tow FORD SIERRA 1982 1.G Routine Manintenance And Servicing Workshop Manual
[x] Cancel search | Manufacturer: FORD, Model Year: 1982, Model line: SIERRA, Model: FORD SIERRA 1982 1.GPages: 22, PDF Size: 1.26 MB
Page 3 of 22
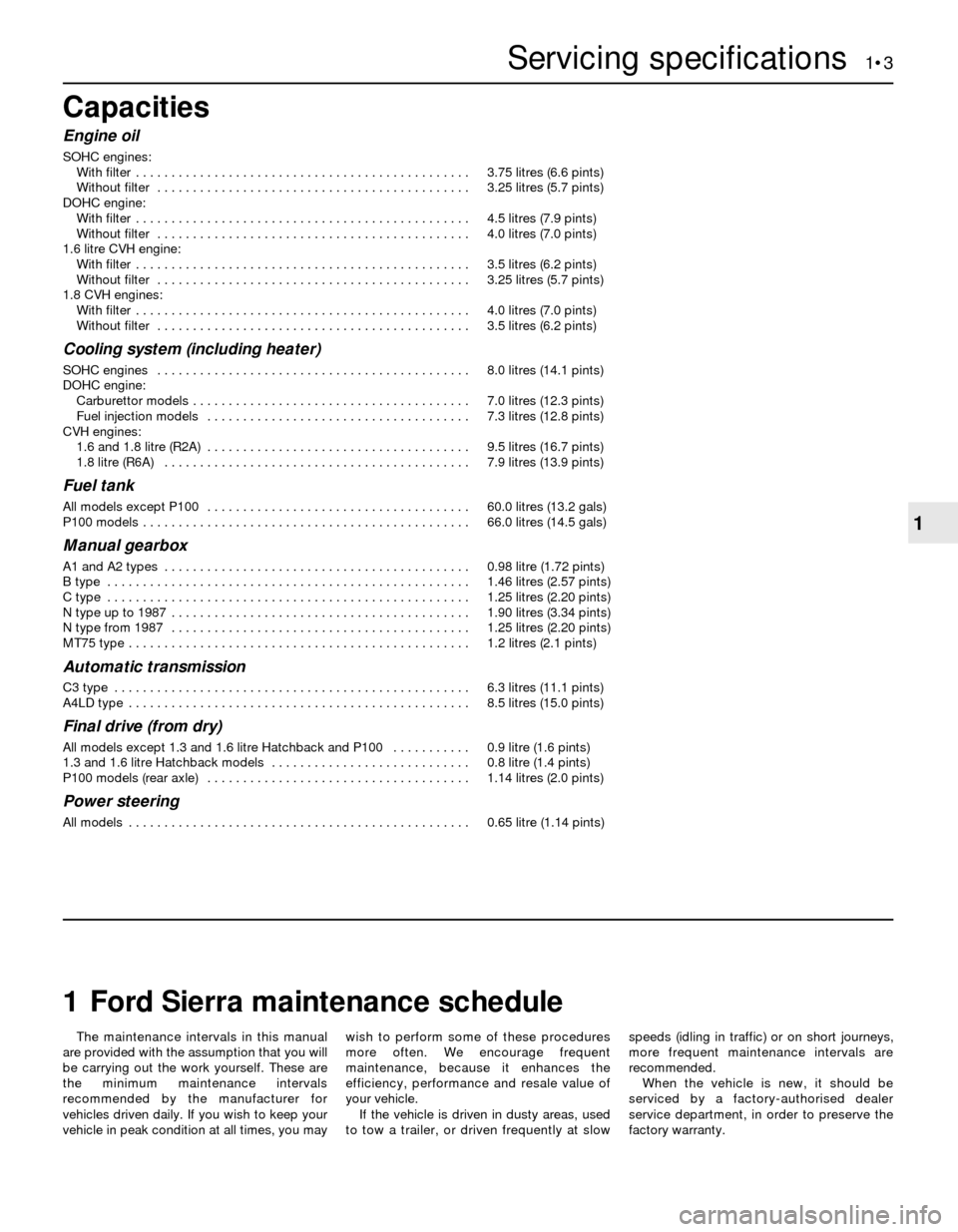
The maintenance intervals in this manual
are provided with the assumption that you will
be carrying out the work yourself. These are
the minimum maintenance intervals
recommended by the manufacturer for
vehicles driven daily. If you wish to keep your
vehicle in peak condition at all times, you maywish to perform some of these procedures
more often. We encourage frequent
maintenance, because it enhances the
efficiency, performance and resale value of
your vehicle.
If the vehicle is driven in dusty areas, used
to tow a trailer, or driven frequently at slowspeeds (idling in traffic) or on short journeys,
more frequent maintenance intervals are
recommended.
When the vehicle is new, it should be
serviced by a factory-authorised dealer
service department, in order to preserve the
factory warranty.
Capacities
Engine oil
SOHC engines:
With filter . . . . . . . . . . . . . . . . . . . . . . . . . . . . . . . . . . . . . . . . . . . . . . .3.75 litres (6.6 pints)
Without filter . . . . . . . . . . . . . . . . . . . . . . . . . . . . . . . . . . . . . . . . . . . .3.25 litres (5.7 pints)
DOHC engine:
With filter . . . . . . . . . . . . . . . . . . . . . . . . . . . . . . . . . . . . . . . . . . . . . . .4.5 litres (7.9 pints)
Without filter . . . . . . . . . . . . . . . . . . . . . . . . . . . . . . . . . . . . . . . . . . . .4.0 litres (7.0 pints)
1.6 litre CVH engine:
With filter . . . . . . . . . . . . . . . . . . . . . . . . . . . . . . . . . . . . . . . . . . . . . . .3.5 litres (6.2 pints)
Without filter . . . . . . . . . . . . . . . . . . . . . . . . . . . . . . . . . . . . . . . . . . . .3.25 litres (5.7 pints)
1.8 CVH engines:
With filter . . . . . . . . . . . . . . . . . . . . . . . . . . . . . . . . . . . . . . . . . . . . . . .4.0 litres (7.0 pints)
Without filter . . . . . . . . . . . . . . . . . . . . . . . . . . . . . . . . . . . . . . . . . . . .3.5 litres (6.2 pints)
Cooling system (including heater)
SOHC engines . . . . . . . . . . . . . . . . . . . . . . . . . . . . . . . . . . . . . . . . . . . .8.0 litres (14.1 pints)
DOHC engine:
Carburettor models . . . . . . . . . . . . . . . . . . . . . . . . . . . . . . . . . . . . . . .7.0 litres (12.3 pints)
Fuel injection models . . . . . . . . . . . . . . . . . . . . . . . . . . . . . . . . . . . . .7.3 litres (12.8 pints)
CVH engines:
1.6 and 1.8 litre (R2A) . . . . . . . . . . . . . . . . . . . . . . . . . . . . . . . . . . . . .9.5 litres (16.7 pints)
1.8 litre (R6A) . . . . . . . . . . . . . . . . . . . . . . . . . . . . . . . . . . . . . . . . . . .7.9 litres (13.9 pints)
Fuel tank
All models except P100 . . . . . . . . . . . . . . . . . . . . . . . . . . . . . . . . . . . . .60.0 litres (13.2 gals)
P100 models . . . . . . . . . . . . . . . . . . . . . . . . . . . . . . . . . . . . . . . . . . . . . .66.0 litres (14.5 gals)
Manual gearbox
A1 and A2 types . . . . . . . . . . . . . . . . . . . . . . . . . . . . . . . . . . . . . . . . . . .0.98 litre (1.72 pints)
B type . . . . . . . . . . . . . . . . . . . . . . . . . . . . . . . . . . . . . . . . . . . . . . . . . . .1.46 litres (2.57 pints)
C type . . . . . . . . . . . . . . . . . . . . . . . . . . . . . . . . . . . . . . . . . . . . . . . . . . .1.25 litres (2.20 pints)
N type up to 1987 . . . . . . . . . . . . . . . . . . . . . . . . . . . . . . . . . . . . . . . . . .1.90 litres (3.34 pints)
N type from 1987 . . . . . . . . . . . . . . . . . . . . . . . . . . . . . . . . . . . . . . . . . .1.25 litres (2.20 pints)
MT75 type . . . . . . . . . . . . . . . . . . . . . . . . . . . . . . . . . . . . . . . . . . . . . . . .1.2 litres (2.1 pints)
Automatic transmission
C3 type . . . . . . . . . . . . . . . . . . . . . . . . . . . . . . . . . . . . . . . . . . . . . . . . . .6.3 litres (11.1 pints)
A4LD type . . . . . . . . . . . . . . . . . . . . . . . . . . . . . . . . . . . . . . . . . . . . . . . .8.5 litres (15.0 pints)
Final drive (from dry)
All models except 1.3 and 1.6 litre Hatchback and P100 . . . . . . . . . . .0.9 litre (1.6 pints)
1.3 and 1.6 litre Hatchback models . . . . . . . . . . . . . . . . . . . . . . . . . . . .0.8 litre (1.4 pints)
P100 models (rear axle) . . . . . . . . . . . . . . . . . . . . . . . . . . . . . . . . . . . . .1.14 litres (2.0 pints)
Power steering
All models . . . . . . . . . . . . . . . . . . . . . . . . . . . . . . . . . . . . . . . . . . . . . . . .0.65 litre (1.14 pints)
Servicing specifications 1•3
1
1Ford Sierra maintenance schedule
Page 14 of 22
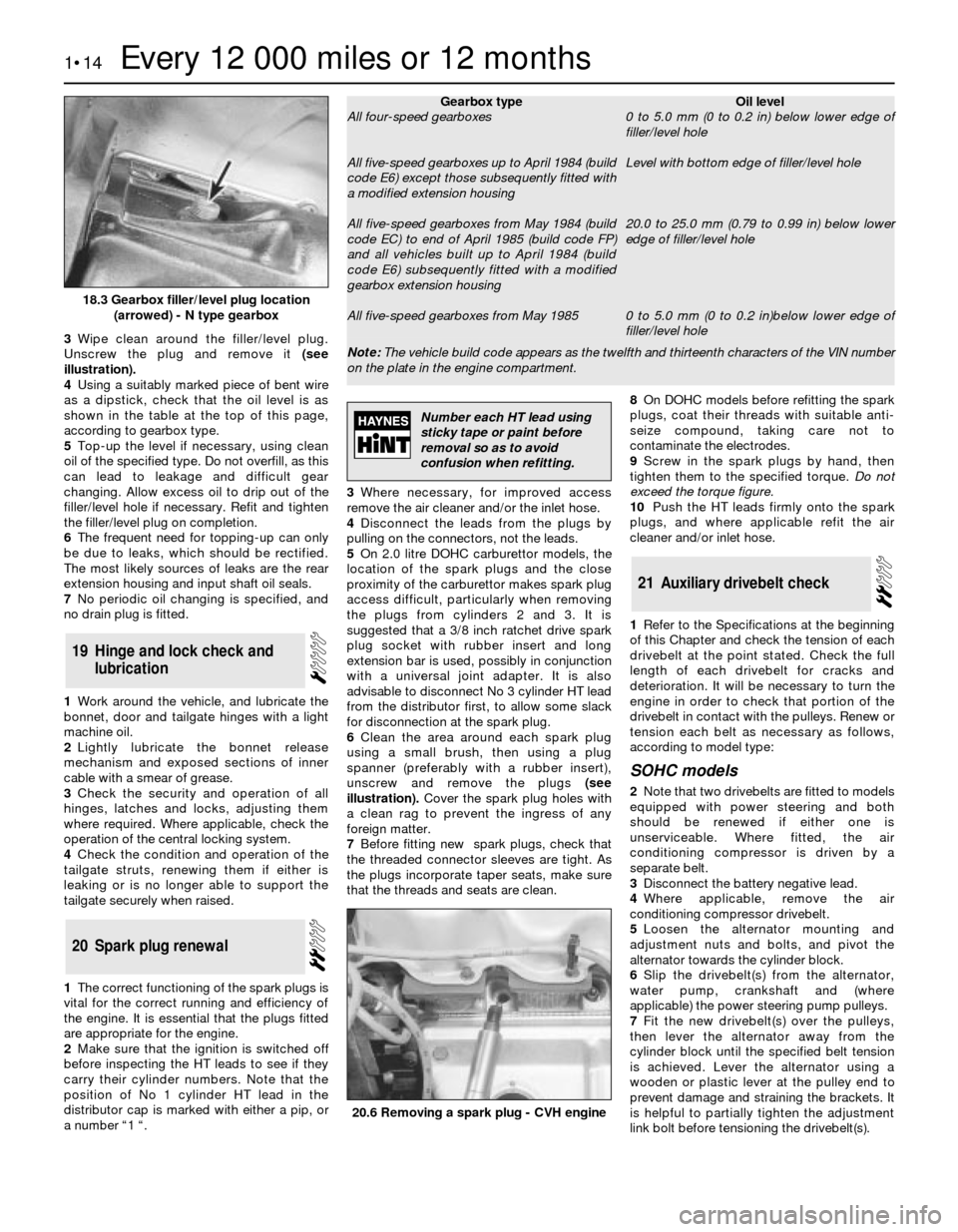
3Wipe clean around the filler/level plug.
Unscrew the plug and remove it(see
illustration).
4Using a suitably marked piece of bent wire
as a dipstick, check that the oil level is as
shown in the table at the top of this page,
according to gearbox type.
5Top-up the level if necessary, using clean
oil of the specified type. Do not overfill, as this
can lead to leakage and difficult gear
changing. Allow excess oil to drip out of the
filler/level hole if necessary. Refit and tighten
the filler/level plug on completion.
6The frequent need for topping-up can only
be due to leaks, which should be rectified.
The most likely sources of leaks are the rear
extension housing and input shaft oil seals.
7No periodic oil changing is specified, and
no drain plug is fitted.
1Work around the vehicle, and lubricate the
bonnet, door and tailgate hinges with a light
machine oil.
2Lightly lubricate the bonnet release
mechanism and exposed sections of inner
cable with a smear of grease.
3Check the security and operation of all
hinges, latches and locks, adjusting them
where required. Where applicable, check the
operation of the central locking system.
4Check the condition and operation of the
tailgate struts, renewing them if either is
leaking or is no longer able to support the
tailgate securely when raised.
1The correct functioning of the spark plugs is
vital for the correct running and efficiency of
the engine. It is essential that the plugs fitted
are appropriate for the engine.
2Make sure that the ignition is switched off
before inspecting the HT leads to see if they
carry their cylinder numbers. Note that the
position of No 1 cylinder HT lead in the
distributor cap is marked with either a pip, or
a number “1 “.3Where necessary, for improved access
remove the air cleaner and/or the inlet hose.
4Disconnect the leads from the plugs by
pulling on the connectors, not the leads.
5On 2.0 litre DOHC carburettor models, the
location of the spark plugs and the close
proximity of the carburettor makes spark plug
access difficult, particularly when removing
the plugs from cylinders 2 and 3. It is
suggested that a 3/8 inch ratchet drive spark
plug socket with rubber insert and long
extension bar is used, possibly in conjunction
with a universal joint adapter. It is also
advisable to disconnect No 3 cylinder HT lead
from the distributor first, to allow some slack
for disconnection at the spark plug.
6Clean the area around each spark plug
using a small brush, then using a plug
spanner (preferably with a rubber insert),
unscrew and remove the plugs(see
illustration).Cover the spark plug holes with
a clean rag to prevent the ingress of any
foreign matter.
7Before fitting new spark plugs, check that
the threaded connector sleeves are tight. As
the plugs incorporate taper seats, make sure
that the threads and seats are clean.8On DOHC models before refitting the spark
plugs, coat their threads with suitable anti-
seize compound, taking care not to
contaminate the electrodes.
9Screw in the spark plugs by hand, then
tighten them to the specified torque. Do not
exceed the torque figure.
10Push the HT leads firmly onto the spark
plugs, and where applicable refit the air
cleaner and/or inlet hose.
1Refer to the Specifications at the beginning
of this Chapter and check the tension of each
drivebelt at the point stated. Check the full
length of each drivebelt for cracks and
deterioration. It will be necessary to turn the
engine in order to check that portion of the
drivebelt in contact with the pulleys. Renew or
tension each belt as necessary as follows,
according to model type:
SOHC models
2Note that two drivebelts are fitted to models
equipped with power steering and both
should be renewed if either one is
unserviceable. Where fitted, the air
conditioning compressor is driven by a
separate belt.
3Disconnect the battery negative lead.
4Where applicable, remove the air
conditioning compressor drivebelt.
5Loosen the alternator mounting and
adjustment nuts and bolts, and pivot the
alternator towards the cylinder block.
6Slip the drivebelt(s) from the alternator,
water pump, crankshaft and (where
applicable) the power steering pump pulleys.
7Fit the new drivebelt(s) over the pulleys,
then lever the alternator away from the
cylinder block until the specified belt tension
is achieved. Lever the alternator using a
wooden or plastic lever at the pulley end to
prevent damage and straining the brackets. It
is helpful to partially tighten the adjustment
link bolt before tensioning the drivebelt(s).
21Auxiliary drivebelt check
20Spark plug renewal
19Hinge and lock check and
lubrication
1•14Every 12 000 miles or 12 months
18.3 Gearbox filler/level plug location
(arrowed) - N type gearbox
20.6 Removing a spark plug - CVH engine
Note: The vehicle build code appears as the twelfth and thirteenth characters of the VIN number
on the plate in the engine compartment.
Gearbox type
All four-speed gearboxes
All five-speed gearboxes up to April 1984 (build
code E6) except those subsequently fitted with
a modified extension housing
All five-speed gearboxes from May 1984 (build
code EC) to end of April 1985 (build code FP)
and all vehicles built up to April 1984 (build
code E6) subsequently fitted with a modified
gearbox extension housing
All five-speed gearboxes from May 1985Oil level
0 to 5.0 mm (0 to 0.2 in) below lower edge of
filler/level hole
Level with bottom edge of filler/level hole
20.0 to 25.0 mm (0.79 to 0.99 in) below lower
edge of filler/level hole
0 to 5.0 mm (0 to 0.2 in)below lower edge of
filler/level hole
Number each HT lead using
sticky tape or paint before
removal so as to avoid
confusion when refitting.
Page 15 of 22
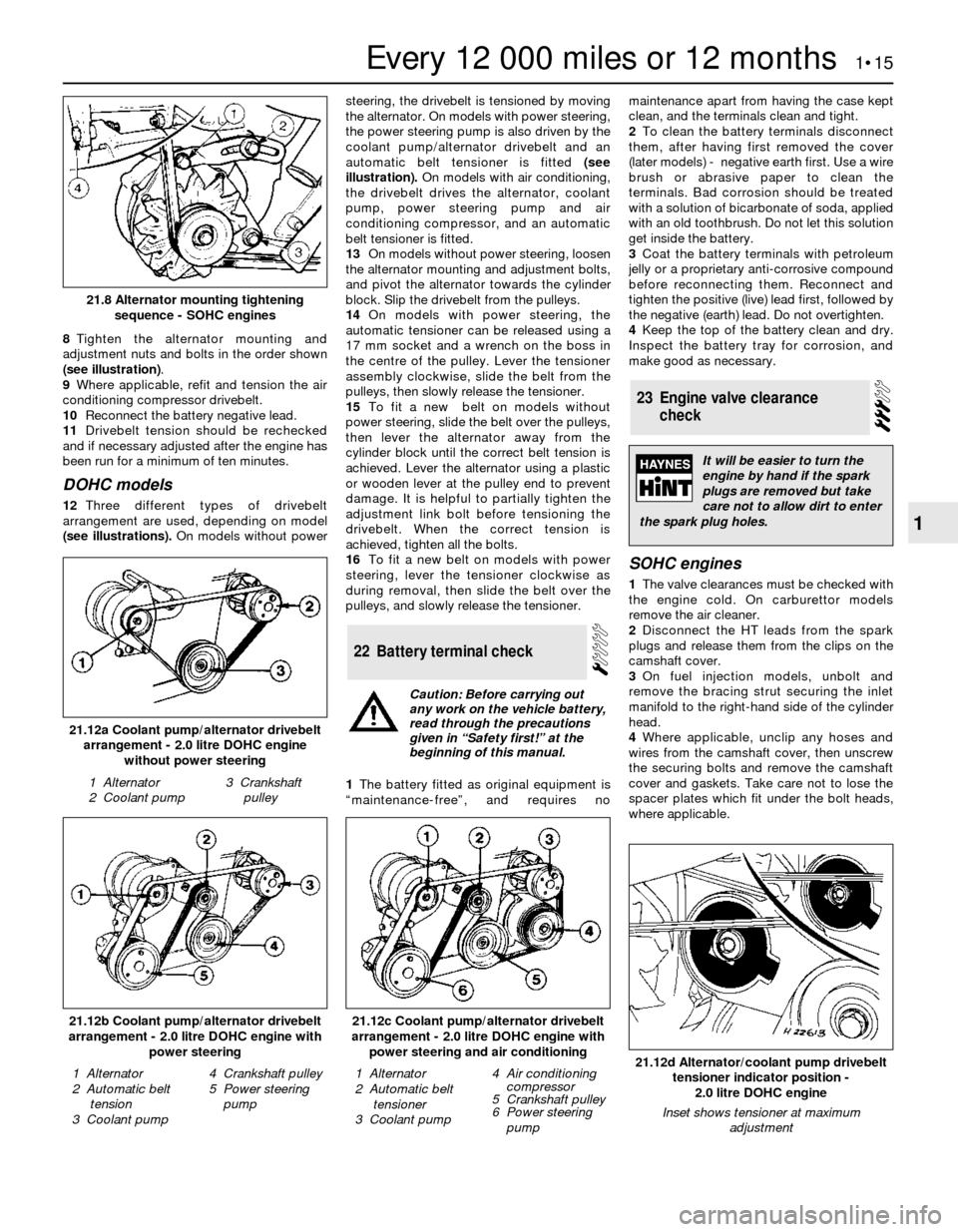
8Tighten the alternator mounting and
adjustment nuts and bolts in the order shown
(see illustration).
9Where applicable, refit and tension the air
conditioning compressor drivebelt.
10Reconnect the battery negative lead.
11Drivebelt tension should be rechecked
and if necessary adjusted after the engine has
been run for a minimum of ten minutes.
DOHC models
12Three different types of drivebelt
arrangement are used, depending on model
(see illustrations).On models without powersteering, the drivebelt is tensioned by moving
the alternator. On models with power steering,
the power steering pump is also driven by the
coolant pump/alternator drivebelt and an
automatic belt tensioner is fitted (see
illustration).On models with air conditioning,
the drivebelt drives the alternator, coolant
pump, power steering pump and air
conditioning compressor, and an automatic
belt tensioner is fitted.
13On models without power steering, loosen
the alternator mounting and adjustment bolts,
and pivot the alternator towards the cylinder
block. Slip the drivebelt from the pulleys.
14On models with power steering, the
automatic tensioner can be released using a
17 mm socket and a wrench on the boss in
the centre of the pulley. Lever the tensioner
assembly clockwise, slide the belt from the
pulleys, then slowly release the tensioner.
15To fit a new belt on models without
power steering, slide the belt over the pulleys,
then lever the alternator away from the
cylinder block until the correct belt tension is
achieved. Lever the alternator using a plastic
or wooden lever at the pulley end to prevent
damage. It is helpful to partially tighten the
adjustment link bolt before tensioning the
drivebelt. When the correct tension is
achieved, tighten all the bolts.
16To fit a new belt on models with power
steering, lever the tensioner clockwise as
during removal, then slide the belt over the
pulleys, and slowly release the tensioner.
1The battery fitted as original equipment is
“maintenance-free”, and requires nomaintenance apart from having the case kept
clean, and the terminals clean and tight.
2To clean the battery terminals disconnect
them, after having first removed the cover
(later models) - negative earth first. Use a wire
brush or abrasive paper to clean the
terminals. Bad corrosion should be treated
with a solution of bicarbonate of soda, applied
with an old toothbrush. Do not let this solution
get inside the battery.
3Coat the battery terminals with petroleum
jelly or a proprietary anti-corrosive compound
before reconnecting them. Reconnect and
tighten the positive (live) lead first, followed by
the negative (earth) lead. Do not overtighten.
4Keep the top of the battery clean and dry.
Inspect the battery tray for corrosion, and
make good as necessary.
SOHC engines
1The valve clearances must be checked with
the engine cold. On carburettor models
remove the air cleaner.
2Disconnect the HT leads from the spark
plugs and release them from the clips on the
camshaft cover.
3On fuel injection models, unbolt and
remove the bracing strut securing the inlet
manifold to the right-hand side of the cylinder
head.
4Where applicable, unclip any hoses and
wires from the camshaft cover, then unscrew
the securing bolts and remove the camshaft
cover and gaskets. Take care not to lose the
spacer plates which fit under the bolt heads,
where applicable.
23Engine valve clearance
check
22Battery terminal check
Every 12 000 miles or 12 months 1•15
1
21.12b Coolant pump/alternator drivebelt
arrangement - 2.0 litre DOHC engine with
power steering
1 Alternator
2 Automatic belt
tension
3 Coolant pump4 Crankshaft pulley
5 Power steering
pump21.12d Alternator/coolant pump drivebelt
tensioner indicator position -
2.0 litre DOHC engine
Inset shows tensioner at maximum
adjustment
1 Alternator
2 Automatic belt
tensioner
3 Coolant pump4 Air conditioning
compressor
5 Crankshaft pulley
6 Power steering
pump
21.12c Coolant pump/alternator drivebelt
arrangement - 2.0 litre DOHC engine with
power steering and air conditioning
21.12a Coolant pump/alternator drivebelt
arrangement - 2.0 litre DOHC engine
without power steering
1 Alternator
2 Coolant pump3 Crankshaft
pulley
21.8 Alternator mounting tightening
sequence - SOHC engines
Caution: Before carrying out
any work on the vehicle battery,
read through the precautions
given in “Safety first!” at the
beginning of this manual.
It will be easier to turn the
engine by hand if the spark
plugs are removed but take
care not to allow dirt to enter
the spark plug holes.
Page 20 of 22
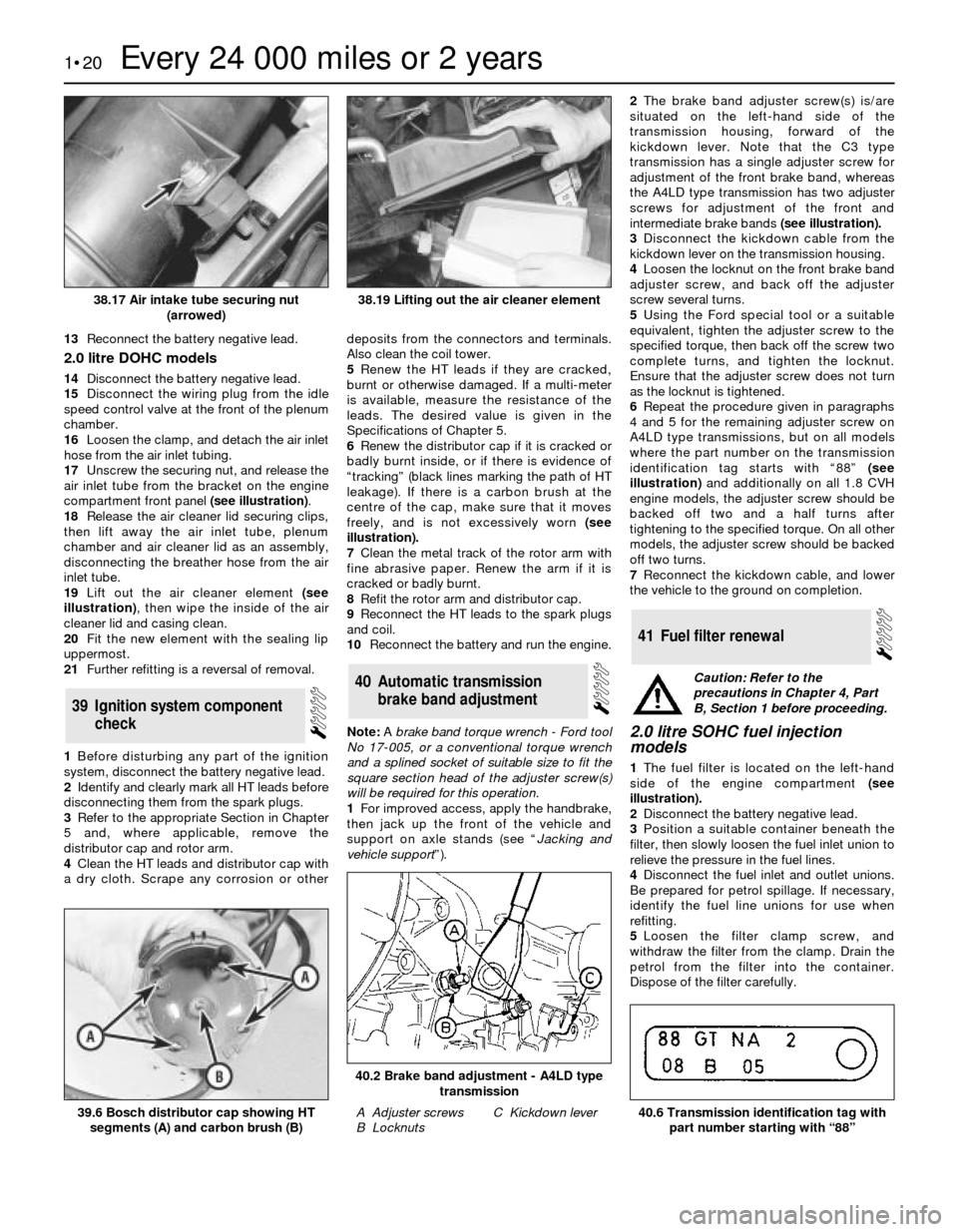
13Reconnect the battery negative lead.
2.0 litre DOHC models
14Disconnect the battery negative lead.
15Disconnect the wiring plug from the idle
speed control valve at the front of the plenum
chamber.
16Loosen the clamp, and detach the air inlet
hose from the air inlet tubing.
17Unscrew the securing nut, and release the
air inlet tube from the bracket on the engine
compartment front panel (see illustration).
18Release the air cleaner lid securing clips,
then lift away the air inlet tube, plenum
chamber and air cleaner lid as an assembly,
disconnecting the breather hose from the air
inlet tube.
19Lift out the air cleaner element (see
illustration), then wipe the inside of the air
cleaner lid and casing clean.
20Fit the new element with the sealing lip
uppermost.
21Further refitting is a reversal of removal.
1Before disturbing any part of the ignition
system, disconnect the battery negative lead.
2Identify and clearly mark all HT leads before
disconnecting them from the spark plugs.
3Refer to the appropriate Section in Chapter
5 and, where applicable, remove the
distributor cap and rotor arm.
4Clean the HT leads and distributor cap with
a dry cloth. Scrape any corrosion or otherdeposits from the connectors and terminals.
Also clean the coil tower.
5Renew the HT leads if they are cracked,
burnt or otherwise damaged. If a multi-meter
is available, measure the resistance of the
leads. The desired value is given in the
Specifications of Chapter 5.
6Renew the distributor cap if it is cracked or
badly burnt inside, or if there is evidence of
“tracking” (black lines marking the path of HT
leakage). If there is a carbon brush at the
centre of the cap, make sure that it moves
freely, and is not excessively worn (see
illustration).
7Clean the metal track of the rotor arm with
fine abrasive paper. Renew the arm if it is
cracked or badly burnt.
8Refit the rotor arm and distributor cap.
9Reconnect the HT leads to the spark plugs
and coil.
10Reconnect the battery and run the engine.
Note: A brake band torque wrench - Ford tool
No 17-005, or a conventional torque wrench
and a splined socket of suitable size to fit the
square section head of the adjuster screw(s)
will be required for this operation.
1For improved access, apply the handbrake,
then jack up the front of the vehicle and
support on axle stands (see “Jacking and
vehicle support”).2The brake band adjuster screw(s) is/are
situated on the left-hand side of the
transmission housing, forward of the
kickdown lever. Note that the C3 type
transmission has a single adjuster screw for
adjustment of the front brake band, whereas
the A4LD type transmission has two adjuster
screws for adjustment of the front and
intermediate brake bands(see illustration).
3Disconnect the kickdown cable from the
kickdown lever on the transmission housing.
4Loosen the locknut on the front brake band
adjuster screw, and back off the adjuster
screw several turns.
5Using the Ford special tool or a suitable
equivalent, tighten the adjuster screw to the
specified torque, then back off the screw two
complete turns, and tighten the locknut.
Ensure that the adjuster screw does not turn
as the locknut is tightened.
6Repeat the procedure given in paragraphs
4 and 5 for the remaining adjuster screw on
A4LD type transmissions, but on all models
where the part number on the transmission
identification tag starts with “88”(see
illustration)and additionally on all 1.8 CVH
engine models, the adjuster screw should be
backed off two and a half turns after
tightening to the specified torque. On all other
models, the adjuster screw should be backed
off two turns.
7Reconnect the kickdown cable, and lower
the vehicle to the ground on completion.
2.0 litre SOHC fuel injection
models
1The fuel filter is located on the left-hand
side of the engine compartment(see
illustration).
2Disconnect the battery negative lead.
3Position a suitable container beneath the
filter, then slowly loosen the fuel inlet union to
relieve the pressure in the fuel lines.
4Disconnect the fuel inlet and outlet unions.
Be prepared for petrol spillage. If necessary,
identify the fuel line unions for use when
refitting.
5Loosen the filter clamp screw, and
withdraw the filter from the clamp. Drain the
petrol from the filter into the container.
Dispose of the filter carefully.
41Fuel filter renewal
40Automatic transmission
brake band adjustment
39Ignition system component
check
1•20Every 24 000 miles or 2 years
38.17 Air intake tube securing nut
(arrowed)
39.6 Bosch distributor cap showing HT
segments (A) and carbon brush (B)40.6 Transmission identification tag with
part number starting with “88”
40.2 Brake band adjustment - A4LD type
transmission
A Adjuster screws
B LocknutsC Kickdown lever
38.19 Lifting out the air cleaner element
Caution: Refer to the
precautions in Chapter 4, Part
B, Section 1 before proceeding.