DODGE RAM 1500 1998 2.G Workshop Manual
Manufacturer: DODGE, Model Year: 1998, Model line: RAM 1500, Model: DODGE RAM 1500 1998 2.GPages: 2627
Page 2581 of 2627
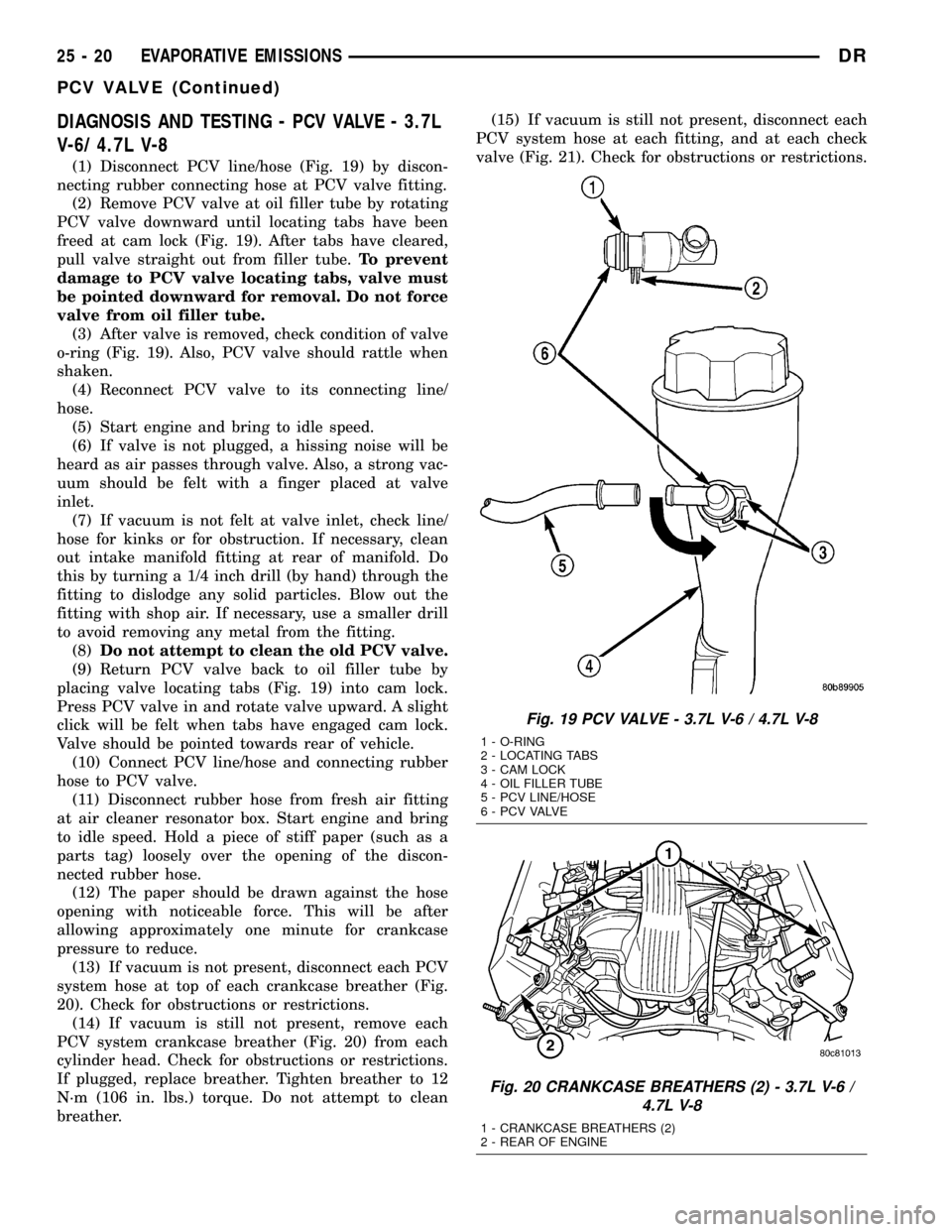
DIAGNOSIS AND TESTING - PCV VALVE - 3.7L
V-6/ 4.7L V-8
(1) Disconnect PCV line/hose (Fig. 19) by discon-
necting rubber connecting hose at PCV valve fitting.
(2) Remove PCV valve at oil filler tube by rotating
PCV valve downward until locating tabs have been
freed at cam lock (Fig. 19). After tabs have cleared,
pull valve straight out from filler tube.To prevent
damage to PCV valve locating tabs, valve must
be pointed downward for removal. Do not force
valve from oil filler tube.
(3) After valve is removed, check condition of valve
o-ring (Fig. 19). Also, PCV valve should rattle when
shaken.
(4) Reconnect PCV valve to its connecting line/
hose.
(5) Start engine and bring to idle speed.
(6) If valve is not plugged, a hissing noise will be
heard as air passes through valve. Also, a strong vac-
uum should be felt with a finger placed at valve
inlet.
(7) If vacuum is not felt at valve inlet, check line/
hose for kinks or for obstruction. If necessary, clean
out intake manifold fitting at rear of manifold. Do
this by turning a 1/4 inch drill (by hand) through the
fitting to dislodge any solid particles. Blow out the
fitting with shop air. If necessary, use a smaller drill
to avoid removing any metal from the fitting.
(8)Do not attempt to clean the old PCV valve.
(9) Return PCV valve back to oil filler tube by
placing valve locating tabs (Fig. 19) into cam lock.
Press PCV valve in and rotate valve upward. A slight
click will be felt when tabs have engaged cam lock.
Valve should be pointed towards rear of vehicle.
(10) Connect PCV line/hose and connecting rubber
hose to PCV valve.
(11) Disconnect rubber hose from fresh air fitting
at air cleaner resonator box. Start engine and bring
to idle speed. Hold a piece of stiff paper (such as a
parts tag) loosely over the opening of the discon-
nected rubber hose.
(12) The paper should be drawn against the hose
opening with noticeable force. This will be after
allowing approximately one minute for crankcase
pressure to reduce.
(13) If vacuum is not present, disconnect each PCV
system hose at top of each crankcase breather (Fig.
20). Check for obstructions or restrictions.
(14) If vacuum is still not present, remove each
PCV system crankcase breather (Fig. 20) from each
cylinder head. Check for obstructions or restrictions.
If plugged, replace breather. Tighten breather to 12
N´m (106 in. lbs.) torque. Do not attempt to clean
breather.(15) If vacuum is still not present, disconnect each
PCV system hose at each fitting, and at each check
valve (Fig. 21). Check for obstructions or restrictions.
Fig. 19 PCV VALVE - 3.7L V-6 / 4.7L V-8
1 - O-RING
2 - LOCATING TABS
3 - CAM LOCK
4 - OIL FILLER TUBE
5 - PCV LINE/HOSE
6 - P C V VA LV E
Fig. 20 CRANKCASE BREATHERS (2) - 3.7L V-6 /
4.7L V-8
1 - CRANKCASE BREATHERS (2)
2 - REAR OF ENGINE
25 - 20 EVAPORATIVE EMISSIONSDR
PCV VALVE (Continued)
Page 2582 of 2627
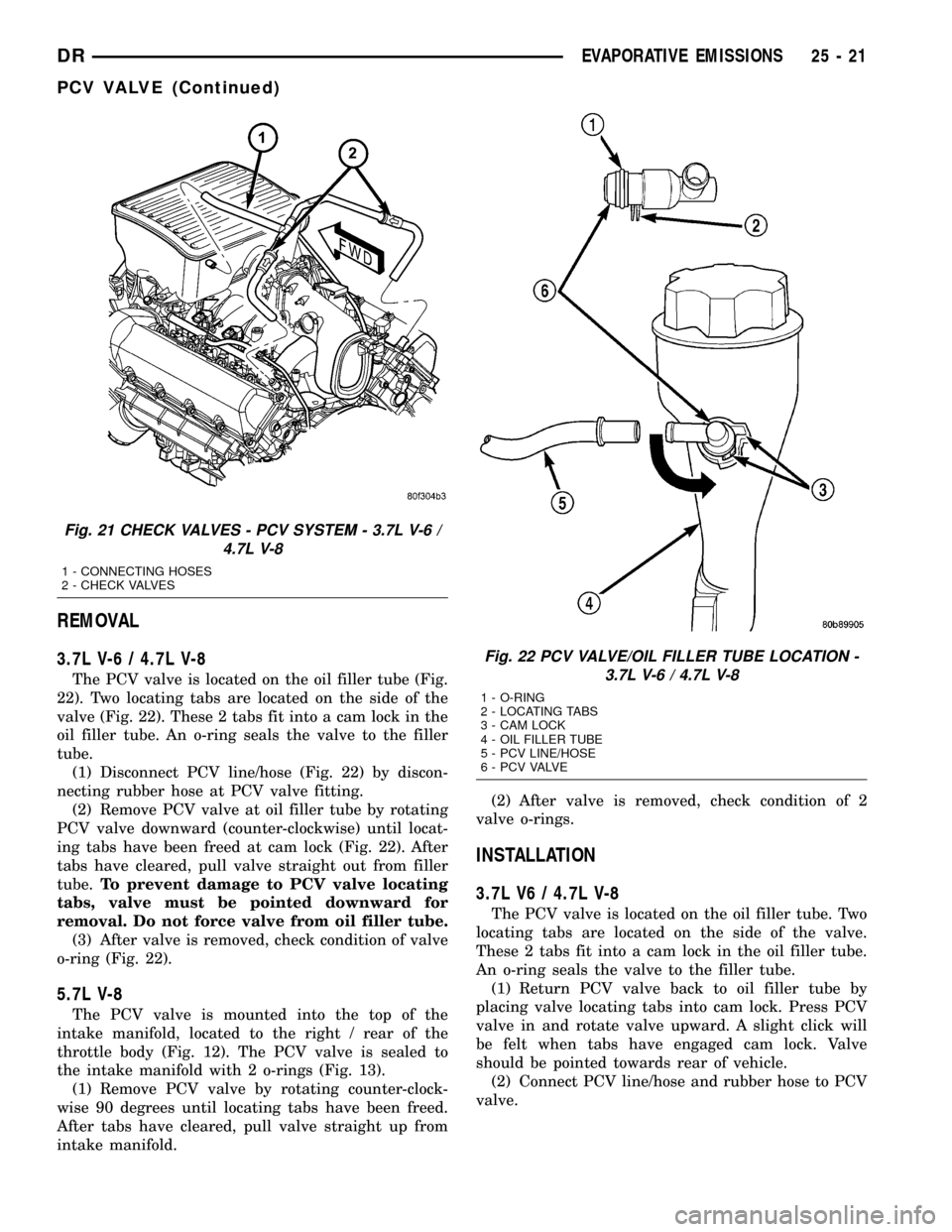
REMOVAL
3.7L V-6 / 4.7L V-8
The PCV valve is located on the oil filler tube (Fig.
22). Two locating tabs are located on the side of the
valve (Fig. 22). These 2 tabs fit into a cam lock in the
oil filler tube. An o-ring seals the valve to the filler
tube.
(1) Disconnect PCV line/hose (Fig. 22) by discon-
necting rubber hose at PCV valve fitting.
(2) Remove PCV valve at oil filler tube by rotating
PCV valve downward (counter-clockwise) until locat-
ing tabs have been freed at cam lock (Fig. 22). After
tabs have cleared, pull valve straight out from filler
tube.To prevent damage to PCV valve locating
tabs, valve must be pointed downward for
removal. Do not force valve from oil filler tube.
(3) After valve is removed, check condition of valve
o-ring (Fig. 22).
5.7L V-8
The PCV valve is mounted into the top of the
intake manifold, located to the right / rear of the
throttle body (Fig. 12). The PCV valve is sealed to
the intake manifold with 2 o-rings (Fig. 13).
(1) Remove PCV valve by rotating counter-clock-
wise 90 degrees until locating tabs have been freed.
After tabs have cleared, pull valve straight up from
intake manifold.(2) After valve is removed, check condition of 2
valve o-rings.
INSTALLATION
3.7L V6 / 4.7L V-8
The PCV valve is located on the oil filler tube. Two
locating tabs are located on the side of the valve.
These 2 tabs fit into a cam lock in the oil filler tube.
An o-ring seals the valve to the filler tube.
(1) Return PCV valve back to oil filler tube by
placing valve locating tabs into cam lock. Press PCV
valve in and rotate valve upward. A slight click will
be felt when tabs have engaged cam lock. Valve
should be pointed towards rear of vehicle.
(2) Connect PCV line/hose and rubber hose to PCV
valve.
Fig. 21 CHECK VALVES - PCV SYSTEM - 3.7L V-6 /
4.7L V-8
1 - CONNECTING HOSES
2 - CHECK VALVES
Fig. 22 PCV VALVE/OIL FILLER TUBE LOCATION -
3.7L V-6 / 4.7L V-8
1 - O-RING
2 - LOCATING TABS
3 - CAM LOCK
4 - OIL FILLER TUBE
5 - PCV LINE/HOSE
6 - P C V VA LV E
DREVAPORATIVE EMISSIONS 25 - 21
PCV VALVE (Continued)
Page 2583 of 2627
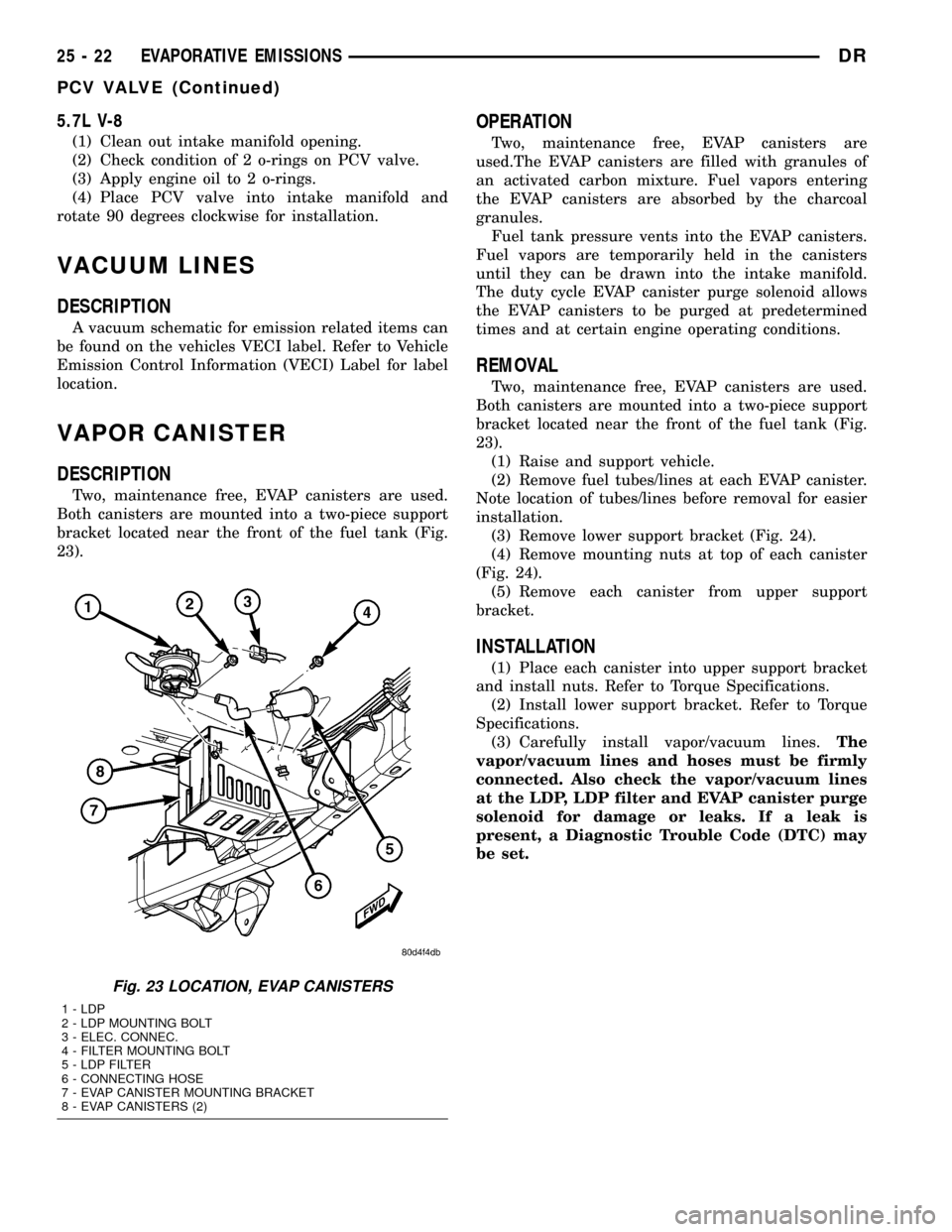
5.7L V-8
(1) Clean out intake manifold opening.
(2) Check condition of 2 o-rings on PCV valve.
(3) Apply engine oil to 2 o-rings.
(4) Place PCV valve into intake manifold and
rotate 90 degrees clockwise for installation.
VACUUM LINES
DESCRIPTION
A vacuum schematic for emission related items can
be found on the vehicles VECI label. Refer to Vehicle
Emission Control Information (VECI) Label for label
location.
VAPOR CANISTER
DESCRIPTION
Two, maintenance free, EVAP canisters are used.
Both canisters are mounted into a two-piece support
bracket located near the front of the fuel tank (Fig.
23).
OPERATION
Two, maintenance free, EVAP canisters are
used.The EVAP canisters are filled with granules of
an activated carbon mixture. Fuel vapors entering
the EVAP canisters are absorbed by the charcoal
granules.
Fuel tank pressure vents into the EVAP canisters.
Fuel vapors are temporarily held in the canisters
until they can be drawn into the intake manifold.
The duty cycle EVAP canister purge solenoid allows
the EVAP canisters to be purged at predetermined
times and at certain engine operating conditions.
REMOVAL
Two, maintenance free, EVAP canisters are used.
Both canisters are mounted into a two-piece support
bracket located near the front of the fuel tank (Fig.
23).
(1) Raise and support vehicle.
(2) Remove fuel tubes/lines at each EVAP canister.
Note location of tubes/lines before removal for easier
installation.
(3) Remove lower support bracket (Fig. 24).
(4) Remove mounting nuts at top of each canister
(Fig. 24).
(5) Remove each canister from upper support
bracket.
INSTALLATION
(1) Place each canister into upper support bracket
and install nuts. Refer to Torque Specifications.
(2) Install lower support bracket. Refer to Torque
Specifications.
(3) Carefully install vapor/vacuum lines.The
vapor/vacuum lines and hoses must be firmly
connected. Also check the vapor/vacuum lines
at the LDP, LDP filter and EVAP canister purge
solenoid for damage or leaks. If a leak is
present, a Diagnostic Trouble Code (DTC) may
be set.
Fig. 23 LOCATION, EVAP CANISTERS
1 - LDP
2 - LDP MOUNTING BOLT
3 - ELEC. CONNEC.
4 - FILTER MOUNTING BOLT
5 - LDP FILTER
6 - CONNECTING HOSE
7 - EVAP CANISTER MOUNTING BRACKET
8 - EVAP CANISTERS (2)
25 - 22 EVAPORATIVE EMISSIONSDR
PCV VALVE (Continued)
Page 2584 of 2627
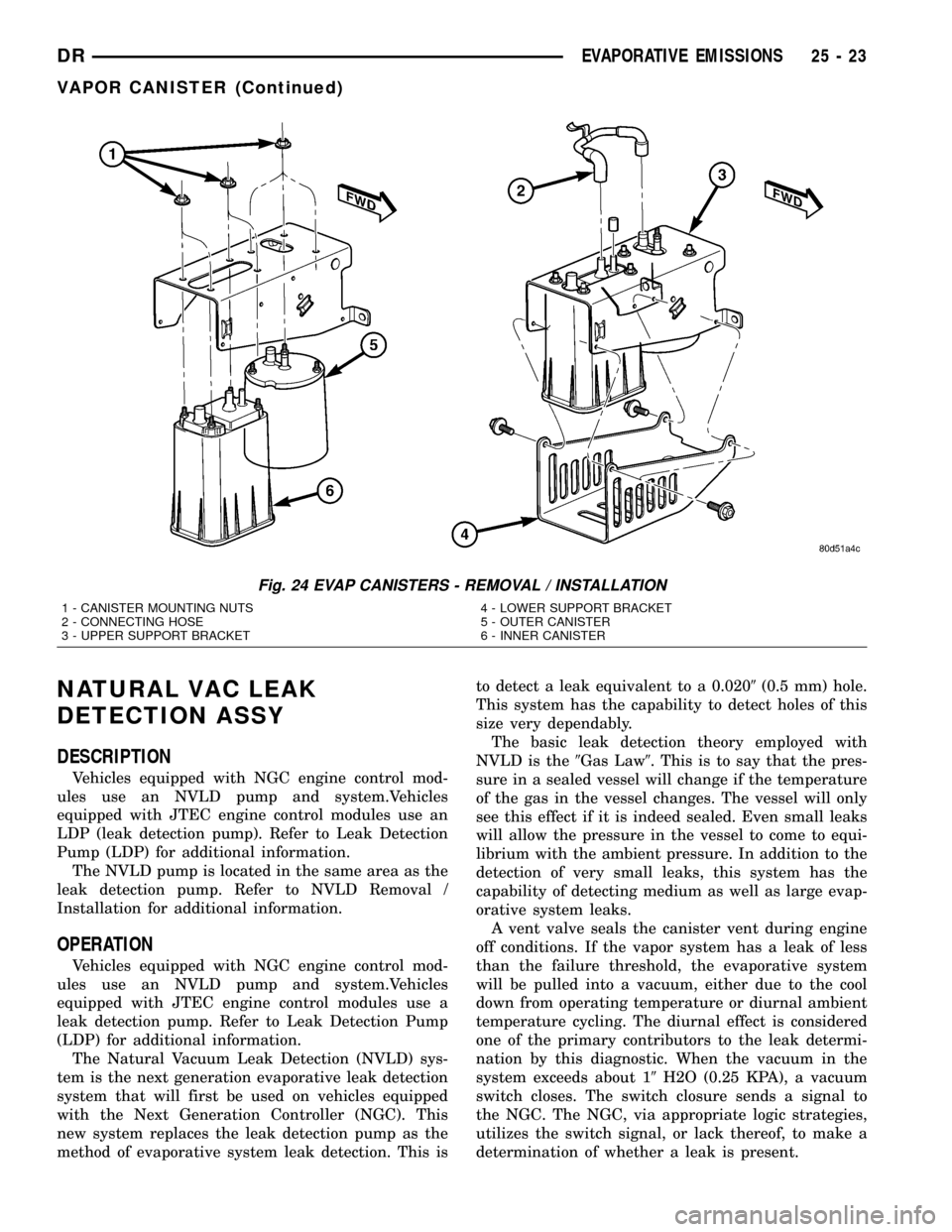
NATURAL VAC LEAK
DETECTION ASSY
DESCRIPTION
Vehicles equipped with NGC engine control mod-
ules use an NVLD pump and system.Vehicles
equipped with JTEC engine control modules use an
LDP (leak detection pump). Refer to Leak Detection
Pump (LDP) for additional information.
The NVLD pump is located in the same area as the
leak detection pump. Refer to NVLD Removal /
Installation for additional information.
OPERATION
Vehicles equipped with NGC engine control mod-
ules use an NVLD pump and system.Vehicles
equipped with JTEC engine control modules use a
leak detection pump. Refer to Leak Detection Pump
(LDP) for additional information.
The Natural Vacuum Leak Detection (NVLD) sys-
tem is the next generation evaporative leak detection
system that will first be used on vehicles equipped
with the Next Generation Controller (NGC). This
new system replaces the leak detection pump as the
method of evaporative system leak detection. This isto detect a leak equivalent to a 0.0209(0.5 mm) hole.
This system has the capability to detect holes of this
size very dependably.
The basic leak detection theory employed with
NVLD is the9Gas Law9. This is to say that the pres-
sure in a sealed vessel will change if the temperature
of the gas in the vessel changes. The vessel will only
see this effect if it is indeed sealed. Even small leaks
will allow the pressure in the vessel to come to equi-
librium with the ambient pressure. In addition to the
detection of very small leaks, this system has the
capability of detecting medium as well as large evap-
orative system leaks.
A vent valve seals the canister vent during engine
off conditions. If the vapor system has a leak of less
than the failure threshold, the evaporative system
will be pulled into a vacuum, either due to the cool
down from operating temperature or diurnal ambient
temperature cycling. The diurnal effect is considered
one of the primary contributors to the leak determi-
nation by this diagnostic. When the vacuum in the
system exceeds about 19H2O (0.25 KPA), a vacuum
switch closes. The switch closure sends a signal to
the NGC. The NGC, via appropriate logic strategies,
utilizes the switch signal, or lack thereof, to make a
determination of whether a leak is present.
Fig. 24 EVAP CANISTERS - REMOVAL / INSTALLATION
1 - CANISTER MOUNTING NUTS
2 - CONNECTING HOSE
3 - UPPER SUPPORT BRACKET4 - LOWER SUPPORT BRACKET
5 - OUTER CANISTER
6 - INNER CANISTER
DREVAPORATIVE EMISSIONS 25 - 23
VAPOR CANISTER (Continued)
Page 2585 of 2627
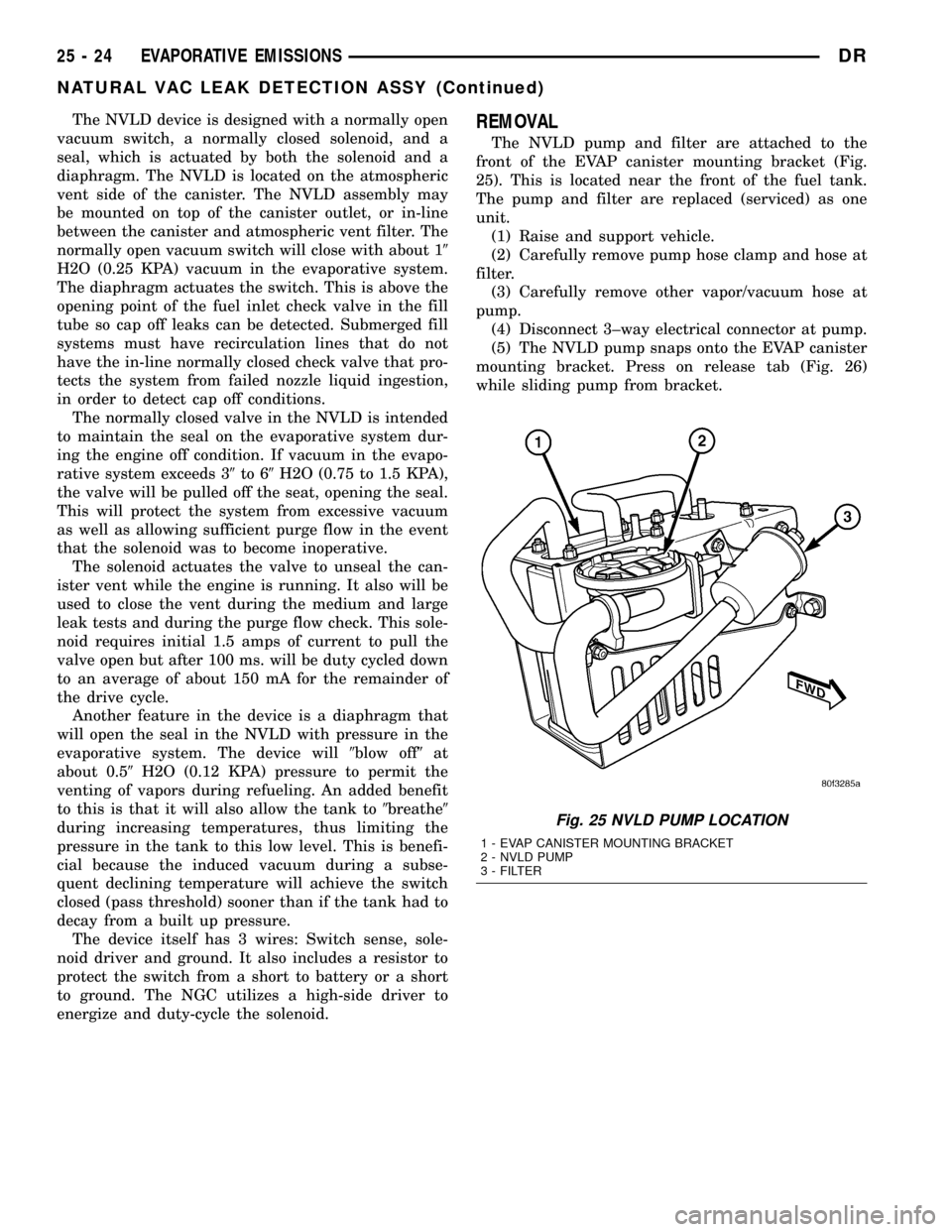
The NVLD device is designed with a normally open
vacuum switch, a normally closed solenoid, and a
seal, which is actuated by both the solenoid and a
diaphragm. The NVLD is located on the atmospheric
vent side of the canister. The NVLD assembly may
be mounted on top of the canister outlet, or in-line
between the canister and atmospheric vent filter. The
normally open vacuum switch will close with about 19
H2O (0.25 KPA) vacuum in the evaporative system.
The diaphragm actuates the switch. This is above the
opening point of the fuel inlet check valve in the fill
tube so cap off leaks can be detected. Submerged fill
systems must have recirculation lines that do not
have the in-line normally closed check valve that pro-
tects the system from failed nozzle liquid ingestion,
in order to detect cap off conditions.
The normally closed valve in the NVLD is intended
to maintain the seal on the evaporative system dur-
ing the engine off condition. If vacuum in the evapo-
rative system exceeds 39to 69H2O (0.75 to 1.5 KPA),
the valve will be pulled off the seat, opening the seal.
This will protect the system from excessive vacuum
as well as allowing sufficient purge flow in the event
that the solenoid was to become inoperative.
The solenoid actuates the valve to unseal the can-
ister vent while the engine is running. It also will be
used to close the vent during the medium and large
leak tests and during the purge flow check. This sole-
noid requires initial 1.5 amps of current to pull the
valve open but after 100 ms. will be duty cycled down
to an average of about 150 mA for the remainder of
the drive cycle.
Another feature in the device is a diaphragm that
will open the seal in the NVLD with pressure in the
evaporative system. The device will9blow off9at
about 0.59H2O (0.12 KPA) pressure to permit the
venting of vapors during refueling. An added benefit
to this is that it will also allow the tank to9breathe9
during increasing temperatures, thus limiting the
pressure in the tank to this low level. This is benefi-
cial because the induced vacuum during a subse-
quent declining temperature will achieve the switch
closed (pass threshold) sooner than if the tank had to
decay from a built up pressure.
The device itself has 3 wires: Switch sense, sole-
noid driver and ground. It also includes a resistor to
protect the switch from a short to battery or a short
to ground. The NGC utilizes a high-side driver to
energize and duty-cycle the solenoid.REMOVAL
The NVLD pump and filter are attached to the
front of the EVAP canister mounting bracket (Fig.
25). This is located near the front of the fuel tank.
The pump and filter are replaced (serviced) as one
unit.
(1) Raise and support vehicle.
(2) Carefully remove pump hose clamp and hose at
filter.
(3) Carefully remove other vapor/vacuum hose at
pump.
(4) Disconnect 3±way electrical connector at pump.
(5) The NVLD pump snaps onto the EVAP canister
mounting bracket. Press on release tab (Fig. 26)
while sliding pump from bracket.
Fig. 25 NVLD PUMP LOCATION
1 - EVAP CANISTER MOUNTING BRACKET
2 - NVLD PUMP
3 - FILTER
25 - 24 EVAPORATIVE EMISSIONSDR
NATURAL VAC LEAK DETECTION ASSY (Continued)
Page 2586 of 2627

INSTALLATION
(1) Install NVLD pump to EVAP canister mount-
ing bracket (snaps on).
(2) Install NVLD filter and bolt to EVAP canister
mounting bracket. Refer to Torque Specifications.
(3) Carefully install vapor/vacuum lines to NVLD
pump, and install hose to filter.The vapor/vacuum
lines and hoses must be firmly connected.
Check the vapor/vacuum lines at the NVLD
pump, filter and EVAP canister purge solenoid
for damage or leaks. If a leak is present, a Diag-
nostic Trouble Code (DTC) may be set.
(4) Connect 3±way electrical connector to pump.
Fig. 26 REMOVE / INSTALL NVLD PUMP
1 - NVLD PUMP
2 - RELEASE TAB
DREVAPORATIVE EMISSIONS 25 - 25
NATURAL VAC LEAK DETECTION ASSY (Continued)
Page 2587 of 2627
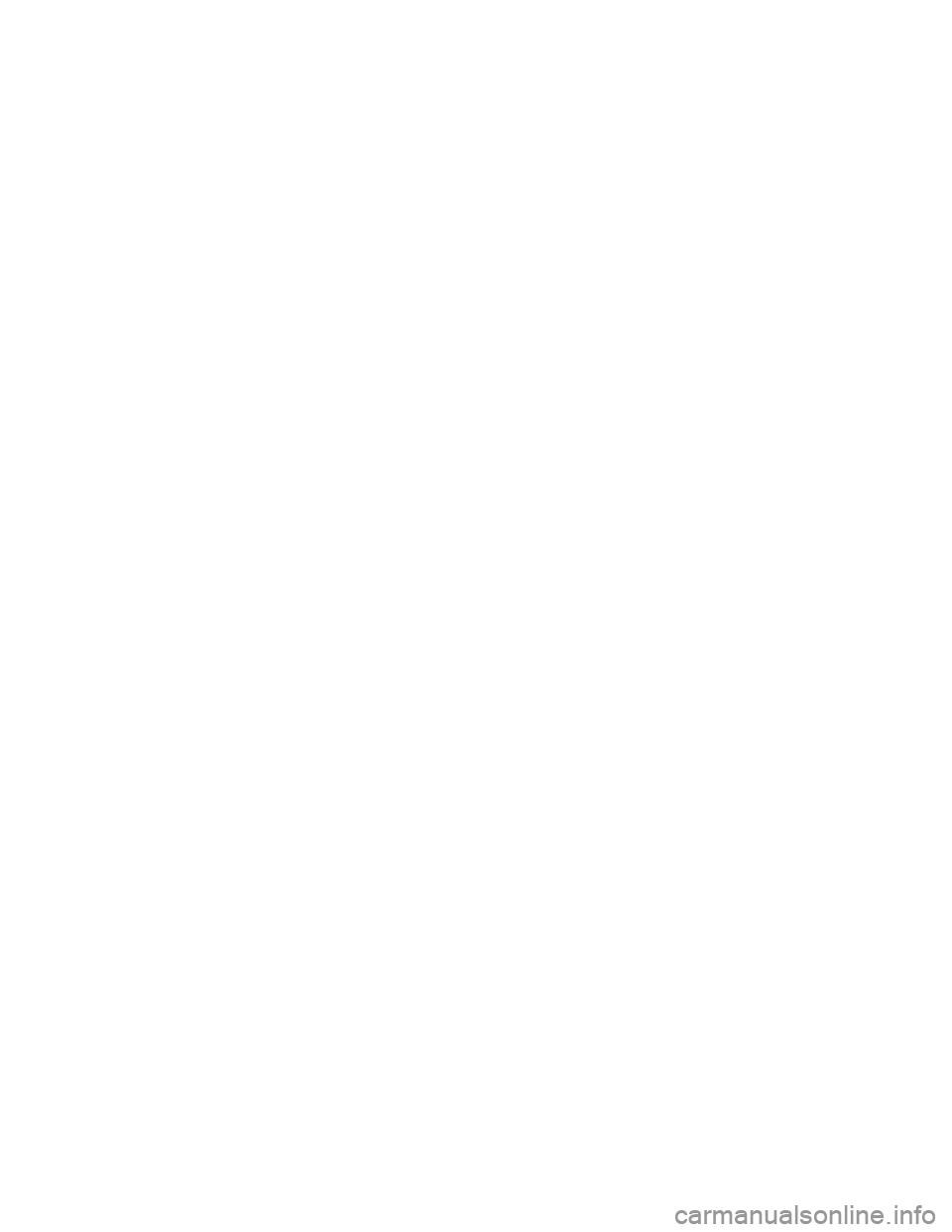
Page 2588 of 2627
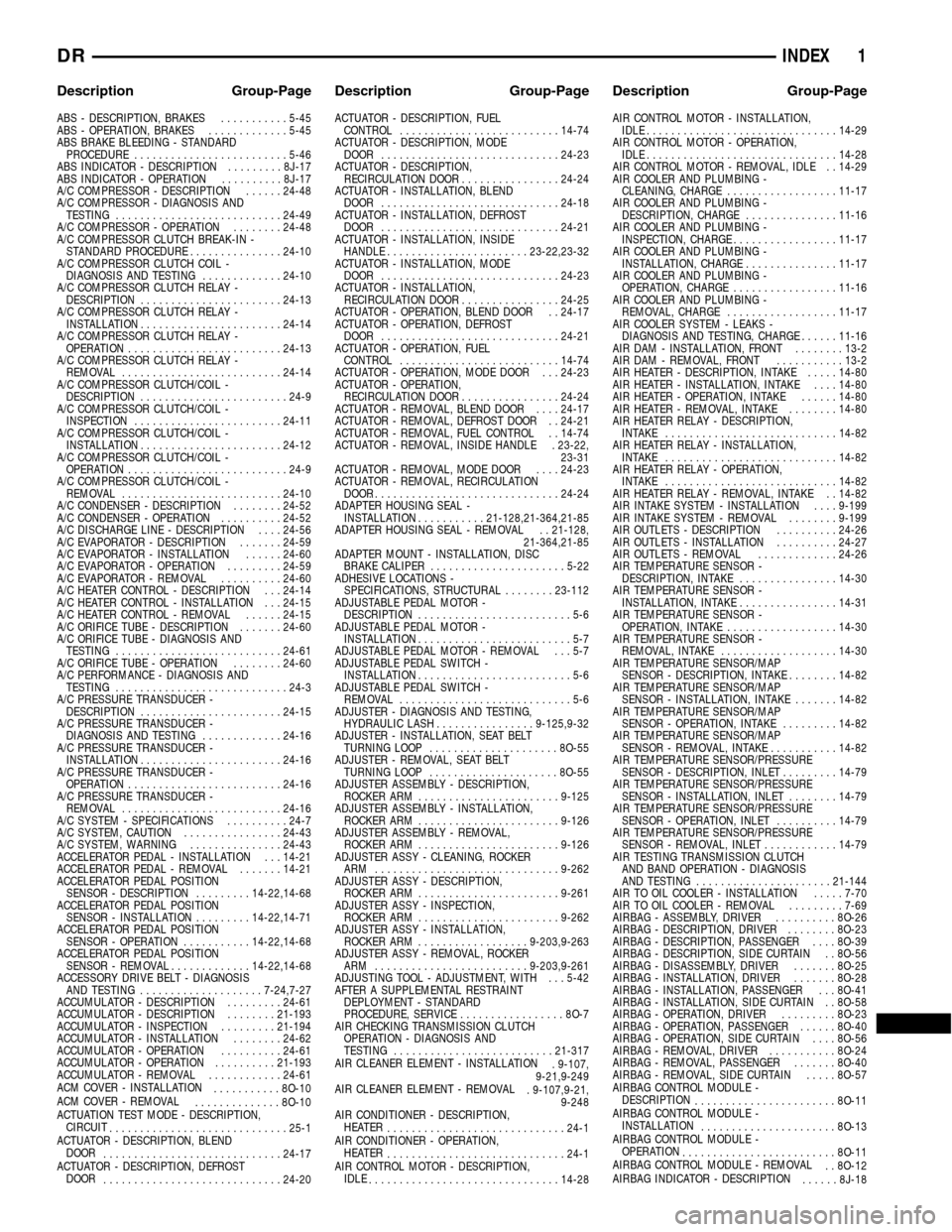
INDEX
ABS - DESCRIPTION, BRAKES...........5-45
ABS - OPERATION, BRAKES.............5-45
ABS BRAKE BLEEDING - STANDARD
PROCEDURE.........................5-46
ABS INDICATOR - DESCRIPTION.........8J-17
ABS INDICATOR - OPERATION..........8J-17
A/C COMPRESSOR - DESCRIPTION......24-48
A/C COMPRESSOR - DIAGNOSIS AND
TESTING...........................24-49
A/C COMPRESSOR - OPERATION........24-48
A/C COMPRESSOR CLUTCH BREAK-IN -
STANDARD PROCEDURE...............24-10
A/C COMPRESSOR CLUTCH COIL -
DIAGNOSIS AND TESTING.............24-10
A/C COMPRESSOR CLUTCH RELAY -
DESCRIPTION.......................24-13
A/C COMPRESSOR CLUTCH RELAY -
INSTALLATION.......................24-14
A/C COMPRESSOR CLUTCH RELAY -
OPERATION.........................24-13
A/C COMPRESSOR CLUTCH RELAY -
REMOVAL..........................24-14
A/C COMPRESSOR CLUTCH/COIL -
DESCRIPTION........................24-9
A/C COMPRESSOR CLUTCH/COIL -
INSPECTION........................24-11
A/C COMPRESSOR CLUTCH/COIL -
INSTALLATION.......................24-12
A/C COMPRESSOR CLUTCH/COIL -
OPERATION..........................24-9
A/C COMPRESSOR CLUTCH/COIL -
REMOVAL..........................24-10
A/C CONDENSER - DESCRIPTION........24-52
A/C CONDENSER - OPERATION..........24-52
A/C DISCHARGE LINE - DESCRIPTION....24-56
A/C EVAPORATOR - DESCRIPTION.......24-59
A/C EVAPORATOR - INSTALLATION......24-60
A/C EVAPORATOR - OPERATION.........24-59
A/C EVAPORATOR - REMOVAL..........24-60
A/C HEATER CONTROL - DESCRIPTION . . . 24-14
A/C HEATER CONTROL - INSTALLATION . . . 24-15
A/C HEATER CONTROL - REMOVAL......24-15
A/C ORIFICE TUBE - DESCRIPTION.......24-60
A/C ORIFICE TUBE - DIAGNOSIS AND
TESTING...........................24-61
A/C ORIFICE TUBE - OPERATION........24-60
A/C PERFORMANCE - DIAGNOSIS AND
TESTING............................24-3
A/C PRESSURE TRANSDUCER -
DESCRIPTION.......................24-15
A/C PRESSURE TRANSDUCER -
DIAGNOSIS AND TESTING.............24-16
A/C PRESSURE TRANSDUCER -
INSTALLATION.......................24-16
A/C PRESSURE TRANSDUCER -
OPERATION.........................24-16
A/C PRESSURE TRANSDUCER -
REMOVAL..........................24-16
A/C SYSTEM - SPECIFICATIONS..........24-7
A/C SYSTEM, CAUTION................24-43
A/C SYSTEM, WARNING...............24-43
ACCELERATOR PEDAL - INSTALLATION . . . 14-21
ACCELERATOR PEDAL - REMOVAL.......14-21
ACCELERATOR PEDAL POSITION
SENSOR - DESCRIPTION.........14-22,14-68
ACCELERATOR PEDAL POSITION
SENSOR - INSTALLATION.........14-22,14-71
ACCELERATOR PEDAL POSITION
SENSOR - OPERATION...........14-22,14-68
ACCELERATOR PEDAL POSITION
SENSOR - REMOVAL.............14-22,14-68
ACCESSORY DRIVE BELT - DIAGNOSIS
AND TESTING....................7-24,7-27
ACCUMULATOR - DESCRIPTION.........24-61
ACCUMULATOR - DESCRIPTION........21-193
ACCUMULATOR - INSPECTION.........21-194
ACCUMULATOR - INSTALLATION........24-62
ACCUMULATOR - OPERATION..........24-61
ACCUMULATOR - OPERATION..........21-193
ACCUMULATOR - REMOVAL............24-61
ACM COVER - INSTALLATION
...........8O-10
ACM COVER - REMOVAL
..............8O-10
ACTUATION TEST MODE - DESCRIPTION,
CIRCUIT
.............................25-1
ACTUATOR - DESCRIPTION, BLEND
DOOR
.............................24-17
ACTUATOR - DESCRIPTION, DEFROST
DOOR
.............................24-20ACTUATOR - DESCRIPTION, FUEL
CONTROL..........................14-74
ACTUATOR - DESCRIPTION, MODE
DOOR.............................24-23
ACTUATOR - DESCRIPTION,
RECIRCULATION DOOR................24-24
ACTUATOR - INSTALLATION, BLEND
DOOR.............................24-18
ACTUATOR - INSTALLATION, DEFROST
DOOR.............................24-21
ACTUATOR - INSTALLATION, INSIDE
HANDLE.......................23-22,23-32
ACTUATOR - INSTALLATION, MODE
DOOR.............................24-23
ACTUATOR - INSTALLATION,
RECIRCULATION DOOR................24-25
ACTUATOR - OPERATION, BLEND DOOR . . 24-17
ACTUATOR - OPERATION, DEFROST
DOOR.............................24-21
ACTUATOR - OPERATION, FUEL
CONTROL..........................14-74
ACTUATOR - OPERATION, MODE DOOR . . . 24-23
ACTUATOR - OPERATION,
RECIRCULATION DOOR................24-24
ACTUATOR - REMOVAL, BLEND DOOR....24-17
ACTUATOR - REMOVAL, DEFROST DOOR . . 24-21
ACTUATOR - REMOVAL, FUEL CONTROL . . 14-74
ACTUATOR - REMOVAL, INSIDE HANDLE . 23-22,
23-31
ACTUATOR - REMOVAL, MODE DOOR....24-23
ACTUATOR - REMOVAL, RECIRCULATION
DOOR...............................24-24
ADAPTER HOUSING SEAL -
INSTALLATION...........21-128,21-364,21-85
ADAPTER HOUSING SEAL - REMOVAL . . 21-128,
21-364,21-85
ADAPTER MOUNT - INSTALLATION, DISC
BRAKE CALIPER......................5-22
ADHESIVE LOCATIONS -
SPECIFICATIONS, STRUCTURAL........23-112
ADJUSTABLE PEDAL MOTOR -
DESCRIPTION.........................5-6
ADJUSTABLE PEDAL MOTOR -
INSTALLATION.........................5-7
ADJUSTABLE PEDAL MOTOR - REMOVAL . . . 5-7
ADJUSTABLE PEDAL SWITCH -
INSTALLATION.........................5-6
ADJUSTABLE PEDAL SWITCH -
REMOVAL............................5-6
ADJUSTER - DIAGNOSIS AND TESTING,
HYDRAULIC LASH................9-125,9-32
ADJUSTER - INSTALLATION, SEAT BELT
TURNING LOOP.....................8O-55
ADJUSTER - REMOVAL, SEAT BELT
TURNING LOOP.....................8O-55
ADJUSTER ASSEMBLY - DESCRIPTION,
ROCKER ARM.......................9-125
ADJUSTER ASSEMBLY - INSTALLATION,
ROCKER ARM.......................9-126
ADJUSTER ASSEMBLY - REMOVAL,
ROCKER ARM.......................9-126
ADJUSTER ASSY - CLEANING, ROCKER
ARM ..............................9-262
ADJUSTER ASSY - DESCRIPTION,
ROCKER ARM.......................9-261
ADJUSTER ASSY - INSPECTION,
ROCKER ARM.......................9-262
ADJUSTER ASSY - INSTALLATION,
ROCKER ARM..................9-203,9-263
ADJUSTER ASSY - REMOVAL, ROCKER
ARM .........................9-203,9-261
ADJUSTING TOOL - ADJUSTMENT, WITH . . . 5-42
AFTER A SUPPLEMENTAL RESTRAINT
DEPLOYMENT - STANDARD
PROCEDURE, SERVICE.................8O-7
AIR CHECKING TRANSMISSION CLUTCH
OPERATION - DIAGNOSIS AND
TESTING..........................21-317
AIR CLEANER ELEMENT - INSTALLATION
. 9-107,
9-21,9-249
AIR CLEANER ELEMENT - REMOVAL
. 9-107,9-21,
9-248
AIR CONDITIONER - DESCRIPTION,
HEATER
.............................24-1
AIR CONDITIONER - OPERATION,
HEATER
.............................24-1
AIR CONTROL MOTOR - DESCRIPTION,
IDLE
...............................14-28AIR CONTROL MOTOR - INSTALLATION,
IDLE...............................14-29
AIR CONTROL MOTOR - OPERATION,
IDLE...............................14-28
AIR CONTROL MOTOR - REMOVAL, IDLE . . 14-29
AIR COOLER AND PLUMBING -
CLEANING, CHARGE..................11-17
AIR COOLER AND PLUMBING -
DESCRIPTION, CHARGE...............11-16
AIR COOLER AND PLUMBING -
INSPECTION, CHARGE.................11-17
AIR COOLER AND PLUMBING -
INSTALLATION, CHARGE...............11-17
AIR COOLER AND PLUMBING -
OPERATION, CHARGE.................11-16
AIR COOLER AND PLUMBING -
REMOVAL, CHARGE..................11-17
AIR COOLER SYSTEM - LEAKS -
DIAGNOSIS AND TESTING, CHARGE......11-16
AIR DAM - INSTALLATION, FRONT........13-2
AIR DAM - REMOVAL, FRONT...........13-2
AIR HEATER - DESCRIPTION, INTAKE.....14-80
AIR HEATER - INSTALLATION, INTAKE....14-80
AIR HEATER - OPERATION, INTAKE......14-80
AIR HEATER - REMOVAL, INTAKE........14-80
AIR HEATER RELAY - DESCRIPTION,
INTAKE ............................14-82
AIR HEATER RELAY - INSTALLATION,
INTAKE ............................14-82
AIR HEATER RELAY - OPERATION,
INTAKE ............................14-82
AIR HEATER RELAY - REMOVAL, INTAKE . . 14-82
AIR INTAKE SYSTEM - INSTALLATION....9-199
AIR INTAKE SYSTEM - REMOVAL........9-199
AIR OUTLETS - DESCRIPTION..........24-26
AIR OUTLETS - INSTALLATION..........24-27
AIR OUTLETS - REMOVAL.............24-26
AIR TEMPERATURE SENSOR -
DESCRIPTION, INTAKE................14-30
AIR TEMPERATURE SENSOR -
INSTALLATION, INTAKE................14-31
AIR TEMPERATURE SENSOR -
OPERATION, INTAKE..................14-30
AIR TEMPERATURE SENSOR -
REMOVAL, INTAKE...................14-30
AIR TEMPERATURE SENSOR/MAP
SENSOR - DESCRIPTION, INTAKE........14-82
AIR TEMPERATURE SENSOR/MAP
SENSOR - INSTALLATION, INTAKE.......14-82
AIR TEMPERATURE SENSOR/MAP
SENSOR - OPERATION, INTAKE.........14-82
AIR TEMPERATURE SENSOR/MAP
SENSOR - REMOVAL, INTAKE...........14-82
AIR TEMPERATURE SENSOR/PRESSURE
SENSOR - DESCRIPTION, INLET.........14-79
AIR TEMPERATURE SENSOR/PRESSURE
SENSOR - INSTALLATION, INLET........14-79
AIR TEMPERATURE SENSOR/PRESSURE
SENSOR - OPERATION, INLET..........14-79
AIR TEMPERATURE SENSOR/PRESSURE
SENSOR - REMOVAL, INLET............14-79
AIR TESTING TRANSMISSION CLUTCH
AND BAND OPERATION - DIAGNOSIS
AND TESTING......................21-144
AIR TO OIL COOLER - INSTALLATION.....7-70
AIR TO OIL COOLER - REMOVAL.........7-69
AIRBAG - ASSEMBLY, DRIVER..........8O-26
AIRBAG - DESCRIPTION, DRIVER........8O-23
AIRBAG - DESCRIPTION, PASSENGER....8O-39
AIRBAG - DESCRIPTION, SIDE CURTAIN . . 8O-56
AIRBAG - DISASSEMBLY, DRIVER.......8O-25
AIRBAG - INSTALLATION, DRIVER.......8O-28
AIRBAG - INSTALLATION, PASSENGER . . . 8O-41
AIRBAG - INSTALLATION, SIDE CURTAIN . . 8O-58
AIRBAG - OPERATION, DRIVER.........8O-23
AIRBAG - OPERATION, PASSENGER......8O-40
AIRBAG - OPERATION, SIDE CURTAIN....8O-56
AIRBAG - REMOVAL, DRIVER...........8O-24
AIRBAG - REMOVAL, PASSENGER.......8O-40
AIRBAG - REMOVAL, SIDE CURTAIN.....8O-57
AIRBAG CONTROL MODULE -
DESCRIPTION
.......................8O-11
AIRBAG CONTROL MODULE -
INSTALLATION
......................8O-13
AIRBAG CONTROL MODULE -
OPERATION
.........................8O-11
AIRBAG CONTROL MODULE - REMOVAL
. . 8O-12
AIRBAG INDICATOR - DESCRIPTION
......8J-18
DRINDEX 1
Description Group-Page Description Group-Page Description Group-Page
Page 2589 of 2627
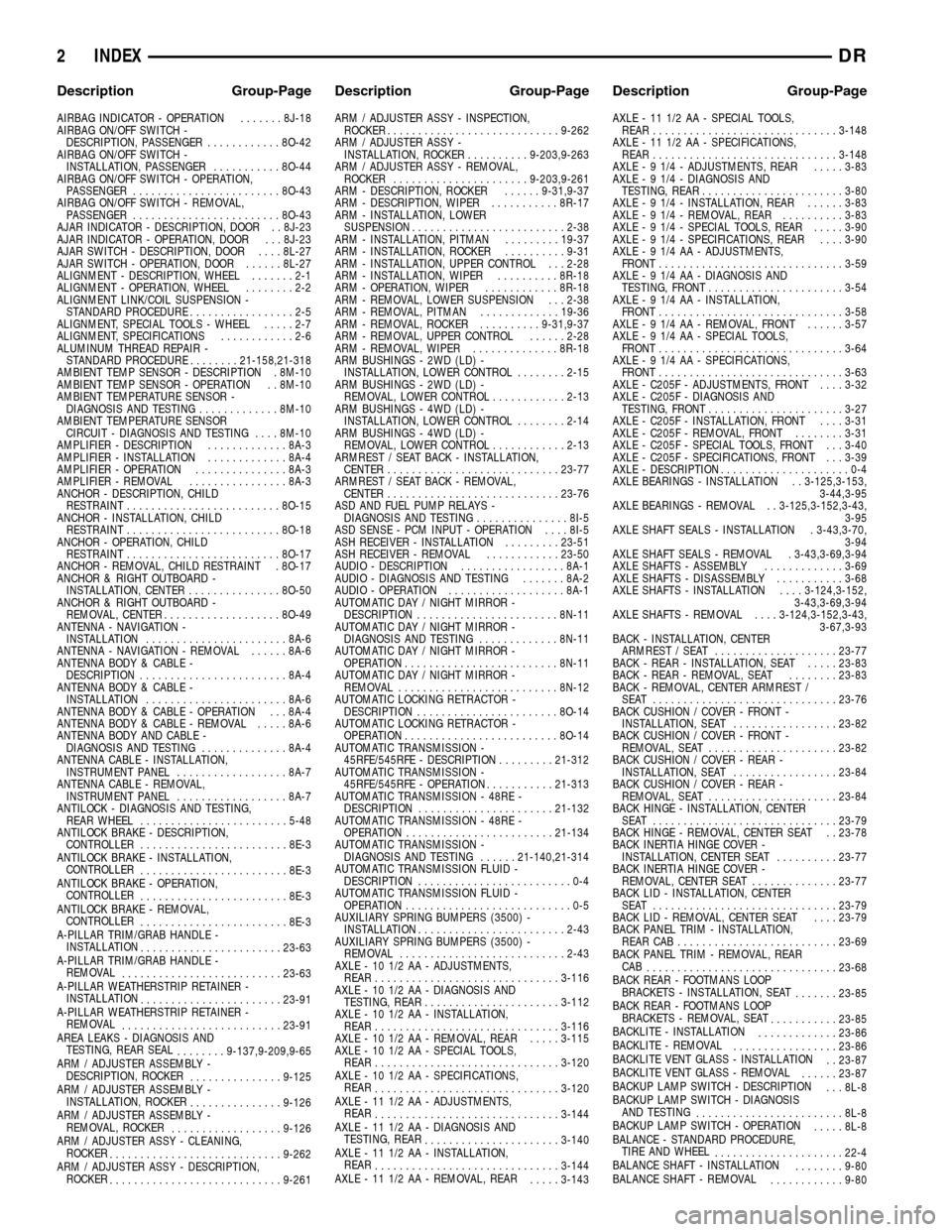
AIRBAG INDICATOR - OPERATION.......8J-18
AIRBAG ON/OFF SWITCH -
DESCRIPTION, PASSENGER............8O-42
AIRBAG ON/OFF SWITCH -
INSTALLATION, PASSENGER...........8O-44
AIRBAG ON/OFF SWITCH - OPERATION,
PASSENGER........................8O-43
AIRBAG ON/OFF SWITCH - REMOVAL,
PASSENGER........................8O-43
AJAR INDICATOR - DESCRIPTION, DOOR . . 8J-23
AJAR INDICATOR - OPERATION, DOOR . . . 8J-23
AJAR SWITCH - DESCRIPTION, DOOR....8L-27
AJAR SWITCH - OPERATION, DOOR......8L-27
ALIGNMENT - DESCRIPTION, WHEEL.......2-1
ALIGNMENT - OPERATION, WHEEL........2-2
ALIGNMENT LINK/COIL SUSPENSION -
STANDARD PROCEDURE.................2-5
ALIGNMENT, SPECIAL TOOLS - WHEEL.....2-7
ALIGNMENT, SPECIFICATIONS............2-6
ALUMINUM THREAD REPAIR -
STANDARD PROCEDURE........21-158,21-318
AMBIENT TEMP SENSOR - DESCRIPTION . 8M-10
AMBIENT TEMP SENSOR - OPERATION . . 8M-10
AMBIENT TEMPERATURE SENSOR -
DIAGNOSIS AND TESTING.............8M-10
AMBIENT TEMPERATURE SENSOR
CIRCUIT - DIAGNOSIS AND TESTING....8M-10
AMPLIFIER - DESCRIPTION.............8A-3
AMPLIFIER - INSTALLATION.............8A-4
AMPLIFIER - OPERATION...............8A-3
AMPLIFIER - REMOVAL................8A-3
ANCHOR - DESCRIPTION, CHILD
RESTRAINT.........................8O-15
ANCHOR - INSTALLATION, CHILD
RESTRAINT.........................8O-18
ANCHOR - OPERATION, CHILD
RESTRAINT.........................8O-17
ANCHOR - REMOVAL, CHILD RESTRAINT . 8O-17
ANCHOR & RIGHT OUTBOARD -
INSTALLATION, CENTER...............8O-50
ANCHOR & RIGHT OUTBOARD -
REMOVAL, CENTER...................8O-49
ANTENNA - NAVIGATION -
INSTALLATION.......................8A-6
ANTENNA - NAVIGATION - REMOVAL......8A-6
ANTENNA BODY & CABLE -
DESCRIPTION........................8A-4
ANTENNA BODY & CABLE -
INSTALLATION.......................8A-6
ANTENNA BODY & CABLE - OPERATION . . . 8A-4
ANTENNA BODY & CABLE - REMOVAL.....8A-6
ANTENNA BODY AND CABLE -
DIAGNOSIS AND TESTING..............8A-4
ANTENNA CABLE - INSTALLATION,
INSTRUMENT PANEL..................8A-7
ANTENNA CABLE - REMOVAL,
INSTRUMENT PANEL..................8A-7
ANTILOCK - DIAGNOSIS AND TESTING,
REAR WHEEL........................5-48
ANTILOCK BRAKE - DESCRIPTION,
CONTROLLER........................8E-3
ANTILOCK BRAKE - INSTALLATION,
CONTROLLER
........................8E-3
ANTILOCK BRAKE - OPERATION,
CONTROLLER
........................8E-3
ANTILOCK BRAKE - REMOVAL,
CONTROLLER
........................8E-3
A-PILLAR TRIM/GRAB HANDLE -
INSTALLATION
.......................23-63
A-PILLAR TRIM/GRAB HANDLE -
REMOVAL
..........................23-63
A-PILLAR WEATHERSTRIP RETAINER -
INSTALLATION
.......................23-91
A-PILLAR WEATHERSTRIP RETAINER -
REMOVAL
..........................23-91
AREA LEAKS - DIAGNOSIS AND
TESTING, REAR SEAL
........9-137,9-209,9-65
ARM / ADJUSTER ASSEMBLY -
DESCRIPTION, ROCKER
...............9-125
ARM / ADJUSTER ASSEMBLY -
INSTALLATION, ROCKER
...............9-126
ARM / ADJUSTER ASSEMBLY -
REMOVAL, ROCKER
..................9-126
ARM / ADJUSTER ASSY - CLEANING,
ROCKER
............................9-262
ARM / ADJUSTER ASSY - DESCRIPTION,
ROCKER
............................9-261ARM / ADJUSTER ASSY - INSPECTION,
ROCKER............................9-262
ARM / ADJUSTER ASSY -
INSTALLATION, ROCKER..........9-203,9-263
ARM / ADJUSTER ASSY - REMOVAL,
ROCKER......................9-203,9-261
ARM - DESCRIPTION, ROCKER......9-31,9-37
ARM - DESCRIPTION, WIPER...........8R-17
ARM - INSTALLATION, LOWER
SUSPENSION.........................2-38
ARM - INSTALLATION, PITMAN.........19-37
ARM - INSTALLATION, ROCKER..........9-31
ARM - INSTALLATION, UPPER CONTROL . . . 2-28
ARM - INSTALLATION, WIPER..........8R-18
ARM - OPERATION, WIPER............8R-18
ARM - REMOVAL, LOWER SUSPENSION . . . 2-38
ARM - REMOVAL, PITMAN.............19-36
ARM - REMOVAL, ROCKER..........9-31,9-37
ARM - REMOVAL, UPPER CONTROL......2-28
ARM - REMOVAL, WIPER..............8R-18
ARM BUSHINGS - 2WD (LD) -
INSTALLATION, LOWER CONTROL........2-15
ARM BUSHINGS - 2WD (LD) -
REMOVAL, LOWER CONTROL............2-13
ARM BUSHINGS - 4WD (LD) -
INSTALLATION, LOWER CONTROL........2-14
ARM BUSHINGS - 4WD (LD) -
REMOVAL, LOWER CONTROL............2-13
ARMREST / SEAT BACK - INSTALLATION,
CENTER.............................23-77
ARMREST / SEAT BACK - REMOVAL,
CENTER............................23-76
ASD AND FUEL PUMP RELAYS -
DIAGNOSIS AND TESTING...............8I-5
ASD SENSE - PCM INPUT - OPERATION....8I-5
ASH RECEIVER - INSTALLATION.........23-51
ASH RECEIVER - REMOVAL............23-50
AUDIO - DESCRIPTION.................8A-1
AUDIO - DIAGNOSIS AND TESTING.......8A-2
AUDIO - OPERATION...................8A-1
AUTOMATIC DAY / NIGHT MIRROR -
DESCRIPTION.......................8N-11
AUTOMATIC DAY / NIGHT MIRROR -
DIAGNOSIS AND TESTING.............8N-11
AUTOMATIC DAY / NIGHT MIRROR -
OPERATION.........................8N-11
AUTOMATIC DAY / NIGHT MIRROR -
REMOVAL..........................8N-12
AUTOMATIC LOCKING RETRACTOR -
DESCRIPTION.......................8O-14
AUTOMATIC LOCKING RETRACTOR -
OPERATION.........................8O-14
AUTOMATIC TRANSMISSION -
45RFE/545RFE - DESCRIPTION.........21-312
AUTOMATIC TRANSMISSION -
45RFE/545RFE - OPERATION...........21-313
AUTOMATIC TRANSMISSION - 48RE -
DESCRIPTION......................21-132
AUTOMATIC TRANSMISSION - 48RE -
OPERATION........................21-134
AUTOMATIC TRANSMISSION -
DIAGNOSIS AND TESTING......21-140,21-314
AUTOMATIC TRANSMISSION FLUID -
DESCRIPTION.........................0-4
AUTOMATIC TRANSMISSION FLUID -
OPERATION...........................0-5
AUXILIARY SPRING BUMPERS (3500) -
INSTALLATION........................2-43
AUXILIARY SPRING BUMPERS (3500) -
REMOVAL...........................2-43
AXLE - 10 1/2 AA - ADJUSTMENTS,
REAR..............................3-116
AXLE - 10 1/2 AA - DIAGNOSIS AND
TESTING, REAR......................3-112
AXLE - 10 1/2 AA - INSTALLATION,
REAR..............................3-116
AXLE - 10 1/2 AA - REMOVAL, REAR.....3-115
AXLE - 10 1/2 AA - SPECIAL TOOLS,
REAR..............................3-120
AXLE - 10 1/2 AA - SPECIFICATIONS,
REAR
..............................3-120
AXLE - 11 1/2 AA - ADJUSTMENTS,
REAR
..............................3-144
AXLE - 11 1/2 AA - DIAGNOSIS AND
TESTING, REAR
......................3-140
AXLE - 11 1/2 AA - INSTALLATION,
REAR
..............................3-144
AXLE - 11 1/2 AA - REMOVAL, REAR
.....3-143AXLE - 11 1/2 AA - SPECIAL TOOLS,
REAR..............................3-148
AXLE - 11 1/2 AA - SPECIFICATIONS,
REAR..............................3-148
AXLE - 9 1/4 - ADJUSTMENTS, REAR.....3-83
AXLE - 9 1/4 - DIAGNOSIS AND
TESTING, REAR.......................3-80
AXLE - 9 1/4 - INSTALLATION, REAR......3-83
AXLE - 9 1/4 - REMOVAL, REAR..........3-83
AXLE - 9 1/4 - SPECIAL TOOLS, REAR.....3-90
AXLE - 9 1/4 - SPECIFICATIONS, REAR....3-90
AXLE - 9 1/4 AA - ADJUSTMENTS,
FRONT..............................3-59
AXLE - 9 1/4 AA - DIAGNOSIS AND
TESTING, FRONT......................3-54
AXLE - 9 1/4 AA - INSTALLATION,
FRONT..............................3-58
AXLE - 9 1/4 AA - REMOVAL, FRONT......3-57
AXLE - 9 1/4 AA - SPECIAL TOOLS,
FRONT..............................3-64
AXLE - 9 1/4 AA - SPECIFICATIONS,
FRONT..............................3-63
AXLE - C205F - ADJUSTMENTS, FRONT....3-32
AXLE - C205F - DIAGNOSIS AND
TESTING, FRONT......................3-27
AXLE - C205F - INSTALLATION, FRONT....3-31
AXLE - C205F - REMOVAL, FRONT........3-31
AXLE - C205F - SPECIAL TOOLS, FRONT . . . 3-40
AXLE - C205F - SPECIFICATIONS, FRONT . . . 3-39
AXLE - DESCRIPTION.....................0-4
AXLE BEARINGS - INSTALLATION . . 3-125,3-153,
3-44,3-95
AXLE BEARINGS - REMOVAL . . 3-125,3-152,3-43,
3-95
AXLE SHAFT SEALS - INSTALLATION . 3-43,3-70,
3-94
AXLE SHAFT SEALS - REMOVAL . 3-43,3-69,3-94
AXLE SHAFTS - ASSEMBLY.............3-69
AXLE SHAFTS - DISASSEMBLY...........3-68
AXLE SHAFTS - INSTALLATION....3-124,3-152,
3-43,3-69,3-94
AXLE SHAFTS - REMOVAL....3-124,3-152,3-43,
3-67,3-93
BACK - INSTALLATION, CENTER
ARMREST / SEAT....................23-77
BACK - REAR - INSTALLATION, SEAT.....23-83
BACK - REAR - REMOVAL, SEAT........23-83
BACK - REMOVAL, CENTER ARMREST /
SEAT ..............................23-76
BACK CUSHION / COVER - FRONT -
INSTALLATION, SEAT.................23-82
BACK CUSHION / COVER - FRONT -
REMOVAL, SEAT.....................23-82
BACK CUSHION / COVER - REAR -
INSTALLATION, SEAT.................23-84
BACK CUSHION / COVER - REAR -
REMOVAL, SEAT.....................23-84
BACK HINGE - INSTALLATION, CENTER
SEAT ..............................23-79
BACK HINGE - REMOVAL, CENTER SEAT . . 23-78
BACK INERTIA HINGE COVER -
INSTALLATION, CENTER SEAT..........23-77
BACK INERTIA HINGE COVER -
REMOVAL, CENTER SEAT..............23-77
BACK LID - INSTALLATION, CENTER
SEAT ..............................23-79
BACK LID - REMOVAL, CENTER SEAT....23-79
BACK PANEL TRIM - INSTALLATION,
REAR CAB..........................23-69
BACK PANEL TRIM - REMOVAL, REAR
CAB
...............................23-68
BACK REAR - FOOTMANS LOOP
BRACKETS - INSTALLATION, SEAT
.......23-85
BACK REAR - FOOTMANS LOOP
BRACKETS - REMOVAL, SEAT
...........23-85
BACKLITE - INSTALLATION
.............23-86
BACKLITE - REMOVAL
.................23-86
BACKLITE VENT GLASS - INSTALLATION
. . 23-87
BACKLITE VENT GLASS - REMOVAL
......23-87
BACKUP LAMP SWITCH - DESCRIPTION
. . . 8L-8
BACKUP LAMP SWITCH - DIAGNOSIS
AND TESTING
........................8L-8
BACKUP LAMP SWITCH - OPERATION
.....8L-8
BALANCE - STANDARD PROCEDURE,
TIRE AND WHEEL
.....................22-4
BALANCE SHAFT - INSTALLATION
........9-80
BALANCE SHAFT - REMOVAL
............9-80
2 INDEXDR
Description Group-Page Description Group-Page Description Group-Page
Page 2590 of 2627
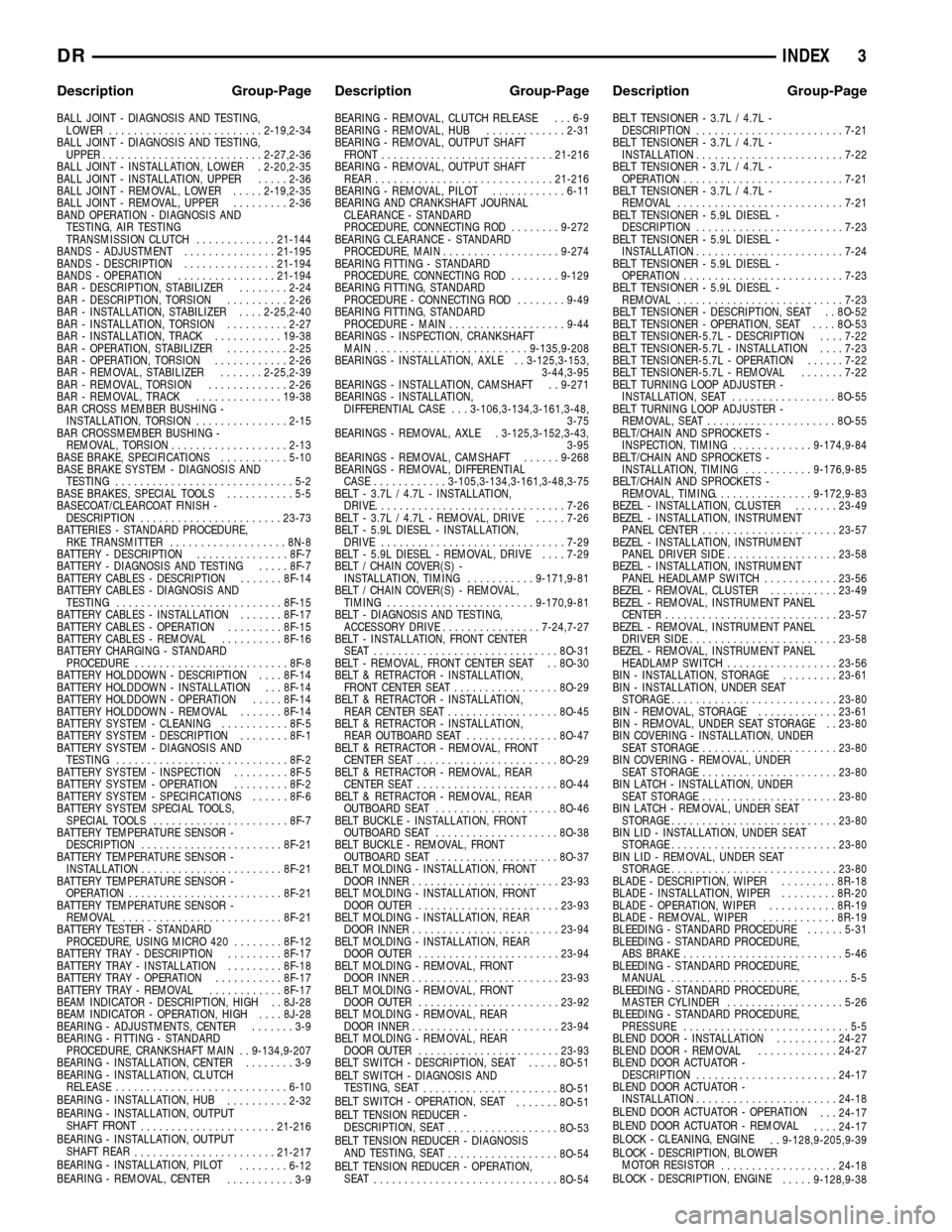
BALL JOINT - DIAGNOSIS AND TESTING,
LOWER.........................2-19,2-34
BALL JOINT - DIAGNOSIS AND TESTING,
UPPER..........................2-27,2-36
BALL JOINT - INSTALLATION, LOWER . 2-20,2-35
BALL JOINT - INSTALLATION, UPPER.....2-36
BALL JOINT - REMOVAL, LOWER.....2-19,2-35
BALL JOINT - REMOVAL, UPPER.........2-36
BAND OPERATION - DIAGNOSIS AND
TESTING, AIR TESTING
TRANSMISSION CLUTCH.............21-144
BANDS - ADJUSTMENT...............21-195
BANDS - DESCRIPTION...............21-194
BANDS - OPERATION................21-194
BAR - DESCRIPTION, STABILIZER........2-24
BAR - DESCRIPTION, TORSION..........2-26
BAR - INSTALLATION, STABILIZER....2-25,2-40
BAR - INSTALLATION, TORSION..........2-27
BAR - INSTALLATION, TRACK...........19-38
BAR - OPERATION, STABILIZER..........2-25
BAR - OPERATION, TORSION............2-26
BAR - REMOVAL, STABILIZER.......2-25,2-39
BAR - REMOVAL, TORSION.............2-26
BAR - REMOVAL, TRACK..............19-38
BAR CROSS MEMBER BUSHING -
INSTALLATION, TORSION...............2-15
BAR CROSSMEMBER BUSHING -
REMOVAL, TORSION...................2-13
BASE BRAKE, SPECIFICATIONS...........5-10
BASE BRAKE SYSTEM - DIAGNOSIS AND
TESTING.............................5-2
BASE BRAKES, SPECIAL TOOLS...........5-5
BASECOAT/CLEARCOAT FINISH -
DESCRIPTION.......................23-73
BATTERIES - STANDARD PROCEDURE,
RKE TRANSMITTER...................8N-8
BATTERY - DESCRIPTION...............8F-7
BATTERY - DIAGNOSIS AND TESTING.....8F-7
BATTERY CABLES - DESCRIPTION.......8F-14
BATTERY CABLES - DIAGNOSIS AND
TESTING...........................8F-15
BATTERY CABLES - INSTALLATION.......8F-17
BATTERY CABLES - OPERATION.........8F-15
BATTERY CABLES - REMOVAL..........8F-16
BATTERY CHARGING - STANDARD
PROCEDURE.........................8F-8
BATTERY HOLDDOWN - DESCRIPTION....8F-14
BATTERY HOLDDOWN - INSTALLATION . . . 8F-14
BATTERY HOLDDOWN - OPERATION.....8F-14
BATTERY HOLDDOWN - REMOVAL.......8F-14
BATTERY SYSTEM - CLEANING...........8F-5
BATTERY SYSTEM - DESCRIPTION........8F-1
BATTERY SYSTEM - DIAGNOSIS AND
TESTING............................8F-2
BATTERY SYSTEM - INSPECTION.........8F-5
BATTERY SYSTEM - OPERATION.........8F-2
BATTERY SYSTEM - SPECIFICATIONS......8F-6
BATTERY SYSTEM SPECIAL TOOLS,
SPECIAL TOOLS......................8F-7
BATTERY TEMPERATURE SENSOR -
DESCRIPTION.......................8F-21
BATTERY TEMPERATURE SENSOR -
INSTALLATION.......................8F-21
BATTERY TEMPERATURE SENSOR -
OPERATION.........................8F-21
BATTERY TEMPERATURE SENSOR -
REMOVAL..........................8F-21
BATTERY TESTER - STANDARD
PROCEDURE, USING MICRO 420........8F-12
BATTERY TRAY - DESCRIPTION.........8F-17
BATTERY TRAY - INSTALLATION.........8F-18
BATTERY TRAY - OPERATION...........8F-17
BATTERY TRAY - REMOVAL............8F-17
BEAM INDICATOR - DESCRIPTION, HIGH . . 8J-28
BEAM INDICATOR - OPERATION, HIGH....8J-28
BEARING - ADJUSTMENTS, CENTER.......3-9
BEARING - FITTING - STANDARD
PROCEDURE, CRANKSHAFT MAIN . . 9-134,9-207
BEARING - INSTALLATION, CENTER........3-9
BEARING - INSTALLATION, CLUTCH
RELEASE............................6-10
BEARING - INSTALLATION, HUB
..........2-32
BEARING - INSTALLATION, OUTPUT
SHAFT FRONT
......................21-216
BEARING - INSTALLATION, OUTPUT
SHAFT REAR
.......................21-217
BEARING - INSTALLATION, PILOT
........6-12
BEARING - REMOVAL, CENTER
...........3-9BEARING - REMOVAL, CLUTCH RELEASE . . . 6-9
BEARING - REMOVAL, HUB.............2-31
BEARING - REMOVAL, OUTPUT SHAFT
FRONT............................21-216
BEARING - REMOVAL, OUTPUT SHAFT
REAR.............................21-216
BEARING - REMOVAL, PILOT............6-11
BEARING AND CRANKSHAFT JOURNAL
CLEARANCE - STANDARD
PROCEDURE, CONNECTING ROD........9-272
BEARING CLEARANCE - STANDARD
PROCEDURE, MAIN...................9-274
BEARING FITTING - STANDARD
PROCEDURE, CONNECTING ROD........9-129
BEARING FITTING, STANDARD
PROCEDURE - CONNECTING ROD........9-49
BEARING FITTING, STANDARD
PROCEDURE - MAIN...................9-44
BEARINGS - INSPECTION, CRANKSHAFT
MAIN.........................9-135,9-208
BEARINGS - INSTALLATION, AXLE . . 3-125,3-153,
3-44,3-95
BEARINGS - INSTALLATION, CAMSHAFT . . 9-271
BEARINGS - INSTALLATION,
DIFFERENTIAL CASE . . . 3-106,3-134,3-161,3-48,
3-75
BEARINGS - REMOVAL, AXLE . 3-125,3-152,3-43,
3-95
BEARINGS - REMOVAL, CAMSHAFT......9-268
BEARINGS - REMOVAL, DIFFERENTIAL
CASE............3-105,3-134,3-161,3-48,3-75
BELT - 3.7L / 4.7L - INSTALLATION,
DRIVE................................7-26
BELT - 3.7L / 4.7L - REMOVAL, DRIVE.....7-26
BELT - 5.9L DIESEL - INSTALLATION,
DRIVE..............................7-29
BELT - 5.9L DIESEL - REMOVAL, DRIVE....7-29
BELT / CHAIN COVER(S) -
INSTALLATION, TIMING...........9-171,9-81
BELT / CHAIN COVER(S) - REMOVAL,
TIMING........................9-170,9-81
BELT - DIAGNOSIS AND TESTING,
ACCESSORY DRIVE................7-24,7-27
BELT - INSTALLATION, FRONT CENTER
SEAT ..............................8O-31
BELT - REMOVAL, FRONT CENTER SEAT . . 8O-30
BELT & RETRACTOR - INSTALLATION,
FRONT CENTER SEAT.................8O-29
BELT & RETRACTOR - INSTALLATION,
REAR CENTER SEAT..................8O-45
BELT & RETRACTOR - INSTALLATION,
REAR OUTBOARD SEAT...............8O-47
BELT & RETRACTOR - REMOVAL, FRONT
CENTER SEAT.......................8O-29
BELT & RETRACTOR - REMOVAL, REAR
CENTER SEAT.......................8O-44
BELT & RETRACTOR - REMOVAL, REAR
OUTBOARD SEAT....................8O-46
BELT BUCKLE - INSTALLATION, FRONT
OUTBOARD SEAT....................8O-38
BELT BUCKLE - REMOVAL, FRONT
OUTBOARD SEAT....................8O-37
BELT MOLDING - INSTALLATION, FRONT
DOOR INNER........................23-93
BELT MOLDING - INSTALLATION, FRONT
DOOR OUTER.......................23-93
BELT MOLDING - INSTALLATION, REAR
DOOR INNER........................23-94
BELT MOLDING - INSTALLATION, REAR
DOOR OUTER.......................23-94
BELT MOLDING - REMOVAL, FRONT
DOOR INNER........................23-93
BELT MOLDING - REMOVAL, FRONT
DOOR OUTER.......................23-92
BELT MOLDING - REMOVAL, REAR
DOOR INNER........................23-94
BELT MOLDING - REMOVAL, REAR
DOOR OUTER.......................23-93
BELT SWITCH - DESCRIPTION, SEAT.....8O-51
BELT SWITCH - DIAGNOSIS AND
TESTING, SEAT
......................8O-51
BELT SWITCH - OPERATION, SEAT
.......8O-51
BELT TENSION REDUCER -
DESCRIPTION, SEAT
..................8O-53
BELT TENSION REDUCER - DIAGNOSIS
AND TESTING, SEAT
..................8O-54
BELT TENSION REDUCER - OPERATION,
SEAT
..............................8O-54BELT TENSIONER - 3.7L / 4.7L -
DESCRIPTION........................7-21
BELT TENSIONER - 3.7L / 4.7L -
INSTALLATION........................7-22
BELT TENSIONER - 3.7L / 4.7L -
OPERATION..........................7-21
BELT TENSIONER - 3.7L / 4.7L -
REMOVAL...........................7-21
BELT TENSIONER - 5.9L DIESEL -
DESCRIPTION........................7-23
BELT TENSIONER - 5.9L DIESEL -
INSTALLATION........................7-24
BELT TENSIONER - 5.9L DIESEL -
OPERATION..........................7-23
BELT TENSIONER - 5.9L DIESEL -
REMOVAL...........................7-23
BELT TENSIONER - DESCRIPTION, SEAT . . 8O-52
BELT TENSIONER - OPERATION, SEAT....8O-53
BELT TENSIONER-5.7L - DESCRIPTION....7-22
BELT TENSIONER-5.7L - INSTALLATION....7-23
BELT TENSIONER-5.7L - OPERATION......7-22
BELT TENSIONER-5.7L - REMOVAL.......7-22
BELT TURNING LOOP ADJUSTER -
INSTALLATION, SEAT.................8O-55
BELT TURNING LOOP ADJUSTER -
REMOVAL, SEAT.....................8O-55
BELT/CHAIN AND SPROCKETS -
INSPECTION, TIMING.............9-174,9-84
BELT/CHAIN AND SPROCKETS -
INSTALLATION, TIMING...........9-176,9-85
BELT/CHAIN AND SPROCKETS -
REMOVAL, TIMING.................9-172,9-83
BEZEL - INSTALLATION, CLUSTER.......23-49
BEZEL - INSTALLATION, INSTRUMENT
PANEL CENTER......................23-57
BEZEL - INSTALLATION, INSTRUMENT
PANEL DRIVER SIDE..................23-58
BEZEL - INSTALLATION, INSTRUMENT
PANEL HEADLAMP SWITCH............23-56
BEZEL - REMOVAL, CLUSTER...........23-49
BEZEL - REMOVAL, INSTRUMENT PANEL
CENTER............................23-57
BEZEL - REMOVAL, INSTRUMENT PANEL
DRIVER SIDE........................23-58
BEZEL - REMOVAL, INSTRUMENT PANEL
HEADLAMP SWITCH..................23-56
BIN - INSTALLATION, STORAGE.........23-61
BIN - INSTALLATION, UNDER SEAT
STORAGE...........................23-80
BIN - REMOVAL, STORAGE.............23-61
BIN - REMOVAL, UNDER SEAT STORAGE . . 23-80
BIN COVERING - INSTALLATION, UNDER
SEAT STORAGE......................23-80
BIN COVERING - REMOVAL, UNDER
SEAT STORAGE......................23-80
BIN LATCH - INSTALLATION, UNDER
SEAT STORAGE......................23-80
BIN LATCH - REMOVAL, UNDER SEAT
STORAGE...........................23-80
BIN LID - INSTALLATION, UNDER SEAT
STORAGE...........................23-80
BIN LID - REMOVAL, UNDER SEAT
STORAGE...........................23-80
BLADE - DESCRIPTION, WIPER.........8R-18
BLADE - INSTALLATION, WIPER.........8R-20
BLADE - OPERATION, WIPER...........8R-19
BLADE - REMOVAL, WIPER............8R-19
BLEEDING - STANDARD PROCEDURE......5-31
BLEEDING - STANDARD PROCEDURE,
ABS BRAKE..........................5-46
BLEEDING - STANDARD PROCEDURE,
MANUAL.............................5-5
BLEEDING - STANDARD PROCEDURE,
MASTER CYLINDER...................5-26
BLEEDING - STANDARD PROCEDURE,
PRESSURE...........................5-5
BLEND DOOR - INSTALLATION..........24-27
BLEND DOOR - REMOVAL.............24-27
BLEND DOOR ACTUATOR -
DESCRIPTION.......................24-17
BLEND DOOR ACTUATOR -
INSTALLATION.......................24-18
BLEND DOOR ACTUATOR - OPERATION
. . . 24-17
BLEND DOOR ACTUATOR - REMOVAL
....24-17
BLOCK - CLEANING, ENGINE
. . 9-128,9-205,9-39
BLOCK - DESCRIPTION, BLOWER
MOTOR RESISTOR
...................24-18
BLOCK - DESCRIPTION, ENGINE
.....9-128,9-38
DRINDEX 3
Description Group-Page Description Group-Page Description Group-Page