tow FORD SIERRA 1986 1.G CVH Engines Workshop Manual
[x] Cancel search | Manufacturer: FORD, Model Year: 1986, Model line: SIERRA, Model: FORD SIERRA 1986 1.GPages: 24, PDF Size: 1.09 MB
Page 18 of 24
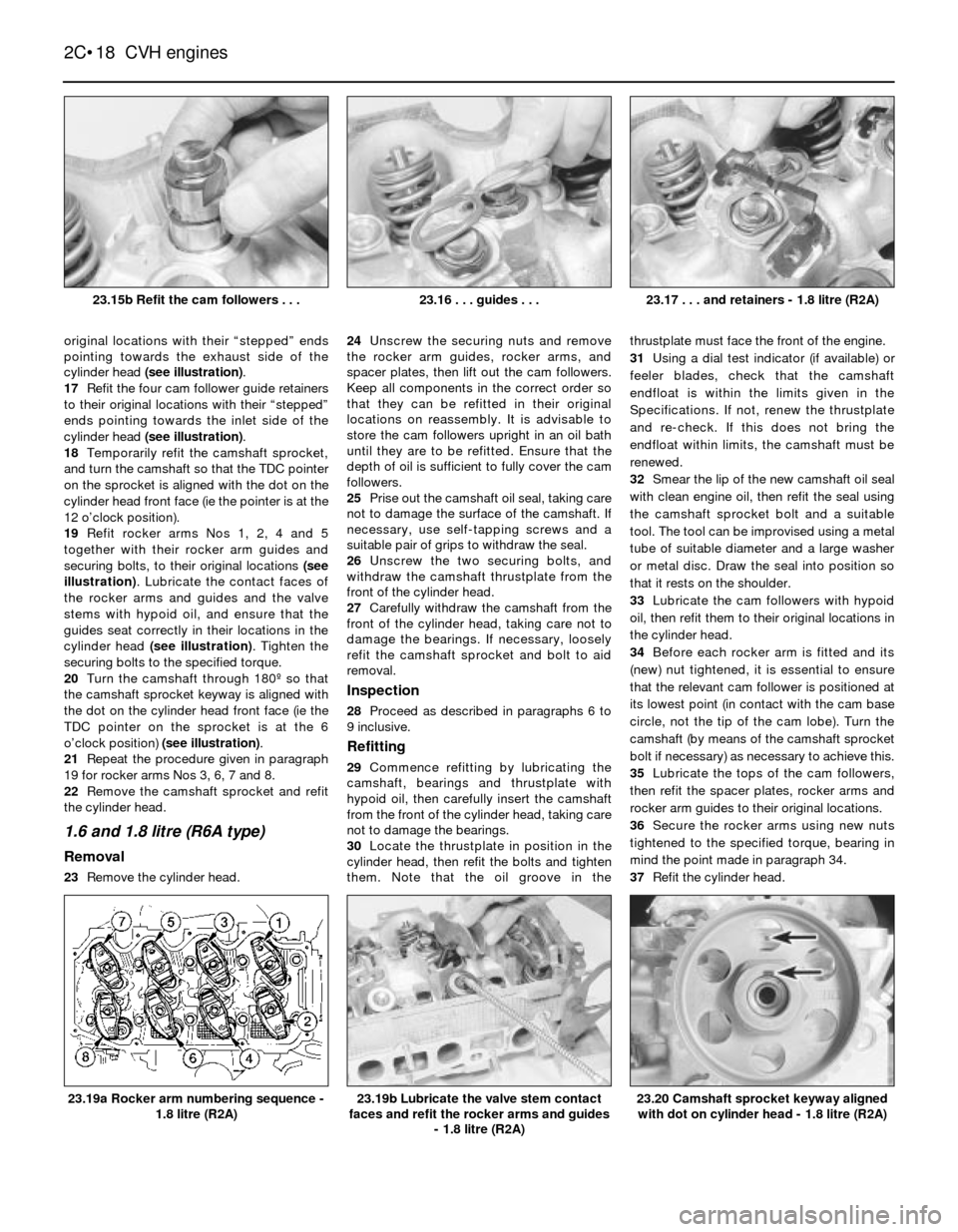
original locations with their “stepped” ends
pointing towards the exhaust side of the
cylinder head (see illustration).
17Refit the four cam follower guide retainers
to their original locations with their “stepped”
ends pointing towards the inlet side of the
cylinder head (see illustration).
18Temporarily refit the camshaft sprocket,
and turn the camshaft so that the TDC pointer
on the sprocket is aligned with the dot on the
cylinder head front face (ie the pointer is at the
12 o’clock position).
19Refit rocker arms Nos 1, 2, 4 and 5
together with their rocker arm guides and
securing bolts, to their original locations (see
illustration). Lubricate the contact faces of
the rocker arms and guides and the valve
stems with hypoid oil, and ensure that the
guides seat correctly in their locations in the
cylinder head (see illustration). Tighten the
securing bolts to the specified torque.
20Turn the camshaft through 180º so that
the camshaft sprocket keyway is aligned with
the dot on the cylinder head front face (ie the
TDC pointer on the sprocket is at the 6
o’clock position) (see illustration).
21Repeat the procedure given in paragraph
19 for rocker arms Nos 3, 6, 7 and 8.
22Remove the camshaft sprocket and refit
the cylinder head.
1.6 and 1.8 litre (R6A type)
Removal
23Remove the cylinder head. 24Unscrew the securing nuts and remove
the rocker arm guides, rocker arms, and
spacer plates, then lift out the cam followers.
Keep all components in the correct order so
that they can be refitted in their original
locations on reassembly. It is advisable to
store the cam followers upright in an oil bath
until they are to be refitted. Ensure that the
depth of oil is sufficient to fully cover the cam
followers.
25Prise out the camshaft oil seal, taking care
not to damage the surface of the camshaft. If
necessary, use self-tapping screws and a
suitable pair of grips to withdraw the seal.
26Unscrew the two securing bolts, and
withdraw the camshaft thrustplate from the
front of the cylinder head.
27Carefully withdraw the camshaft from the
front of the cylinder head, taking care not to
damage the bearings. If necessary, loosely
refit the camshaft sprocket and bolt to aid
removal.
Inspection
28Proceed as described in paragraphs 6 to
9 inclusive.
Refitting
29Commence refitting by lubricating the
camshaft, bearings and thrustplate with
hypoid oil, then carefully insert the camshaft
from the front of the cylinder head, taking care
not to damage the bearings.
30Locate the thrustplate in position in the
cylinder head, then refit the bolts and tighten
them. Note that the oil groove in thethrustplate must face the front of the engine.
31Using a dial test indicator (if available) or
feeler blades, check that the camshaft
endfloat is within the limits given in the
Specifications. If not, renew the thrustplate
and re-check. If this does not bring the
endfloat within limits, the camshaft must be
renewed.
32Smear the lip of the new camshaft oil seal
with clean engine oil, then refit the seal using
the camshaft sprocket bolt and a suitable
tool. The tool can be improvised using a metal
tube of suitable diameter and a large washer
or metal disc. Draw the seal into position so
that it rests on the shoulder.
33Lubricate the cam followers with hypoid
oil, then refit them to their original locations in
the cylinder head.
34Before each rocker arm is fitted and its
(new) nut tightened, it is essential to ensure
that the relevant cam follower is positioned at
its lowest point (in contact with the cam base
circle, not the tip of the cam lobe). Turn the
camshaft (by means of the camshaft sprocket
bolt if necessary) as necessary to achieve this.
35Lubricate the tops of the cam followers,
then refit the spacer plates, rocker arms and
rocker arm guides to their original locations.
36Secure the rocker arms using new nuts
tightened to the specified torque, bearing in
mind the point made in paragraph 34.
37Refit the cylinder head.
2C•18CVH engines
23.17 . . . and retainers - 1.8 litre (R2A)
23.20 Camshaft sprocket keyway aligned
with dot on cylinder head - 1.8 litre (R2A)23.19b Lubricate the valve stem contact
faces and refit the rocker arms and guides
- 1.8 litre (R2A)23.19a Rocker arm numbering sequence -
1.8 litre (R2A)
23.16 . . . guides . . .23.15b Refit the cam followers . . .
Page 23 of 24
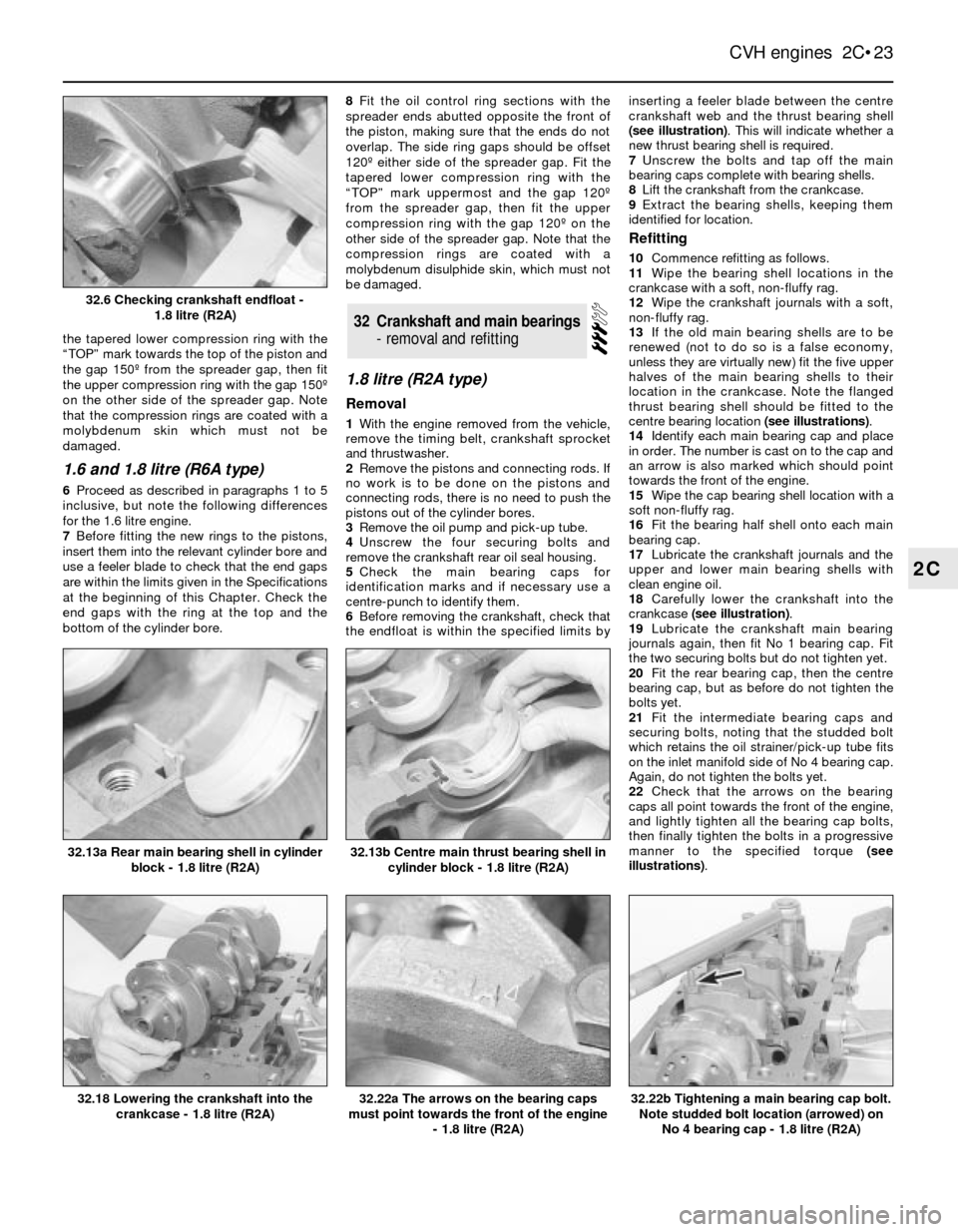
the tapered lower compression ring with the
“TOP” mark towards the top of the piston and
the gap 150º from the spreader gap, then fit
the upper compression ring with the gap 150º
on the other side of the spreader gap. Note
that the compression rings are coated with a
molybdenum skin which must not be
damaged.
1.6 and 1.8 litre (R6A type)
6Proceed as described in paragraphs 1 to 5
inclusive, but note the following differences
for the 1.6 litre engine.
7Before fitting the new rings to the pistons,
insert them into the relevant cylinder bore and
use a feeler blade to check that the end gaps
are within the limits given in the Specifications
at the beginning of this Chapter. Check the
end gaps with the ring at the top and the
bottom of the cylinder bore.8Fit the oil control ring sections with the
spreader ends abutted opposite the front of
the piston, making sure that the ends do not
overlap. The side ring gaps should be offset
120º either side of the spreader gap. Fit the
tapered lower compression ring with the
“TOP” mark uppermost and the gap 120º
from the spreader gap, then fit the upper
compression ring with the gap 120º on the
other side of the spreader gap. Note that the
compression rings are coated with a
molybdenum disulphide skin, which must not
be damaged.
1.8 litre (R2A type)
Removal
1With the engine removed from the vehicle,
remove the timing belt, crankshaft sprocket
and thrustwasher.
2Remove the pistons and connecting rods. If
no work is to be done on the pistons and
connecting rods, there is no need to push the
pistons out of the cylinder bores.
3Remove the oil pump and pick-up tube.
4Unscrew the four securing bolts and
remove the crankshaft rear oil seal housing.
5Check the main bearing caps for
identification marks and if necessary use a
centre-punch to identify them.
6Before removing the crankshaft, check that
the endfloat is within the specified limits byinserting a feeler blade between the centre
crankshaft web and the thrust bearing shell
(see illustration). This will indicate whether a
new thrust bearing shell is required.
7Unscrew the bolts and tap off the main
bearing caps complete with bearing shells.
8Lift the crankshaft from the crankcase.
9Extract the bearing shells, keeping them
identified for location.
Refitting
10Commence refitting as follows.
11Wipe the bearing shell locations in the
crankcase with a soft, non-fluffy rag.
12Wipe the crankshaft journals with a soft,
non-fluffy rag.
13If the old main bearing shells are to be
renewed (not to do so is a false economy,
unless they are virtually new) fit the five upper
halves of the main bearing shells to their
location in the crankcase. Note the flanged
thrust bearing shell should be fitted to the
centre bearing location (see illustrations).
14Identify each main bearing cap and place
in order. The number is cast on to the cap and
an arrow is also marked which should point
towards the front of the engine.
15Wipe the cap bearing shell location with a
soft non-fluffy rag.
16Fit the bearing half shell onto each main
bearing cap.
17Lubricate the crankshaft journals and the
upper and lower main bearing shells with
clean engine oil.
18Carefully lower the crankshaft into the
crankcase (see illustration).
19Lubricate the crankshaft main bearing
journals again, then fit No 1 bearing cap. Fit
the two securing bolts but do not tighten yet.
20Fit the rear bearing cap, then the centre
bearing cap, but as before do not tighten the
bolts yet.
21Fit the intermediate bearing caps and
securing bolts, noting that the studded bolt
which retains the oil strainer/pick-up tube fits
on the inlet manifold side of No 4 bearing cap.
Again, do not tighten the bolts yet.
22Check that the arrows on the bearing
caps all point towards the front of the engine,
and lightly tighten all the bearing cap bolts,
then finally tighten the bolts in a progressive
manner to the specified torque (see
illustrations).
32Crankshaft and main bearings
- removal and refitting
CVH engines 2C•23
2C
32.13b Centre main thrust bearing shell in
cylinder block - 1.8 litre (R2A)
32.22b Tightening a main bearing cap bolt.
Note studded bolt location (arrowed) on
No 4 bearing cap - 1.8 litre (R2A)32.22a The arrows on the bearing caps
must point towards the front of the engine
- 1.8 litre (R2A)32.18 Lowering the crankshaft into the
crankcase - 1.8 litre (R2A)
32.13a Rear main bearing shell in cylinder
block - 1.8 litre (R2A)
32.6 Checking crankshaft endfloat -
1.8 litre (R2A)