air condition INFINITI FX35 2005 Service Manual
[x] Cancel search | Manufacturer: INFINITI, Model Year: 2005, Model line: FX35, Model: INFINITI FX35 2005Pages: 4731, PDF Size: 60.13 MB
Page 1334 of 4731
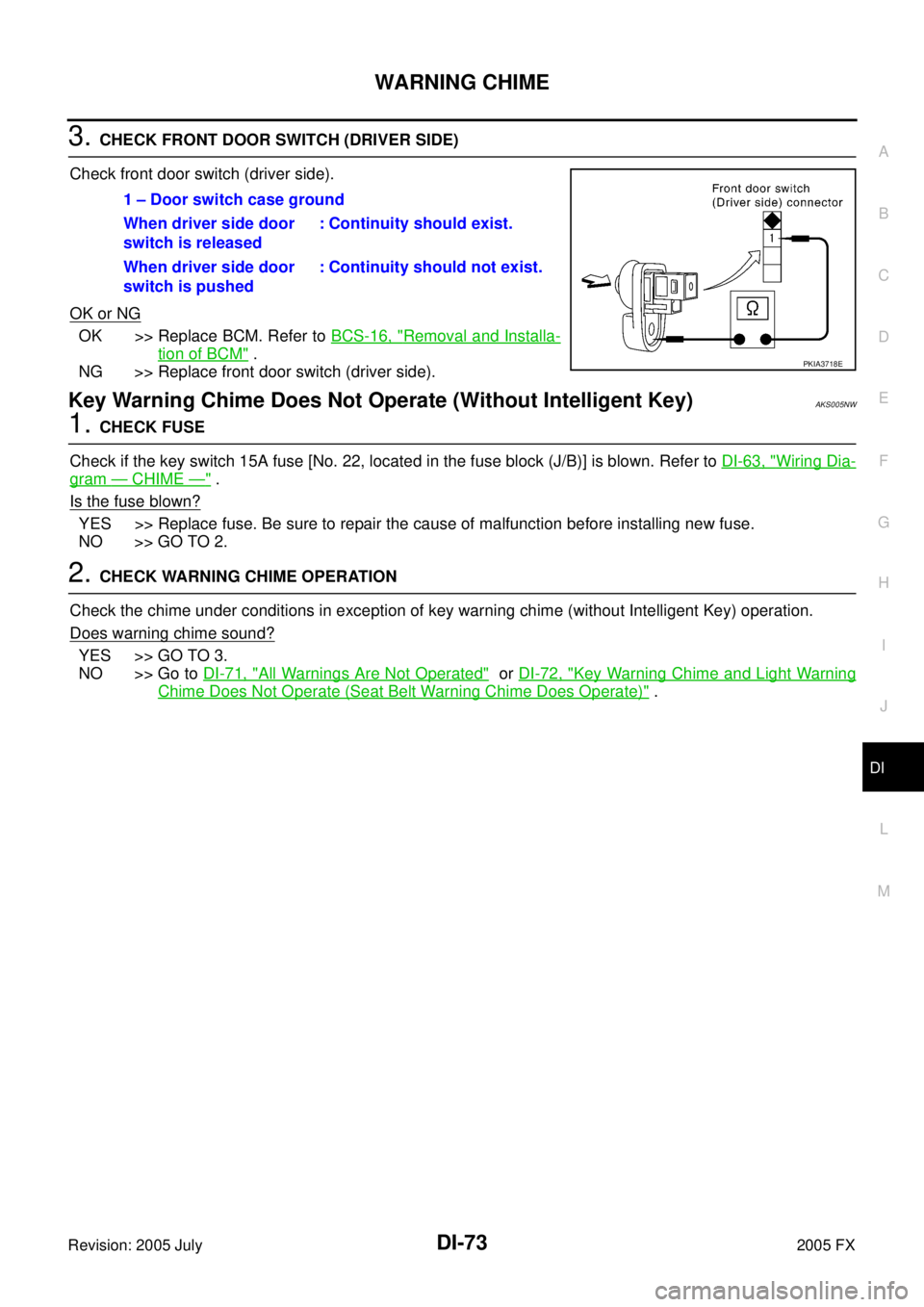
WARNING CHIME DI-73
C
D E
F
G H
I
J
L
M A
B
DI
Revision: 2005 July 2005 FX
3. CHECK FRONT DOOR SWITCH (DRIVER SIDE)
Check front door switch (driver side).
OK or NG
OK >> Replace BCM. Refer to BCS-16, "Removal and Installa-
tion of BCM" .
NG >> Replace front door switch (driver side).
Key Warning Chime Does Not Operate (Without Intelligent Key)AKS005NW
1. CHECK FUSE
Check if the key switch 15A fuse [No. 22, located in the fuse block (J/B)] is blown. Refer to DI-63, "
Wiring Dia-
gram — CHIME —" .
Is the fuse blown?
YES >> Replace fuse. Be sure to repair the cause of malfunction before installing new fuse.
NO >> GO TO 2.
2. CHECK WARNING CHIME OPERATION
Check the chime under conditions in exception of key warning chime (without Intelligent Key) operation.
Does warning chime sound?
YES >> GO TO 3.
NO >> Go to DI-71, "
All Warnings Are Not Operated" or DI-72, "Key Warning Chime and Light Warning
Chime Does Not Operate (Seat Belt Warning Chime Does Operate)" .
1 – Door switch case ground
When driver side door
switch is released : Continuity should exist.
When driver side door
switch is pushed : Continuity should not exist.
PKIA3718E
Page 1336 of 4731
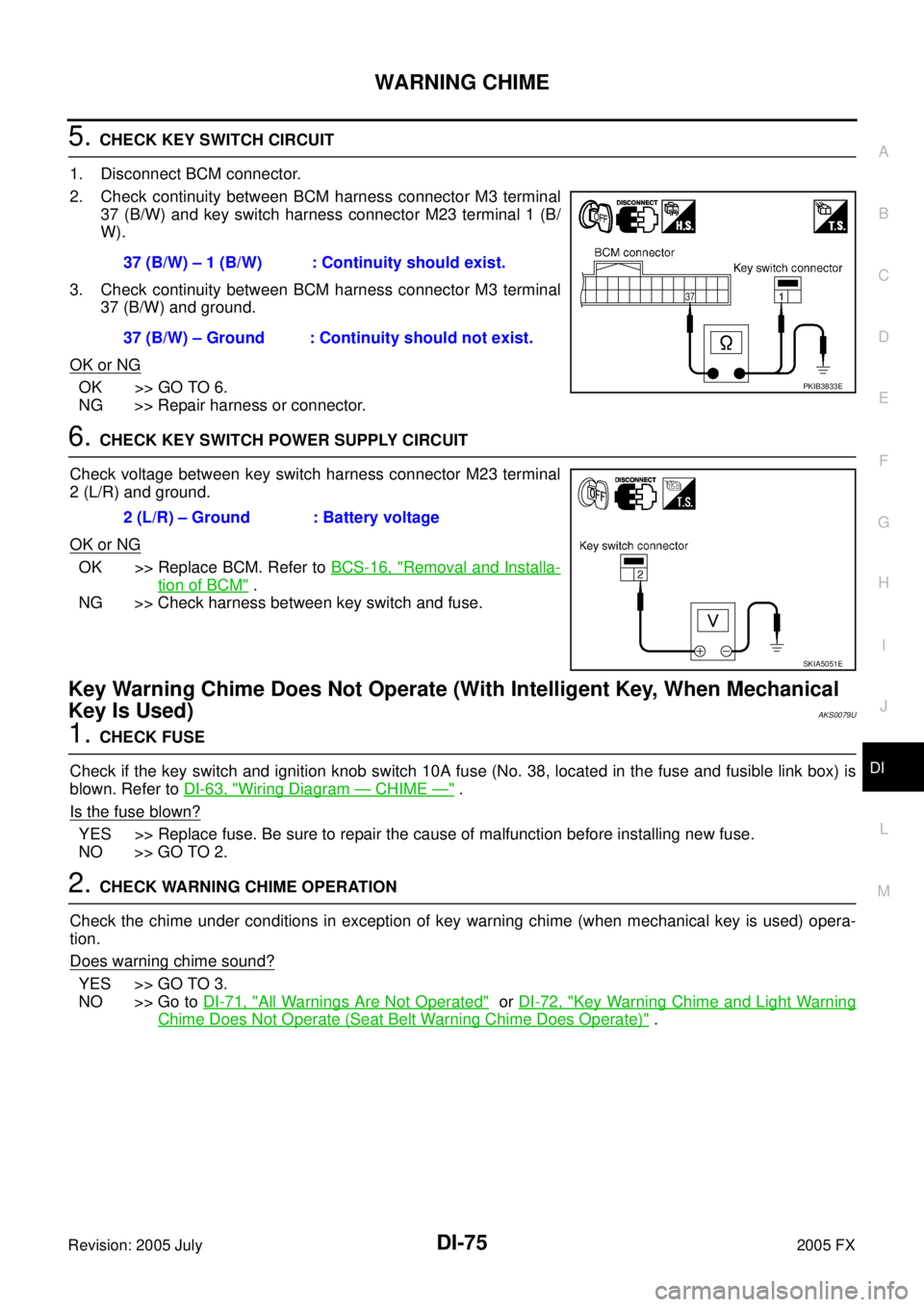
WARNING CHIME DI-75
C
D E
F
G H
I
J
L
M A
B
DI
Revision: 2005 July 2005 FX
5. CHECK KEY SWITCH CIRCUIT
1. Disconnect BCM connector.
2. Check continuity between BCM harness connector M3 terminal 37 (B/W) and key switch harness connector M23 terminal 1 (B/
W).
3. Check continuity between BCM harness connector M3 terminal 37 (B/W) and ground.
OK or NG
OK >> GO TO 6.
NG >> Repair harness or connector.
6. CHECK KEY SWITCH POWER SUPPLY CIRCUIT
Check voltage between key switch harness connector M23 terminal
2 (L/R) and ground.
OK or NG
OK >> Replace BCM. Refer to BCS-16, "Removal and Installa-
tion of BCM" .
NG >> Check harness between key switch and fuse.
Key Warning Chime Does Not Operate (With Intelligent Key, When Mechanical
Key Is Used)
AKS0079U
1. CHECK FUSE
Check if the key switch and ignition knob switch 10A fuse (No. 38, located in the fuse and fusible link box) is
blown. Refer to DI-63, "
Wiring Diagram — CHIME —" .
Is the fuse blown?
YES >> Replace fuse. Be sure to repair the cause of malfunction before installing new fuse.
NO >> GO TO 2.
2. CHECK WARNING CHIME OPERATION
Check the chime under conditions in exception of key warning chime (when mechanical key is used) opera-
tion.
Does warning chime sound?
YES >> GO TO 3.
NO >> Go to DI-71, "
All Warnings Are Not Operated" or DI-72, "Key Warning Chime and Light Warning
Chime Does Not Operate (Seat Belt Warning Chime Does Operate)" .
37 (B/W) – 1 (B/W) : Continuity should exist.
37 (B/W) – Ground : Continuity should not exist.
PKIB3833E
2 (L/R) – Ground : Battery voltage
SKIA5051E
Page 1338 of 4731
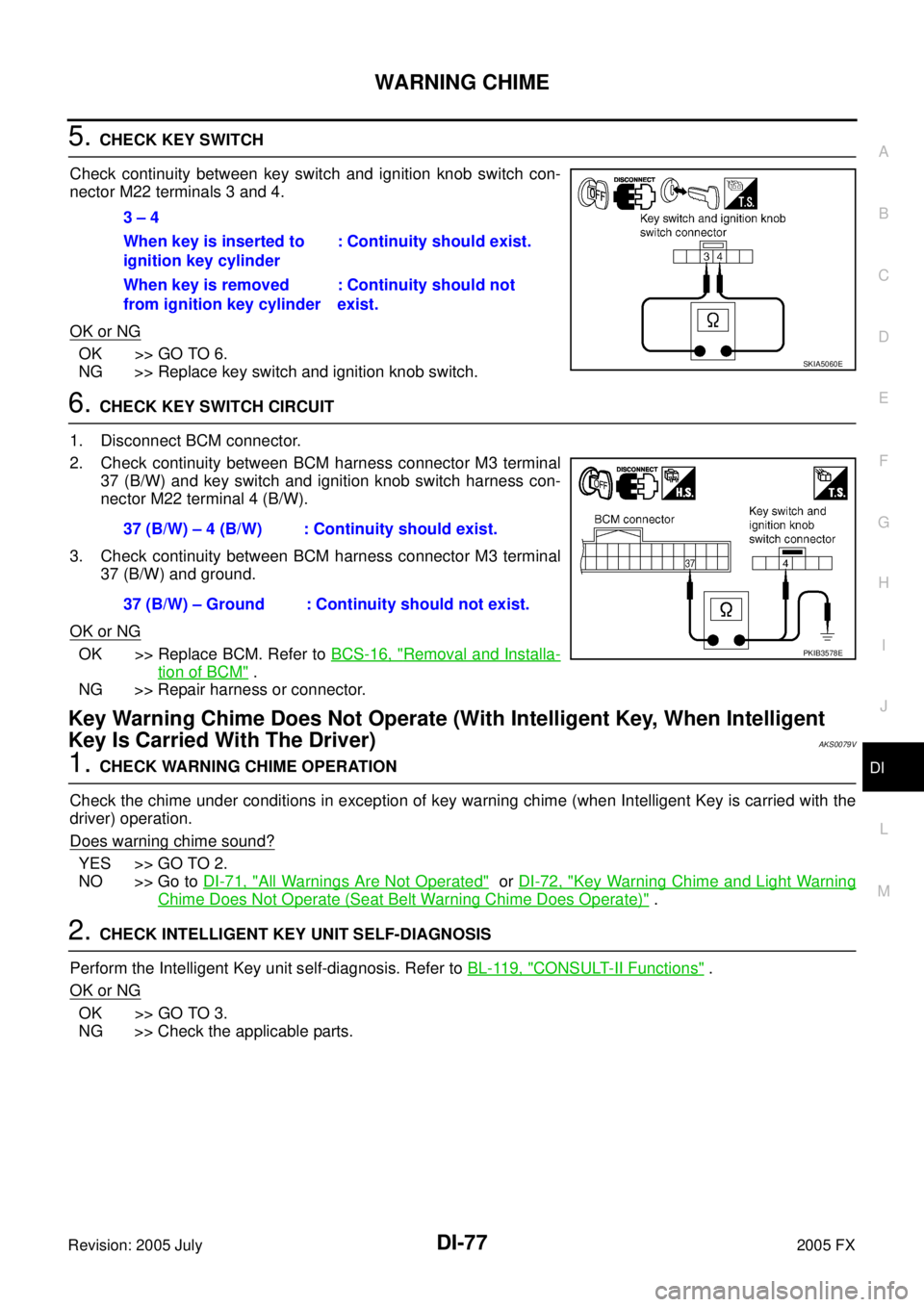
WARNING CHIME DI-77
C
D E
F
G H
I
J
L
M A
B
DI
Revision: 2005 July 2005 FX
5. CHECK KEY SWITCH
Check continuity between key switch and ignition knob switch con-
nector M22 terminals 3 and 4.
OK or NG
OK >> GO TO 6.
NG >> Replace key switch and ignition knob switch.
6. CHECK KEY SWITCH CIRCUIT
1. Disconnect BCM connector.
2. Check continuity between BCM harness connector M3 terminal 37 (B/W) and key switch and ignition knob switch harness con-
nector M22 terminal 4 (B/W).
3. Check continuity between BCM harness connector M3 terminal 37 (B/W) and ground.
OK or NG
OK >> Replace BCM. Refer to BCS-16, "Removal and Installa-
tion of BCM" .
NG >> Repair harness or connector.
Key Warning Chime Does Not Operate (With Intelligent Key, When Intelligent
Key Is Carried With The Driver)
AKS0079V
1. CHECK WARNING CHIME OPERATION
Check the chime under conditions in exception of key warning chime (when Intelligent Key is carried with the
driver) operation.
Does warning chime sound?
YES >> GO TO 2.
NO >> Go to DI-71, "
All Warnings Are Not Operated" or DI-72, "Key Warning Chime and Light Warning
Chime Does Not Operate (Seat Belt Warning Chime Does Operate)" .
2. CHECK INTELLIGENT KEY UNIT SELF-DIAGNOSIS
Perform the Intelligent Key unit self-diagnosis. Refer to BL-119, "
CONSULT-II Functions" .
OK or NG
OK >> GO TO 3.
NG >> Check the applicable parts. 3 – 4
When key is inserted to
ignition key cylinder : Continuity should exist.
When key is removed
from ignition key cylinder : Continuity should not
exist.
SKIA5060E
37 (B/W) – 4 (B/W) : Continuity should exist.
37 (B/W) – Ground : Continuity should not exist.
PKIB3578E
Page 1340 of 4731
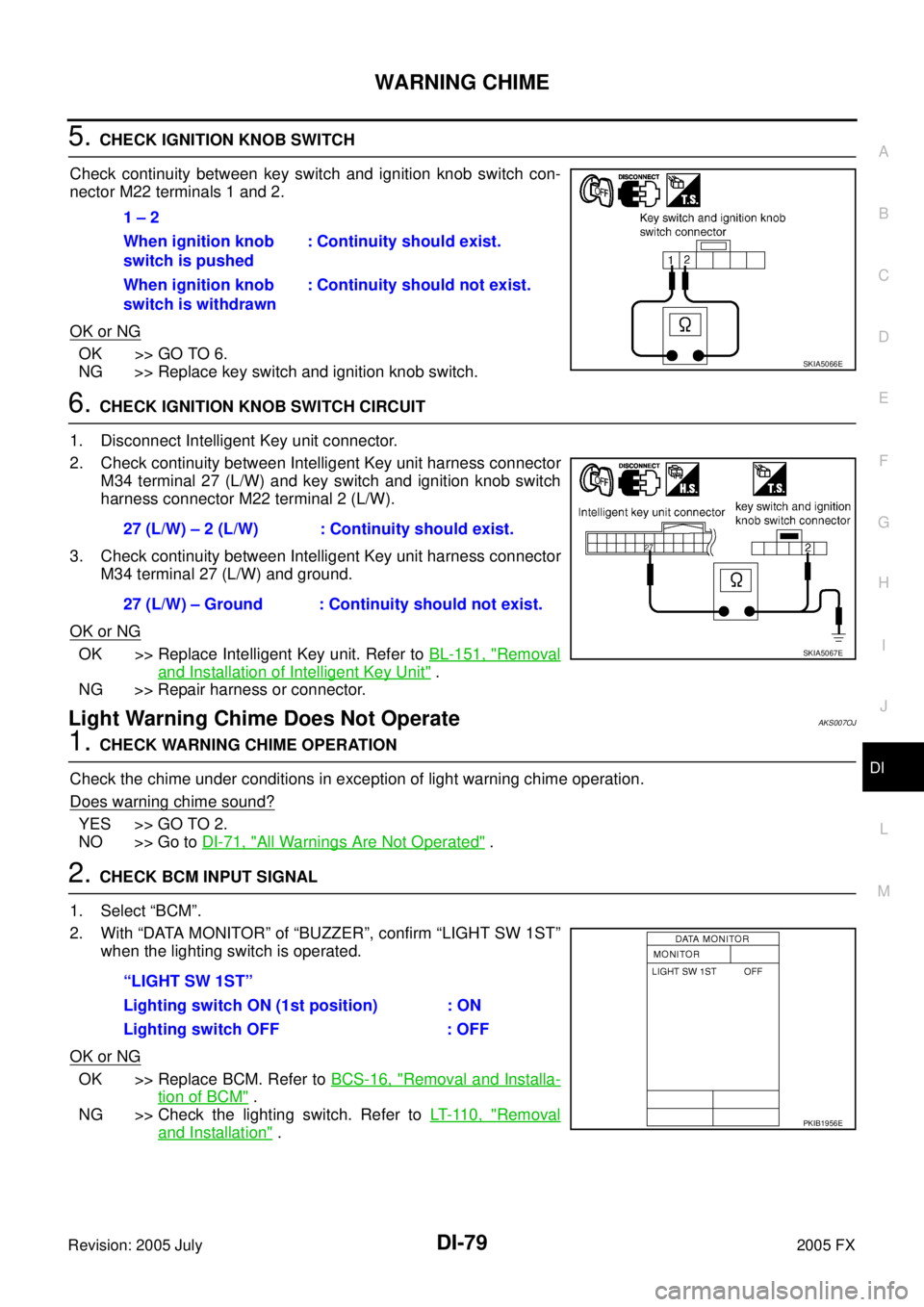
WARNING CHIME DI-79
C
D E
F
G H
I
J
L
M A
B
DI
Revision: 2005 July 2005 FX
5. CHECK IGNITION KNOB SWITCH
Check continuity between key switch and ignition knob switch con-
nector M22 terminals 1 and 2.
OK or NG
OK >> GO TO 6.
NG >> Replace key switch and ignition knob switch.
6. CHECK IGNITION KNOB SWITCH CIRCUIT
1. Disconnect Intelligent Key unit connector.
2. Check continuity between Intelligent Key unit harness connector M34 terminal 27 (L/W) and key switch and ignition knob switch
harness connector M22 terminal 2 (L/W).
3. Check continuity between Intelligent Key unit harness connector M34 terminal 27 (L/W) and ground.
OK or NG
OK >> Replace Intelligent Key unit. Refer to BL-151, "Removal
and Installation of Intelligent Key Unit" .
NG >> Repair harness or connector.
Light Warning Chime Does Not OperateAKS007OJ
1. CHECK WARNING CHIME OPERATION
Check the chime under conditions in exception of light warning chime operation.
Does warning chime sound?
YES >> GO TO 2.
NO >> Go to DI-71, "
All Warnings Are Not Operated" .
2. CHECK BCM INPUT SIGNAL
1. Select “BCM”.
2. With “DATA MONITOR” of “BUZZER”, confirm “LIGHT SW 1ST” when the lighting switch is operated.
OK or NG
OK >> Replace BCM. Refer to BCS-16, "Removal and Installa-
tion of BCM" .
NG >> Check the lighting switch. Refer to LT- 11 0 , "
Removal
and Installation" .
1 – 2
When ignition knob
switch is pushed : Continuity should exist.
When ignition knob
switch is withdrawn : Continuity should not exist.
SKIA5066E
27 (L/W) – 2 (L/W) : Continuity should exist.
27 (L/W) – Ground : Continuity should not exist.
SKIA5067E
“LIGHT SW 1ST”
Lighting switch ON (1st position) : ON
Lighting switch OFF : OFF
PKIB1956E
Page 1363 of 4731
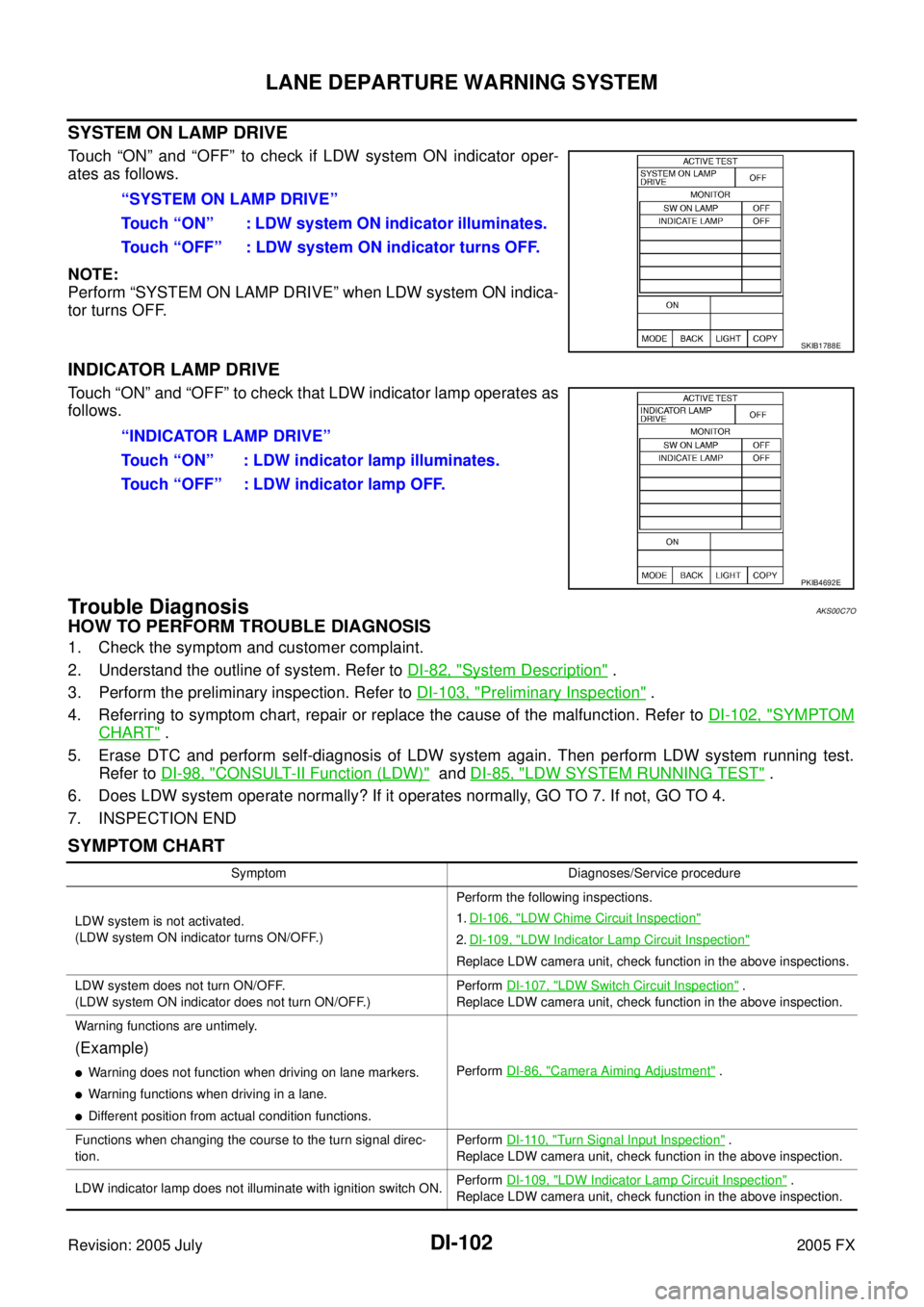
DI-102
LANE DEPARTURE WARNING SYSTEM
Revision: 2005 July 2005 FX
SYSTEM ON LAMP DRIVE
Touch “ON” and “OFF” to check if LDW system ON indicator oper-
ates as follows.
NOTE:
Perform “SYSTEM ON LAMP DRIVE” when LDW system ON indica-
tor turns OFF.
INDICATOR LAMP DRIVE
Touch “ON” and “OFF” to check that LDW indicator lamp operates as
follows.
Trouble DiagnosisAKS00C7O
HOW TO PERFORM TROUBLE DIAGNOSIS
1. Check the symptom and customer complaint.
2. Understand the outline of system. Refer to DI-82, "
System Description" .
3. Perform the preliminary inspection. Refer to DI-103, "
Preliminary Inspection" .
4. Referring to symptom chart, repair or replace the cause of the malfunction. Refer to DI-102, "
SYMPTOM
CHART" .
5. Erase DTC and perform self-diagnosis of LDW system again. Then perform LDW system running test. Refer to DI-98, "
CONSULT-II Function (LDW)" and DI-85, "LDW SYSTEM RUNNING TEST" .
6. Does LDW system operate normally? If it operates normally, GO TO 7. If not, GO TO 4.
7. INSPECTION END
SYMPTOM CHART
“SYSTEM ON LAMP DRIVE”
Touch “ON” : LDW system ON indicator illuminates.
Touch “OFF” : LDW system ON indicator turns OFF.
SKIB1788E
“INDICATOR LAMP DRIVE”
Touch “ON” : LDW indicator lamp illuminates.
Touch “OFF” : LDW indicator lamp OFF.
PKIB4692E
Symptom Diagnoses/Service procedure
LDW system is not activated.
(LDW system ON indicator turns ON/OFF.) Perform the following inspections.
1. DI-106, "
LDW Chime Circuit Inspection"
2.DI-109, "LDW Indicator Lamp Circuit Inspection"
Replace LDW camera unit, check function in the above inspections.
LDW system does not turn ON/OFF.
(LDW system ON indicator does not turn ON/OFF.) Perform
DI-107, "
LDW Switch Circuit Inspection" .
Replace LDW camera unit, check function in the above inspection.
Warning functions are untimely.
(Example)
Warning does not function when driving on lane markers.
Warning functions when driving in a lane.
Different position from actual condition functions. Perform
DI-86, "
Camera Aiming Adjustment" .
Functions when changing the course to the turn signal direc-
tion. Perform
DI-110, "
Turn Signal Input Inspection" .
Replace LDW camera unit, check function in the above inspection.
LDW indicator lamp does not illuminate with ignition switch ON. Perform
DI-109, "
LDW Indicator Lamp Circuit Inspection" .
Replace LDW camera unit, check function in the above inspection.
Page 1364 of 4731
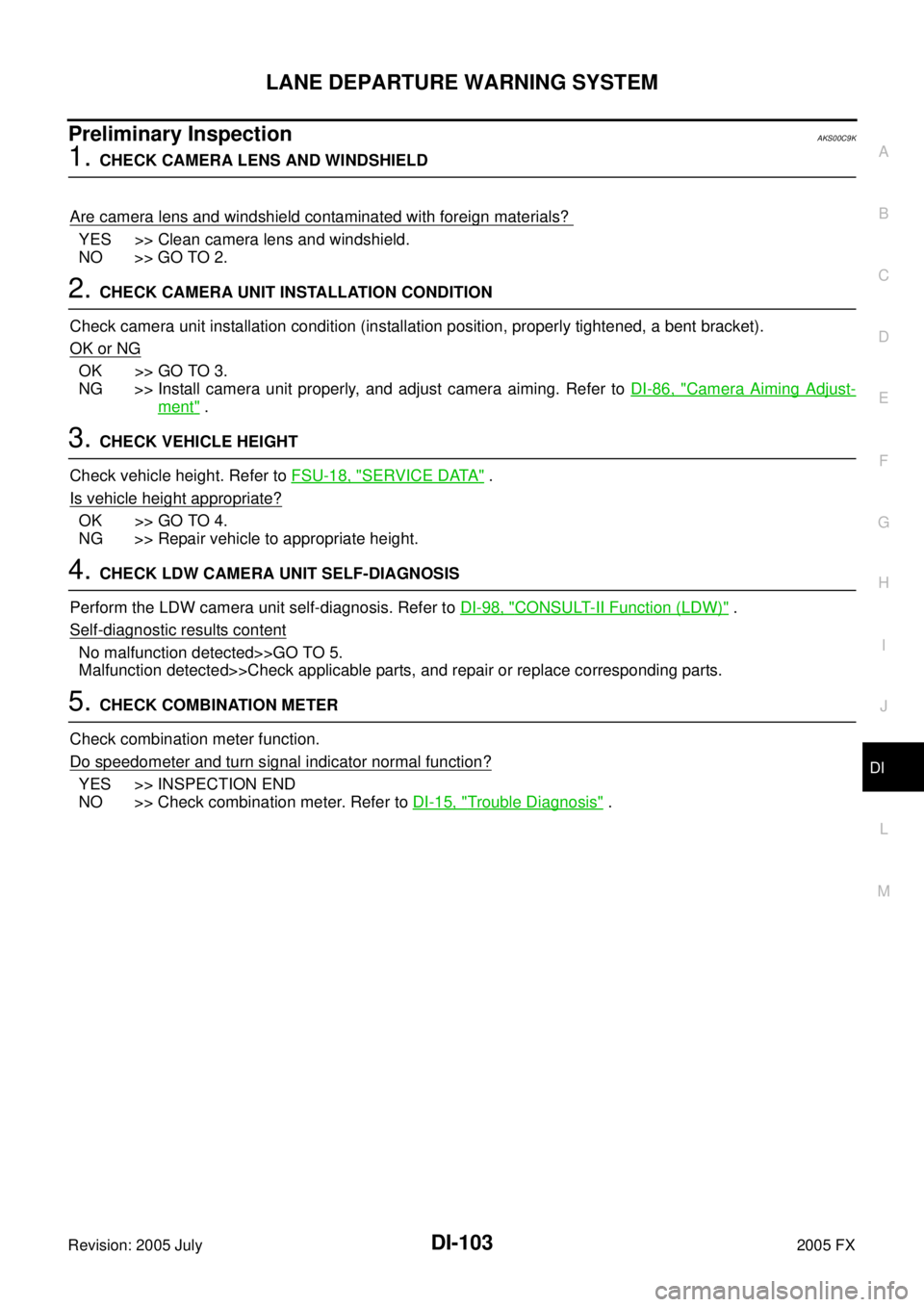
LANE DEPARTURE WARNING SYSTEM DI-103
C
D E
F
G H
I
J
L
M A
B
DI
Revision: 2005 July 2005 FX
Preliminary InspectionAKS00C9K
1. CHECK CAMERA LENS AND WINDSHIELD
Are camera lens and windshield contaminated with foreign materials?
YES >> Clean camera lens and windshield.
NO >> GO TO 2.
2. CHECK CAMERA UNIT INSTALLATION CONDITION
Check camera unit installation condition (installation position, properly tightened, a bent bracket).
OK or NG
OK >> GO TO 3.
NG >> Install camera unit properly, and adjust camera aiming. Refer to DI-86, "
Camera Aiming Adjust-
ment" .
3. CHECK VEHICLE HEIGHT
Check vehicle height. Refer to FSU-18, "
SERVICE DATA" .
Is vehicle height appropriate?
OK >> GO TO 4.
NG >> Repair vehicle to appropriate height.
4. CHECK LDW CAMERA UNIT SELF-DIAGNOSIS
Perform the LDW camera unit self-diagnosis. Refer to DI-98, "
CONSULT-II Function (LDW)" .
Self
-diagnostic results content
No malfunction detected>>GO TO 5.
Malfunction detected>>Check applicable parts, and repair or replace corresponding parts.
5. CHECK COMBINATION METER
Check combination meter function.
Do speedometer and turn signal indicator normal function?
YES >> INSPECTION END
NO >> Check combination meter. Refer to DI-15, "
Trouble Diagnosis" .
Page 1394 of 4731
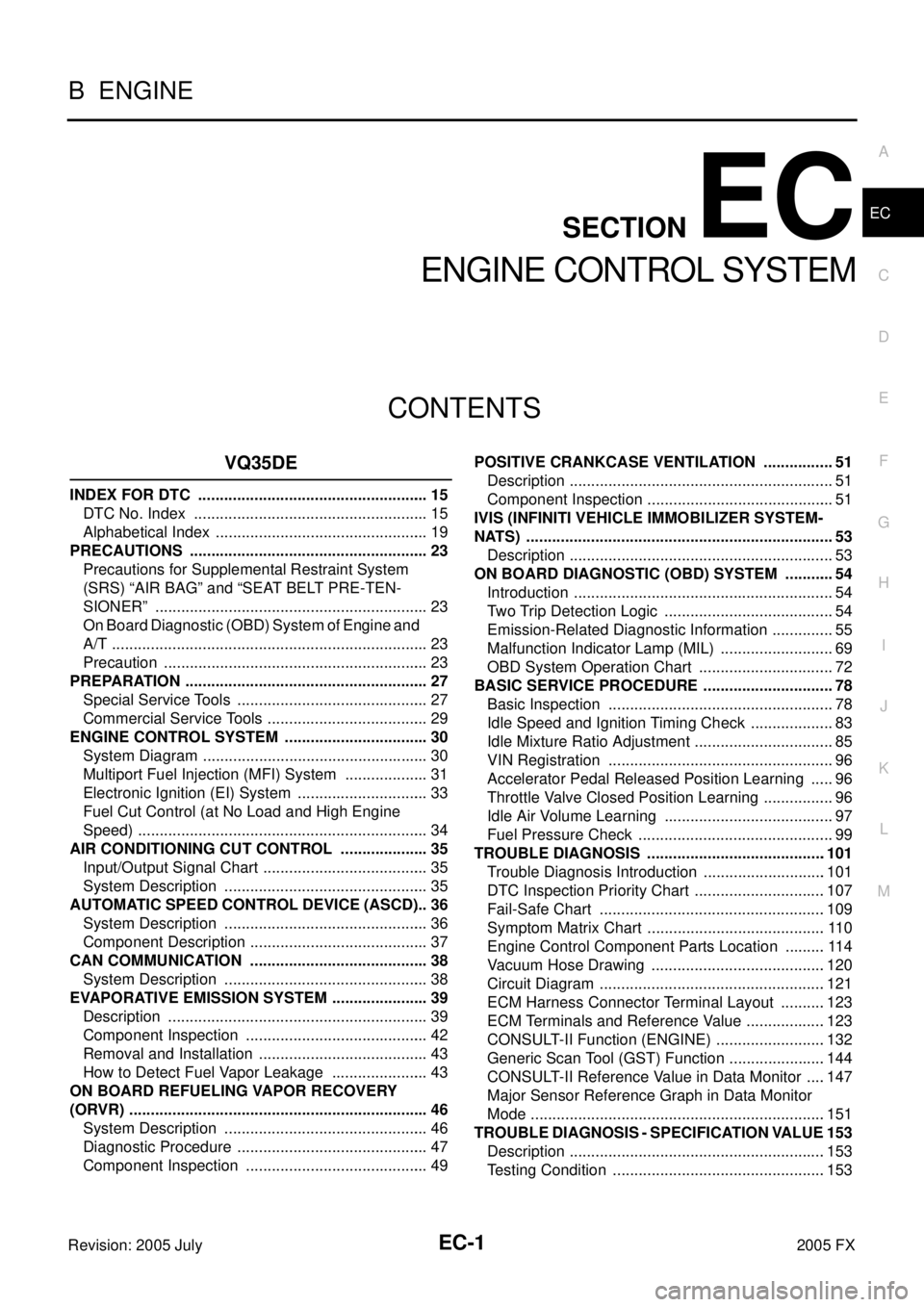
EC-1
ENGINE CONTROL SYSTEM
B ENGINE
CONTENTS
C
D E
F
G H
I
J
K L
M
SECTION EC
A
EC
Revision: 2005 July 2005 FX
ENGINE CONTROL SYSTEM
VQ35DE
INDEX FOR DTC ...................................................... 15
DTC No. Index .................................................... ... 15
Alphabetical Index ............................................... ... 19
PRECAUTIONS ..................................................... ... 23
Precautions for Supplemental Restraint System
(SRS) “AIR BAG” and “SEAT BELT PRE-TEN-
SIONER” ............................................................. ... 23
On Board Diagnostic (OBD) System of Engine and
A/T ....................................................................... ... 23
Precaution ........................................................... ... 23
PREPARATION ...................................................... ... 27
Special Service Tools .......................................... ... 27
Commercial Service Tools ................................... ... 29
ENGINE CONTROL SYSTEM ............................... ... 30
System Diagram .................................................. ... 30
Multiport Fuel Injection (MFI) System ................. ... 31
Electronic Ignition (EI) System ............................ ... 33
Fuel Cut Control (at No Load and High Engine
Speed) ................................................................. ... 34
AIR CONDITIONING CUT CONTROL .................. ... 35
Input/Output Signal Chart .................................... ... 35
System Description ............................................. ... 35
AUTOMATIC SPEED CONTROL DEVICE (ASCD) ... 36
System Description ............................................. ... 36
Component Description ....................................... ... 37
CAN COMMUNICATION ....................................... ... 38
System Description ............................................. ... 38
EVAPORATIVE EMISSION SYSTEM .................... ... 39
Description .......................................................... ... 39
Component Inspection ........................................ ... 42
Removal and Installation ..................................... ... 43
How to Detect Fuel Vapor Leakage .................... ... 43
ON BOARD REFUELING VAPOR RECOVERY
(ORVR) ................................................................... ... 46
System Description ............................................. ... 46
Diagnostic Procedure .......................................... ... 47
Component Inspection ........................................ ... 49 POSITIVE CRANKCASE VENTILATION ..............
... 51
Description ........................................................... ... 51
Component Inspection ......................................... ... 51
IVIS (INFINITI VEHICLE IMMOBILIZER SYSTEM-
NATS) ..................................................................... ... 53
Description ........................................................... ... 53
ON BOARD DIAGNOSTIC (OBD) SYSTEM ......... ... 54
Introduction .......................................................... ... 54
Two Trip Detection Logic ..................................... ... 54
Emission-Related Diagnostic Information ............ ... 55
Malfunction Indicator Lamp (MIL) ........................ ... 69
OBD System Operation Chart ............................. ... 72
BASIC SERVICE PROCEDURE ............................ ... 78
Basic Inspection .................................................. ... 78
Idle Speed and Ignition Timing Check ................. ... 83
Idle Mixture Ratio Adjustment .............................. ... 85
VIN Registration .................................................. ... 96
Accelerator Pedal Released Position Learning ... ... 96
Throttle Valve Closed Position Learning .............. ... 96
Idle Air Volume Learning ..................................... ... 97
Fuel Pressure Check ........................................... ... 99
TROUBLE DIAGNOSIS ......................................... .101
Trouble Diagnosis Introduction ............................ .101
DTC Inspection Priority Chart .............................. .107
Fail-Safe Chart .................................................... .109
Symptom Matrix Chart ......................................... .110
Engine Control Component Parts Location ......... .114
Vacuum Hose Drawing ........................................ .120
Circuit Diagram .................................................... .121
ECM Harness Connector Terminal Layout .......... .123
ECM Terminals and Reference Value .................. .123
CONSULT-II Function (ENGINE) ......................... .132
Generic Scan Tool (GST) Function ...................... .144
CONSULT-II Reference Value in Data Monitor .... .147
Major Sensor Reference Graph in Data Monitor
Mode .................................................................... .151
TROUBLE DIAGNOSIS - SPECIFICATION VALUE .153
Description ........................................................... .153
Testing Condition ................................................. .153
Page 1401 of 4731
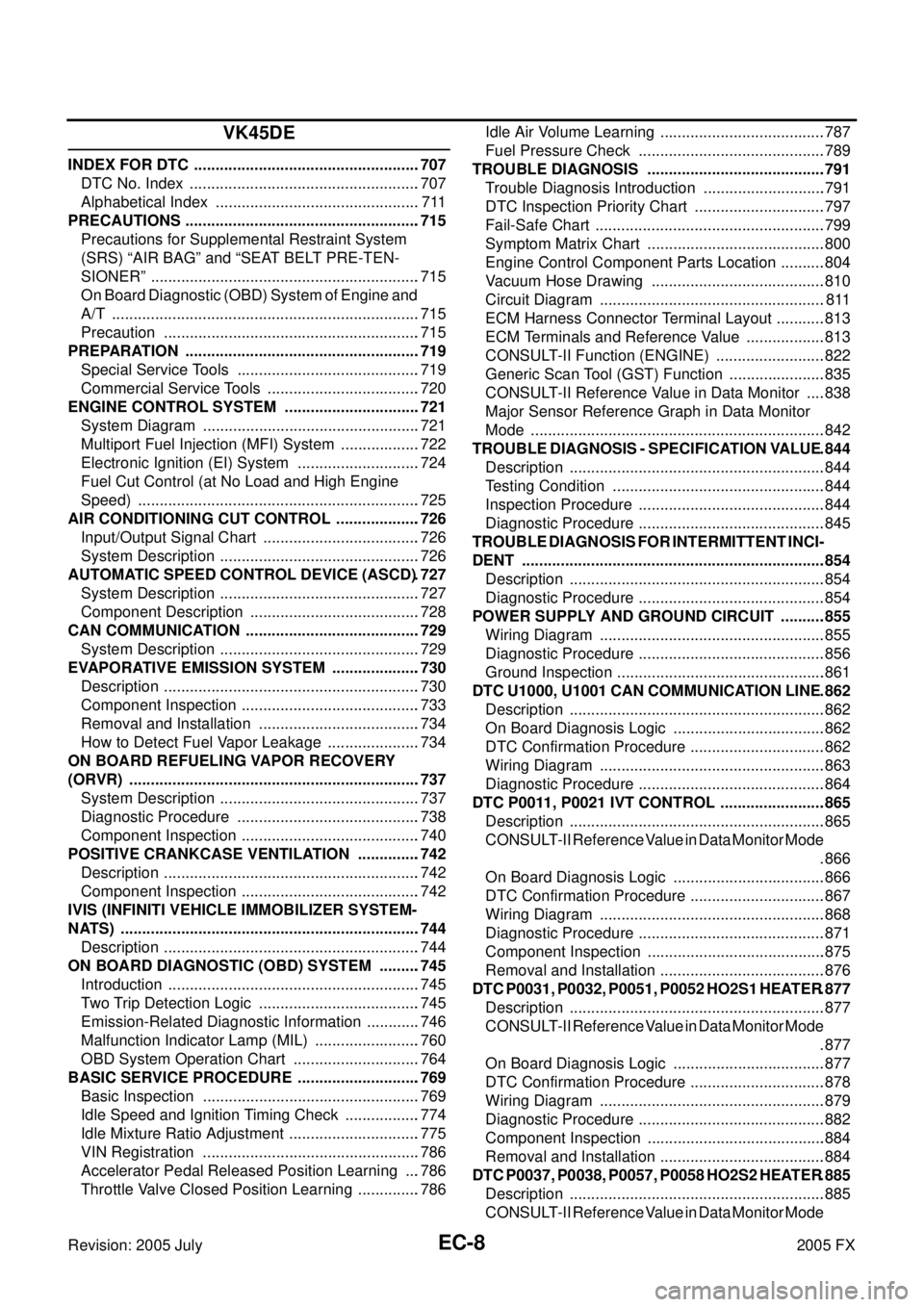
EC-8Revision: 2005 July 2005 FX
VK45DE
INDEX FOR DTC .....................................................707
DTC No. Index ..................................................... .707
Alphabetical Index ............................................... .711
PRECAUTIONS ...................................................... .715
Precautions for Supplemental Restraint System
(SRS) “AIR BAG” and “SEAT BELT PRE-TEN-
SIONER” .............................................................. .715
On Board Diagnostic (OBD) System of Engine and
A/T ....................................................................... .715
Precaution ........................................................... .715
PREPARATION ...................................................... .719
Special Service Tools .......................................... .719
Commercial Service Tools ................................... .720
ENGINE CONTROL SYSTEM ............................... .721
System Diagram .................................................. .721
Multiport Fuel Injection (MFI) System .................. .722
Electronic Ignition (EI) System ............................ .724
Fuel Cut Control (at No Load and High Engine
Speed) ................................................................. .725
AIR CONDITIONING CUT CONTROL ................... .726
Input/Output Signal Chart .................................... .726
System Description .............................................. .726
AUTOMATIC SPEED CONTROL DEVICE (ASCD) .727
System Description .............................................. .727
Component Description ....................................... .728
CAN COMMUNICATION ........................................ .729
System Description .............................................. .729
EVAPORATIVE EMISSION SYSTEM .................... .730
Description ........................................................... .730
Component Inspection ......................................... .733
Removal and Installation ..................................... .734
How to Detect Fuel Vapor Leakage ..................... .734
ON BOARD REFUELING VAPOR RECOVERY
(ORVR) ................................................................... .737
System Description .............................................. .737
Diagnostic Procedure .......................................... .738
Component Inspection ......................................... .740
POSITIVE CRANKCASE VENTILATION .............. .742
Description ........................................................... .742
Component Inspection ......................................... .742
IVIS (INFINITI VEHICLE IMMOBILIZER SYSTEM-
NATS) ..................................................................... .744
Description ........................................................... .744
ON BOARD DIAGNOSTIC (OBD) SYSTEM ......... .745
Introduction .......................................................... .745
Two Trip Detection Logic ..................................... .745
Emission-Related Diagnostic Information ............ .746
Malfunction Indicator Lamp (MIL) ........................ .760
OBD System Operation Chart ............................. .764
BASIC SERVICE PROCEDURE ............................ .769
Basic Inspection .................................................. .769
Idle Speed and Ignition Timing Check ................. .774
Idle Mixture Ratio Adjustment .............................. .775
VIN Registration .................................................. .786
Accelerator Pedal Released Position Learning ... .786
Throttle Valve Closed Position Learning .............. .786 Idle Air Volume Learning ......................................
.787
Fuel Pressure Check ........................................... .789
TROUBLE DIAGNOSIS ......................................... .791
Trouble Diagnosis Introduction ............................ .791
DTC Inspection Priority Chart .............................. .797
Fail-Safe Chart ..................................................... .799
Symptom Matrix Chart ......................................... .800
Engine Control Component Parts Location .......... .804
Vacuum Hose Drawing ........................................ .810
Circuit Diagram .................................................... .811
ECM Harness Connector Terminal Layout ........... .813
ECM Terminals and Reference Value .................. .813
CONSULT-II Function (ENGINE) ......................... .822
Generic Scan Tool (GST) Function ...................... .835
CONSULT-II Reference Value in Data Monitor .... .838
Major Sensor Reference Graph in Data Monitor
Mode .................................................................... .842
TROUBLE DIAGNOSIS - SPECIFICATION VALUE .844
Description ........................................................... .844
Testing Condition ................................................. .844
Inspection Procedure ........................................... .844
Diagnostic Procedure ........................................... .845
TROUBLE DIAGNOSIS FOR INTERMITTENT INCI-
DENT ...................................................................... .854
Description ........................................................... .854
Diagnostic Procedure ........................................... .854
POWER SUPPLY AND GROUND CIRCUIT .......... .855
Wiring Diagram .................................................... .855
Diagnostic Procedure ........................................... .856
Ground Inspection ................................................ .861
DTC U1000, U1001 CAN COMMUNICATION LINE .862
Description ........................................................... .862
On Board Diagnosis Logic ................................... .862
DTC Confirmation Procedure ............................... .862
Wiring Diagram .................................................... .863
Diagnostic Procedure ........................................... .864
DTC P0011, P0021 IVT CONTROL ........................ .865
Description ........................................................... .865
CONSULT-II Reference Value in Data Monitor Mode .866
On Board Diagnosis Logic ................................... .866
DTC Confirmation Procedure ............................... .867
Wiring Diagram .................................................... .868
Diagnostic Procedure ........................................... .871
Component Inspection ......................................... .875
Removal and Installation ...................................... .876
DTC P0031, P0032, P0051, P0052 HO2S1 HEATER .877
Description ........................................................... .877
CONSULT-II Reference Value in Data Monitor Mode .877
On Board Diagnosis Logic ................................... .877
DTC Confirmation Procedure ............................... .878
Wiring Diagram .................................................... .879
Diagnostic Procedure ........................................... .882
Component Inspection ......................................... .884
Removal and Installation ...................................... .884
DTC P0037, P0038, P0057, P0058 HO2S2 HEATER .885
Description ........................................................... .885
CONSULT-II Reference Value in Data Monitor Mode
Page 1424 of 4731
![INFINITI FX35 2005 Service Manual ENGINE CONTROL SYSTEM EC-31
[VQ35DE]
C
D E
F
G H
I
J
K L
M A
EC
Revision: 2005 July 2005 FX
Multiport Fuel Injection (MFI) SystemABS006K7
INPUT/OUTPUT SIGNAL CHART
*1: This sensor is not INFINITI FX35 2005 Service Manual ENGINE CONTROL SYSTEM EC-31
[VQ35DE]
C
D E
F
G H
I
J
K L
M A
EC
Revision: 2005 July 2005 FX
Multiport Fuel Injection (MFI) SystemABS006K7
INPUT/OUTPUT SIGNAL CHART
*1: This sensor is not](/img/42/57020/w960_57020-1423.png)
ENGINE CONTROL SYSTEM EC-31
[VQ35DE]
C
D E
F
G H
I
J
K L
M A
EC
Revision: 2005 July 2005 FX
Multiport Fuel Injection (MFI) SystemABS006K7
INPUT/OUTPUT SIGNAL CHART
*1: This sensor is not used to control the engine system under normal conditions.
*2: This signal is sent to the ECM through CAN communication line.
*3: ECM determines the start signal status by the signals of engine speed and battery voltage.
SYSTEM DESCRIPTION
The amount of fuel injected from the fuel injector is determined by the ECM. The ECM controls the length of
time the valve remains open (injection pulse duration). The amount of fuel injected is a program value in the
ECM memory. The program value is preset by engine operating conditions. These conditions are determined
by input signals (for engine speed and intake air) from both the crankshaft position sensor and the mass air
flow sensor.
VARIOUS FUEL INJECTION INCREASE/DECREASE COMPENSATION
In addition, the amount of fuel injected is compensated to improve engine performance under various operat-
ing conditions as listed below.
During warm-up
When starting the engine
During acceleration
Hot-engine operation
When selector lever is changed from N to D
High-load, high-speed operation
During deceleration
During high engine speed operation
Sensor Input Signal to ECM ECM function Actuator
Crankshaft position sensor (POS) Engine speed*
3
Piston position
Fuel injection
& mixture ratio
control Fuel injector
Camshaft position sensor (PHASE)
Mass air flow sensor Amount of intake air
Engine coolant temperature sensor Engine coolant temperature
Air fuel ratio (A/F) sensor 1 Density of oxygen in exhaust gas
Throttle position sensor Throttle position
Accelerator pedal position sensor Accelerator pedal position
Park/neutral position (PNP) switch Gear position
Knock sensor Engine knocking condition
Battery Battery voltage*
3
Power steering pressure sensor Power steering operation
Heated oxygen sensor 2*
1Density of oxygen in exhaust gas
Air conditioner switch*
2Air conditioner operation
Wheel sensor*
2Vehicle speed
Page 1425 of 4731
![INFINITI FX35 2005 Service Manual EC-32
[VQ35DE]
ENGINE CONTROL SYSTEM
Revision: 2005 July 2005 FX
MIXTURE RATIO FEEDBACK CONTROL (CLOSED LOOP CONTROL)
The mixture ratio feedback system provides the best air-fuel mixture ratio for dri INFINITI FX35 2005 Service Manual EC-32
[VQ35DE]
ENGINE CONTROL SYSTEM
Revision: 2005 July 2005 FX
MIXTURE RATIO FEEDBACK CONTROL (CLOSED LOOP CONTROL)
The mixture ratio feedback system provides the best air-fuel mixture ratio for dri](/img/42/57020/w960_57020-1424.png)
EC-32
[VQ35DE]
ENGINE CONTROL SYSTEM
Revision: 2005 July 2005 FX
MIXTURE RATIO FEEDBACK CONTROL (CLOSED LOOP CONTROL)
The mixture ratio feedback system provides the best air-fuel mixture ratio for driveability and emission control.
The three way catalyst 1 can then better reduce CO, HC and NOx emissions. This system uses air fuel ratio
(A/F) sensor 1 in the exhaust manifold to monitor whether the engine operation is rich or lean. The ECM
adjusts the injection pulse width according to the sensor voltage signal. For more information about air fuel
ratio (A/F) sensor 1, refer to EC-488
. This maintains the mixture ratio within the range of stoichiometric (ideal
air-fuel mixture).
This stage is referred to as the closed loop control condition.
Heated oxygen sensor 2 is located downstream of the three way catalyst 1. Even if the switching characteris-
tics of air fuel ratio (A/F) sensor 1 shift, the air-fuel ratio is controlled to stoichiometric by the signal from
heated oxygen sensor 2.
Open Loop Control
The open loop system condition refers to when the ECM detects any of the following conditions. Feedback
control stops in order to maintain stabilized fuel combustion.
Deceleration and acceleration
High-load, high-speed operation
Malfunction of air fuel ratio (A/F) sensor 1 or its circuit
Insufficient activation of air fuel ratio (A/F) sensor 1 at low engine coolant temperature
High engine coolant temperature
During warm-up
After shifting from N to D
When starting the engine
MIXTURE RATIO SELF-LEARNING CONTROL
The mixture ratio feedback control system monitors the mixture ratio signal transmitted from air fuel ratio (A/F)
sensor 1. This feedback signal is then sent to the ECM. The ECM controls the basic mixture ratio as close to
the theoretical mixture ratio as possible. However, the basic mixture ratio is not necessarily controlled as orig-
inally designed. Both manufacturing differences (i.e., mass air flow sensor hot wire) and characteristic
changes during operation (i.e., injector clogging) directly affect mixture ratio.
Accordingly, the difference between the basic and theoretical mixture ratios is monitored in this system. This is
then computed in terms of “injection pulse duration” to automatically compensate for the difference between
the two ratios.
“Fuel trim” refers to the feedback compensation value compared against the basic injection duration. Fuel trim
includes short term fuel trim and long term fuel trim.
“Short term fuel trim” is the short-term fuel compensation used to maintain the mixture ratio at its theoretical
value. The signal from air fuel ratio (A/F) sensor 1 indicates whether the mixture ratio is RICH or LEAN com-
pared to the theoretical value. The signal then triggers a reduction in fuel volume if the mixture ratio is rich, and
an increase in fuel volume if it is lean.
“Long term fuel trim” is overall fuel compensation carried out long-term to compensate for continual deviation
of the short term fuel trim from the central value. Such deviation will occur due to individual engine differences,
wear over time and changes in the usage environment.
SEF503YB