clock FIAT DUCATO BASE CAMPER 2017 Owner handbook (in English)
[x] Cancel search | Manufacturer: FIAT, Model Year: 2017, Model line: DUCATO BASE CAMPER, Model: FIAT DUCATO BASE CAMPER 2017Pages: 296, PDF Size: 14.44 MB
Page 149 of 296
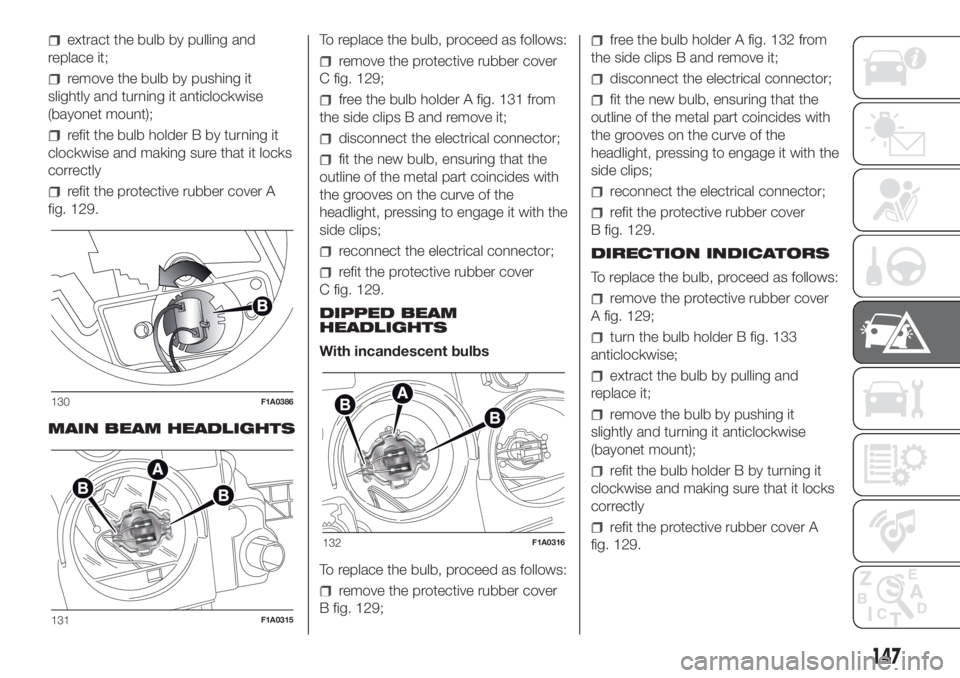
extract the bulb by pulling and
replace it;
remove the bulb by pushing it
slightly and turning it anticlockwise
(bayonet mount);
refit the bulb holder B by turning it
clockwise and making sure that it locks
correctly
refit the protective rubber cover A
fig. 129.
MAIN BEAM HEADLIGHTSTo replace the bulb, proceed as follows:
remove the protective rubber cover
C fig. 129;
free the bulb holder A fig. 131 from
the side clips B and remove it;
disconnect the electrical connector;
fit the new bulb, ensuring that the
outline of the metal part coincides with
the grooves on the curve of the
headlight, pressing to engage it with the
side clips;
reconnect the electrical connector;
refit the protective rubber cover
C fig. 129.
DIPPED BEAM
HEADLIGHTS
With incandescent bulbs
To replace the bulb, proceed as follows:
remove the protective rubber cover
B fig. 129;
free the bulb holder A fig. 132 from
the side clips B and remove it;
disconnect the electrical connector;
fit the new bulb, ensuring that the
outline of the metal part coincides with
the grooves on the curve of the
headlight, pressing to engage it with the
side clips;
reconnect the electrical connector;
refit the protective rubber cover
B fig. 129.
DIRECTION INDICATORS
To replace the bulb, proceed as follows:
remove the protective rubber cover
A fig. 129;
turn the bulb holder B fig. 133
anticlockwise;
extract the bulb by pulling and
replace it;
remove the bulb by pushing it
slightly and turning it anticlockwise
(bayonet mount);
refit the bulb holder B by turning it
clockwise and making sure that it locks
correctly
refit the protective rubber cover A
fig. 129.
130F1A0386
131F1A0315
132F1A0316
147
Page 150 of 296
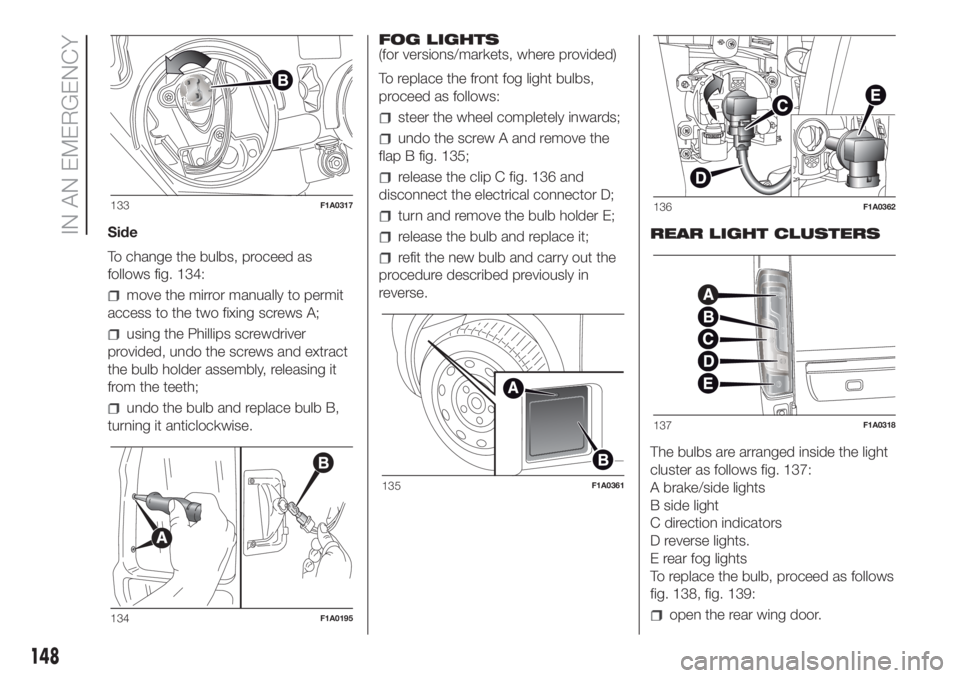
Side
To change the bulbs, proceed as
follows fig. 134:
move the mirror manually to permit
access to the two fixing screws A;
using the Phillips screwdriver
provided, undo the screws and extract
the bulb holder assembly, releasing it
from the teeth;
undo the bulb and replace bulb B,
turning it anticlockwise.FOG LIGHTS
(for versions/markets, where provided)
To replace the front fog light bulbs,
proceed as follows:
steer the wheel completely inwards;
undo the screw A and remove the
flap B fig. 135;
release the clip C fig. 136 and
disconnect the electrical connector D;
turn and remove the bulb holder E;
release the bulb and replace it;
refit the new bulb and carry out the
procedure described previously in
reverse.REAR LIGHT CLUSTERS
The bulbs are arranged inside the light
cluster as follows fig. 137:
A brake/side lights
B side light
C direction indicators
D reverse lights.
E rear fog lights
To replace the bulb, proceed as follows
fig. 138, fig. 139:
open the rear wing door.
133F1A0317
134F1A0195
135F1A0361
136F1A0362
137F1A0318
148
IN AN EMERGENCY
Page 151 of 296
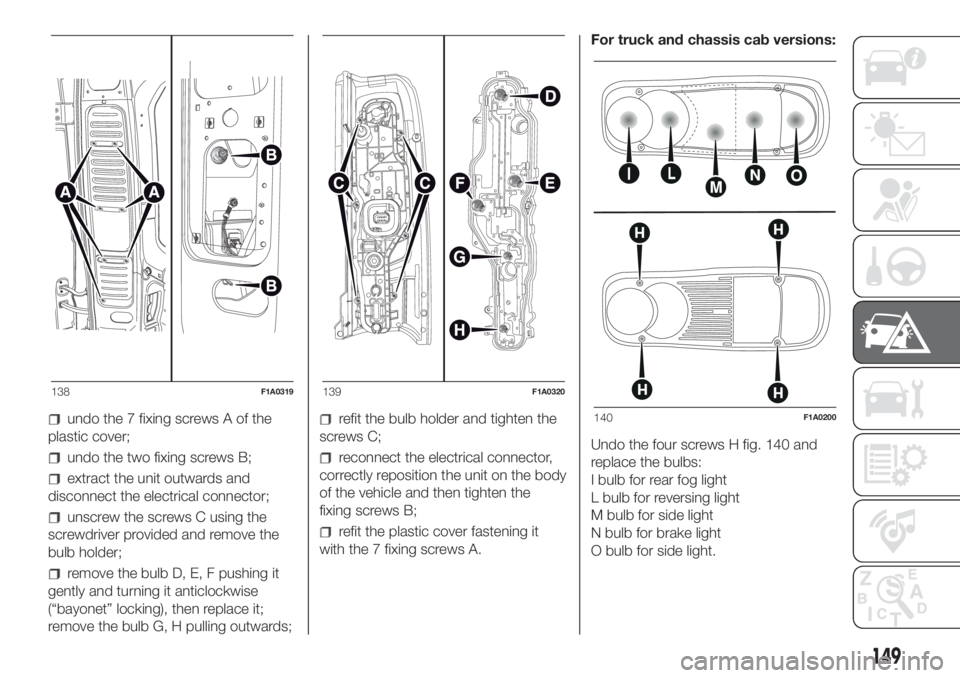
undo the 7 fixing screws A of the
plastic cover;
undo the two fixing screws B;
extract the unit outwards and
disconnect the electrical connector;
unscrew the screws C using the
screwdriver provided and remove the
bulb holder;
remove the bulb D, E, F pushing it
gently and turning it anticlockwise
(“bayonet” locking), then replace it;
remove the bulb G, H pulling outwards;
refit the bulb holder and tighten the
screws C;
reconnect the electrical connector,
correctly reposition the unit on the body
of the vehicle and then tighten the
fixing screws B;
refit the plastic cover fastening it
with the 7 fixing screws A.For truck and chassis cab versions:
Undo the four screws H fig. 140 and
replace the bulbs:
I bulb for rear fog light
L bulb for reversing light
M bulb for side light
N bulb for brake light
O bulb for side light.
138F1A0319139F1A0320
140F1A0200
149
Page 154 of 296

FUSE LOCATION
The vehicle fuses are grouped in three
control units located on the dashboard,
passenger compartment right pillar
and engine compartment.
DASHBOARD FUSEBOX
To access the dashboard fuse box fig.
148, undo the screws A fig. 149 and
remove the cover.ENGINE COMPARTMENT
FUSEBOX – OPTIONAL WIRING
MODULE
To access the fusebox fig. 151 - fig.
152 - fig. 153 - fig. 154, remove its
protective cover fig. 150.
Proceed as follows:
fully tighten the captive screw using
the dedicated Phillips screwdriver
provided;
slowly rotate the screw
anticlockwise until resistance is
encountered (do not overtighten);
slowly release the screw;
opening is indicated by the entire
screw head coming out of its housing;
remove the cover.
To refit the cover proceed as follows:
join the cover with the box correctly;
fully tighten the captive screw using
the dedicated Phillips screwdriver
provided;
slowly rotate the screw clockwise
until resistance is encountered (do not
overtighten);
slowly release the screw;
closure is indicated by the inset of
the entire screw head in its housing.
148F1A0214
149F1A0213
150F1A0334
152
IN AN EMERGENCY
Page 173 of 296
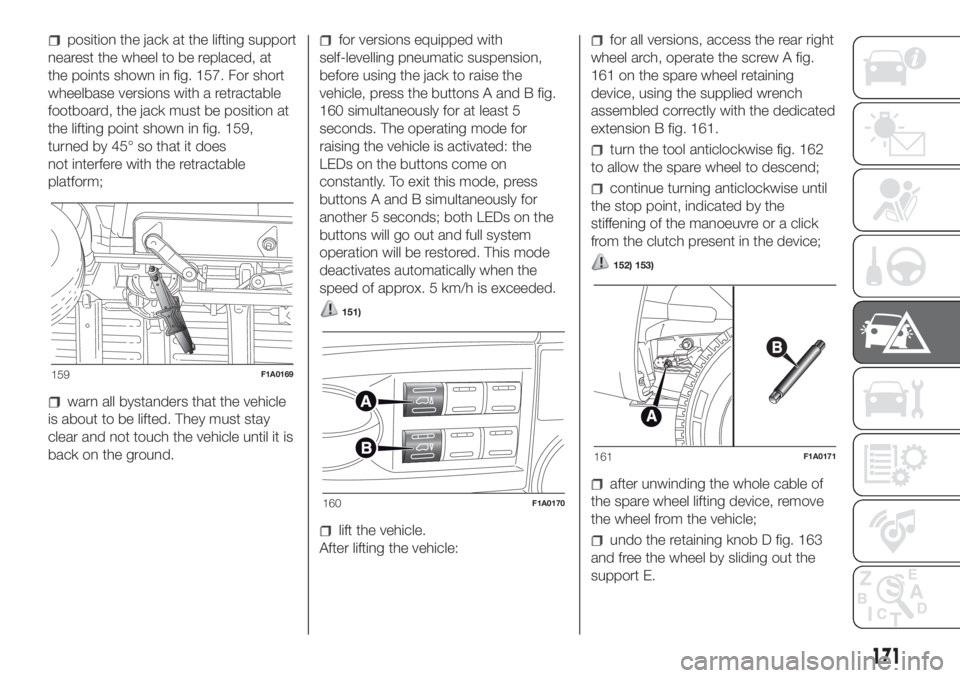
position the jack at the lifting support
nearest the wheel to be replaced, at
the points shown in fig. 157. For short
wheelbase versions with a retractable
footboard, the jack must be position at
the lifting point shown in fig. 159,
turned by 45° so that it does
not interfere with the retractable
platform;
warn all bystanders that the vehicle
is about to be lifted. They must stay
clear and not touch the vehicle until it is
back on the ground.
for versions equipped with
self-levelling pneumatic suspension,
before using the jack to raise the
vehicle, press the buttons A and B fig.
160 simultaneously for at least 5
seconds. The operating mode for
raising the vehicle is activated: the
LEDs on the buttons come on
constantly. To exit this mode, press
buttons A and B simultaneously for
another 5 seconds; both LEDs on the
buttons will go out and full system
operation will be restored. This mode
deactivates automatically when the
speed of approx. 5 km/h is exceeded.
151)
lift the vehicle.
After lifting the vehicle:
for all versions, access the rear right
wheel arch, operate the screw A fig.
161 on the spare wheel retaining
device, using the supplied wrench
assembled correctly with the dedicated
extension B fig. 161.
turn the tool anticlockwise fig. 162
to allow the spare wheel to descend;
continue turning anticlockwise until
the stop point, indicated by the
stiffening of the manoeuvre or a click
from the clutch present in the device;
152) 153)
after unwinding the whole cable of
the spare wheel lifting device, remove
the wheel from the vehicle;
undo the retaining knob D fig. 163
and free the wheel by sliding out the
support E.
159F1A0169
160F1A0170
161F1A0171
171
Page 174 of 296
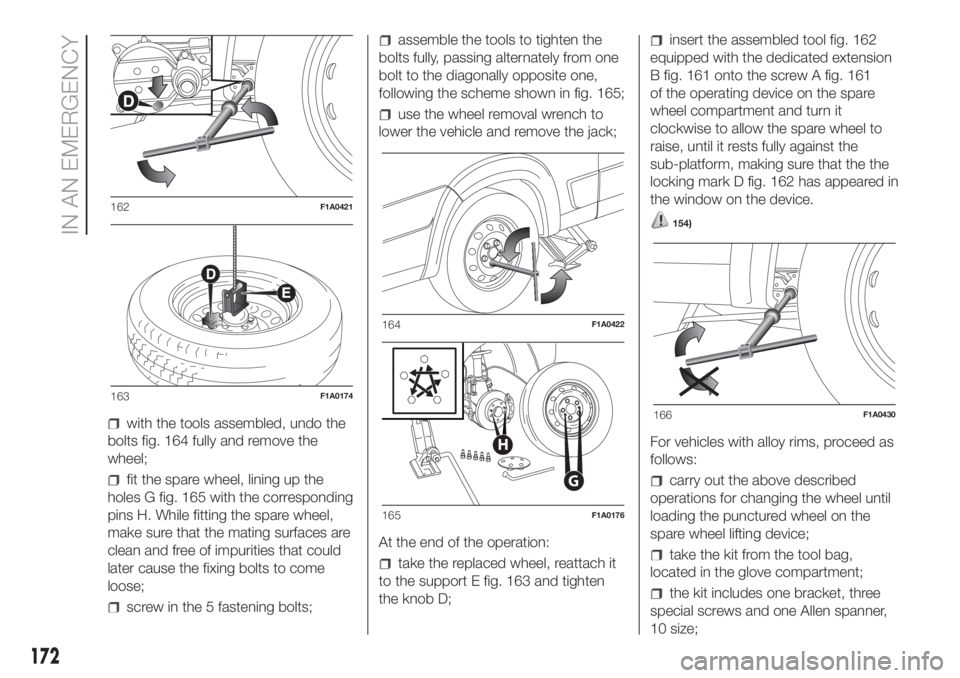
with the tools assembled, undo the
bolts fig. 164 fully and remove the
wheel;
fit the spare wheel, lining up the
holes G fig. 165 with the corresponding
pins H. While fitting the spare wheel,
make sure that the mating surfaces are
clean and free of impurities that could
later cause the fixing bolts to come
loose;
screw in the 5 fastening bolts;
assemble the tools to tighten the
bolts fully, passing alternately from one
bolt to the diagonally opposite one,
following the scheme shown in fig. 165;
use the wheel removal wrench to
lower the vehicle and remove the jack;
At the end of the operation:
take the replaced wheel, reattach it
to the support E fig. 163 and tighten
the knob D;
insert the assembled tool fig. 162
equipped with the dedicated extension
B fig. 161 onto the screw A fig. 161
of the operating device on the spare
wheel compartment and turn it
clockwise to allow the spare wheel to
raise, until it rests fully against the
sub-platform, making sure that the the
locking mark D fig. 162 has appeared in
the window on the device.
154)
For vehicles with alloy rims, proceed as
follows:
carry out the above described
operations for changing the wheel until
loading the punctured wheel on the
spare wheel lifting device;
take the kit from the tool bag,
located in the glove compartment;
the kit includes one bracket, three
special screws and one Allen spanner,
10 size;
162F1A0421
163F1A0174
164F1A0422
G
H
165F1A0176
166F1A0430
172
IN AN EMERGENCY
Page 175 of 296
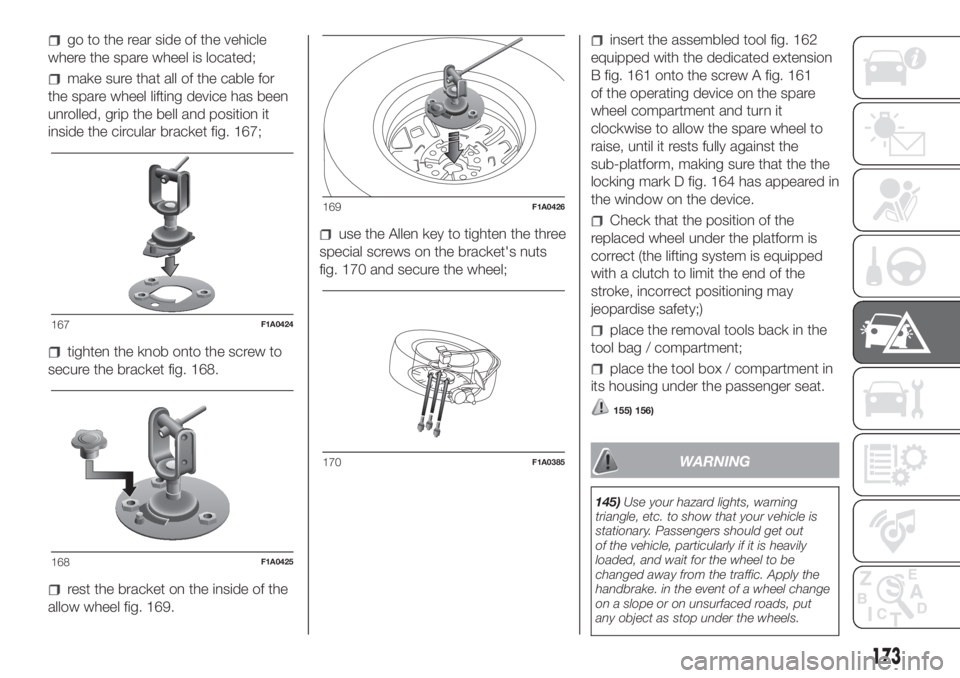
go to the rear side of the vehicle
where the spare wheel is located;
make sure that all of the cable for
the spare wheel lifting device has been
unrolled, grip the bell and position it
inside the circular bracket fig. 167;
tighten the knob onto the screw to
secure the bracket fig. 168.
rest the bracket on the inside of the
allow wheel fig. 169.
use the Allen key to tighten the three
special screws on the bracket's nuts
fig. 170 and secure the wheel;
insert the assembled tool fig. 162
equipped with the dedicated extension
B fig. 161 onto the screw A fig. 161
of the operating device on the spare
wheel compartment and turn it
clockwise to allow the spare wheel to
raise, until it rests fully against the
sub-platform, making sure that the the
locking mark D fig. 164 has appeared in
the window on the device.
Check that the position of the
replaced wheel under the platform is
correct (the lifting system is equipped
with a clutch to limit the end of the
stroke, incorrect positioning may
jeopardise safety;)
place the removal tools back in the
tool bag / compartment;
place the tool box / compartment in
its housing under the passenger seat.
155) 156)
WARNING
145)Use your hazard lights, warning
triangle, etc. to show that your vehicle is
stationary. Passengers should get out
of the vehicle, particularly if it is heavily
loaded, and wait for the wheel to be
changed away from the traffic. Apply the
handbrake. in the event of a wheel change
on a slope or on unsurfaced roads, put
any object as stop under the wheels.
167F1A0424
168F1A0425
169F1A0426
170F1A0385
173
Page 177 of 296
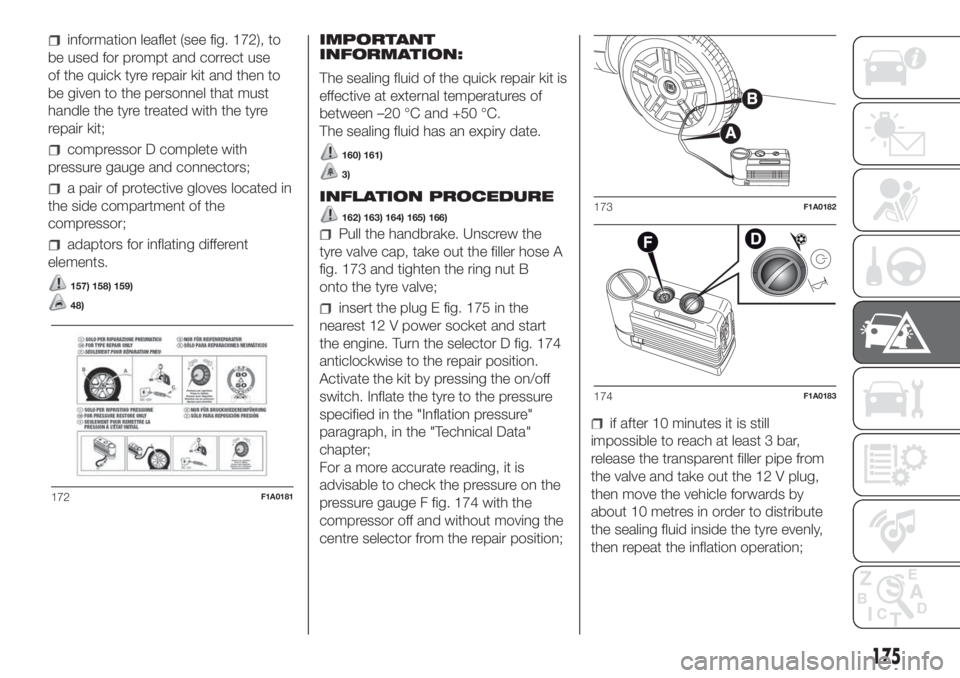
information leaflet (see fig. 172), to
be used for prompt and correct use
of the quick tyre repair kit and then to
be given to the personnel that must
handle the tyre treated with the tyre
repair kit;
compressor D complete with
pressure gauge and connectors;
a pair of protective gloves located in
the side compartment of the
compressor;
adaptors for inflating different
elements.
157) 158) 159)
48)
IMPORTANT
INFORMATION:
The sealing fluid of the quick repair kit is
effective at external temperatures of
between –20 °C and +50 °C.
The sealing fluid has an expiry date.
160) 161)
3)
INFLATION PROCEDURE
162) 163) 164) 165) 166)
Pull the handbrake. Unscrew the
tyre valve cap, take out the filler hose A
fig. 173 and tighten the ring nut B
onto the tyre valve;
insert the plug E fig. 175 in the
nearest 12 V power socket and start
the engine. Turn the selector D fig. 174
anticlockwise to the repair position.
Activate the kit by pressing the on/off
switch. Inflate the tyre to the pressure
specified in the "Inflation pressure"
paragraph, in the "Technical Data"
chapter;
For a more accurate reading, it is
advisable to check the pressure on the
pressure gauge F fig. 174 with the
compressor off and without moving the
centre selector from the repair position;
if after 10 minutes it is still
impossible to reach at least 3 bar,
release the transparent filler pipe from
the valve and take out the 12 V plug,
then move the vehicle forwards by
about 10 metres in order to distribute
the sealing fluid inside the tyre evenly,
then repeat the inflation operation;
172F1A0181
173F1A0182
174F1A0183
175
Page 182 of 296
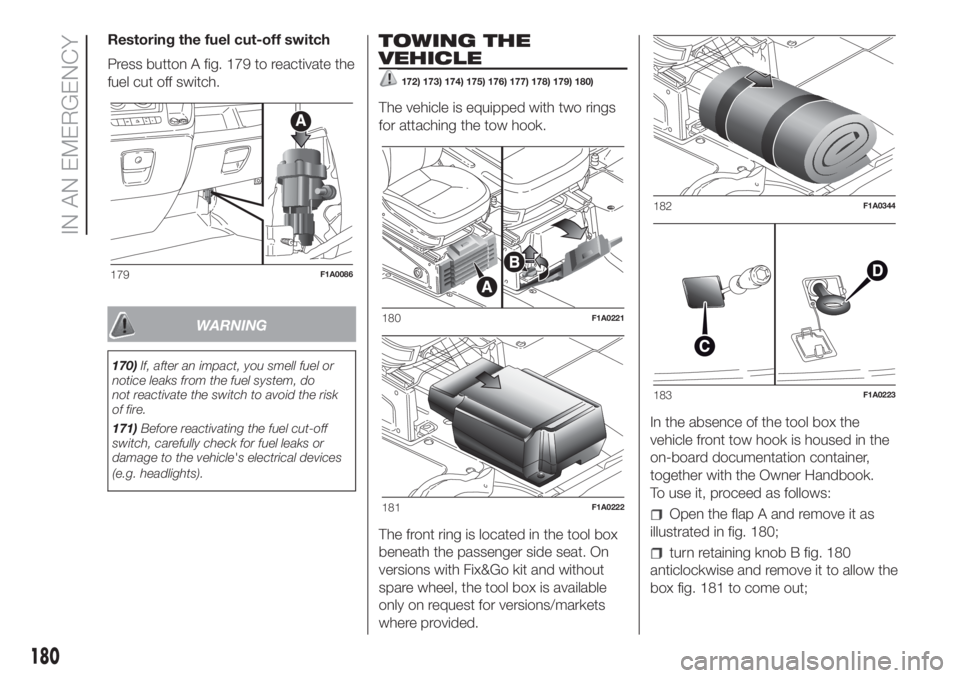
Restoring the fuel cut-off switch
Press button A fig. 179 to reactivate the
fuel cut off switch.
WARNING
170)If, after an impact, you smell fuel or
notice leaks from the fuel system, do
not reactivate the switch to avoid the risk
of fire.
171)Before reactivating the fuel cut-off
switch, carefully check for fuel leaks or
damage to the vehicle's electrical devices
(e.g. headlights).
TOWING THE
VEHICLE
172) 173) 174) 175) 176) 177) 178) 179) 180)
The vehicle is equipped with two rings
for attaching the tow hook.
The front ring is located in the tool box
beneath the passenger side seat. On
versions with Fix&Go kit and without
spare wheel, the tool box is available
only on request for versions/markets
where provided.In the absence of the tool box the
vehicle front tow hook is housed in the
on-board documentation container,
together with the Owner Handbook.
To use it, proceed as follows:
Open the flap A and remove it as
illustrated in fig. 180;
turn retaining knob B fig. 180
anticlockwise and remove it to allow the
box fig. 181 to come out;
179F1A0086
180F1A0221
181F1A0222
182F1A0344
183F1A0223
180
IN AN EMERGENCY
Page 198 of 296
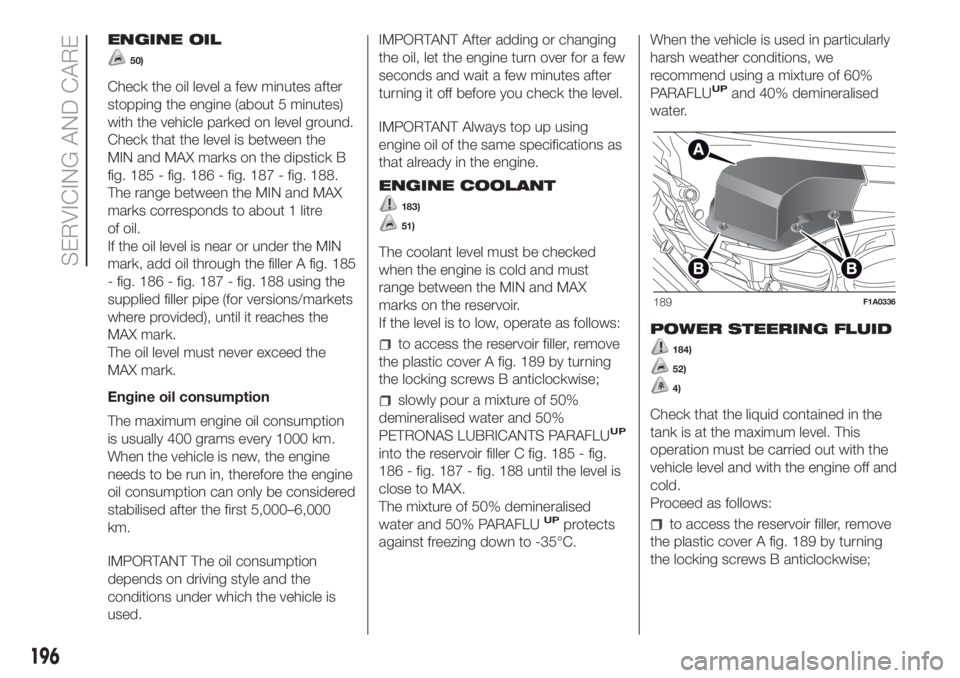
ENGINE OIL
50)
Check the oil level a few minutes after
stopping the engine (about 5 minutes)
with the vehicle parked on level ground.
Check that the level is between the
MIN and MAX marks on the dipstick B
fig. 185 - fig. 186 - fig. 187 - fig. 188.
The range between the MIN and MAX
marks corresponds to about 1 litre
of oil.
If the oil level is near or under the MIN
mark, add oil through the filler A fig. 185
- fig. 186 - fig. 187 - fig. 188 using the
supplied filler pipe (for versions/markets
where provided), until it reaches the
MAX mark.
The oil level must never exceed the
MAX mark.
Engine oil consumption
The maximum engine oil consumption
is usually 400 grams every 1000 km.
When the vehicle is new, the engine
needs to be run in, therefore the engine
oil consumption can only be considered
stabilised after the first 5,000–6,000
km.
IMPORTANT The oil consumption
depends on driving style and the
conditions under which the vehicle is
used.IMPORTANT After adding or changing
the oil, let the engine turn over for a few
seconds and wait a few minutes after
turning it off before you check the level.
IMPORTANT Always top up using
engine oil of the same specifications as
that already in the engine.
ENGINE COOLANT
183)
51)
The coolant level must be checked
when the engine is cold and must
range between the MIN and MAX
marks on the reservoir.
If the level is to low, operate as follows:
to access the reservoir filler, remove
the plastic cover A fig. 189 by turning
the locking screws B anticlockwise;
slowly pour a mixture of 50%
demineralised water and 50%
PETRONAS LUBRICANTS PARAFLU
UP
into the reservoir filler C fig. 185 - fig.
186 - fig. 187 - fig. 188 until the level is
close to MAX.
The mixture of 50% demineralised
water and 50% PARAFLU
UPprotects
against freezing down to -35°C.When the vehicle is used in particularly
harsh weather conditions, we
recommend using a mixture of 60%
PARAFLU
UPand 40% demineralised
water.
POWER STEERING FLUID
184)
52)
4)
Check that the liquid contained in the
tank is at the maximum level. This
operation must be carried out with the
vehicle level and with the engine off and
cold.
Proceed as follows:
to access the reservoir filler, remove
the plastic cover A fig. 189 by turning
the locking screws B anticlockwise;
189F1A0336
196
SERVICING AND CARE