OBD port DODGE RAM 1500 1998 2.G Workshop Manual
[x] Cancel search | Manufacturer: DODGE, Model Year: 1998, Model line: RAM 1500, Model: DODGE RAM 1500 1998 2.GPages: 2627
Page 357 of 2627
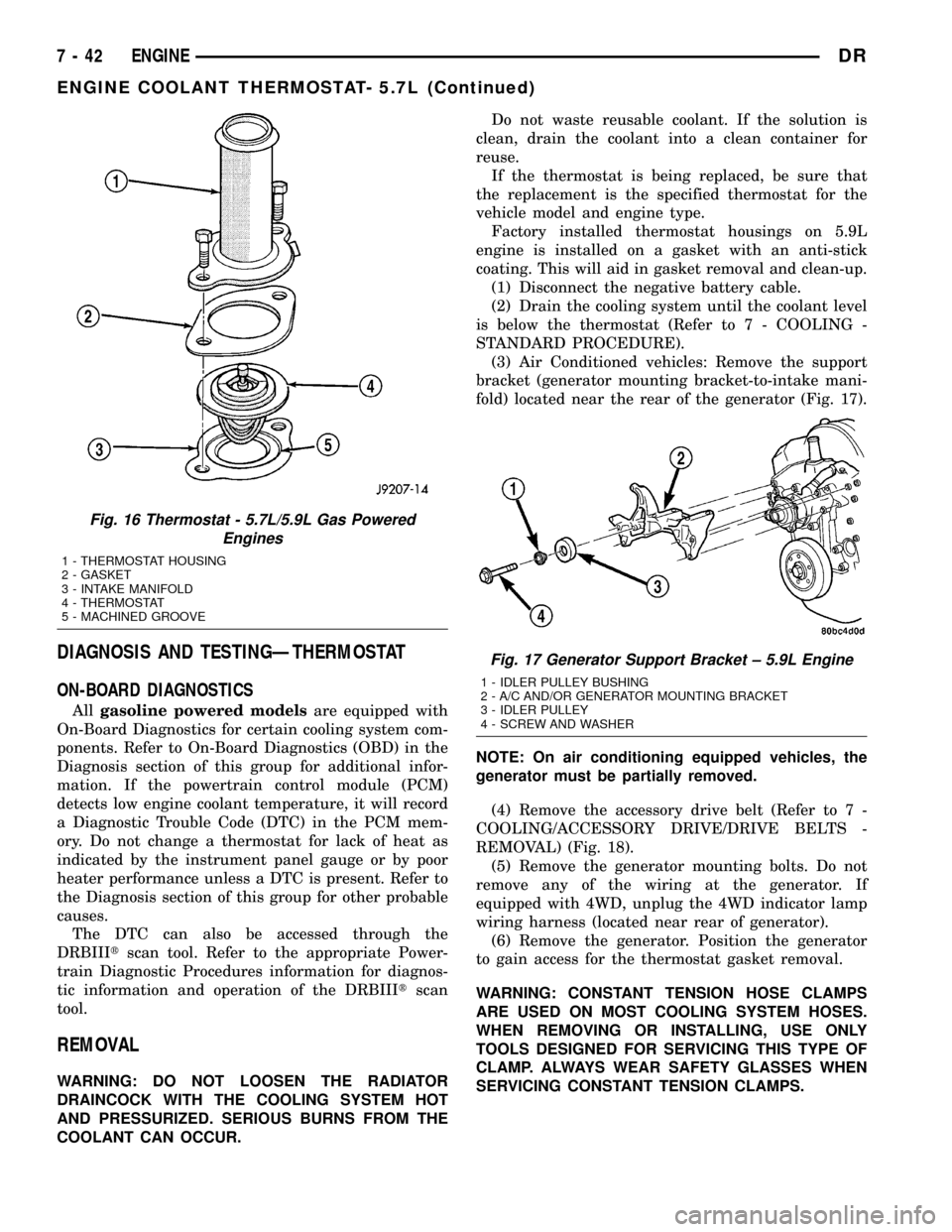
DIAGNOSIS AND TESTINGÐTHERMOSTAT
ON-BOARD DIAGNOSTICS
Allgasoline powered modelsare equipped with
On-Board Diagnostics for certain cooling system com-
ponents. Refer to On-Board Diagnostics (OBD) in the
Diagnosis section of this group for additional infor-
mation. If the powertrain control module (PCM)
detects low engine coolant temperature, it will record
a Diagnostic Trouble Code (DTC) in the PCM mem-
ory. Do not change a thermostat for lack of heat as
indicated by the instrument panel gauge or by poor
heater performance unless a DTC is present. Refer to
the Diagnosis section of this group for other probable
causes.
The DTC can also be accessed through the
DRBIIItscan tool. Refer to the appropriate Power-
train Diagnostic Procedures information for diagnos-
tic information and operation of the DRBIIItscan
tool.
REMOVAL
WARNING: DO NOT LOOSEN THE RADIATOR
DRAINCOCK WITH THE COOLING SYSTEM HOT
AND PRESSURIZED. SERIOUS BURNS FROM THE
COOLANT CAN OCCUR.Do not waste reusable coolant. If the solution is
clean, drain the coolant into a clean container for
reuse.
If the thermostat is being replaced, be sure that
the replacement is the specified thermostat for the
vehicle model and engine type.
Factory installed thermostat housings on 5.9L
engine is installed on a gasket with an anti-stick
coating. This will aid in gasket removal and clean-up.
(1) Disconnect the negative battery cable.
(2) Drain the cooling system until the coolant level
is below the thermostat (Refer to 7 - COOLING -
STANDARD PROCEDURE).
(3) Air Conditioned vehicles: Remove the support
bracket (generator mounting bracket-to-intake mani-
fold) located near the rear of the generator (Fig. 17).
NOTE: On air conditioning equipped vehicles, the
generator must be partially removed.
(4) Remove the accessory drive belt (Refer to 7 -
COOLING/ACCESSORY DRIVE/DRIVE BELTS -
REMOVAL) (Fig. 18).
(5) Remove the generator mounting bolts. Do not
remove any of the wiring at the generator. If
equipped with 4WD, unplug the 4WD indicator lamp
wiring harness (located near rear of generator).
(6) Remove the generator. Position the generator
to gain access for the thermostat gasket removal.
WARNING: CONSTANT TENSION HOSE CLAMPS
ARE USED ON MOST COOLING SYSTEM HOSES.
WHEN REMOVING OR INSTALLING, USE ONLY
TOOLS DESIGNED FOR SERVICING THIS TYPE OF
CLAMP. ALWAYS WEAR SAFETY GLASSES WHEN
SERVICING CONSTANT TENSION CLAMPS.
Fig. 16 Thermostat - 5.7L/5.9L Gas Powered
Engines
1 - THERMOSTAT HOUSING
2 - GASKET
3 - INTAKE MANIFOLD
4 - THERMOSTAT
5 - MACHINED GROOVE
Fig. 17 Generator Support Bracket ± 5.9L Engine
1 - IDLER PULLEY BUSHING
2 - A/C AND/OR GENERATOR MOUNTING BRACKET
3 - IDLER PULLEY
4 - SCREW AND WASHER
7 - 42 ENGINEDR
ENGINE COOLANT THERMOSTAT- 5.7L (Continued)
Page 359 of 2627
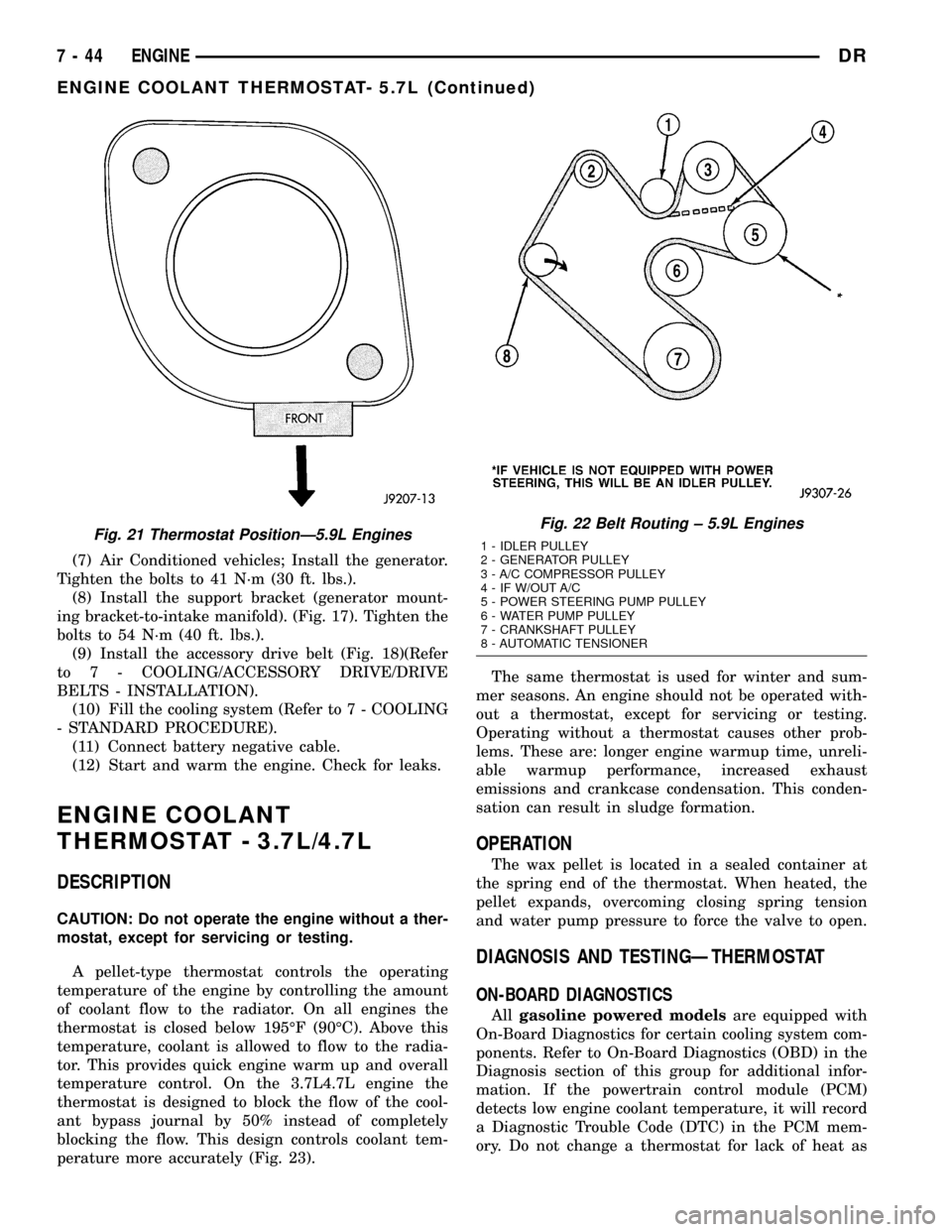
(7) Air Conditioned vehicles; Install the generator.
Tighten the bolts to 41 N´m (30 ft. lbs.).
(8) Install the support bracket (generator mount-
ing bracket-to-intake manifold). (Fig. 17). Tighten the
bolts to 54 N´m (40 ft. lbs.).
(9) Install the accessory drive belt (Fig. 18)(Refer
to 7 - COOLING/ACCESSORY DRIVE/DRIVE
BELTS - INSTALLATION).
(10) Fill the cooling system (Refer to 7 - COOLING
- STANDARD PROCEDURE).
(11) Connect battery negative cable.
(12) Start and warm the engine. Check for leaks.
ENGINE COOLANT
THERMOSTAT - 3.7L/4.7L
DESCRIPTION
CAUTION: Do not operate the engine without a ther-
mostat, except for servicing or testing.
A pellet-type thermostat controls the operating
temperature of the engine by controlling the amount
of coolant flow to the radiator. On all engines the
thermostat is closed below 195ÉF (90ÉC). Above this
temperature, coolant is allowed to flow to the radia-
tor. This provides quick engine warm up and overall
temperature control. On the 3.7L4.7L engine the
thermostat is designed to block the flow of the cool-
ant bypass journal by 50% instead of completely
blocking the flow. This design controls coolant tem-
perature more accurately (Fig. 23).The same thermostat is used for winter and sum-
mer seasons. An engine should not be operated with-
out a thermostat, except for servicing or testing.
Operating without a thermostat causes other prob-
lems. These are: longer engine warmup time, unreli-
able warmup performance, increased exhaust
emissions and crankcase condensation. This conden-
sation can result in sludge formation.
OPERATION
The wax pellet is located in a sealed container at
the spring end of the thermostat. When heated, the
pellet expands, overcoming closing spring tension
and water pump pressure to force the valve to open.
DIAGNOSIS AND TESTINGÐTHERMOSTAT
ON-BOARD DIAGNOSTICS
Allgasoline powered modelsare equipped with
On-Board Diagnostics for certain cooling system com-
ponents. Refer to On-Board Diagnostics (OBD) in the
Diagnosis section of this group for additional infor-
mation. If the powertrain control module (PCM)
detects low engine coolant temperature, it will record
a Diagnostic Trouble Code (DTC) in the PCM mem-
ory. Do not change a thermostat for lack of heat as
Fig. 21 Thermostat PositionÐ5.9L EnginesFig. 22 Belt Routing ± 5.9L Engines
1 - IDLER PULLEY
2 - GENERATOR PULLEY
3 - A/C COMPRESSOR PULLEY
4 - IF W/OUT A/C
5 - POWER STEERING PUMP PULLEY
6 - WATER PUMP PULLEY
7 - CRANKSHAFT PULLEY
8 - AUTOMATIC TENSIONER
7 - 44 ENGINEDR
ENGINE COOLANT THERMOSTAT- 5.7L (Continued)
Page 433 of 2627
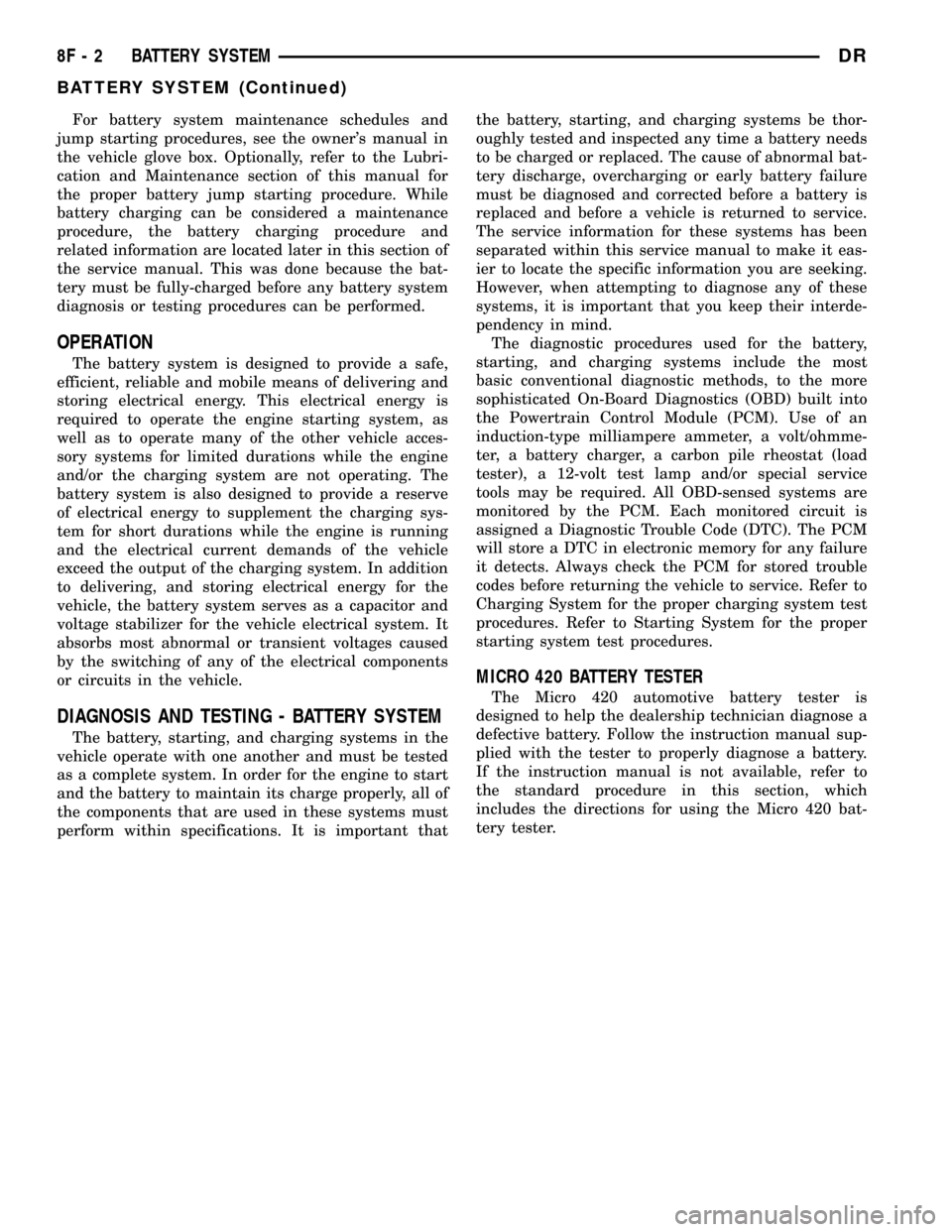
For battery system maintenance schedules and
jump starting procedures, see the owner's manual in
the vehicle glove box. Optionally, refer to the Lubri-
cation and Maintenance section of this manual for
the proper battery jump starting procedure. While
battery charging can be considered a maintenance
procedure, the battery charging procedure and
related information are located later in this section of
the service manual. This was done because the bat-
tery must be fully-charged before any battery system
diagnosis or testing procedures can be performed.
OPERATION
The battery system is designed to provide a safe,
efficient, reliable and mobile means of delivering and
storing electrical energy. This electrical energy is
required to operate the engine starting system, as
well as to operate many of the other vehicle acces-
sory systems for limited durations while the engine
and/or the charging system are not operating. The
battery system is also designed to provide a reserve
of electrical energy to supplement the charging sys-
tem for short durations while the engine is running
and the electrical current demands of the vehicle
exceed the output of the charging system. In addition
to delivering, and storing electrical energy for the
vehicle, the battery system serves as a capacitor and
voltage stabilizer for the vehicle electrical system. It
absorbs most abnormal or transient voltages caused
by the switching of any of the electrical components
or circuits in the vehicle.
DIAGNOSIS AND TESTING - BATTERY SYSTEM
The battery, starting, and charging systems in the
vehicle operate with one another and must be tested
as a complete system. In order for the engine to start
and the battery to maintain its charge properly, all of
the components that are used in these systems must
perform within specifications. It is important thatthe battery, starting, and charging systems be thor-
oughly tested and inspected any time a battery needs
to be charged or replaced. The cause of abnormal bat-
tery discharge, overcharging or early battery failure
must be diagnosed and corrected before a battery is
replaced and before a vehicle is returned to service.
The service information for these systems has been
separated within this service manual to make it eas-
ier to locate the specific information you are seeking.
However, when attempting to diagnose any of these
systems, it is important that you keep their interde-
pendency in mind.
The diagnostic procedures used for the battery,
starting, and charging systems include the most
basic conventional diagnostic methods, to the more
sophisticated On-Board Diagnostics (OBD) built into
the Powertrain Control Module (PCM). Use of an
induction-type milliampere ammeter, a volt/ohmme-
ter, a battery charger, a carbon pile rheostat (load
tester), a 12-volt test lamp and/or special service
tools may be required. All OBD-sensed systems are
monitored by the PCM. Each monitored circuit is
assigned a Diagnostic Trouble Code (DTC). The PCM
will store a DTC in electronic memory for any failure
it detects. Always check the PCM for stored trouble
codes before returning the vehicle to service. Refer to
Charging System for the proper charging system test
procedures. Refer to Starting System for the proper
starting system test procedures.
MICRO 420 BATTERY TESTER
The Micro 420 automotive battery tester is
designed to help the dealership technician diagnose a
defective battery. Follow the instruction manual sup-
plied with the tester to properly diagnose a battery.
If the instruction manual is not available, refer to
the standard procedure in this section, which
includes the directions for using the Micro 420 bat-
tery tester.
8F - 2 BATTERY SYSTEMDR
BATTERY SYSTEM (Continued)
Page 451 of 2627
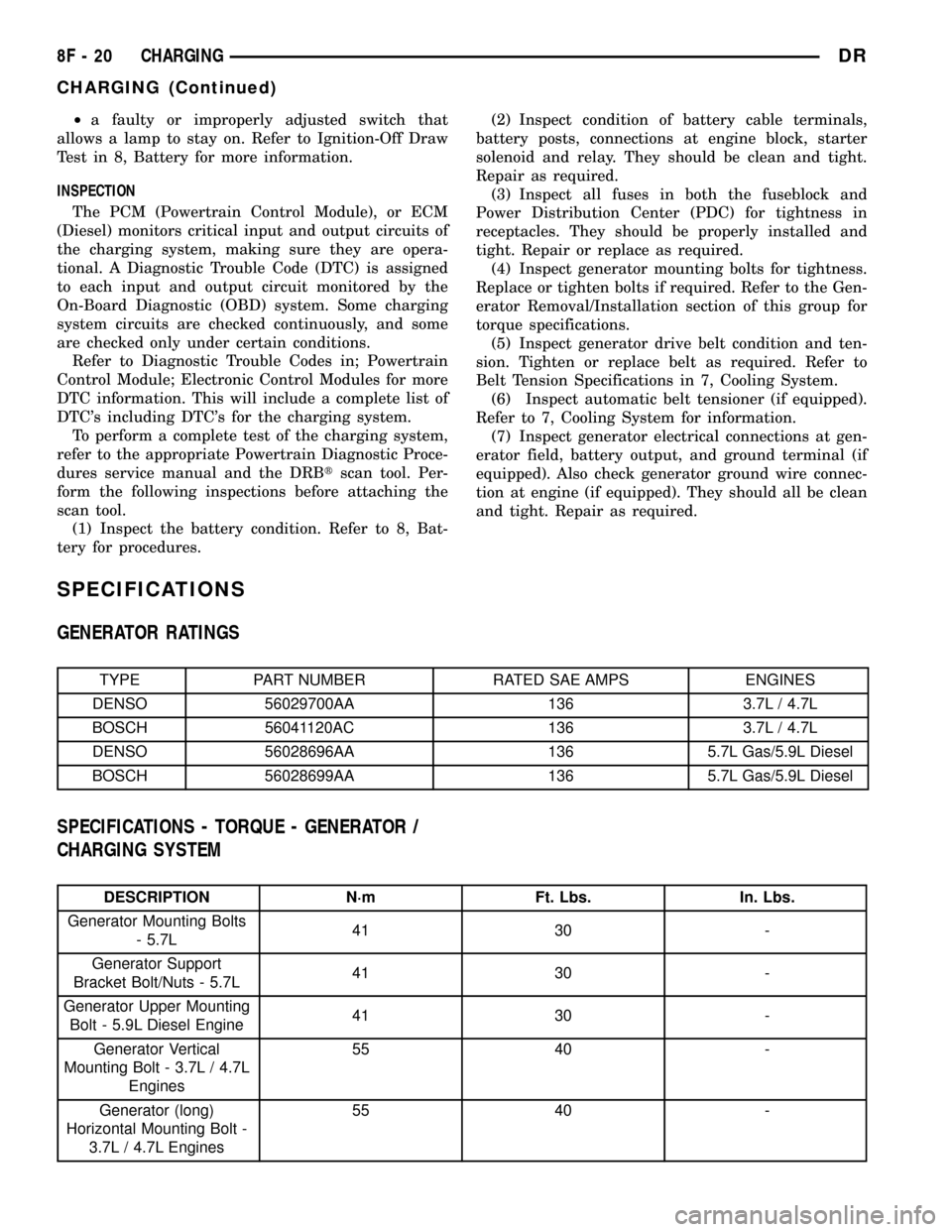
²a faulty or improperly adjusted switch that
allows a lamp to stay on. Refer to Ignition-Off Draw
Test in 8, Battery for more information.
INSPECTION
The PCM (Powertrain Control Module), or ECM
(Diesel) monitors critical input and output circuits of
the charging system, making sure they are opera-
tional. A Diagnostic Trouble Code (DTC) is assigned
to each input and output circuit monitored by the
On-Board Diagnostic (OBD) system. Some charging
system circuits are checked continuously, and some
are checked only under certain conditions.
Refer to Diagnostic Trouble Codes in; Powertrain
Control Module; Electronic Control Modules for more
DTC information. This will include a complete list of
DTC's including DTC's for the charging system.
To perform a complete test of the charging system,
refer to the appropriate Powertrain Diagnostic Proce-
dures service manual and the DRBtscan tool. Per-
form the following inspections before attaching the
scan tool.
(1) Inspect the battery condition. Refer to 8, Bat-
tery for procedures.(2) Inspect condition of battery cable terminals,
battery posts, connections at engine block, starter
solenoid and relay. They should be clean and tight.
Repair as required.
(3) Inspect all fuses in both the fuseblock and
Power Distribution Center (PDC) for tightness in
receptacles. They should be properly installed and
tight. Repair or replace as required.
(4) Inspect generator mounting bolts for tightness.
Replace or tighten bolts if required. Refer to the Gen-
erator Removal/Installation section of this group for
torque specifications.
(5) Inspect generator drive belt condition and ten-
sion. Tighten or replace belt as required. Refer to
Belt Tension Specifications in 7, Cooling System.
(6) Inspect automatic belt tensioner (if equipped).
Refer to 7, Cooling System for information.
(7) Inspect generator electrical connections at gen-
erator field, battery output, and ground terminal (if
equipped). Also check generator ground wire connec-
tion at engine (if equipped). They should all be clean
and tight. Repair as required.
SPECIFICATIONS
GENERATOR RATINGS
TYPE PART NUMBER RATED SAE AMPS ENGINES
DENSO 56029700AA 136 3.7L / 4.7L
BOSCH 56041120AC 136 3.7L / 4.7L
DENSO 56028696AA 136 5.7L Gas/5.9L Diesel
BOSCH 56028699AA 136 5.7L Gas/5.9L Diesel
SPECIFICATIONS - TORQUE - GENERATOR /
CHARGING SYSTEM
DESCRIPTION N´m Ft. Lbs. In. Lbs.
Generator Mounting Bolts
- 5.7L41 30 -
Generator Support
Bracket Bolt/Nuts - 5.7L41 30 -
Generator Upper Mounting
Bolt - 5.9L Diesel Engine41 30 -
Generator Vertical
Mounting Bolt - 3.7L / 4.7L
Engines55 40 -
Generator (long)
Horizontal Mounting Bolt -
3.7L / 4.7L Engines55 40 -
8F - 20 CHARGINGDR
CHARGING (Continued)
Page 457 of 2627
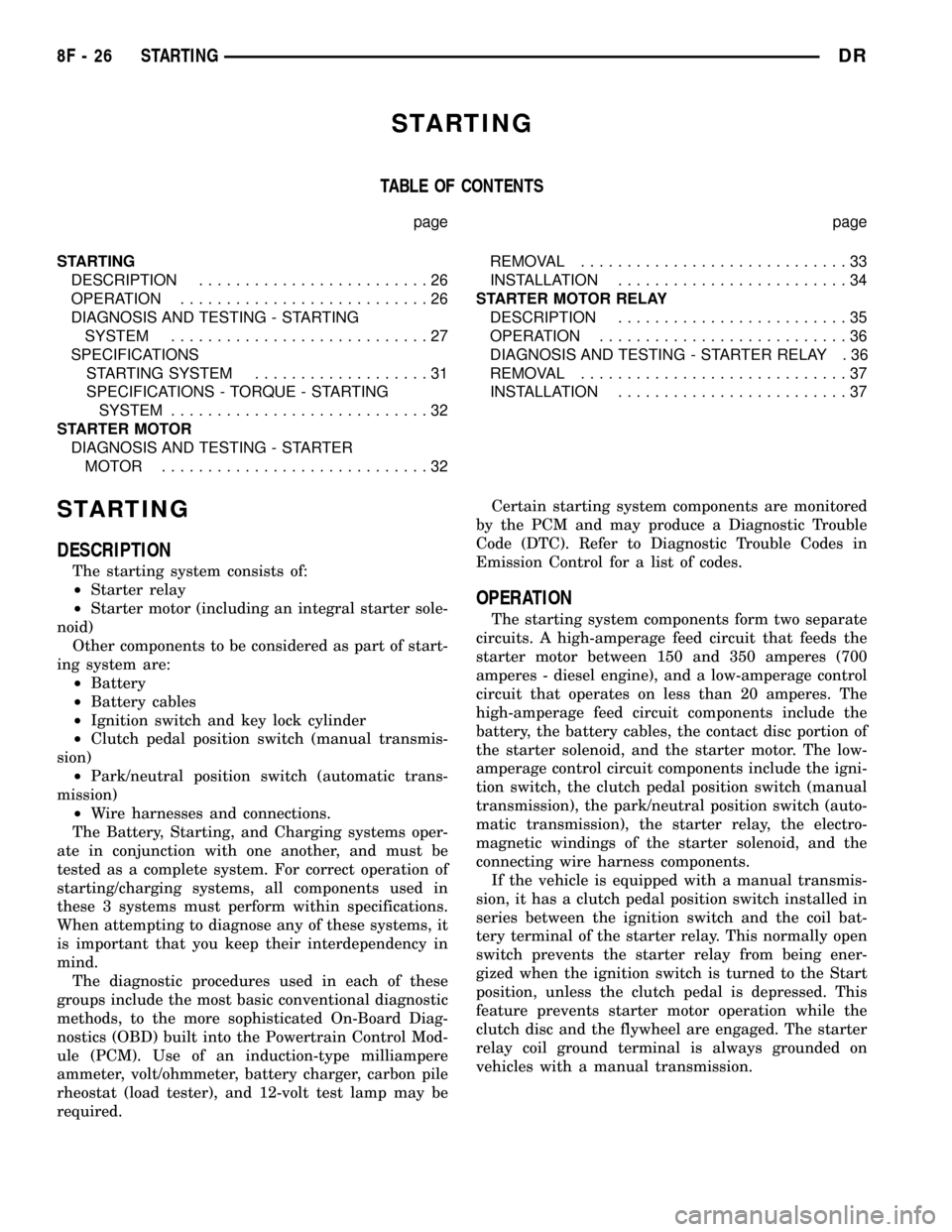
STARTING
TABLE OF CONTENTS
page page
STARTING
DESCRIPTION.........................26
OPERATION...........................26
DIAGNOSIS AND TESTING - STARTING
SYSTEM............................27
SPECIFICATIONS
STARTING SYSTEM...................31
SPECIFICATIONS - TORQUE - STARTING
SYSTEM............................32
STARTER MOTOR
DIAGNOSIS AND TESTING - STARTER
MOTOR .............................32REMOVAL.............................33
INSTALLATION.........................34
STARTER MOTOR RELAY
DESCRIPTION.........................35
OPERATION...........................36
DIAGNOSIS AND TESTING - STARTER RELAY . 36
REMOVAL.............................37
INSTALLATION.........................37
STARTING
DESCRIPTION
The starting system consists of:
²Starter relay
²Starter motor (including an integral starter sole-
noid)
Other components to be considered as part of start-
ing system are:
²Battery
²Battery cables
²Ignition switch and key lock cylinder
²Clutch pedal position switch (manual transmis-
sion)
²Park/neutral position switch (automatic trans-
mission)
²Wire harnesses and connections.
The Battery, Starting, and Charging systems oper-
ate in conjunction with one another, and must be
tested as a complete system. For correct operation of
starting/charging systems, all components used in
these 3 systems must perform within specifications.
When attempting to diagnose any of these systems, it
is important that you keep their interdependency in
mind.
The diagnostic procedures used in each of these
groups include the most basic conventional diagnostic
methods, to the more sophisticated On-Board Diag-
nostics (OBD) built into the Powertrain Control Mod-
ule (PCM). Use of an induction-type milliampere
ammeter, volt/ohmmeter, battery charger, carbon pile
rheostat (load tester), and 12-volt test lamp may be
required.Certain starting system components are monitored
by the PCM and may produce a Diagnostic Trouble
Code (DTC). Refer to Diagnostic Trouble Codes in
Emission Control for a list of codes.
OPERATION
The starting system components form two separate
circuits. A high-amperage feed circuit that feeds the
starter motor between 150 and 350 amperes (700
amperes - diesel engine), and a low-amperage control
circuit that operates on less than 20 amperes. The
high-amperage feed circuit components include the
battery, the battery cables, the contact disc portion of
the starter solenoid, and the starter motor. The low-
amperage control circuit components include the igni-
tion switch, the clutch pedal position switch (manual
transmission), the park/neutral position switch (auto-
matic transmission), the starter relay, the electro-
magnetic windings of the starter solenoid, and the
connecting wire harness components.
If the vehicle is equipped with a manual transmis-
sion, it has a clutch pedal position switch installed in
series between the ignition switch and the coil bat-
tery terminal of the starter relay. This normally open
switch prevents the starter relay from being ener-
gized when the ignition switch is turned to the Start
position, unless the clutch pedal is depressed. This
feature prevents starter motor operation while the
clutch disc and the flywheel are engaged. The starter
relay coil ground terminal is always grounded on
vehicles with a manual transmission.
8F - 26 STARTINGDR
Page 540 of 2627
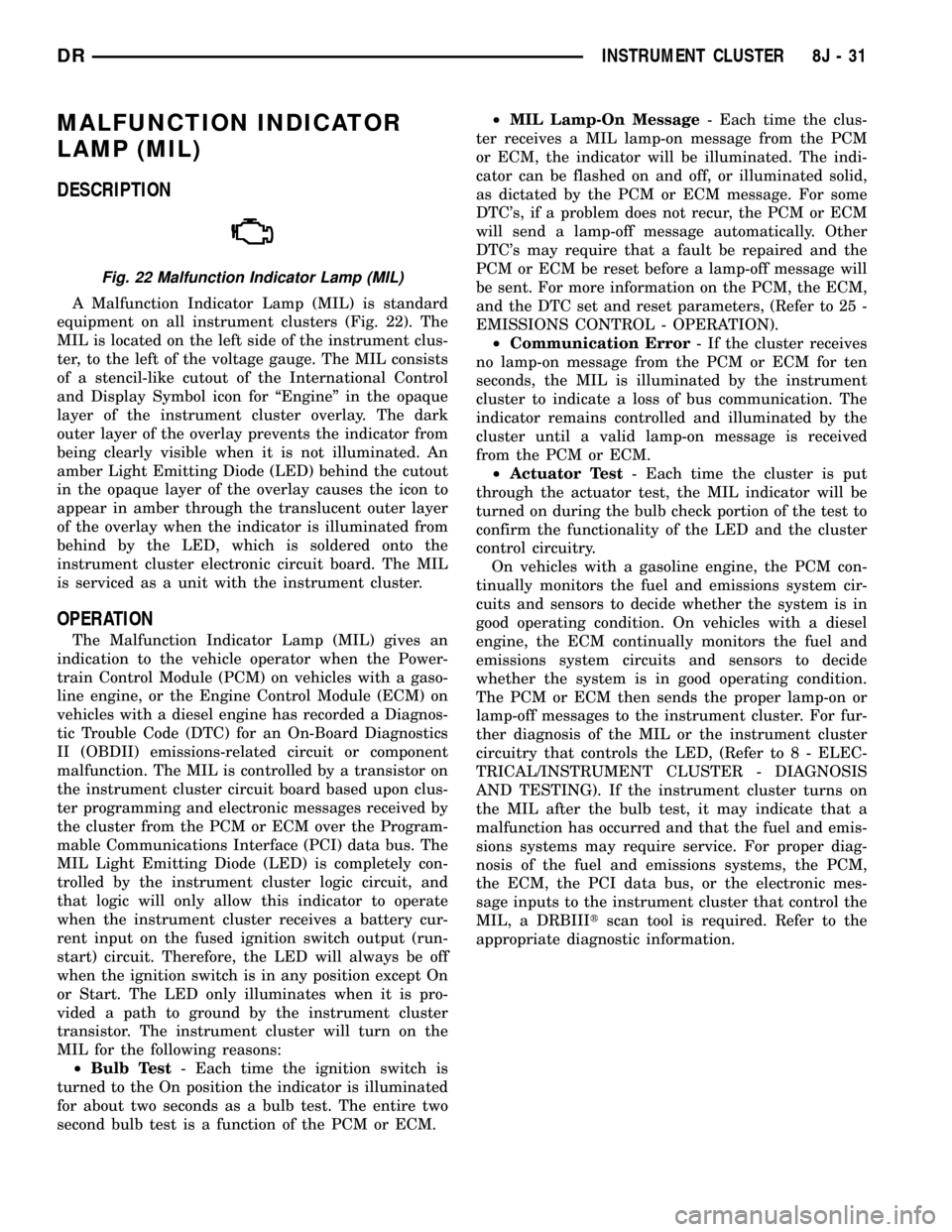
MALFUNCTION INDICATOR
LAMP (MIL)
DESCRIPTION
A Malfunction Indicator Lamp (MIL) is standard
equipment on all instrument clusters (Fig. 22). The
MIL is located on the left side of the instrument clus-
ter, to the left of the voltage gauge. The MIL consists
of a stencil-like cutout of the International Control
and Display Symbol icon for ªEngineº in the opaque
layer of the instrument cluster overlay. The dark
outer layer of the overlay prevents the indicator from
being clearly visible when it is not illuminated. An
amber Light Emitting Diode (LED) behind the cutout
in the opaque layer of the overlay causes the icon to
appear in amber through the translucent outer layer
of the overlay when the indicator is illuminated from
behind by the LED, which is soldered onto the
instrument cluster electronic circuit board. The MIL
is serviced as a unit with the instrument cluster.
OPERATION
The Malfunction Indicator Lamp (MIL) gives an
indication to the vehicle operator when the Power-
train Control Module (PCM) on vehicles with a gaso-
line engine, or the Engine Control Module (ECM) on
vehicles with a diesel engine has recorded a Diagnos-
tic Trouble Code (DTC) for an On-Board Diagnostics
II (OBDII) emissions-related circuit or component
malfunction. The MIL is controlled by a transistor on
the instrument cluster circuit board based upon clus-
ter programming and electronic messages received by
the cluster from the PCM or ECM over the Program-
mable Communications Interface (PCI) data bus. The
MIL Light Emitting Diode (LED) is completely con-
trolled by the instrument cluster logic circuit, and
that logic will only allow this indicator to operate
when the instrument cluster receives a battery cur-
rent input on the fused ignition switch output (run-
start) circuit. Therefore, the LED will always be off
when the ignition switch is in any position except On
or Start. The LED only illuminates when it is pro-
vided a path to ground by the instrument cluster
transistor. The instrument cluster will turn on the
MIL for the following reasons:
²Bulb Test- Each time the ignition switch is
turned to the On position the indicator is illuminated
for about two seconds as a bulb test. The entire two
second bulb test is a function of the PCM or ECM.²MIL Lamp-On Message- Each time the clus-
ter receives a MIL lamp-on message from the PCM
or ECM, the indicator will be illuminated. The indi-
cator can be flashed on and off, or illuminated solid,
as dictated by the PCM or ECM message. For some
DTC's, if a problem does not recur, the PCM or ECM
will send a lamp-off message automatically. Other
DTC's may require that a fault be repaired and the
PCM or ECM be reset before a lamp-off message will
be sent. For more information on the PCM, the ECM,
and the DTC set and reset parameters, (Refer to 25 -
EMISSIONS CONTROL - OPERATION).
²Communication Error- If the cluster receives
no lamp-on message from the PCM or ECM for ten
seconds, the MIL is illuminated by the instrument
cluster to indicate a loss of bus communication. The
indicator remains controlled and illuminated by the
cluster until a valid lamp-on message is received
from the PCM or ECM.
²Actuator Test- Each time the cluster is put
through the actuator test, the MIL indicator will be
turned on during the bulb check portion of the test to
confirm the functionality of the LED and the cluster
control circuitry.
On vehicles with a gasoline engine, the PCM con-
tinually monitors the fuel and emissions system cir-
cuits and sensors to decide whether the system is in
good operating condition. On vehicles with a diesel
engine, the ECM continually monitors the fuel and
emissions system circuits and sensors to decide
whether the system is in good operating condition.
The PCM or ECM then sends the proper lamp-on or
lamp-off messages to the instrument cluster. For fur-
ther diagnosis of the MIL or the instrument cluster
circuitry that controls the LED, (Refer to 8 - ELEC-
TRICAL/INSTRUMENT CLUSTER - DIAGNOSIS
AND TESTING). If the instrument cluster turns on
the MIL after the bulb test, it may indicate that a
malfunction has occurred and that the fuel and emis-
sions systems may require service. For proper diag-
nosis of the fuel and emissions systems, the PCM,
the ECM, the PCI data bus, or the electronic mes-
sage inputs to the instrument cluster that control the
MIL, a DRBIIItscan tool is required. Refer to the
appropriate diagnostic information.
Fig. 22 Malfunction Indicator Lamp (MIL)
DRINSTRUMENT CLUSTER 8J - 31
Page 630 of 2627
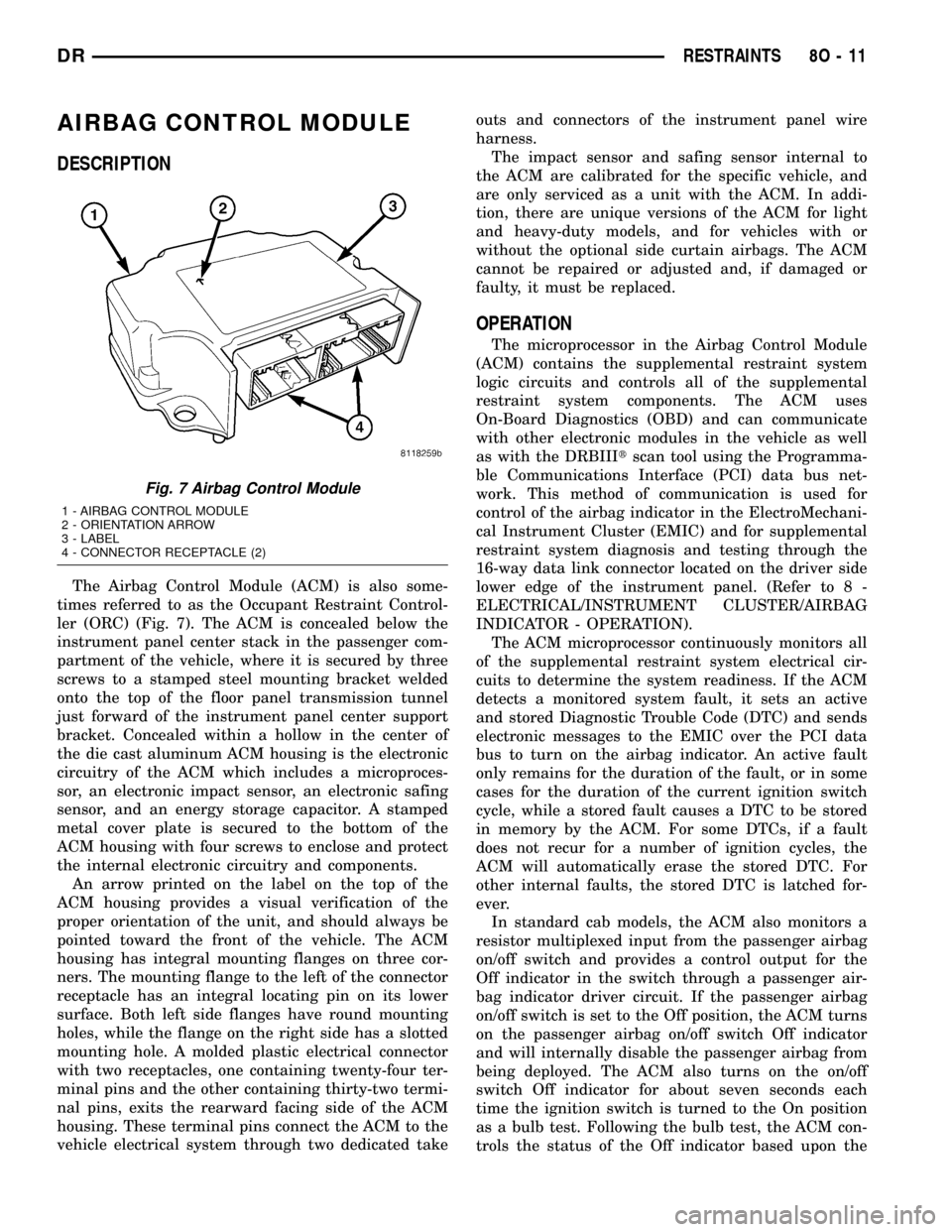
AIRBAG CONTROL MODULE
DESCRIPTION
The Airbag Control Module (ACM) is also some-
times referred to as the Occupant Restraint Control-
ler (ORC) (Fig. 7). The ACM is concealed below the
instrument panel center stack in the passenger com-
partment of the vehicle, where it is secured by three
screws to a stamped steel mounting bracket welded
onto the top of the floor panel transmission tunnel
just forward of the instrument panel center support
bracket. Concealed within a hollow in the center of
the die cast aluminum ACM housing is the electronic
circuitry of the ACM which includes a microproces-
sor, an electronic impact sensor, an electronic safing
sensor, and an energy storage capacitor. A stamped
metal cover plate is secured to the bottom of the
ACM housing with four screws to enclose and protect
the internal electronic circuitry and components.
An arrow printed on the label on the top of the
ACM housing provides a visual verification of the
proper orientation of the unit, and should always be
pointed toward the front of the vehicle. The ACM
housing has integral mounting flanges on three cor-
ners. The mounting flange to the left of the connector
receptacle has an integral locating pin on its lower
surface. Both left side flanges have round mounting
holes, while the flange on the right side has a slotted
mounting hole. A molded plastic electrical connector
with two receptacles, one containing twenty-four ter-
minal pins and the other containing thirty-two termi-
nal pins, exits the rearward facing side of the ACM
housing. These terminal pins connect the ACM to the
vehicle electrical system through two dedicated takeouts and connectors of the instrument panel wire
harness.
The impact sensor and safing sensor internal to
the ACM are calibrated for the specific vehicle, and
are only serviced as a unit with the ACM. In addi-
tion, there are unique versions of the ACM for light
and heavy-duty models, and for vehicles with or
without the optional side curtain airbags. The ACM
cannot be repaired or adjusted and, if damaged or
faulty, it must be replaced.
OPERATION
The microprocessor in the Airbag Control Module
(ACM) contains the supplemental restraint system
logic circuits and controls all of the supplemental
restraint system components. The ACM uses
On-Board Diagnostics (OBD) and can communicate
with other electronic modules in the vehicle as well
as with the DRBIIItscan tool using the Programma-
ble Communications Interface (PCI) data bus net-
work. This method of communication is used for
control of the airbag indicator in the ElectroMechani-
cal Instrument Cluster (EMIC) and for supplemental
restraint system diagnosis and testing through the
16-way data link connector located on the driver side
lower edge of the instrument panel. (Refer to 8 -
ELECTRICAL/INSTRUMENT CLUSTER/AIRBAG
INDICATOR - OPERATION).
The ACM microprocessor continuously monitors all
of the supplemental restraint system electrical cir-
cuits to determine the system readiness. If the ACM
detects a monitored system fault, it sets an active
and stored Diagnostic Trouble Code (DTC) and sends
electronic messages to the EMIC over the PCI data
bus to turn on the airbag indicator. An active fault
only remains for the duration of the fault, or in some
cases for the duration of the current ignition switch
cycle, while a stored fault causes a DTC to be stored
in memory by the ACM. For some DTCs, if a fault
does not recur for a number of ignition cycles, the
ACM will automatically erase the stored DTC. For
other internal faults, the stored DTC is latched for-
ever.
In standard cab models, the ACM also monitors a
resistor multiplexed input from the passenger airbag
on/off switch and provides a control output for the
Off indicator in the switch through a passenger air-
bag indicator driver circuit. If the passenger airbag
on/off switch is set to the Off position, the ACM turns
on the passenger airbag on/off switch Off indicator
and will internally disable the passenger airbag from
being deployed. The ACM also turns on the on/off
switch Off indicator for about seven seconds each
time the ignition switch is turned to the On position
as a bulb test. Following the bulb test, the ACM con-
trols the status of the Off indicator based upon the
Fig. 7 Airbag Control Module
1 - AIRBAG CONTROL MODULE
2 - ORIENTATION ARROW
3 - LABEL
4 - CONNECTOR RECEPTACLE (2)
DRRESTRAINTS 8O - 11
Page 2567 of 2627
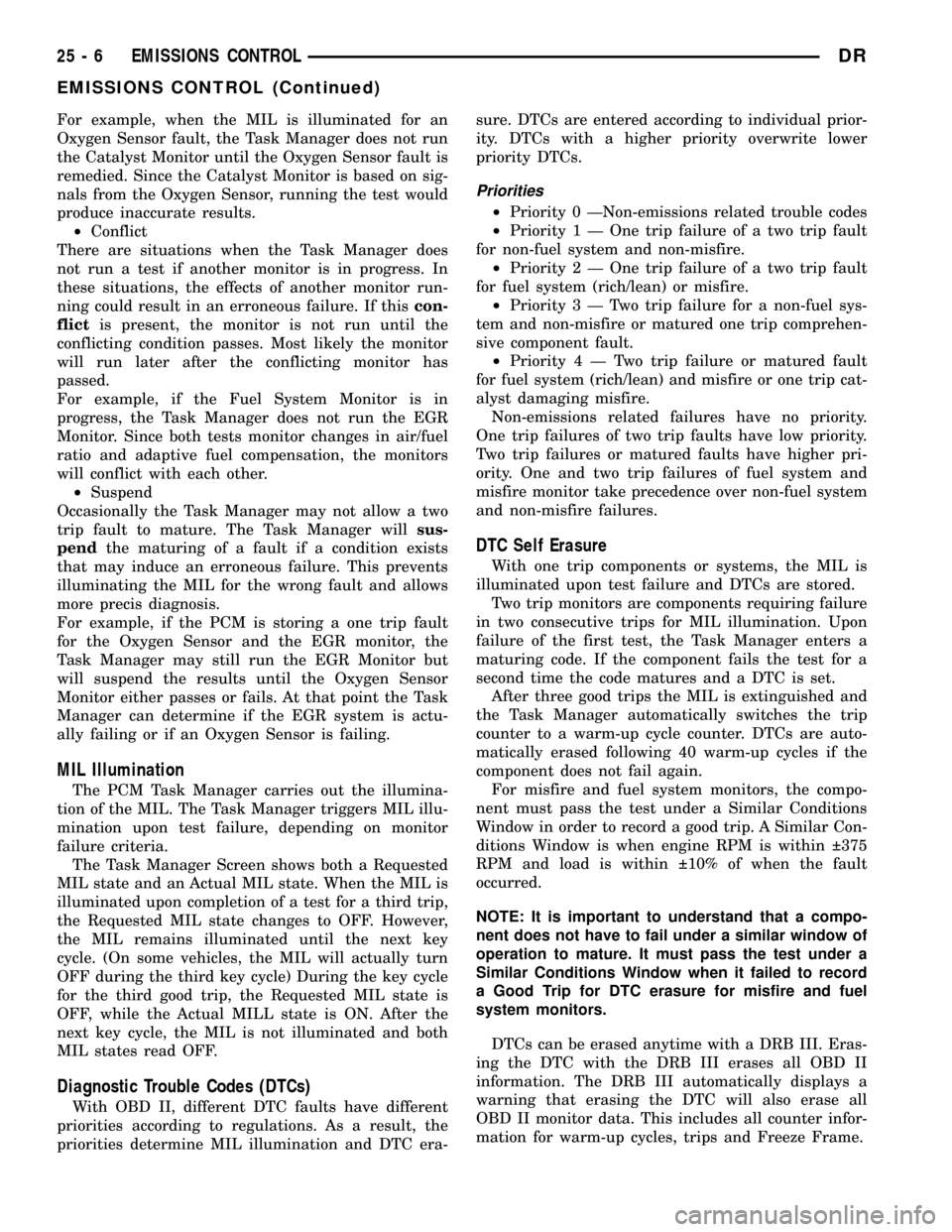
For example, when the MIL is illuminated for an
Oxygen Sensor fault, the Task Manager does not run
the Catalyst Monitor until the Oxygen Sensor fault is
remedied. Since the Catalyst Monitor is based on sig-
nals from the Oxygen Sensor, running the test would
produce inaccurate results.
²Conflict
There are situations when the Task Manager does
not run a test if another monitor is in progress. In
these situations, the effects of another monitor run-
ning could result in an erroneous failure. If thiscon-
flictis present, the monitor is not run until the
conflicting condition passes. Most likely the monitor
will run later after the conflicting monitor has
passed.
For example, if the Fuel System Monitor is in
progress, the Task Manager does not run the EGR
Monitor. Since both tests monitor changes in air/fuel
ratio and adaptive fuel compensation, the monitors
will conflict with each other.
²Suspend
Occasionally the Task Manager may not allow a two
trip fault to mature. The Task Manager willsus-
pendthe maturing of a fault if a condition exists
that may induce an erroneous failure. This prevents
illuminating the MIL for the wrong fault and allows
more precis diagnosis.
For example, if the PCM is storing a one trip fault
for the Oxygen Sensor and the EGR monitor, the
Task Manager may still run the EGR Monitor but
will suspend the results until the Oxygen Sensor
Monitor either passes or fails. At that point the Task
Manager can determine if the EGR system is actu-
ally failing or if an Oxygen Sensor is failing.
MIL Illumination
The PCM Task Manager carries out the illumina-
tion of the MIL. The Task Manager triggers MIL illu-
mination upon test failure, depending on monitor
failure criteria.
The Task Manager Screen shows both a Requested
MIL state and an Actual MIL state. When the MIL is
illuminated upon completion of a test for a third trip,
the Requested MIL state changes to OFF. However,
the MIL remains illuminated until the next key
cycle. (On some vehicles, the MIL will actually turn
OFF during the third key cycle) During the key cycle
for the third good trip, the Requested MIL state is
OFF, while the Actual MILL state is ON. After the
next key cycle, the MIL is not illuminated and both
MIL states read OFF.
Diagnostic Trouble Codes (DTCs)
With OBD II, different DTC faults have different
priorities according to regulations. As a result, the
priorities determine MIL illumination and DTC era-sure. DTCs are entered according to individual prior-
ity. DTCs with a higher priority overwrite lower
priority DTCs.
Priorities
²Priority 0 ÐNon-emissions related trouble codes
²Priority 1 Ð One trip failure of a two trip fault
for non-fuel system and non-misfire.
²Priority 2 Ð One trip failure of a two trip fault
for fuel system (rich/lean) or misfire.
²Priority3ÐTwotrip failure for a non-fuel sys-
tem and non-misfire or matured one trip comprehen-
sive component fault.
²Priority4ÐTwotrip failure or matured fault
for fuel system (rich/lean) and misfire or one trip cat-
alyst damaging misfire.
Non-emissions related failures have no priority.
One trip failures of two trip faults have low priority.
Two trip failures or matured faults have higher pri-
ority. One and two trip failures of fuel system and
misfire monitor take precedence over non-fuel system
and non-misfire failures.
DTC Self Erasure
With one trip components or systems, the MIL is
illuminated upon test failure and DTCs are stored.
Two trip monitors are components requiring failure
in two consecutive trips for MIL illumination. Upon
failure of the first test, the Task Manager enters a
maturing code. If the component fails the test for a
second time the code matures and a DTC is set.
After three good trips the MIL is extinguished and
the Task Manager automatically switches the trip
counter to a warm-up cycle counter. DTCs are auto-
matically erased following 40 warm-up cycles if the
component does not fail again.
For misfire and fuel system monitors, the compo-
nent must pass the test under a Similar Conditions
Window in order to record a good trip. A Similar Con-
ditions Window is when engine RPM is within 375
RPM and load is within 10% of when the fault
occurred.
NOTE: It is important to understand that a compo-
nent does not have to fail under a similar window of
operation to mature. It must pass the test under a
Similar Conditions Window when it failed to record
a Good Trip for DTC erasure for misfire and fuel
system monitors.
DTCs can be erased anytime with a DRB III. Eras-
ing the DTC with the DRB III erases all OBD II
information. The DRB III automatically displays a
warning that erasing the DTC will also erase all
OBD II monitor data. This includes all counter infor-
mation for warm-up cycles, trips and Freeze Frame.
25 - 6 EMISSIONS CONTROLDR
EMISSIONS CONTROL (Continued)
Page 2571 of 2627
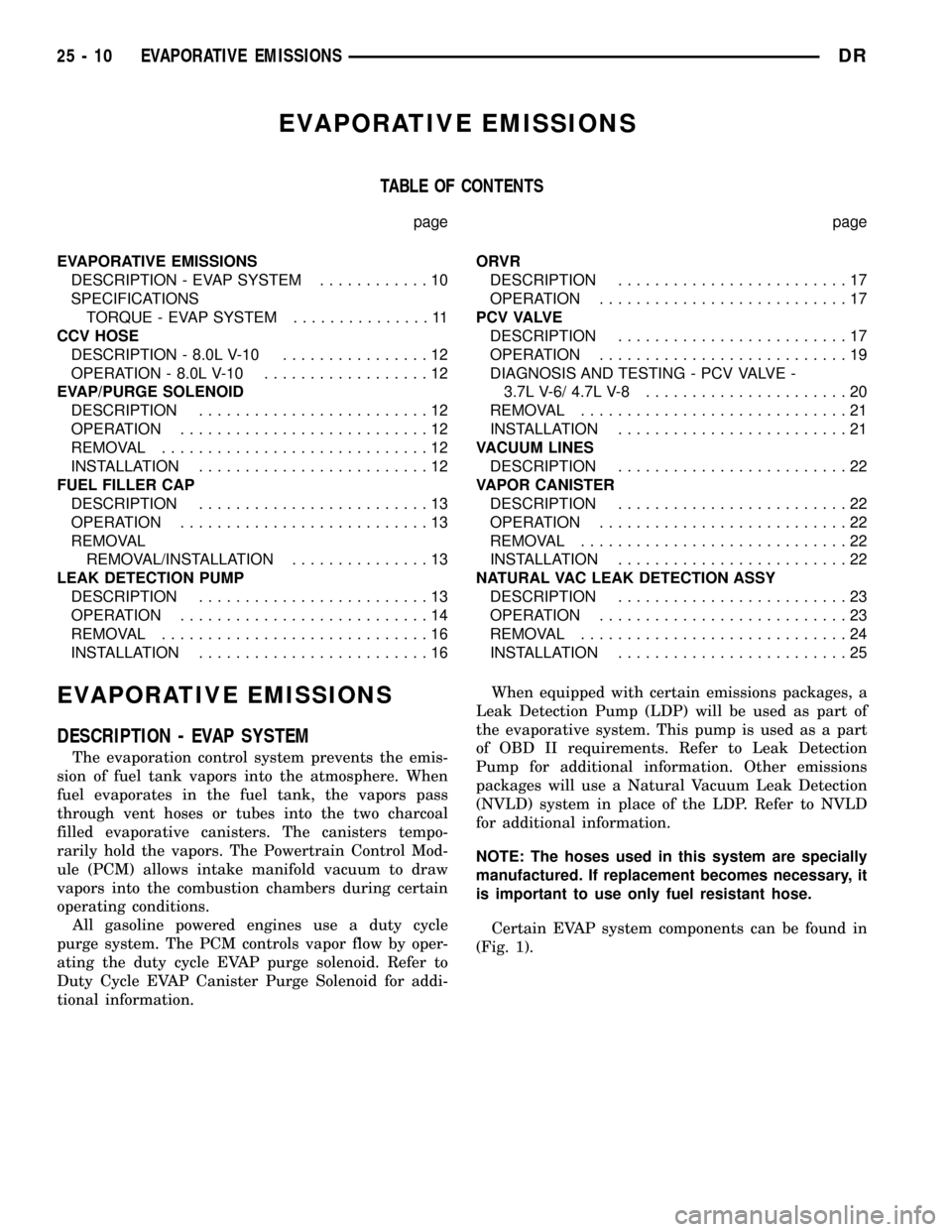
EVAPORATIVE EMISSIONS
TABLE OF CONTENTS
page page
EVAPORATIVE EMISSIONS
DESCRIPTION - EVAP SYSTEM............10
SPECIFICATIONS
TORQUE - EVAP SYSTEM...............11
CCV HOSE
DESCRIPTION - 8.0L V-10................12
OPERATION - 8.0L V-10..................12
EVAP/PURGE SOLENOID
DESCRIPTION.........................12
OPERATION...........................12
REMOVAL.............................12
INSTALLATION.........................12
FUEL FILLER CAP
DESCRIPTION.........................13
OPERATION...........................13
REMOVAL
REMOVAL/INSTALLATION...............13
LEAK DETECTION PUMP
DESCRIPTION.........................13
OPERATION...........................14
REMOVAL.............................16
INSTALLATION.........................16ORVR
DESCRIPTION.........................17
OPERATION...........................17
P C V VA LV E
DESCRIPTION.........................17
OPERATION...........................19
DIAGNOSIS AND TESTING - PCV VALVE -
3.7L V-6/ 4.7L V-8......................20
REMOVAL.............................21
INSTALLATION.........................21
VACUUM LINES
DESCRIPTION.........................22
VAPOR CANISTER
DESCRIPTION.........................22
OPERATION...........................22
REMOVAL.............................22
INSTALLATION.........................22
NATURAL VAC LEAK DETECTION ASSY
DESCRIPTION.........................23
OPERATION...........................23
REMOVAL.............................24
INSTALLATION.........................25
EVAPORATIVE EMISSIONS
DESCRIPTION - EVAP SYSTEM
The evaporation control system prevents the emis-
sion of fuel tank vapors into the atmosphere. When
fuel evaporates in the fuel tank, the vapors pass
through vent hoses or tubes into the two charcoal
filled evaporative canisters. The canisters tempo-
rarily hold the vapors. The Powertrain Control Mod-
ule (PCM) allows intake manifold vacuum to draw
vapors into the combustion chambers during certain
operating conditions.
All gasoline powered engines use a duty cycle
purge system. The PCM controls vapor flow by oper-
ating the duty cycle EVAP purge solenoid. Refer to
Duty Cycle EVAP Canister Purge Solenoid for addi-
tional information.When equipped with certain emissions packages, a
Leak Detection Pump (LDP) will be used as part of
the evaporative system. This pump is used as a part
of OBD II requirements. Refer to Leak Detection
Pump for additional information. Other emissions
packages will use a Natural Vacuum Leak Detection
(NVLD) system in place of the LDP. Refer to NVLD
for additional information.
NOTE: The hoses used in this system are specially
manufactured. If replacement becomes necessary, it
is important to use only fuel resistant hose.
Certain EVAP system components can be found in
(Fig. 1).
25 - 10 EVAPORATIVE EMISSIONSDR
Page 2609 of 2627
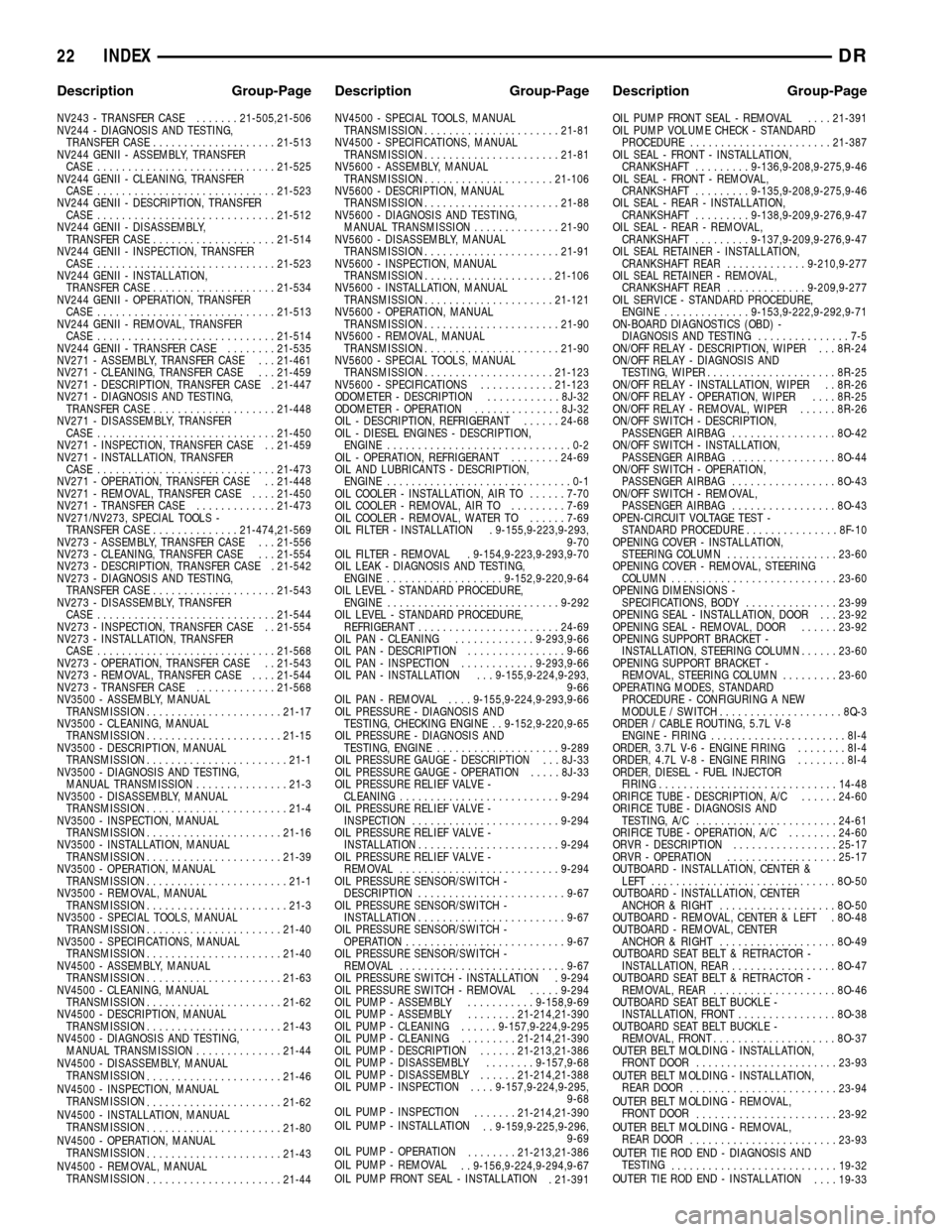
NV243 - TRANSFER CASE.......21-505,21-506
NV244 - DIAGNOSIS AND TESTING,
TRANSFER CASE....................21-513
NV244 GENII - ASSEMBLY, TRANSFER
CASE.............................21-525
NV244 GENII - CLEANING, TRANSFER
CASE.............................21-523
NV244 GENII - DESCRIPTION, TRANSFER
CASE.............................21-512
NV244 GENII - DISASSEMBLY,
TRANSFER CASE....................21-514
NV244 GENII - INSPECTION, TRANSFER
CASE.............................21-523
NV244 GENII - INSTALLATION,
TRANSFER CASE....................21-534
NV244 GENII - OPERATION, TRANSFER
CASE.............................21-513
NV244 GENII - REMOVAL, TRANSFER
CASE.............................21-514
NV244 GENII - TRANSFER CASE........21-535
NV271 - ASSEMBLY, TRANSFER CASE . . . 21-461
NV271 - CLEANING, TRANSFER CASE . . . 21-459
NV271 - DESCRIPTION, TRANSFER CASE . 21-447
NV271 - DIAGNOSIS AND TESTING,
TRANSFER CASE....................21-448
NV271 - DISASSEMBLY, TRANSFER
CASE.............................21-450
NV271 - INSPECTION, TRANSFER CASE . . 21-459
NV271 - INSTALLATION, TRANSFER
CASE.............................21-473
NV271 - OPERATION, TRANSFER CASE . . 21-448
NV271 - REMOVAL, TRANSFER CASE....21-450
NV271 - TRANSFER CASE.............21-473
NV271/NV273, SPECIAL TOOLS -
TRANSFER CASE..............21-474,21-569
NV273 - ASSEMBLY, TRANSFER CASE . . . 21-556
NV273 - CLEANING, TRANSFER CASE . . . 21-554
NV273 - DESCRIPTION, TRANSFER CASE . 21-542
NV273 - DIAGNOSIS AND TESTING,
TRANSFER CASE....................21-543
NV273 - DISASSEMBLY, TRANSFER
CASE.............................21-544
NV273 - INSPECTION, TRANSFER CASE . . 21-554
NV273 - INSTALLATION, TRANSFER
CASE.............................21-568
NV273 - OPERATION, TRANSFER CASE . . 21-543
NV273 - REMOVAL, TRANSFER CASE....21-544
NV273 - TRANSFER CASE.............21-568
NV3500 - ASSEMBLY, MANUAL
TRANSMISSION......................21-17
NV3500 - CLEANING, MANUAL
TRANSMISSION......................21-15
NV3500 - DESCRIPTION, MANUAL
TRANSMISSION.......................21-1
NV3500 - DIAGNOSIS AND TESTING,
MANUAL TRANSMISSION...............21-3
NV3500 - DISASSEMBLY, MANUAL
TRANSMISSION.......................21-4
NV3500 - INSPECTION, MANUAL
TRANSMISSION......................21-16
NV3500 - INSTALLATION, MANUAL
TRANSMISSION......................21-39
NV3500 - OPERATION, MANUAL
TRANSMISSION.......................21-1
NV3500 - REMOVAL, MANUAL
TRANSMISSION.......................21-3
NV3500 - SPECIAL TOOLS, MANUAL
TRANSMISSION......................21-40
NV3500 - SPECIFICATIONS, MANUAL
TRANSMISSION......................21-40
NV4500 - ASSEMBLY, MANUAL
TRANSMISSION......................21-63
NV4500 - CLEANING, MANUAL
TRANSMISSION......................21-62
NV4500 - DESCRIPTION, MANUAL
TRANSMISSION......................21-43
NV4500 - DIAGNOSIS AND TESTING,
MANUAL TRANSMISSION..............21-44
NV4500 - DISASSEMBLY, MANUAL
TRANSMISSION
......................21-46
NV4500 - INSPECTION, MANUAL
TRANSMISSION
......................21-62
NV4500 - INSTALLATION, MANUAL
TRANSMISSION
......................21-80
NV4500 - OPERATION, MANUAL
TRANSMISSION
......................21-43
NV4500 - REMOVAL, MANUAL
TRANSMISSION
......................21-44NV4500 - SPECIAL TOOLS, MANUAL
TRANSMISSION......................21-81
NV4500 - SPECIFICATIONS, MANUAL
TRANSMISSION......................21-81
NV5600 - ASSEMBLY, MANUAL
TRANSMISSION.....................21-106
NV5600 - DESCRIPTION, MANUAL
TRANSMISSION......................21-88
NV5600 - DIAGNOSIS AND TESTING,
MANUAL TRANSMISSION..............21-90
NV5600 - DISASSEMBLY, MANUAL
TRANSMISSION......................21-91
NV5600 - INSPECTION, MANUAL
TRANSMISSION.....................21-106
NV5600 - INSTALLATION, MANUAL
TRANSMISSION.....................21-121
NV5600 - OPERATION, MANUAL
TRANSMISSION......................21-90
NV5600 - REMOVAL, MANUAL
TRANSMISSION......................21-90
NV5600 - SPECIAL TOOLS, MANUAL
TRANSMISSION.....................21-123
NV5600 - SPECIFICATIONS............21-123
ODOMETER - DESCRIPTION............8J-32
ODOMETER - OPERATION..............8J-32
OIL - DESCRIPTION, REFRIGERANT......24-68
OIL - DIESEL ENGINES - DESCRIPTION,
ENGINE..............................0-2
OIL - OPERATION, REFRIGERANT........24-69
OIL AND LUBRICANTS - DESCRIPTION,
ENGINE..............................0-1
OIL COOLER - INSTALLATION, AIR TO......7-70
OIL COOLER - REMOVAL, AIR TO.........7-69
OIL COOLER - REMOVAL, WATER TO......7-69
OIL FILTER - INSTALLATION . 9-155,9-223,9-293,
9-70
OIL FILTER - REMOVAL . 9-154,9-223,9-293,9-70
OIL LEAK - DIAGNOSIS AND TESTING,
ENGINE...................9-152,9-220,9-64
OIL LEVEL - STANDARD PROCEDURE,
ENGINE............................9-292
OIL LEVEL - STANDARD PROCEDURE,
REFRIGERANT.......................24-69
OIL PAN - CLEANING.............9-293,9-66
OIL PAN - DESCRIPTION................9-66
OIL PAN - INSPECTION............9-293,9-66
OIL PAN - INSTALLATION . . . 9-155,9-224,9-293,
9-66
OIL PAN - REMOVAL....9-155,9-224,9-293,9-66
OIL PRESSURE - DIAGNOSIS AND
TESTING, CHECKING ENGINE . . 9-152,9-220,9-65
OIL PRESSURE - DIAGNOSIS AND
TESTING, ENGINE....................9-289
OIL PRESSURE GAUGE - DESCRIPTION . . . 8J-33
OIL PRESSURE GAUGE - OPERATION.....8J-33
OIL PRESSURE RELIEF VALVE -
CLEANING..........................9-294
OIL PRESSURE RELIEF VALVE -
INSPECTION........................9-294
OIL PRESSURE RELIEF VALVE -
INSTALLATION.......................9-294
OIL PRESSURE RELIEF VALVE -
REMOVAL..........................9-294
OIL PRESSURE SENSOR/SWITCH -
DESCRIPTION........................9-67
OIL PRESSURE SENSOR/SWITCH -
INSTALLATION........................9-67
OIL PRESSURE SENSOR/SWITCH -
OPERATION..........................9-67
OIL PRESSURE SENSOR/SWITCH -
REMOVAL...........................9-67
OIL PRESSURE SWITCH - INSTALLATION . 9-294
OIL PRESSURE SWITCH - REMOVAL.....9-294
OIL PUMP - ASSEMBLY...........9-158,9-69
OIL PUMP - ASSEMBLY........21-214,21-390
OIL PUMP - CLEANING......9-157,9-224,9-295
OIL PUMP - CLEANING.........21-214,21-390
OIL PUMP - DESCRIPTION......21-213,21-386
OIL PUMP - DISASSEMBLY........9-157,9-68
OIL PUMP - DISASSEMBLY......21-214,21-388
OIL PUMP - INSPECTION....9-157,9-224,9-295,
9-68
OIL PUMP - INSPECTION
.......21-214,21-390
OIL PUMP - INSTALLATION
. . 9-159,9-225,9-296,
9-69
OIL PUMP - OPERATION
........21-213,21-386
OIL PUMP - REMOVAL
. . 9-156,9-224,9-294,9-67
OIL PUMP FRONT SEAL - INSTALLATION
. 21-391OIL PUMP FRONT SEAL - REMOVAL....21-391
OIL PUMP VOLUME CHECK - STANDARD
PROCEDURE.......................21-387
OIL SEAL - FRONT - INSTALLATION,
CRANKSHAFT.........9-136,9-208,9-275,9-46
OIL SEAL - FRONT - REMOVAL,
CRANKSHAFT.........9-135,9-208,9-275,9-46
OIL SEAL - REAR - INSTALLATION,
CRANKSHAFT.........9-138,9-209,9-276,9-47
OIL SEAL - REAR - REMOVAL,
CRANKSHAFT.........9-137,9-209,9-276,9-47
OIL SEAL RETAINER - INSTALLATION,
CRANKSHAFT REAR.............9-210,9-277
OIL SEAL RETAINER - REMOVAL,
CRANKSHAFT REAR.............9-209,9-277
OIL SERVICE - STANDARD PROCEDURE,
ENGINE..............9-153,9-222,9-292,9-71
ON-BOARD DIAGNOSTICS (OBD) -
DIAGNOSIS AND TESTING...............7-5
ON/OFF RELAY - DESCRIPTION, WIPER . . . 8R-24
ON/OFF RELAY - DIAGNOSIS AND
TESTING, WIPER.....................8R-25
ON/OFF RELAY - INSTALLATION, WIPER . . 8R-26
ON/OFF RELAY - OPERATION, WIPER....8R-25
ON/OFF RELAY - REMOVAL, WIPER......8R-26
ON/OFF SWITCH - DESCRIPTION,
PASSENGER AIRBAG.................8O-42
ON/OFF SWITCH - INSTALLATION,
PASSENGER AIRBAG.................8O-44
ON/OFF SWITCH - OPERATION,
PASSENGER AIRBAG.................8O-43
ON/OFF SWITCH - REMOVAL,
PASSENGER AIRBAG.................8O-43
OPEN-CIRCUIT VOLTAGE TEST -
STANDARD PROCEDURE...............8F-10
OPENING COVER - INSTALLATION,
STEERING COLUMN..................23-60
OPENING COVER - REMOVAL, STEERING
COLUMN...........................23-60
OPENING DIMENSIONS -
SPECIFICATIONS, BODY...............23-99
OPENING SEAL - INSTALLATION, DOOR . . . 23-92
OPENING SEAL - REMOVAL, DOOR......23-92
OPENING SUPPORT BRACKET -
INSTALLATION, STEERING COLUMN......23-60
OPENING SUPPORT BRACKET -
REMOVAL, STEERING COLUMN.........23-60
OPERATING MODES, STANDARD
PROCEDURE - CONFIGURING A NEW
MODULE / SWITCH....................8Q-3
ORDER / CABLE ROUTING, 5.7L V-8
ENGINE - FIRING......................8I-4
ORDER, 3.7L V-6 - ENGINE FIRING........8I-4
ORDER, 4.7L V-8 - ENGINE FIRING........8I-4
ORDER, DIESEL - FUEL INJECTOR
FIRING.............................14-48
ORIFICE TUBE - DESCRIPTION, A/C......24-60
ORIFICE TUBE - DIAGNOSIS AND
TESTING, A/C.......................24-61
ORIFICE TUBE - OPERATION, A/C........24-60
ORVR - DESCRIPTION.................25-17
ORVR - OPERATION..................25-17
OUTBOARD - INSTALLATION, CENTER &
LEFT..............................8O-50
OUTBOARD - INSTALLATION, CENTER
ANCHOR & RIGHT...................8O-50
OUTBOARD - REMOVAL, CENTER & LEFT . 8O-48
OUTBOARD - REMOVAL, CENTER
ANCHOR & RIGHT...................8O-49
OUTBOARD SEAT BELT & RETRACTOR -
INSTALLATION, REAR.................8O-47
OUTBOARD SEAT BELT & RETRACTOR -
REMOVAL, REAR....................8O-46
OUTBOARD SEAT BELT BUCKLE -
INSTALLATION, FRONT................8O-38
OUTBOARD SEAT BELT BUCKLE -
REMOVAL, FRONT....................8O-37
OUTER BELT MOLDING - INSTALLATION,
FRONT DOOR.......................23-93
OUTER BELT MOLDING - INSTALLATION,
REAR DOOR
........................23-94
OUTER BELT MOLDING - REMOVAL,
FRONT DOOR
.......................23-92
OUTER BELT MOLDING - REMOVAL,
REAR DOOR
........................23-93
OUTER TIE ROD END - DIAGNOSIS AND
TESTING
...........................19-32
OUTER TIE ROD END - INSTALLATION
....19-33
22 INDEXDR
Description Group-Page Description Group-Page Description Group-Page