suspension GEELY MK 2008 Workshop Manual
[x] Cancel search | Manufacturer: GEELY, Model Year: 2008, Model line: MK, Model: GEELY MK 2008Pages: 416, PDF Size: 25.19 MB
Page 6 of 416
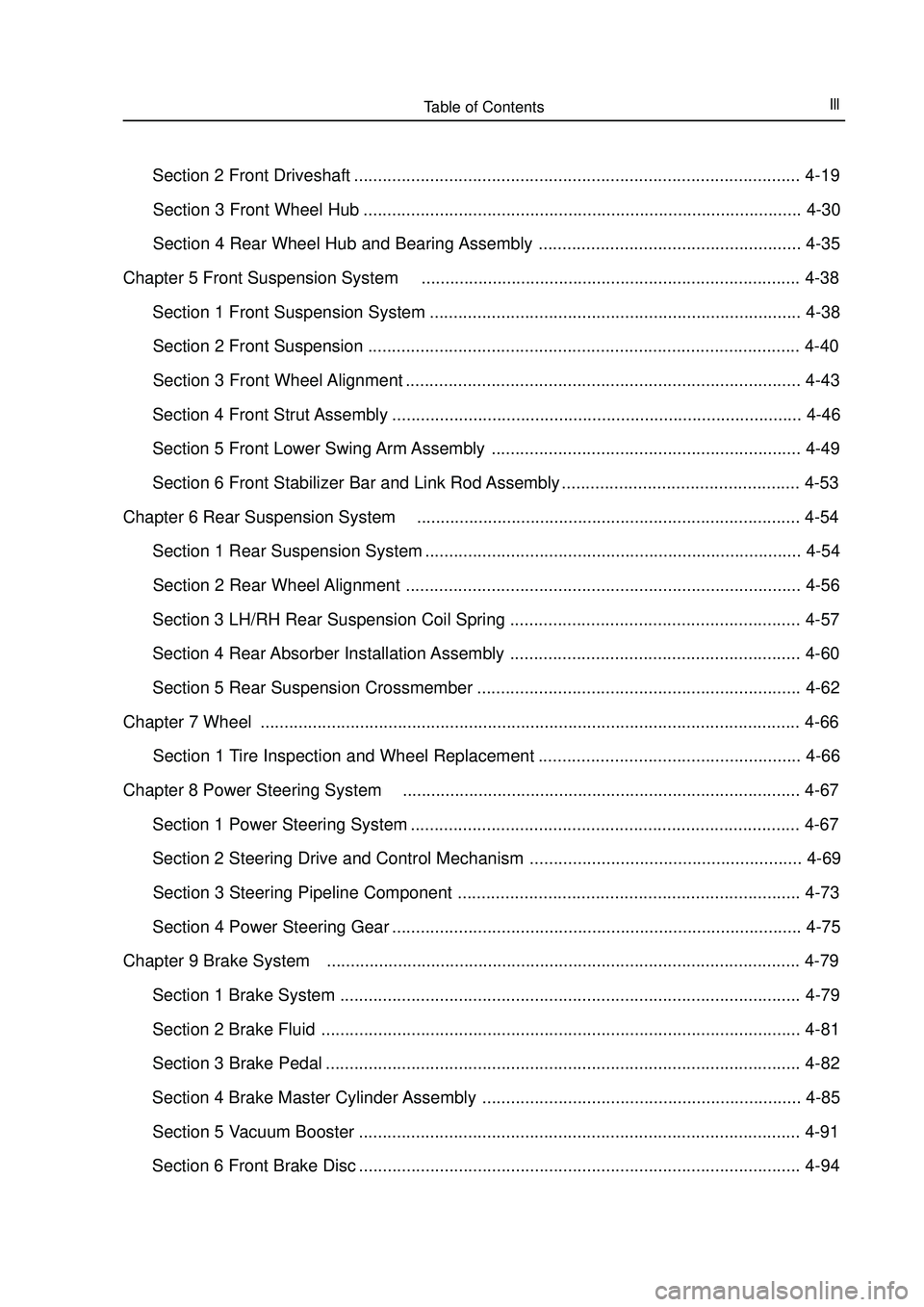
Table of ContentsIII Section 2 Front Driveshaft .............................................................................................. 4-19
Section 3 Front Wheel Hub ............................................................................................ 4-30
Section 4 Rear Wheel Hub and Bearing Assembly ....................................................... 4-35
Chapter 5 Front Suspension System................................................................................ 4-38
Section 1 Front Suspension System .............................................................................. 4-38
Section 2 Front Suspension ........................................................................................... 4-40
Section 3 Front Wheel Alignment ................................................................................... 4-43
Section 4 Front Strut Assembly ...................................................................................... 4-46
Section 5 Front Lower Swing Arm Assembly ................................................................. 4-49
Section 6 Front Stabilizer Bar and Link Rod Assembly .................................................. 4-53
Chapter 6 Rear Suspension System................................................................................. 4-54
Section 1 Rear Suspension System ............................................................................... 4-54
Section 2 Rear Wheel Alignment ................................................................................... 4-56
Section 3 LH/RH Rear Suspension Coil Spring ............................................................. 4-57
Section 4 Rear Absorber Installation Assembly ............................................................. 4-60
Section 5 Rear Suspension Crossmember .................................................................... 4-62
Chapter 7 Wheel.................................................................................................................. 4-66
Section 1 Tire Inspection and Wheel Replacement ....................................................... 4-66
Chapter 8 Power Steering System.................................................................................... 4-67
Section 1 Power Steering System .................................................................................. 4-67
Section 2 Steering Drive and Control Mechanism ......................................................... 4-69
Section 3 Steering Pipeline Component ........................................................................ 4-73
Section 4 Power Steering Gear ...................................................................................... 4-75
Chapter 9 Brake System.................................................................................................... 4-79
Section 1 Brake System ................................................................................................. 4-79
Section 2 Brake Fluid ..................................................................................................... 4-81
Section 3 Brake Pedal ....................................................................................................4-82
Section 4 Brake Master Cylinder Assembly ................................................................... 4-85
Section 5 Vacuum Booster ............................................................................................. 4-91
Section 6 Front Brake Disc ............................................................................................. 4-94
Page 22 of 416
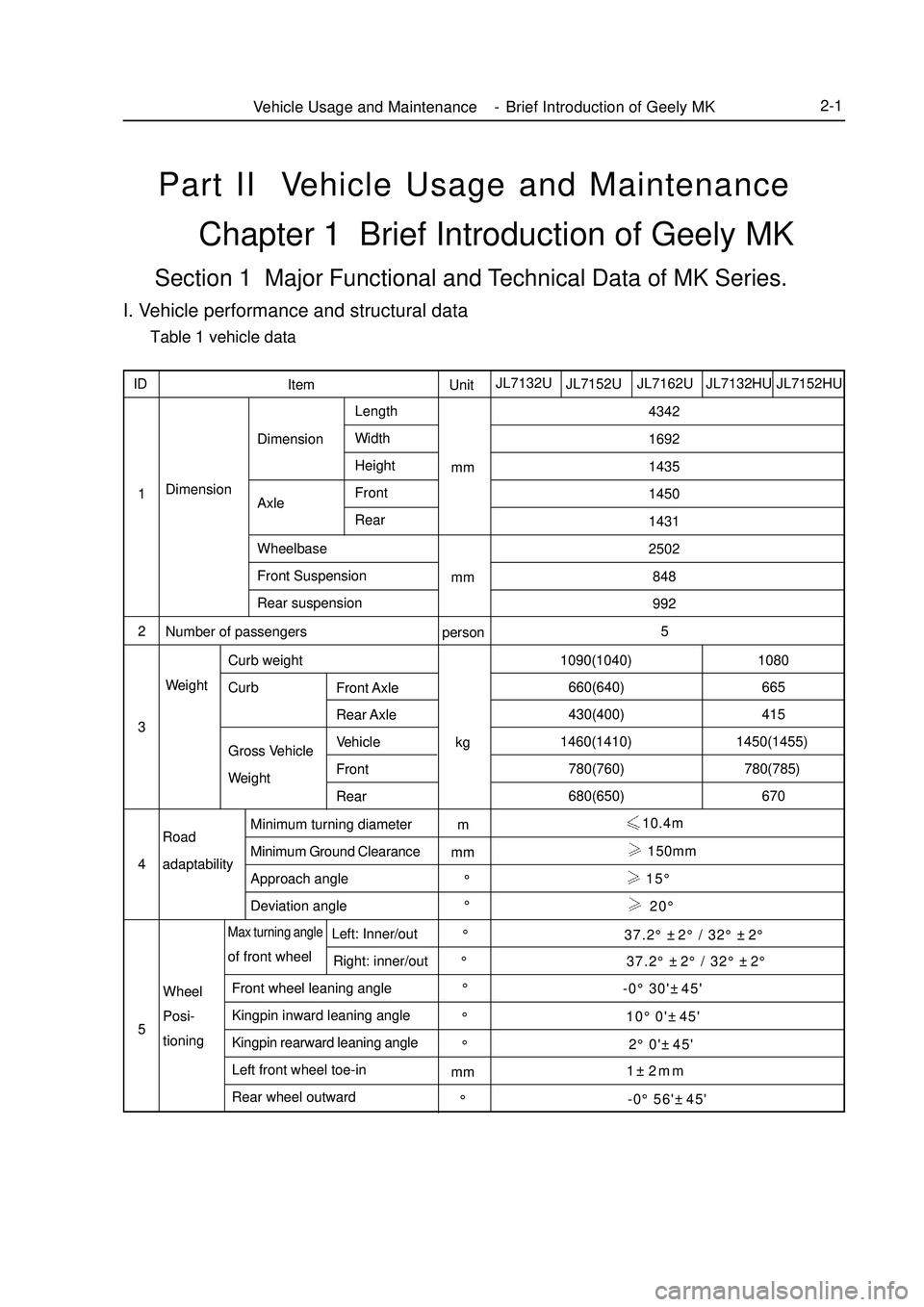
Part II Vehicle Usage and MaintenanceChapter 1 Brief Introduction of Geely MKSection 1 Major Functional and Technical Data of MK Series.I. Vehicle performance and structural data Table 1 vehicle dataVehicle Usage and Maintenance - Brief Introduction of Geely MK2-1JL7162U
JL7152U JL7132UUnit
mm
mm
person
kg
m
mm
°
mm Item ID
1
2
3
4
5DimensionDimension
Axle4342
1692
1435
1450
1431
2502
848
992
5
150mm
15°
20°
-0°30'±45'
1±2mmLength
Width
Height
Front
Rear
Wheelbase
Front Suspension
Rear suspension
Number of passengersWeightCurb weight
Front Axle
Rear Axle
Vehicle
Front
Rear CurbGross Vehicle
Weight
Road
adaptabilityMinimum turning diameter
Minimum Ground Clearance
Approach angle
Deviation angleWheel
Posi-
tioningLeft: Inner/out
Right: inner/outMax turning angleof front wheel
Front wheel leaning angle
Kingpin inward leaning angle
Kingpin rearward leaning angle
Left front wheel toe-in
Rear wheel outwardJL7132HU JL7152HU1090(1040)
660(640)
430(400)
1460(1410)
780(760)
680(650)1080
665
415
1450(1455)
780(785)
670 10.4m
°
°
°
°
°
°°37.2°±2°/ 32°±2°
37.2°±2°/ 32°±2°
2°0'±45' 10°0'±45'
-0°56'±45'
Page 23 of 416
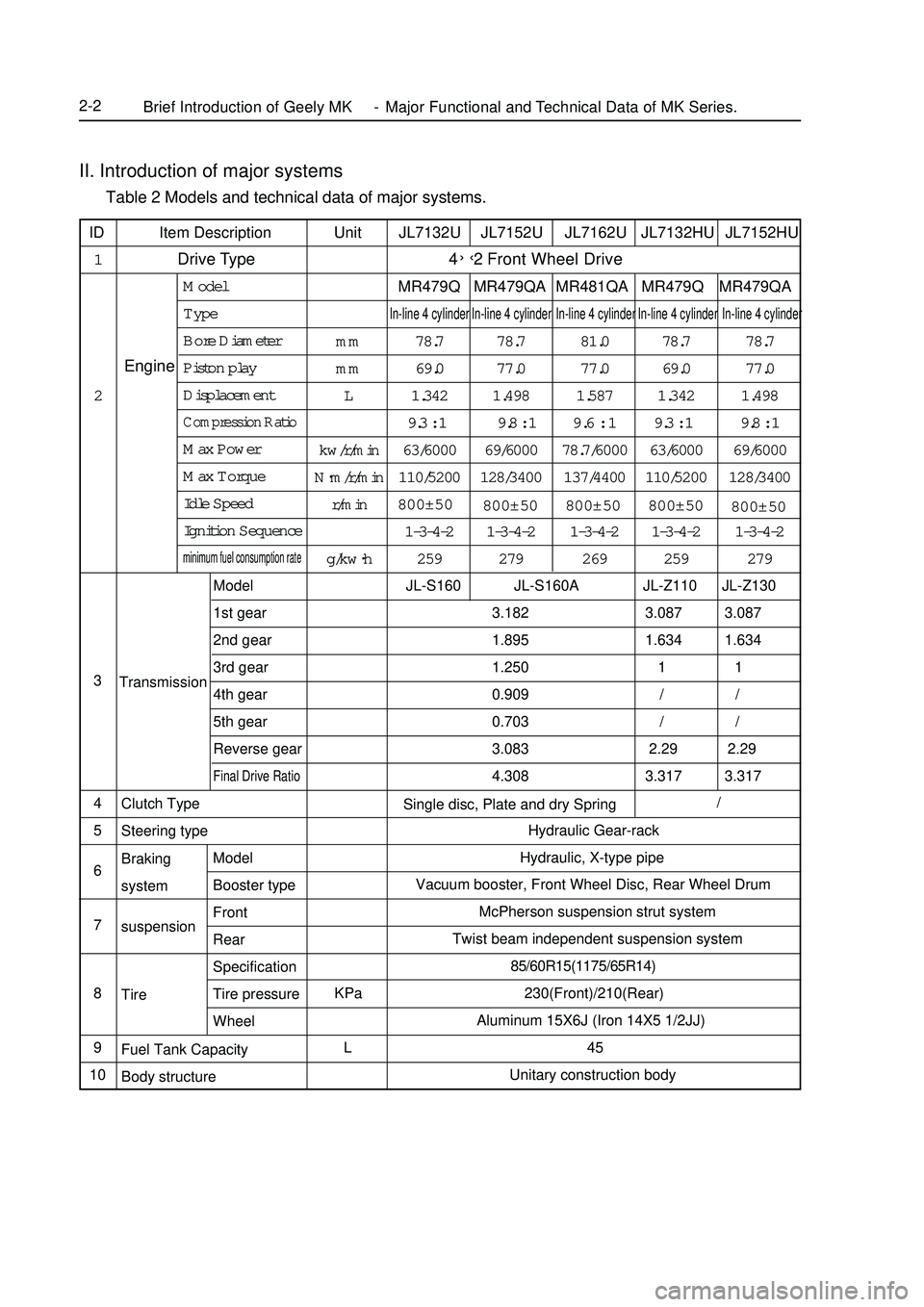
II. Introduction of major systems Table 2 Models and technical data of major systems.
JL7132U JL7152U JL7162U JL7132HU JL7152HU
4
MR479Q MR479QA MR481QA MR479Q MR479QAIn-line 4 cylinder In-line 4 cylinder In-line 4 cylinder In-line 4 cylinder In-line 4 cylinder78.7 78.7 81.0 78.7 78.7
69.0 77.0 77.0 69.0 77.0
1.342 1.498 1.587 1.342 1.498
9.3 : 1 9.8 : 19.6 : 19.3 : 1 9.8 : 1
63/6000 69/6000 78.7/6000 63/6000 69/6000
110/5200 128/3400 137/4400 110/5200 128/3400
800±50
1-3-4-2 1-3-4-2 1-3-4-2 1-3-4-2 1-3-4-2
259 279 269 259 279
JL-S160 JL-S160A JL-Z110 JL-Z130
3.182 3.087 3.087
1.895 1.634 1.634
1.250 1 1
0.909 / /
0.703 / /
3.083 2.29 2.29
4.308 3.317 3.317
Hydraulic Gear-rack
Hydraulic, X-type pipe
Vacuum booster, Front Wheel Disc, Rear Wheel Drum
McPherson suspension strut system
Twist beam independent suspension system
85/60R15(1175/65R14)
230(Front)/210(Rear)
Aluminum 15X6J (Iron 14X5 1/2JJ)
45
Unitary construction body Unit
mm
mm
L
kw/r/min
N.
m/r/min
r/min
g/kw.
h
KPa
L Item Description
Drive Type ID
1
2
3
4
5
6
7
8
9
10EngineModel
Type
Bore Diameter
Piston play
DisplacementCompression RatioMax Power
Max Torque
Idle Speed
Ignition Sequenceminimum fuel consumption rateTransmission
Braking
system
suspension
Tire Clutch Type
Steering type
Model
Booster type
Front
Rear
Specification
Tire pressure
Wheel
Fuel Tank Capacity
Body structureSingle disc, Plate and dry SpringBrief Introduction of Geely MK - Major Functional and Technical Data of MK Series.2-2Model
1st gear
2nd gear
3rd gear
4th gear
5th gear
Reverse gearFinal Drive Ratio /Front Wheel Drive ›‹
2
800±50800±50
800±50
800±50
Page 29 of 416
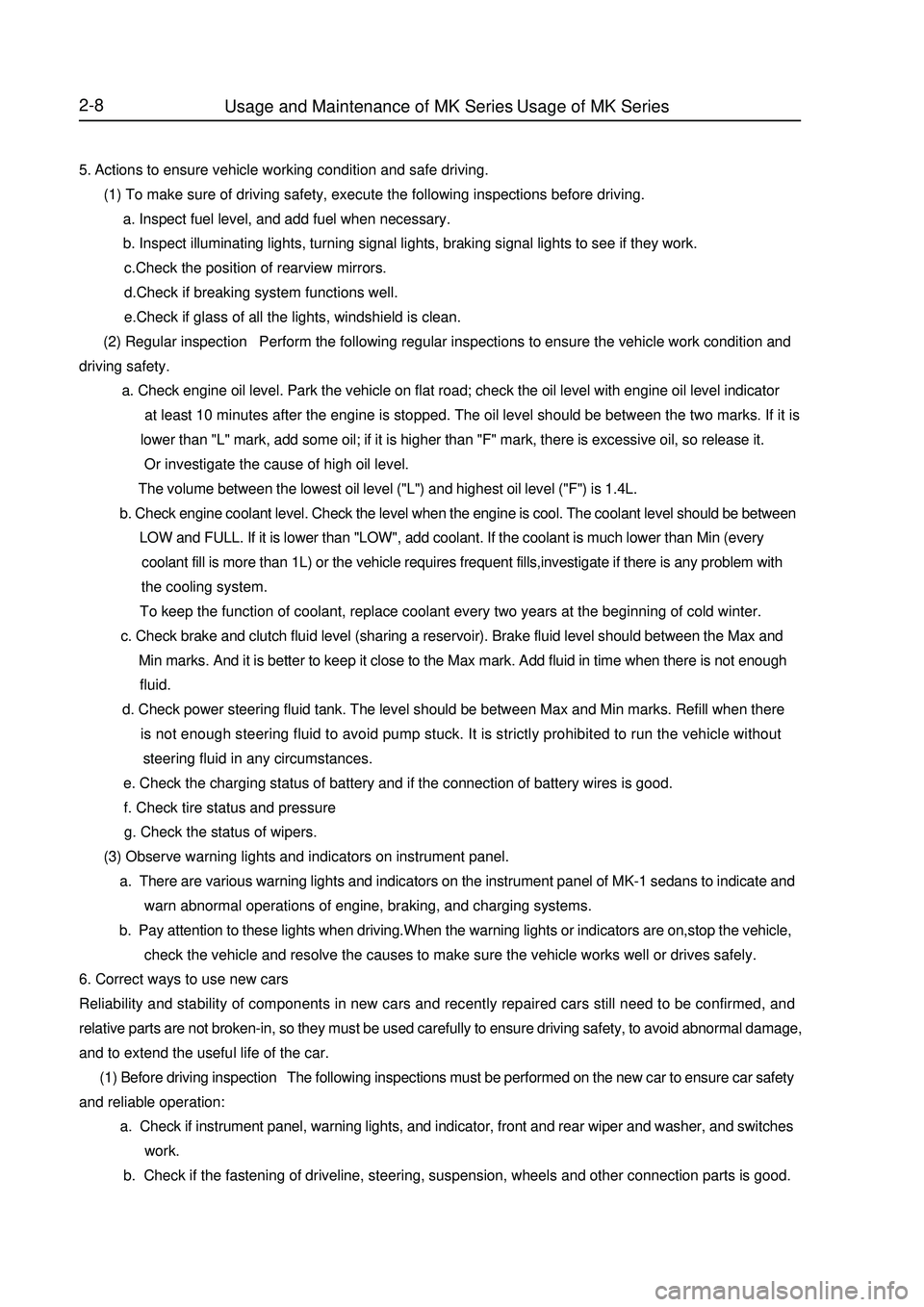
2-85. Actions to ensure vehicle working condition and safe driving.
(1) To make sure of driving safety, execute the following inspections before driving.
a. Inspect fuel level, and add fuel when necessary.
b. Inspect illuminating lights, turning signal lights, braking signal lights to see if they work.
c.Check the position of rearview mirrors.
d.Check if breaking system functions well.
e.Check if glass of all the lights, windshield is clean.
(2) Regular inspection Perform the following regular inspections to ensure the vehicle work condition and
driving safety.
a. Check engine oil level. Park the vehicle on flat road; check the oil level with engine oil level indicator
at least 10 minutes after the engine is stopped. The oil level should be between the two marks. If it is
lower than "L" mark, add some oil; if it is higher than "F" mark, there is excessive oil, so release it.
Or investigate the cause of high oil level.
The volume between the lowest oil level ("L") and highest oil level ("F") is 1.4L.
b. Check engine coolant level. Check the level when the engine is cool. The coolant level should be between
LOW and FULL. If it is lower than "LOW", add coolant. If the coolant is much lower than Min (every
coolant fill is more than 1L) or the vehicle requires frequent fills,investigate if there is any problem with
the cooling system.
To keep the function of coolant, replace coolant every two years at the beginning of cold winter.
c. Check brake and clutch fluid level (sharing a reservoir). Brake fluid level should between the Max and
Min marks. And it is better to keep it close to the Max mark. Add fluid in time when there is not enough
fluid.
d. Check power steering fluid tank. The level should be between Max and Min marks. Refill when there
is not enough steering fluid to avoid pump stuck. It is strictly prohibited to run the vehicle without
steering fluid in any circumstances.
e. Check the charging status of battery and if the connection of battery wires is good.
f. Check tire status and pressure
g. Check the status of wipers.
(3) Observe warning lights and indicators on instrument panel.
a. There are various warning lights and indicators on the instrument panel of MK-1 sedans to indicate and
warn abnormal operations of engine, braking, and charging systems.
b. Pay attention to these lights when driving.When the warning lights or indicators are on,stop the vehicle,
check the vehicle and resolve the causes to make sure the vehicle works well or drives safely.
6. Correct ways to use new cars
Reliability and stability of components in new cars and recently repaired cars still need to be confirmed, and
relative parts are not broken-in, so they must be used carefully to ensure driving safety, to avoid abnormal damage,
and to extend the useful life of the car.
(1) Before driving inspection The following inspections must be performed on the new car to ensure car safety
and reliable operation:
a. Check if instrument panel, warning lights, and indicator, front and rear wiper and washer, and switches
work.
b. Check if the fastening of driveline, steering, suspension, wheels and other connection parts is good.Usage and Maintenance of MK Series - Usage of MK Series
Page 37 of 416
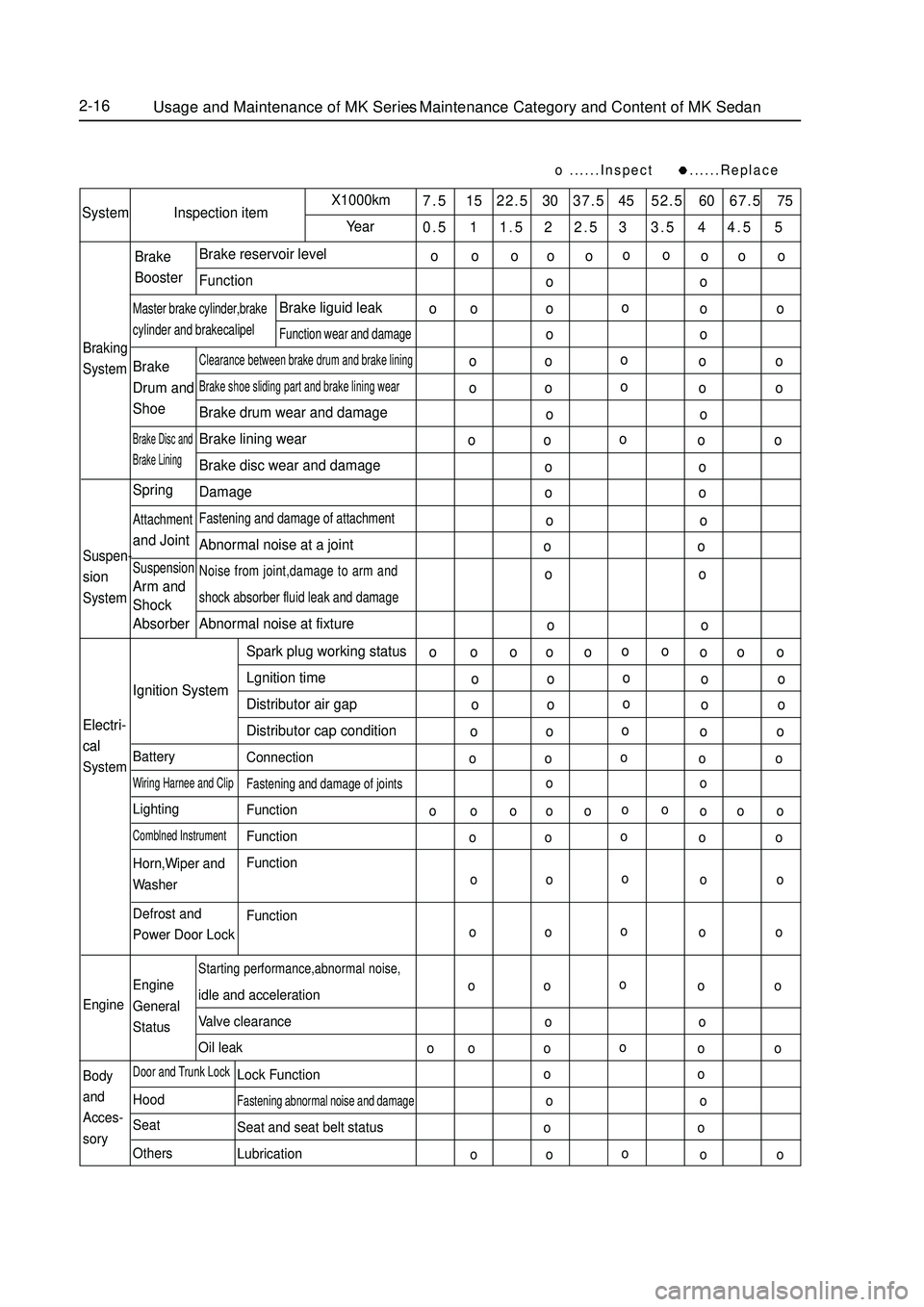
2-16......Inspect ......Replace7.5 15 22.5 30 37.5 45 52.5 60 67.5 75
0.5 1 1.5 2 2.5 3 3.5 4 4.5 5System Inspection itemX1000km
YearBraking
SystemBrake reservoir level
FunctionClearance between brake drum and brake liningBrake shoe sliding part and brake lining wearBrake drum wear and damage
Brake lining wear
Brake disc wear and damage
DamageFastening and damage of attachmentAbnormal noise at a jointNoise from joint,damage to arm and
shock absorber fluid leak and damageAbnormal noise at fixtureBrake
BoosterMaster brake cylinder,brakecylinder and brakecalipelBrake liguid leakFunction wear and damageBrake
Drum and
ShoeBrake Disc and
Brake LiningSuspen-sionSystemSpringAttachmentand JointSuspensionArm and
Shock
Absorber
Electri-
cal
SystemEngine
Body
and
Acces-
soryIgnition System
BatteryWiring Harnee and ClipLightingComblned InstrumentHorn,Wiper and
Washer
Defrost and
Power Door Lock
Engine
General
StatusDoor and Trunk LockHood
Seat
OthersStarting performance,abnormal noise,idle and acceleration
Valve clearance
Oil leakSpark plug working status
Lgnition time
Distributor air gap
Distributor cap condition
ConnectionFastening and damage of jointsFunction
Function
Function
FunctionLock FunctionFastening abnormal noise and damageSeat and seat belt status
LubricationUsage and Maintenance of MK Series - Maintenance Category and Content of MK Sedano
oo
o o o
o
o o ooo o
o o
ooo o
o o
o o
oo o
o o
oo o
o o
oo oo o
o o
o o
o o
o o
o o
o o
oo o o
o o ooo o
o o
oo o
o o
oo o
o o
oo o
o o
oo o
o o
oo o o
o o ooo o
o o
oo o
o o
oo o
o o
oo o
o o
oo o
o o
o o
ooo o
o o
oo oo oo oo o
Page 38 of 416

2-17
VII . Additional maintenance scheduleVehicles run in special circumstances require higher frequency of maintenance as listed below. Replacement of engine oil
Replacement of engine oil filter B-1: repeated short-distance driving and outer air temperature under zero within 8km (kilometer)
Inspection of the brake friction wafer and braking drum
Inspection of the braking pad and braking disc B-2: long-term empty run and / or long-distance driving with low speed, such as police wagon, taxi or automobile delivering
goods to the customers etcEvery 2,500km (kilometer) or every 3 months
Every 5,000km (kilometer) or every 6 months
Every 10,000 km (kilometer) or every 6 months
Every 5,000km (kilometer) or every 3 monthsB-3: continuous high-speed driving for more than 2 hours (80% of the maximum vehicle speed or above)
Replacement of driving axle oil of the manual transmission
Inspection or replacement of the driving axle fluid of the
automatic transmissionEvery 40,000km (kilometer) or every 48 months
Every 40,000km (kilometer) or every 24 months Inspection of the brake friction wafer and braking drum
Inspection of the braking pad and braking disc
Inspection of the brake piping and hose
Inspection of the transmit shaft ball and joint and dust shield
Inspection of the drive shaft cover
Inspection of the steering wheel, connecting rod and steering gear
box oil
Inspection of the front and rear suspension devices
Screwing down the bolts and nuts of the chassis and vehicle body A-1: driving on bumpy, muddy or melted snow road.
Replacement of engine oil
Replacement of engine oil filter
Inspection and replacement of air filter
Inspection of the brake friction wafer and braking drum
Inspection of the braking pad and braking disc
Replacement of the air conditioner filterA-2: driving on dusty roadEvery 10,000 km (kilometer) or every 6 months
Every 5,000km (kilometer) or every 3 months
Driving for 1000 km (kilometer) for the first time and
then every 10,000 km or every 6 months
Every 10,000 km (kilometer) or every 6 months
Every 10,000 km (kilometer) or every 12 months
Every 5,000km (kilometer) or every 3 months
Every 10,000 km (kilometer) or every 6 months
Every 10,000 km (kilometer) or every 6 months
Every 5,000km (kilometer) or every 6 months
Every 5,000km (kilometer) or every 6 months
Every 2,500km (kilometer) or every 3 months
Every 10,000 km (kilometer) or every 6 months
Every 5,000km (kilometer) or every 3 months
Every 10,000km (kilometer)Usage and Maintenance of MK Series - Maintenance Category and Content of MK Sedanoo o
o o o o
o o
o
o o
o o
o o
o ooo
Page 47 of 416
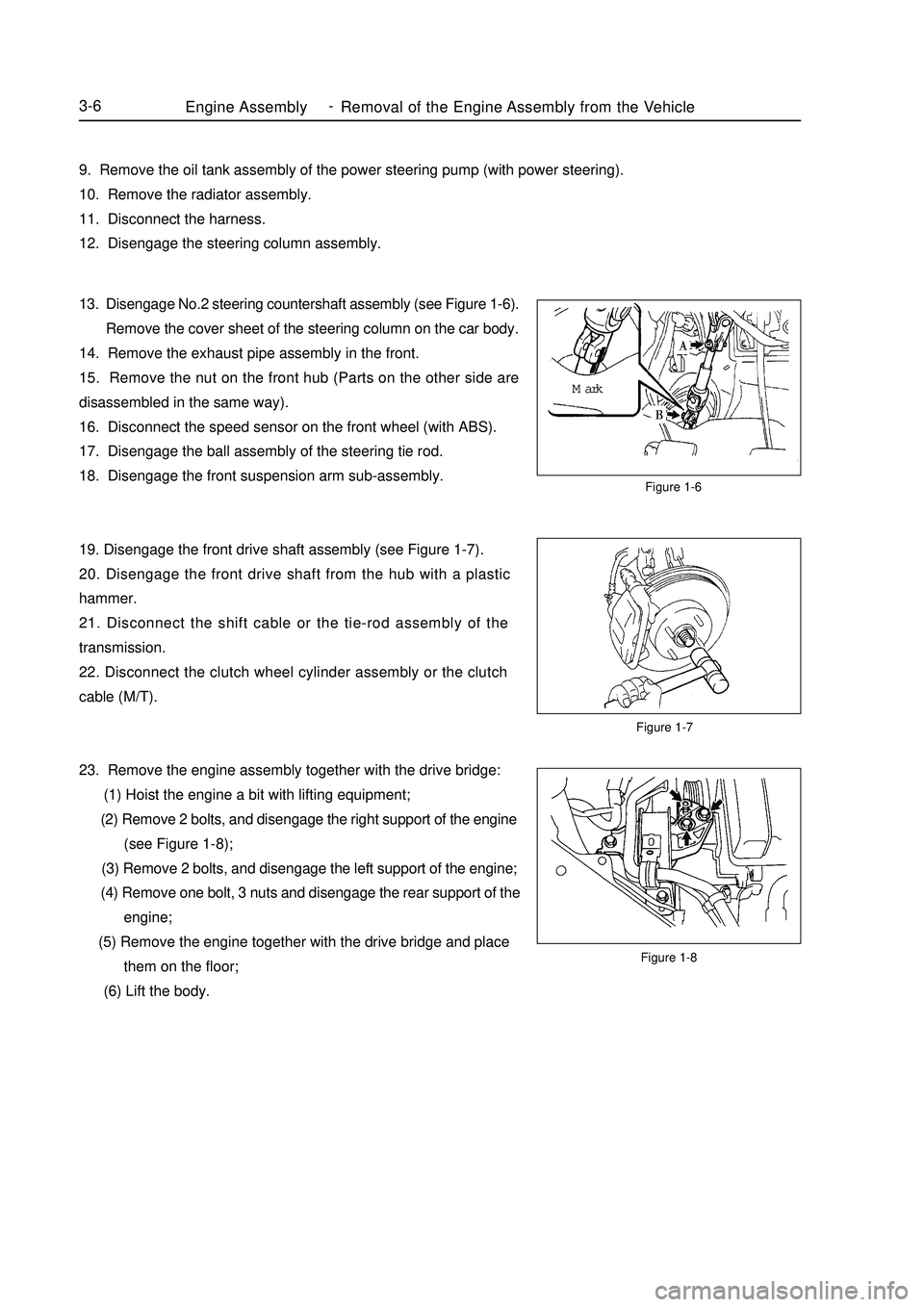
Figure 1-7Figure 1-6
Figure 1-8Engine AssemblyRemoval of the Engine Assembly from the Vehicle3-69. Remove the oil tank assembly of the power steering pump (with power steering).
10. Remove the radiator assembly.
11. Disconnect the harness.
12. Disengage the steering column assembly.
13. Disengage No.2 steering countershaft assembly (see Figure 1-6).
Remove the cover sheet of the steering column on the car body.
14. Remove the exhaust pipe assembly in the front.
15. Remove the nut on the front hub (Parts on the other side are
disassembled in the same way).
16. Disconnect the speed sensor on the front wheel (with ABS).
17. Disengage the ball assembly of the steering tie rod.
18. Disengage the front suspension arm sub-assembly.
19. Disengage the front drive shaft assembly (see Figure 1-7).
20. Disengage the front drive shaft from the hub with a plastic
hammer.
21. Disconnect the shift cable or the tie-rod assembly of the
transmission.
22. Disconnect the clutch wheel cylinder assembly or the clutch
cable (M/T).
23. Remove the engine assembly together with the drive bridge:
(1) Hoist the engine a bit with lifting equipment;
(2) Remove 2 bolts, and disengage the right support of the engine
(see Figure 1-8);
(3) Remove 2 bolts, and disengage the left support of the engine;
(4) Remove one bolt, 3 nuts and disengage the rear support of the
engine;
(5) Remove the engine together with the drive bridge and place
them on the floor;
(6) Lift the body.Mark -
Page 71 of 416
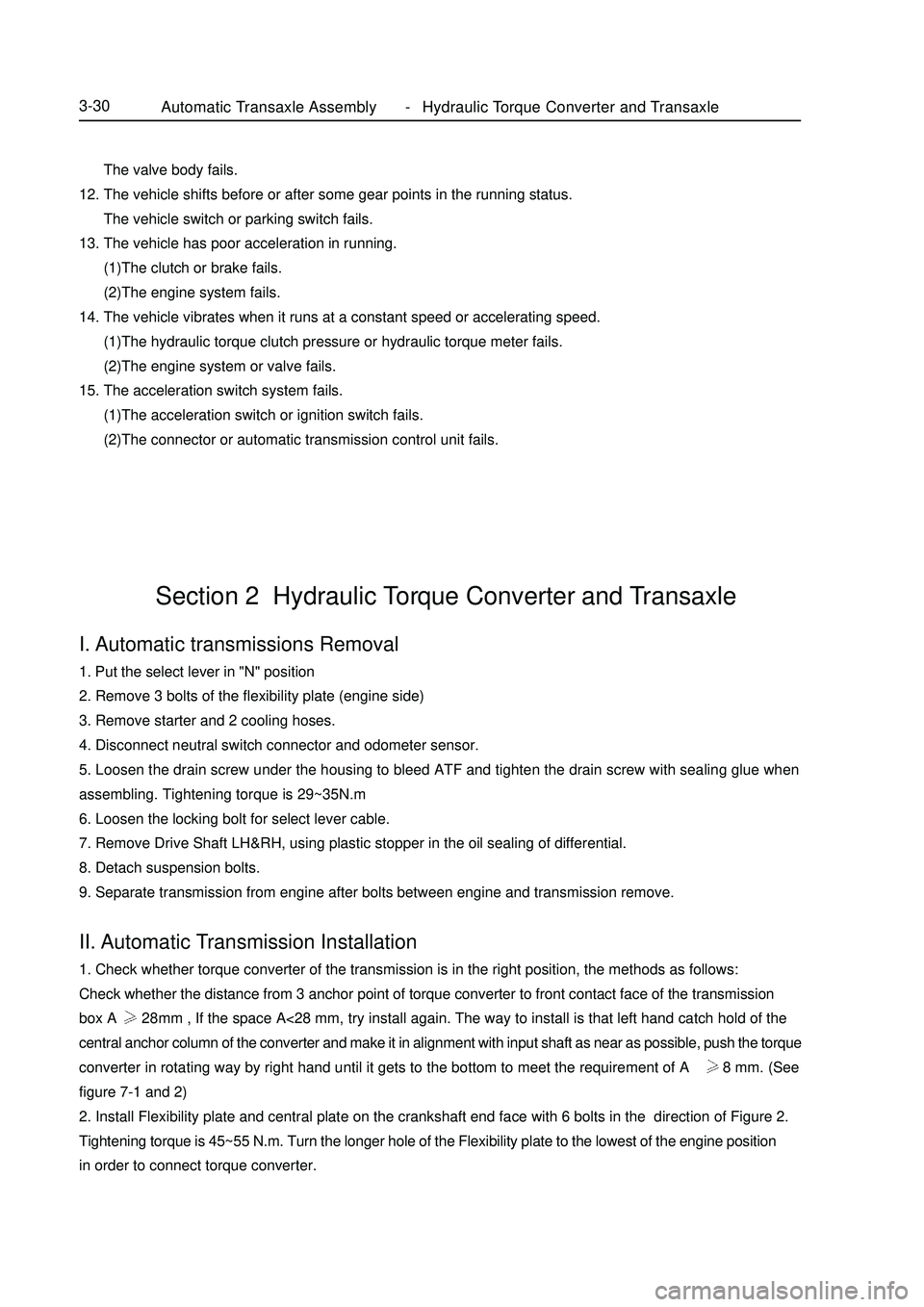
The valve body fails.
12. The vehicle shifts before or after some gear points in the running status.
The vehicle switch or parking switch fails.
13. The vehicle has poor acceleration in running.
(1)The clutch or brake fails.
(2)The engine system fails.
14. The vehicle vibrates when it runs at a constant speed or accelerating speed.
(1)The hydraulic torque clutch pressure or hydraulic torque meter fails.
(2)The engine system or valve fails.
15. The acceleration switch system fails.
(1)The acceleration switch or ignition switch fails.
(2)The connector or automatic transmission control unit fails.I. Automatic transmissions Removal1. Put the select lever in "N" position
2. Remove 3 bolts of the flexibility plate (engine side)
3. Remove starter and 2 cooling hoses.
4. Disconnect neutral switch connector and odometer sensor.
5. Loosen the drain screw under the housing to bleed ATF and tighten the drain screw with sealing glue when
assembling. Tightening torque is 29~35N.m
6. Loosen the locking bolt for select lever cable.
7. Remove Drive Shaft LH&RH, using plastic stopper in the oil sealing of differential.
8. Detach suspension bolts.
9. Separate transmission from engine after bolts between engine and transmission remove.II. Automatic Transmission Installation1. Check whether torque converter of the transmission is in the right position, the methods as follows:
Check whether the distance from 3 anchor point of torque converter to front contact face of the transmission
box A 28mm , If the space A<28 mm, try install again. The way to install is that left hand catch hold of the
central anchor column of the converter and make it in alignment with input shaft as near as possible, push the torque
converter in rotating way by right hand until it gets to the bottom to meet the requirement of A 28 mm. (See
figure 7-1 and 2)
2. Install Flexibility plate and central plate on the crankshaft end face with 6 bolts in the direction of Figure 2.
Tightening torque is 45~55 N.m. Turn the longer hole of the Flexibility plate to the lowest of the engine position
in order to connect torque converter.Section 2 Hydraulic Torque Converter and TransaxleAutomatic Transaxle Assembly Hydraulic Torque Converter and Transaxle3-30 -
Page 72 of 416
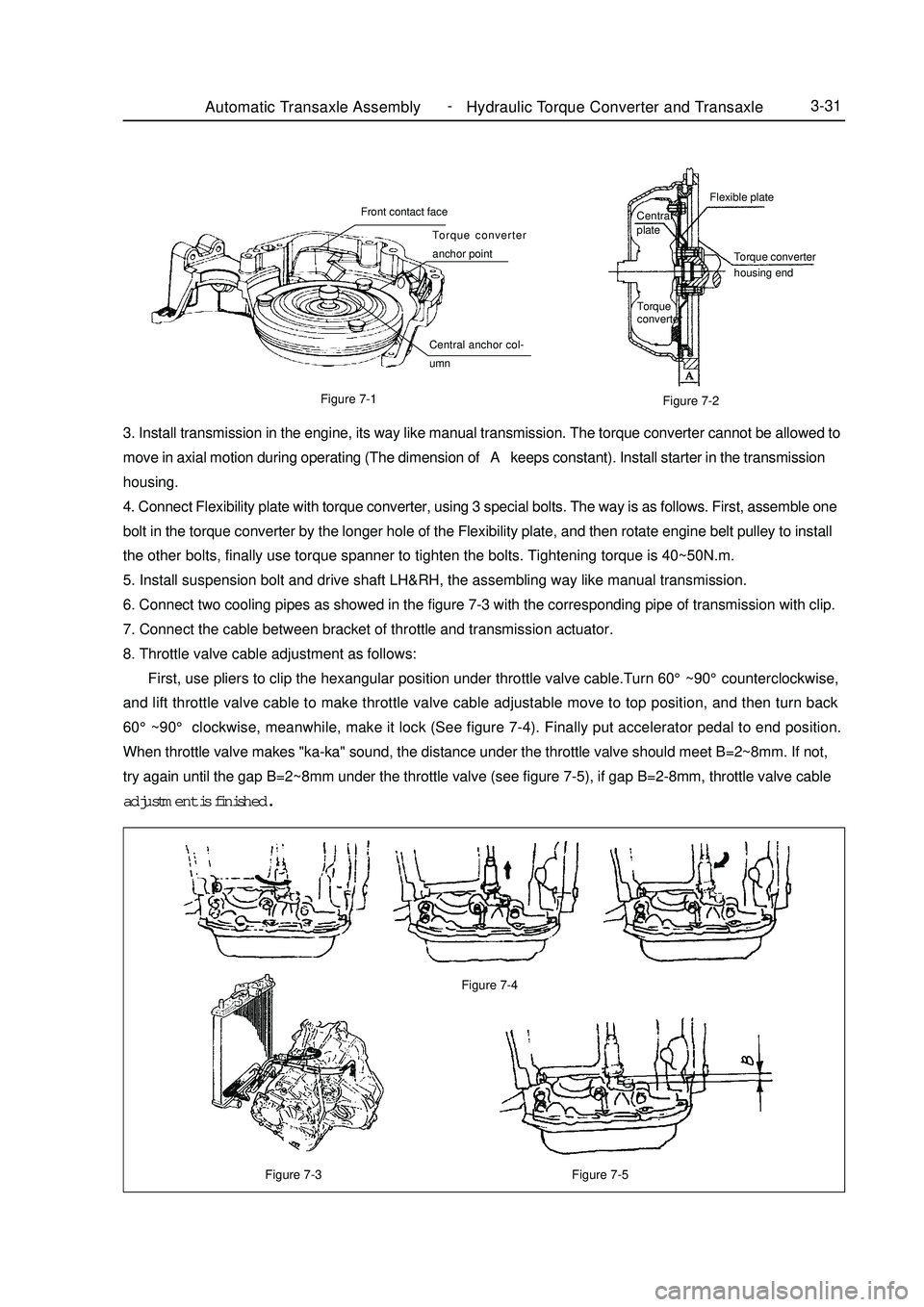
Figure 7-3Automatic Transaxle Assembly Hydraulic Torque Converter and Transaxle3-31Figure 7-5 Figure 7-4Figure 7-1
Figure 7-23. Install transmission in the engine, its way like manual transmission. The torque converter cannot be allowed to
move in axial motion during operating (The dimension of A keeps constant). Install starter in the transmission
housing.
4. Connect Flexibility plate with torque converter, using 3 special bolts. The way is as follows. First, assemble one
bolt in the torque converter by the longer hole of the Flexibility plate, and then rotate engine belt pulley to install
the other bolts, finally use torque spanner to tighten the bolts. Tightening torque is 40~50N.m.
5. Install suspension bolt and drive shaft LH&RH, the assembling way like manual transmission.
6. Connect two cooling pipes as showed in the figure 7-3 with the corresponding pipe of transmission with clip.
7. Connect the cable between bracket of throttle and transmission actuator.
8. Throttle valve cable adjustment as follows:
First, use pliers to clip the hexangular position under throttle valve cable.Turn 60°~90°counterclockwise,
and lift throttle valve cable to make throttle valve cable adjustable move to top position, and then turn back
60°~90° clockwise, meanwhile, make it lock (See figure 7-4). Finally put accelerator pedal to end position.
When throttle valve makes "ka-ka" sound, the distance under the throttle valve should meet B=2~8mm. If not,
try again until the gap B=2~8mm under the throttle valve (see figure 7-5), if gap B=2-8mm, throttle valve cable
adjustment is finished.Central
plateFlexible plate
Torque converter
housing end
Torque
converterFront contact face
Torque converter
anchor point
Central anchor col-
umn -
Page 74 of 416
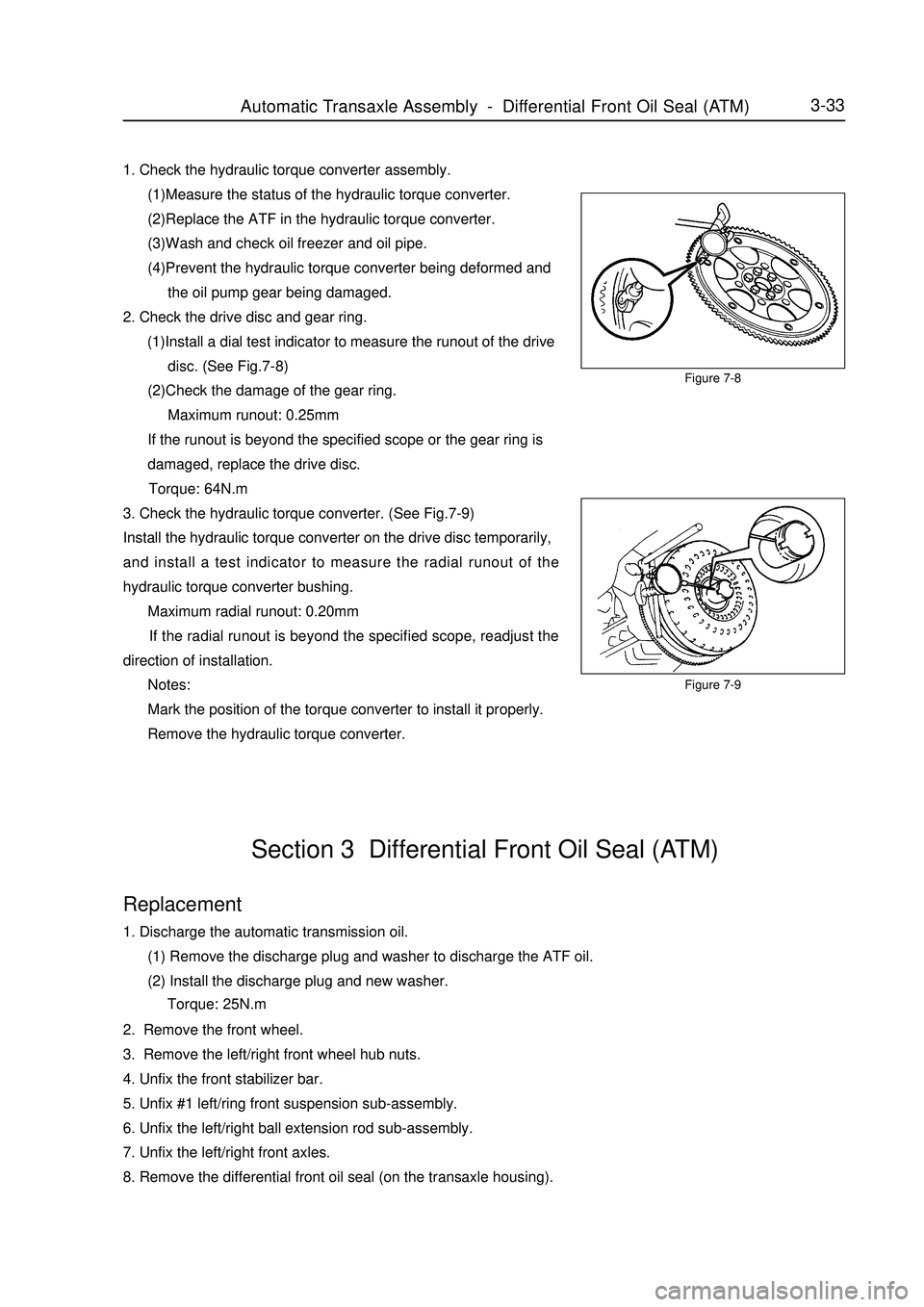
Figure 7-93-33Replacement1. Discharge the automatic transmission oil.
(1) Remove the discharge plug and washer to discharge the ATF oil.
(2) Install the discharge plug and new washer.
Torque: 25N.m
2. Remove the front wheel.
3. Remove the left/right front wheel hub nuts.
4. Unfix the front stabilizer bar.
5. Unfix #1 left/ring front suspension sub-assembly.
6. Unfix the left/right ball extension rod sub-assembly.
7. Unfix the left/right front axles.
8. Remove the differential front oil seal (on the transaxle housing).Section 3 Differential Front Oil Seal (ATM)1. Check the hydraulic torque converter assembly.
(1)Measure the status of the hydraulic torque converter.
(2)Replace the ATF in the hydraulic torque converter.
(3)Wash and check oil freezer and oil pipe.
(4)Prevent the hydraulic torque converter being deformed and
the oil pump gear being damaged.
2. Check the drive disc and gear ring.
(1)Install a dial test indicator to measure the runout of the drive
disc. (See Fig.7-8)
(2)Check the damage of the gear ring.
Maximum runout: 0.25mm
If the runout is beyond the specified scope or the gear ring is
damaged, replace the drive disc.
Torque: 64N.m
3. Check the hydraulic torque converter. (See Fig.7-9)
Install the hydraulic torque converter on the drive disc temporarily,
and install a test indicator to measure the radial runout of the
hydraulic torque converter bushing.
Maximum radial runout: 0.20mm
If the radial runout is beyond the specified scope, readjust the
direction of installation.
Notes:
Mark the position of the torque converter to install it properly.
Remove the hydraulic torque converter.Figure 7-8Automatic Transaxle Assembly Differential Front Oil Seal (ATM) -