sensor DODGE RAM 2002 Service Repair Manual
[x] Cancel search | Manufacturer: DODGE, Model Year: 2002, Model line: RAM, Model: DODGE RAM 2002Pages: 2255, PDF Size: 62.07 MB
Page 2200 of 2255
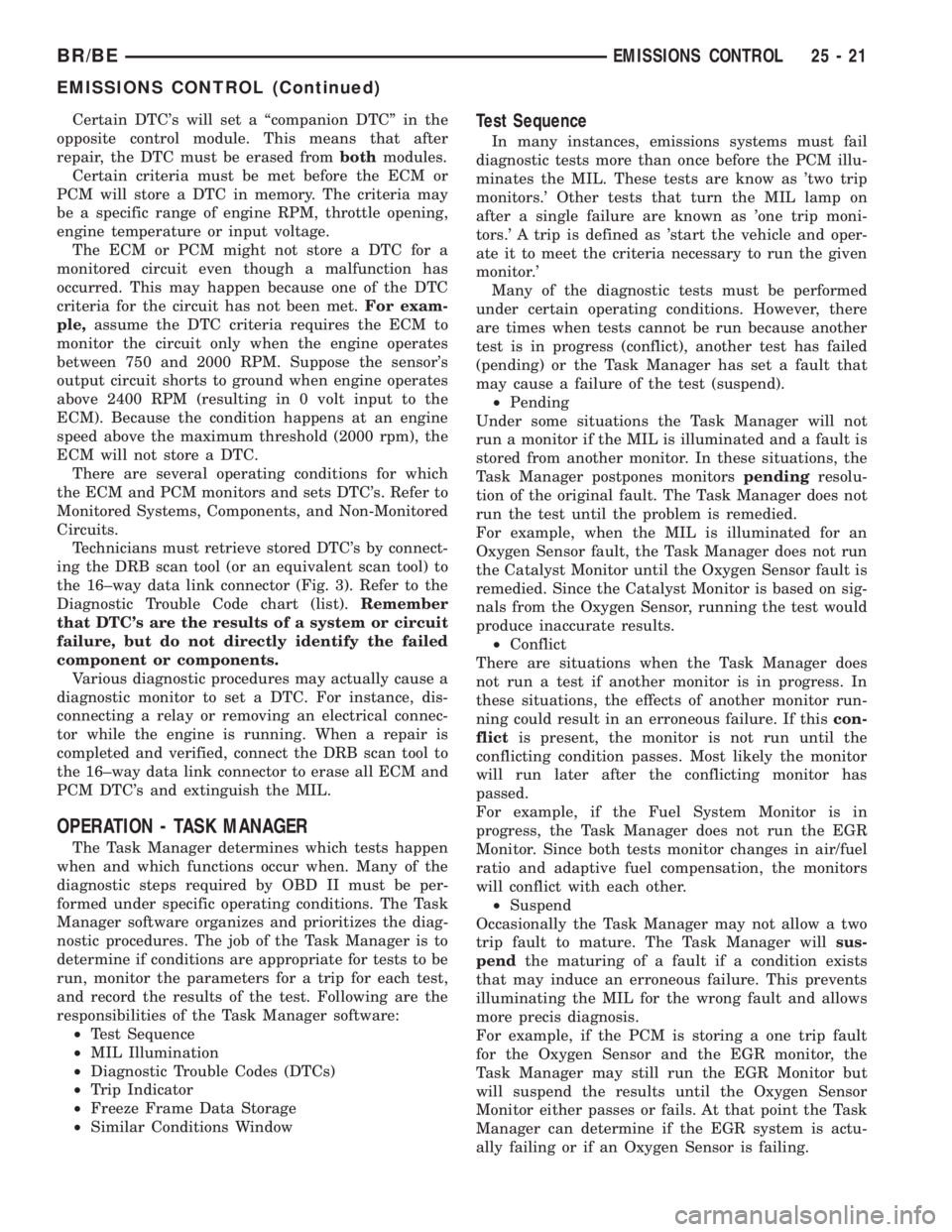
Certain DTC's will set a ªcompanion DTCº in the
opposite control module. This means that after
repair, the DTC must be erased frombothmodules.
Certain criteria must be met before the ECM or
PCM will store a DTC in memory. The criteria may
be a specific range of engine RPM, throttle opening,
engine temperature or input voltage.
The ECM or PCM might not store a DTC for a
monitored circuit even though a malfunction has
occurred. This may happen because one of the DTC
criteria for the circuit has not been met.For exam-
ple,assume the DTC criteria requires the ECM to
monitor the circuit only when the engine operates
between 750 and 2000 RPM. Suppose the sensor's
output circuit shorts to ground when engine operates
above 2400 RPM (resulting in 0 volt input to the
ECM). Because the condition happens at an engine
speed above the maximum threshold (2000 rpm), the
ECM will not store a DTC.
There are several operating conditions for which
the ECM and PCM monitors and sets DTC's. Refer to
Monitored Systems, Components, and Non-Monitored
Circuits.
Technicians must retrieve stored DTC's by connect-
ing the DRB scan tool (or an equivalent scan tool) to
the 16±way data link connector (Fig. 3). Refer to the
Diagnostic Trouble Code chart (list).Remember
that DTC's are the results of a system or circuit
failure, but do not directly identify the failed
component or components.
Various diagnostic procedures may actually cause a
diagnostic monitor to set a DTC. For instance, dis-
connecting a relay or removing an electrical connec-
tor while the engine is running. When a repair is
completed and verified, connect the DRB scan tool to
the 16±way data link connector to erase all ECM and
PCM DTC's and extinguish the MIL.
OPERATION - TASK MANAGER
The Task Manager determines which tests happen
when and which functions occur when. Many of the
diagnostic steps required by OBD II must be per-
formed under specific operating conditions. The Task
Manager software organizes and prioritizes the diag-
nostic procedures. The job of the Task Manager is to
determine if conditions are appropriate for tests to be
run, monitor the parameters for a trip for each test,
and record the results of the test. Following are the
responsibilities of the Task Manager software:
²Test Sequence
²MIL Illumination
²Diagnostic Trouble Codes (DTCs)
²Trip Indicator
²Freeze Frame Data Storage
²Similar Conditions Window
Test Sequence
In many instances, emissions systems must fail
diagnostic tests more than once before the PCM illu-
minates the MIL. These tests are know as 'two trip
monitors.' Other tests that turn the MIL lamp on
after a single failure are known as 'one trip moni-
tors.' A trip is defined as 'start the vehicle and oper-
ate it to meet the criteria necessary to run the given
monitor.'
Many of the diagnostic tests must be performed
under certain operating conditions. However, there
are times when tests cannot be run because another
test is in progress (conflict), another test has failed
(pending) or the Task Manager has set a fault that
may cause a failure of the test (suspend).
²Pending
Under some situations the Task Manager will not
run a monitor if the MIL is illuminated and a fault is
stored from another monitor. In these situations, the
Task Manager postpones monitorspendingresolu-
tion of the original fault. The Task Manager does not
run the test until the problem is remedied.
For example, when the MIL is illuminated for an
Oxygen Sensor fault, the Task Manager does not run
the Catalyst Monitor until the Oxygen Sensor fault is
remedied. Since the Catalyst Monitor is based on sig-
nals from the Oxygen Sensor, running the test would
produce inaccurate results.
²Conflict
There are situations when the Task Manager does
not run a test if another monitor is in progress. In
these situations, the effects of another monitor run-
ning could result in an erroneous failure. If thiscon-
flictis present, the monitor is not run until the
conflicting condition passes. Most likely the monitor
will run later after the conflicting monitor has
passed.
For example, if the Fuel System Monitor is in
progress, the Task Manager does not run the EGR
Monitor. Since both tests monitor changes in air/fuel
ratio and adaptive fuel compensation, the monitors
will conflict with each other.
²Suspend
Occasionally the Task Manager may not allow a two
trip fault to mature. The Task Manager willsus-
pendthe maturing of a fault if a condition exists
that may induce an erroneous failure. This prevents
illuminating the MIL for the wrong fault and allows
more precis diagnosis.
For example, if the PCM is storing a one trip fault
for the Oxygen Sensor and the EGR monitor, the
Task Manager may still run the EGR Monitor but
will suspend the results until the Oxygen Sensor
Monitor either passes or fails. At that point the Task
Manager can determine if the EGR system is actu-
ally failing or if an Oxygen Sensor is failing.
BR/BEEMISSIONS CONTROL 25 - 21
EMISSIONS CONTROL (Continued)
Page 2201 of 2255
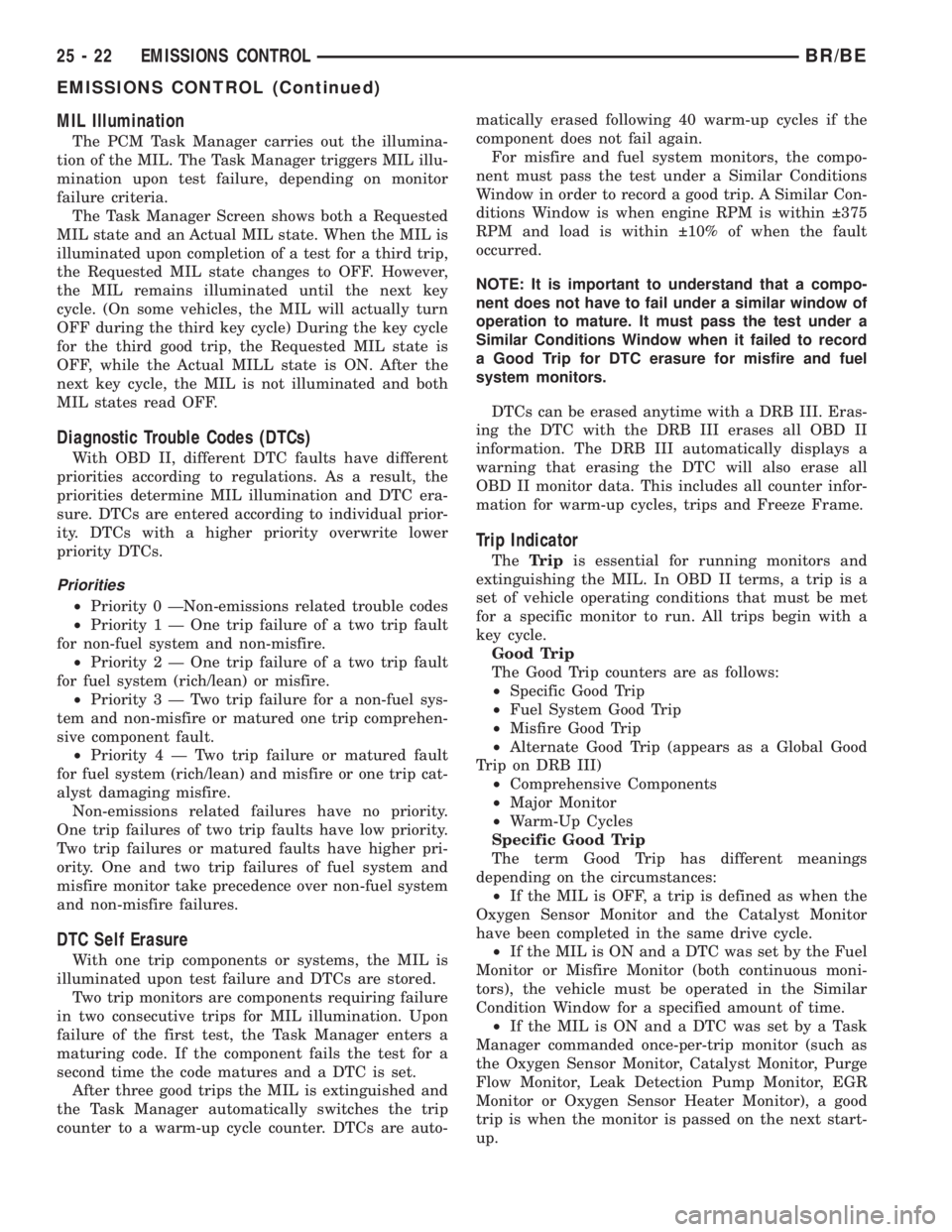
MIL Illumination
The PCM Task Manager carries out the illumina-
tion of the MIL. The Task Manager triggers MIL illu-
mination upon test failure, depending on monitor
failure criteria.
The Task Manager Screen shows both a Requested
MIL state and an Actual MIL state. When the MIL is
illuminated upon completion of a test for a third trip,
the Requested MIL state changes to OFF. However,
the MIL remains illuminated until the next key
cycle. (On some vehicles, the MIL will actually turn
OFF during the third key cycle) During the key cycle
for the third good trip, the Requested MIL state is
OFF, while the Actual MILL state is ON. After the
next key cycle, the MIL is not illuminated and both
MIL states read OFF.
Diagnostic Trouble Codes (DTCs)
With OBD II, different DTC faults have different
priorities according to regulations. As a result, the
priorities determine MIL illumination and DTC era-
sure. DTCs are entered according to individual prior-
ity. DTCs with a higher priority overwrite lower
priority DTCs.
Priorities
²Priority 0 ÐNon-emissions related trouble codes
²Priority 1 Ð One trip failure of a two trip fault
for non-fuel system and non-misfire.
²Priority 2 Ð One trip failure of a two trip fault
for fuel system (rich/lean) or misfire.
²Priority3ÐTwotrip failure for a non-fuel sys-
tem and non-misfire or matured one trip comprehen-
sive component fault.
²Priority4ÐTwotrip failure or matured fault
for fuel system (rich/lean) and misfire or one trip cat-
alyst damaging misfire.
Non-emissions related failures have no priority.
One trip failures of two trip faults have low priority.
Two trip failures or matured faults have higher pri-
ority. One and two trip failures of fuel system and
misfire monitor take precedence over non-fuel system
and non-misfire failures.
DTC Self Erasure
With one trip components or systems, the MIL is
illuminated upon test failure and DTCs are stored.
Two trip monitors are components requiring failure
in two consecutive trips for MIL illumination. Upon
failure of the first test, the Task Manager enters a
maturing code. If the component fails the test for a
second time the code matures and a DTC is set.
After three good trips the MIL is extinguished and
the Task Manager automatically switches the trip
counter to a warm-up cycle counter. DTCs are auto-matically erased following 40 warm-up cycles if the
component does not fail again.
For misfire and fuel system monitors, the compo-
nent must pass the test under a Similar Conditions
Window in order to record a good trip. A Similar Con-
ditions Window is when engine RPM is within 375
RPM and load is within 10% of when the fault
occurred.
NOTE: It is important to understand that a compo-
nent does not have to fail under a similar window of
operation to mature. It must pass the test under a
Similar Conditions Window when it failed to record
a Good Trip for DTC erasure for misfire and fuel
system monitors.
DTCs can be erased anytime with a DRB III. Eras-
ing the DTC with the DRB III erases all OBD II
information. The DRB III automatically displays a
warning that erasing the DTC will also erase all
OBD II monitor data. This includes all counter infor-
mation for warm-up cycles, trips and Freeze Frame.
Trip Indicator
TheTripis essential for running monitors and
extinguishing the MIL. In OBD II terms, a trip is a
set of vehicle operating conditions that must be met
for a specific monitor to run. All trips begin with a
key cycle.
Good Trip
The Good Trip counters are as follows:
²Specific Good Trip
²Fuel System Good Trip
²Misfire Good Trip
²Alternate Good Trip (appears as a Global Good
Trip on DRB III)
²Comprehensive Components
²Major Monitor
²Warm-Up Cycles
Specific Good Trip
The term Good Trip has different meanings
depending on the circumstances:
²If the MIL is OFF, a trip is defined as when the
Oxygen Sensor Monitor and the Catalyst Monitor
have been completed in the same drive cycle.
²If the MIL is ON and a DTC was set by the Fuel
Monitor or Misfire Monitor (both continuous moni-
tors), the vehicle must be operated in the Similar
Condition Window for a specified amount of time.
²If the MIL is ON and a DTC was set by a Task
Manager commanded once-per-trip monitor (such as
the Oxygen Sensor Monitor, Catalyst Monitor, Purge
Flow Monitor, Leak Detection Pump Monitor, EGR
Monitor or Oxygen Sensor Heater Monitor), a good
trip is when the monitor is passed on the next start-
up.
25 - 22 EMISSIONS CONTROLBR/BE
EMISSIONS CONTROL (Continued)
Page 2202 of 2255
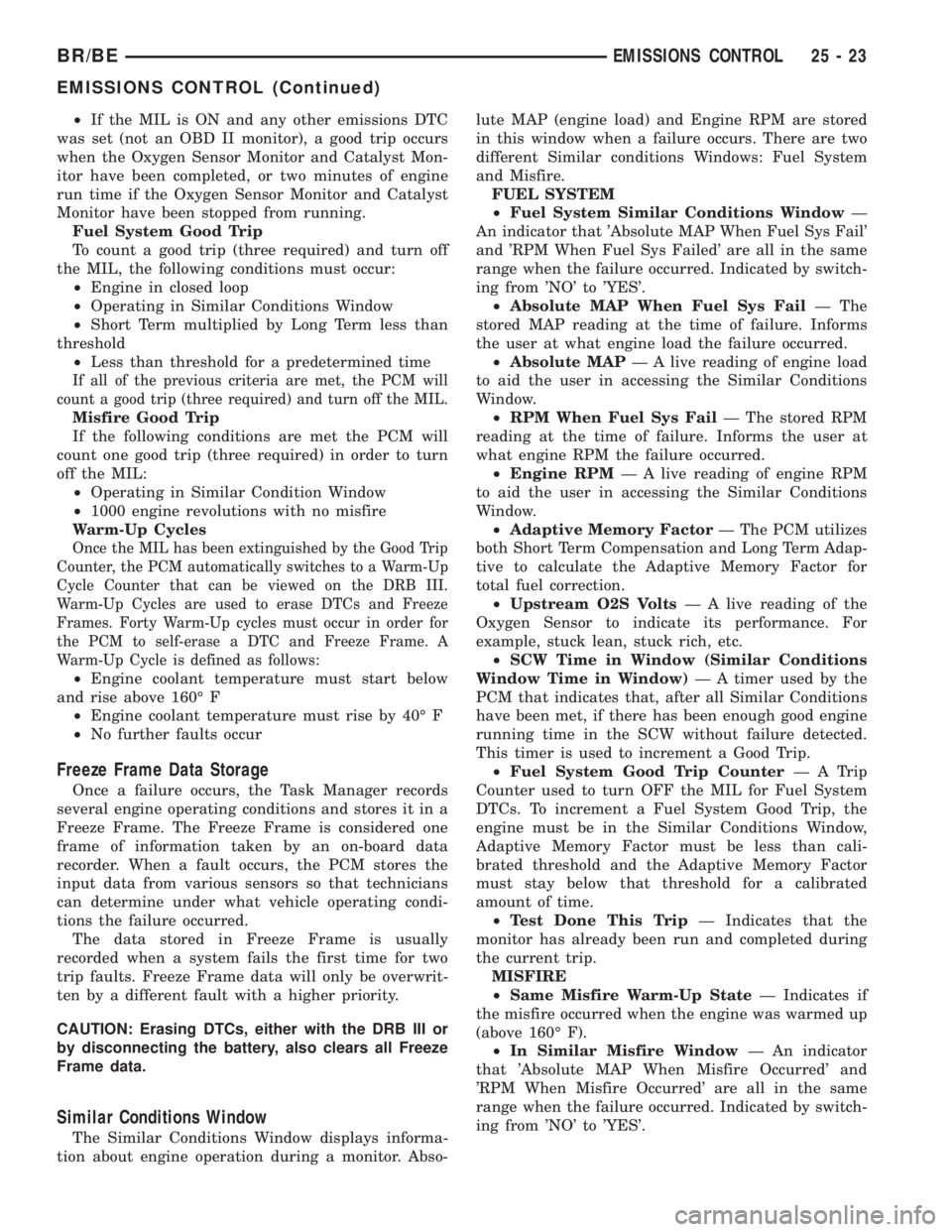
²If the MIL is ON and any other emissions DTC
was set (not an OBD II monitor), a good trip occurs
when the Oxygen Sensor Monitor and Catalyst Mon-
itor have been completed, or two minutes of engine
run time if the Oxygen Sensor Monitor and Catalyst
Monitor have been stopped from running.
Fuel System Good Trip
To count a good trip (three required) and turn off
the MIL, the following conditions must occur:
²Engine in closed loop
²Operating in Similar Conditions Window
²Short Term multiplied by Long Term less than
threshold
²Less than threshold for a predetermined time
If all of the previous criteria are met, the PCM will
count a good trip (three required) and turn off the MIL.
Misfire Good Trip
If the following conditions are met the PCM will
count one good trip (three required) in order to turn
off the MIL:
²Operating in Similar Condition Window
²1000 engine revolutions with no misfire
Warm-Up Cycles
Once the MIL has been extinguished by the Good Trip
Counter, the PCM automatically switches to a Warm-Up
Cycle Counter that can be viewed on the DRB III.
Warm-Up Cycles are used to erase DTCs and Freeze
Frames. Forty Warm-Up cycles must occur in order for
the PCM to self-erase a DTC and Freeze Frame. A
Warm-Up Cycle is defined as follows:
²Engine coolant temperature must start below
and rise above 160É F
²Engine coolant temperature must rise by 40É F
²No further faults occur
Freeze Frame Data Storage
Once a failure occurs, the Task Manager records
several engine operating conditions and stores it in a
Freeze Frame. The Freeze Frame is considered one
frame of information taken by an on-board data
recorder. When a fault occurs, the PCM stores the
input data from various sensors so that technicians
can determine under what vehicle operating condi-
tions the failure occurred.
The data stored in Freeze Frame is usually
recorded when a system fails the first time for two
trip faults. Freeze Frame data will only be overwrit-
ten by a different fault with a higher priority.
CAUTION: Erasing DTCs, either with the DRB III or
by disconnecting the battery, also clears all Freeze
Frame data.
Similar Conditions Window
The Similar Conditions Window displays informa-
tion about engine operation during a monitor. Abso-lute MAP (engine load) and Engine RPM are stored
in this window when a failure occurs. There are two
different Similar conditions Windows: Fuel System
and Misfire.
FUEL SYSTEM
²Fuel System Similar Conditions WindowÐ
An indicator that 'Absolute MAP When Fuel Sys Fail'
and 'RPM When Fuel Sys Failed' are all in the same
range when the failure occurred. Indicated by switch-
ing from 'NO' to 'YES'.
²Absolute MAP When Fuel Sys FailÐ The
stored MAP reading at the time of failure. Informs
the user at what engine load the failure occurred.
²Absolute MAPÐ A live reading of engine load
to aid the user in accessing the Similar Conditions
Window.
²RPM When Fuel Sys FailÐ The stored RPM
reading at the time of failure. Informs the user at
what engine RPM the failure occurred.
²Engine RPMÐ A live reading of engine RPM
to aid the user in accessing the Similar Conditions
Window.
²Adaptive Memory FactorÐ The PCM utilizes
both Short Term Compensation and Long Term Adap-
tive to calculate the Adaptive Memory Factor for
total fuel correction.
²Upstream O2S VoltsÐ A live reading of the
Oxygen Sensor to indicate its performance. For
example, stuck lean, stuck rich, etc.
²SCW Time in Window (Similar Conditions
Window Time in Window)Ð A timer used by the
PCM that indicates that, after all Similar Conditions
have been met, if there has been enough good engine
running time in the SCW without failure detected.
This timer is used to increment a Good Trip.
²Fuel System Good Trip CounterÐATrip
Counter used to turn OFF the MIL for Fuel System
DTCs. To increment a Fuel System Good Trip, the
engine must be in the Similar Conditions Window,
Adaptive Memory Factor must be less than cali-
brated threshold and the Adaptive Memory Factor
must stay below that threshold for a calibrated
amount of time.
²Test Done This TripÐ Indicates that the
monitor has already been run and completed during
the current trip.
MISFIRE
²Same Misfire Warm-Up StateÐ Indicates if
the misfire occurred when the engine was warmed up
(above 160É F).
²In Similar Misfire WindowÐ An indicator
that 'Absolute MAP When Misfire Occurred' and
'RPM When Misfire Occurred' are all in the same
range when the failure occurred. Indicated by switch-
ing from 'NO' to 'YES'.
BR/BEEMISSIONS CONTROL 25 - 23
EMISSIONS CONTROL (Continued)
Page 2203 of 2255
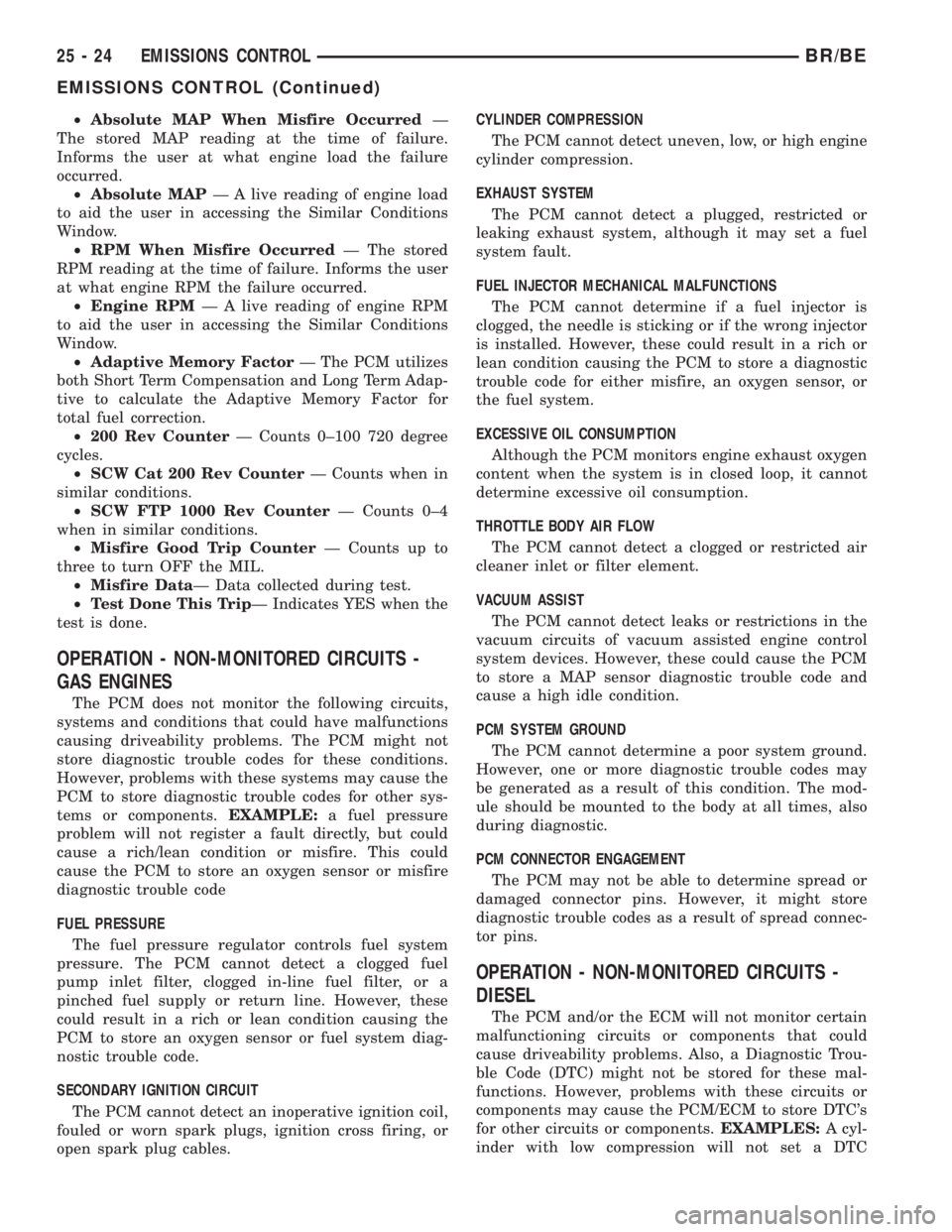
²Absolute MAP When Misfire OccurredÐ
The stored MAP reading at the time of failure.
Informs the user at what engine load the failure
occurred.
²Absolute MAPÐ A live reading of engine load
to aid the user in accessing the Similar Conditions
Window.
²RPM When Misfire OccurredÐ The stored
RPM reading at the time of failure. Informs the user
at what engine RPM the failure occurred.
²Engine RPMÐ A live reading of engine RPM
to aid the user in accessing the Similar Conditions
Window.
²Adaptive Memory FactorÐ The PCM utilizes
both Short Term Compensation and Long Term Adap-
tive to calculate the Adaptive Memory Factor for
total fuel correction.
²200 Rev CounterÐ Counts 0±100 720 degree
cycles.
²SCW Cat 200 Rev CounterÐ Counts when in
similar conditions.
²SCW FTP 1000 Rev CounterÐ Counts 0±4
when in similar conditions.
²Misfire Good Trip CounterÐ Counts up to
three to turn OFF the MIL.
²Misfire DataÐ Data collected during test.
²Test Done This TripÐ Indicates YES when the
test is done.
OPERATION - NON-MONITORED CIRCUITS -
GAS ENGINES
The PCM does not monitor the following circuits,
systems and conditions that could have malfunctions
causing driveability problems. The PCM might not
store diagnostic trouble codes for these conditions.
However, problems with these systems may cause the
PCM to store diagnostic trouble codes for other sys-
tems or components.EXAMPLE:a fuel pressure
problem will not register a fault directly, but could
cause a rich/lean condition or misfire. This could
cause the PCM to store an oxygen sensor or misfire
diagnostic trouble code
FUEL PRESSURE
The fuel pressure regulator controls fuel system
pressure. The PCM cannot detect a clogged fuel
pump inlet filter, clogged in-line fuel filter, or a
pinched fuel supply or return line. However, these
could result in a rich or lean condition causing the
PCM to store an oxygen sensor or fuel system diag-
nostic trouble code.
SECONDARY IGNITION CIRCUIT
The PCM cannot detect an inoperative ignition coil,
fouled or worn spark plugs, ignition cross firing, or
open spark plug cables.CYLINDER COMPRESSION
The PCM cannot detect uneven, low, or high engine
cylinder compression.
EXHAUST SYSTEM
The PCM cannot detect a plugged, restricted or
leaking exhaust system, although it may set a fuel
system fault.
FUEL INJECTOR MECHANICAL MALFUNCTIONS
The PCM cannot determine if a fuel injector is
clogged, the needle is sticking or if the wrong injector
is installed. However, these could result in a rich or
lean condition causing the PCM to store a diagnostic
trouble code for either misfire, an oxygen sensor, or
the fuel system.
EXCESSIVE OIL CONSUMPTION
Although the PCM monitors engine exhaust oxygen
content when the system is in closed loop, it cannot
determine excessive oil consumption.
THROTTLE BODY AIR FLOW
The PCM cannot detect a clogged or restricted air
cleaner inlet or filter element.
VACUUM ASSIST
The PCM cannot detect leaks or restrictions in the
vacuum circuits of vacuum assisted engine control
system devices. However, these could cause the PCM
to store a MAP sensor diagnostic trouble code and
cause a high idle condition.
PCM SYSTEM GROUND
The PCM cannot determine a poor system ground.
However, one or more diagnostic trouble codes may
be generated as a result of this condition. The mod-
ule should be mounted to the body at all times, also
during diagnostic.
PCM CONNECTOR ENGAGEMENT
The PCM may not be able to determine spread or
damaged connector pins. However, it might store
diagnostic trouble codes as a result of spread connec-
tor pins.
OPERATION - NON-MONITORED CIRCUITS -
DIESEL
The PCM and/or the ECM will not monitor certain
malfunctioning circuits or components that could
cause driveability problems. Also, a Diagnostic Trou-
ble Code (DTC) might not be stored for these mal-
functions. However, problems with these circuits or
components may cause the PCM/ECM to store DTC's
for other circuits or components.EXAMPLES:A cyl-
inder with low compression will not set a DTC
25 - 24 EMISSIONS CONTROLBR/BE
EMISSIONS CONTROL (Continued)
Page 2204 of 2255
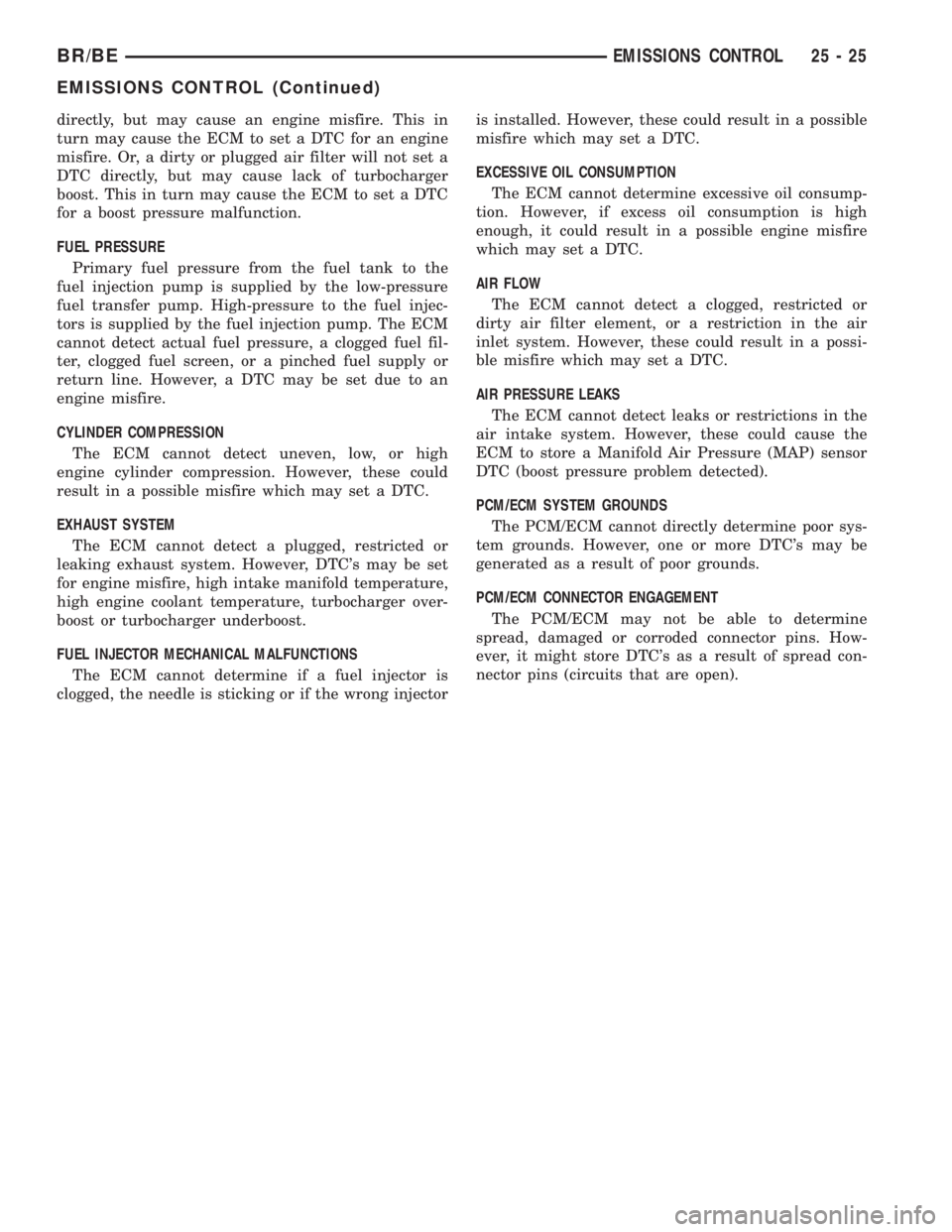
directly, but may cause an engine misfire. This in
turn may cause the ECM to set a DTC for an engine
misfire. Or, a dirty or plugged air filter will not set a
DTC directly, but may cause lack of turbocharger
boost. This in turn may cause the ECM to set a DTC
for a boost pressure malfunction.
FUEL PRESSURE
Primary fuel pressure from the fuel tank to the
fuel injection pump is supplied by the low-pressure
fuel transfer pump. High-pressure to the fuel injec-
tors is supplied by the fuel injection pump. The ECM
cannot detect actual fuel pressure, a clogged fuel fil-
ter, clogged fuel screen, or a pinched fuel supply or
return line. However, a DTC may be set due to an
engine misfire.
CYLINDER COMPRESSION
The ECM cannot detect uneven, low, or high
engine cylinder compression. However, these could
result in a possible misfire which may set a DTC.
EXHAUST SYSTEM
The ECM cannot detect a plugged, restricted or
leaking exhaust system. However, DTC's may be set
for engine misfire, high intake manifold temperature,
high engine coolant temperature, turbocharger over-
boost or turbocharger underboost.
FUEL INJECTOR MECHANICAL MALFUNCTIONS
The ECM cannot determine if a fuel injector is
clogged, the needle is sticking or if the wrong injectoris installed. However, these could result in a possible
misfire which may set a DTC.
EXCESSIVE OIL CONSUMPTION
The ECM cannot determine excessive oil consump-
tion. However, if excess oil consumption is high
enough, it could result in a possible engine misfire
which may set a DTC.
AIR FLOW
The ECM cannot detect a clogged, restricted or
dirty air filter element, or a restriction in the air
inlet system. However, these could result in a possi-
ble misfire which may set a DTC.
AIR PRESSURE LEAKS
The ECM cannot detect leaks or restrictions in the
air intake system. However, these could cause the
ECM to store a Manifold Air Pressure (MAP) sensor
DTC (boost pressure problem detected).
PCM/ECM SYSTEM GROUNDS
The PCM/ECM cannot directly determine poor sys-
tem grounds. However, one or more DTC's may be
generated as a result of poor grounds.
PCM/ECM CONNECTOR ENGAGEMENT
The PCM/ECM may not be able to determine
spread, damaged or corroded connector pins. How-
ever, it might store DTC's as a result of spread con-
nector pins (circuits that are open).
BR/BEEMISSIONS CONTROL 25 - 25
EMISSIONS CONTROL (Continued)
Page 2218 of 2255
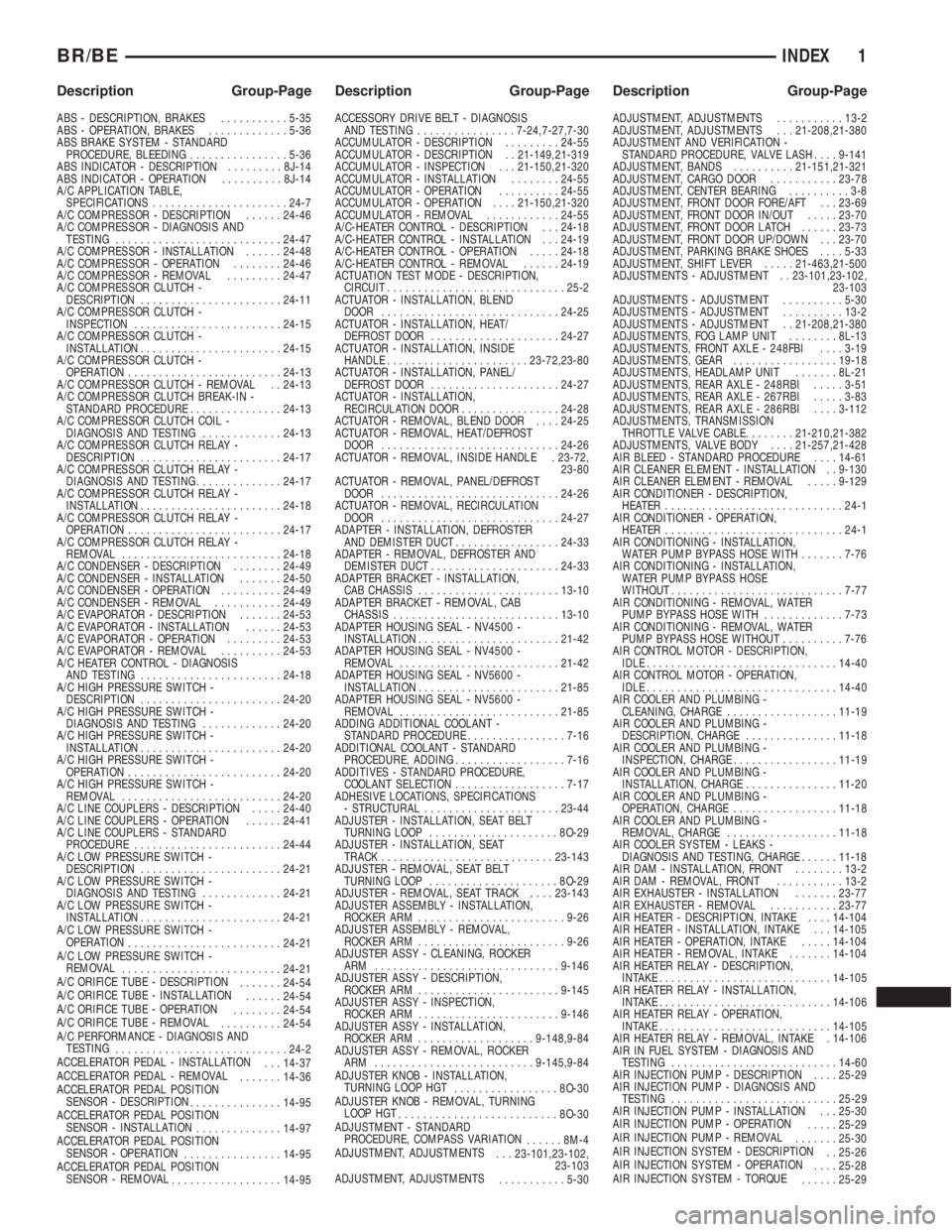
ABS - DESCRIPTION, BRAKES...........5-35
ABS - OPERATION, BRAKES.............5-36
ABS BRAKE SYSTEM - STANDARD
PROCEDURE, BLEEDING................5-36
ABS INDICATOR - DESCRIPTION.........8J-14
ABS INDICATOR - OPERATION..........8J-14
A/C APPLICATION TABLE,
SPECIFICATIONS......................24-7
A/C COMPRESSOR - DESCRIPTION......24-46
A/C COMPRESSOR - DIAGNOSIS AND
TESTING...........................24-47
A/C COMPRESSOR - INSTALLATION......24-48
A/C COMPRESSOR - OPERATION........24-46
A/C COMPRESSOR - REMOVAL.........24-47
A/C COMPRESSOR CLUTCH -
DESCRIPTION.......................24-11
A/C COMPRESSOR CLUTCH -
INSPECTION........................24-15
A/C COMPRESSOR CLUTCH -
INSTALLATION.......................24-15
A/C COMPRESSOR CLUTCH -
OPERATION.........................24-13
A/C COMPRESSOR CLUTCH - REMOVAL . . 24-13
A/C COMPRESSOR CLUTCH BREAK-IN -
STANDARD PROCEDURE...............24-13
A/C COMPRESSOR CLUTCH COIL -
DIAGNOSIS AND TESTING.............24-13
A/C COMPRESSOR CLUTCH RELAY -
DESCRIPTION.......................24-17
A/C COMPRESSOR CLUTCH RELAY -
DIAGNOSIS AND TESTING...............24-17
A/C COMPRESSOR CLUTCH RELAY -
INSTALLATION.......................24-18
A/C COMPRESSOR CLUTCH RELAY -
OPERATION.........................24-17
A/C COMPRESSOR CLUTCH RELAY -
REMOVAL..........................24-18
A/C CONDENSER - DESCRIPTION........24-49
A/C CONDENSER - INSTALLATION.......24-50
A/C CONDENSER - OPERATION..........24-49
A/C CONDENSER - REMOVAL...........24-49
A/C EVAPORATOR - DESCRIPTION.......24-53
A/C EVAPORATOR - INSTALLATION......24-53
A/C EVAPORATOR - OPERATION.........24-53
A/C EVAPORATOR - REMOVAL..........24-53
A/C HEATER CONTROL - DIAGNOSIS
AND TESTING.......................24-18
A/C HIGH PRESSURE SWITCH -
DESCRIPTION.......................24-20
A/C HIGH PRESSURE SWITCH -
DIAGNOSIS AND TESTING.............24-20
A/C HIGH PRESSURE SWITCH -
INSTALLATION.......................24-20
A/C HIGH PRESSURE SWITCH -
OPERATION.........................24-20
A/C HIGH PRESSURE SWITCH -
REMOVAL..........................24-20
A/C LINE COUPLERS - DESCRIPTION.....24-40
A/C LINE COUPLERS - OPERATION......24-41
A/C LINE COUPLERS - STANDARD
PROCEDURE........................24-44
A/C LOW PRESSURE SWITCH -
DESCRIPTION.......................24-21
A/C LOW PRESSURE SWITCH -
DIAGNOSIS AND TESTING.............24-21
A/C LOW PRESSURE SWITCH -
INSTALLATION.......................24-21
A/C LOW PRESSURE SWITCH -
OPERATION
.........................24-21
A/C LOW PRESSURE SWITCH -
REMOVAL
..........................24-21
A/C ORIFICE TUBE - DESCRIPTION
.......24-54
A/C ORIFICE TUBE - INSTALLATION
......24-54
A/C ORIFICE TUBE - OPERATION
........24-54
A/C ORIFICE TUBE - REMOVAL
..........24-54
A/C PERFORMANCE - DIAGNOSIS AND
TESTING
............................24-2
ACCELERATOR PEDAL - INSTALLATION
. . . 14-37
ACCELERATOR PEDAL - REMOVAL
.......14-36
ACCELERATOR PEDAL POSITION
SENSOR - DESCRIPTION
...............14-95
ACCELERATOR PEDAL POSITION
SENSOR - INSTALLATION
..............14-97
ACCELERATOR PEDAL POSITION
SENSOR - OPERATION
................14-95
ACCELERATOR PEDAL POSITION
SENSOR - REMOVAL
..................14-95ACCESSORY DRIVE BELT - DIAGNOSIS
AND TESTING................7-24,7-27,7-30
ACCUMULATOR - DESCRIPTION.........24-55
ACCUMULATOR - DESCRIPTION . . 21-149,21-319
ACCUMULATOR - INSPECTION . . . 21-150,21-320
ACCUMULATOR - INSTALLATION........24-55
ACCUMULATOR - OPERATION..........24-55
ACCUMULATOR - OPERATION....21-150,21-320
ACCUMULATOR - REMOVAL............24-55
A/C-HEATER CONTROL - DESCRIPTION . . . 24-18
A/C-HEATER CONTROL - INSTALLATION . . . 24-19
A/C-HEATER CONTROL - OPERATION.....24-18
A/C-HEATER CONTROL - REMOVAL......24-19
ACTUATION TEST MODE - DESCRIPTION,
CIRCUIT.............................25-2
ACTUATOR - INSTALLATION, BLEND
DOOR.............................24-25
ACTUATOR - INSTALLATION, HEAT/
DEFROST DOOR.....................24-27
ACTUATOR - INSTALLATION, INSIDE
HANDLE.......................23-72,23-80
ACTUATOR - INSTALLATION, PANEL/
DEFROST DOOR.....................24-27
ACTUATOR - INSTALLATION,
RECIRCULATION DOOR................24-28
ACTUATOR - REMOVAL, BLEND DOOR....24-25
ACTUATOR - REMOVAL, HEAT/DEFROST
DOOR.............................24-26
ACTUATOR - REMOVAL, INSIDE HANDLE . 23-72,
23-80
ACTUATOR - REMOVAL, PANEL/DEFROST
DOOR.............................24-26
ACTUATOR - REMOVAL, RECIRCULATION
DOOR.............................24-27
ADAPTER - INSTALLATION, DEFROSTER
AND DEMISTER DUCT.................24-33
ADAPTER - REMOVAL, DEFROSTER AND
DEMISTER DUCT.....................24-33
ADAPTER BRACKET - INSTALLATION,
CAB CHASSIS.......................13-10
ADAPTER BRACKET - REMOVAL, CAB
CHASSIS...........................13-10
ADAPTER HOUSING SEAL - NV4500 -
INSTALLATION.......................21-42
ADAPTER HOUSING SEAL - NV4500 -
REMOVAL..........................21-42
ADAPTER HOUSING SEAL - NV5600 -
INSTALLATION.......................21-85
ADAPTER HOUSING SEAL - NV5600 -
REMOVAL..........................21-85
ADDING ADDITIONAL COOLANT -
STANDARD PROCEDURE................7-16
ADDITIONAL COOLANT - STANDARD
PROCEDURE, ADDING..................7-16
ADDITIVES - STANDARD PROCEDURE,
COOLANT SELECTION..................7-17
ADHESIVE LOCATIONS, SPECIFICATIONS
- STRUCTURAL......................23-44
ADJUSTER - INSTALLATION, SEAT BELT
TURNING LOOP.....................8O-29
ADJUSTER - INSTALLATION, SEAT
TRACK............................23-143
ADJUSTER - REMOVAL, SEAT BELT
TURNING LOOP.....................8O-29
ADJUSTER - REMOVAL, SEAT TRACK....23-143
ADJUSTER ASSEMBLY - INSTALLATION,
ROCKER ARM........................9-26
ADJUSTER ASSEMBLY - REMOVAL,
ROCKER ARM........................9-26
ADJUSTER ASSY - CLEANING, ROCKER
ARM ..............................9-146
ADJUSTER ASSY - DESCRIPTION,
ROCKER ARM.......................9-145
ADJUSTER ASSY - INSPECTION,
ROCKER ARM.......................9-146
ADJUSTER ASSY - INSTALLATION,
ROCKER ARM...................9-148,9-84
ADJUSTER ASSY - REMOVAL, ROCKER
ARM ..........................9-145,9-84
ADJUSTER KNOB - INSTALLATION,
TURNING LOOP HGT
.................8O-30
ADJUSTER KNOB - REMOVAL, TURNING
LOOP HGT
..........................8O-30
ADJUSTMENT - STANDARD
PROCEDURE, COMPASS VARIATION
......8M-4
ADJUSTMENT, ADJUSTMENTS
. . . 23-101,23-102,
23-103
ADJUSTMENT, ADJUSTMENTS
...........5-30ADJUSTMENT, ADJUSTMENTS...........13-2
ADJUSTMENT, ADJUSTMENTS . . . 21-208,21-380
ADJUSTMENT AND VERIFICATION -
STANDARD PROCEDURE, VALVE LASH....9-141
ADJUSTMENT, BANDS..........21-151,21-321
ADJUSTMENT, CARGO DOOR...........23-78
ADJUSTMENT, CENTER BEARING..........3-8
ADJUSTMENT, FRONT DOOR FORE/AFT . . . 23-69
ADJUSTMENT, FRONT DOOR IN/OUT.....23-70
ADJUSTMENT, FRONT DOOR LATCH......23-73
ADJUSTMENT, FRONT DOOR UP/DOWN . . . 23-70
ADJUSTMENT, PARKING BRAKE SHOES....5-33
ADJUSTMENT, SHIFT LEVER.....21-463,21-500
ADJUSTMENTS - ADJUSTMENT . . 23-101,23-102,
23-103
ADJUSTMENTS - ADJUSTMENT..........5-30
ADJUSTMENTS - ADJUSTMENT..........13-2
ADJUSTMENTS - ADJUSTMENT . . 21-208,21-380
ADJUSTMENTS, FOG LAMP UNIT........8L-13
ADJUSTMENTS, FRONT AXLE - 248FBI....3-19
ADJUSTMENTS, GEAR.................19-18
ADJUSTMENTS, HEADLAMP UNIT.......8L-21
ADJUSTMENTS, REAR AXLE - 248RBI.....3-51
ADJUSTMENTS, REAR AXLE - 267RBI.....3-83
ADJUSTMENTS, REAR AXLE - 286RBI....3-112
ADJUSTMENTS, TRANSMISSION
THROTTLE VALVE CABLE.........21-210,21-382
ADJUSTMENTS, VALVE BODY....21-257,21-428
AIR BLEED - STANDARD PROCEDURE....14-61
AIR CLEANER ELEMENT - INSTALLATION . . 9-130
AIR CLEANER ELEMENT - REMOVAL.....9-129
AIR CONDITIONER - DESCRIPTION,
HEATER .............................24-1
AIR CONDITIONER - OPERATION,
HEATER .............................24-1
AIR CONDITIONING - INSTALLATION,
WATER PUMP BYPASS HOSE WITH.......7-76
AIR CONDITIONING - INSTALLATION,
WATER PUMP BYPASS HOSE
WITHOUT............................7-77
AIR CONDITIONING - REMOVAL, WATER
PUMP BYPASS HOSE WITH.............7-73
AIR CONDITIONING - REMOVAL, WATER
PUMP BYPASS HOSE WITHOUT..........7-76
AIR CONTROL MOTOR - DESCRIPTION,
IDLE...............................14-40
AIR CONTROL MOTOR - OPERATION,
IDLE...............................14-40
AIR COOLER AND PLUMBING -
CLEANING, CHARGE..................11-19
AIR COOLER AND PLUMBING -
DESCRIPTION, CHARGE...............11-18
AIR COOLER AND PLUMBING -
INSPECTION, CHARGE.................11-19
AIR COOLER AND PLUMBING -
INSTALLATION, CHARGE...............11-20
AIR COOLER AND PLUMBING -
OPERATION, CHARGE.................11-18
AIR COOLER AND PLUMBING -
REMOVAL, CHARGE..................11-18
AIR COOLER SYSTEM - LEAKS -
DIAGNOSIS AND TESTING, CHARGE......11-18
AIR DAM - INSTALLATION, FRONT........13-2
AIR DAM - REMOVAL, FRONT...........13-2
AIR EXHAUSTER - INSTALLATION.......23-77
AIR EXHAUSTER - REMOVAL...........23-77
AIR HEATER - DESCRIPTION, INTAKE....14-104
AIR HEATER - INSTALLATION, INTAKE . . . 14-105
AIR HEATER - OPERATION, INTAKE.....14-104
AIR HEATER - REMOVAL, INTAKE.......14-104
AIR HEATER RELAY - DESCRIPTION,
INTAKE............................14-105
AIR HEATER RELAY - INSTALLATION,
INTAKE............................14-106
AIR HEATER RELAY - OPERATION,
INTAKE............................14-105
AIR HEATER RELAY - REMOVAL, INTAKE . 14-106
AIR IN FUEL SYSTEM - DIAGNOSIS AND
TESTING...........................14-60
AIR INJECTION PUMP - DESCRIPTION....25-29
AIR INJECTION PUMP - DIAGNOSIS AND
TESTING...........................25-29
AIR INJECTION PUMP - INSTALLATION . . . 25-30
AIR INJECTION PUMP - OPERATION
.....25-29
AIR INJECTION PUMP - REMOVAL
.......25-30
AIR INJECTION SYSTEM - DESCRIPTION
. . 25-26
AIR INJECTION SYSTEM - OPERATION
....25-28
AIR INJECTION SYSTEM - TORQUE
......25-29
BR/BEINDEX 1
Description Group-Page Description Group-Page Description Group-Page
Page 2219 of 2255
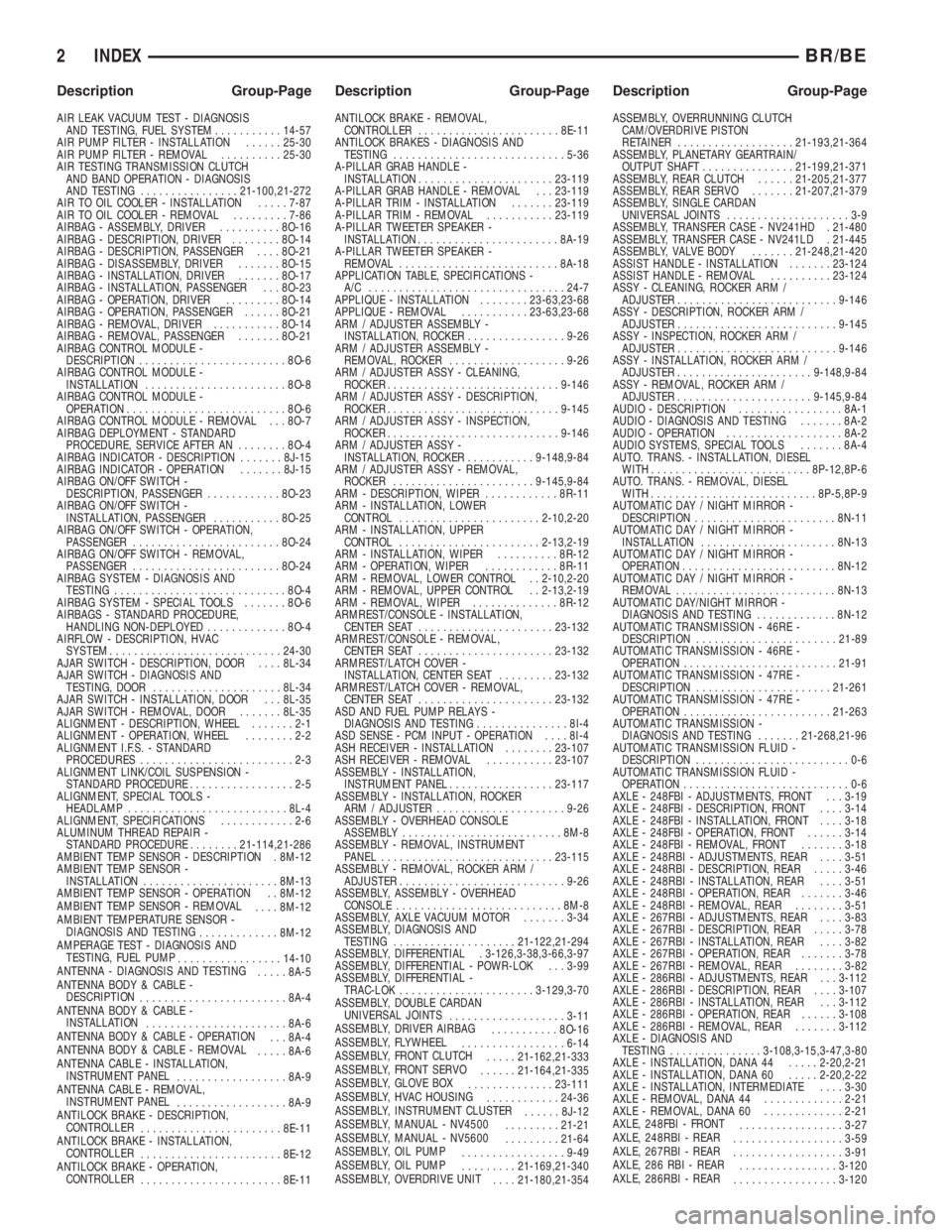
AIR LEAK VACUUM TEST - DIAGNOSIS
AND TESTING, FUEL SYSTEM...........14-57
AIR PUMP FILTER - INSTALLATION......25-30
AIR PUMP FILTER - REMOVAL..........25-30
AIR TESTING TRANSMISSION CLUTCH
AND BAND OPERATION - DIAGNOSIS
AND TESTING................21-100,21-272
AIR TO OIL COOLER - INSTALLATION.....7-87
AIR TO OIL COOLER - REMOVAL.........7-86
AIRBAG - ASSEMBLY, DRIVER..........8O-16
AIRBAG - DESCRIPTION, DRIVER........8O-14
AIRBAG - DESCRIPTION, PASSENGER....8O-21
AIRBAG - DISASSEMBLY, DRIVER.......8O-15
AIRBAG - INSTALLATION, DRIVER.......8O-17
AIRBAG - INSTALLATION, PASSENGER . . . 8O-23
AIRBAG - OPERATION, DRIVER.........8O-14
AIRBAG - OPERATION, PASSENGER......8O-21
AIRBAG - REMOVAL, DRIVER...........8O-14
AIRBAG - REMOVAL, PASSENGER.......8O-21
AIRBAG CONTROL MODULE -
DESCRIPTION........................8O-6
AIRBAG CONTROL MODULE -
INSTALLATION.......................8O-8
AIRBAG CONTROL MODULE -
OPERATION..........................8O-6
AIRBAG CONTROL MODULE - REMOVAL . . . 8O-7
AIRBAG DEPLOYMENT - STANDARD
PROCEDURE, SERVICE AFTER AN........8O-4
AIRBAG INDICATOR - DESCRIPTION.......8J-15
AIRBAG INDICATOR - OPERATION.......8J-15
AIRBAG ON/OFF SWITCH -
DESCRIPTION, PASSENGER............8O-23
AIRBAG ON/OFF SWITCH -
INSTALLATION, PASSENGER...........8O-25
AIRBAG ON/OFF SWITCH - OPERATION,
PASSENGER........................8O-24
AIRBAG ON/OFF SWITCH - REMOVAL,
PASSENGER........................8O-24
AIRBAG SYSTEM - DIAGNOSIS AND
TESTING............................8O-4
AIRBAG SYSTEM - SPECIAL TOOLS.......8O-6
AIRBAGS - STANDARD PROCEDURE,
HANDLING NON-DEPLOYED.............8O-4
AIRFLOW - DESCRIPTION, HVAC
SYSTEM............................24-30
AJAR SWITCH - DESCRIPTION, DOOR....8L-34
AJAR SWITCH - DIAGNOSIS AND
TESTING, DOOR.....................8L-34
AJAR SWITCH - INSTALLATION, DOOR . . . 8L-35
AJAR SWITCH - REMOVAL, DOOR.......8L-35
ALIGNMENT - DESCRIPTION, WHEEL.......2-1
ALIGNMENT - OPERATION, WHEEL........2-2
ALIGNMENT I.F.S. - STANDARD
PROCEDURES.........................2-3
ALIGNMENT LINK/COIL SUSPENSION -
STANDARD PROCEDURE.................2-5
ALIGNMENT, SPECIAL TOOLS -
HEADLAMP..........................8L-4
ALIGNMENT, SPECIFICATIONS............2-6
ALUMINUM THREAD REPAIR -
STANDARD PROCEDURE........21-114,21-286
AMBIENT TEMP SENSOR - DESCRIPTION . 8M-12
AMBIENT TEMP SENSOR -
INSTALLATION......................8M-13
AMBIENT TEMP SENSOR - OPERATION . . 8M-12
AMBIENT TEMP SENSOR - REMOVAL
....8M-12
AMBIENT TEMPERATURE SENSOR -
DIAGNOSIS AND TESTING
.............8M-12
AMPERAGE TEST - DIAGNOSIS AND
TESTING, FUEL PUMP
.................14-10
ANTENNA - DIAGNOSIS AND TESTING
.....8A-5
ANTENNA BODY & CABLE -
DESCRIPTION
........................8A-4
ANTENNA BODY & CABLE -
INSTALLATION
.......................8A-6
ANTENNA BODY & CABLE - OPERATION
. . . 8A-4
ANTENNA BODY & CABLE - REMOVAL
.....8A-6
ANTENNA CABLE - INSTALLATION,
INSTRUMENT PANEL
..................8A-9
ANTENNA CABLE - REMOVAL,
INSTRUMENT PANEL
..................8A-9
ANTILOCK BRAKE - DESCRIPTION,
CONTROLLER
.......................8E-11
ANTILOCK BRAKE - INSTALLATION,
CONTROLLER
.......................8E-12
ANTILOCK BRAKE - OPERATION,
CONTROLLER
.......................8E-11ANTILOCK BRAKE - REMOVAL,
CONTROLLER.......................8E-11
ANTILOCK BRAKES - DIAGNOSIS AND
TESTING............................5-36
A-PILLAR GRAB HANDLE -
INSTALLATION......................23-119
A-PILLAR GRAB HANDLE - REMOVAL . . . 23-119
A-PILLAR TRIM - INSTALLATION.......23-119
A-PILLAR TRIM - REMOVAL...........23-119
A-PILLAR TWEETER SPEAKER -
INSTALLATION.......................8A-19
A-PILLAR TWEETER SPEAKER -
REMOVAL..........................8A-18
APPLICATION TABLE, SPECIFICATIONS -
A/C ................................24-7
APPLIQUE - INSTALLATION........23-63,23-68
APPLIQUE - REMOVAL...........23-63,23-68
ARM / ADJUSTER ASSEMBLY -
INSTALLATION, ROCKER................9-26
ARM / ADJUSTER ASSEMBLY -
REMOVAL, ROCKER...................9-26
ARM / ADJUSTER ASSY - CLEANING,
ROCKER............................9-146
ARM / ADJUSTER ASSY - DESCRIPTION,
ROCKER............................9-145
ARM / ADJUSTER ASSY - INSPECTION,
ROCKER............................9-146
ARM / ADJUSTER ASSY -
INSTALLATION, ROCKER...........9-148,9-84
ARM / ADJUSTER ASSY - REMOVAL,
ROCKER.......................9-145,9-84
ARM - DESCRIPTION, WIPER............8R-11
ARM - INSTALLATION, LOWER
CONTROL.......................2-10,2-20
ARM - INSTALLATION, UPPER
CONTROL.......................2-13,2-19
ARM - INSTALLATION, WIPER..........8R-12
ARM - OPERATION, WIPER............8R-11
ARM - REMOVAL, LOWER CONTROL . . 2-10,2-20
ARM - REMOVAL, UPPER CONTROL . . 2-13,2-19
ARM - REMOVAL, WIPER..............8R-12
ARMREST/CONSOLE - INSTALLATION,
CENTER SEAT......................23-132
ARMREST/CONSOLE - REMOVAL,
CENTER SEAT......................23-132
ARMREST/LATCH COVER -
INSTALLATION, CENTER SEAT.........23-132
ARMREST/LATCH COVER - REMOVAL,
CENTER SEAT......................23-132
ASD AND FUEL PUMP RELAYS -
DIAGNOSIS AND TESTING...............8I-4
ASD SENSE - PCM INPUT - OPERATION....8I-4
ASH RECEIVER - INSTALLATION........23-107
ASH RECEIVER - REMOVAL...........23-107
ASSEMBLY - INSTALLATION,
INSTRUMENT PANEL.................23-117
ASSEMBLY - INSTALLATION, ROCKER
ARM / ADJUSTER.....................9-26
ASSEMBLY - OVERHEAD CONSOLE
ASSEMBLY..........................8M-8
ASSEMBLY - REMOVAL, INSTRUMENT
PANEL............................23-115
ASSEMBLY - REMOVAL, ROCKER ARM /
ADJUSTER...........................9-26
ASSEMBLY, ASSEMBLY - OVERHEAD
CONSOLE...........................8M-8
ASSEMBLY, AXLE VACUUM MOTOR.......3-34
ASSEMBLY, DIAGNOSIS AND
TESTING....................21-122,21-294
ASSEMBLY, DIFFERENTIAL . 3-126,3-38,3-66,3-97
ASSEMBLY, DIFFERENTIAL - POWR-LOK . . . 3-99
ASSEMBLY, DIFFERENTIAL -
TRAC-LOK......................3-129,3-70
ASSEMBLY, DOUBLE CARDAN
UNIVERSAL JOINTS
...................3-11
ASSEMBLY, DRIVER AIRBAG
...........8O-16
ASSEMBLY, FLYWHEEL
.................6-14
ASSEMBLY, FRONT CLUTCH
.....21-162,21-333
ASSEMBLY, FRONT SERVO
......21-164,21-335
ASSEMBLY, GLOVE BOX
..............23-111
ASSEMBLY, HVAC HOUSING
............24-36
ASSEMBLY, INSTRUMENT CLUSTER
......8J-12
ASSEMBLY, MANUAL - NV4500
.........21-21
ASSEMBLY, MANUAL - NV5600
.........21-64
ASSEMBLY, OIL PUMP
.................9-49
ASSEMBLY, OIL PUMP
.........21-169,21-340
ASSEMBLY, OVERDRIVE UNIT
....21-180,21-354ASSEMBLY, OVERRUNNING CLUTCH
CAM/OVERDRIVE PISTON
RETAINER...................21-193,21-364
ASSEMBLY, PLANETARY GEARTRAIN/
OUTPUT SHAFT...............21-199,21-371
ASSEMBLY, REAR CLUTCH......21-205,21-377
ASSEMBLY, REAR SERVO.......21-207,21-379
ASSEMBLY, SINGLE CARDAN
UNIVERSAL JOINTS....................3-9
ASSEMBLY, TRANSFER CASE - NV241HD . 21-480
ASSEMBLY, TRANSFER CASE - NV241LD . 21-445
ASSEMBLY, VALVE BODY.......21-248,21-420
ASSIST HANDLE - INSTALLATION.......23-124
ASSIST HANDLE - REMOVAL..........23-124
ASSY - CLEANING, ROCKER ARM /
ADJUSTER..........................9-146
ASSY - DESCRIPTION, ROCKER ARM /
ADJUSTER..........................9-145
ASSY - INSPECTION, ROCKER ARM /
ADJUSTER..........................9-146
ASSY - INSTALLATION, ROCKER ARM /
ADJUSTER......................9-148,9-84
ASSY - REMOVAL, ROCKER ARM /
ADJUSTER......................9-145,9-84
AUDIO - DESCRIPTION.................8A-1
AUDIO - DIAGNOSIS AND TESTING.......8A-2
AUDIO - OPERATION...................8A-2
AUDIO SYSTEMS, SPECIAL TOOLS.......8A-4
AUTO. TRANS. - INSTALLATION, DIESEL
WITH..........................8P-12,8P-6
AUTO. TRANS. - REMOVAL, DIESEL
WITH...........................8P-5,8P-9
AUTOMATIC DAY / NIGHT MIRROR -
DESCRIPTION.......................8N-11
AUTOMATIC DAY / NIGHT MIRROR -
INSTALLATION......................8N-13
AUTOMATIC DAY / NIGHT MIRROR -
OPERATION.........................8N-12
AUTOMATIC DAY / NIGHT MIRROR -
REMOVAL..........................8N-13
AUTOMATIC DAY/NIGHT MIRROR -
DIAGNOSIS AND TESTING.............8N-12
AUTOMATIC TRANSMISSION - 46RE -
DESCRIPTION.......................21-89
AUTOMATIC TRANSMISSION - 46RE -
OPERATION.........................21-91
AUTOMATIC TRANSMISSION - 47RE -
DESCRIPTION......................21-261
AUTOMATIC TRANSMISSION - 47RE -
OPERATION........................21-263
AUTOMATIC TRANSMISSION -
DIAGNOSIS AND TESTING.......21-268,21-96
AUTOMATIC TRANSMISSION FLUID -
DESCRIPTION.........................0-6
AUTOMATIC TRANSMISSION FLUID -
OPERATION...........................0-6
AXLE - 248FBI - ADJUSTMENTS, FRONT . . . 3-19
AXLE - 248FBI - DESCRIPTION, FRONT....3-14
AXLE - 248FBI - INSTALLATION, FRONT....3-18
AXLE - 248FBI - OPERATION, FRONT......3-14
AXLE - 248FBI - REMOVAL, FRONT.......3-18
AXLE - 248RBI - ADJUSTMENTS, REAR....3-51
AXLE - 248RBI - DESCRIPTION, REAR.....3-46
AXLE - 248RBI - INSTALLATION, REAR....3-51
AXLE - 248RBI - OPERATION, REAR.......3-46
AXLE - 248RBI - REMOVAL, REAR........3-51
AXLE - 267RBI - ADJUSTMENTS, REAR....3-83
AXLE - 267RBI - DESCRIPTION, REAR.....3-78
AXLE - 267RBI - INSTALLATION, REAR....3-82
AXLE - 267RBI - OPERATION, REAR.......3-78
AXLE - 267RBI - REMOVAL, REAR........3-82
AXLE - 286RBI - ADJUSTMENTS, REAR . . . 3-112
AXLE - 286RBI - DESCRIPTION, REAR....3-107
AXLE - 286RBI - INSTALLATION, REAR . . . 3-112
AXLE - 286RBI - OPERATION, REAR......3-108
AXLE - 286RBI - REMOVAL, REAR.......3-112
AXLE - DIAGNOSIS AND
TESTING...............3-108,3-15,3-47,3-80
AXLE - INSTALLATION, DANA 44.....2-20,2-21
AXLE - INSTALLATION, DANA 60.....2-20,2-22
AXLE - INSTALLATION, INTERMEDIATE....3-30
AXLE - REMOVAL, DANA 44.............2-21
AXLE - REMOVAL, DANA 60.............2-21
AXLE, 248FBI - FRONT
.................3-27
AXLE, 248RBI - REAR
..................3-59
AXLE, 267RBI - REAR
..................3-91
AXLE, 286 RBI - REAR
................3-120
AXLE, 286RBI - REAR
.................3-120
2 INDEXBR/BE
Description Group-Page Description Group-Page Description Group-Page
Page 2220 of 2255
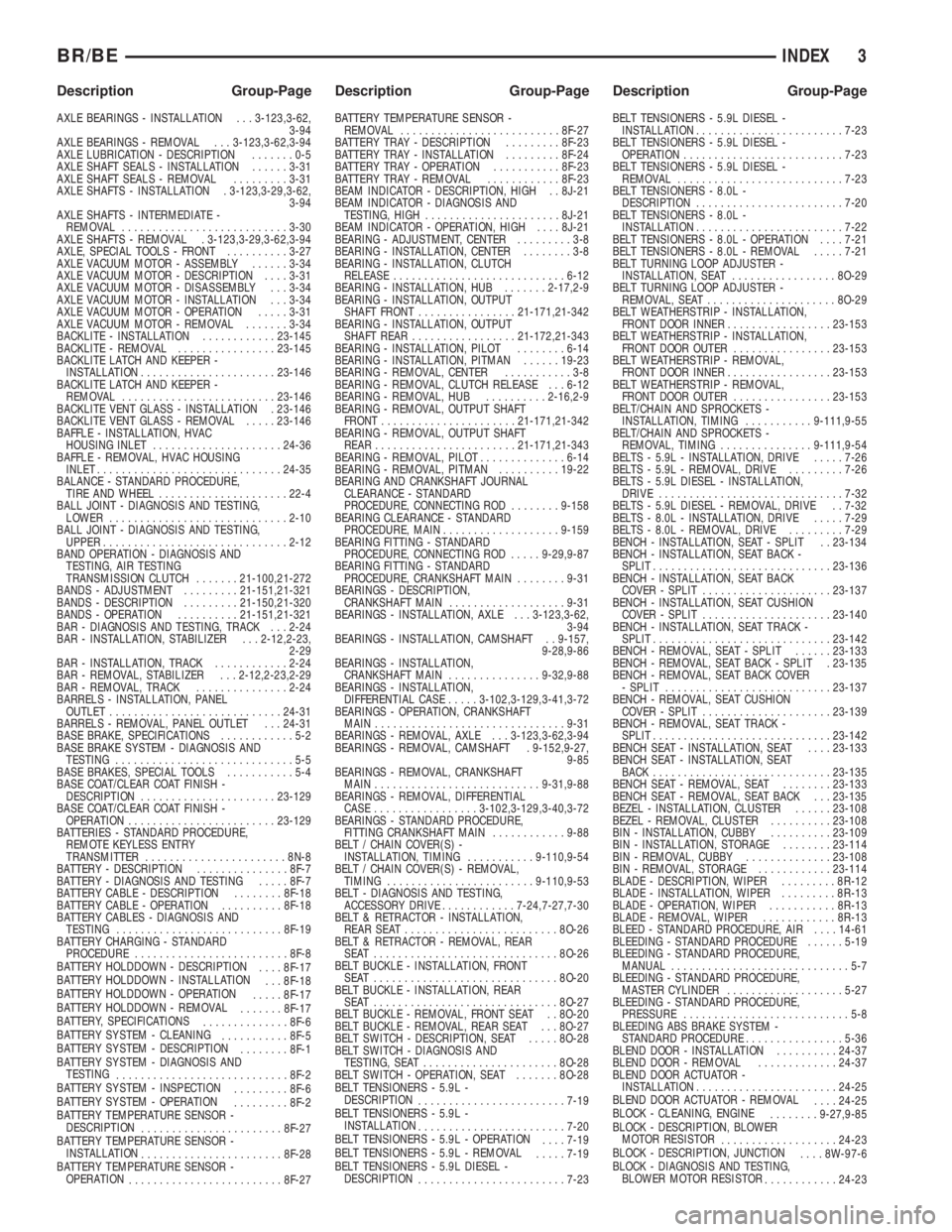
AXLE BEARINGS - INSTALLATION . . . 3-123,3-62,
3-94
AXLE BEARINGS - REMOVAL . . . 3-123,3-62,3-94
AXLE LUBRICATION - DESCRIPTION.......0-5
AXLE SHAFT SEALS - INSTALLATION......3-31
AXLE SHAFT SEALS - REMOVAL.........3-31
AXLE SHAFTS - INSTALLATION . 3-123,3-29,3-62,
3-94
AXLE SHAFTS - INTERMEDIATE -
REMOVAL...........................3-30
AXLE SHAFTS - REMOVAL . 3-123,3-29,3-62,3-94
AXLE, SPECIAL TOOLS - FRONT..........3-27
AXLE VACUUM MOTOR - ASSEMBLY......3-34
AXLE VACUUM MOTOR - DESCRIPTION....3-31
AXLE VACUUM MOTOR - DISASSEMBLY . . . 3-34
AXLE VACUUM MOTOR - INSTALLATION . . . 3-34
AXLE VACUUM MOTOR - OPERATION.....3-31
AXLE VACUUM MOTOR - REMOVAL.......3-34
BACKLITE - INSTALLATION............23-145
BACKLITE - REMOVAL................23-145
BACKLITE LATCH AND KEEPER -
INSTALLATION......................23-146
BACKLITE LATCH AND KEEPER -
REMOVAL.........................23-146
BACKLITE VENT GLASS - INSTALLATION . 23-146
BACKLITE VENT GLASS - REMOVAL.....23-146
BAFFLE - INSTALLATION, HVAC
HOUSING INLET.....................24-36
BAFFLE - REMOVAL, HVAC HOUSING
INLET..............................24-35
BALANCE - STANDARD PROCEDURE,
TIRE AND WHEEL.....................22-4
BALL JOINT - DIAGNOSIS AND TESTING,
LOWER.............................2-10
BALL JOINT - DIAGNOSIS AND TESTING,
UPPER..............................2-12
BAND OPERATION - DIAGNOSIS AND
TESTING, AIR TESTING
TRANSMISSION CLUTCH.......21-100,21-272
BANDS - ADJUSTMENT.........21-151,21-321
BANDS - DESCRIPTION.........21-150,21-320
BANDS - OPERATION..........21-151,21-321
BAR - DIAGNOSIS AND TESTING, TRACK . . . 2-24
BAR - INSTALLATION, STABILIZER . . . 2-12,2-23,
2-29
BAR - INSTALLATION, TRACK............2-24
BAR - REMOVAL, STABILIZER . . . 2-12,2-23,2-29
BAR - REMOVAL, TRACK...............2-24
BARRELS - INSTALLATION, PANEL
OUTLET............................24-31
BARRELS - REMOVAL, PANEL OUTLET . . . 24-31
BASE BRAKE, SPECIFICATIONS............5-2
BASE BRAKE SYSTEM - DIAGNOSIS AND
TESTING.............................5-5
BASE BRAKES, SPECIAL TOOLS...........5-4
BASE COAT/CLEAR COAT FINISH -
DESCRIPTION......................23-129
BASE COAT/CLEAR COAT FINISH -
OPERATION........................23-129
BATTERIES - STANDARD PROCEDURE,
REMOTE KEYLESS ENTRY
TRANSMITTER.......................8N-8
BATTERY - DESCRIPTION...............8F-7
BATTERY - DIAGNOSIS AND TESTING.....8F-7
BATTERY CABLE - DESCRIPTION........8F-18
BATTERY CABLE - OPERATION..........8F-18
BATTERY CABLES - DIAGNOSIS AND
TESTING...........................8F-19
BATTERY CHARGING - STANDARD
PROCEDURE.........................8F-8
BATTERY HOLDDOWN - DESCRIPTION
....8F-17
BATTERY HOLDDOWN - INSTALLATION
. . . 8F-18
BATTERY HOLDDOWN - OPERATION
.....8F-17
BATTERY HOLDDOWN - REMOVAL
.......8F-17
BATTERY, SPECIFICATIONS
..............8F-6
BATTERY SYSTEM - CLEANING
...........8F-5
BATTERY SYSTEM - DESCRIPTION
........8F-1
BATTERY SYSTEM - DIAGNOSIS AND
TESTING
............................8F-2
BATTERY SYSTEM - INSPECTION
.........8F-6
BATTERY SYSTEM - OPERATION
.........8F-2
BATTERY TEMPERATURE SENSOR -
DESCRIPTION
.......................8F-27
BATTERY TEMPERATURE SENSOR -
INSTALLATION
.......................8F-28
BATTERY TEMPERATURE SENSOR -
OPERATION
.........................8F-27BATTERY TEMPERATURE SENSOR -
REMOVAL..........................8F-27
BATTERY TRAY - DESCRIPTION.........8F-23
BATTERY TRAY - INSTALLATION.........8F-24
BATTERY TRAY - OPERATION...........8F-23
BATTERY TRAY - REMOVAL............8F-23
BEAM INDICATOR - DESCRIPTION, HIGH . . 8J-21
BEAM INDICATOR - DIAGNOSIS AND
TESTING, HIGH......................8J-21
BEAM INDICATOR - OPERATION, HIGH....8J-21
BEARING - ADJUSTMENT, CENTER.........3-8
BEARING - INSTALLATION, CENTER........3-8
BEARING - INSTALLATION, CLUTCH
RELEASE............................6-12
BEARING - INSTALLATION, HUB.......2-17,2-9
BEARING - INSTALLATION, OUTPUT
SHAFT FRONT................21-171,21-342
BEARING - INSTALLATION, OUTPUT
SHAFT REAR.................21-172,21-343
BEARING - INSTALLATION, PILOT........6-14
BEARING - INSTALLATION, PITMAN......19-23
BEARING - REMOVAL, CENTER...........3-8
BEARING - REMOVAL, CLUTCH RELEASE . . . 6-12
BEARING - REMOVAL, HUB..........2-16,2-9
BEARING - REMOVAL, OUTPUT SHAFT
FRONT......................21-171,21-342
BEARING - REMOVAL, OUTPUT SHAFT
REAR.......................21-171,21-343
BEARING - REMOVAL, PILOT..............6-14
BEARING - REMOVAL, PITMAN..........19-22
BEARING AND CRANKSHAFT JOURNAL
CLEARANCE - STANDARD
PROCEDURE, CONNECTING ROD........9-158
BEARING CLEARANCE - STANDARD
PROCEDURE, MAIN...................9-159
BEARING FITTING - STANDARD
PROCEDURE, CONNECTING ROD.....9-29,9-87
BEARING FITTING - STANDARD
PROCEDURE, CRANKSHAFT MAIN........9-31
BEARINGS - DESCRIPTION,
CRANKSHAFT MAIN...................9-31
BEARINGS - INSTALLATION, AXLE . . . 3-123,3-62,
3-94
BEARINGS - INSTALLATION, CAMSHAFT . . 9-157,
9-28,9-86
BEARINGS - INSTALLATION,
CRANKSHAFT MAIN...............9-32,9-88
BEARINGS - INSTALLATION,
DIFFERENTIAL CASE.....3-102,3-129,3-41,3-72
BEARINGS - OPERATION, CRANKSHAFT
MAIN...............................9-31
BEARINGS - REMOVAL, AXLE . . . 3-123,3-62,3-94
BEARINGS - REMOVAL, CAMSHAFT . 9-152,9-27,
9-85
BEARINGS - REMOVAL, CRANKSHAFT
MAIN...........................9-31,9-88
BEARINGS - REMOVAL, DIFFERENTIAL
CASE.................3-102,3-129,3-40,3-72
BEARINGS - STANDARD PROCEDURE,
FITTING CRANKSHAFT MAIN............9-88
BELT / CHAIN COVER(S) -
INSTALLATION, TIMING...........9-110,9-54
BELT / CHAIN COVER(S) - REMOVAL,
TIMING........................9-110,9-53
BELT - DIAGNOSIS AND TESTING,
ACCESSORY DRIVE............7-24,7-27,7-30
BELT & RETRACTOR - INSTALLATION,
REAR SEAT.........................8O-26
BELT & RETRACTOR - REMOVAL, REAR
SEAT ..............................8O-26
BELT BUCKLE - INSTALLATION, FRONT
SEAT ..............................8O-20
BELT BUCKLE - INSTALLATION, REAR
SEAT ..............................8O-27
BELT BUCKLE - REMOVAL, FRONT SEAT . . 8O-20
BELT BUCKLE - REMOVAL, REAR SEAT . . . 8O-27
BELT SWITCH - DESCRIPTION, SEAT.....8O-28
BELT SWITCH - DIAGNOSIS AND
TESTING, SEAT......................8O-28
BELT SWITCH - OPERATION, SEAT.......8O-28
BELT TENSIONERS - 5.9L -
DESCRIPTION
........................7-19
BELT TENSIONERS - 5.9L -
INSTALLATION
........................7-20
BELT TENSIONERS - 5.9L - OPERATION
....7-19
BELT TENSIONERS - 5.9L - REMOVAL
.....7-19
BELT TENSIONERS - 5.9L DIESEL -
DESCRIPTION
........................7-23BELT TENSIONERS - 5.9L DIESEL -
INSTALLATION........................7-23
BELT TENSIONERS - 5.9L DIESEL -
OPERATION..........................7-23
BELT TENSIONERS - 5.9L DIESEL -
REMOVAL...........................7-23
BELT TENSIONERS - 8.0L -
DESCRIPTION........................7-20
BELT TENSIONERS - 8.0L -
INSTALLATION........................7-22
BELT TENSIONERS - 8.0L - OPERATION....7-21
BELT TENSIONERS - 8.0L - REMOVAL.....7-21
BELT TURNING LOOP ADJUSTER -
INSTALLATION, SEAT.................8O-29
BELT TURNING LOOP ADJUSTER -
REMOVAL, SEAT.....................8O-29
BELT WEATHERSTRIP - INSTALLATION,
FRONT DOOR INNER.................23-153
BELT WEATHERSTRIP - INSTALLATION,
FRONT DOOR OUTER................23-153
BELT WEATHERSTRIP - REMOVAL,
FRONT DOOR INNER.................23-153
BELT WEATHERSTRIP - REMOVAL,
FRONT DOOR OUTER................23-153
BELT/CHAIN AND SPROCKETS -
INSTALLATION, TIMING...........9-111,9-55
BELT/CHAIN AND SPROCKETS -
REMOVAL, TIMING...............9-111,9-54
BELTS - 5.9L - INSTALLATION, DRIVE.....7-26
BELTS - 5.9L - REMOVAL, DRIVE.........7-26
BELTS - 5.9L DIESEL - INSTALLATION,
DRIVE..............................7-32
BELTS - 5.9L DIESEL - REMOVAL, DRIVE . . 7-32
BELTS - 8.0L - INSTALLATION, DRIVE.....7-29
BELTS - 8.0L - REMOVAL, DRIVE.........7-29
BENCH - INSTALLATION, SEAT - SPLIT . . 23-134
BENCH - INSTALLATION, SEAT BACK -
SPLIT.............................23-136
BENCH - INSTALLATION, SEAT BACK
COVER - SPLIT.....................23-137
BENCH - INSTALLATION, SEAT CUSHION
COVER - SPLIT.....................23-140
BENCH - INSTALLATION, SEAT TRACK -
SPLIT.............................23-142
BENCH - REMOVAL, SEAT - SPLIT......23-133
BENCH - REMOVAL, SEAT BACK - SPLIT . 23-135
BENCH - REMOVAL, SEAT BACK COVER
- SPLIT...........................23-137
BENCH - REMOVAL, SEAT CUSHION
COVER - SPLIT.....................23-139
BENCH - REMOVAL, SEAT TRACK -
SPLIT.............................23-142
BENCH SEAT - INSTALLATION, SEAT....23-133
BENCH SEAT - INSTALLATION, SEAT
BACK.............................23-135
BENCH SEAT - REMOVAL, SEAT........23-133
BENCH SEAT - REMOVAL, SEAT BACK . . . 23-135
BEZEL - INSTALLATION, CLUSTER......23-108
BEZEL - REMOVAL, CLUSTER..........23-108
BIN - INSTALLATION, CUBBY..........23-109
BIN - INSTALLATION, STORAGE........23-114
BIN - REMOVAL, CUBBY..............23-108
BIN - REMOVAL, STORAGE............23-114
BLADE - DESCRIPTION, WIPER.........8R-12
BLADE - INSTALLATION, WIPER.........8R-13
BLADE - OPERATION, WIPER...........8R-13
BLADE - REMOVAL, WIPER............8R-13
BLEED - STANDARD PROCEDURE, AIR....14-61
BLEEDING - STANDARD PROCEDURE......5-19
BLEEDING - STANDARD PROCEDURE,
MANUAL.............................5-7
BLEEDING - STANDARD PROCEDURE,
MASTER CYLINDER...................5-27
BLEEDING - STANDARD PROCEDURE,
PRESSURE...........................5-8
BLEEDING ABS BRAKE SYSTEM -
STANDARD PROCEDURE................5-36
BLEND DOOR - INSTALLATION..........24-37
BLEND DOOR - REMOVAL.............24-37
BLEND DOOR ACTUATOR -
INSTALLATION.......................24-25
BLEND DOOR ACTUATOR - REMOVAL
....24-25
BLOCK - CLEANING, ENGINE
........9-27,9-85
BLOCK - DESCRIPTION, BLOWER
MOTOR RESISTOR
...................24-23
BLOCK - DESCRIPTION, JUNCTION
....8W-97-6
BLOCK - DIAGNOSIS AND TESTING,
BLOWER MOTOR RESISTOR
............24-23
BR/BEINDEX 3
Description Group-Page Description Group-Page Description Group-Page
Page 2225 of 2255
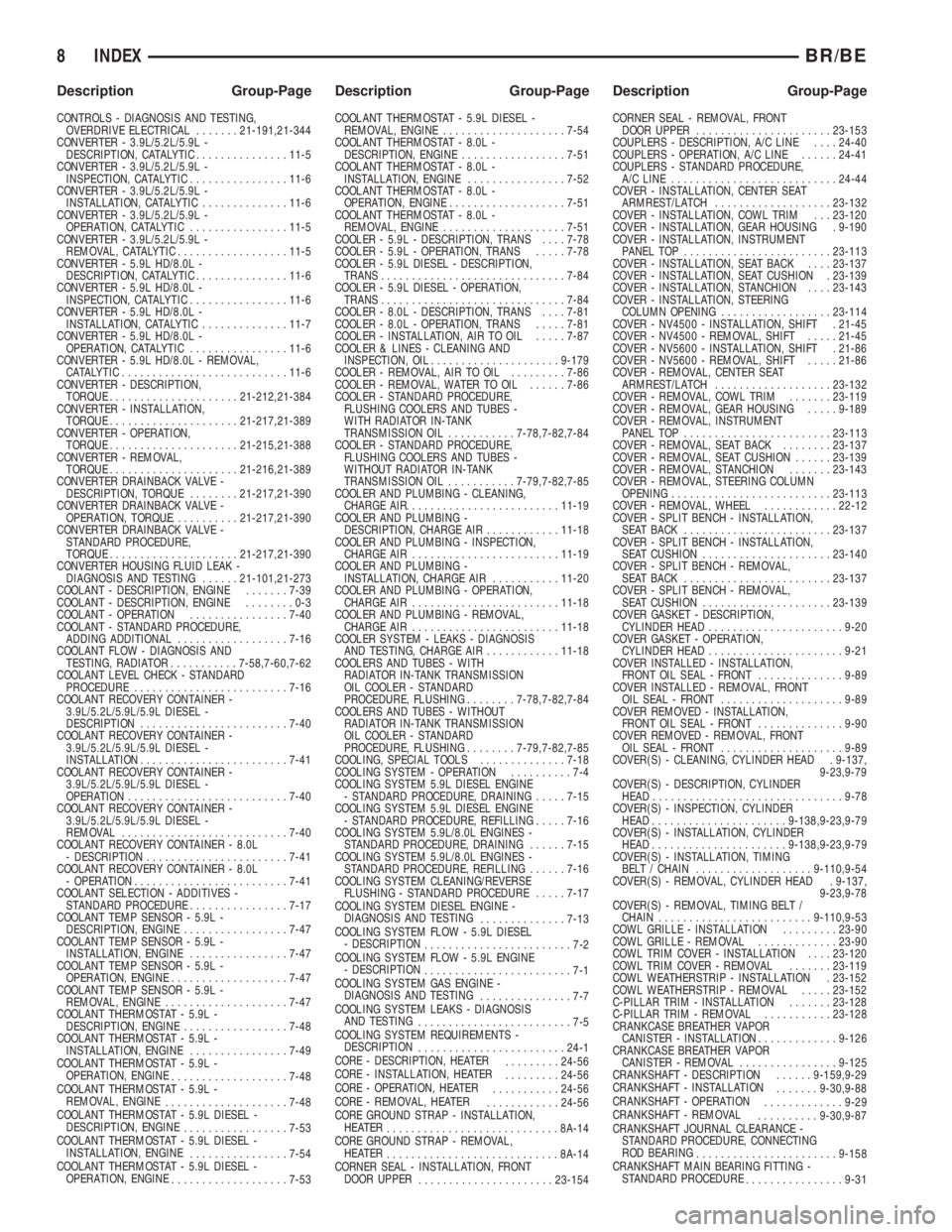
CONTROLS - DIAGNOSIS AND TESTING,
OVERDRIVE ELECTRICAL.......21-191,21-344
CONVERTER - 3.9L/5.2L/5.9L -
DESCRIPTION, CATALYTIC...............11-5
CONVERTER - 3.9L/5.2L/5.9L -
INSPECTION, CATALYTIC................11-6
CONVERTER - 3.9L/5.2L/5.9L -
INSTALLATION, CATALYTIC..............11-6
CONVERTER - 3.9L/5.2L/5.9L -
OPERATION, CATALYTIC................11-5
CONVERTER - 3.9L/5.2L/5.9L -
REMOVAL, CATALYTIC..................11-5
CONVERTER - 5.9L HD/8.0L -
DESCRIPTION, CATALYTIC...............11-6
CONVERTER - 5.9L HD/8.0L -
INSPECTION, CATALYTIC................11-6
CONVERTER - 5.9L HD/8.0L -
INSTALLATION, CATALYTIC..............11-7
CONVERTER - 5.9L HD/8.0L -
OPERATION, CATALYTIC................11-6
CONVERTER - 5.9L HD/8.0L - REMOVAL,
CATALYTIC...........................11-6
CONVERTER - DESCRIPTION,
TORQUE.....................21-212,21-384
CONVERTER - INSTALLATION,
TORQUE.....................21-217,21-389
CONVERTER - OPERATION,
TORQUE.....................21-215,21-388
CONVERTER - REMOVAL,
TORQUE.....................21-216,21-389
CONVERTER DRAINBACK VALVE -
DESCRIPTION, TORQUE........21-217,21-390
CONVERTER DRAINBACK VALVE -
OPERATION, TORQUE............21-217,21-390
CONVERTER DRAINBACK VALVE -
STANDARD PROCEDURE,
TORQUE.....................21-217,21-390
CONVERTER HOUSING FLUID LEAK -
DIAGNOSIS AND TESTING......21-101,21-273
COOLANT - DESCRIPTION, ENGINE.......7-39
COOLANT - DESCRIPTION, ENGINE........0-3
COOLANT - OPERATION................7-40
COOLANT - STANDARD PROCEDURE,
ADDING ADDITIONAL..................7-16
COOLANT FLOW - DIAGNOSIS AND
TESTING, RADIATOR...........7-58,7-60,7-62
COOLANT LEVEL CHECK - STANDARD
PROCEDURE.........................7-16
COOLANT RECOVERY CONTAINER -
3.9L/5.2L/5.9L/5.9L DIESEL -
DESCRIPTION........................7-40
COOLANT RECOVERY CONTAINER -
3.9L/5.2L/5.9L/5.9L DIESEL -
INSTALLATION........................7-41
COOLANT RECOVERY CONTAINER -
3.9L/5.2L/5.9L/5.9L DIESEL -
OPERATION..........................7-40
COOLANT RECOVERY CONTAINER -
3.9L/5.2L/5.9L/5.9L DIESEL -
REMOVAL...........................7-40
COOLANT RECOVERY CONTAINER - 8.0L
- DESCRIPTION.......................7-41
COOLANT RECOVERY CONTAINER - 8.0L
- OPERATION.........................7-41
COOLANT SELECTION - ADDITIVES -
STANDARD PROCEDURE................7-17
COOLANT TEMP SENSOR - 5.9L -
DESCRIPTION, ENGINE.................7-47
COOLANT TEMP SENSOR - 5.9L -
INSTALLATION, ENGINE................7-47
COOLANT TEMP SENSOR - 5.9L -
OPERATION, ENGINE...................7-47
COOLANT TEMP SENSOR - 5.9L -
REMOVAL, ENGINE....................7-47
COOLANT THERMOSTAT - 5.9L -
DESCRIPTION, ENGINE.................7-48
COOLANT THERMOSTAT - 5.9L -
INSTALLATION, ENGINE................7-49
COOLANT THERMOSTAT - 5.9L -
OPERATION, ENGINE
...................7-48
COOLANT THERMOSTAT - 5.9L -
REMOVAL, ENGINE
....................7-48
COOLANT THERMOSTAT - 5.9L DIESEL -
DESCRIPTION, ENGINE
.................7-53
COOLANT THERMOSTAT - 5.9L DIESEL -
INSTALLATION, ENGINE
................7-54
COOLANT THERMOSTAT - 5.9L DIESEL -
OPERATION, ENGINE
...................7-53COOLANT THERMOSTAT - 5.9L DIESEL -
REMOVAL, ENGINE....................7-54
COOLANT THERMOSTAT - 8.0L -
DESCRIPTION, ENGINE.................7-51
COOLANT THERMOSTAT - 8.0L -
INSTALLATION, ENGINE................7-52
COOLANT THERMOSTAT - 8.0L -
OPERATION, ENGINE...................7-51
COOLANT THERMOSTAT - 8.0L -
REMOVAL, ENGINE....................7-51
COOLER - 5.9L - DESCRIPTION, TRANS....7-78
COOLER - 5.9L - OPERATION, TRANS.....7-78
COOLER - 5.9L DIESEL - DESCRIPTION,
TRANS..............................7-84
COOLER - 5.9L DIESEL - OPERATION,
TRANS..............................7-84
COOLER - 8.0L - DESCRIPTION, TRANS....7-81
COOLER - 8.0L - OPERATION, TRANS.....7-81
COOLER - INSTALLATION, AIR TO OIL.....7-87
COOLER & LINES - CLEANING AND
INSPECTION, OIL.....................9-179
COOLER - REMOVAL, AIR TO OIL.........7-86
COOLER - REMOVAL, WATER TO OIL......7-86
COOLER - STANDARD PROCEDURE,
FLUSHING COOLERS AND TUBES -
WITH RADIATOR IN-TANK
TRANSMISSION OIL...........7-78,7-82,7-84
COOLER - STANDARD PROCEDURE,
FLUSHING COOLERS AND TUBES -
WITHOUT RADIATOR IN-TANK
TRANSMISSION OIL...........7-79,7-82,7-85
COOLER AND PLUMBING - CLEANING,
CHARGE AIR..........................11-19
COOLER AND PLUMBING -
DESCRIPTION, CHARGE AIR............11-18
COOLER AND PLUMBING - INSPECTION,
CHARGE AIR........................11-19
COOLER AND PLUMBING -
INSTALLATION, CHARGE AIR...........11-20
COOLER AND PLUMBING - OPERATION,
CHARGE AIR........................11-18
COOLER AND PLUMBING - REMOVAL,
CHARGE AIR........................11-18
COOLER SYSTEM - LEAKS - DIAGNOSIS
AND TESTING, CHARGE AIR............11-18
COOLERS AND TUBES - WITH
RADIATOR IN-TANK TRANSMISSION
OIL COOLER - STANDARD
PROCEDURE, FLUSHING........7-78,7-82,7-84
COOLERS AND TUBES - WITHOUT
RADIATOR IN-TANK TRANSMISSION
OIL COOLER - STANDARD
PROCEDURE, FLUSHING........7-79,7-82,7-85
COOLING, SPECIAL TOOLS..............7-18
COOLING SYSTEM - OPERATION..........7-4
COOLING SYSTEM 5.9L DIESEL ENGINE
- STANDARD PROCEDURE, DRAINING.....7-15
COOLING SYSTEM 5.9L DIESEL ENGINE
- STANDARD PROCEDURE, REFILLING.....7-16
COOLING SYSTEM 5.9L/8.0L ENGINES -
STANDARD PROCEDURE, DRAINING......7-15
COOLING SYSTEM 5.9L/8.0L ENGINES -
STANDARD PROCEDURE, REFILLING......7-16
COOLING SYSTEM CLEANING/REVERSE
FLUSHING - STANDARD PROCEDURE.....7-17
COOLING SYSTEM DIESEL ENGINE -
DIAGNOSIS AND TESTING
..............7-13
COOLING SYSTEM FLOW - 5.9L DIESEL
- DESCRIPTION
........................7-2
COOLING SYSTEM FLOW - 5.9L ENGINE
- DESCRIPTION
........................7-1
COOLING SYSTEM GAS ENGINE -
DIAGNOSIS AND TESTING
...............7-7
COOLING SYSTEM LEAKS - DIAGNOSIS
AND TESTING
.........................7-5
COOLING SYSTEM REQUIREMENTS -
DESCRIPTION
........................24-1
CORE - DESCRIPTION, HEATER
.........24-56
CORE - INSTALLATION, HEATER
.........24-56
CORE - OPERATION, HEATER
...........24-56
CORE - REMOVAL, HEATER
............24-56
CORE GROUND STRAP - INSTALLATION,
HEATER
............................8A-14
CORE GROUND STRAP - REMOVAL,
HEATER
............................8A-14
CORNER SEAL - INSTALLATION, FRONT
DOOR UPPER
......................23-154CORNER SEAL - REMOVAL, FRONT
DOOR UPPER......................23-153
COUPLERS - DESCRIPTION, A/C LINE....24-40
COUPLERS - OPERATION, A/C LINE......24-41
COUPLERS - STANDARD PROCEDURE,
A/C LINE...........................24-44
COVER - INSTALLATION, CENTER SEAT
ARMREST/LATCH...................23-132
COVER - INSTALLATION, COWL TRIM . . . 23-120
COVER - INSTALLATION, GEAR HOUSING . 9-190
COVER - INSTALLATION, INSTRUMENT
PANEL TOP........................23-113
COVER - INSTALLATION, SEAT BACK....23-137
COVER - INSTALLATION, SEAT CUSHION . 23-139
COVER - INSTALLATION, STANCHION....23-143
COVER - INSTALLATION, STEERING
COLUMN OPENING..................23-114
COVER - NV4500 - INSTALLATION, SHIFT . 21-45
COVER - NV4500 - REMOVAL, SHIFT.....21-45
COVER - NV5600 - INSTALLATION, SHIFT . 21-86
COVER - NV5600 - REMOVAL, SHIFT.....21-86
COVER - REMOVAL, CENTER SEAT
ARMREST/LATCH...................23-132
COVER - REMOVAL, COWL TRIM.......23-119
COVER - REMOVAL, GEAR HOUSING.....9-189
COVER - REMOVAL, INSTRUMENT
PANEL TOP........................23-113
COVER - REMOVAL, SEAT BACK........23-137
COVER - REMOVAL, SEAT CUSHION......23-139
COVER - REMOVAL, STANCHION.......23-143
COVER - REMOVAL, STEERING COLUMN
OPENING..........................23-113
COVER - REMOVAL, WHEEL............22-12
COVER - SPLIT BENCH - INSTALLATION,
SEAT BACK........................23-137
COVER - SPLIT BENCH - INSTALLATION,
SEAT CUSHION.....................23-140
COVER - SPLIT BENCH - REMOVAL,
SEAT BACK........................23-137
COVER - SPLIT BENCH - REMOVAL,
SEAT CUSHION.....................23-139
COVER GASKET - DESCRIPTION,
CYLINDER HEAD......................9-20
COVER GASKET - OPERATION,
CYLINDER HEAD......................9-21
COVER INSTALLED - INSTALLATION,
FRONT OIL SEAL - FRONT..............9-89
COVER INSTALLED - REMOVAL, FRONT
OIL SEAL - FRONT....................9-89
COVER REMOVED - INSTALLATION,
FRONT OIL SEAL - FRONT..............9-90
COVER REMOVED - REMOVAL, FRONT
OIL SEAL - FRONT....................9-89
COVER(S) - CLEANING, CYLINDER HEAD . 9-137,
9-23,9-79
COVER(S) - DESCRIPTION, CYLINDER
HEAD...............................9-78
COVER(S) - INSPECTION, CYLINDER
HEAD......................9-138,9-23,9-79
COVER(S) - INSTALLATION, CYLINDER
HEAD......................9-138,9-23,9-79
COVER(S) - INSTALLATION, TIMING
BELT / CHAIN...................9-110,9-54
COVER(S) - REMOVAL, CYLINDER HEAD . 9-137,
9-23,9-78
COVER(S) - REMOVAL, TIMING BELT /
CHAIN.........................9-110,9-53
COWL GRILLE - INSTALLATION.........23-90
COWL GRILLE - REMOVAL.............23-90
COWL TRIM COVER - INSTALLATION....23-120
COWL TRIM COVER - REMOVAL.......23-119
COWL WEATHERSTRIP - INSTALLATION . 23-152
COWL WEATHERSTRIP - REMOVAL.....23-152
C-PILLAR TRIM - INSTALLATION.......23-128
C-PILLAR TRIM - REMOVAL...........23-128
CRANKCASE BREATHER VAPOR
CANISTER - INSTALLATION.............9-126
CRANKCASE BREATHER VAPOR
CANISTER - REMOVAL................9-125
CRANKSHAFT - DESCRIPTION......9-159,9-29
CRANKSHAFT - INSTALLATION
.......9-30,9-88
CRANKSHAFT - OPERATION
.............9-29
CRANKSHAFT - REMOVAL
..........9-30,9-87
CRANKSHAFT JOURNAL CLEARANCE -
STANDARD PROCEDURE, CONNECTING
ROD BEARING
.......................9-158
CRANKSHAFT MAIN BEARING FITTING -
STANDARD PROCEDURE
................9-31
8 INDEXBR/BE
Description Group-Page Description Group-Page Description Group-Page
Page 2228 of 2255
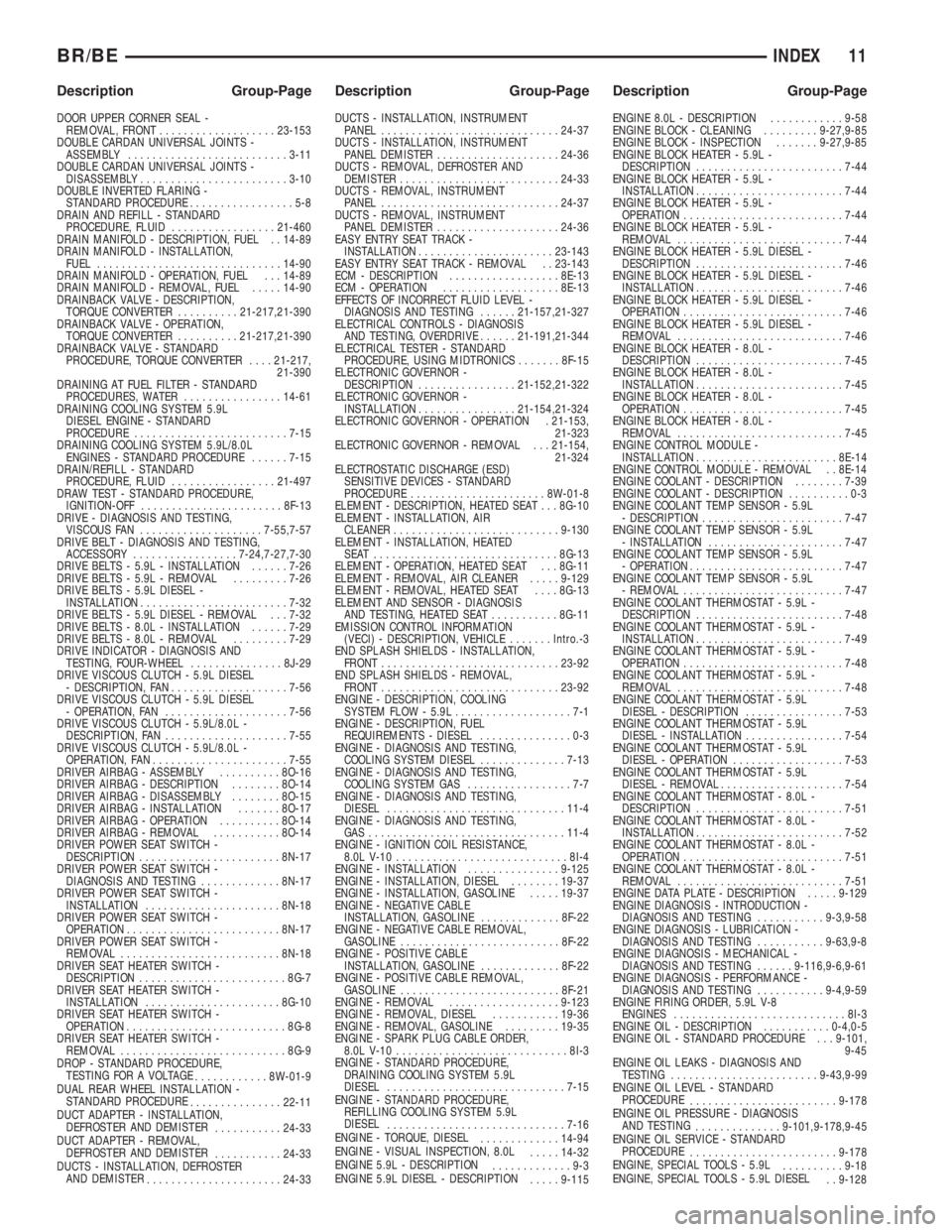
DOOR UPPER CORNER SEAL -
REMOVAL, FRONT...................23-153
DOUBLE CARDAN UNIVERSAL JOINTS -
ASSEMBLY..........................3-11
DOUBLE CARDAN UNIVERSAL JOINTS -
DISASSEMBLY........................3-10
DOUBLE INVERTED FLARING -
STANDARD PROCEDURE.................5-8
DRAIN AND REFILL - STANDARD
PROCEDURE, FLUID.................21-460
DRAIN MANIFOLD - DESCRIPTION, FUEL . . 14-89
DRAIN MANIFOLD - INSTALLATION,
FUEL..............................14-90
DRAIN MANIFOLD - OPERATION, FUEL . . . 14-89
DRAIN MANIFOLD - REMOVAL, FUEL.....14-90
DRAINBACK VALVE - DESCRIPTION,
TORQUE CONVERTER..........21-217,21-390
DRAINBACK VALVE - OPERATION,
TORQUE CONVERTER..........21-217,21-390
DRAINBACK VALVE - STANDARD
PROCEDURE, TORQUE CONVERTER....21-217,
21-390
DRAINING AT FUEL FILTER - STANDARD
PROCEDURES, WATER................14-61
DRAINING COOLING SYSTEM 5.9L
DIESEL ENGINE - STANDARD
PROCEDURE.........................7-15
DRAINING COOLING SYSTEM 5.9L/8.0L
ENGINES - STANDARD PROCEDURE......7-15
DRAIN/REFILL - STANDARD
PROCEDURE, FLUID.................21-497
DRAW TEST - STANDARD PROCEDURE,
IGNITION-OFF.......................8F-13
DRIVE - DIAGNOSIS AND TESTING,
VISCOUS FAN....................7-55,7-57
DRIVE BELT - DIAGNOSIS AND TESTING,
ACCESSORY.................7-24,7-27,7-30
DRIVE BELTS - 5.9L - INSTALLATION......7-26
DRIVE BELTS - 5.9L - REMOVAL.........7-26
DRIVE BELTS - 5.9L DIESEL -
INSTALLATION........................7-32
DRIVE BELTS - 5.9L DIESEL - REMOVAL . . . 7-32
DRIVE BELTS - 8.0L - INSTALLATION......7-29
DRIVE BELTS - 8.0L - REMOVAL.........7-29
DRIVE INDICATOR - DIAGNOSIS AND
TESTING, FOUR-WHEEL...............8J-29
DRIVE VISCOUS CLUTCH - 5.9L DIESEL
- DESCRIPTION, FAN...................7-56
DRIVE VISCOUS CLUTCH - 5.9L DIESEL
- OPERATION, FAN....................7-56
DRIVE VISCOUS CLUTCH - 5.9L/8.0L -
DESCRIPTION, FAN....................7-55
DRIVE VISCOUS CLUTCH - 5.9L/8.0L -
OPERATION, FAN......................7-55
DRIVER AIRBAG - ASSEMBLY..........8O-16
DRIVER AIRBAG - DESCRIPTION........8O-14
DRIVER AIRBAG - DISASSEMBLY........8O-15
DRIVER AIRBAG - INSTALLATION.......8O-17
DRIVER AIRBAG - OPERATION..........8O-14
DRIVER AIRBAG - REMOVAL...........8O-14
DRIVER POWER SEAT SWITCH -
DESCRIPTION.......................8N-17
DRIVER POWER SEAT SWITCH -
DIAGNOSIS AND TESTING.............8N-17
DRIVER POWER SEAT SWITCH -
INSTALLATION......................8N-18
DRIVER POWER SEAT SWITCH -
OPERATION.........................8N-17
DRIVER POWER SEAT SWITCH -
REMOVAL..........................8N-18
DRIVER SEAT HEATER SWITCH -
DESCRIPTION........................8G-7
DRIVER SEAT HEATER SWITCH -
INSTALLATION......................8G-10
DRIVER SEAT HEATER SWITCH -
OPERATION..........................8G-8
DRIVER SEAT HEATER SWITCH -
REMOVAL...........................8G-9
DROP - STANDARD PROCEDURE,
TESTING FOR A VOLTAGE
............8W-01-9
DUAL REAR WHEEL INSTALLATION -
STANDARD PROCEDURE
...............22-11
DUCT ADAPTER - INSTALLATION,
DEFROSTER AND DEMISTER
...........24-33
DUCT ADAPTER - REMOVAL,
DEFROSTER AND DEMISTER
...........24-33
DUCTS - INSTALLATION, DEFROSTER
AND DEMISTER
......................24-33DUCTS - INSTALLATION, INSTRUMENT
PANEL.............................24-37
DUCTS - INSTALLATION, INSTRUMENT
PANEL DEMISTER....................24-36
DUCTS - REMOVAL, DEFROSTER AND
DEMISTER..........................24-33
DUCTS - REMOVAL, INSTRUMENT
PANEL.............................24-37
DUCTS - REMOVAL, INSTRUMENT
PANEL DEMISTER....................24-36
EASY ENTRY SEAT TRACK -
INSTALLATION......................23-143
EASY ENTRY SEAT TRACK - REMOVAL . . 23-143
ECM - DESCRIPTION..................8E-13
ECM - OPERATION...................8E-13
EFFECTS OF INCORRECT FLUID LEVEL -
DIAGNOSIS AND TESTING......21-157,21-327
ELECTRICAL CONTROLS - DIAGNOSIS
AND TESTING, OVERDRIVE......21-191,21-344
ELECTRICAL TESTER - STANDARD
PROCEDURE, USING MIDTRONICS.......8F-15
ELECTRONIC GOVERNOR -
DESCRIPTION................21-152,21-322
ELECTRONIC GOVERNOR -
INSTALLATION................21-154,21-324
ELECTRONIC GOVERNOR - OPERATION . 21-153,
21-323
ELECTRONIC GOVERNOR - REMOVAL . . . 21-154,
21-324
ELECTROSTATIC DISCHARGE (ESD)
SENSITIVE DEVICES - STANDARD
PROCEDURE......................8W-01-8
ELEMENT - DESCRIPTION, HEATED SEAT . . . 8G-10
ELEMENT - INSTALLATION, AIR
CLEANER...........................9-130
ELEMENT - INSTALLATION, HEATED
SEAT ..............................8G-13
ELEMENT - OPERATION, HEATED SEAT . . . 8G-11
ELEMENT - REMOVAL, AIR CLEANER.....9-129
ELEMENT - REMOVAL, HEATED SEAT....8G-13
ELEMENT AND SENSOR - DIAGNOSIS
AND TESTING, HEATED SEAT...........8G-11
EMISSION CONTROL INFORMATION
(VECI) - DESCRIPTION, VEHICLE.......Intro.-3
END SPLASH SHIELDS - INSTALLATION,
FRONT.............................23-92
END SPLASH SHIELDS - REMOVAL,
FRONT.............................23-92
ENGINE - DESCRIPTION, COOLING
SYSTEM FLOW - 5.9L...................7-1
ENGINE - DESCRIPTION, FUEL
REQUIREMENTS - DIESEL...............0-3
ENGINE - DIAGNOSIS AND TESTING,
COOLING SYSTEM DIESEL..............7-13
ENGINE - DIAGNOSIS AND TESTING,
COOLING SYSTEM GAS.................7-7
ENGINE - DIAGNOSIS AND TESTING,
DIESEL.............................11-4
ENGINE - DIAGNOSIS AND TESTING,
GAS................................11-4
ENGINE - IGNITION COIL RESISTANCE,
8.0L V-10............................8I-4
ENGINE - INSTALLATION...............9-125
ENGINE - INSTALLATION, DIESEL........19-37
ENGINE - INSTALLATION, GASOLINE.....19-37
ENGINE - NEGATIVE CABLE
INSTALLATION, GASOLINE.............8F-22
ENGINE - NEGATIVE CABLE REMOVAL,
GASOLINE..........................8F-22
ENGINE - POSITIVE CABLE
INSTALLATION, GASOLINE.............8F-22
ENGINE - POSITIVE CABLE REMOVAL,
GASOLINE..........................8F-21
ENGINE - REMOVAL..................9-123
ENGINE - REMOVAL, DIESEL...........19-36
ENGINE - REMOVAL, GASOLINE.........19-35
ENGINE - SPARK PLUG CABLE ORDER,
8.0L V-10............................8I-3
ENGINE - STANDARD PROCEDURE,
DRAINING COOLING SYSTEM 5.9L
DIESEL.............................7-15
ENGINE - STANDARD PROCEDURE,
REFILLING COOLING SYSTEM 5.9L
DIESEL
.............................7-16
ENGINE - TORQUE, DIESEL
.............14-94
ENGINE - VISUAL INSPECTION, 8.0L
.....14-32
ENGINE 5.9L - DESCRIPTION
.............9-3
ENGINE 5.9L DIESEL - DESCRIPTION
.....9-115ENGINE 8.0L - DESCRIPTION............9-58
ENGINE BLOCK - CLEANING.........9-27,9-85
ENGINE BLOCK - INSPECTION.......9-27,9-85
ENGINE BLOCK HEATER - 5.9L -
DESCRIPTION........................7-44
ENGINE BLOCK HEATER - 5.9L -
INSTALLATION........................7-44
ENGINE BLOCK HEATER - 5.9L -
OPERATION..........................7-44
ENGINE BLOCK HEATER - 5.9L -
REMOVAL...........................7-44
ENGINE BLOCK HEATER - 5.9L DIESEL -
DESCRIPTION........................7-46
ENGINE BLOCK HEATER - 5.9L DIESEL -
INSTALLATION........................7-46
ENGINE BLOCK HEATER - 5.9L DIESEL -
OPERATION..........................7-46
ENGINE BLOCK HEATER - 5.9L DIESEL -
REMOVAL...........................7-46
ENGINE BLOCK HEATER - 8.0L -
DESCRIPTION........................7-45
ENGINE BLOCK HEATER - 8.0L -
INSTALLATION........................7-45
ENGINE BLOCK HEATER - 8.0L -
OPERATION..........................7-45
ENGINE BLOCK HEATER - 8.0L -
REMOVAL...........................7-45
ENGINE CONTROL MODULE -
INSTALLATION.......................8E-14
ENGINE CONTROL MODULE - REMOVAL . . 8E-14
ENGINE COOLANT - DESCRIPTION........7-39
ENGINE COOLANT - DESCRIPTION..........0-3
ENGINE COOLANT TEMP SENSOR - 5.9L
- DESCRIPTION.......................7-47
ENGINE COOLANT TEMP SENSOR - 5.9L
- INSTALLATION......................7-47
ENGINE COOLANT TEMP SENSOR - 5.9L
- OPERATION.........................7-47
ENGINE COOLANT TEMP SENSOR - 5.9L
- REMOVAL..........................7-47
ENGINE COOLANT THERMOSTAT - 5.9L -
DESCRIPTION........................7-48
ENGINE COOLANT THERMOSTAT - 5.9L -
INSTALLATION........................7-49
ENGINE COOLANT THERMOSTAT - 5.9L -
OPERATION..........................7-48
ENGINE COOLANT THERMOSTAT - 5.9L -
REMOVAL...........................7-48
ENGINE COOLANT THERMOSTAT - 5.9L
DIESEL - DESCRIPTION................7-53
ENGINE COOLANT THERMOSTAT - 5.9L
DIESEL - INSTALLATION................7-54
ENGINE COOLANT THERMOSTAT - 5.9L
DIESEL - OPERATION..................7-53
ENGINE COOLANT THERMOSTAT - 5.9L
DIESEL - REMOVAL....................7-54
ENGINE COOLANT THERMOSTAT - 8.0L -
DESCRIPTION........................7-51
ENGINE COOLANT THERMOSTAT - 8.0L -
INSTALLATION........................7-52
ENGINE COOLANT THERMOSTAT - 8.0L -
OPERATION..........................7-51
ENGINE COOLANT THERMOSTAT - 8.0L -
REMOVAL...........................7-51
ENGINE DATA PLATE - DESCRIPTION.....9-129
ENGINE DIAGNOSIS - INTRODUCTION -
DIAGNOSIS AND TESTING...........9-3,9-58
ENGINE DIAGNOSIS - LUBRICATION -
DIAGNOSIS AND TESTING...........9-63,9-8
ENGINE DIAGNOSIS - MECHANICAL -
DIAGNOSIS AND TESTING......9-116,9-6,9-61
ENGINE DIAGNOSIS - PERFORMANCE -
DIAGNOSIS AND TESTING...........9-4,9-59
ENGINE FIRING ORDER, 5.9L V-8
ENGINES............................8I-3
ENGINE OIL - DESCRIPTION...........0-4,0-5
ENGINE OIL - STANDARD PROCEDURE . . . 9-101,
9-45
ENGINE OIL LEAKS - DIAGNOSIS AND
TESTING........................9-43,9-99
ENGINE OIL LEVEL - STANDARD
PROCEDURE
........................9-178
ENGINE OIL PRESSURE - DIAGNOSIS
AND TESTING
..............9-101,9-178,9-45
ENGINE OIL SERVICE - STANDARD
PROCEDURE
........................9-178
ENGINE, SPECIAL TOOLS - 5.9L
..........9-18
ENGINE, SPECIAL TOOLS - 5.9L DIESEL
. . 9-128
BR/BEINDEX 11
Description Group-Page Description Group-Page Description Group-Page