check engine DODGE RAM 1500 1998 2.G Repair Manual
[x] Cancel search | Manufacturer: DODGE, Model Year: 1998, Model line: RAM 1500, Model: DODGE RAM 1500 1998 2.GPages: 2627
Page 365 of 2627
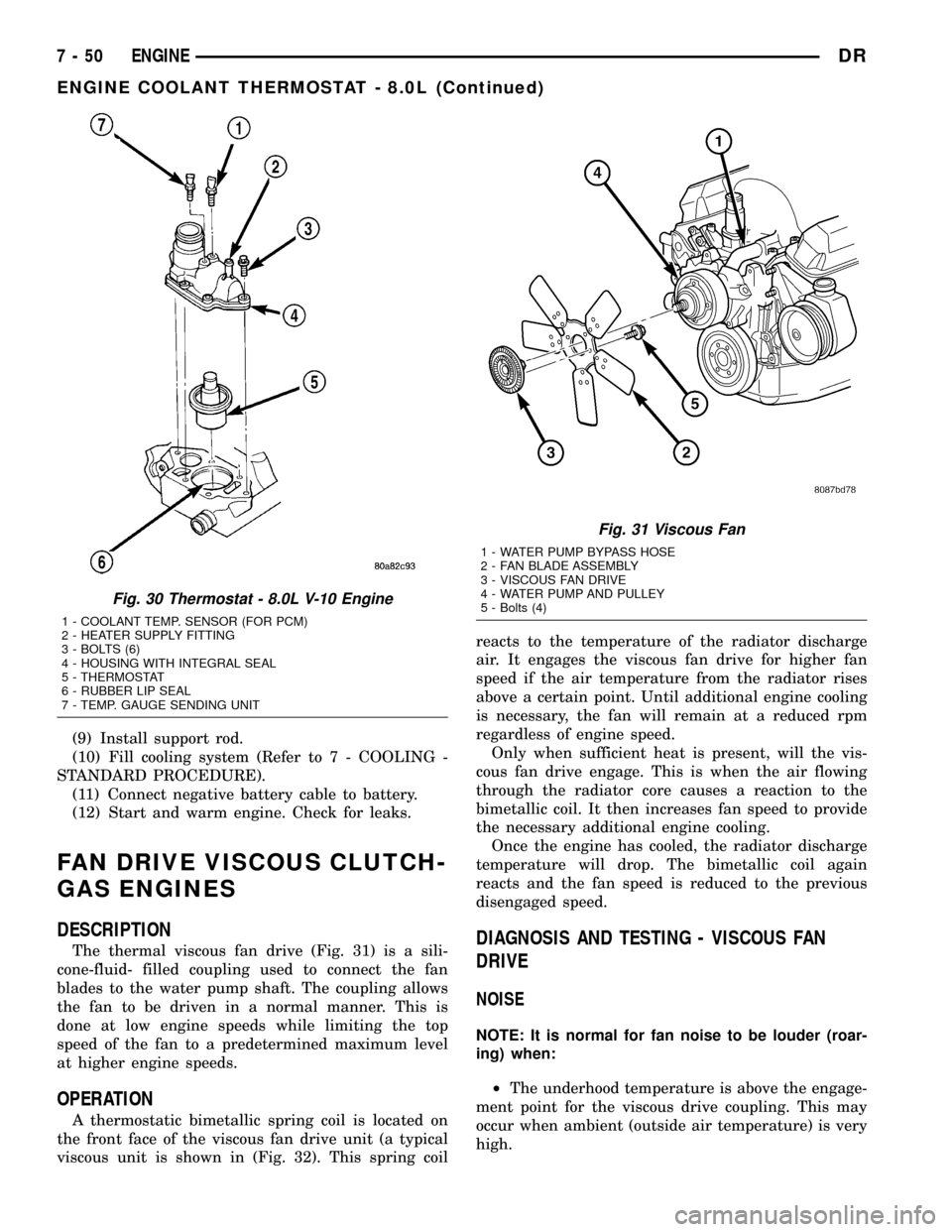
(9) Install support rod.
(10) Fill cooling system (Refer to 7 - COOLING -
STANDARD PROCEDURE).
(11) Connect negative battery cable to battery.
(12) Start and warm engine. Check for leaks.
FAN DRIVE VISCOUS CLUTCH-
GAS ENGINES
DESCRIPTION
The thermal viscous fan drive (Fig. 31) is a sili-
cone-fluid- filled coupling used to connect the fan
blades to the water pump shaft. The coupling allows
the fan to be driven in a normal manner. This is
done at low engine speeds while limiting the top
speed of the fan to a predetermined maximum level
at higher engine speeds.
OPERATION
A thermostatic bimetallic spring coil is located on
the front face of the viscous fan drive unit (a typical
viscous unit is shown in (Fig. 32). This spring coilreacts to the temperature of the radiator discharge
air. It engages the viscous fan drive for higher fan
speed if the air temperature from the radiator rises
above a certain point. Until additional engine cooling
is necessary, the fan will remain at a reduced rpm
regardless of engine speed.
Only when sufficient heat is present, will the vis-
cous fan drive engage. This is when the air flowing
through the radiator core causes a reaction to the
bimetallic coil. It then increases fan speed to provide
the necessary additional engine cooling.
Once the engine has cooled, the radiator discharge
temperature will drop. The bimetallic coil again
reacts and the fan speed is reduced to the previous
disengaged speed.
DIAGNOSIS AND TESTING - VISCOUS FAN
DRIVE
NOISE
NOTE: It is normal for fan noise to be louder (roar-
ing) when:
²The underhood temperature is above the engage-
ment point for the viscous drive coupling. This may
occur when ambient (outside air temperature) is very
high.
Fig. 30 Thermostat - 8.0L V-10 Engine
1 - COOLANT TEMP. SENSOR (FOR PCM)
2 - HEATER SUPPLY FITTING
3 - BOLTS (6)
4 - HOUSING WITH INTEGRAL SEAL
5 - THERMOSTAT
6 - RUBBER LIP SEAL
7 - TEMP. GAUGE SENDING UNIT
Fig. 31 Viscous Fan
1 - WATER PUMP BYPASS HOSE
2 - FAN BLADE ASSEMBLY
3 - VISCOUS FAN DRIVE
4 - WATER PUMP AND PULLEY
5 - Bolts (4)
7 - 50 ENGINEDR
ENGINE COOLANT THERMOSTAT - 8.0L (Continued)
Page 368 of 2627
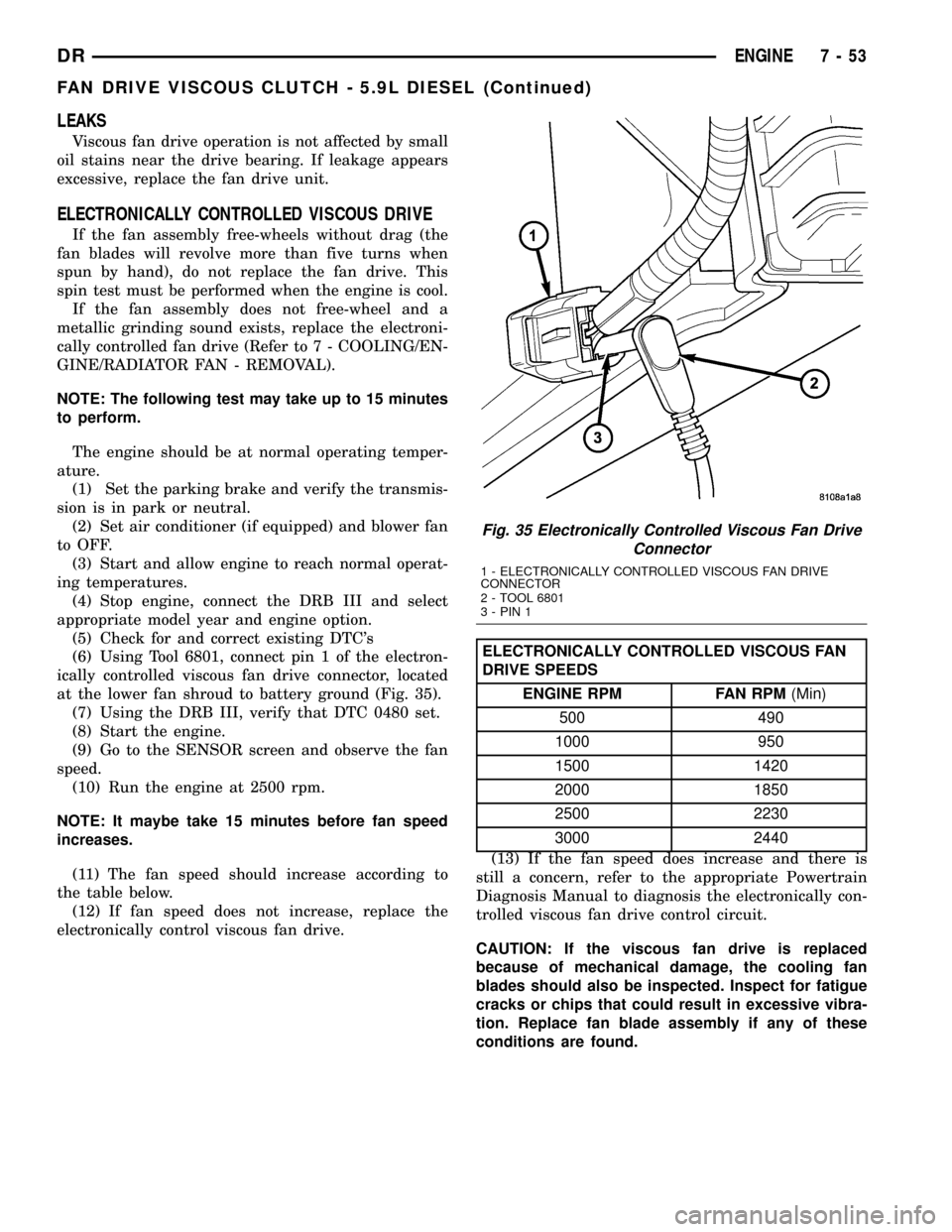
LEAKS
Viscous fan drive operation is not affected by small
oil stains near the drive bearing. If leakage appears
excessive, replace the fan drive unit.
ELECTRONICALLY CONTROLLED VISCOUS DRIVE
If the fan assembly free-wheels without drag (the
fan blades will revolve more than five turns when
spun by hand), do not replace the fan drive. This
spin test must be performed when the engine is cool.
If the fan assembly does not free-wheel and a
metallic grinding sound exists, replace the electroni-
cally controlled fan drive (Refer to 7 - COOLING/EN-
GINE/RADIATOR FAN - REMOVAL).
NOTE: The following test may take up to 15 minutes
to perform.
The engine should be at normal operating temper-
ature.
(1) Set the parking brake and verify the transmis-
sion is in park or neutral.
(2) Set air conditioner (if equipped) and blower fan
to OFF.
(3) Start and allow engine to reach normal operat-
ing temperatures.
(4) Stop engine, connect the DRB III and select
appropriate model year and engine option.
(5) Check for and correct existing DTC's
(6) Using Tool 6801, connect pin 1 of the electron-
ically controlled viscous fan drive connector, located
at the lower fan shroud to battery ground (Fig. 35).
(7) Using the DRB III, verify that DTC 0480 set.
(8) Start the engine.
(9) Go to the SENSOR screen and observe the fan
speed.
(10) Run the engine at 2500 rpm.
NOTE: It maybe take 15 minutes before fan speed
increases.
(11) The fan speed should increase according to
the table below.
(12) If fan speed does not increase, replace the
electronically control viscous fan drive.
ELECTRONICALLY CONTROLLED VISCOUS FAN
DRIVE SPEEDS
ENGINE RPM FAN RPM(Min)
500 490
1000 950
1500 1420
2000 1850
2500 2230
3000 2440
(13) If the fan speed does increase and there is
still a concern, refer to the appropriate Powertrain
Diagnosis Manual to diagnosis the electronically con-
trolled viscous fan drive control circuit.
CAUTION: If the viscous fan drive is replaced
because of mechanical damage, the cooling fan
blades should also be inspected. Inspect for fatigue
cracks or chips that could result in excessive vibra-
tion. Replace fan blade assembly if any of these
conditions are found.
Fig. 35 Electronically Controlled Viscous Fan Drive
Connector
1 - ELECTRONICALLY CONTROLLED VISCOUS FAN DRIVE
CONNECTOR
2 - TOOL 6801
3 - PIN 1
DRENGINE 7 - 53
FAN DRIVE VISCOUS CLUTCH - 5.9L DIESEL (Continued)
Page 370 of 2627
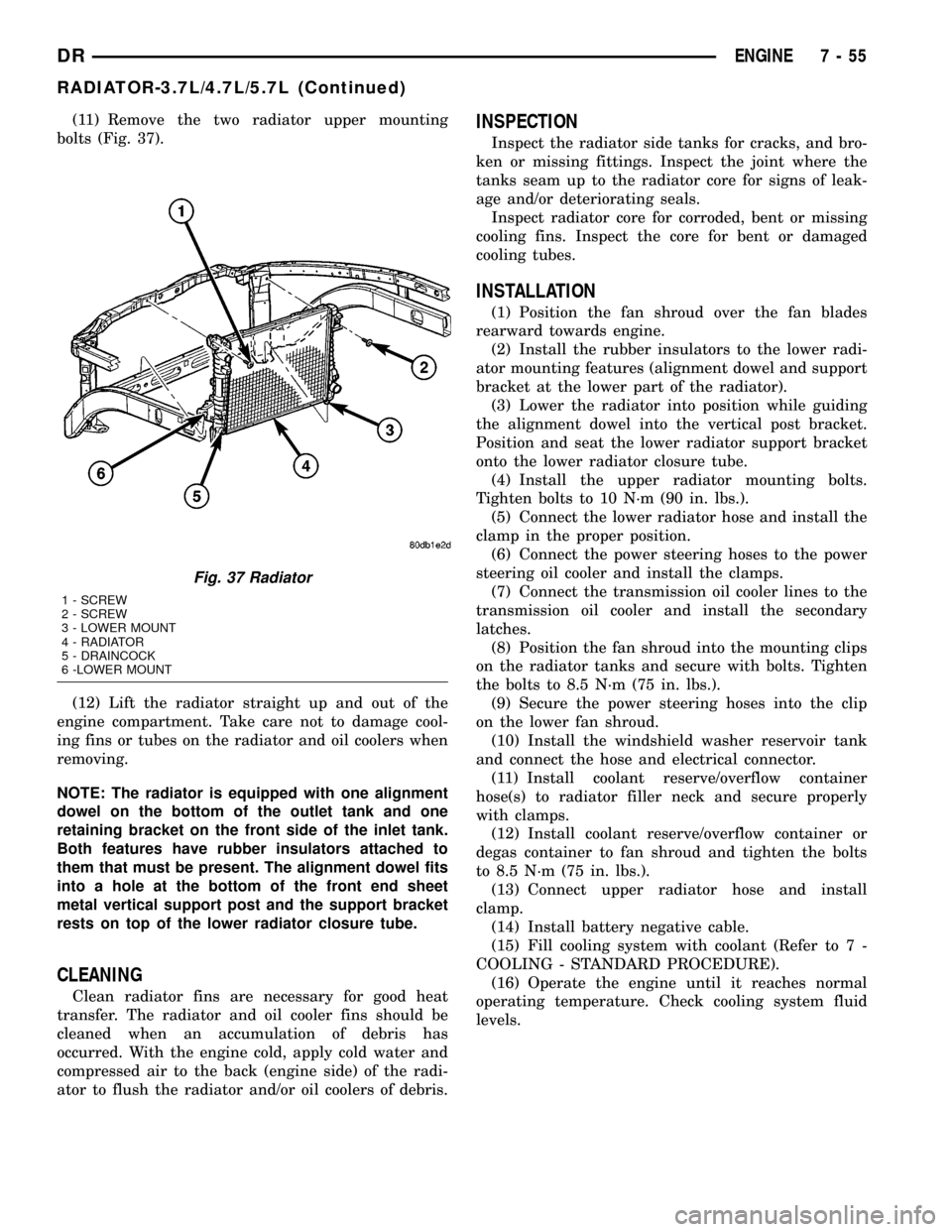
(11) Remove the two radiator upper mounting
bolts (Fig. 37).
(12) Lift the radiator straight up and out of the
engine compartment. Take care not to damage cool-
ing fins or tubes on the radiator and oil coolers when
removing.
NOTE: The radiator is equipped with one alignment
dowel on the bottom of the outlet tank and one
retaining bracket on the front side of the inlet tank.
Both features have rubber insulators attached to
them that must be present. The alignment dowel fits
into a hole at the bottom of the front end sheet
metal vertical support post and the support bracket
rests on top of the lower radiator closure tube.
CLEANING
Clean radiator fins are necessary for good heat
transfer. The radiator and oil cooler fins should be
cleaned when an accumulation of debris has
occurred. With the engine cold, apply cold water and
compressed air to the back (engine side) of the radi-
ator to flush the radiator and/or oil coolers of debris.
INSPECTION
Inspect the radiator side tanks for cracks, and bro-
ken or missing fittings. Inspect the joint where the
tanks seam up to the radiator core for signs of leak-
age and/or deteriorating seals.
Inspect radiator core for corroded, bent or missing
cooling fins. Inspect the core for bent or damaged
cooling tubes.
INSTALLATION
(1) Position the fan shroud over the fan blades
rearward towards engine.
(2) Install the rubber insulators to the lower radi-
ator mounting features (alignment dowel and support
bracket at the lower part of the radiator).
(3) Lower the radiator into position while guiding
the alignment dowel into the vertical post bracket.
Position and seat the lower radiator support bracket
onto the lower radiator closure tube.
(4) Install the upper radiator mounting bolts.
Tighten bolts to 10 N´m (90 in. lbs.).
(5) Connect the lower radiator hose and install the
clamp in the proper position.
(6) Connect the power steering hoses to the power
steering oil cooler and install the clamps.
(7) Connect the transmission oil cooler lines to the
transmission oil cooler and install the secondary
latches.
(8) Position the fan shroud into the mounting clips
on the radiator tanks and secure with bolts. Tighten
the bolts to 8.5 N´m (75 in. lbs.).
(9) Secure the power steering hoses into the clip
on the lower fan shroud.
(10) Install the windshield washer reservoir tank
and connect the hose and electrical connector.
(11) Install coolant reserve/overflow container
hose(s) to radiator filler neck and secure properly
with clamps.
(12) Install coolant reserve/overflow container or
degas container to fan shroud and tighten the bolts
to 8.5 N´m (75 in. lbs.).
(13) Connect upper radiator hose and install
clamp.
(14) Install battery negative cable.
(15) Fill cooling system with coolant (Refer to 7 -
COOLING - STANDARD PROCEDURE).
(16) Operate the engine until it reaches normal
operating temperature. Check cooling system fluid
levels.
Fig. 37 Radiator
1 - SCREW
2 - SCREW
3 - LOWER MOUNT
4 - RADIATOR
5 - DRAINCOCK
6 -LOWER MOUNT
DRENGINE 7 - 55
RADIATOR-3.7L/4.7L/5.7L (Continued)
Page 372 of 2627
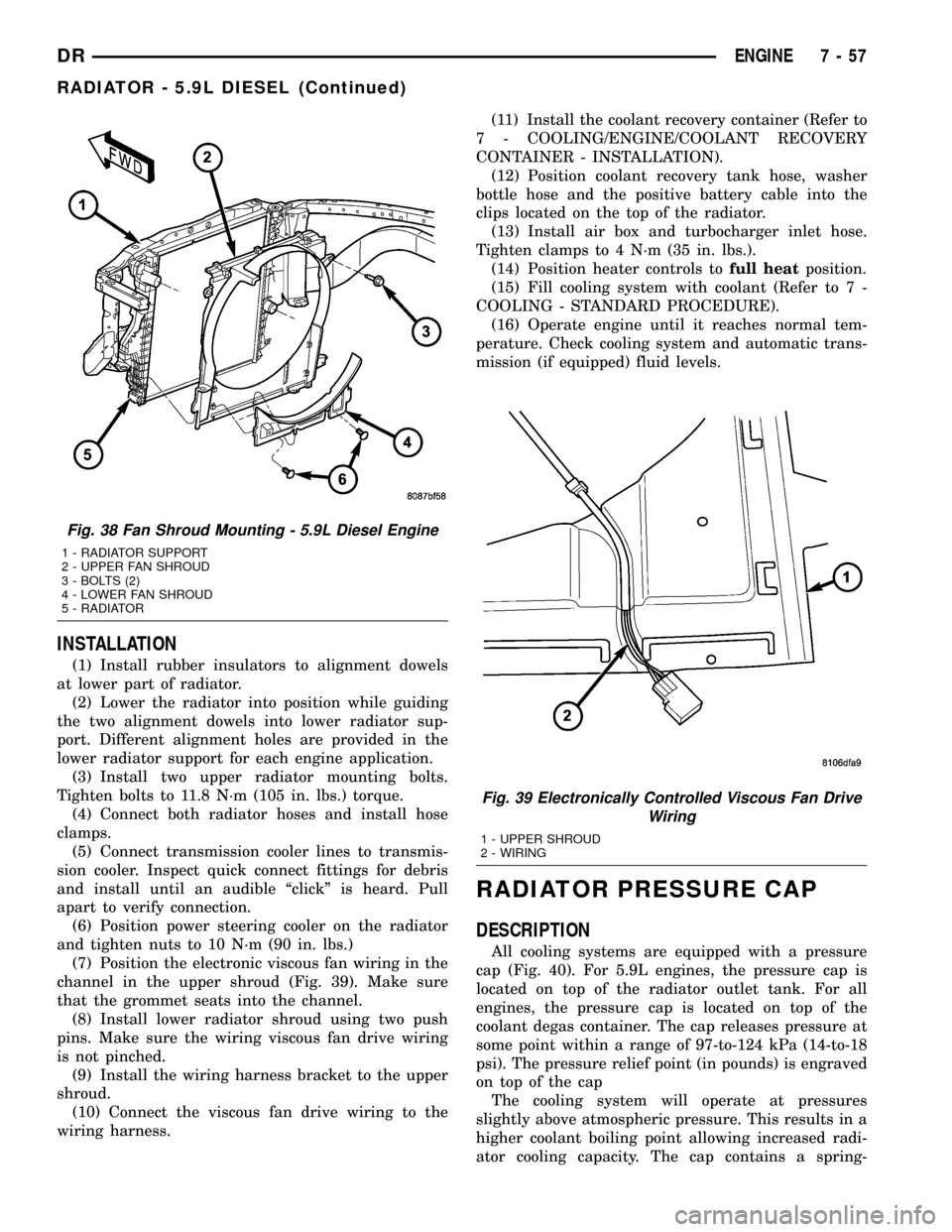
INSTALLATION
(1) Install rubber insulators to alignment dowels
at lower part of radiator.
(2) Lower the radiator into position while guiding
the two alignment dowels into lower radiator sup-
port. Different alignment holes are provided in the
lower radiator support for each engine application.
(3) Install two upper radiator mounting bolts.
Tighten bolts to 11.8 N´m (105 in. lbs.) torque.
(4) Connect both radiator hoses and install hose
clamps.
(5) Connect transmission cooler lines to transmis-
sion cooler. Inspect quick connect fittings for debris
and install until an audible ªclickº is heard. Pull
apart to verify connection.
(6) Position power steering cooler on the radiator
and tighten nuts to 10 N´m (90 in. lbs.)
(7) Position the electronic viscous fan wiring in the
channel in the upper shroud (Fig. 39). Make sure
that the grommet seats into the channel.
(8) Install lower radiator shroud using two push
pins. Make sure the wiring viscous fan drive wiring
is not pinched.
(9) Install the wiring harness bracket to the upper
shroud.
(10) Connect the viscous fan drive wiring to the
wiring harness.(11) Install the coolant recovery container (Refer to
7 - COOLING/ENGINE/COOLANT RECOVERY
CONTAINER - INSTALLATION).
(12) Position coolant recovery tank hose, washer
bottle hose and the positive battery cable into the
clips located on the top of the radiator.
(13) Install air box and turbocharger inlet hose.
Tighten clamps to 4 N´m (35 in. lbs.).
(14) Position heater controls tofull heatposition.
(15) Fill cooling system with coolant (Refer to 7 -
COOLING - STANDARD PROCEDURE).
(16) Operate engine until it reaches normal tem-
perature. Check cooling system and automatic trans-
mission (if equipped) fluid levels.
RADIATOR PRESSURE CAP
DESCRIPTION
All cooling systems are equipped with a pressure
cap (Fig. 40). For 5.9L engines, the pressure cap is
located on top of the radiator outlet tank. For all
engines, the pressure cap is located on top of the
coolant degas container. The cap releases pressure at
some point within a range of 97-to-124 kPa (14-to-18
psi). The pressure relief point (in pounds) is engraved
on top of the cap
The cooling system will operate at pressures
slightly above atmospheric pressure. This results in a
higher coolant boiling point allowing increased radi-
ator cooling capacity. The cap contains a spring-
Fig. 38 Fan Shroud Mounting - 5.9L Diesel Engine
1 - RADIATOR SUPPORT
2 - UPPER FAN SHROUD
3 - BOLTS (2)
4 - LOWER FAN SHROUD
5 - RADIATOR
Fig. 39 Electronically Controlled Viscous Fan Drive
Wiring
1 - UPPER SHROUD
2 - WIRING
DRENGINE 7 - 57
RADIATOR - 5.9L DIESEL (Continued)
Page 373 of 2627
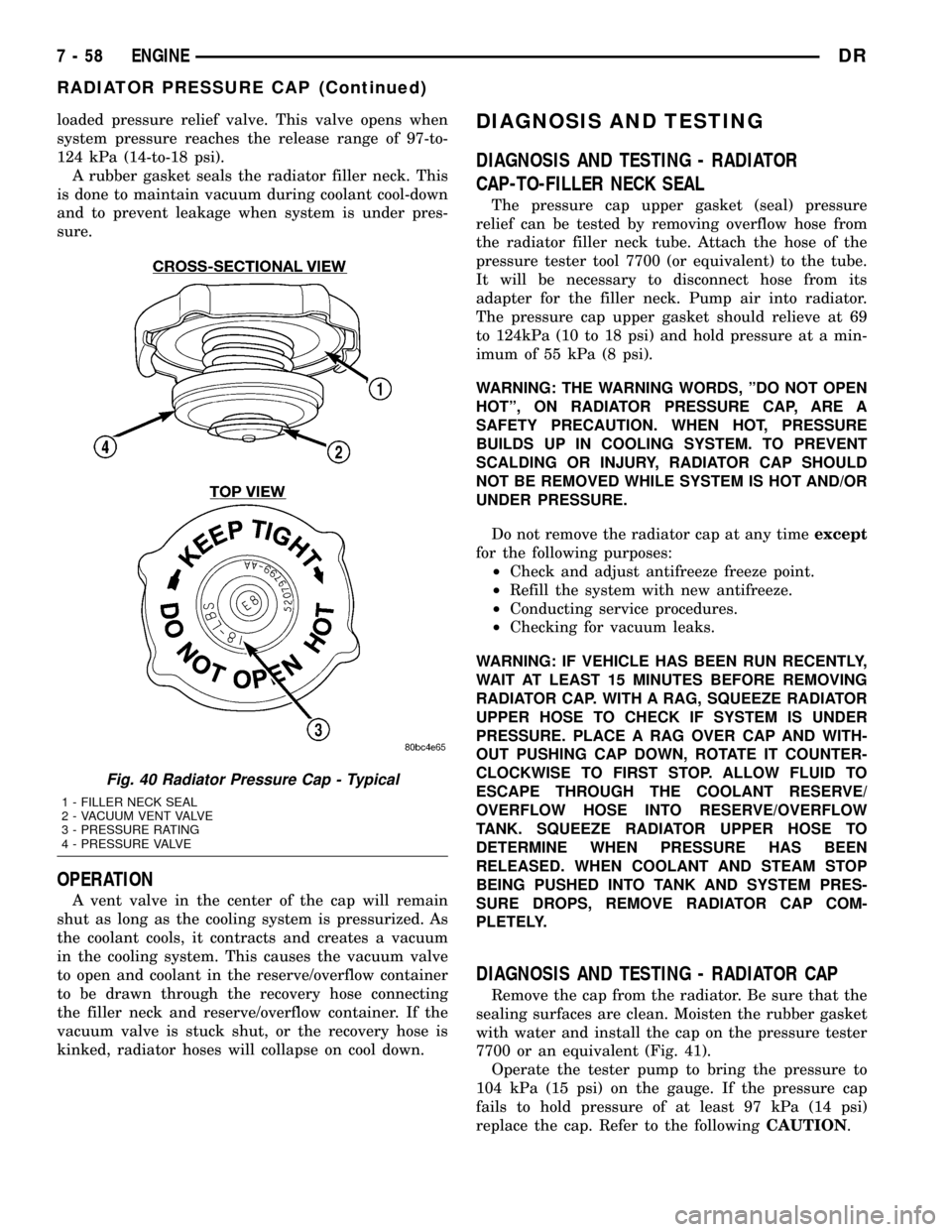
loaded pressure relief valve. This valve opens when
system pressure reaches the release range of 97-to-
124 kPa (14-to-18 psi).
A rubber gasket seals the radiator filler neck. This
is done to maintain vacuum during coolant cool-down
and to prevent leakage when system is under pres-
sure.
OPERATION
A vent valve in the center of the cap will remain
shut as long as the cooling system is pressurized. As
the coolant cools, it contracts and creates a vacuum
in the cooling system. This causes the vacuum valve
to open and coolant in the reserve/overflow container
to be drawn through the recovery hose connecting
the filler neck and reserve/overflow container. If the
vacuum valve is stuck shut, or the recovery hose is
kinked, radiator hoses will collapse on cool down.
DIAGNOSIS AND TESTING
DIAGNOSIS AND TESTING - RADIATOR
CAP-TO-FILLER NECK SEAL
The pressure cap upper gasket (seal) pressure
relief can be tested by removing overflow hose from
the radiator filler neck tube. Attach the hose of the
pressure tester tool 7700 (or equivalent) to the tube.
It will be necessary to disconnect hose from its
adapter for the filler neck. Pump air into radiator.
The pressure cap upper gasket should relieve at 69
to 124kPa (10 to 18 psi) and hold pressure at a min-
imum of 55 kPa (8 psi).
WARNING: THE WARNING WORDS, ºDO NOT OPEN
HOTº, ON RADIATOR PRESSURE CAP, ARE A
SAFETY PRECAUTION. WHEN HOT, PRESSURE
BUILDS UP IN COOLING SYSTEM. TO PREVENT
SCALDING OR INJURY, RADIATOR CAP SHOULD
NOT BE REMOVED WHILE SYSTEM IS HOT AND/OR
UNDER PRESSURE.
Do not remove the radiator cap at any timeexcept
for the following purposes:
²Check and adjust antifreeze freeze point.
²Refill the system with new antifreeze.
²Conducting service procedures.
²Checking for vacuum leaks.
WARNING: IF VEHICLE HAS BEEN RUN RECENTLY,
WAIT AT LEAST 15 MINUTES BEFORE REMOVING
RADIATOR CAP. WITH A RAG, SQUEEZE RADIATOR
UPPER HOSE TO CHECK IF SYSTEM IS UNDER
PRESSURE. PLACE A RAG OVER CAP AND WITH-
OUT PUSHING CAP DOWN, ROTATE IT COUNTER-
CLOCKWISE TO FIRST STOP. ALLOW FLUID TO
ESCAPE THROUGH THE COOLANT RESERVE/
OVERFLOW HOSE INTO RESERVE/OVERFLOW
TANK. SQUEEZE RADIATOR UPPER HOSE TO
DETERMINE WHEN PRESSURE HAS BEEN
RELEASED. WHEN COOLANT AND STEAM STOP
BEING PUSHED INTO TANK AND SYSTEM PRES-
SURE DROPS, REMOVE RADIATOR CAP COM-
PLETELY.
DIAGNOSIS AND TESTING - RADIATOR CAP
Remove the cap from the radiator. Be sure that the
sealing surfaces are clean. Moisten the rubber gasket
with water and install the cap on the pressure tester
7700 or an equivalent (Fig. 41).
Operate the tester pump to bring the pressure to
104 kPa (15 psi) on the gauge. If the pressure cap
fails to hold pressure of at least 97 kPa (14 psi)
replace the cap. Refer to the followingCAUTION.
Fig. 40 Radiator Pressure Cap - Typical
1 - FILLER NECK SEAL
2 - VACUUM VENT VALVE
3 - PRESSURE RATING
4 - PRESSURE VALVE
7 - 58 ENGINEDR
RADIATOR PRESSURE CAP (Continued)
Page 374 of 2627
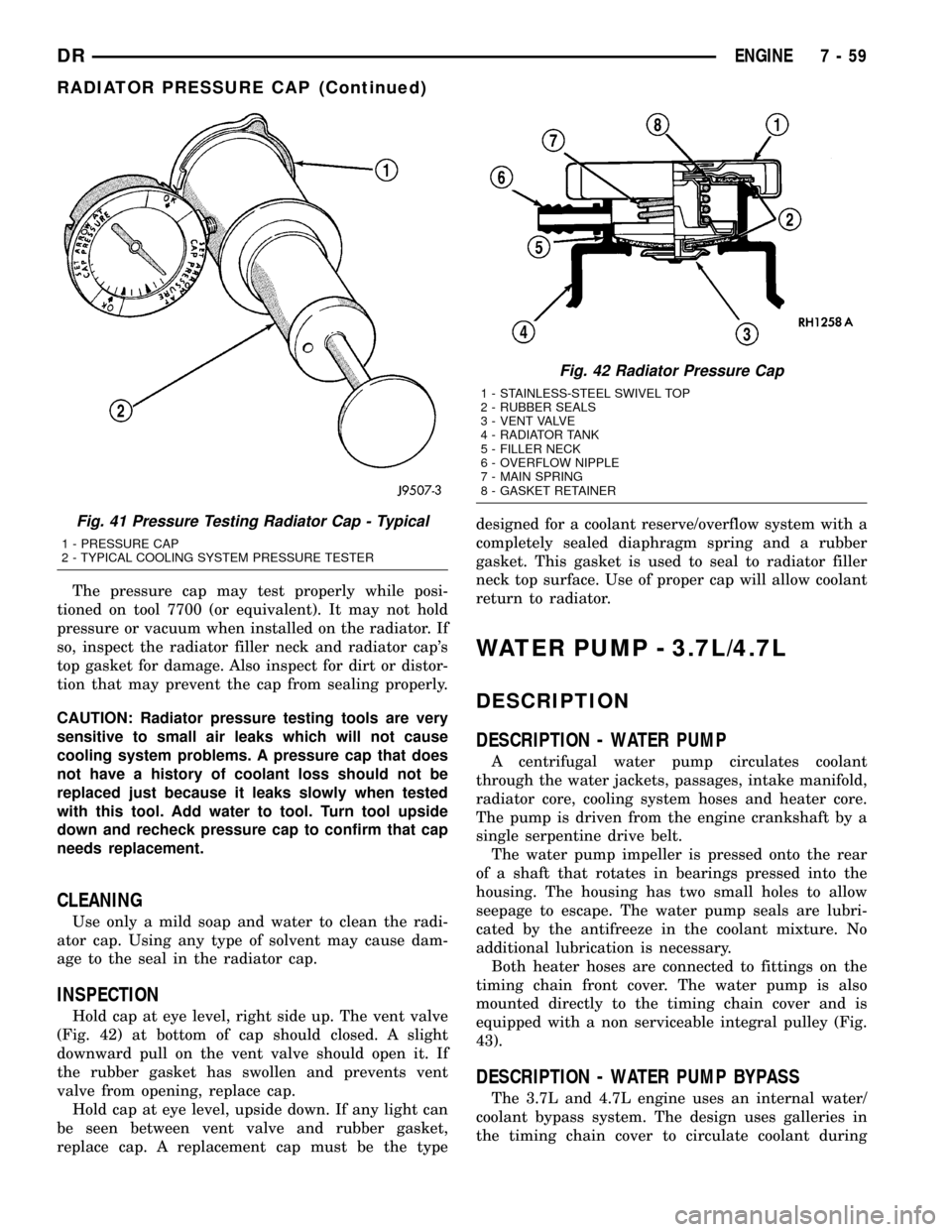
The pressure cap may test properly while posi-
tioned on tool 7700 (or equivalent). It may not hold
pressure or vacuum when installed on the radiator. If
so, inspect the radiator filler neck and radiator cap's
top gasket for damage. Also inspect for dirt or distor-
tion that may prevent the cap from sealing properly.
CAUTION: Radiator pressure testing tools are very
sensitive to small air leaks which will not cause
cooling system problems. A pressure cap that does
not have a history of coolant loss should not be
replaced just because it leaks slowly when tested
with this tool. Add water to tool. Turn tool upside
down and recheck pressure cap to confirm that cap
needs replacement.
CLEANING
Use only a mild soap and water to clean the radi-
ator cap. Using any type of solvent may cause dam-
age to the seal in the radiator cap.
INSPECTION
Hold cap at eye level, right side up. The vent valve
(Fig. 42) at bottom of cap should closed. A slight
downward pull on the vent valve should open it. If
the rubber gasket has swollen and prevents vent
valve from opening, replace cap.
Hold cap at eye level, upside down. If any light can
be seen between vent valve and rubber gasket,
replace cap. A replacement cap must be the typedesigned for a coolant reserve/overflow system with a
completely sealed diaphragm spring and a rubber
gasket. This gasket is used to seal to radiator filler
neck top surface. Use of proper cap will allow coolant
return to radiator.
WATER PUMP - 3.7L/4.7L
DESCRIPTION
DESCRIPTION - WATER PUMP
A centrifugal water pump circulates coolant
through the water jackets, passages, intake manifold,
radiator core, cooling system hoses and heater core.
The pump is driven from the engine crankshaft by a
single serpentine drive belt.
The water pump impeller is pressed onto the rear
of a shaft that rotates in bearings pressed into the
housing. The housing has two small holes to allow
seepage to escape. The water pump seals are lubri-
cated by the antifreeze in the coolant mixture. No
additional lubrication is necessary.
Both heater hoses are connected to fittings on the
timing chain front cover. The water pump is also
mounted directly to the timing chain cover and is
equipped with a non serviceable integral pulley (Fig.
43).
DESCRIPTION - WATER PUMP BYPASS
The 3.7L and 4.7L engine uses an internal water/
coolant bypass system. The design uses galleries in
the timing chain cover to circulate coolant during
Fig. 41 Pressure Testing Radiator Cap - Typical
1 - PRESSURE CAP
2 - TYPICAL COOLING SYSTEM PRESSURE TESTER
Fig. 42 Radiator Pressure Cap
1 - STAINLESS-STEEL SWIVEL TOP
2 - RUBBER SEALS
3 - VENT VALVE
4 - RADIATOR TANK
5 - FILLER NECK
6 - OVERFLOW NIPPLE
7 - MAIN SPRING
8 - GASKET RETAINER
DRENGINE 7 - 59
RADIATOR PRESSURE CAP (Continued)
Page 377 of 2627
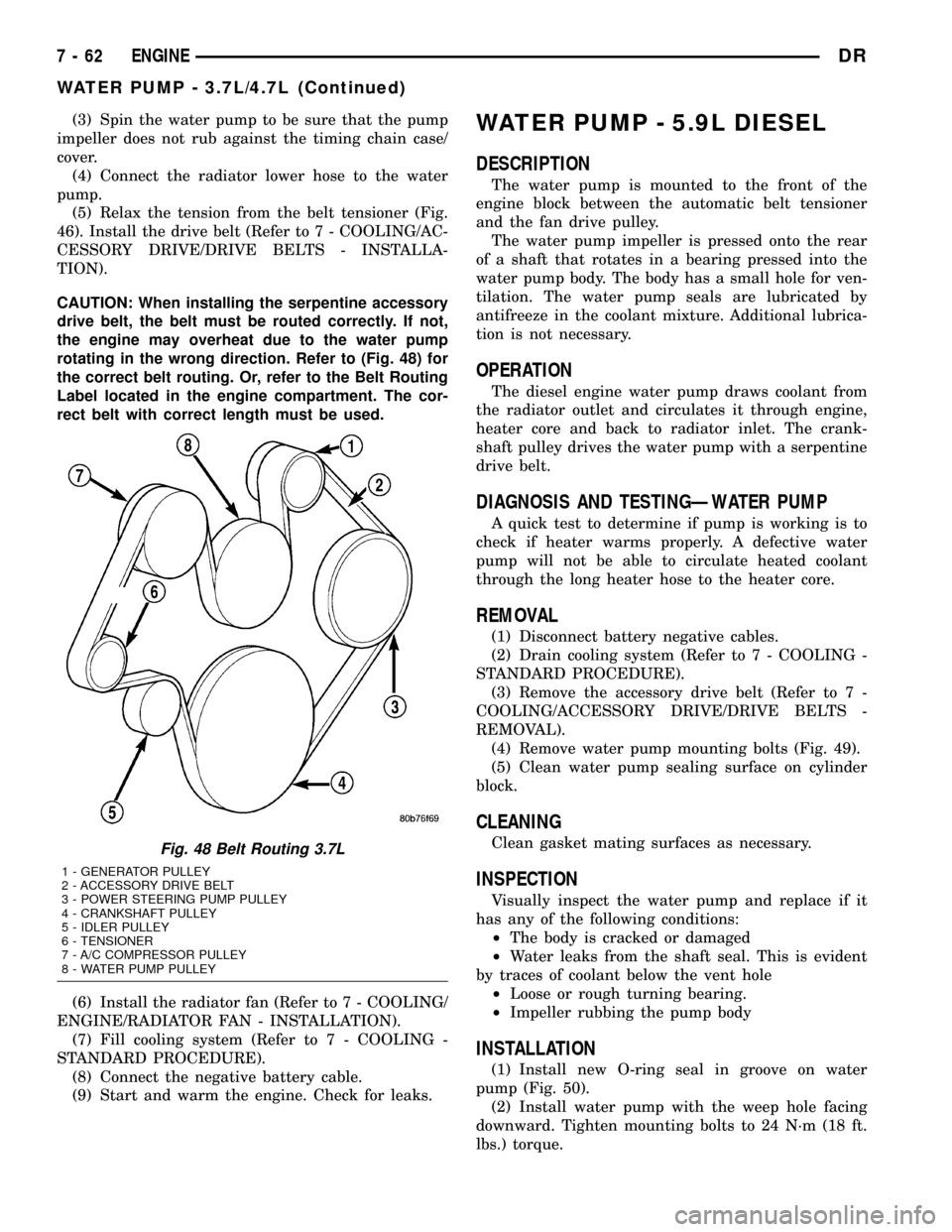
(3) Spin the water pump to be sure that the pump
impeller does not rub against the timing chain case/
cover.
(4) Connect the radiator lower hose to the water
pump.
(5) Relax the tension from the belt tensioner (Fig.
46). Install the drive belt (Refer to 7 - COOLING/AC-
CESSORY DRIVE/DRIVE BELTS - INSTALLA-
TION).
CAUTION: When installing the serpentine accessory
drive belt, the belt must be routed correctly. If not,
the engine may overheat due to the water pump
rotating in the wrong direction. Refer to (Fig. 48) for
the correct belt routing. Or, refer to the Belt Routing
Label located in the engine compartment. The cor-
rect belt with correct length must be used.
(6) Install the radiator fan (Refer to 7 - COOLING/
ENGINE/RADIATOR FAN - INSTALLATION).
(7) Fill cooling system (Refer to 7 - COOLING -
STANDARD PROCEDURE).
(8) Connect the negative battery cable.
(9) Start and warm the engine. Check for leaks.WATER PUMP - 5.9L DIESEL
DESCRIPTION
The water pump is mounted to the front of the
engine block between the automatic belt tensioner
and the fan drive pulley.
The water pump impeller is pressed onto the rear
of a shaft that rotates in a bearing pressed into the
water pump body. The body has a small hole for ven-
tilation. The water pump seals are lubricated by
antifreeze in the coolant mixture. Additional lubrica-
tion is not necessary.
OPERATION
The diesel engine water pump draws coolant from
the radiator outlet and circulates it through engine,
heater core and back to radiator inlet. The crank-
shaft pulley drives the water pump with a serpentine
drive belt.
DIAGNOSIS AND TESTINGÐWATER PUMP
A quick test to determine if pump is working is to
check if heater warms properly. A defective water
pump will not be able to circulate heated coolant
through the long heater hose to the heater core.
REMOVAL
(1) Disconnect battery negative cables.
(2) Drain cooling system (Refer to 7 - COOLING -
STANDARD PROCEDURE).
(3) Remove the accessory drive belt (Refer to 7 -
COOLING/ACCESSORY DRIVE/DRIVE BELTS -
REMOVAL).
(4) Remove water pump mounting bolts (Fig. 49).
(5) Clean water pump sealing surface on cylinder
block.
CLEANING
Clean gasket mating surfaces as necessary.
INSPECTION
Visually inspect the water pump and replace if it
has any of the following conditions:
²The body is cracked or damaged
²Water leaks from the shaft seal. This is evident
by traces of coolant below the vent hole
²Loose or rough turning bearing.
²Impeller rubbing the pump body
INSTALLATION
(1) Install new O-ring seal in groove on water
pump (Fig. 50).
(2) Install water pump with the weep hole facing
downward. Tighten mounting bolts to 24 N´m (18 ft.
lbs.) torque.
Fig. 48 Belt Routing 3.7L
1 - GENERATOR PULLEY
2 - ACCESSORY DRIVE BELT
3 - POWER STEERING PUMP PULLEY
4 - CRANKSHAFT PULLEY
5 - IDLER PULLEY
6 - TENSIONER
7 - A/C COMPRESSOR PULLEY
8 - WATER PUMP PULLEY
7 - 62 ENGINEDR
WATER PUMP - 3.7L/4.7L (Continued)
Page 378 of 2627
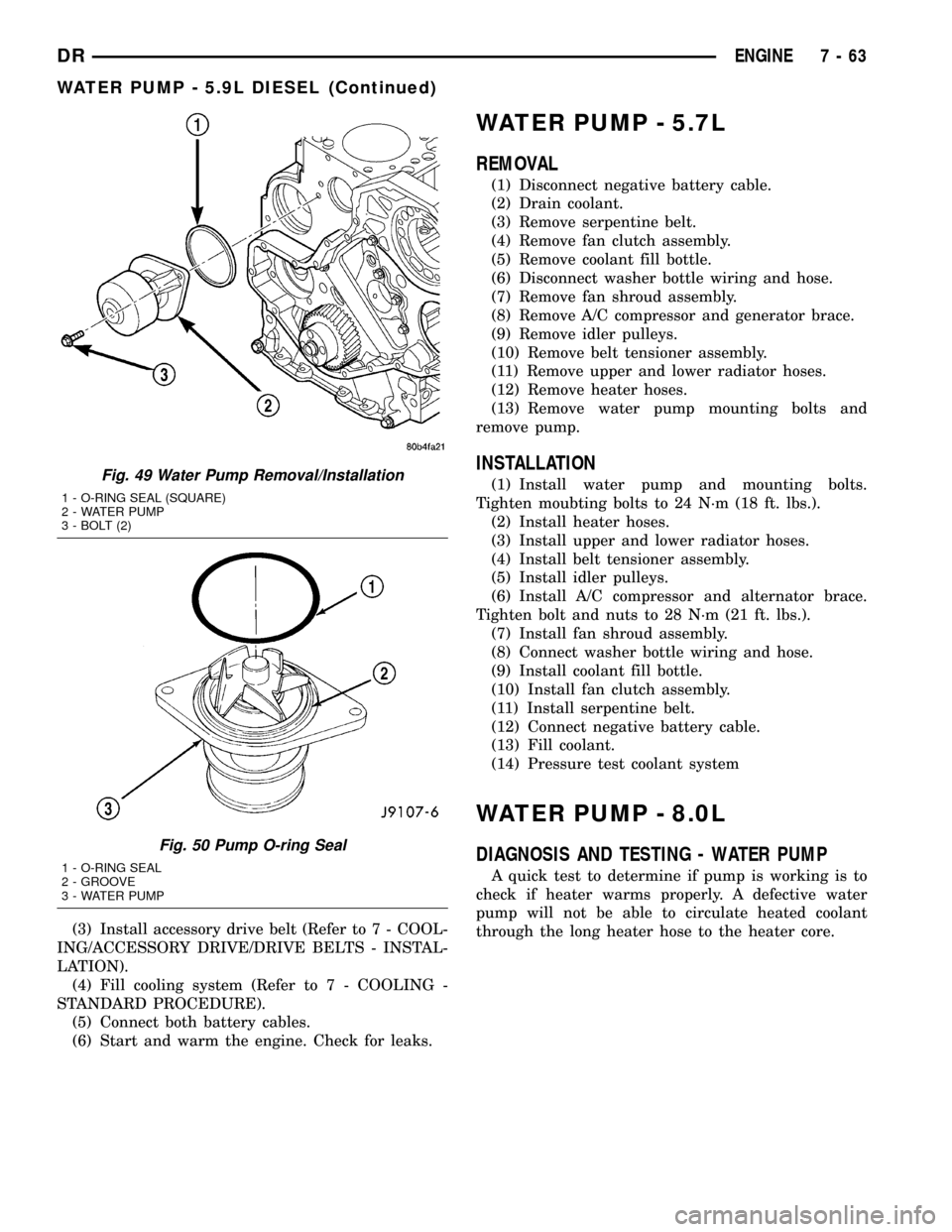
(3) Install accessory drive belt (Refer to 7 - COOL-
ING/ACCESSORY DRIVE/DRIVE BELTS - INSTAL-
LATION).
(4) Fill cooling system (Refer to 7 - COOLING -
STANDARD PROCEDURE).
(5) Connect both battery cables.
(6) Start and warm the engine. Check for leaks.
WATER PUMP - 5.7L
REMOVAL
(1) Disconnect negative battery cable.
(2) Drain coolant.
(3) Remove serpentine belt.
(4) Remove fan clutch assembly.
(5) Remove coolant fill bottle.
(6) Disconnect washer bottle wiring and hose.
(7) Remove fan shroud assembly.
(8) Remove A/C compressor and generator brace.
(9) Remove idler pulleys.
(10) Remove belt tensioner assembly.
(11) Remove upper and lower radiator hoses.
(12) Remove heater hoses.
(13) Remove water pump mounting bolts and
remove pump.
INSTALLATION
(1) Install water pump and mounting bolts.
Tighten moubting bolts to 24 N´m (18 ft. lbs.).
(2) Install heater hoses.
(3) Install upper and lower radiator hoses.
(4) Install belt tensioner assembly.
(5) Install idler pulleys.
(6) Install A/C compressor and alternator brace.
Tighten bolt and nuts to 28 N´m (21 ft. lbs.).
(7) Install fan shroud assembly.
(8) Connect washer bottle wiring and hose.
(9) Install coolant fill bottle.
(10) Install fan clutch assembly.
(11) Install serpentine belt.
(12) Connect negative battery cable.
(13) Fill coolant.
(14) Pressure test coolant system
WATER PUMP - 8.0L
DIAGNOSIS AND TESTING - WATER PUMP
A quick test to determine if pump is working is to
check if heater warms properly. A defective water
pump will not be able to circulate heated coolant
through the long heater hose to the heater core.
Fig. 49 Water Pump Removal/Installation
1 - O-RING SEAL (SQUARE)
2 - WATER PUMP
3 - BOLT (2)
Fig. 50 Pump O-ring Seal
1 - O-RING SEAL
2 - GROOVE
3 - WATER PUMP
DRENGINE 7 - 63
WATER PUMP - 5.9L DIESEL (Continued)
Page 379 of 2627
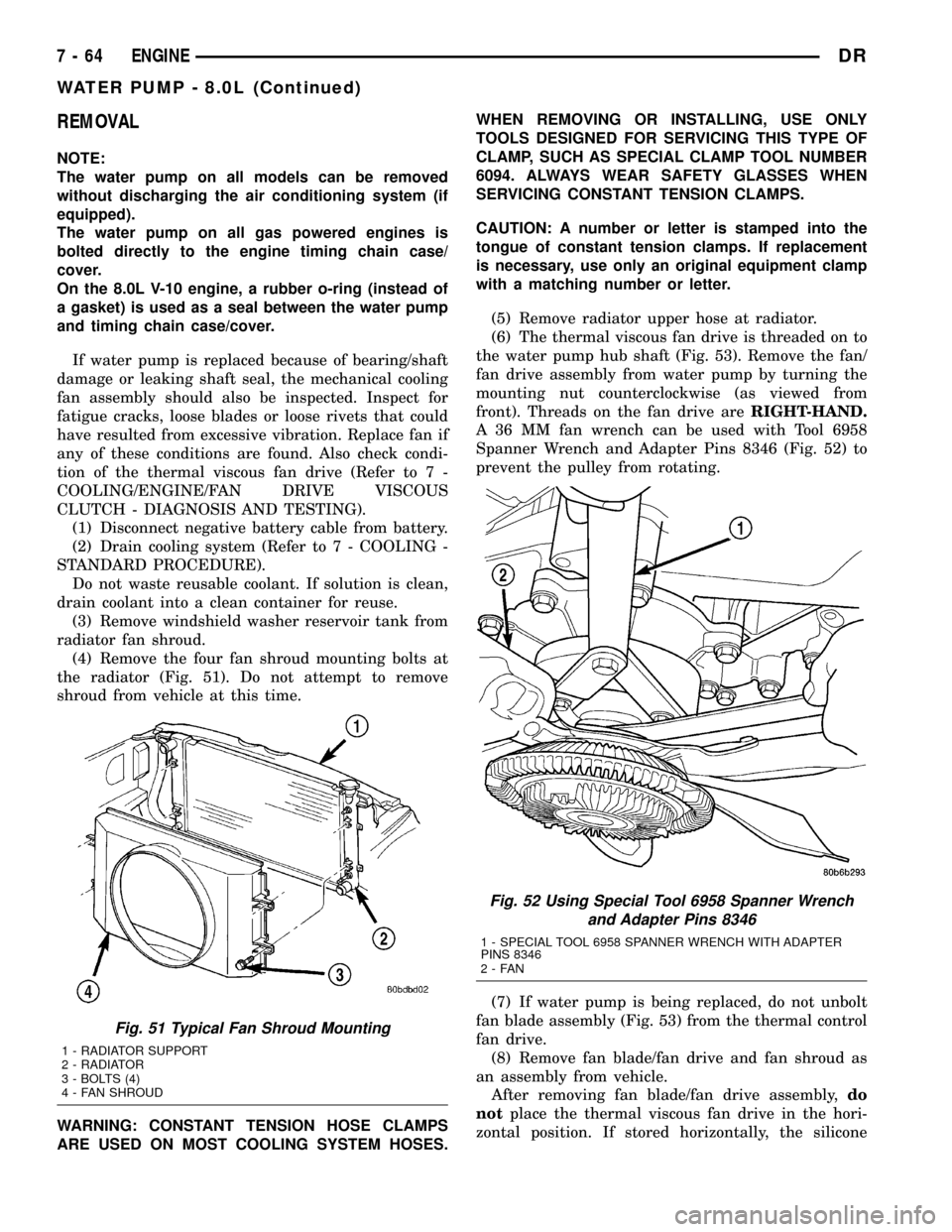
REMOVAL
NOTE:
The water pump on all models can be removed
without discharging the air conditioning system (if
equipped).
The water pump on all gas powered engines is
bolted directly to the engine timing chain case/
cover.
On the 8.0L V-10 engine, a rubber o-ring (instead of
a gasket) is used as a seal between the water pump
and timing chain case/cover.
If water pump is replaced because of bearing/shaft
damage or leaking shaft seal, the mechanical cooling
fan assembly should also be inspected. Inspect for
fatigue cracks, loose blades or loose rivets that could
have resulted from excessive vibration. Replace fan if
any of these conditions are found. Also check condi-
tion of the thermal viscous fan drive (Refer to 7 -
COOLING/ENGINE/FAN DRIVE VISCOUS
CLUTCH - DIAGNOSIS AND TESTING).
(1) Disconnect negative battery cable from battery.
(2) Drain cooling system (Refer to 7 - COOLING -
STANDARD PROCEDURE).
Do not waste reusable coolant. If solution is clean,
drain coolant into a clean container for reuse.
(3) Remove windshield washer reservoir tank from
radiator fan shroud.
(4) Remove the four fan shroud mounting bolts at
the radiator (Fig. 51). Do not attempt to remove
shroud from vehicle at this time.
WARNING: CONSTANT TENSION HOSE CLAMPS
ARE USED ON MOST COOLING SYSTEM HOSES.WHEN REMOVING OR INSTALLING, USE ONLY
TOOLS DESIGNED FOR SERVICING THIS TYPE OF
CLAMP, SUCH AS SPECIAL CLAMP TOOL NUMBER
6094. ALWAYS WEAR SAFETY GLASSES WHEN
SERVICING CONSTANT TENSION CLAMPS.
CAUTION: A number or letter is stamped into the
tongue of constant tension clamps. If replacement
is necessary, use only an original equipment clamp
with a matching number or letter.
(5) Remove radiator upper hose at radiator.
(6) The thermal viscous fan drive is threaded on to
the water pump hub shaft (Fig. 53). Remove the fan/
fan drive assembly from water pump by turning the
mounting nut counterclockwise (as viewed from
front). Threads on the fan drive areRIGHT-HAND.
A 36 MM fan wrench can be used with Tool 6958
Spanner Wrench and Adapter Pins 8346 (Fig. 52) to
prevent the pulley from rotating.
(7) If water pump is being replaced, do not unbolt
fan blade assembly (Fig. 53) from the thermal control
fan drive.
(8) Remove fan blade/fan drive and fan shroud as
an assembly from vehicle.
After removing fan blade/fan drive assembly,do
notplace the thermal viscous fan drive in the hori-
zontal position. If stored horizontally, the silicone
Fig. 51 Typical Fan Shroud Mounting
1 - RADIATOR SUPPORT
2 - RADIATOR
3 - BOLTS (4)
4 - FAN SHROUD
Fig. 52 Using Special Tool 6958 Spanner Wrench
and Adapter Pins 8346
1 - SPECIAL TOOL 6958 SPANNER WRENCH WITH ADAPTER
PINS 8346
2-FAN
7 - 64 ENGINEDR
WATER PUMP - 8.0L (Continued)
Page 381 of 2627
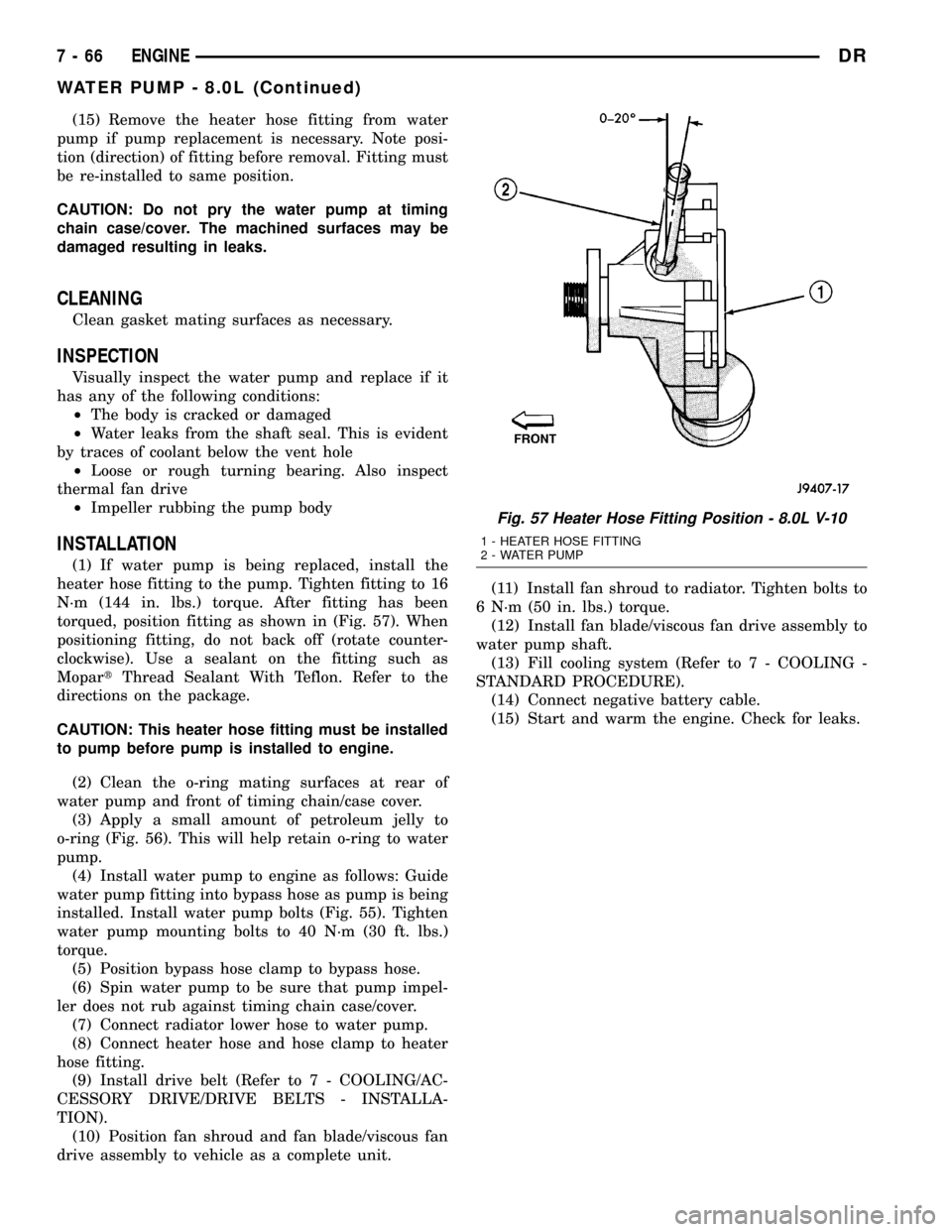
(15) Remove the heater hose fitting from water
pump if pump replacement is necessary. Note posi-
tion (direction) of fitting before removal. Fitting must
be re-installed to same position.
CAUTION: Do not pry the water pump at timing
chain case/cover. The machined surfaces may be
damaged resulting in leaks.
CLEANING
Clean gasket mating surfaces as necessary.
INSPECTION
Visually inspect the water pump and replace if it
has any of the following conditions:
²The body is cracked or damaged
²Water leaks from the shaft seal. This is evident
by traces of coolant below the vent hole
²Loose or rough turning bearing. Also inspect
thermal fan drive
²Impeller rubbing the pump body
INSTALLATION
(1) If water pump is being replaced, install the
heater hose fitting to the pump. Tighten fitting to 16
N´m (144 in. lbs.) torque. After fitting has been
torqued, position fitting as shown in (Fig. 57). When
positioning fitting, do not back off (rotate counter-
clockwise). Use a sealant on the fitting such as
MopartThread Sealant With Teflon. Refer to the
directions on the package.
CAUTION: This heater hose fitting must be installed
to pump before pump is installed to engine.
(2) Clean the o-ring mating surfaces at rear of
water pump and front of timing chain/case cover.
(3) Apply a small amount of petroleum jelly to
o-ring (Fig. 56). This will help retain o-ring to water
pump.
(4) Install water pump to engine as follows: Guide
water pump fitting into bypass hose as pump is being
installed. Install water pump bolts (Fig. 55). Tighten
water pump mounting bolts to 40 N´m (30 ft. lbs.)
torque.
(5) Position bypass hose clamp to bypass hose.
(6) Spin water pump to be sure that pump impel-
ler does not rub against timing chain case/cover.
(7) Connect radiator lower hose to water pump.
(8) Connect heater hose and hose clamp to heater
hose fitting.
(9) Install drive belt (Refer to 7 - COOLING/AC-
CESSORY DRIVE/DRIVE BELTS - INSTALLA-
TION).
(10) Position fan shroud and fan blade/viscous fan
drive assembly to vehicle as a complete unit.(11) Install fan shroud to radiator. Tighten bolts to
6 N´m (50 in. lbs.) torque.
(12) Install fan blade/viscous fan drive assembly to
water pump shaft.
(13) Fill cooling system (Refer to 7 - COOLING -
STANDARD PROCEDURE).
(14) Connect negative battery cable.
(15) Start and warm the engine. Check for leaks.
Fig. 57 Heater Hose Fitting Position - 8.0L V-10
1 - HEATER HOSE FITTING
2 - WATER PUMP
7 - 66 ENGINEDR
WATER PUMP - 8.0L (Continued)