4B 1 FIAT PUNTO 1998 176 / 1.G Manual Online
[x] Cancel search | Manufacturer: FIAT, Model Year: 1998, Model line: PUNTO, Model: FIAT PUNTO 1998 176 / 1.GPages: 225, PDF Size: 18.54 MB
Page 81 of 225
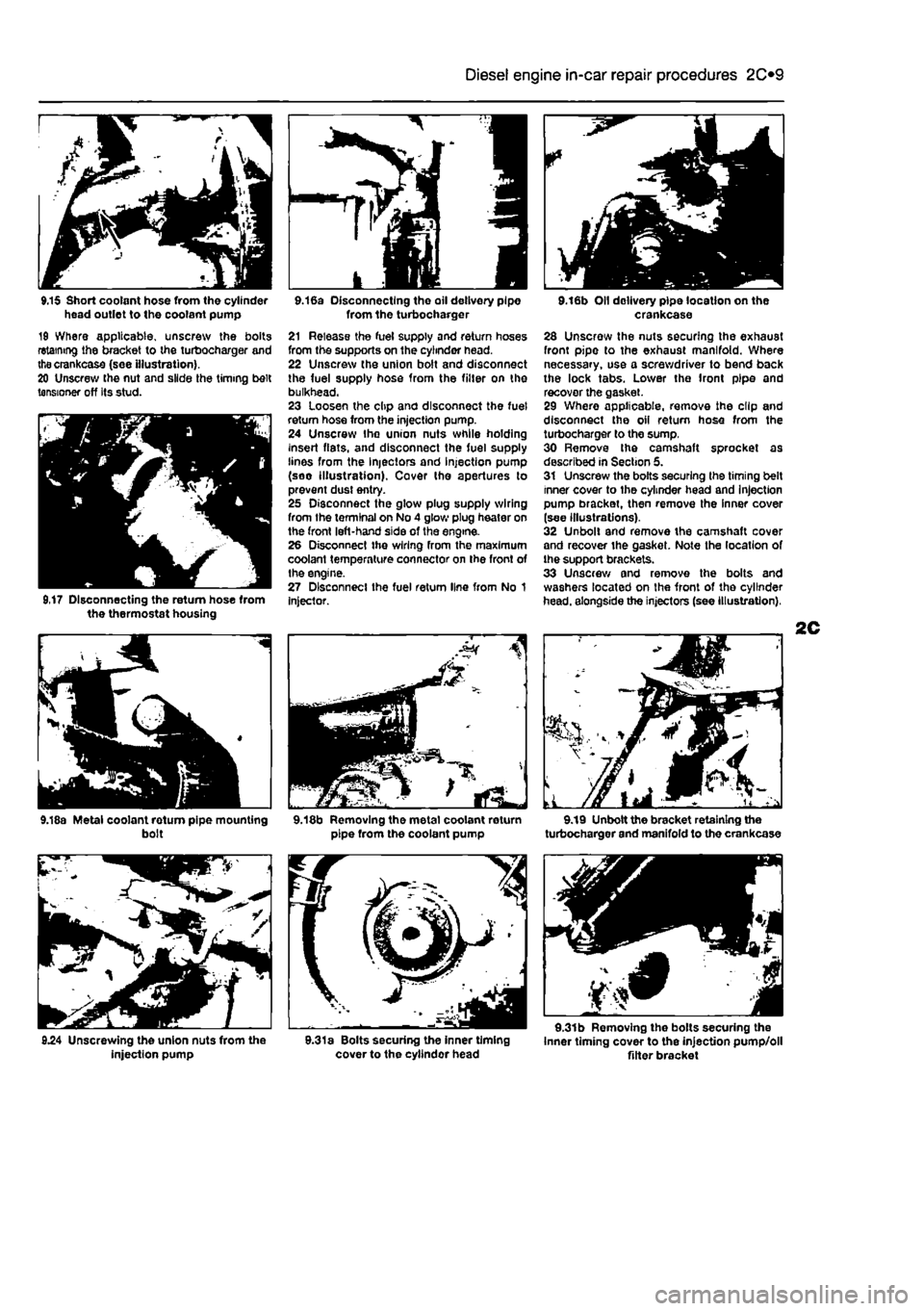
Diesel engine in-car repair procedures
2C*11
9.15 Short coolant hose from the cylinder head outlet to the coolant pump 19 Where applicable, unscrew the bolts retaining the bracket to the turbocharger and thecrankcase (see illustration). 20 Unscrew the nut and slide the timing belt tensioner off Its stud.
9,17 Disconnecting the return hose from the thermostat housing
9.18a Metal coolant rotum pipe mounting bolt
injection pump
9.16a Disconnecting the oil delivery pipe from the turbocharger 21 Release the fuel supply and return hoses from the supports on the cylinder head. 22 Unscrew the union bolt and disconnect the fuel supply hose from the filter on the bulkhead. 23 Loosen the clip and disconnect the fuel return hose from the injection pump. 24 Unscrew Ihe union nuts while holding insert fiats, and disconnect the fuel supply lines from the Injectors and injection pump (soo illustration). Cover tho apertures to prevent dust entry. 25 Disconnect the glow plug supply wiring from the terminal on No 4 glow plug heater on the front left-hand side of the engine. 26 Disconnect the wiring from the maximum coolant temperature connector on the front of the engine. 27 Disconnect the fuel return line from No 1 Injector.
9.18b Removing the metal coolant return pipe from the coolant pump
9.31a Bolts securing the inner timing cover to the cyllndor head
9.16b Oil delivery pipe location on the crankcase 28 Unscrew the nuts securing the exhaust front pipe to the exhaust manifold. Where necessary, use a screwdriver to bend back the lock tabs. Lower the front pipe and recover the gasket. 29 Where applicable, remove the clip and disconnect the oil return hose from the turbocharger to the sump. 30 Remove the camshaft sprocket as described in Section 5. 31 Unscrew the bolts securing the timing belt inner cover to the cylinder head and injection pump bracket, then remove the inner cover (see illustrations). 32 Unbolt and remove the camshaft cover and recover the gasket. Note the location of the support brackets. 33 Unscrew and remove the bolts and washers located on the front of the cylinder head, alongside the injectors (see illustration),
9.19 Unbolt the bracket retaining the turbocharger and manifold to the crankcase
9.31b Removing the bolts securing the Inner timing cover to the injection pump/oll Alter bracket
Page 82 of 225
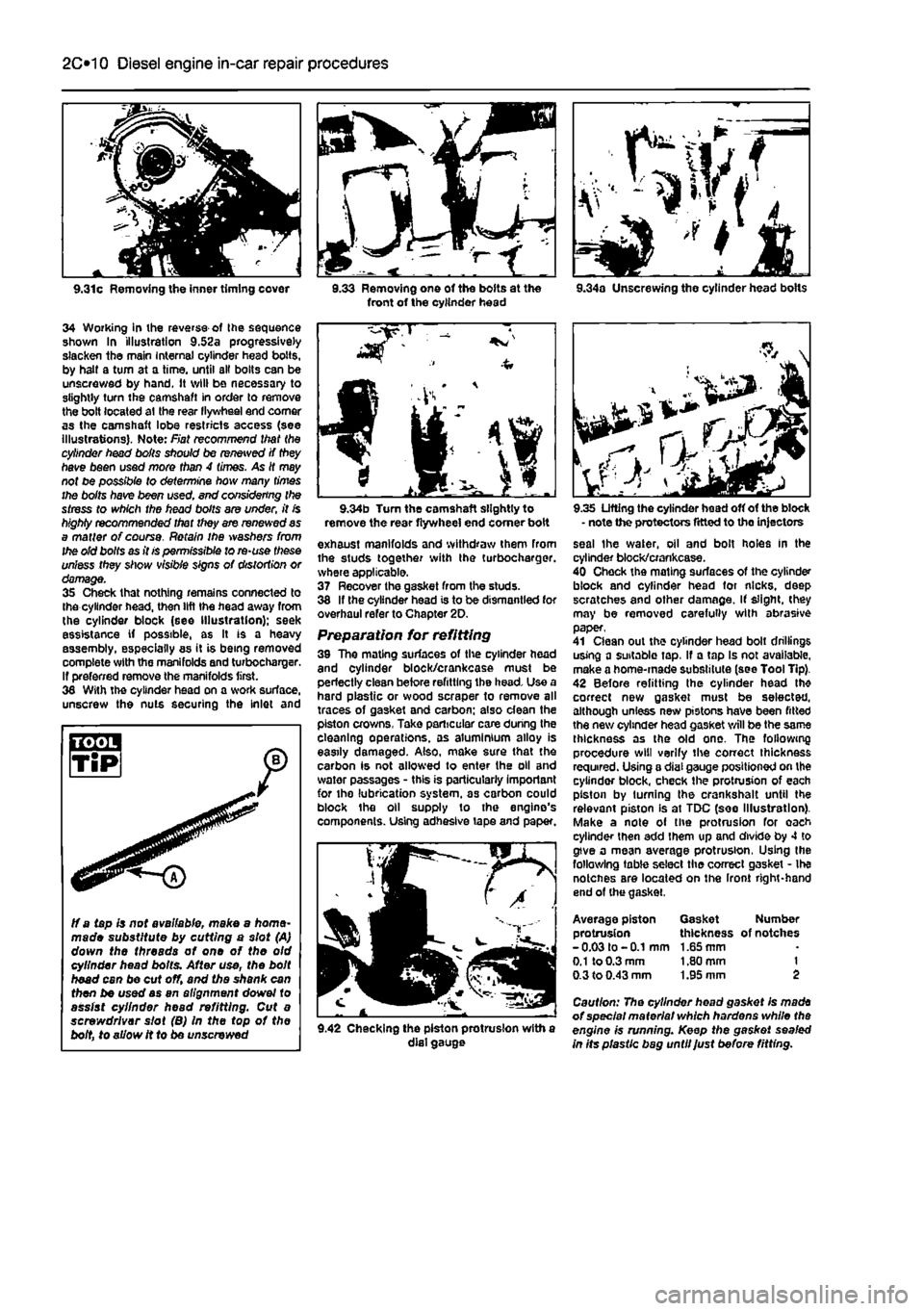
2C*2 Diesel engine in-car repair procedures
9.31c Removing the inner timing cover
34 Working in ihe reverse of Ihe sequence shown In illustration 9.52a progressively slacken the main Internal cylinder head bolts, by halt a turn at a time, until all bolts can be unscrewed by hand. It will be necessary to slightly turn the camshaft in order to remove the bolt located at the rear llywheel end comer as the camshaft lobe restricts access (see illustrations). Note: Fiat recommend that the cylinder head boils should be renewed if they have been used more than 4 times. As It may not be possible to determine how many times the bolts have been used. end considering the stress to which the head bolts are under, it is highly recommended that they are renewed as a matter of course. Retain ihe washers from the old bolts as it is permissible to re-use these unless they show visible signs of distortion or damage. 35 Check that nothing remains connected to the cylinder head, then lift the head away from the cylinder block (see Illustration); seek assistance if possible, as It is a heavy assembly, especially as it is being removed complete with the manifolds and turbochargar. If preferred remove the manifolds first. 36 With the cylinder head on a work surface, unscrew the nuts securing the inlet and
3.33 Removing one of the bolts at the front of the cylinder head 9.34a Unscrewing the cylinder head bolts
ff a tapis not available, make a home-made substitute by cutting a slot (A) down the threads of one of the old cylinder head bolts. After use, the bolt head can be cut off, and the shank can then be used as an alignment dowel to assist cylinder head refitting. Cut a screwdriver slot (B) In the top of the bolt, to allow it to be unscrewed
9.34b Turn the camshaft slightly to remove the rear flywheel end comer boit exhaust manifolds and withdraw them from the studs together with the turbocharger. where applicable. 37 Recover the gasket from the studs. 38 If the cylinder head is to be dismantled for overhaul refer to Chapter 2D. Preparation for refitting 39 The mating surfaces of the cylinder head and cylinder block/crankcase must be perfectly clean before refitting the head. Use a hard plastic or wood scraper to remove all traces of gasket and carbon; also dean the piston crowns, Take particular care during the cleaning operations, as aluminium alloy is easily damaged. Also, make sure that the carbon is not allowed to enter the oil and water passages - this is particularly important for the lubrication system, as carbon could block the oil supply to the engine's components. Using adhesive tape and paper.
9.42 Checking the piston protrusion with a dial gauge
9.35 Lifting the cylinder head off of the block - note the protectors fitted to the injectors seal the water, oil and bolt holes In the cylinder block/crankcase. 40 Check the mating surfaces of the cylinder block and cylinder head for nicks, deep scratches and other damage. If slight, (hey may be removed carefully with abrasive paper, 41 Clean out the cylinder head bolt drillings using a suitable tap, If a tap Is not available, make a home-made substitute (see Tool Tip). 42 Before refitting the cylinder head th* correct new gasket must be selected, although unless new pistons have been fitted the new cylinder head gasket will be the same thickness as the old one. The following procedure will verify the correct thickness required. Using a dial gauge positioned on the cylinder block, check the protrusion of each piston by turning the crankshalt until the relevant piston Is at TDC (see Illustration). Make a note of the protrusion for oach cylinder then add them up and divide by 4 to give a mean average protrusion, Using the following table select the correct gasket - Ihe notcnes are located on the Iront right-hand end of (he gasket.
Average piston Gasket Number protrusion thickness of notches -0.03 to -0.1 mm 1.65 mm
0.1
to 0.3 mm 1.80 mm 1 0.3 to 0.43 mm 1.95 mm 2
Caution: The cylinder head gasket Is made of special material which hardens while the engine is running. Keep the gasket sealed in Its plastic bag until Just before fitting.
Page 83 of 225
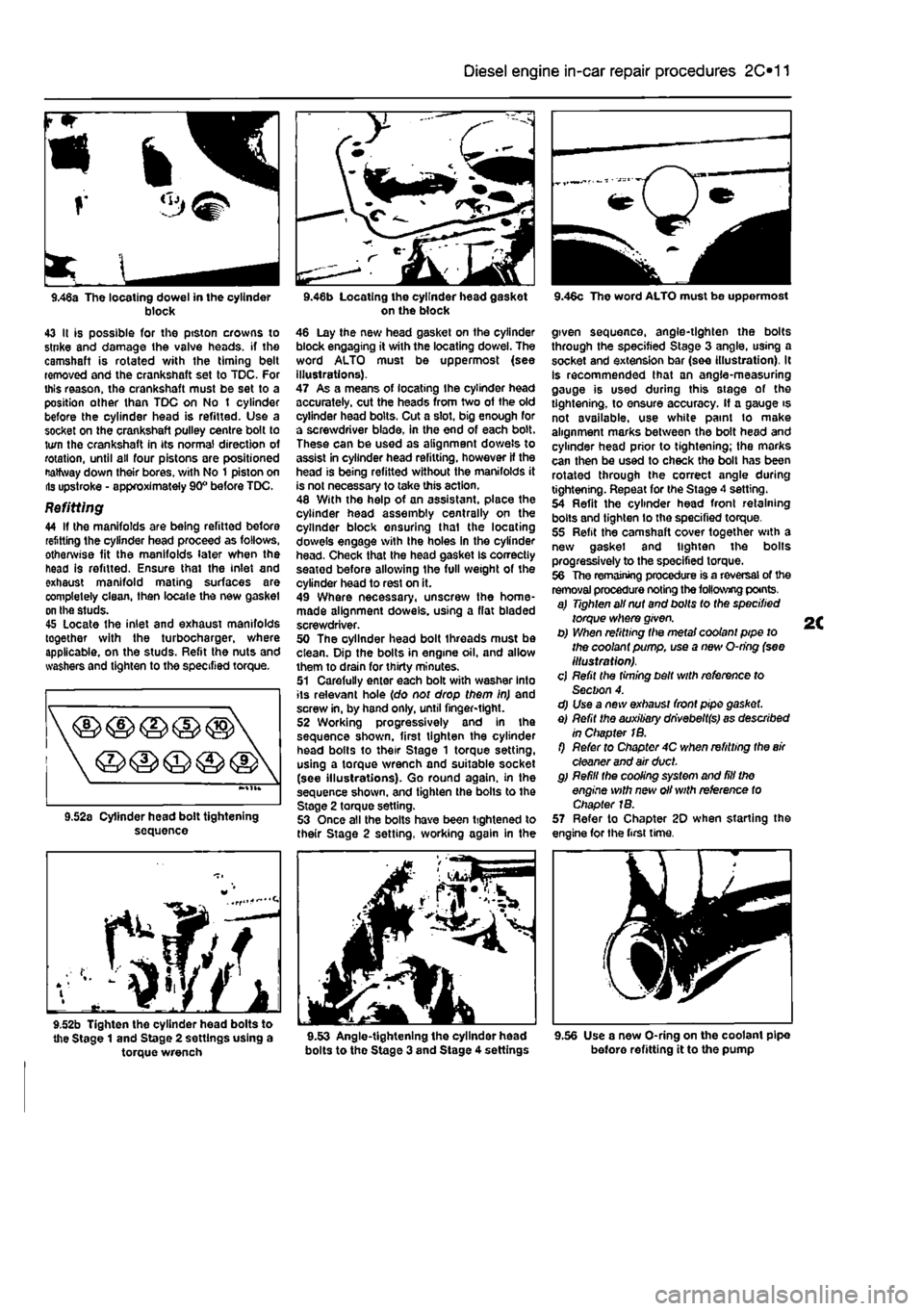
Diesel engine in-car repair procedures 2C*11
r
<3^
9.46a The locating dowel in the cylinder block 43 It is possible for the ptston crowns to stnke and damage the valve heads, if the camshaft is rotated v/ith the timing belt removed and the crankshaft set to TDC. For this reason, the crankshaft must be set to a position other than TDC on No t cylinder before the cylinder head is refitted. Use a socket on the crankshaft pulley centre bolt to turn the crankshaft in its normal direction of rotation, until all four pistons are positioned Halfway down their bores, v/ith No 1 piston on lis upstroke - approximately 90° before TDC.
Refitting 44 If the manifolds are being refitted before refitting the cylinder head proceed as follows, otherwise fit the manifolds later when the head is refitted. Ensure thai the inlet and exhaust manifold mating surfaces are completely clean, then locale the new gasket on the studs. 45 Locate the inlet and exhaust manifolds together with the turbocharger, where applicable, on the studs. Refit the nuts and washers and tighten to the specified torque.
sequence
f^/f
9.52b Tighten the cylinder head bolts to the Stage 1 and Stage 2 settings using a torque wrench
on the block 46 Lay the new head gasket on the cylinder block engaging it with the locating dowel. The word ALTO must be uppermost (see illustrations). 47 As a means of locating Ihe cylinder head accurately, cut the heads from two of the old cylinder head bolts. Cut a slot, big enough for a screwdriver blade, in the end of each bolt. These can be used as alignment dowels to assist in cylinder head refitting, however If the head is being refitted without the manifolds it is not necessary to take this action. 48 With the help of an assistant, place the cylinder head assembly centrally on the cylinder block ensuring thai the locating dowels engage with Ihe holes in the cylinder head. Check that the head gasket Is correctly seatod before allowing the full weight of the cylinder head to rest on it. 49 Where necessary, unscrew the home-made alignment dowels, using a flat bladed screwdriver. 50 The oyllnder head bolt threads must be clean. Dip the bolts in engine oil. and allow them to drain for thirty minutes. 51 Carefully enter each bolt with washer into its relevant hole (do not drop them in) and screw in, by hand only, until finger-tight. 52 Working progressively and In the sequence shown, first tighten the cylinder head bolts to their Stage 1 torque setting, using a torque wrench and suitable socket (see illustrations). Go round again, in the sequence shown, and tighten the bolls to the Stage 2 torque setting. 53 Once all the bolts have been tightened to their Stage 2 setting, working again in the
bolts to the Stage 3 and Stage 4 settings
9.46c The word ALTO must be uppermost
given sequence, angle-tighten the bolts through the specified Stage 3 angle, using a socket and extension bar (see illustration). It Is recommended that an angle-measuring gauge is used during this stage of the tightening, to ensure accuracy. If a gauge is not available, use white paint to make alignment marks between the bolt head and cylinder head prior to tightening; the marks can then be used to check tho bolt has been rotated through the correct angle during tightening. Repeat for the Stage 4 setting. 54 Refit the cylinder head front retaining bolts and tighten lo the specified torque. 55 Refit the camshaft cover together with a new gasket and tighten the bolts progressively to the specified torque. 56 The remaining procedure is a reversal of the removal procedure noting the following points. a) Tighten all nut and bolts to the specified torque where given. b) When refitting the metal coolant pipe to the coolant pump, use a new O-ring (see illustration). cj Refit the timing belt with reference to Section 4. d) Use a new exhaust front pipe gasket. e) Refit the auxiliary dhvebeltfs) as described in Chapter 1B. f) Refer to Chapter 4C when refitting the
air
cleaner and air duct. g) Refill the cooling system and fill the engine with new oil with reference to Chapter 1B. 57 Refer to Chapter 20 when starting the engine for the first time.
9.56 Use a new O-ring on the coolant pipe before refitting it to the pump
Page 84 of 225
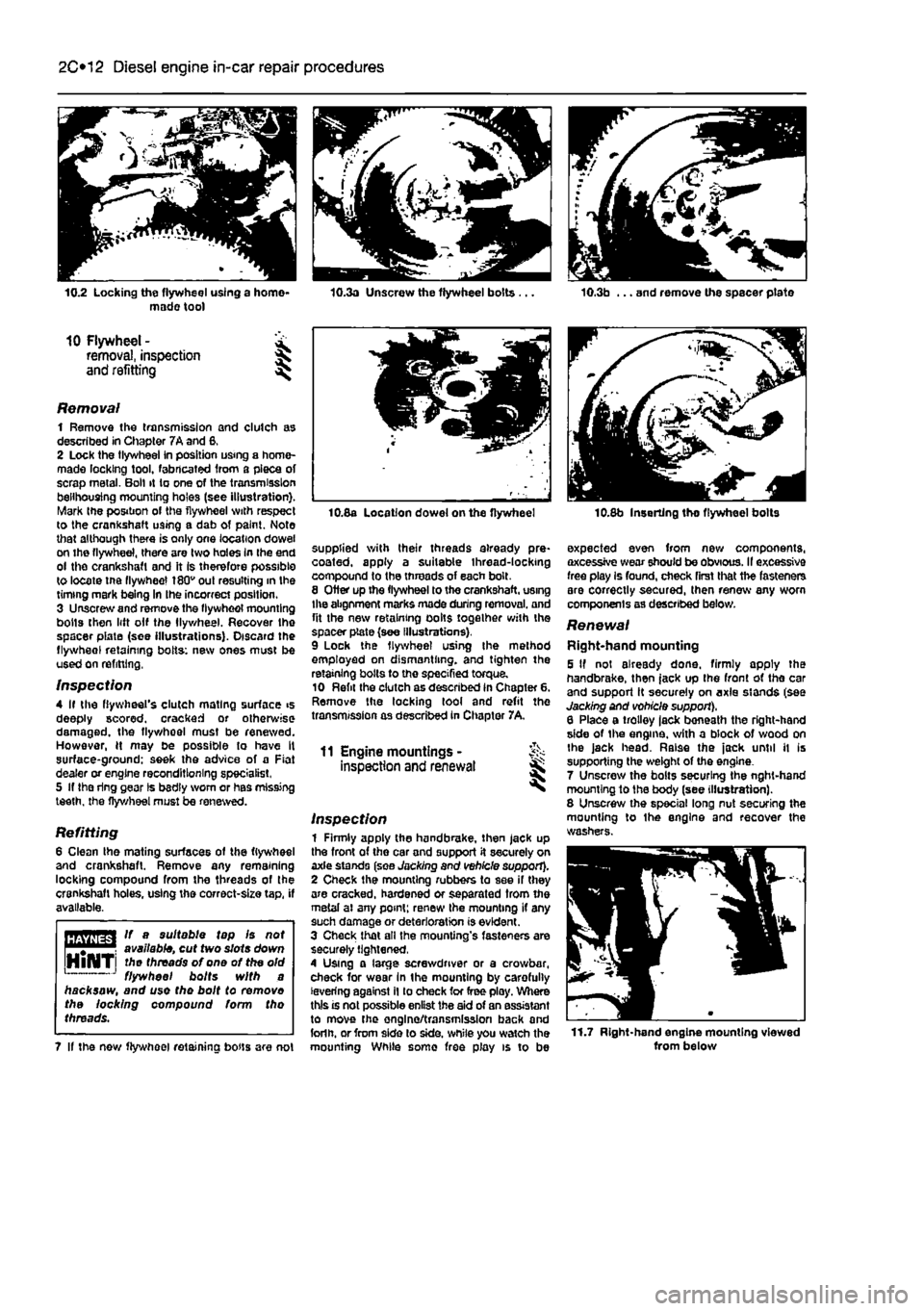
2C*2 Diesel engine in-car repair procedures
10.2 Locking the flywheel using a homo* made tool
10 Flywheel - £ removal, inspection § and refitting ^
Removal 1 Remove the transmission and clutch as described in Chapter 7A and 6, 2 Lock the tlywheei in position using a home-made locking tool, fabricated from a piece of scrap metal. Boll it to one of the transmission belihousing mounting holes (see illustration). Mark the position of the flywheel with respect to the crankshaft using a dab of paint. Note that although there is only one location dowel on the flywheel, there are two holes In the end ol the crankshaft and it Is therefore possible to locate tne flywheel 180v out resulting in the timing mark being In Ihe incorrect position. 3 Unscrew and remove the flywheol mounting bolts then lift olf the llywheel. Recover the spacer piate (see illustrations). Discard the flywheol retaining bolts: new ones must be used on refitting,
Inspection 4 If the flywheel's clutch mating surface >s deeply scored, cracked or otherwise damaged, the flywhoel must be renewed. However, H may be possible to have It surface-ground: seek the advice of a Fiat dealer or engine reconditioning specialist, 5 If the ring gear Is bsdly worn or has missing teeth, the flywheel must be renewed.
Refitting 6 Clean the mating surfaces of the flywheel and crankshaft. Remove any remaining locking compound from the threads of the crankshaft holes, using the correct-size tap, if available.
HBTiffSrl If a suitable tap Is not
Wijlilfil
available, cut two slots down HlNTi threads of one of the old 1 J flywheel bolts with a hacksaw, and use the bolt to removo the locking compound form tho threads.
7 If the now flywheel retaining bous are not
10.8a Location dowel on the flywheel
supplied with their threads already pre* coated, apply a suitable thread-locking compound to the threads of each bolt. 8 Otter up the flywheel to the crankshaft, using the abgnment marks made during removal, and fit the new retaining oolts together with the spacer plate (see Illustrations). 9 Lock the flywheel using Ihe method employed on dismantling, and tighten the retaining bolts to the specified torque. 10 Refit the clutch as described in Chapter 6. Remove the locking tool and refit the transmission as described in Chapter 7A,
11 Engine mountings -inspection and renewal
Inspection 1 Firmly apply the handbrake, then jack up the front of the car and support it securely on axle stands (see Jacking and vehicle support). 2 Check the mounting rubbers to see if they are cracked, hardened or separated from the metal ai any point; renew Ihe mounting if any such damage or deterioration is evident. 3 Check that all the mounting's fasteners are securely tightened, 4 Using a large screwdriver or a crowbar, check for wear In the mounting by carefully levering against il to check for free ploy. Where this is not possible enlist the aid of an assistant to move the onglno/transmission back and forlh. or from side lo side, while you watch the mounting While some free play is to be
10.8b Inserting tho flywheel bolts
expected even from new components, axcessive wear should be obvious. II excessive free play Is found, check first that the fasteners are correctly secured, then renew any worn components as described below.
Renewal Right-hand mounting 5 If not already done, firmly apply the handbrake, then jack up the front ot tho car and support it securely on axle stands (see Jacking and vohicle support), 6 Place a trolley lack beneath the right-hand side of the engine, with a block of wood on Ihe jack head. Raise the jack until it is supporting the weight of the engine. 7 Unscrew the bolts securing the nght-hand mounting to the body (see illustration). 8 Unscrew the special long nut securing the mounting to Ihe engine and recover the washers.
11.7 Right-hand engine mounting viewed from below
Page 85 of 225
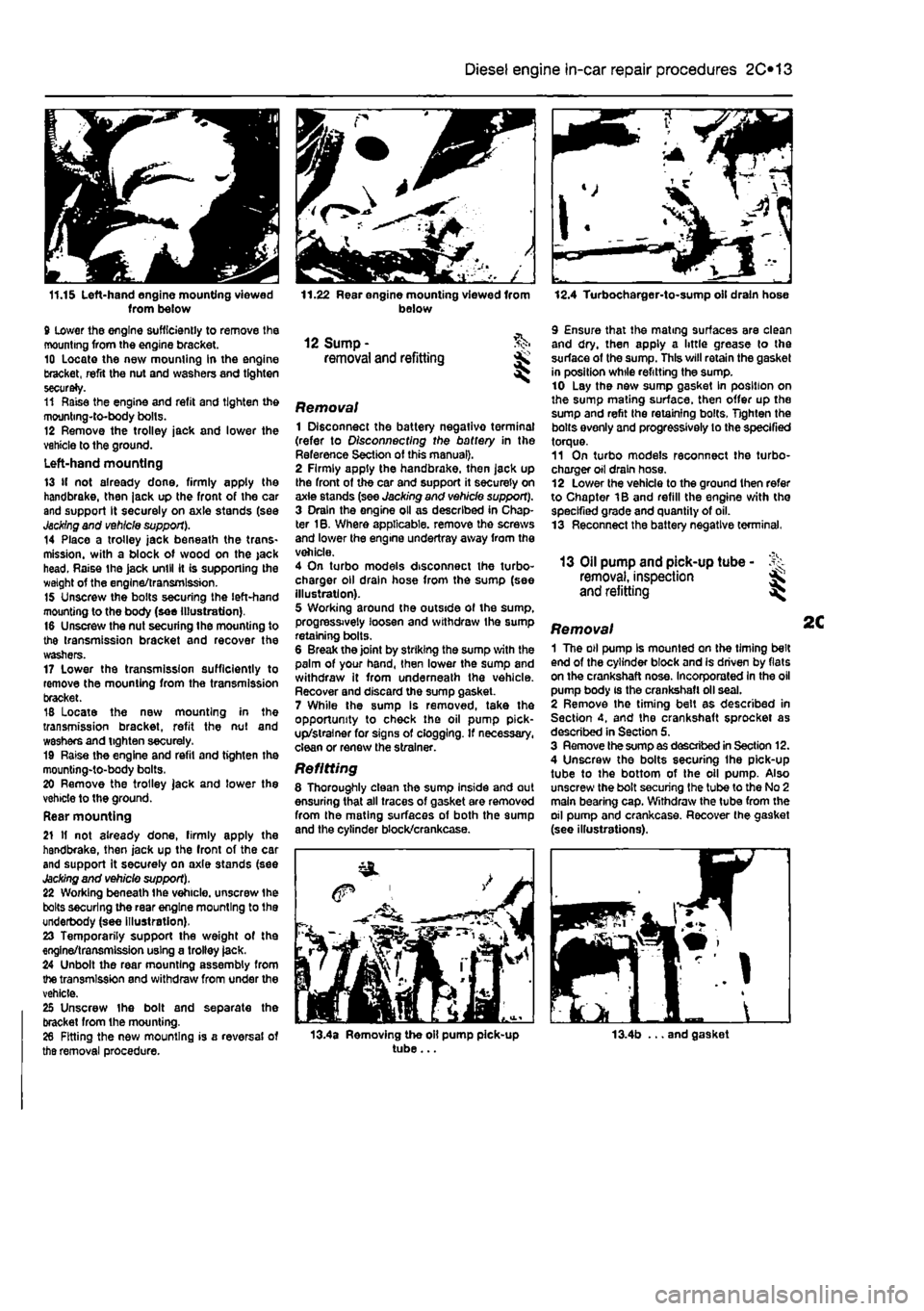
11.15 Left-hand engine mounting viewed from below 9 lower the engine sufficiently to remove the mounting from the engine bracket. 10 Locate the new mounting in the engine bracket, refit the nut and washers and tighten securely. 11 Raise the engine and refit and tighten the mounting-to-body bolts. 12 Remove the trolley jack and lower the vehicle to the ground. Left-hand mounting 13 If not already done, firmly apply the handbrake, then jack up the front of the car and support It securely on axle stands (see
Jacking
and vehicle support). 14 Place a trolley jack beneath the trans-mission. with a block of wood on the jack head. Raise the jack until it is supporting the weight of the engine/transmission. 15 Unscrew the bolts securing the left-hand mounting to the body (see Illustration). 16 Unscrew the nut securing the mounting to the transmission bracket and recover the washers. 17 Lower the transmission sufficiently to remove the mounting from the transmission bracket. 18 Locate the new mounting in the transmission bracket, refit the nut and washers and tighten securely. 19 Raise the engine and refil and tighten the mounting-to-body bolts. 20 Remove the trolley jack and lower the vehicle to the ground. Rear mounting 21 If not already done, firmly apply the handbrake, then jack up the front of the car and support it securely on axle stands (see
Jacking
and vehicle support). 22 Working beneath the vehicle, unscrew the bolts securing the rear engine mounting to the underbody (see illustration). 23 Temporarily support the weight of the engine/transmission using a trolley jack. 24 Unbolt the rear mounting assembly from the transmission and withdraw from under the vehicle. 25 Unscrew the bolt and separate the bracket from the mounting. 28 Fitting the new mounting is a reversal of tha removal procedure.
Diesel engine in-car repair procedures 2C*11
11.22 Rear engine mounting viewed from below
12 Sump -removal and refitting
Removal 1 Disconnect the battery negativo terminal (refer to Disconnecting the battery in the Reference Section of this manual). 2 Firmly apply the handbrake, then jack up the front of the car and support it securely on axie stands (see Jacking and vehicle support). 3 Drain the engine oil as described in Chap-ter 1B. Where applicable, remove the screws and lower the engine undertray away from the vehicle. 4 On turbo models disconnect the turbo-charger oil drain hose from the sump (see illustration). 5 Working around the outside of the sump, progressively loosen and withdraw the sump retaining bolts. 6 Break the joint by striking the sump with the palm of your hand, then lower the sump and withdraw it from underneath the vehicle. Recover and discard the sump gasket. 7 While the sump Is removed, take the opportunity to check the oil pump pick-up/strainer for signs of clogging. If necessary, clean or renew the strainer.
Refitting 8 Thoroughly clean the sump inside and out ensuring that all traces of gasket are removed from the mating surfaces of both the sump and the cylinder block/crankcase.
12.4 Turbocharger-to-sump oil drain hose
9 Ensure that the mating surfaces are clean and dry, then apply a little grease to the surface of the sump. This will retain the gasket in position while refitting the sump. 10 Lay the new sump gasket In position on the sump mating surface, then offer up the sump and refit the retaining bolts. Tighten the bolts evenly and progressively lo the specified torque. 11 On turbo models reconnect the turbo-charger oil drain hose. 12 Lower the vehicle to the ground then refer to Chapter 1B and refill the engine with the specified grade and quantity of oil. 13 Reconnect the battery negative terminal.
13 Oil pump and pick-up tube -removal, inspection and refitting
Removal 1 The oil pump Is mounted on the timing belt end of the cylinder block and is driven by flats on the crankshaft nose. Incorporated In the oil pump body is the crankshaft oil seal. 2 Remove the timing belt as described in Section 4, and the crankshaft sprocket as described in Section 5. 3 Remove the sump as described in Section 12. 4 Unscrew the bolts securing Ihe pick-up tube to the bottom of the oil pump. Also unscrew the bolt securing the tube to the No 2 main bearing cap. Withdraw the tube from the oil pump and crankcase. Recover the gasket (see illustrations).
13.4a Removing the oil pump pick-up tube... 13.4b ... and gasket
Page 86 of 225
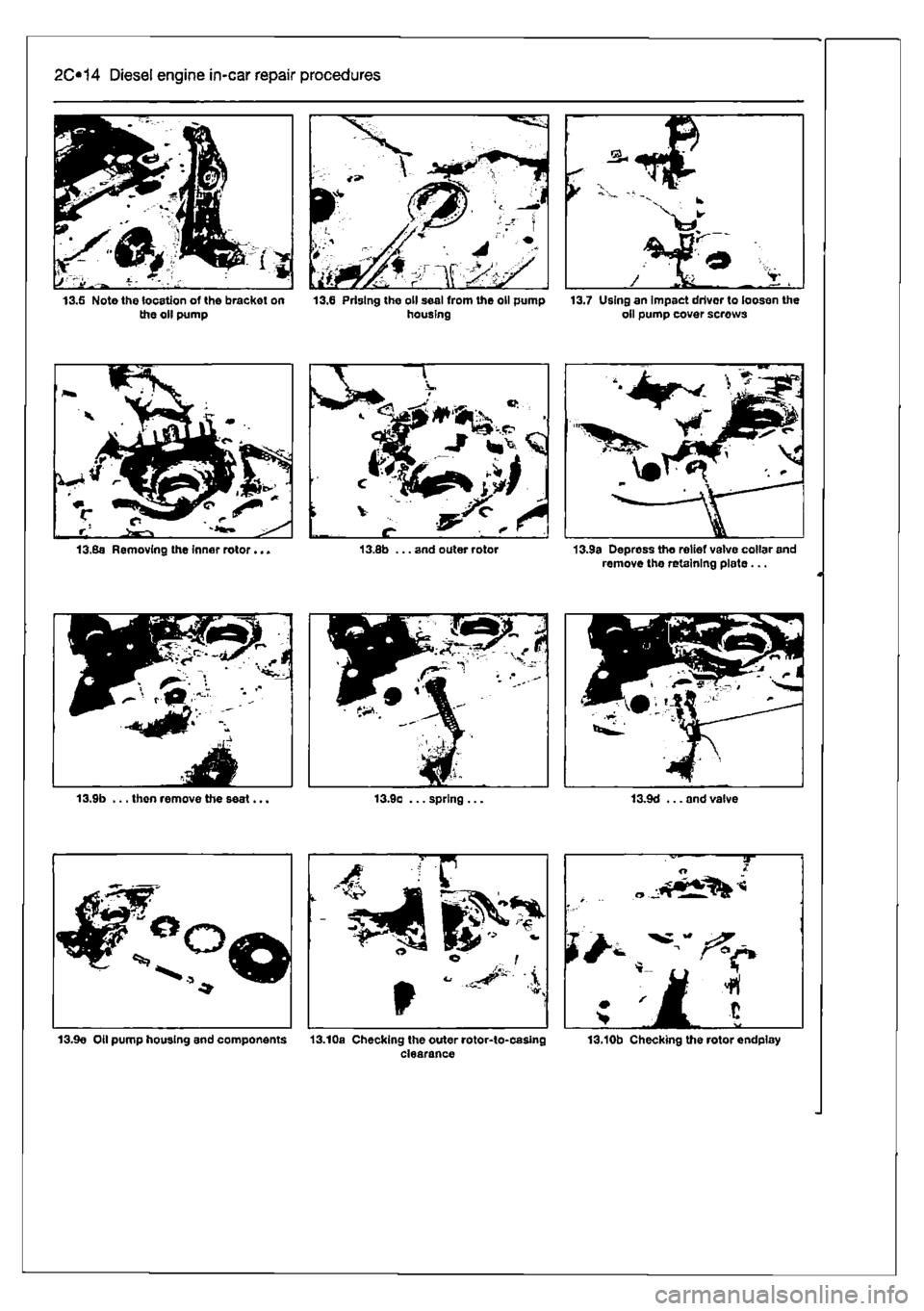
2014 Diesel engine in-car repair procedures
^ ^^ i > ; v. » •
•
.
r, ^
W
(fM
•
;
13.5 Note the location of the bracket on the oil pump 13.6 Prising the oil seal from the oil pump housing 13.7 Using an impact drivor to loosen the oil pump cover screws
'' r' -*•<- ^
- •
• J
; v _Vc >•
13.6a Removing the inner rotor... 13.8b ... and outer rotor 13.9a Depress tho relief valve collar and remove the retaining plate...
JB <0
1MU55U
13.9b ... then remove the seat... 13.9c ... spring ... 13.9d ... and valve
. ' IT
® f
9 ; I 1 13.9e Oil pump housing and components 13.10a Checking the outer rotor-to-casing clearance 13.10b Checking the rotor endplay
Page 87 of 225
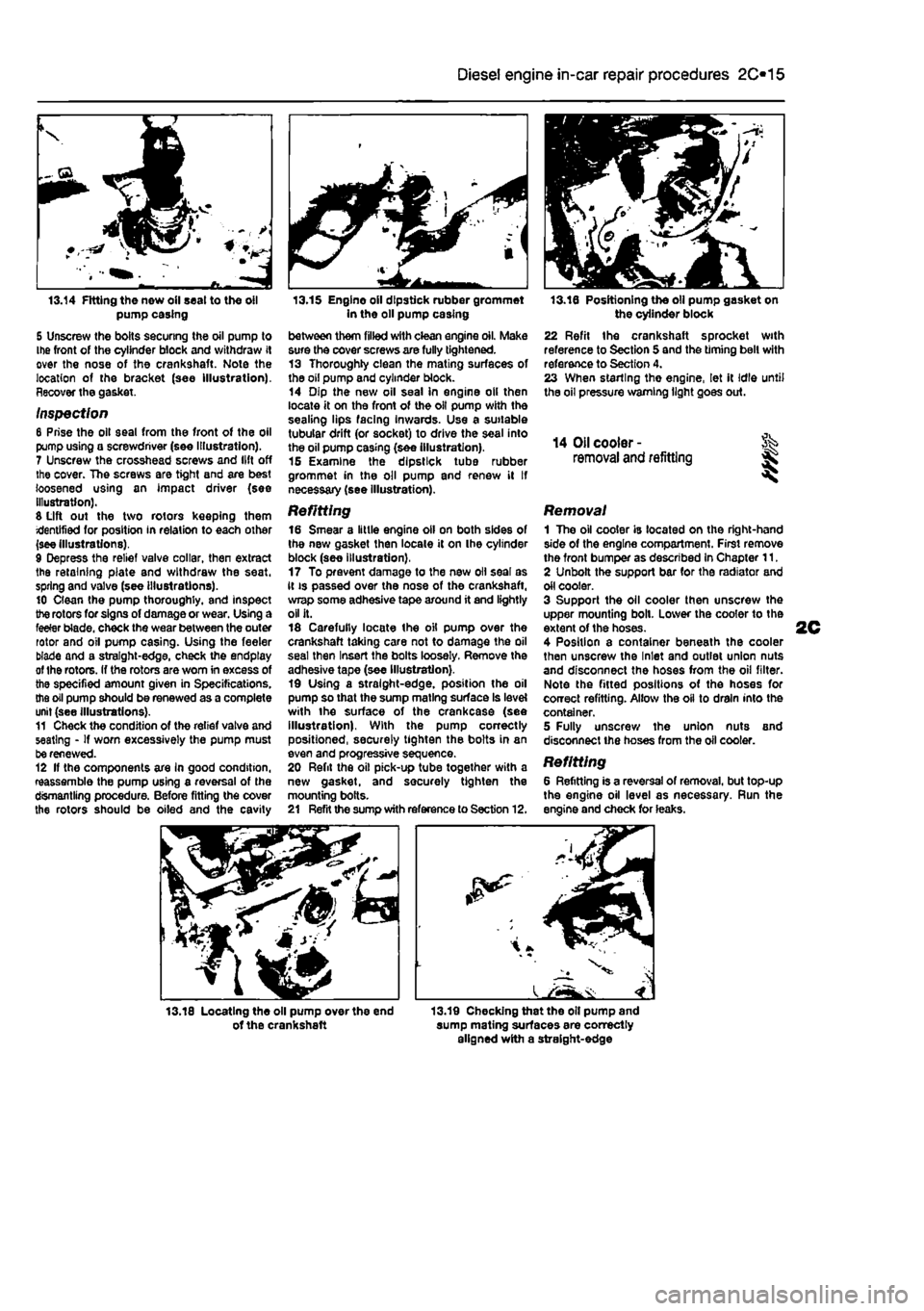
Diesel engine in-car repair procedures 2C*11
X
a 13.14 Fitting the new oil seal to the oil pump casing
S Unscrew the bolts securing the oil pump to Ihe front of the cylinder block and withdraw it over the nose of the crankshaft. Note the location of the bracket (see Illustration). Recover the gasket.
Inspection 8 Prise the oil seal from the front of the oil pump using a screwdriver (see Illustration). 7 Unscrew the crosshead screws and lift off the cover. The screws are tight and are best loosened using an impact driver (see illustration). S Lift out the two rotors keeping them identified for position in relation to each other (see illustrations). 9 Depress the relief valve collar, then extract the retaining plate and withdraw the seat, spring and valve (see illustrations). 10 Clean the pump thoroughly, and Inspect the rotors for signs of damage or wear. Using a feeler blade, check the wear between the outer rotor and oil pump casing. Using the feeler blade and a straight-edge, check the endptay of Ihe rotors. If the rotors are worn in excess of the specified amount given in Specifications, the oil pump should be renewed as a complete unit (see Illustrations). 11 Check the condition of the relief valve and seating - If worn excessively the pump must be renewed. 12 If the components are In good condition, reassemble the pump using a reversal of the dismantling procedure. Before fitting the cover the rotors should be oiled and the cavity
13.15 Engine oil dipstick rubber grommet in the oil pump casing between them filled with clean engine oil. Make sure the cover screws are fully tightened. 13 Thoroughly clean the mating surfaces of the oil pump and cylinder block. 14 Dip the new oil seal in engine oil then locate it on the front of the oil pump with the sealing lips facing Inwards. Use a suitable tubular drift (or socket) to drive the seal into the oil pump casing (see illustration). 16 Examine the dipstick tube rubber grommet in the oil pump and renew il If necessary (see illustration).
Refitting 16 Smear a little engine oil on both sides of the new gasket then locate it on the cylinder block (see illustration), 17 To prevent damage to the new oil seal as it is passed over the nose of the crankshaft, wrap some adhesive tape around it and lightly oil it. 18 Carefully locate the oil pump over the crankshaft taking care not to damage the oil seal then Insert the bolts loosely. Remove the adhesive tape (see Illustration). 19 Using a straight-edge, position the oil pump so that the sump mating surface Is level with the surface of the crankcase (see illustration). With the pump correctly positioned, securely tighten the bolts in an even and progressive sequence. 20 Refit the oil pick-up tube together with a new gasket, and securely tighten the mounting bolts. 21 Refit the sump with reference to Section 12.
13.16 Positioning the oil pump gasket on the cylinder block 22 Refit the crankshaft sprocket with reference to Section 5 and the timing belt with reference to Section 4. 23 When starling the engine, let it Idle until the oil pressure warning light goes out.
14 Oil cooler -removal and refitting I I
Removal 1 The oil cooler is located on the right-hand side of the engine compartment. First remove the front bumper as described In Chapter 11. 2 Unbolt the support bar for the radiator and oil cooler. 3 Support the oil cooler then unscrew the upper mounting boll. Lower the cooler to the extent of the hoses. 4 Position a container beneath the cooler then unscrew the Inlet and outlet union nuts and disconnect the hoses from the oil filter. Note the fitted positions of the hoses for correct refitting. Allow the oil to drain into the container. 5 Fully unscrew the union nuts and disconnect the hoses from the oil cooler.
Refitting 6 Refitting is a reversal of removal, but top-up the engine oil level as necessary. Run the engine and check for leaks.
13.18 Locating the oil pump over the end of the crankshaft 13.19 Checking that the oil pump and sump mating surfaces are correctly aligned with a straight-edge
Page 88 of 225
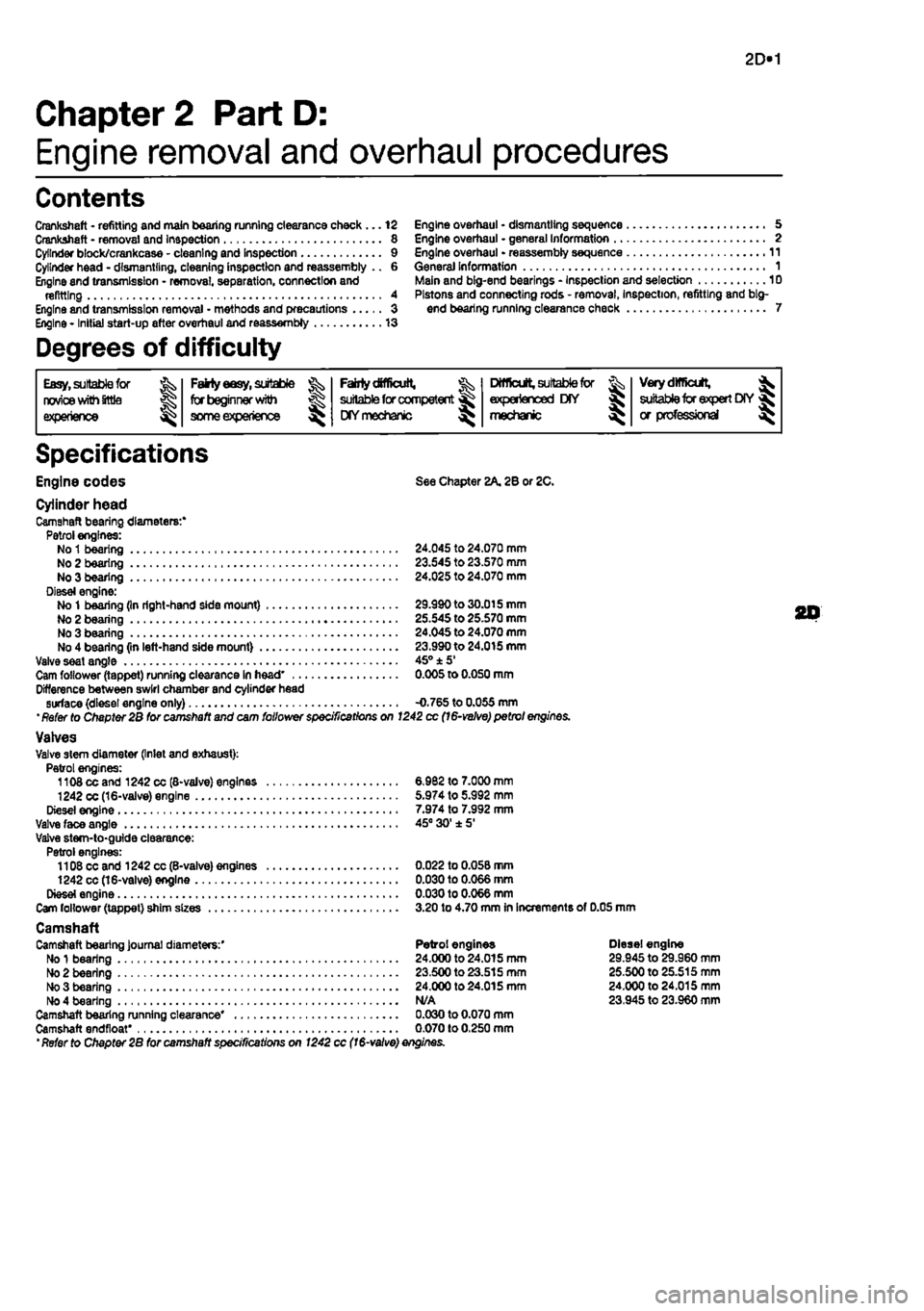
2D»1
Chapter 2 Part D:
Engine removal and overhaul procedures
Contents
Crankshaft - refitting and main bearing running clearance check... 12 Engine overhaul • dismantling sequence 5 Crankshaft • removal and inspection 8 Engine overhaul • general Information .. Cylinder block/crankcase - cleaning and Inspection 9 Engine overhaul - reassembly sequence Cylinder head - dismantling, cleaning inspection and reassembly .. 6 General Information Engine and transmission - removal, separation, connection and refitting 4 Engine and transmission removal • methods and precautions 3 Engine * Initial start-up after overhaul and reassembly 13
Degrees of difficulty
Engine overhaul - general Information 2 11 1 Main and big-end bearings - Inspection and selection 10 Pistons and connecting rods - removal, inspection, refitting and big-end bearing running clearance check 7
Easy, suftable for FaHy easy, suitable ^ FaMy difficult, ^ Difficult, suitable for % Very difficult, ^ novice with littla | for beginner with suitable for competent ^ experienced DIY suitable for expert DIY « experience | some experience ^ HYmechanic mechanic or professional ^
Specifications
Engine codes See Chapter 2A. 2B or ZC.
Cylinder head Camshaft bearing diameters:* Petrol engines: No
1
bearing 24.045 to 24.070 mm No 2 bearing 23.S45 to 23.570 mm No 3 bearing 24.025 to 24.070 mm Diesel engine: No
1
bearing (In right-hand side mount) 29.990to30.015mm No 2 bearing 25.545 to 25.570 mm No 3 bearing 24.045 to 24.070 mm No 4 bearing (in left-hand side mount) 23.990 to 24.015 mm Valve seat angle 45° ±5' Cam follower (tappet) running clearance In head' 0.005 to 0.050 mm Difference between swirl chamber and cylinder head surface (diesel engine only) -0.765 to 0.055 mm '
Refer
to Chapter 2B for camshaft and cam follower specifications on 1242 cc
(16-velve)
petrol engines. Valves Valve stem diameter (Inlet and exhaust): Petrol engines: 1108 cc and 1242 cc (8-valve) engines 6.982 to 7.000 mm 1242
CC
(16-valve) engine 5.974 to 5.992 mm Diesel engine 7.974 to 7.992 mm Valve face angle 45° 30'±5' Valve stem-to-guide clearance: Petrol engines: 1108 cc and 1242 cc(B-valve) engines 0.022 to 0.05B mm 1242 cc (16-valve) engine 0.030 to 0.066 mm Diesel engine 0.030 to 0.066 mm Cam follower (tappet) sJiim sizes 3.20 to 4.70 mm In Increments of 0.05 mm Camshaft Camshaft bearing Journal diameters:' Petrol engines Diesel engine No
1
bearing 24.000 to 24.015 mm 29.945 to 29.960 mm No 2 bearing 23.500 to 23.515 mm 25.500 to 25.515 mm No 3 bearing 24.000 to 24.015 mm 24.000 to 24.015 mm No 4 bearing N/A 23.945 to 23.960 mm Camshaft bearing running clearance* 0.030 to 0.070 mm Camshaft endfloat* 0.070 to 0.250 mm 'Refer to Chapter 2B for camshaft specifications on 1242 cc
(16-valve)
enginss.
20
Page 89 of 225
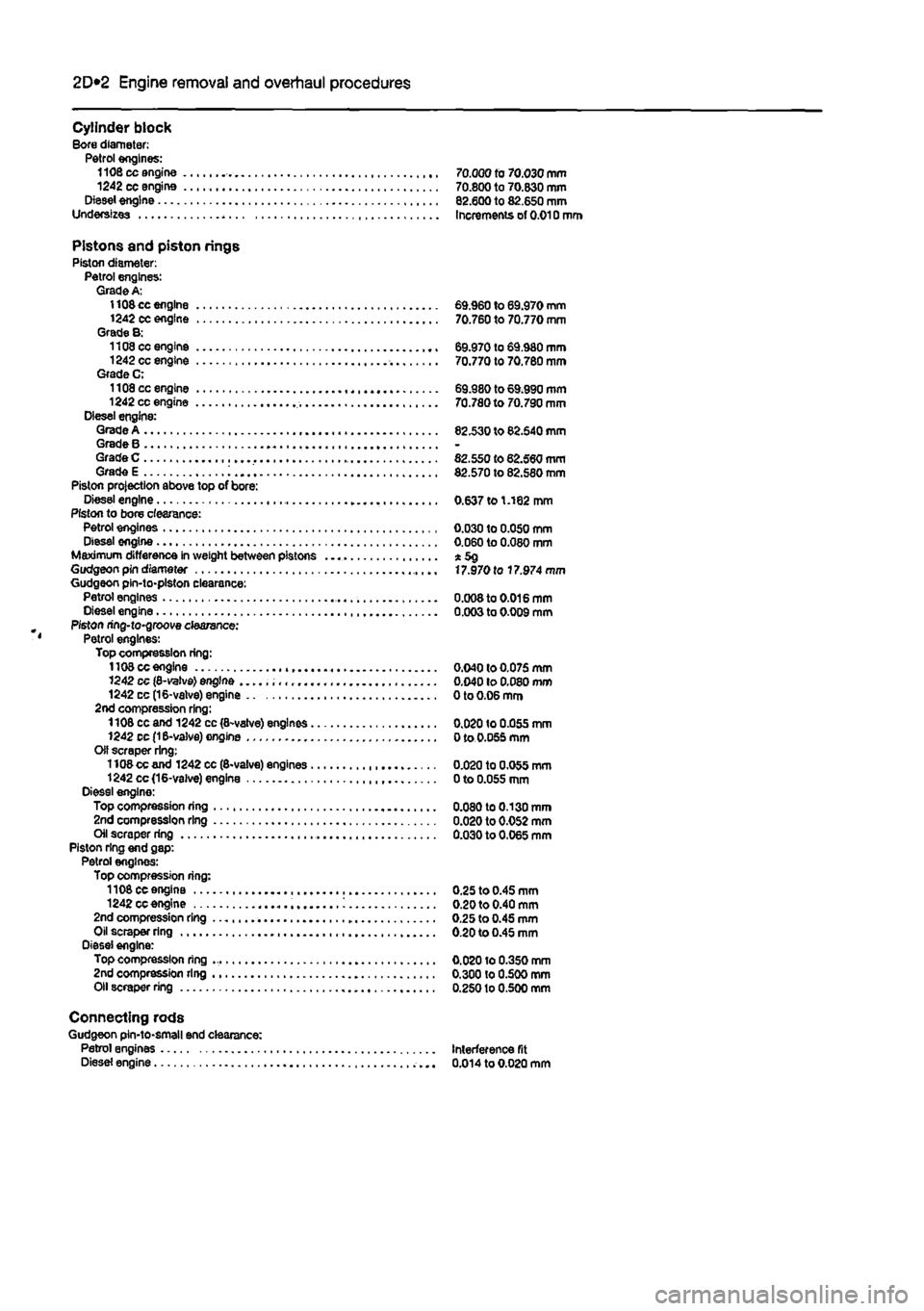
2D*10 Engine removal and overhaul procedures
Cylinder block Bore diameter: Petrol engines: 1106 cc engine 70.000 to 70.030 mm 1242 cc engine 70.800 to 70.630 mm Diesel engine 82.600 to 82.650 mm Underslzes * Increments of 0.010 mm
Pistons and piston rings Piston diameter: Petrol engines: Grade A; 1108 cc engine 69.960 to 69.970 mm 1242 cc engine 70.760 to 70.770 mm Grade 8: 1108 cc engine 69.970 to 69.980 mm 1242 cc engine 70.770 to 70.780 mm Grade C; 1108 cc engine 69.980 to 69;990 mm 1242 cc engine 70.780 to 70.790 mm Diesel engine: Grade A 82.530 to 82.640 mm GradeB GradeC , 82.550 to 62.560 mm Grade E ; 82.570 to 82.580 mm Piston projection above top of bore: Diesel engine 0.637 to 1.162 mm Piston to bore clearance: Petrol engines 0.030 to 0.050 mm Diesel engine 0.060 to 0.080 mm Maximum difference in weight between pistons x 5g Gudgeon pin diameter 17.970 fo 17.974 mm Gudgeon pin-to-plston clearance: Petrol engines 0.008 to 0.016 mm Diesel engine 0.003 to 0.009 mm Piston ring-to-groove clearance: Petrol engines: Top compression ring: 1108 cc engine 0.040 to 0.075 mm 1242 cc (8-valve) engine 0,040 lo 0,080 mm 1242 cc (16-valve) engine 0 to 0.06 mm 2nd compression ring: 1108 cc and 1242 cc (8-valve) engines 0.020 to 0.055 mm 1242 cc
(1
B-valve) engine 0 to 0.055 mm Oil scraper ring: 1108 cc and 1242 cc (8-valve) engines 0.020 to 0.055 mm 1242 cc (16-valve) engine 0 to 0.055 mm Diesel engine: Top compression ring 0.080 to 0.130 mm 2nd compression ring 0.020 to 0.052 mm Oil scraper ring 0.030 to 0.065 mm Piston ring end gap: Petrol engines: Top compression ring: 1108 cc engine 0.25 to 0.45 mm 1242ccengine : 0.20to0.40mm 2nd compression ring 0.25 to 0.45 mm Oil scraper ring 0.20 to 0.45 mm Diesel engine: Top compression ring 0.020 to 0.350 mm 2nd compression ring 0.300 to 0.500 mm Oil scraper ring 0.250 lo 0.500 mm
Connecting rods Gudgeon pin-to-small end clearance: Petrol engines Interference fit Diesel engine 0.014 to 0.020 mm
Page 90 of 225
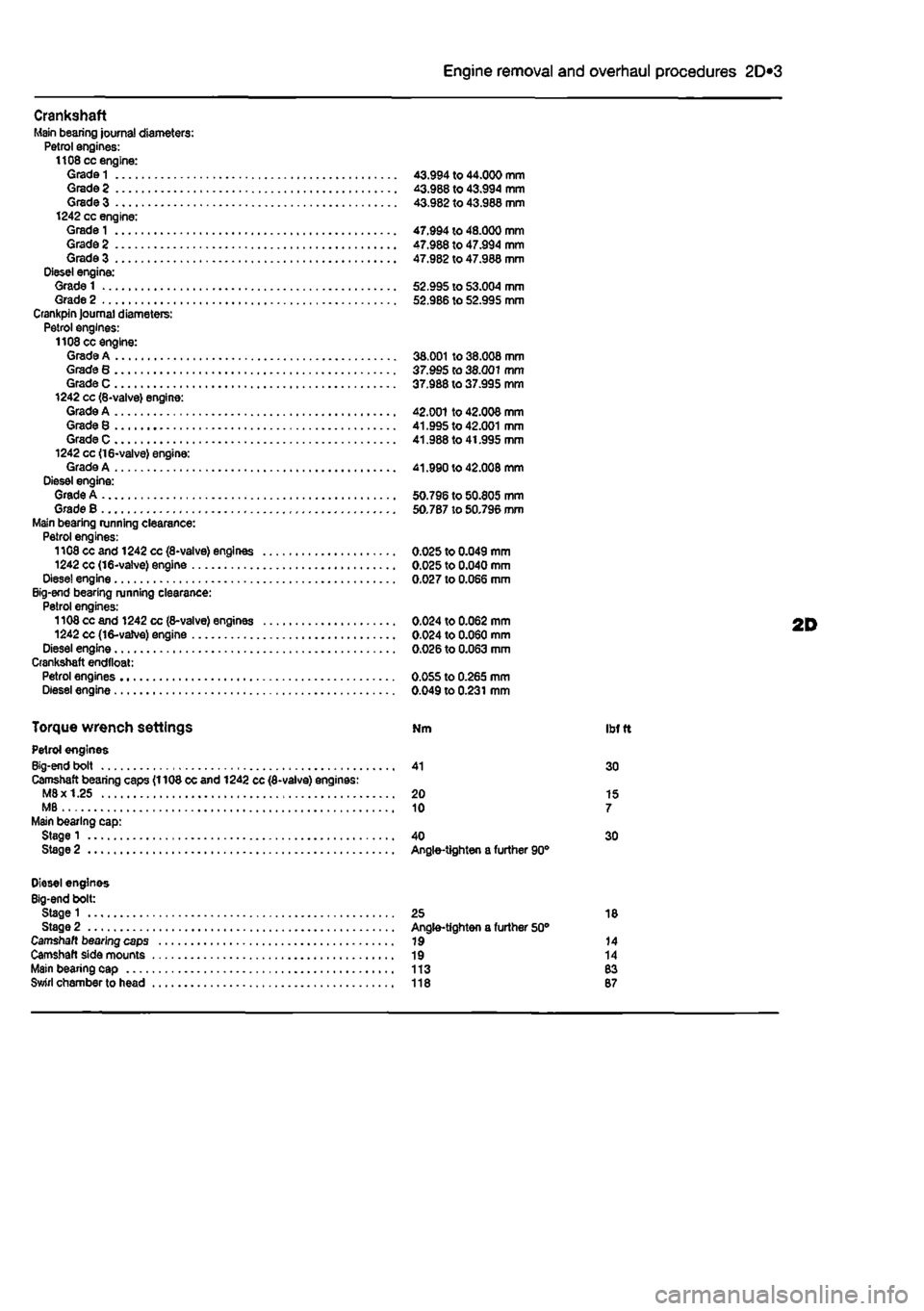
2D*10 Engine removal and overhaul procedures
Crankshaft Main bearing journal diameters: Petrol engines: 1108 cc engine: Grade
1
43.994 to 44.000 mm Grade 2 43.988 to 43.994 mm Grade 3 43.982 to 43.988 mm 1242 cc engine: Grade
1
47.994 to 48.000 mm Grade 2 47.988 to 47.994 mm Grade 3 47.982 to 47.988 mm Diesel engine: Grade 1 52.995 to 53.004 mm Grade 2 52.986 to 52.995 mm Crankpin Journal diameters: Petrol engines: 1108 cc engine: Grade A 38.001 to 38.008 mm Grade 8 37.995 to 38.001 mm Grade C 37.988 to 37.995 mm 1242 cc (8-valve) engine: Grade A 42.001 to 42.008 mm Grade 8 41.995 to 42.001 mm Grade C 41.988 to 41.995 mm 1242 cc <16-valve) engine: Grade A 41.990 to 42.008 mm Diesel engine: Grade A 50.796 to 50.805 mm Grade B 50.787 to 50.796 mm Main bearing running clearance: Petrol engines: 1108 cc and 1242 cc (8-valve) engines 0.025 to 0.049 mm 1242 cc (16-valve) engine 0.025 to 0.040 mm Dlese! engine 0.027 to 0.066 mm Big-end bearing running clearance: Petrol engines: 1108 cc and 1242 cc (8-valve) engines 0.024 to 0.062 mm 1242 cc (16-vaJve) engine 0.024 to 0.060 mm Diesel engine 0.026 to 0.063 mm Crankshaft endtloat: Petrol engines 0.055 to 0.265 mm Diesel engine 0.049 to 0.231 mm
Torque wrench settings Nm ibf
t
Petrol engines Big-end bolt 41 30 Camshaft bearing caps (1108 cc and 1242 cc (8-valve) engines: M8x 1.25 20 15 MB 10 7 Main bearing cap: Stage 1 40 30 Stage 2 Angle-tighten a further 90°
Diesel engines Big-end bolt: Stage 1 25 18 Stage 2 Angle-tighten a further 50° Camshaft bearing caps 19 14 Camshaft side mounts 19 14 Main bearing cap 113 83 Swirl chamber to head 118 87