clutch FORD SIERRA 1983 1.G SOHC Engines Workshop Manual
[x] Cancel search | Manufacturer: FORD, Model Year: 1983, Model line: SIERRA, Model: FORD SIERRA 1983 1.GPages: 24, PDF Size: 1.03 MB
Page 8 of 24
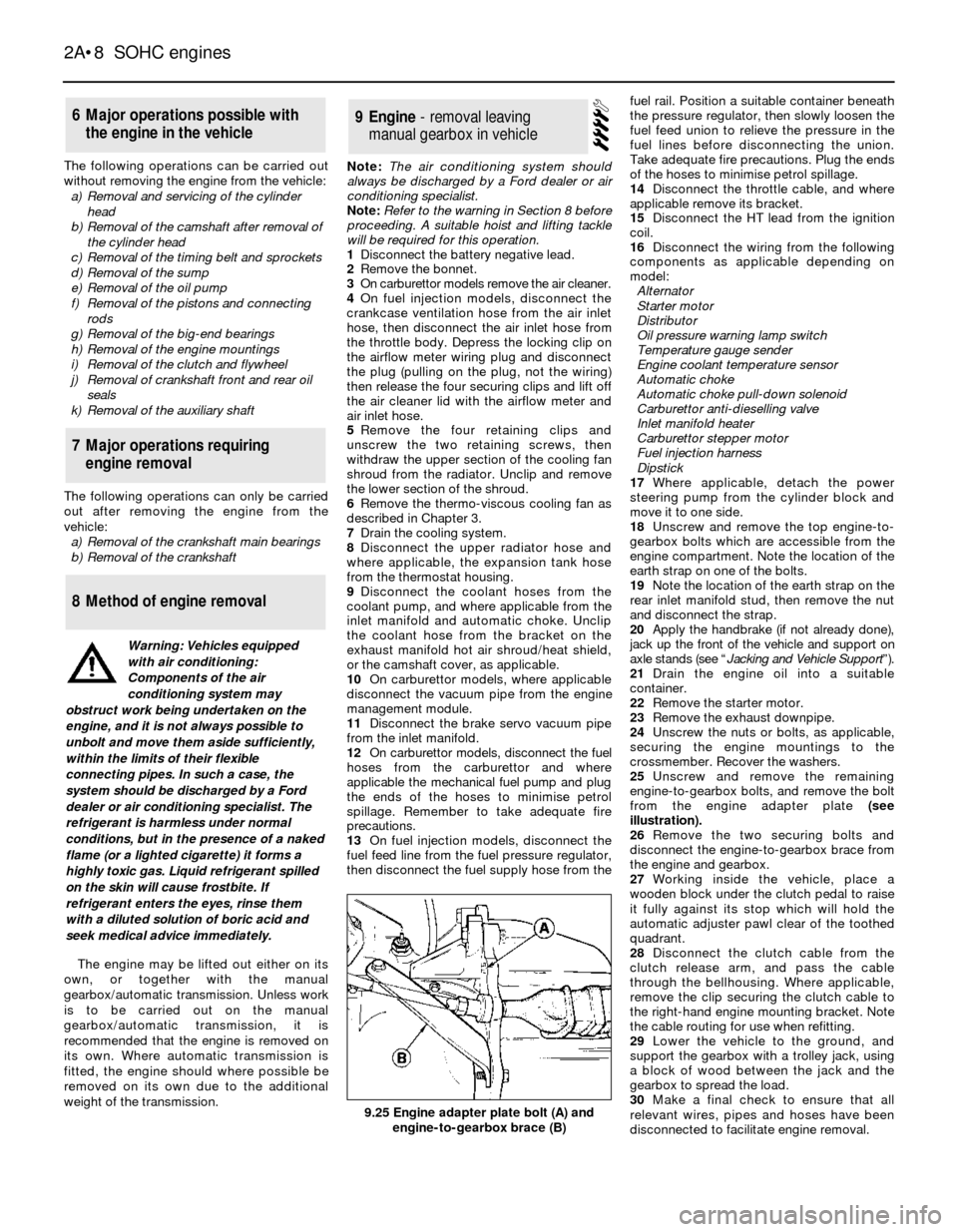
The following operations can be carried out
without removing the engine from the vehicle:
a)Removal and servicing of the cylinder
head
b)Removal of the camshaft after removal of
the cylinder head
c)Removal of the timing belt and sprockets
d)Removal of the sump
e)Removal of the oil pump
f)Removal of the pistons and connecting
rods
g)Removal of the big-end bearings
h)Removal of the engine mountings
i)Removal of the clutch and flywheel
j)Removal of crankshaft front and rear oil
seals
k)Removal of the auxiliary shaft
The following operations can only be carried
out after removing the engine from the
vehicle:
a)Removal of the crankshaft main bearings
b)Removal of the crankshaft
The engine may be lifted out either on its
own, or together with the manual
gearbox/automatic transmission. Unless work
is to be carried out on the manual
gearbox/automatic transmission, it is
recommended that the engine is removed on
its own. Where automatic transmission is
fitted, the engine should where possible be
removed on its own due to the additional
weight of the transmission. Note: The air conditioning system should
always be discharged by a Ford dealer or air
conditioning specialist.
Note: Refer to the warning in Section 8 before
proceeding. A suitable hoist and lifting tackle
will be required for this operation.
1Disconnect the battery negative lead.
2Remove the bonnet.
3On carburettor models remove the air cleaner.
4On fuel injection models, disconnect the
crankcase ventilation hose from the air inlet
hose, then disconnect the air inlet hose from
the throttle body. Depress the locking clip on
the airflow meter wiring plug and disconnect
the plug (pulling on the plug, not the wiring)
then release the four securing clips and lift off
the air cleaner lid with the airflow meter and
air inlet hose.
5Remove the four retaining clips and
unscrew the two retaining screws, then
withdraw the upper section of the cooling fan
shroud from the radiator. Unclip and remove
the lower section of the shroud.
6Remove the thermo-viscous cooling fan as
described in Chapter 3.
7Drain the cooling system.
8Disconnect the upper radiator hose and
where applicable, the expansion tank hose
from the thermostat housing.
9Disconnect the coolant hoses from the
coolant pump, and where applicable from the
inlet manifold and automatic choke. Unclip
the coolant hose from the bracket on the
exhaust manifold hot air shroud/heat shield,
or the camshaft cover, as applicable.
10On carburettor models, where applicable
disconnect the vacuum pipe from the engine
management module.
11Disconnect the brake servo vacuum pipe
from the inlet manifold.
12On carburettor models, disconnect the fuel
hoses from the carburettor and where
applicable the mechanical fuel pump and plug
the ends of the hoses to minimise petrol
spillage. Remember to take adequate fire
precautions.
13On fuel injection models, disconnect the
fuel feed line from the fuel pressure regulator,
then disconnect the fuel supply hose from thefuel rail. Position a suitable container beneath
the pressure regulator, then slowly loosen the
fuel feed union to relieve the pressure in the
fuel lines before disconnecting the union.
Take adequate fire precautions. Plug the ends
of the hoses to minimise petrol spillage.
14Disconnect the throttle cable, and where
applicable remove its bracket.
15Disconnect the HT lead from the ignition
coil.
16Disconnect the wiring from the following
components as applicable depending on
model:
Alternator
Starter motor
Distributor
Oil pressure warning lamp switch
Temperature gauge sender
Engine coolant temperature sensor
Automatic choke
Automatic choke pull-down solenoid
Carburettor anti-dieselling valve
Inlet manifold heater
Carburettor stepper motor
Fuel injection harness
Dipstick
17Where applicable, detach the power
steering pump from the cylinder block and
move it to one side.
18Unscrew and remove the top engine-to-
gearbox bolts which are accessible from the
engine compartment. Note the location of the
earth strap on one of the bolts.
19Note the location of the earth strap on the
rear inlet manifold stud, then remove the nut
and disconnect the strap.
20Apply the handbrake (if not already done),
jack up the front of the vehicle and support on
axle stands (see ÒJacking and Vehicle SupportÓ).
21Drain the engine oil into a suitable
container.
22Remove the starter motor.
23Remove the exhaust downpipe.
24Unscrew the nuts or bolts, as applicable,
securing the engine mountings to the
crossmember. Recover the washers.
25Unscrew and remove the remaining
engine-to-gearbox bolts, and remove the bolt
from the engine adapter plate (see
illustration).
26Remove the two securing bolts and
disconnect the engine-to-gearbox brace from
the engine and gearbox.
27Working inside the vehicle, place a
wooden block under the clutch pedal to raise
it fully against its stop which will hold the
automatic adjuster pawl clear of the toothed
quadrant.
28Disconnect the clutch cable from the
clutch release arm, and pass the cable
through the bellhousing. Where applicable,
remove the clip securing the clutch cable to
the right-hand engine mounting bracket. Note
the cable routing for use when refitting.
29Lower the vehicle to the ground, and
support the gearbox with a trolley jack, using
a block of wood between the jack and the
gearbox to spread the load.
30Make a final check to ensure that all
relevant wires, pipes and hoses have been
disconnected to facilitate engine removal.
9Engine - removal leaving
manual gearbox in vehicle
8Method of engine removal
7Major operations requiring
engine removal
6Major operations possible with
the engine in the vehicle
2A¥8SOHC engines
9.25 Engine adapter plate bolt (A) and
engine-to-gearbox brace (B)
Warning: Vehicles equipped
with air conditioning:
Components of the air
conditioning system may
obstruct work being undertaken on the
engine, and it is not always possible to
unbolt and move them aside sufficiently,
within the limits of their flexible
connecting pipes. In such a case, the
system should be discharged by a Ford
dealer or air conditioning specialist. The
refrigerant is harmless under normal
conditions, but in the presence of a naked
flame (or a lighted cigarette) it forms a
highly toxic gas. Liquid refrigerant spilled
on the skin will cause frostbite. If
refrigerant enters the eyes, rinse them
with a diluted solution of boric acid and
seek medical advice immediately.
Page 10 of 24
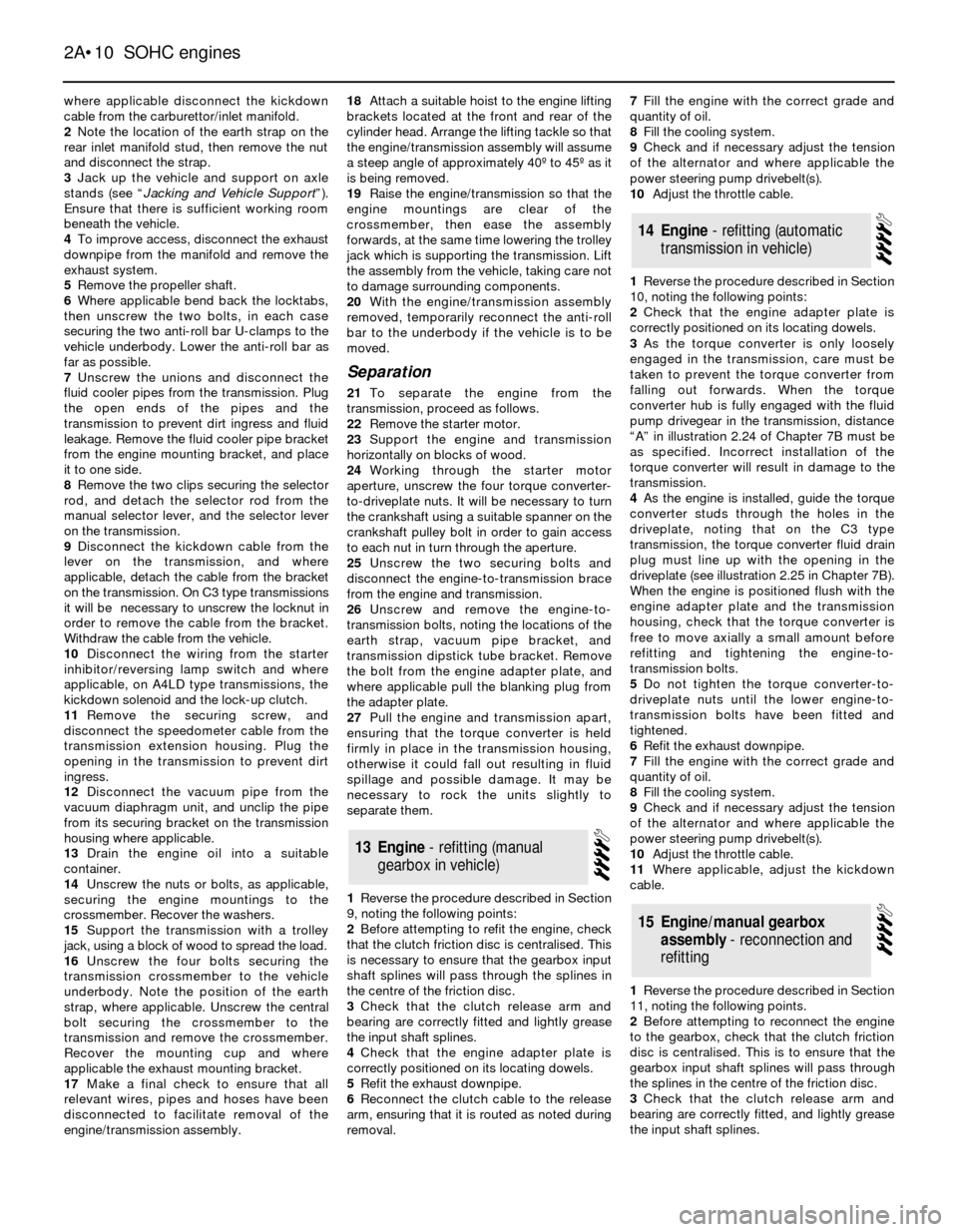
where applicable disconnect the kickdown
cable from the carburettor/inlet manifold.
2Note the location of the earth strap on the
rear inlet manifold stud, then remove the nut
and disconnect the strap.
3Jack up the vehicle and support on axle
stands (see ÒJacking and Vehicle SupportÓ).
Ensure that there is sufficient working room
beneath the vehicle.
4To improve access, disconnect the exhaust
downpipe from the manifold and remove the
exhaust system.
5Remove the propeller shaft.
6Where applicable bend back the locktabs,
then unscrew the two bolts, in each case
securing the two anti-roll bar U-clamps to the
vehicle underbody. Lower the anti-roll bar as
far as possible.
7Unscrew the unions and disconnect the
fluid cooler pipes from the transmission. Plug
the open ends of the pipes and the
transmission to prevent dirt ingress and fluid
leakage. Remove the fluid cooler pipe bracket
from the engine mounting bracket, and place
it to one side.
8Remove the two clips securing the selector
rod, and detach the selector rod from the
manual selector lever, and the selector lever
on the transmission.
9Disconnect the kickdown cable from the
lever on the transmission, and where
applicable, detach the cable from the bracket
on the transmission. On C3 type transmissions
it will be necessary to unscrew the locknut in
order to remove the cable from the bracket.
Withdraw the cable from the vehicle.
10Disconnect the wiring from the starter
inhibitor/reversing lamp switch and where
applicable, on A4LD type transmissions, the
kickdown solenoid and the lock-up clutch.
11Remove the securing screw, and
disconnect the speedometer cable from the
transmission extension housing. Plug the
opening in the transmission to prevent dirt
ingress.
12Disconnect the vacuum pipe from the
vacuum diaphragm unit, and unclip the pipe
from its securing bracket on the transmission
housing where applicable.
13Drain the engine oil into a suitable
container.
14Unscrew the nuts or bolts, as applicable,
securing the engine mountings to the
crossmember. Recover the washers.
15Support the transmission with a trolley
jack, using a block of wood to spread the load.
16Unscrew the four bolts securing the
transmission crossmember to the vehicle
underbody. Note the position of the earth
strap, where applicable. Unscrew the central
bolt securing the crossmember to the
transmission and remove the crossmember.
Recover the mounting cup and where
applicable the exhaust mounting bracket.
17Make a final check to ensure that all
relevant wires, pipes and hoses have been
disconnected to facilitate removal of the
engine/transmission assembly.18Attach a suitable hoist to the engine lifting
brackets located at the front and rear of the
cylinder head. Arrange the lifting tackle so that
the engine/transmission assembly will assume
a steep angle of approximately 40¼ to 45¼ as it
is being removed.
19Raise the engine/transmission so that the
engine mountings are clear of the
crossmember, then ease the assembly
forwards, at the same time lowering the trolley
jack which is supporting the transmission. Lift
the assembly from the vehicle, taking care not
to damage surrounding components.
20With the engine/transmission assembly
removed, temporarily reconnect the anti-roll
bar to the underbody if the vehicle is to be
moved.
Separation
21To separate the engine from the
transmission, proceed as follows.
22Remove the starter motor.
23Support the engine and transmission
horizontally on blocks of wood.
24Working through the starter motor
aperture, unscrew the four torque converter-
to-driveplate nuts. It will be necessary to turn
the crankshaft using a suitable spanner on the
crankshaft pulley bolt in order to gain access
to each nut in turn through the aperture.
25Unscrew the two securing bolts and
disconnect the engine-to-transmission brace
from the engine and transmission.
26Unscrew and remove the engine-to-
transmission bolts, noting the locations of the
earth strap, vacuum pipe bracket, and
transmission dipstick tube bracket. Remove
the bolt from the engine adapter plate, and
where applicable pull the blanking plug from
the adapter plate.
27Pull the engine and transmission apart,
ensuring that the torque converter is held
firmly in place in the transmission housing,
otherwise it could fall out resulting in fluid
spillage and possible damage. It may be
necessary to rock the units slightly to
separate them.
1Reverse the procedure described in Section
9, noting the following points:
2Before attempting to refit the engine, check
that the clutch friction disc is centralised. This
is necessary to ensure that the gearbox input
shaft splines will pass through the splines in
the centre of the friction disc.
3Check that the clutch release arm and
bearing are correctly fitted and lightly grease
the input shaft splines.
4Check that the engine adapter plate is
correctly positioned on its locating dowels.
5Refit the exhaust downpipe.
6Reconnect the clutch cable to the release
arm, ensuring that it is routed as noted during
removal. 7Fill the engine with the correct grade and
quantity of oil.
8Fill the cooling system.
9Check and if necessary adjust the tension
of the alternator and where applicable the
power steering pump drivebelt(s).
10Adjust the throttle cable.
1Reverse the procedure described in Section
10, noting the following points:
2Check that the engine adapter plate is
correctly positioned on its locating dowels.
3As the torque converter is only loosely
engaged in the transmission, care must be
taken to prevent the torque converter from
falling out forwards. When the torque
converter hub is fully engaged with the fluid
pump drivegear in the transmission, distance
ÒAÓ in illustration 2.24 of Chapter 7B must be
as specified. Incorrect installation of the
torque converter will result in damage to the
transmission.
4As the engine is installed, guide the torque
converter studs through the holes in the
driveplate, noting that on the C3 type
transmission, the torque converter fluid drain
plug must line up with the opening in the
driveplate (see illustration 2.25 in Chapter 7B).
When the engine is positioned flush with the
engine adapter plate and the transmission
housing, check that the torque converter is
free to move axially a small amount before
refitting and tightening the engine-to-
transmission bolts.
5Do not tighten the torque converter-to-
driveplate nuts until the lower engine-to-
transmission bolts have been fitted and
tightened.
6Refit the exhaust downpipe.
7Fill the engine with the correct grade and
quantity of oil.
8Fill the cooling system.
9Check and if necessary adjust the tension
of the alternator and where applicable the
power steering pump drivebelt(s).
10Adjust the throttle cable.
11Where applicable, adjust the kickdown
cable.
1Reverse the procedure described in Section
11, noting the following points.
2Before attempting to reconnect the engine
to the gearbox, check that the clutch friction
disc is centralised. This is to ensure that the
gearbox input shaft splines will pass through
the splines in the centre of the friction disc.
3Check that the clutch release arm and
bearing are correctly fitted, and lightly grease
the input shaft splines.
15Engine/manual gearbox
assembly - reconnection and
refitting
14Engine - refitting (automatic
transmission in vehicle)
13Engine - refitting (manual
gearbox in vehicle)
2A¥10SOHC engines
Page 11 of 24
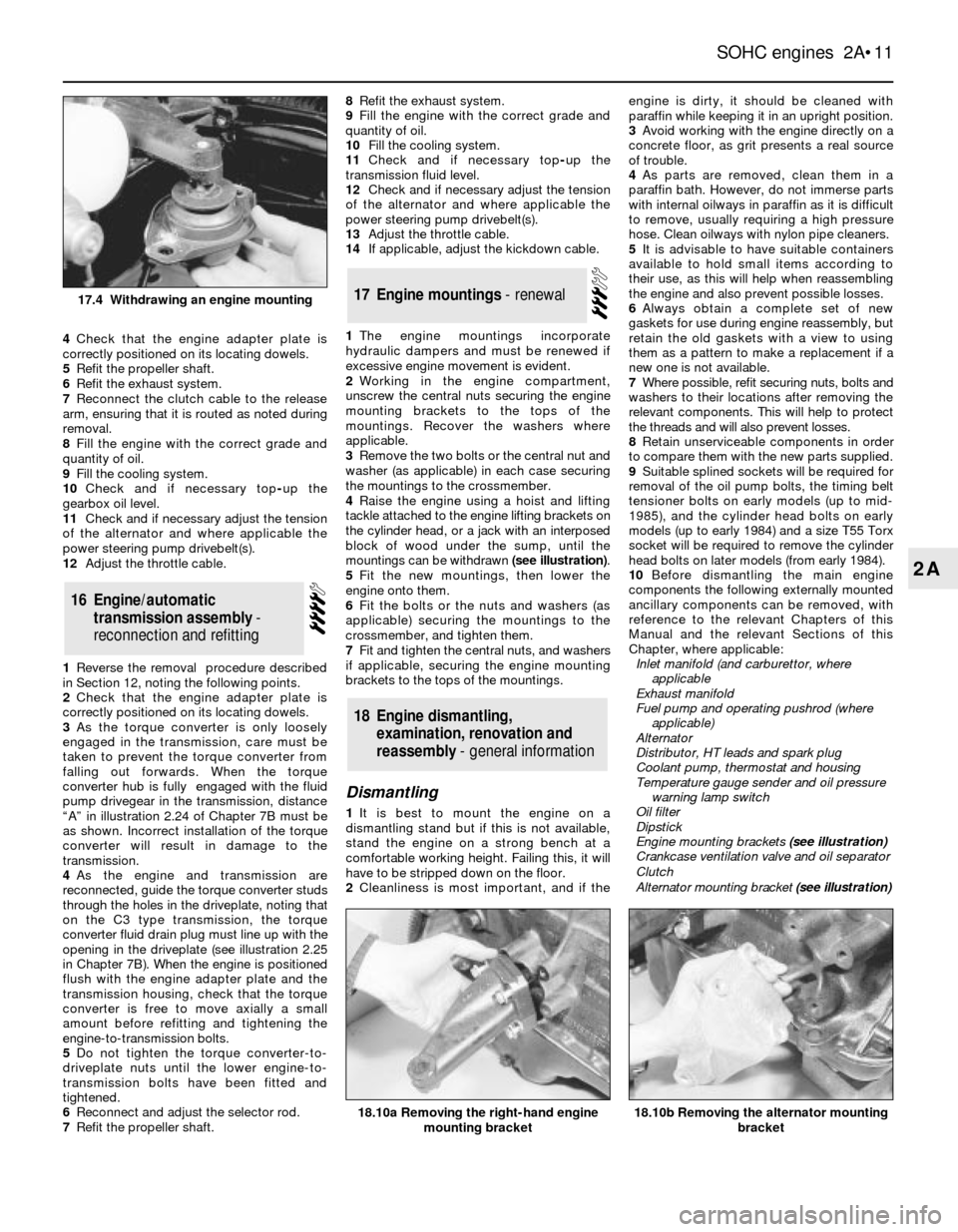
4Check that the engine adapter plate is
correctly positioned on its locating dowels.
5Refit the propeller shaft.
6Refit the exhaust system.
7Reconnect the clutch cable to the release
arm, ensuring that it is routed as noted during
removal.
8Fill the engine with the correct grade and
quantity of oil.
9Fill the cooling system.
10Check and if necessary top-up the
gearbox oil level.
11Check and if necessary adjust the tension
of the alternator and where applicable the
power steering pump drivebelt(s).
12Adjust the throttle cable.
1Reverse the removal procedure described
in Section 12, noting the following points.
2Check that the engine adapter plate is
correctly positioned on its locating dowels.
3As the torque converter is only loosely
engaged in the transmission, care must be
taken to prevent the torque converter from
falling out forwards. When the torque
converter hub is fully engaged with the fluid
pump drivegear in the transmission, distance
ÒAÓ in illustration 2.24 of Chapter 7B must be
as shown. Incorrect installation of the torque
converter will result in damage to the
transmission.
4As the engine and transmission are
reconnected, guide the torque converter studs
through the holes in the driveplate, noting that
on the C3 type transmission, the torque
converter fluid drain plug must line up with the
opening in the driveplate (see illustration 2.25
in Chapter 7B). When the engine is positioned
flush with the engine adapter plate and the
transmission housing, check that the torque
converter is free to move axially a small
amount before refitting and tightening the
engine-to-transmission bolts.
5Do not tighten the torque converter-to-
driveplate nuts until the lower engine-to-
transmission bolts have been fitted and
tightened.
6Reconnect and adjust the selector rod.
7Refit the propeller shaft.8Refit the exhaust system.
9Fill the engine with the correct grade and
quantity of oil.
10Fill the cooling system.
11Check and if necessary top-up the
transmission fluid level.
12Check and if necessary adjust the tension
of the alternator and where applicable the
power steering pump drivebelt(s).
13Adjust the throttle cable.
14If applicable, adjust the kickdown cable.
1The engine mountings incorporate
hydraulic dampers and must be renewed if
excessive engine movement is evident.
2Working in the engine compartment,
unscrew the central nuts securing the engine
mounting brackets to the tops of the
mountings. Recover the washers where
applicable.
3Remove the two bolts or the central nut and
washer (as applicable) in each case securing
the mountings to the crossmember.
4Raise the engine using a hoist and lifting
tackle attached to the engine lifting brackets on
the cylinder head, or a jack with an interposed
block of wood under the sump, until the
mountings can be withdrawn (see illustration).
5Fit the new mountings, then lower the
engine onto them.
6Fit the bolts or the nuts and washers (as
applicable) securing the mountings to the
crossmember, and tighten them.
7Fit and tighten the central nuts, and washers
if applicable, securing the engine mounting
brackets to the tops of the mountings.
Dismantling
1It is best to mount the engine on a
dismantling stand but if this is not available,
stand the engine on a strong bench at a
comfortable working height. Failing this, it will
have to be stripped down on the floor.
2Cleanliness is most important, and if theengine is dirty, it should be cleaned with
paraffin while keeping it in an upright position.
3Avoid working with the engine directly on a
concrete floor, as grit presents a real source
of trouble.
4As parts are removed, clean them in a
paraffin bath. However, do not immerse parts
with internal oilways in paraffin as it is difficult
to remove, usually requiring a high pressure
hose. Clean oilways with nylon pipe cleaners.
5It is advisable to have suitable containers
available to hold small items according to
their use, as this will help when reassembling
the engine and also prevent possible losses.
6Always obtain a complete set of new
gaskets for use during engine reassembly, but
retain the old gaskets with a view to using
them as a pattern to make a replacement if a
new one is not available.
7Where possible, refit securing nuts, bolts and
washers to their locations after removing the
relevant components. This will help to protect
the threads and will also prevent losses.
8Retain unserviceable components in order
to compare them with the new parts supplied.
9Suitable splined sockets will be required for
removal of the oil pump bolts, the timing belt
tensioner bolts on early models (up to mid-
1985), and the cylinder head bolts on early
models (up to early 1984) and a size T55 Torx
socket will be required to remove the cylinder
head bolts on later models (from early 1984).
10Before dismantling the main engine
components the following externally mounted
ancillary components can be removed, with
reference to the relevant Chapters of this
Manual and the relevant Sections of this
Chapter, where applicable:
Inlet manifold (and carburettor, where
applicable
Exhaust manifold
Fuel pump and operating pushrod (where
applicable)
Alternator
Distributor, HT leads and spark plug
Coolant pump, thermostat and housing
Temperature gauge sender and oil pressure
warning lamp switch
Oil filter
Dipstick
Engine mounting brackets (see illustration)
Crankcase ventilation valve and oil separator
Clutch
Alternator mounting bracket (see illustration)
18Engine dismantling,
examination, renovation and
reassembly - general information
17Engine mountings - renewal
16Engine/automatic
transmission assembly -
reconnection and refitting
SOHC engines 2A¥11
2A
18.10b Removing the alternator mounting
bracket18.10a Removing the right-hand engine
mounting bracket
17.4 Withdrawing an engine mounting
Page 18 of 24
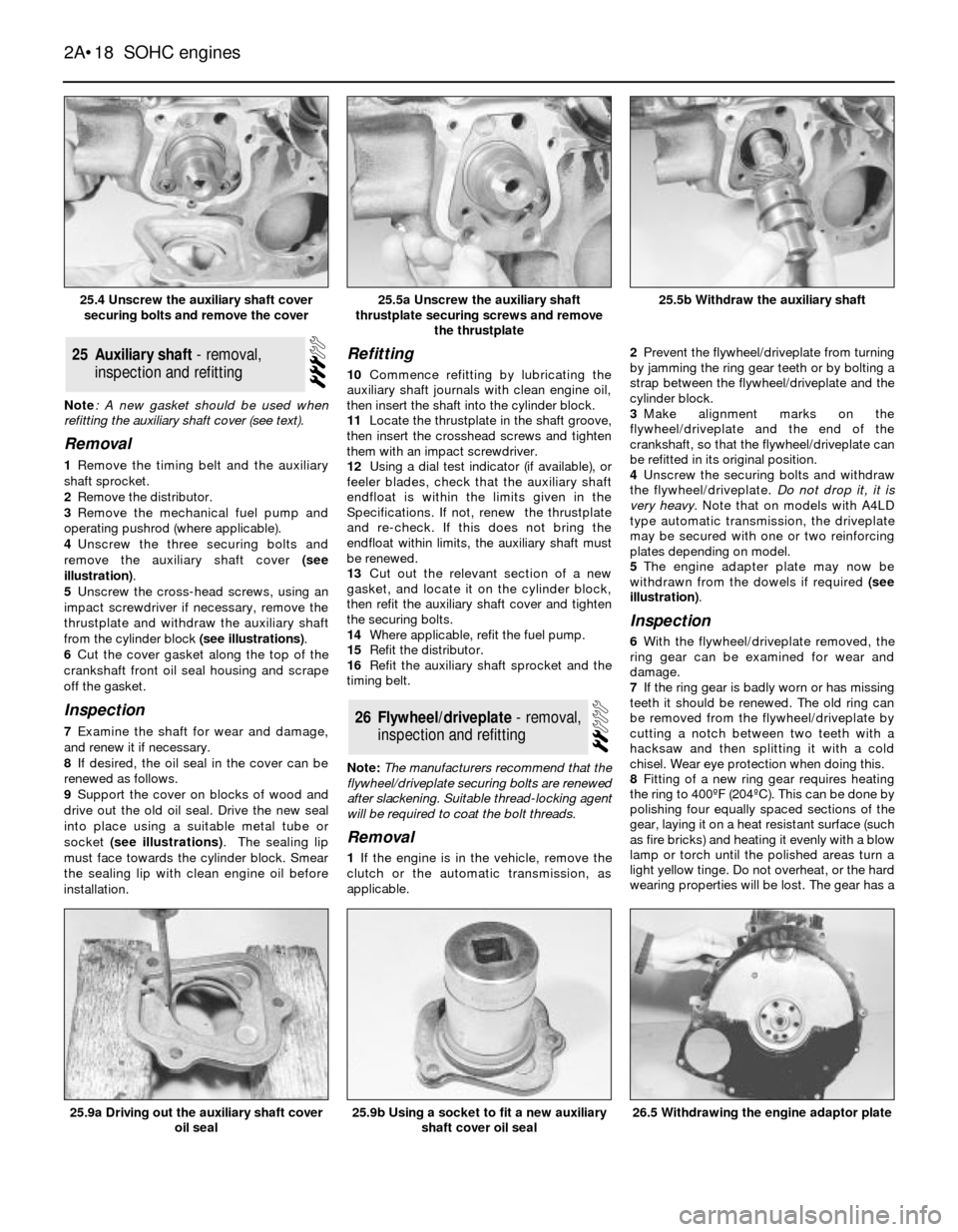
Note: A new gasket should be used when
refitting the auxiliary shaft cover (see text).
Removal
1Remove the timing belt and the auxiliary
shaft sprocket.
2Remove the distributor.
3Remove the mechanical fuel pump and
operating pushrod (where applicable).
4Unscrew the three securing bolts and
remove the auxiliary shaft cover (see
illustration).
5Unscrew the cross-head screws, using an
impact screwdriver if necessary, remove the
thrustplate and withdraw the auxiliary shaft
from the cylinder block (see illustrations).
6Cut the cover gasket along the top of the
crankshaft front oil seal housing and scrape
off the gasket.
Inspection
7Examine the shaft for wear and damage,
and renew it if necessary.
8If desired, the oil seal in the cover can be
renewed as follows.
9Support the cover on blocks of wood and
drive out the old oil seal. Drive the new seal
into place using a suitable metal tube or
socket (see illustrations). The sealing lip
must face towards the cylinder block. Smear
the sealing lip with clean engine oil before
installation.
Refitting
10Commence refitting by lubricating the
auxiliary shaft journals with clean engine oil,
then insert the shaft into the cylinder block.
11Locate the thrustplate in the shaft groove,
then insert the crosshead screws and tighten
them with an impact screwdriver.
12Using a dial test indicator (if available), or
feelerblades, check that the auxiliary shaft
endfloat is within the limits given in the
Specifications. If not, renew the thrustplate
and re-check. If this does not bring the
endfloat within limits, the auxiliary shaft must
be renewed.
13Cut out the relevant section of a new
gasket, and locate it on the cylinder block,
then refit the auxiliary shaft cover and tighten
the securing bolts.
14Where applicable, refit the fuel pump.
15Refit the distributor.
16Refit the auxiliary shaft sprocket and the
timing belt.
Note: The manufacturers recommend that the
flywheel/driveplate securing bolts are renewed
after slackening. Suitable thread-locking agent
will be required to coat the bolt threads.
Removal
1If the engine is in the vehicle, remove the
clutch or the automatic transmission, as
applicable.2Prevent the flywheel/driveplate from turning
by jamming the ring gear teeth or by bolting a
strap between the flywheel/driveplate and the
cylinder block.
3Make alignment marks on the
flywheel/driveplate and the end of the
crankshaft, so that the flywheel/driveplate can
be refitted in its original position.
4Unscrew the securing bolts and withdraw
the flywheel/driveplate. Do not drop it, it is
very heavy. Note that on models with A4LD
type automatic transmission, the driveplate
may be secured with one or two reinforcing
plates depending on model.
5The engine adapter plate may now be
withdrawn from the dowels if required (see
illustration).
Inspection
6With the flywheel/driveplate removed, the
ring gear can be examined for wear and
damage.
7If the ring gear is badly worn or has missing
teeth it should be renewed. The old ring can
be removed from the flywheel/driveplate by
cutting a notch between two teeth with a
hacksaw and then splitting it with a cold
chisel. Wear eye protection when doing this.
8Fitting of a new ring gear requires heating
the ring to 400¼F (204¼C). This can be done by
polishing four equally spaced sections of the
gear, laying it on a heat resistant surface (such
as fire bricks) and heating it evenly with a blow
lamp or torch until the polished areas turn a
light yellow tinge. Do not overheat, or the hard
wearing properties will be lost. The gear has a
26Flywheel/driveplate - removal,
inspection and refitting
25Auxiliary shaft - removal,
inspection and refitting
2A¥18SOHC engines
25.4 Unscrew the auxiliary shaft cover
securing bolts and remove the cover25.5b Withdraw the auxiliary shaft
26.5 Withdrawing the engine adaptor plate25.9b Using a socket to fit a new auxiliary
shaft cover oil seal25.9a Driving out the auxiliary shaft cover
oil seal
25.5a Unscrew the auxiliary shaft
thrustplate securing screws and remove
the thrustplate
Page 19 of 24
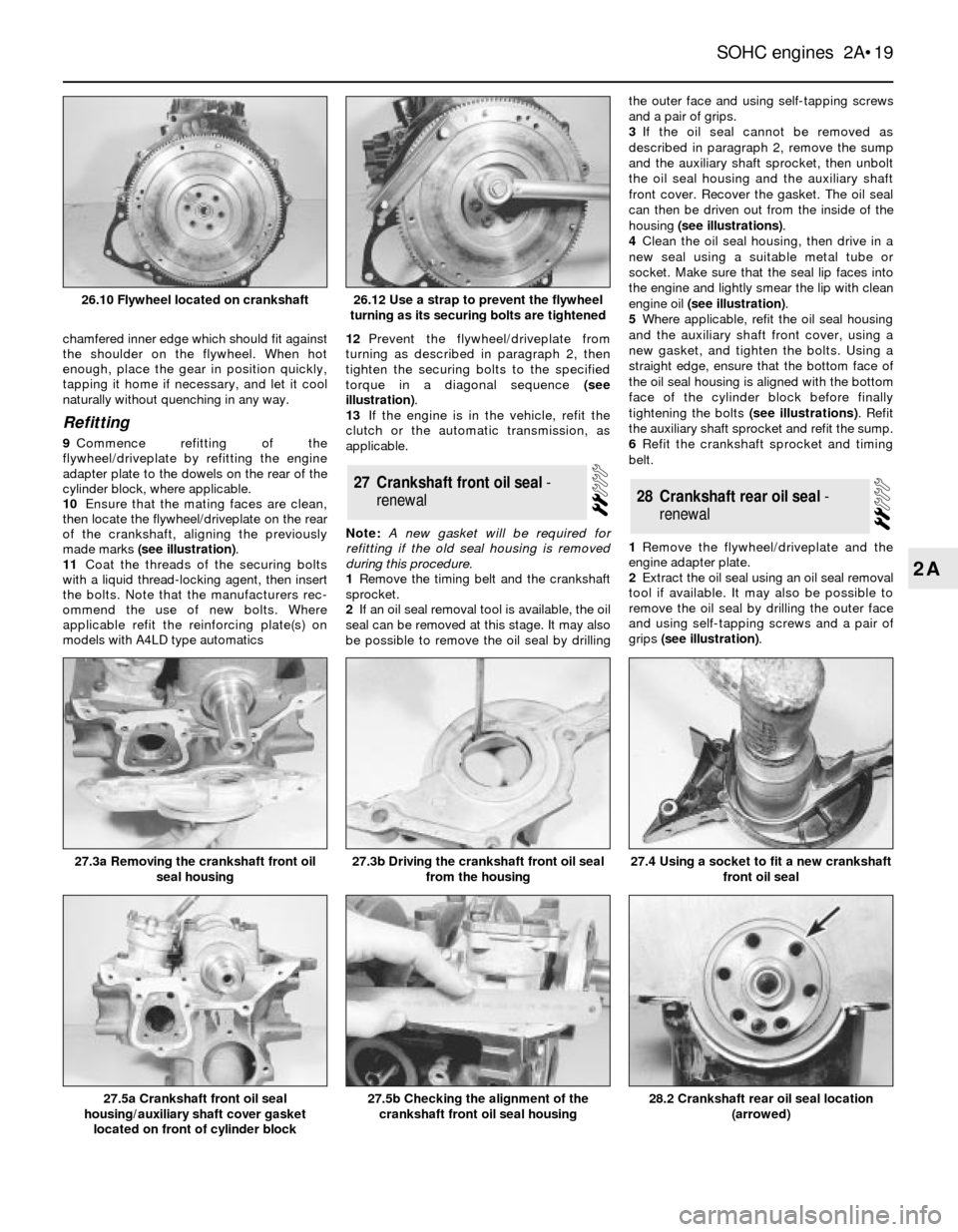
chamfered inner edge which should fit against
the shoulder on the flywheel. When hot
enough, place the gear in position quickly,
tapping it home if necessary, and let it cool
naturally without quenching in any way.
Refitting
9Commence refitting of the
flywheel/driveplate by refitting the engine
adapter plate to the dowels on the rear of the
cylinder block, where applicable.
10Ensure that the mating faces are clean,
then locate the flywheel/driveplate on the rear
of the crankshaft, aligning the previously
made marks (see illustration).
11Coat the threads of the securing bolts
with a liquid thread-locking agent, then insert
the bolts. Note that the manufacturers rec-
ommend the use of new bolts. Where
applicable refit the reinforcing plate(s) on
models with A4LD type automatics12Prevent the flywheel/driveplate from
turning as described in paragraph 2, then
tighten the securing bolts to the specified
torque in a diagonal sequence (see
illustration).
13If the engine is in the vehicle, refit the
clutch or the automatic transmission, as
applicable.
Note: A new gasket will be required for
refitting if the old seal housing is removed
during this procedure.
1Remove the timing belt and the crankshaft
sprocket.
2If an oil seal removal tool is available, the oil
seal can be removed at this stage. It may also
be possible to remove the oil seal by drillingthe outer face and using self-tapping screws
and a pair of grips.
3If the oil seal cannot be removed as
described in paragraph 2, remove the sump
and the auxiliary shaft sprocket, then unbolt
the oil seal housing and the auxiliary shaft
front cover. Recover the gasket. The oil seal
can then be driven out from the inside of the
housing (see illustrations).
4Clean the oil seal housing, then drive in a
new seal using a suitable metal tube or
socket. Make sure that the seal lip faces into
the engine and lightly smear the lip with clean
engine oil (see illustration).
5Where applicable, refit the oil seal housing
and the auxiliary shaft front cover, using a
new gasket, and tighten the bolts. Using a
straight edge, ensure that the bottom face of
the oil seal housing is aligned with the bottom
face of the cylinder block before finally
tightening the bolts (see illustrations). Refit
the auxiliary shaft sprocket and refit the sump.
6Refit the crankshaft sprocket and timing
belt.
1Remove the flywheel/driveplate and the
engine adapter plate.
2Extract the oil seal using an oil seal removal
tool if available. It may also be possible to
remove the oil seal by drilling the outer face
and using self-tapping screws and a pair of
grips (see illustration).
28Crankshaft rear oil seal -
renewal27Crankshaft front oil seal -
renewal
SOHC engines 2A¥19
2A
27.3a Removing the crankshaft front oil
seal housing27.3b Driving the crankshaft front oil seal
from the housing
28.2 Crankshaft rear oil seal location
(arrowed)27.5b Checking the alignment of the
crankshaft front oil seal housing27.5a Crankshaft front oil seal
housing/auxiliary shaft cover gasket
located on front of cylinder block
27.4 Using a socket to fit a new crankshaft
front oil seal
26.12 Use a strap to prevent the flywheel
turning as its securing bolts are tightened26.10 Flywheel located on crankshaft