specified torque FIAT PUNTO 1998 176 / 1.G Owner's Guide
[x] Cancel search | Manufacturer: FIAT, Model Year: 1998, Model line: PUNTO, Model: FIAT PUNTO 1998 176 / 1.GPages: 225, PDF Size: 18.54 MB
Page 151 of 225
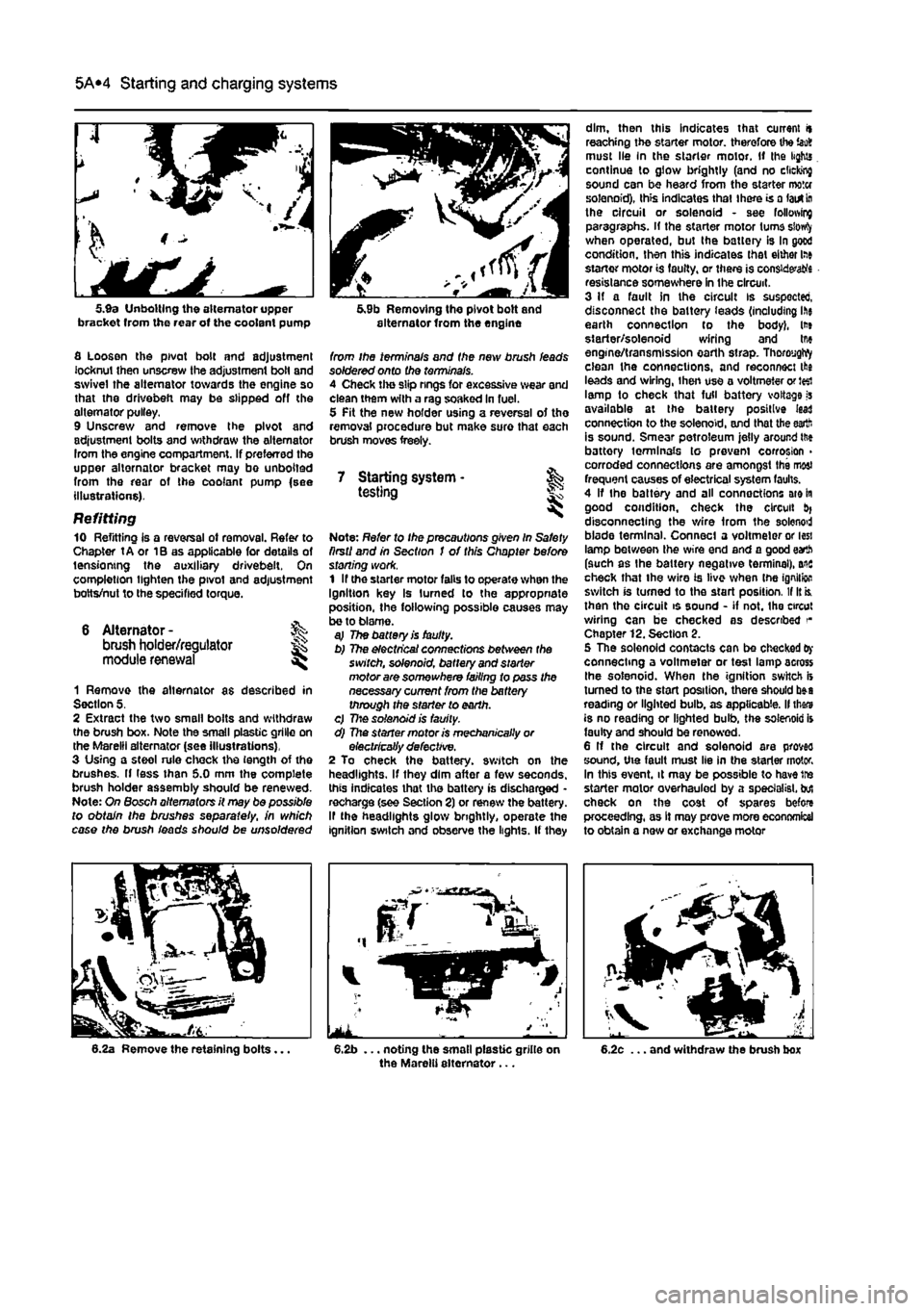
5A«2 Starting and charging systems
5.9a Unbolting the alternator upper bracket from the rear of the coolant pump
fl Loosen the pivot bolt and adjustment locknut then unscrew the adjustment bolt and swivel the alternator towards the engine so that the drivebefi may be slipped off the alternator pulley. 9 Unscrew and remove the pivot and adjustment bolts and withdraw the alternator Irom the engine compartment. If preferred the upper alternator bracket may bo unbolted from the rear of the coolant pump {see illustrations).
Refitting 10 Refitting is a reversal ot removal. Refer to Chapter tA or 1B as applicable for details of tensioning the auxiliary drivebeit. On completion lighten the pivot and adjustment botts/nut to the specified torque.
6 Alternator -brush holder/regulator module renewal
%
1 Remove the alternator as described in Section 5. 2 Extract the two small bolts and withdraw the brush box. Note the small plastic grille on the Marelli alternator (see illustrations), 3 Using a steol rule chock the length of the brushes. If less than 5.0 mm the complete brush holder assembly should be renewed. Note: On Bosch alternators it may be possible to obtain the brushes separate//, in which case the brush ieads should be unsoldered
5.9b Removing the pivot bolt and alternator from the engine
from ihe terminals and the new brush leads soldered onto the terminals. 4 Check the slip rings for excessive wear and clean them with a rag soaked in fuel. 5 Pit the new holder using a reversal of the removal procedure but make sure that each brush moves freely.
7 Starting system • & testing
Note: Refer to Ihe precautions given In Safety firstI and in Section I of this Chapter before stoning work. 1 If the starter motor falls to operate when the Ignition key Is turned to the appropriate position, the following possible causes may be to blame. aj The battery is faulty. b) The electrical connections between the switch, solenoid, battery and starter motor are somewhere failing to pass the necessary current from the battery through the starter to earth. c) 77:© solenoid is faulty. d) The starter motor is mechanically or electrically defective. 2 To check the battery, switch on the headlights. If they dim after a few seconds, this indicates that the battery is discharged -recharge (see Section 2) or renew the battery. If the headlights glow brightly, operate the ignition switch and observe the lights. If they
dim, then this indicates that current it reaching the starter motor, therefore the iao8 must lie In the starter motor. If the lights continue to glow brightly (and no clicking sound can be heard from the starter motor solenoid), this indicates that there is a lairt
In
the circuit or solenoid - see following paragraphs, if the starter motor turns siowfy when operated, but the battery is In good condition, then this indicates that either lae starter motor is faulty, or there is considers resistance somewhere in the circuit. 3 If a fault in the circuit is suspected, disconnect the battery ieads (including ihe earth connection to the body), lt» starter/solenoid wiring and tne engine/transmission earth strap. ThoroygWy clean the connections, and reconnect the leads and wiring, ihen use a voltmeter or J«i lamp to check that full battery voltage is available at the battery positive lead connection to the solenoid, and that the earth is sound. Smear petroleum jelly around ttie battory terminals to prevent corrosion > corroded connections are amongst the most frequent causes of electrical system faults. 4 If the battery and all connections are in good condition, check the circuit disconnecting the wire from the solenod blade terminal. Connect a voltmeter or less lamp between the wire end and a good earth (such as the battery negative terminal), ais check that the wire is live when tne ignition switch is turned to the start position. If It is. then the circuit is sound - if not. the circut wiring can be checked as described Chapter 12. Section 2. 5 The solenoid contacts can be checked
Oy
connecting a voltmeter or test lamp across Ihe solenoid. When the ignition switch is turned to the start position, there should b»a reading or lighted bulb, as applicable. II thars is no reading or lighted bulb, the solenoid is faulty and should be renewed. 6 If the circuit and solenoid are proves sound, the fault must lie in the starter motor. In this event, it may be possible to have tre starter motor overhauled by a specialist, but check on the cost of spares before proceeding, as It may prove more economical to obtain a new or exchange motor
Page 157 of 225
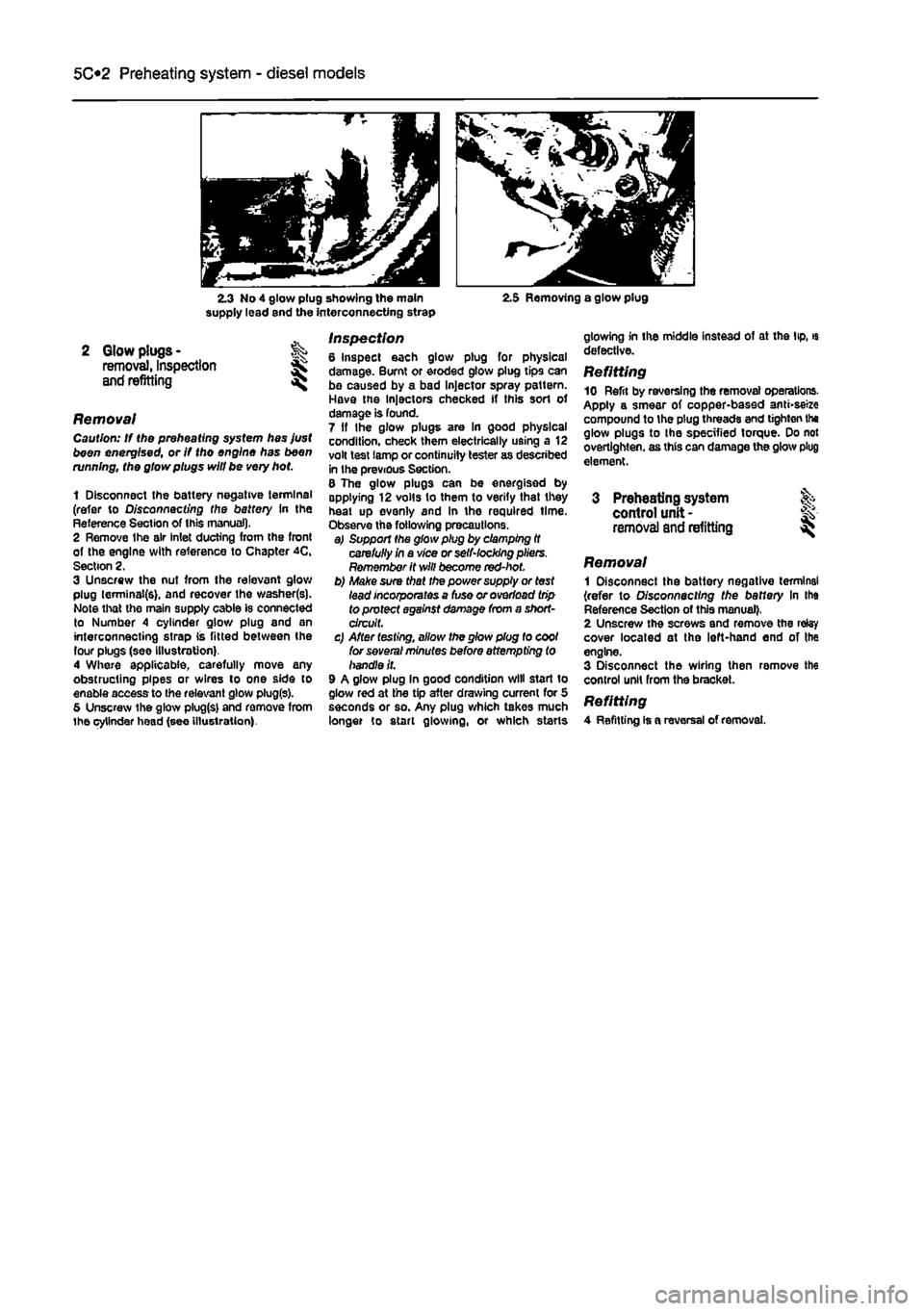
5C«2 Preheating system - diesel models
2.3 No 4 glow plug showing the main supply lead end the interconnecting strap 2.5 Removing a glow plug
2 Glow plugs -removal, Inspection and refitting
Removal Caution: If the preheating system has just been energised, or If tho engine has been running, the glow plugs will be very hot
1 Disconnect the battery negative terminal (refer to Disconnecting the battery in the Reference Section of this manual), 2 Remove Ihe air Inlet ducting from the front of the engine with reference to Chapter 4C, Section 2. 3 Unscrew the nut from the relevant glow plug lerminai(s). and recover the washer(s). Note that tho main supply cable is connected to Number 4 cylinder glow plug and an interconnecting strap lis fitted between the four plugs (see Illustration). 4 Where applicable, carefully move any obstructing pipes or wires lo one side to enable access to the relevant glow plug(s). 5 Unscrew the glow plug(s) and remove from the cylinder head (see illustration).
Inspection 8 Inspect each glow plug for physical damage. Burnt or eroded glow plug tips can bo caused by a bad Injector spray pattern. Have the Injectors checked if this sort of damage is found. 7 If Ihe glow plugs are In good physical condition, check them electrically using a 12 volt test lamp or continuity tester as described in the previous Section. 8 The glow plugs can be energised by applying 12 volts to them to verity that they heat up evenly and In the required time. Observe the following precautions. a) Support the glow plug by clamping it carefully in a vice or selNocking pliers. Remember it will become red-hot. b) Make sura that the power supply or test lead incorporates a fuse or overload trip to protect against damage from a short-circuit. c) After testing, allow the glow plug to cool for several minutes before attempting to handle it. 9 A glow plug In good condition will start to glow red at the tip after drawing current for 5 seconds or so. Any plug which takes much longer to start glowing, or which starts
glowing in the middle instead of at the lip, « defective. Refitting 10 Refit by reversing the removal operations. Apply a smear of copper-based anti-seize compound to the plug threads and tighten Ihe glow plugs to Ihe specified torque. Do not overtighten, as this can damage the glow plug element.
3 Preheating system control unit -removal
and
refitting I
Removal 1 Disconnect the battery negative terminal (refer to Disconnecting the baffery In Ihe Reference Section of this manual). 2 Unscrew the screws and remove the relay cover located at the left-hand end of the engine. 3 Disconnect the wiring then remove the control unit from the bracket. Refitting 4 Refitting is a reversal of removal.
Page 158 of 225
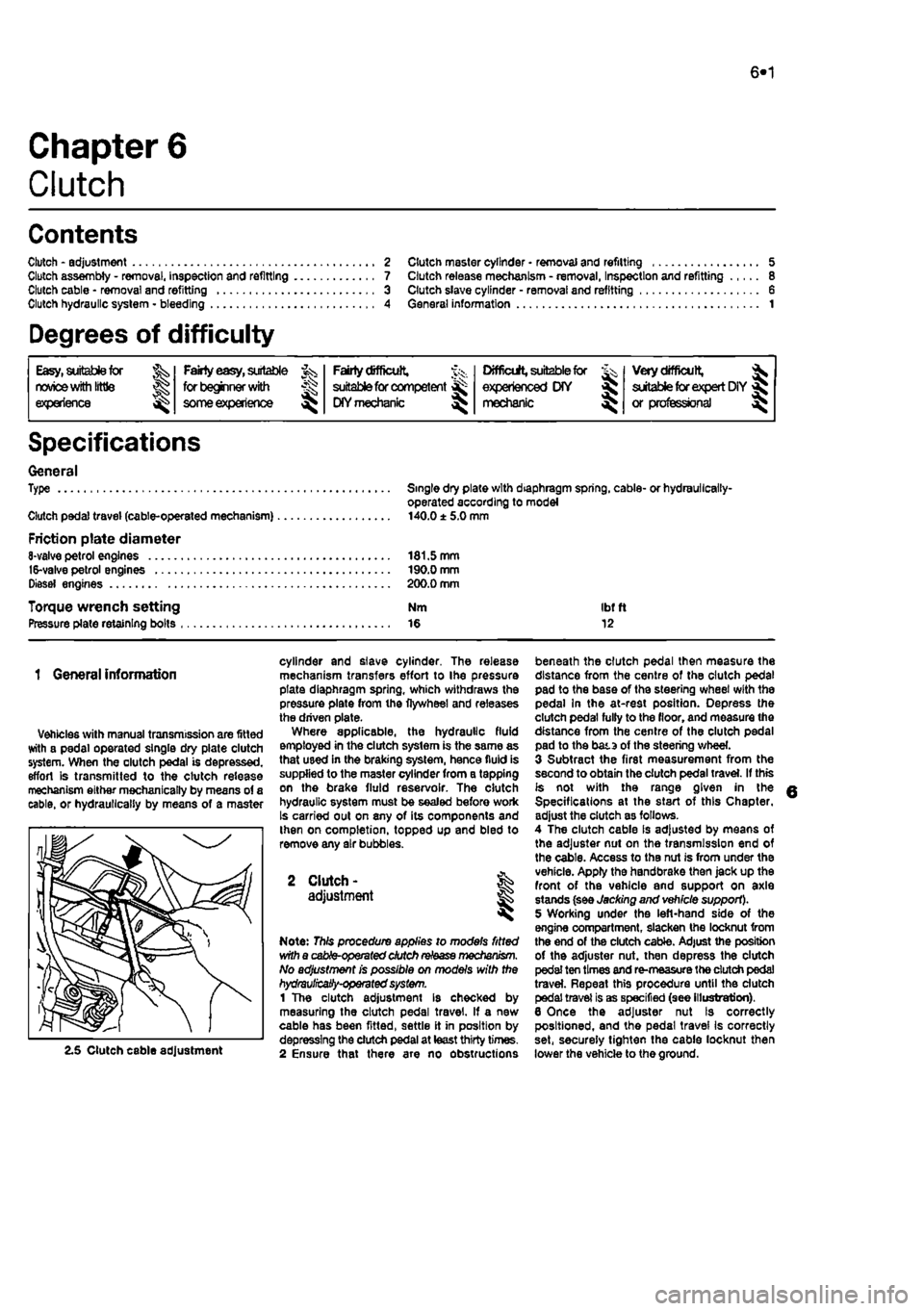
6*1
Chapter 6
Clutch
Contents
Clutch - adjustment Clutch assembly - removal, inspection and refitting Clutch cable • removal and refitting Clutch hydraulic system - bleeding
Degrees of difficulty
2 Clutch master cylinder • removal and refitting 5 7 Clutch release mechanism - removal, Inspection and refitting 8 3 Clutch slave cylinder - removal and refitting 6 4 General information 1
Easy, suitable for
novice with little experience oi^
Faidy easy,
suitable for beginner
with
^
some
experience
Fairly difficult, suitable
for
competent ^
DIY
mechanic ^
Difficiit, suitable for ^ experienced DIY JR mechanic ^
V<*y difficult,
jk
suitable
for expert
DIY
« or professional ^
Specifications
General Type
Clutch pedal travel (cable-operated mechanism)
Friction plate diameter 8-valve petrol engines 16-valve petrol engines Diesel engines
Torque wrench setting Pressure plate retaining bolts
Single dry plate with diaphragm spring, cable- or hydraullcally-operated according to model 140.0 ± 5.0 mm
181.5 mm 190.0 mm 200.0 mm
Nm Ibf ft 16 12
1 General information
Vehicles with manual transmission are fitted with a pedal operated single dry plate clutch system. When the clutch pedal is depressed, effort is transmitted to the clutch release mechanism either mechanically by means of a cable, or hydraullcally by means of a master
2.5 Clutch cable adjustment
cylinder and slave cylinder. The release mechanism transfers effort to Ihe pressure plate diaphragm spring, which withdraws the pressure plate from the flywheel and releases the driven plate-Where applicable, the hydraulic fluid employed in the clutch system is the same as that used in the braking system, hence fluid is supplied to the master cylinder from a tapping on the brake fluid reservoir. The clutch hydraulic system must be sealed before work Is carried out on any of its components and then on completion, topped up and bled to remove any air bubbles.
2 Clutch - % adjustment §§ ^
Note: This procedure applies to models fitted with a cable-operated dutch
release
mechanism. No adjustment is possible on models with the hydrauHcaSy-operated system. 1 The clutch adjustment Is checked by measuring the clutch pedal travel. If a new cable has been fitted, settle it in position by depressing the clutch pedal at least thirty times. 2 Ensure that there are no obstructions
beneath the clutch pedal then measure the distance from the centre of the clutch pedal pad to the base of the steering wheel with the pedal In the at-rest position. Depress the clutch pedal fully to the floor, and measure the distance from the centre of the clutch pedal pad to the bata of the steering wheel. 3 Subtract the first measurement from the second to obtain the clutch pedal travel. If this is not with the range given in the Specifications at the start of this Chapter, adjust the clutch as follows. 4 The clutch cable Is adjusted by means of the adjuster nut on the transmission end of the cable. Access to the nut is from under the vehicle. Apply the handbrake then jack up the front of the vehicle and support on axle stands (see Jacking and vehicle support). 5 Working under the left-hand side of the engine compartment, slacken the locknut from the end of the clutch cable. Adjust the position of the adjuster nut. then depress the clutch pedal ten times and re-measure the dutch pedal travel. Repeat this procedure until the clutch pedal travel is as specified (see illustration). 6 Once the adjuster nut Is correctly positioned, and the pedal travel Is correctly set, securely tighten the cable locknut then lower the vehicle to the ground.
Page 161 of 225
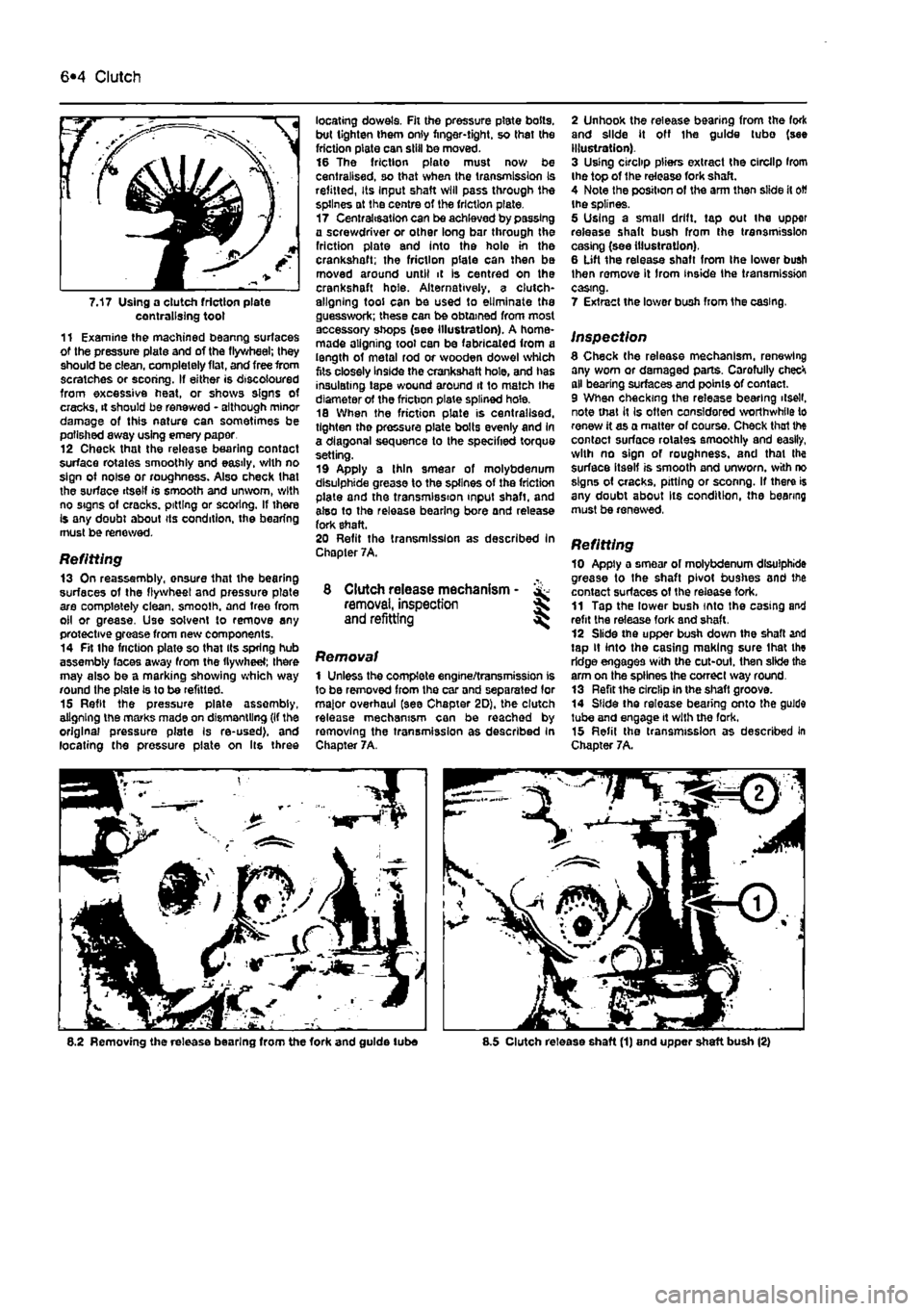
6*4 Clutch
7.17 Using a clutch friction plate centralising toot 11 Examine the machined beanng surfaces of the pressure plate and of the flywheel; they should be clean, completely flat, and free from scratches or scoring. If either is discoloured from excessive heat, or shows signs of cracks, it should be renewed - although minor damage of this nature can sometimes be polished away using emery paper 12 Check that the release bearing contact surface rotates smoothly and easily, with no sign of noise or roughness. Also check that the surface itself is smooth and unworn, with no signs of cracks, pitting or scoring. If there Is any doubt about its condition, the bearing must be renewed.
Refitting 13 On reassembly, onsure that the bearing surfaces of the flywheel and pressure plate are completely clean, smoolh. and tree from oil or grease. Use solvent to remove any protective grease from new components. 14 Fit the friction plate so that its spring hub assembly faces away from the flywheel; there may also be a marking showing which way round the plate Is to be refitted. 15 Refit the pressure plate assembly, aligning the marks made on dismantling (If the original pressure plate Is re-used), and locating the pressure plate on Its three
locating dowels. Fit the pressure plate bolts, but tighten them only finger-tight, so thai the friction plate can skill be moved. 16 The friction plate must now be centralised, so that when the transmission Is refitted, Its Input shaft will pass through the splines at the centre of the friction plate. 17 Centralisation can be achieved by passing a screwdriver or other long bar through the friction plate and into the holo in the crankshaft; the friction plate can then be moved around until it is centred on the crankshaft hole. Alternatively, a clutch-aligning tool can be used to eliminate the guesswork; these can be obtained from most accessory shops (see illustration). A home-made aligning tool can be fabricated from a length of metal rod or wooden dowel which fits closely Inside the crankshaft hole, and has insulating tape wound around it to match Ihe diameter of the friction plate splined hole. 18 When the friction plate is centralised, tighten tho pressure plate bolts evenly and In a diagonal sequence to the specified torque setting. 19 Apply a Ihin smear of molybdenum dlsulphide grease to the splines of the friction plate and the transmission input shaft, and also to the release bearing bore and release fork shaft. 20 Refit the transmission as described In Chapter 7A.
8 Clutch release mechanism - & removal, inspection J and refitting ^
Removal 1 Unless the complete engine/transmission is to be removed from the car and separated lor major overhaul (see Chapter 2D), the clutch release mechanism can be reached by removing the transmission as described In Chapter 7A.
2 Unhook the release bearing from the fork and slide it off Ihe guide tubo (see illustration). 3 Using circlip pliers extract the circllp Irom the top of the release fork shaft. 4 Note the position of the arm then slide it
oW
the splines. 5 Using a small drift, tap out the upper release shaft bush from the transmission casing (see illustration). 6 Lift the release shaft from Ihe lower bush then remove it Irom inside Ihe transmission casing.
7 Extract the lower bush from 1he casing.
inspection 8 Check (he release mechanism, renewing any worn or damaged parts. Carofully checH all bearing surfaces and points of contact. 9 When checking the release bearing ilsell. note that it Is often considered worthwhile to renew it as a matter of course. Check thai the contact surface rotates smoothly and easily, with no sign of roughness, and that Ihe surface itself is smooth and unworn, with no signs of cracks, pitting or sconng. If there is any doubt about Its condition, the bearing must be renewed, Refitting 10 Apply a smear of molybdenum dlsulphide grease to the shaft pivot bushes and the contact surfaces of the release fork. 11 Tap the lower bush into the casing and refit the release fork and shaft. 12 Slide the upper bush down the shaft and tap it into the casing making sure lhat the ridge engages with the cut-out. then slide the arm on the splines the correct way round. 13 Refit the circlip in the shaft groove. 14 Slide the release bearing onto the guide tube and engage it with the fork. 15 Refil the transmission as described in Chapter 7A.
8.2 Removing the release bearing from the fork and guide lube 8.5 Clutch release shaft (1) and upper shaft bush (2)
Page 164 of 225
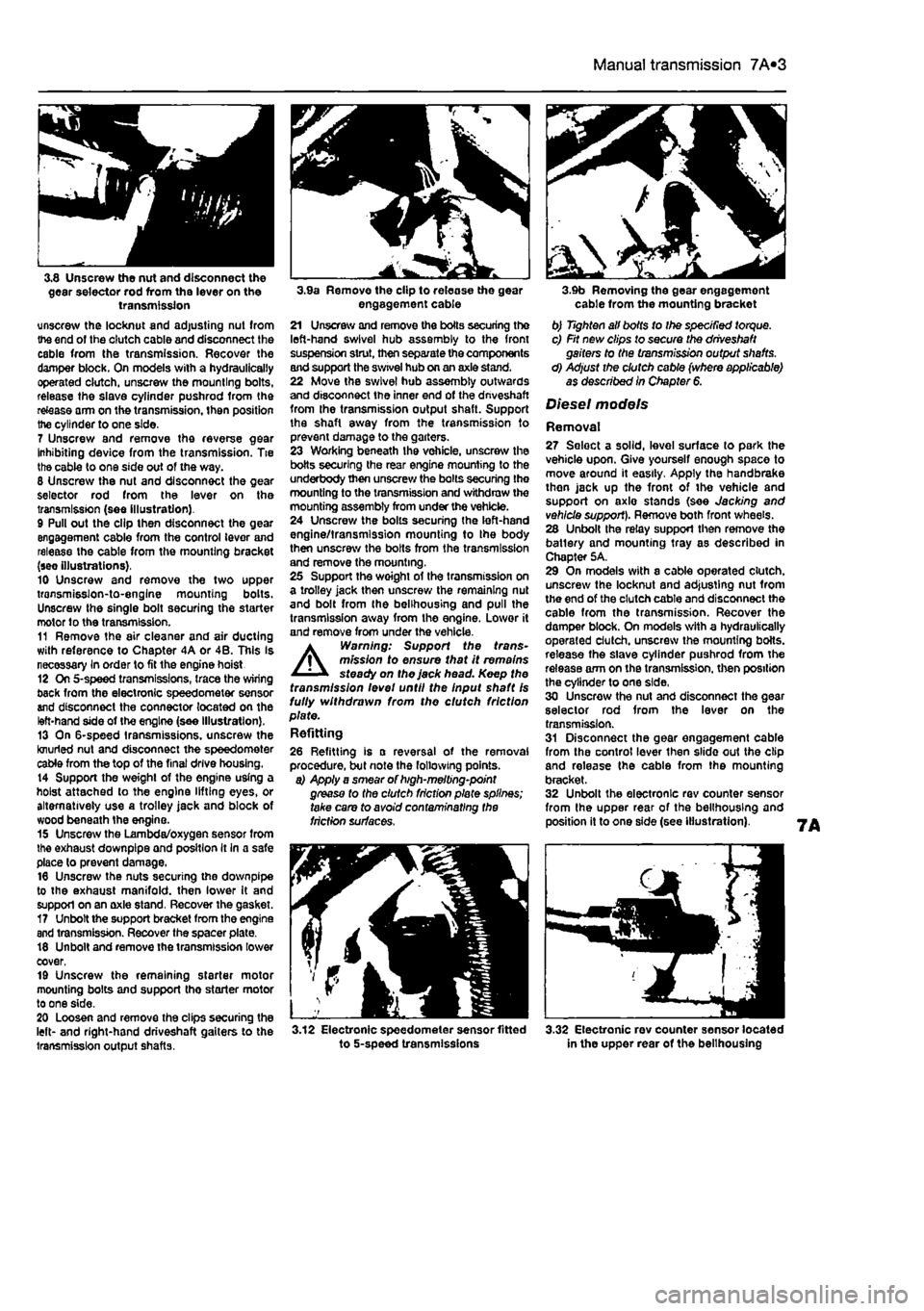
Manual transmission 7A*3
3,8 Unscrew the nut and disconnect the gear selector rod from the lever on the transmission unscrew the locknut and adjusting nut from the end of the clutch cable and disconnect the cable from the transmission. Recover the damper block. On models with a hydraulically operated clutch, unscrew the mounting bolts, release the slave cylinder pushrod from the re&ase arm on the transmission, then position the cylinder to one side.
7 Unscrew and remove the reverse gear Inhibiting device from the transmission. Tie the cable to one side out of the way. 8 Unscrew the nut and disconnect the gear selector rod from the lever on the transmission (see illustration). 9 Pull out the clip then disconnect the gear engagement cable from the control lever and release the cable from the mounting bracket (see illustrations). 10 Unscrew and remove the two upper transmisslon-to-englne mounting bolts. Unscrew the single bolt securing the starter motor to the transmission. 11 Remove the air cleaner and air ducting with reference to Chapter 4A or 4B. This Is necessary In order to fit the engine hoist 12 On 5-speed transmissions, trace the wiring back from the electronic speedometer sensor and disconnect the connector located on the left-hand side of the engine (see illustration). 13 On 6-speed transmissions, unscrew the knurled nut and disconnect the speedometer cable from the top of the final drive housing. 14 Support the weight of the engine using a hoist attached to the engine lifting eyes, or alternatively use a trolley jack and block of wood beneath Ihe engine. 15 Unscrew the Lambda/oxygen sensor from the exhaust downpipe and position It In a safe place to prevent damage. 16 Unscrew the nuts securing the downpipe to the exhaust manifold, then lower It and support on an axle stand. Recover the gasket. 17 Unbolt the support bracket from the engine and transmission. Recover the spacer plate. 18 Unbolt and remove the transmission lower cover, 19 Unscrew the remaining starter motor mounting bolts and support tho starter motor to one side. 20 Loosen and remove the clips securing the left- and right-hand driveshaft gaiters to the transmission output shafts.
3.9a Remove the clip to release the gear engagement cable 21 Unscrew and remove the boils securing the left-hand swivel hub assembly to the front suspension strut, then separate the components and support the swivel hub on an axle stand. 22 Move the swivel hub assembly outwards and disconnect the inner end of the dnveshaft from the transmission output shaft. Support the shaft away from the transmission to prevent damage to the garters. 23 Working beneath the vehicle, unscrew the botts securing the rear engine mounting to the underbody then unscrew the bolts securing the mounting to the transmission and withdraw the mounting assembly from under the vehicle. 24 Unscrew the bolts securing the left-hand engine/transmission mounting to Ihe body then unscrew the bolts from the transmission and remove the mounting. 25 Support the woight of the transmission on a trolley jack then unscrew the remaining nut and bolt from the belihousing and pull the transmission away from the engine. Lower it and remove from under the vehicle. A Warning: Support the trans-mission to ensure that it remains steady on the jack head. Keep the transmission levet until the Input shaft Is fully withdrawn from the clutch friction plate. Refitting
26 Refitting is a reversal of the removal procedure, but note the following points. a) Apply a smear of high-melting-point grease to the clutch friction plate splines; take care to avoid contaminating the friction surfaces.
3.12 Electronic speedometer sensor fitted to 5-speed transmissions
3.9b Removing the gear engagement cable from the mounting bracket b) Tighten all bolts to Ihe specified torque. c) Fit new clips to secure the driveshaft gaiters to the transmission output shafts. d) Adjust the clutch cable (where applicable) as described In Chapter 6.
Diesel models
Removal 27 Seloct a solid, level surface to park the vehicle upon. Give yourself enough space to move around it easily. Apply the handbrake then jack up the front of tho vehicle and support on axlo stands (see Jacking and vehicle support). Remove both front wheels. 28 Unbolt the relay support then remove the batlery and mounting tray as described in Chapter 5A. 29 On models with a cable operated clutch, unscrew the locknut and adjusting nut from the end of the clutch cable and disconnect the cable from the transmission. Recover the damper block. On models with a hydraulically operated clutch, unscrew the mounting botts. release the slave cylinder pushrod from the release arm on the transmission, then position the cylinder to one side, 30 Unscrew the nut and disconnect the gear selector rod from the lever on the transmission. 31 Disconnect the gear engagement cable from the control lever then slide out the clip and release the cable from the mounting bracket. 32 Unbolt the electronic rev counter sensor from the upper rear of the belihousing and position it to one side (see illustration).
3.32 Electronic rev counter sensor located in the upper rear of the belihousing
Page 165 of 225
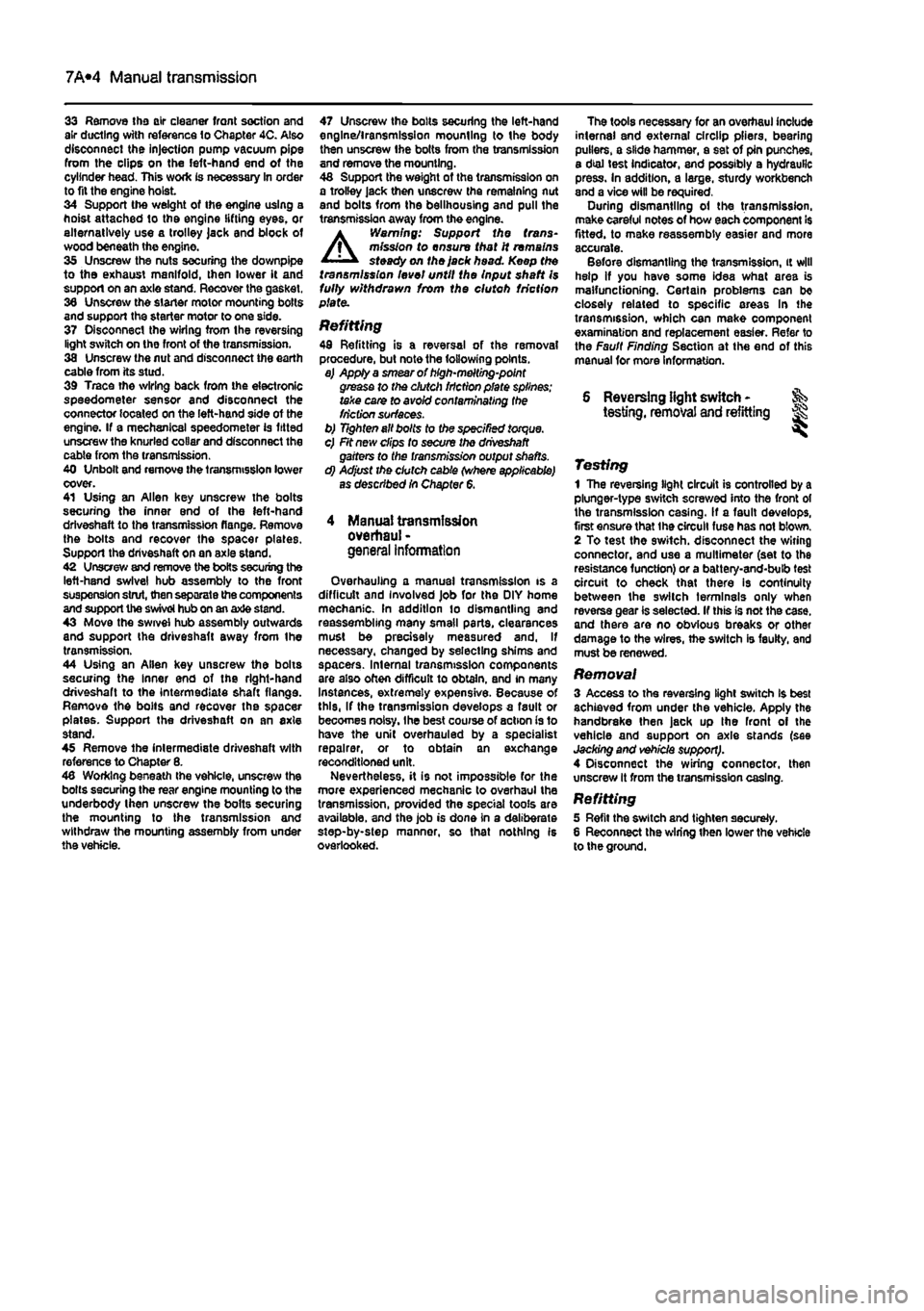
7A«4 Manual transmission
33 Remove lha air cleaner front section and air ducting with reference to Chapter 4C. Also disconnect the injection pump vacuum pipe from the clips on the left-hand end of the cylinder head. This work is necessary in order to fit the engine hoist 34 Support the weight of the engine using a hoist attached to the engine lifting eyes, or alternatively use a trolley Jack and block of wood beneath the engine. 35 Unscrew the nuts securing the downpipe to the exhaust manifold, then lower it and support on an axle stand. Recover the gasket. 36 Unscrew the starter motor mounting bolts and support the starter motor to one side. 37 Disconnect the wiring from the reversing light switch on the front of the transmission. 38 Unscrew the nut and disconnect the earth cable from its stud. 39 Trace the wiring back from the electronic speedometer sensor and disconnect the connector located on the left-hand side ot the engine. If a mechanical speedometer Is fitted unscrew the knurled collar and disconnect the cabte from the transmission. 40 Unbolt and remove the transmission lower cover. 41 Using an Allen key unscrew the bolts securing the inner end of the left-hand driveshaft to the transmission flange. Remove the bolts and recover the spacer plates. Support the driveshaft on an axle stand. 42 Unscrew and remove the bolts securing the left-hand swivel hub assembly to the front suspension strut, then separate the components and support the swivel hub on an axle stand. 43 Move the swrvel hub assembly outwards and support the driveshaft away from Ihe transmission. 44 Using an Allen key unscrew the bolts securing the Inner end of the right-hand driveshaft to the intermediate shaft flange. Remove the bolts and recover the spacer plates. Support the driveshaft on an axle stand. 45 Remove the intermediate driveshaft with reference to Chapter 8. 46 Working beneath the vehicle, unscrew the bolts securing the rear engine mounting to the underbody then unscrew the bolts securing the mounting to the transmission and withdraw the mounting assembly from under the vehicle.
47 Unscrew the bolts securing the left-hand engine/transmission mounting to the body then unscrew Ihe bolts from the transmission and remove the mounting. 48 Support the weight of the transmission on a trolley jack then unscrew the remaining nut and bolts from the bellhousing and pull the transmission away from the engine.
A
Warning: Support the trans-mission to ensure that It remains steady o/i the jack head. Keep the transmission level until the Input shaft
1$
fully withdrawn from the clutch friction plate.
Refitting 48 Refitting is a reversal of the removal procedure, but note the following points. a) Appiy a smear* of high-meiting-point grease to the clutch friction piate splines; take care to avoid contaminating the friction surfaces. b) Tighten all bolts to the specified torque. c) Fit new clips to secure the driveshaft gaiters to the transmission output shafts. d) Adjust the clutch cable (where applicable) as described In Chapter 6.
4 Manual transmission overhaul -general Infomtatlon
Overhauling a manual transmission is a difficult and Involved Job for the DIY home mechanic. In addition to dismantling and reassembling many small parts, clearances must be precisely measured and, if necessary, changed by selecting shims and spacers. Internal transmission components are also often difficult to obtain, and in many Instances, extremely expensive. Because of this, If the transmission develops a fault or becomes noisy. Ihe best course of action is to have the unit overhauled by a specialist repairer, or to obtain an exchange reconditioned unit. Nevertheless, it is not impossible for the more experienced mechanic to overhaul the transmission, provided the special tools are available, and the Job is done in a deliberate step-by-step manner, so that nothing is overlooked.
The tools necessary for an overhaul include internal and external clrclip pliers, bearing pullers, a slide hammer, a sat of pin punches, a dial test Indicator, and possibly a hydraulic press. In addition, a large, sturdy workbench 8od a vice will be required. During dismantling o1 the transmission, make careful notes of how each component
1$
fitted, to make reassembly easier and more accurate. Before dismantling the transmission, it will help if you have some idea what area is malfunctioning. Certain problems can be closely related to specific areas In the transmission, which can make component examination and replacement easier. Refer to the Fault Finding Section at the end of this manual for more Information.
5 Reversing light switch -testing, removal and refitting ||
Testing 1 The reversing light circuit is controlled by a plunger-type switch screwed into the front of the transmission casing. If a fault develops, first ensure that Ihe circuit fuse has not blown. 2 To test the switch, disconnect the wiring connector, and use a multimeter (set to the resistance function) or a battery-and-bulb test circuit to check that there is continuity between the switch terminals only when reverse gear is selected. If this is not the case, and there are no obvious breaks or other damage to the wires, the switch is faulty, and must be renewed.
Removal 3 Access to the reversing light switch Is best achieved from under the vehicle. Apply the handbrake then jack up Ihe front of the vehicle and support on axle stands (see Jacking and vehicle support). 4 Disconnect the wiring connector, then unscrew It from the transmission casing.
Refitting 5 Refit the switch and tighten securely. 6 Reconnect the wiring then lower the vehicle to the ground.
Page 169 of 225
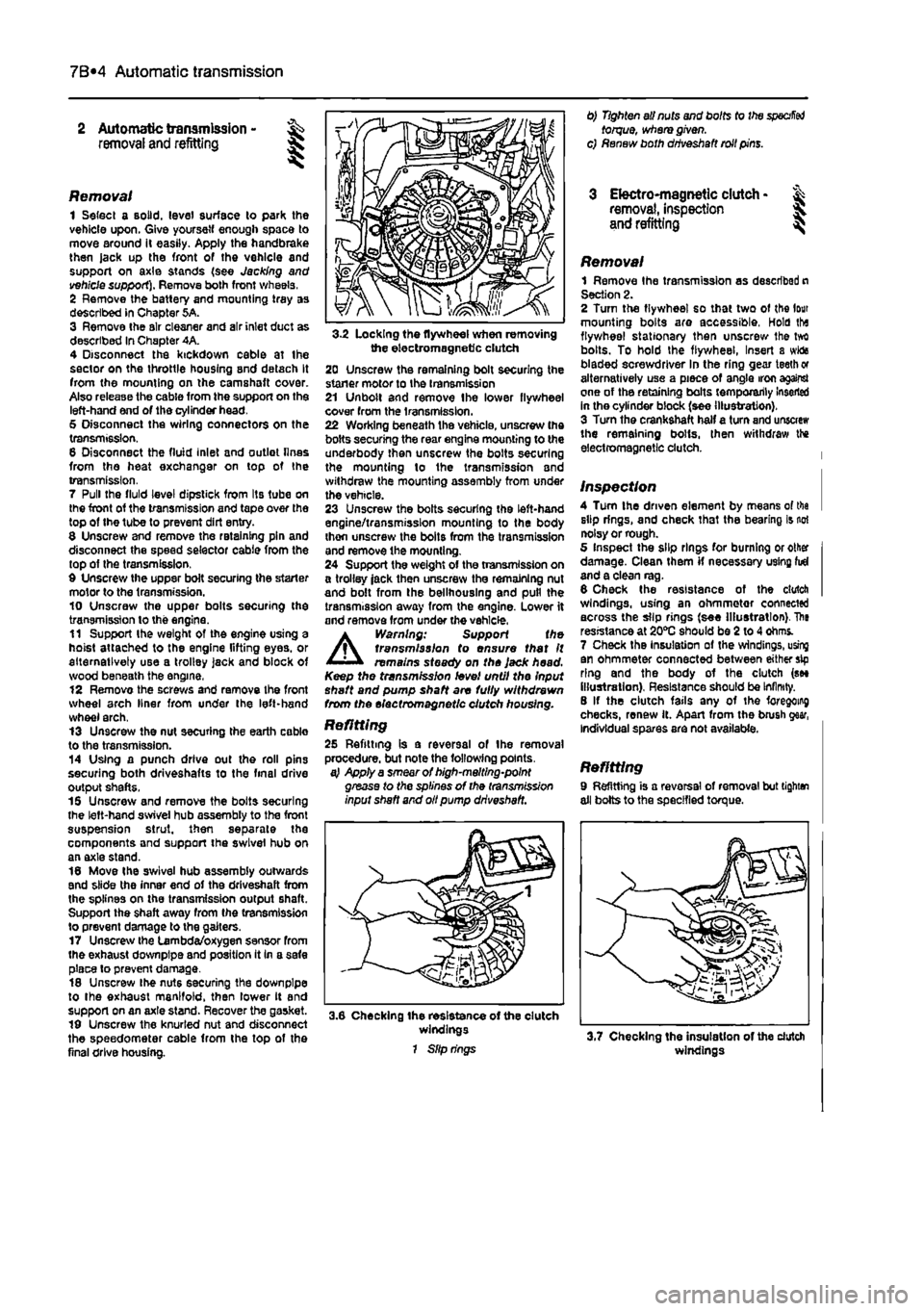
7B*4 Automatic transmission
2 Automatic transmission - ^ removal and refitting St
Removal 1 Select a solid, level surface to park the vehicle upon. Give yourself enough space to move around it easily. Apply the handbrake then jack up the front of the vehicle and support on axle stands (see Jacking and vehicle support). Remove both front wheels, 2 Remove the battery and mounting tray as described In Chapter 5A. 3 Remove the air cleaner and air inlet duct as described In Chapter 4A. 4 Disconnect the kickdown cable at the sector on the throttle housing and detach It from the mounting on the camshaft cover. Also release the cable from the support on the left-hand end of the cylinder head. 5 Disconnect the wiring connectors on the transmission. 6 Disconnect the fluid inlet and outlet Unas from the heat exchanger on top of the transmission. 7 Pull the fluid level dipstick from Its tube on the front of the transmission and tape over the top of the tube to prevent dirt entry. 8 Unscrew and remove the retaining pin and disconnect the speed selector cable from the top of the transmission. 9 Unscrew the upper bolt securing the starter motor to the transmission. 10 Unscrew the upper bolts securing the transmission to the engine. 11 Support the weight of the engine using a hoist attached to the engine lifting eyes, or alternatively UBO a trolley jack and block of wood beneath the engine, 12 Remove the screws and remove the front wheel arch liner from under the left-hand wheel arch. 13 Unscrew the nut securing the earth cablo to the transmission. 14 Using a punch drive out the roll pins securing both driveshafts to the final drive output shafts. 15 Unscrew and remove the bolts securing the left-hand swivel hub assembly to the front suspension strut, then separate the components and support the swivel hub on an axle stand. 16 Move the swivel hub assembly outwards and slide the inner end of the driveshaft from the splines on the transmission output shaft. Support the shaft away from the transmission to prevent damage to the gaiters. 17 Unscrew the lambdafoxygen sensor from the exhaust downpipe and position it In a safe place to prevent damage. 18 Unscrew ihe nuts securing the downpipe to Ihe exhaust manifold, then lower It and suppon on an axle stand. Recover the gasket. 19 Unscrew the knurled nut and disconnect the speedometer cable from the top of the final drive housing.
3-2 Locking the flywheel when removing the electromagnetic clutch 20 Unscrew the remaining bolt securing the staner motor to the transmission 21 Unbolt and remove Ihe lower flywheel cover from the transmission. 22 Working beneath the vehicle, unscrew the bolts securing the rear engine mounting to the underbody then unscrew the bolts securing the mounting lo the transmission and withdraw the mounting assembly from under the vehicle. 23 Unscrew the bolts securing the left-hand engine/transmission mounting to the body thon unscrew the bolts from the transmission and remove the mounting. 24 Support the weight of the transmission on a trolley jack then unscrew the remaining nut and bolt from the bellhouslng and pull the transmission away from the engine. Lower it and remove from under the vehicle.
A
Warning: Support the transmission to ensure that It remains steady on the Jack head. Keep the transmission level until the Input shaft and pump shaft are fully withdrawn from the electromagnetic clutch housing.
Refitting 25 Refitting is a reversal of the removal procedure, but note the following points. a} Apply a smear of high-melting-point grease to the splines of the transmission input shaft and oil pump driveshaft.
3.6 Checking the resistance of the clutch windings 1 Slip rings
0) Tighten all nuts and bolts to the
specified
torque, where given, c) Renew both driveshaft roll pins.
3 Electro-magnetic clutch • & removal, inspection 5. and refitting ^
Removal 1 Remove Ihe transmission as described n Section 2. 2 Turn the flywheel so that two of the lour mounting bolts are accessible, Hold tha flywheel stationary then unscrew Ihe tvrt bolts. To hold the flywheel, Insert a wida bladed screwdriver In the ring gear teeth or alternatively use a piece of angle iron against one of the retaining bolts temporarily Inserted in the cylinder block (see illustration). 3 Turn the crankshaft half a turn and unscrew the remaining bolts, then withdraw the electromagnetic clutch.
Inspection 4 Turn the driven element by means of tha slip rings, and check that the bearing is not noisy or rough. 5 Inspect the slip rings for burning or other damage. Clean them if necessary using fid and a clean rag. 6 Check the resistance of the clutch windings, using an ohmmetor connected across the slip rings (see Illustration). The resistance at 20*0 should be 2 to 4 ohms. 7 Check the Insulation of the windings, using an ohmmeter connected between either sip ring and the body of the clutch (see illustration). Resistance should be Infinity. 8 If the clutch fails any of the foregoing checks, renew it. Apart from the brush gear, Individual spares are not available.
Refitting 9 Refitting is a reversal of removal but tighten all bolts to the specified torque.
windings
Page 174 of 225
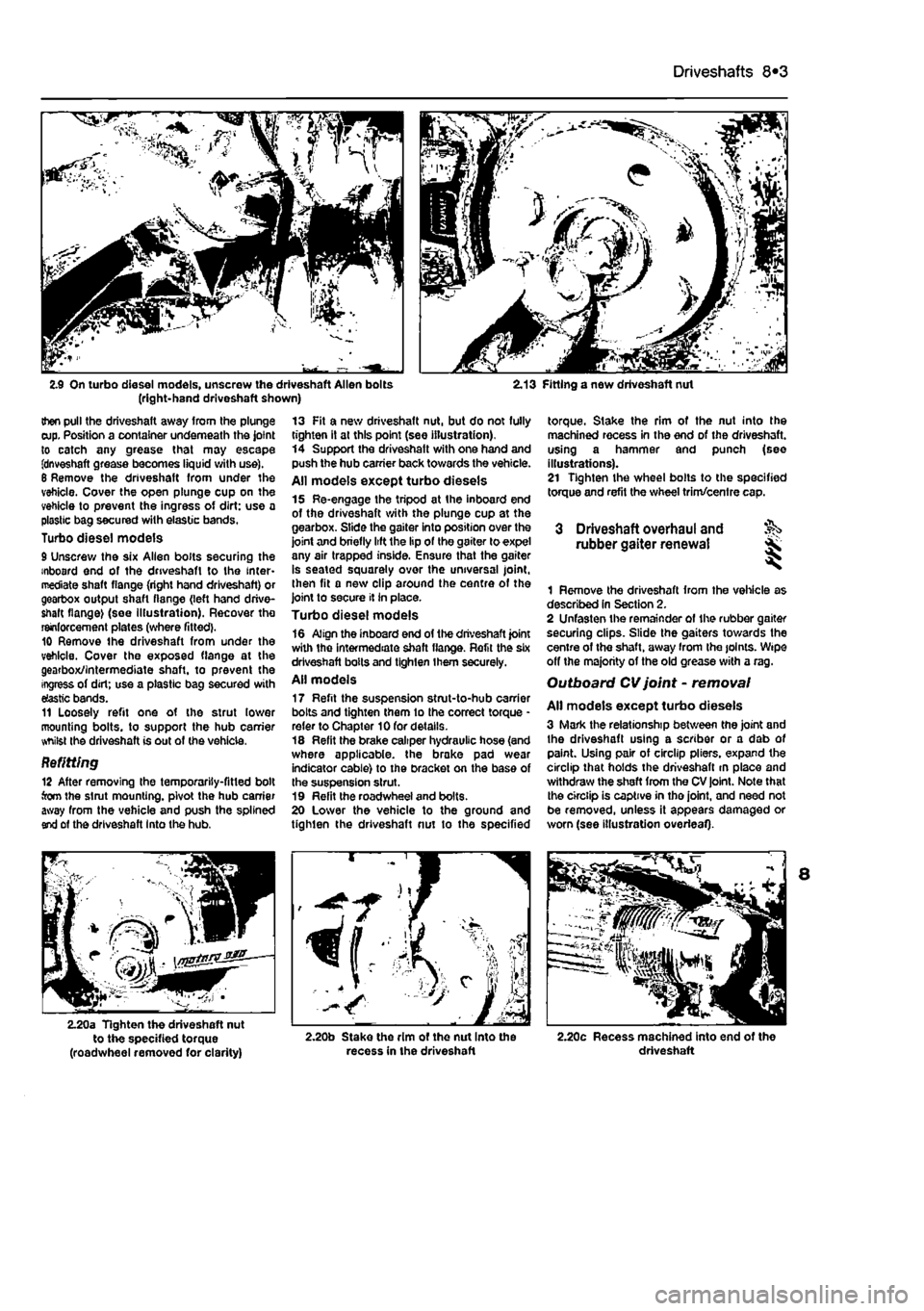
Driveshafts 8*3
2.9 On turbo diesel models, unscrew the driveshaft Allen bolts (right-hand driveshaft shown) 2.13 Fitting a new driveshaft nut
then pull the driveshaft away from the plunge cup. Position a container underneath the joint to catch any grease that may escape fdnveshaft grease becomes liquid with use). 6 Remove the driveshaft from under the vehicle. Cover the open plunge cup on the vehicle to prevent the ingress of dirt: use a plastic bag secured with elastic bands. Turbo diesel models 9 Unscrew the six Allen bolts securing the inboard end of the driveshaft to the inter-mediate shaft flange (right hand driveshaft) or gearbox output shaft flange (left hand drive-shaft flange) (see Illustration). Recover tho reinforcement plates (where fitted). 10 Remove the driveshaft from under the vehicle. Cover the exposed flange at the gearbox/intermediate shaft, to prevent the ingress of dirt; use a plastic bag secured with elastic bands. 11 Loosely refit one of the strut lower mounting bolts, to support the hub carrier whilst the driveshaft is out of the vehicle.
Befitting 12 After removing the temporarily-fitted bolt torn the strut mounting, pivot the hub carrier away from the vehicle and push the splined end of the driveshaft Into the hub.
13 Fit a new driveshaft nut, but do not fully tighten it at this point (see illustration). 14 Support the driveshatt with one hand and push the hub carrier back towards the vehicle. All models except turbo diesels 15 Re-engage the tripod at the inboard end of the driveshaft with the plunge cup at the gearbox. Slide the gaiter into position over the joint and briefly lift the lip of the gaiter to expel any air trapped inside. Ensure that the gaiter is seated squarely over the universal joint, then fit a new clip around the centre of the joint to secure it in place. Turbo diesel models 16 Align the inboard end of the driveshaft joint with the intermediate shaft flange. Refit the six driveshaft bolts and tighten them securely. All models 17 Refit the suspension strut-to-hub carrier bolts and tighten them to the correct torque * refer to Chapter 10 for details. 18 Refit the brake caliper hydraulic hose (and where applicable, the brake pad wear indicator cable) to the bracket on the base of the suspension strut. 19 Refit the roadwheel and bolts. 20 Lower the vehicle to the ground and tighten the driveshaft nut to the specified
torque. Stake the rim of the nut into the machined recess in the end of the driveshaft. using a hammer and punch (see illustrations). 21 Tighten the wheel bolts to the specified torque and refit the wheel trim/centre cap.
3 Driveshaft overhaul and rubber gaiter renewal
1 Remove the driveshaft from the vehicle as described In Section 2. 2 Unfasten the remainder of the rubber gaiter securing clips. Slide the gaiters towards the centre of the shaft, away from Ihe joints. Wipe off the majority of the old grease with a rag. Outboard CV joint - removal
All models except turbo diesels 3 Mark the relationship between the joint and the driveshaft using a scriber or a dab of paint. Using pair of circlip pliers, expand the circlip that holds the driveshaft m place and withdraw the shaft from the CV joint. Note that the circlip is captive in tho joint, and need not be removed, unless it appears damaged or worn (see illustration overleaf).
2.20a Tighten the driveshaft nut to the specified torque (roadwheel removed for clarity) 2.20b Stake the rim ot the nut Into the recess in the driveshaft 2.20c Recess machined into end of the driveshaft
Page 176 of 225
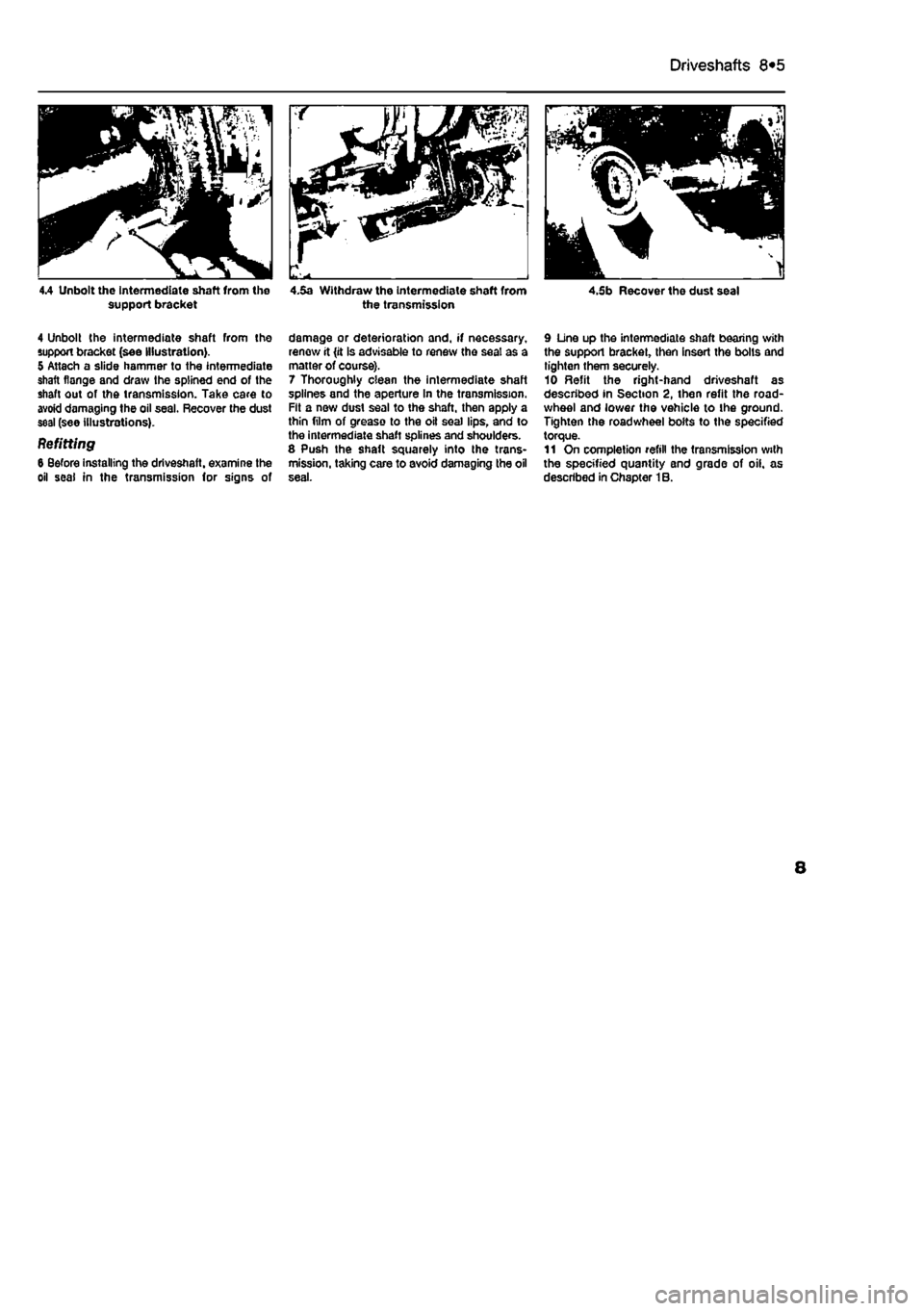
Driveshafts 8*5
4.4 Unbolt the Intermediate shaft from the 4.5a Withdraw the intermediate shaft from support bracket the transmission 4.5b Recover the dust seal
4 Unbolt the intermediate shaft from the support bracket (see Illustration). 5 Attach a slide hammer to the intermediate shaft flange and draw the splined end of the shaft out of the transmission. Take care to avoid damaging the oil seal. Recover the dust seal (see illustrations).
Refitting 6 Before installing the driveshaft, examine the oil seal in the transmission for signs of
damage or deterioration and, if necessary, renew it (it is advisable to renew the seal as a matter of course). 7 Thoroughly- clean the intermediate shaft splines and the aperture In the transmission. Fit a new dust seal to the shaft, then apply a thin film of grease to the oil seal lips, and to the intermediate shaft splines and shoulders. 8 Push the shaft squarely into the trans-mission, taking care to avoid damaging the oil
9 Line up the intermediate shaft bearing with the suppori bracket, then insert the bolls and tighten them securely. 10 Refit the right-hand driveshaft as described in Section 2, then refit the road-wheel and lower the vehicle to the ground. Tighten the roadwheel bolts to the specified torque. 11 On completion refill the transmission with the specified quantity and grade of oil. as described in Chapter 1B.
8
Page 179 of 225
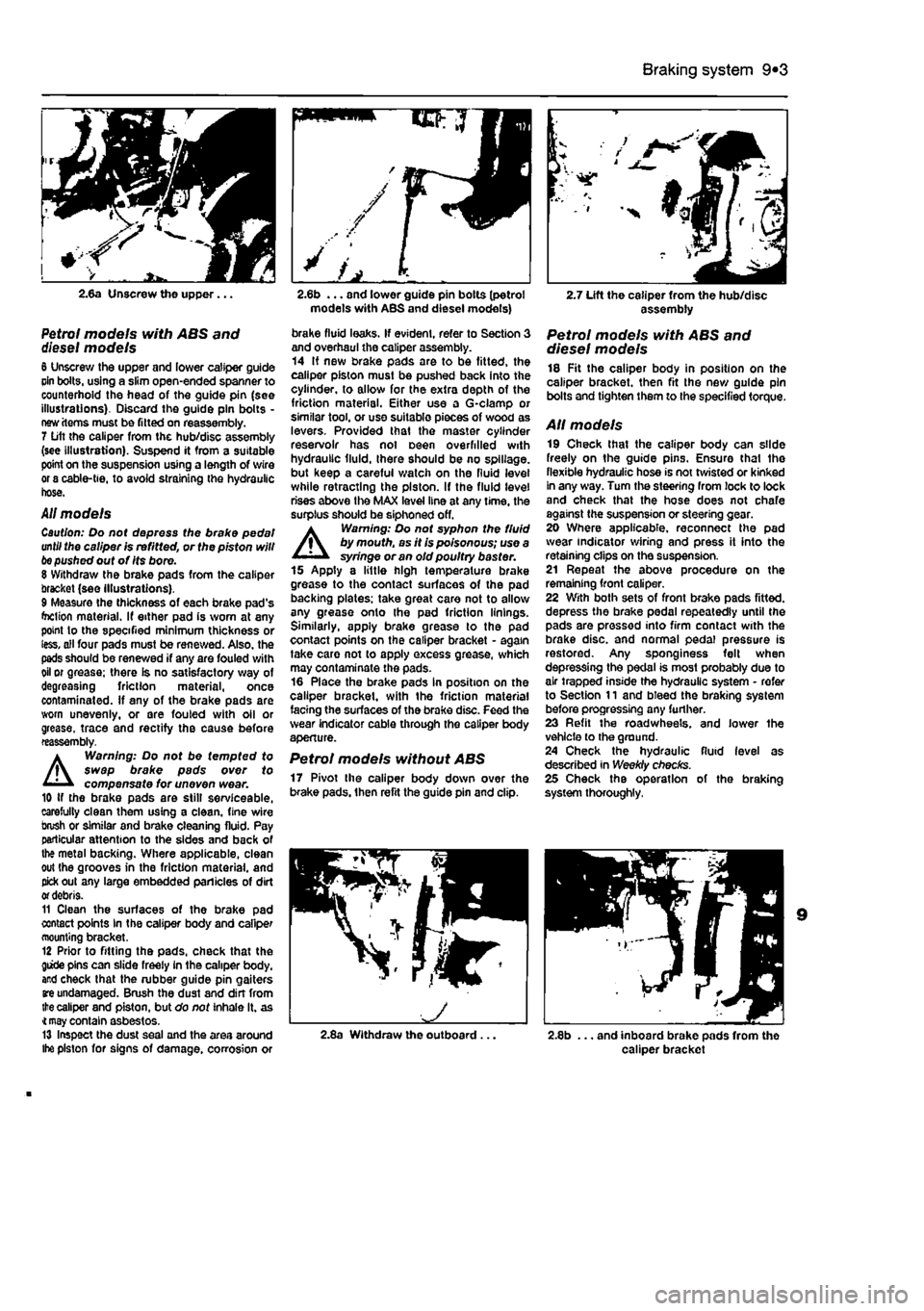
Braking system 9®3
2.6a Unscrew the upper...
Petrol models with ABS and diesel models 6 Unscrew the upper and lower caliper guide cin bolts, using a slim open-ended spanner to counterhold the head of the guide pin (see illustrations). Discard the guide pin bolts -new items must be fitted on reassembly. 7 Lift the caliper from the hub/disc assembly (see illustration). Suspend it from a suitable point on the suspension using a length of wire or 8 cable-tie, to avoid straining the hydraulic hose.
All models Caution: Do not depress the brake pedal until the caliper is refitted, or the piston will
be
pushed out of Its bore. 8 Withdraw the brake pads from the caliper bracket (see illustrations). 9 Measure the thickness of each brake pad's foclion material. If either pad is worn at any point to the specified minimum thickness or less, all four pads must be renewed. Also, the pads should be renewed if any are fouled with oil or grease; there is no satisfactory way of degreasing friction material, once contaminated. If any of the brake pads are worn unevenly, or are fouled with oil or grease, trace and rectify the cause before reassembly.
A
Warning: Do not be tempted to swap brake pads over to compensate for uneven wear. 10 if the brake pads are still serviceable, carefully clean them using a clean, fine wire brush or similar and brake cleaning fluid. Pay particular attention to the sides and back of the metal backing. Where applicable, clean out the grooves in the friction material, and pick out any large embedded panicles of dirt
or
debris. 11 Clean the surfaces of the brake pad contact points In the caliper body and caliper mounting bracket. 12 Prior to fitting the pads, check that the giide pins can slide freely in the caliper body, and check that the rubber guide pin gaiters
are
undamaged. Brush the dust and din from
the
caliper and piston, but do not inhale it. as
4 may
contain asbestos. 13 Inspect the dust seal and the area around Ihe piston for signs of damage, corrosion or
models with ABS and diesel models)
brake fluid leaks. If evident, refer to Section 3 and overhaul the caliper assembly. 14 If new brake pads are to be fitted, the caliper piston must be pushed back into the cylinder, to allow for the extra depth of the friction material. Either use a G-clamp or similar tool, or use suitable pieces of wood as levers. Provided that the master cylinder reservoir has not oeen overfilled with hydraulic fluid, there should be no spillage, but keep a careful watch on the fluid level while retracting the piston. If the fluid level rises above the MAX level line at any time, the surplus should be siphoned off. A Warning: Do not syphon the fluid by mouth, as it is poisonous; use a syringe or an old poultry baster. 15 Apply a little high temperature brake grease to the contact surfaces of the pad backing plates: take great care not to allow any grease onto the pad friction linings. Similarly, apply brake grease to the pad contact points on the caliper bracket - again take care not to apply excess grease, which may contaminate the pads. 16 Place the brake pads in position on the caliper bracket, with the friction material facing the surfaces of the brake disc. Feed the wear indicator cable through the caliper body aperture.
Petrol models without ABS 17 Pivot the caliper body down over the brake pads, then refit the guide pin and clip.
2.7 Lift the caliper from the hub/disc assembly
Petrol models with ABS and diesel models 18 Fit the caliper body in position on the caliper bracket, then fit the new guide pin bolts and tighten them to the specified torque.
AH models 19 Check that the caliper body can slide freely on the guide pins. Ensure that the flexible hydraulic hose is not twisted or kinked In any way. Turn the steering from lock to lock and check that the hose does not chafe against the suspension or steering gear. 20 Where applicable, reconnect the pad wear indicator wiring and press it into the retaining clips on the suspension. 21 Repeat the above procedure on the remaining front caliper. 22 With both sets of front brake pads fitted, depress the brake pedal repeatedly until the pads are pressed into firm contact with the brake disc, and normal pedal pressure is restored. Any sponginess felt when depressing the pedal is most probably due to air trapped inside the hydraulic system - refer to Section 11 and bleed the braking system before progressing any further. 23 Refit the roadwheels. and lower the vehicle to the ground. 24 Check the hydraulic fluid level as described in Weekly checks. 25 Check the operation of the braking system thoroughly,
2.8a Withdraw the outboard... 2.8b ... and inboard brake pads from the caliper bracket