
(6) Remove breather from cylinder head cover.
INSTALLATION
INSTALLATION - ENGINE
(1) Remove cylinder head bolts according to the
diagram below. Install special Tool 9009. Torque bolts
to 105N´m (77ft. lbs.)
(2) Lower engine into the engine compartment and
install the engine the engine mount through bolts
and nuts.
(3) Tighten the mount through bolts and nuts to
88 N-m (65 ft-lbs) torque.
(4) Remove the engine lifting device (Tool 9009).
(5) Check cylinder head capscrew length and
install into cylinder head.
(6) Torque in 4 steps to:
²Step 1ÐTighten to 70 N´m (52 ft. lbs.) torque.
²Step 2ÐBack off 360É.
²Step 3ÐTighten to 105 N´m (77 ft. lbs.) torque.
²Step 4ÐRotate 90É.
(7) Install rocker housing. Torque to 24 N-m (18 ft-
lbs). Refer to (Refer to 9 - ENGINE/CYLINDER
HEAD/CYLINDER HEAD COVER(S) - INSTALLA-
TION).
Fig. 3 ENGINE LIFT BRACKET
1 - Head bolt
2 - Engine Lift Bracket
3 - Head Bolt
Fig. 4 Crankcase Breather Vapor Canister
1 - BREATHER COVER BOLT
2 - BREATHER COVER
3 - BREATHER TUBE
4 - ROCKER COVER
5 - BREATHER TUBE MOUNTING BRACKET
6 - LUBE OIL DRAIN TUBE
7 - O-RING
8 - BREATHER
9- BREATHER MOUNTING BOLT
9 - 242 ENGINE 5.9L DIESELDR
ENGINE 5.9L DIESEL (Continued)
Page 2497 of 2627
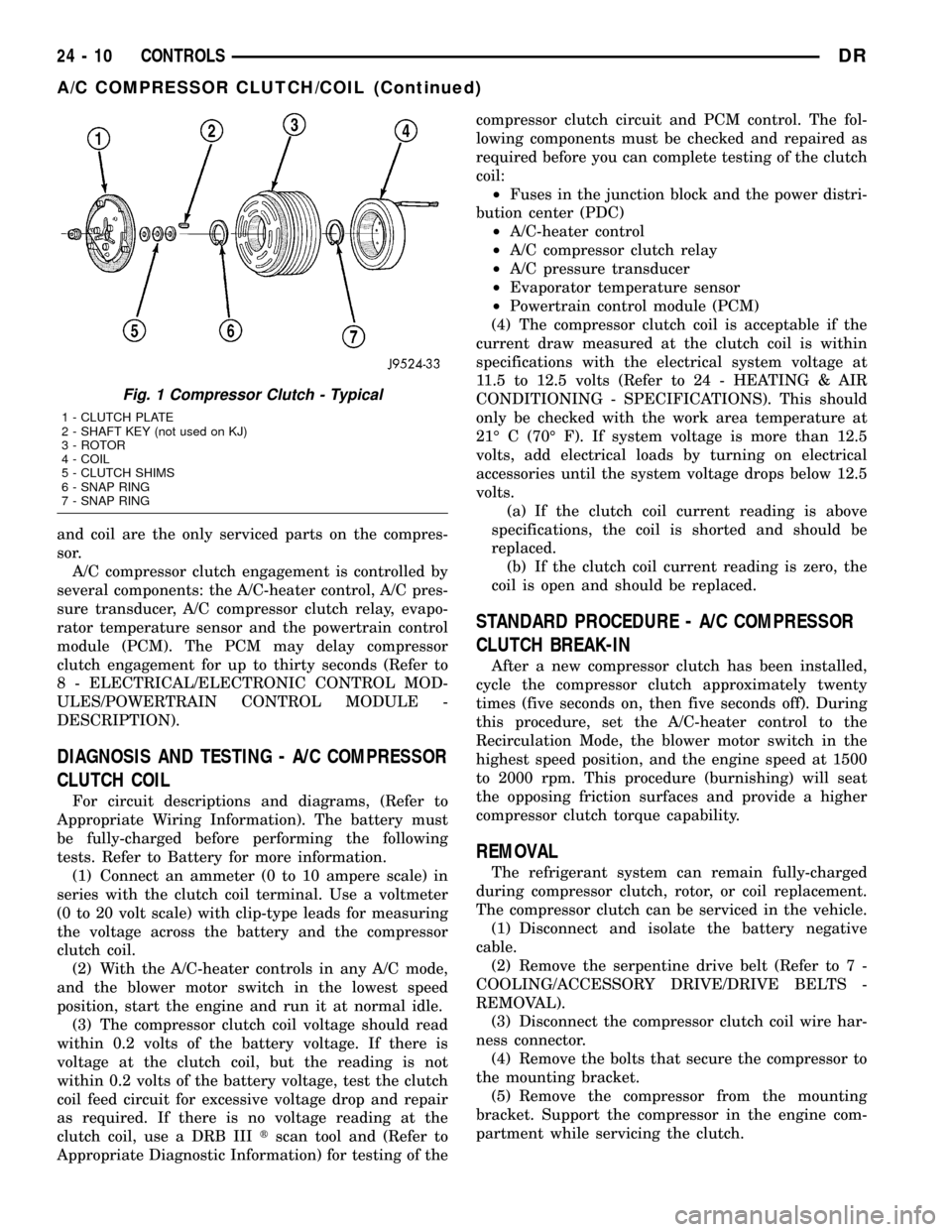
and coil are the only serviced parts on the compres-
sor.
A/C compressor clutch engagement is controlled by
several components: the A/C-heater control, A/C pres-
sure transducer, A/C compressor clutch relay, evapo-
rator temperature sensor and the powertrain control
module (PCM). The PCM may delay compressor
clutch engagement for up to thirty seconds (Refer to
8 - ELECTRICAL/ELECTRONIC CONTROL MOD-
ULES/POWERTRAIN CONTROL MODULE -
DESCRIPTION).
DIAGNOSIS AND TESTING - A/C COMPRESSOR
CLUTCH COIL
For circuit descriptions and diagrams, (Refer to
Appropriate Wiring Information). The battery must
be fully-charged before performing the following
tests. Refer to Battery for more information.
(1) Connect an ammeter (0 to 10 ampere scale) in
series with the clutch coil terminal. Use a voltmeter
(0 to 20 volt scale) with clip-type leads for measuring
the voltage across the battery and the compressor
clutch coil.
(2) With the A/C-heater controls in any A/C mode,
and the blower motor switch in the lowest speed
position, start the engine and run it at normal idle.
(3) The compressor clutch coil voltage should read
within 0.2 volts of the battery voltage. If there is
voltage at the clutch coil, but the reading is not
within 0.2 volts of the battery voltage, test the clutch
coil feed circuit for excessive voltage drop and repair
as required. If there is no voltage reading at the
clutch coil, use a DRB IIItscan tool and (Refer to
Appropriate Diagnostic Information) for testing of thecompressor clutch circuit and PCM control. The fol-
lowing components must be checked and repaired as
required before you can complete testing of the clutch
coil:
²Fuses in the junction block and the power distri-
bution center (PDC)
²A/C-heater control
²A/C compressor clutch relay
²A/C pressure transducer
²Evaporator temperature sensor
²Powertrain control module (PCM)
(4) The compressor clutch coil is acceptable if the
current draw measured at the clutch coil is within
specifications with the electrical system voltage at
11.5 to 12.5 volts (Refer to 24 - HEATING & AIR
CONDITIONING - SPECIFICATIONS). This should
only be checked with the work area temperature at
21É C (70É F). If system voltage is more than 12.5
volts, add electrical loads by turning on electrical
accessories until the system voltage drops below 12.5
volts.
(a) If the clutch coil current reading is above
specifications, the coil is shorted and should be
replaced.
(b) If the clutch coil current reading is zero, the
coil is open and should be replaced.
STANDARD PROCEDURE - A/C COMPRESSOR
CLUTCH BREAK-IN
After a new compressor clutch has been installed,
cycle the compressor clutch approximately twenty
times (five seconds on, then five seconds off). During
this procedure, set the A/C-heater control to the
Recirculation Mode, the blower motor switch in the
highest speed position, and the engine speed at 1500
to 2000 rpm. This procedure (burnishing) will seat
the opposing friction surfaces and provide a higher
compressor clutch torque capability.
REMOVAL
The refrigerant system can remain fully-charged
during compressor clutch, rotor, or coil replacement.
The compressor clutch can be serviced in the vehicle.
(1) Disconnect and isolate the battery negative
cable.
(2) Remove the serpentine drive belt (Refer to 7 -
COOLING/ACCESSORY DRIVE/DRIVE BELTS -
REMOVAL).
(3) Disconnect the compressor clutch coil wire har-
ness connector.
(4) Remove the bolts that secure the compressor to
the mounting bracket.
(5) Remove the compressor from the mounting
bracket. Support the compressor in the engine com-
partment while servicing the clutch.
Fig. 1 Compressor Clutch - Typical
1 - CLUTCH PLATE
2 - SHAFT KEY (not used on KJ)
3 - ROTOR
4 - COIL
5 - CLUTCH SHIMS
6 - SNAP RING
7 - SNAP RING
24 - 10 CONTROLSDR
A/C COMPRESSOR CLUTCH/COIL (Continued)
Page 2535 of 2627
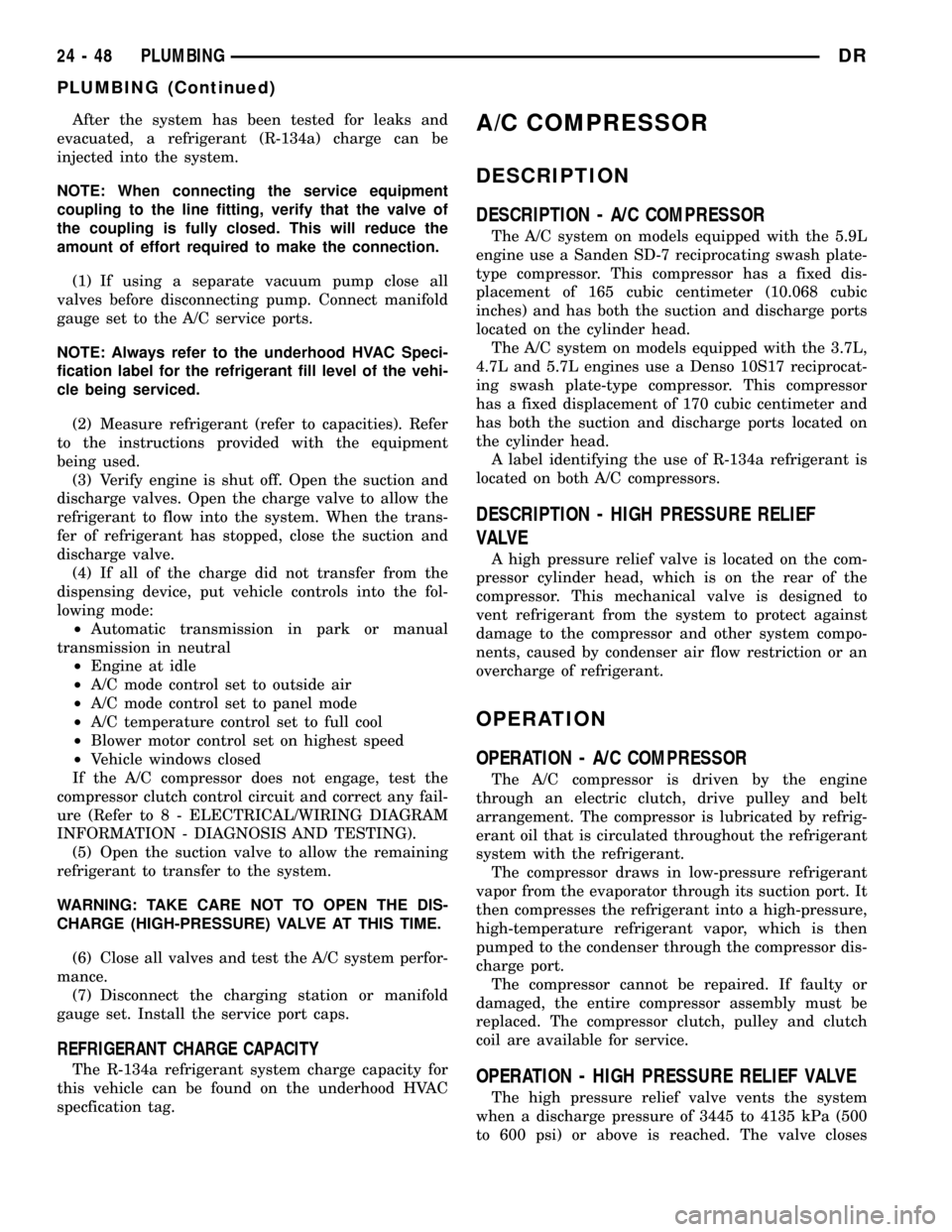
After the system has been tested for leaks and
evacuated, a refrigerant (R-134a) charge can be
injected into the system.
NOTE: When connecting the service equipment
coupling to the line fitting, verify that the valve of
the coupling is fully closed. This will reduce the
amount of effort required to make the connection.
(1) If using a separate vacuum pump close all
valves before disconnecting pump. Connect manifold
gauge set to the A/C service ports.
NOTE: Always refer to the underhood HVAC Speci-
fication label for the refrigerant fill level of the vehi-
cle being serviced.
(2) Measure refrigerant (refer to capacities). Refer
to the instructions provided with the equipment
being used.
(3) Verify engine is shut off. Open the suction and
discharge valves. Open the charge valve to allow the
refrigerant to flow into the system. When the trans-
fer of refrigerant has stopped, close the suction and
discharge valve.
(4) If all of the charge did not transfer from the
dispensing device, put vehicle controls into the fol-
lowing mode:
²Automatic transmission in park or manual
transmission in neutral
²Engine at idle
²A/C mode control set to outside air
²A/C mode control set to panel mode
²A/C temperature control set to full cool
²Blower motor control set on highest speed
²Vehicle windows closed
If the A/C compressor does not engage, test the
compressor clutch control circuit and correct any fail-
ure (Refer to 8 - ELECTRICAL/WIRING DIAGRAM
INFORMATION - DIAGNOSIS AND TESTING).
(5) Open the suction valve to allow the remaining
refrigerant to transfer to the system.
WARNING: TAKE CARE NOT TO OPEN THE DIS-
CHARGE (HIGH-PRESSURE) VALVE AT THIS TIME.
(6) Close all valves and test the A/C system perfor-
mance.
(7) Disconnect the charging station or manifold
gauge set. Install the service port caps.
REFRIGERANT CHARGE CAPACITY
The R-134a refrigerant system charge capacity for
this vehicle can be found on the underhood HVAC
specfication tag.
A/C COMPRESSOR
DESCRIPTION
DESCRIPTION - A/C COMPRESSOR
The A/C system on models equipped with the 5.9L
engine use a Sanden SD-7 reciprocating swash plate-
type compressor. This compressor has a fixed dis-
placement of 165 cubic centimeter (10.068 cubic
inches) and has both the suction and discharge ports
located on the cylinder head.
The A/C system on models equipped with the 3.7L,
4.7L and 5.7L engines use a Denso 10S17 reciprocat-
ing swash plate-type compressor. This compressor
has a fixed displacement of 170 cubic centimeter and
has both the suction and discharge ports located on
the cylinder head.
A label identifying the use of R-134a refrigerant is
located on both A/C compressors.
DESCRIPTION - HIGH PRESSURE RELIEF
VALVE
A high pressure relief valve is located on the com-
pressor cylinder head, which is on the rear of the
compressor. This mechanical valve is designed to
vent refrigerant from the system to protect against
damage to the compressor and other system compo-
nents, caused by condenser air flow restriction or an
overcharge of refrigerant.
OPERATION
OPERATION - A/C COMPRESSOR
The A/C compressor is driven by the engine
through an electric clutch, drive pulley and belt
arrangement. The compressor is lubricated by refrig-
erant oil that is circulated throughout the refrigerant
system with the refrigerant.
The compressor draws in low-pressure refrigerant
vapor from the evaporator through its suction port. It
then compresses the refrigerant into a high-pressure,
high-temperature refrigerant vapor, which is then
pumped to the condenser through the compressor dis-
charge port.
The compressor cannot be repaired. If faulty or
damaged, the entire compressor assembly must be
replaced. The compressor clutch, pulley and clutch
coil are available for service.
OPERATION - HIGH PRESSURE RELIEF VALVE
The high pressure relief valve vents the system
when a discharge pressure of 3445 to 4135 kPa (500
to 600 psi) or above is reached. The valve closes
24 - 48 PLUMBINGDR
PLUMBING (Continued)
Page 2597 of 2627
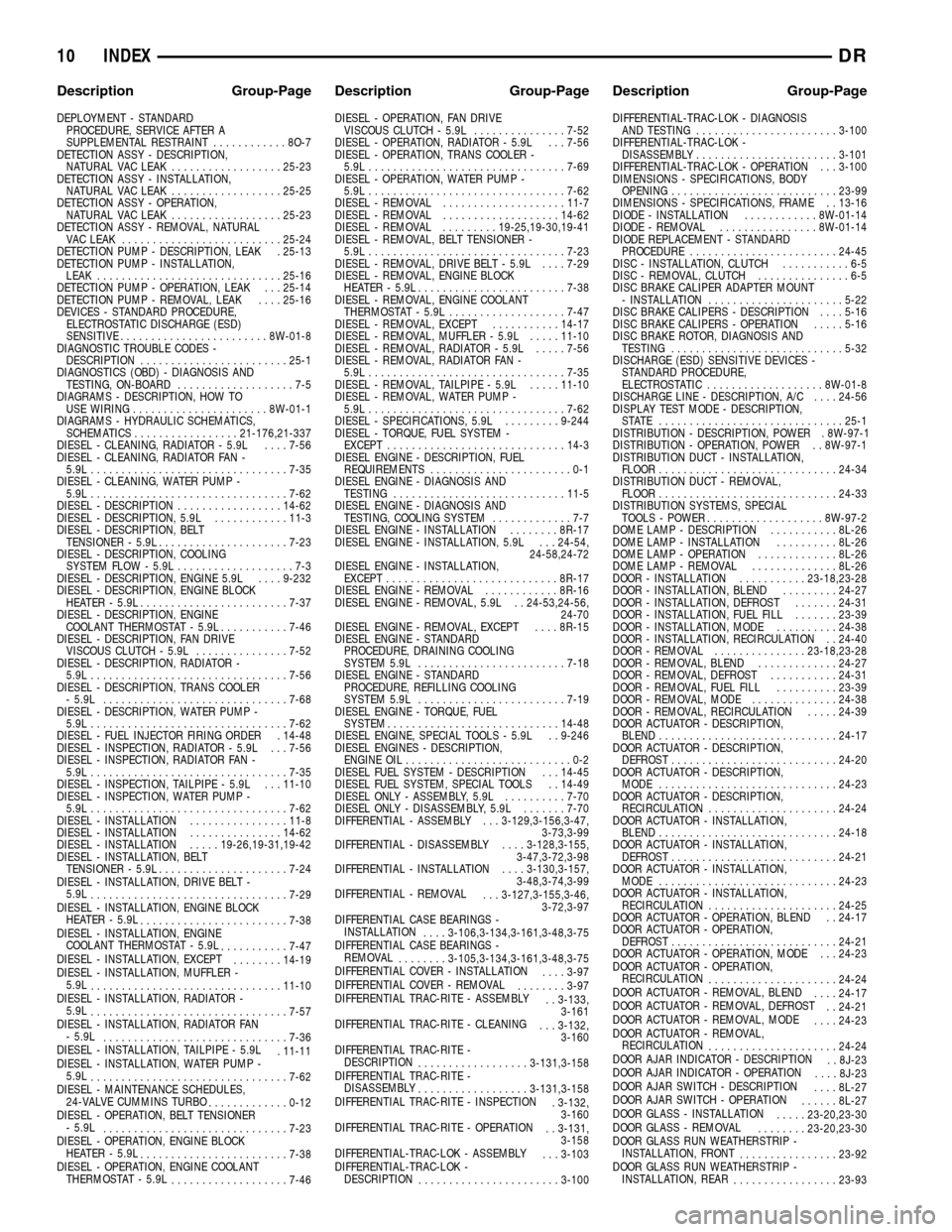
DEPLOYMENT - STANDARD
PROCEDURE, SERVICE AFTER A
SUPPLEMENTAL RESTRAINT............8O-7
DETECTION ASSY - DESCRIPTION,
NATURAL VAC LEAK..................25-23
DETECTION ASSY - INSTALLATION,
NATURAL VAC LEAK..................25-25
DETECTION ASSY - OPERATION,
NATURAL VAC LEAK..................25-23
DETECTION ASSY - REMOVAL, NATURAL
VAC LEAK..........................25-24
DETECTION PUMP - DESCRIPTION, LEAK . 25-13
DETECTION PUMP - INSTALLATION,
LEAK..............................25-16
DETECTION PUMP - OPERATION, LEAK . . . 25-14
DETECTION PUMP - REMOVAL, LEAK....25-16
DEVICES - STANDARD PROCEDURE,
ELECTROSTATIC DISCHARGE (ESD)
SENSITIVE........................8W-01-8
DIAGNOSTIC TROUBLE CODES -
DESCRIPTION........................25-1
DIAGNOSTICS (OBD) - DIAGNOSIS AND
TESTING, ON-BOARD...................7-5
DIAGRAMS - DESCRIPTION, HOW TO
USE WIRING......................8W-01-1
DIAGRAMS - HYDRAULIC SCHEMATICS,
SCHEMATICS.................21-176,21-337
DIESEL - CLEANING, RADIATOR - 5.9L....7-56
DIESEL - CLEANING, RADIATOR FAN -
5.9L................................7-35
DIESEL - CLEANING, WATER PUMP -
5.9L................................7-62
DIESEL - DESCRIPTION.................14-62
DIESEL - DESCRIPTION, 5.9L............11-3
DIESEL - DESCRIPTION, BELT
TENSIONER - 5.9L.....................7-23
DIESEL - DESCRIPTION, COOLING
SYSTEM FLOW - 5.9L...................7-3
DIESEL - DESCRIPTION, ENGINE 5.9L....9-232
DIESEL - DESCRIPTION, ENGINE BLOCK
HEATER - 5.9L........................7-37
DIESEL - DESCRIPTION, ENGINE
COOLANT THERMOSTAT - 5.9L...........7-46
DIESEL - DESCRIPTION, FAN DRIVE
VISCOUS CLUTCH - 5.9L...............7-52
DIESEL - DESCRIPTION, RADIATOR -
5.9L................................7-56
DIESEL - DESCRIPTION, TRANS COOLER
- 5.9L..............................7-68
DIESEL - DESCRIPTION, WATER PUMP -
5.9L................................7-62
DIESEL - FUEL INJECTOR FIRING ORDER . 14-48
DIESEL - INSPECTION, RADIATOR - 5.9L . . . 7-56
DIESEL - INSPECTION, RADIATOR FAN -
5.9L................................7-35
DIESEL - INSPECTION, TAILPIPE - 5.9L . . . 11-10
DIESEL - INSPECTION, WATER PUMP -
5.9L................................7-62
DIESEL - INSTALLATION................11-8
DIESEL - INSTALLATION...............14-62
DIESEL - INSTALLATION.....19-26,19-31,19-42
DIESEL - INSTALLATION, BELT
TENSIONER - 5.9L.....................7-24
DIESEL - INSTALLATION, DRIVE BELT -
5.9L
................................7-29
DIESEL - INSTALLATION, ENGINE BLOCK
HEATER - 5.9L
........................7-38
DIESEL - INSTALLATION, ENGINE
COOLANT THERMOSTAT - 5.9L
...........7-47
DIESEL - INSTALLATION, EXCEPT
........14-19
DIESEL - INSTALLATION, MUFFLER -
5.9L
...............................11-10
DIESEL - INSTALLATION, RADIATOR -
5.9L
................................7-57
DIESEL - INSTALLATION, RADIATOR FAN
- 5.9L
..............................7-36
DIESEL - INSTALLATION, TAILPIPE - 5.9L
. 11-11
DIESEL - INSTALLATION, WATER PUMP -
5.9L
................................7-62
DIESEL - MAINTENANCE SCHEDULES,
24-VALVE CUMMINS TURBO
.............0-12
DIESEL - OPERATION, BELT TENSIONER
- 5.9L
..............................7-23
DIESEL - OPERATION, ENGINE BLOCK
HEATER - 5.9L
........................7-38
DIESEL - OPERATION, ENGINE COOLANT
THERMOSTAT - 5.9L
...................7-46DIESEL - OPERATION, FAN DRIVE
VISCOUS CLUTCH - 5.9L...............7-52
DIESEL - OPERATION, RADIATOR - 5.9L . . . 7-56
DIESEL - OPERATION, TRANS COOLER -
5.9L................................7-69
DIESEL - OPERATION, WATER PUMP -
5.9L................................7-62
DIESEL - REMOVAL....................11-7
DIESEL - REMOVAL...................14-62
DIESEL - REMOVAL.........19-25,19-30,19-41
DIESEL - REMOVAL, BELT TENSIONER -
5.9L................................7-23
DIESEL - REMOVAL, DRIVE BELT - 5.9L....7-29
DIESEL - REMOVAL, ENGINE BLOCK
HEATER - 5.9L........................7-38
DIESEL - REMOVAL, ENGINE COOLANT
THERMOSTAT - 5.9L...................7-47
DIESEL - REMOVAL, EXCEPT...........14-17
DIESEL - REMOVAL, MUFFLER - 5.9L.....11-10
DIESEL - REMOVAL, RADIATOR - 5.9L.....7-56
DIESEL - REMOVAL, RADIATOR FAN -
5.9L................................7-35
DIESEL - REMOVAL, TAILPIPE - 5.9L.....11-10
DIESEL - REMOVAL, WATER PUMP -
5.9L................................7-62
DIESEL - SPECIFICATIONS, 5.9L.........9-244
DIESEL - TORQUE, FUEL SYSTEM -
EXCEPT.............................14-3
DIESEL ENGINE - DESCRIPTION, FUEL
REQUIREMENTS.......................0-1
DIESEL ENGINE - DIAGNOSIS AND
TESTING............................11-5
DIESEL ENGINE - DIAGNOSIS AND
TESTING, COOLING SYSTEM.............7-7
DIESEL ENGINE - INSTALLATION........8R-17
DIESEL ENGINE - INSTALLATION, 5.9L . . . 24-54,
24-58,24-72
DIESEL ENGINE - INSTALLATION,
EXCEPT............................8R-17
DIESEL ENGINE - REMOVAL............8R-16
DIESEL ENGINE - REMOVAL, 5.9L . . 24-53,24-56,
24-70
DIESEL ENGINE - REMOVAL, EXCEPT....8R-15
DIESEL ENGINE - STANDARD
PROCEDURE, DRAINING COOLING
SYSTEM 5.9L........................7-18
DIESEL ENGINE - STANDARD
PROCEDURE, REFILLING COOLING
SYSTEM 5.9L........................7-19
DIESEL ENGINE - TORQUE, FUEL
SYSTEM............................14-48
DIESEL ENGINE, SPECIAL TOOLS - 5.9L . . 9-246
DIESEL ENGINES - DESCRIPTION,
ENGINE OIL...........................0-2
DIESEL FUEL SYSTEM - DESCRIPTION . . . 14-45
DIESEL FUEL SYSTEM, SPECIAL TOOLS . . 14-49
DIESEL ONLY - ASSEMBLY, 5.9L..........7-70
DIESEL ONLY - DISASSEMBLY, 5.9L.......7-70
DIFFERENTIAL - ASSEMBLY . . . 3-129,3-156,3-47,
3-73,3-99
DIFFERENTIAL - DISASSEMBLY....3-128,3-155,
3-47,3-72,3-98
DIFFERENTIAL - INSTALLATION....3-130,3-157,
3-48,3-74,3-99
DIFFERENTIAL - REMOVAL
. . . 3-127,3-155,3-46,
3-72,3-97
DIFFERENTIAL CASE BEARINGS -
INSTALLATION
....3-106,3-134,3-161,3-48,3-75
DIFFERENTIAL CASE BEARINGS -
REMOVAL
........3-105,3-134,3-161,3-48,3-75
DIFFERENTIAL COVER - INSTALLATION
....3-97
DIFFERENTIAL COVER - REMOVAL
........3-97
DIFFERENTIAL TRAC-RITE - ASSEMBLY
. . 3-133,
3-161
DIFFERENTIAL TRAC-RITE - CLEANING
. . . 3-132,
3-160
DIFFERENTIAL TRAC-RITE -
DESCRIPTION
..................3-131,3-158
DIFFERENTIAL TRAC-RITE -
DISASSEMBLY
..................3-131,3-158
DIFFERENTIAL TRAC-RITE - INSPECTION
. 3-132,
3-160
DIFFERENTIAL TRAC-RITE - OPERATION
. . 3-131,
3-158
DIFFERENTIAL-TRAC-LOK - ASSEMBLY
. . . 3-103
DIFFERENTIAL-TRAC-LOK -
DESCRIPTION
.......................3-100DIFFERENTIAL-TRAC-LOK - DIAGNOSIS
AND TESTING.......................3-100
DIFFERENTIAL-TRAC-LOK -
DISASSEMBLY.......................3-101
DIFFERENTIAL-TRAC-LOK - OPERATION . . . 3-100
DIMENSIONS - SPECIFICATIONS, BODY
OPENING...........................23-99
DIMENSIONS - SPECIFICATIONS, FRAME . . 13-16
DIODE - INSTALLATION............8W-01-14
DIODE - REMOVAL................8W-01-14
DIODE REPLACEMENT - STANDARD
PROCEDURE........................24-45
DISC - INSTALLATION, CLUTCH...........6-5
DISC - REMOVAL, CLUTCH...............6-5
DISC BRAKE CALIPER ADAPTER MOUNT
- INSTALLATION......................5-22
DISC BRAKE CALIPERS - DESCRIPTION....5-16
DISC BRAKE CALIPERS - OPERATION.....5-16
DISC BRAKE ROTOR, DIAGNOSIS AND
TESTING............................5-32
DISCHARGE (ESD) SENSITIVE DEVICES -
STANDARD PROCEDURE,
ELECTROSTATIC...................8W-01-8
DISCHARGE LINE - DESCRIPTION, A/C....24-56
DISPLAY TEST MODE - DESCRIPTION,
STATE ..............................25-1
DISTRIBUTION - DESCRIPTION, POWER . 8W-97-1
DISTRIBUTION - OPERATION, POWER . . 8W-97-1
DISTRIBUTION DUCT - INSTALLATION,
FLOOR.............................24-34
DISTRIBUTION DUCT - REMOVAL,
FLOOR.............................24-33
DISTRIBUTION SYSTEMS, SPECIAL
TOOLS - POWER...................8W-97-2
DOME LAMP - DESCRIPTION...........8L-26
DOME LAMP - INSTALLATION..........8L-26
DOME LAMP - OPERATION.............8L-26
DOME LAMP - REMOVAL..............8L-26
DOOR - INSTALLATION...........23-18,23-28
DOOR - INSTALLATION, BLEND.........24-27
DOOR - INSTALLATION, DEFROST.......24-31
DOOR - INSTALLATION, FUEL FILL.......23-39
DOOR - INSTALLATION, MODE..........24-38
DOOR - INSTALLATION, RECIRCULATION . . 24-40
DOOR - REMOVAL...............23-18,23-28
DOOR - REMOVAL, BLEND.............24-27
DOOR - REMOVAL, DEFROST...........24-31
DOOR - REMOVAL, FUEL FILL..........23-39
DOOR - REMOVAL, MODE..............24-38
DOOR - REMOVAL, RECIRCULATION.....24-39
DOOR ACTUATOR - DESCRIPTION,
BLEND.............................24-17
DOOR ACTUATOR - DESCRIPTION,
DEFROST...........................24-20
DOOR ACTUATOR - DESCRIPTION,
MODE.............................24-23
DOOR ACTUATOR - DESCRIPTION,
RECIRCULATION.....................24-24
DOOR ACTUATOR - INSTALLATION,
BLEND.............................24-18
DOOR ACTUATOR - INSTALLATION,
DEFROST...........................24-21
DOOR ACTUATOR - INSTALLATION,
MODE.............................24-23
DOOR ACTUATOR - INSTALLATION,
RECIRCULATION.....................24-25
DOOR ACTUATOR - OPERATION, BLEND . . 24-17
DOOR ACTUATOR - OPERATION,
DEFROST...........................24-21
DOOR ACTUATOR - OPERATION, MODE . . . 24-23
DOOR ACTUATOR - OPERATION,
RECIRCULATION
.....................24-24
DOOR ACTUATOR - REMOVAL, BLEND
....24-17
DOOR ACTUATOR - REMOVAL, DEFROST
. . 24-21
DOOR ACTUATOR - REMOVAL, MODE
....24-23
DOOR ACTUATOR - REMOVAL,
RECIRCULATION
.....................24-24
DOOR AJAR INDICATOR - DESCRIPTION
. . 8J-23
DOOR AJAR INDICATOR - OPERATION
....8J-23
DOOR AJAR SWITCH - DESCRIPTION
....8L-27
DOOR AJAR SWITCH - OPERATION
......8L-27
DOOR GLASS - INSTALLATION
.....23-20,23-30
DOOR GLASS - REMOVAL
........23-20,23-30
DOOR GLASS RUN WEATHERSTRIP -
INSTALLATION, FRONT
................23-92
DOOR GLASS RUN WEATHERSTRIP -
INSTALLATION, REAR
.................23-93
10 INDEXDR
Description Group-Page Description Group-Page Description Group-Page
Page 2603 of 2627
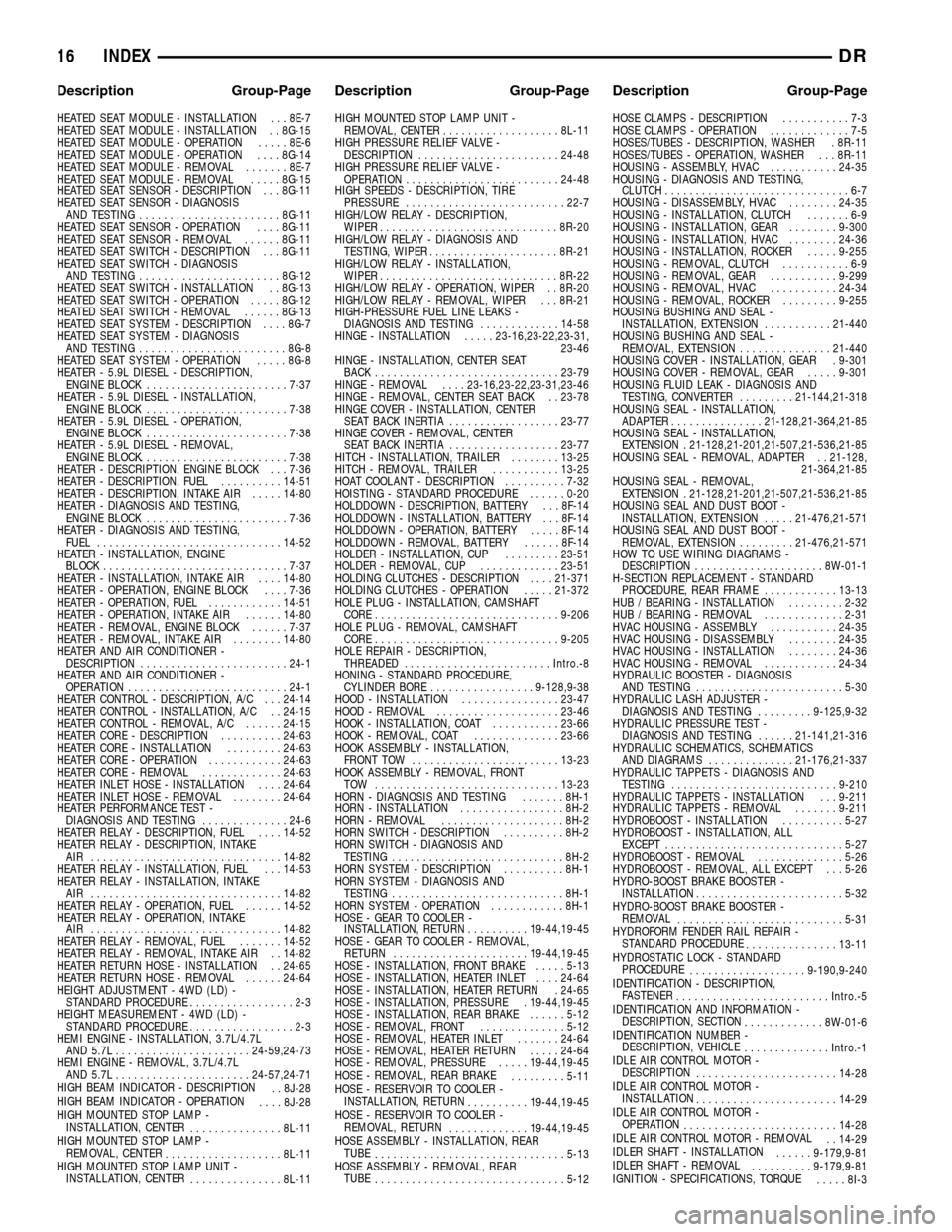
HEATED SEAT MODULE - INSTALLATION . . . 8E-7
HEATED SEAT MODULE - INSTALLATION . . 8G-15
HEATED SEAT MODULE - OPERATION.....8E-6
HEATED SEAT MODULE - OPERATION....8G-14
HEATED SEAT MODULE - REMOVAL.......8E-7
HEATED SEAT MODULE - REMOVAL.....8G-15
HEATED SEAT SENSOR - DESCRIPTION . . . 8G-11
HEATED SEAT SENSOR - DIAGNOSIS
AND TESTING.......................8G-11
HEATED SEAT SENSOR - OPERATION....8G-11
HEATED SEAT SENSOR - REMOVAL......8G-11
HEATED SEAT SWITCH - DESCRIPTION . . . 8G-11
HEATED SEAT SWITCH - DIAGNOSIS
AND TESTING.......................8G-12
HEATED SEAT SWITCH - INSTALLATION . . 8G-13
HEATED SEAT SWITCH - OPERATION.....8G-12
HEATED SEAT SWITCH - REMOVAL......8G-13
HEATED SEAT SYSTEM - DESCRIPTION....8G-7
HEATED SEAT SYSTEM - DIAGNOSIS
AND TESTING........................8G-8
HEATED SEAT SYSTEM - OPERATION.....8G-8
HEATER - 5.9L DIESEL - DESCRIPTION,
ENGINE BLOCK.......................7-37
HEATER - 5.9L DIESEL - INSTALLATION,
ENGINE BLOCK.......................7-38
HEATER - 5.9L DIESEL - OPERATION,
ENGINE BLOCK.......................7-38
HEATER - 5.9L DIESEL - REMOVAL,
ENGINE BLOCK.........................7-38
HEATER - DESCRIPTION, ENGINE BLOCK . . . 7-36
HEATER - DESCRIPTION, FUEL..........14-51
HEATER - DESCRIPTION, INTAKE AIR.....14-80
HEATER - DIAGNOSIS AND TESTING,
ENGINE BLOCK.......................7-36
HEATER - DIAGNOSIS AND TESTING,
FUEL..............................14-52
HEATER - INSTALLATION, ENGINE
BLOCK..............................7-37
HEATER - INSTALLATION, INTAKE AIR....14-80
HEATER - OPERATION, ENGINE BLOCK....7-36
HEATER - OPERATION, FUEL............14-51
HEATER - OPERATION, INTAKE AIR......14-80
HEATER - REMOVAL, ENGINE BLOCK......7-37
HEATER - REMOVAL, INTAKE AIR........14-80
HEATER AND AIR CONDITIONER -
DESCRIPTION........................24-1
HEATER AND AIR CONDITIONER -
OPERATION..........................24-1
HEATER CONTROL - DESCRIPTION, A/C . . . 24-14
HEATER CONTROL - INSTALLATION, A/C . . 24-15
HEATER CONTROL - REMOVAL, A/C......24-15
HEATER CORE - DESCRIPTION..........24-63
HEATER CORE - INSTALLATION.........24-63
HEATER CORE - OPERATION............24-63
HEATER CORE - REMOVAL.............24-63
HEATER INLET HOSE - INSTALLATION....24-64
HEATER INLET HOSE - REMOVAL........24-64
HEATER PERFORMANCE TEST -
DIAGNOSIS AND TESTING..............24-6
HEATER RELAY - DESCRIPTION, FUEL....14-52
HEATER RELAY - DESCRIPTION, INTAKE
AIR ...............................14-82
HEATER RELAY - INSTALLATION, FUEL . . . 14-53
HEATER RELAY - INSTALLATION, INTAKE
AIR ...............................14-82
HEATER RELAY - OPERATION, FUEL......14-52
HEATER RELAY - OPERATION, INTAKE
AIR ...............................14-82
HEATER RELAY - REMOVAL, FUEL.......14-52
HEATER RELAY - REMOVAL, INTAKE AIR . . 14-82
HEATER RETURN HOSE - INSTALLATION . . 24-65
HEATER RETURN HOSE - REMOVAL......24-64
HEIGHT ADJUSTMENT - 4WD (LD) -
STANDARD PROCEDURE.................2-3
HEIGHT MEASUREMENT - 4WD (LD) -
STANDARD PROCEDURE.................2-3
HEMI ENGINE - INSTALLATION, 3.7L/4.7L
AND 5.7L......................24-59,24-73
HEMI ENGINE - REMOVAL, 3.7L/4.7L
AND 5.7L......................24-57,24-71
HIGH BEAM INDICATOR - DESCRIPTION
. . 8J-28
HIGH BEAM INDICATOR - OPERATION
....8J-28
HIGH MOUNTED STOP LAMP -
INSTALLATION, CENTER
...............8L-11
HIGH MOUNTED STOP LAMP -
REMOVAL, CENTER
...................8L-11
HIGH MOUNTED STOP LAMP UNIT -
INSTALLATION, CENTER
...............8L-11HIGH MOUNTED STOP LAMP UNIT -
REMOVAL, CENTER...................8L-11
HIGH PRESSURE RELIEF VALVE -
DESCRIPTION.......................24-48
HIGH PRESSURE RELIEF VALVE -
OPERATION.........................24-48
HIGH SPEEDS - DESCRIPTION, TIRE
PRESSURE..........................22-7
HIGH/LOW RELAY - DESCRIPTION,
WIPER.............................8R-20
HIGH/LOW RELAY - DIAGNOSIS AND
TESTING, WIPER.....................8R-21
HIGH/LOW RELAY - INSTALLATION,
WIPER.............................8R-22
HIGH/LOW RELAY - OPERATION, WIPER . . 8R-20
HIGH/LOW RELAY - REMOVAL, WIPER . . . 8R-21
HIGH-PRESSURE FUEL LINE LEAKS -
DIAGNOSIS AND TESTING.............14-58
HINGE - INSTALLATION.....23-16,23-22,23-31,
23-46
HINGE - INSTALLATION, CENTER SEAT
BACK..............................23-79
HINGE - REMOVAL....23-16,23-22,23-31,23-46
HINGE - REMOVAL, CENTER SEAT BACK . . 23-78
HINGE COVER - INSTALLATION, CENTER
SEAT BACK INERTIA..................23-77
HINGE COVER - REMOVAL, CENTER
SEAT BACK INERTIA..................23-77
HITCH - INSTALLATION, TRAILER........13-25
HITCH - REMOVAL, TRAILER...........13-25
HOAT COOLANT - DESCRIPTION..........7-32
HOISTING - STANDARD PROCEDURE......0-20
HOLDDOWN - DESCRIPTION, BATTERY . . . 8F-14
HOLDDOWN - INSTALLATION, BATTERY . . . 8F-14
HOLDDOWN - OPERATION, BATTERY.....8F-14
HOLDDOWN - REMOVAL, BATTERY......8F-14
HOLDER - INSTALLATION, CUP.........23-51
HOLDER - REMOVAL, CUP.............23-51
HOLDING CLUTCHES - DESCRIPTION....21-371
HOLDING CLUTCHES - OPERATION.....21-372
HOLE PLUG - INSTALLATION, CAMSHAFT
CORE..............................9-206
HOLE PLUG - REMOVAL, CAMSHAFT
CORE..............................9-205
HOLE REPAIR - DESCRIPTION,
THREADED........................Intro.-8
HONING - STANDARD PROCEDURE,
CYLINDER BORE.................9-128,9-38
HOOD - INSTALLATION................23-47
HOOD - REMOVAL....................23-46
HOOK - INSTALLATION, COAT...........23-66
HOOK - REMOVAL, COAT..............23-66
HOOK ASSEMBLY - INSTALLATION,
FRONT TOW........................13-23
HOOK ASSEMBLY - REMOVAL, FRONT
TOW ..............................13-23
HORN - DIAGNOSIS AND TESTING.......8H-1
HORN - INSTALLATION.................8H-2
HORN - REMOVAL....................8H-2
HORN SWITCH - DESCRIPTION..........8H-2
HORN SWITCH - DIAGNOSIS AND
TESTING............................8H-2
HORN SYSTEM - DESCRIPTION..........8H-1
HORN SYSTEM - DIAGNOSIS AND
TESTING............................8H-1
HORN SYSTEM - OPERATION............8H-1
HOSE - GEAR TO COOLER -
INSTALLATION, RETURN..........19-44,19-45
HOSE - GEAR TO COOLER - REMOVAL,
RETURN......................19-44,19-45
HOSE - INSTALLATION, FRONT BRAKE.....5-13
HOSE - INSTALLATION, HEATER INLET....24-64
HOSE - INSTALLATION, HEATER RETURN . 24-65
HOSE - INSTALLATION, PRESSURE . 19-44,19-45
HOSE - INSTALLATION, REAR BRAKE......5-12
HOSE - REMOVAL, FRONT..............5-12
HOSE - REMOVAL, HEATER INLET.......24-64
HOSE - REMOVAL, HEATER RETURN.....24-64
HOSE - REMOVAL, PRESSURE.....19-44,19-45
HOSE - REMOVAL, REAR BRAKE
.........5-11
HOSE - RESERVOIR TO COOLER -
INSTALLATION, RETURN
..........19-44,19-45
HOSE - RESERVOIR TO COOLER -
REMOVAL, RETURN
.............19-44,19-45
HOSE ASSEMBLY - INSTALLATION, REAR
TUBE
...............................5-13
HOSE ASSEMBLY - REMOVAL, REAR
TUBE
...............................5-12HOSE CLAMPS - DESCRIPTION...........7-3
HOSE CLAMPS - OPERATION.............7-5
HOSES/TUBES - DESCRIPTION, WASHER . 8R-11
HOSES/TUBES - OPERATION, WASHER . . . 8R-11
HOUSING - ASSEMBLY, HVAC...........24-35
HOUSING - DIAGNOSIS AND TESTING,
CLUTCH..............................6-7
HOUSING - DISASSEMBLY, HVAC........24-35
HOUSING - INSTALLATION, CLUTCH.......6-9
HOUSING - INSTALLATION, GEAR........9-300
HOUSING - INSTALLATION, HVAC........24-36
HOUSING - INSTALLATION, ROCKER.....9-255
HOUSING - REMOVAL, CLUTCH...........6-9
HOUSING - REMOVAL, GEAR...........9-299
HOUSING - REMOVAL, HVAC...........24-34
HOUSING - REMOVAL, ROCKER.........9-255
HOUSING BUSHING AND SEAL -
INSTALLATION, EXTENSION...........21-440
HOUSING BUSHING AND SEAL -
REMOVAL, EXTENSION...............21-440
HOUSING COVER - INSTALLATION, GEAR . 9-301
HOUSING COVER - REMOVAL, GEAR.....9-301
HOUSING FLUID LEAK - DIAGNOSIS AND
TESTING, CONVERTER.........21-144,21-318
HOUSING SEAL - INSTALLATION,
ADAPTER...............21-128,21-364,21-85
HOUSING SEAL - INSTALLATION,
EXTENSION . 21-128,21-201,21-507,21-536,21-85
HOUSING SEAL - REMOVAL, ADAPTER . . 21-128,
21-364,21-85
HOUSING SEAL - REMOVAL,
EXTENSION . 21-128,21-201,21-507,21-536,21-85
HOUSING SEAL AND DUST BOOT -
INSTALLATION, EXTENSION.....21-476,21-571
HOUSING SEAL AND DUST BOOT -
REMOVAL, EXTENSION.........21-476,21-571
HOW TO USE WIRING DIAGRAMS -
DESCRIPTION.....................8W-01-1
H-SECTION REPLACEMENT - STANDARD
PROCEDURE, REAR FRAME............13-13
HUB / BEARING - INSTALLATION.........2-32
HUB / BEARING - REMOVAL.............2-31
HVAC HOUSING - ASSEMBLY...........24-35
HVAC HOUSING - DISASSEMBLY........24-35
HVAC HOUSING - INSTALLATION........24-36
HVAC HOUSING - REMOVAL............24-34
HYDRAULIC BOOSTER - DIAGNOSIS
AND TESTING........................5-30
HYDRAULIC LASH ADJUSTER -
DIAGNOSIS AND TESTING.........9-125,9-32
HYDRAULIC PRESSURE TEST -
DIAGNOSIS AND TESTING......21-141,21-316
HYDRAULIC SCHEMATICS, SCHEMATICS
AND DIAGRAMS..............21-176,21-337
HYDRAULIC TAPPETS - DIAGNOSIS AND
TESTING...........................9-210
HYDRAULIC TAPPETS - INSTALLATION . . . 9-211
HYDRAULIC TAPPETS - REMOVAL.......9-211
HYDROBOOST - INSTALLATION..........5-27
HYDROBOOST - INSTALLATION, ALL
EXCEPT.............................5-27
HYDROBOOST - REMOVAL..............5-26
HYDROBOOST - REMOVAL, ALL EXCEPT . . . 5-26
HYDRO-BOOST BRAKE BOOSTER -
INSTALLATION........................5-32
HYDRO-BOOST BRAKE BOOSTER -
REMOVAL
...........................5-31
HYDROFORM FENDER RAIL REPAIR -
STANDARD PROCEDURE
...............13-11
HYDROSTATIC LOCK - STANDARD
PROCEDURE
...................9-190,9-240
IDENTIFICATION - DESCRIPTION,
FASTENER
.........................Intro.-5
IDENTIFICATION AND INFORMATION -
DESCRIPTION, SECTION
.............8W-01-6
IDENTIFICATION NUMBER -
DESCRIPTION, VEHICLE
..............Intro.-1
IDLE AIR CONTROL MOTOR -
DESCRIPTION
.......................14-28
IDLE AIR CONTROL MOTOR -
INSTALLATION
.......................14-29
IDLE AIR CONTROL MOTOR -
OPERATION
.........................14-28
IDLE AIR CONTROL MOTOR - REMOVAL
. . 14-29
IDLER SHAFT - INSTALLATION
......9-179,9-81
IDLER SHAFT - REMOVAL
..........9-179,9-81
IGNITION - SPECIFICATIONS, TORQUE
.....8I-3
16 INDEXDR
Description Group-Page Description Group-Page Description Group-Page