check engine light FORD SIERRA 1987 2.G CVH Engines Workshop Manual
[x] Cancel search | Manufacturer: FORD, Model Year: 1987, Model line: SIERRA, Model: FORD SIERRA 1987 2.GPages: 24, PDF Size: 1.09 MB
Page 8 of 24
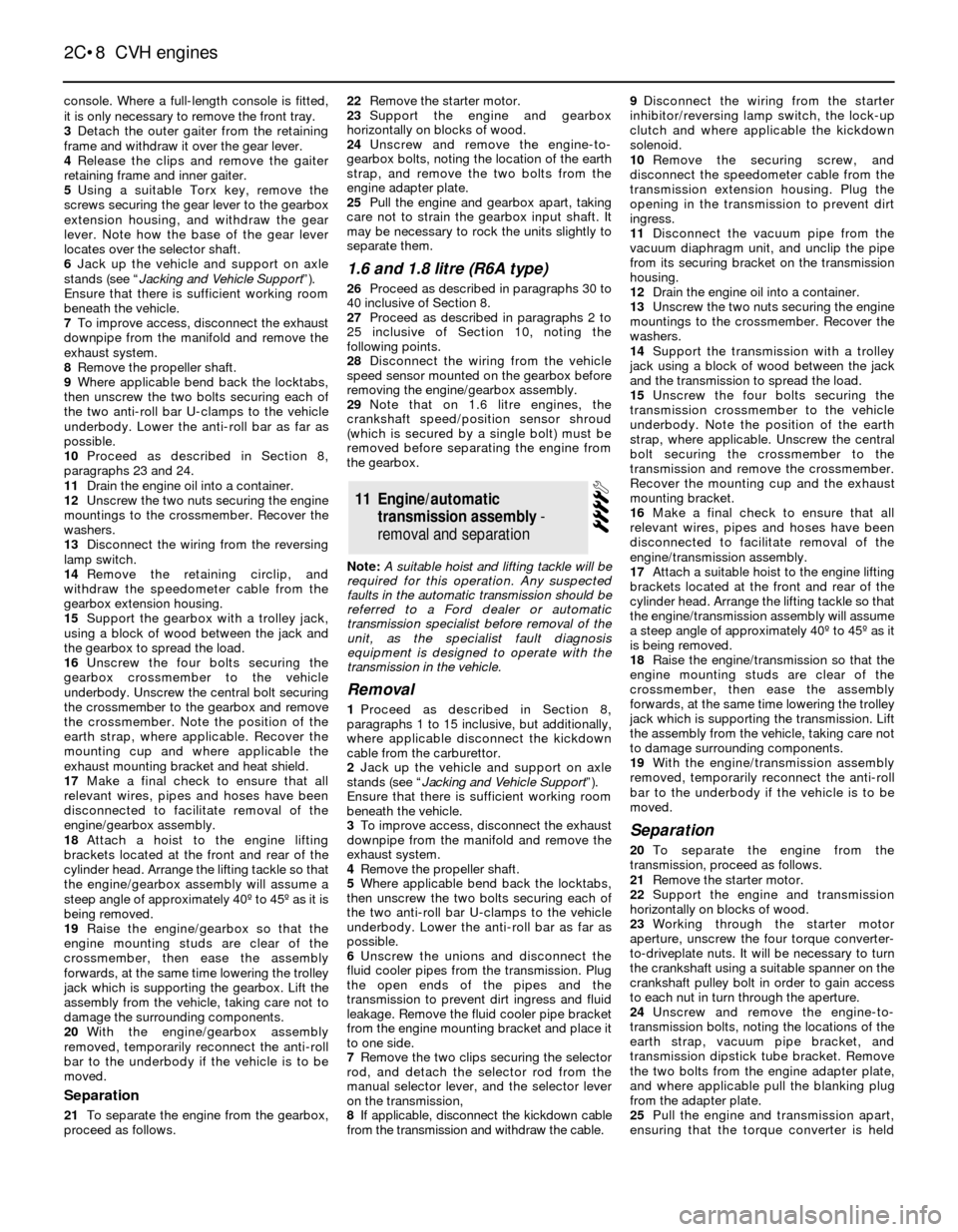
console. Where a full-length console is fitted,
it is only necessary to remove the front tray.
3Detach the outer gaiter from the retaining
frame and withdraw it over the gear lever.
4Release the clips and remove the gaiter
retaining frame and inner gaiter.
5Using a suitable Torx key, remove the
screws securing the gear lever to the gearbox
extension housing, and withdraw the gear
lever. Note how the base of the gear lever
locates over the selector shaft.
6Jack up the vehicle and support on axle
stands (see “Jacking and Vehicle Support”).
Ensure that there is sufficient working room
beneath the vehicle.
7To improve access, disconnect the exhaust
downpipe from the manifold and remove the
exhaust system.
8Remove the propeller shaft.
9Where applicable bend back the locktabs,
then unscrew the two bolts securing each of
the two anti-roll bar U-clamps to the vehicle
underbody. Lower the anti-roll bar as far as
possible.
10Proceed as described in Section 8,
paragraphs 23 and 24.
11Drain the engine oil into a container.
12Unscrew the two nuts securing the engine
mountings to the crossmember. Recover the
washers.
13Disconnect the wiring from the reversing
lamp switch.
14Remove the retaining circlip, and
withdraw the speedometer cable from the
gearbox extension housing.
15Support the gearbox with a trolley jack,
using a block of wood between the jack and
the gearbox to spread the load.
16Unscrew the four bolts securing the
gearbox crossmember to the vehicle
underbody. Unscrew the central bolt securing
the crossmember to the gearbox and remove
the crossmember. Note the position of the
earth strap, where applicable. Recover the
mounting cup and where applicable the
exhaust mounting bracket and heat shield.
17Make a final check to ensure that all
relevant wires, pipes and hoses have been
disconnected to facilitate removal of the
engine/gearbox assembly.
18Attach a hoist to the engine lifting
brackets located at the front and rear of the
cylinder head. Arrange the lifting tackle so that
the engine/gearbox assembly will assume a
steep angle of approximately 40º to 45º as it is
being removed.
19Raise the engine/gearbox so that the
engine mounting studs are clear of the
crossmember, then ease the assembly
forwards, at the same time lowering the trolley
jack which is supporting the gearbox. Lift the
assembly from the vehicle, taking care not to
damage the surrounding components.
20With the engine/gearbox assembly
removed, temporarily reconnect the anti-roll
bar to the underbody if the vehicle is to be
moved.
Separation
21To separate the engine from the gearbox,
proceed as follows. 22Remove the starter motor.
23Support the engine and gearbox
horizontally on blocks of wood.
24Unscrew and remove the engine-to-
gearbox bolts, noting the location of the earth
strap, and remove the two bolts from the
engine adapter plate.
25Pull the engine and gearbox apart, taking
care not to strain the gearbox input shaft. It
may be necessary to rock the units slightly to
separate them.
1.6 and 1.8 litre (R6A type)
26Proceed as described in paragraphs 30 to
40 inclusive of Section 8.
27Proceed as described in paragraphs 2 to
25 inclusive of Section 10, noting the
following points.
28Disconnect the wiring from the vehicle
speed sensor mounted on the gearbox before
removing the engine/gearbox assembly.
29Note that on 1.6 litre engines, the
crankshaft speed/position sensor shroud
(which is secured by a single bolt) must be
removed before separating the engine from
the gearbox.
Note: A suitable hoist and lifting tackle will be
required for this operation. Any suspected
faults in the automatic transmission should be
referred to a Ford dealer or automatic
transmission specialist before removal of the
unit, as the specialist fault diagnosis
equipment is designed to operate with the
transmission in the vehicle.
Removal
1Proceed as described in Section 8,
paragraphs 1 to 15 inclusive, but additionally,
where applicable disconnect the kickdown
cable from the carburettor.
2Jack up the vehicle and support on axle
stands (see “Jacking and Vehicle Support”).
Ensure that there is sufficient working room
beneath the vehicle.
3To improve access, disconnect the exhaust
downpipe from the manifold and remove the
exhaust system.
4Remove the propeller shaft.
5Where applicable bend back the locktabs,
then unscrew the two bolts securing each of
the two anti-roll bar U-clamps to the vehicle
underbody. Lower the anti-roll bar as far as
possible.
6Unscrew the unions and disconnect the
fluid cooler pipes from the transmission. Plug
the open ends of the pipes and the
transmission to prevent dirt ingress and fluid
leakage. Remove the fluid cooler pipe bracket
from the engine mounting bracket and place it
to one side.
7Remove the two clips securing the selector
rod, and detach the selector rod from the
manual selector lever, and the selector lever
on the transmission,
8If applicable, disconnect the kickdown cable
from the transmission and withdraw the cable.9Disconnect the wiring from the starter
inhibitor/reversing lamp switch, the lock-up
clutch and where applicable the kickdown
solenoid.
10Remove the securing screw, and
disconnect the speedometer cable from the
transmission extension housing. Plug the
opening in the transmission to prevent dirt
ingress.
11Disconnect the vacuum pipe from the
vacuum diaphragm unit, and unclip the pipe
from its securing bracket on the transmission
housing.
12Drain the engine oil into a container.
13Unscrew the two nuts securing the engine
mountings to the crossmember. Recover the
washers.
14Support the transmission with a trolley
jack using a block of wood between the jack
and the transmission to spread the load.
15Unscrew the four bolts securing the
transmission crossmember to the vehicle
underbody. Note the position of the earth
strap, where applicable. Unscrew the central
bolt securing the crossmember to the
transmission and remove the crossmember.
Recover the mounting cup and the exhaust
mounting bracket.
16Make a final check to ensure that all
relevant wires, pipes and hoses have been
disconnected to facilitate removal of the
engine/transmission assembly.
17Attach a suitable hoist to the engine lifting
brackets located at the front and rear of the
cylinder head. Arrange the lifting tackle so that
the engine/transmission assembly will assume
a steep angle of approximately 40º to 45º as it
is being removed.
18Raise the engine/transmission so that the
engine mounting studs are clear of the
crossmember, then ease the assembly
forwards, at the same time lowering the trolley
jack which is supporting the transmission. Lift
the assembly from the vehicle, taking care not
to damage surrounding components.
19With the engine/transmission assembly
removed, temporarily reconnect the anti-roll
bar to the underbody if the vehicle is to be
moved.
Separation
20To separate the engine from the
transmission, proceed as follows.
21Remove the starter motor.
22Support the engine and transmission
horizontally on blocks of wood.
23Working through the starter motor
aperture, unscrew the four torque converter-
to-driveplate nuts. It will be necessary to turn
the crankshaft using a suitable spanner on the
crankshaft pulley bolt in order to gain access
to each nut in turn through the aperture.
24Unscrew and remove the engine-to-
transmission bolts, noting the locations of the
earth strap, vacuum pipe bracket, and
transmission dipstick tube bracket. Remove
the two bolts from the engine adapter plate,
and where applicable pull the blanking plug
from the adapter plate.
25Pull the engine and transmission apart,
ensuring that the torque converter is held
11Engine/automatic
transmission assembly -
removal and separation
2C•8CVH engines
Page 9 of 24
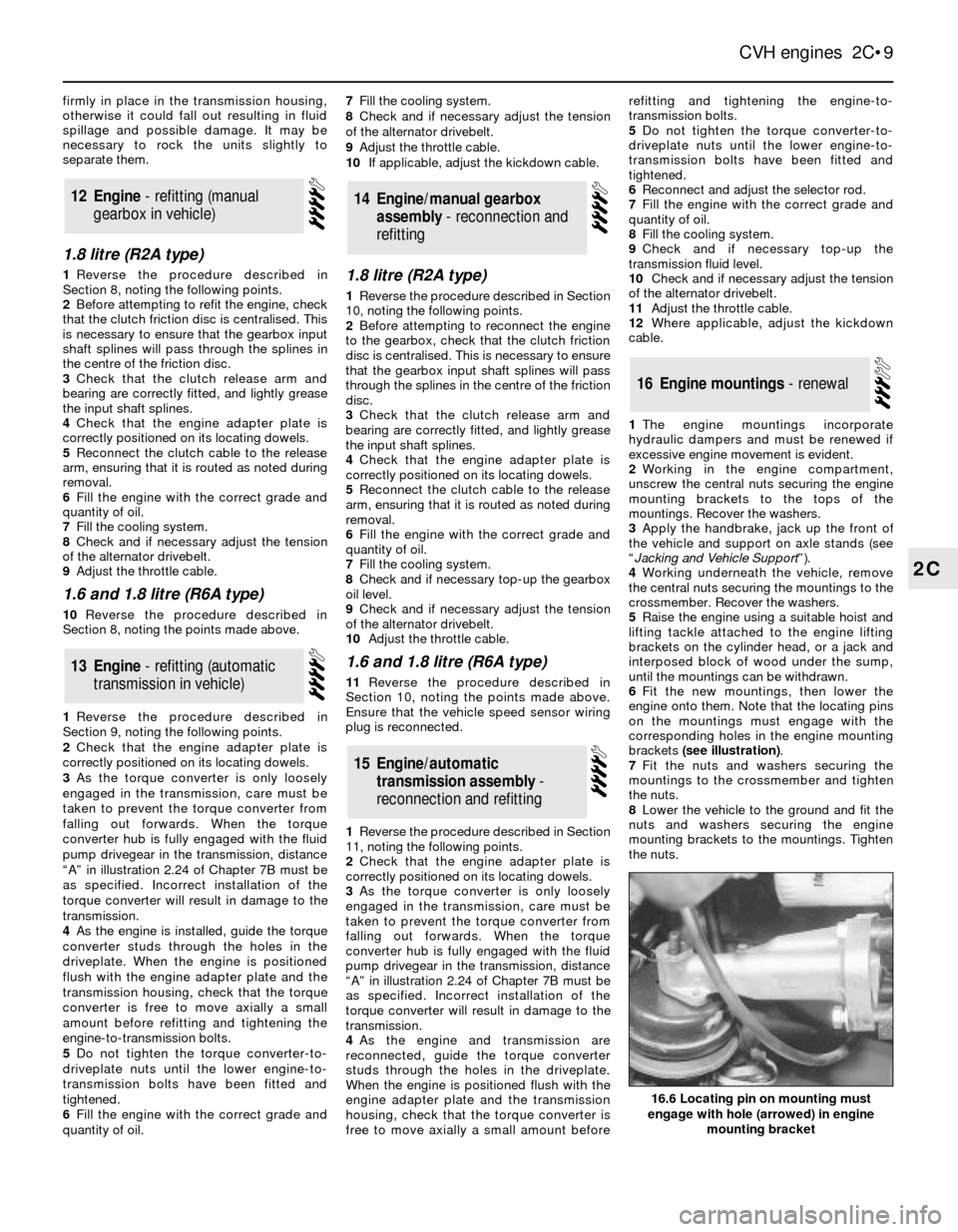
firmly in place in the transmission housing,
otherwise it could fall out resulting in fluid
spillage and possible damage. It may be
necessary to rock the units slightly to
separate them.
1.8 litre (R2A type)
1Reverse the procedure described in
Section 8, noting the following points.
2Before attempting to refit the engine, check
that the clutch friction disc is centralised. This
is necessary to ensure that the gearbox input
shaft splines will pass through the splines in
the centre of the friction disc.
3Check that the clutch release arm and
bearing are correctly fitted, and lightly grease
the input shaft splines.
4Check that the engine adapter plate is
correctly positioned on its locating dowels.
5Reconnect the clutch cable to the release
arm, ensuring that it is routed as noted during
removal.
6Fill the engine with the correct grade and
quantity of oil.
7Fill the cooling system.
8Check and if necessary adjust the tension
of the alternator drivebelt.
9Adjust the throttle cable.
1.6 and 1.8 litre (R6A type)
10Reverse the procedure described in
Section 8, noting the points made above.
1Reverse the procedure described in
Section 9, noting the following points.
2Check that the engine adapter plate is
correctly positioned on its locating dowels.
3As the torque converter is only loosely
engaged in the transmission, care must be
taken to prevent the torque converter from
falling out forwards. When the torque
converter hub is fully engaged with the fluid
pump drivegear in the transmission, distance
“A” in illustration 2.24 of Chapter 7B must be
as specified. Incorrect installation of the
torque converter will result in damage to the
transmission.
4As the engine is installed, guide the torque
converter studs through the holes in the
driveplate. When the engine is positioned
flush with the engine adapter plate and the
transmission housing, check that the torque
converter is free to move axially a small
amount before refitting and tightening the
engine-to-transmission bolts.
5Do not tighten the torque converter-to-
driveplate nuts until the lower engine-to-
transmission bolts have been fitted and
tightened.
6Fill the engine with the correct grade and
quantity of oil. 7Fill the cooling system.
8Check and if necessary adjust the tension
of the alternator drivebelt.
9Adjust the throttle cable.
10If applicable, adjust the kickdown cable.
1.8 litre (R2A type)
1Reverse the procedure described in Section
10, noting the following points.
2Before attempting to reconnect the engine
to the gearbox, check that the clutch friction
disc is centralised. This is necessary to ensure
that the gearbox input shaft splines will pass
through the splines in the centre of the friction
disc.
3Check that the clutch release arm and
bearing are correctly fitted, and lightly grease
the input shaft splines.
4Check that the engine adapter plate is
correctly positioned on its locating dowels.
5Reconnect the clutch cable to the release
arm, ensuring that it is routed as noted during
removal.
6Fill the engine with the correct grade and
quantity of oil.
7Fill the cooling system.
8Check and if necessary top-up the gearbox
oil level.
9Check and if necessary adjust the tension
of the alternator drivebelt.
10Adjust the throttle cable.
1.6 and 1.8 litre (R6A type)
11Reverse the procedure described in
Section 10, noting the points made above.
Ensure that the vehicle speed sensor wiring
plug is reconnected.
1Reverse the procedure described in Section
11, noting the following points.
2Check that the engine adapter plate is
correctly positioned on its locating dowels.
3As the torque converter is only loosely
engaged in the transmission, care must be
taken to prevent the torque converter from
falling out forwards. When the torque
converter hub is fully engaged with the fluid
pump drivegear in the transmission, distance
“A” in illustration 2.24 of Chapter 7B must be
as specified. Incorrect installation of the
torque converter will result in damage to the
transmission.
4As the engine and transmission are
reconnected, guide the torque converter
studs through the holes in the driveplate.
When the engine is positioned flush with the
engine adapter plate and the transmission
housing, check that the torque converter is
free to move axially a small amount beforerefitting and tightening the engine-to-
transmission bolts.
5Do not tighten the torque converter-to-
driveplate nuts until the lower engine-to-
transmission bolts have been fitted and
tightened.
6Reconnect and adjust the selector rod.
7Fill the engine with the correct grade and
quantity of oil.
8Fill the cooling system.
9Check and if necessary top-up the
transmission fluid level.
10Check and if necessary adjust the tension
of the alternator drivebelt.
11Adjust the throttle cable.
12Where applicable, adjust the kickdown
cable.
1The engine mountings incorporate
hydraulic dampers and must be renewed if
excessive engine movement is evident.
2Working in the engine compartment,
unscrew the central nuts securing the engine
mounting brackets to the tops of the
mountings. Recover the washers.
3Apply the handbrake, jack up the front of
the vehicle and support on axle stands (see
“Jacking and Vehicle Support”).
4Working underneath the vehicle, remove
the central nuts securing the mountings to the
crossmember. Recover the washers.
5Raise the engine using a suitable hoist and
lifting tackle attached to the engine lifting
brackets on the cylinder head, or a jack and
interposed block of wood under the sump,
until the mountings can be withdrawn.
6Fit the new mountings, then lower the
engine onto them. Note that the locating pins
on the mountings must engage with the
corresponding holes in the engine mounting
brackets (see illustration).
7Fit the nuts and washers securing the
mountings to the crossmember and tighten
the nuts.
8Lower the vehicle to the ground and fit the
nuts and washers securing the engine
mounting brackets to the mountings. Tighten
the nuts.
16Engine mountings - renewal
15Engine/automatic
transmission assembly -
reconnection and refitting
14Engine/manual gearbox
assembly - reconnection and
refitting
13Engine - refitting (automatic
transmission in vehicle)
12Engine - refitting (manual
gearbox in vehicle)
CVH engines 2C•9
2C
16.6 Locating pin on mounting must
engage with hole (arrowed) in engine
mounting bracket
Page 23 of 24
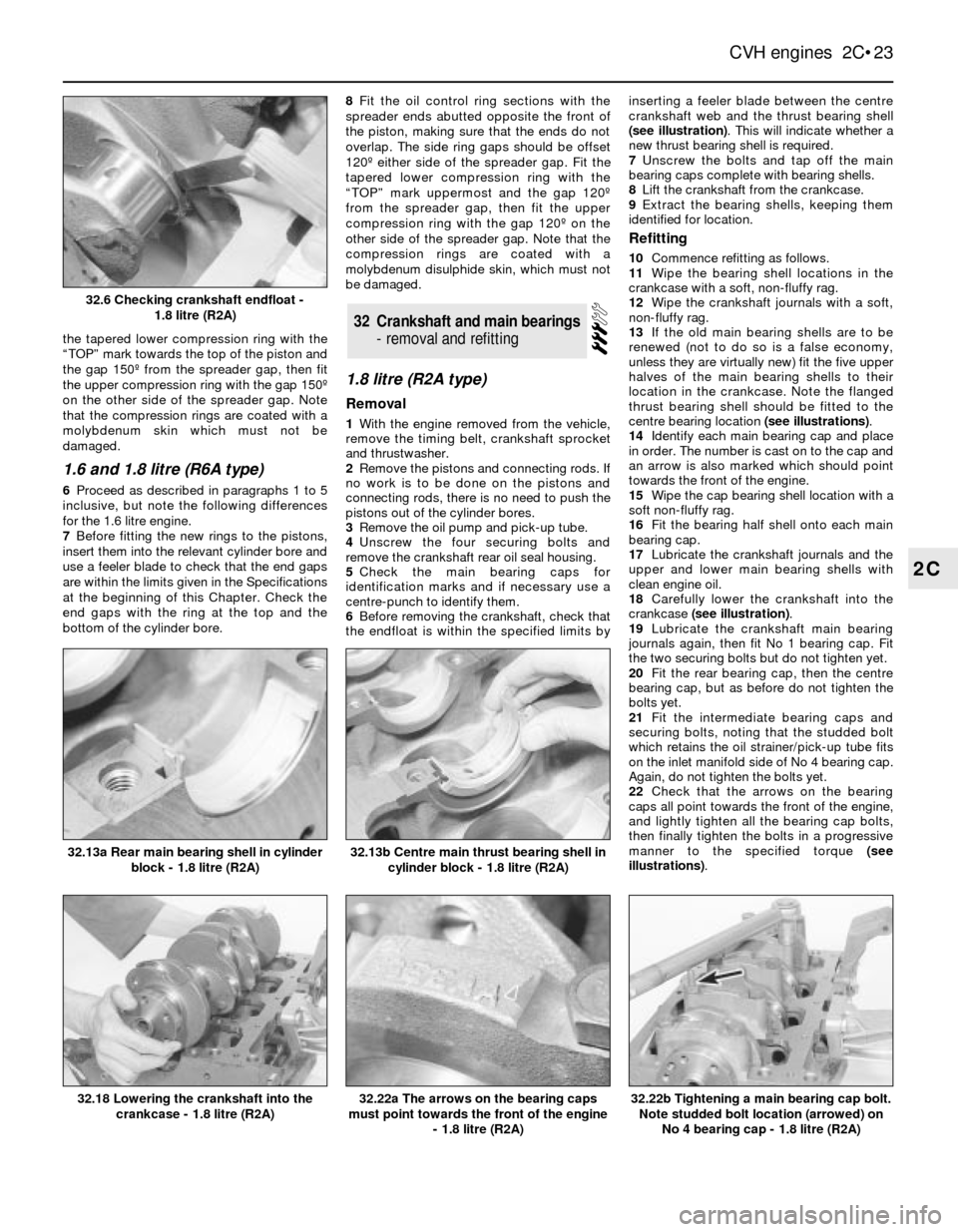
the tapered lower compression ring with the
“TOP” mark towards the top of the piston and
the gap 150º from the spreader gap, then fit
the upper compression ring with the gap 150º
on the other side of the spreader gap. Note
that the compression rings are coated with a
molybdenum skin which must not be
damaged.
1.6 and 1.8 litre (R6A type)
6Proceed as described in paragraphs 1 to 5
inclusive, but note the following differences
for the 1.6 litre engine.
7Before fitting the new rings to the pistons,
insert them into the relevant cylinder bore and
use a feeler blade to check that the end gaps
are within the limits given in the Specifications
at the beginning of this Chapter. Check the
end gaps with the ring at the top and the
bottom of the cylinder bore.8Fit the oil control ring sections with the
spreader ends abutted opposite the front of
the piston, making sure that the ends do not
overlap. The side ring gaps should be offset
120º either side of the spreader gap. Fit the
tapered lower compression ring with the
“TOP” mark uppermost and the gap 120º
from the spreader gap, then fit the upper
compression ring with the gap 120º on the
other side of the spreader gap. Note that the
compression rings are coated with a
molybdenum disulphide skin, which must not
be damaged.
1.8 litre (R2A type)
Removal
1With the engine removed from the vehicle,
remove the timing belt, crankshaft sprocket
and thrustwasher.
2Remove the pistons and connecting rods. If
no work is to be done on the pistons and
connecting rods, there is no need to push the
pistons out of the cylinder bores.
3Remove the oil pump and pick-up tube.
4Unscrew the four securing bolts and
remove the crankshaft rear oil seal housing.
5Check the main bearing caps for
identification marks and if necessary use a
centre-punch to identify them.
6Before removing the crankshaft, check that
the endfloat is within the specified limits byinserting a feeler blade between the centre
crankshaft web and the thrust bearing shell
(see illustration). This will indicate whether a
new thrust bearing shell is required.
7Unscrew the bolts and tap off the main
bearing caps complete with bearing shells.
8Lift the crankshaft from the crankcase.
9Extract the bearing shells, keeping them
identified for location.
Refitting
10Commence refitting as follows.
11Wipe the bearing shell locations in the
crankcase with a soft, non-fluffy rag.
12Wipe the crankshaft journals with a soft,
non-fluffy rag.
13If the old main bearing shells are to be
renewed (not to do so is a false economy,
unless they are virtually new) fit the five upper
halves of the main bearing shells to their
location in the crankcase. Note the flanged
thrust bearing shell should be fitted to the
centre bearing location (see illustrations).
14Identify each main bearing cap and place
in order. The number is cast on to the cap and
an arrow is also marked which should point
towards the front of the engine.
15Wipe the cap bearing shell location with a
soft non-fluffy rag.
16Fit the bearing half shell onto each main
bearing cap.
17Lubricate the crankshaft journals and the
upper and lower main bearing shells with
clean engine oil.
18Carefully lower the crankshaft into the
crankcase (see illustration).
19Lubricate the crankshaft main bearing
journals again, then fit No 1 bearing cap. Fit
the two securing bolts but do not tighten yet.
20Fit the rear bearing cap, then the centre
bearing cap, but as before do not tighten the
bolts yet.
21Fit the intermediate bearing caps and
securing bolts, noting that the studded bolt
which retains the oil strainer/pick-up tube fits
on the inlet manifold side of No 4 bearing cap.
Again, do not tighten the bolts yet.
22Check that the arrows on the bearing
caps all point towards the front of the engine,
and lightly tighten all the bearing cap bolts,
then finally tighten the bolts in a progressive
manner to the specified torque (see
illustrations).
32Crankshaft and main bearings
- removal and refitting
CVH engines 2C•23
2C
32.13b Centre main thrust bearing shell in
cylinder block - 1.8 litre (R2A)
32.22b Tightening a main bearing cap bolt.
Note studded bolt location (arrowed) on
No 4 bearing cap - 1.8 litre (R2A)32.22a The arrows on the bearing caps
must point towards the front of the engine
- 1.8 litre (R2A)32.18 Lowering the crankshaft into the
crankcase - 1.8 litre (R2A)
32.13a Rear main bearing shell in cylinder
block - 1.8 litre (R2A)
32.6 Checking crankshaft endfloat -
1.8 litre (R2A)