oil change FORD SIERRA 1983 1.G SOHC Engines Workshop Manual
[x] Cancel search | Manufacturer: FORD, Model Year: 1983, Model line: SIERRA, Model: FORD SIERRA 1983 1.GPages: 24, PDF Size: 1.03 MB
Page 15 of 24
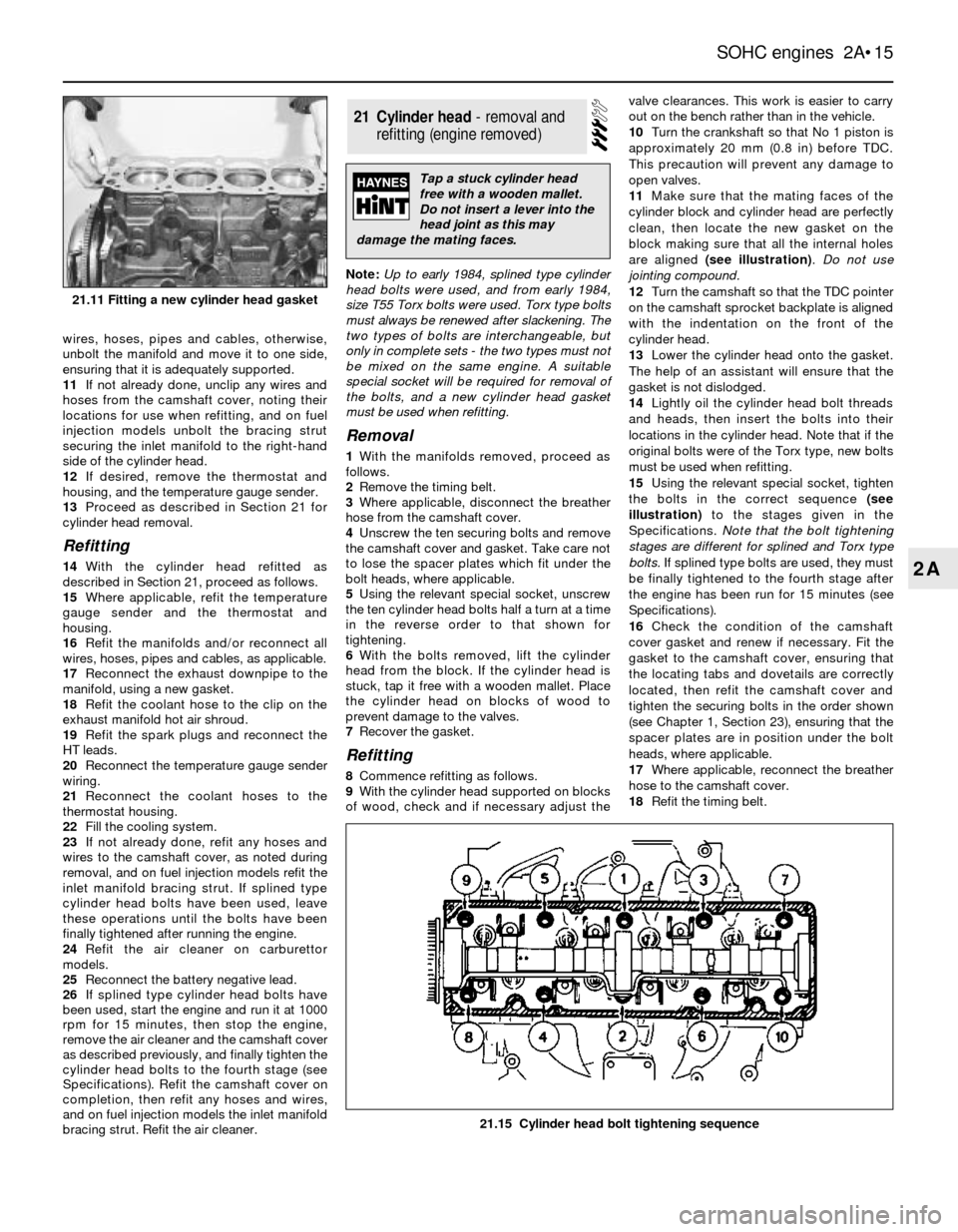
wires, hoses, pipes and cables, otherwise,
unbolt the manifold and move it to one side,
ensuring that it is adequately supported.
11If not already done, unclip any wires and
hoses from the camshaft cover, noting their
locations for use when refitting, and on fuel
injection models unbolt the bracing strut
securing the inlet manifold to the right-hand
side of the cylinder head.
12If desired, remove the thermostat and
housing, and the temperature gauge sender.
13Proceed as described in Section 21 for
cylinder head removal.
Refitting
14With the cylinder head refitted as
described in Section 21, proceed as follows.
15Where applicable, refit the temperature
gauge sender and the thermostat and
housing.
16Refit the manifolds and/or reconnect all
wires, hoses, pipes and cables, as applicable.
17Reconnect the exhaust downpipe to the
manifold, using a new gasket.
18Refit the coolant hose to the clip on the
exhaust manifold hot air shroud.
19Refit the spark plugs and reconnect the
HT leads.
20Reconnect the temperature gauge sender
wiring.
21Reconnect the coolant hoses to the
thermostat housing.
22Fill the cooling system.
23If not already done, refit any hoses and
wires to the camshaft cover, as noted during
removal, and on fuel injection models refit the
inlet manifold bracing strut. If splined type
cylinder head bolts have been used, leave
these operations until the bolts have been
finally tightened after running the engine.
24Refit the air cleaner on carburettor
models.
25Reconnect the battery negative lead.
26If splined type cylinder head bolts have
been used, start the engine and run it at 1000
rpm for 15 minutes, then stop the engine,
remove the air cleaner and the camshaft cover
as described previously, and finally tighten the
cylinder head bolts to the fourth stage (see
Specifications). Refit the camshaft cover on
completion, then refit any hoses and wires,
and on fuel injection models the inlet manifold
bracing strut. Refit the air cleaner.Note: Up to early 1984, splined type cylinder
head bolts were used, and from early 1984,
size T55 Torx bolts were used. Torx type bolts
must always be renewed after slackening. The
two types of bolts are interchangeable, but
only in complete sets - the two types must not
be mixed on the same engine. A suitable
special socket will be required for removal of
the bolts, and a new cylinder head gasket
must be used when refitting.
Removal
1With the manifolds removed, proceed as
follows.
2Remove the timing belt.
3Where applicable, disconnect the breather
hose from the camshaft cover.
4Unscrew the ten securing bolts and remove
the camshaft cover and gasket. Take care not
to lose the spacer plates which fit under the
bolt heads, where applicable.
5Using the relevant special socket, unscrew
the ten cylinder head bolts half a turn at a time
in the reverse order to that shown for
tightening.
6With the bolts removed, lift the cylinder
head from the block. If the cylinder head is
stuck, tap it free with a wooden mallet. Place
the cylinder head on blocks of wood to
prevent damage to the valves.
7Recover the gasket.
Refitting
8Commence refitting as follows.
9With the cylinder head supported on blocks
of wood, check and if necessary adjust thevalve clearances. This work is easier to carry
out on the bench rather than in the vehicle.
10Turn the crankshaft so that No 1 piston is
approximately 20 mm (0.8 in) before TDC.
This precaution will prevent any damage to
open valves.
11Make sure that the mating faces of the
cylinder block and cylinder head are perfectly
clean, then locate the new gasket on the
block making sure that all the internal holes
are aligned (see illustration). Do not use
jointing compound.
12Turn the camshaft so that the TDC pointer
on the camshaft sprocket backplate is aligned
with the indentation on the front of the
cylinder head.
13Lower the cylinder head onto the gasket.
The help of an assistant will ensure that the
gasket is not dislodged.
14Lightly oil the cylinder head bolt threads
and heads, then insert the bolts into their
locations in the cylinder head. Note that if the
original bolts were of the Torx type, new bolts
must be used when refitting.
15Using the relevant special socket, tighten
the bolts in the correct sequence (see
illustration)to the stages given in the
Specifications. Note that the bolt tightening
stages are different for splined and Torx type
bolts. If splined type bolts are used, they must
be finally tightened to the fourth stage after
the engine has been run for 15 minutes (see
Specifications).
16Check the condition of the camshaft
cover gasket and renew if necessary. Fit the
gasket to the camshaft cover, ensuring that
the locating tabs and dovetails are correctly
located, then refit the camshaft cover and
tighten the securing bolts in the order shown
(see Chapter 1, Section 23), ensuring that the
spacer plates are in position under the bolt
heads, where applicable.
17Where applicable, reconnect the breather
hose to the camshaft cover.
18Refit the timing belt.
21Cylinder head - removal and
refitting (engine removed)
SOHC engines 2A¥15
2A
21.15 Cylinder head bolt tightening sequence
21.11 Fitting a new cylinder head gasket
Tap a stuck cylinder head
free with a wooden mallet.
Do not insert a lever into the
head joint as this may
damage the mating faces.
Page 24 of 24
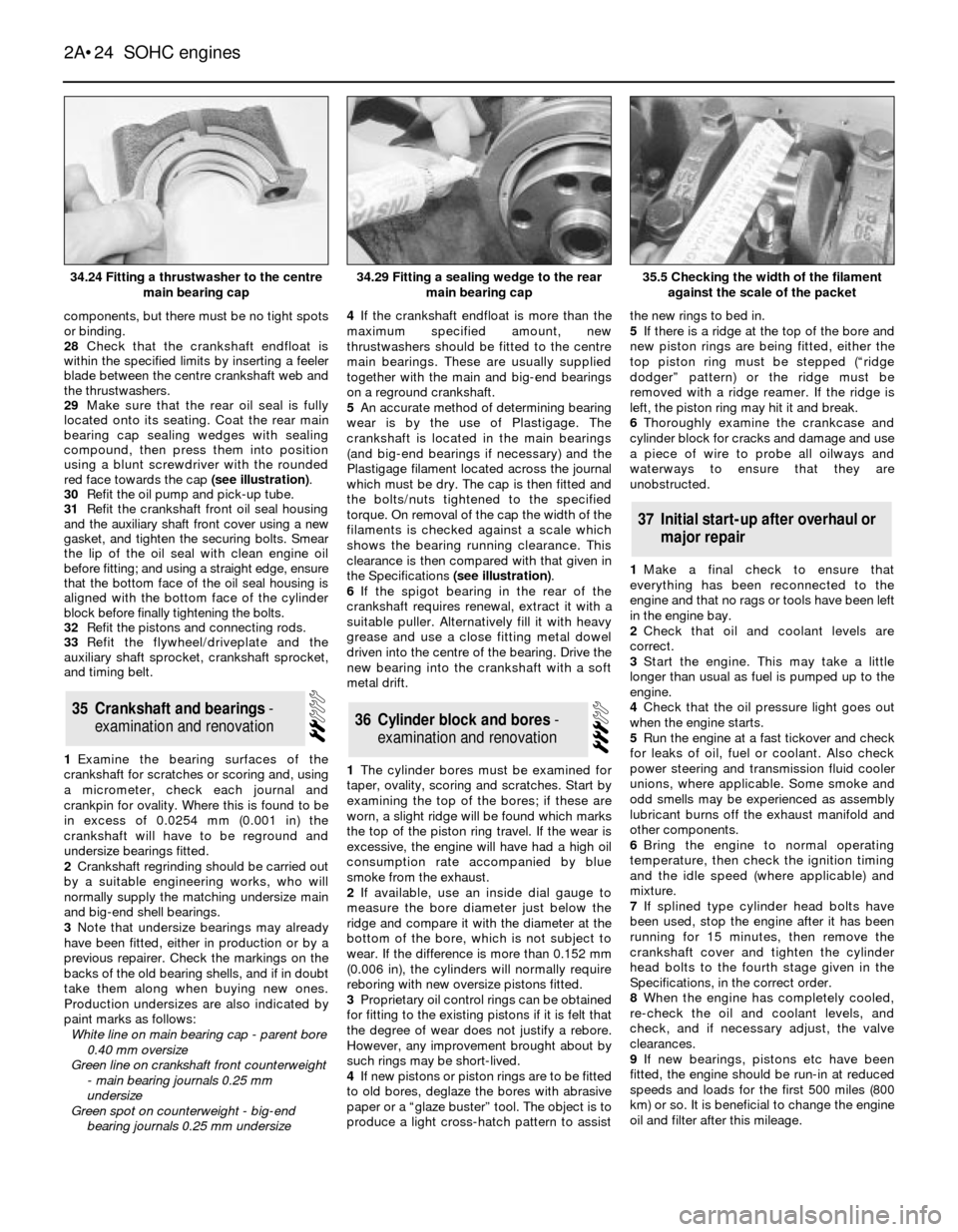
components, but there must be no tight spots
or binding.
28Check that the crankshaft endfloat is
within the specified limits by inserting a feeler
blade between the centre crankshaft web and
the thrustwashers.
29Make sure that the rear oil seal is fully
located onto its seating. Coat the rear main
bearing cap sealing wedges with sealing
compound, then press them into position
using a blunt screwdriver with the rounded
red face towards the cap (see illustration).
30Refit the oil pump and pick-up tube.
31Refit the crankshaft front oil seal housing
and the auxiliary shaft front cover using a new
gasket, and tighten the securing bolts. Smear
the lip of the oil seal with clean engine oil
before fitting; and using a straight edge, ensure
that the bottom face of the oil seal housing is
aligned with the bottom face of the cylinder
block before finally tightening the bolts.
32Refit the pistons and connecting rods.
33Refit the flywheel/driveplate and the
auxiliary shaft sprocket, crankshaft sprocket,
and timing belt.
1Examine the bearing surfaces of the
crankshaft for scratches or scoring and, using
a micrometer, check each journal and
crankpin for ovality. Where this is found to be
in excess of 0.0254 mm (0.001 in) the
crankshaft will have to be reground and
undersize bearings fitted.
2Crankshaft regrinding should be carried out
by a suitable engineering works, who will
normally supply the matching undersize main
and big-end shell bearings.
3Note that undersize bearings may already
have been fitted, either in production or by a
previous repairer. Check the markings on the
backs of the old bearing shells, and if in doubt
take them along when buying new ones.
Production undersizes are also indicated by
paint marks as follows:
White line on main bearing cap - parent bore
0.40 mm oversize
Green line on crankshaft front counterweight
- main bearing journals 0.25 mm
undersize
Green spot on counterweight - big-end
bearing journals 0.25 mm undersize4If the crankshaft endfloat is more than the
maximum specified amount, new
thrustwashers should be fitted to the centre
main bearings. These are usually supplied
together with the main and big-end bearings
on a reground crankshaft.
5An accurate method of determining bearing
wear is by the use of Plastigage. The
crankshaft is located in the main bearings
(and big-end bearings if necessary) and the
Plastigage filament located across the journal
which must be dry. The cap is then fitted and
the bolts/nuts tightened to the specified
torque. On removal of the cap the width of the
filaments is checked against a scale which
shows the bearing running clearance. This
clearance is then compared with that given in
the Specifications (see illustration).
6If the spigot bearing in the rear of the
crankshaft requires renewal, extract it with a
suitable puller. Alternatively fill it with heavy
grease and use a close fitting metal dowel
driven into the centre of the bearing. Drive the
new bearing into the crankshaft with a soft
metal drift.
1The cylinder bores must be examined for
taper, ovality, scoring and scratches. Start by
examining the top of the bores; if these are
worn, a slight ridge will be found which marks
the top of the piston ring travel. If the wear is
excessive, the engine will have had a high oil
consumption rate accompanied by blue
smoke from the exhaust.
2If available, use an inside dial gauge to
measure the bore diameter just below the
ridge and compare it with the diameter at the
bottom of the bore, which is not subject to
wear. If the difference is more than 0.152 mm
(0.006 in), the cylinders will normally require
reboring with new oversize pistons fitted.
3Proprietary oil control rings can be obtained
for fitting to the existing pistons if it is felt that
the degree of wear does not justify a rebore.
However, any improvement brought about by
such rings may be short-lived.
4If new pistons or piston rings are to be fitted
to old bores, deglaze the bores with abrasive
paper or a Òglaze busterÓ tool. The object is to
produce a light cross-hatch pattern to assistthe new rings to bed in.
5If there is a ridge at the top of the bore and
new piston rings are being fitted, either the
top piston ring must be stepped (Òridge
dodgerÓ pattern) or the ridge must be
removed with a ridge reamer. If the ridge is
left, the piston ring may hit it and break.
6Thoroughly examine the crankcase and
cylinder block for cracks and damage and use
a piece of wire to probe all oilways and
waterways to ensurethatthey are
unobstructed.
1Make a final check to ensure that
everything has been reconnected to the
engine and that no rags or tools have been left
in the engine bay.
2Check that oil and coolant levels are
correct.
3Start the engine. This may take a little
longer than usual as fuel is pumped up to the
engine.
4Check that the oil pressure light goes out
when the engine starts.
5Run the engine at a fast tickover and check
for leaks of oil, fuel or coolant. Also check
power steering and transmission fluid cooler
unions, where applicable. Some smoke and
odd smells may be experienced as assembly
lubricant burns off the exhaust manifold and
other components.
6Bring the engine to normal operating
temperature, then check the ignition timing
and the idle speed (where applicable) and
mixture.
7If splined type cylinder head bolts have
been used, stop the engine after it has been
running for 15 minutes, then remove the
crankshaft cover and tighten the cylinder
head bolts to the fourth stage given in the
Specifications, in the correct order.
8When the engine has completely cooled,
re-check the oil and coolant levels, and
check, and if necessary adjust, the valve
clearances.
9If new bearings, pistons etc have been
fitted, the engine should be run-in at reduced
speeds and loads for the first 500 miles (800
km) or so. It is beneficial to change the engine
oil and filter after this mileage.
37Initial start-up after overhaul or
major repair
36Cylinder block and bores -
examination and renovation35Crankshaft and bearings -
examination and renovation
2A¥24SOHC engines
34.24 Fitting a thrustwasher to the centre
main bearing cap35.5 Checking the width of the filament
against the scale of the packet34.29 Fitting a sealing wedge to the rear
main bearing cap