side mirror DODGE RAM 1500 1998 2.G Owner's Manual
[x] Cancel search | Manufacturer: DODGE, Model Year: 1998, Model line: RAM 1500, Model: DODGE RAM 1500 1998 2.GPages: 2627
Page 2338 of 2627
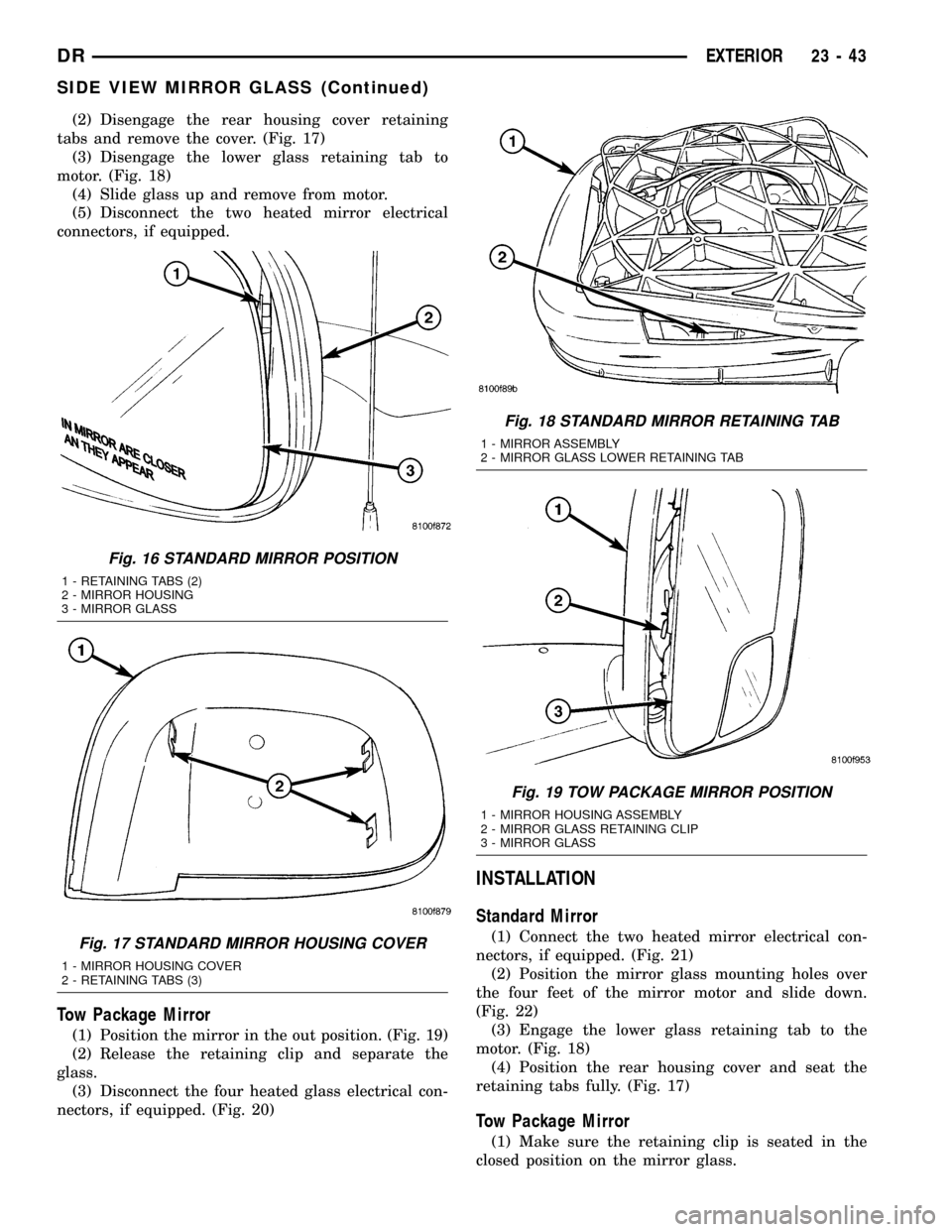
(2) Disengage the rear housing cover retaining
tabs and remove the cover. (Fig. 17)
(3) Disengage the lower glass retaining tab to
motor. (Fig. 18)
(4) Slide glass up and remove from motor.
(5) Disconnect the two heated mirror electrical
connectors, if equipped.
Tow Package Mirror
(1) Position the mirror in the out position. (Fig. 19)
(2) Release the retaining clip and separate the
glass.
(3) Disconnect the four heated glass electrical con-
nectors, if equipped. (Fig. 20)
INSTALLATION
Standard Mirror
(1) Connect the two heated mirror electrical con-
nectors, if equipped. (Fig. 21)
(2) Position the mirror glass mounting holes over
the four feet of the mirror motor and slide down.
(Fig. 22)
(3) Engage the lower glass retaining tab to the
motor. (Fig. 18)
(4) Position the rear housing cover and seat the
retaining tabs fully. (Fig. 17)
Tow Package Mirror
(1) Make sure the retaining clip is seated in the
closed position on the mirror glass.
Fig. 16 STANDARD MIRROR POSITION
1 - RETAINING TABS (2)
2 - MIRROR HOUSING
3 - MIRROR GLASS
Fig. 17 STANDARD MIRROR HOUSING COVER
1 - MIRROR HOUSING COVER
2 - RETAINING TABS (3)
Fig. 18 STANDARD MIRROR RETAINING TAB
1 - MIRROR ASSEMBLY
2 - MIRROR GLASS LOWER RETAINING TAB
Fig. 19 TOW PACKAGE MIRROR POSITION
1 - MIRROR HOUSING ASSEMBLY
2 - MIRROR GLASS RETAINING CLIP
3 - MIRROR GLASS
DREXTERIOR 23 - 43
SIDE VIEW MIRROR GLASS (Continued)
Page 2339 of 2627
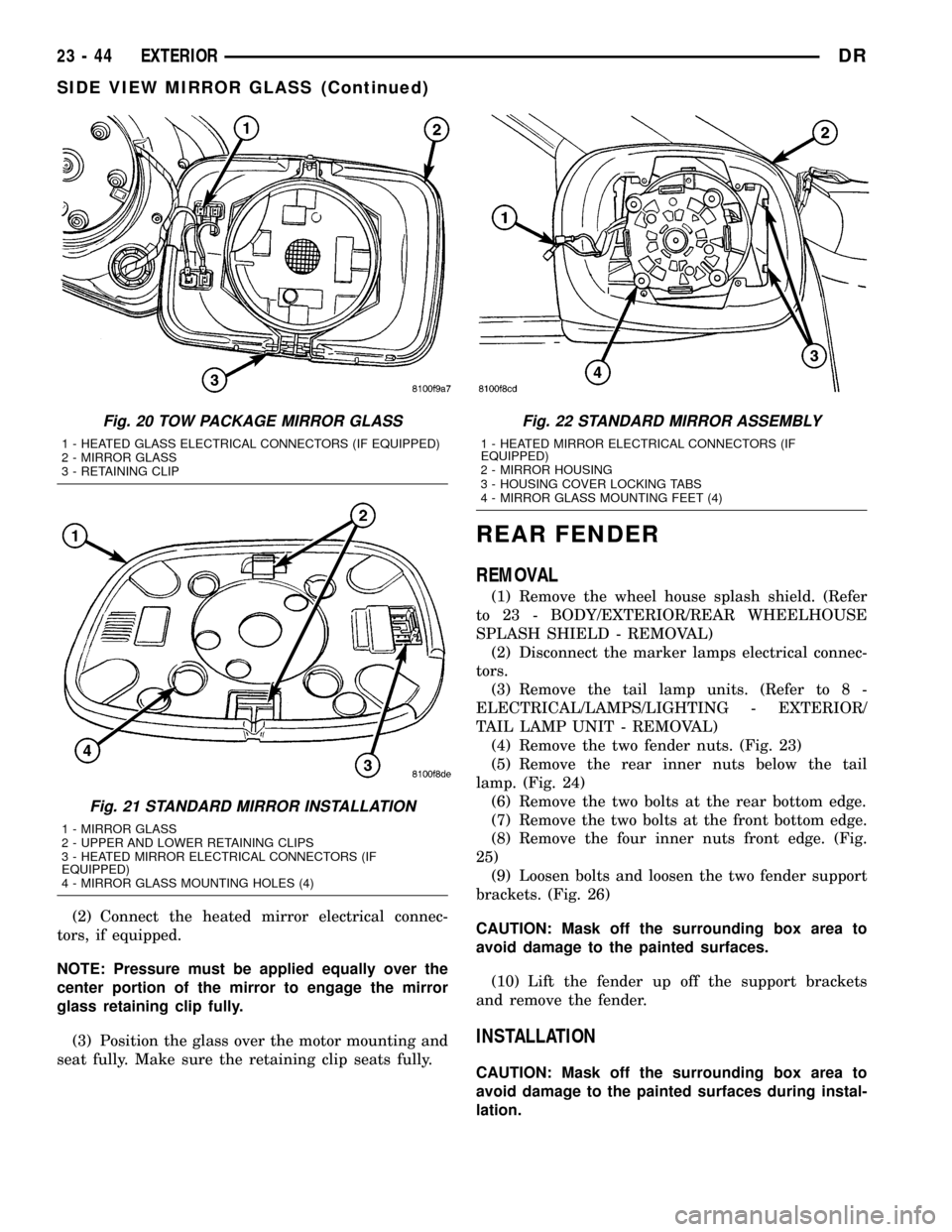
(2) Connect the heated mirror electrical connec-
tors, if equipped.
NOTE: Pressure must be applied equally over the
center portion of the mirror to engage the mirror
glass retaining clip fully.
(3) Position the glass over the motor mounting and
seat fully. Make sure the retaining clip seats fully.
REAR FENDER
REMOVAL
(1) Remove the wheel house splash shield. (Refer
to 23 - BODY/EXTERIOR/REAR WHEELHOUSE
SPLASH SHIELD - REMOVAL)
(2) Disconnect the marker lamps electrical connec-
tors.
(3) Remove the tail lamp units. (Refer to 8 -
ELECTRICAL/LAMPS/LIGHTING - EXTERIOR/
TAIL LAMP UNIT - REMOVAL)
(4) Remove the two fender nuts. (Fig. 23)
(5) Remove the rear inner nuts below the tail
lamp. (Fig. 24)
(6) Remove the two bolts at the rear bottom edge.
(7) Remove the two bolts at the front bottom edge.
(8) Remove the four inner nuts front edge. (Fig.
25)
(9) Loosen bolts and loosen the two fender support
brackets. (Fig. 26)
CAUTION: Mask off the surrounding box area to
avoid damage to the painted surfaces.
(10) Lift the fender up off the support brackets
and remove the fender.
INSTALLATION
CAUTION: Mask off the surrounding box area to
avoid damage to the painted surfaces during instal-
lation.
Fig. 20 TOW PACKAGE MIRROR GLASS
1 - HEATED GLASS ELECTRICAL CONNECTORS (IF EQUIPPED)
2 - MIRROR GLASS
3 - RETAINING CLIP
Fig. 21 STANDARD MIRROR INSTALLATION
1 - MIRROR GLASS
2 - UPPER AND LOWER RETAINING CLIPS
3 - HEATED MIRROR ELECTRICAL CONNECTORS (IF
EQUIPPED)
4 - MIRROR GLASS MOUNTING HOLES (4)
Fig. 22 STANDARD MIRROR ASSEMBLY
1 - HEATED MIRROR ELECTRICAL CONNECTORS (IF
EQUIPPED)
2 - MIRROR HOUSING
3 - HOUSING COVER LOCKING TABS
4 - MIRROR GLASS MOUNTING FEET (4)
23 - 44 EXTERIORDR
SIDE VIEW MIRROR GLASS (Continued)
Page 2365 of 2627
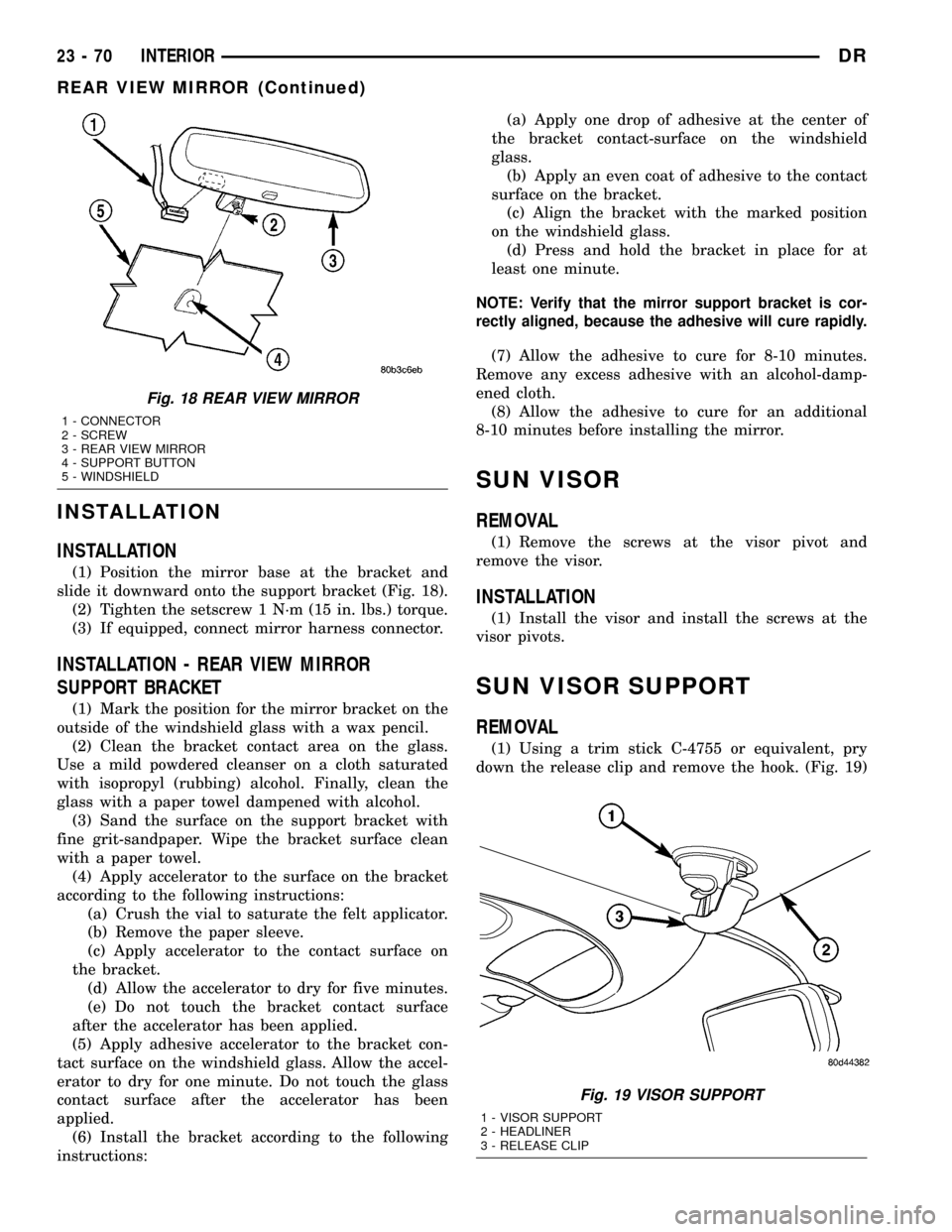
INSTALLATION
INSTALLATION
(1) Position the mirror base at the bracket and
slide it downward onto the support bracket (Fig. 18).
(2) Tighten the setscrew 1 N´m (15 in. lbs.) torque.
(3) If equipped, connect mirror harness connector.
INSTALLATION - REAR VIEW MIRROR
SUPPORT BRACKET
(1) Mark the position for the mirror bracket on the
outside of the windshield glass with a wax pencil.
(2) Clean the bracket contact area on the glass.
Use a mild powdered cleanser on a cloth saturated
with isopropyl (rubbing) alcohol. Finally, clean the
glass with a paper towel dampened with alcohol.
(3) Sand the surface on the support bracket with
fine grit-sandpaper. Wipe the bracket surface clean
with a paper towel.
(4) Apply accelerator to the surface on the bracket
according to the following instructions:
(a) Crush the vial to saturate the felt applicator.
(b) Remove the paper sleeve.
(c) Apply accelerator to the contact surface on
the bracket.
(d) Allow the accelerator to dry for five minutes.
(e) Do not touch the bracket contact surface
after the accelerator has been applied.
(5) Apply adhesive accelerator to the bracket con-
tact surface on the windshield glass. Allow the accel-
erator to dry for one minute. Do not touch the glass
contact surface after the accelerator has been
applied.
(6) Install the bracket according to the following
instructions:(a) Apply one drop of adhesive at the center of
the bracket contact-surface on the windshield
glass.
(b) Apply an even coat of adhesive to the contact
surface on the bracket.
(c) Align the bracket with the marked position
on the windshield glass.
(d) Press and hold the bracket in place for at
least one minute.
NOTE: Verify that the mirror support bracket is cor-
rectly aligned, because the adhesive will cure rapidly.
(7) Allow the adhesive to cure for 8-10 minutes.
Remove any excess adhesive with an alcohol-damp-
ened cloth.
(8) Allow the adhesive to cure for an additional
8-10 minutes before installing the mirror.
SUN VISOR
REMOVAL
(1) Remove the screws at the visor pivot and
remove the visor.
INSTALLATION
(1) Install the visor and install the screws at the
visor pivots.
SUN VISOR SUPPORT
REMOVAL
(1) Using a trim stick C-4755 or equivalent, pry
down the release clip and remove the hook. (Fig. 19)
Fig. 18 REAR VIEW MIRROR
1 - CONNECTOR
2 - SCREW
3 - REAR VIEW MIRROR
4 - SUPPORT BUTTON
5 - WINDSHIELD
Fig. 19 VISOR SUPPORT
1 - VISOR SUPPORT
2 - HEADLINER
3 - RELEASE CLIP
23 - 70 INTERIORDR
REAR VIEW MIRROR (Continued)
Page 2383 of 2627
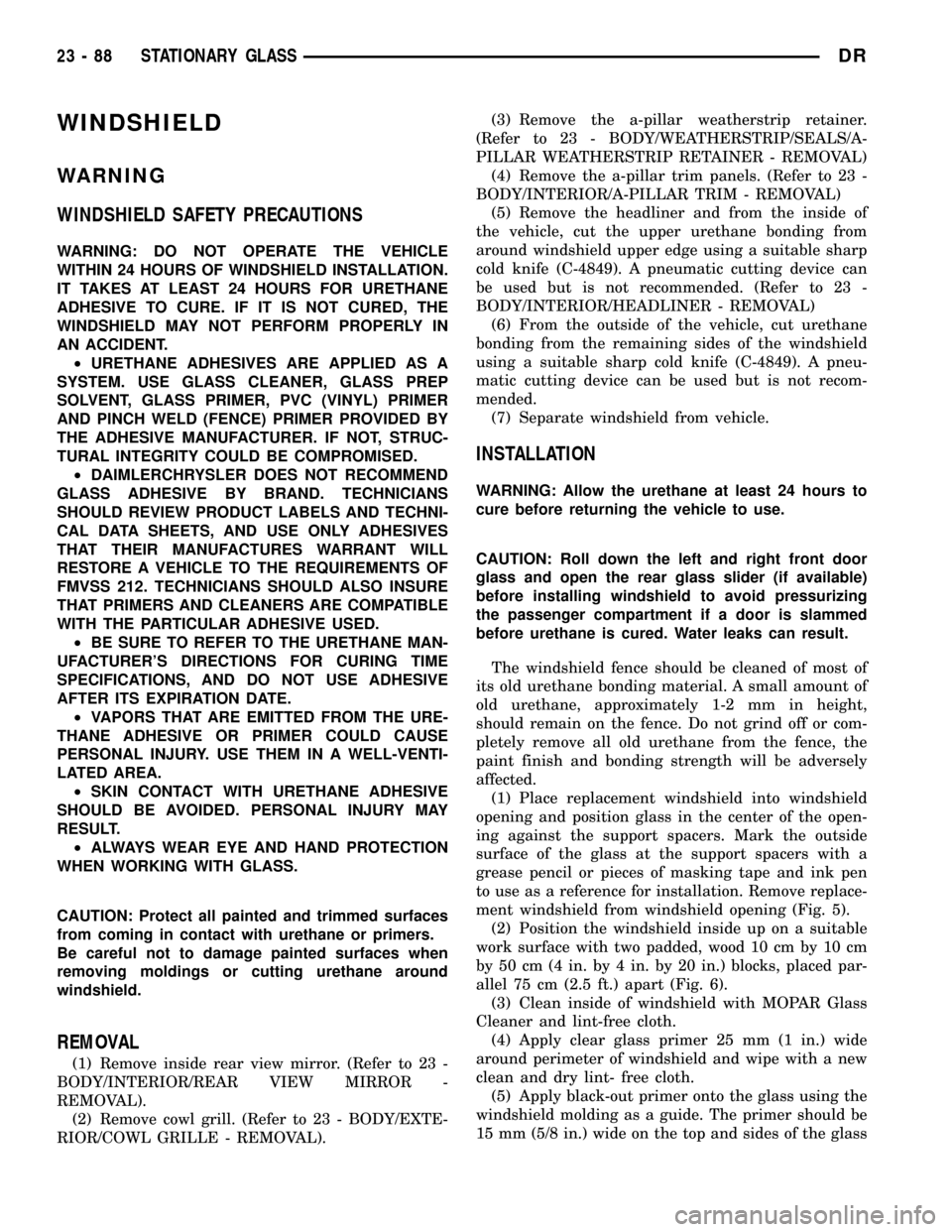
WINDSHIELD
WARNING
WINDSHIELD SAFETY PRECAUTIONS
WARNING: DO NOT OPERATE THE VEHICLE
WITHIN 24 HOURS OF WINDSHIELD INSTALLATION.
IT TAKES AT LEAST 24 HOURS FOR URETHANE
ADHESIVE TO CURE. IF IT IS NOT CURED, THE
WINDSHIELD MAY NOT PERFORM PROPERLY IN
AN ACCIDENT.
²URETHANE ADHESIVES ARE APPLIED AS A
SYSTEM. USE GLASS CLEANER, GLASS PREP
SOLVENT, GLASS PRIMER, PVC (VINYL) PRIMER
AND PINCH WELD (FENCE) PRIMER PROVIDED BY
THE ADHESIVE MANUFACTURER. IF NOT, STRUC-
TURAL INTEGRITY COULD BE COMPROMISED.
²DAIMLERCHRYSLER DOES NOT RECOMMEND
GLASS ADHESIVE BY BRAND. TECHNICIANS
SHOULD REVIEW PRODUCT LABELS AND TECHNI-
CAL DATA SHEETS, AND USE ONLY ADHESIVES
THAT THEIR MANUFACTURES WARRANT WILL
RESTORE A VEHICLE TO THE REQUIREMENTS OF
FMVSS 212. TECHNICIANS SHOULD ALSO INSURE
THAT PRIMERS AND CLEANERS ARE COMPATIBLE
WITH THE PARTICULAR ADHESIVE USED.
²BE SURE TO REFER TO THE URETHANE MAN-
UFACTURER'S DIRECTIONS FOR CURING TIME
SPECIFICATIONS, AND DO NOT USE ADHESIVE
AFTER ITS EXPIRATION DATE.
²VAPORS THAT ARE EMITTED FROM THE URE-
THANE ADHESIVE OR PRIMER COULD CAUSE
PERSONAL INJURY. USE THEM IN A WELL-VENTI-
LATED AREA.
²SKIN CONTACT WITH URETHANE ADHESIVE
SHOULD BE AVOIDED. PERSONAL INJURY MAY
RESULT.
²ALWAYS WEAR EYE AND HAND PROTECTION
WHEN WORKING WITH GLASS.
CAUTION: Protect all painted and trimmed surfaces
from coming in contact with urethane or primers.
Be careful not to damage painted surfaces when
removing moldings or cutting urethane around
windshield.
REMOVAL
(1) Remove inside rear view mirror. (Refer to 23 -
BODY/INTERIOR/REAR VIEW MIRROR -
REMOVAL).
(2) Remove cowl grill. (Refer to 23 - BODY/EXTE-
RIOR/COWL GRILLE - REMOVAL).(3) Remove the a-pillar weatherstrip retainer.
(Refer to 23 - BODY/WEATHERSTRIP/SEALS/A-
PILLAR WEATHERSTRIP RETAINER - REMOVAL)
(4) Remove the a-pillar trim panels. (Refer to 23 -
BODY/INTERIOR/A-PILLAR TRIM - REMOVAL)
(5) Remove the headliner and from the inside of
the vehicle, cut the upper urethane bonding from
around windshield upper edge using a suitable sharp
cold knife (C-4849). A pneumatic cutting device can
be used but is not recommended. (Refer to 23 -
BODY/INTERIOR/HEADLINER - REMOVAL)
(6) From the outside of the vehicle, cut urethane
bonding from the remaining sides of the windshield
using a suitable sharp cold knife (C-4849). A pneu-
matic cutting device can be used but is not recom-
mended.
(7) Separate windshield from vehicle.
INSTALLATION
WARNING: Allow the urethane at least 24 hours to
cure before returning the vehicle to use.
CAUTION: Roll down the left and right front door
glass and open the rear glass slider (if available)
before installing windshield to avoid pressurizing
the passenger compartment if a door is slammed
before urethane is cured. Water leaks can result.
The windshield fence should be cleaned of most of
its old urethane bonding material. A small amount of
old urethane, approximately 1-2 mm in height,
should remain on the fence. Do not grind off or com-
pletely remove all old urethane from the fence, the
paint finish and bonding strength will be adversely
affected.
(1) Place replacement windshield into windshield
opening and position glass in the center of the open-
ing against the support spacers. Mark the outside
surface of the glass at the support spacers with a
grease pencil or pieces of masking tape and ink pen
to use as a reference for installation. Remove replace-
ment windshield from windshield opening (Fig. 5).
(2) Position the windshield inside up on a suitable
work surface with two padded, wood 10 cm by 10 cm
by 50 cm (4 in. by 4 in. by 20 in.) blocks, placed par-
allel 75 cm (2.5 ft.) apart (Fig. 6).
(3) Clean inside of windshield with MOPAR Glass
Cleaner and lint-free cloth.
(4) Apply clear glass primer 25 mm (1 in.) wide
around perimeter of windshield and wipe with a new
clean and dry lint- free cloth.
(5) Apply black-out primer onto the glass using the
windshield molding as a guide. The primer should be
15 mm (5/8 in.) wide on the top and sides of the glass
23 - 88 STATIONARY GLASSDR
Page 2384 of 2627
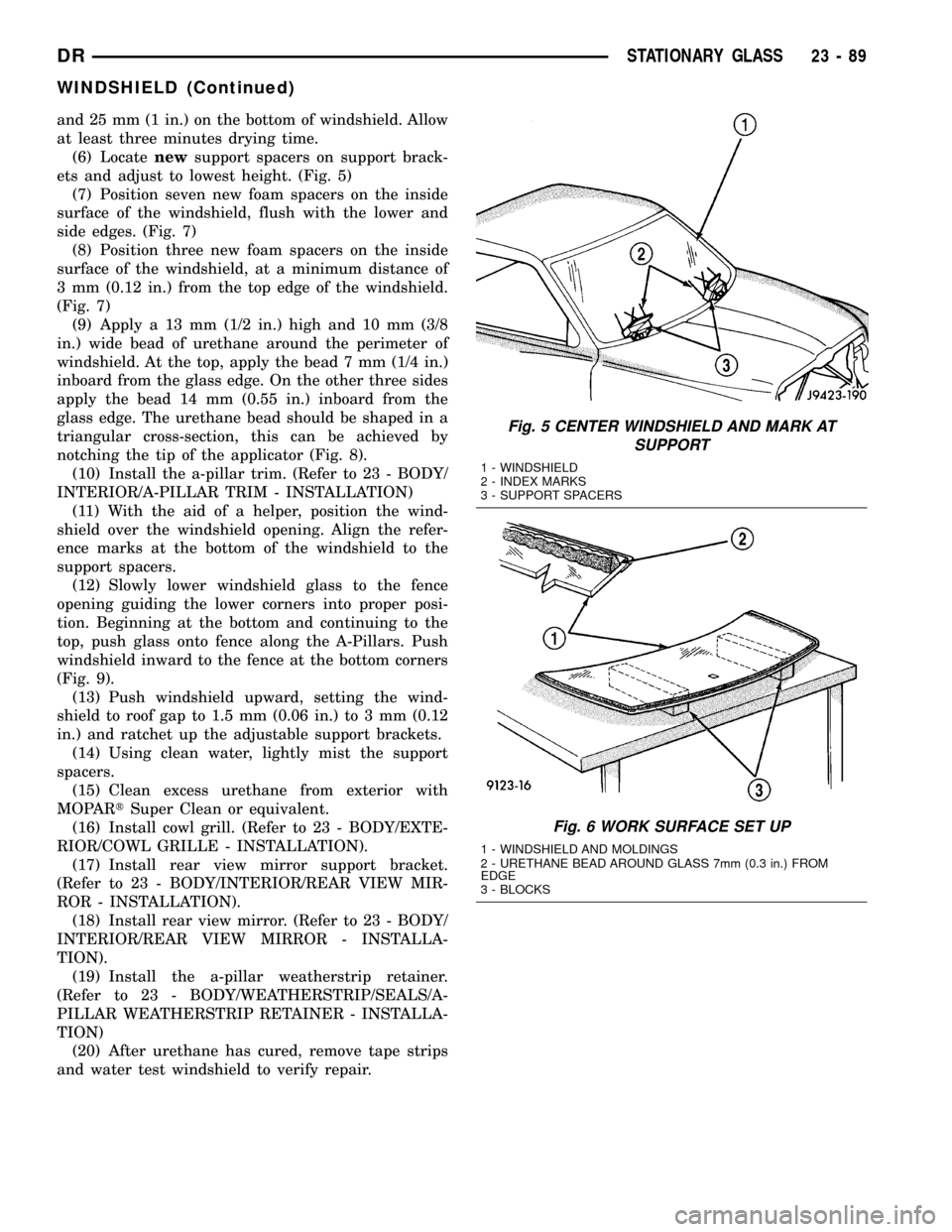
and 25 mm (1 in.) on the bottom of windshield. Allow
at least three minutes drying time.
(6) Locatenewsupport spacers on support brack-
ets and adjust to lowest height. (Fig. 5)
(7) Position seven new foam spacers on the inside
surface of the windshield, flush with the lower and
side edges. (Fig. 7)
(8) Position three new foam spacers on the inside
surface of the windshield, at a minimum distance of
3 mm (0.12 in.) from the top edge of the windshield.
(Fig. 7)
(9) Apply a 13 mm (1/2 in.) high and 10 mm (3/8
in.) wide bead of urethane around the perimeter of
windshield. At the top, apply the bead 7 mm (1/4 in.)
inboard from the glass edge. On the other three sides
apply the bead 14 mm (0.55 in.) inboard from the
glass edge. The urethane bead should be shaped in a
triangular cross-section, this can be achieved by
notching the tip of the applicator (Fig. 8).
(10) Install the a-pillar trim. (Refer to 23 - BODY/
INTERIOR/A-PILLAR TRIM - INSTALLATION)
(11) With the aid of a helper, position the wind-
shield over the windshield opening. Align the refer-
ence marks at the bottom of the windshield to the
support spacers.
(12) Slowly lower windshield glass to the fence
opening guiding the lower corners into proper posi-
tion. Beginning at the bottom and continuing to the
top, push glass onto fence along the A-Pillars. Push
windshield inward to the fence at the bottom corners
(Fig. 9).
(13) Push windshield upward, setting the wind-
shield to roof gap to 1.5 mm (0.06 in.) to 3 mm (0.12
in.) and ratchet up the adjustable support brackets.
(14) Using clean water, lightly mist the support
spacers.
(15) Clean excess urethane from exterior with
MOPARtSuper Clean or equivalent.
(16) Install cowl grill. (Refer to 23 - BODY/EXTE-
RIOR/COWL GRILLE - INSTALLATION).
(17) Install rear view mirror support bracket.
(Refer to 23 - BODY/INTERIOR/REAR VIEW MIR-
ROR - INSTALLATION).
(18) Install rear view mirror. (Refer to 23 - BODY/
INTERIOR/REAR VIEW MIRROR - INSTALLA-
TION).
(19) Install the a-pillar weatherstrip retainer.
(Refer to 23 - BODY/WEATHERSTRIP/SEALS/A-
PILLAR WEATHERSTRIP RETAINER - INSTALLA-
TION)
(20) After urethane has cured, remove tape strips
and water test windshield to verify repair.
Fig. 5 CENTER WINDSHIELD AND MARK AT
SUPPORT
1 - WINDSHIELD
2 - INDEX MARKS
3 - SUPPORT SPACERS
Fig. 6 WORK SURFACE SET UP
1 - WINDSHIELD AND MOLDINGS
2 - URETHANE BEAD AROUND GLASS 7mm (0.3 in.) FROM
EDGE
3 - BLOCKS
DRSTATIONARY GLASS 23 - 89
WINDSHIELD (Continued)
Page 2501 of 2627
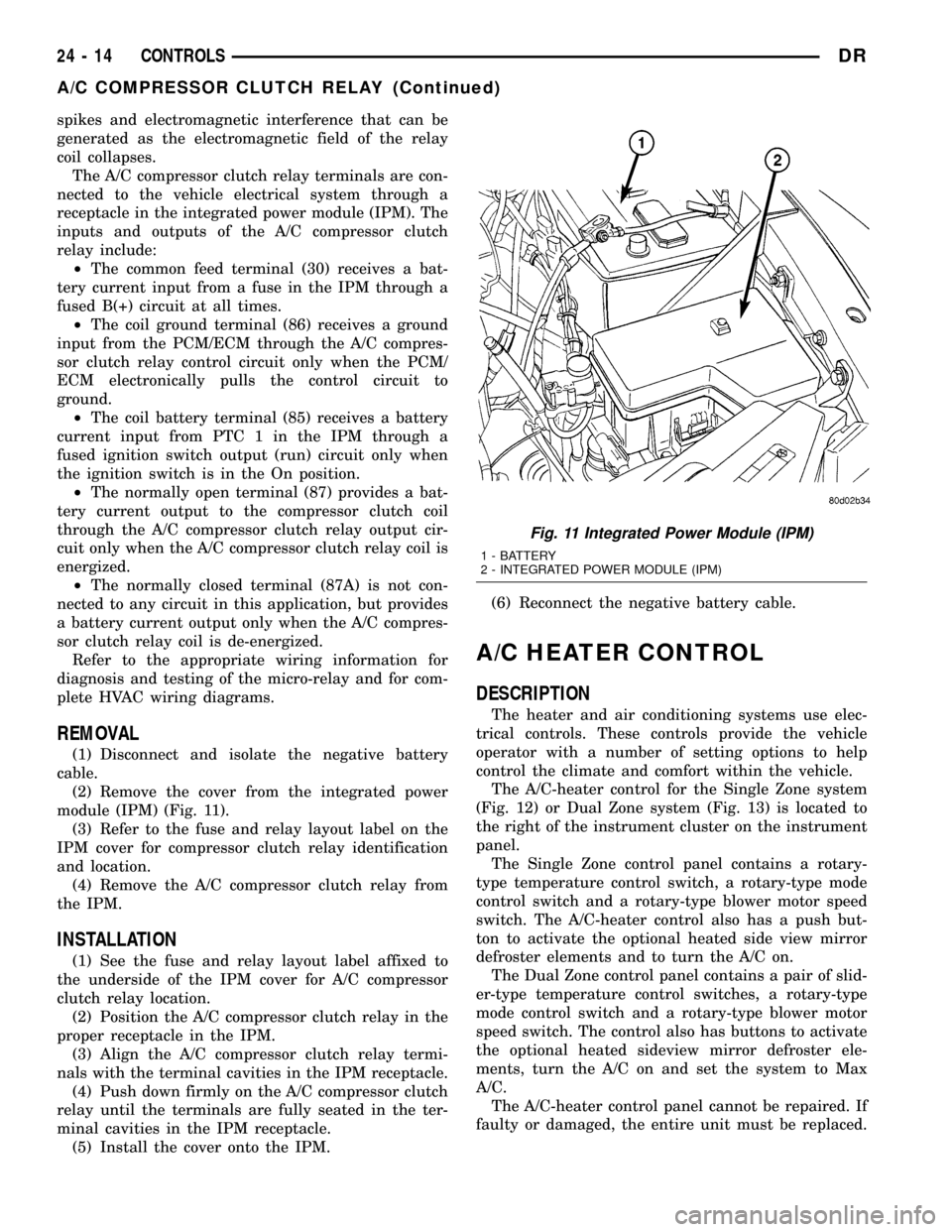
spikes and electromagnetic interference that can be
generated as the electromagnetic field of the relay
coil collapses.
The A/C compressor clutch relay terminals are con-
nected to the vehicle electrical system through a
receptacle in the integrated power module (IPM). The
inputs and outputs of the A/C compressor clutch
relay include:
²The common feed terminal (30) receives a bat-
tery current input from a fuse in the IPM through a
fused B(+) circuit at all times.
²The coil ground terminal (86) receives a ground
input from the PCM/ECM through the A/C compres-
sor clutch relay control circuit only when the PCM/
ECM electronically pulls the control circuit to
ground.
²The coil battery terminal (85) receives a battery
current input from PTC 1 in the IPM through a
fused ignition switch output (run) circuit only when
the ignition switch is in the On position.
²The normally open terminal (87) provides a bat-
tery current output to the compressor clutch coil
through the A/C compressor clutch relay output cir-
cuit only when the A/C compressor clutch relay coil is
energized.
²The normally closed terminal (87A) is not con-
nected to any circuit in this application, but provides
a battery current output only when the A/C compres-
sor clutch relay coil is de-energized.
Refer to the appropriate wiring information for
diagnosis and testing of the micro-relay and for com-
plete HVAC wiring diagrams.
REMOVAL
(1) Disconnect and isolate the negative battery
cable.
(2) Remove the cover from the integrated power
module (IPM) (Fig. 11).
(3) Refer to the fuse and relay layout label on the
IPM cover for compressor clutch relay identification
and location.
(4) Remove the A/C compressor clutch relay from
the IPM.
INSTALLATION
(1) See the fuse and relay layout label affixed to
the underside of the IPM cover for A/C compressor
clutch relay location.
(2) Position the A/C compressor clutch relay in the
proper receptacle in the IPM.
(3) Align the A/C compressor clutch relay termi-
nals with the terminal cavities in the IPM receptacle.
(4) Push down firmly on the A/C compressor clutch
relay until the terminals are fully seated in the ter-
minal cavities in the IPM receptacle.
(5) Install the cover onto the IPM.(6) Reconnect the negative battery cable.
A/C HEATER CONTROL
DESCRIPTION
The heater and air conditioning systems use elec-
trical controls. These controls provide the vehicle
operator with a number of setting options to help
control the climate and comfort within the vehicle.
The A/C-heater control for the Single Zone system
(Fig. 12) or Dual Zone system (Fig. 13) is located to
the right of the instrument cluster on the instrument
panel.
The Single Zone control panel contains a rotary-
type temperature control switch, a rotary-type mode
control switch and a rotary-type blower motor speed
switch. The A/C-heater control also has a push but-
ton to activate the optional heated side view mirror
defroster elements and to turn the A/C on.
The Dual Zone control panel contains a pair of slid-
er-type temperature control switches, a rotary-type
mode control switch and a rotary-type blower motor
speed switch. The control also has buttons to activate
the optional heated sideview mirror defroster ele-
ments, turn the A/C on and set the system to Max
A/C.
The A/C-heater control panel cannot be repaired. If
faulty or damaged, the entire unit must be replaced.
Fig. 11 Integrated Power Module (IPM)
1 - BATTERY
2 - INTEGRATED POWER MODULE (IPM)
24 - 14 CONTROLSDR
A/C COMPRESSOR CLUTCH RELAY (Continued)
Page 2502 of 2627
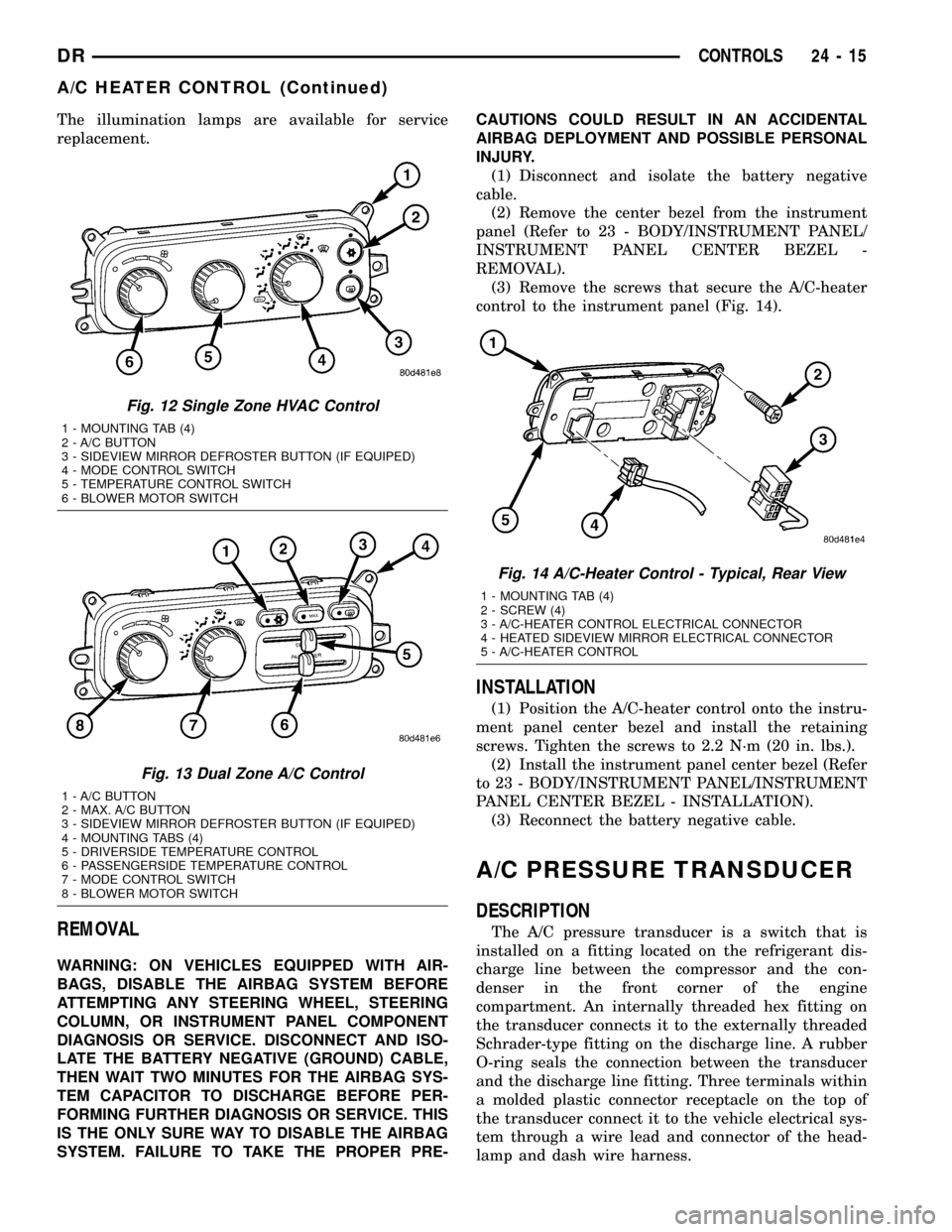
The illumination lamps are available for service
replacement.
REMOVAL
WARNING: ON VEHICLES EQUIPPED WITH AIR-
BAGS, DISABLE THE AIRBAG SYSTEM BEFORE
ATTEMPTING ANY STEERING WHEEL, STEERING
COLUMN, OR INSTRUMENT PANEL COMPONENT
DIAGNOSIS OR SERVICE. DISCONNECT AND ISO-
LATE THE BATTERY NEGATIVE (GROUND) CABLE,
THEN WAIT TWO MINUTES FOR THE AIRBAG SYS-
TEM CAPACITOR TO DISCHARGE BEFORE PER-
FORMING FURTHER DIAGNOSIS OR SERVICE. THIS
IS THE ONLY SURE WAY TO DISABLE THE AIRBAG
SYSTEM. FAILURE TO TAKE THE PROPER PRE-CAUTIONS COULD RESULT IN AN ACCIDENTAL
AIRBAG DEPLOYMENT AND POSSIBLE PERSONAL
INJURY.
(1) Disconnect and isolate the battery negative
cable.
(2) Remove the center bezel from the instrument
panel (Refer to 23 - BODY/INSTRUMENT PANEL/
INSTRUMENT PANEL CENTER BEZEL -
REMOVAL).
(3) Remove the screws that secure the A/C-heater
control to the instrument panel (Fig. 14).
INSTALLATION
(1) Position the A/C-heater control onto the instru-
ment panel center bezel and install the retaining
screws. Tighten the screws to 2.2 N´m (20 in. lbs.).
(2) Install the instrument panel center bezel (Refer
to 23 - BODY/INSTRUMENT PANEL/INSTRUMENT
PANEL CENTER BEZEL - INSTALLATION).
(3) Reconnect the battery negative cable.
A/C PRESSURE TRANSDUCER
DESCRIPTION
The A/C pressure transducer is a switch that is
installed on a fitting located on the refrigerant dis-
charge line between the compressor and the con-
denser in the front corner of the engine
compartment. An internally threaded hex fitting on
the transducer connects it to the externally threaded
Schrader-type fitting on the discharge line. A rubber
O-ring seals the connection between the transducer
and the discharge line fitting. Three terminals within
a molded plastic connector receptacle on the top of
the transducer connect it to the vehicle electrical sys-
tem through a wire lead and connector of the head-
lamp and dash wire harness.
Fig. 12 Single Zone HVAC Control
1 - MOUNTING TAB (4)
2 - A/C BUTTON
3 - SIDEVIEW MIRROR DEFROSTER BUTTON (IF EQUIPED)
4 - MODE CONTROL SWITCH
5 - TEMPERATURE CONTROL SWITCH
6 - BLOWER MOTOR SWITCH
Fig. 13 Dual Zone A/C Control
1 - A/C BUTTON
2 - MAX. A/C BUTTON
3 - SIDEVIEW MIRROR DEFROSTER BUTTON (IF EQUIPED)
4 - MOUNTING TABS (4)
5 - DRIVERSIDE TEMPERATURE CONTROL
6 - PASSENGERSIDE TEMPERATURE CONTROL
7 - MODE CONTROL SWITCH
8 - BLOWER MOTOR SWITCH
Fig. 14 A/C-Heater Control - Typical, Rear View
1 - MOUNTING TAB (4)
2 - SCREW (4)
3 - A/C-HEATER CONTROL ELECTRICAL CONNECTOR
4 - HEATED SIDEVIEW MIRROR ELECTRICAL CONNECTOR
5 - A/C-HEATER CONTROL
DRCONTROLS 24 - 15
A/C HEATER CONTROL (Continued)
Page 2507 of 2627
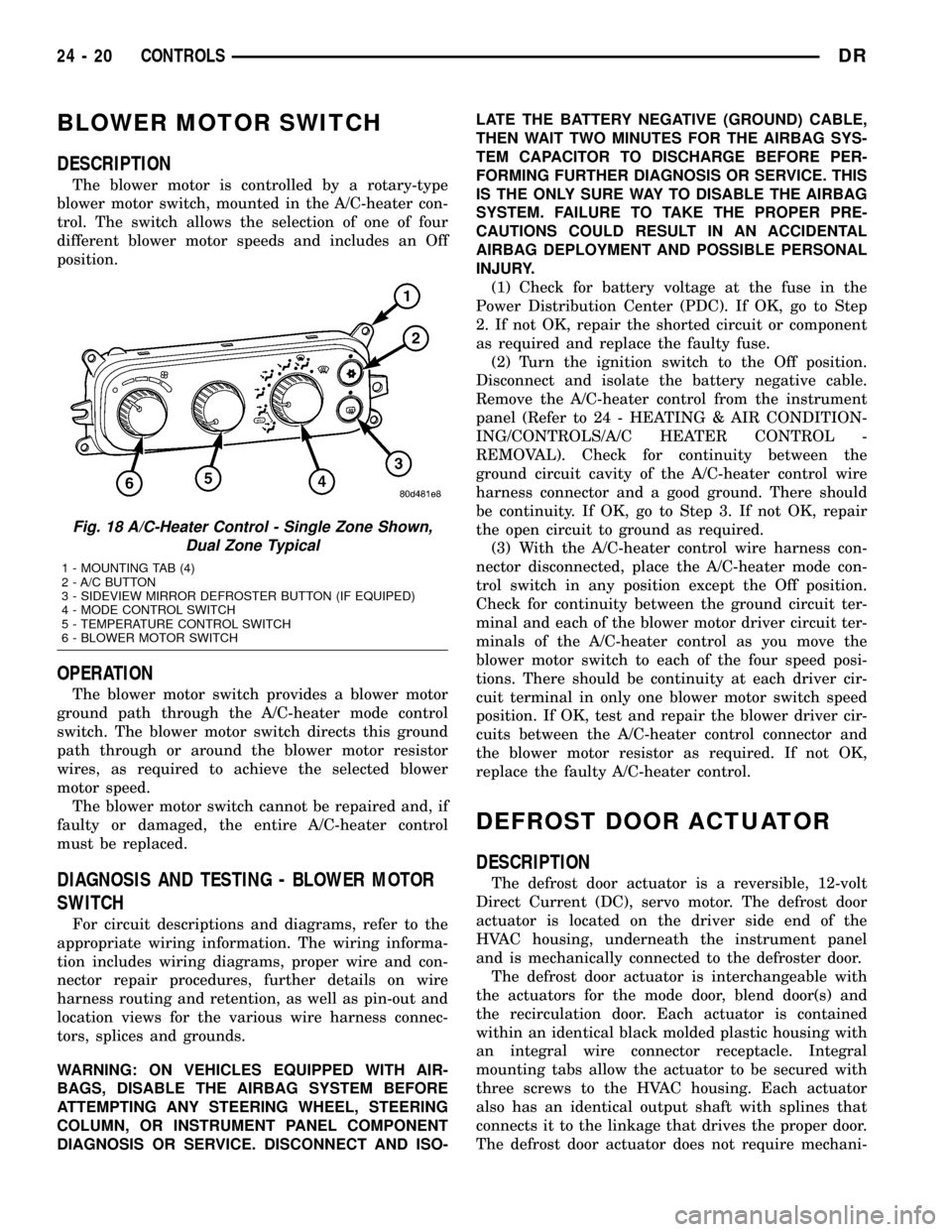
BLOWER MOTOR SWITCH
DESCRIPTION
The blower motor is controlled by a rotary-type
blower motor switch, mounted in the A/C-heater con-
trol. The switch allows the selection of one of four
different blower motor speeds and includes an Off
position.
OPERATION
The blower motor switch provides a blower motor
ground path through the A/C-heater mode control
switch. The blower motor switch directs this ground
path through or around the blower motor resistor
wires, as required to achieve the selected blower
motor speed.
The blower motor switch cannot be repaired and, if
faulty or damaged, the entire A/C-heater control
must be replaced.
DIAGNOSIS AND TESTING - BLOWER MOTOR
SWITCH
For circuit descriptions and diagrams, refer to the
appropriate wiring information. The wiring informa-
tion includes wiring diagrams, proper wire and con-
nector repair procedures, further details on wire
harness routing and retention, as well as pin-out and
location views for the various wire harness connec-
tors, splices and grounds.
WARNING: ON VEHICLES EQUIPPED WITH AIR-
BAGS, DISABLE THE AIRBAG SYSTEM BEFORE
ATTEMPTING ANY STEERING WHEEL, STEERING
COLUMN, OR INSTRUMENT PANEL COMPONENT
DIAGNOSIS OR SERVICE. DISCONNECT AND ISO-LATE THE BATTERY NEGATIVE (GROUND) CABLE,
THEN WAIT TWO MINUTES FOR THE AIRBAG SYS-
TEM CAPACITOR TO DISCHARGE BEFORE PER-
FORMING FURTHER DIAGNOSIS OR SERVICE. THIS
IS THE ONLY SURE WAY TO DISABLE THE AIRBAG
SYSTEM. FAILURE TO TAKE THE PROPER PRE-
CAUTIONS COULD RESULT IN AN ACCIDENTAL
AIRBAG DEPLOYMENT AND POSSIBLE PERSONAL
INJURY.
(1) Check for battery voltage at the fuse in the
Power Distribution Center (PDC). If OK, go to Step
2. If not OK, repair the shorted circuit or component
as required and replace the faulty fuse.
(2) Turn the ignition switch to the Off position.
Disconnect and isolate the battery negative cable.
Remove the A/C-heater control from the instrument
panel (Refer to 24 - HEATING & AIR CONDITION-
ING/CONTROLS/A/C HEATER CONTROL -
REMOVAL). Check for continuity between the
ground circuit cavity of the A/C-heater control wire
harness connector and a good ground. There should
be continuity. If OK, go to Step 3. If not OK, repair
the open circuit to ground as required.
(3) With the A/C-heater control wire harness con-
nector disconnected, place the A/C-heater mode con-
trol switch in any position except the Off position.
Check for continuity between the ground circuit ter-
minal and each of the blower motor driver circuit ter-
minals of the A/C-heater control as you move the
blower motor switch to each of the four speed posi-
tions. There should be continuity at each driver cir-
cuit terminal in only one blower motor switch speed
position. If OK, test and repair the blower driver cir-
cuits between the A/C-heater control connector and
the blower motor resistor as required. If not OK,
replace the faulty A/C-heater control.
DEFROST DOOR ACTUATOR
DESCRIPTION
The defrost door actuator is a reversible, 12-volt
Direct Current (DC), servo motor. The defrost door
actuator is located on the driver side end of the
HVAC housing, underneath the instrument panel
and is mechanically connected to the defroster door.
The defrost door actuator is interchangeable with
the actuators for the mode door, blend door(s) and
the recirculation door. Each actuator is contained
within an identical black molded plastic housing with
an integral wire connector receptacle. Integral
mounting tabs allow the actuator to be secured with
three screws to the HVAC housing. Each actuator
also has an identical output shaft with splines that
connects it to the linkage that drives the proper door.
The defrost door actuator does not require mechani-
Fig. 18 A/C-Heater Control - Single Zone Shown,
Dual Zone Typical
1 - MOUNTING TAB (4)
2 - A/C BUTTON
3 - SIDEVIEW MIRROR DEFROSTER BUTTON (IF EQUIPED)
4 - MODE CONTROL SWITCH
5 - TEMPERATURE CONTROL SWITCH
6 - BLOWER MOTOR SWITCH
24 - 20 CONTROLSDR
Page 2591 of 2627

BLOCK - DIAGNOSIS AND TESTING,
BLOWER MOTOR RESISTOR............24-19
BLOCK - INSPECTION, ENGINE . 9-128,9-205,9-39
BLOCK - INSTALLATION, BLOWER
MOTOR RESISTOR...................24-19
BLOCK - INSTALLATION, BRAKE
JUNCTION...........................5-24
BLOCK - OPERATION, BLOWER MOTOR
RESISTOR..........................24-18
BLOCK - REMOVAL, BLOWER MOTOR
RESISTOR..........................24-19
BLOCK - REMOVAL, BRAKE JUNCTION....5-24
BLOCK HEATER - 5.9L DIESEL -
DESCRIPTION, ENGINE.................7-37
BLOCK HEATER - 5.9L DIESEL -
INSTALLATION, ENGINE................7-38
BLOCK HEATER - 5.9L DIESEL -
OPERATION, ENGINE...................7-38
BLOCK HEATER - 5.9L DIESEL -
REMOVAL, ENGINE....................7-38
BLOCK HEATER - DESCRIPTION, ENGINE . . . 7-36
BLOCK HEATER - DIAGNOSIS AND
TESTING, ENGINE.....................7-36
BLOCK HEATER - INSTALLATION,
ENGINE.............................7-37
BLOCK HEATER - OPERATION, ENGINE....7-36
BLOCK HEATER - REMOVAL, ENGINE......7-37
BLOCK REFACING - STANDARD
PROCEDURE, CYLINDER...............9-264
BLOWER MOTOR - DESCRIPTION.......24-28
BLOWER MOTOR - DIAGNOSIS AND
TESTING.............................24-28
BLOWER MOTOR - INSTALLATION.......24-31
BLOWER MOTOR - OPERATION.........24-28
BLOWER MOTOR - REMOVAL...........24-31
BLOWER MOTOR RESISTOR BLOCK -
DESCRIPTION.......................24-18
BLOWER MOTOR RESISTOR BLOCK -
DIAGNOSIS AND TESTING.............24-19
BLOWER MOTOR RESISTOR BLOCK -
INSTALLATION.......................24-19
BLOWER MOTOR RESISTOR BLOCK -
OPERATION.........................24-18
BLOWER MOTOR RESISTOR BLOCK -
REMOVAL..........................24-19
BLOWER MOTOR SWITCH -
DESCRIPTION.......................24-20
BLOWER MOTOR SWITCH - DIAGNOSIS
AND TESTING.......................24-20
BLOWER MOTOR SWITCH - OPERATION . . 24-20
BODY - ADJUSTMENTS, VALVE........21-310
BODY - ASSEMBLY, VALVE......21-299,21-414
BODY & CABLE - DESCRIPTION,
ANTENNA...........................8A-4
BODY & CABLE - INSTALLATION,
ANTENNA...........................8A-6
BODY & CABLE - OPERATION, ANTENNA . . . 8A-4
BODY & CABLE - REMOVAL, ANTENNA....8A-6
BODY - CLEANING, VALVE......21-298,21-412
BODY - DESCRIPTION, THROTTLE.......14-36
BODY - DESCRIPTION, VALVE....21-267,21-408
BODY - DISASSEMBLY, VALVE . . . 21-287,21-410
BODY - INSPECTION, VALVE.....21-298,21-413
BODY - INSTALLATION, THROTTLE.......14-37
BODY - INSTALLATION, VALVE . . . 21-309,21-414
BODY - OPERATION, THROTTLE.........14-36
BODY - OPERATION, VALVE.....21-272,21-408
BODY - REMOVAL, THROTTLE..........14-36
BODY - REMOVAL, VALVE.......21-286,21-410
BODY AND CABLE - DIAGNOSIS AND
TESTING, ANTENNA
...................8A-4
BODY CODE PLATE - DESCRIPTION
.....Intro.-3
BODY ISOLATORS - INSTALLATION
......23-37
BODY ISOLATORS - REMOVAL
..........23-36
BODY LUBRICATION - STANDARD
PROCEDURE
.........................23-3
BODY OPENING DIMENSIONS -
SPECIFICATIONS
.....................23-99
BODY PANEL REPAIR - STANDARD
PROCEDURE, PLASTIC
.................23-3
BODY SIDE MOLDINGS - INSTALLATION
. . 23-36
BODY SIDE MOLDINGS - REMOVAL
......23-36
BODY, SPECIAL TOOLS
................23-14
BODY VENT - INSTALLATION
...........23-71
BODY VENT - REMOVAL
...............23-71
BOOST PRESSURE - DIAGNOSIS AND
TESTING, TURBOCHARGER
.............11-11BOOSTER - DESCRIPTION, POWER
BRAKE..............................5-29
BOOSTER - DIAGNOSIS AND TESTING,
HYDRAULIC..........................5-30
BOOSTER - DIAGNOSIS AND TESTING,
MASTER CYLINDER/POWER.............5-25
BOOSTER - INSTALLATION, HYDRO-
BOOST BRAKE........................5-32
BOOSTER - INSTALLATION, POWER
BRAKE..............................5-29
BOOSTER - OPERATION, POWER BRAKE . . . 5-29
BOOSTER - REMOVAL, HYDRO-BOOST
BRAKE..............................5-31
BOOSTER - REMOVAL, POWER BRAKE....5-29
BOOT - INSTALLATION, 4WD FLOOR
SHIFT..............................23-62
BOOT - INSTALLATION, EXTENSION
HOUSING SEAL AND DUST......21-476,21-571
BOOT - REMOVAL, 4WD FLOOR SHIFT....23-62
BOOT - REMOVAL, EXTENSION HOUSING
SEAL AND DUST..............21-476,21-571
BORE - DE-GLAZE - STANDARD
PROCEDURE, CYLINDER...............9-264
BORE HONING - STANDARD
PROCEDURE, CYLINDER...........9-128,9-38
BORE REPAIR - STANDARD
PROCEDURE, CAM...................9-267
BORE REPAIR - STANDARD
PROCEDURE, CYLINDER...............9-265
BOX - INSTALLATION, CARGO..........23-37
BOX - INSTALLATION, GLOVE...........23-52
BOX - INSTALLATION, WITH CARGO . 8L-22,8L-23,
8L-24,8L-7,8L-9
BOX - INSTALLATION, WITHOUT CARGO . . 8L-22,
8L-23,8L-24,8L-8,8L-9
BOX - REMOVAL, CARGO..............23-37
BOX - REMOVAL, GLOVE..............23-52
BOX - REMOVAL, WITH CARGO....8L-22,8L-24,
8L-7,8L-9
BOX - REMOVAL, WITHOUT CARGO.....8L-22,
8L-23,8L-24,8L-7,8L-9
BOX - TIE DOWN - INSTALLATION,
CARGO............................23-38
BOX - TIE DOWN - REMOVAL, CARGO....23-38
BOX LAMP/SWITCH - INSTALLATION,
GLOVE.............................8L-28
BOX LAMP/SWITCH - REMOVAL, GLOVE . . 8L-27
BOX LATCH - INSTALLATION, GLOVE.....23-52
BOX LATCH - REMOVAL, GLOVE.........23-52
B-PILLAR GRAB HANDLE -
INSTALLATION.......................23-68
B-PILLAR GRAB HANDLE - REMOVAL....23-68
B-PILLAR LOWER TRIM - INSTALLATION . . 23-64
B-PILLAR LOWER TRIM - REMOVAL.....23-63
B-PILLAR UPPER TRIM - INSTALLATION . . 23-64
B-PILLAR UPPER TRIM - REMOVAL......23-64
BRACKET - INSTALLATION, REAR VIEW
MIRROR SUPPORT...................23-70
BRACKET - INSTALLATION, STEERING
COLUMN OPENING SUPPORT...........23-60
BRACKET - REMOVAL, STEERING
COLUMN OPENING SUPPORT...........23-60
BRACKETS - INSTALLATION, SEAT BACK
REAR - FOOTMANS LOOP..............23-85
BRACKETS - REMOVAL, SEAT BACK
REAR - FOOTMANS LOOP..............23-85
BRAKE - CLEANING, REAR DRUM IN
HAT ................................5-39
BRAKE - DESCRIPTION, CONTROLLER
ANTILOCK...........................8E-3
BRAKE - DESCRIPTION, PARKING........5-36
BRAKE - INSPECTION, REAR DRUM IN
HAT ................................5-39
BRAKE - INSTALLATION, CONTROLLER
ANTILOCK...........................8E-3
BRAKE - OPERATION, CONTROLLER
ANTILOCK...........................8E-3
BRAKE - OPERATION, PARKING..........5-36
BRAKE - REMOVAL, CONTROLLER
ANTILOCK
...........................8E-3
BRAKE BLEEDING - STANDARD
PROCEDURE, ABS
.....................5-46
BRAKE BOOSTER - DESCRIPTION,
POWER
.............................5-29
BRAKE BOOSTER - INSTALLATION,
HYDRO-BOOST
.......................5-32
BRAKE BOOSTER - INSTALLATION,
POWER
.............................5-29BRAKE BOOSTER - OPERATION, POWER . . . 5-29
BRAKE BOOSTER - REMOVAL,
HYDRO-BOOST.......................5-31
BRAKE BOOSTER - REMOVAL, POWER....5-29
BRAKE CABLE - INSTALLATION, FRONT
PARKING............................5-38
BRAKE CABLE - INSTALLATION, REAR
PARK...............................5-38
BRAKE CABLE - REMOVAL, FRONT
PARKING............................5-36
BRAKE CABLE - REMOVAL, REAR PARK . . . 5-37
BRAKE CALIPER ADAPTER MOUNT -
INSTALLATION, DISC...................5-22
BRAKE CALIPERS - DESCRIPTION, DISC . . . 5-16
BRAKE CALIPERS - OPERATION, DISC.....5-16
BRAKE FLUID CONTAMINATION -
DIAGNOSIS AND TESTING..............5-23
BRAKE FLUID LEVEL - STANDARD
PROCEDURE.........................5-23
BRAKE FLUID, SPECIFICATIONS..........5-23
BRAKE HOSE - INSTALLATION, FRONT.....5-13
BRAKE HOSE - INSTALLATION, REAR......5-12
BRAKE HOSE - REMOVAL, REAR.........5-11
BRAKE INDICATOR - DESCRIPTION,
BRAKE/PARK........................8J-19
BRAKE INDICATOR - DIAGNOSIS AND
TESTING...........................8J-20
BRAKE INDICATOR - OPERATION,
BRAKE/PARK........................8J-19
BRAKE JUNCTION BLOCK -
INSTALLATION.........................5-24
BRAKE JUNCTION BLOCK - REMOVAL.....5-24
BRAKE LAMP SWITCH - DESCRIPTION....8L-9
BRAKE LAMP SWITCH - DIAGNOSIS
AND TESTING.......................8L-10
BRAKE LAMP SWITCH - INSTALLATION . . . 8L-11
BRAKE LAMP SWITCH - OPERATION......8L-9
BRAKE LAMP SWITCH - REMOVAL......8L-10
BRAKE PROPORTIONING -
DESCRIPTION, ELECTRONIC VARIABLE....5-49
BRAKE PROPORTIONING - OPERATION,
ELECTRONIC VARIABLE................5-49
BRAKE ROTOR, DIAGNOSIS AND
TESTING - DISC......................5-32
BRAKE SHOES - ADJUSTMENT, PARKING . . 5-41
BRAKE, SPECIFICATIONS - BASE.........5-10
BRAKE SYSTEM - DIAGNOSIS AND
TESTING, BASE........................5-2
BRAKE TRANSMISSION SHIFT
INTERLOCK - ADJUSTMENTS....21-196,21-365
BRAKE TRANSMISSION SHIFT
INTERLOCK - DIAGNOSIS AND
TESTING....................21-196,21-364
BRAKE TRANSMISSION SHIFT
INTERLOCK SYSTEM - DESCRIPTION . . . 21-196,
21-364
BRAKE TRANSMISSION SHIFT
INTERLOCK SYSTEM - OPERATION.....21-196,
21-364
BRAKE/PARK BRAKE INDICATOR -
DESCRIPTION.......................8J-19
BRAKE/PARK BRAKE INDICATOR -
OPERATION.........................8J-19
BRAKES - ABS - DESCRIPTION...........5-45
BRAKES - ABS - OPERATION............5-45
BRAKES, SPECIAL TOOLS - BASE.........5-5
BREAK-IN - STANDARD PROCEDURE,
A/C COMPRESSOR CLUTCH............24-10
BREATHER - INSTALLATION,
CRANKCASE
........................9-243
BREATHER - REMOVAL, CRANKCASE
.....9-242
BUCKLE - INSTALLATION, FRONT
OUTBOARD SEAT BELT
................8O-38
BUCKLE - REMOVAL, FRONT OUTBOARD
SEAT BELT
.........................8O-37
BUILT-IN INDICATOR TEST - STANDARD
PROCEDURE
........................8F-10
BUMPER - INSTALLATION, FRONT
........13-2
BUMPER - INSTALLATION, JOUNCE
.......2-43
BUMPER - INSTALLATION, REAR
.........13-4
BUMPER - REMOVAL, FRONT
............13-2
BUMPER - REMOVAL, JOUNCE
...........2-43
BUMPER - REMOVAL, REAR
.............13-3
BUMPERS (3500) - INSTALLATION,
AUXILIARY SPRING
....................2-43
BUMPERS (3500) - REMOVAL,
AUXILIARY SPRING
....................2-43
4 INDEXDR
Description Group-Page Description Group-Page Description Group-Page
Page 2596 of 2627
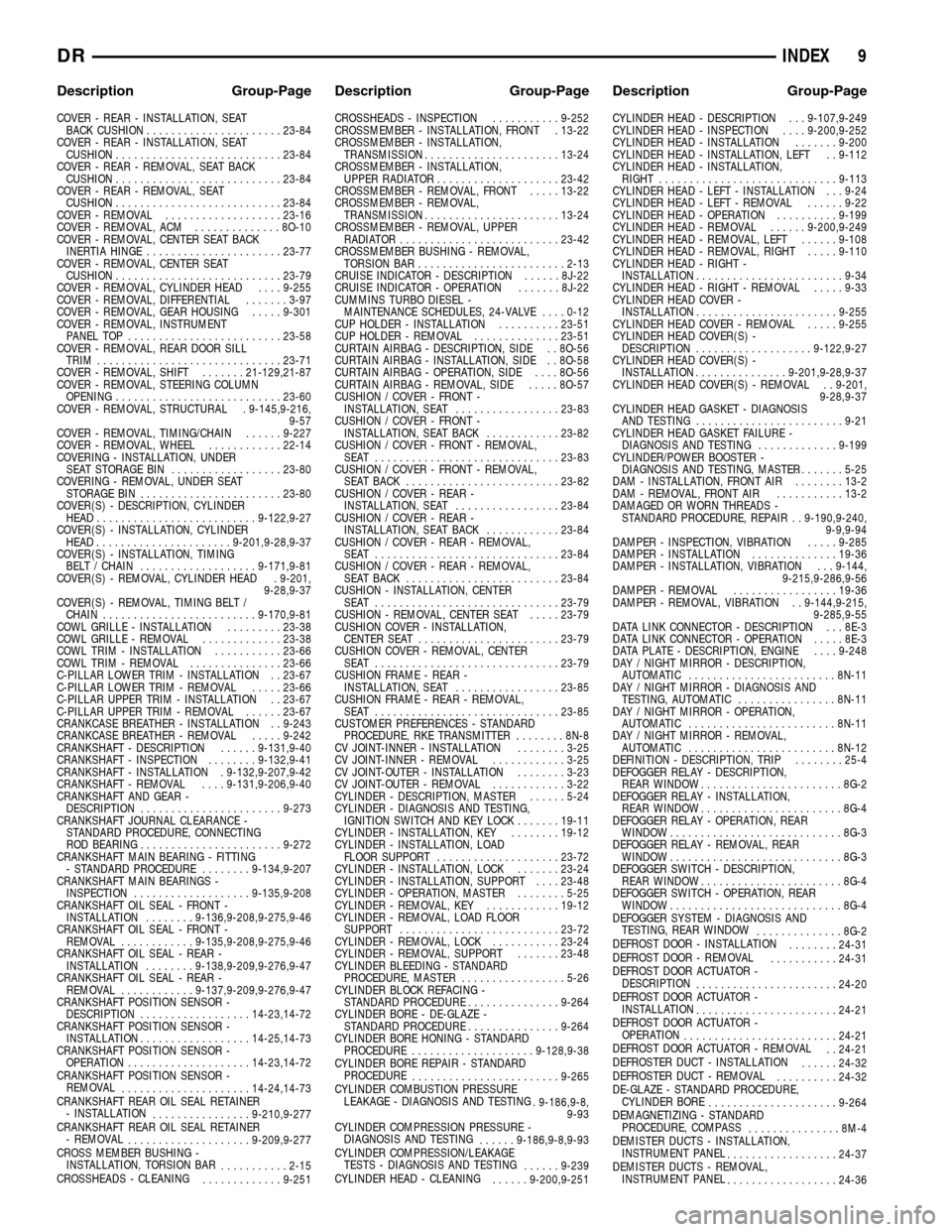
COVER - REAR - INSTALLATION, SEAT
BACK CUSHION......................23-84
COVER - REAR - INSTALLATION, SEAT
CUSHION...........................23-84
COVER - REAR - REMOVAL, SEAT BACK
CUSHION...........................23-84
COVER - REAR - REMOVAL, SEAT
CUSHION...........................23-84
COVER - REMOVAL...................23-16
COVER - REMOVAL, ACM..............8O-10
COVER - REMOVAL, CENTER SEAT BACK
INERTIA HINGE......................23-77
COVER - REMOVAL, CENTER SEAT
CUSHION...........................23-79
COVER - REMOVAL, CYLINDER HEAD....9-255
COVER - REMOVAL, DIFFERENTIAL.......3-97
COVER - REMOVAL, GEAR HOUSING.....9-301
COVER - REMOVAL, INSTRUMENT
PANEL TOP.........................23-58
COVER - REMOVAL, REAR DOOR SILL
TRIM..............................23-71
COVER - REMOVAL, SHIFT.......21-129,21-87
COVER - REMOVAL, STEERING COLUMN
OPENING...........................23-60
COVER - REMOVAL, STRUCTURAL . 9-145,9-216,
9-57
COVER - REMOVAL, TIMING/CHAIN......9-227
COVER - REMOVAL, WHEEL............22-14
COVERING - INSTALLATION, UNDER
SEAT STORAGE BIN..................23-80
COVERING - REMOVAL, UNDER SEAT
STORAGE BIN.......................23-80
COVER(S) - DESCRIPTION, CYLINDER
HEAD..........................9-122,9-27
COVER(S) - INSTALLATION, CYLINDER
HEAD......................9-201,9-28,9-37
COVER(S) - INSTALLATION, TIMING
BELT / CHAIN...................9-171,9-81
COVER(S) - REMOVAL, CYLINDER HEAD . 9-201,
9-28,9-37
COVER(S) - REMOVAL, TIMING BELT /
CHAIN.........................9-170,9-81
COWL GRILLE - INSTALLATION.........23-38
COWL GRILLE - REMOVAL.............23-38
COWL TRIM - INSTALLATION...........23-66
COWL TRIM - REMOVAL...............23-66
C-PILLAR LOWER TRIM - INSTALLATION . . 23-67
C-PILLAR LOWER TRIM - REMOVAL.....23-66
C-PILLAR UPPER TRIM - INSTALLATION . . 23-67
C-PILLAR UPPER TRIM - REMOVAL......23-67
CRANKCASE BREATHER - INSTALLATION . . 9-243
CRANKCASE BREATHER - REMOVAL.....9-242
CRANKSHAFT - DESCRIPTION......9-131,9-40
CRANKSHAFT - INSPECTION........9-132,9-41
CRANKSHAFT - INSTALLATION . 9-132,9-207,9-42
CRANKSHAFT - REMOVAL....9-131,9-206,9-40
CRANKSHAFT AND GEAR -
DESCRIPTION.......................9-273
CRANKSHAFT JOURNAL CLEARANCE -
STANDARD PROCEDURE, CONNECTING
ROD BEARING.......................9-272
CRANKSHAFT MAIN BEARING - FITTING
- STANDARD PROCEDURE........9-134,9-207
CRANKSHAFT MAIN BEARINGS -
INSPECTION...................9-135,9-208
CRANKSHAFT OIL SEAL - FRONT -
INSTALLATION........9-136,9-208,9-275,9-46
CRANKSHAFT OIL SEAL - FRONT -
REMOVAL............9-135,9-208,9-275,9-46
CRANKSHAFT OIL SEAL - REAR -
INSTALLATION........9-138,9-209,9-276,9-47
CRANKSHAFT OIL SEAL - REAR -
REMOVAL............9-137,9-209,9-276,9-47
CRANKSHAFT POSITION SENSOR -
DESCRIPTION..................14-23,14-72
CRANKSHAFT POSITION SENSOR -
INSTALLATION..................14-25,14-73
CRANKSHAFT POSITION SENSOR -
OPERATION....................14-23,14-72
CRANKSHAFT POSITION SENSOR -
REMOVAL
.....................14-24,14-73
CRANKSHAFT REAR OIL SEAL RETAINER
- INSTALLATION
................9-210,9-277
CRANKSHAFT REAR OIL SEAL RETAINER
- REMOVAL
....................9-209,9-277
CROSS MEMBER BUSHING -
INSTALLATION, TORSION BAR
...........2-15
CROSSHEADS - CLEANING
.............9-251CROSSHEADS - INSPECTION...........9-252
CROSSMEMBER - INSTALLATION, FRONT . 13-22
CROSSMEMBER - INSTALLATION,
TRANSMISSION......................13-24
CROSSMEMBER - INSTALLATION,
UPPER RADIATOR....................23-42
CROSSMEMBER - REMOVAL, FRONT.....13-22
CROSSMEMBER - REMOVAL,
TRANSMISSION......................13-24
CROSSMEMBER - REMOVAL, UPPER
RADIATOR..........................23-42
CROSSMEMBER BUSHING - REMOVAL,
TORSION BAR........................2-13
CRUISE INDICATOR - DESCRIPTION......8J-22
CRUISE INDICATOR - OPERATION.......8J-22
CUMMINS TURBO DIESEL -
MAINTENANCE SCHEDULES, 24-VALVE....0-12
CUP HOLDER - INSTALLATION..........23-51
CUP HOLDER - REMOVAL..............23-51
CURTAIN AIRBAG - DESCRIPTION, SIDE . . 8O-56
CURTAIN AIRBAG - INSTALLATION, SIDE . . 8O-58
CURTAIN AIRBAG - OPERATION, SIDE....8O-56
CURTAIN AIRBAG - REMOVAL, SIDE.....8O-57
CUSHION / COVER - FRONT -
INSTALLATION, SEAT.................23-83
CUSHION / COVER - FRONT -
INSTALLATION, SEAT BACK............23-82
CUSHION / COVER - FRONT - REMOVAL,
SEAT ..............................23-83
CUSHION / COVER - FRONT - REMOVAL,
SEAT BACK.........................23-82
CUSHION / COVER - REAR -
INSTALLATION, SEAT.................23-84
CUSHION / COVER - REAR -
INSTALLATION, SEAT BACK............23-84
CUSHION / COVER - REAR - REMOVAL,
SEAT ..............................23-84
CUSHION / COVER - REAR - REMOVAL,
SEAT BACK.........................23-84
CUSHION - INSTALLATION, CENTER
SEAT ..............................23-79
CUSHION - REMOVAL, CENTER SEAT.....23-79
CUSHION COVER - INSTALLATION,
CENTER SEAT.......................23-79
CUSHION COVER - REMOVAL, CENTER
SEAT ..............................23-79
CUSHION FRAME - REAR -
INSTALLATION, SEAT.................23-85
CUSHION FRAME - REAR - REMOVAL,
SEAT ..............................23-85
CUSTOMER PREFERENCES - STANDARD
PROCEDURE, RKE TRANSMITTER........8N-8
CV JOINT-INNER - INSTALLATION........3-25
CV JOINT-INNER - REMOVAL............3-25
CV JOINT-OUTER - INSTALLATION........3-23
CV JOINT-OUTER - REMOVAL............3-22
CYLINDER - DESCRIPTION, MASTER......5-24
CYLINDER - DIAGNOSIS AND TESTING,
IGNITION SWITCH AND KEY LOCK.......19-11
CYLINDER - INSTALLATION, KEY........19-12
CYLINDER - INSTALLATION, LOAD
FLOOR SUPPORT....................23-72
CYLINDER - INSTALLATION, LOCK.......23-24
CYLINDER - INSTALLATION, SUPPORT....23-48
CYLINDER - OPERATION, MASTER........5-25
CYLINDER - REMOVAL, KEY............19-12
CYLINDER - REMOVAL, LOAD FLOOR
SUPPORT..........................23-72
CYLINDER - REMOVAL, LOCK...........23-24
CYLINDER - REMOVAL, SUPPORT.......23-48
CYLINDER BLEEDING - STANDARD
PROCEDURE, MASTER.................5-26
CYLINDER BLOCK REFACING -
STANDARD PROCEDURE...............9-264
CYLINDER BORE - DE-GLAZE -
STANDARD PROCEDURE...............9-264
CYLINDER BORE HONING - STANDARD
PROCEDURE....................9-128,9-38
CYLINDER BORE REPAIR - STANDARD
PROCEDURE
........................9-265
CYLINDER COMBUSTION PRESSURE
LEAKAGE - DIAGNOSIS AND TESTING
. 9-186,9-8,
9-93
CYLINDER COMPRESSION PRESSURE -
DIAGNOSIS AND TESTING
......9-186,9-8,9-93
CYLINDER COMPRESSION/LEAKAGE
TESTS - DIAGNOSIS AND TESTING
......9-239
CYLINDER HEAD - CLEANING
......9-200,9-251CYLINDER HEAD - DESCRIPTION . . . 9-107,9-249
CYLINDER HEAD - INSPECTION....9-200,9-252
CYLINDER HEAD - INSTALLATION.......9-200
CYLINDER HEAD - INSTALLATION, LEFT . . 9-112
CYLINDER HEAD - INSTALLATION,
RIGHT.............................9-113
CYLINDER HEAD - LEFT - INSTALLATION . . . 9-24
CYLINDER HEAD - LEFT - REMOVAL......9-22
CYLINDER HEAD - OPERATION..........9-199
CYLINDER HEAD - REMOVAL......9-200,9-249
CYLINDER HEAD - REMOVAL, LEFT......9-108
CYLINDER HEAD - REMOVAL, RIGHT.....9-110
CYLINDER HEAD - RIGHT -
INSTALLATION........................9-34
CYLINDER HEAD - RIGHT - REMOVAL.....9-33
CYLINDER HEAD COVER -
INSTALLATION.......................9-255
CYLINDER HEAD COVER - REMOVAL.....9-255
CYLINDER HEAD COVER(S) -
DESCRIPTION...................9-122,9-27
CYLINDER HEAD COVER(S) -
INSTALLATION...............9-201,9-28,9-37
CYLINDER HEAD COVER(S) - REMOVAL . . 9-201,
9-28,9-37
CYLINDER HEAD GASKET - DIAGNOSIS
AND TESTING........................9-21
CYLINDER HEAD GASKET FAILURE -
DIAGNOSIS AND TESTING.............9-199
CYLINDER/POWER BOOSTER -
DIAGNOSIS AND TESTING, MASTER........5-25
DAM - INSTALLATION, FRONT AIR........13-2
DAM - REMOVAL, FRONT AIR...........13-2
DAMAGED OR WORN THREADS -
STANDARD PROCEDURE, REPAIR . . 9-190,9-240,
9-9,9-94
DAMPER - INSPECTION, VIBRATION.....9-285
DAMPER - INSTALLATION..............19-36
DAMPER - INSTALLATION, VIBRATION . . . 9-144,
9-215,9-286,9-56
DAMPER - REMOVAL.................19-36
DAMPER - REMOVAL, VIBRATION . . 9-144,9-215,
9-285,9-55
DATA LINK CONNECTOR - DESCRIPTION . . . 8E-3
DATA LINK CONNECTOR - OPERATION.....8E-3
DATA PLATE - DESCRIPTION, ENGINE....9-248
DAY / NIGHT MIRROR - DESCRIPTION,
AUTOMATIC........................8N-11
DAY / NIGHT MIRROR - DIAGNOSIS AND
TESTING, AUTOMATIC................8N-11
DAY / NIGHT MIRROR - OPERATION,
AUTOMATIC........................8N-11
DAY / NIGHT MIRROR - REMOVAL,
AUTOMATIC........................8N-12
DEFINITION - DESCRIPTION, TRIP........25-4
DEFOGGER RELAY - DESCRIPTION,
REAR WINDOW.......................8G-2
DEFOGGER RELAY - INSTALLATION,
REAR WINDOW.......................8G-4
DEFOGGER RELAY - OPERATION, REAR
WINDOW............................8G-3
DEFOGGER RELAY - REMOVAL, REAR
WINDOW............................8G-3
DEFOGGER SWITCH - DESCRIPTION,
REAR WINDOW.......................8G-4
DEFOGGER SWITCH - OPERATION, REAR
WINDOW............................8G-4
DEFOGGER SYSTEM - DIAGNOSIS AND
TESTING, REAR WINDOW
..............8G-2
DEFROST DOOR - INSTALLATION
........24-31
DEFROST DOOR - REMOVAL
...........24-31
DEFROST DOOR ACTUATOR -
DESCRIPTION
.......................24-20
DEFROST DOOR ACTUATOR -
INSTALLATION
.......................24-21
DEFROST DOOR ACTUATOR -
OPERATION
.........................24-21
DEFROST DOOR ACTUATOR - REMOVAL
. . 24-21
DEFROSTER DUCT - INSTALLATION
......24-32
DEFROSTER DUCT - REMOVAL
..........24-32
DE-GLAZE - STANDARD PROCEDURE,
CYLINDER BORE
.....................9-264
DEMAGNETIZING - STANDARD
PROCEDURE, COMPASS
...............8M-4
DEMISTER DUCTS - INSTALLATION,
INSTRUMENT PANEL
..................24-37
DEMISTER DUCTS - REMOVAL,
INSTRUMENT PANEL
..................24-36
DRINDEX 9
Description Group-Page Description Group-Page Description Group-Page