air filter FORD SIERRA 1992 2.G Reference Workshop Manual
[x] Cancel search | Manufacturer: FORD, Model Year: 1992, Model line: SIERRA, Model: FORD SIERRA 1992 2.GPages: 26, PDF Size: 0.57 MB
Page 3 of 26
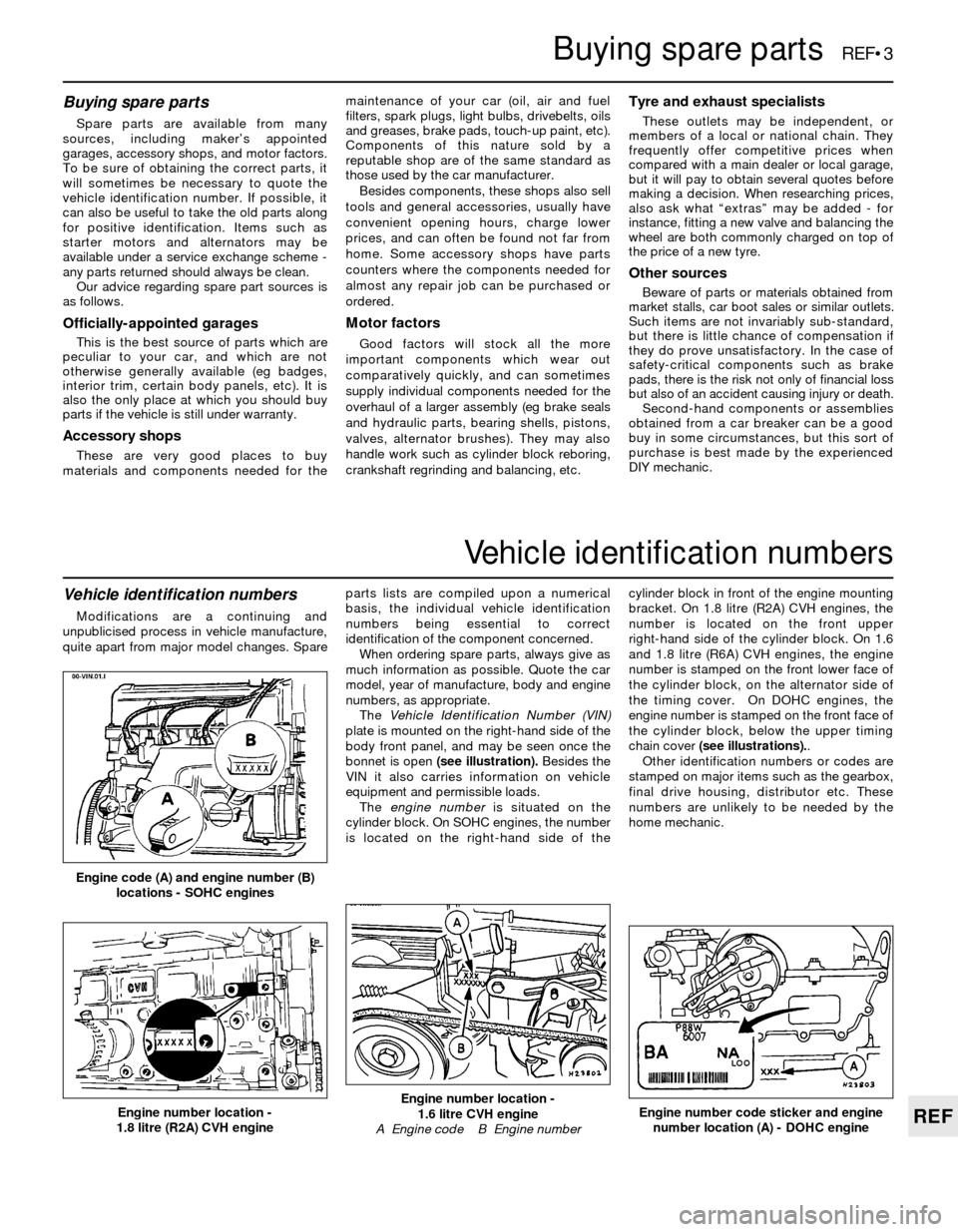
Buying spare parts
Spare parts are available from many
sources, including maker’s appointed
garages, accessory shops, and motor factors.
To be sure of obtaining the correct parts, it
will sometimes be necessary to quote the
vehicle identification number. If possible, it
can also be useful to take the old parts along
for positive identification. Items such as
starter motors and alternators may be
available under a service exchange scheme -
any parts returned should always be clean.
Our advice regarding spare part sources is
as follows.
Officially-appointed garages
This is the best source of parts which are
peculiar to your car, and which are not
otherwise generally available (eg badges,
interior trim, certain body panels, etc). It is
also the only place at which you should buy
parts if the vehicle is still under warranty.
Accessory shops
These are very good places to buy
materials and components needed for themaintenance of your car (oil, air and fuel
filters, spark plugs, light bulbs, drivebelts, oils
and greases, brake pads, touch-up paint, etc).
Components of this nature sold by a
reputable shop are of the same standard as
those used by the car manufacturer.
Besides components, these shops also sell
tools and general accessories, usually have
convenient opening hours, charge lower
prices, and can often be found not far from
home. Some accessory shops have parts
counters where the components needed for
almost any repair job can be purchased or
ordered.
Motor factors
Good factors will stock all the more
important components which wear out
comparatively quickly, and can sometimes
supply individual components needed for the
overhaul of a larger assembly (eg brake seals
and hydraulic parts, bearing shells, pistons,
valves, alternator brushes). They may also
handle work such as cylinder block reboring,
crankshaft regrinding and balancing, etc.
Tyre and exhaust specialists
These outlets may be independent, or
members of a local or national chain. They
frequently offer competitive prices when
compared with a main dealer or local garage,
but it will pay to obtain several quotes before
making a decision. When researching prices,
also ask what “extras” may be added - for
instance, fitting a new valve and balancing the
wheel are both commonly charged on top of
the price of a new tyre.
Other sources
Beware of parts or materials obtained from
market stalls, car boot sales or similar outlets.
Such items are not invariably sub-standard,
but there is little chance of compensation if
they do prove unsatisfactory. In the case of
safety-critical components such as brake
pads, there is the risk not only of financial loss
but also of an accident causing injury or death.
Second-hand components or assemblies
obtained from a car breaker can be a good
buy in some circumstances, but this sort of
purchase is best made by the experienced
DIY mechanic.
Vehicle identification numbers
Modifications are a continuing and
unpublicised process in vehicle manufacture,
quite apart from major model changes. Spareparts lists are compiled upon a numerical
basis, the individual vehicle identification
numbers being essential to correct
identification of the component concerned.
When ordering spare parts, always give as
much information as possible. Quote the car
model, year of manufacture, body and engine
numbers, as appropriate.
The Vehicle Identification Number (VIN)
plate is mounted on the right-hand side of the
body front panel, and may be seen once the
bonnet is open (see illustration).Besides the
VIN it also carries information on vehicle
equipment and permissible loads.
The engine numberis situated on the
cylinder block. On SOHC engines, the number
is located on the right-hand side of thecylinder block in front of the engine mounting
bracket. On 1.8 litre (R2A) CVH engines, the
number is located on the front upper
right-hand side of the cylinder block. On 1.6
and 1.8 litre (R6A) CVH engines, the engine
number is stamped on the front lower face of
the cylinder block, on the alternator side of
the timing cover. On DOHC engines, the
engine number is stamped on the front face of
the cylinder block, below the upper timing
chain cover (see illustrations)..
Other identification numbers or codes are
stamped on major items such as the gearbox,
final drive housing, distributor etc. These
numbers are unlikely to be needed by the
home mechanic.
Buying spare parts REF•3
Engine code (A) and engine number (B)
locations - SOHC engines
Engine number location -
1.8 litre (R2A) CVH engineEngine number code sticker and engine
number location (A) - DOHC engineEngine number location -
1.6 litre CVH engine
A Engine code B Engine number
REF
Vehicle identification numbers
Page 5 of 26
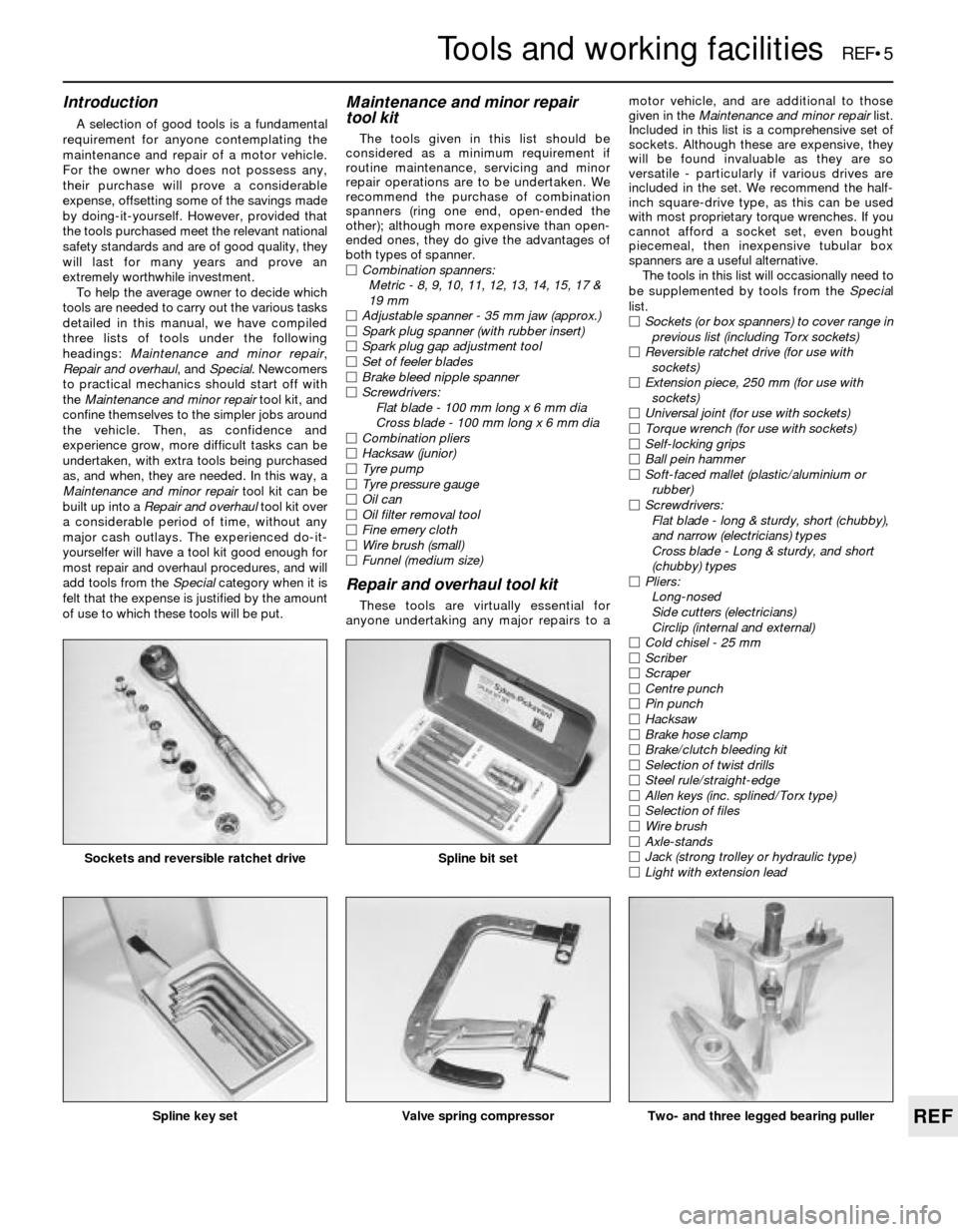
Introduction
A selection of good tools is a fundamental
requirement for anyone contemplating the
maintenance and repair of a motor vehicle.
For the owner who does not possess any,
their purchase will prove a considerable
expense, offsetting some of the savings made
by doing-it-yourself. However, provided that
the tools purchased meet the relevant national
safety standards and are of good quality, they
will last for many years and prove an
extremely worthwhile investment.
To help the average owner to decide which
tools are needed to carry out the various tasks
detailed in this manual, we have compiled
three lists of tools under the following
headings: Maintenance and minor repair,
Repair and overhaul, and Special. Newcomers
to practical mechanics should start off with
the Maintenance and minor repairtool kit, and
confine themselves to the simpler jobs around
the vehicle. Then, as confidence and
experience grow, more difficult tasks can be
undertaken, with extra tools being purchased
as, and when, they are needed. In this way, a
Maintenance and minor repairtool kit can be
built up into a Repair and overhaultool kit over
a considerable period of time, without any
major cash outlays. The experienced do-it-
yourselfer will have a tool kit good enough for
most repair and overhaul procedures, and will
add tools from the Specialcategory when it is
felt that the expense is justified by the amount
of use to which these tools will be put.
Maintenance and minor repair
tool kit
The tools given in this list should be
considered as a minimum requirement if
routine maintenance, servicing and minor
repair operations are to be undertaken. We
recommend the purchase of combination
spanners (ring one end, open-ended the
other); although more expensive than open-
ended ones, they do give the advantages of
both types of spanner.
MCombination spanners:
Metric - 8, 9, 10, 11, 12, 13, 14, 15, 17 &
19 mm
MAdjustable spanner - 35 mm jaw (approx.)
MSpark plug spanner (with rubber insert)
MSpark plug gap adjustment tool
MSet of feeler blades
MBrake bleed nipple spanner
MScrewdrivers:
Flat blade - 100 mm long x 6 mm dia
Cross blade - 100 mm long x 6 mm dia
MCombination pliers
MHacksaw (junior)
MTyre pump
MTyre pressure gauge
MOil can
MOil filter removal tool
MFine emery cloth
MWire brush (small)
MFunnel (medium size)
Repair and overhaul tool kit
These tools are virtually essential for
anyone undertaking any major repairs to amotor vehicle, and are additional to those
given in the Maintenance and minor repairlist.
Included in this list is a comprehensive set of
sockets. Although these are expensive, they
will be found invaluable as they are so
versatile - particularly if various drives are
included in the set. We recommend the half-
inch square-drive type, as this can be used
with most proprietary torque wrenches. If you
cannot afford a socket set, even bought
piecemeal, then inexpensive tubular box
spanners are a useful alternative.
The tools in this list will occasionally need to
be supplemented by tools from the Special
list.
MSockets (or box spanners) to cover range in
previous list (including Torx sockets)
MReversible ratchet drive (for use with
sockets)
MExtension piece, 250 mm (for use with
sockets)
MUniversal joint (for use with sockets)
MTorque wrench (for use with sockets)
MSelf-locking grips
MBall pein hammer
MSoft-faced mallet (plastic/aluminium or
rubber)
MScrewdrivers:
Flat blade - long & sturdy, short (chubby),
and narrow (electricians) types
Cross blade - Long & sturdy, and short
(chubby) types
MPliers:
Long-nosed
Side cutters (electricians)
Circlip (internal and external)
MCold chisel - 25 mm
MScriber
MScraper
MCentre punch
MPin punch
MHacksaw
MBrake hose clamp
MBrake/clutch bleeding kit
MSelection of twist drills
MSteel rule/straight-edge
MAllen keys (inc. splined/Torx type)
MSelection of files
MWire brush
MAxle-stands
MJack (strong trolley or hydraulic type)
MLight with extension lead
Tools and working facilities REF•5
Sockets and reversible ratchet driveSpline bit set
Spline key setValve spring compressorTwo- and three legged bearing pullerREF
Page 10 of 26
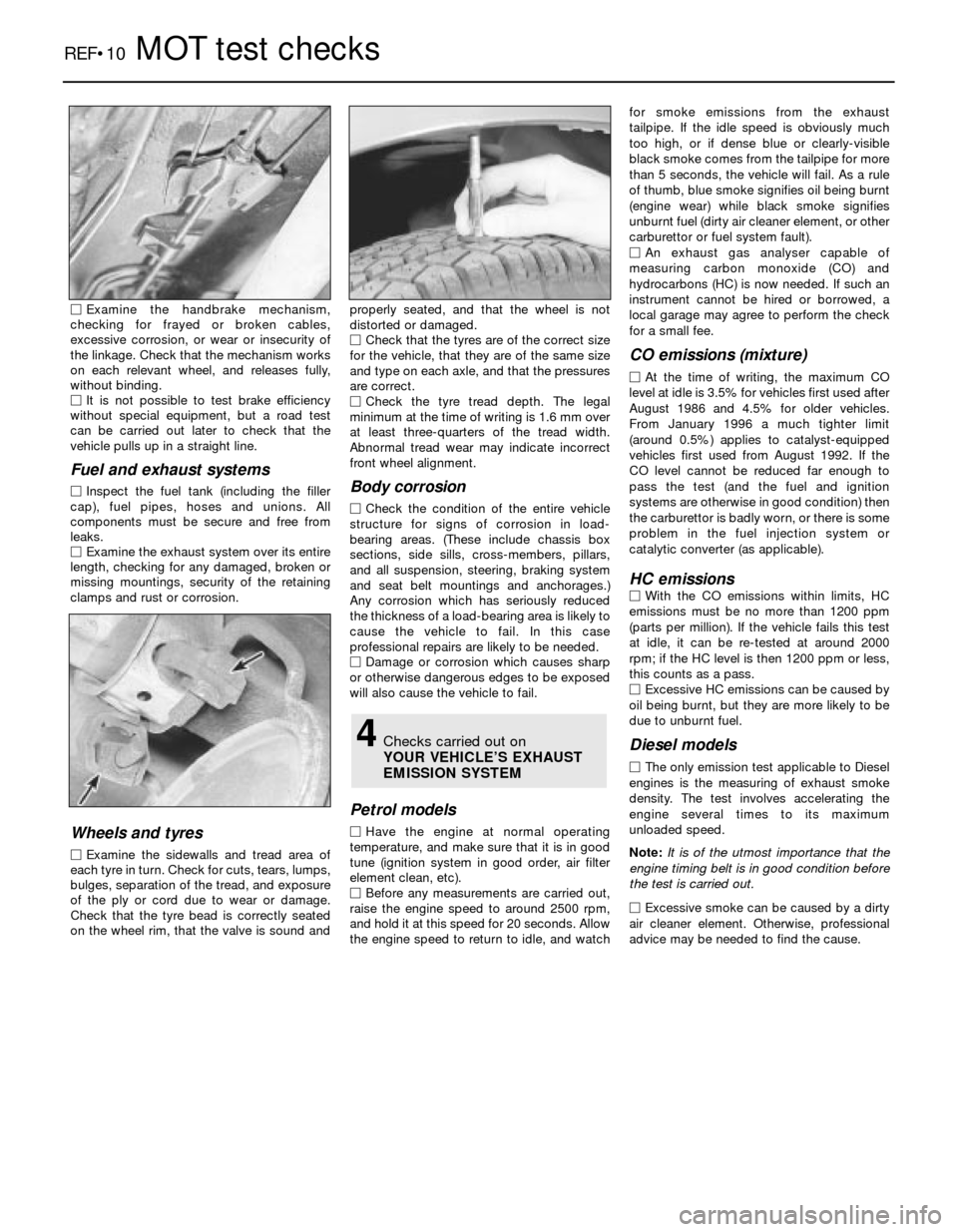
REF•10MOTtest checks
MExamine the handbrake mechanism,
checking for frayed or broken cables,
excessive corrosion, or wear or insecurity of
the linkage. Check that the mechanism works
on each relevant wheel, and releases fully,
without binding.
MIt is not possible to test brake efficiency
without special equipment, but a road test
can be carried out later to check that the
vehicle pulls up in a straight line.
Fuel and exhaust systems
MInspect the fuel tank (including the filler
cap), fuel pipes, hoses and unions. All
components must be secure and free from
leaks.
MExamine the exhaust system over its entire
length, checking for any damaged, broken or
missing mountings, security of the retaining
clamps and rust or corrosion.
Wheels and tyres
MExamine the sidewalls and tread area of
each tyre in turn. Check for cuts, tears, lumps,
bulges, separation of the tread, and exposure
of the ply or cord due to wear or damage.
Check that the tyre bead is correctly seated
on the wheel rim, that the valve is sound andproperly seated, and that the wheel is not
distorted or damaged.
MCheck that the tyres are of the correct size
for the vehicle, that they are of the same size
and type on each axle, and that the pressures
are correct.
MCheck the tyre tread depth. The legal
minimum at the time of writing is 1.6 mm over
at least three-quarters of the tread width.
Abnormal tread wear may indicate incorrect
front wheel alignment.
Body corrosion
MCheck the condition of the entire vehicle
structure for signs of corrosion in load-
bearing areas. (These include chassis box
sections, side sills, cross-members, pillars,
and all suspension, steering, braking system
and seat belt mountings and anchorages.)
Any corrosion which has seriously reduced
the thickness of a load-bearing area is likely to
cause the vehicle to fail. In this case
professional repairs are likely to be needed.
MDamage or corrosion which causes sharp
or otherwise dangerous edges to be exposed
will also cause the vehicle to fail.
Petrol models
MHave the engine at normal operating
temperature, and make sure that it is in good
tune (ignition system in good order, air filter
element clean, etc).
MBefore any measurements are carried out,
raise the engine speed to around 2500 rpm,
and hold it at this speed for 20 seconds. Allow
the engine speed to return to idle, and watchfor smoke emissions from the exhaust
tailpipe. If the idle speed is obviously much
too high, or if dense blue or clearly-visible
black smoke comes from the tailpipe for more
than 5 seconds, the vehicle will fail. As a rule
of thumb, blue smoke signifies oil being burnt
(engine wear) while black smoke signifies
unburnt fuel (dirty air cleaner element, or other
carburettor or fuel system fault).
MAn exhaust gas analyser capable of
measuring carbon monoxide (CO) and
hydrocarbons (HC) is now needed. If such an
instrument cannot be hired or borrowed, a
local garage may agree to perform the check
for a small fee.
CO emissions (mixture)
MAt the time of writing, the maximum CO
level at idle is 3.5% for vehicles first used after
August 1986 and 4.5% for older vehicles.
From January 1996 a much tighter limit
(around 0.5%) applies to catalyst-equipped
vehicles first used from August 1992. If the
CO level cannot be reduced far enough to
pass the test (and the fuel and ignition
systems are otherwise in good condition) then
the carburettor is badly worn, or there is some
problem in the fuel injection system or
catalytic converter (as applicable).
HC emissionsMWith the CO emissions within limits, HC
emissions must be no more than 1200 ppm
(parts per million). If the vehicle fails this test
at idle, it can be re-tested at around 2000
rpm; if the HC level is then 1200 ppm or less,
this counts as a pass.
MExcessive HC emissions can be caused by
oil being burnt, but they are more likely to be
due to unburnt fuel.
Diesel models
MThe only emission test applicable to Diesel
engines is the measuring of exhaust smoke
density. The test involves accelerating the
engine several times to its maximum
unloaded speed.
Note: It is of the utmost importance that the
engine timing belt is in good condition before
the test is carried out.
M
Excessive smoke can be caused by a dirty
air cleaner element. Otherwise, professional
advice may be needed to find the cause.
4Checks carried out on
YOUR VEHICLE’S EXHAUST
EMISSION SYSTEM
Page 12 of 26
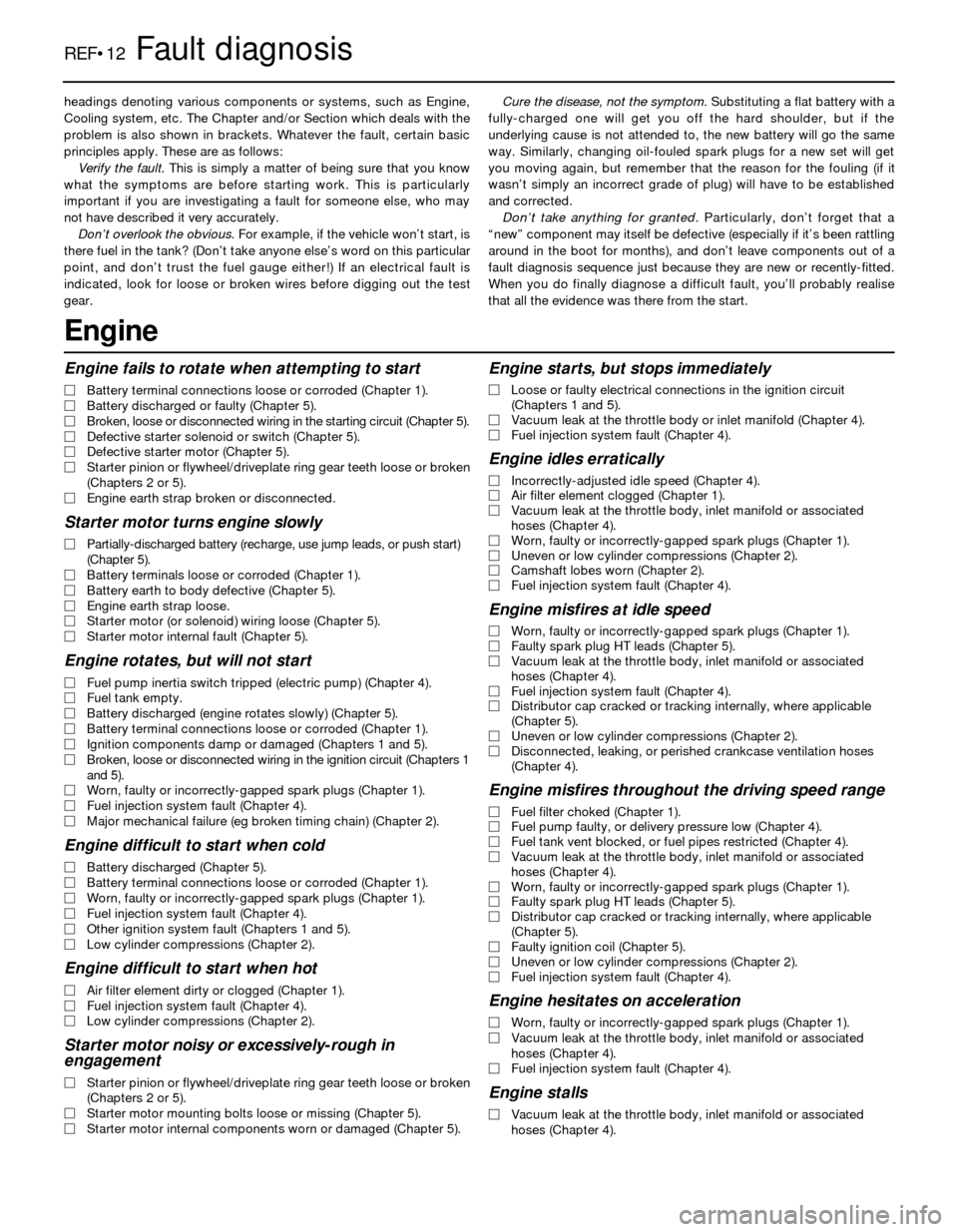
headings denoting various components or systems, such as Engine,
Cooling system, etc. The Chapter and/or Section which deals with the
problem is also shown in brackets. Whatever the fault, certain basic
principles apply. These are as follows:
Verify the fault. This is simply a matter of being sure that you know
what the symptoms are before starting work. This is particularly
important if you are investigating a fault for someone else, who may
not have described it very accurately.
Don’t overlook the obvious. For example, if the vehicle won’t start, is
there fuel in the tank? (Don’t take anyone else’s word on this particular
point, and don’t trust the fuel gauge either!) If an electrical fault is
indicated, look for loose or broken wires before digging out the test
gear.Cure the disease, not the symptom. Substituting a flat battery with a
fully-charged one will get you off the hard shoulder, but if the
underlying cause is not attended to, the new battery will go the same
way. Similarly, changing oil-fouled spark plugs for a new set will get
you moving again, but remember that the reason for the fouling (if it
wasn’t simply an incorrect grade of plug) will have to be established
and corrected.
Don’t take anything for granted. Particularly, don’t forget that a
“new” component may itself be defective (especially if it’s been rattling
around in the boot for months), and don’t leave components out of a
fault diagnosis sequence just because they are new or recently-fitted.
When you do finally diagnose a difficult fault, you’ll probably realise
that all the evidence was there from the start.
Engine fails to rotate when attempting to start
MBattery terminal connections loose or corroded (Chapter 1).
MBattery discharged or faulty (Chapter 5).
MBroken, loose or disconnected wiring in the starting circuit (Chapter 5).
MDefective starter solenoid or switch (Chapter 5).
MDefective starter motor (Chapter 5).
MStarter pinion or flywheel/driveplate ring gear teeth loose or broken
(Chapters 2 or 5).
MEngine earth strap broken or disconnected.
Starter motor turns engine slowly
MPartially-discharged battery (recharge, use jump leads, or push start)
(Chapter 5).
MBattery terminals loose or corroded (Chapter 1).
MBattery earth to body defective (Chapter 5).
MEngine earth strap loose.
MStarter motor (or solenoid) wiring loose (Chapter 5).
MStarter motor internal fault (Chapter 5).
Engine rotates, but will not start
MFuel pump inertia switch tripped (electric pump) (Chapter 4).
MFuel tank empty.
MBattery discharged (engine rotates slowly) (Chapter 5).
MBattery terminal connections loose or corroded (Chapter 1).
MIgnition components damp or damaged (Chapters 1 and 5).
MBroken, loose or disconnected wiring in the ignition circuit (Chapters 1
and 5).
MWorn, faulty or incorrectly-gapped spark plugs (Chapter 1).
MFuel injection system fault (Chapter 4).
MMajor mechanical failure (eg broken timing chain) (Chapter 2).
Engine difficult to start when cold
MBattery discharged (Chapter 5).
MBattery terminal connections loose or corroded (Chapter 1).
MWorn, faulty or incorrectly-gapped spark plugs (Chapter 1).
MFuel injection system fault (Chapter 4).
MOther ignition system fault (Chapters 1 and 5).
MLow cylinder compressions (Chapter 2).
Engine difficult to start when hot
MAir filter element dirty or clogged (Chapter 1).
MFuel injection system fault (Chapter 4).
MLow cylinder compressions (Chapter 2).
Starter motor noisy or excessively-rough in
engagement
MStarter pinion or flywheel/driveplate ring gear teeth loose or broken
(Chapters 2 or 5).
MStarter motor mounting bolts loose or missing (Chapter 5).
MStarter motor internal components worn or damaged (Chapter 5).
Engine starts, but stops immediately
MLoose or faulty electrical connections in the ignition circuit
(Chapters 1 and 5).
MVacuum leak at the throttle body or inlet manifold (Chapter 4).
MFuel injection system fault (Chapter 4).
Engine idles erratically
MIncorrectly-adjusted idle speed (Chapter 4).
MAir filter element clogged (Chapter 1).
MVacuum leak at the throttle body, inlet manifold or associated
hoses (Chapter 4).
MWorn, faulty or incorrectly-gapped spark plugs (Chapter 1).
MUneven or low cylinder compressions (Chapter 2).
MCamshaft lobes worn (Chapter 2).
MFuel injection system fault (Chapter 4).
Engine misfires at idle speed
MWorn, faulty or incorrectly-gapped spark plugs (Chapter 1).
MFaulty spark plug HT leads (Chapter 5).
MVacuum leak at the throttle body, inlet manifold or associated
hoses (Chapter 4).
MFuel injection system fault (Chapter 4).
MDistributor cap cracked or tracking internally, where applicable
(Chapter 5).
MUneven or low cylinder compressions (Chapter 2).
MDisconnected, leaking, or perished crankcase ventilation hoses
(Chapter 4).
Engine misfires throughout the driving speed range
MFuel filter choked (Chapter 1).
MFuel pump faulty, or delivery pressure low (Chapter 4).
MFuel tank vent blocked, or fuel pipes restricted (Chapter 4).
MVacuum leak at the throttle body, inlet manifold or associated
hoses (Chapter 4).
MWorn, faulty or incorrectly-gapped spark plugs (Chapter 1).
MFaulty spark plug HT leads (Chapter 5).
MDistributor cap cracked or tracking internally, where applicable
(Chapter 5).
MFaulty ignition coil (Chapter 5).
MUneven or low cylinder compressions (Chapter 2).
MFuel injection system fault (Chapter 4).
Engine hesitates on acceleration
MWorn, faulty or incorrectly-gapped spark plugs (Chapter 1).
MVacuum leak at the throttle body, inlet manifold or associated
hoses (Chapter 4).
MFuel injection system fault (Chapter 4).
Engine stalls
MVacuum leak at the throttle body, inlet manifold or associated
hoses (Chapter 4).
REF•12Fault diagnosis
Engine
Page 13 of 26
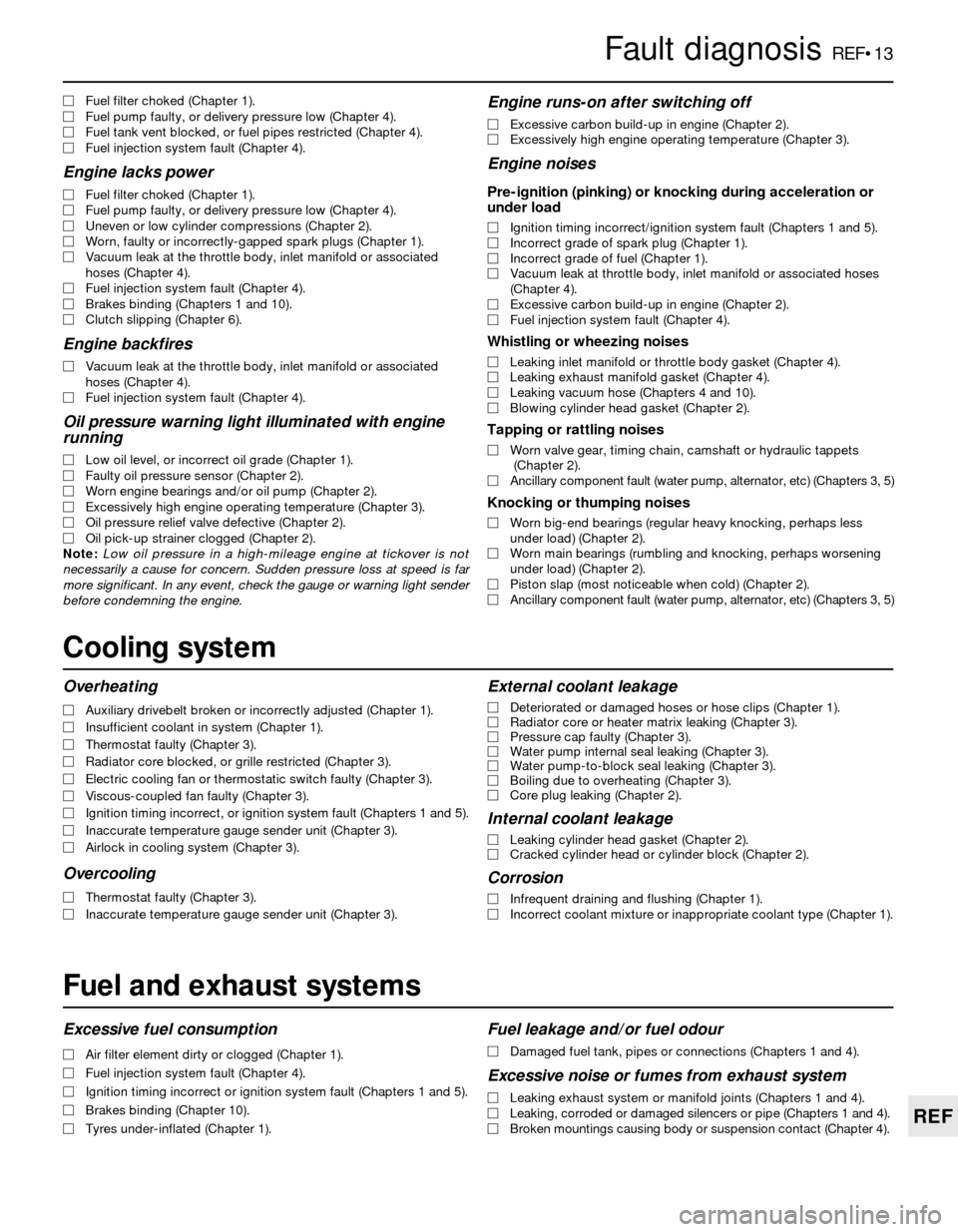
MFuel filter choked (Chapter 1).
MFuel pump faulty, or delivery pressure low (Chapter 4).
MFuel tank vent blocked, or fuel pipes restricted (Chapter 4).
MFuel injection system fault (Chapter 4).
Engine lacks power
MFuel filter choked (Chapter 1).
MFuel pump faulty, or delivery pressure low (Chapter 4).
MUneven or low cylinder compressions (Chapter 2).
MWorn, faulty or incorrectly-gapped spark plugs (Chapter 1).
MVacuum leak at the throttle body, inlet manifold or associated
hoses (Chapter 4).
MFuel injection system fault (Chapter 4).
MBrakes binding (Chapters 1 and 10).
MClutch slipping (Chapter 6).
Engine backfires
MVacuum leak at the throttle body, inlet manifold or associated
hoses (Chapter 4).
MFuel injection system fault (Chapter 4).
Oil pressure warning light illuminated with engine
running
MLow oil level, or incorrect oil grade (Chapter 1).
MFaulty oil pressure sensor (Chapter 2).
MWorn engine bearings and/or oil pump (Chapter 2).
MExcessively high engine operating temperature (Chapter 3).
MOil pressure relief valve defective (Chapter 2).
MOil pick-up strainer clogged (Chapter 2).
Note:Low oil pressure in a high-mileage engine at tickover is not
necessarily a cause for concern. Sudden pressure loss at speed is far
more significant. In any event, check the gauge or warning light sender
before condemning the engine.
Engine runs-on after switching off
MExcessive carbon build-up in engine (Chapter 2).
MExcessively high engine operating temperature (Chapter 3).
Engine noises
Pre-ignition (pinking) or knocking during acceleration or
under load
MIgnition timing incorrect/ignition system fault (Chapters 1 and 5).
MIncorrect grade of spark plug (Chapter 1).
MIncorrect grade of fuel (Chapter 1).
MVacuum leak at throttle body, inlet manifold or associated hoses
(Chapter 4).
MExcessive carbon build-up in engine (Chapter 2).
MFuel injection system fault (Chapter 4).
Whistling or wheezing noises
MLeaking inlet manifold or throttle body gasket (Chapter 4).
MLeaking exhaust manifold gasket (Chapter 4).
MLeaking vacuum hose (Chapters 4 and 10).
MBlowing cylinder head gasket (Chapter 2).
Tapping or rattling noises
MWorn valve gear, timing chain, camshaft or hydraulic tappets
(Chapter 2).
MAncillary component fault (water pump, alternator, etc) (Chapters 3, 5)
Knocking or thumping noises
MWorn big-end bearings (regular heavy knocking, perhaps less
under load) (Chapter 2).
MWorn main bearings (rumbling and knocking, perhaps worsening
under load) (Chapter 2).
MPiston slap (most noticeable when cold) (Chapter 2).
MAncillary component fault (water pump, alternator, etc) (Chapters 3, 5)
Overheating
MAuxiliary drivebelt broken or incorrectly adjusted (Chapter 1).
MInsufficient coolant in system (Chapter 1).
MThermostat faulty (Chapter 3).
MRadiator core blocked, or grille restricted (Chapter 3).
MElectric cooling fan or thermostatic switch faulty (Chapter 3).
MViscous-coupled fan faulty (Chapter 3).
MIgnition timing incorrect, or ignition system fault (Chapters 1 and 5).
MInaccurate temperature gauge sender unit (Chapter 3).
MAirlock in cooling system (Chapter 3).
Overcooling
MThermostat faulty (Chapter 3).
MInaccurate temperature gauge sender unit (Chapter 3).
External coolant leakage
MDeteriorated or damaged hoses or hose clips (Chapter 1).
MRadiator core or heater matrix leaking (Chapter 3).
MPressure cap faulty (Chapter 3).
MWater pump internal seal leaking (Chapter 3).
MWater pump-to-block seal leaking (Chapter 3).
MBoiling due to overheating (Chapter 3).
MCore plug leaking (Chapter 2).
Internal coolant leakage
MLeaking cylinder head gasket (Chapter 2).
MCracked cylinder head or cylinder block (Chapter 2).
Corrosion
MInfrequent draining and flushing (Chapter 1).
MIncorrect coolant mixture or inappropriate coolant type (Chapter 1).
Fault diagnosisREF•13
REF
Cooling system
Excessive fuel consumption
MAir filter element dirty or clogged (Chapter 1).
MFuel injection system fault (Chapter 4).
MIgnition timing incorrect or ignition system fault (Chapters 1 and 5).
MBrakes binding (Chapter 10).
MTyres under-inflated (Chapter 1).
Fuel leakage and/or fuel odour
MDamaged fuel tank, pipes or connections (Chapters 1 and 4).
Excessive noise or fumes from exhaust system
MLeaking exhaust system or manifold joints (Chapters 1 and 4).
MLeaking, corroded or damaged silencers or pipe (Chapters 1 and 4).
MBroken mountings causing body or suspension contact (Chapter 4).
Fuel and exhaust systems
Page 15 of 26
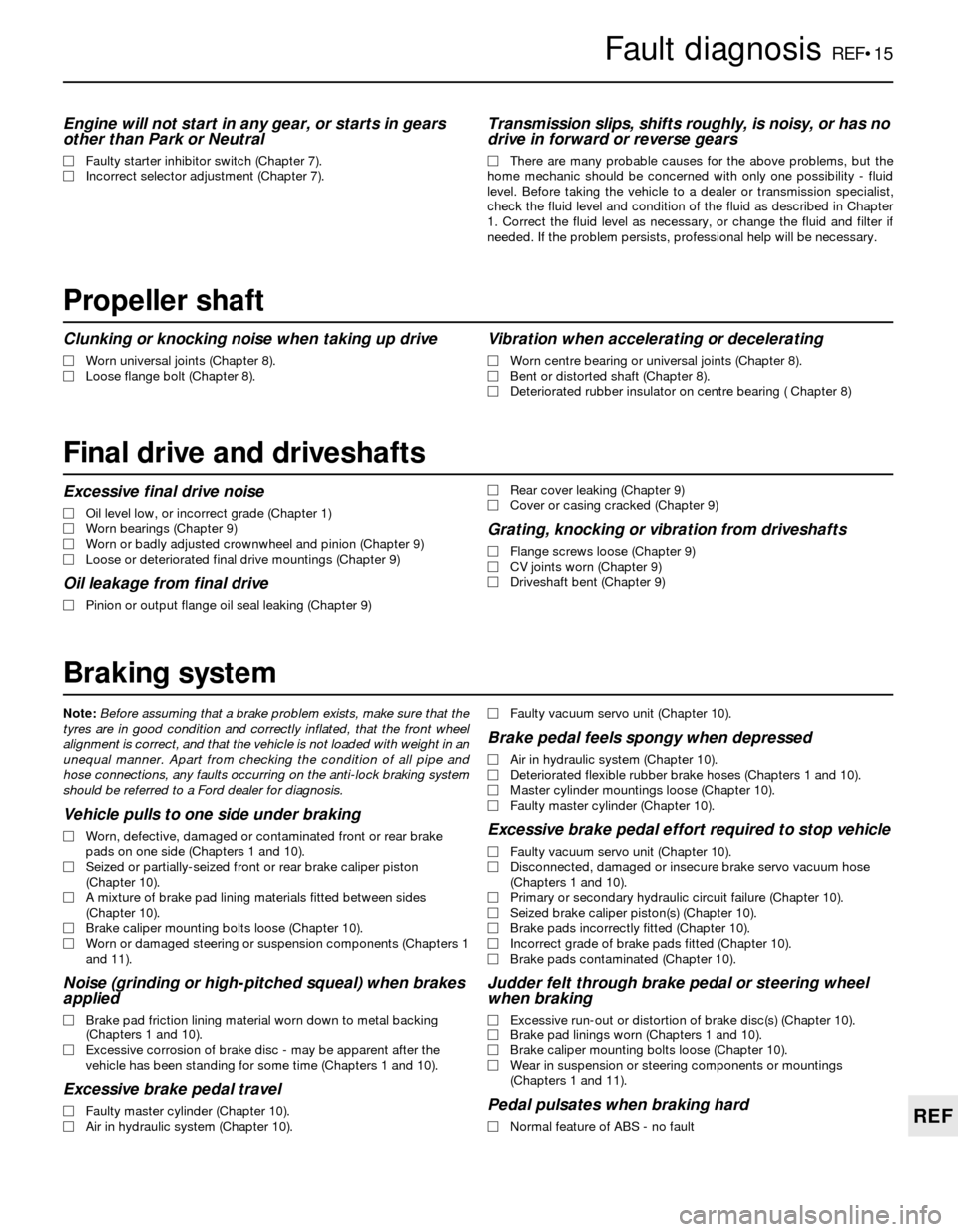
Excessive final drive noise
MOil level low, or incorrect grade (Chapter 1)
MWorn bearings (Chapter 9)
MWorn or badly adjusted crownwheel and pinion (Chapter 9)
MLoose or deteriorated final drive mountings (Chapter 9)
Oil leakage from final drive
MPinion or output flange oil seal leaking (Chapter 9)MRear cover leaking (Chapter 9)
MCover or casing cracked (Chapter 9)
Grating, knocking or vibration from driveshafts
MFlange screws loose (Chapter 9)
MCV joints worn (Chapter 9)
MDriveshaft bent (Chapter 9)
Note:Before assuming that a brake problem exists, make sure that the
tyres are in good condition and correctly inflated, that the front wheel
alignment is correct, and that the vehicle is not loaded with weight in an
unequal manner. Apart from checking the condition of all pipe and
hose connections, any faults occurring on the anti-lock braking system
should be referred to a Ford dealer for diagnosis.
Vehicle pulls to one side under braking
MWorn, defective, damaged or contaminated front or rear brake
pads on one side (Chapters 1 and 10).
MSeized or partially-seized front or rear brake caliper piston
(Chapter 10).
MA mixture of brake pad lining materials fitted between sides
(Chapter 10).
MBrake caliper mounting bolts loose (Chapter 10).
MWorn or damaged steering or suspension components (Chapters 1
and 11).
Noise (grinding or high-pitched squeal) when brakes
applied
MBrake pad friction lining material worn down to metal backing
(Chapters 1 and 10).
MExcessive corrosion of brake disc - may be apparent after the
vehicle has been standing for some time (Chapters 1 and 10).
Excessive brake pedal travel
MFaulty master cylinder (Chapter 10).
MAir in hydraulic system (Chapter 10).MFaulty vacuum servo unit (Chapter 10).
Brake pedal feels spongy when depressed
MAir in hydraulic system (Chapter 10).
MDeteriorated flexible rubber brake hoses (Chapters 1 and 10).
MMaster cylinder mountings loose (Chapter 10).
MFaulty master cylinder (Chapter 10).
Excessive brake pedal effort required to stop vehicle
MFaulty vacuum servo unit (Chapter 10).
MDisconnected, damaged or insecure brake servo vacuum hose
(Chapters 1 and 10).
MPrimary or secondary hydraulic circuit failure (Chapter 10).
MSeized brake caliper piston(s) (Chapter 10).
MBrake pads incorrectly fitted (Chapter 10).
MIncorrect grade of brake pads fitted (Chapter 10).
MBrake pads contaminated (Chapter 10).
Judder felt through brake pedal or steering wheel
when braking
MExcessive run-out or distortion of brake disc(s) (Chapter 10).
MBrake pad linings worn (Chapters 1 and 10).
MBrake caliper mounting bolts loose (Chapter 10).
MWear in suspension or steering components or mountings
(Chapters 1 and 11).
Pedal pulsates when braking hard
MNormal feature of ABS - no fault
Clunking or knocking noise when taking up drive
MWorn universal joints (Chapter 8).
MLoose flange bolt (Chapter 8).
Vibration when accelerating or decelerating
MWorn centre bearing or universal joints (Chapter 8).
MBent or distorted shaft (Chapter 8).
MDeteriorated rubber insulator on centre bearing ( Chapter 8)
Engine will not start in any gear, or starts in gears
other than Park or Neutral
MFaulty starter inhibitor switch (Chapter 7).
MIncorrect selector adjustment (Chapter 7).
Transmission slips, shifts roughly, is noisy, or has no
drive in forward or reverse gears
MThere are many probable causes for the above problems, but the
home mechanic should be concerned with only one possibility - fluid
level. Before taking the vehicle to a dealer or transmission specialist,
check the fluid level and condition of the fluid as described in Chapter
1. Correct the fluid level as necessary, or change the fluid and filter if
needed. If the problem persists, professional help will be necessary.
Fault diagnosisREF•15
REF
Propeller shaft
Final drive and driveshafts
Braking system
Page 18 of 26
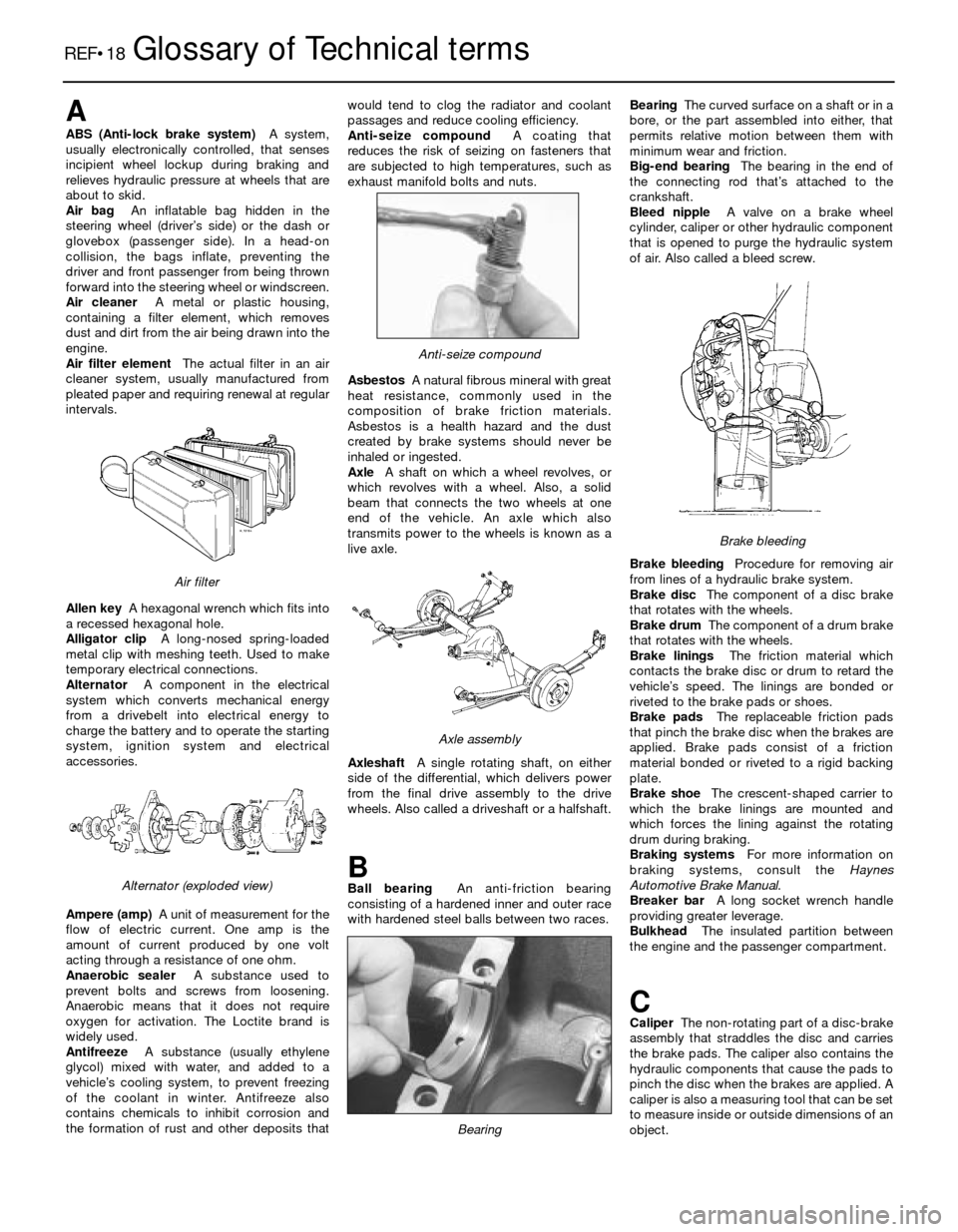
REF•18Glossary of Technical terms
A
ABS (Anti-lock brake system)A system,
usually electronically controlled, that senses
incipient wheel lockup during braking and
relieves hydraulic pressure at wheels that are
about to skid.
Air bag An inflatable bag hidden in the
steering wheel (driver’s side) or the dash or
glovebox (passenger side). In a head-on
collision, the bags inflate, preventing the
driver and front passenger from being thrown
forward into the steering wheel or windscreen.
Air cleanerA metal or plastic housing,
containing a filter element, which removes
dust and dirt from the air being drawn into the
engine.
Air filter elementThe actual filter in an air
cleaner system, usually manufactured from
pleated paper and requiring renewal at regular
intervals.
Allen keyA hexagonal wrench which fits into
a recessed hexagonal hole.
Alligator clipA long-nosed spring-loaded
metal clip with meshing teeth. Used to make
temporary electrical connections.
AlternatorA component in the electrical
system which converts mechanical energy
from a drivebelt into electrical energy to
charge the battery and to operate the starting
system, ignition system and electrical
accessories.
Ampere (amp)A unit of measurement for the
flow of electric current. One amp is the
amount of current produced by one volt
acting through a resistance of one ohm.
Anaerobic sealerA substance used to
prevent bolts and screws from loosening.
Anaerobic means that it does not require
oxygen for activation. The Loctite brand is
widely used.
AntifreezeA substance (usually ethylene
glycol) mixed with water, and added to a
vehicle’s cooling system, to prevent freezing
of the coolant in winter. Antifreeze also
contains chemicals to inhibit corrosion and
the formation of rust and other deposits thatwould tend to clog the radiator and coolant
passages and reduce cooling efficiency.
Anti-seize compoundA coating that
reduces the risk of seizing on fasteners that
are subjected to high temperatures, such as
exhaust manifold bolts and nuts.
AsbestosA natural fibrous mineral with great
heat resistance, commonly used in the
composition of brake friction materials.
Asbestos is a health hazard and the dust
created by brake systems should never be
inhaled or ingested.
AxleA shaft on which a wheel revolves, or
which revolves with a wheel. Also, a solid
beam that connects the two wheels at one
end of the vehicle. An axle which also
transmits power to the wheels is known as a
live axle.
AxleshaftA single rotating shaft, on either
side of the differential, which delivers power
from the final drive assembly to the drive
wheels. Also called a driveshaft or a halfshaft.
BBall bearingAn anti-friction bearing
consisting of a hardened inner and outer race
with hardened steel balls between two races.BearingThe curved surface on a shaft or in a
bore, or the part assembled into either, that
permits relative motion between them with
minimum wear and friction.
Big-end bearingThe bearing in the end of
the connecting rod that’s attached to the
crankshaft.
Bleed nippleA valve on a brake wheel
cylinder, caliper or other hydraulic component
that is opened to purge the hydraulic system
of air. Also called a bleed screw.
Brake bleedingProcedure for removing air
from lines of a hydraulic brake system.
Brake discThe component of a disc brake
that rotates with the wheels.
Brake drumThe component of a drum brake
that rotates with the wheels.
Brake liningsThe friction material which
contacts the brake disc or drum to retard the
vehicle’s speed. The linings are bonded or
riveted to the brake pads or shoes.
Brake padsThe replaceable friction pads
that pinch the brake disc when the brakes are
applied. Brake pads consist of a friction
material bonded or riveted to a rigid backing
plate.
Brake shoeThe crescent-shaped carrier to
which the brake linings are mounted and
which forces the lining against the rotating
drum during braking.
Braking systemsFor more information on
braking systems, consult the Haynes
Automotive Brake Manual.
Breaker barA long socket wrench handle
providing greater leverage.
BulkheadThe insulated partition between
the engine and the passenger compartment.
CCaliperThe non-rotating part of a disc-brake
assembly that straddles the disc and carries
the brake pads. The caliper also contains the
hydraulic components that cause the pads to
pinch the disc when the brakes are applied. A
caliper is also a measuring tool that can be set
to measure inside or outside dimensions of an
object.
Brake bleeding
Bearing
Axle assembly
Anti-seize compound
Alternator (exploded view)
Air filter
Page 23 of 26
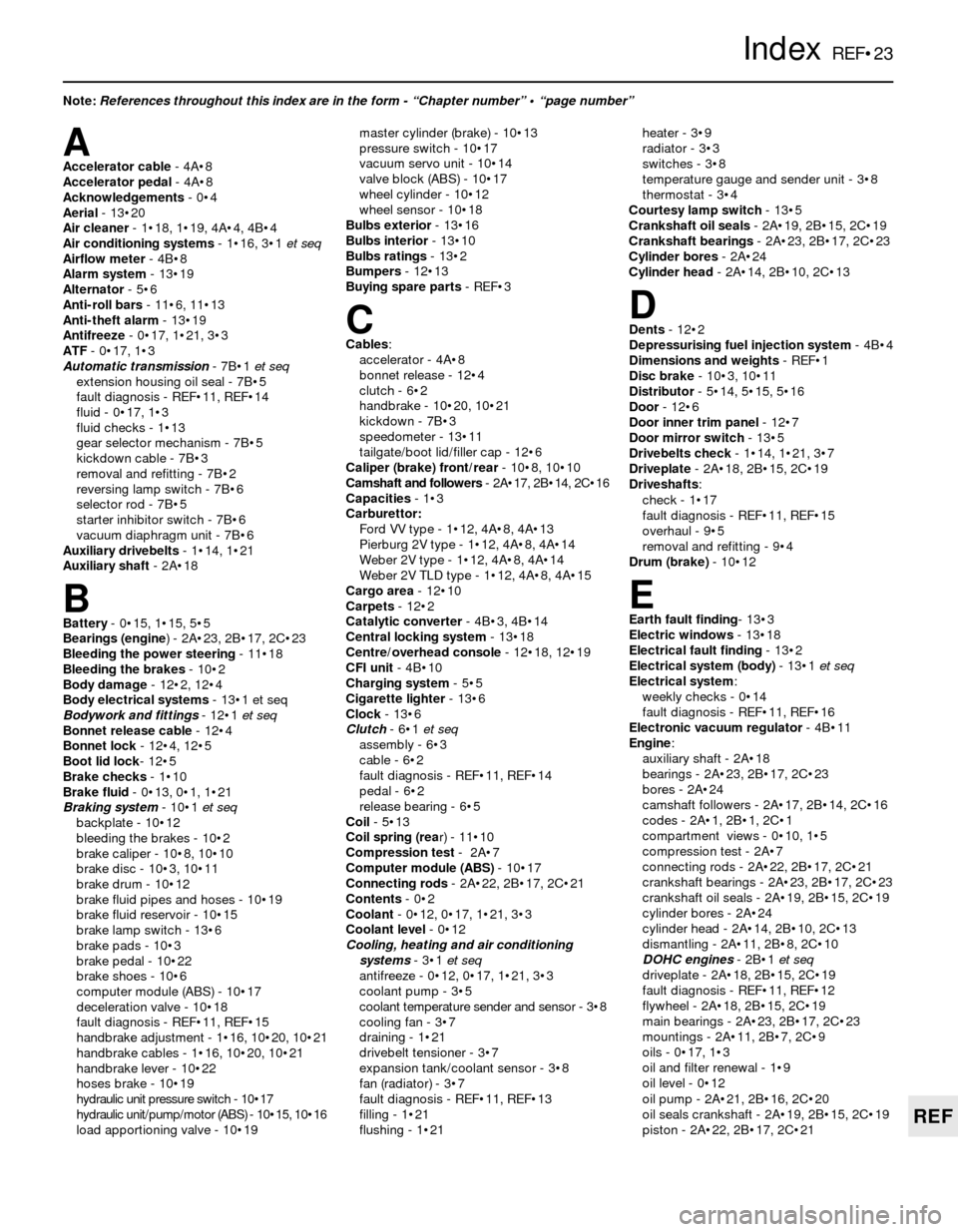
AAccelerator cable- 4A•8
Accelerator pedal- 4A•8
Acknowledgements- 0•4
Aerial- 13•20
Air cleaner- 1•18, 1•19, 4A•4, 4B•4
Air conditioning systems- 1•16, 3•1 et seq
Airflow meter- 4B•8
Alarm system- 13•19
Alternator- 5•6
Anti-roll bars- 11•6, 11•13
Anti-theft alarm- 13•19
Antifreeze- 0•17, 1•21, 3•3
ATF- 0•17, 1•3
Automatic transmission- 7B•1 et seq
extension housing oil seal - 7B•5
fault diagnosis - REF•11, REF•14
fluid - 0•17, 1•3
fluid checks - 1•13
gear selector mechanism - 7B•5
kickdown cable - 7B•3
removal and refitting - 7B•2
reversing lamp switch - 7B•6
selector rod - 7B•5
starter inhibitor switch - 7B•6
vacuum diaphragm unit - 7B•6
Auxiliary drivebelts- 1•14, 1•21
Auxiliary shaft- 2A•18
BBattery- 0•15, 1•15, 5•5
Bearings (engine) - 2A•23, 2B•17, 2C•23
Bleeding the power steering- 11•18
Bleeding the brakes- 10•2
Body damage- 12•2, 12•4
Body electrical systems - 13•1 et seq
Bodywork and fittings- 12•1 et seq
Bonnet release cable- 12•4
Bonnet lock- 12•4, 12•5
Boot lid lock- 12•5
Brake checks- 1•10
Brake fluid- 0•13, 0•1, 1•21
Braking system- 10•1 et seq
backplate - 10•12
bleeding the brakes - 10•2
brake caliper - 10•8, 10•10
brake disc - 10•3, 10•11
brake drum - 10•12
brake fluid pipes and hoses - 10•19
brake fluid reservoir - 10•15
brake lamp switch - 13•6
brake pads - 10•3
brake pedal - 10•22
brake shoes - 10•6
computer module (ABS) - 10•17
deceleration valve - 10•18
fault diagnosis - REF•11, REF•15
handbrake adjustment - 1•16, 10•20, 10•21
handbrake cables - 1•16, 10•20, 10•21
handbrake lever - 10•22
hoses brake - 10•19
hydraulic unit pressure switch - 10•17
hydraulic unit/pump/motor (ABS) - 10•15, 10•16
load apportioning valve - 10•19master cylinder (brake) - 10•13
pressure switch - 10•17
vacuum servo unit - 10•14
valve block (ABS) - 10•17
wheel cylinder - 10•12
wheel sensor - 10•18
Bulbs exterior- 13•16
Bulbs interior- 13•10
Bulbs ratings- 13•2
Bumpers- 12•13
Buying spare parts - REF•3
CCables:
accelerator - 4A•8
bonnet release - 12•4
clutch - 6•2
handbrake - 10•20, 10•21
kickdown - 7B•3
speedometer - 13•11
tailgate/boot lid/filler cap - 12•6
Caliper (brake) front/rear- 10•8, 10•10
Camshaft and followers- 2A•17, 2B•14, 2C•16
Capacities- 1•3
Carburettor:
Ford VV type - 1•12, 4A•8, 4A•13
Pierburg 2V type - 1•12, 4A•8, 4A•14
Weber 2V type - 1•12, 4A•8, 4A•14
Weber 2V TLD type - 1•12, 4A•8, 4A•15
Cargo area- 12•10
Carpets- 12•2
Catalytic converter- 4B•3, 4B•14
Central locking system- 13•18
Centre/overhead console- 12•18, 12•19
CFI unit- 4B•10
Charging system- 5•5
Cigarette lighter- 13•6
Clock- 13•6
Clutch- 6•1 et seq
assembly - 6•3
cable - 6•2
fault diagnosis - REF•11, REF•14
pedal - 6•2
release bearing - 6•5
Coil- 5•13
Coil spring (rear) - 11•10
Compression test- 2A•7
Computer module (ABS)- 10•17
Connecting rods- 2A•22, 2B•17, 2C•21
Contents- 0•2
Coolant- 0•12, 0•17, 1•21, 3•3
Coolant level- 0•12
Cooling, heating and air conditioning
systems- 3•1 et seq
antifreeze - 0•12, 0•17, 1•21, 3•3
coolant pump - 3•5
coolant temperature sender and sensor - 3•8
cooling fan - 3•7
draining - 1•21
drivebelt tensioner - 3•7
expansion tank/coolant sensor - 3•8
fan (radiator) - 3•7
fault diagnosis - REF•11, REF•13
filling - 1•21
flushing - 1•21heater - 3•9
radiator - 3•3
switches - 3•8
temperature gauge and sender unit - 3•8
thermostat - 3•4
Courtesy lamp switch- 13•5
Crankshaft oil seals- 2A•19, 2B•15, 2C•19
Crankshaft bearings- 2A•23, 2B•17, 2C•23
Cylinder bores- 2A•24
Cylinder head- 2A•14, 2B•10, 2C•13
DDents- 12•2
Depressurising fuel injection system- 4B•4
Dimensions and weights- REF•1
Disc brake - 10•3, 10•11
Distributor- 5•14, 5•15, 5•16
Door- 12•6
Door inner trim panel- 12•7
Door mirror switch- 13•5
Drivebelts check- 1•14, 1•21, 3•7
Driveplate- 2A•18, 2B•15, 2C•19
Driveshafts:
check - 1•17
fault diagnosis - REF•11, REF•15
overhaul - 9•5
removal and refitting - 9•4
Drum (brake)- 10•12
EEarth fault finding- 13•3
Electric windows- 13•18
Electrical fault finding- 13•2
Electrical system (body)- 13•1 et seq
Electrical system:
weekly checks - 0•14
fault diagnosis - REF•11, REF•16
Electronic vacuum regulator- 4B•11
Engine:
auxiliary shaft - 2A•18
bearings - 2A•23, 2B•17, 2C•23
bores - 2A•24
camshaft followers - 2A•17, 2B•14, 2C•16
codes - 2A•1, 2B•1, 2C•1
compartment views - 0•10, 1•5
compression test - 2A•7
connecting rods - 2A•22, 2B•17, 2C•21
crankshaft bearings - 2A•23, 2B•17, 2C•23
crankshaft oil seals - 2A•19, 2B•15, 2C•19
cylinder bores - 2A•24
cylinder head - 2A•14, 2B•10, 2C•13
dismantling - 2A•11, 2B•8, 2C•10
DOHC engines- 2B•1 et seq
driveplate - 2A•18, 2B•15, 2C•19
fault diagnosis - REF•11, REF•12
flywheel - 2A•18, 2B•15, 2C•19
main bearings - 2A•23, 2B•17, 2C•23
mountings - 2A•11, 2B•7, 2C•9
oils - 0•17, 1•3
oil and filter renewal - 1•9
oil level - 0•12
oil pump - 2A•21, 2B•16, 2C•20
oil seals crankshaft - 2A•19, 2B•15, 2C•19
piston - 2A•22, 2B•17, 2C•21
IndexREF•23
REF
Note: References throughout this index are in the form - “Chapter number” • “page number”
Page 24 of 26
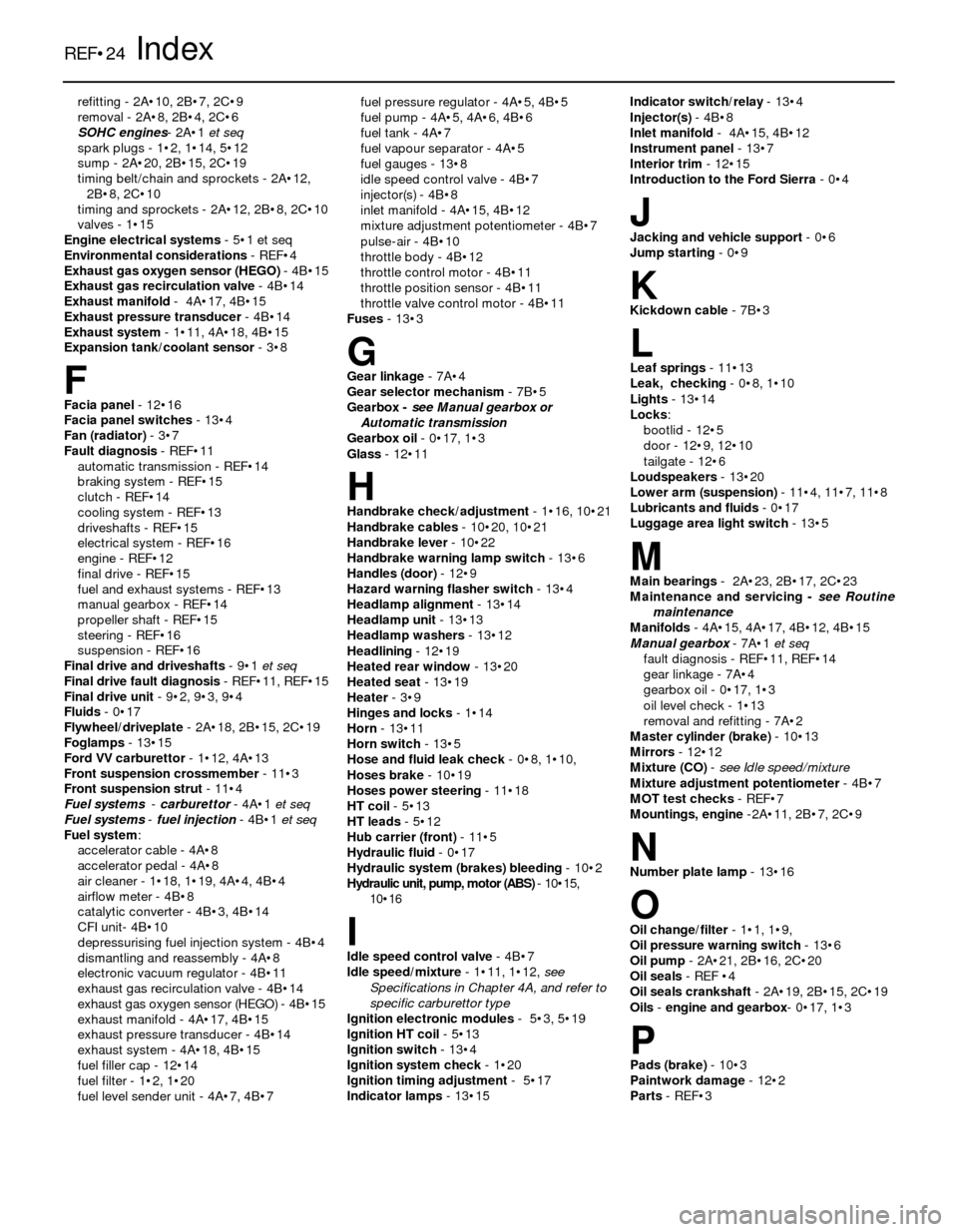
refitting - 2A•10, 2B•7, 2C•9
removal - 2A•8, 2B•4, 2C•6
SOHC engines- 2A•1et seq
spark plugs - 1•2, 1•14, 5•12
sump - 2A•20, 2B•15, 2C•19
timing belt/chain and sprockets - 2A•12,
2B•8, 2C•10
timing and sprockets - 2A•12, 2B•8, 2C•10
valves - 1•15
Engine electrical systems - 5•1 et seq
Environmental considerations- REF•4
Exhaust gas oxygen sensor (HEGO)- 4B•15
Exhaust gas recirculation valve- 4B•14
Exhaust manifold- 4A•17, 4B•15
Exhaust pressure transducer- 4B•14
Exhaust system- 1•11, 4A•18, 4B•15
Expansion tank/coolant sensor- 3•8
FFacia panel- 12•16
Facia panel switches- 13•4
Fan (radiator)- 3•7
Fault diagnosis- REF•11
automatic transmission - REF•14
braking system - REF•15
clutch - REF•14
cooling system - REF•13
driveshafts - REF•15
electrical system - REF•16
engine - REF•12
final drive - REF•15
fuel and exhaust systems - REF•13
manual gearbox - REF•14
propeller shaft - REF•15
steering - REF•16
suspension - REF•16
Final drive and driveshafts- 9•1 et seq
Final drive fault diagnosis- REF•11, REF•15
Final drive unit- 9•2, 9•3, 9•4
Fluids- 0•17
Flywheel/driveplate- 2A•18, 2B•15, 2C•19
Foglamps- 13•15
Ford VV carburettor- 1•12, 4A•13
Front suspension crossmember- 11•3
Front suspension strut- 11•4
Fuel systems- carburettor - 4A•1 et seq
Fuel systems- fuel injection - 4B•1 et seq
Fuel system:
accelerator cable - 4A•8
accelerator pedal - 4A•8
air cleaner - 1•18, 1•19, 4A•4, 4B•4
airflow meter - 4B•8
catalytic converter - 4B•3, 4B•14
CFI unit- 4B•10
depressurising fuel injection system - 4B•4
dismantling and reassembly - 4A•8
electronic vacuum regulator - 4B•11
exhaust gas recirculation valve - 4B•14
exhaust gas oxygen sensor (HEGO) - 4B•15
exhaust manifold - 4A•17, 4B•15
exhaust pressure transducer - 4B•14
exhaust system - 4A•18, 4B•15
fuel filler cap - 12•14
fuel filter - 1•2, 1•20
fuel level sender unit - 4A•7, 4B•7fuel pressure regulator - 4A•5, 4B•5
fuel pump - 4A•5, 4A•6, 4B•6
fuel tank - 4A•7
fuel vapour separator - 4A•5
fuel gauges - 13•8
idle speed control valve - 4B•7
injector(s) - 4B•8
inlet manifold - 4A•15, 4B•12
mixture adjustment potentiometer - 4B•7
pulse-air - 4B•10
throttle body - 4B•12
throttle control motor - 4B•11
throttle position sensor - 4B•11
throttle valve control motor - 4B•11
Fuses- 13•3
GGear linkage- 7A•4
Gear selector mechanism- 7B•5
Gearbox - see Manual gearbox or
Automatic transmission
Gearbox oil- 0•17, 1•3
Glass- 12•11
HHandbrake check/adjustment- 1•16, 10•21
Handbrake cables- 10•20, 10•21
Handbrake lever - 10•22
Handbrake warning lamp switch- 13•6
Handles (door)- 12•9
Hazard warning flasher switch- 13•4
Headlamp alignment- 13•14
Headlamp unit- 13•13
Headlamp washers- 13•12
Headlining - 12•19
Heated rear window- 13•20
Heated seat- 13•19
Heater- 3•9
Hinges and locks- 1•14
Horn- 13•11
Horn switch- 13•5
Hose and fluid leak check- 0•8, 1•10,
Hoses brake- 10•19
Hoses power steering- 11•18
HT coil- 5•13
HT leads- 5•12
Hub carrier (front) - 11•5
Hydraulic fluid- 0•17
Hydraulic system (brakes) bleeding- 10•2
Hydraulic unit, pump, motor (ABS)- 10•15,
10•16
IIdle speed control valve- 4B•7
Idle speed/mixture- 1•11, 1•12, see
Specifications in Chapter 4A, and refer to
specific carburettor type
Ignition electronic modules- 5•3, 5•19
Ignition HT coil- 5•13
Ignition switch- 13•4
Ignition system check- 1•20
Ignition timing adjustment- 5•17
Indicator lamps- 13•15Indicator switch/relay- 13•4
Injector(s)- 4B•8
Inlet manifold- 4A•15, 4B•12
Instrument panel- 13•7
Interior trim- 12•15
Introduction to the Ford Sierra- 0•4
JJacking and vehicle support- 0•6
Jump starting- 0•9
KKickdown cable - 7B•3
LLeaf springs- 11•13
Leak, checking- 0•8, 1•10
Lights- 13•14
Locks:
bootlid - 12•5
door - 12•9, 12•10
tailgate - 12•6
Loudspeakers- 13•20
Lower arm (suspension)- 11•4, 11•7, 11•8
Lubricants and fluids- 0•17
Luggage area light switch- 13•5
MMain bearings- 2A•23, 2B•17, 2C•23
Maintenance and servicing - see Routine
maintenance
Manifolds- 4A•15, 4A•17, 4B•12, 4B•15
Manual gearbox- 7A•1 et seq
fault diagnosis - REF•11, REF•14
gear linkage - 7A•4
gearbox oil - 0•17, 1•3
oil level check - 1•13
removal and refitting - 7A•2
Master cylinder (brake)- 10•13
Mirrors- 12•12
Mixture (CO)- see Idle speed/mixture
Mixture adjustment potentiometer- 4B•7
MOT test checks- REF•7
Mountings, engine-2A•11, 2B•7, 2C•9
NNumber plate lamp- 13•16
OOil change/filter- 1•1, 1•9,
Oil pressure warning switch- 13•6
Oil pump- 2A•21, 2B•16, 2C•20
Oil seals- REF •4
Oil seals crankshaft- 2A•19, 2B•15, 2C•19
Oils- engine and gearbox- 0•17, 1•3
PPads (brake) - 10•3
Paintwork damage- 12•2
Parts- REF•3
REF•24Index