DODGE RAM 1500 1998 2.G Workshop Manual
Manufacturer: DODGE, Model Year: 1998, Model line: RAM 1500, Model: DODGE RAM 1500 1998 2.GPages: 2627
Page 631 of 2627
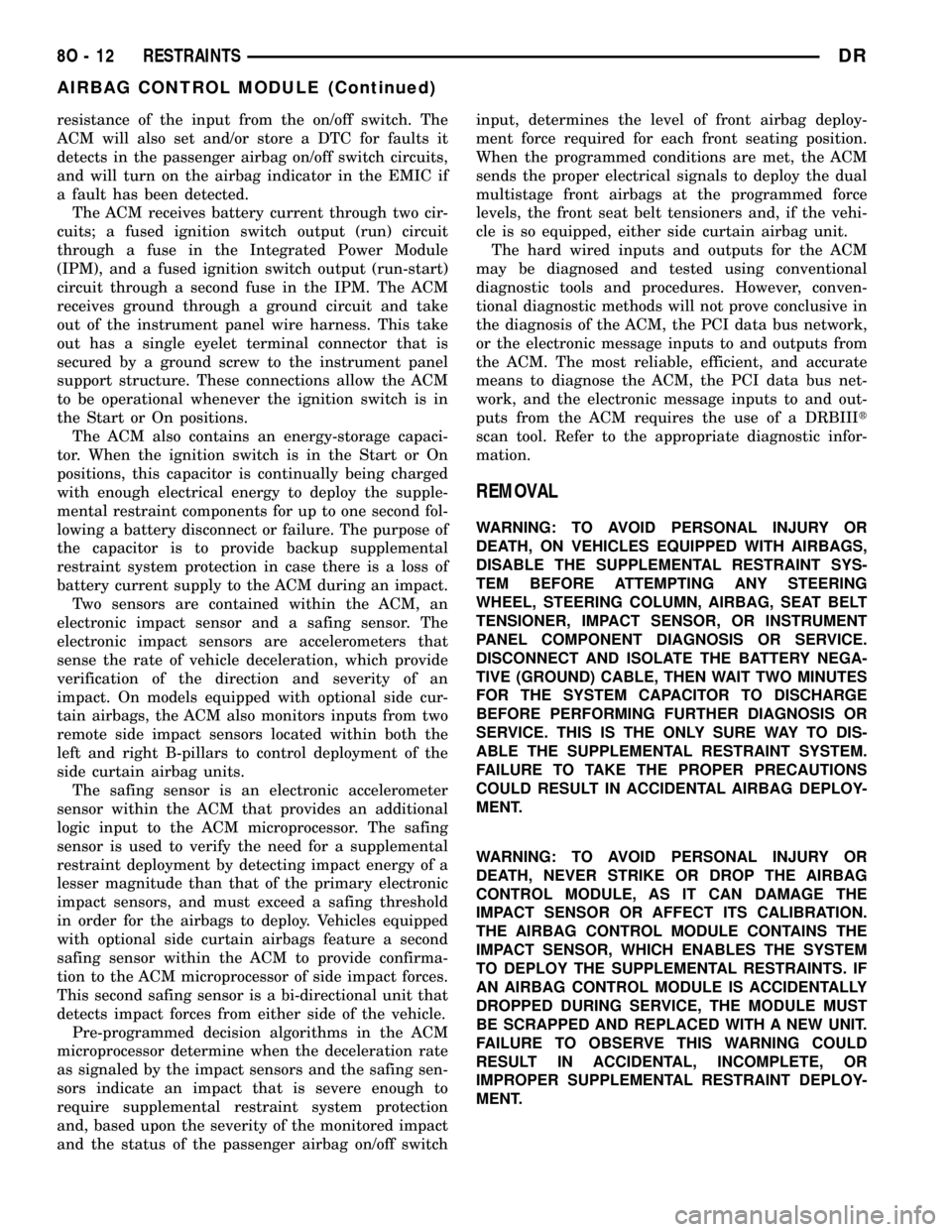
resistance of the input from the on/off switch. The
ACM will also set and/or store a DTC for faults it
detects in the passenger airbag on/off switch circuits,
and will turn on the airbag indicator in the EMIC if
a fault has been detected.
The ACM receives battery current through two cir-
cuits; a fused ignition switch output (run) circuit
through a fuse in the Integrated Power Module
(IPM), and a fused ignition switch output (run-start)
circuit through a second fuse in the IPM. The ACM
receives ground through a ground circuit and take
out of the instrument panel wire harness. This take
out has a single eyelet terminal connector that is
secured by a ground screw to the instrument panel
support structure. These connections allow the ACM
to be operational whenever the ignition switch is in
the Start or On positions.
The ACM also contains an energy-storage capaci-
tor. When the ignition switch is in the Start or On
positions, this capacitor is continually being charged
with enough electrical energy to deploy the supple-
mental restraint components for up to one second fol-
lowing a battery disconnect or failure. The purpose of
the capacitor is to provide backup supplemental
restraint system protection in case there is a loss of
battery current supply to the ACM during an impact.
Two sensors are contained within the ACM, an
electronic impact sensor and a safing sensor. The
electronic impact sensors are accelerometers that
sense the rate of vehicle deceleration, which provide
verification of the direction and severity of an
impact. On models equipped with optional side cur-
tain airbags, the ACM also monitors inputs from two
remote side impact sensors located within both the
left and right B-pillars to control deployment of the
side curtain airbag units.
The safing sensor is an electronic accelerometer
sensor within the ACM that provides an additional
logic input to the ACM microprocessor. The safing
sensor is used to verify the need for a supplemental
restraint deployment by detecting impact energy of a
lesser magnitude than that of the primary electronic
impact sensors, and must exceed a safing threshold
in order for the airbags to deploy. Vehicles equipped
with optional side curtain airbags feature a second
safing sensor within the ACM to provide confirma-
tion to the ACM microprocessor of side impact forces.
This second safing sensor is a bi-directional unit that
detects impact forces from either side of the vehicle.
Pre-programmed decision algorithms in the ACM
microprocessor determine when the deceleration rate
as signaled by the impact sensors and the safing sen-
sors indicate an impact that is severe enough to
require supplemental restraint system protection
and, based upon the severity of the monitored impact
and the status of the passenger airbag on/off switchinput, determines the level of front airbag deploy-
ment force required for each front seating position.
When the programmed conditions are met, the ACM
sends the proper electrical signals to deploy the dual
multistage front airbags at the programmed force
levels, the front seat belt tensioners and, if the vehi-
cle is so equipped, either side curtain airbag unit.
The hard wired inputs and outputs for the ACM
may be diagnosed and tested using conventional
diagnostic tools and procedures. However, conven-
tional diagnostic methods will not prove conclusive in
the diagnosis of the ACM, the PCI data bus network,
or the electronic message inputs to and outputs from
the ACM. The most reliable, efficient, and accurate
means to diagnose the ACM, the PCI data bus net-
work, and the electronic message inputs to and out-
puts from the ACM requires the use of a DRBIIIt
scan tool. Refer to the appropriate diagnostic infor-
mation.
REMOVAL
WARNING: TO AVOID PERSONAL INJURY OR
DEATH, ON VEHICLES EQUIPPED WITH AIRBAGS,
DISABLE THE SUPPLEMENTAL RESTRAINT SYS-
TEM BEFORE ATTEMPTING ANY STEERING
WHEEL, STEERING COLUMN, AIRBAG, SEAT BELT
TENSIONER, IMPACT SENSOR, OR INSTRUMENT
PANEL COMPONENT DIAGNOSIS OR SERVICE.
DISCONNECT AND ISOLATE THE BATTERY NEGA-
TIVE (GROUND) CABLE, THEN WAIT TWO MINUTES
FOR THE SYSTEM CAPACITOR TO DISCHARGE
BEFORE PERFORMING FURTHER DIAGNOSIS OR
SERVICE. THIS IS THE ONLY SURE WAY TO DIS-
ABLE THE SUPPLEMENTAL RESTRAINT SYSTEM.
FAILURE TO TAKE THE PROPER PRECAUTIONS
COULD RESULT IN ACCIDENTAL AIRBAG DEPLOY-
MENT.
WARNING: TO AVOID PERSONAL INJURY OR
DEATH, NEVER STRIKE OR DROP THE AIRBAG
CONTROL MODULE, AS IT CAN DAMAGE THE
IMPACT SENSOR OR AFFECT ITS CALIBRATION.
THE AIRBAG CONTROL MODULE CONTAINS THE
IMPACT SENSOR, WHICH ENABLES THE SYSTEM
TO DEPLOY THE SUPPLEMENTAL RESTRAINTS. IF
AN AIRBAG CONTROL MODULE IS ACCIDENTALLY
DROPPED DURING SERVICE, THE MODULE MUST
BE SCRAPPED AND REPLACED WITH A NEW UNIT.
FAILURE TO OBSERVE THIS WARNING COULD
RESULT IN ACCIDENTAL, INCOMPLETE, OR
IMPROPER SUPPLEMENTAL RESTRAINT DEPLOY-
MENT.
8O - 12 RESTRAINTSDR
AIRBAG CONTROL MODULE (Continued)
Page 632 of 2627

(1) Disconnect and isolate the battery negative
cable. Wait two minutes for the system capacitor to
discharge before further service.
(2) On models with a manual transmission,
remove the floor console from the top of the floor
panel transmission tunnel. (Refer to 23 - BODY/IN-
TERIOR/FLOOR CONSOLE - REMOVAL).
(3) On models with an automatic transmission,
remove the ACM cover from the instrument panel.
(Refer to 8 - ELECTRICAL/RESTRAINTS/ACM
COVER - REMOVAL).
(4) Reach through the rearward facing opening
below the instrument panel center stack support
bracket on the top of the floor panel transmission
tunnel to access and disconnect the two instrument
panel wire harness connectors for the Airbag Control
Module (ACM) from the ACM connector receptacles
located on the rearward facing side of the module
(Fig. 8). To disconnect the wire harness connectors
from the ACM, depress the release tab and lift the
lever arm on each connector.
(5) From the left side of the floor panel transmis-
sion tunnel, reach behind the module to access and
loosen the screw that secures the right side of the
ACM to the bracket on the floor panel transmission
tunnel. Loosen the screw about 7 millimeters (0.25
inch).
(6) From the left side of the floor panel transmis-
sion tunnel, remove the two screws that secure the
left side of the ACM to the bracket on the floor panel
transmission tunnel.
(7) Still working from the left side of the floor
panel transmission tunnel, lift the ACM upward far
enough to disengage the locating pin on the bottom ofthe ACM mounting flange from the locating hole in
the mounting bracket, then slide the ACM toward
the left far enough to disengage the slotted hole in
the right ACM mounting flange from under the head
of the previously loosened right mounting screw.
(8) Remove the ACM from the left side of the floor
panel transmission tunnel.
INSTALLATION
WARNING: TO AVOID PERSONAL INJURY OR DEATH,
ON VEHICLES EQUIPPED WITH AIRBAGS, DISABLE
THE SUPPLEMENTAL RESTRAINT SYSTEM BEFORE
ATTEMPTING ANY STEERING WHEEL, STEERING
COLUMN, AIRBAG, SEAT BELT TENSIONER, IMPACT
SENSOR, OR INSTRUMENT PANEL COMPONENT
DIAGNOSIS OR SERVICE. DISCONNECT AND ISO-
LATE THE BATTERY NEGATIVE (GROUND) CABLE,
THEN WAIT TWO MINUTES FOR THE SYSTEM
CAPACITOR TO DISCHARGE BEFORE PERFORMING
FURTHER DIAGNOSIS OR SERVICE. THIS IS THE
ONLY SURE WAY TO DISABLE THE SUPPLEMENTAL
RESTRAINT SYSTEM. FAILURE TO TAKE THE
PROPER PRECAUTIONS COULD RESULT IN ACCI-
DENTAL AIRBAG DEPLOYMENT.
WARNING: TO AVOID PERSONAL INJURY OR DEATH,
NEVER STRIKE OR DROP THE AIRBAG CONTROL
MODULE, AS IT CAN DAMAGE THE IMPACT SENSOR
OR AFFECT ITS CALIBRATION. THE AIRBAG CON-
TROL MODULE CONTAINS THE IMPACT SENSOR,
WHICH ENABLES THE SYSTEM TO DEPLOY THE
SUPPLEMENTAL RESTRAINTS. IF AN AIRBAG CON-
TROL MODULE IS ACCIDENTALLY DROPPED DUR-
ING SERVICE, THE MODULE MUST BE SCRAPPED
AND REPLACED WITH A NEW UNIT. FAILURE TO
OBSERVE THIS WARNING COULD RESULT IN ACCI-
DENTAL, INCOMPLETE, OR IMPROPER SUPPLEMEN-
TAL RESTRAINT DEPLOYMENT.
(1) Position the Airbag Control Module (ACM) to
the left side of the floor panel transmission tunnel
near the ACM bracket (Fig. 8). When the ACM is cor-
rectly positioned, the arrow on the ACM label will be
pointed forward in the vehicle.
(2) From the left side of the floor panel transmis-
sion tunnel, slide the ACM toward the right far
enough to engage the slotted hole in the right ACM
mounting flange under the head of the previously
loosened right mounting screw, then engage the
locating pin on the bottom of the left ACM mounting
flange into the locating hole in the bracket.
(3) Still working from the left side of the floor
panel transmission tunnel, install and tighten the
two screws that secure the left ACM mounting
flanges to the bracket that is welded onto the floor
Fig. 8 Airbag Control Module Remove/Install
1 - AIRBAG CONTROL MODULE
2 - SCREW (3)
3 - BODY WIRE HARNESS CONNECTOR
4 - INSTRUMENT PANEL WIRE HARNESS CONNECTOR
5 - FLOOR PANEL TRANSMISSION TUNNEL
DRRESTRAINTS 8O - 13
AIRBAG CONTROL MODULE (Continued)
Page 633 of 2627
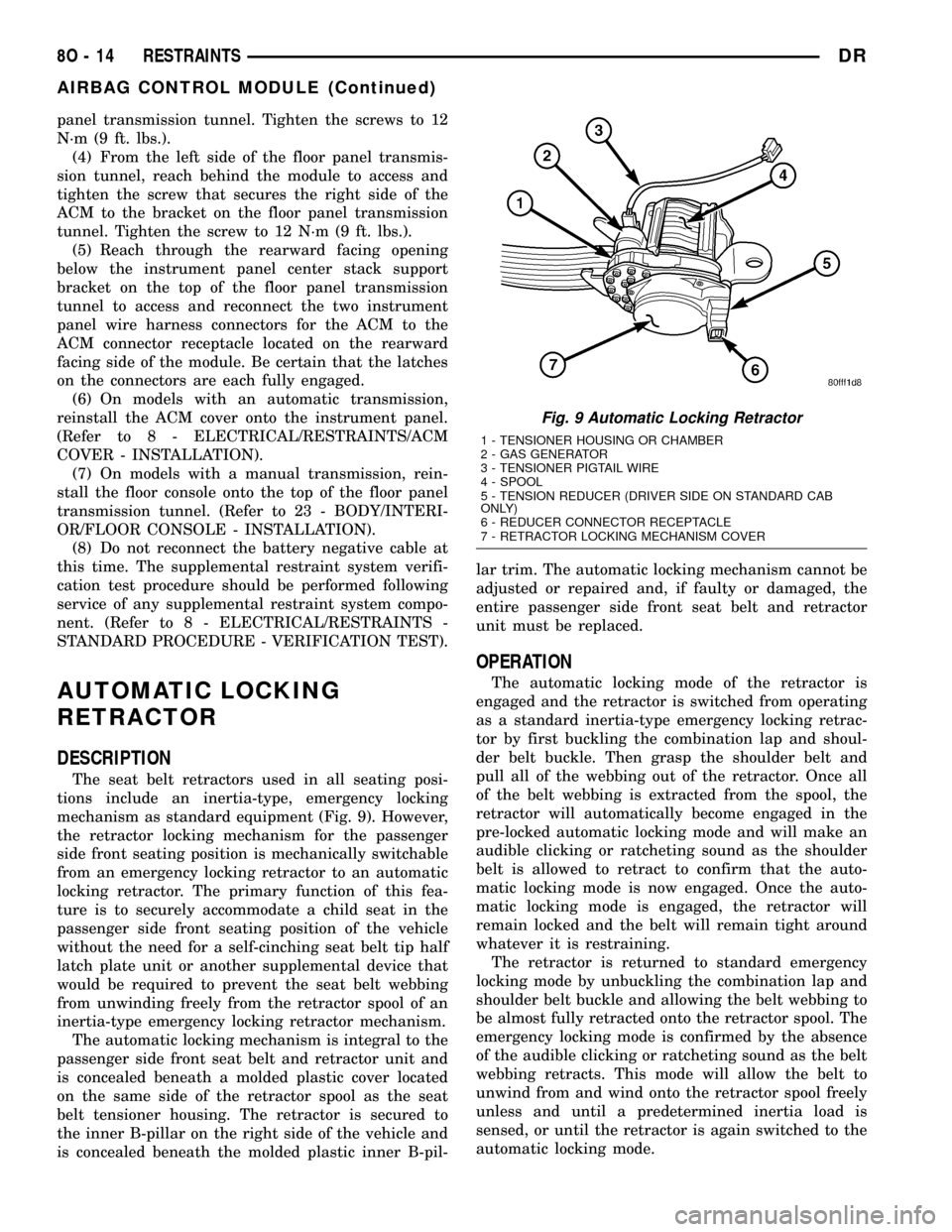
panel transmission tunnel. Tighten the screws to 12
N´m (9 ft. lbs.).
(4) From the left side of the floor panel transmis-
sion tunnel, reach behind the module to access and
tighten the screw that secures the right side of the
ACM to the bracket on the floor panel transmission
tunnel. Tighten the screw to 12 N´m (9 ft. lbs.).
(5) Reach through the rearward facing opening
below the instrument panel center stack support
bracket on the top of the floor panel transmission
tunnel to access and reconnect the two instrument
panel wire harness connectors for the ACM to the
ACM connector receptacle located on the rearward
facing side of the module. Be certain that the latches
on the connectors are each fully engaged.
(6) On models with an automatic transmission,
reinstall the ACM cover onto the instrument panel.
(Refer to 8 - ELECTRICAL/RESTRAINTS/ACM
COVER - INSTALLATION).
(7) On models with a manual transmission, rein-
stall the floor console onto the top of the floor panel
transmission tunnel. (Refer to 23 - BODY/INTERI-
OR/FLOOR CONSOLE - INSTALLATION).
(8) Do not reconnect the battery negative cable at
this time. The supplemental restraint system verifi-
cation test procedure should be performed following
service of any supplemental restraint system compo-
nent. (Refer to 8 - ELECTRICAL/RESTRAINTS -
STANDARD PROCEDURE - VERIFICATION TEST).
AUTOMATIC LOCKING
RETRACTOR
DESCRIPTION
The seat belt retractors used in all seating posi-
tions include an inertia-type, emergency locking
mechanism as standard equipment (Fig. 9). However,
the retractor locking mechanism for the passenger
side front seating position is mechanically switchable
from an emergency locking retractor to an automatic
locking retractor. The primary function of this fea-
ture is to securely accommodate a child seat in the
passenger side front seating position of the vehicle
without the need for a self-cinching seat belt tip half
latch plate unit or another supplemental device that
would be required to prevent the seat belt webbing
from unwinding freely from the retractor spool of an
inertia-type emergency locking retractor mechanism.
The automatic locking mechanism is integral to the
passenger side front seat belt and retractor unit and
is concealed beneath a molded plastic cover located
on the same side of the retractor spool as the seat
belt tensioner housing. The retractor is secured to
the inner B-pillar on the right side of the vehicle and
is concealed beneath the molded plastic inner B-pil-lar trim. The automatic locking mechanism cannot be
adjusted or repaired and, if faulty or damaged, the
entire passenger side front seat belt and retractor
unit must be replaced.
OPERATION
The automatic locking mode of the retractor is
engaged and the retractor is switched from operating
as a standard inertia-type emergency locking retrac-
tor by first buckling the combination lap and shoul-
der belt buckle. Then grasp the shoulder belt and
pull all of the webbing out of the retractor. Once all
of the belt webbing is extracted from the spool, the
retractor will automatically become engaged in the
pre-locked automatic locking mode and will make an
audible clicking or ratcheting sound as the shoulder
belt is allowed to retract to confirm that the auto-
matic locking mode is now engaged. Once the auto-
matic locking mode is engaged, the retractor will
remain locked and the belt will remain tight around
whatever it is restraining.
The retractor is returned to standard emergency
locking mode by unbuckling the combination lap and
shoulder belt buckle and allowing the belt webbing to
be almost fully retracted onto the retractor spool. The
emergency locking mode is confirmed by the absence
of the audible clicking or ratcheting sound as the belt
webbing retracts. This mode will allow the belt to
unwind from and wind onto the retractor spool freely
unless and until a predetermined inertia load is
sensed, or until the retractor is again switched to the
automatic locking mode.
Fig. 9 Automatic Locking Retractor
1 - TENSIONER HOUSING OR CHAMBER
2 - GAS GENERATOR
3 - TENSIONER PIGTAIL WIRE
4 - SPOOL
5 - TENSION REDUCER (DRIVER SIDE ON STANDARD CAB
ONLY)
6 - REDUCER CONNECTOR RECEPTACLE
7 - RETRACTOR LOCKING MECHANISM COVER
8O - 14 RESTRAINTSDR
AIRBAG CONTROL MODULE (Continued)
Page 634 of 2627
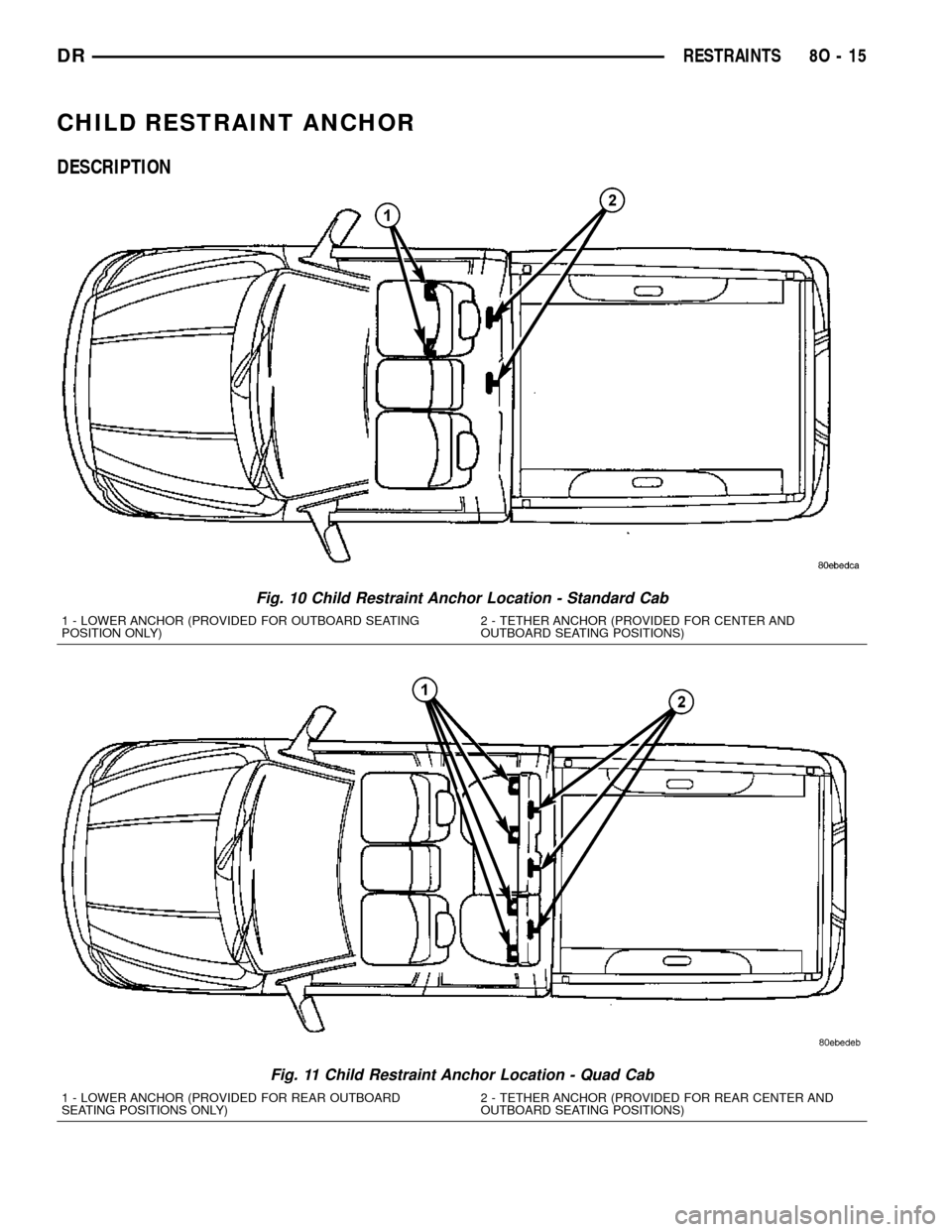
CHILD RESTRAINT ANCHOR
DESCRIPTION
Fig. 10 Child Restraint Anchor Location - Standard Cab
1 - LOWER ANCHOR (PROVIDED FOR OUTBOARD SEATING
POSITION ONLY)2 - TETHER ANCHOR (PROVIDED FOR CENTER AND
OUTBOARD SEATING POSITIONS)
Fig. 11 Child Restraint Anchor Location - Quad Cab
1 - LOWER ANCHOR (PROVIDED FOR REAR OUTBOARD
SEATING POSITIONS ONLY)2 - TETHER ANCHOR (PROVIDED FOR REAR CENTER AND
OUTBOARD SEATING POSITIONS)
DRRESTRAINTS 8O - 15
Page 635 of 2627
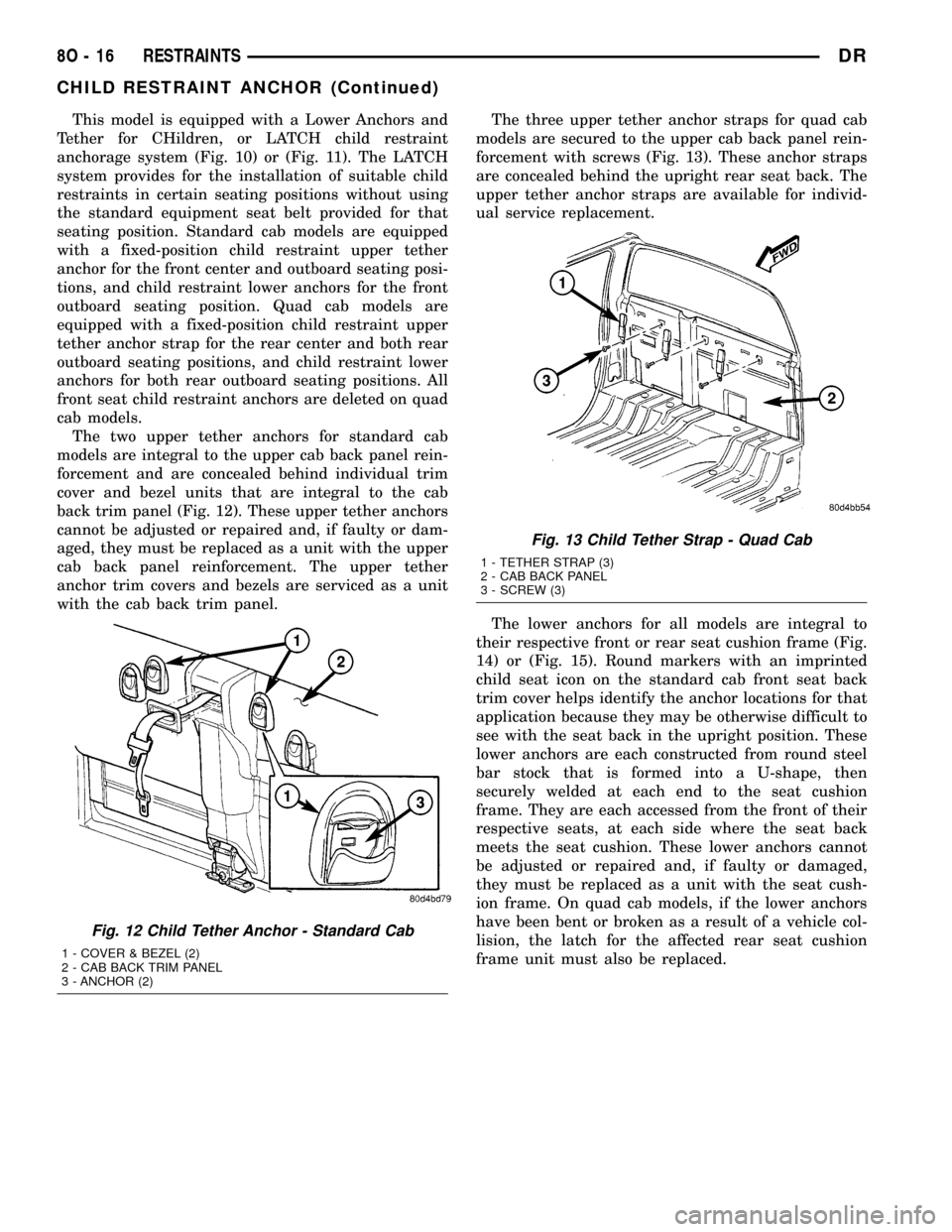
This model is equipped with a Lower Anchors and
Tether for CHildren, or LATCH child restraint
anchorage system (Fig. 10) or (Fig. 11). The LATCH
system provides for the installation of suitable child
restraints in certain seating positions without using
the standard equipment seat belt provided for that
seating position. Standard cab models are equipped
with a fixed-position child restraint upper tether
anchor for the front center and outboard seating posi-
tions, and child restraint lower anchors for the front
outboard seating position. Quad cab models are
equipped with a fixed-position child restraint upper
tether anchor strap for the rear center and both rear
outboard seating positions, and child restraint lower
anchors for both rear outboard seating positions. All
front seat child restraint anchors are deleted on quad
cab models.
The two upper tether anchors for standard cab
models are integral to the upper cab back panel rein-
forcement and are concealed behind individual trim
cover and bezel units that are integral to the cab
back trim panel (Fig. 12). These upper tether anchors
cannot be adjusted or repaired and, if faulty or dam-
aged, they must be replaced as a unit with the upper
cab back panel reinforcement. The upper tether
anchor trim covers and bezels are serviced as a unit
with the cab back trim panel.The three upper tether anchor straps for quad cab
models are secured to the upper cab back panel rein-
forcement with screws (Fig. 13). These anchor straps
are concealed behind the upright rear seat back. The
upper tether anchor straps are available for individ-
ual service replacement.
The lower anchors for all models are integral to
their respective front or rear seat cushion frame (Fig.
14) or (Fig. 15). Round markers with an imprinted
child seat icon on the standard cab front seat back
trim cover helps identify the anchor locations for that
application because they may be otherwise difficult to
see with the seat back in the upright position. These
lower anchors are each constructed from round steel
bar stock that is formed into a U-shape, then
securely welded at each end to the seat cushion
frame. They are each accessed from the front of their
respective seats, at each side where the seat back
meets the seat cushion. These lower anchors cannot
be adjusted or repaired and, if faulty or damaged,
they must be replaced as a unit with the seat cush-
ion frame. On quad cab models, if the lower anchors
have been bent or broken as a result of a vehicle col-
lision, the latch for the affected rear seat cushion
frame unit must also be replaced.
Fig. 12 Child Tether Anchor - Standard Cab
1 - COVER & BEZEL (2)
2 - CAB BACK TRIM PANEL
3 - ANCHOR (2)
Fig. 13 Child Tether Strap - Quad Cab
1 - TETHER STRAP (3)
2 - CAB BACK PANEL
3 - SCREW (3)
8O - 16 RESTRAINTSDR
CHILD RESTRAINT ANCHOR (Continued)
Page 636 of 2627
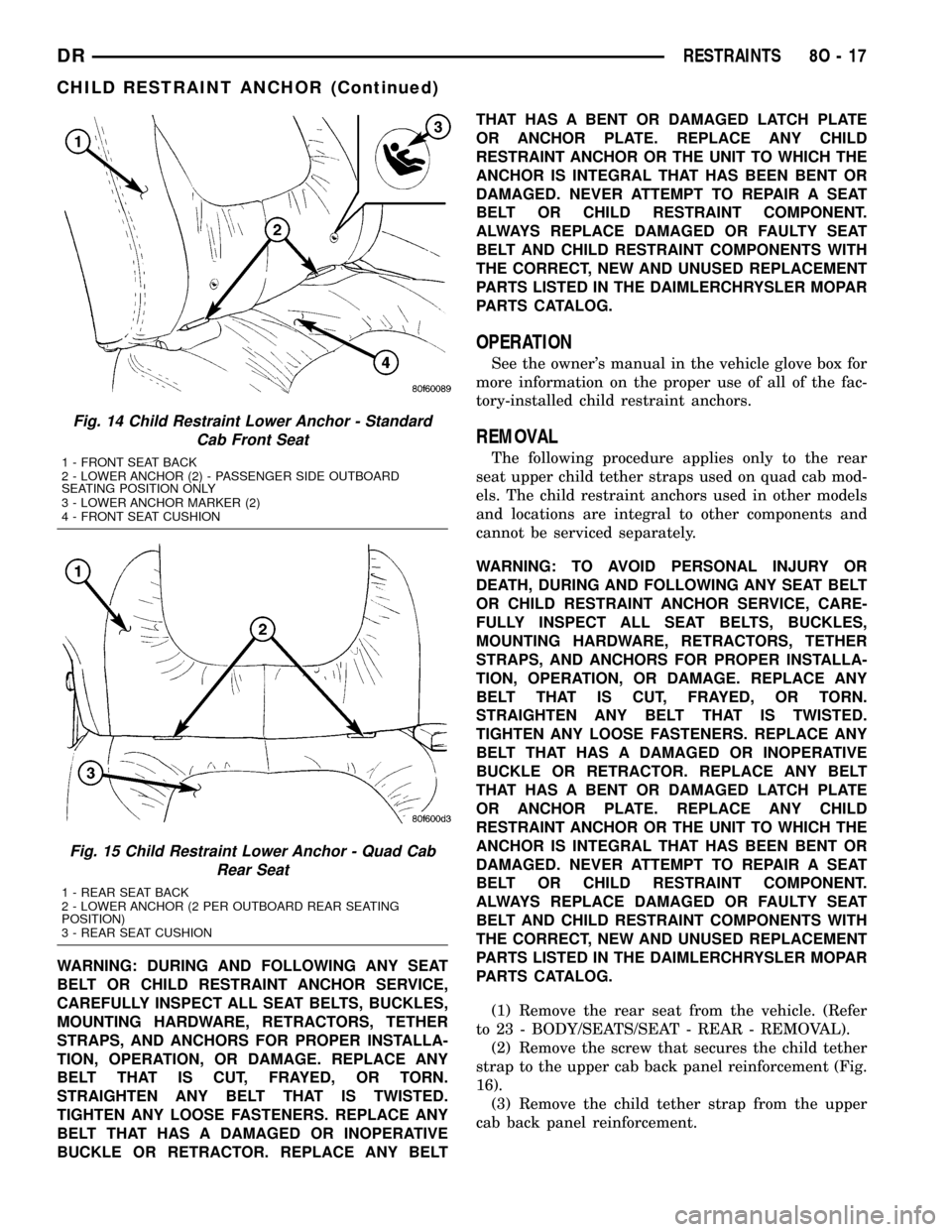
WARNING: DURING AND FOLLOWING ANY SEAT
BELT OR CHILD RESTRAINT ANCHOR SERVICE,
CAREFULLY INSPECT ALL SEAT BELTS, BUCKLES,
MOUNTING HARDWARE, RETRACTORS, TETHER
STRAPS, AND ANCHORS FOR PROPER INSTALLA-
TION, OPERATION, OR DAMAGE. REPLACE ANY
BELT THAT IS CUT, FRAYED, OR TORN.
STRAIGHTEN ANY BELT THAT IS TWISTED.
TIGHTEN ANY LOOSE FASTENERS. REPLACE ANY
BELT THAT HAS A DAMAGED OR INOPERATIVE
BUCKLE OR RETRACTOR. REPLACE ANY BELTTHAT HAS A BENT OR DAMAGED LATCH PLATE
OR ANCHOR PLATE. REPLACE ANY CHILD
RESTRAINT ANCHOR OR THE UNIT TO WHICH THE
ANCHOR IS INTEGRAL THAT HAS BEEN BENT OR
DAMAGED. NEVER ATTEMPT TO REPAIR A SEAT
BELT OR CHILD RESTRAINT COMPONENT.
ALWAYS REPLACE DAMAGED OR FAULTY SEAT
BELT AND CHILD RESTRAINT COMPONENTS WITH
THE CORRECT, NEW AND UNUSED REPLACEMENT
PARTS LISTED IN THE DAIMLERCHRYSLER MOPAR
PARTS CATALOG.
OPERATION
See the owner's manual in the vehicle glove box for
more information on the proper use of all of the fac-
tory-installed child restraint anchors.
REMOVAL
The following procedure applies only to the rear
seat upper child tether straps used on quad cab mod-
els. The child restraint anchors used in other models
and locations are integral to other components and
cannot be serviced separately.
WARNING: TO AVOID PERSONAL INJURY OR
DEATH, DURING AND FOLLOWING ANY SEAT BELT
OR CHILD RESTRAINT ANCHOR SERVICE, CARE-
FULLY INSPECT ALL SEAT BELTS, BUCKLES,
MOUNTING HARDWARE, RETRACTORS, TETHER
STRAPS, AND ANCHORS FOR PROPER INSTALLA-
TION, OPERATION, OR DAMAGE. REPLACE ANY
BELT THAT IS CUT, FRAYED, OR TORN.
STRAIGHTEN ANY BELT THAT IS TWISTED.
TIGHTEN ANY LOOSE FASTENERS. REPLACE ANY
BELT THAT HAS A DAMAGED OR INOPERATIVE
BUCKLE OR RETRACTOR. REPLACE ANY BELT
THAT HAS A BENT OR DAMAGED LATCH PLATE
OR ANCHOR PLATE. REPLACE ANY CHILD
RESTRAINT ANCHOR OR THE UNIT TO WHICH THE
ANCHOR IS INTEGRAL THAT HAS BEEN BENT OR
DAMAGED. NEVER ATTEMPT TO REPAIR A SEAT
BELT OR CHILD RESTRAINT COMPONENT.
ALWAYS REPLACE DAMAGED OR FAULTY SEAT
BELT AND CHILD RESTRAINT COMPONENTS WITH
THE CORRECT, NEW AND UNUSED REPLACEMENT
PARTS LISTED IN THE DAIMLERCHRYSLER MOPAR
PARTS CATALOG.
(1) Remove the rear seat from the vehicle. (Refer
to 23 - BODY/SEATS/SEAT - REAR - REMOVAL).
(2) Remove the screw that secures the child tether
strap to the upper cab back panel reinforcement (Fig.
16).
(3) Remove the child tether strap from the upper
cab back panel reinforcement.
Fig. 14 Child Restraint Lower Anchor - Standard
Cab Front Seat
1 - FRONT SEAT BACK
2 - LOWER ANCHOR (2) - PASSENGER SIDE OUTBOARD
SEATING POSITION ONLY
3 - LOWER ANCHOR MARKER (2)
4 - FRONT SEAT CUSHION
Fig. 15 Child Restraint Lower Anchor - Quad Cab
Rear Seat
1 - REAR SEAT BACK
2 - LOWER ANCHOR (2 PER OUTBOARD REAR SEATING
POSITION)
3 - REAR SEAT CUSHION
DRRESTRAINTS 8O - 17
CHILD RESTRAINT ANCHOR (Continued)
Page 637 of 2627
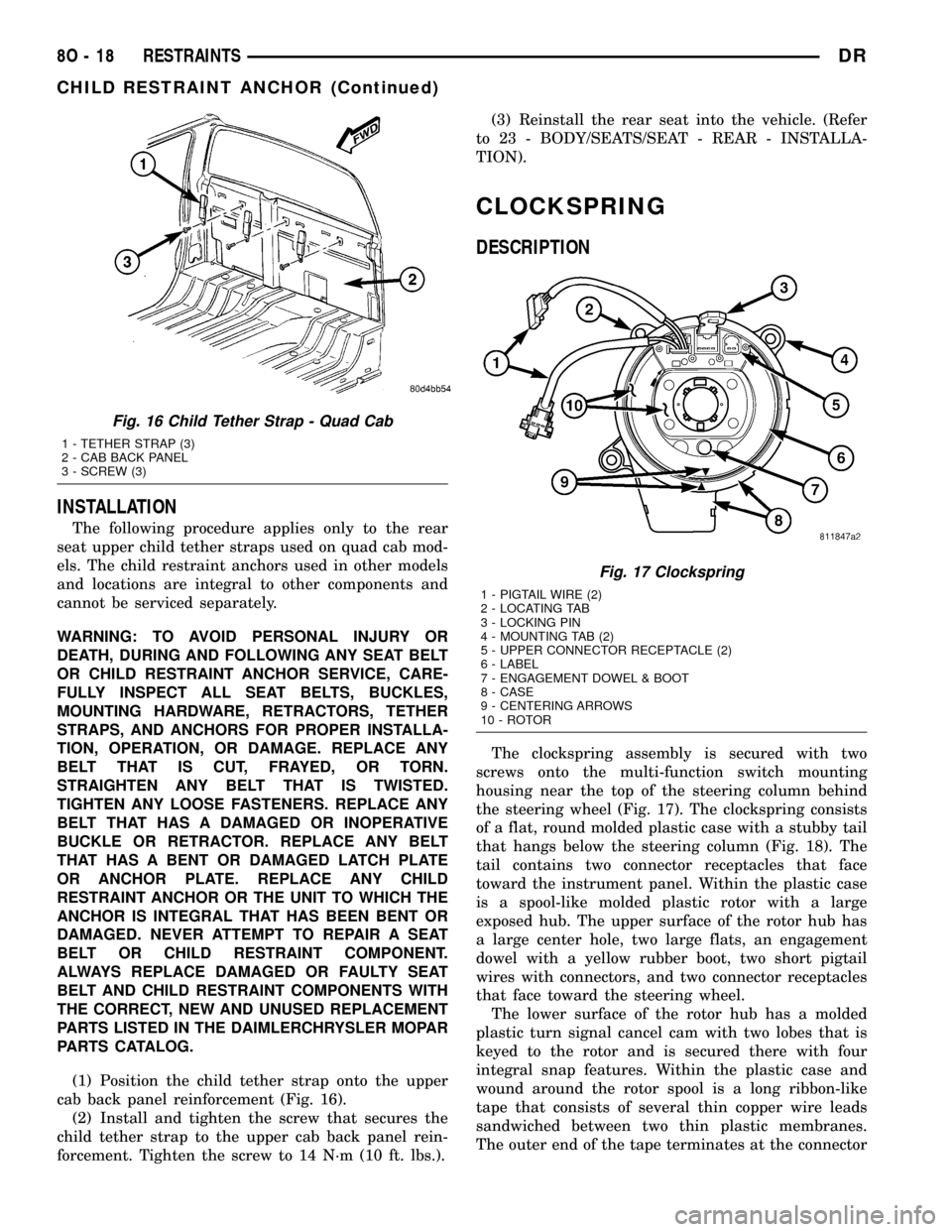
INSTALLATION
The following procedure applies only to the rear
seat upper child tether straps used on quad cab mod-
els. The child restraint anchors used in other models
and locations are integral to other components and
cannot be serviced separately.
WARNING: TO AVOID PERSONAL INJURY OR
DEATH, DURING AND FOLLOWING ANY SEAT BELT
OR CHILD RESTRAINT ANCHOR SERVICE, CARE-
FULLY INSPECT ALL SEAT BELTS, BUCKLES,
MOUNTING HARDWARE, RETRACTORS, TETHER
STRAPS, AND ANCHORS FOR PROPER INSTALLA-
TION, OPERATION, OR DAMAGE. REPLACE ANY
BELT THAT IS CUT, FRAYED, OR TORN.
STRAIGHTEN ANY BELT THAT IS TWISTED.
TIGHTEN ANY LOOSE FASTENERS. REPLACE ANY
BELT THAT HAS A DAMAGED OR INOPERATIVE
BUCKLE OR RETRACTOR. REPLACE ANY BELT
THAT HAS A BENT OR DAMAGED LATCH PLATE
OR ANCHOR PLATE. REPLACE ANY CHILD
RESTRAINT ANCHOR OR THE UNIT TO WHICH THE
ANCHOR IS INTEGRAL THAT HAS BEEN BENT OR
DAMAGED. NEVER ATTEMPT TO REPAIR A SEAT
BELT OR CHILD RESTRAINT COMPONENT.
ALWAYS REPLACE DAMAGED OR FAULTY SEAT
BELT AND CHILD RESTRAINT COMPONENTS WITH
THE CORRECT, NEW AND UNUSED REPLACEMENT
PARTS LISTED IN THE DAIMLERCHRYSLER MOPAR
PARTS CATALOG.
(1) Position the child tether strap onto the upper
cab back panel reinforcement (Fig. 16).
(2) Install and tighten the screw that secures the
child tether strap to the upper cab back panel rein-
forcement. Tighten the screw to 14 N´m (10 ft. lbs.).(3) Reinstall the rear seat into the vehicle. (Refer
to 23 - BODY/SEATS/SEAT - REAR - INSTALLA-
TION).
CLOCKSPRING
DESCRIPTION
The clockspring assembly is secured with two
screws onto the multi-function switch mounting
housing near the top of the steering column behind
the steering wheel (Fig. 17). The clockspring consists
of a flat, round molded plastic case with a stubby tail
that hangs below the steering column (Fig. 18). The
tail contains two connector receptacles that face
toward the instrument panel. Within the plastic case
is a spool-like molded plastic rotor with a large
exposed hub. The upper surface of the rotor hub has
a large center hole, two large flats, an engagement
dowel with a yellow rubber boot, two short pigtail
wires with connectors, and two connector receptacles
that face toward the steering wheel.
The lower surface of the rotor hub has a molded
plastic turn signal cancel cam with two lobes that is
keyed to the rotor and is secured there with four
integral snap features. Within the plastic case and
wound around the rotor spool is a long ribbon-like
tape that consists of several thin copper wire leads
sandwiched between two thin plastic membranes.
The outer end of the tape terminates at the connector
Fig. 16 Child Tether Strap - Quad Cab
1 - TETHER STRAP (3)
2 - CAB BACK PANEL
3 - SCREW (3)
Fig. 17 Clockspring
1 - PIGTAIL WIRE (2)
2 - LOCATING TAB
3 - LOCKING PIN
4 - MOUNTING TAB (2)
5 - UPPER CONNECTOR RECEPTACLE (2)
6 - LABEL
7 - ENGAGEMENT DOWEL & BOOT
8 - CASE
9 - CENTERING ARROWS
10 - ROTOR
8O - 18 RESTRAINTSDR
CHILD RESTRAINT ANCHOR (Continued)
Page 638 of 2627
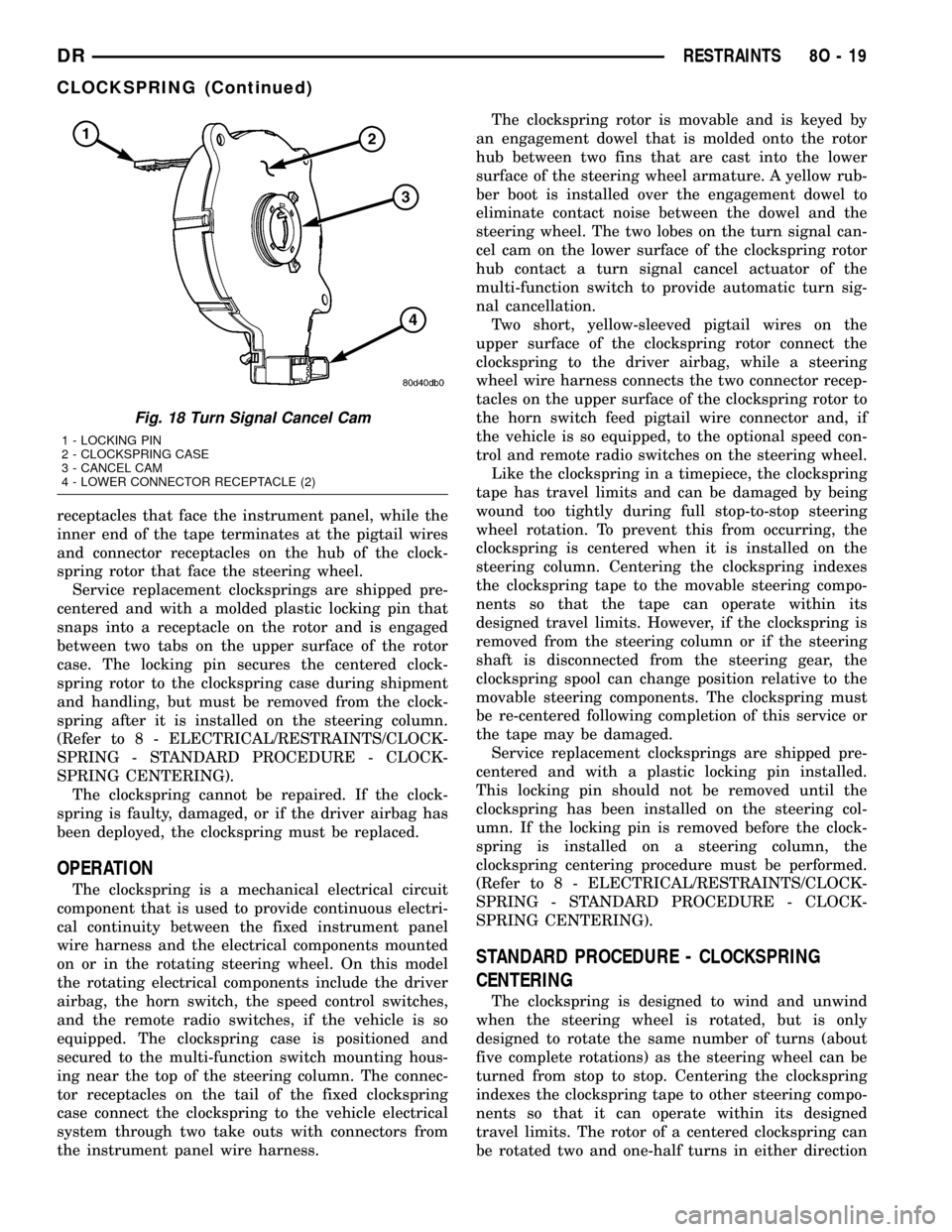
receptacles that face the instrument panel, while the
inner end of the tape terminates at the pigtail wires
and connector receptacles on the hub of the clock-
spring rotor that face the steering wheel.
Service replacement clocksprings are shipped pre-
centered and with a molded plastic locking pin that
snaps into a receptacle on the rotor and is engaged
between two tabs on the upper surface of the rotor
case. The locking pin secures the centered clock-
spring rotor to the clockspring case during shipment
and handling, but must be removed from the clock-
spring after it is installed on the steering column.
(Refer to 8 - ELECTRICAL/RESTRAINTS/CLOCK-
SPRING - STANDARD PROCEDURE - CLOCK-
SPRING CENTERING).
The clockspring cannot be repaired. If the clock-
spring is faulty, damaged, or if the driver airbag has
been deployed, the clockspring must be replaced.
OPERATION
The clockspring is a mechanical electrical circuit
component that is used to provide continuous electri-
cal continuity between the fixed instrument panel
wire harness and the electrical components mounted
on or in the rotating steering wheel. On this model
the rotating electrical components include the driver
airbag, the horn switch, the speed control switches,
and the remote radio switches, if the vehicle is so
equipped. The clockspring case is positioned and
secured to the multi-function switch mounting hous-
ing near the top of the steering column. The connec-
tor receptacles on the tail of the fixed clockspring
case connect the clockspring to the vehicle electrical
system through two take outs with connectors from
the instrument panel wire harness.The clockspring rotor is movable and is keyed by
an engagement dowel that is molded onto the rotor
hub between two fins that are cast into the lower
surface of the steering wheel armature. A yellow rub-
ber boot is installed over the engagement dowel to
eliminate contact noise between the dowel and the
steering wheel. The two lobes on the turn signal can-
cel cam on the lower surface of the clockspring rotor
hub contact a turn signal cancel actuator of the
multi-function switch to provide automatic turn sig-
nal cancellation.
Two short, yellow-sleeved pigtail wires on the
upper surface of the clockspring rotor connect the
clockspring to the driver airbag, while a steering
wheel wire harness connects the two connector recep-
tacles on the upper surface of the clockspring rotor to
the horn switch feed pigtail wire connector and, if
the vehicle is so equipped, to the optional speed con-
trol and remote radio switches on the steering wheel.
Like the clockspring in a timepiece, the clockspring
tape has travel limits and can be damaged by being
wound too tightly during full stop-to-stop steering
wheel rotation. To prevent this from occurring, the
clockspring is centered when it is installed on the
steering column. Centering the clockspring indexes
the clockspring tape to the movable steering compo-
nents so that the tape can operate within its
designed travel limits. However, if the clockspring is
removed from the steering column or if the steering
shaft is disconnected from the steering gear, the
clockspring spool can change position relative to the
movable steering components. The clockspring must
be re-centered following completion of this service or
the tape may be damaged.
Service replacement clocksprings are shipped pre-
centered and with a plastic locking pin installed.
This locking pin should not be removed until the
clockspring has been installed on the steering col-
umn. If the locking pin is removed before the clock-
spring is installed on a steering column, the
clockspring centering procedure must be performed.
(Refer to 8 - ELECTRICAL/RESTRAINTS/CLOCK-
SPRING - STANDARD PROCEDURE - CLOCK-
SPRING CENTERING).
STANDARD PROCEDURE - CLOCKSPRING
CENTERING
The clockspring is designed to wind and unwind
when the steering wheel is rotated, but is only
designed to rotate the same number of turns (about
five complete rotations) as the steering wheel can be
turned from stop to stop. Centering the clockspring
indexes the clockspring tape to other steering compo-
nents so that it can operate within its designed
travel limits. The rotor of a centered clockspring can
be rotated two and one-half turns in either direction
Fig. 18 Turn Signal Cancel Cam
1 - LOCKING PIN
2 - CLOCKSPRING CASE
3 - CANCEL CAM
4 - LOWER CONNECTOR RECEPTACLE (2)
DRRESTRAINTS 8O - 19
CLOCKSPRING (Continued)
Page 639 of 2627
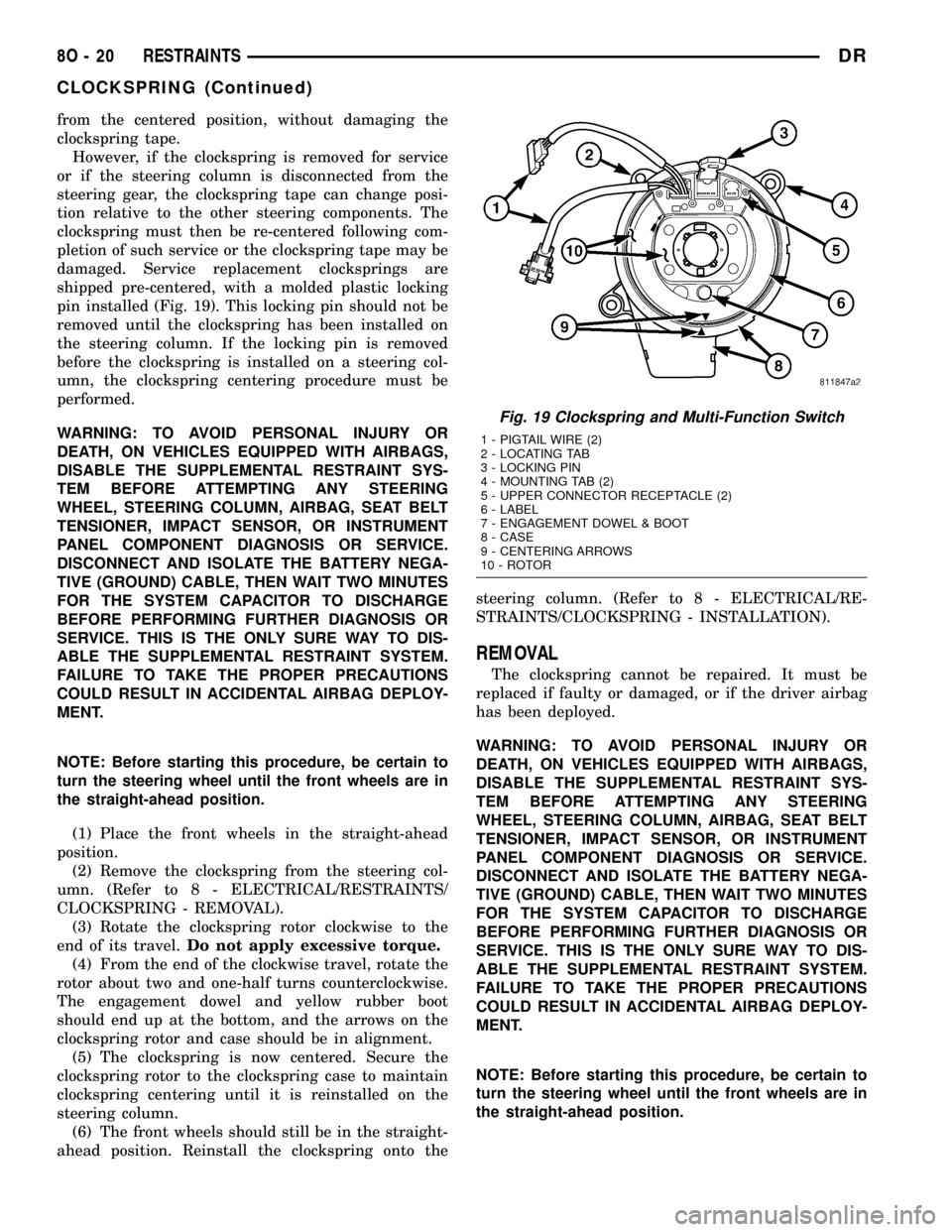
from the centered position, without damaging the
clockspring tape.
However, if the clockspring is removed for service
or if the steering column is disconnected from the
steering gear, the clockspring tape can change posi-
tion relative to the other steering components. The
clockspring must then be re-centered following com-
pletion of such service or the clockspring tape may be
damaged. Service replacement clocksprings are
shipped pre-centered, with a molded plastic locking
pin installed (Fig. 19). This locking pin should not be
removed until the clockspring has been installed on
the steering column. If the locking pin is removed
before the clockspring is installed on a steering col-
umn, the clockspring centering procedure must be
performed.
WARNING: TO AVOID PERSONAL INJURY OR
DEATH, ON VEHICLES EQUIPPED WITH AIRBAGS,
DISABLE THE SUPPLEMENTAL RESTRAINT SYS-
TEM BEFORE ATTEMPTING ANY STEERING
WHEEL, STEERING COLUMN, AIRBAG, SEAT BELT
TENSIONER, IMPACT SENSOR, OR INSTRUMENT
PANEL COMPONENT DIAGNOSIS OR SERVICE.
DISCONNECT AND ISOLATE THE BATTERY NEGA-
TIVE (GROUND) CABLE, THEN WAIT TWO MINUTES
FOR THE SYSTEM CAPACITOR TO DISCHARGE
BEFORE PERFORMING FURTHER DIAGNOSIS OR
SERVICE. THIS IS THE ONLY SURE WAY TO DIS-
ABLE THE SUPPLEMENTAL RESTRAINT SYSTEM.
FAILURE TO TAKE THE PROPER PRECAUTIONS
COULD RESULT IN ACCIDENTAL AIRBAG DEPLOY-
MENT.
NOTE: Before starting this procedure, be certain to
turn the steering wheel until the front wheels are in
the straight-ahead position.
(1) Place the front wheels in the straight-ahead
position.
(2) Remove the clockspring from the steering col-
umn. (Refer to 8 - ELECTRICAL/RESTRAINTS/
CLOCKSPRING - REMOVAL).
(3) Rotate the clockspring rotor clockwise to the
end of its travel.Do not apply excessive torque.
(4) From the end of the clockwise travel, rotate the
rotor about two and one-half turns counterclockwise.
The engagement dowel and yellow rubber boot
should end up at the bottom, and the arrows on the
clockspring rotor and case should be in alignment.
(5) The clockspring is now centered. Secure the
clockspring rotor to the clockspring case to maintain
clockspring centering until it is reinstalled on the
steering column.
(6) The front wheels should still be in the straight-
ahead position. Reinstall the clockspring onto thesteering column. (Refer to 8 - ELECTRICAL/RE-
STRAINTS/CLOCKSPRING - INSTALLATION).
REMOVAL
The clockspring cannot be repaired. It must be
replaced if faulty or damaged, or if the driver airbag
has been deployed.
WARNING: TO AVOID PERSONAL INJURY OR
DEATH, ON VEHICLES EQUIPPED WITH AIRBAGS,
DISABLE THE SUPPLEMENTAL RESTRAINT SYS-
TEM BEFORE ATTEMPTING ANY STEERING
WHEEL, STEERING COLUMN, AIRBAG, SEAT BELT
TENSIONER, IMPACT SENSOR, OR INSTRUMENT
PANEL COMPONENT DIAGNOSIS OR SERVICE.
DISCONNECT AND ISOLATE THE BATTERY NEGA-
TIVE (GROUND) CABLE, THEN WAIT TWO MINUTES
FOR THE SYSTEM CAPACITOR TO DISCHARGE
BEFORE PERFORMING FURTHER DIAGNOSIS OR
SERVICE. THIS IS THE ONLY SURE WAY TO DIS-
ABLE THE SUPPLEMENTAL RESTRAINT SYSTEM.
FAILURE TO TAKE THE PROPER PRECAUTIONS
COULD RESULT IN ACCIDENTAL AIRBAG DEPLOY-
MENT.
NOTE: Before starting this procedure, be certain to
turn the steering wheel until the front wheels are in
the straight-ahead position.
Fig. 19 Clockspring and Multi-Function Switch
1 - PIGTAIL WIRE (2)
2 - LOCATING TAB
3 - LOCKING PIN
4 - MOUNTING TAB (2)
5 - UPPER CONNECTOR RECEPTACLE (2)
6 - LABEL
7 - ENGAGEMENT DOWEL & BOOT
8 - CASE
9 - CENTERING ARROWS
10 - ROTOR
8O - 20 RESTRAINTSDR
CLOCKSPRING (Continued)
Page 640 of 2627
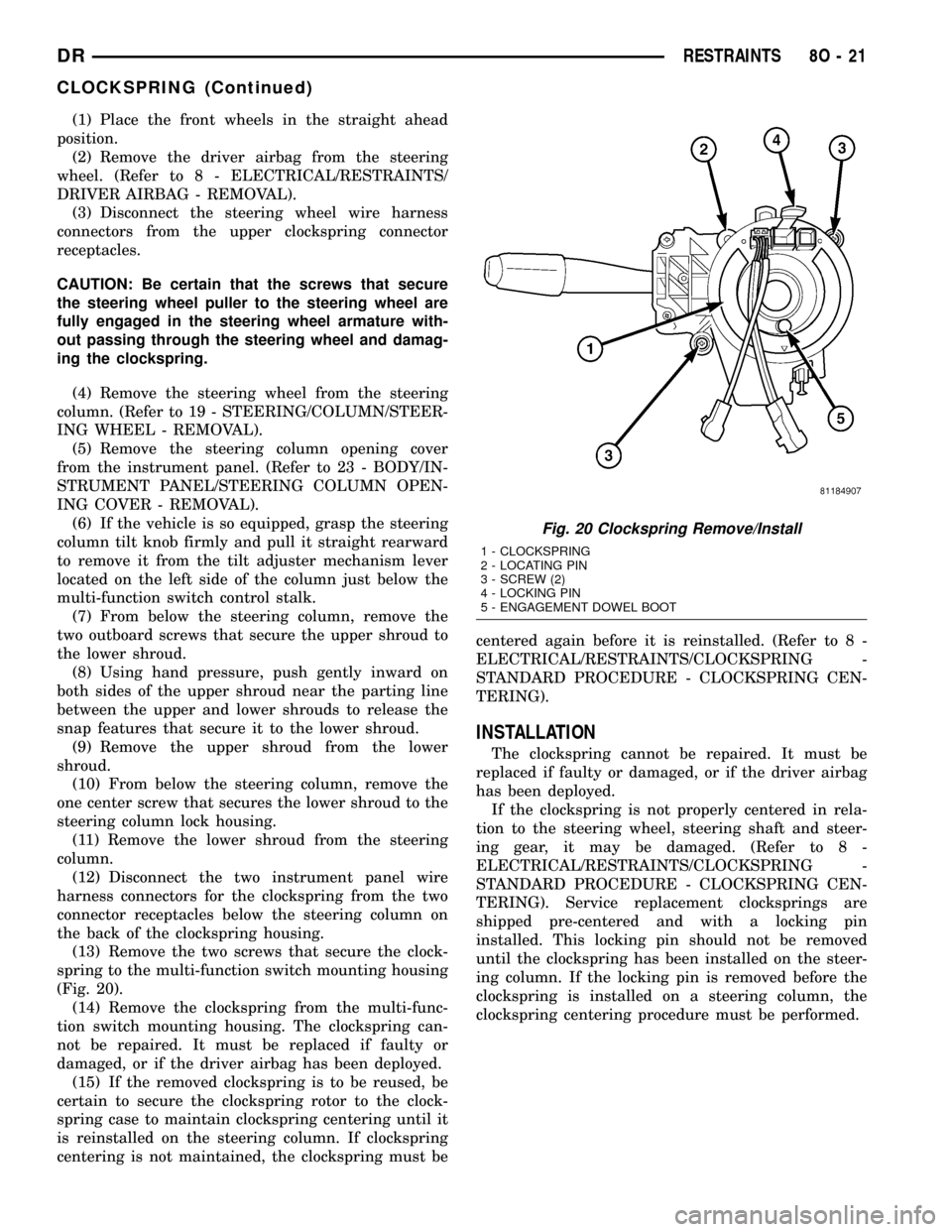
(1) Place the front wheels in the straight ahead
position.
(2) Remove the driver airbag from the steering
wheel. (Refer to 8 - ELECTRICAL/RESTRAINTS/
DRIVER AIRBAG - REMOVAL).
(3) Disconnect the steering wheel wire harness
connectors from the upper clockspring connector
receptacles.
CAUTION: Be certain that the screws that secure
the steering wheel puller to the steering wheel are
fully engaged in the steering wheel armature with-
out passing through the steering wheel and damag-
ing the clockspring.
(4) Remove the steering wheel from the steering
column. (Refer to 19 - STEERING/COLUMN/STEER-
ING WHEEL - REMOVAL).
(5) Remove the steering column opening cover
from the instrument panel. (Refer to 23 - BODY/IN-
STRUMENT PANEL/STEERING COLUMN OPEN-
ING COVER - REMOVAL).
(6) If the vehicle is so equipped, grasp the steering
column tilt knob firmly and pull it straight rearward
to remove it from the tilt adjuster mechanism lever
located on the left side of the column just below the
multi-function switch control stalk.
(7) From below the steering column, remove the
two outboard screws that secure the upper shroud to
the lower shroud.
(8) Using hand pressure, push gently inward on
both sides of the upper shroud near the parting line
between the upper and lower shrouds to release the
snap features that secure it to the lower shroud.
(9) Remove the upper shroud from the lower
shroud.
(10) From below the steering column, remove the
one center screw that secures the lower shroud to the
steering column lock housing.
(11) Remove the lower shroud from the steering
column.
(12) Disconnect the two instrument panel wire
harness connectors for the clockspring from the two
connector receptacles below the steering column on
the back of the clockspring housing.
(13) Remove the two screws that secure the clock-
spring to the multi-function switch mounting housing
(Fig. 20).
(14) Remove the clockspring from the multi-func-
tion switch mounting housing. The clockspring can-
not be repaired. It must be replaced if faulty or
damaged, or if the driver airbag has been deployed.
(15) If the removed clockspring is to be reused, be
certain to secure the clockspring rotor to the clock-
spring case to maintain clockspring centering until it
is reinstalled on the steering column. If clockspring
centering is not maintained, the clockspring must becentered again before it is reinstalled. (Refer to 8 -
ELECTRICAL/RESTRAINTS/CLOCKSPRING -
STANDARD PROCEDURE - CLOCKSPRING CEN-
TERING).
INSTALLATION
The clockspring cannot be repaired. It must be
replaced if faulty or damaged, or if the driver airbag
has been deployed.
If the clockspring is not properly centered in rela-
tion to the steering wheel, steering shaft and steer-
ing gear, it may be damaged. (Refer to 8 -
ELECTRICAL/RESTRAINTS/CLOCKSPRING -
STANDARD PROCEDURE - CLOCKSPRING CEN-
TERING). Service replacement clocksprings are
shipped pre-centered and with a locking pin
installed. This locking pin should not be removed
until the clockspring has been installed on the steer-
ing column. If the locking pin is removed before the
clockspring is installed on a steering column, the
clockspring centering procedure must be performed.
Fig. 20 Clockspring Remove/Install
1 - CLOCKSPRING
2 - LOCATING PIN
3 - SCREW (2)
4 - LOCKING PIN
5 - ENGAGEMENT DOWEL BOOT
DRRESTRAINTS 8O - 21
CLOCKSPRING (Continued)