engine DODGE RAM 1500 1998 2.G Workshop Manual
[x] Cancel search | Manufacturer: DODGE, Model Year: 1998, Model line: RAM 1500, Model: DODGE RAM 1500 1998 2.GPages: 2627
Page 1237 of 2627
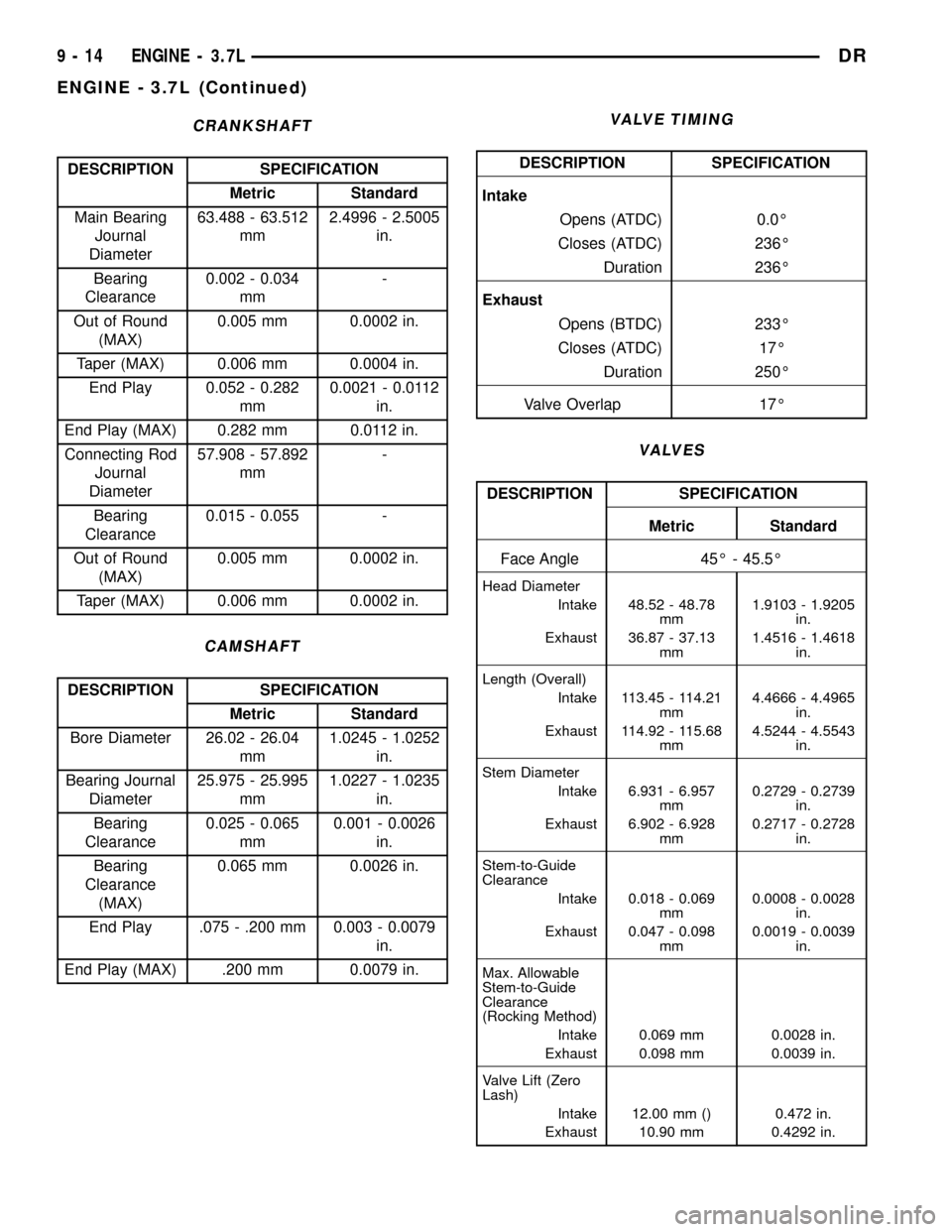
CRANKSHAFT
DESCRIPTION SPECIFICATION
Metric Standard
Main Bearing
Journal
Diameter63.488 - 63.512
mm2.4996 - 2.5005
in.
Bearing
Clearance0.002 - 0.034
mm-
Out of Round
(MAX)0.005 mm 0.0002 in.
Taper (MAX) 0.006 mm 0.0004 in.
End Play 0.052 - 0.282
mm0.0021 - 0.0112
in.
End Play (MAX) 0.282 mm 0.0112 in.
Connecting Rod
Journal
Diameter57.908 - 57.892
mm-
Bearing
Clearance0.015 - 0.055 -
Out of Round
(MAX)0.005 mm 0.0002 in.
Taper (MAX) 0.006 mm 0.0002 in.
CAMSHAFT
DESCRIPTION SPECIFICATION
Metric Standard
Bore Diameter 26.02 - 26.04
mm1.0245 - 1.0252
in.
Bearing Journal
Diameter25.975 - 25.995
mm1.0227 - 1.0235
in.
Bearing
Clearance0.025 - 0.065
mm0.001 - 0.0026
in.
Bearing
Clearance
(MAX)0.065 mm 0.0026 in.
End Play .075 - .200 mm 0.003 - 0.0079
in.
End Play (MAX) .200 mm 0.0079 in.
VALVE TIMING
DESCRIPTION SPECIFICATION
Intake
Opens (ATDC) 0.0É
Closes (ATDC) 236É
Duration 236É
Exhaust
Opens (BTDC) 233É
Closes (ATDC) 17É
Duration 250É
Valve Overlap 17É
VALVES
DESCRIPTION SPECIFICATION
Metric Standard
Face Angle 45É - 45.5É
Head Diameter
Intake 48.52 - 48.78
mm1.9103 - 1.9205
in.
Exhaust 36.87 - 37.13
mm1.4516 - 1.4618
in.
Length (Overall)
Intake 113.45 - 114.21
mm4.4666 - 4.4965
in.
Exhaust 114.92 - 115.68
mm4.5244 - 4.5543
in.
Stem Diameter
Intake 6.931 - 6.957
mm0.2729 - 0.2739
in.
Exhaust 6.902 - 6.928
mm0.2717 - 0.2728
in.
Stem-to-Guide
Clearance
Intake 0.018 - 0.069
mm0.0008 - 0.0028
in.
Exhaust 0.047 - 0.098
mm0.0019 - 0.0039
in.
Max. Allowable
Stem-to-Guide
Clearance
(Rocking Method)
Intake 0.069 mm 0.0028 in.
Exhaust 0.098 mm 0.0039 in.
Valve Lift (Zero
Lash)
Intake 12.00 mm () 0.472 in.
Exhaust 10.90 mm 0.4292 in.
9 - 14 ENGINE - 3.7LDR
ENGINE - 3.7L (Continued)
Page 1238 of 2627
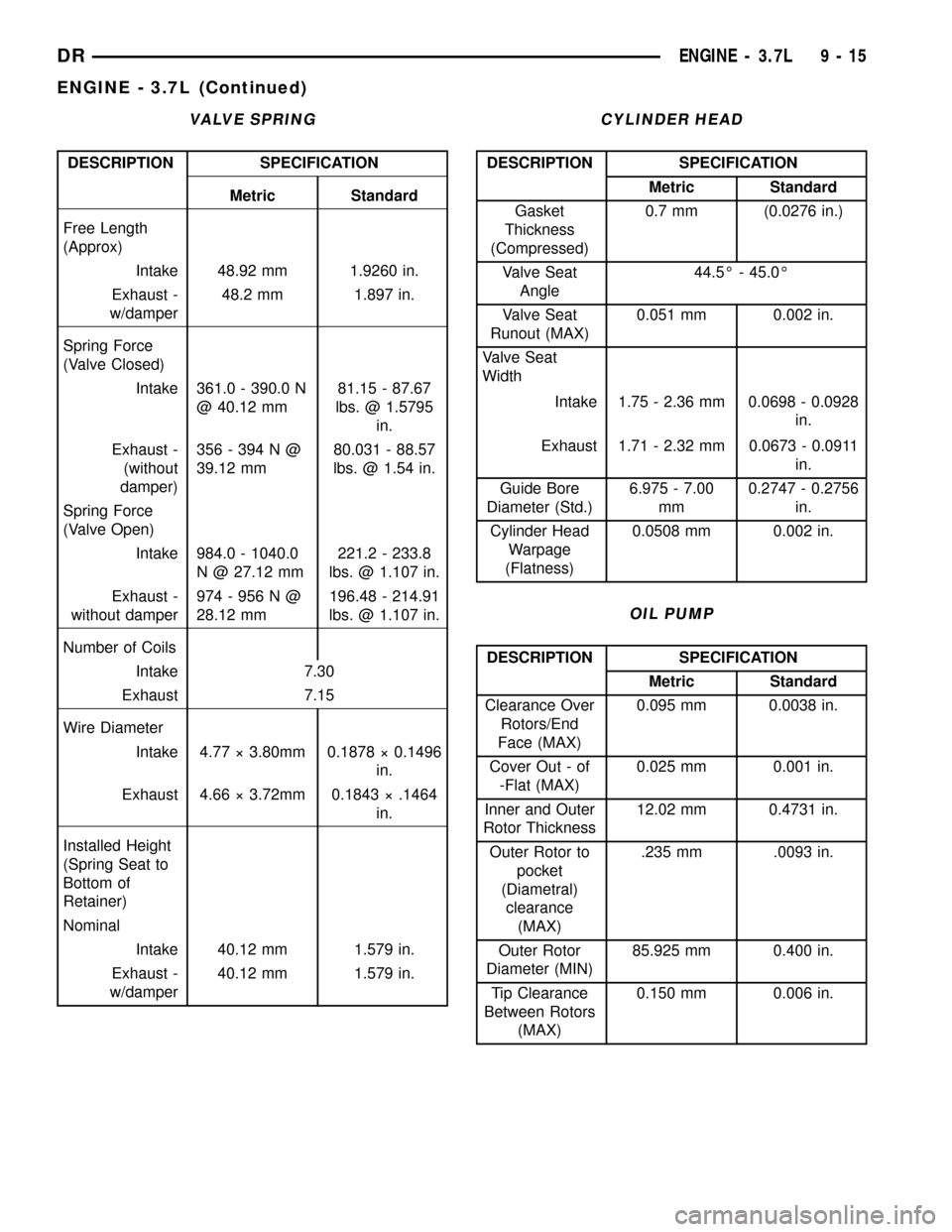
VALVE SPRING
DESCRIPTION SPECIFICATION
Metric Standard
Free Length
(Approx)
Intake 48.92 mm 1.9260 in.
Exhaust -
w/damper48.2 mm 1.897 in.
Spring Force
(Valve Closed)
Intake 361.0 - 390.0 N
@ 40.12 mm81.15 - 87.67
lbs. @ 1.5795
in.
Exhaust -
(without
damper)356-394N@
39.12 mm80.031 - 88.57
lbs. @ 1.54 in.
Spring Force
(Valve Open)
Intake 984.0 - 1040.0
N @ 27.12 mm221.2 - 233.8
lbs. @ 1.107 in.
Exhaust -
without damper974-956N@
28.12 mm196.48 - 214.91
lbs. @ 1.107 in.
Number of Coils
Intake 7.30
Exhaust 7.15
Wire Diameter
Intake 4.77 ý 3.80mm 0.1878 ý 0.1496
in.
Exhaust 4.66 ý 3.72mm 0.1843 ý .1464
in.
Installed Height
(Spring Seat to
Bottom of
Retainer)
Nominal
Intake 40.12 mm 1.579 in.
Exhaust -
w/damper40.12 mm 1.579 in.
CYLINDER HEAD
DESCRIPTION SPECIFICATION
Metric Standard
Gasket
Thickness
(Compressed)0.7 mm (0.0276 in.)
Valve Seat
Angle44.5É - 45.0É
Valve Seat
Runout (MAX)0.051 mm 0.002 in.
Valve Seat
Width
Intake 1.75 - 2.36 mm 0.0698 - 0.0928
in.
Exhaust 1.71 - 2.32 mm 0.0673 - 0.0911
in.
Guide Bore
Diameter (Std.)6.975 - 7.00
mm0.2747 - 0.2756
in.
Cylinder Head
Warpage
(Flatness)0.0508 mm 0.002 in.
OIL PUMP
DESCRIPTION SPECIFICATION
Metric Standard
Clearance Over
Rotors/End
Face (MAX)0.095 mm 0.0038 in.
Cover Out - of
-Flat (MAX)0.025 mm 0.001 in.
Inner and Outer
Rotor Thickness12.02 mm 0.4731 in.
Outer Rotor to
pocket
(Diametral)
clearance
(MAX).235 mm .0093 in.
Outer Rotor
Diameter (MIN)85.925 mm 0.400 in.
Tip Clearance
Between Rotors
(MAX)0.150 mm 0.006 in.
DRENGINE - 3.7L 9 - 15
ENGINE - 3.7L (Continued)
Page 1239 of 2627
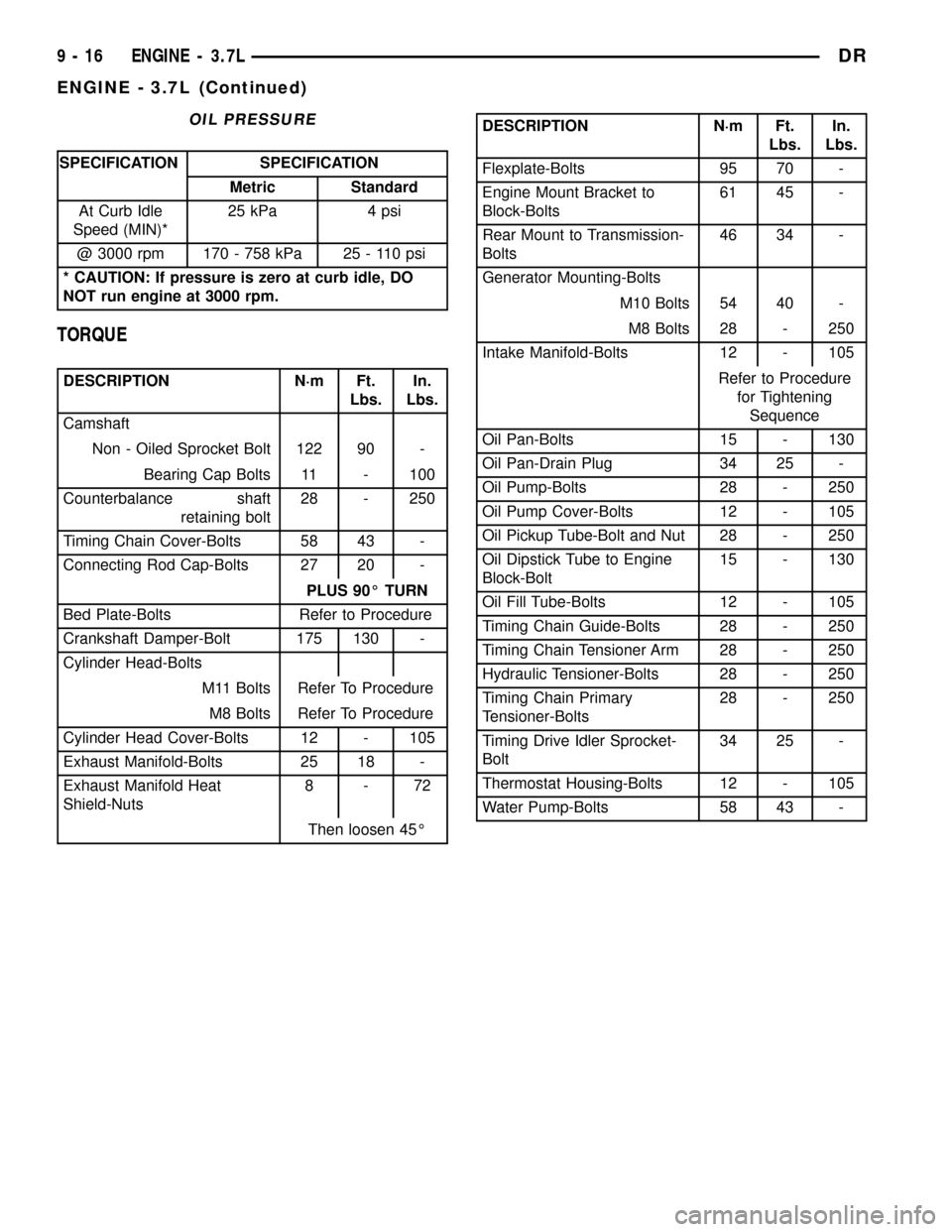
OIL PRESSURE
SPECIFICATION SPECIFICATION
Metric Standard
At Curb Idle
Speed (MIN)*25 kPa 4 psi
@ 3000 rpm 170 - 758 kPa 25 - 110 psi
* CAUTION: If pressure is zero at curb idle, DO
NOT run engine at 3000 rpm.
TORQUE
DESCRIPTION N´m Ft.
Lbs.In.
Lbs.
Camshaft
Non - Oiled Sprocket Bolt 122 90 -
Bearing Cap Bolts 11 - 100
Counterbalance shaft
retaining bolt28 - 250
Timing Chain Cover-Bolts 58 43 -
Connecting Rod Cap-Bolts 27 20 -
PLUS 90É TURN
Bed Plate-Bolts Refer to Procedure
Crankshaft Damper-Bolt 175 130 -
Cylinder Head-Bolts
M11 Bolts Refer To Procedure
M8 Bolts Refer To Procedure
Cylinder Head Cover-Bolts 12 - 105
Exhaust Manifold-Bolts 25 18 -
Exhaust Manifold Heat
Shield-Nuts8-72
Then loosen 45É
DESCRIPTION N´m Ft.
Lbs.In.
Lbs.
Flexplate-Bolts 95 70 -
Engine Mount Bracket to
Block-Bolts61 45 -
Rear Mount to Transmission-
Bolts46 34 -
Generator Mounting-Bolts
M10 Bolts 54 40 -
M8 Bolts 28 - 250
Intake Manifold-Bolts 12 - 105
Refer to Procedure
for Tightening
Sequence
Oil Pan-Bolts 15 - 130
Oil Pan-Drain Plug 34 25 -
Oil Pump-Bolts 28 - 250
Oil Pump Cover-Bolts 12 - 105
Oil Pickup Tube-Bolt and Nut 28 - 250
Oil Dipstick Tube to Engine
Block-Bolt15 - 130
Oil Fill Tube-Bolts 12 - 105
Timing Chain Guide-Bolts 28 - 250
Timing Chain Tensioner Arm 28 - 250
Hydraulic Tensioner-Bolts 28 - 250
Timing Chain Primary
Tensioner-Bolts28 - 250
Timing Drive Idler Sprocket-
Bolt34 25 -
Thermostat Housing-Bolts 12 - 105
Water Pump-Bolts 58 43 -
9 - 16 ENGINE - 3.7LDR
ENGINE - 3.7L (Continued)
Page 1240 of 2627
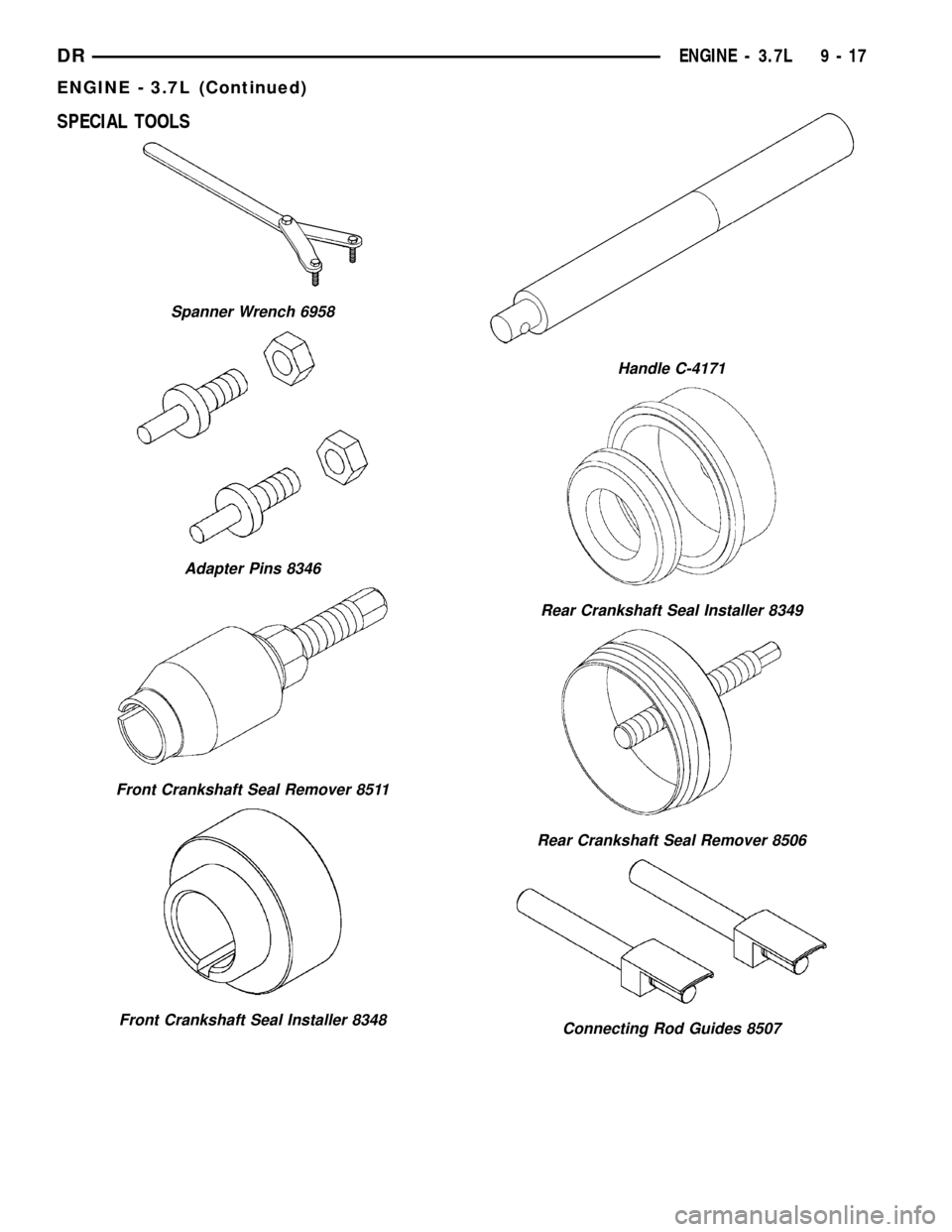
SPECIAL TOOLS
Spanner Wrench 6958
Adapter Pins 8346
Front Crankshaft Seal Remover 8511
Front Crankshaft Seal Installer 8348
Handle C-4171
Rear Crankshaft Seal Installer 8349
Rear Crankshaft Seal Remover 8506
Connecting Rod Guides 8507
DRENGINE - 3.7L 9 - 17
ENGINE - 3.7L (Continued)
Page 1241 of 2627
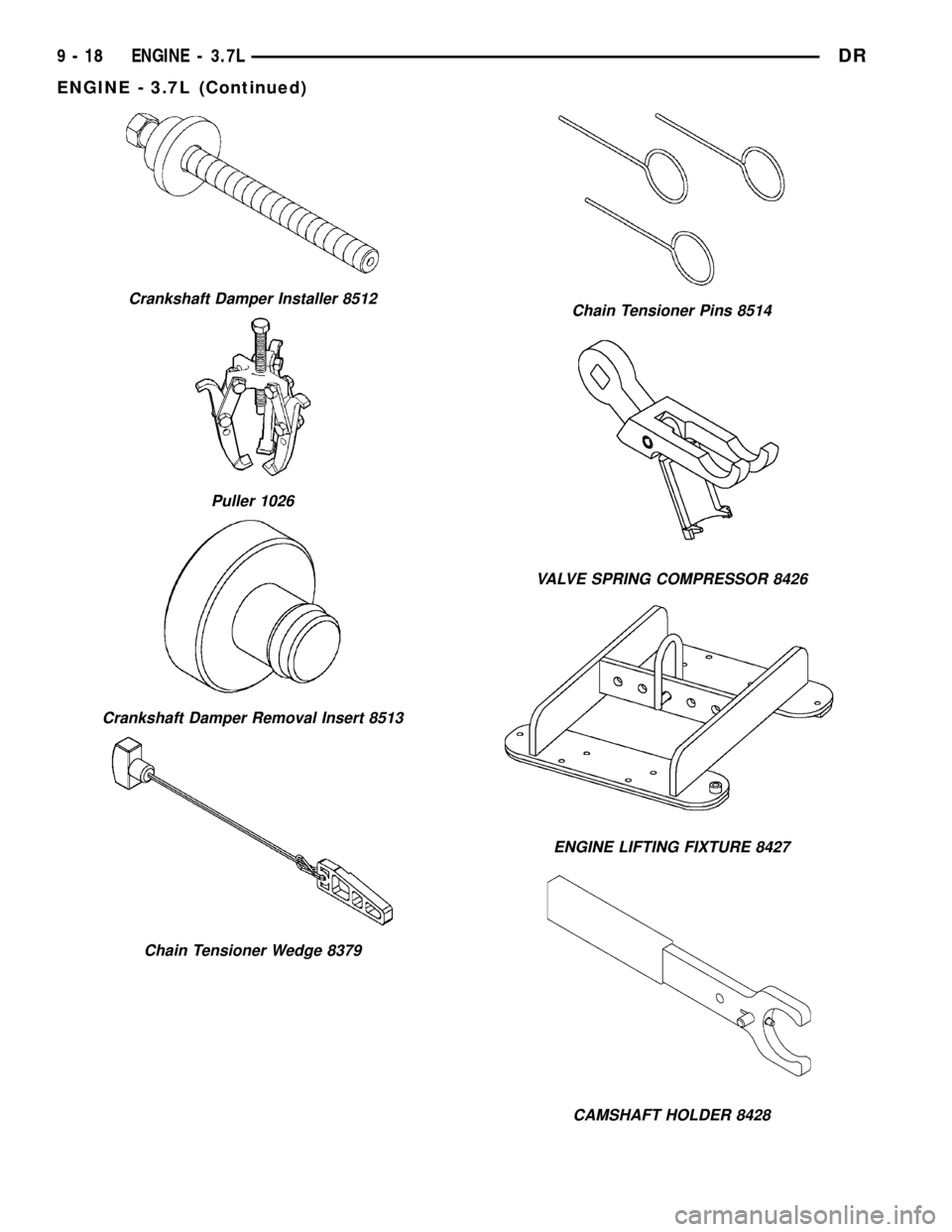
Crankshaft Damper Installer 8512
Puller 1026
Crankshaft Damper Removal Insert 8513
Chain Tensioner Wedge 8379
Chain Tensioner Pins 8514
VALVE SPRING COMPRESSOR 8426
ENGINE LIFTING FIXTURE 8427
CAMSHAFT HOLDER 8428
9 - 18 ENGINE - 3.7LDR
ENGINE - 3.7L (Continued)
Page 1242 of 2627
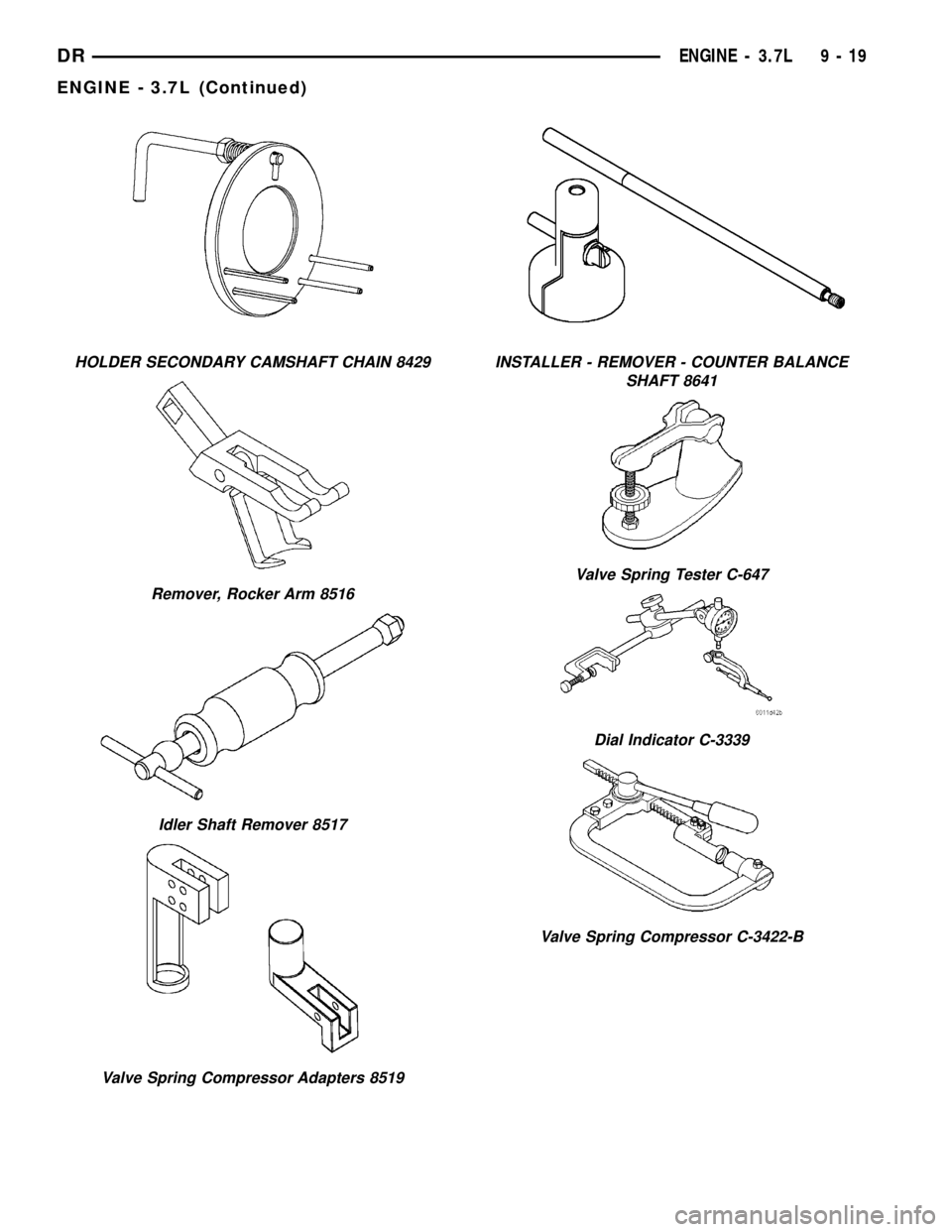
HOLDER SECONDARY CAMSHAFT CHAIN 8429
Remover, Rocker Arm 8516
Idler Shaft Remover 8517
Valve Spring Compressor Adapters 8519
INSTALLER - REMOVER - COUNTER BALANCE
SHAFT 8641
Valve Spring Tester C-647
Dial Indicator C-3339
Valve Spring Compressor C-3422-B
DRENGINE - 3.7L 9 - 19
ENGINE - 3.7L (Continued)
Page 1243 of 2627
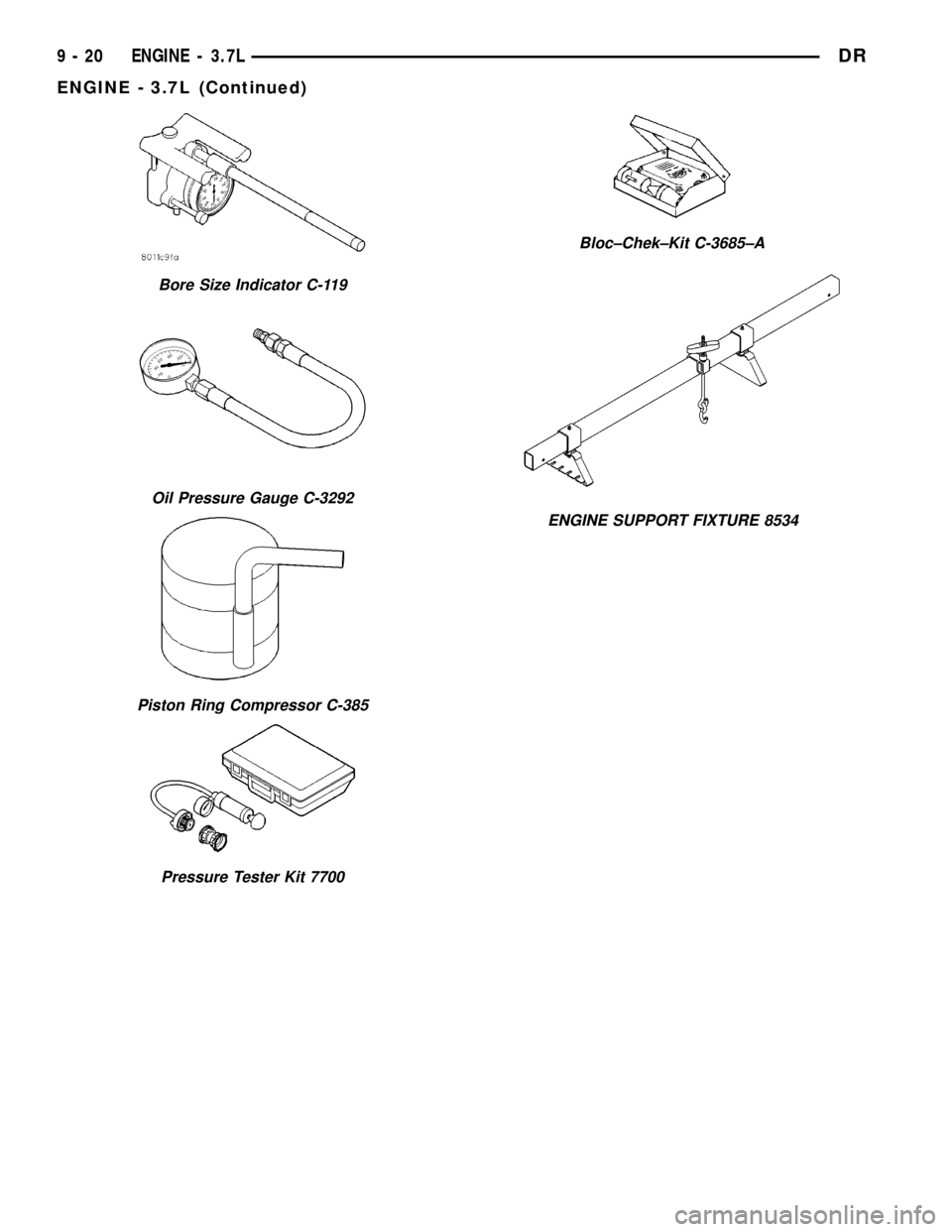
Bore Size Indicator C-119
Oil Pressure Gauge C-3292
Piston Ring Compressor C-385
Pressure Tester Kit 7700
Bloc±Chek±Kit C-3685±A
ENGINE SUPPORT FIXTURE 8534
9 - 20 ENGINE - 3.7LDR
ENGINE - 3.7L (Continued)
Page 1244 of 2627
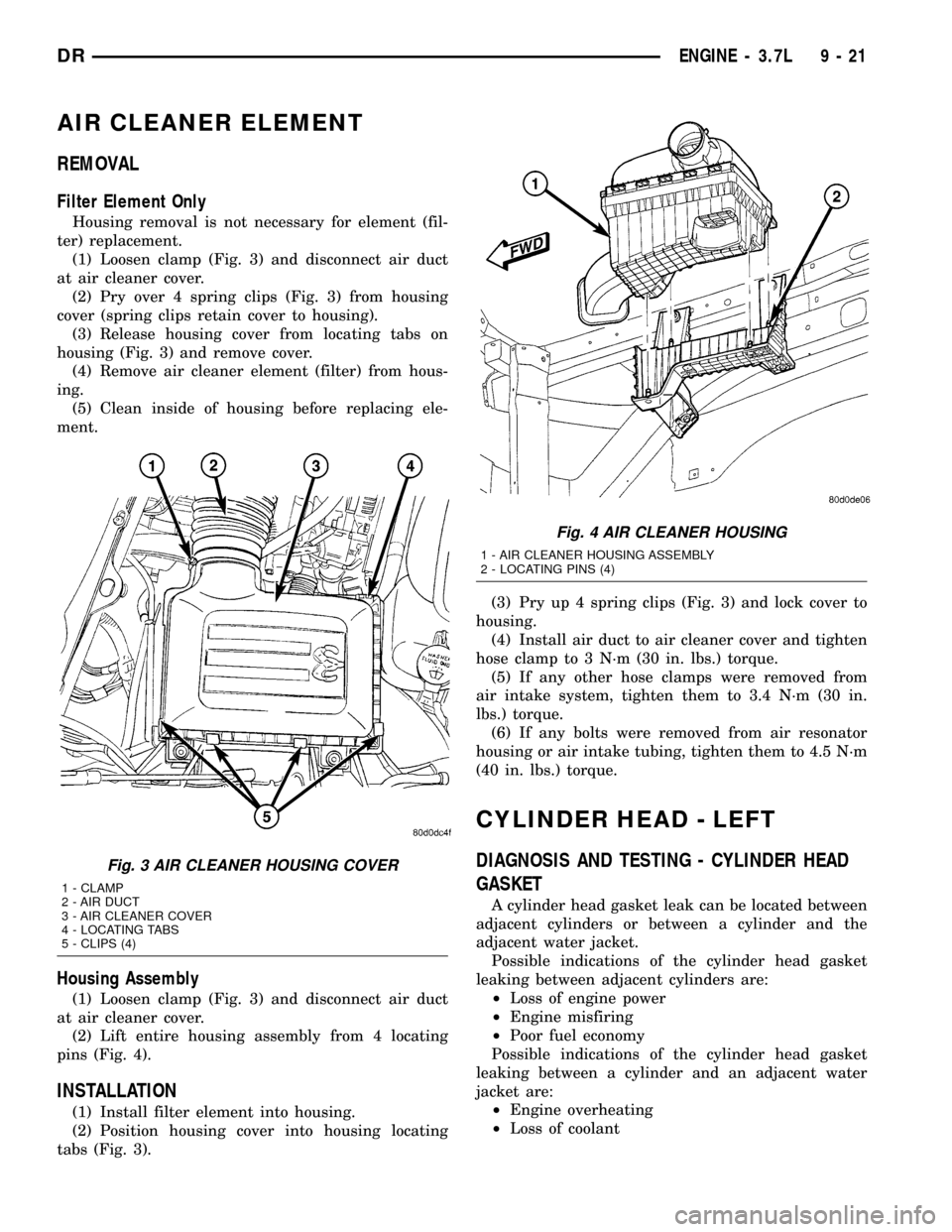
AIR CLEANER ELEMENT
REMOVAL
Filter Element Only
Housing removal is not necessary for element (fil-
ter) replacement.
(1) Loosen clamp (Fig. 3) and disconnect air duct
at air cleaner cover.
(2) Pry over 4 spring clips (Fig. 3) from housing
cover (spring clips retain cover to housing).
(3) Release housing cover from locating tabs on
housing (Fig. 3) and remove cover.
(4) Remove air cleaner element (filter) from hous-
ing.
(5) Clean inside of housing before replacing ele-
ment.
Housing Assembly
(1) Loosen clamp (Fig. 3) and disconnect air duct
at air cleaner cover.
(2) Lift entire housing assembly from 4 locating
pins (Fig. 4).
INSTALLATION
(1) Install filter element into housing.
(2) Position housing cover into housing locating
tabs (Fig. 3).(3) Pry up 4 spring clips (Fig. 3) and lock cover to
housing.
(4) Install air duct to air cleaner cover and tighten
hose clamp to 3 N´m (30 in. lbs.) torque.
(5) If any other hose clamps were removed from
air intake system, tighten them to 3.4 N´m (30 in.
lbs.) torque.
(6) If any bolts were removed from air resonator
housing or air intake tubing, tighten them to 4.5 N´m
(40 in. lbs.) torque.
CYLINDER HEAD - LEFT
DIAGNOSIS AND TESTING - CYLINDER HEAD
GASKET
A cylinder head gasket leak can be located between
adjacent cylinders or between a cylinder and the
adjacent water jacket.
Possible indications of the cylinder head gasket
leaking between adjacent cylinders are:
²Loss of engine power
²Engine misfiring
²Poor fuel economy
Possible indications of the cylinder head gasket
leaking between a cylinder and an adjacent water
jacket are:
²Engine overheating
²Loss of coolant
Fig. 3 AIR CLEANER HOUSING COVER
1 - CLAMP
2 - AIR DUCT
3 - AIR CLEANER COVER
4 - LOCATING TABS
5 - CLIPS (4)
Fig. 4 AIR CLEANER HOUSING
1 - AIR CLEANER HOUSING ASSEMBLY
2 - LOCATING PINS (4)
DRENGINE - 3.7L 9 - 21
Page 1245 of 2627
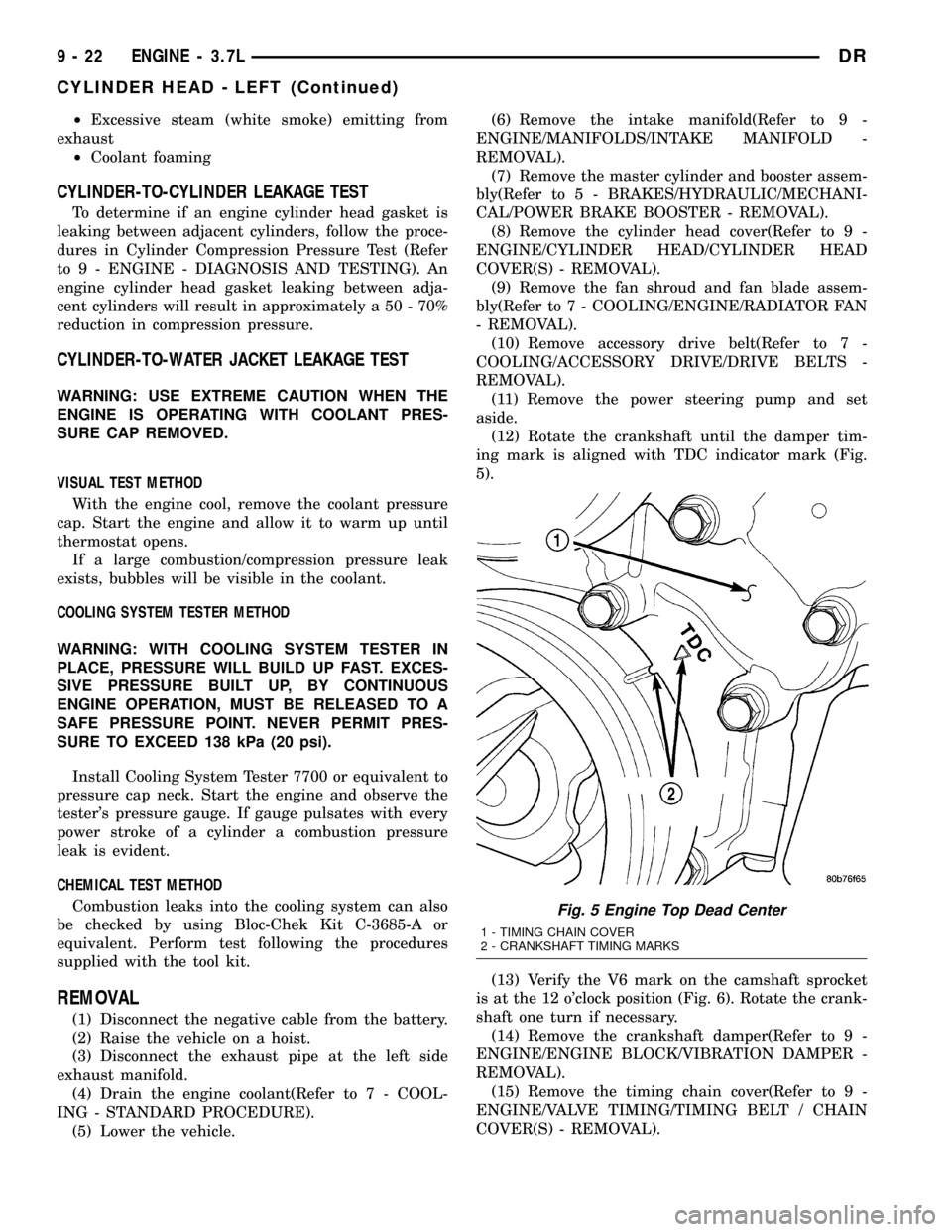
²Excessive steam (white smoke) emitting from
exhaust
²Coolant foaming
CYLINDER-TO-CYLINDER LEAKAGE TEST
To determine if an engine cylinder head gasket is
leaking between adjacent cylinders, follow the proce-
dures in Cylinder Compression Pressure Test (Refer
to 9 - ENGINE - DIAGNOSIS AND TESTING). An
engine cylinder head gasket leaking between adja-
cent cylinders will result in approximately a 50 - 70%
reduction in compression pressure.
CYLINDER-TO-WATER JACKET LEAKAGE TEST
WARNING: USE EXTREME CAUTION WHEN THE
ENGINE IS OPERATING WITH COOLANT PRES-
SURE CAP REMOVED.
VISUAL TEST METHOD
With the engine cool, remove the coolant pressure
cap. Start the engine and allow it to warm up until
thermostat opens.
If a large combustion/compression pressure leak
exists, bubbles will be visible in the coolant.
COOLING SYSTEM TESTER METHOD
WARNING: WITH COOLING SYSTEM TESTER IN
PLACE, PRESSURE WILL BUILD UP FAST. EXCES-
SIVE PRESSURE BUILT UP, BY CONTINUOUS
ENGINE OPERATION, MUST BE RELEASED TO A
SAFE PRESSURE POINT. NEVER PERMIT PRES-
SURE TO EXCEED 138 kPa (20 psi).
Install Cooling System Tester 7700 or equivalent to
pressure cap neck. Start the engine and observe the
tester's pressure gauge. If gauge pulsates with every
power stroke of a cylinder a combustion pressure
leak is evident.
CHEMICAL TEST METHOD
Combustion leaks into the cooling system can also
be checked by using Bloc-Chek Kit C-3685-A or
equivalent. Perform test following the procedures
supplied with the tool kit.
REMOVAL
(1) Disconnect the negative cable from the battery.
(2) Raise the vehicle on a hoist.
(3) Disconnect the exhaust pipe at the left side
exhaust manifold.
(4) Drain the engine coolant(Refer to 7 - COOL-
ING - STANDARD PROCEDURE).
(5) Lower the vehicle.(6) Remove the intake manifold(Refer to 9 -
ENGINE/MANIFOLDS/INTAKE MANIFOLD -
REMOVAL).
(7) Remove the master cylinder and booster assem-
bly(Refer to 5 - BRAKES/HYDRAULIC/MECHANI-
CAL/POWER BRAKE BOOSTER - REMOVAL).
(8) Remove the cylinder head cover(Refer to 9 -
ENGINE/CYLINDER HEAD/CYLINDER HEAD
COVER(S) - REMOVAL).
(9) Remove the fan shroud and fan blade assem-
bly(Refer to 7 - COOLING/ENGINE/RADIATOR FAN
- REMOVAL).
(10) Remove accessory drive belt(Refer to 7 -
COOLING/ACCESSORY DRIVE/DRIVE BELTS -
REMOVAL).
(11) Remove the power steering pump and set
aside.
(12) Rotate the crankshaft until the damper tim-
ing mark is aligned with TDC indicator mark (Fig.
5).
(13) Verify the V6 mark on the camshaft sprocket
is at the 12 o'clock position (Fig. 6). Rotate the crank-
shaft one turn if necessary.
(14) Remove the crankshaft damper(Refer to 9 -
ENGINE/ENGINE BLOCK/VIBRATION DAMPER -
REMOVAL).
(15) Remove the timing chain cover(Refer to 9 -
ENGINE/VALVE TIMING/TIMING BELT / CHAIN
COVER(S) - REMOVAL).
Fig. 5 Engine Top Dead Center
1 - TIMING CHAIN COVER
2 - CRANKSHAFT TIMING MARKS
9 - 22 ENGINE - 3.7LDR
CYLINDER HEAD - LEFT (Continued)
Page 1246 of 2627
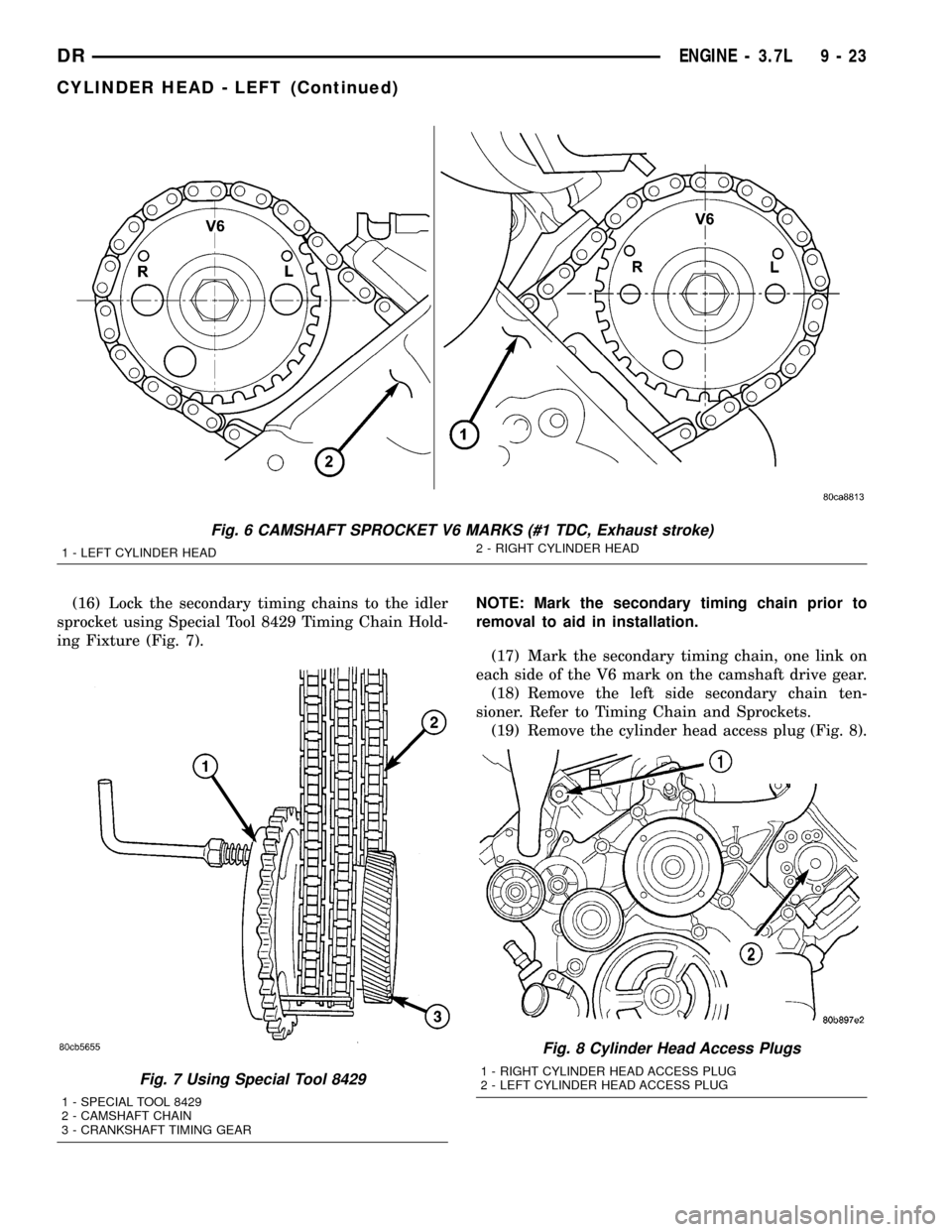
(16) Lock the secondary timing chains to the idler
sprocket using Special Tool 8429 Timing Chain Hold-
ing Fixture (Fig. 7).NOTE: Mark the secondary timing chain prior to
removal to aid in installation.
(17) Mark the secondary timing chain, one link on
each side of the V6 mark on the camshaft drive gear.
(18) Remove the left side secondary chain ten-
sioner. Refer to Timing Chain and Sprockets.
(19) Remove the cylinder head access plug (Fig. 8).
Fig. 6 CAMSHAFT SPROCKET V6 MARKS (#1 TDC, Exhaust stroke)
1 - LEFT CYLINDER HEAD2 - RIGHT CYLINDER HEAD
Fig. 7 Using Special Tool 8429
1 - SPECIAL TOOL 8429
2 - CAMSHAFT CHAIN
3 - CRANKSHAFT TIMING GEAR
Fig. 8 Cylinder Head Access Plugs
1 - RIGHT CYLINDER HEAD ACCESS PLUG
2 - LEFT CYLINDER HEAD ACCESS PLUG
DRENGINE - 3.7L 9 - 23
CYLINDER HEAD - LEFT (Continued)