check engine light FIAT PUNTO 1998 176 / 1.G User Guide
[x] Cancel search | Manufacturer: FIAT, Model Year: 1998, Model line: PUNTO, Model: FIAT PUNTO 1998 176 / 1.GPages: 225, PDF Size: 18.54 MB
Page 29 of 225
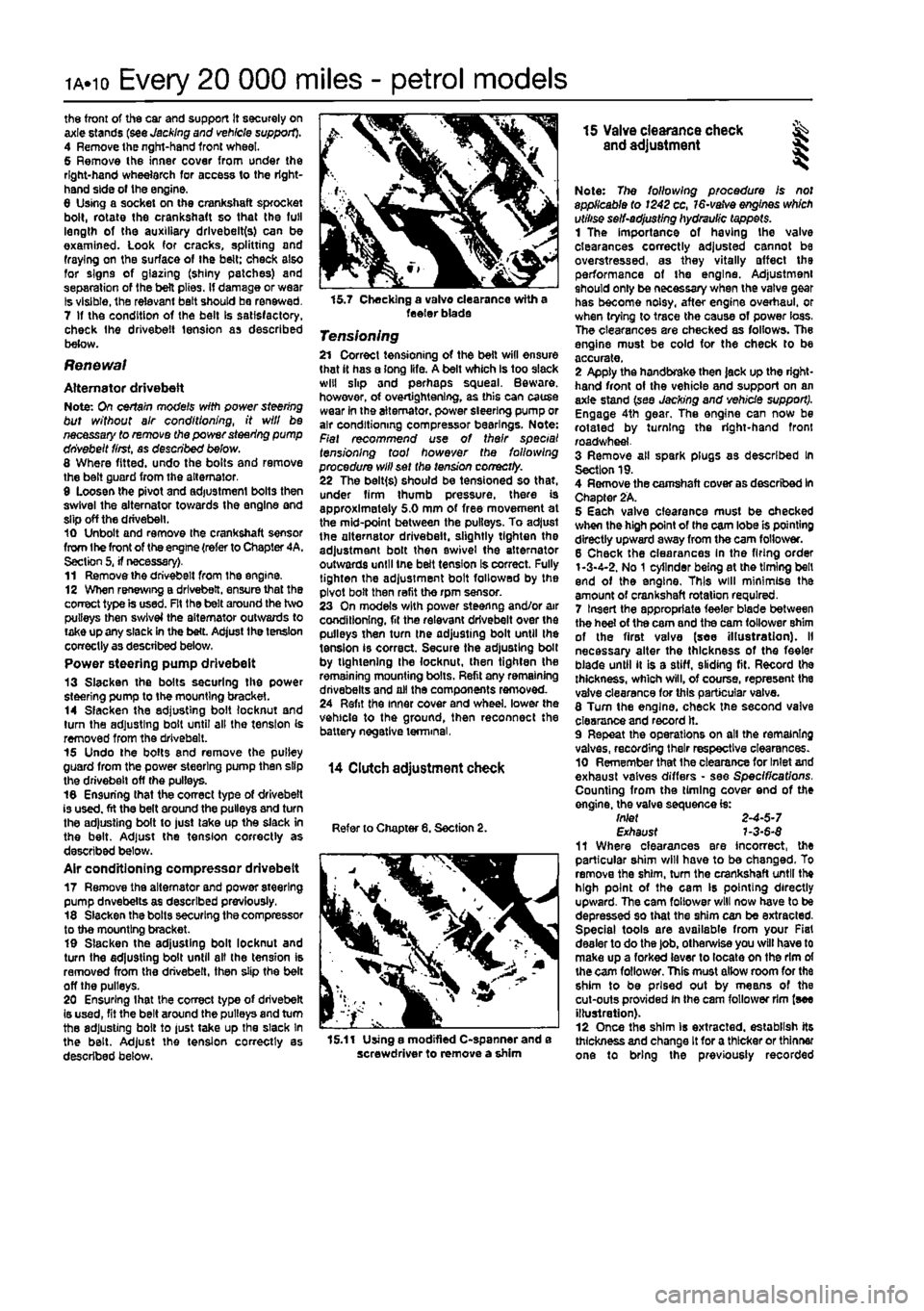
ia.io Every 20 000 miles - petrol models
the front of the car and support It securely on axle stands (see Jacking and vehicle support}. 4 Remove the nght-hand front wheel. 5 Remove the inner cover from under the right-hand wheeiarch for access to the right-hand side of the engine. 0 Using a socket on the crankshaft sprocket boll, rotate the crankshaft so that the full length of the auxiliary drlvebelt(s) can be examined. Look for cracks, splitting and fraying on the surface of the belt: check also for signs of glazing (shiny patches) and separation of the belt plies. If damage or wear Is visible, the relevant belt should be renewed. 7 If the condition of the belt Is satisfactory, check Ihe drivebeit tension as described below.
Renewal
Alternator drivebeit Note: On certain models with power steering but without air conditioning, it will be necessary to remove the power steering pump drivebeit ffrst, as described below. 8 Where fitted, undo the bolts and remove the belt guard from the alternator. 9 Loosen the pivot and adjustment bolts then swivel the alternator towards the engine and slip off the drivebeit. 10 Unbolt and remove the crankshaft sensor from Ihe front of the engine (refer to Chapter 4A. Section 5, if necessary). 11 Remove the drivebeit from the engine. 12 When renewing a drivebeit. ensure that the correct type is used. Fit the belt around the two pulleys then swivel the alternator outwaids to take up any slack in the betL Adjust the tension correctly as described below. Power steering pump drivebeit 13 Slacken the bolts securing the power steering pump to the mounting bracket. 14 Slacken the adjusting bolt locknut and turn the adjusting boit until all the tension is removed from the drivebeit. 15 Undo the bolts and remove the pultey guard from the power steering pump then slip the drivebeit off (he pulleys. 18 Ensuring that the correct type of drivebeit is used, fit the belt around the pulleys and turn the adjusting bolt to just take up the slack in the belt. Adjust the tension correctly as described below. Air conditioning compressor drivebeit 17 Remove the alternator and power steering pump dnvebelts as described previously. 18 Slacken the bolts securing the compressor to the mounting bracket. 19 Slacken the adjusting bolt locknut and turn the adjusting bolt until alt the tension is removed from the drivebeit, then slip the belt off the pulleys. 20 Ensuring lhat the correct type of drivebeit is used, fit the belt around the pulleys and turn the adjusting bolt to just take up the slack In the belt. Adjust the tension correctly as described below.
15.7 Checking a valve clearance with a feeler blade
Tensioning 21 Correct tensioning of the belt will ensure that it has a long life. A belt which Is too slack will slip and perhaps squeal. Beware, however, of overtightening, as this can cause wear in the alternator, power steering pump or air conditioning compressor bearings. Note: Fiat recommend use of their special tensioning tool however the fallowing procedure will set the tension correctly. 22 The belt(s) should be tensioned so that, under firm thumb pressure, there is approximately 5.0 mm of free movement at the mid-point between the pulleys. To adjust the alternator drivebeit, slightly tighten the adjustment bolt then swivel the alternator outwards until tne beft tension Is correct. Fully tighten the adjustment bolt followed by the pivot bolt then refit the rpm sensor. 23 On models with power steering and/or air conditioning, fit the relevant drivebeit over the pulleys then turn the adjusting bolt until the tension is correct. Secure the adjusting bolt by tightening Ihe locknut, then tighten the remaining mounting bolts. Refit any remaining dnvebelts and all the components removed. 24 Refit the inner cover and wheel, lower the vehicle to the ground, then reconnect the battery negative terminal,
14 Clutch adjustment check
Refer to Chapter 8. Section 2.
15.11 Using a modified C-spanner and e screwdriver to remove a shim
15 Valve clearance check ^ and adjustment S
Note: The following procedure Is not applicable to 1242 cc,
16-vatve
engines which utilise self-adjusting hydraulic tappets. 1 The importance of having the valve clearances correctly adjusted cannot be overstressed, as they vitally affect the performance of the engine. Adjustment should only be necessary when the valve gear has become noisy, after engine overhaul, or when trying to trace the cause of power loss. The clearances are checked as follows. The engine must be cold for the check to be accurate. 2 Apply the handbrake then jack up the right* hand front of the vehicle and support on an axle stand (see Jacking and vehicle support). Engage 4th gear. The engine can now be rotated by turning the right-hand front road wheel. 3 Remove all spark plugs as described In Section 19. 4 Remove the camshaft cover as described In Chapter 2A. 5 Each valve clearance must be checked when the high point of the cam lobe is pointing directly upward away from the cam follower. 6 Check the clearances In the firing order 1-3-4-2. No
1
cylinder being at the timing bell end of the engine. This will minimise the amount of crankshaft rotation required. 7 Insert the appropriate feeler blade between the heel of the cam and the cam follower shim of the first valve (see illustration). II necessary alter the thickness of the feeler blade until it is a stiff, sliding fit. Record the thickness, which will, of course, represent the valve clearance for this particular valve. 8 Tum the engine, check the second valve clearance and record it. 9 Repeat the operations on all the remaining valves, recording their respective clearances. 10 Remember that the clearance for Inlet and exhaust valves differs • see Specifications. Counting from the timing cover end of the engine, the valve sequence is: tnlet 2-4-5-7 Exhaust 7-3-6-$ 11 Where clearances are incorrect, the particular shim will have to be changed. To remove the shim, turn the crankshaft until the high point of the cam Is pointing directly upward. The cam follower will now have to be depressed so that the shim can be extracted. Special tools are available from your Fiat dealer to do the job, otherwise you will have to make up a forked (ever to locate on the rim of the cam follower. This must allow room for the shim to be prised out by means of the cut-outs provided in the cam follower rim {see illustration). 12 Once the shim is extracted, establish its thickness and change It for a thicker or thinner one to bring the previously recorded
Page 30 of 225
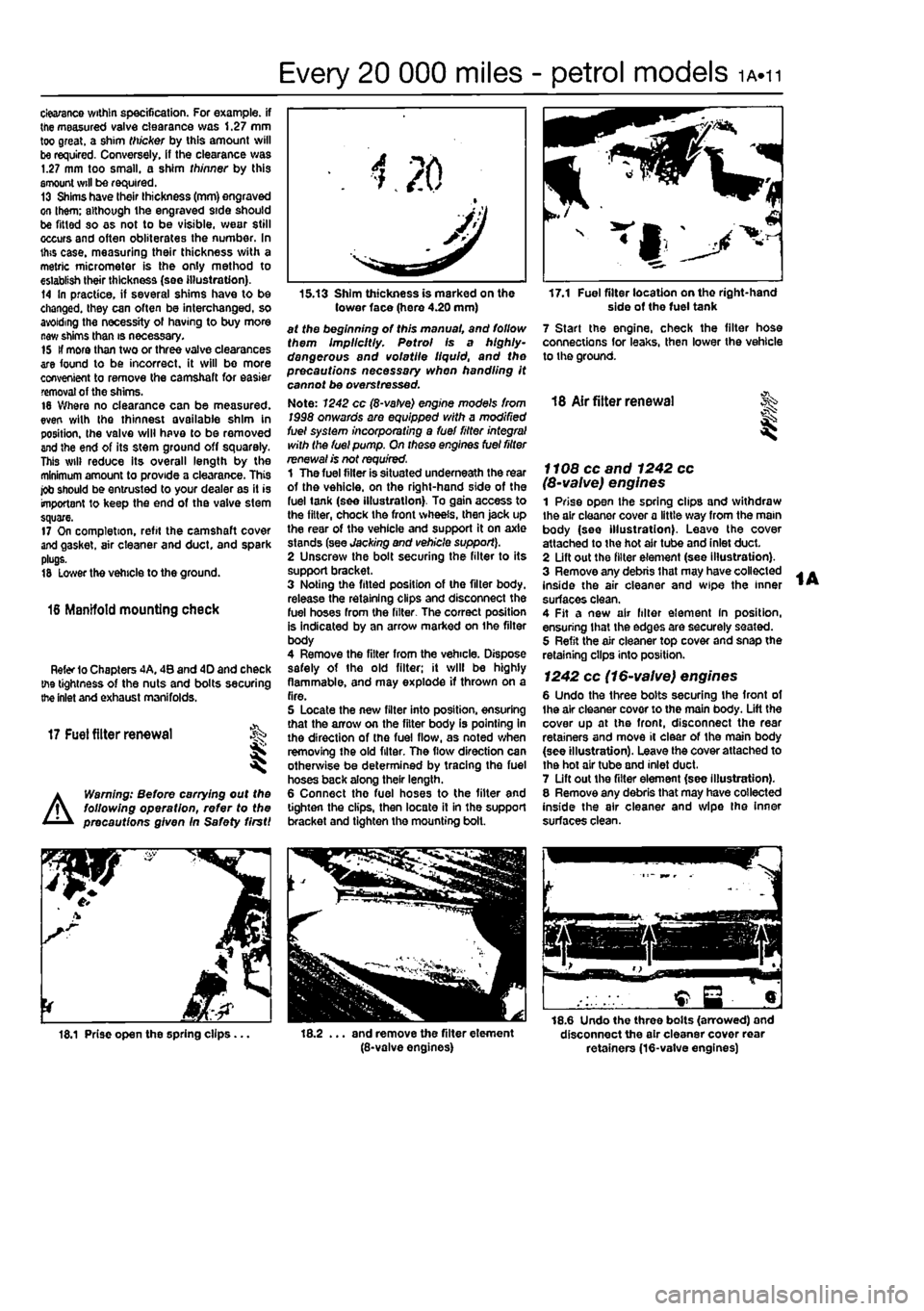
Every 20 000 miles - petrol models ia-h
clearance within specification. For example, if the measured valve clearance was 1.27 mm too great, a shim thicker by this amount will be required. Conversely, if the clearance was 1.27 mm too small, a shim thinner by this amount will be required. 13 Shims have their thickness (mm) engraved on them; although the engraved side should be fitted so as not to be visible, wear still occurs and often obliterates the number. In this case, measuring their thickness with a metric micrometer is the only method to establish their thickness (see illustration). t4 In practice, if several shims have to be changed, they can often be interchanged, so avoiding the necessity of having to buy more new shims than is necessary. 15 If more than two or three valve clearances are found to be incorrect, it will be more convenient to remove the camshaft for easier removal of the shims. 16 Where no clearance can be measured, even with the thinnest available shim in position, the valve will have to be removed and the end of its stem ground off squarely. This will reduce its overall length by the minimum amount to provide a clearance. This job should be entrusted to your dealer as it is important to keep the end of the valve stem square. 17 On completion, refit the camshaft cover and gasket, air cleaner and duct, and spark plugs. 18 lower the vehicle to the ground.
16 Manifold mounting check
Refer
1O
Chapters 4A. 48 and 4D and check tne tightness of the nuts and bolts securing the inlet and exhaust manifolds.
17
Fuel
filter renewal I I
Warning: Before carrying out the !\ f°llow'n9 operation, refer to the precautions given In Safety firstI A
15.13 Shim thickness is marked on the tower face (here 4.20 mm) at the beginning of this manual, and follow them Implicitly. Petrol Is a highly-dangerous and volatile liquid, and the precautions necessary when handling it cannot be overstressed. Note: 1242 cc (8-vatve) engine mode's from 1998 onwards are equipped with a modified fuel system incorporating a fuel fitter integral with the fuel pump. On these engines fuel filter renewal is not required. 1 The fuel filter is situated underneath the rear of the vehicle, on the right-hand side of the fuel tank (see illustration). To gain access to the filter, chock the front wheels, then jack up the rear of the vehicle and support it on axle stands (see Jacking and vehicle support). 2 Unscrew the bolt securing the filter to its support bracket. 3 Noting the fitted position of the filter body, release the retaining clips and disconnect the fuel hoses from the filter. The correct position is indicated by an arrow marked on ihe filter body 4 Remove the filter from the vehicle. Dispose safely of the old filter; it will be highly flammable, and may explode if thrown on a fire. 5 Locate the new filter into position, ensuring that the arrow on the filter body is pointing in the direction of the fuel flow, as noted when removing the old filter. The flow direction can otherwise be determined by tracing the fuel hoses back along their length. 6 Connect the fuel hoses to the filter and lighten the clips, then locate it in the support bracket and tighten the mounting bolt.
17.1 Fuel filter location on tho right-hand side of the fuel tank 7 Start the engine, check the filter hose connections for leaks, then lower the vehicle to the ground.
18 Air fitter renewal
I
f f 08 cc and 1242 cc (8-valve) engines 1 Prise open the spring clips and withdraw the air cleaner cover a little way from the main body (see illustration). Leave the cover attached to the hot air tube and inlet duct. 2 Lift out the filter element (see illustration). 3 Remove any debris that may have collected inside the air cleaner and wipe the inner surfaces clean. 4 Fit a new air filter element In position, ensuring that the edges are securely seated. 5 Refit the air cleaner top cover and snap the retaining clips into position.
1242 cc (16-valve) engines 6 Undo the three bolts securing the front of Ihe air cleaner cover to the main body. Lift the cover up at the front, disconnect the rear retainers and move it clear of the main body {see illustration). Leave the cover attached to the hot air tube and inlet duct. 7 Lift out the filter element (see illustration). 8 Remove any debris that may have collected inside the air cleaner and wipe the inner surfaces clean.
18.1 Prise open the spring clips... . and remove the filter element (8-valve engines)
18.6 Undo the three bolts (arrowed) and disconnect the air cleaner cover rear retainers (16-vatve engines)
Page 31 of 225
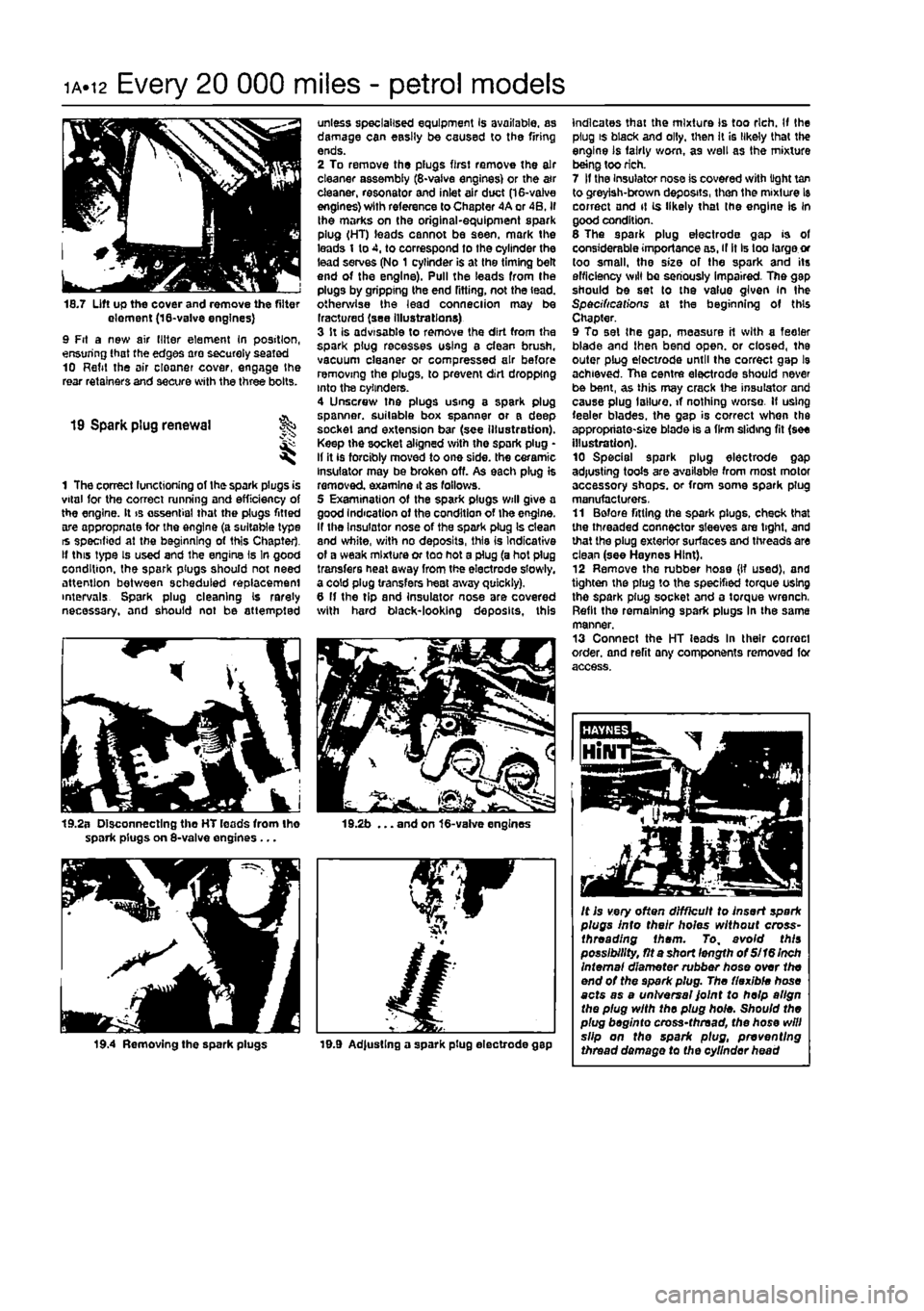
1A.12
Every 20 000 miles - petrol models
18.7 Lift up the cover and remove the filter element (18-va!ve engines) 9 Fit a new air (liter element In position, ensuring that the edges are securely seated 10 Refit the air cloaner cover, engage the rear retainers and secure with the three bolts.
19 Spark plug renewal
1 The correct functioning of the spark plugs is vital for the correct running and efficiency of the engine. It is essential that the plugs fitted are appropnate for the engine (a suitable type is specified at the beginning of this Chapter. If this type is used and the engine Is In good condition, the spark plugs should not need attention between scheduled replacement intervals Spark plug cleaning Is rarely necessary, and should not be attempted
19.2a Disconnecting tho HT leads from Iho spark plugs on 8-valve engines ...
19.4 Removing the spark plugs
unless specialised equipment Is available, as damage can easily be caused to the firing ends. 2 To remove the plugs first remove the air cleaner assembly (8-vaive engines) or the a»r cleaner, resonator and inlet air duct (16-valve engines) with reference to Chapter 4A or 4B. if the marks on the original-equipment spark plug (HT) leads cannot be seen, mark the leads 1 to 4, to correspond to the cylinder the lead serves (No 1 cylinder is at the timing belt end of the engine). Pull the leads from the plugs by gripping the end fitting, not the lead, otherwise the lead conneciion may be Iractured (see illustrations) 3 It is advisable to remove the dirt from the spark plug recesses using a clean brush, vacuum cleaner or compressed air before removing the plugs, to prevent dirt dropping into the cylinders. 4 Unscrew the plugs using a spark plug spanner, suitable box spanner or a deep socket and extension bar (see illustration). Keep the socket aligned with the spark plug • If it is forcibly moved to one side, the ceramic insulator may be broken off. As each plug is removed examine 4 as fallows. 5 Examination of the spark plugs will give a good Indication of the condition of the engine. If the Insulator nose of the spark plug Is clean and white, with no deposits, this is Indicative of a weak mixture or too hot a plug (a hot plug transfers heal away from the electrode slowly, a cold plug transfers heat away quickly). 6 If the tip and insulator nose are covered with hard black-looking deposits, this
19.2b ... and on 16-valve engines
19.9 Ad|ustlng a spark plug electrode gap
indicates that the mixture Is too rich. If the plug is black and oily, then It is likely that the engine is fairly worn, as well as the mixture being too rich. 7 If the Insulator nose is covered with light tan to greyish-brown deposits, then the mixture Is correct and it is likely that (he engine Is in good condition. 6 The spark plug electrode gap is of considerable importance as, if it Is too large or too small, the size of the spark and its efficiency will be seriously impaired. The gap should be set to the value given in the Specifications at the beginning of this Chapter. 9 To set the gap. measure it with a feeler blade and then bend open, or closed, the outer plug elect/ode until the correct gap l9 achieved. The centre electrode should never be bent, as this may crack the insulator and cause plug I allure, if nothing worse. If using feeler blades, the gap is correct when the appropriate-size blade is a firm sliding fit (see illustration). 10 Special spark plug electrode gap adjusting tools are available from most motor accessory shops, or from some spark plug manufacturers, 11 Before fitting the spark plugs, check that the threaded connector sleeves are tight, and that the plug exterior surfaces and threads are clean (see Haynes Hint). 12 Remove the rubber hose (If used), and tighten the plug to the specified torque using the spark plug socket and a torque wrench, Refit the remaining spark plugs In the same manner. 13 Connect the HT leads In their correct order, and refit any components removed for access.
It is very often difficult to insert spark plugs into their holes without cross-threading them. To, avoid this possibility, fit a short length of Si 16 Inch Internal diameter rubber hose over the end of the spark plug. The flexible hose acts as a universal Joint to help align the plug with the plug hole. Should the plug beginto cross-thread, the hose will slip on the spark plug, preventing thread damage to the cylinder head
Page 32 of 225
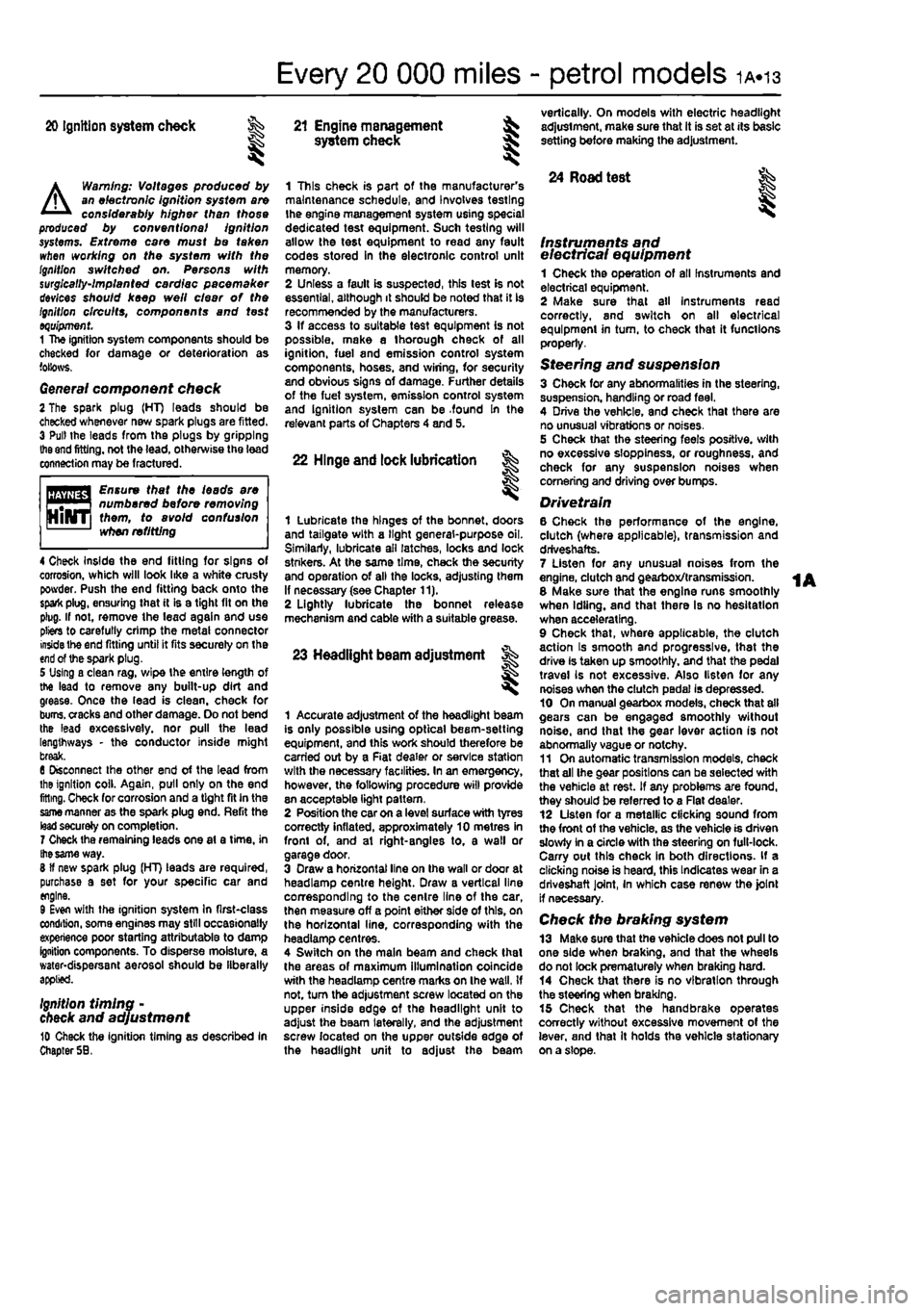
Every 20 000 miles - petrol models 1A.13
20 Ignition system check
81
21 Engine management system check
A
Warning: Voltages produced by an electronic ignition system are considerably higher than those produced by conventional ignition systems. Extreme care must be taken when working on the system with the Ignition switched on. Persons with surgically-Implanted cardiac pacemaker devices should keep well clear of the ignition circuits, components and test oquipment. 1 The ignition system components should be checked for damage or deterioration as follows.
General component check 2 The spark plug (HT) leads should be checked whenever new spark plugs are fitted. 3 Pull the leads from the plugs by gripping
the end
fitting, not the lead, otherwise the lead connection may be fractured.
Ensure that the leads are i numbered before removing i them, to avoid confusion when refitting
4 Check Inside the end fitting for signs of corrosion, which will look like a white crusty powder. Push the end fitting back onto the spark plug, ensuring that it is a tight fit on the plug. if not, remove the lead again and use pliers to carefully crimp the metal connector inside the end fitting until it fits securely on the
end
of the spark plug. 5 Using a clean rag, wipe Ihe emlre length of the lead to remove any built-up dirt and grease. Once the lead is clean, check for bums, cracks and other damage. Do not bend the lead excessively, nor pull the lead lengthways - the conductor inside might break. 6 Disconnect the other end of the lead from the ignition coll. Again, pull only on the end fitting. Check for corrosion and a tight fit in the
same
manner as the spark plug end. Refit the bad securely on completion. 7 Check the remaining leads one at a time, in
ihe same
way. 8 if new spark plug (HT) leads are required, purchase a set for your specific car and engine. 9 Even with the ignition system In first-class condition, some engines may still occasionally experience poor starting attributable to damp ignition components. To disperse moisture, a water-dispersant aerosol should be liberally
Ignition timing -
check
and adjustment 10 Check the ignition timing as described In Chapter 58.
1 This check is part of the manufacturer's maintenance schedule, and Involves testing Ihe engine management system using special dedicated test equipment. Such testing will allow the test equipment to read any fault codes stored in the electronic control unit memory. 2 Unless a fault is suspected, this test te not essential, although it should be noted that it is recommended by the manufacturers. 3 If access to suitable test equipment is not possible, make a thorough check of all ignition, fuel and emission control system components, hoses, and wiring, for security and obvious signs of damage. Further details of the fuet system, emission control system and ignition system can be .found In the relevant parts of Chapters 4 and 5.
22 Hinge and lock lubrication %
1
1 Lubricate the hinges of the bonnet, doors and tailgate with a light general-purpose oil. Similarly, lubricate ail latches, locks and lock strikers. At the same time, check the security and operation of all the locks, adjusting them If necessary (see Chapter 11). 2 Lightly lubricate the bonnet release mechanism and cable with a suitable grease.
23 Headlight beam adjustment % & ^
1 Accurate adjustment of the headlight beam is only possible using optical beem-setting equipment, and this work should therefore be carried out by a Fiat dealer or service station with the necessary facilities. In an emergency, however, the following procedure will provide an acceptable light pattern. 2 Position the car on a level surface with tyres correctly inflated, approximately 10 metres in front of. and at right-angles to, a wall or garage door, 3 Draw a horizontal line on the wall or door at headlamp centre height. Draw a vertical line corresponding to the centre line of the car, then measure off a point either side of this, on the horizontal line, corresponding with the headlamp centres. 4 Switch on the main beam and check that the areas of maximum illumination coincide with the headlamp centre marfcs on Ihe wall, if not. turn the adjustment screw located on the upper inside edge of the headlight unit to adjust the beam laterally, and the adjustment screw located on the upper outside edge of the headlight unit to adjust the beam
vertically. On models with electric headlight adjustment, make sure that it is set at its basic setting before making the adjustment.
24 Road test
Instruments and electrical equipment 1 Check the operation of all Instruments and electrical equipment. 2 Make sure that all instruments read correctly, and switch on all electrical equipment in turn, to check that it functions properly.
Steering and suspension 3 Check for any abnormalities in the steering, suspension, handling or road feel. 4 Drive the vehicle, and check that there are no unusual vibrations or noises. 5 Check that the steering feels positive, with no excessive sloppiness, or roughness, and check for any suspension noises when cornering and driving over bumps.
Drivetrain 6 Check the performance of the engine, clutch (where applicable), transmission and driveshafts. 7 Listen for any unusual noises from the engine, clutch and gearbox/transmission. 8 Make sure that the engine runs smoothly when Idling, and that there Is no hesitation when accelerating. 9 Check that, where applicable, the clutch action Is smooth and progressive, that the drive is taken up smoothly, and that the pedal travel is not excessive. Also listen for any noises when the clutch pedal is depressed. 10 On manual gearbox models, check that all gears can be engaged smoothly without noise, and that the gear lever action is not abnormally vsgue or notchy. 11 On automatic transmission models, check that all Ihe gear positions can be selected with the vehicle at rest, if any problems are found, they should be referred to a Flat dealer. 12 Listen for a metallic clicking sound from the front of the vehicle, as the vehicle is driven slowly in a circle with the steering on full-lock. Carry out this check in both directions. If a clicking noise is heard, this Indicates wear in a drtveshaft joint, In which case renew the joint if necessary.
Check the braking system 13 Make sure that the vehicle does not pull to one side when braking, and that the wheels do not lock prematurely when braking hard. 14 Check that there is no vibration through the steering when braking. 15 Check that the handbrake operates correctly without excessive movement of the lever, and that It holds the vehicle stationary on a slope.
Page 34 of 225
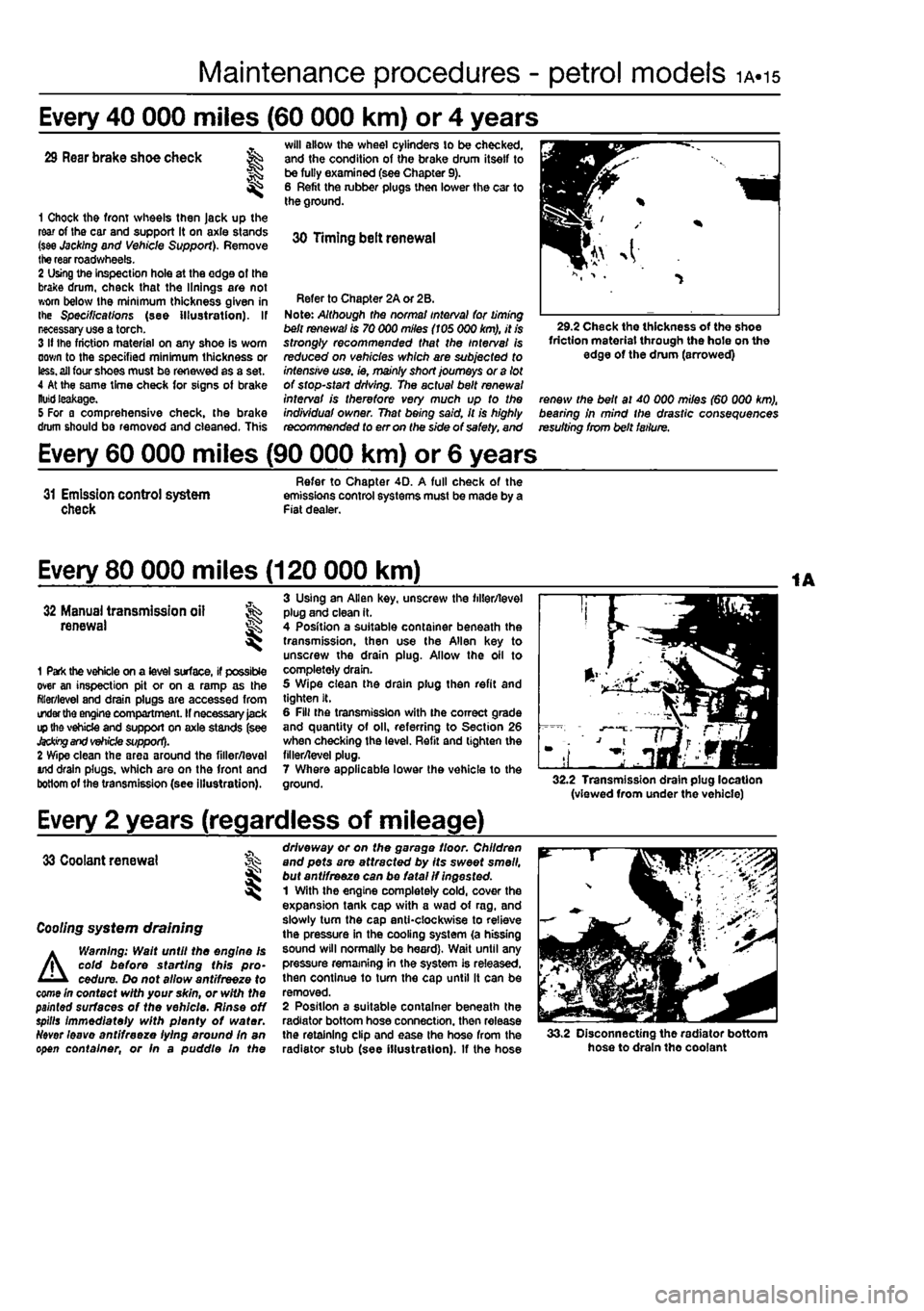
Maintenance procedures - petrol models 1A.15
Every 40 000 miles (60 000 km) or 4 years
29 Rear brake shoe check
1 Chock the front wheels then Jack up the rear of Ihe car and support it on axle stands (see Jacking and Vehicle Support). Remove the rear roadwheels. 2 Using the inspection hole at the edge of the brake drum, check that the linings are not worn below Ihe minimum thickness given in the Specifications (see illustration). If necessary use a torch. 3 If the friction material on any shoe is worn down to the specified minimum thickness or
less,
all four shoes must be renewed as a set. 4 At the same time check for signs of brake
Kutti
leakage. 5 For a comprehensive check, the brake drum should be removed and cleaned. This
will allow the wheel cylinders to be checked, and the condition of the brake drum itself to be fully examined (see Chapter 9). 6 Refit the lubber plugs then lower the car to the ground.
30 Timing belt renewal
Refer to Chapter 2A or 2B. Note: Although the norma/ interval for timing belt renewal is 70 000 miles (105 000 km), it is strongly recommended that the interval Is reduced on vehicles which are subjected to intensive use. ie, mainly short journeys or a lot of stop-start driving. The actual belt renewal interval is therefore very much up to the individuaf owner. That being said, it is highly recommended to err on the side of safety, and
29.2 Check the thickness of the shoe friction material through the hole on the edge of the drum (arrowed)
renew the belt at 40 000 miles (60 000 km), bearing in mind the drastic consequences resulting from belt failure.
Every 60 000 miles (90 000 km) or 6 years
31 Emission control system check
Refer to Chapter 4D. A full check of the emissions control systems must be made by a Fiat dealer.
Every 80 000 miles (120 000 km)
32 Manual transmission all renewal S
1 Park the vehicle on a level surface, if possible over an inspection pit or on a ramp as the filler/level and drain plugs are accessed from order
the
engine compartment. If necessary
Jack
ip the vehicle and support on axle stands (see
Jacking and vehicle
support). 2 Wipe clean the area around the filler/leval And drain plugs, which are on the front and bottom of the transmission (see illustration).
3 Using an Allen key. unscrew the filler/level plug and clean it. 4 Position a suitable container beneath the transmission, then use the Allen key to unscrew the drain plug. Allow the oil to completely drain. 5 Wipe clean the drain plug then refit and tighten It. 6 Fill the transmission with ihe correct grade and quantity of oil, referring to Section 26 when checking the level. Refit and lighten the filler/level plug. 7 Where applicable lower the vehicle to the ground. 32.2 Transmission drain plug location (viewed from under the vehicle)
Every 2 years (regardless of mileage)
33 Coolant renewal
I
Cooling system draining
A
Warning: Walt until the engine Is cold before starting this pro-cedure. Do not allow antifreeze to come In contact with your skin, or with the painted surfaces of the vehicle. Rinse off spills immediately with plenty of water.
Ndver
leave antifreeze lying around In an open container, or fn a puddle In the
driveway or on the garage floor. Children and pets are attracted by its sweet smell, but ant/freeze can be fatal if ingested. 1 With the engine completely cold, cover the expansion tank cap with a wad of rag. and slowly turn the cap anticlockwise to relieve the pressure in the cooling system (a hissing sound will normally be heard). Wait until any pressure remaining in the system is released, then continue to tum the cap until it can be removed. 2 Position a suitable container beneath the radiator bottom hose connection, then release the retaining clip and ease the hose from the radiator stub (see illustration). If the hose 33.2 Disconnecting the radiator bottom hose to drain tho coolant
Page 38 of 225
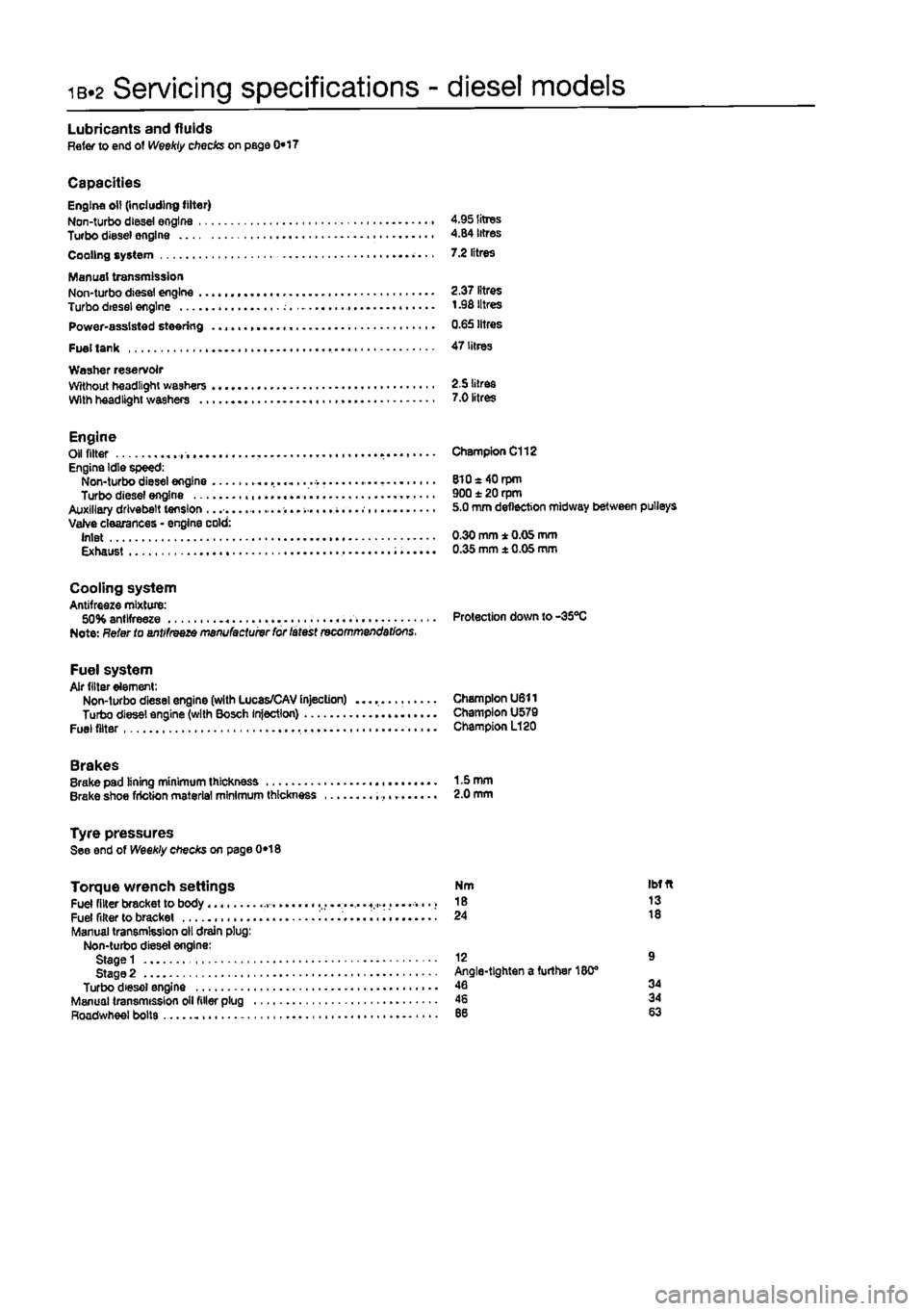
1B.2
Servicing specifications - diesel models
Lubricants and fluids Refer to end of Weekly checks on page 0*17
Capacities Engine oil (including filter) Non-turbo diesei engine 4.95 litres Turbo diesel engine 4.84 litres Cooling system 7.2 litres
Manual transmission Non-turbo diesel engine 2.37 litres Turbo diesei engine t .98 litres Power-assisted steering 0.65 litres
Fuel tank 47 litres Washer reservoir Without headlight washers 2.5 litres With headlight washers 7.0 litres
Engine Oil fitter Engine Idle speed: Non-turbo diesel engine Turbo diesel engine Auxiliary drivebelt tension ...... Valve clearances • engine cold: Inlet Exhaust
Champion C112
8l0«40rpm 900 ± 20 rpm 5.0 mm deflection midway between pulleys
0.30 mm * 0.05 mm 0.35 mm ± 0.05 mm
Cooling system Antifreeze mixture: 50% antifreeze Protection down to-35°C Note: Refer to antifreeze manufactuivr for latest recommendations.
Fuel system Air filter element: Non-turbo diesel engine (with Lucas/CAV Injection) Champion U611 Turbo diesel engine (with Bosch Injection) Champion U579 Fuel filter Champion L120
Brakes Brake pad lining minimum thickness 1-5 mm Brake shoe friction material minimum thickness 2.0 mm
Tyre pressures See end of Weekly checks on page 0*18
Torque wrench settings Fuel filter bracket to body ..... « Fuel filter to bracket i........ Manual transmission oil drain plug: Non-turbo diesel engine: Stage 1 Stage 2 Turbo diesel engine Manual transmission oil filler plug Roadwheel bolts
Nm Ibfft 18 13 24 18
12 9 Angle-tighten a further 180® 46 34 46 34
Page 39 of 225
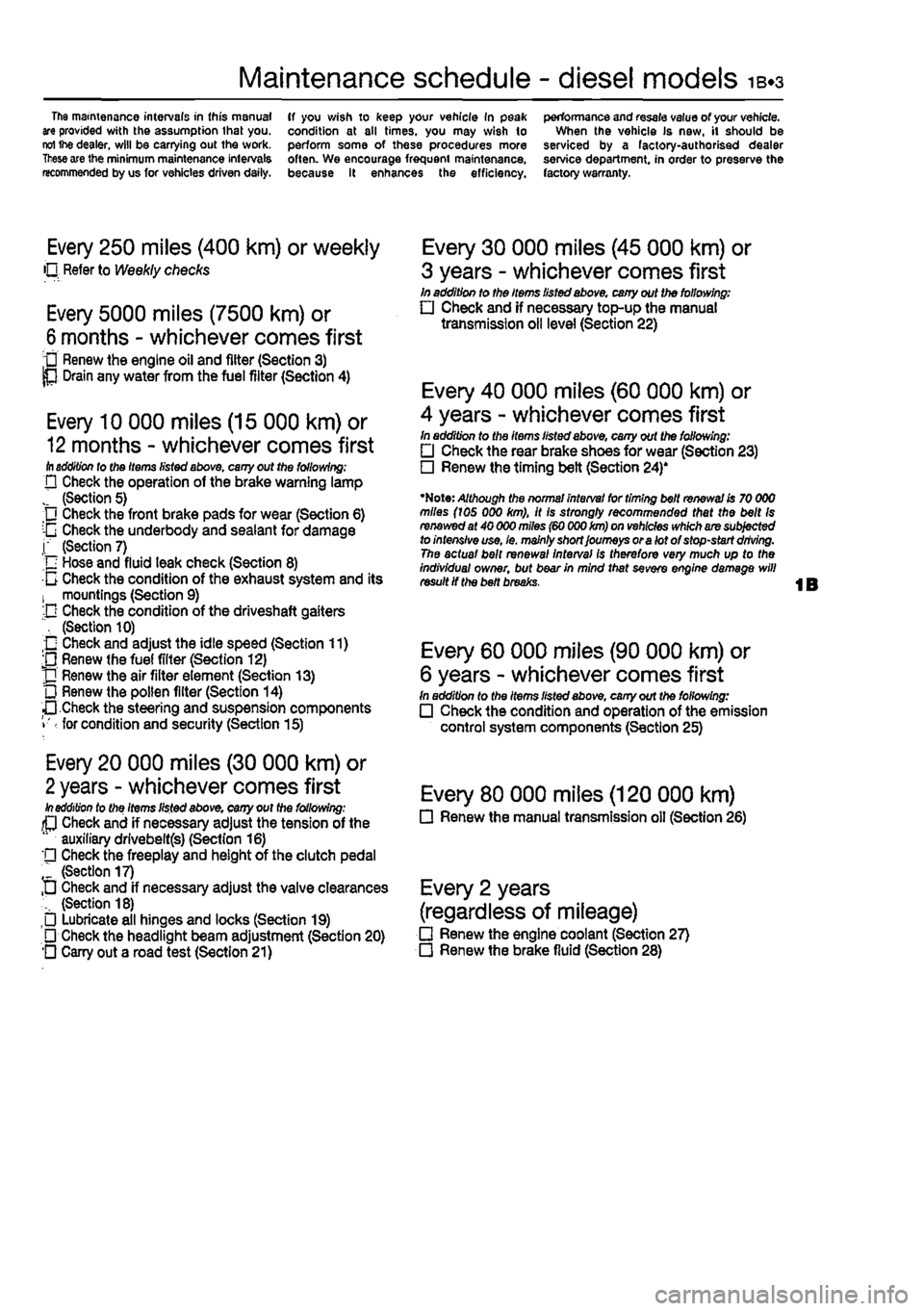
Maintenance schedule - diesel models 1B.3
The mamtenance intervals in this manual are provided with the assumption that you. reI ihe dealer, will be carrying out the work.
These
are the minimum maintenance intervals recommended by us for vehicles driven daily.
ff you wish to keep your vehicle In peak condition at all times, you may wish to perform some of these procedures more often. We encourage frequent maintenance, because it enhances the efficiency.
performance and resale value of your vehicle. When the vehicle Is new, it should be serviced by a factory-authorised dealer service department, in order to preserve the factory warranty.
Every 250 miles (400 km) or weekly O Refer to Weekly checks
Every 5000 miles (7500 km) or
6
months - whichever comes first • Renew the engine oil and filter (Section 3) P Drain any water from the fuel filter (Section 4)
Every 10 000 miles (15 000 km) or
12
months - whichever comes first ill addition lo tho Items listed above, cany out the following; D Check the operation of the brake warning lamp J (Section 5) Check the front brake pads for wear (Section 6) :-G Check the underbody and sealant for damage j" (Section 7) n Hose and fluid leak check (Section 8) 0 Check the condition of the exhaust system and its 1 mountings (Section 9) -D Check the condition of the driveshaft gaiters ", (Section 10) O Check and adjust the idle speed (Section 11) ;0 Renew (he fuel filter (Section 12) J] Renew the air filter element (Section 13) L) Renew the pollen filter (Section 14) •• Check the steering and suspension components • for condition and security (Section 15)
Every 20 000 miles (30 000 km) or
2
years - whichever comes first In addition to the Items listed above, cany out the following: (P Check and if necessary adjust the tension of the auxiliary drlvebeltfs) (Section 16) '• Check the freeplay and height of the clutch pedal " (Section 17) D Check and if necessary adjust the valve clearances (Section 18) Lubricate all hinges and locks (Section 19) • Check the headlight beam adjustment (Section 20) O Cany out a road test (Section 21)
Every 30 000 miles (45 000 km) or
3 years - whichever comes first In addition to the Items listed above, cany out the following: • Check and if necessary top-up the manual transmission oil level (Section 22)
Every 40 000 miles (60 000 km) or
4 years - whichever comes first In addition to the items listed above, cany out the following: • Check the rear brake shoes for wear (Section 23) • Renew the timing belt (Section 24)'
•Note: Although the normal interval for timing belt renewal is 70 000 miles (ids 000 km), it is strongly recommended that the belt Is renewed at 40 000 miles (60 000 km) on vehicles which are subjected to intensive use, le. mainly short Journeys or a lot of stop-start driving. The actual bait renewal interval Is therefore very much up to the Individual owner, but bear in mind that sevefe engine damage will result if the belt breaks.
Every 60 000 miles (90 000 km) or
6 years - whichever comes first In addition to the Items listed above, cany out the following: • Check the condition and operation of the emission control system components (Section 25)
Every 80 000 miles (120 000 km) • Renew the manual transmission oil (Section 26)
Every 2 years
(regardless of mileage) • Renew the engine coolant (Section 27) • Renew the brake fluid (Section 28)
Page 42 of 225
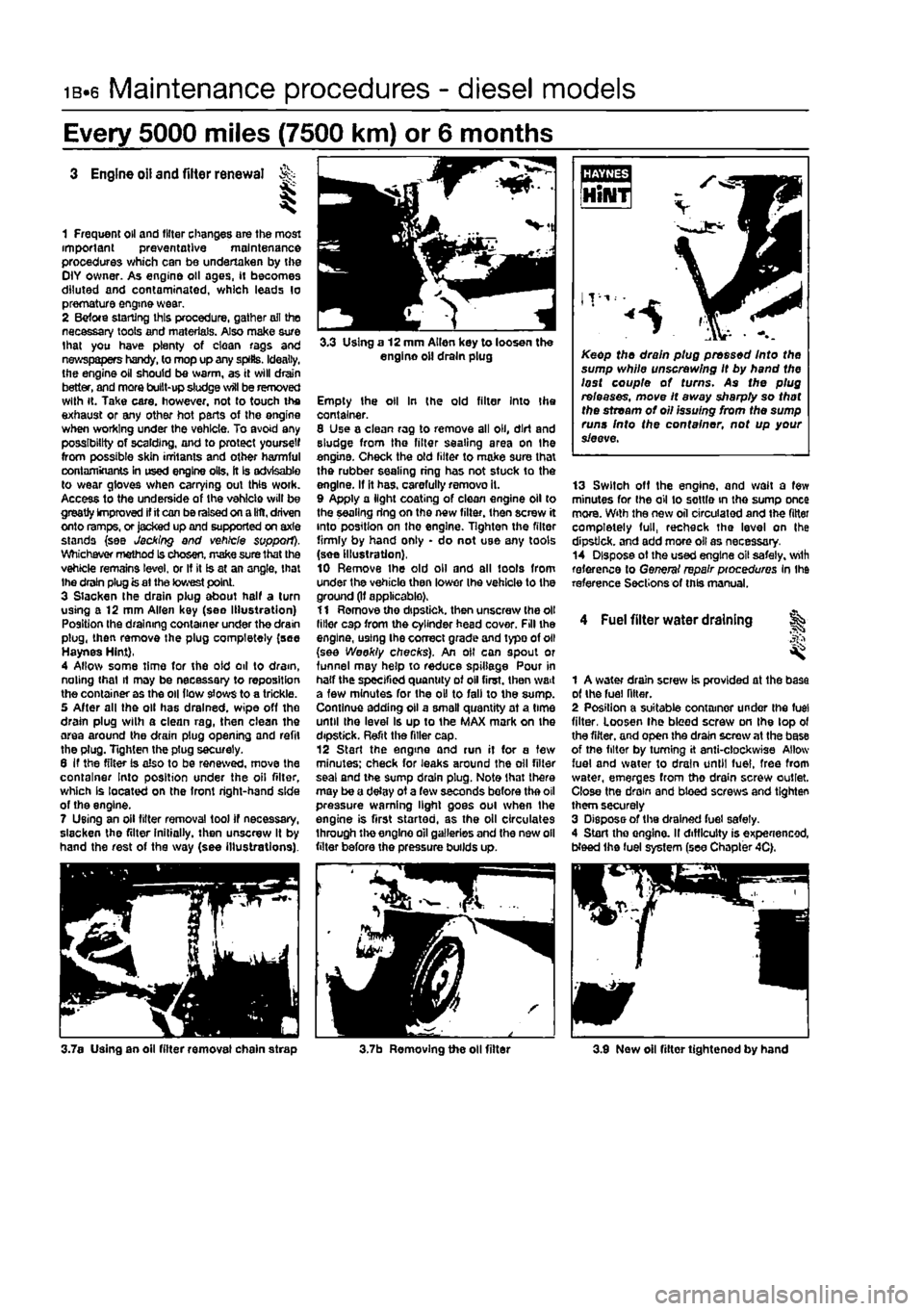
ib.6 Maintenance procedures - diesel models
Every 5000 miles (7500 km) or 6 months
3 Engine oil and filter renewal it-
1 Frequent oil and filter changes are the most important preventative maintenance procedures which can be undertaken by the OlY owner. As engine oil ages, if becomes diluted and contaminated, which leads lo premature engine wear. 2 Befote starting this procedure, gather ail the necessary tools and materials. Also make sure that you have plenty of clean rags and newspapers handy, to mop up any splits. Ideally, the engine oil should be warm, as it will drain better, and more built-up sludge will be removed with it. Take care, however, not to touch the exhaust or any other hot parts of the engine when working under the vehicle. To avoid any possibility of scalding, and to protect yourself from possible skin irritants and other harmful contaminants in used engine oils, it is advisable to wear gloves when carrying out this woik. Access to the underside of the vehicle will be greatly improved if it can be raised on a lilt, driven onto ramps, or jacked up and supported on axle stands {see Jacking and vehicle support). Whichever method Is chosen, make sure that the vehicle remains level, or If it is at an angle, that Ihe drain plug is at the lowest point. 3 Slacken the drain plug about half a turn using a 12 mm Allen key (see Illustration) Position the draining container under the drain plug, then remove the plug completely (see Haynes Hint), 4 Allow some time for the oid oil to dram, noting that it may be necessary to reposition the container as the oil (tow slows to a trickle. 5 After all the oil has drained, wipe off the drain plug wilh a clean rag, then clean the area around the drain plug opening and refit the plug. Tighten the ptug securely. 6 If the filter is also to be renewed, move the container Into position under the oil filter, which Is located on the front right-hand side of the engine. 7 Using an oil filter removal tool if necessary, slacken the filter initially, then unscrew It by hand the rest of the way (see illustrations).
3.3 Using a 12 mm Allen key to loosen the engine oil drain plug
Empty the oil In (he old filter Into Ihe container. 8 Use a clean rag to remove all oil, dirt and sludge from the filter sealing area on the engine. Check the old lilter to make sure thai the rubber sealing ring has not stuck to the engine. If it has. carefully removo it. 9 Apply a light coating of clean engine oil to the sealing ring on the new filter, then screw it into position on the engine. Tighten the filter firmly by hand only • do not use any tools (see Illustration), 10 Remove Ihe old oil and all tools from under the vehicle then lower Ihe vehicle to the ground (If applicable). 11 Remove tho dipstick, then unscrew (he oil liiler cap from the cylinder head cover. Fill the engine, using Ihe correct grade and typo of oil (see Weekly checks). An oil can spout or funnel may help to reduce spillage Pour in half the specified quantity of oil first, then wait a few minutes for the oil to fall to the sump. Continue adding oil a smalt quantity at a time until Ihe level Is up to the MAX mark on the dipstick. Refit the filler cap. 12 Start the engine and run it for a tew minutes; check for leaks around the oil filter seal and the sump drain plug. Note that there may be a delay of a few seconds before the oil pressure warning light goes oul when the engine is first started, as the oil circulates through the engine oil galleries and the new oil filter before the pressure builds up.
Keep the drain plug pressed Into the sump while unscrewing It by hand the lost couple of turns. As the plug releases, move It away sharpty so that the stream of oil issuing from the sump runs Into the container, not up your sieeve.
13 Switoh off the engine, and wait a few minutes for Ihe oil to settle in the sump once mora. With the new oil circulated and the fitter completely full, recheck the level on Ihe dipstick, and add more oil as necessary. 14 Dispose ot the used engine oil safely, wilh reference lo General repair pioceduros In Ihe reference Sections of this manual.
4 Fuel filter water draining ^
1 A water drain screw is provided at the base of the fuel filter. 2 Position a suitable container under ihe fuel filter, Loosen Ihe bleed screw on the lop ol the filter, and open the drain screw at the base of tne filter by turning it anti-clockwise Allow fuel and water to drain until fuel, free from water, emerges from tho drain screw outlet. Close tne drain and bleed screws and tighten them securely 3 Dispose of the drained fuel safely. 4 Start tho onglno. II difficulty is experienced, Weed the fuel system (see Chapter 4C).
3.7a Using an oil fitter removal chain strap 3.7b Removing the oil filter 3.9 Now oil filter tightened by hand
Page 43 of 225
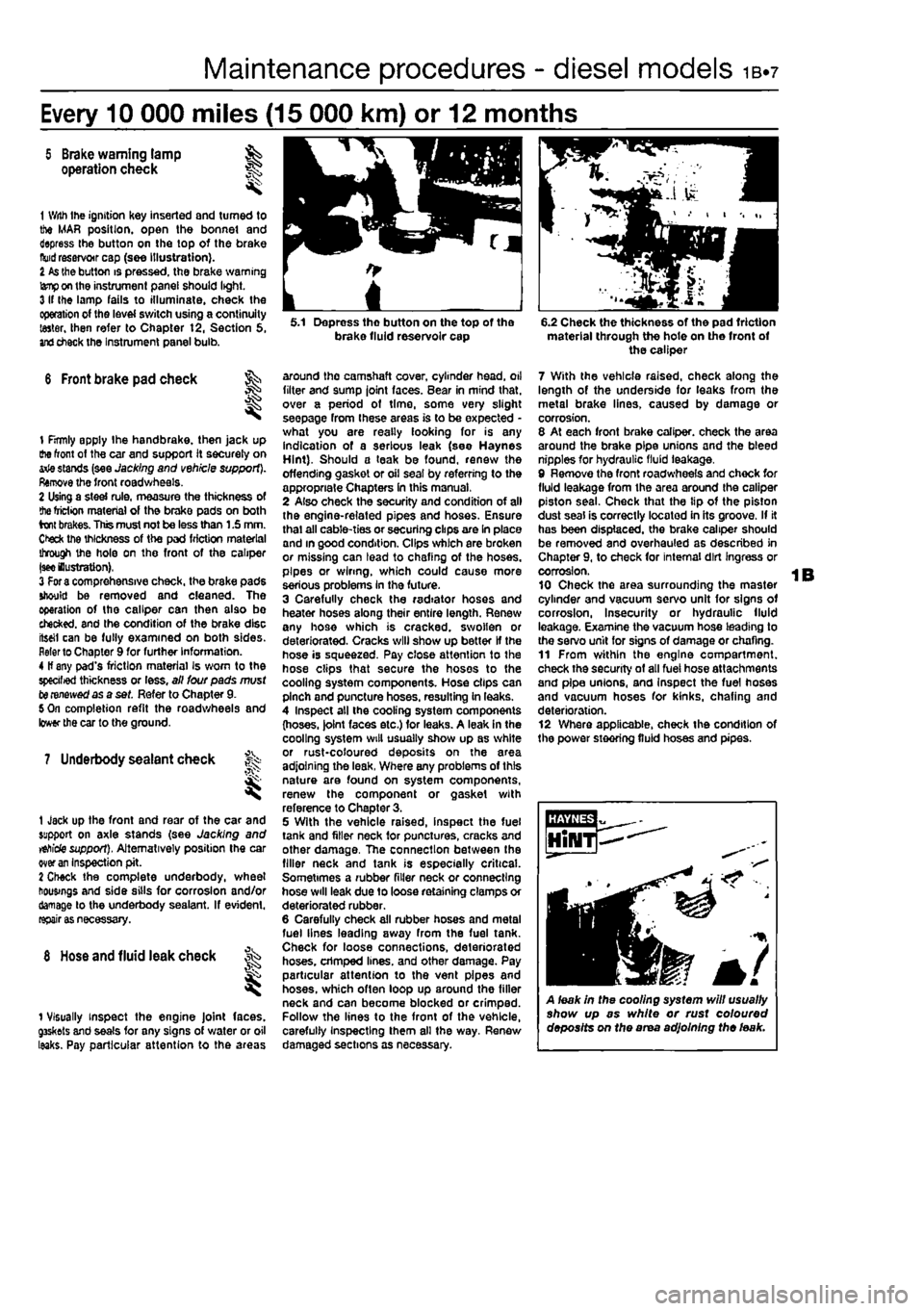
Maintenance procedures - diesel models ib.?
Every 10 000 miles (15 000 km) or 12 months
5 Brake warning lamp operation check 1
1 With Ihe ignition Key inserted and turned to the MAR position, open the bonnet and depress the button on the top of the brake
fluid
reservoir cap (see illustration). I
As
the button is pressed, the brake warning
lamp
on the instrument panel should light. 3 If Ihe lamp fails to illuminate, check the operation of the level switch using a continuity taster, then refer to Chapter t2, Section 5,
and
check the Instrument panel bulb.
6 Front brake pad check ^
I
1 firmly apply Ihe handbrake, then jack up the front of the car and support it securely on arie stands (see Jacking and vehicle support). Remove the front roadwheels. 2 Using a steel rule, measure the thickness of
the
friction material of the brake pads on both brakes. This must not be less than 1.5 mm. Ctefc the thickness of the pad friction material through the hole on the front of the caliper
|see
lustration), 3
For a
comprehensive check, the brake pads should be removed and cleaned. The operation of the caliper can then also bo checked, and the condition of the brake disc iteeil can be fully examined on both sides. Refer to Chapter 9 for further Information. 4 If any pad's friction material Is worn to the specified thickness or less, all lour pads must to renewed as a set. Refer to Chapter 9. 5 On completion refit the roadwheels and lower the car to the ground.
7 Underbody sealant check f^
1 Jack up the front and rear of the car and support on axle stands (see Jacking and
vehicle
support). Alternatively position the car over
an
Inspection pit. 2 Check the complete underbody, wheel housings and side sills for corrosion and/or damage to the underbody sealant. If evident,
rapairi
8
Hose
and fluid leak check
1 Visually inspect the engine Joint faces. g3skets and seals for any signs of water or oil leaks. Pay particular attention to the areas
5.1 Depress tho button on the top of the brake fluid reservoir cap
around the camshaft cover, cylinder head, oil filter and sump joint faces. Bear in mind that, over a period of time, some very slight seepage from these areas is to be expected -what you are really looking for is any indication of a serious leak (see Haynes Hint). Should a teak be found, renew the offending gasket or oil seal by referring to the appropriate Chapters In this manual, 2 Also check the security and condition of all the engine-related pipes and hoses. Ensure thai all cable-ties or securing clips are In place and in good condition. Clips which are broken or missing can lead to chafing of the hoses, pipes or wiring, which could cause more serious problems In the future. 3 Carefully check the radiator hoses and heater hoses along their entire length. Renew any hose which is cracked, swollen or deteriorated. Cracks will show up better If the hose is squeezed. Pay close attention to the hose clips that secure the hoses to the cooling system components. Hose clips can pinch and puncture hoses, resulting in leaks. 4 Inspect all the cooling system components (hoses. )olnt faces etc.) for leaks. A leak in the cooling system will usually show up as white or rust-coloured deposits on the area adjoining the leak, Where any problems of this nature are found on system components, renew the component or gasket with reference to Chapter 3. 5 With the vehicle raised, inspect the fuel tank and filler neck for punctures, cracks and other damage, The connection between the filler neck and tank is especially critical. Sometimes a rubber filler neck or connecting hose will leak due to loose retaining clamps or deteriorated rubber. 6 Carefully check all rubber hoses and metal fuel lines leading away from the fuel tank. Check for loose connections, deteriorated hoses, crimped lines, and other damage. Pay particular attention to the vent pipes and hoses, which often loop up around the filler neck and can become blocked or crimped. Follow the lines to the front of the vehicle, carefully Inspecting them all the way. Renew damaged sections as necessary.
6.2 Check the thickness of the pad friction material through the hote on the front of the caliper
7 With the vehicle raised, check along the length of the underside for leaks from the metal brake lines, caused by damage or corrosion. 8 At each front brake caliper, check the area around the brake pipe unions and the bleed nipples for hydraulic fluid leakage, 9 Remove the front roadwheels and chock for fluid leakage from the area around the caliper piston seal. Check that the tip of the piston dust seal is correctly located in its groove. If it has been displaced, the brake caliper should be removed and overhauled as described in Chapter 9, to check for internal dirt Ingress or corrosion. 10 Check the area surrounding the master cylinder and vacuum servo unit for signs of corrosion, Insecurity or hydraulic fluid leakage. Examine the vacuum hose leading to the servo unit for signs of damage or chafing. 11 From within the engine compartment, check the security of all fuel hose attachments and pipe unions, and Inspect the fuel hoses and vacuum hoses for kinks, chafing and deterioration. 12 Where applicable, check the condition of the power steering fluid hoses and pipes.
A leak in the cooling system will usually show up as white or rust coloured deposits on the area adjoining the leak.
Page 45 of 225
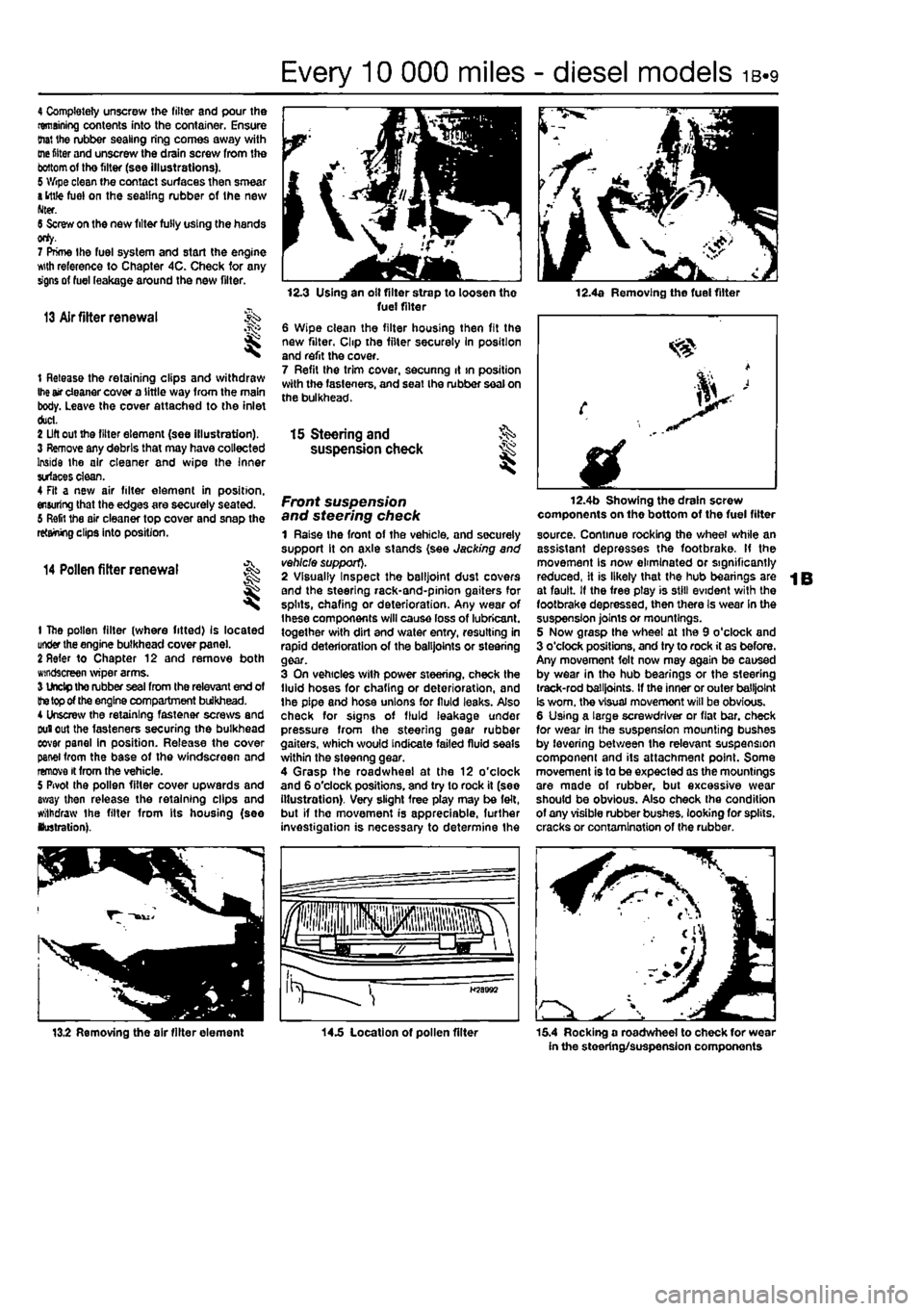
Every 10 000 miles - diesel models ib«9
4 Completely unscrew the filter and pour the remaining contents into the container. Ensure (hat the rubber sealing ring comes away with
me
fitter and unscrew the drain screw from the
bottom
of tho filter (see illustrations). 5 Wipe clean the contact surfaces then smear
a
ittfe fuel on the sealing rubber of the new Nter. 6 Screw on the new filter fully using the hands orty. 7 Prime the fuel system and start the engine wth reference to Chapter 4C. Check for any signs of fuel leakage around the new filter.
13 Air fitter renewal
t Release the retaining clips and withdraw
Ihe
air cleaner cover a little way from the main body. Leave the cover attached to the inlet duct. 2 Lift out the filter element (see illustration). 3 Remove any debris that may have collected Inside the air cleaner and wipe the Inner surfaces clean. 4 Fit a new air filter element in position, ensuring that the edges are securely seated. 6 Refit the air cleaner top cover and snap the retaining clips into position.
14 Pollen filter renewal
t
1 The pollen filter (where fitted) Is located under the engine bulkhead cover pane). 2 Refer to Chapter 12 and remove both windscreen wiper arms. 3 Undp tho rubber seal from the relevant end of
the top
of the engine compartment bulkhead. 4 Unscrew the retaining fastener screws and Duiout the fasteners securing the bulkhead eovar panel in position. Release the cover panel from the base of the windscreen and remove it from the vehicle. 5 Pivot the pollen filter cover upwards and away then release the retaining clips and withdraw the filter from Its housing (see lustration).
12.3 Using an olt filter strap to loosen the fuel filter 6 Wipe clean the filter housing then fit the new filter, Clip the filter securely In position and refit the cover. 7 Refit the trim cover, secunng it >n position with the fasteners, and seat Ihe rubber seal on the bulkhead.
12.4a Removing the fuel filter
15 Steering and §S> suspension check ^
Front suspension and steering check 1 Raise the front of the vehicle, and securely support it on axle stands (see Jacking and vehicle support). 2 Visually Inspect the balljoint dust covers and the steering rack-and-pinion gaiters for splits, chafing or deterioration. Any wear of Ihese components will cause loss of lubricant, together with dirt and water entry, resulting in rapid deterioration of the balljoints or steering gear. 3 On vehicles with power steering, check the fluid hoses for chafing or deterioration, and the pipe and hose unions for fluid leaks. Also check for signs of fluid leakage under pressure from the steering gear rubber gaiters, which would indicate failed fluid seals within the steenng gear. 4 Grasp the roadwheel at the 12 o'clock and 6 o'clock positions, and try to rock it (see illustration). Very slight free play may be felt, but if the movement is appreciable, further investigation is necessary to determine the
fplllll iHpjiiisisps fa^aJw a LJgr >
H58B92
12.4b Showing the drain screw components on the bottom of the fuel filter source. Continue rocking the wheel while an assistant depresses the footbrake. If the movement Is now eliminated or significantly reduced, it is likely that the hub bearings are at fault. If the free ptay is still evident with the footbrake depressed, then there Is wear In the suspension joints or mountings. 5 Now grasp the wheel at the 9 o'clock and 3 o'clock positions, and try to rock it as before. Any movement felt now may again be caused by wear in the hub bearings or the steering track-rod balljoints. If the inner or outer balljoint Is worn, the visual movemont will be obvious. 6 Using a large screwdriver or flat bar. check for wear in the suspension mounting bushes by levering between the relevant suspension component and its attachment point. Some movement is to be expected as the mountings are made of rubber, but excessive wear should be obvious. Also check the condition of any visible rubber bushes, looking for splits, cracks or contamination of the rubber.
13.2 Removing the air filter element 14.5 Location of pollen filter 15.4 Rocking a roadwheel to check for wear in the steering/suspension components