headlamp FORD SIERRA 1987 2.G Bodywork And Fittings Workshop Manual
[x] Cancel search | Manufacturer: FORD, Model Year: 1987, Model line: SIERRA, Model: FORD SIERRA 1987 2.GPages: 22, PDF Size: 1.2 MB
Page 3 of 22
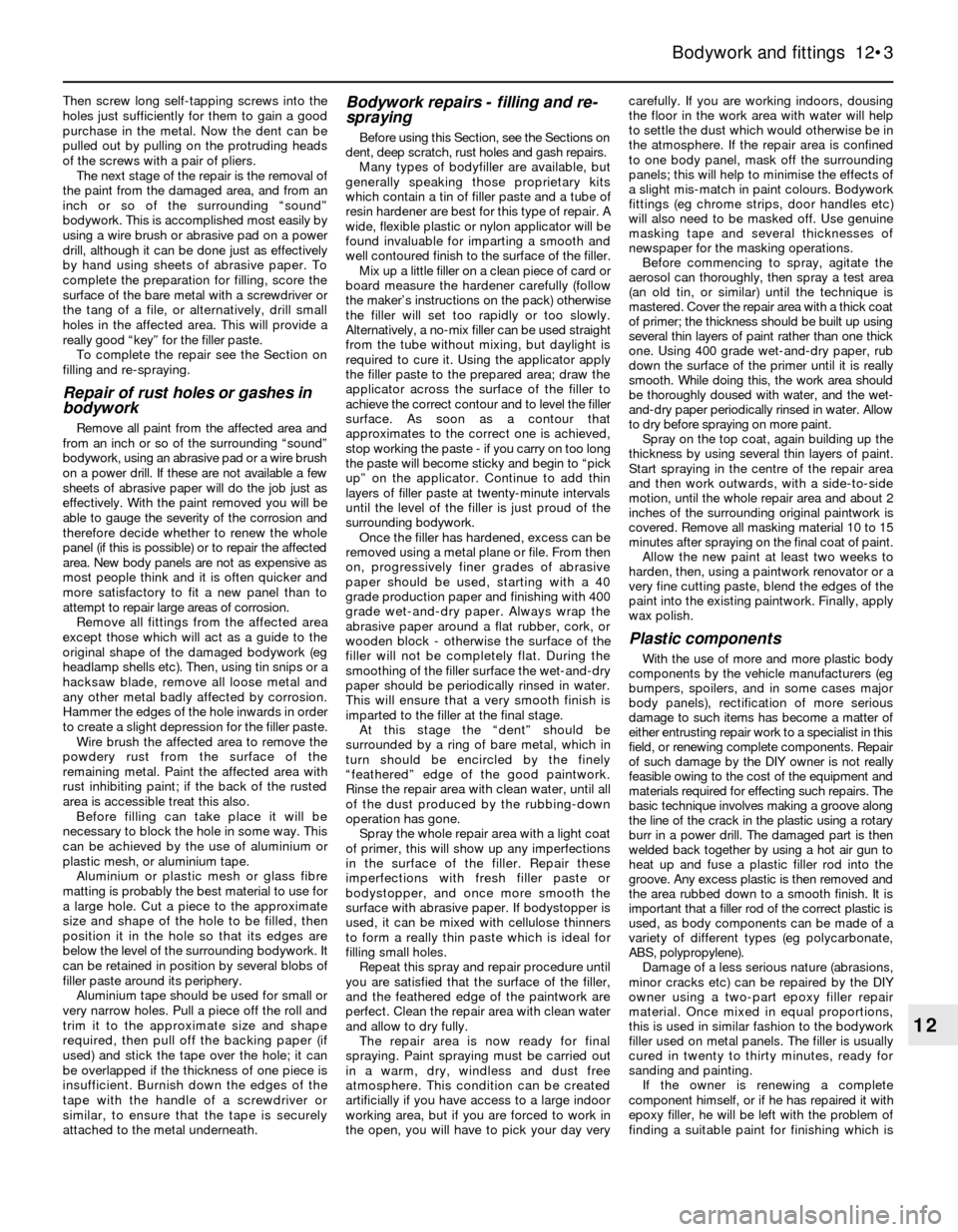
Then screw long self-tapping screws into the
holes just sufficiently for them to gain a good
purchase in the metal. Now the dent can be
pulled out by pulling on the protruding heads
of the screws with a pair of pliers.
The next stage of the repair is the removal of
the paint from the damaged area, and from an
inch or so of the surrounding “sound”
bodywork. This is accomplished most easily by
using a wire brush or abrasive pad on a power
drill, although it can be done just as effectively
by hand using sheets of abrasive paper. To
complete the preparation for filling, score the
surface of the bare metal with a screwdriver or
the tang of a file, or alternatively, drill small
holes in the affected area. This will provide a
really good “key” for the filler paste.
To complete the repair see the Section on
filling and re-spraying.
Repair of rust holes or gashes in
bodywork
Remove all paint from the affected area and
from an inch or so of the surrounding “sound”
bodywork, using an abrasive pad or a wire brush
on a power drill. If these are not available a few
sheets of abrasive paper will do the job just as
effectively. With the paint removed you will be
able to gauge the severity of the corrosion and
therefore decide whether to renew the whole
panel (if this is possible) or to repair the affected
area. New body panels are not as expensive as
most people think and it is often quicker and
more satisfactory to fit a new panel than to
attempt to repair large areas of corrosion.
Remove all fittings from the affected area
except those which will act as a guide to the
original shape of the damaged bodywork (eg
headlamp shells etc). Then, using tin snips or a
hacksaw blade, remove all loose metal and
any other metal badly affected by corrosion.
Hammer the edges of the hole inwards in order
to create a slight depression for the filler paste.
Wire brush the affected area to remove the
powdery rust from the surface of the
remaining metal. Paint the affected area with
rust inhibiting paint; if the back of the rusted
area is accessible treat this also.
Before filling can take place it will be
necessary to block the hole in some way. This
can be achieved by the use of aluminium or
plastic mesh, or aluminium tape.
Aluminium or plastic mesh or glass fibre
matting is probably the best material to use for
a large hole. Cut a piece to the approximate
size and shape of the hole to be filled, then
position it in the hole so that its edges are
below the level of the surrounding bodywork. It
can be retained in position by several blobs of
filler paste around its periphery.
Aluminium tape should be used for small or
very narrow holes. Pull a piece off the roll and
trim it to the approximate size and shape
required, then pull off the backing paper (if
used) and stick the tape over the hole; it can
be overlapped if the thickness of one piece is
insufficient. Burnish down the edges of the
tape with the handle of a screwdriver or
similar, to ensure that the tape is securely
attached to the metal underneath.
Bodywork repairs - filling and re-
spraying
Before using this Section, see the Sections on
dent, deep scratch, rust holes and gash repairs.
Many types of bodyfiller are available, but
generally speaking those proprietary kits
which contain a tin of filler paste and a tube of
resin hardener are best for this type of repair. A
wide, flexible plastic or nylon applicator will be
found invaluable for imparting a smooth and
well contoured finish to the surface of the filler.
Mix up a little filler on a clean piece of card or
board measure the hardener carefully (follow
the maker’s instructions on the pack) otherwise
the filler will set too rapidly or too slowly.
Alternatively, a no-mix filler can be used straight
from the tube without mixing, but daylight is
required to cure it. Using the applicator apply
the filler paste to the prepared area; draw the
applicator across the surface of the filler to
achieve the correct contour and to level the filler
surface. As soon as a contour that
approximates to the correct one is achieved,
stop working the paste - if you carry on too long
the paste will become sticky and begin to “pick
up” on the applicator. Continue to add thin
layers of filler paste at twenty-minute intervals
until the level of the filler is just proud of the
surrounding bodywork.
Once the filler has hardened, excess can be
removed using a metal plane or file. From then
on, progressively finer grades of abrasive
paper should be used, starting with a 40
grade production paper and finishing with 400
grade wet-and-dry paper. Always wrap the
abrasive paper around a flat rubber, cork, or
wooden block - otherwise the surface of the
filler will not be completely flat. During the
smoothing of the filler surface the wet-and-dry
paper should be periodically rinsed in water.
This will ensure that a very smooth finish is
imparted to the filler at the final stage.
At this stage the “dent” should be
surrounded by a ring of bare metal, which in
turn should be encircled by the finely
“feathered” edge of the good paintwork.
Rinse the repair area with clean water, until all
of the dust produced by the rubbing-down
operation has gone.
Spray the whole repair area with a light coat
of primer, this will show up any imperfections
in the surface of the filler. Repair these
imperfections with fresh filler paste or
bodystopper, and once more smooth the
surface with abrasive paper. If bodystopper is
used, it can be mixed with cellulose thinners
to form a really thin paste which is ideal for
filling small holes.
Repeat this spray and repair procedure until
you are satisfied that the surface of the filler,
and the feathered edge of the paintwork are
perfect. Clean the repair area with clean water
and allow to dry fully.
The repair area is now ready for final
spraying. Paint spraying must be carried out
in a warm, dry, windless and dust free
atmosphere. This condition can be created
artificially if you have access to a large indoor
working area, but if you are forced to work in
the open, you will have to pick your day verycarefully. If you are working indoors, dousing
the floor in the work area with water will help
to settle the dust which would otherwise be in
the atmosphere. If the repair area is confined
to one body panel, mask off the surrounding
panels; this willhelp to minimise the effects of
a slight mis-match in paint colours. Bodywork
fittings (eg chrome strips, door handles etc)
will also need to be masked off. Use genuine
masking tape and several thicknesses of
newspaper for the masking operations.
Before commencing to spray, agitate the
aerosol can thoroughly, then spray a test area
(an old tin, or similar) until the technique is
mastered. Cover the repair area with a thick coat
of primer; the thickness should be built up using
several thin layers of paint rather than one thick
one. Using 400 grade wet-and-dry paper, rub
down the surface of the primer until it is really
smooth. While doing this, the work area should
be thoroughly doused with water, and the wet-
and-dry paper periodically rinsed in water. Allow
to dry before spraying on more paint.
Spray on the top coat, again building up the
thickness by using several thin layers of paint.
Start spraying in the centre of the repair area
and then work outwards, with a side-to-side
motion, until the whole repair area and about 2
inches of the surrounding original paintwork is
covered. Remove all masking material 10 to 15
minutes after spraying on the final coat of paint.
Allow the new paint at least two weeks to
harden, then, using a paintwork renovator or a
very fine cutting paste, blend the edges of the
paint into the existing paintwork. Finally, apply
wax polish.
Plastic components
With the use of more and more plastic body
components by the vehicle manufacturers (eg
bumpers, spoilers, and in some cases major
body panels), rectification of more serious
damage to such items has become a matter of
either entrusting repair work to a specialist in this
field, or renewing complete components. Repair
of such damage by the DIY owner is not really
feasible owing to the cost of the equipment and
materials required for effecting such repairs. The
basic technique involves making a groove along
the line of the crack in the plastic using a rotary
burr in a power drill. The damaged part is then
welded back together by using a hot air gun to
heat up and fuse a plastic filler rod into the
groove. Any excess plastic is then removed and
the area rubbed down to a smooth finish. It is
important that a filler rod of the correct plastic is
used, as body components can be made of a
variety of different types (eg polycarbonate,
ABS, polypropylene).
Damage of a less serious nature (abrasions,
minor cracks etc) can be repaired by the DIY
owner using a two-part epoxy filler repair
material. Once mixed in equal proportions,
this is used in similar fashion to the bodywork
filler used on metal panels. The filler is usually
cured in twenty to thirty minutes, ready for
sanding and painting.
If the owner is renewing a complete
component himself, or if he has repaired it with
epoxy filler, he will be left with the problem of
finding a suitable paint for finishing which is
Bodywork and fittings 12•3
12