wheel torque FIAT TEMPRA 1988 Service And Repair Manual
[x] Cancel search | Manufacturer: FIAT, Model Year: 1988, Model line: TEMPRA, Model: FIAT TEMPRA 1988Pages: 171, PDF Size: 18.05 MB
Page 19 of 171
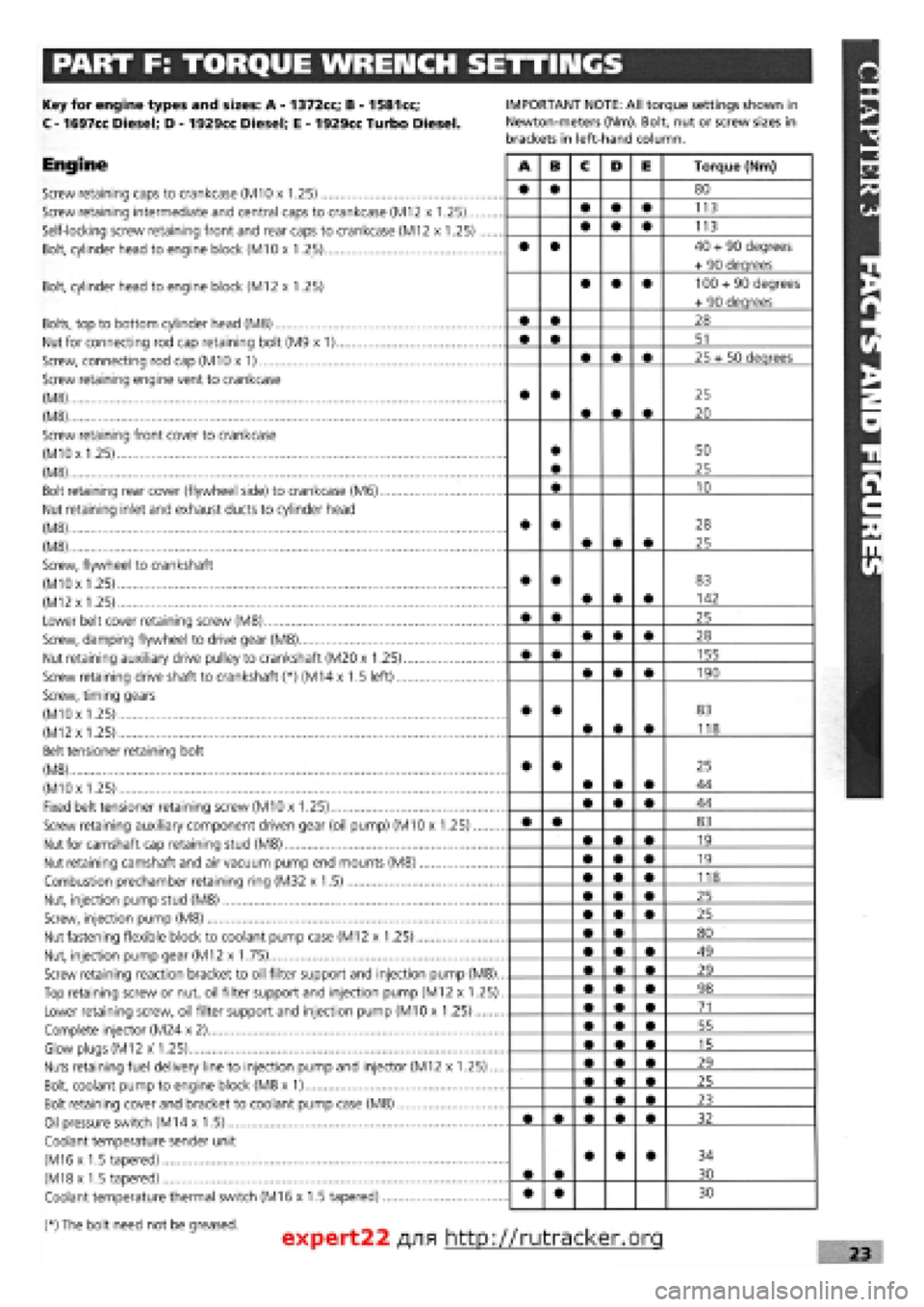
PART F: TORQUE WRENCH SETTINGS
Key for engine types and sizes: A
-
1372cc; B
-
1581cc;
C
-
1697cc Diesel; D
-
1929cc Diesel; E
-
1929cc Turbo Diesel.
Engine
Screw retaining caps to crankcase (M10 x 1.25)
Screw retaining intermediate and central caps to crankcase (M12 x 1.25)...
Self-locking screw retaining front and rear caps to crankcase (M12 x 1.25)
Bolt, cylinder head to engine block (M10 x 1.25)
IMPORTANT NOTE: All torque settings shown in
Newton-meters (Nm). Bolt, nut or screw sizes in
brackets in left-hand column.
Bolt, cylinder head to engine block (M12 x 1.25)
Bolts, top to bottom cylinder head (M8)
Nut for connecting rod cap retaining bolt (M9 x 1)
Screw, connecting rod cap (M10 x 1)
Screw retaining engine vent to crankcase
(M8)
(M8)
Screw retaining front cover to crankcase
(MlOx 1.25)
(M8)
Bolt retaining rear cover (flywheel side) to crankcase (M6)
Nut retaining inlet and exhaust ducts to cylinder head
(M8)
(M8)
Screw, flywheel to crankshaft
(M10x 1.25)
(M12
x
1.25)
Lower belt cover retaining screw (M8)
Screw, damping flywheel to drive gear (M8)
Nut retaining auxiliary drive pulley to crankshaft (M20 x 1.25)
Screw retaining drive shaft to crankshaft (*) (M14 x 1.5 left)
Screw, timing gears
(M10x 1.25)
(M12x 1.25)
Belt tensioner retaining bolt
(M8)
(M10x 1.25)
Fixed belt tensioner retaining screw (M10 x 1.25)
Screw retaining auxiliary component driven gear (oil pump) (M10 x 1.25)
Nut for camshaft cap retaining stud (M8)
Nut retaining camshaft and air vacuum pump end mounts (M8)
Combustion prechamber retaining ring (M32 x 1.5)
Nut, injection pump stud (M8)
Screw, injection pump (M8)
Nut fastening flexible block to coolant pump case (M12 x 1.25)
Nut, injection pump gear (M12 x 1.75)
Screw retaining reaction bracket to oil filter support and injection pump (M8).
Top retaining screw or nut, oil filter support and injection pump (M12 x 1.25)
Lower retaining screw, oil filter support and injection pump (M10 x 1.25)
Complete injector (M24 x 2)
Glow plugs (M12 x 1.25)
Nuts retaining fuel delivery line to injection pump and injector (M12 x 1.25)...
Bolt, coolant pump to engine block (M8 x 1)
Bolt retaining cover and bracket to coolant pump case (M8)
Oil pressure switch (M14 x 1.5)
Coolant temperature sender unit
(M16 x 1.5 tapered)
(M18x 1.5 tapered)
Coolant temperature thermal switch (M16 x 1.5 tapered)
(*) The bolt need not be greased.
A B C D E Torque (Nm)
• • 80
• • • 113
• • • 113
• • 40
+
90 degrees
+ 90 deqrees
• • • 100
+
90 degrees
+ 90 deqrees
• • 28
• • 51
• • • 25 + 50 deqrees
• •
• • •
25
20
• • 50
25
• 10
• •
• • •
28
25
• •
• • •
83
142
• • 25
• • • 28
• • 155
• • • 190
• •
• • •
83
118
• •
• • •
25
44
• • • 44
• • 83
• • • 19
• • • 19
• • • 118
• • • 25
• • • 25
• • 80
• • • 49
• • • 29
• • • 98
• • • 71
• • • 55
• • • 15
• • • 29
• • • 25
• • • 23
32
• •
• • • 34
30
• • 30
expert22 fl/i* http://rutracker.org 23
Page 22 of 171
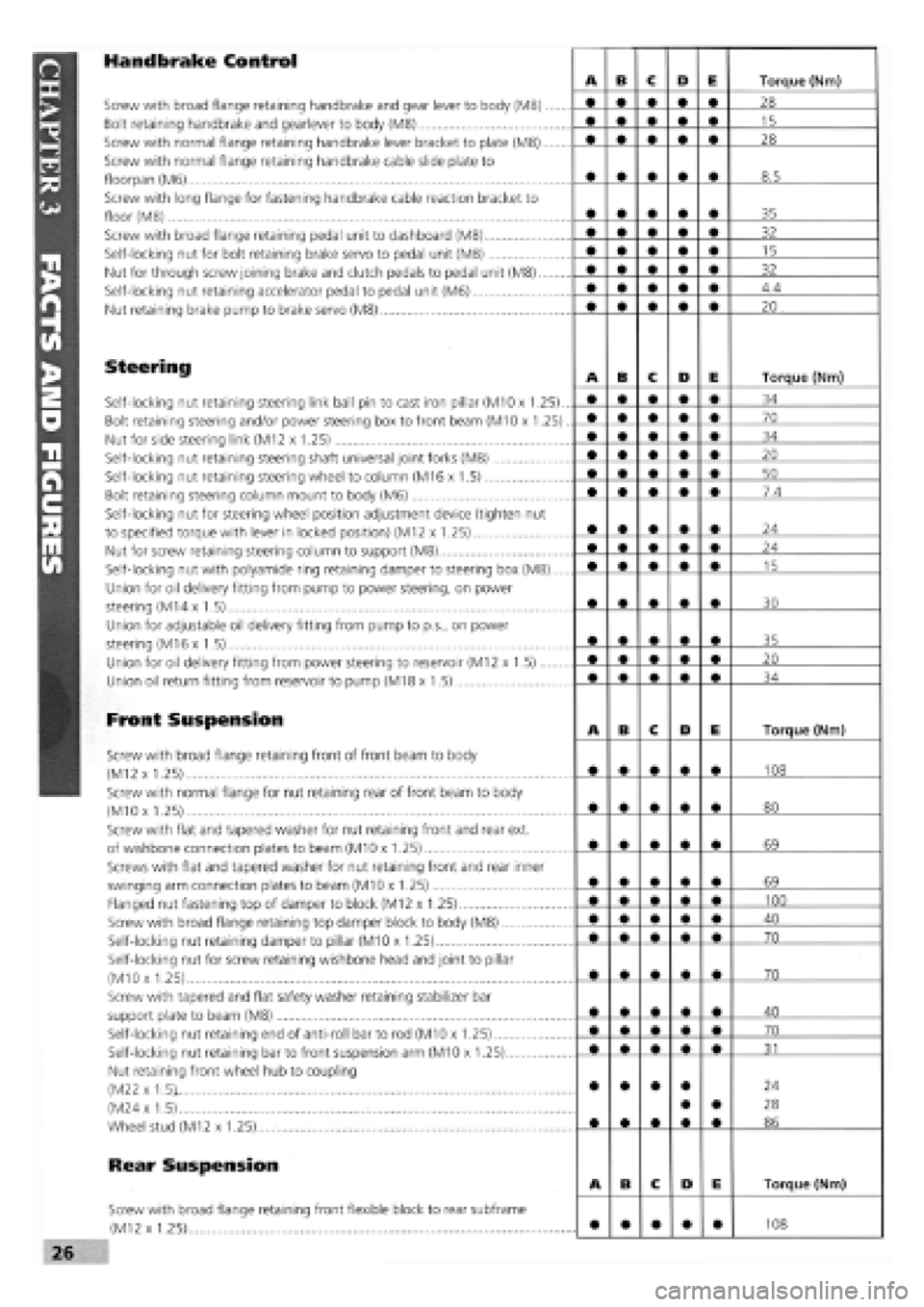
Handbrake Control
Screw with broad flange retaining handbrake and gear lever to body (M8)
Bolt retaining handbrake and gearlever to body (M8)
Screw with normal flange retaining handbrake lever bracket to plate (M8)
Screw with normal flange retaining handbrake cable slide plate to
floorpan (M6)
Screw with long flange for fastening handbrake cable reaction bracket to
floor (M8)
Screw with broad flange retaining pedal unit to dashboard (M8)
Self-locking nut for bolt retaining brake servo to pedal unit (M8)
Nut for through screw joining brake and clutch pedals to pedal unit (M8).
Self-locking nut retaining accelerator pedal to pedal unit (M6)
Nut retaining brake pump to brake servo (M8)
Steering
Self-locking nut retaining steering link ball pin to cast iron pillar (M10 x 1.25)..
Bolt retaining steering and/or power steering box to front beam (M10 x 1.25).
Nut for side steering link (M12 x 1.25)
Self-locking nut retaining steering shaft universal joint forks (M8)
Self-locking nut retaining steering wheel to column (M16 x 1.5)
Bolt retaining steering column mount to body (M6)
Self-locking nut for steering wheel position adjustment device (tighten nut
to specified torque with lever in locked position) (M12 x 1.25)
Nut for screw retaining steering column to support (M8)
Self-locking nut with polyamide ring retaining damper to steering box (M8)
Union for oil delivery fitting from pump to power steering, on power
steering (M14 x 1.5)
Union for adjustable oil delivery fitting from pump to p.s., on power
steering (M16 x 1.5)
Union for oil delivery fitting from power steering to reservoir (M12 x 1.5)
Union oil return fitting from reservoir to pump (M18 x 1.5)
Front Suspension
Screw with broad flange retaining front of front beam to body
(M12 x 1.25)
Screw with normal flange for nut retaining rear of front beam to body
(M10
x
1.25)
Screw with flat and tapered washer for nut retaining front and rear ext.
of wishbone connection plates to beam (M10 x 1.25)
Screws with flat and tapered washer for nut retaining front and rear inner
swinging arm connection plates to beam (M10 x 1.25)
Flanged nut fastening top of damper to block (M12 x 1.25)
Screw with broad flange retaining top damper block to body (M8)
Self-locking nut retaining damper to pillar (M10 x 1.25)
Self-locking nut for screw retaining wishbone head and joint to pillar
(M10
x
1.25)
Screw with tapered and flat safety washer retaining stabilizer bar
support plate to beam (M8)
Self-locking nut retaining end of anti-roll bar to rod (M10 x 1.25)
Self-locking nut retaining bar to front suspension arm (M10 x 1.25)
Nut retaining front wheel hub to coupling
(M22 x 1.5)i
(M24
x
1.5)
Wheel stud (M12 x 1.25).....
Rear Suspension
Screw with broad flange retaining front flexible block to rear subframe
(M12 x 1.25)
A B C D E Torque (Nm)
• • • • • 28
• • • • • 15
• • • • • 28
8.5
35
32
15
32
4.4
20 .
A B C D E Torque (Nm)
• • • • • 34
70
34
• • • • • 20
50
7.4
24
24
15
30
35
20
34
A B c D E Torque (Nm)
108
80
69
69
100
40
70
70
40
70
31
• • • • • •
24
28
86
A B c D E Torque (Nm)
108
Page 23 of 171
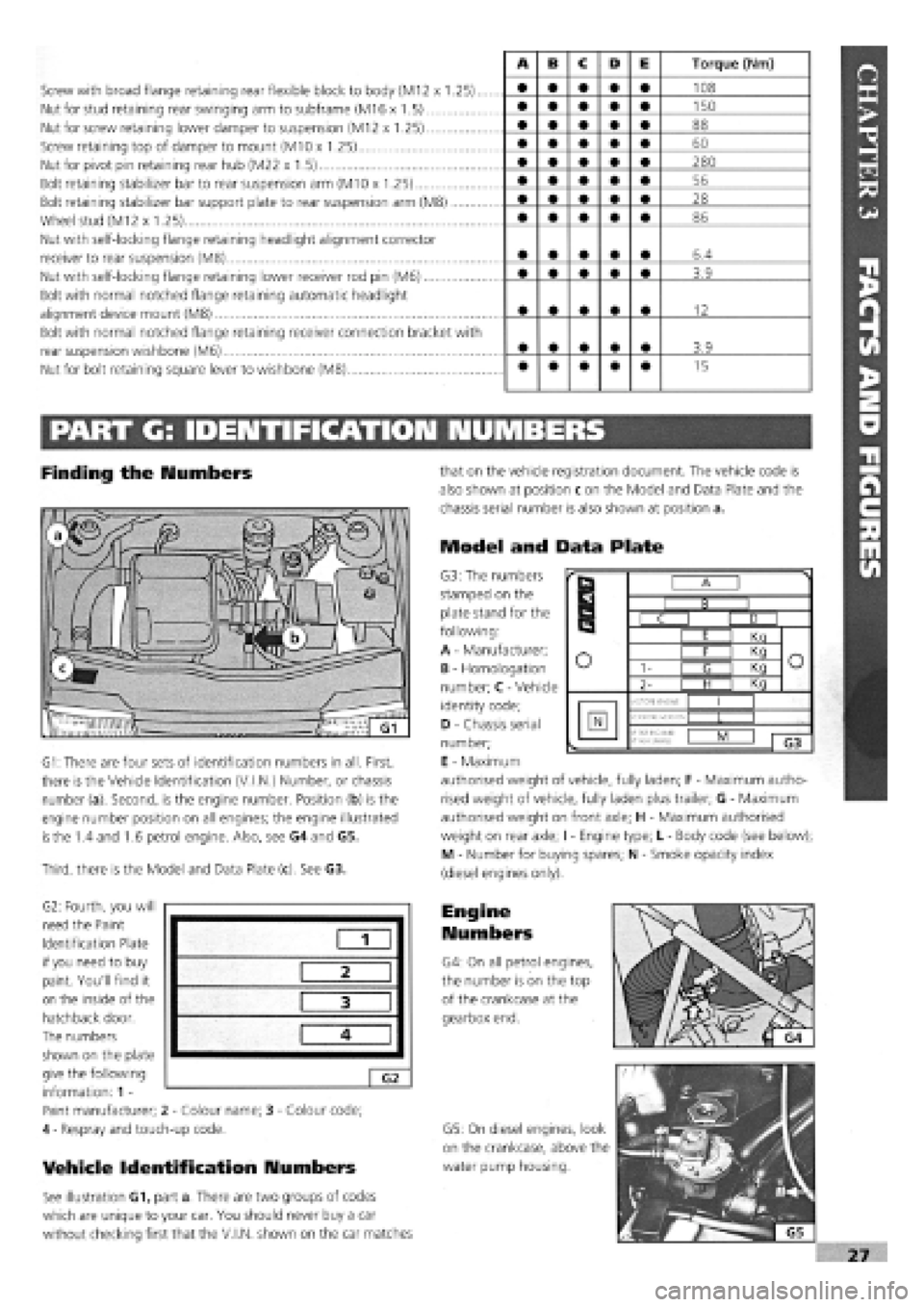
Screw with broad flange retaining rear flexible block to body (M12 x 1.25)..
Nut for stud retaining rear swinging arm to subframe (M16 x 1.5)
Nut for screw retaining lower damper to suspension (M12 x 1.25)
Screw retaining top of damper to mount (M10 x 1.25)
Nut for pivot pin retaining rear hub (M22 x 1.5)
Bolt retaining stabilizer bar to rear suspension arm (M10 x 1.25)
Bolt retaining stabilizer bar support plate to rear suspension arm (M8)
Wheel stud (M12 x 1.25)
Nut with self-locking flange retaining headlight alignment corrector
receiver to rear suspension (M8)
Nut with self-locking flange retaining lower receiver rod pin (M6)
Bolt with normal notched flange retaining automatic headlight
alignment device mount (M8)
Bolt with normal notched flange retaining receiver connection bracket with
rear suspension wishbone (M6)
Nut for bolt retaining square lever to wishbone (M8)
A B c D E Torque (Nm)
• • • • • 108
• • • • • 150
• • • • • 88
• • • • • 60
• • • • • 280
• • • • • 56
• • • • • 28
• • • • • 86
• • • • • 6.4
• • • • • 3.9
• • • • • 12
• • • • • 3.9
• • • • • 15
PART G: IDENTIFICATION NUMBERS
Finding the Numbers
G1: There are four sets of identification numbers in all. First,
there is the Vehicle Identification (V.I.N.) Number, or chassis
number (a). Second, is the engine number. Position (b) is the
engine number position on all engines; the engine illustrated
is
the 1.4 and 1.6 petrol engine. Also, see G4 and G5.
Third, there is the Model and Data Plate (c). See G3.
G2: Fourth, you will
need the Paint
Identification Plate
if you need to buy
paint. You'll find it
on the inside of the
hatchback door.
The numbers
shown on the plate
give the following
information: 1 -
Paint manufacturer; 2
-
Colour name; 3
-
Colour code;
4
-
Respray and touch-up code.
Vehicle Identification Numbers
See illustration G1, part a. There are two groups of codes
which are unique to your car. You should never buy a car
without checking first that the V.I.N, shown on the car matches
that on the vehicle registration document. The vehicle code is
also shown at position c on the Model and Data Plate and the
chassis serial number is also shown at position a.
Model and Data Plate
G3: The numbers
stamped on the
plate stand for the
following:
A
-
Manufacturer;
B
-
Homologation
number; C
-
Vehicle
identity code;
D
-
Chassis serial
number;
E
-
Maximum
authorised weight of vehicle, fully laden; F
-
Maximum autho-
rised weight of vehicle, fully laden plus trailer; G
-
Maximum
authorised weight on front axle; H
-
Maximum authorised
weight on rear axle; I
-
Engine type; L
-
Body code (see below);
M - Number for buying spares; N
-
Smoke opacity index
(diesel engines only).
Engine
Numbers
G4: On all petrol engines,
the number is on the top
of the crankcase at the
gearbox end.
G5: On diesel engines, look
on the crankcase, above the
water pump housing.
1
2
3
4
G2
r
B
r
B I B I
r
B
C I D I
r
B
I E I Kn
o o I F I Kq o o 1- I <3 I Kq o o
2- | H I Kq
o
MOTORE ENGINE
I I
N VERSIONE-VERSION •f
PER RICAM8:
N*
FOR SPARED
L I
1 G3
Page 55 of 171
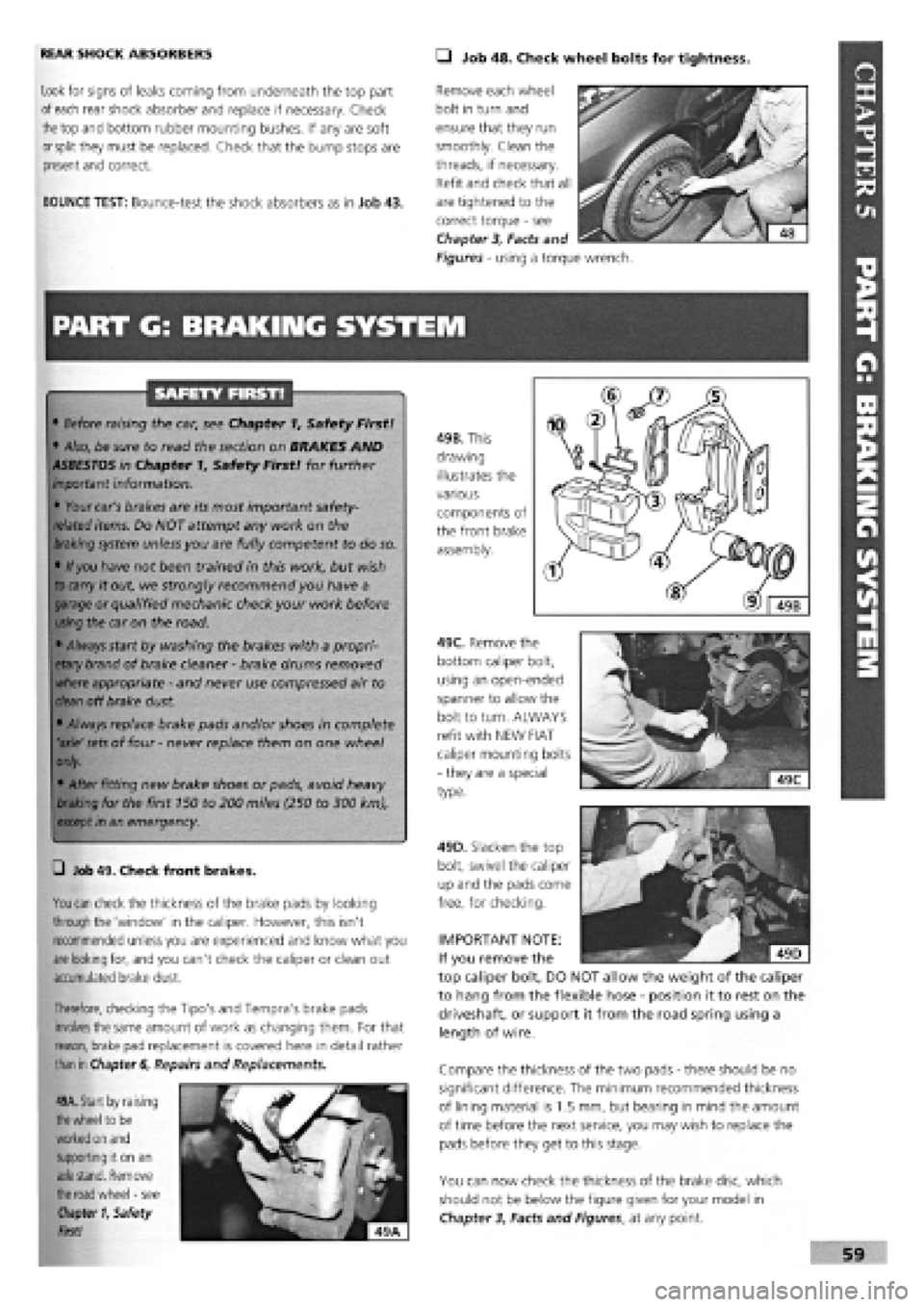
REAR SHOCK ABSORBERS • Job 48. Check wheel bolts for tightness.
Look for signs of leaks coming from underneath the top part
of
each
rear shock absorber and replace if necessary. Check
the
top and bottom rubber mounting bushes. If any are soft
or
split they must be replaced. Check that the bump stops are
present and correct.
BOUNCE TEST: Bounce-test the shock absorbers as in Job 43.
PART G: BRAKING SYSTEM
SAFETY FIRST!
• Job 49. Check front brakes.
You can
check the thickness of the brake pads by looking
through
the 'window' in the caliper. However, this isn't
recommended
unless you are experienced and know what you
are looking for,
and you can't check the caliper or clean out
accumulated
brake dust.
• Before raising the car, see Chapter 1, Safety First!
•
Also,
be sure to read the section on BRAKES AND
ASBESTOS in Chapter 1, Safety First! for further
important
information.
•
Your car's
brakes are its most important
safety-
related items.
Do NOT attempt any work on the
braking system unless
you are fully competent to do so.
• If you have not been trained in this work, but wish
to
carry
it out, we strongly recommend you have a
garage
or qualified mechanic check your work before
using
the car on the road.
•
Always
start by washing the brakes with a propri-
etary
brand of brake cleaner
-
brake drums removed
where
appropriate
-
and never use compressed air to
clean
off
brake
dust.
•
Always
replace brake pads and/or shoes in complete
'axle' sets
of four
-
never replace them on one wheel
only.
• After fitting new brake shoes or pads, avoid heavy
braking
for the first
150
to 200 miles (250 to 300 km),
except
in
an emergency.
49B. This
drawing
illustrates the
various
components of
the front brake
assembly.
49C. Remove the
bottom caliper bolt,
using an open-ended
spanner to allow the
bolt to turn. ALWAYS
refit with NEW FIAT
caliper mounting bolts
-
they are a special
type.
Therefore,
checking the Tipo's and Tempra's brake pads
involves
the same amount of work as changing them. For that
reason, brake
pad replacement is covered here in detail rather
than in
Chapter
6,
Repairs and Replacements.
49A. Start by raising
the
wheel to
be
worked on and
supporting it on
an
axle stand. Remove
the road wheel
-
see
Chapter
1, Safety
First!
Compare the thickness of the two pads
-
there should be no
significant difference. The minimum recommended thickness
of lining material is 1.5 mm, but bearing in mind the amount
of time before the next service, you may wish to replace the
pads before they get to this stage.
You can now check the thickness of the brake disc, which
should not be below the figure given for your model in
Chapter
3,
Facts and Figures, at any point.
Remove each wheel
bolt in turn and
ensure that they run
smoothly. Clean the
threads, if necessary.
Refit and check that all
are tightened to the
correct torque
-
see
Chapter
3,
Facts and
Figures
-
using a torque wrench.
49D. Slacken the top
bolt, swivel the caliper
up and the pads come
free, for checking.
IMPORTANT NOTE:
If you remove the
top caliper bolt, DO NOT allow the weight of the caliper
to hang from the flexible hose
-
position it to rest on the
driveshaft, or support it from the road spring using a
length of wire.
Page 63 of 171
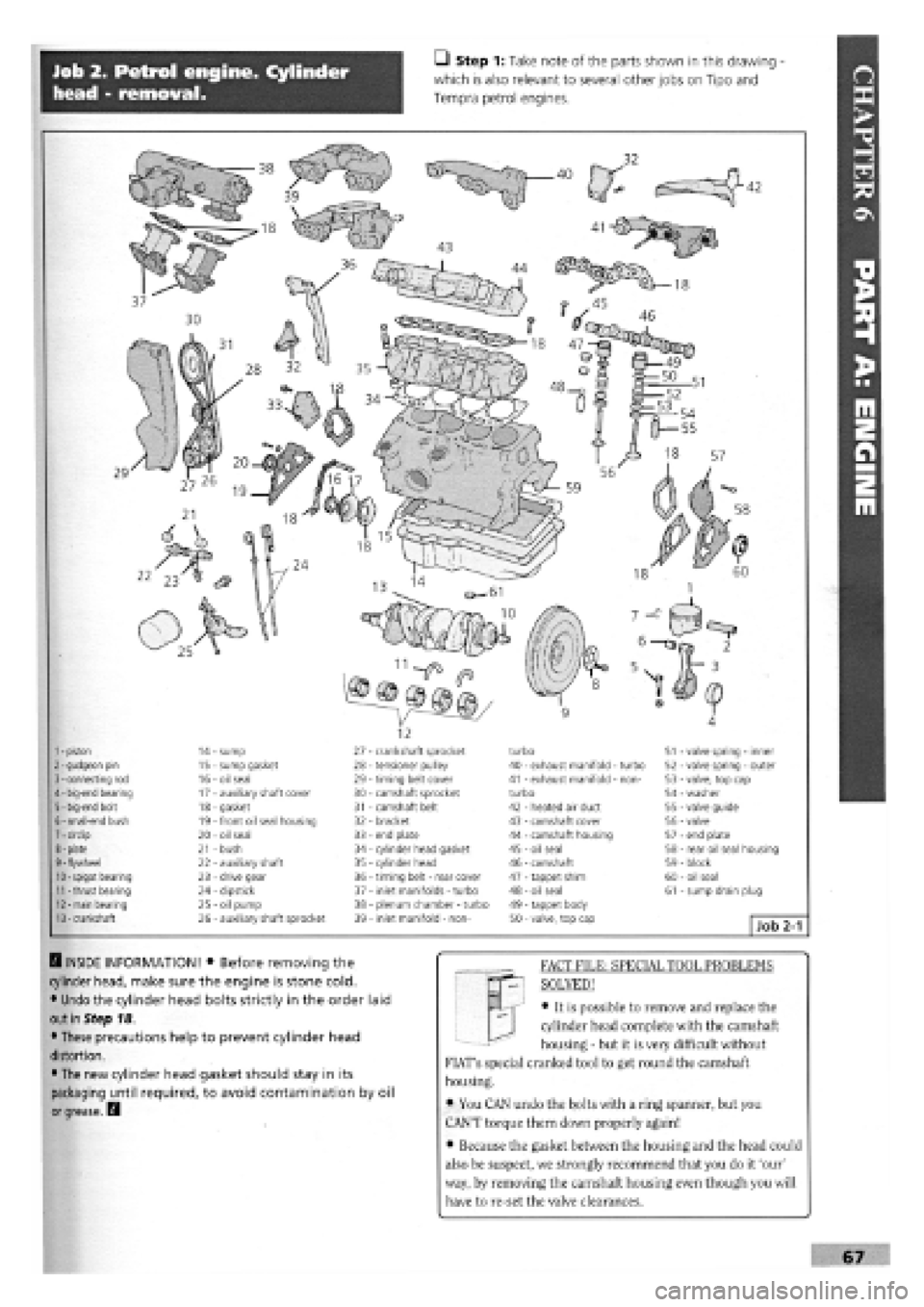
Job 2. Petrol engine. Cylinder
head • removal.
• Step 1: Take note of the parts shown in this drawing -
which is also relevant to several other jobs on Tipo and
Tempra petrol engines.
7
-
cirdip 8
-
plate 9
-
flywheel 10-spigot bearing
11 -
thrust bearing 12
-
main bearing 13-crankshaft
14 - sump 15 - sump gasket 16 - oil seal 17 - auxiliary shaft cover 18 - gasket 19 - front oil seal housing 20 - oil seal 21 - bush 22 - auxiliary shaft 23 - drive gear 24 - dipstick 25 - oil pump 26 - auxiliary shaft sprocket
1
-
piston 2
-
gudgeon pin 3
-
connecting rod 4
-
big-end bearing 5
-
big-end bolt 6
-
small-end bush
27 28 29 30 31 32 33 34 35 36 37 38 39
turbo 40 - exhaust manifold - turbo 41 - exhaust manifold - non-turbo 42 - heated air duct 43 - camshaft cover 44 - camshaft housing 45 - oil seal 46 - camshaft 47 - tappet shim 48 - oil seal 49 - tappet body 50
-
valve, top cap Job 2-1
- crankshaft sprocket - tensioner pulley - timing belt cover - camshaft sprocket - camshaft belt - bracket - end plate - cylinder head gasket - cylinder head - timing belt - rear cover - inlet manifolds - turbo - plenum chamber
-
turbo - inlet manifold - non-
51 - valve spring - inner 52 - valve spring
-
outer 53 - valve, top cap 54 - washer 55 - valve guide 56 - valve 57 - end plate 58 - rear oil seal housing 59 - block 60 - oil seal 61 - sump drain plug
Q INSIDE INFORMATION! • Before removing the
cylinder head, make sure the engine is stone cold.
• Undo the cylinder head bolts strictly in the order laid
out in Step 18.
• These precautions help to prevent cylinder head
distortion.
• The new cylinder head gasket should stay in its
packaging until required, to avoid contamination by oil
or grease.
B
FACT FILE: SPECIAL TOOL PROBLEMS
SOLVED!
• It is possible to remove and replace the
cylinder head complete with the camshaft
housing - but it is very difficult without
FIAT's special cranked tool to get round the camshaft
housing.
• You CAN undo the bolts with a ring spanner, but you
CAN'T torque them down properly again!
• Because the gasket between the housing and the head could
also be suspect, we strongly recommend that you do it 'our'
way, by removing the camshaft housing even though you will
have to re-set the valve clearances.
Page 74 of 171

• Step 30: Fit
the crankshaft
pulley and
tighten. See
Chapter 3,
Facts and
Figures.
• Step 31: Fit the
water pump and
distribution pipe.
• Step 32A: Refit the
flywheel. Do not unbolt the
TDC sensor (1) from the oil seal
housing at its mounting plate
bolts
(2)
unless it is essential to
do so.
• Step 32B: If
the sensor
mounting plate has
to be disturbed, you
will need the FIAT
special tool illus-
trated here (inset) in
order to reposition it
correctly. Position
the timing mark on
the crankshaft
pulley with the zero
degrees mark on the outer timing belt cover (and double
check that the timing mark on the flywheel
-
rubber bung
removed
-
is aligned at zero degrees).
With the bracket fitted to the oil seal housing, fit the FIAT
special tool onto the bracket in place of the sensor with a slot
in the tool fitting exactly over the TDC pin on the flywheel.
When everything is lined up, position the bracket accurately
and tighten the bolts. Remove the tool and refit the sensor.
IMPORTANT NOTE: During assembly, a shear-bolt will
have been fitted to prevent accidental movement of the
bracket. If you need to undo it, you will need to drill it
out and you should replace it with a new one obtained
from your FIAT dealership.
• Step 33: Refit the clutch. See PARTB: TRANSMISSION,
Job 4.
Q Step 34: Refit the fuel pump and pushrod using new
gaskets on both sides of the spacer block, 0.3 mm thick
between the spacer and the engine and 0.7 mm between the
spacer and the pump. See PART F: FUEL AND EXHAUST for
information on setting the pump position.
• Step 35:
Lubricate the sealing
ring and screw on a
new oil filter.
• Step 36:
Before refitting the
distributor, (see
PART D: IGNITION)
refit, if necessary,
the oil pump drive
gear.
• Step 37: Refit
all remaining
auxiliary compo-
nents (including the
oil vapour recovery
device, shown here),
using new gaskets
as necessary and
referring to
Chapter
3,
Facts
and Figures for the
torque settings.
Q Step 38: Reconnect the engine to the transmission. See
Job 11.
Q Step 39: Refit the complete unit to the car. See Job
9.
• Step 40: fl INSIDE INFORMATION! Before fitting the
spark plugs and with a fully charged battery, turn the
engine on the starter until the oil warning light goes
out. This primes the lubrication system and gives more
immediate oil pressure on initial start up after overhaul-
a critical time in the life of an engine. B
• Step 41: Fit the spark plugs and start the engine
-
this
might take a few seconds more than normal on the initial start
up.
• Step 42: Allow the engine to warm up on fast idle
until
it
reaches working temperature and then slow it down to its
normal speed (if adjustable
-
see PART F: FUEL AND
EXHAUST)
Page 89 of 171
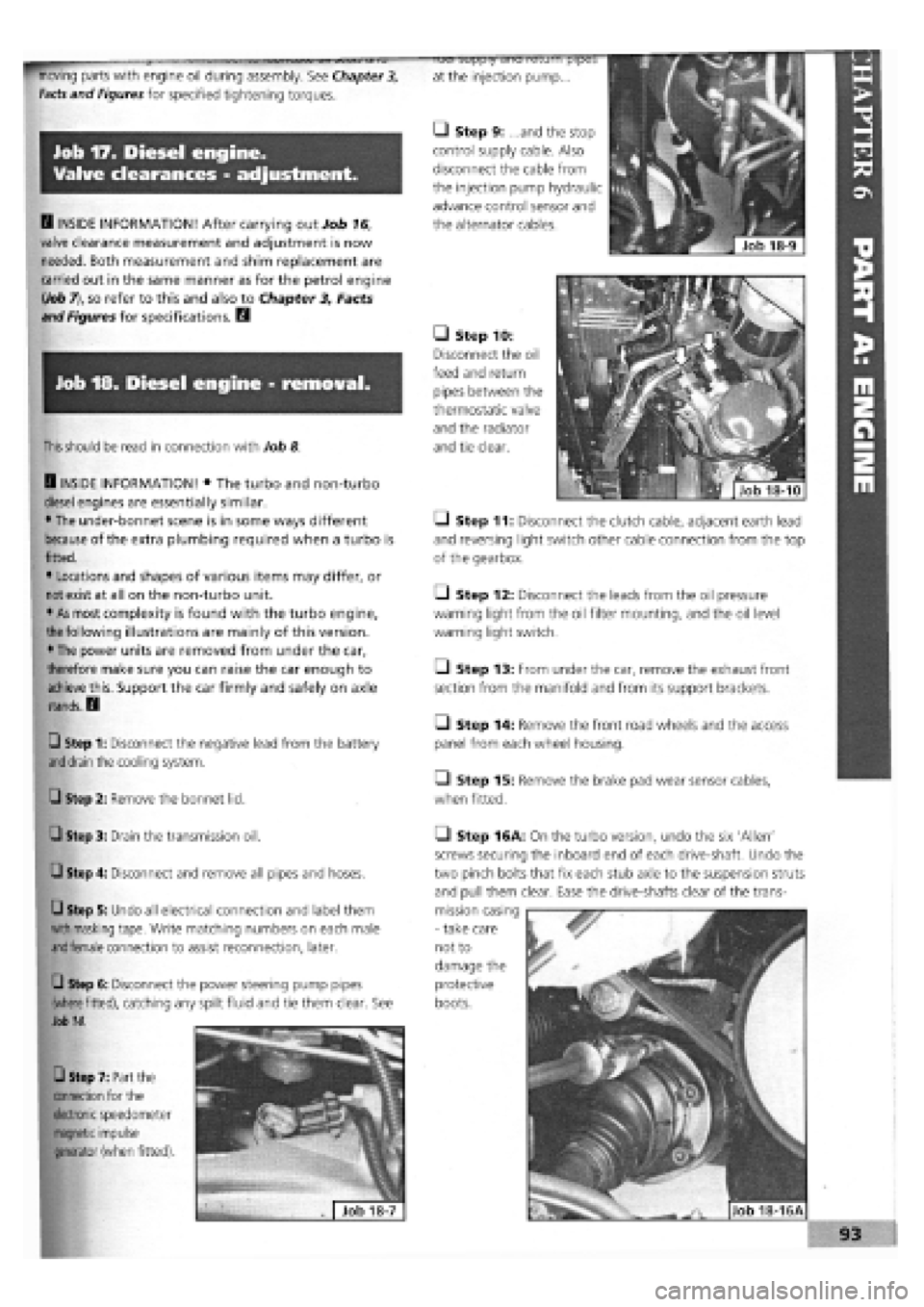
Job 17. Diesel engine.
Valve clearances - adjustment.
D INSIDE INFORMATION! After carrying out Job 16,
valve clearance measurement and adjustment is now
needed. Both measurement and shim replacement are
carried out in the same manner as for the petrol engine
(.Job
7), so refer to this and also to Chapter 3, Facts
and Figures for specifications. B
Job 18. Diesel engine - removal.
moving parts with engine oil during assembly. See Chapter 3,
Facts
and Figures for specified tightening torques.
luei suppiy diiu leium pipe;>
at the injection pump...
• Step 9: ...and the stop
control supply cable. Also
disconnect the cable from
the injection pump hydraulic
advance control sensor and
the alternator cables.
• Step 10:
Disconnect the oil
feed and return
pipes between the
thermostatic valve
and the radiator
and tie clear.
I
This should
be read in connection with Job 8
Q INSIDE INFORMATION! • The turbo and non-turbo
diesel engines are essentially similar.
• The under-bonnet scene is in some ways different
because of the extra plumbing required when a turbo is
fitted.
• Locations and shapes of various items may differ, or
not exist at all on the non-turbo unit.
• As most complexity is found with the turbo engine,
I
the
following illustrations are mainly of this version.
• The power units are removed from under the car,
therefore make sure you can raise the car enough to
achieve this. Support the car firmly and safely on axle
stands. D
Q Step 1: Disconnect the negative lead from the battery
and drain
the cooling system. Q Step 2: Remove the bonnet lid.
• Step 3: Drain the transmission oil.
Q Step 4: Disconnect and remove all pipes and hoses.
Q Step 5: Undo all electrical connection and label them
with masking
tape. Write matching numbers on each male
and female
connection to assist reconnection, later.
Q Step 6: Disconnect the power steering pump pipes
(where fitted),
catching any spilt fluid and tie them clear. See
Job 14.
• Step 7: Part the
connection for the
electronic
speedometer
magnetic impulse
generator
(when fitted).
Q Step 11: Disconnect the clutch cable, adjacent earth lead
and reversing light switch other cable connection from the top
of the gearbox.
• Step 12: Disconnect the leads from the oil pressure
warning light from the oil filter mounting, and the oil level
warning light switch.
• Step 13: From under the car, remove the exhaust front
section from the manifold and from its support brackets.
O Step 14: Remove the front road wheels and the access
panel from each wheel housing.
• Step 15: Remove the brake pad wear sensor cables,
when fitted.
Q Step 16A: On the turbo version, undo the six 'Allen'
screws securing the inboard end of each drive-shaft. Undo the
two pinch bolts that fix each stub axle to the suspension struts
and pull them clear. Ease the drive-shafts clear of the trans-
mission casing
-
take care
not to
damage the
protective
boots.
Page 93 of 171
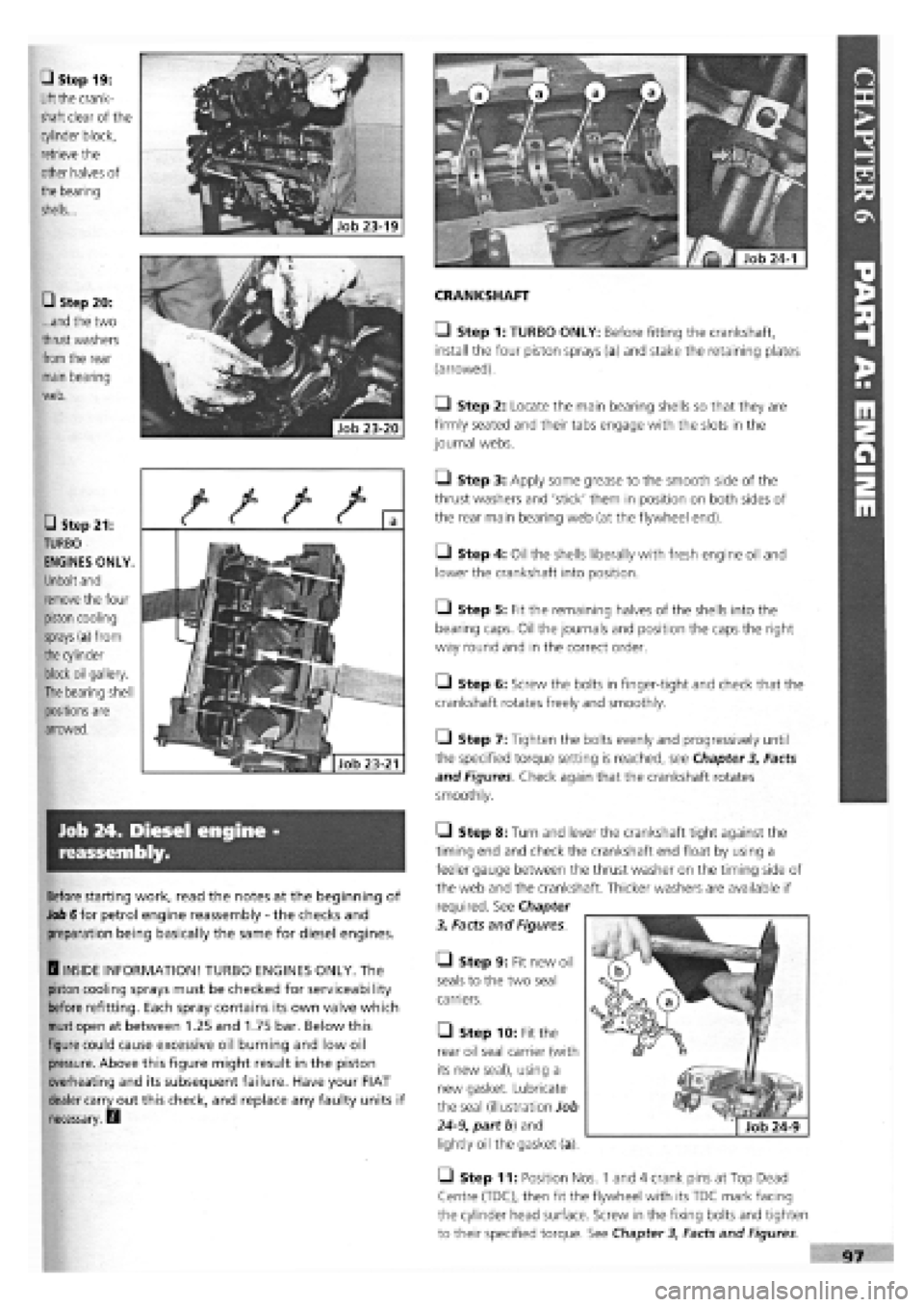
CRANKSHAFT
• Step 1: TURBO ONLY: Before fitting the crankshaft,
install the four piston sprays (a) and stake the retaining plates
(arrowed).
Q Step 2: Locate the main bearing shells so that they are
firmly seated and their tabs engage with the slots in the
journal webs.
• Step 3: Apply some grease to the smooth side of the
thrust washers and 'stick' them in position on both sides of
the rear main bearing web (at the flywheel end).
• Step 4: Oil the shells liberally with fresh engine oil and
lower the crankshaft into position.
• Step 5: Fit the remaining halves of the shells into the
bearing caps. Oil the journals and position the caps the right
way round and in the correct order.
• Step 6: Screw the bolts in finger-tight and check that the
crankshaft rotates freely and smoothly.
Q Step 7: Tighten the bolts evenly and progressively until
the specified torque setting is reached, see Chapter
3,
Facts
and Figures. Check again that the crankshaft rotates
smoothly.
• Step 19:
Lift
the crank-
shaft clear of the
cylinder block,
retrieve the
other halves of
the
bearing
shells...
• Step 20:
...and
the two
thrust
washers
from
the rear
main bearing
web.
• Step 21:
TURBO
ENGINES ONLY.
Unbolt and
remove
the four
piston cooling
sprays
(a) from
the
cylinder
block oil gallery.
The
bearing shell
positions are
arrowed.
Job 24. Diesel engine -
reassembly.
Before starting work, read the notes at the beginning of
Job 6 for petrol engine reassembly
-
the checks and
preparation being basically the same for diesel engines.
H INSIDE INFORMATION! TURBO ENGINES ONLY. The
piston cooling sprays must be checked for serviceability
before refitting. Each spray contains its own valve which
must
open at between 1.25 and 1.75 bar. Below this
figure could cause excessive oil burning and low oil
pressure. Above this figure might result in the piston
overheating and its subsequent failure. Have your FIAT
dealer carry out this check, and replace any faulty units if
necessary. Q
• Step 9: Fit new oil
seals to the two seal
carriers.
• Step 10: Fit the
rear oil seal carrier (with
its new seal), using a
new gasket. Lubricate
the seal (illustration Job
24-9,
part b) and
lightly oil the gasket (a).
• Step 11: Position Nos. 1 and 4 crank pins at Top Dead
Centre (TDC), then fit the flywheel with its TDC mark facing
the cylinder head surface. Screw in the fixing bolts and tighten
to their specified torque. See Chapter
3,
Facts and Figures
Job 23-21
Q Step 8: Turn and lever the crankshaft tight against the
timing end and check the crankshaft end float by using a
feeler gauge between the thrust washer on the timing side of
the web and the crankshaft. Thicker washers are available if
required. See Chapter
3, Facts and Figures.
Page 96 of 171
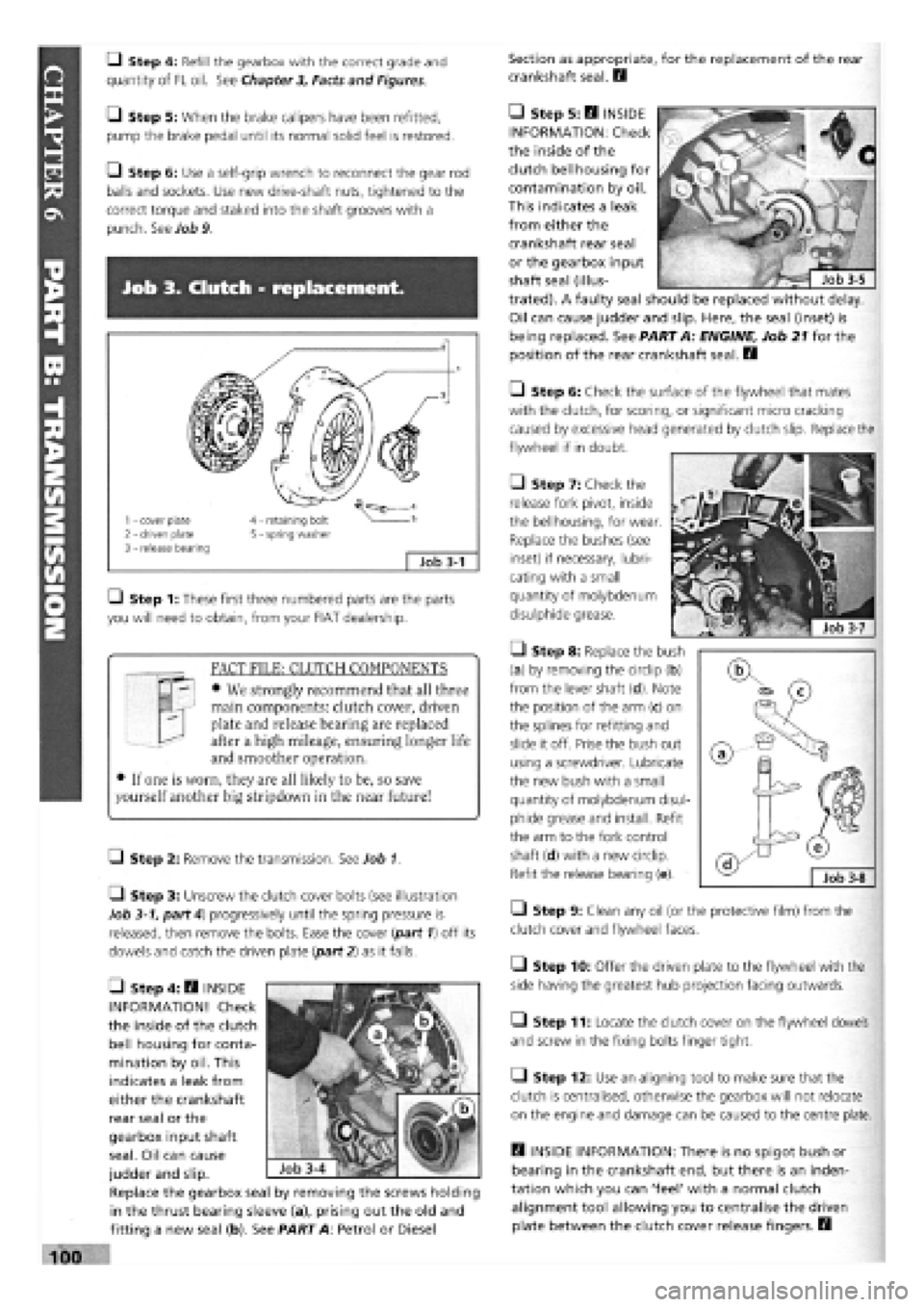
• Step 4: Refill the gearbox with the correct grade and
quantity of FL oil. See Chapter
3,
Facts and Figures.
Section as appropriate, for the replacement of the rear
crankshaft seal. B
—1 Step 5: When the brake calipers have been refitted,
pump the brake pedal until its normal solid feel is restored.
• Step 6: Use a self-grip wrench to reconnect the gear rod
balls and sockets. Use new drive-shaft nuts, tightened to the
correct torque and staked into the shaft grooves with a
punch. See Job 9.
Job 3. Clutch - replacement.
1 - cover plate 2 - driven plate 3 - release bearing
4 - retaining bolt 5 - spring washer
;
Job 3-1
Q Step 1: These first three numbered parts are the parts
you will need to obtain, from your FIAT dealership.
FACT FILE: CLUTCH COMPONENTS
• We strongly recommend that all three
main components: clutch cover, driven
plate and release bearing are replaced
after a high mileage, ensuring longer life
and smoother operation.
• If one is worn, they are all likely to be, so save
yourself another big stripdown in the near future!
LI Step 2: Remove the transmission. See Job 1.
• Step 3: Unscrew the clutch cover bolts (see illustration
Job
3-1,
part 4) progressively until the spring pressure is
released, then remove the bolts. Ease the cover (part 1) off its
dowels and catch the driven plate {part 2) as it falls.
• Step 6: Check the surface of the flywheel that mates
with the clutch, for scoring, or significant micro cracking
caused by excessive head generated by clutch slip. Replace the
flywheel if in doubt.
7ZJ
• Step 7: Check the
release fork pivot, inside
the bellhousing, for wear
Replace the bushes (see
inset) if necessary, lubri-
cating with a small
quantity of molybdenum
disulphide grease.
• Step 8: Replace the bush
(a) by removing the circlip (b)
from the lever shaft (d). Note
the position of the arm (c) on
the splines for refitting and
slide it off. Prise the bush out
using a screwdriver. Lubricate
the new bush with a small
quantity of molybdenum disul-
phide grease and install. Refit
the arm to the fork control
shaft (d) with a new circlip.
Refit the release bearing (e).
• Step 9: Clean any oil (or the protective film) from the
clutch cover and flywheel faces.
• Step 10: Offer the driven plate to the flywheel with the
side having the greatest hub projection facing outwards.
• Step 11: Locate the clutch cover on the flywheel dowels
and screw in the fixing bolts finger tight.
• Step 12: Use an aligning tool to make sure that the
clutch is centralised, otherwise the gearbox will not relocate
on the engine and damage can be caused to the centre plate.
B INSIDE INFORMATION: There is no spigot bush or
bearing in the crankshaft end, but there is an inden-
tation which you can 'feel' with a normal clutch
alignment tool allowing you to centralise the driven
plate between the clutch cover release fingers. B
• Step 5: B INSIDE
INFORMATION: Check
the inside of the
clutch bellhousing for
contamination by oil.
This indicates a leak
from either the
crankshaft rear seal
or the gearbox input
shaft seal (illus-
trated). A faulty seal should be replaced without delay.
Oil can cause judder and slip. Here, the seal (inset) is
being replaced. See PART A: ENGINE, Job 21 for the
position of the rear crankshaft seal. B
• Step 4: B INSIDE
INFORMATION! Check
the inside of the clutch
bell housing for conta-
mination by oil. This
indicates a leak from
either the crankshaft
rear seal or the
gearbox input shaft
seal. Oil can cause
judder and slip.
Replace the gearbox seal by removing the screws holding
in the thrust bearing sleeve (a), prising out the old and
fitting a new seal (b). See PART A: Petrol or Diesel
Page 99 of 171
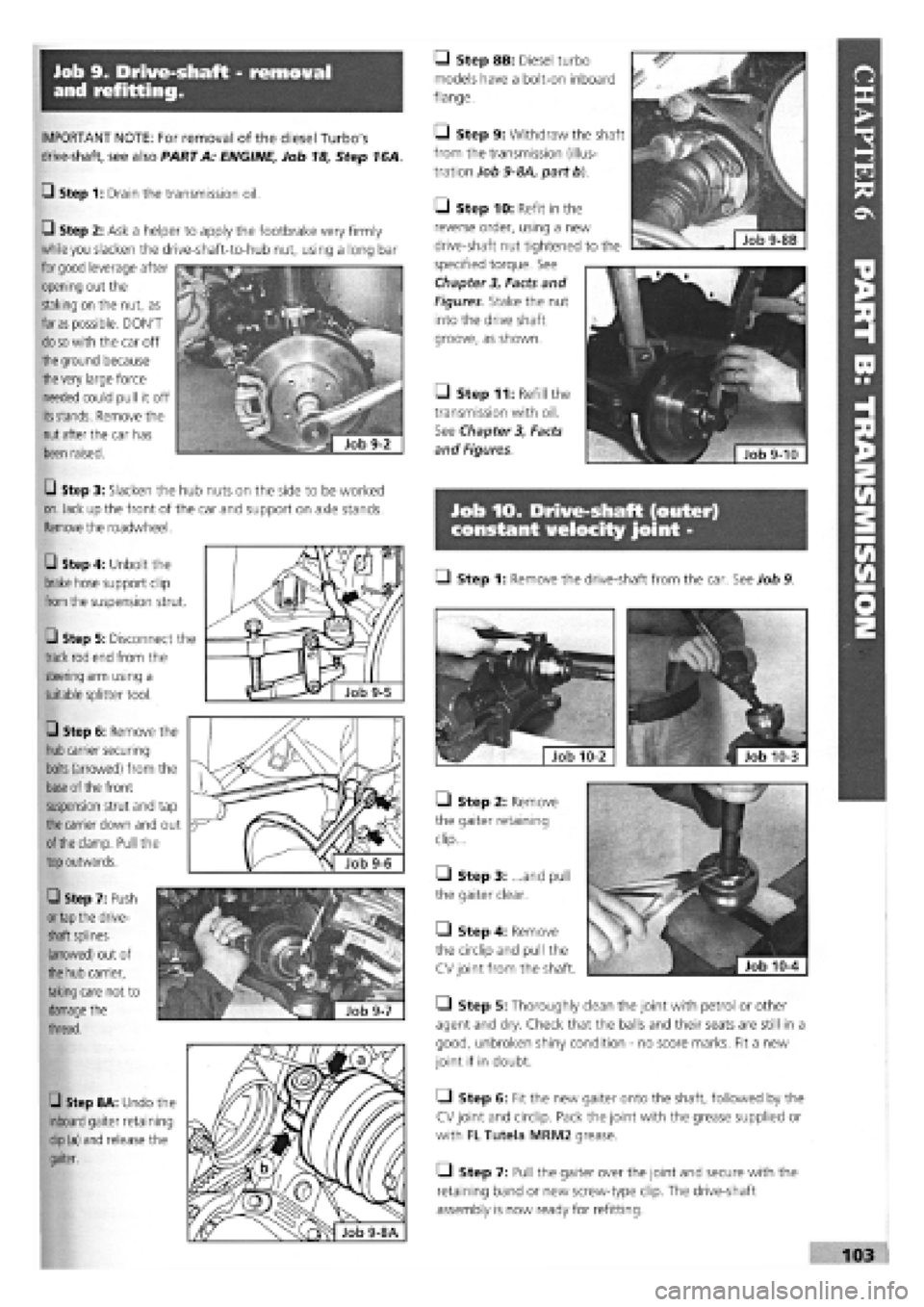
Job 9. Drive-shaft - removal
and refitting.
IMPORTANT NOTE: For removal of the diesel Turbo's
drive-shaft, see also PART A: ENGINE, Job 18, Step 16A.
G Step 1: Drain the transmission oil.
• Step 8B: Diesel turbo
models have a bolt-on inboard
flange.
• Step 9: Withdraw the shaft
from the transmission (illus-
tration Job
9-8A,
part b).
G Step 2: Ask a helper to apply the footbrake very firmly
while
you
slacken the drive-shaft-to-hub nut, using a long bar
for
good
leverage after
opening out the
staking on the nut, as
far
as
possible. DON'T
do so
with the car off
the
ground because
the
very large force
needed could pull it off
its stands.
Remove the
nut
after the car has
been raised.
Job 10. Drive-shaft (outer)
constant velocity joint -
G Step 8A: Undo the
inboard
gaiter retaining
clip
(a) and release the
gaiter.
• Step 11: Refill the
transmission with oil.
See Chapter
3,
Facts
and Figures.
G Step 3: Slacken the hub nuts on the side to be worked
on.
Jack up the front of the car and support on axle stands.
Remove the roadwheel.
G Step 6: Remove the
hub
carrier securing
bolts
(arrowed) from the
base
of the front
suspension strut and tap
the
carrier down and out
of the
clamp. Pull the
top
outwards.
G Step 7: Push
or tap
the drive-
shaft
splines
(arrowed) out of
the hub
carrier,
taking
care not to
damage
the
thread.
Q Step 1: Remove the drive-shaft from the car. See Job 9. G Step 4: Unbolt the
brake hose support clip
from
the suspension strut.
G Step 5: Disconnect the
track rod end from the
steering arm using a
suitable splitter tool.
• Step 2: Remove
the gaiter retaining
clip...
Q Step 3: ...and pull
the gaiter clear.
• Step 4: Remove
the circlip and pull the
CV joint from the shaft.
Q Step 5: Thoroughly clean the joint with petrol or other
agent and dry. Check that the balls and their seats are still in a
good, unbroken shiny condition
-
no score marks. Fit a new
joint if in doubt.
• Step 6: Fit the new gaiter onto the shaft, followed by the
CV joint and circlip. Pack the joint with the grease supplied or
with FL Tutela MRM2 grease.
Q Step 7: Pull the gaiter over the joint and secure with the
retaining band or new screw-type clip. The drive-shaft
assembly is now ready for refitting.
• Step 10: Refit in the
reverse order, using a new
drive-shaft nut tightened to the
specified torque. See
Chapter
3,
Facts and
Figures Stake the nut
into the drive shaft
groove, as shown.