sensor DODGE RAM 1500 1998 2.G Workshop Manual
[x] Cancel search | Manufacturer: DODGE, Model Year: 1998, Model line: RAM 1500, Model: DODGE RAM 1500 1998 2.GPages: 2627
Page 2509 of 2627
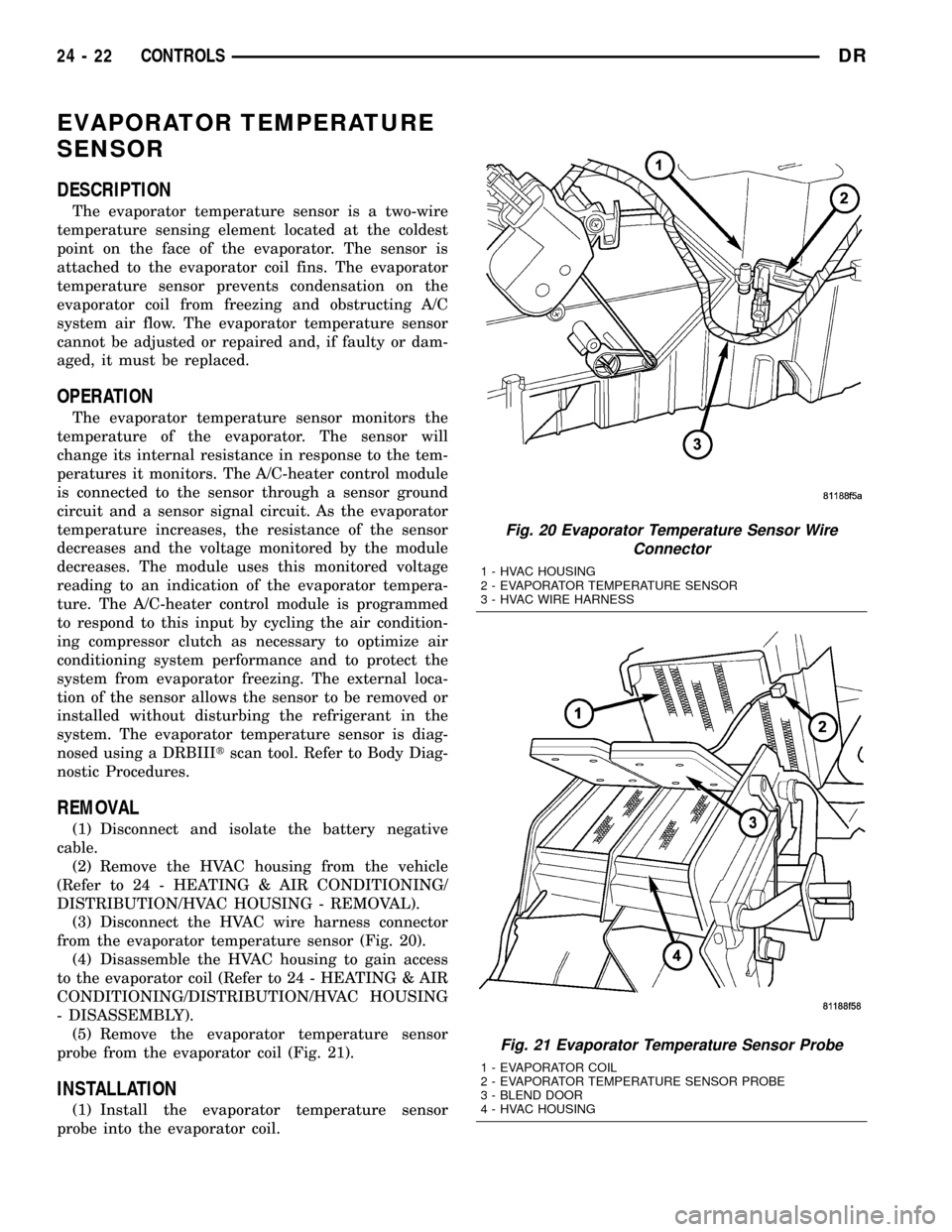
EVAPORATOR TEMPERATURE
SENSOR
DESCRIPTION
The evaporator temperature sensor is a two-wire
temperature sensing element located at the coldest
point on the face of the evaporator. The sensor is
attached to the evaporator coil fins. The evaporator
temperature sensor prevents condensation on the
evaporator coil from freezing and obstructing A/C
system air flow. The evaporator temperature sensor
cannot be adjusted or repaired and, if faulty or dam-
aged, it must be replaced.
OPERATION
The evaporator temperature sensor monitors the
temperature of the evaporator. The sensor will
change its internal resistance in response to the tem-
peratures it monitors. The A/C-heater control module
is connected to the sensor through a sensor ground
circuit and a sensor signal circuit. As the evaporator
temperature increases, the resistance of the sensor
decreases and the voltage monitored by the module
decreases. The module uses this monitored voltage
reading to an indication of the evaporator tempera-
ture. The A/C-heater control module is programmed
to respond to this input by cycling the air condition-
ing compressor clutch as necessary to optimize air
conditioning system performance and to protect the
system from evaporator freezing. The external loca-
tion of the sensor allows the sensor to be removed or
installed without disturbing the refrigerant in the
system. The evaporator temperature sensor is diag-
nosed using a DRBIIItscan tool. Refer to Body Diag-
nostic Procedures.
REMOVAL
(1) Disconnect and isolate the battery negative
cable.
(2) Remove the HVAC housing from the vehicle
(Refer to 24 - HEATING & AIR CONDITIONING/
DISTRIBUTION/HVAC HOUSING - REMOVAL).
(3) Disconnect the HVAC wire harness connector
from the evaporator temperature sensor (Fig. 20).
(4) Disassemble the HVAC housing to gain access
to the evaporator coil (Refer to 24 - HEATING & AIR
CONDITIONING/DISTRIBUTION/HVAC HOUSING
- DISASSEMBLY).
(5) Remove the evaporator temperature sensor
probe from the evaporator coil (Fig. 21).
INSTALLATION
(1) Install the evaporator temperature sensor
probe into the evaporator coil.
Fig. 20 Evaporator Temperature Sensor Wire
Connector
1 - HVAC HOUSING
2 - EVAPORATOR TEMPERATURE SENSOR
3 - HVAC WIRE HARNESS
Fig. 21 Evaporator Temperature Sensor Probe
1 - EVAPORATOR COIL
2 - EVAPORATOR TEMPERATURE SENSOR PROBE
3 - BLEND DOOR
4 - HVAC HOUSING
24 - 22 CONTROLSDR
Page 2510 of 2627
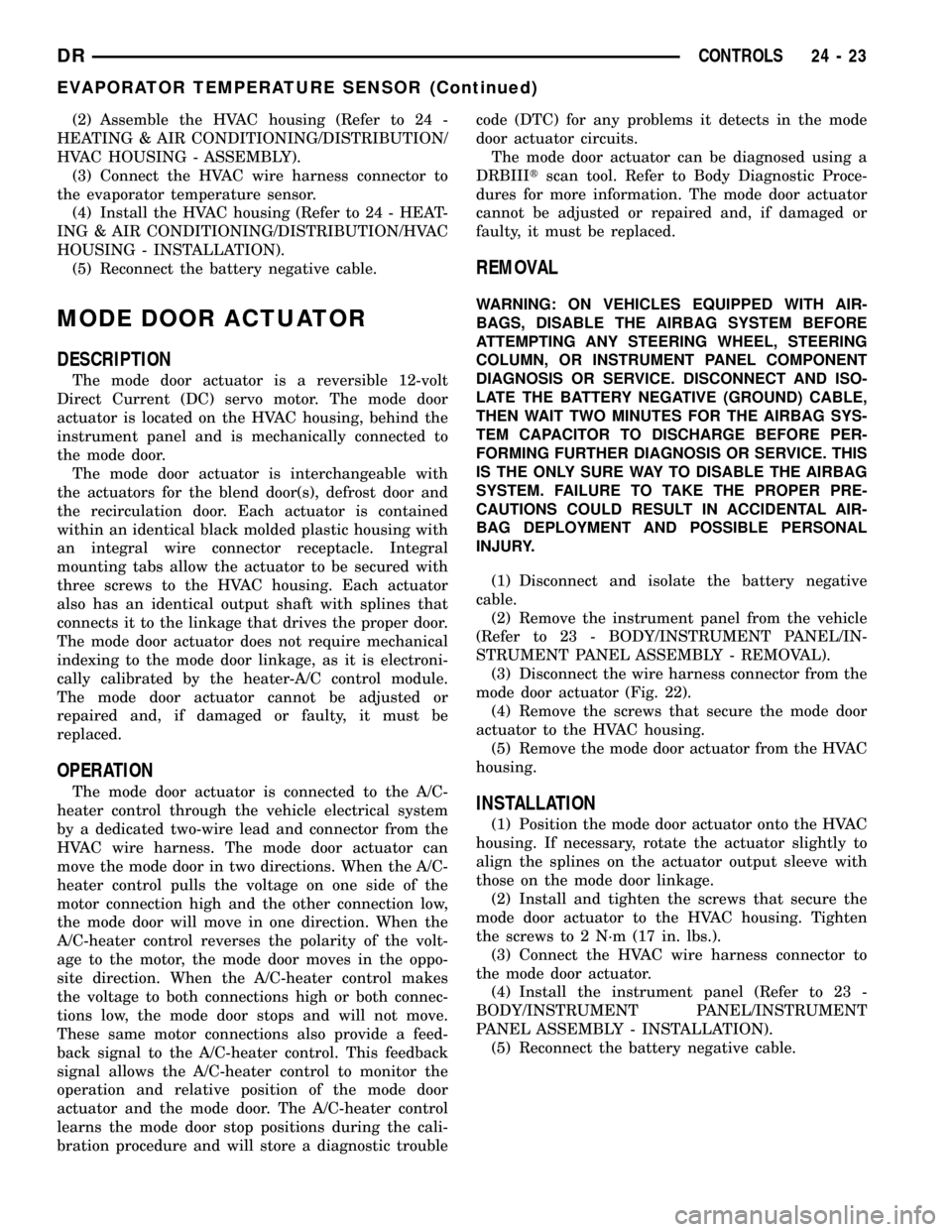
(2) Assemble the HVAC housing (Refer to 24 -
HEATING & AIR CONDITIONING/DISTRIBUTION/
HVAC HOUSING - ASSEMBLY).
(3) Connect the HVAC wire harness connector to
the evaporator temperature sensor.
(4) Install the HVAC housing (Refer to 24 - HEAT-
ING & AIR CONDITIONING/DISTRIBUTION/HVAC
HOUSING - INSTALLATION).
(5) Reconnect the battery negative cable.
MODE DOOR ACTUATOR
DESCRIPTION
The mode door actuator is a reversible 12-volt
Direct Current (DC) servo motor. The mode door
actuator is located on the HVAC housing, behind the
instrument panel and is mechanically connected to
the mode door.
The mode door actuator is interchangeable with
the actuators for the blend door(s), defrost door and
the recirculation door. Each actuator is contained
within an identical black molded plastic housing with
an integral wire connector receptacle. Integral
mounting tabs allow the actuator to be secured with
three screws to the HVAC housing. Each actuator
also has an identical output shaft with splines that
connects it to the linkage that drives the proper door.
The mode door actuator does not require mechanical
indexing to the mode door linkage, as it is electroni-
cally calibrated by the heater-A/C control module.
The mode door actuator cannot be adjusted or
repaired and, if damaged or faulty, it must be
replaced.
OPERATION
The mode door actuator is connected to the A/C-
heater control through the vehicle electrical system
by a dedicated two-wire lead and connector from the
HVAC wire harness. The mode door actuator can
move the mode door in two directions. When the A/C-
heater control pulls the voltage on one side of the
motor connection high and the other connection low,
the mode door will move in one direction. When the
A/C-heater control reverses the polarity of the volt-
age to the motor, the mode door moves in the oppo-
site direction. When the A/C-heater control makes
the voltage to both connections high or both connec-
tions low, the mode door stops and will not move.
These same motor connections also provide a feed-
back signal to the A/C-heater control. This feedback
signal allows the A/C-heater control to monitor the
operation and relative position of the mode door
actuator and the mode door. The A/C-heater control
learns the mode door stop positions during the cali-
bration procedure and will store a diagnostic troublecode (DTC) for any problems it detects in the mode
door actuator circuits.
The mode door actuator can be diagnosed using a
DRBIIItscan tool. Refer to Body Diagnostic Proce-
dures for more information. The mode door actuator
cannot be adjusted or repaired and, if damaged or
faulty, it must be replaced.
REMOVAL
WARNING: ON VEHICLES EQUIPPED WITH AIR-
BAGS, DISABLE THE AIRBAG SYSTEM BEFORE
ATTEMPTING ANY STEERING WHEEL, STEERING
COLUMN, OR INSTRUMENT PANEL COMPONENT
DIAGNOSIS OR SERVICE. DISCONNECT AND ISO-
LATE THE BATTERY NEGATIVE (GROUND) CABLE,
THEN WAIT TWO MINUTES FOR THE AIRBAG SYS-
TEM CAPACITOR TO DISCHARGE BEFORE PER-
FORMING FURTHER DIAGNOSIS OR SERVICE. THIS
IS THE ONLY SURE WAY TO DISABLE THE AIRBAG
SYSTEM. FAILURE TO TAKE THE PROPER PRE-
CAUTIONS COULD RESULT IN ACCIDENTAL AIR-
BAG DEPLOYMENT AND POSSIBLE PERSONAL
INJURY.
(1) Disconnect and isolate the battery negative
cable.
(2) Remove the instrument panel from the vehicle
(Refer to 23 - BODY/INSTRUMENT PANEL/IN-
STRUMENT PANEL ASSEMBLY - REMOVAL).
(3) Disconnect the wire harness connector from the
mode door actuator (Fig. 22).
(4) Remove the screws that secure the mode door
actuator to the HVAC housing.
(5) Remove the mode door actuator from the HVAC
housing.
INSTALLATION
(1) Position the mode door actuator onto the HVAC
housing. If necessary, rotate the actuator slightly to
align the splines on the actuator output sleeve with
those on the mode door linkage.
(2) Install and tighten the screws that secure the
mode door actuator to the HVAC housing. Tighten
the screws to 2 N´m (17 in. lbs.).
(3) Connect the HVAC wire harness connector to
the mode door actuator.
(4) Install the instrument panel (Refer to 23 -
BODY/INSTRUMENT PANEL/INSTRUMENT
PANEL ASSEMBLY - INSTALLATION).
(5) Reconnect the battery negative cable.
DRCONTROLS 24 - 23
EVAPORATOR TEMPERATURE SENSOR (Continued)
Page 2514 of 2627
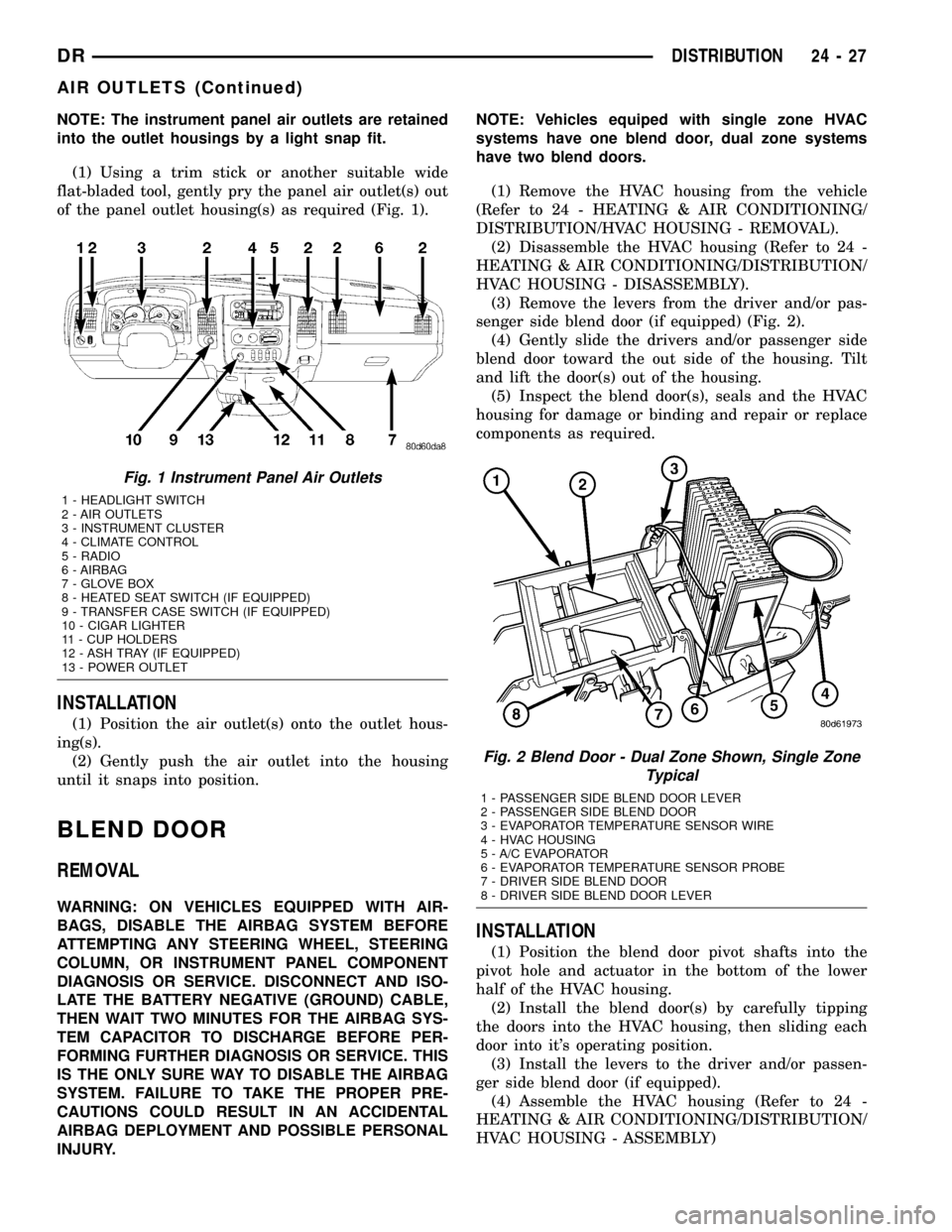
NOTE: The instrument panel air outlets are retained
into the outlet housings by a light snap fit.
(1) Using a trim stick or another suitable wide
flat-bladed tool, gently pry the panel air outlet(s) out
of the panel outlet housing(s) as required (Fig. 1).
INSTALLATION
(1) Position the air outlet(s) onto the outlet hous-
ing(s).
(2) Gently push the air outlet into the housing
until it snaps into position.
BLEND DOOR
REMOVAL
WARNING: ON VEHICLES EQUIPPED WITH AIR-
BAGS, DISABLE THE AIRBAG SYSTEM BEFORE
ATTEMPTING ANY STEERING WHEEL, STEERING
COLUMN, OR INSTRUMENT PANEL COMPONENT
DIAGNOSIS OR SERVICE. DISCONNECT AND ISO-
LATE THE BATTERY NEGATIVE (GROUND) CABLE,
THEN WAIT TWO MINUTES FOR THE AIRBAG SYS-
TEM CAPACITOR TO DISCHARGE BEFORE PER-
FORMING FURTHER DIAGNOSIS OR SERVICE. THIS
IS THE ONLY SURE WAY TO DISABLE THE AIRBAG
SYSTEM. FAILURE TO TAKE THE PROPER PRE-
CAUTIONS COULD RESULT IN AN ACCIDENTAL
AIRBAG DEPLOYMENT AND POSSIBLE PERSONAL
INJURY.NOTE: Vehicles equiped with single zone HVAC
systems have one blend door, dual zone systems
have two blend doors.
(1) Remove the HVAC housing from the vehicle
(Refer to 24 - HEATING & AIR CONDITIONING/
DISTRIBUTION/HVAC HOUSING - REMOVAL).
(2) Disassemble the HVAC housing (Refer to 24 -
HEATING & AIR CONDITIONING/DISTRIBUTION/
HVAC HOUSING - DISASSEMBLY).
(3) Remove the levers from the driver and/or pas-
senger side blend door (if equipped) (Fig. 2).
(4) Gently slide the drivers and/or passenger side
blend door toward the out side of the housing. Tilt
and lift the door(s) out of the housing.
(5) Inspect the blend door(s), seals and the HVAC
housing for damage or binding and repair or replace
components as required.
INSTALLATION
(1) Position the blend door pivot shafts into the
pivot hole and actuator in the bottom of the lower
half of the HVAC housing.
(2) Install the blend door(s) by carefully tipping
the doors into the HVAC housing, then sliding each
door into it's operating position.
(3) Install the levers to the driver and/or passen-
ger side blend door (if equipped).
(4) Assemble the HVAC housing (Refer to 24 -
HEATING & AIR CONDITIONING/DISTRIBUTION/
HVAC HOUSING - ASSEMBLY)
Fig. 1 Instrument Panel Air Outlets
1 - HEADLIGHT SWITCH
2 - AIR OUTLETS
3 - INSTRUMENT CLUSTER
4 - CLIMATE CONTROL
5 - RADIO
6 - AIRBAG
7 - GLOVE BOX
8 - HEATED SEAT SWITCH (IF EQUIPPED)
9 - TRANSFER CASE SWITCH (IF EQUIPPED)
10 - CIGAR LIGHTER
11 - CUP HOLDERS
12 - ASH TRAY (IF EQUIPPED)
13 - POWER OUTLET
Fig. 2 Blend Door - Dual Zone Shown, Single Zone
Typical
1 - PASSENGER SIDE BLEND DOOR LEVER
2 - PASSENGER SIDE BLEND DOOR
3 - EVAPORATOR TEMPERATURE SENSOR WIRE
4 - HVAC HOUSING
5 - A/C EVAPORATOR
6 - EVAPORATOR TEMPERATURE SENSOR PROBE
7 - DRIVER SIDE BLEND DOOR
8 - DRIVER SIDE BLEND DOOR LEVER
DRDISTRIBUTION 24 - 27
AIR OUTLETS (Continued)
Page 2522 of 2627
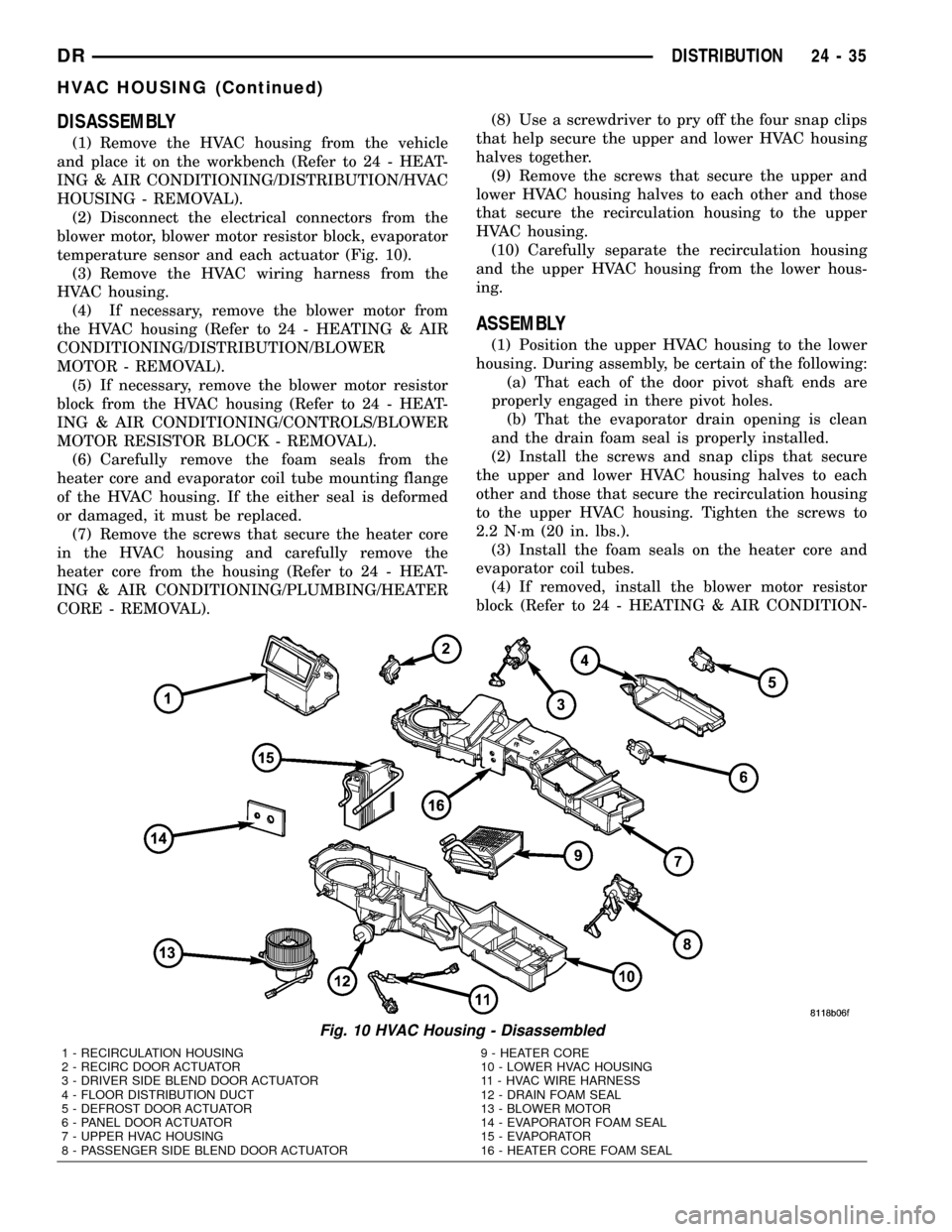
DISASSEMBLY
(1) Remove the HVAC housing from the vehicle
and place it on the workbench (Refer to 24 - HEAT-
ING & AIR CONDITIONING/DISTRIBUTION/HVAC
HOUSING - REMOVAL).
(2) Disconnect the electrical connectors from the
blower motor, blower motor resistor block, evaporator
temperature sensor and each actuator (Fig. 10).
(3) Remove the HVAC wiring harness from the
HVAC housing.
(4) If necessary, remove the blower motor from
the HVAC housing (Refer to 24 - HEATING & AIR
CONDITIONING/DISTRIBUTION/BLOWER
MOTOR - REMOVAL).
(5) If necessary, remove the blower motor resistor
block from the HVAC housing (Refer to 24 - HEAT-
ING & AIR CONDITIONING/CONTROLS/BLOWER
MOTOR RESISTOR BLOCK - REMOVAL).
(6) Carefully remove the foam seals from the
heater core and evaporator coil tube mounting flange
of the HVAC housing. If the either seal is deformed
or damaged, it must be replaced.
(7) Remove the screws that secure the heater core
in the HVAC housing and carefully remove the
heater core from the housing (Refer to 24 - HEAT-
ING & AIR CONDITIONING/PLUMBING/HEATER
CORE - REMOVAL).(8) Use a screwdriver to pry off the four snap clips
that help secure the upper and lower HVAC housing
halves together.
(9) Remove the screws that secure the upper and
lower HVAC housing halves to each other and those
that secure the recirculation housing to the upper
HVAC housing.
(10) Carefully separate the recirculation housing
and the upper HVAC housing from the lower hous-
ing.
ASSEMBLY
(1) Position the upper HVAC housing to the lower
housing. During assembly, be certain of the following:
(a) That each of the door pivot shaft ends are
properly engaged in there pivot holes.
(b) That the evaporator drain opening is clean
and the drain foam seal is properly installed.
(2) Install the screws and snap clips that secure
the upper and lower HVAC housing halves to each
other and those that secure the recirculation housing
to the upper HVAC housing. Tighten the screws to
2.2 N´m (20 in. lbs.).
(3) Install the foam seals on the heater core and
evaporator coil tubes.
(4) If removed, install the blower motor resistor
block (Refer to 24 - HEATING & AIR CONDITION-
Fig. 10 HVAC Housing - Disassembled
1 - RECIRCULATION HOUSING
2 - RECIRC DOOR ACTUATOR
3 - DRIVER SIDE BLEND DOOR ACTUATOR
4 - FLOOR DISTRIBUTION DUCT
5 - DEFROST DOOR ACTUATOR
6 - PANEL DOOR ACTUATOR
7 - UPPER HVAC HOUSING
8 - PASSENGER SIDE BLEND DOOR ACTUATOR9 - HEATER CORE
10 - LOWER HVAC HOUSING
11 - HVAC WIRE HARNESS
12 - DRAIN FOAM SEAL
13 - BLOWER MOTOR
14 - EVAPORATOR FOAM SEAL
15 - EVAPORATOR
16 - HEATER CORE FOAM SEAL
DRDISTRIBUTION 24 - 35
HVAC HOUSING (Continued)
Page 2523 of 2627
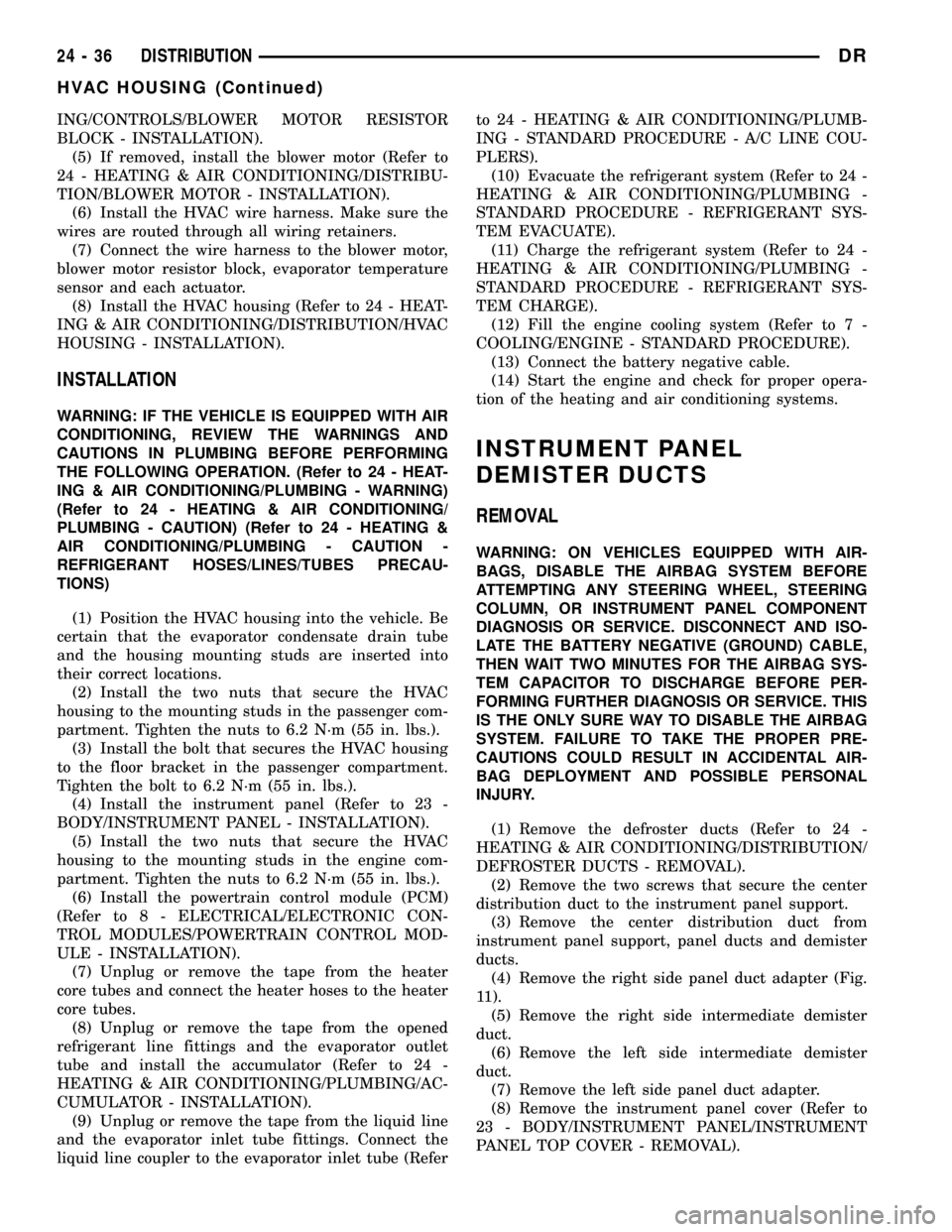
ING/CONTROLS/BLOWER MOTOR RESISTOR
BLOCK - INSTALLATION).
(5) If removed, install the blower motor (Refer to
24 - HEATING & AIR CONDITIONING/DISTRIBU-
TION/BLOWER MOTOR - INSTALLATION).
(6) Install the HVAC wire harness. Make sure the
wires are routed through all wiring retainers.
(7) Connect the wire harness to the blower motor,
blower motor resistor block, evaporator temperature
sensor and each actuator.
(8) Install the HVAC housing (Refer to 24 - HEAT-
ING & AIR CONDITIONING/DISTRIBUTION/HVAC
HOUSING - INSTALLATION).
INSTALLATION
WARNING: IF THE VEHICLE IS EQUIPPED WITH AIR
CONDITIONING, REVIEW THE WARNINGS AND
CAUTIONS IN PLUMBING BEFORE PERFORMING
THE FOLLOWING OPERATION. (Refer to 24 - HEAT-
ING & AIR CONDITIONING/PLUMBING - WARNING)
(Refer to 24 - HEATING & AIR CONDITIONING/
PLUMBING - CAUTION) (Refer to 24 - HEATING &
AIR CONDITIONING/PLUMBING - CAUTION -
REFRIGERANT HOSES/LINES/TUBES PRECAU-
TIONS)
(1) Position the HVAC housing into the vehicle. Be
certain that the evaporator condensate drain tube
and the housing mounting studs are inserted into
their correct locations.
(2) Install the two nuts that secure the HVAC
housing to the mounting studs in the passenger com-
partment. Tighten the nuts to 6.2 N´m (55 in. lbs.).
(3) Install the bolt that secures the HVAC housing
to the floor bracket in the passenger compartment.
Tighten the bolt to 6.2 N´m (55 in. lbs.).
(4) Install the instrument panel (Refer to 23 -
BODY/INSTRUMENT PANEL - INSTALLATION).
(5) Install the two nuts that secure the HVAC
housing to the mounting studs in the engine com-
partment. Tighten the nuts to 6.2 N´m (55 in. lbs.).
(6) Install the powertrain control module (PCM)
(Refer to 8 - ELECTRICAL/ELECTRONIC CON-
TROL MODULES/POWERTRAIN CONTROL MOD-
ULE - INSTALLATION).
(7) Unplug or remove the tape from the heater
core tubes and connect the heater hoses to the heater
core tubes.
(8) Unplug or remove the tape from the opened
refrigerant line fittings and the evaporator outlet
tube and install the accumulator (Refer to 24 -
HEATING & AIR CONDITIONING/PLUMBING/AC-
CUMULATOR - INSTALLATION).
(9) Unplug or remove the tape from the liquid line
and the evaporator inlet tube fittings. Connect the
liquid line coupler to the evaporator inlet tube (Referto 24 - HEATING & AIR CONDITIONING/PLUMB-
ING - STANDARD PROCEDURE - A/C LINE COU-
PLERS).
(10) Evacuate the refrigerant system (Refer to 24 -
HEATING & AIR CONDITIONING/PLUMBING -
STANDARD PROCEDURE - REFRIGERANT SYS-
TEM EVACUATE).
(11) Charge the refrigerant system (Refer to 24 -
HEATING & AIR CONDITIONING/PLUMBING -
STANDARD PROCEDURE - REFRIGERANT SYS-
TEM CHARGE).
(12) Fill the engine cooling system (Refer to 7 -
COOLING/ENGINE - STANDARD PROCEDURE).
(13) Connect the battery negative cable.
(14) Start the engine and check for proper opera-
tion of the heating and air conditioning systems.
INSTRUMENT PANEL
DEMISTER DUCTS
REMOVAL
WARNING: ON VEHICLES EQUIPPED WITH AIR-
BAGS, DISABLE THE AIRBAG SYSTEM BEFORE
ATTEMPTING ANY STEERING WHEEL, STEERING
COLUMN, OR INSTRUMENT PANEL COMPONENT
DIAGNOSIS OR SERVICE. DISCONNECT AND ISO-
LATE THE BATTERY NEGATIVE (GROUND) CABLE,
THEN WAIT TWO MINUTES FOR THE AIRBAG SYS-
TEM CAPACITOR TO DISCHARGE BEFORE PER-
FORMING FURTHER DIAGNOSIS OR SERVICE. THIS
IS THE ONLY SURE WAY TO DISABLE THE AIRBAG
SYSTEM. FAILURE TO TAKE THE PROPER PRE-
CAUTIONS COULD RESULT IN ACCIDENTAL AIR-
BAG DEPLOYMENT AND POSSIBLE PERSONAL
INJURY.
(1) Remove the defroster ducts (Refer to 24 -
HEATING & AIR CONDITIONING/DISTRIBUTION/
DEFROSTER DUCTS - REMOVAL).
(2) Remove the two screws that secure the center
distribution duct to the instrument panel support.
(3) Remove the center distribution duct from
instrument panel support, panel ducts and demister
ducts.
(4) Remove the right side panel duct adapter (Fig.
11).
(5) Remove the right side intermediate demister
duct.
(6) Remove the left side intermediate demister
duct.
(7) Remove the left side panel duct adapter.
(8) Remove the instrument panel cover (Refer to
23 - BODY/INSTRUMENT PANEL/INSTRUMENT
PANEL TOP COVER - REMOVAL).
24 - 36 DISTRIBUTIONDR
HVAC HOUSING (Continued)
Page 2547 of 2627
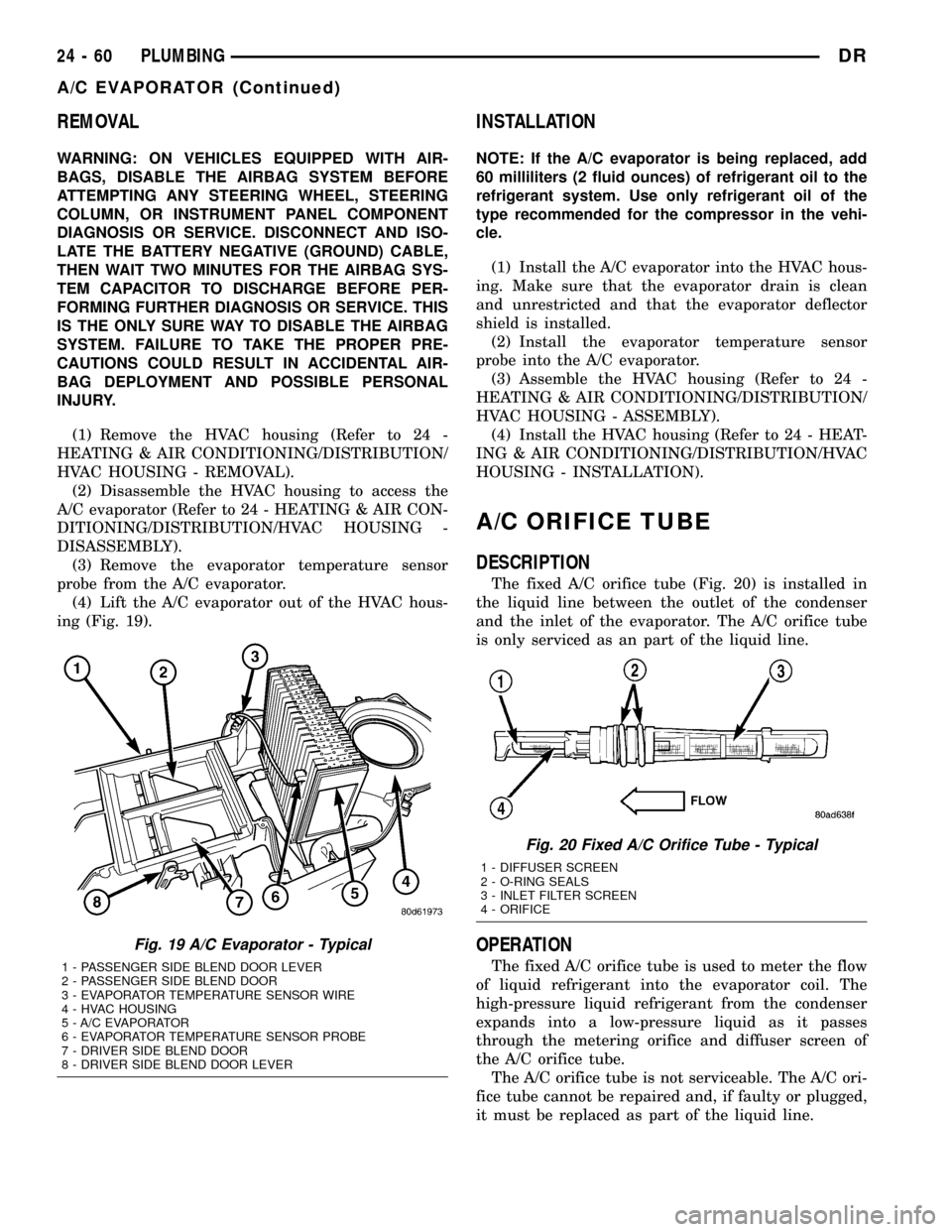
REMOVAL
WARNING: ON VEHICLES EQUIPPED WITH AIR-
BAGS, DISABLE THE AIRBAG SYSTEM BEFORE
ATTEMPTING ANY STEERING WHEEL, STEERING
COLUMN, OR INSTRUMENT PANEL COMPONENT
DIAGNOSIS OR SERVICE. DISCONNECT AND ISO-
LATE THE BATTERY NEGATIVE (GROUND) CABLE,
THEN WAIT TWO MINUTES FOR THE AIRBAG SYS-
TEM CAPACITOR TO DISCHARGE BEFORE PER-
FORMING FURTHER DIAGNOSIS OR SERVICE. THIS
IS THE ONLY SURE WAY TO DISABLE THE AIRBAG
SYSTEM. FAILURE TO TAKE THE PROPER PRE-
CAUTIONS COULD RESULT IN ACCIDENTAL AIR-
BAG DEPLOYMENT AND POSSIBLE PERSONAL
INJURY.
(1) Remove the HVAC housing (Refer to 24 -
HEATING & AIR CONDITIONING/DISTRIBUTION/
HVAC HOUSING - REMOVAL).
(2) Disassemble the HVAC housing to access the
A/C evaporator (Refer to 24 - HEATING & AIR CON-
DITIONING/DISTRIBUTION/HVAC HOUSING -
DISASSEMBLY).
(3) Remove the evaporator temperature sensor
probe from the A/C evaporator.
(4) Lift the A/C evaporator out of the HVAC hous-
ing (Fig. 19).
INSTALLATION
NOTE: If the A/C evaporator is being replaced, add
60 milliliters (2 fluid ounces) of refrigerant oil to the
refrigerant system. Use only refrigerant oil of the
type recommended for the compressor in the vehi-
cle.
(1) Install the A/C evaporator into the HVAC hous-
ing. Make sure that the evaporator drain is clean
and unrestricted and that the evaporator deflector
shield is installed.
(2) Install the evaporator temperature sensor
probe into the A/C evaporator.
(3) Assemble the HVAC housing (Refer to 24 -
HEATING & AIR CONDITIONING/DISTRIBUTION/
HVAC HOUSING - ASSEMBLY).
(4) Install the HVAC housing (Refer to 24 - HEAT-
ING & AIR CONDITIONING/DISTRIBUTION/HVAC
HOUSING - INSTALLATION).
A/C ORIFICE TUBE
DESCRIPTION
The fixed A/C orifice tube (Fig. 20) is installed in
the liquid line between the outlet of the condenser
and the inlet of the evaporator. The A/C orifice tube
is only serviced as an part of the liquid line.
OPERATION
The fixed A/C orifice tube is used to meter the flow
of liquid refrigerant into the evaporator coil. The
high-pressure liquid refrigerant from the condenser
expands into a low-pressure liquid as it passes
through the metering orifice and diffuser screen of
the A/C orifice tube.
The A/C orifice tube is not serviceable. The A/C ori-
fice tube cannot be repaired and, if faulty or plugged,
it must be replaced as part of the liquid line.
Fig. 19 A/C Evaporator - Typical
1 - PASSENGER SIDE BLEND DOOR LEVER
2 - PASSENGER SIDE BLEND DOOR
3 - EVAPORATOR TEMPERATURE SENSOR WIRE
4 - HVAC HOUSING
5 - A/C EVAPORATOR
6 - EVAPORATOR TEMPERATURE SENSOR PROBE
7 - DRIVER SIDE BLEND DOOR
8 - DRIVER SIDE BLEND DOOR LEVER
Fig. 20 Fixed A/C Orifice Tube - Typical
1 - DIFFUSER SCREEN
2 - O-RING SEALS
3 - INLET FILTER SCREEN
4 - ORIFICE
24 - 60 PLUMBINGDR
A/C EVAPORATOR (Continued)
Page 2562 of 2627
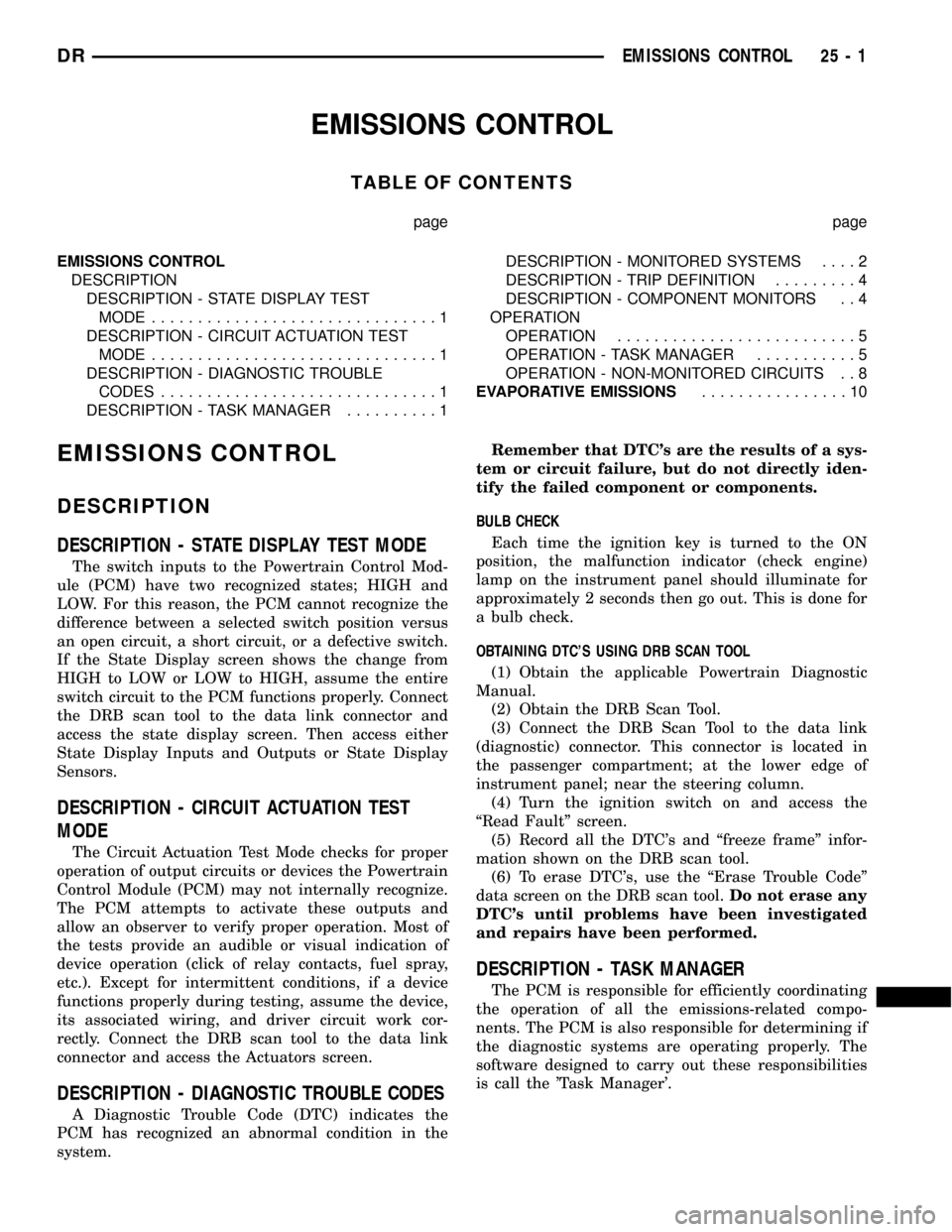
EMISSIONS CONTROL
TABLE OF CONTENTS
page page
EMISSIONS CONTROL
DESCRIPTION
DESCRIPTION - STATE DISPLAY TEST
MODE...............................1
DESCRIPTION - CIRCUIT ACTUATION TEST
MODE...............................1
DESCRIPTION - DIAGNOSTIC TROUBLE
CODES..............................1
DESCRIPTION - TASK MANAGER..........1DESCRIPTION - MONITORED SYSTEMS....2
DESCRIPTION - TRIP DEFINITION.........4
DESCRIPTION - COMPONENT MONITORS . . 4
OPERATION
OPERATION..........................5
OPERATION - TASK MANAGER...........5
OPERATION - NON-MONITORED CIRCUITS . . 8
EVAPORATIVE EMISSIONS................10
EMISSIONS CONTROL
DESCRIPTION
DESCRIPTION - STATE DISPLAY TEST MODE
The switch inputs to the Powertrain Control Mod-
ule (PCM) have two recognized states; HIGH and
LOW. For this reason, the PCM cannot recognize the
difference between a selected switch position versus
an open circuit, a short circuit, or a defective switch.
If the State Display screen shows the change from
HIGH to LOW or LOW to HIGH, assume the entire
switch circuit to the PCM functions properly. Connect
the DRB scan tool to the data link connector and
access the state display screen. Then access either
State Display Inputs and Outputs or State Display
Sensors.
DESCRIPTION - CIRCUIT ACTUATION TEST
MODE
The Circuit Actuation Test Mode checks for proper
operation of output circuits or devices the Powertrain
Control Module (PCM) may not internally recognize.
The PCM attempts to activate these outputs and
allow an observer to verify proper operation. Most of
the tests provide an audible or visual indication of
device operation (click of relay contacts, fuel spray,
etc.). Except for intermittent conditions, if a device
functions properly during testing, assume the device,
its associated wiring, and driver circuit work cor-
rectly. Connect the DRB scan tool to the data link
connector and access the Actuators screen.
DESCRIPTION - DIAGNOSTIC TROUBLE CODES
A Diagnostic Trouble Code (DTC) indicates the
PCM has recognized an abnormal condition in the
system.Remember that DTC's are the results of a sys-
tem or circuit failure, but do not directly iden-
tify the failed component or components.
BULB CHECK
Each time the ignition key is turned to the ON
position, the malfunction indicator (check engine)
lamp on the instrument panel should illuminate for
approximately 2 seconds then go out. This is done for
a bulb check.
OBTAINING DTC'S USING DRB SCAN TOOL
(1) Obtain the applicable Powertrain Diagnostic
Manual.
(2) Obtain the DRB Scan Tool.
(3) Connect the DRB Scan Tool to the data link
(diagnostic) connector. This connector is located in
the passenger compartment; at the lower edge of
instrument panel; near the steering column.
(4) Turn the ignition switch on and access the
ªRead Faultº screen.
(5) Record all the DTC's and ªfreeze frameº infor-
mation shown on the DRB scan tool.
(6) To erase DTC's, use the ªErase Trouble Codeº
data screen on the DRB scan tool.Do not erase any
DTC's until problems have been investigated
and repairs have been performed.
DESCRIPTION - TASK MANAGER
The PCM is responsible for efficiently coordinating
the operation of all the emissions-related compo-
nents. The PCM is also responsible for determining if
the diagnostic systems are operating properly. The
software designed to carry out these responsibilities
is call the 'Task Manager'.
DREMISSIONS CONTROL 25 - 1
Page 2563 of 2627
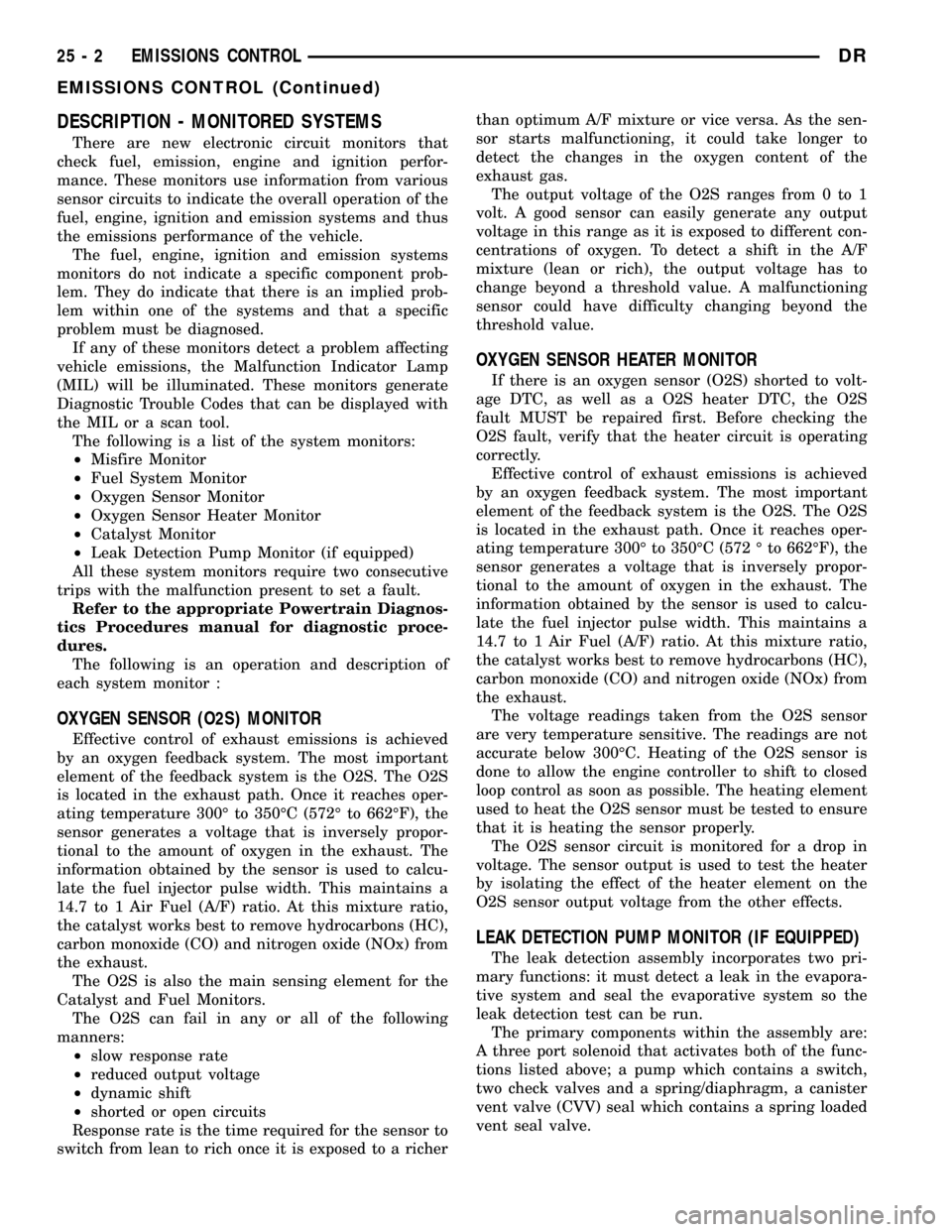
DESCRIPTION - MONITORED SYSTEMS
There are new electronic circuit monitors that
check fuel, emission, engine and ignition perfor-
mance. These monitors use information from various
sensor circuits to indicate the overall operation of the
fuel, engine, ignition and emission systems and thus
the emissions performance of the vehicle.
The fuel, engine, ignition and emission systems
monitors do not indicate a specific component prob-
lem. They do indicate that there is an implied prob-
lem within one of the systems and that a specific
problem must be diagnosed.
If any of these monitors detect a problem affecting
vehicle emissions, the Malfunction Indicator Lamp
(MIL) will be illuminated. These monitors generate
Diagnostic Trouble Codes that can be displayed with
the MIL or a scan tool.
The following is a list of the system monitors:
²Misfire Monitor
²Fuel System Monitor
²Oxygen Sensor Monitor
²Oxygen Sensor Heater Monitor
²Catalyst Monitor
²Leak Detection Pump Monitor (if equipped)
All these system monitors require two consecutive
trips with the malfunction present to set a fault.
Refer to the appropriate Powertrain Diagnos-
tics Procedures manual for diagnostic proce-
dures.
The following is an operation and description of
each system monitor :
OXYGEN SENSOR (O2S) MONITOR
Effective control of exhaust emissions is achieved
by an oxygen feedback system. The most important
element of the feedback system is the O2S. The O2S
is located in the exhaust path. Once it reaches oper-
ating temperature 300É to 350ÉC (572É to 662ÉF), the
sensor generates a voltage that is inversely propor-
tional to the amount of oxygen in the exhaust. The
information obtained by the sensor is used to calcu-
late the fuel injector pulse width. This maintains a
14.7 to 1 Air Fuel (A/F) ratio. At this mixture ratio,
the catalyst works best to remove hydrocarbons (HC),
carbon monoxide (CO) and nitrogen oxide (NOx) from
the exhaust.
The O2S is also the main sensing element for the
Catalyst and Fuel Monitors.
The O2S can fail in any or all of the following
manners:
²slow response rate
²reduced output voltage
²dynamic shift
²shorted or open circuits
Response rate is the time required for the sensor to
switch from lean to rich once it is exposed to a richerthan optimum A/F mixture or vice versa. As the sen-
sor starts malfunctioning, it could take longer to
detect the changes in the oxygen content of the
exhaust gas.
The output voltage of the O2S ranges from 0 to 1
volt. A good sensor can easily generate any output
voltage in this range as it is exposed to different con-
centrations of oxygen. To detect a shift in the A/F
mixture (lean or rich), the output voltage has to
change beyond a threshold value. A malfunctioning
sensor could have difficulty changing beyond the
threshold value.
OXYGEN SENSOR HEATER MONITOR
If there is an oxygen sensor (O2S) shorted to volt-
age DTC, as well as a O2S heater DTC, the O2S
fault MUST be repaired first. Before checking the
O2S fault, verify that the heater circuit is operating
correctly.
Effective control of exhaust emissions is achieved
by an oxygen feedback system. The most important
element of the feedback system is the O2S. The O2S
is located in the exhaust path. Once it reaches oper-
ating temperature 300É to 350ÉC (572 É to 662ÉF), the
sensor generates a voltage that is inversely propor-
tional to the amount of oxygen in the exhaust. The
information obtained by the sensor is used to calcu-
late the fuel injector pulse width. This maintains a
14.7 to 1 Air Fuel (A/F) ratio. At this mixture ratio,
the catalyst works best to remove hydrocarbons (HC),
carbon monoxide (CO) and nitrogen oxide (NOx) from
the exhaust.
The voltage readings taken from the O2S sensor
are very temperature sensitive. The readings are not
accurate below 300ÉC. Heating of the O2S sensor is
done to allow the engine controller to shift to closed
loop control as soon as possible. The heating element
used to heat the O2S sensor must be tested to ensure
that it is heating the sensor properly.
The O2S sensor circuit is monitored for a drop in
voltage. The sensor output is used to test the heater
by isolating the effect of the heater element on the
O2S sensor output voltage from the other effects.
LEAK DETECTION PUMP MONITOR (IF EQUIPPED)
The leak detection assembly incorporates two pri-
mary functions: it must detect a leak in the evapora-
tive system and seal the evaporative system so the
leak detection test can be run.
The primary components within the assembly are:
A three port solenoid that activates both of the func-
tions listed above; a pump which contains a switch,
two check valves and a spring/diaphragm, a canister
vent valve (CVV) seal which contains a spring loaded
vent seal valve.
25 - 2 EMISSIONS CONTROLDR
EMISSIONS CONTROL (Continued)
Page 2564 of 2627
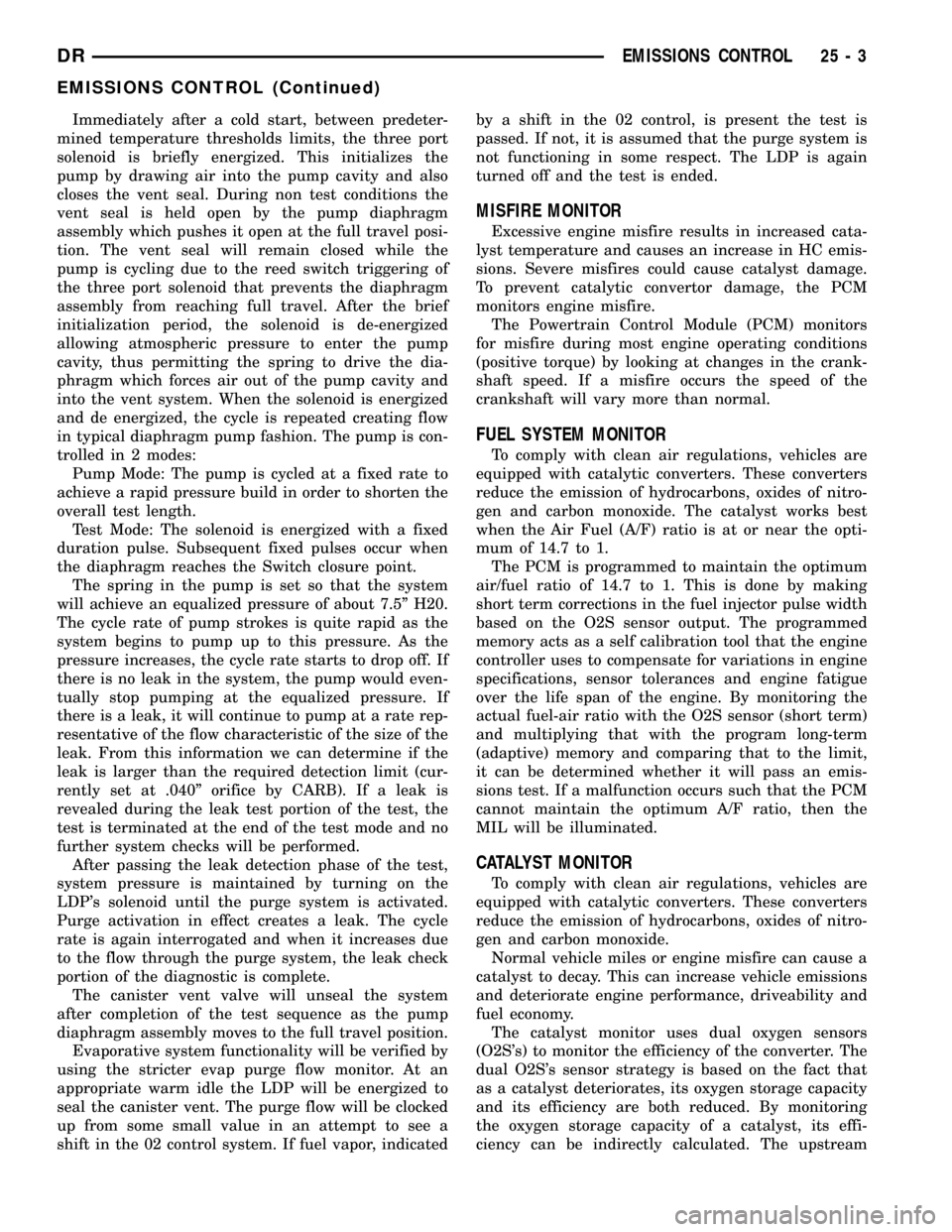
Immediately after a cold start, between predeter-
mined temperature thresholds limits, the three port
solenoid is briefly energized. This initializes the
pump by drawing air into the pump cavity and also
closes the vent seal. During non test conditions the
vent seal is held open by the pump diaphragm
assembly which pushes it open at the full travel posi-
tion. The vent seal will remain closed while the
pump is cycling due to the reed switch triggering of
the three port solenoid that prevents the diaphragm
assembly from reaching full travel. After the brief
initialization period, the solenoid is de-energized
allowing atmospheric pressure to enter the pump
cavity, thus permitting the spring to drive the dia-
phragm which forces air out of the pump cavity and
into the vent system. When the solenoid is energized
and de energized, the cycle is repeated creating flow
in typical diaphragm pump fashion. The pump is con-
trolled in 2 modes:
Pump Mode: The pump is cycled at a fixed rate to
achieve a rapid pressure build in order to shorten the
overall test length.
Test Mode: The solenoid is energized with a fixed
duration pulse. Subsequent fixed pulses occur when
the diaphragm reaches the Switch closure point.
The spring in the pump is set so that the system
will achieve an equalized pressure of about 7.5º H20.
The cycle rate of pump strokes is quite rapid as the
system begins to pump up to this pressure. As the
pressure increases, the cycle rate starts to drop off. If
there is no leak in the system, the pump would even-
tually stop pumping at the equalized pressure. If
there is a leak, it will continue to pump at a rate rep-
resentative of the flow characteristic of the size of the
leak. From this information we can determine if the
leak is larger than the required detection limit (cur-
rently set at .040º orifice by CARB). If a leak is
revealed during the leak test portion of the test, the
test is terminated at the end of the test mode and no
further system checks will be performed.
After passing the leak detection phase of the test,
system pressure is maintained by turning on the
LDP's solenoid until the purge system is activated.
Purge activation in effect creates a leak. The cycle
rate is again interrogated and when it increases due
to the flow through the purge system, the leak check
portion of the diagnostic is complete.
The canister vent valve will unseal the system
after completion of the test sequence as the pump
diaphragm assembly moves to the full travel position.
Evaporative system functionality will be verified by
using the stricter evap purge flow monitor. At an
appropriate warm idle the LDP will be energized to
seal the canister vent. The purge flow will be clocked
up from some small value in an attempt to see a
shift in the 02 control system. If fuel vapor, indicatedby a shift in the 02 control, is present the test is
passed. If not, it is assumed that the purge system is
not functioning in some respect. The LDP is again
turned off and the test is ended.
MISFIRE MONITOR
Excessive engine misfire results in increased cata-
lyst temperature and causes an increase in HC emis-
sions. Severe misfires could cause catalyst damage.
To prevent catalytic convertor damage, the PCM
monitors engine misfire.
The Powertrain Control Module (PCM) monitors
for misfire during most engine operating conditions
(positive torque) by looking at changes in the crank-
shaft speed. If a misfire occurs the speed of the
crankshaft will vary more than normal.
FUEL SYSTEM MONITOR
To comply with clean air regulations, vehicles are
equipped with catalytic converters. These converters
reduce the emission of hydrocarbons, oxides of nitro-
gen and carbon monoxide. The catalyst works best
when the Air Fuel (A/F) ratio is at or near the opti-
mum of 14.7 to 1.
The PCM is programmed to maintain the optimum
air/fuel ratio of 14.7 to 1. This is done by making
short term corrections in the fuel injector pulse width
based on the O2S sensor output. The programmed
memory acts as a self calibration tool that the engine
controller uses to compensate for variations in engine
specifications, sensor tolerances and engine fatigue
over the life span of the engine. By monitoring the
actual fuel-air ratio with the O2S sensor (short term)
and multiplying that with the program long-term
(adaptive) memory and comparing that to the limit,
it can be determined whether it will pass an emis-
sions test. If a malfunction occurs such that the PCM
cannot maintain the optimum A/F ratio, then the
MIL will be illuminated.
CATALYST MONITOR
To comply with clean air regulations, vehicles are
equipped with catalytic converters. These converters
reduce the emission of hydrocarbons, oxides of nitro-
gen and carbon monoxide.
Normal vehicle miles or engine misfire can cause a
catalyst to decay. This can increase vehicle emissions
and deteriorate engine performance, driveability and
fuel economy.
The catalyst monitor uses dual oxygen sensors
(O2S's) to monitor the efficiency of the converter. The
dual O2S's sensor strategy is based on the fact that
as a catalyst deteriorates, its oxygen storage capacity
and its efficiency are both reduced. By monitoring
the oxygen storage capacity of a catalyst, its effi-
ciency can be indirectly calculated. The upstream
DREMISSIONS CONTROL 25 - 3
EMISSIONS CONTROL (Continued)
Page 2565 of 2627
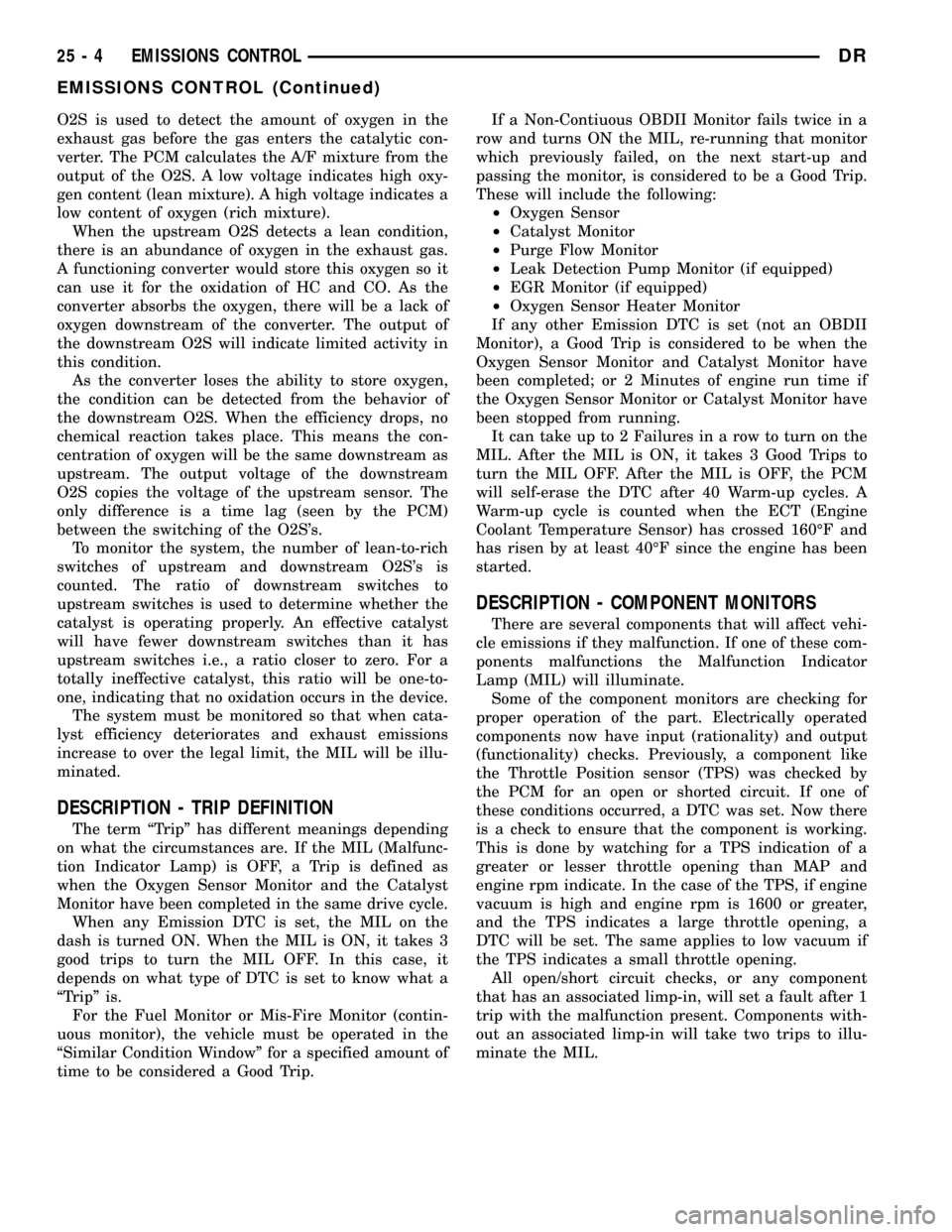
O2S is used to detect the amount of oxygen in the
exhaust gas before the gas enters the catalytic con-
verter. The PCM calculates the A/F mixture from the
output of the O2S. A low voltage indicates high oxy-
gen content (lean mixture). A high voltage indicates a
low content of oxygen (rich mixture).
When the upstream O2S detects a lean condition,
there is an abundance of oxygen in the exhaust gas.
A functioning converter would store this oxygen so it
can use it for the oxidation of HC and CO. As the
converter absorbs the oxygen, there will be a lack of
oxygen downstream of the converter. The output of
the downstream O2S will indicate limited activity in
this condition.
As the converter loses the ability to store oxygen,
the condition can be detected from the behavior of
the downstream O2S. When the efficiency drops, no
chemical reaction takes place. This means the con-
centration of oxygen will be the same downstream as
upstream. The output voltage of the downstream
O2S copies the voltage of the upstream sensor. The
only difference is a time lag (seen by the PCM)
between the switching of the O2S's.
To monitor the system, the number of lean-to-rich
switches of upstream and downstream O2S's is
counted. The ratio of downstream switches to
upstream switches is used to determine whether the
catalyst is operating properly. An effective catalyst
will have fewer downstream switches than it has
upstream switches i.e., a ratio closer to zero. For a
totally ineffective catalyst, this ratio will be one-to-
one, indicating that no oxidation occurs in the device.
The system must be monitored so that when cata-
lyst efficiency deteriorates and exhaust emissions
increase to over the legal limit, the MIL will be illu-
minated.
DESCRIPTION - TRIP DEFINITION
The term ªTripº has different meanings depending
on what the circumstances are. If the MIL (Malfunc-
tion Indicator Lamp) is OFF, a Trip is defined as
when the Oxygen Sensor Monitor and the Catalyst
Monitor have been completed in the same drive cycle.
When any Emission DTC is set, the MIL on the
dash is turned ON. When the MIL is ON, it takes 3
good trips to turn the MIL OFF. In this case, it
depends on what type of DTC is set to know what a
ªTripº is.
For the Fuel Monitor or Mis-Fire Monitor (contin-
uous monitor), the vehicle must be operated in the
ªSimilar Condition Windowº for a specified amount of
time to be considered a Good Trip.If a Non-Contiuous OBDII Monitor fails twice in a
row and turns ON the MIL, re-running that monitor
which previously failed, on the next start-up and
passing the monitor, is considered to be a Good Trip.
These will include the following:
²Oxygen Sensor
²Catalyst Monitor
²Purge Flow Monitor
²Leak Detection Pump Monitor (if equipped)
²EGR Monitor (if equipped)
²Oxygen Sensor Heater Monitor
If any other Emission DTC is set (not an OBDII
Monitor), a Good Trip is considered to be when the
Oxygen Sensor Monitor and Catalyst Monitor have
been completed; or 2 Minutes of engine run time if
the Oxygen Sensor Monitor or Catalyst Monitor have
been stopped from running.
It can take up to 2 Failures in a row to turn on the
MIL. After the MIL is ON, it takes 3 Good Trips to
turn the MIL OFF. After the MIL is OFF, the PCM
will self-erase the DTC after 40 Warm-up cycles. A
Warm-up cycle is counted when the ECT (Engine
Coolant Temperature Sensor) has crossed 160ÉF and
has risen by at least 40ÉF since the engine has been
started.
DESCRIPTION - COMPONENT MONITORS
There are several components that will affect vehi-
cle emissions if they malfunction. If one of these com-
ponents malfunctions the Malfunction Indicator
Lamp (MIL) will illuminate.
Some of the component monitors are checking for
proper operation of the part. Electrically operated
components now have input (rationality) and output
(functionality) checks. Previously, a component like
the Throttle Position sensor (TPS) was checked by
the PCM for an open or shorted circuit. If one of
these conditions occurred, a DTC was set. Now there
is a check to ensure that the component is working.
This is done by watching for a TPS indication of a
greater or lesser throttle opening than MAP and
engine rpm indicate. In the case of the TPS, if engine
vacuum is high and engine rpm is 1600 or greater,
and the TPS indicates a large throttle opening, a
DTC will be set. The same applies to low vacuum if
the TPS indicates a small throttle opening.
All open/short circuit checks, or any component
that has an associated limp-in, will set a fault after 1
trip with the malfunction present. Components with-
out an associated limp-in will take two trips to illu-
minate the MIL.
25 - 4 EMISSIONS CONTROLDR
EMISSIONS CONTROL (Continued)