FORD SIERRA 1983 1.G CVH Engines User Guide
Manufacturer: FORD, Model Year: 1983, Model line: SIERRA, Model: FORD SIERRA 1983 1.GPages: 24, PDF Size: 1.09 MB
Page 11 of 24
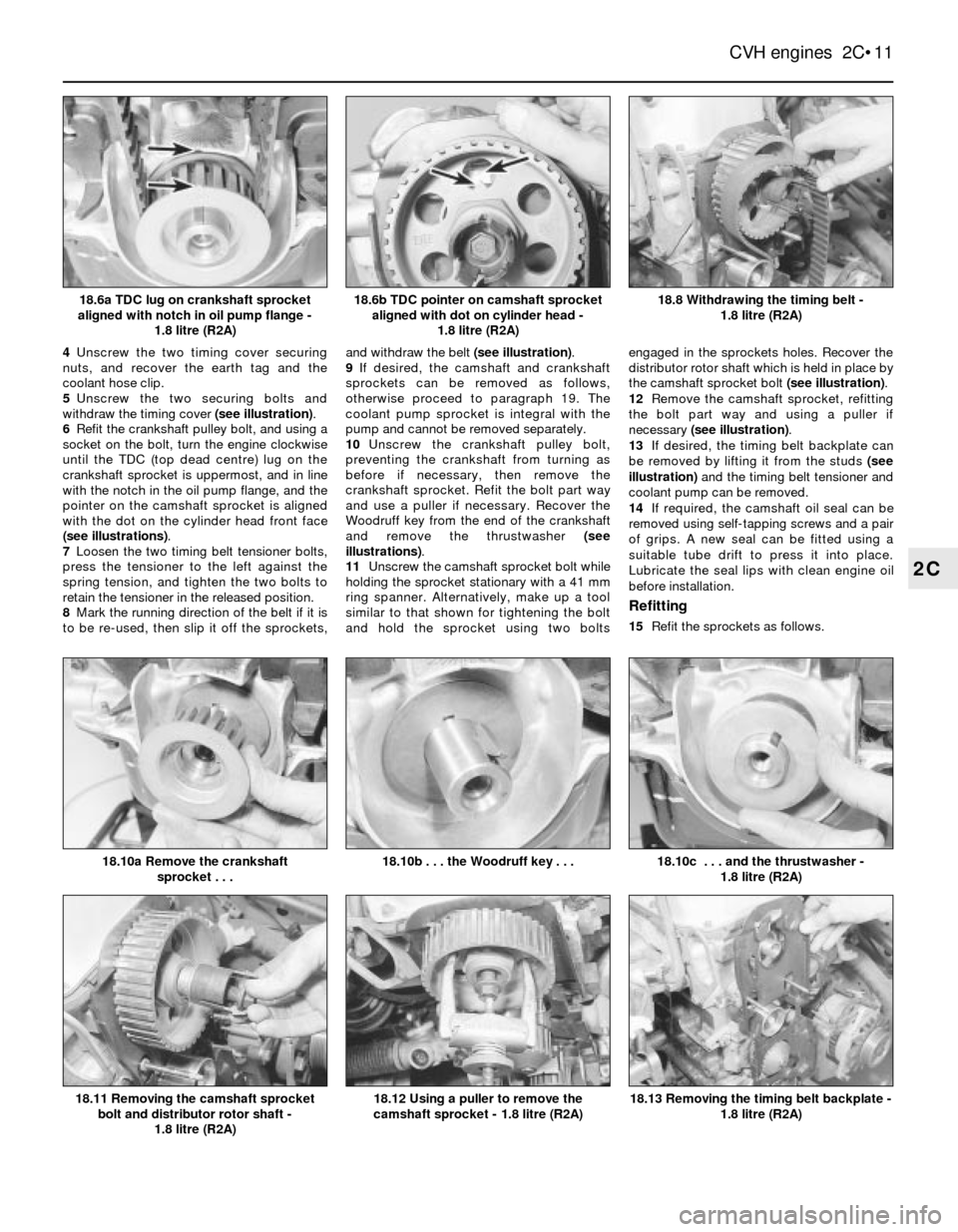
4Unscrew the two timing cover securing
nuts, and recover the earth tag and the
coolant hose clip.
5Unscrew the two securing bolts and
withdraw the timing cover (see illustration).
6Refit the crankshaft pulley bolt, and using a
socket on the bolt, turn the engine clockwise
until the TDC (top dead centre) lug on the
crankshaft sprocket is uppermost, and in line
with the notch in the oil pump flange, and the
pointer on the camshaft sprocket is aligned
with the dot on the cylinder head front face
(see illustrations).
7Loosen the two timing belt tensioner bolts,
press the tensioner to the left against the
spring tension, and tighten the two bolts to
retain the tensioner in the released position.
8Mark the running direction of the belt if it is
to be re-used, then slip it off the sprockets,and withdraw the belt (see illustration).
9If desired, the camshaft and crankshaft
sprockets can be removed as follows,
otherwise proceed to paragraph 19. The
coolant pump sprocket is integral with the
pump and cannot be removed separately.
10Unscrew the crankshaft pulley bolt,
preventing the crankshaft from turning as
before if necessary, then remove the
crankshaft sprocket. Refit the bolt part way
and use a puller if necessary. Recover the
Woodruff key from the end of the crankshaft
and remove the thrustwasher (see
illustrations).
11Unscrew the camshaft sprocket bolt while
holding the sprocket stationary with a 41 mm
ring spanner. Alternatively, make up a tool
similar to that shown for tightening the bolt
and hold the sprocket using two boltsengaged in the sprockets holes. Recover the
distributor rotor shaft which is held in place by
the camshaft sprocket bolt (see illustration).
12Remove the camshaft sprocket, refitting
the bolt part way and using a puller if
necessary (see illustration).
13If desired, the timing belt backplate can
be removed by lifting it from the studs (see
illustration)and the timing belt tensioner and
coolant pump can be removed.
14If required, the camshaft oil seal can be
removed using self-tapping screws and a pair
of grips. A new seal can be fitted using a
suitable tube drift to press it into place.
Lubricate the seal lips with clean engine oil
before installation.
Refitting
15Refit the sprockets as follows.
CVH engines 2C•11
2C
18.8 Withdrawing the timing belt -
1.8 litre (R2A)
18.13 Removing the timing belt backplate -
1.8 litre (R2A)18.12 Using a puller to remove the
camshaft sprocket - 1.8 litre (R2A)18.11 Removing the camshaft sprocket
bolt and distributor rotor shaft -
1.8 litre (R2A)
18.10c . . . and the thrustwasher -
1.8 litre (R2A)18.10b . . . the Woodruff key . . .18.10a Remove the crankshaft
sprocket . . .
18.6b TDC pointer on camshaft sprocket
aligned with dot on cylinder head -
1.8 litre (R2A)18.6a TDC lug on crankshaft sprocket
aligned with notch in oil pump flange -
1.8 litre (R2A)
Page 12 of 24
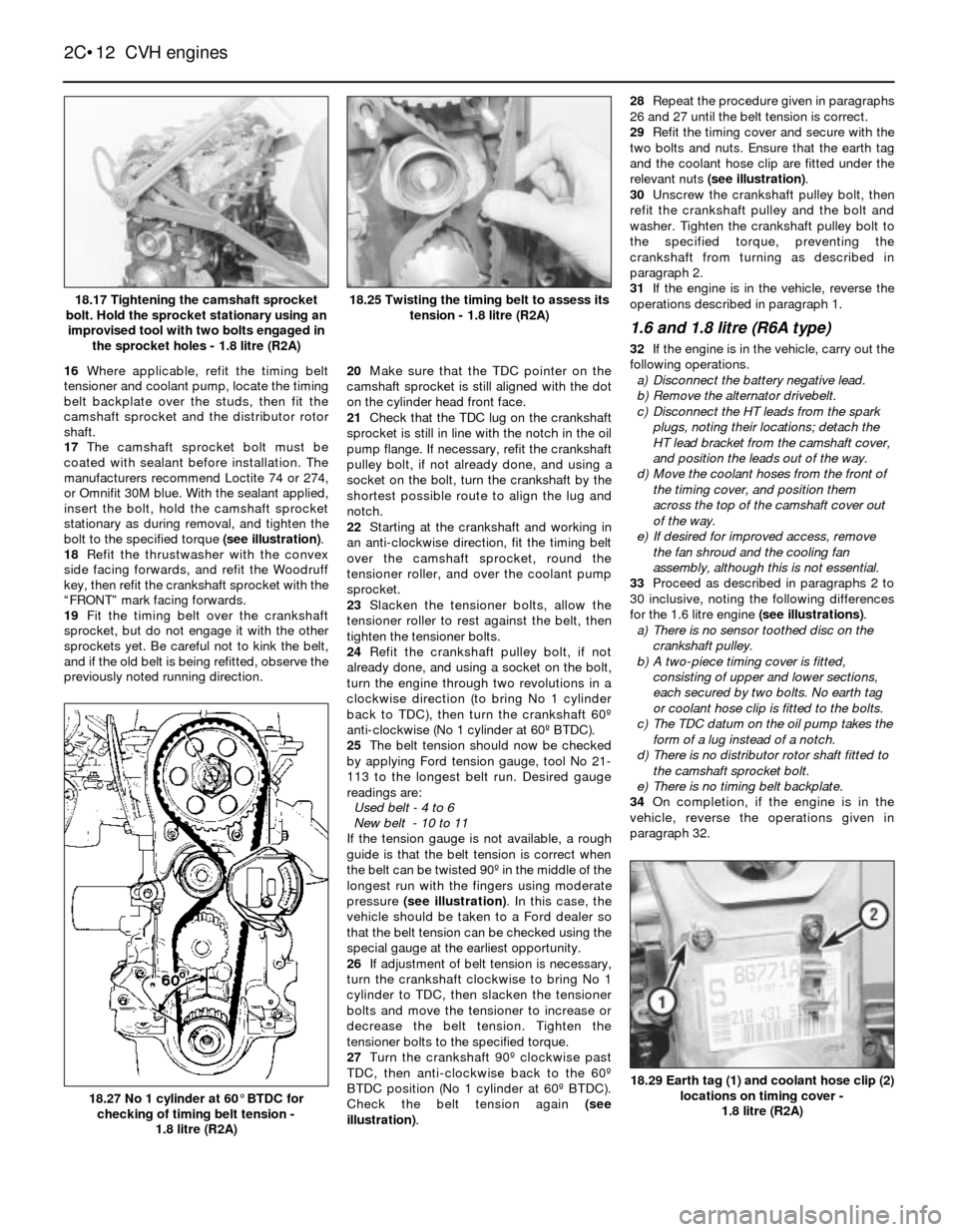
16Where applicable, refit the timing belt
tensioner and coolant pump, locate the timing
belt backplate over the studs, then fit the
camshaft sprocket and the distributor rotor
shaft.
17The camshaft sprocket bolt must be
coated with sealant before installation. The
manufacturers recommend Loctite 74 or 274,
or Omnifit 30M blue. With the sealant applied,
insert the bolt, hold the camshaft sprocket
stationary as during removal, and tighten the
bolt to the specified torque (see illustration).
18Refit the thrustwasher with the convex
side facing forwards, and refit the Woodruff
key, then refit the crankshaft sprocket with the
“FRONT” mark facing forwards.
19Fit the timing belt over the crankshaft
sprocket, but do not engage it with the other
sprockets yet. Be careful not to kink the belt,
and if the old belt is being refitted, observe the
previously noted running direction.20Make sure that the TDC pointer on the
camshaft sprocket is still aligned with the dot
on the cylinder head front face.
21Check that the TDC lug on the crankshaft
sprocket is still in line with the notch in the oil
pump flange. If necessary, refit the crankshaft
pulley bolt, if not already done, and using a
socket on the bolt, turn the crankshaft by the
shortest possible route to align the lug and
notch.
22Starting at the crankshaft and working in
an anti-clockwise direction, fit the timing belt
over the camshaft sprocket, round the
tensioner roller, and over the coolant pump
sprocket.
23Slacken the tensioner bolts, allow the
tensioner roller to rest against the belt, then
tighten the tensioner bolts.
24Refit the crankshaft pulley bolt, if not
already done, and using a socket on the bolt,
turn the engine through two revolutions in a
clockwise direction (to bring No 1 cylinder
back to TDC), then turn the crankshaft 60º
anti-clockwise (No 1 cylinder at 60º BTDC).
25The belt tension should now be checked
by applying Ford tension gauge, tool No 21-
113 to the longest belt run. Desired gauge
readings are:
Used belt - 4 to 6
New belt - 10 to 11
If the tension gauge is not available, a rough
guide is that the belt tension is correct when
the belt can be twisted 90º in the middle of the
longest run with the fingers using moderate
pressure (see illustration). In this case, the
vehicle should be taken to a Ford dealer so
that the belt tension can be checked using the
special gauge at the earliest opportunity.
26If adjustment of belt tension is necessary,
turn the crankshaft clockwise to bring No 1
cylinder to TDC, then slacken the tensioner
bolts and move the tensioner to increase or
decrease the belt tension. Tighten the
tensioner bolts to the specified torque.
27Turn the crankshaft 90º clockwise past
TDC, then anti-clockwise back to the 60º
BTDC position (No 1 cylinder at 60º BTDC).
Check the belt tension again (see
illustration).28Repeat the procedure given in paragraphs
26 and 27 until the belt tension is correct.
29Refit the timing cover and secure with the
two bolts and nuts. Ensure that the earth tag
and the coolant hose clip are fitted under the
relevant nuts (see illustration).
30Unscrew the crankshaft pulley bolt, then
refit the crankshaft pulley and the bolt and
washer. Tighten the crankshaft pulley bolt to
the specified torque, preventing the
crankshaft from turning as described in
paragraph 2.
31If the engine is in the vehicle, reverse the
operations described in paragraph 1.
1.6 and 1.8 litre (R6A type)
32If the engine is in the vehicle, carry out the
following operations.
a)Disconnect the battery negative lead.
b)Remove the alternator drivebelt.
c)Disconnect the HT leads from the spark
plugs, noting their locations; detach the
HT lead bracket from the camshaft cover,
and position the leads out of the way.
d)Move the coolant hoses from the front of
the timing cover, and position them
across the top of the camshaft cover out
of the way.
e)If desired for improved access, remove
the fan shroud and the cooling fan
assembly, although this is not essential.
33Proceed as described in paragraphs 2 to
30 inclusive, noting the following differences
for the 1.6 litre engine (see illustrations).
a)There is no sensor toothed disc on the
crankshaft pulley.
b)A two-piece timing cover is fitted,
consisting of upper and lower sections,
each secured by two bolts. No earth tag
or coolant hose clip is fitted to the bolts.
c)The TDC datum on the oil pump takes the
form of a lug instead of a notch.
d)There is no distributor rotor shaft fitted to
the camshaft sprocket bolt.
e)There is no timing belt backplate.
34On completion, if the engine is in the
vehicle, reverse the operations given in
paragraph 32.
2C•12CVH engines
18.17 Tightening the camshaft sprocket
bolt. Hold the sprocket stationary using an
improvised tool with two bolts engaged in
the sprocket holes - 1.8 litre (R2A)
18.27 No 1 cylinder at 60°BTDC for
checking of timing belt tension -
1.8 litre (R2A)
18.29 Earth tag (1) and coolant hose clip (2)
locations on timing cover -
1.8 litre (R2A)
18.25 Twisting the timing belt to assess its
tension - 1.8 litre (R2A)
Page 13 of 24
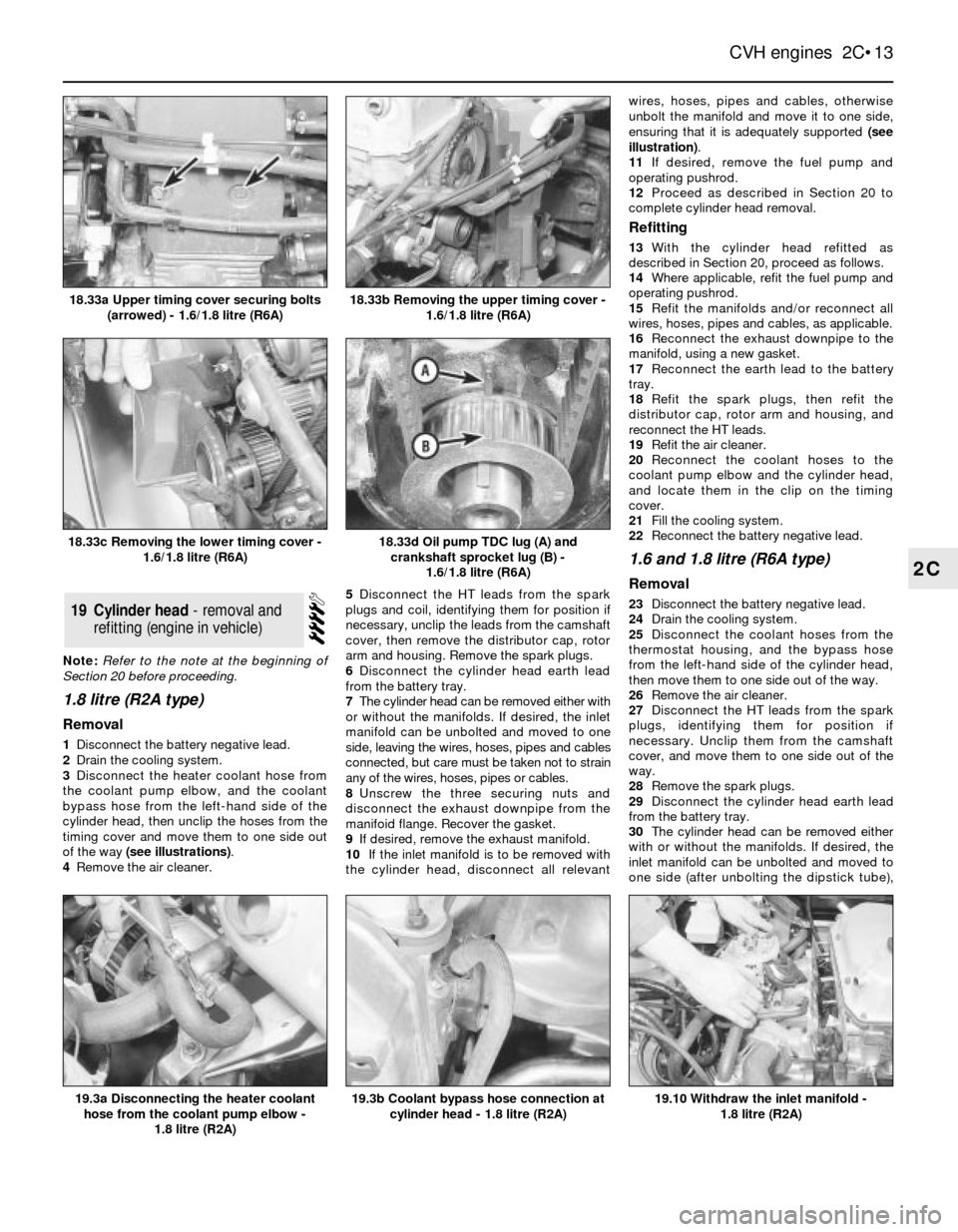
Note: Refer to the note at the beginning of
Section 20 before proceeding.
1.8 litre (R2A type)
Removal
1Disconnect the battery negative lead.
2Drain the cooling system.
3Disconnect the heater coolant hose from
the coolant pump elbow, and the coolant
bypass hose from the left-hand side of the
cylinder head, then unclip the hoses from the
timing cover and move them to one side out
of the way (see illustrations).
4Remove the air cleaner.5Disconnect the HT leads from the spark
plugs and coil, identifying them for position if
necessary, unclip the leads from the camshaft
cover, then remove the distributor cap, rotor
arm and housing. Remove the spark plugs.
6Disconnect the cylinder head earth lead
from the battery tray.
7The cylinder head can be removed either with
or without the manifolds. If desired, the inlet
manifold can be unbolted and moved to one
side, leaving the wires, hoses, pipes and cables
connected, but care must be taken not to strain
any of the wires, hoses, pipes or cables.
8Unscrew the three securing nuts and
disconnect the exhaust downpipe from the
manifoid flange. Recover the gasket.
9If desired, remove the exhaust manifold.
10If the inlet manifold is to be removed with
the cylinder head, disconnect all relevantwires, hoses, pipes and cables, otherwise
unbolt the manifold and move it to one side,
ensuring that it is adequately supported (see
illustration).
11If desired, remove the fuel pump and
operating pushrod.
12Proceed as described in Section 20 to
complete cylinder head removal.
Refitting
13With the cylinder head refitted as
described in Section 20, proceed as follows.
14Where applicable, refit the fuel pump and
operating pushrod.
15Refit the manifolds and/or reconnect all
wires, hoses, pipes and cables, as applicable.
16Reconnect the exhaust downpipe to the
manifold, using a new gasket.
17Reconnect the earth lead to the battery
tray.
18Refit the spark plugs, then refit the
distributor cap, rotor arm and housing, and
reconnect the HT leads.
19Refit the air cleaner.
20Reconnect the coolant hoses to the
coolant pump elbow and the cylinder head,
and locate them in the clip on the timing
cover.
21Fill the cooling system.
22Reconnect the battery negative lead.
1.6 and 1.8 litre (R6A type)
Removal
23Disconnect the battery negative lead.
24Drain the cooling system.
25Disconnect the coolant hoses from the
thermostat housing, and the bypass hose
from the left-hand side of the cylinder head,
then move them to one side out of the way.
26Remove the air cleaner.
27Disconnect the HT leads from the spark
plugs, identifying them for position if
necessary. Unclip them from the camshaft
cover, and move them to one side out of the
way.
28Remove the spark plugs.
29Disconnect the cylinder head earth lead
from the battery tray.
30The cylinder head can be removed either
with or without the manifolds. If desired, the
inlet manifold can be unbolted and moved to
one side (after unbolting the dipstick tube),19Cylinder head - removal and
refitting (engine in vehicle)
CVH engines 2C•13
2C
19.10 Withdraw the inlet manifold -
1.8 litre (R2A)19.3b Coolant bypass hose connection at
cylinder head - 1.8 litre (R2A)19.3a Disconnecting the heater coolant
hose from the coolant pump elbow -
1.8 litre (R2A)
18.33d Oil pump TDC lug (A) and
crankshaft sprocket lug (B) -
1.6/1.8 litre (R6A)18.33c Removing the lower timing cover -
1.6/1.8 litre (R6A)
18.33b Removing the upper timing cover -
1.6/1.8 litre (R6A)18.33a Upper timing cover securing bolts
(arrowed) - 1.6/1.8 litre (R6A)
Page 14 of 24
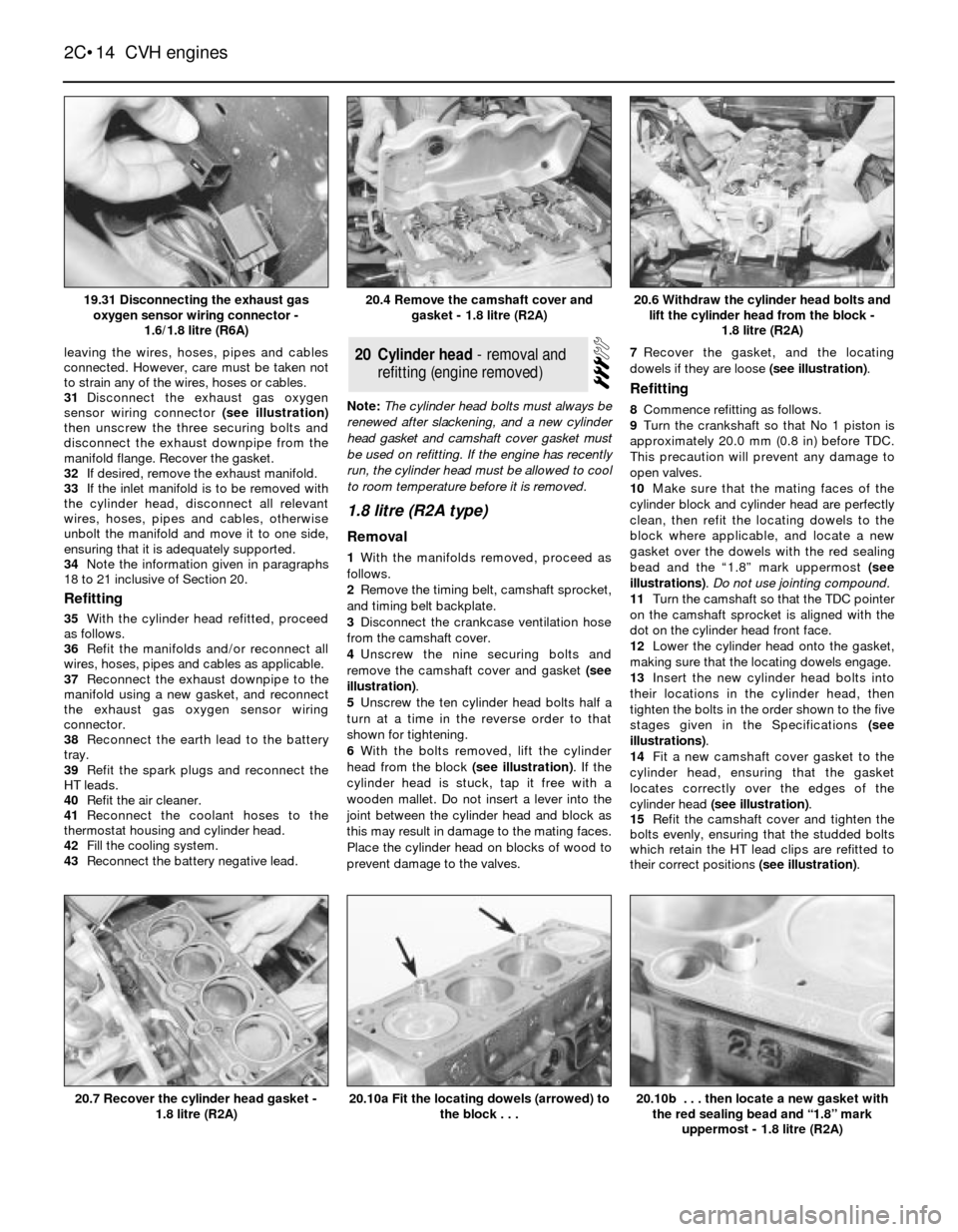
leaving the wires, hoses, pipes and cables
connected. However, care must be taken not
to strain any of the wires, hoses or cables.
31Disconnect the exhaust gas oxygen
sensor wiring connector (see illustration)
then unscrew the three securing bolts and
disconnect the exhaust downpipe from the
manifold flange. Recover the gasket.
32If desired, remove the exhaust manifold.
33If the inlet manifold is to be removed with
the cylinder head, disconnect all relevant
wires, hoses, pipes and cables, otherwise
unbolt the manifold and move it to one side,
ensuring that it is adequately supported.
34Note the information given in paragraphs
18 to 21 inclusive of Section 20.
Refitting
35With the cylinder head refitted, proceed
as follows.
36Refit the manifolds and/or reconnect all
wires, hoses, pipes and cables as applicable.
37Reconnect the exhaust downpipe to the
manifold using a new gasket, and reconnect
the exhaust gas oxygen sensor wiring
connector.
38Reconnect the earth lead to the battery
tray.
39Refit the spark plugs and reconnect the
HT leads.
40Refit the air cleaner.
41Reconnect the coolant hoses to the
thermostat housing and cylinder head.
42Fill the cooling system.
43Reconnect the battery negative lead.Note: The cylinder head bolts must always be
renewed after slackening, and a new cylinder
head gasket and camshaft cover gasket must
be used on refitting. If the engine has recently
run, the cylinder head must be allowed to cool
to room temperature before it is removed.
1.8 litre (R2A type)
Removal
1With the manifolds removed, proceed as
follows.
2Remove the timing belt, camshaft sprocket,
and timing belt backplate.
3Disconnect the crankcase ventilation hose
from the camshaft cover.
4Unscrew the nine securing bolts and
remove the camshaft cover and gasket (see
illustration).
5Unscrew the ten cylinder head bolts half a
turn at a time in the reverse order to that
shown for tightening.
6With the bolts removed, lift the cylinder
head from the block (see illustration). If the
cylinder head is stuck, tap it free with a
wooden mallet. Do not insert a lever into the
joint between the cylinder head and block as
this may result in damage to the mating faces.
Place the cylinder head on blocks of wood to
prevent damage to the valves.7Recover the gasket, and the locating
dowels if they are loose (see illustration).
Refitting
8Commence refitting as follows.
9Turn the crankshaft so that No 1 piston is
approximately 20.0 mm (0.8 in) before TDC.
This precaution will prevent any damage to
open valves.
10Make sure that the mating faces of the
cylinder block and cylinder head are perfectly
clean, then refit the locating dowels to the
block where applicable, and locate a new
gasket over the dowels with the red sealing
bead and the “1.8” mark uppermost (see
illustrations). Do not use jointing compound.
11Turn the camshaft so that the TDC pointer
on the camshaft sprocket is aligned with the
dot on the cylinder head front face.
12Lower the cylinder head onto the gasket,
making sure that the locating dowels engage.
13Insert the new cylinder head bolts into
their locations in the cylinder head, then
tighten the bolts in the order shown to the five
stages given in the Specifications (see
illustrations).
14Fit a new camshaft cover gasket to the
cylinder head, ensuring that the gasket
locates correctly over the edges of the
cylinder head (see illustration).
15Refit the camshaft cover and tighten the
bolts evenly, ensuring that the studded bolts
which retain the HT lead clips are refitted to
their correct positions (see illustration).
20Cylinder head - removal and
refitting (engine removed)
2C•14CVH engines
19.31 Disconnecting the exhaust gas
oxygen sensor wiring connector -
1.6/1.8 litre (R6A)20.6 Withdraw the cylinder head bolts and
lift the cylinder head from the block -
1.8 litre (R2A)
20.10b . . . then locate a new gasket with
the red sealing bead and “1.8” mark
uppermost - 1.8 litre (R2A)20.10a Fit the locating dowels (arrowed) to
the block . . .20.7 Recover the cylinder head gasket -
1.8 litre (R2A)
20.4 Remove the camshaft cover and
gasket - 1.8 litre (R2A)
Page 15 of 24
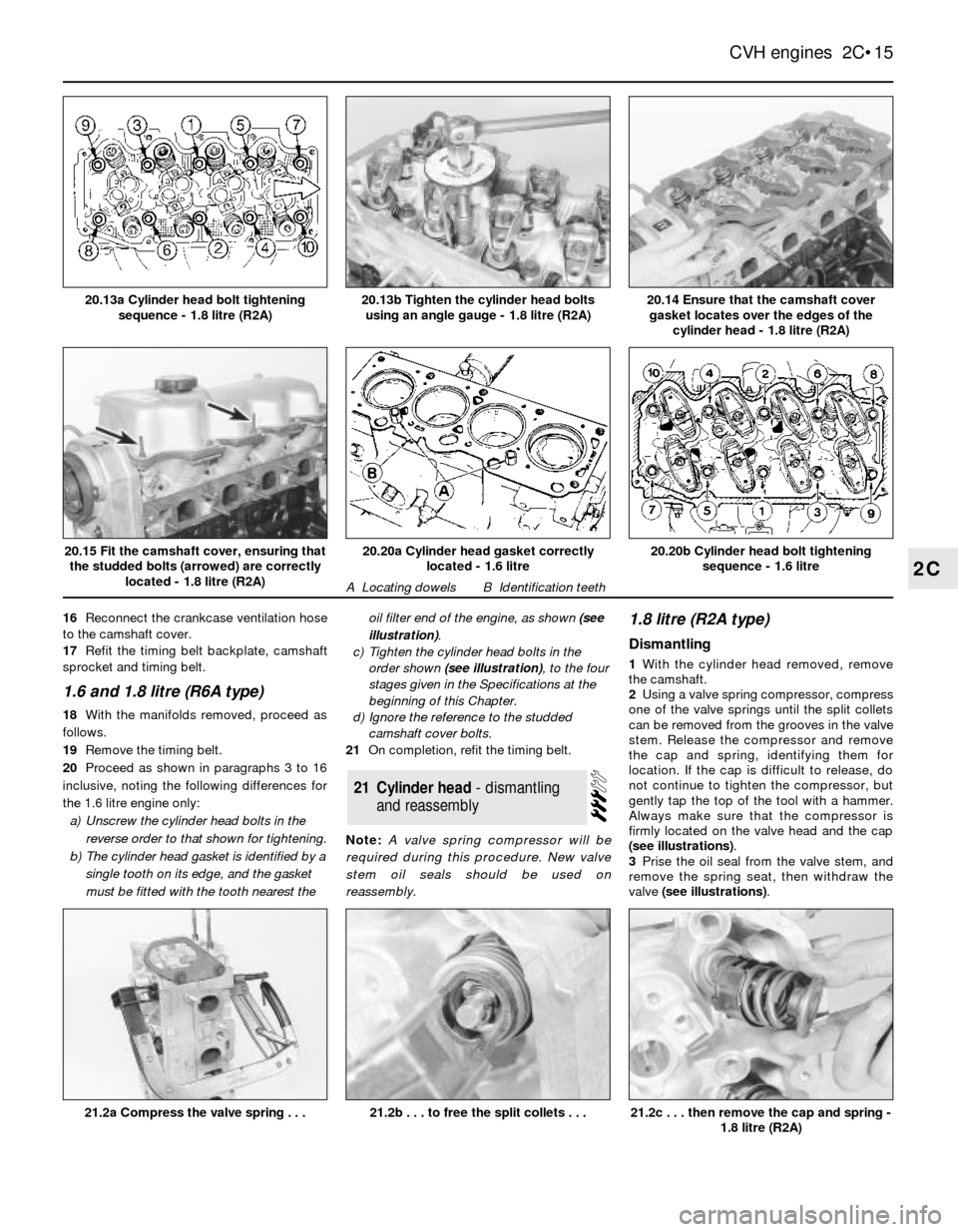
16Reconnect the crankcase ventilation hose
to the camshaft cover.
17Refit the timing belt backplate, camshaft
sprocket and timing belt.
1.6 and 1.8 litre (R6A type)
18With the manifolds removed, proceed as
follows.
19Remove the timing belt.
20Proceed as shown in paragraphs 3 to 16
inclusive, noting the following differences for
the 1.6 litre engine only:
a)Unscrew the cylinder head bolts in the
reverse order to that shown for tightening.
b)The cylinder head gasket is identified by a
single tooth on its edge, and the gasket
must be fitted with the tooth nearest theoil filter end of the engine, as shown (see
illustration).
c)Tighten the cylinder head bolts in the
order shown (see illustration), to the four
stages given in the Specifications at the
beginning of this Chapter.
d)Ignore the reference to the studded
camshaft cover bolts.
21On completion, refit the timing belt.
Note: A valve spring compressor will be
required during this procedure. New valve
stem oil seals should be used on
reassembly.
1.8 litre (R2A type)
Dismantling
1With the cylinder head removed, remove
the camshaft.
2Using a valve spring compressor, compress
one of the valve springs until the split collets
can be removed from the grooves in the valve
stem. Release the compressor and remove
the cap and spring, identifying them for
location. If the cap is difficult to release, do
not continue to tighten the compressor, but
gently tap the top of the tool with a hammer.
Always make sure that the compressor is
firmly located on the valve head and the cap
(see illustrations).
3Prise the oil seal from the valve stem, and
remove the spring seat, then withdraw the
valve (see illustrations).
21Cylinder head - dismantling
and reassembly
CVH engines 2C•15
2C
20.14 Ensure that the camshaft cover
gasket locates over the edges of the
cylinder head - 1.8 litre (R2A)
21.2c . . . then remove the cap and spring -
1.8 litre (R2A)21.2b . . . to free the split collets . . .
20.20b Cylinder head bolt tightening
sequence - 1.6 litre20.20a Cylinder head gasket correctly
located - 1.6 litre
A Locating dowelsB Identification teeth
21.2a Compress the valve spring . . .
20.13b Tighten the cylinder head bolts
using an angle gauge - 1.8 litre (R2A)20.13a Cylinder head bolt tightening
sequence - 1.8 litre (R2A)
20.15 Fit the camshaft cover, ensuring that
the studded bolts (arrowed) are correctly
located - 1.8 litre (R2A)
Page 16 of 24
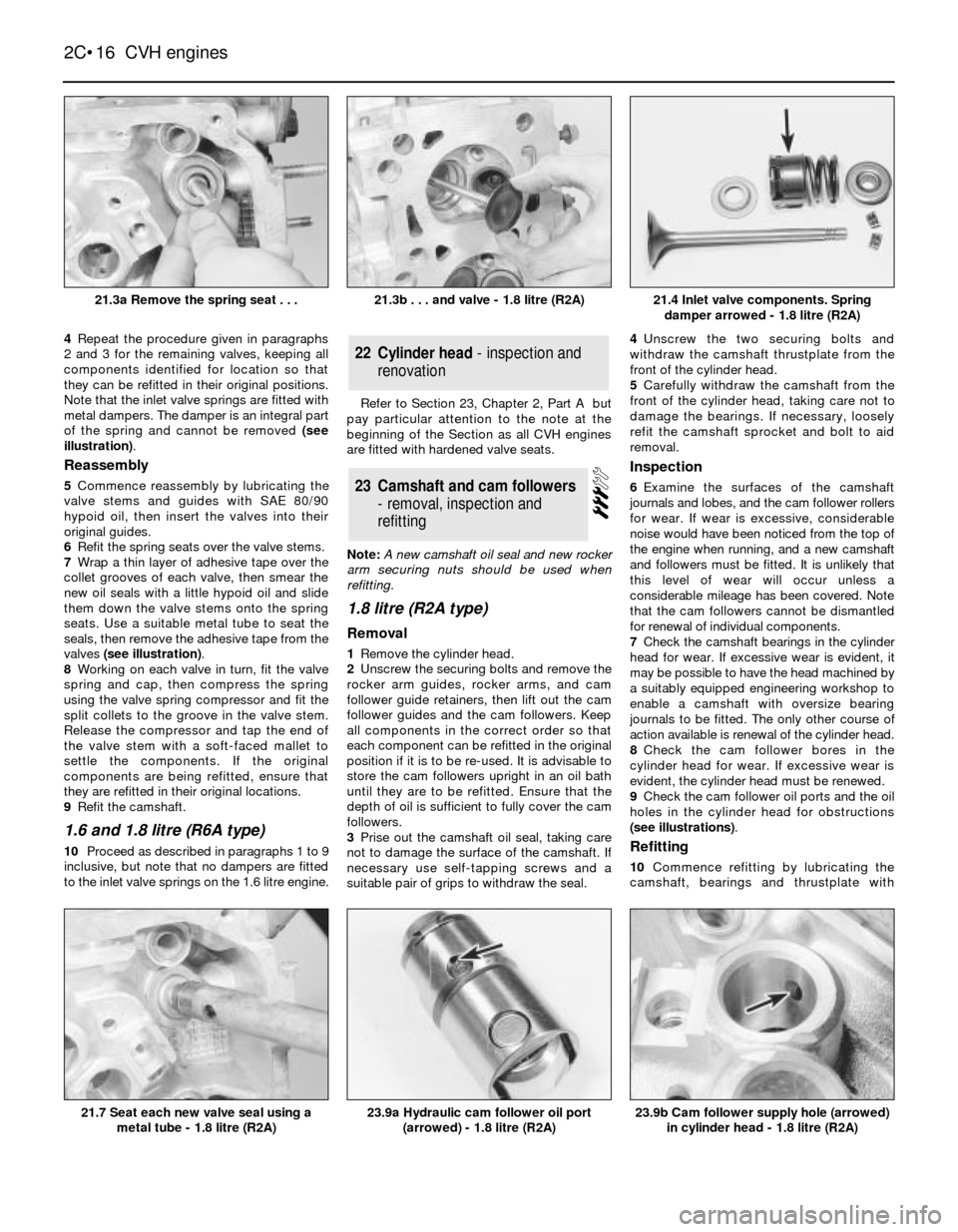
4Repeat the procedure given in paragraphs
2 and 3 for the remaining valves, keeping all
components identified for location so that
they can be refitted in their original positions.
Note that the inlet valve springs are fitted with
metal dampers. The damper is an integral part
of the spring and cannot be removed (see
illustration).
Reassembly
5Commence reassembly by lubricating the
valve stems and guides with SAE 80/90
hypoid oil, then insert the valves into their
original guides.
6Refit the spring seats over the valve stems.
7Wrap a thin layer of adhesive tape over the
collet grooves of each valve, then smear the
new oil seals with a little hypoid oil and slide
them down the valve stems onto the spring
seats. Use a suitable metal tube to seat the
seals, then remove the adhesive tape from the
valves (see illustration).
8Working on each valve in turn, fit the valve
spring and cap, then compress the spring
using the valve spring compressor and fit the
split collets to the groove in the valve stem.
Release the compressor and tap the end of
the valve stem with a soft-faced mallet to
settle the components. If the original
components are being refitted, ensure that
they are refitted in their original locations.
9Refit the camshaft.
1.6 and 1.8 litre (R6A type)
10Proceed as described in paragraphs 1 to 9
inclusive, but note that no dampers are fitted
to the inlet valve springs on the 1.6 litre engine.Refer to Section 23, Chapter 2, Part A but
pay particular attention to the note at the
beginning of the Section as all CVH engines
are fitted with hardened valve seats.
Note: A new camshaft oil seal and new rocker
arm securing nuts should be used when
refitting.
1.8 litre (R2A type)
Removal
1Remove the cylinder head.
2Unscrew the securing bolts and remove the
rocker arm guides, rocker arms, and cam
follower guide retainers, then lift out the cam
follower guides and the cam followers. Keep
all components in the correct order so that
each component can be refitted in the original
position if it is to be re-used. It is advisable to
store the cam followers upright in an oil bath
until they are to be refitted. Ensure that the
depth of oil is sufficient to fully cover the cam
followers.
3Prise out the camshaft oil seal, taking care
not to damage the surface of the camshaft. If
necessary use self-tapping screws and a
suitable pair of grips to withdraw the seal.4Unscrew the two securing bolts and
withdraw the camshaft thrustplate from the
front of the cylinder head.
5Carefully withdraw the camshaft from the
front of the cylinder head, taking care not to
damage the bearings. If necessary, loosely
refit the camshaft sprocket and bolt to aid
removal.
Inspection
6Examine the surfaces of the camshaft
journals and lobes, and the cam follower rollers
for wear. If wear is excessive, considerable
noise would have been noticed from the top of
the engine when running, and a new camshaft
and followers must be fitted. It is unlikely that
this level of wear will occur unless a
considerable mileage has been covered. Note
that the cam followers cannot be dismantled
for renewal of individual components.
7Check the camshaft bearings in the cylinder
head for wear. If excessive wear is evident, it
may be possible to have the head machined by
a suitably equipped engineering workshop to
enable a camshaft with oversize bearing
journals to be fitted. The only other course of
action available is renewal of the cylinder head.
8Check the cam follower bores in the
cylinder head for wear. If excessive wear is
evident, the cylinder head must be renewed.
9Check the cam follower oil ports and the oil
holes in the cylinder head for obstructions
(see illustrations).
Refitting
10Commence refitting by lubricating the
camshaft, bearings and thrustplate with
23Camshaft and cam followers
- removal, inspection and
refitting
22Cylinder head - inspection and
renovation
2C•16CVH engines
21.3a Remove the spring seat . . .21.4 Inlet valve components. Spring
damper arrowed - 1.8 litre (R2A)
23.9b Cam follower supply hole (arrowed)
in cylinder head - 1.8 litre (R2A)23.9a Hydraulic cam follower oil port
(arrowed) - 1.8 litre (R2A)21.7 Seat each new valve seal using a
metal tube - 1.8 litre (R2A)
21.3b . . . and valve - 1.8 litre (R2A)
Page 17 of 24
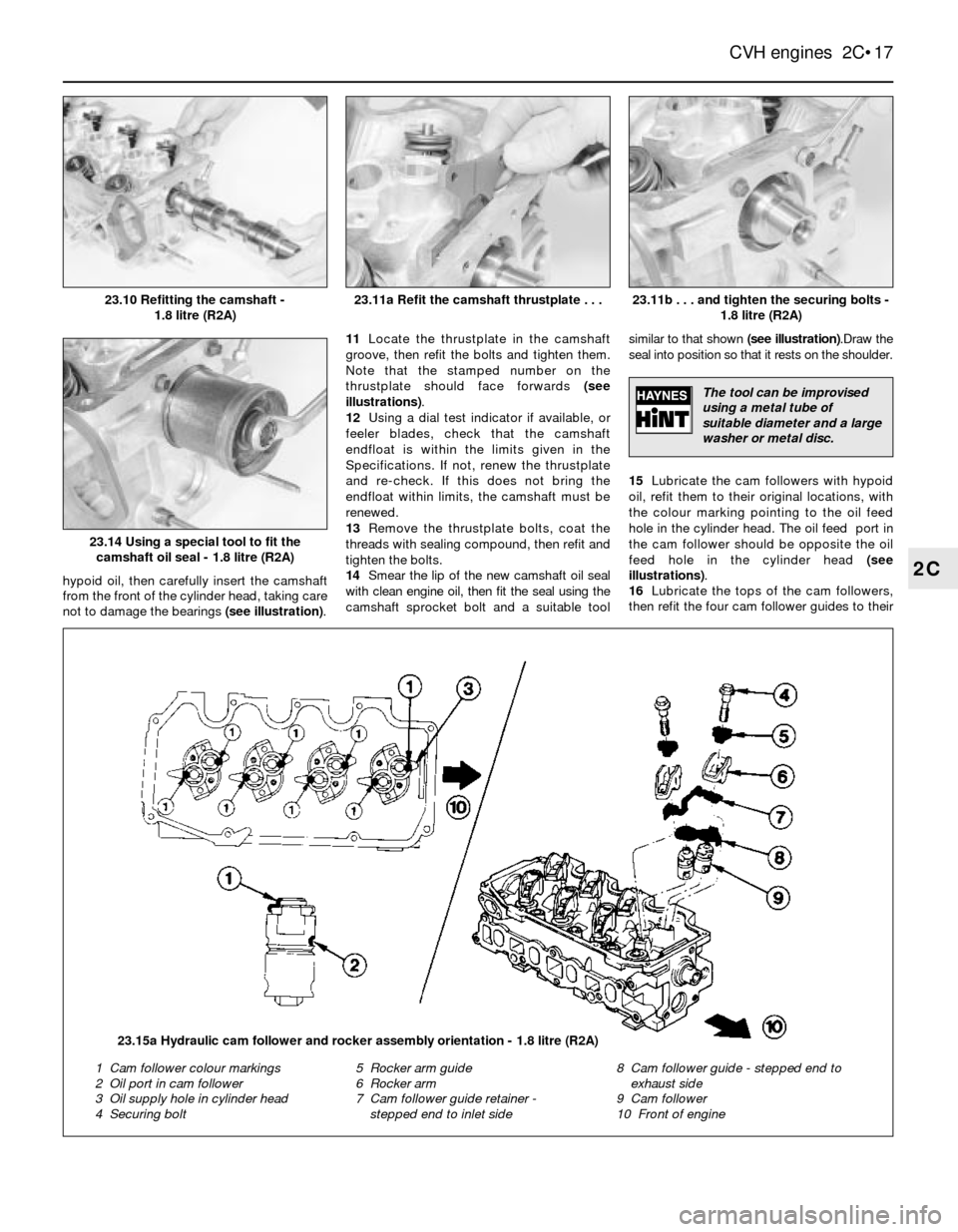
hypoid oil, then carefully insert the camshaft
from the front of the cylinder head, taking care
not to damage the bearings (see illustration).11Locate the thrustplate in the camshaft
groove, then refit the bolts and tighten them.
Note that the stamped number on the
thrustplate should face forwards (see
illustrations).
12Using a dial test indicator if available, or
feeler blades, check that the camshaft
endfloat is within the limits given in the
Specifications. If not, renew the thrustplate
and re-check. If this does not bring the
endfloat within limits, the camshaft must be
renewed.
13Remove the thrustplate bolts, coat the
threads with sealing compound, then refit and
tighten the bolts.
14Smear the lip of the new camshaft oil seal
with clean engine oil, then fit the seal using the
camshaft sprocket bolt and a suitable toolsimilar to that shown (see illustration).Draw the
seal into position so that it rests on the shoulder.
15Lubricate the cam followers with hypoid
oil, refit them to their original locations, with
the colour marking pointing to the oil feed
hole in the cylinder head. The oil feed port in
the cam follower should be opposite the oil
feed hole in the cylinder head (see
illustrations).
16Lubricate the tops of the cam followers,
then refit the four cam follower guides to their
CVH engines 2C•17
2C
23.11b . . . and tighten the securing bolts -
1.8 litre (R2A)
23.14 Using a special tool to fit the
camshaft oil seal - 1.8 litre (R2A)
23.11a Refit the camshaft thrustplate . . .23.10 Refitting the camshaft -
1.8 litre (R2A)
23.15a Hydraulic cam follower and rocker assembly orientation - 1.8 litre (R2A)
1 Cam follower colour markings
2 Oil port in cam follower
3 Oil supply hole in cylinder head
4 Securing bolt5 Rocker arm guide
6 Rocker arm
7 Cam follower guide retainer -
stepped end to inlet side8 Cam follower guide - stepped end to
exhaust side
9 Cam follower
10 Front of engine
The tool can be improvised
using a metal tube of
suitable diameter and a large
washer or metal disc.
Page 18 of 24
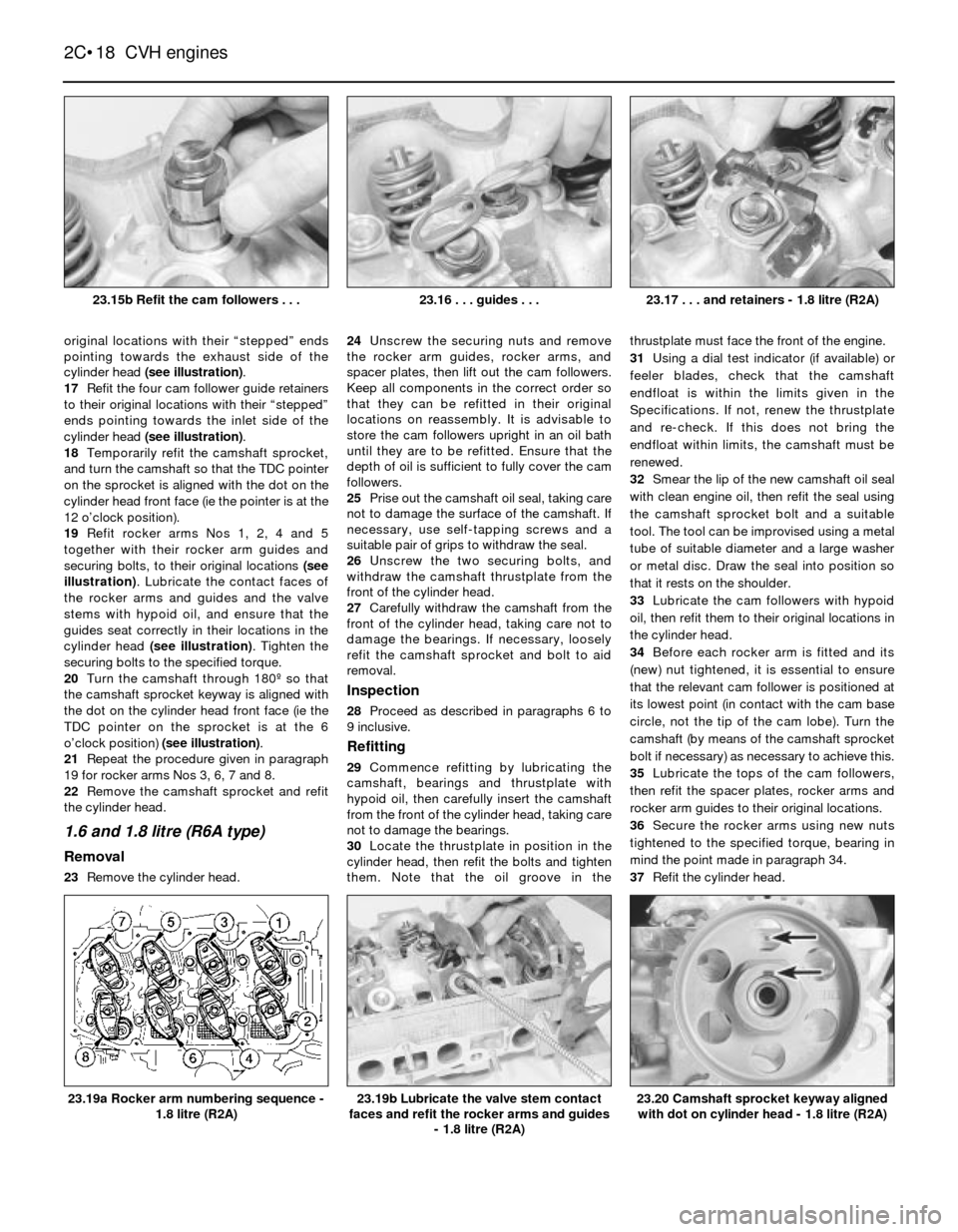
original locations with their “stepped” ends
pointing towards the exhaust side of the
cylinder head (see illustration).
17Refit the four cam follower guide retainers
to their original locations with their “stepped”
ends pointing towards the inlet side of the
cylinder head (see illustration).
18Temporarily refit the camshaft sprocket,
and turn the camshaft so that the TDC pointer
on the sprocket is aligned with the dot on the
cylinder head front face (ie the pointer is at the
12 o’clock position).
19Refit rocker arms Nos 1, 2, 4 and 5
together with their rocker arm guides and
securing bolts, to their original locations (see
illustration). Lubricate the contact faces of
the rocker arms and guides and the valve
stems with hypoid oil, and ensure that the
guides seat correctly in their locations in the
cylinder head (see illustration). Tighten the
securing bolts to the specified torque.
20Turn the camshaft through 180º so that
the camshaft sprocket keyway is aligned with
the dot on the cylinder head front face (ie the
TDC pointer on the sprocket is at the 6
o’clock position) (see illustration).
21Repeat the procedure given in paragraph
19 for rocker arms Nos 3, 6, 7 and 8.
22Remove the camshaft sprocket and refit
the cylinder head.
1.6 and 1.8 litre (R6A type)
Removal
23Remove the cylinder head. 24Unscrew the securing nuts and remove
the rocker arm guides, rocker arms, and
spacer plates, then lift out the cam followers.
Keep all components in the correct order so
that they can be refitted in their original
locations on reassembly. It is advisable to
store the cam followers upright in an oil bath
until they are to be refitted. Ensure that the
depth of oil is sufficient to fully cover the cam
followers.
25Prise out the camshaft oil seal, taking care
not to damage the surface of the camshaft. If
necessary, use self-tapping screws and a
suitable pair of grips to withdraw the seal.
26Unscrew the two securing bolts, and
withdraw the camshaft thrustplate from the
front of the cylinder head.
27Carefully withdraw the camshaft from the
front of the cylinder head, taking care not to
damage the bearings. If necessary, loosely
refit the camshaft sprocket and bolt to aid
removal.
Inspection
28Proceed as described in paragraphs 6 to
9 inclusive.
Refitting
29Commence refitting by lubricating the
camshaft, bearings and thrustplate with
hypoid oil, then carefully insert the camshaft
from the front of the cylinder head, taking care
not to damage the bearings.
30Locate the thrustplate in position in the
cylinder head, then refit the bolts and tighten
them. Note that the oil groove in thethrustplate must face the front of the engine.
31Using a dial test indicator (if available) or
feeler blades, check that the camshaft
endfloat is within the limits given in the
Specifications. If not, renew the thrustplate
and re-check. If this does not bring the
endfloat within limits, the camshaft must be
renewed.
32Smear the lip of the new camshaft oil seal
with clean engine oil, then refit the seal using
the camshaft sprocket bolt and a suitable
tool. The tool can be improvised using a metal
tube of suitable diameter and a large washer
or metal disc. Draw the seal into position so
that it rests on the shoulder.
33Lubricate the cam followers with hypoid
oil, then refit them to their original locations in
the cylinder head.
34Before each rocker arm is fitted and its
(new) nut tightened, it is essential to ensure
that the relevant cam follower is positioned at
its lowest point (in contact with the cam base
circle, not the tip of the cam lobe). Turn the
camshaft (by means of the camshaft sprocket
bolt if necessary) as necessary to achieve this.
35Lubricate the tops of the cam followers,
then refit the spacer plates, rocker arms and
rocker arm guides to their original locations.
36Secure the rocker arms using new nuts
tightened to the specified torque, bearing in
mind the point made in paragraph 34.
37Refit the cylinder head.
2C•18CVH engines
23.17 . . . and retainers - 1.8 litre (R2A)
23.20 Camshaft sprocket keyway aligned
with dot on cylinder head - 1.8 litre (R2A)23.19b Lubricate the valve stem contact
faces and refit the rocker arms and guides
- 1.8 litre (R2A)23.19a Rocker arm numbering sequence -
1.8 litre (R2A)
23.16 . . . guides . . .23.15b Refit the cam followers . . .
Page 19 of 24
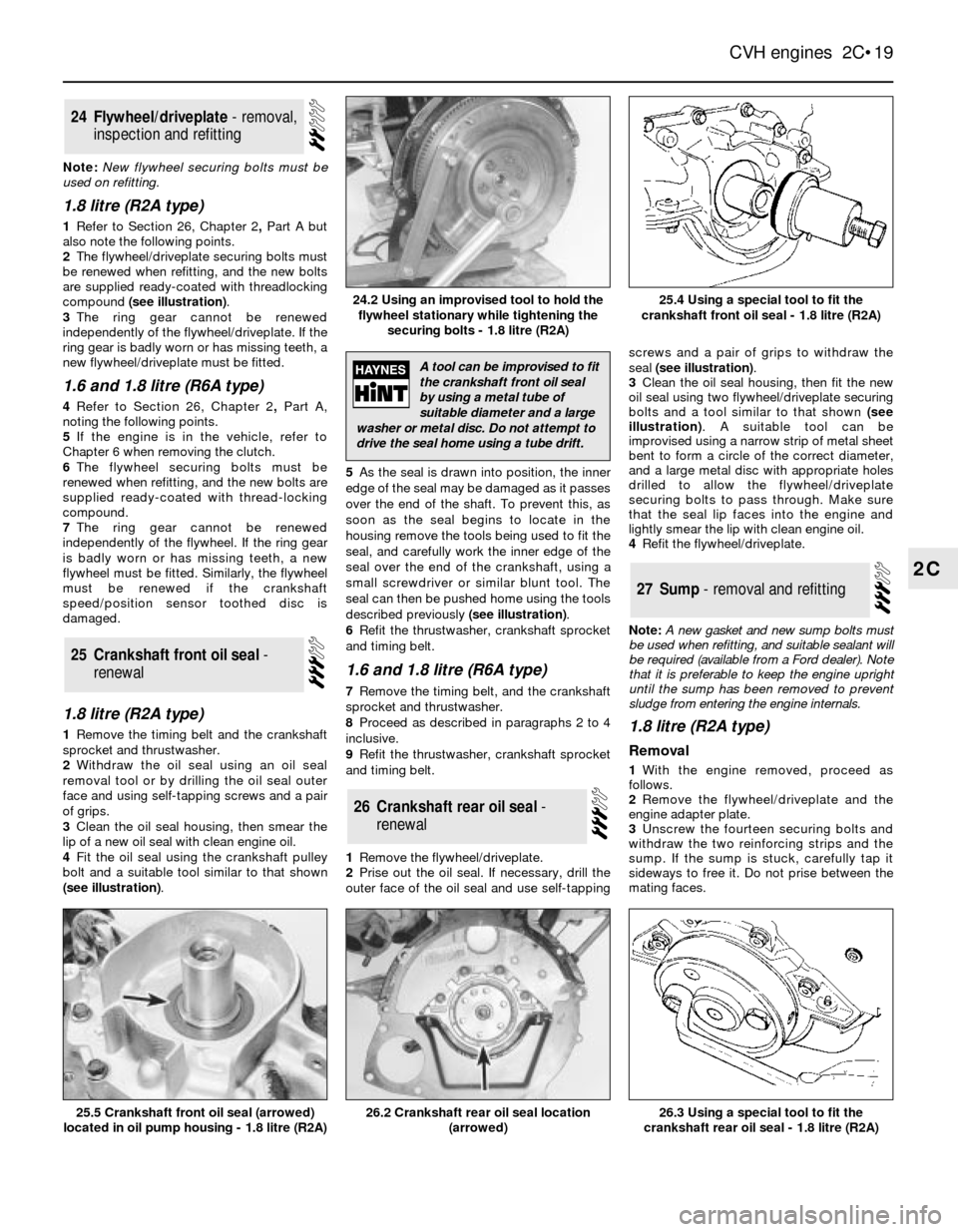
Note: New flywheel securing bolts must be
used on refitting.
1.8 litre (R2A type)
1Refer to Section 26, Chapter 2, PartA but
also note the following points.
2The flywheel/driveplate securing bolts must
be renewed when refitting, and the new bolts
are supplied ready-coated with threadlocking
compound (see illustration).
3The ring gear cannot be renewed
independently of the flywheel/driveplate. If the
ring gear is badly worn or has missing teeth, a
new flywheel/driveplate must be fitted.
1.6 and 1.8 litre (R6A type)
4Refer to Section 26, Chapter 2, PartA,
noting the following points.
5If the engine is in the vehicle, refer to
Chapter 6 when removing the clutch.
6The flywheel securing bolts must be
renewed when refitting, and the new bolts are
supplied ready-coated with thread-locking
compound.
7The ring gear cannot be renewed
independently of the flywheel. If the ring gear
is badly worn or has missing teeth, a new
flywheel must be fitted. Similarly, the flywheel
must be renewed if the crankshaft
speed/position sensor toothed disc is
damaged.
1.8 litre (R2A type)
1Remove the timing belt and the crankshaft
sprocket and thrustwasher.
2Withdraw the oil seal using an oil seal
removal tool or by drilling the oil seal outer
face and using self-tapping screws and a pair
of grips.
3Clean the oil seal housing, then smear the
lip of a new oil seal with clean engine oil.
4Fit the oil seal using the crankshaft pulley
bolt and a suitable tool similar to that shown
(see illustration).5As the seal is drawn into position, the inner
edge of the seal may be damaged as it passes
over the end of the shaft. To prevent this, as
soon as the seal begins to locate in the
housing remove the tools being used to fit the
seal, and carefully work the inner edge of the
seal over the end of the crankshaft, using a
small screwdriver or similar blunt tool. The
seal can then be pushed home using the tools
described previously (see illustration).
6Refit the thrustwasher, crankshaft sprocket
and timing belt.
1.6 and 1.8 litre (R6A type)
7Remove the timing belt, and the crankshaft
sprocket and thrustwasher.
8Proceed as described in paragraphs 2 to 4
inclusive.
9Refit the thrustwasher, crankshaft sprocket
and timing belt.
1Remove the flywheel/driveplate.
2Prise out the oil seal. If necessary, drill the
outer face of the oil seal and use self-tappingscrews and a pair of grips to withdraw the
seal (see illustration).
3Clean the oil seal housing, then fit the new
oil seal using two flywheel/driveplate securing
bolts and a tool similar to that shown (see
illustration). A suitable tool can be
improvised using a narrow strip of metal sheet
bent to form a circle of the correct diameter,
and a large metal disc with appropriate holes
drilled to allow the flywheel/driveplate
securing bolts to pass through. Make sure
that the seal lip faces into the engine and
lightly smear the lip with clean engine oil.
4Refit the flywheel/driveplate.
Note: A new gasket and new sump bolts must
be used when refitting, and suitable sealant will
be required (available from a Ford dealer). Note
that it is preferable to keep the engine upright
until the sump has been removed to prevent
sludge from entering the engine internals.
1.8 litre (R2A type)
Removal
1With the engine removed, proceed as
follows.
2Remove the flywheel/driveplate and the
engine adapter plate.
3Unscrew the fourteen securing bolts and
withdraw the two reinforcing strips and the
sump. If the sump is stuck, carefully tap it
sideways to free it. Do not prise between the
mating faces.
27Sump - removal and refitting
26Crankshaft rear oil seal -
renewal
25Crankshaft front oil seal -
renewal
24Flywheel/driveplate - removal,
inspection and refitting
CVH engines 2C•19
2C
25.5 Crankshaft front oil seal (arrowed)
located in oil pump housing - 1.8 litre (R2A)26.3 Using a special tool to fit the
crankshaft rear oil seal - 1.8 litre (R2A)26.2 Crankshaft rear oil seal location
(arrowed)
25.4 Using a special tool to fit the
crankshaft front oil seal - 1.8 litre (R2A)24.2 Using an improvised tool to hold the
flywheel stationary while tightening the
securing bolts - 1.8 litre (R2A)
A tool can be improvised to fit
the crankshaft front oil seal
by using a metal tube of
suitable diameter and a large
washer or metal disc. Do not attempt to
drive the seal home using a tube drift.
Page 20 of 24
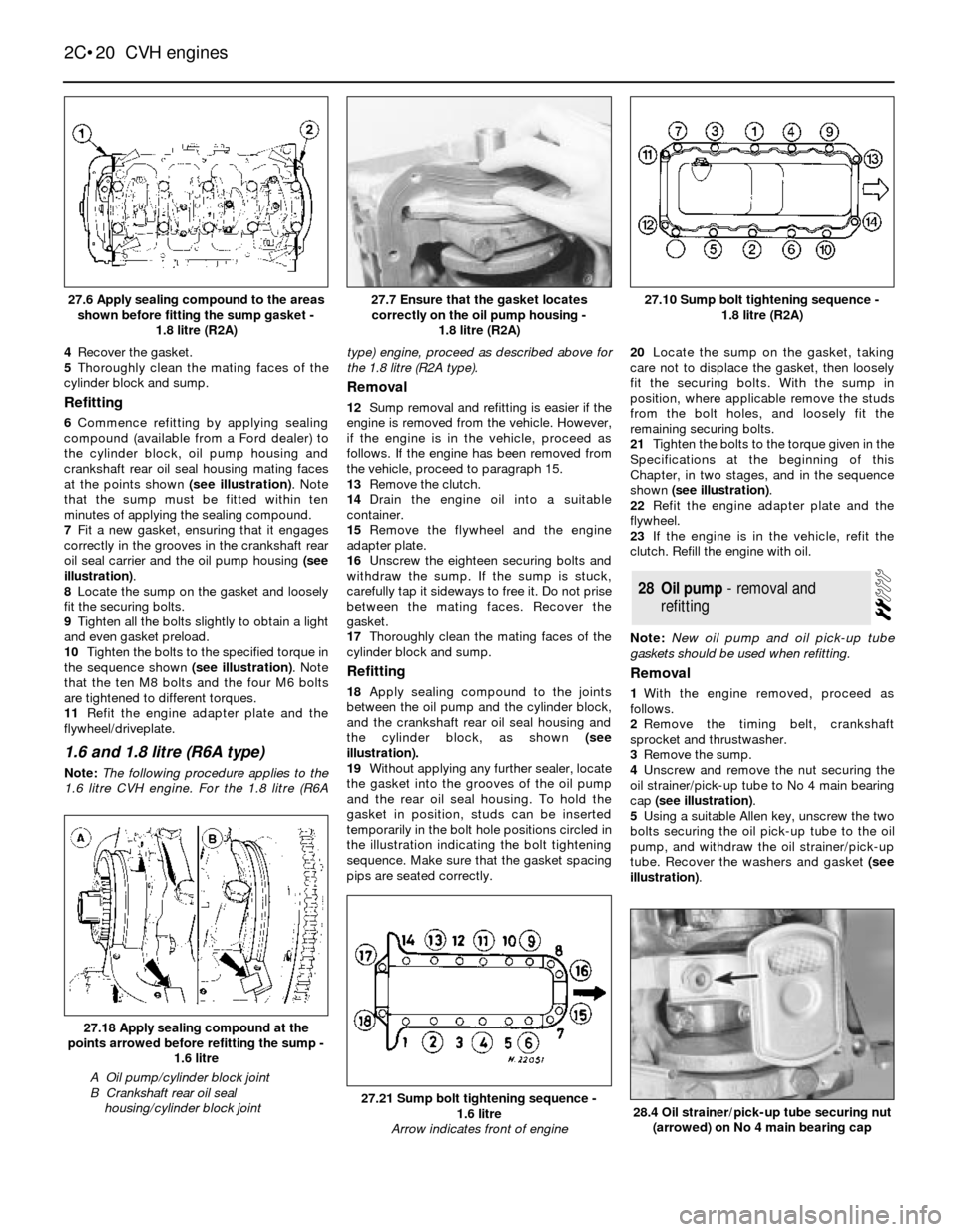
4Recover the gasket.
5Thoroughly clean the mating faces of the
cylinder block and sump.
Refitting
6Commence refitting by applying sealing
compound (available from a Ford dealer) to
the cylinder block, oil pump housing and
crankshaft rear oil seal housing mating faces
at the points shown (see illustration). Note
that the sump must be fitted within ten
minutes of applying the sealing compound.
7Fit a new gasket, ensuring that it engages
correctly in the grooves in the crankshaft rear
oil seal carrier and the oil pump housing (see
illustration).
8Locate the sump on the gasket and loosely
fit the securing bolts.
9Tighten all the bolts slightly to obtain a light
and even gasket preload.
10Tighten the bolts to the specified torque in
the sequence shown (see illustration). Note
that the ten M8 bolts and the four M6 bolts
are tightened to different torques.
11Refit the engine adapter plate and the
flywheel/driveplate.
1.6 and 1.8 litre (R6A type)
Note: The following procedure applies to the
1.6 litre CVH engine. For the 1.8 litre (R6Atype) engine, proceed as described above for
the 1.8 litre (R2A type).
Removal
12Sump removal and refitting is easier if the
engine is removed from the vehicle. However,
if the engine is in the vehicle, proceed as
follows. If the engine has been removed from
the vehicle, proceed to paragraph 15.
13Remove the clutch.
14Drain the engine oil into a suitable
container.
15Remove the flywheel and the engine
adapter plate.
16Unscrew the eighteen securing bolts and
withdraw the sump. If the sump is stuck,
carefully tap it sideways to free it. Do not prise
between the mating faces. Recover the
gasket.
17Thoroughly clean the mating faces of the
cylinder block and sump.
Refitting
18Apply sealing compound to the joints
between the oil pump and the cylinder block,
and the crankshaft rear oil seal housing and
the cylinder block, as shown (see
illustration).
19Without applying any further sealer, locate
the gasket into the grooves of the oil pump
and the rear oil seal housing. To hold the
gasket in position, studs can be inserted
temporarily in the bolt hole positions circled in
the illustration indicating the bolt tightening
sequence. Make sure that the gasket spacing
pips are seated correctly.20Locate the sump on the gasket, taking
care not to displace the gasket, then loosely
fit the securing bolts. With the sump in
position, where applicable remove the studs
from the bolt holes, and loosely fit the
remaining securing bolts.
21Tighten the bolts to the torque given in the
Specifications at the beginning of this
Chapter, in two stages, and in the sequence
shown (see illustration).
22Refit the engine adapter plate and the
flywheel.
23If the engine is in the vehicle, refit the
clutch. Refill the engine with oil.
Note: New oil pump and oil pick-up tube
gaskets should be used when refitting.
Removal
1With the engine removed, proceed as
follows.
2Remove the timing belt, crankshaft
sprocket and thrustwasher.
3Remove the sump.
4Unscrew and remove the nut securing the
oil strainer/pick-up tube to No 4 main bearing
cap (see illustration).
5Using a suitable Allen key, unscrew the two
bolts securing the oil pick-up tube to the oil
pump, and withdraw the oil strainer/pick-up
tube. Recover the washers and gasket (see
illustration).
28Oil pump - removal and
refitting
2C•20CVH engines
27.6 Apply sealing compound to the areas
shown before fitting the sump gasket -
1.8 litre (R2A)27.10 Sump bolt tightening sequence -
1.8 litre (R2A)
27.21 Sump bolt tightening sequence -
1.6 litre
Arrow indicates front of engine
27.18 Apply sealing compound at the
points arrowed before refitting the sump -
1.6 litre
A Oil pump/cylinder block joint
B Crankshaft rear oil seal
housing/cylinder block joint
27.7 Ensure that the gasket locates
correctly on the oil pump housing -
1.8 litre (R2A)
28.4 Oil strainer/pick-up tube securing nut
(arrowed) on No 4 main bearing cap