wind FIAT PUNTO 1997 176 / 1.G Owner's Manual
[x] Cancel search | Manufacturer: FIAT, Model Year: 1997, Model line: PUNTO, Model: FIAT PUNTO 1997 176 / 1.GPages: 225, PDF Size: 18.54 MB
Page 204 of 225
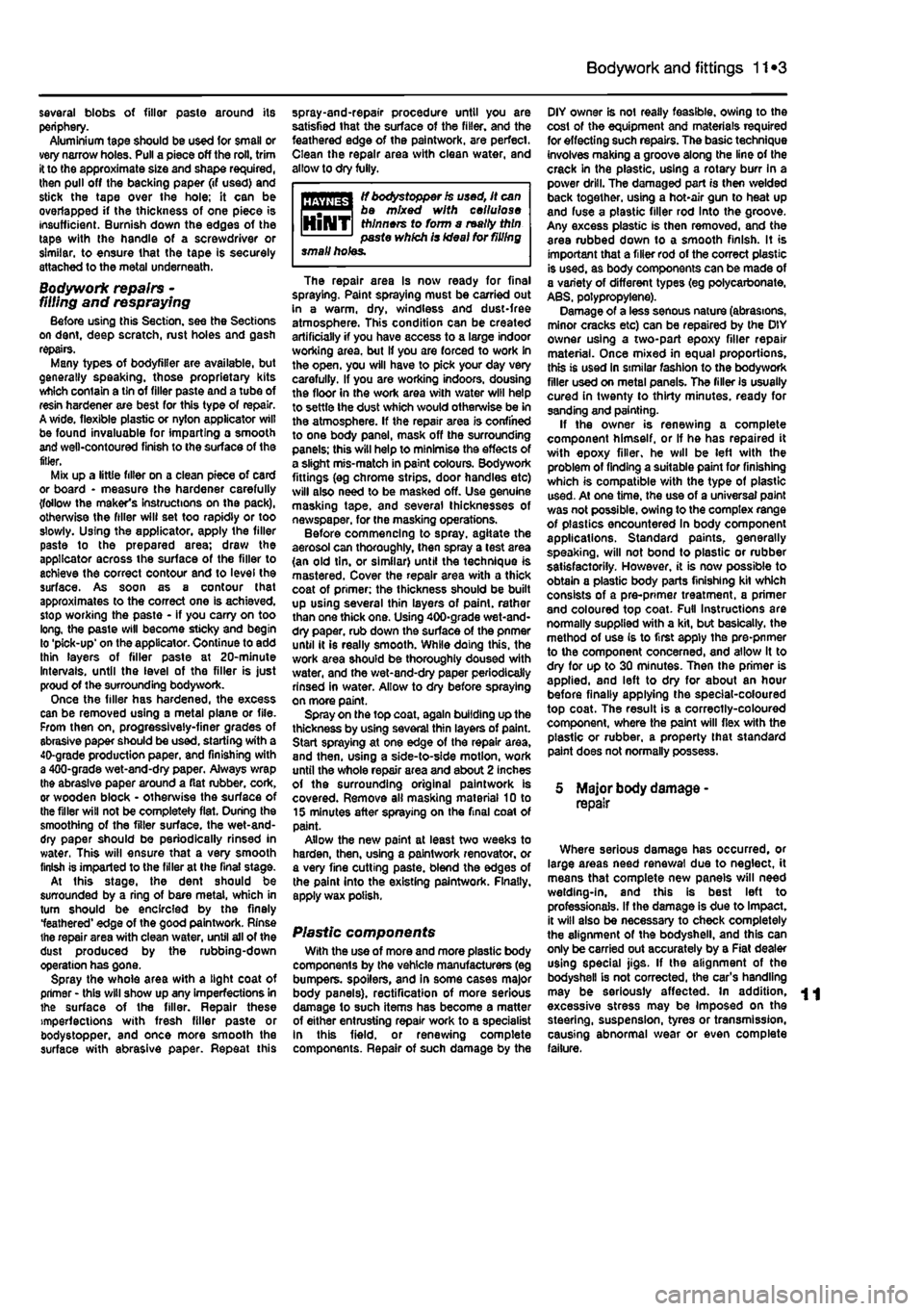
Bodywork and fittings
11
*3
several blobs of filler paste around its periphery. Aluminium tape should be used for small or very narrow holes. Pull a piece off the roll, trim it to the approximate size and shape required, then pull off the backing paper (if used) and stick the tape over the hole; it can be overlapped if the thickness of one piece is Insufficient. Burnish down the edges of the tape with the handle of a screwdriver or similar, to ensure that the tape is securely attached to the metal underneath.
Bodywork repairs -filling and respraying Before using this Section, see the Sections on dent, deep scratch, rust holes and gash repairs. Many types of bodyfiller are available, but generally speaking, those proprietary kits which contain a tin of filler paste and a tube of resin hardener are best for this type of repair. A wide, flexible plastic or nylon applicator will be found invaluable for imparting a smooth and well-contoured finish to the surface of the filler. Mix up a little filler on a clean piece of card or board • measure the hardener carefully (follow the maker's instructions on the pack), otherwise the filler will set too rapidly or too slowly. U3ing the applicator, apply the filler paste to the prepared area; draw the applicator across the surface of the filler to achieve the correct contour and to level the surface. As soon as a contour that approximates to the correct one is achieved, stop working the paste - if you carry on too long, the paste will become sticky and begin lo 'pick-up' on the applicator. Continue to add thin layers of filler paste at 20-minute Intervals, until the level of the filler is just proud of the surrounding bodywork. Once the filler has hardened, the excess can be removed using a metal plane or file. From then on, progressively-finer grades of abrasive paper should be used, starting with a 40-grade production paper, and finishing with a 400-grade wet-and-dry paper. Always wrap the abrasive paper around a flat rubber, cork, or wooden block • otherwise the surface of the filler will not be completely flat. During the smoothing of the filler surface, the wet-and-dry paper should be periodically rinsed in water. This will ensure that a very smooth finish is imparled to the filler at the final stage. At this stage, the dent should be surrounded by a ring of bare metal, which in turn should be encircled by the finely feathered' edge of the good paintwork. Rinse the repair area with clean water, until all of the dust produced by the rubbing-down operation has gone. Spray the whole area with a light coat of primer - this will show up any imperfections In the surface of the filler. Repair these imperfections with fresh filler paste or bodystopper, and once more smooth the surface with abrasive paper. Repeat this
spray-and-repair procedure until you are satisfied that the surface of the filler, and the feathered edge of the paintwork, are perfect. Clean the repair area with clean water, and allow to dry fully.
flflfl^gl tf txxfystopper is used, it can WiMiiBi be mixed with cellulose Hi NT thinners to form a really thin 1 1 paste which is Ideal for filling small holes.
The repair area Is now ready for final spraying. Paint spraying must be carried out in a warm, dry, windless and dust-free atmosphere. This condition can be created artificially if you have access to a large indoor working area, but If you are forced to work in the open, you will have to pick your day very carefully. If you are working indoors, dousing the floor In the work area with water will help to settle the dust which would otherwise be in the atmosphere. If the repair area is confined to one body panel, mask off the surrounding panels; this will help to minimise the effects of a slight mis-match in paint colours. Bodywork fittings (eg chrome strips, door handles etc) will also need to be masked off. Use genuine masking tape, and several thicknesses of newspaper, for the masking operations. Before commencing to spray, agitate the aerosol can thoroughly, then spray a test area (an old tin. or similar) until the technique is mastered. Cover the repair area with a thick coat of primer; the thickness should be built up using several thin layers of paint, rather than one thick one. Using 400-grade wet-and-dry paper, rub down the surface of the pnmer until it is really smooth. While doing this, the work area should be thoroughly doused with water, and the wet-and-dry paper periodically rinsed in water. Allow to dry before spraying on more paint. Spray on the top coat, again building up the thickness by using several thin layers of paint. Start spraying at one edge of the repair area, and then, using a side-to-side motion, work until the whole repair area and about 2 inches of the surrounding original paintwork is covered. Remove all masking material 10 to 15 minutes after spraying on the final coat of paint. Allow the new paint at least two weeks to harden, then, using a paintwork renovator, or a very fine cutting paste, blend the edges of the paint into the existing paintwork. Finally, apply wax polish.
Plastic components With the use of more and more plastic body components by the vehicle manufacturers (eg bumpers, spoilers, and in some cases major body panels), rectification of more serious damage to such items has become a matter of either entrusting repair work to a specialist in this field, or renewing complete components. Repair of such damage by the
DIY owner is not really feasible, owing to the cost of the equipment and materials required for effecting such repairs. The basic technique involves making a groove along the line of the crack in the plastic, using a rotary burr In a power drill. The damaged part is then welded back together, using a hot-air gun to heat up and fuse a plastic filler rod Into the groove. Any excess plastic is then removed, and the area rubbed down to a smooth finish. It is important that a filler rod of the correct plastic is used, as body components can be made of a variety of different types (eg polycarbonate, ABS, polypropylene). Damage of a less senous nature (abrasions, minor cracks etc) can be repaired by the DIY owner using a two-part epoxy filler repair material. Once mixed in equal proportions, this is used in similar fashion to the bodywork filler used on metal panels. The filler is usually cured in twenty to thirty minutes, ready for sanding and painting. If the owner is renewing a complete component himself, or If he has repaired it with epoxy filler, he will be left with the problem of finding a suitable paint for finishing which is compatible with the type of plastic used. At one time, the use of a universal paint was not possible, owing to the complex range of plastics encountered In body component applications. Standard paints, generally speaking, will not bond to plastic or rubber satisfactorily. However, it is now possible to obtain a plastic body parts finishing kit which consists of a pre-pnmer treatment, a primer and coloured top coat. Full Instructions are normally supplied with a kit, but basically, the method of use is to first apply the pre-pnmer to the component concerned, and allow It to dry for up to 30 minutes. Then the primer is applied, and left to dry for about an hour before finally applying the special-coloured top coat. The result is a correctly-coloured component, where the paint will flex with the plastic or rubber, a property that standard paint does not normally possess.
5 Major body damage -repair
Where serious damage has occurred, or large areas need renewal due to neglect, it means that complete new panels will need welding-in, and this is best left to professionals. If the damage is due to Impact, it will also be necessary to check completely the alignment of the bodyshell, and this can only be carried out accurately by a Fiat dealer using special jigs. If the alignment of the bodyshell is not corrected, the car's handling may be seriously affected. In addition, excessive stress may be Imposed on the steering, suspension, tyres or transmission, causing abnormal wear or even complete failure.
Page 208 of 225
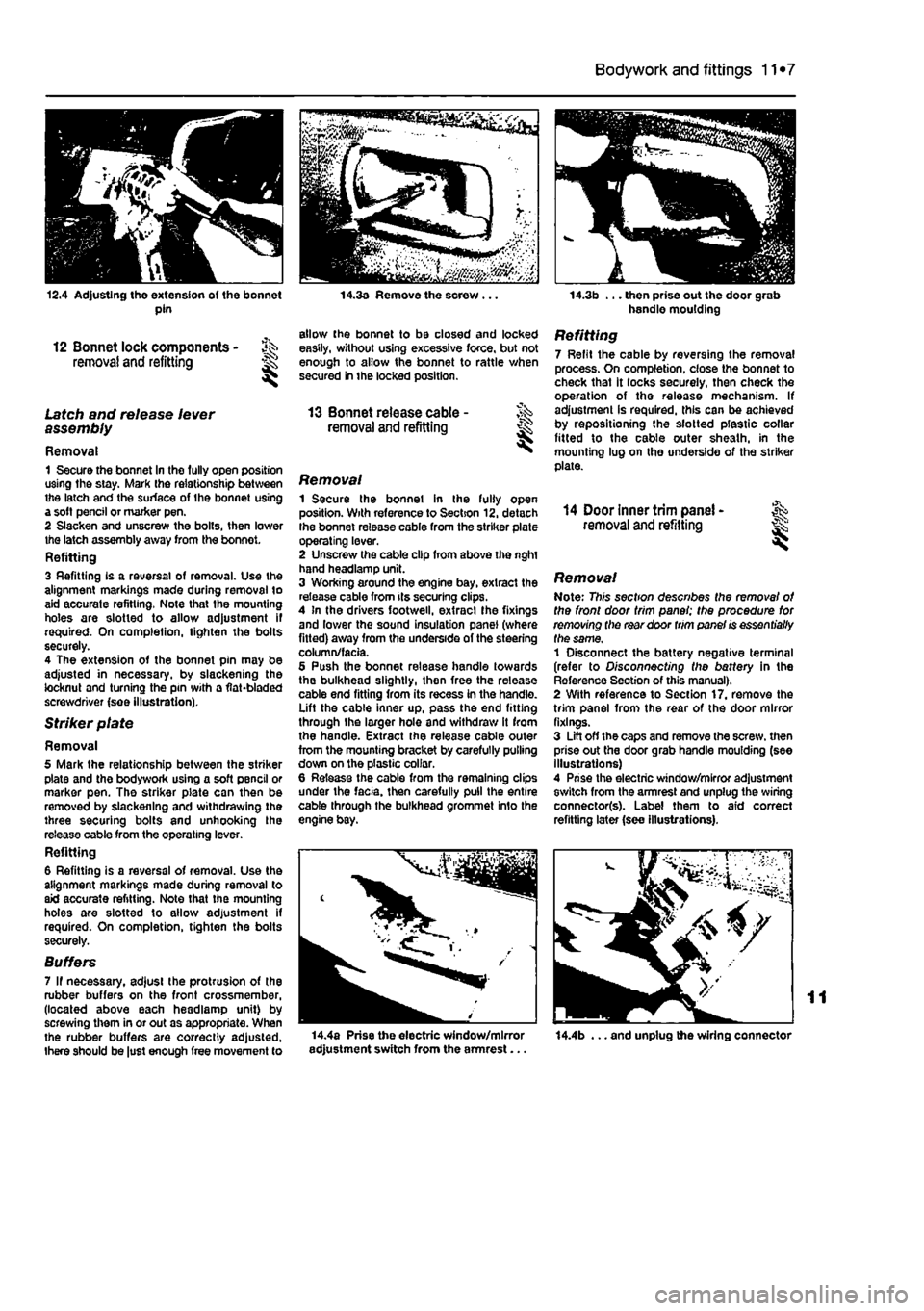
Bodywork and fittings
11
*7
12.4 Adjusting the extension of the bonnet pin
12 Bonnet lock components - ^ removal and refitting H
Latch and release lever assembly
Removal 1 Secure the bonnet In the fully open position using the stay. Mark the relationship between the latch and the surface of the bonnet using a soft pencil or marker pen. 2 Slacken and unscrew the bolts, then lower the latch assembly away from the bonnot. Refitting 3 Refitting is a reversal of removal. Use the alignment markings made during removal to aid accurate refitting. Note that the mounting holes are slotted to allow adjustment if required. On completion, tighten the bolts securely. 4 The extension of the bonnet pin may be adjusted in necessary, by slackening the locknut and turning the pin with a flat-bladed screwdriver (see illustration).
Striker plate
Removal 5 Mark the relationship between the striker plate and the bodywork using a soft pencil or marker pen. The striker plate can then be removed by slackening and withdrawing the three securing bolts and unhooking the release cable from the operating lever. Refitting 6 Refitting is a reversal of removal. Use the alignment markings made during removal to aid accurate refitting. Note that the mounting holes are slotted to allow adjustment if required. On completion, tighten the bolts securely.
Suffers 7 If necessary, adjust the protrusion of the rubber buffers on the front crossmember, (located above each headlamp unit) by screwing them in or out as appropriate. When the rubber buffers are correctly adjusted, there should be just enough free movement to
14.3a Remove the screw .
allow the bonnet to be closed and locked easily, without using excessive force, but not enough to allow the bonnet to rattle when secured in the locked position.
13 Bonnet release cable -removal and refitting I
Removal 1 Secure the bonnet in the fully open position. With reference to Section 12, detach Ihe bonnet release cable from the striker plate operating lever. 2 Unscrew the cable clip from above the nght hand headlamp unit. 3 Working around the engine bay, extract the release cable from its securing clips. 4 In the drivers footweil, extracl Ihe fixings and lower the sound insulation panel (where fitted) away from the underside of the steering column/facia. 5 Push the bonnet release handle towards the bulkhead slightly, then free the release cable end fitting from its recess in the handle. Lift the cable inner up, pass the end fitting through the larger hole and withdraw it from the handle. Extract the release cable outer from the mounting bracket by carefully pulling down on the plastic collar. 6 Release the cable from the remaining clips under the facia, then carefully pull the entire cable through the bulkhead grommet Info the engine bay.
14.3b ... then prise out the door grab handle moulding
Refitting 7 Refit the cable by reversing the removal process. On completion, close the bonnet to check that it locks securely, then check the operation of tho release mechanism. If adjustment is required, this can be achieved by repositioning the slotted plastic collar fitted to the cable outer sheath, in the mounting lug on the underside of the striker plate.
14 Door inner trim panel -removal and refitting I
Removal Note: This section describes the removal of the front door trim panel; the procedure for removing the rear door trim panel is essentially the same, 1 Disconnect the battery negative terminal (refer to Disconnecting the battery in the Reference Section of this manual). 2 With reference to Section 17. remove the trim panel from the rear of the door mirror fixings. 3 Lift off the caps and remove the screw, then prise out the door grab handle moulding (see Illustrations) 4 Prise the electric window/mirror adjustment switch from the armrest and unplug the wiring connector(s). Label them to aid correct refitting later (see illustrations).
14.4a Prise the electric window/mirror adjustment switch from the armrest... 14.4b ... and unplug the wiring connector
Page 209 of 225
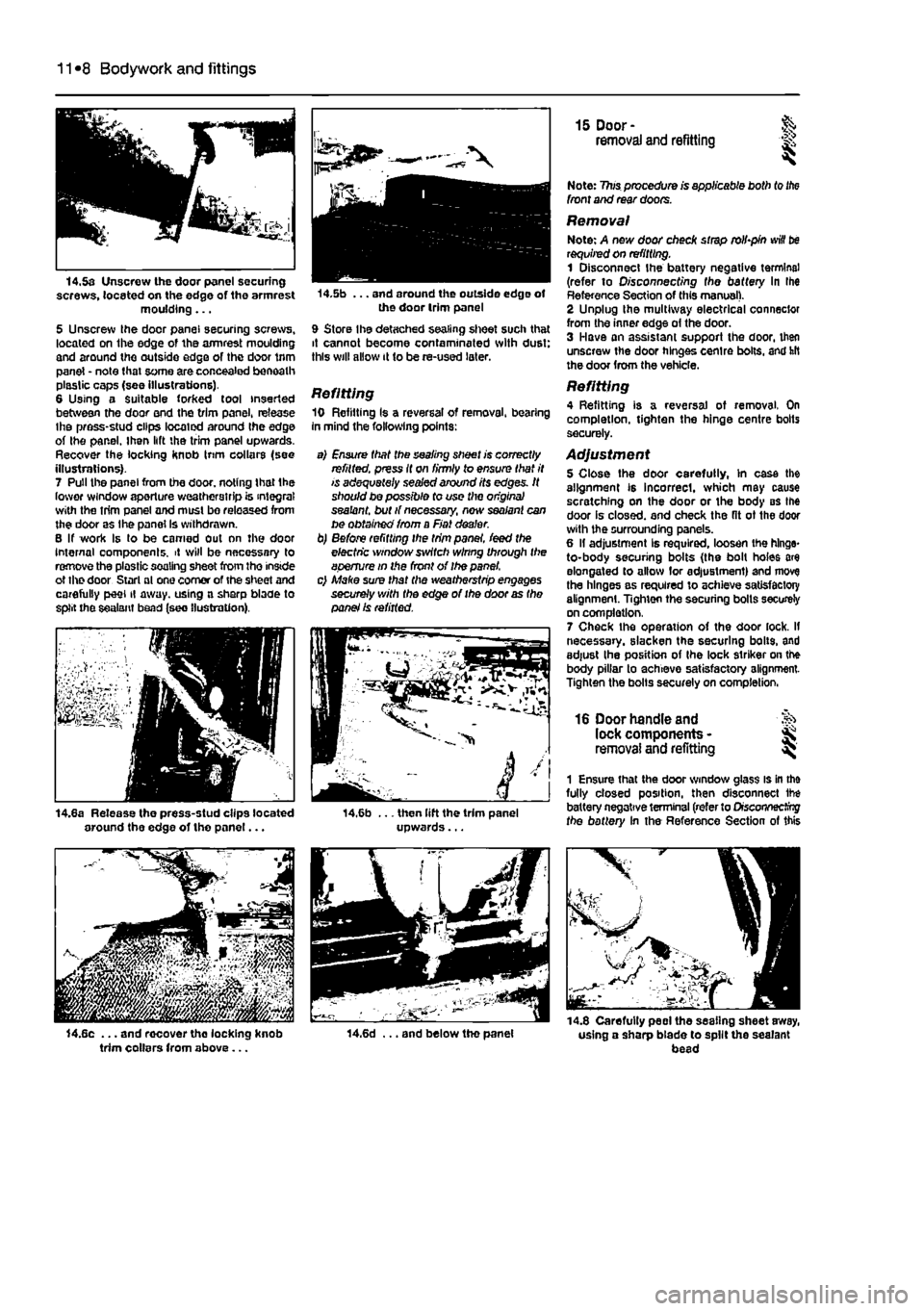
11
*8 Bodywork and fittings
14.5a Unscrew the door panel securing screws, located on the edge of the armrest moulding... 5 Unscrew Ihe door panel securing screws, located on Ihe edge of the armrest moulding and around the outside edge of the door trim panel - note that some are concealed beneath plastic caps (see illustrations). 6 Using a Suitable forked tool inserted between the door end the trim panel, release Ihe press-stud clips located around Ihe edge of Ihe panel. Ihen lift the trim panel upwards. Recover the locking knob Inm collars (see illustrations). 7 Pull the panel from the door, noting that Ihe lower window aperture weatherstrip is integral with the trim panel and must bo released from the door as the panel Is withdrawn. B If work Is lo be earned out nn the door Internal oomponenls. it will be necessary to remove the plastic soaling sheet from tho inside ot the door Starl ol one comer of the sheet and carefully peel il away, using a sharp blade to split the sealant bead (see (lustration).
j
14.8a Release the press-stud clips located around the edge of tho panel...
trim collars from above...
14.5b ... and around the outside edge of the door trim panel
9 Store Ihe detached sealing sheet such that it cannot become contaminated with dust: this will allow it to be re-used later.
Refitting 10 Refilling Is a reversal of removal, bearing in mind the following points:
a) Ensure that the sealing sheet is correctly refitted, press it on firmly to ensure that it is adequately sealed around its edges. It should be possible fo use the origins} sealant, but if necessary, new sealant can be obtained from a Fiat dealer. b) Before refitting the trim panel, feed the electric window switch wlnng through the aperture in the front of Ihe panel. c) Make sure that the weatherstrip engages securely with the edge of the door as the panel Is refitted.
i4,6b ... then lift the trim panel upwards...
14.6d ... and below tho panel
15 Door- & removal and refitting is
Note: 7?ws procedure is applicable both to
the
front and rear doors.
Removal Note: A new door check strap rolbpin
win
be requited on refitting. 1 Disconnect the battery negative terminal (refer to O/sconoecf/ng fhe battery In Ihe Reference Section of this manual). 2 Unplug Ihe multiway electrical connector from the inner edge of the door. 3 Have an assistant support the door, then unscrew the door hinges centre bolts, and hit the door from the vehicle.
Refitting 4 Refitting is a reversal of removal. On completion, tighten the hinge centre bolts securely.
Adjustment 5 Close the door carefully, In case the alignment is incorrect, which may cause scratching on the door or the body BS the door is closed, and check the fit ot the door with the surrounding panels. 6 II adjustment Is required, loosen the hinge-to-body securing bolts (the bolt holes are elongated to allow lor adjustment) and move the hinges as required to achieve satisfactory alignment. Tighten the securing bolls securely on completion. 7 Check the operation of the door lock. If necessary, slacken the securing bolts, and adjust Ihe position of Ihe lock striker on the body pillar to achieve satisfactory alignment-Tighten the bolts securely on completion,
16 Door handle and lock components -removal and refitting ^
1 Ensure that the door window glass is in the fully closed position, then disconnect ihe battery negative terminal (refer to Drscoryiecfrrg fhe battery In the Reference Section of this
•
m-i -14.8 Carefully peel the sealing sheet away, using a sharp blade to spilt the sealant bead
Page 210 of 225
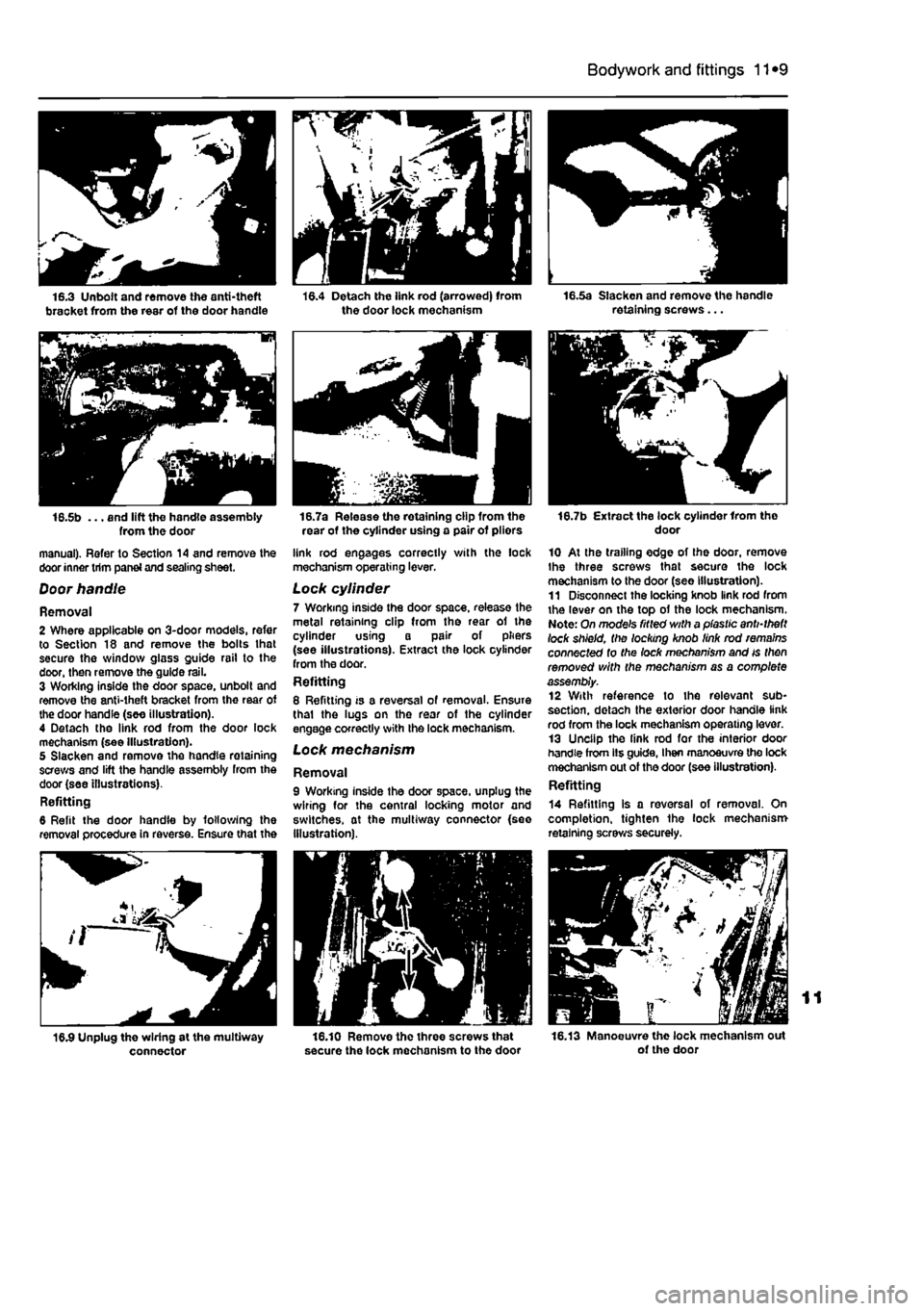
Bodywork and fittings
11
*9
16.5b ... and lift the handle assembly from the door manual). Refer to Section 14 and remove the door inner trim panei and sealing sheet.
Door handle
Removal 2 Where applicable on 3-door models, refer to Section 18 and remove the bolts lhat secure the window glass guide rail to the door, then remove the guide rail. 3 Working inside the door space, unbolt and remove the anti-theft bracket from the rear of the door handle (see illustration). 4 Detach the link rod from the door lock mechanism (see Illustration). 5 Slacken and remove the handle retaining screws and lift the handle assembly from the door (see illustrations). Refitting 6 Refit the door handle by following the removal procedure in reverse. Ensure that the
connector
16.7a Release the retaining clip from the rear of the cylinder using a pair of pliors
link rod engages correctly with the lock mechanism operating lever.
Lock cylinder 7 Working inside the door space, release the metal retaining clip from the rear of the cylinder using a pair of pliers (see illustrations). Extract the lock cylinder from the door. Refitting 8 Refitting is a reversal of removal. Ensure thai the lugs on the rear of the cylinder engage correctly with the lock mechanism. Lock mechanism
Removal 9 Working inside the door space, unplug the wiring for the central locking motor and switches, at the multiway connector {see Illustration).
16.10 Remove the three screws that secure the lock mechanism to the door
16.7b Extract the lock cylinder Irom tho door
10 At the trailing edge of the door, remove Ihe three screws that secure the lock mechanism to the door (see Illustration). 11 Disconnect the locking knob link rod from the lever on the top of the lock mechanism. Note: On mode's fitted with a plastic anti-theft lock shield, the locking knob link rod remains connected to the lock mechanism and is then removed with the mechanism as a complete assembly. 12 With reference to the relevant sub-section. detach the exterior door handle link rod from the lock mechanism operating lever. 13 Unclip the link rod for the interior door handle from lis guide, I hen manoeuvre the lock mechanism out of the door (see illustration). Refitting
14 Refitting is a reversal of removal. On completion, tighten the lock mechanism retaining screws securely.
16.13 Manoeuvre the lock mechanism out of the door
Page 211 of 225
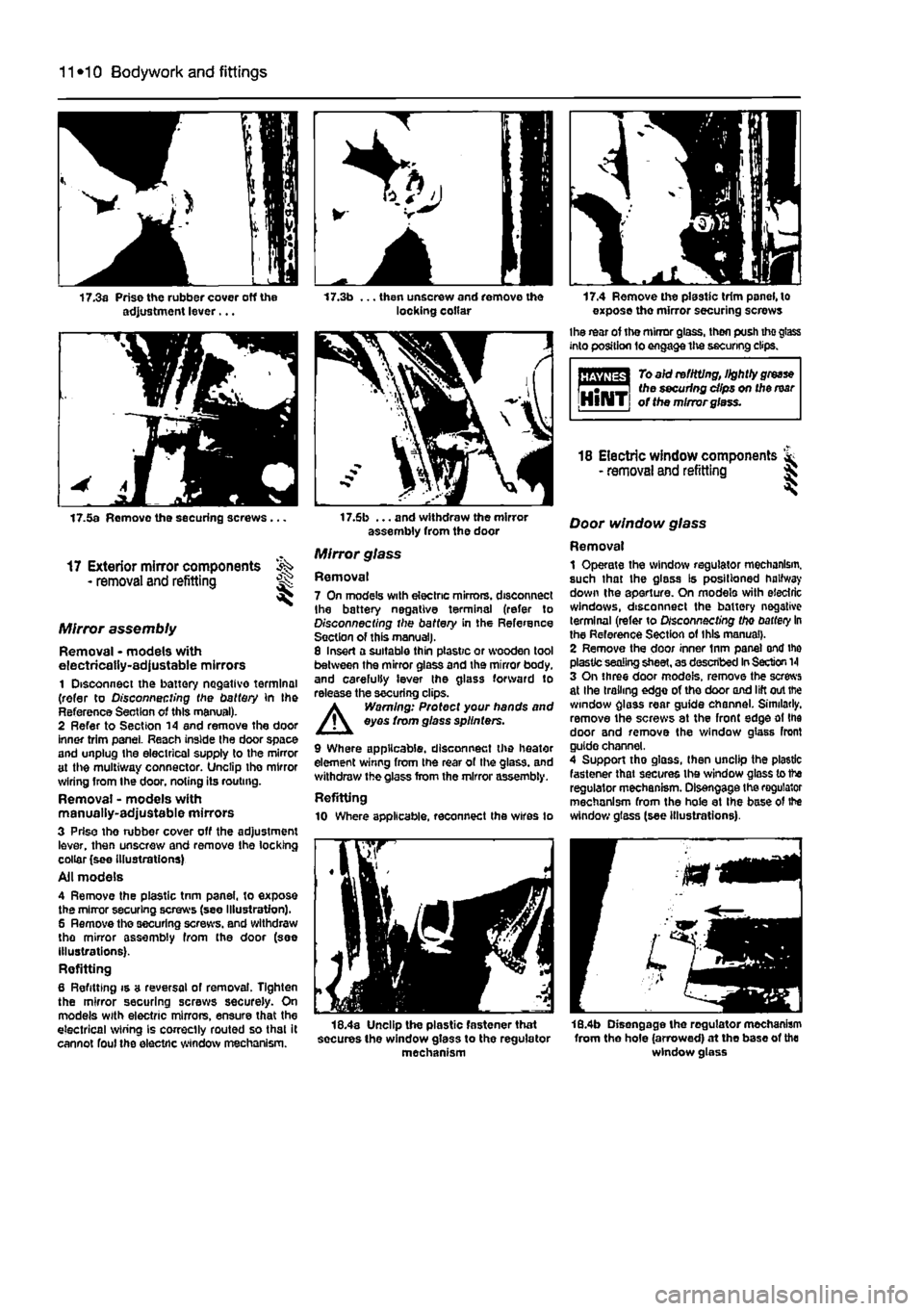
11
*10 Bodywork and fittings
17.3a Prise the rubber cover off the adjustment lever... 17.3b ... then unscrew and remove the locking collar 17.4 Remove the plastic trim panel, to expose the mirror securing screws
Ihe rear of the mirror glass, then push tho glass into position fo engage the securing clips.
To aid re fitting, lightly
grease
^•-.—i the securing dips on the mar IjlllliTj of the mirror glass.
17.5a Remove the securing screws .
17 Exterior mirror components - removal and refitting
Mirror assembly
Removal • models with electrically-adjustable mirrors 1 Disconnect the battery negative terminal (refer to Disconnecting the battery in the Reference Section of this manual). 2 Refer to Section 14 and remove the door inner trim panel. Reach inside the door space and unplug the electrical supply to the mirror at the multiway connector. Unclip tho mirror wiring from Ihe door, noting its routing. Removal - models with manually-adjustable mirrors 3 Prise tho nibber cover off the adjustment lever, then unscrew and remove the locking collar (see Illustrations) Ail models 4 Remove the plastic tnm panel, to expose the mirror securing screws (see Illustration). 6 Remove the securing screws, and withdraw the mirror assembly from the door (see illustrations). Refitting 6 Refitting is a reversal of removal. Tighten the mirror securing screws securely. On models with electric mirrors, ensure that the electrical wiring is correctly routed so that it cannot foul the electric window mechanism.
17.6b ... and withdraw the mirror assembly from the door
Mirror glass
Removal 7 On models with electric mirrors, disconnect Ihe battery negative terminal (refer to Disconnecting the battery in the Reference Section of this manual). 8 Insert a suitable thin plastic or wooden tool between the mirror glass and the mirror body, and carefully lever the glass forward to release the securing clips. A Warning: Protect your hands and eyes from glass sp//nfers.
9 Where applicable, disconnect the heater element winng from the rear of the glass, and withdraw the glass from the mirror assembly. Refitting 10 Where applicable, reconnect the wires to
18 Electric window components & - removal and refitting 5
Door window glass
Removal 1 Operate the window regulator mechanism, such that the glass Is positioned halfway down the aperture. On modelo with electric windows, disconnect the battery negative terminal (refer to Disconnecting tho
battery
In the Reference Section of this manual). 2 Remove the door inner inm pane) ond ihe plastic sealing sheet, as described
In
Section
1
3 On three door models, remove the screws at Ihe trailing edge of the door and lift out the window glass rear guide channel. Similarly, remove the screws at the front edge at the door and remove the window glass front guide channel. 4 Support tho glass, (hen unclip the plastic fastener that secures the window glass to the regulator mechanism. Disengage the regulator mechanism from the hole at Ihe base of the window glass (see illustrations).
18.4a Unclip the plastic fastener that socures the window glass to the regulator mechanism
18.4b Disengage the regulator mechanism from the hole (arrowed) at the base of the window glass
Page 212 of 225
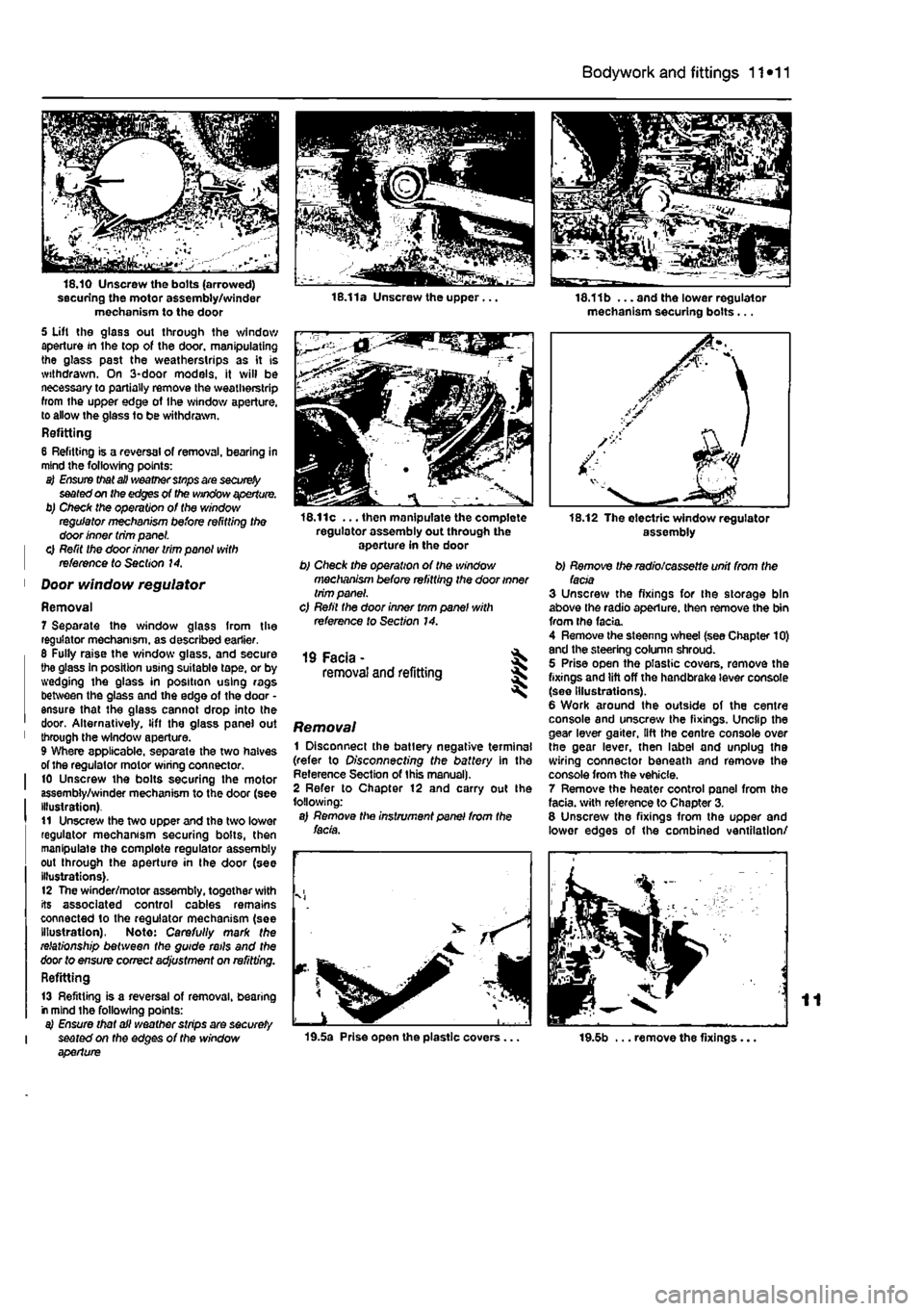
Bodywork and fittings
11
*11
securing the motor assembly/winder mechanism to the door 5 Uft the glass out through the window aperture in the top of the door, manipulating the glass past the weatherstrips as it is withdrawn. On 3-door models, it will be necessary to partially remove the weatherstrip from the upper edge of Ihe window aperture, to allow the glass to be withdrawn. Refitting 6 Refitting is a reversal of removal, bearing in mind the following points: a) Ensure that all weather stnps are
securely
seated on the edges of the window aperture. b) Check the operation of the window regulator mechanism before refitting the door inner trim panel. | 0 Refit the door inner trim panel with | reference to Section 14.
1 Door window regulator
Removal 7 Separate the window glass from the regulator mechanism, as described earlier. 6 Fully raise the window glass, and secure the glass In position using suitable tape, or by wedging the glass in position using rags between the glass and the edge of the door • ensure that the glass cannot drop into the door. Alternatively, lift the glass panel out 1 through the window aperture. 9 Where applicable, separate the two halves of the regulator motor wiring connector. I 10 Unscrew the bolts securing the motor assembly/winder mechanism to the door (see Illustration). t1 Unscrew the two upper and the two lower regulator mechanism securing bolts, then manipulate the complete regulator assembly out through the aperture in the door (see illustrations). 12 The winder/motor assembly, together with its associated control cables remains connected to the regulator mechanism (see Illustration), Note: Carefully mark the relationship between the guide rails and the door to ensure correct adjustment on refitting. Refitting
13 Refitting is a reversal of removal, bearing r mind the following points: a) Ensure that all weather strips are securely I seated on the edges of the window aperture
16.11c ... then manipulate the complete regulator assembly out through the aperture in the door b) Check the operation of the window mechanism before refitting the door inner trim panel. c) Refil the door inner tnm panel with reference to Section 14.
19 Facia - ^ removal and refitting 5
Removal 1 Disconnect the batlery negative terminal (refer to Disconnecting the battery in the Reference Section of this manual). 2 Refer to Chapter 12 and carry out Ihe following: a) Remove the instrument panel from the facia.
19.5a Prise open the plastic covers...
18.11b ... and the lower regulator mechanism securing bolts...
assembly
b) Remove the radio/cassette unit from the facia 3 Unscrew the fixings for the storage bin above the radio aperture, then remove the bin from the facia. 4 Remove the steenng wheel (see Chapter 10) and the steering column shroud. 5 Prise open the plastic covers, remove the fixings and lift off the handbrake lever console (see Illustrations). 6 Work around the outside of the centre console and unscrew the fixings. Unclip the gear lever gaiter, lift the centre console over the gear lever, then label and unplug the wiring connector beneath and remove the console from the vehicle. 7 Remove the heater control panel from the facia, with reference to Chapter 3. 8 Unscrew the fixings from the upper and lower edges of the combined ventilation/
19.5b ... remove the fixings...
Page 214 of 225
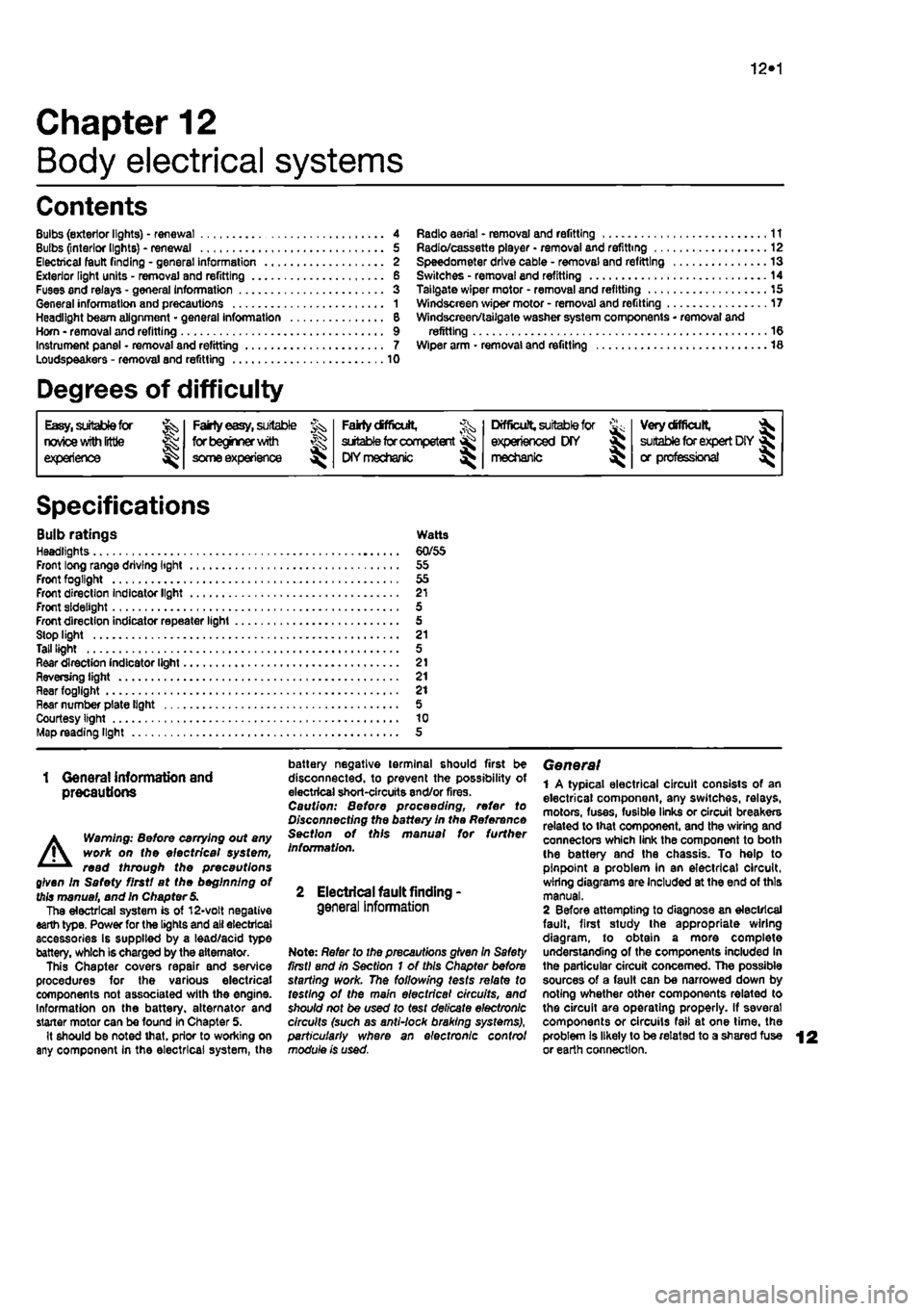
10*1
Chapter 12
Body electrical systems
Contents
Bulbs (exterior lights) - renewal 4 Bulbs (interior lights) - renewal 5 Electrical fault finding - general information 2 Exterior light units - removal and refitting 6 Fuses and relays - general Information 3 General information and precautions 1 Headlight beam alignment • general Information 6 Horn • removal and refitting 9 Instrument panel - removal and refitting 7 Loudspeakers - removal and refitting 10
Degrees of difficulty
Radio aerial - removal and refitting 11 Radio/cassette player • removal and refitting 12 Speedometer drive cable - removal and refitting 13 Switches - removal end refitting 14 Tailgate wiper motor - removal and refitting 15 Windscreen wiper motor - removal and refitting 17 Windscreen/tailgate washer system components • removal and refitting 16 Wiper arm • removal and refitting 18
Easy,
statable for ^
novice with liffle
|| experience ^
Fairly
easy,
suitable for beginner with ^ some experience ^
Fabtycffficiit,
suitable
for competent ^
DIY
mechanic ^
Difficult, suitable for
^ experienced DIY JR mechanic
Very difficult,
A,
suitable
for
expert DIY
Sj or professional ^
Specifications
Bulb ratings Watts Headlights 60/55 Front long range driving light 55 Front fogllght 55 Front direction Indicator light 21 Front sidelight 5 Front direction indicator repeater light 5 Stop light 21 Tall light 5 Rear direction indicator light 21 Reversing light 21 near fogllght 21 Hear number plate light 5 Courtesy light 10 Map reading light 5
1 Genera! information and precautions
A
Warning: fie/Ore carrying out any work on the electrical system, read through the precautions given in Safety first! at the beginning of this manual, and in Chapter 8. The electrical system is of 12-volt negative earth type. Power for the lights and all electrical accessories is supplied by a lead/acid type battery, which is charged by the alternator. This Chapter covers repair and service procedures for the various electrical components not associated with the engine. Information on the battery, alternator and starter motor can be found in Chapter 5. It should be noted that, prior to working on any component In the electrical system, the
battery negative terminal should first be disconnected, to prevent the possibility of electrical short-circuits and/or fires. Caution: Before proceeding, refer to Disconnecting the battery In the Reference Section of this manual for further information.
2 Electrical fault finding-general information
Note: Refer to the precautions given In Safety first! and in Section 1 of this Chapter before starting work. The following tests relate to testing ot the main electrical circuits, and should not be used to test delicate electronic circuits (such as antHock braking systems), particularly where an electronic con fro/ module is used.
General 1 A typical electrical circuit consists of an electrical component, any switches, relays, motors, fuses, fusible links or circuit breakers related to that component, and the wiring and connectors which link the component to both the battery and the chassis. To help to pinpoint a problem in an electrical circuit, wiring diagrams are Included at the end of this manual. 2 Before attempting to diagnose an electrical fault, first study the appropriate wiring diagram, to obtain a more complete understanding of the components included In the particular circuit concerned. The possible sources of a fault can be narrowed down by noting whether other components related to the circuit are operating properly. If several components or circuits fait at one time, the problem Is likely to be related to a shared fuse or earth connection.
Page 223 of 225
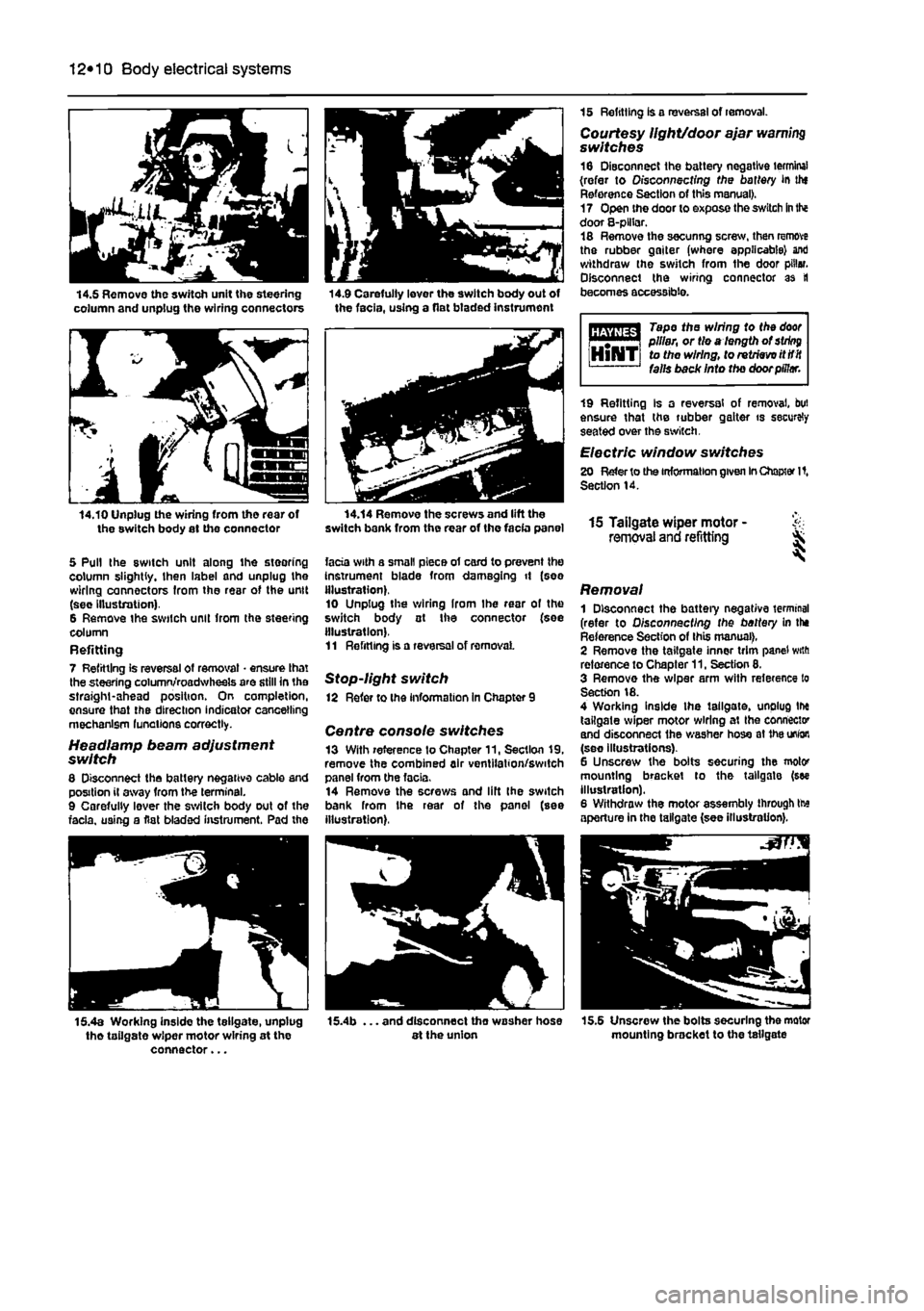
12*10 Body electrical systems
14.5 Remove the switch unit the steering column and unplug the wiring connectors 14.9 Carefully lever the switch body out of the facia, using a flat btaded instrument
14.10 Unplug the wiring from tho rear of the switch body at the connector
5 Pull the switch unit along ihe steering column slightly, then label and unplug the wiring connectors from the rear of the unit (sec Illustration). 6 Remove the switch unit from the steering column Refitting 7 Refitting is reversal of removal • ensure that the steering column/roadwheels are still in the straight-ahead position. On completion, ensure that the direction indicator cancelling mechanism lunations correctly.
Headlamp beam adjustment switch 8 Disconnect the battery negative cable and position il away from the terminal. 9 Carefully lever the switch body out of the facia, using a flat bladed instrument. Pad the
15 Refitting is a reversal of removal. Courtesy light/door ajar warning switches 16 Disconnect the battery negative terminal (refer to Disconnecting the battery in thf Reference Section of this manual). 17 Open the door to expose the switch
in
the door 8-plHar. 18 Remove the secunng screw, then remove the rubber gaiter (where applicable) ant) withdraw the switch from the door pillar. Disconnect the wiring connector as tl becomes accessible.
Tape the wiring to the
door
i m | pillar, or tie a length of
string
HlNTi to the wiring, to retrieve itttit falls back Into the door pillar.
14.14 Remove the screws and lift the switch bank from the rear of the facia panel
facia with a small piece of card to prevent the Instrument blade from damaging it (see illustration). 10 Unplug the wiring Irom Ihe rear of the switch body at Ihe connector (see illustration). 11 Refitting is a reversal of removal
Stop-light switch 12 Refer to the information in Chapter 9
Centre console switches 13 With reference to Chapter 11, Section 19, remove the combined air ventilation/switch panel from the facia. 14 Remove the screws and lift Ihe switch bank from Ihe rear of the panel (see illustration),
19 Refitting Is a reversal of removal, but ensure that the rubber gaiter is securely seated over the switch.
Electric window switches 20 Refer to the information given
In
Chapter It, Section 14.
15 Tailgate wiper motor - & removal and refitting ^
Removal 1 Disconnect the battery negative terminal (refer to Disconnecting the battery in the Reference Section of this manual), 2 Remove the tailgate inner trim panel with reference to Chapter 11, Section 8. 3 Remove the wiper arm with reference to Section 18. 4 Working inside the tailgate, unplug tlx tailgate wiper motor wiring at Ihe connector and disconnect the washer hose at
1he
union (see illustrations). 6 Unscrew the bolts securing the motor mounting bracket to the tailgate (see illustration). 6 Withdraw the motor assembly through tte aperture in the tailgate (see illustration).
15.4a Working inside the tellgate, unplug tho tailgate wiper motor wiring at the connector...
. and disconnect tho washer hose at the union 15.5 Unscrew the bolts securing the motor mounting bracket to the tailgate
Page 224 of 225
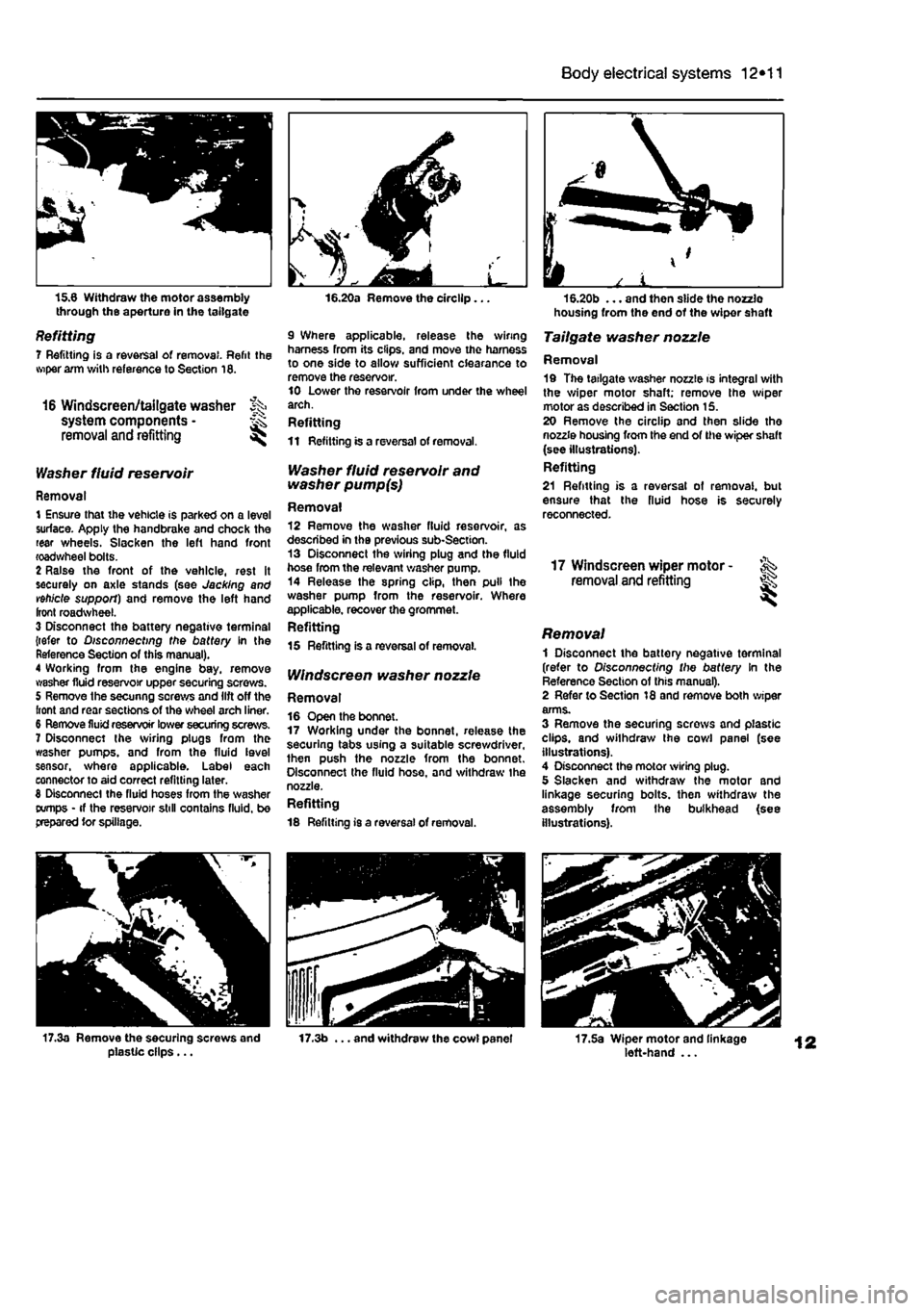
Body electrical systems 12*11
15.6 Withdraw the motor assembly through the aperture in the tailgate
Refitting 7 Refitting is a reversal of removal. Refit the wiper arm with reference to Section 16.
16 Windscreen/tailgate washer % system components • ^ removal and refitting ^
Washer fluid reservoir
Removal 1 Ensure that the vehicle is parked on a level surface. Apply the handbrake and chock the rear wheels. Slacken the left hand front roadwheel bolts. 2 Raise the front of the vehicle, rest it securely on axle stands (see Jacking and vehicle support) and remove the left hand front roadwheel. 3 Disconnect the battery negative terminal {refer to Disconnecting the battery In the Reference Section of this manual). 4 Working from the engine bay, remove washer fluid reservoir upper securing screws. 5 Remove the secunng screws and lift off the front and rear sections of the wheel arch liner. 6 Remove fluid reservoir lower securing screws. 7 Disconnect the sviring plugs from the washer pumps, and from the fluid level sensor, where applicable. Label each connector to aid correct refitting later. 8 Disconnect the fluid hoses from the washer tx/mps • if the reservoir still contains fluid, be prepared tor spillage.
16.20a Remove the circllp...
9 Where applicable, release the wiring harness from its clips, and move the harness to one side to allow sufficient clearance to remove the reservoir. 10 Lower the reservoir from under the wheel arch. Refitting 11 Refitting is a reversal of removal.
Washer fluid reservoir and washer pump(s)
Removal 12 Remove the washer fluid reservoir, as described in the previous sub-Section. 13 Disconnect the wiring plug and the fluid hose from the relevant washer pump. 14 Release the spring clip, then pull the washer pump from the reservoir. Where applicable, recover the grommet. Refitting 15 Refitting is a reversal of removal.
IV/nctecreen washer nozzle
Removal 16 Open the bonnet. 17 Working under the bonnet, release the securing tabs using a suitable screwdriver, then push the nozzle from the bonnet. Disconnect the fluid hose, and withdraw the nozzle. Refitting 18 Refitting is a reversal of removal.
housing from the end of the wiper shaft
Tailgate washer nozzle
Removal 19 The tailgate washer nozzle is integral with the wiper motor shaft; remove the wiper motor as described in Section 15. 20 Remove the circllp and then slide the nozzle housing from the end of the wiper shaft (see illustrations). Refitting 21 Refitting is a reversal of removal, but ensure that the fluid hose is securely reconnected.
17 Windscreen wiper motor -removal and refitting ^
Removal 1 Disconnect the battery negative terminal (refer to Disconnecting the battery In the Reference Section of this manual). 2 Refer to Section 18 and remove both wiper arms. 3 Remove the securing screws and plastic clips, and withdraw the cowl panel (see illustrations). 4 Disconnect the motor wiring plug. 5 Slacken and withdraw the motor and linkage securing bolts, then withdraw the assembly from the bulkhead (see illustrations).
17.3a Remove the securing screws and plasUc clips... 17.3b ... and withdraw the cowl panel 17.5a Wiper motor and linkage left-hand ...
Page 225 of 225

12*12 Body electrical systems
17.0 If desired, the motor may be detached from the linkage by removing the securing screws (arrowed) 17.5b ... and right-hand securing bolts (arrowed)
6 If desired, the motor may be detached from the linkage by removing the securing screws (see illustration).
Refitting 7 Refitting Is a reversal of removal, but ensure that the motor drrve is in the 'parked' position before reconnecting ihe crank arm.
18 Wiper arm - fe removal and refitting
Removal 1 Operate the wiper motor, then switch ft off
so that the wiper arm returns to tha at-rest/parked position, 2 If a windscreen or tailgate wiper Is being removed, stick a length of masking tape on tha glass below ihe edge of tha wiper blade, to use as an alignment aid on refitting. 3 Where applicable, lift up the wiper arm spindle nut cover, then slacken and remove the spindle nut (see illustrations). 4 Lift the blade of
I
the glass, and pull the wiper arm off its spindle. If necessary, the aim can be carefully lavered off the spindle using a suitable fiat-bladed screwdriver. If both windscreen wiper arms are removed, note their locations, as different arms are fitted to the driver's and passenger's sides.
Refitting 5 Ensure that the wiper arm and spindle splines are dean and dry. 6 When refitting a windscreen or tailgate wiper arm, refit tha arm to the spindle,
aMgnhg
the wiper blade with the tape fitted before removal. If both windscreen wiper arms have been removed, ensure that the arms are refitted to their correct positions as noted before removal. 7 Rflfit the spindle nut, tighten It securely,
ana
where applicable, clip the nut cover back into position.
expert22 fl/in http://rutracker.org