power steering system INFINITI M35 2007 Factory Owner's Guide
[x] Cancel search | Manufacturer: INFINITI, Model Year: 2007, Model line: M35, Model: INFINITI M35 2007Pages: 4647, PDF Size: 93.69 MB
Page 1094 of 4647
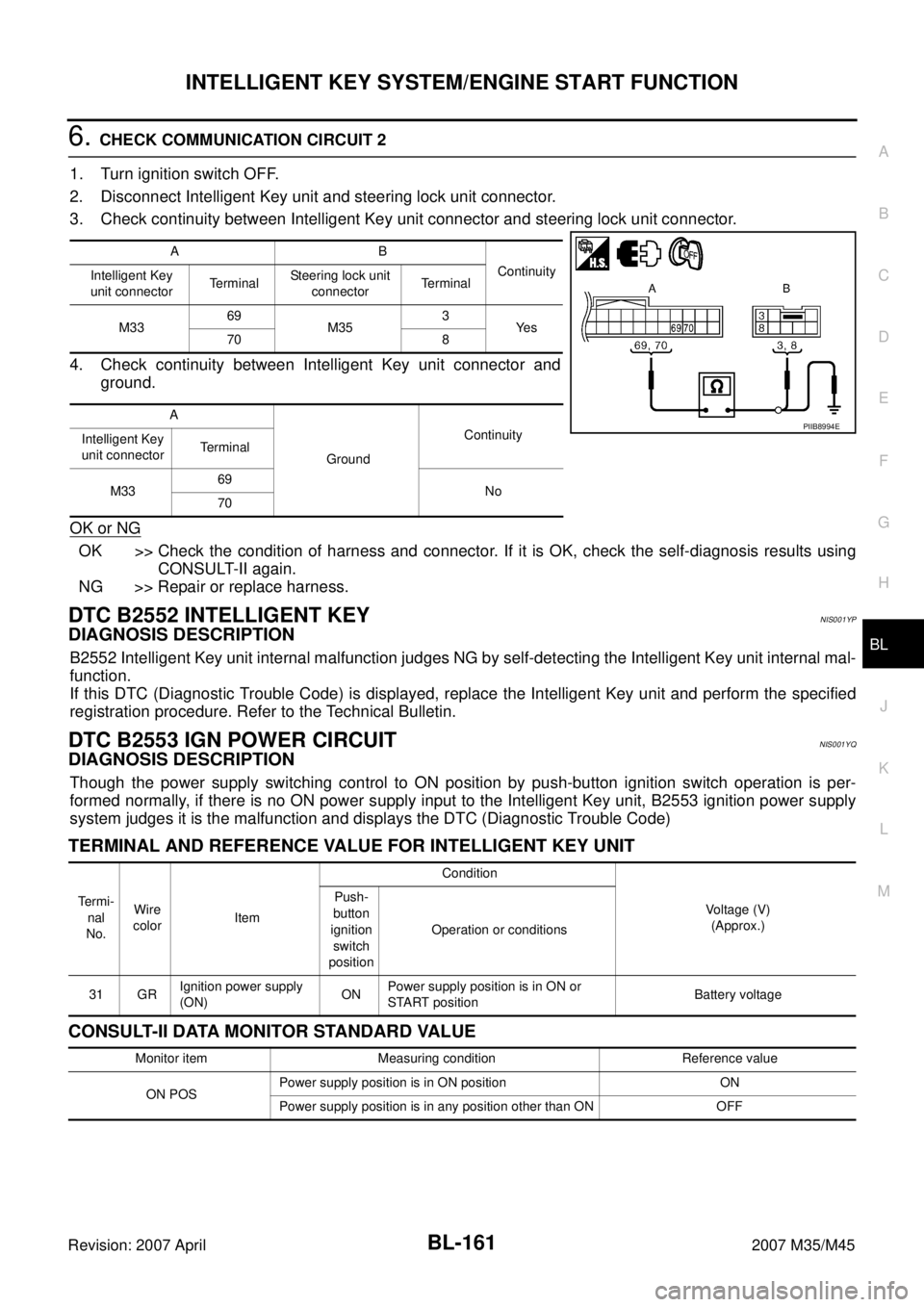
INTELLIGENT KEY SYSTEM/ENGINE START FUNCTION
BL-161
C
D
E
F
G
H
J
K
L
MA
B
BL
Revision: 2007 April2007 M35/M45
6. CHECK COMMUNICATION CIRCUIT 2
1. Turn ignition switch OFF.
2. Disconnect Intelligent Key unit and steering lock unit connector.
3. Check continuity between Intelligent Key unit connector and steering lock unit connector.
4. Check continuity between Intelligent Key unit connector and
ground.
OK or NG
OK >> Check the condition of harness and connector. If it is OK, check the self-diagnosis results using
CONSULT-II again.
NG >> Repair or replace harness.
DTC B2552 INTELLIGENT KEYNIS001YP
DIAGNOSIS DESCRIPTION
B2552 Intelligent Key unit internal malfunction judges NG by self-detecting the Intelligent Key unit internal mal-
function.
If this DTC (Diagnostic Trouble Code) is displayed, replace the Intelligent Key unit and perform the specified
registration procedure. Refer to the Technical Bulletin.
DTC B2553 IGN POWER CIRCUITNIS001YQ
DIAGNOSIS DESCRIPTION
Though the power supply switching control to ON position by push-button ignition switch operation is per-
formed normally, if there is no ON power supply input to the Intelligent Key unit, B2553 ignition power supply
system judges it is the malfunction and displays the DTC (Diagnostic Trouble Code)
TERMINAL AND REFERENCE VALUE FOR INTELLIGENT KEY UNIT
CONSULT-II DATA MONITOR STANDARD VALUE
AB
Continuity
Intelligent Key
unit connectorTerminalSteering lock unit
connectorTerminal
M3369
M353
Ye s
70 8
A
GroundContinuity
Intelligent Key
unit connectorTerminal
M3369
No
70
PIIB8994E
Te r m i -
nal
No.Wire
colorItemCondition
Voltage (V)
(Approx.) Push-
button
ignition
switch
positionOperation or conditions
31 GRIgnition power supply
(ON)ONPower supply position is in ON or
START positionBattery voltage
Monitor item Measuring condition Reference value
ON POSPower supply position is in ON position ON
Power supply position is in any position other than ON OFF
Page 1180 of 4647
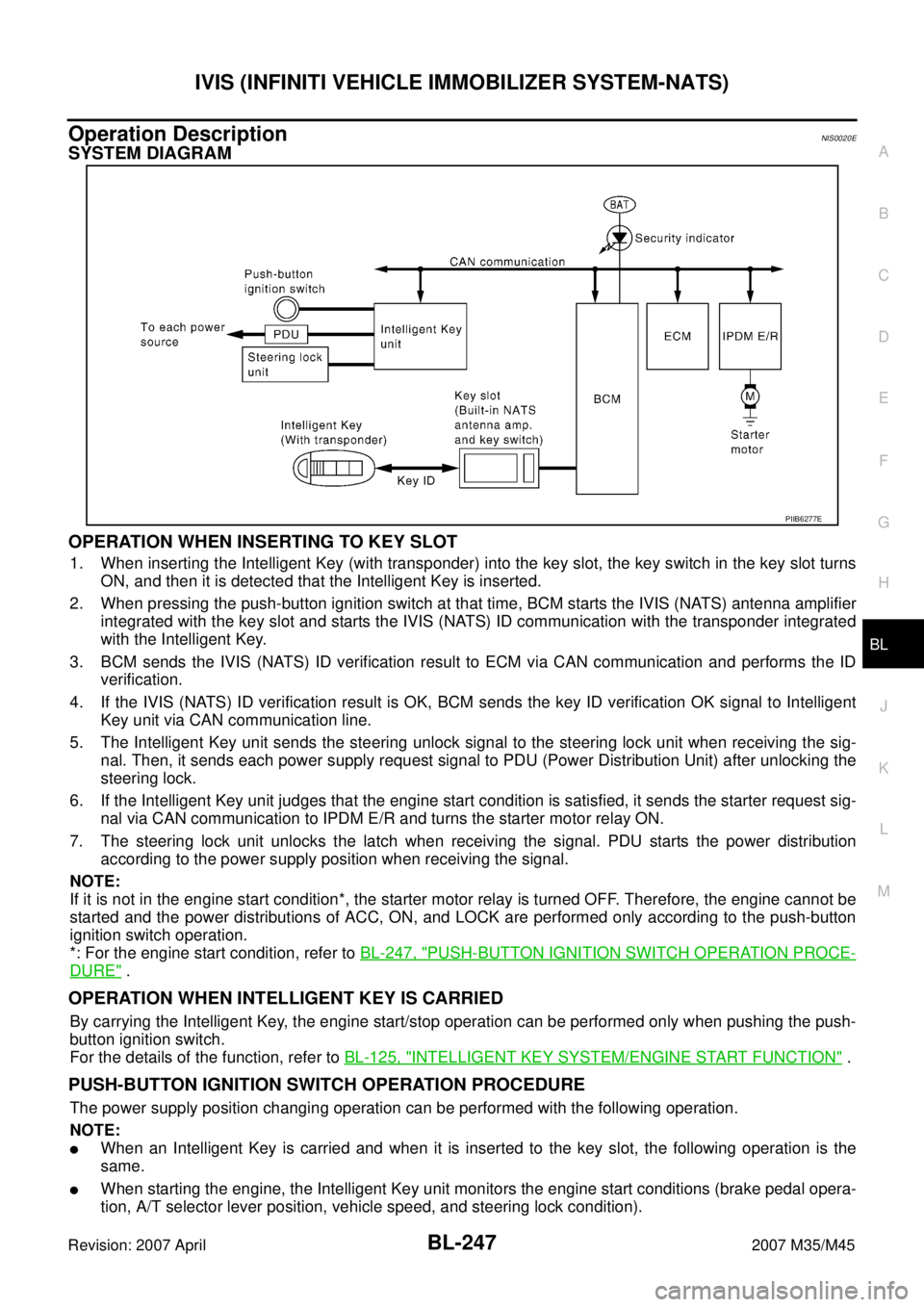
IVIS (INFINITI VEHICLE IMMOBILIZER SYSTEM-NATS)
BL-247
C
D
E
F
G
H
J
K
L
MA
B
BL
Revision: 2007 April2007 M35/M45
Operation DescriptionNIS0020E
SYSTEM DIAGRAM
OPERATION WHEN INSERTING TO KEY SLOT
1. When inserting the Intelligent Key (with transponder) into the key slot, the key switch in the key slot turns
ON, and then it is detected that the Intelligent Key is inserted.
2. When pressing the push-button ignition switch at that time, BCM starts the IVIS (NATS) antenna amplifier
integrated with the key slot and starts the IVIS (NATS) ID communication with the transponder integrated
with the Intelligent Key.
3. BCM sends the IVIS (NATS) ID verification result to ECM via CAN communication and performs the ID
verification.
4. If the IVIS (NATS) ID verification result is OK, BCM sends the key ID verification OK signal to Intelligent
Key unit via CAN communication line.
5. The Intelligent Key unit sends the steering unlock signal to the steering lock unit when receiving the sig-
nal. Then, it sends each power supply request signal to PDU (Power Distribution Unit) after unlocking the
steering lock.
6. If the Intelligent Key unit judges that the engine start condition is satisfied, it sends the starter request sig-
nal via CAN communication to IPDM E/R and turns the starter motor relay ON.
7. The steering lock unit unlocks the latch when receiving the signal. PDU starts the power distribution
according to the power supply position when receiving the signal.
NOTE:
If it is not in the engine start condition*, the starter motor relay is turned OFF. Therefore, the engine cannot be
started and the power distributions of ACC, ON, and LOCK are performed only according to the push-button
ignition switch operation.
*: For the engine start condition, refer to BL-247, "
PUSH-BUTTON IGNITION SWITCH OPERATION PROCE-
DURE" .
OPERATION WHEN INTELLIGENT KEY IS CARRIED
By carrying the Intelligent Key, the engine start/stop operation can be performed only when pushing the push-
button ignition switch.
For the details of the function, refer to BL-125, "
INTELLIGENT KEY SYSTEM/ENGINE START FUNCTION" .
PUSH-BUTTON IGNITION SWITCH OPERATION PROCEDURE
The power supply position changing operation can be performed with the following operation.
NOTE:
When an Intelligent Key is carried and when it is inserted to the key slot, the following operation is the
same.
When starting the engine, the Intelligent Key unit monitors the engine start conditions (brake pedal opera-
tion, A/T selector lever position, vehicle speed, and steering lock condition).
PIIB6277E
Page 1193 of 4647
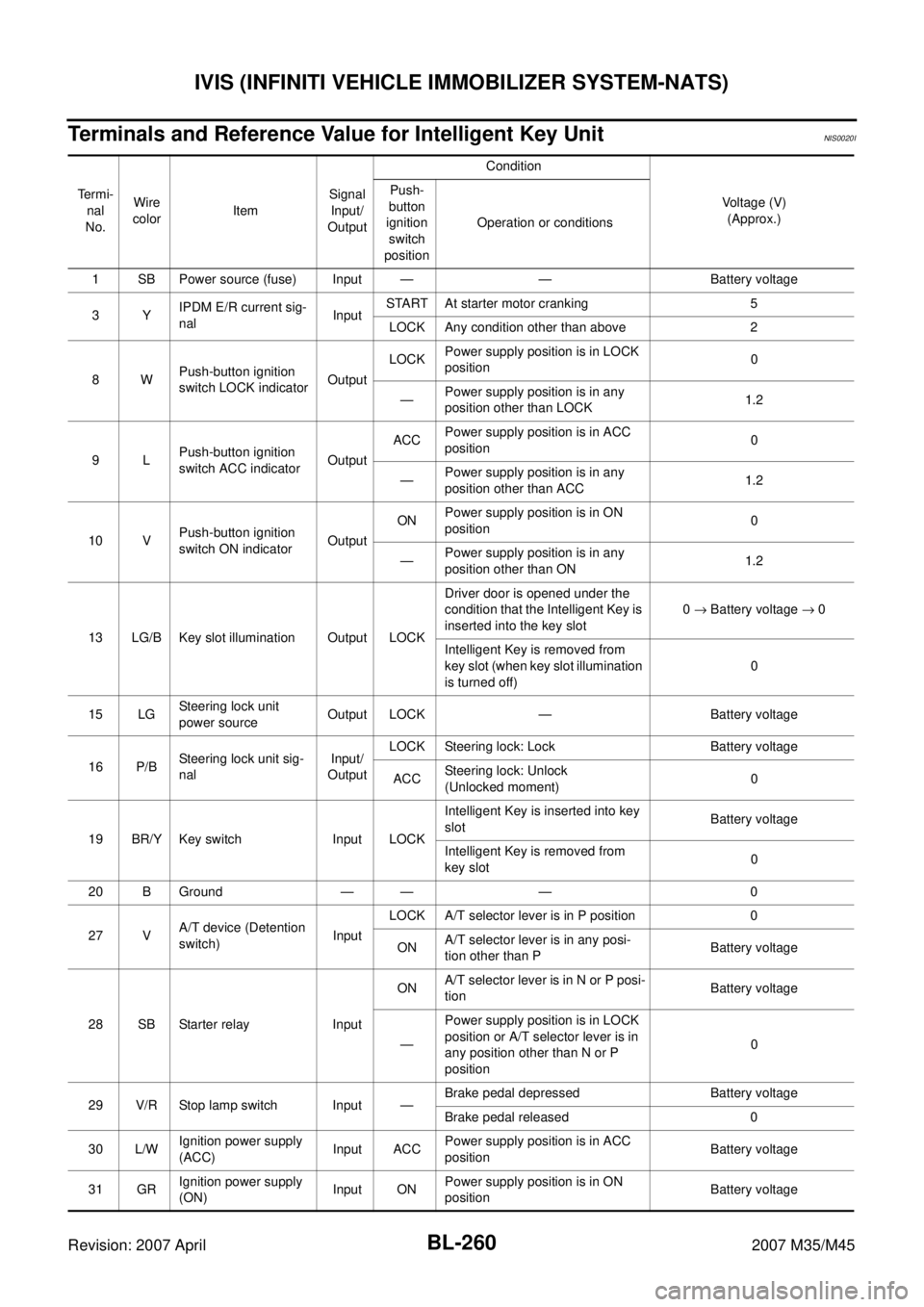
BL-260
IVIS (INFINITI VEHICLE IMMOBILIZER SYSTEM-NATS)
Revision: 2007 April2007 M35/M45
Terminals and Reference Value for Intelligent Key UnitNIS0020I
Termi-
nal
No.Wire
colorItemSignal
Input/
OutputCondition
Voltage (V)
(Approx.) Push-
button
ignition
switch
positionOperation or conditions
1 SB Power source (fuse) Input — — Battery voltage
3YIPDM E/R current sig-
nalInputSTART At starter motor cranking 5
LOCK Any condition other than above 2
8WPush-button ignition
switch LOCK indicatorOutputLOCKPower supply position is in LOCK
position0
—Power supply position is in any
position other than LOCK1.2
9LPush-button ignition
switch ACC indicatorOutputACCPower supply position is in ACC
position0
—Power supply position is in any
position other than ACC1.2
10 VPush-button ignition
switch ON indicatorOutputONPower supply position is in ON
position0
—Power supply position is in any
position other than ON1.2
13 LG/B Key slot illumination Output LOCKDriver door is opened under the
condition that the Intelligent Key is
inserted into the key slot0 → Battery voltage → 0
Intelligent Key is removed from
key slot (when key slot illumination
is turned off)0
15 LGSteering lock unit
power sourceOutput LOCK — Battery voltage
16 P/BSteering lock unit sig-
nalInput/
OutputLOCK Steering lock: Lock Battery voltage
ACCSteering lock: Unlock
(Unlocked moment)0
19 BR/Y Key switch Input LOCKIntelligent Key is inserted into key
slotBattery voltage
Intelligent Key is removed from
key slot0
20 B Ground — — — 0
27 VA/T device (Detention
switch)InputLOCK A/T selector lever is in P position 0
ONA/T selector lever is in any posi-
tion other than PBattery voltage
28 SB Starter relay InputONA/T selector lever is in N or P posi-
tionBattery voltage
—Power supply position is in LOCK
position or A/T selector lever is in
any position other than N or P
position0
29 V/R Stop lamp switch Input —Brake pedal depressed Battery voltage
Brake pedal released 0
30 L/WIgnition power supply
(ACC)Input ACCPower supply position is in ACC
positionBattery voltage
31 GRIgnition power supply
(ON)Input ONPower supply position is in ON
positionBattery voltage
Page 1194 of 4647
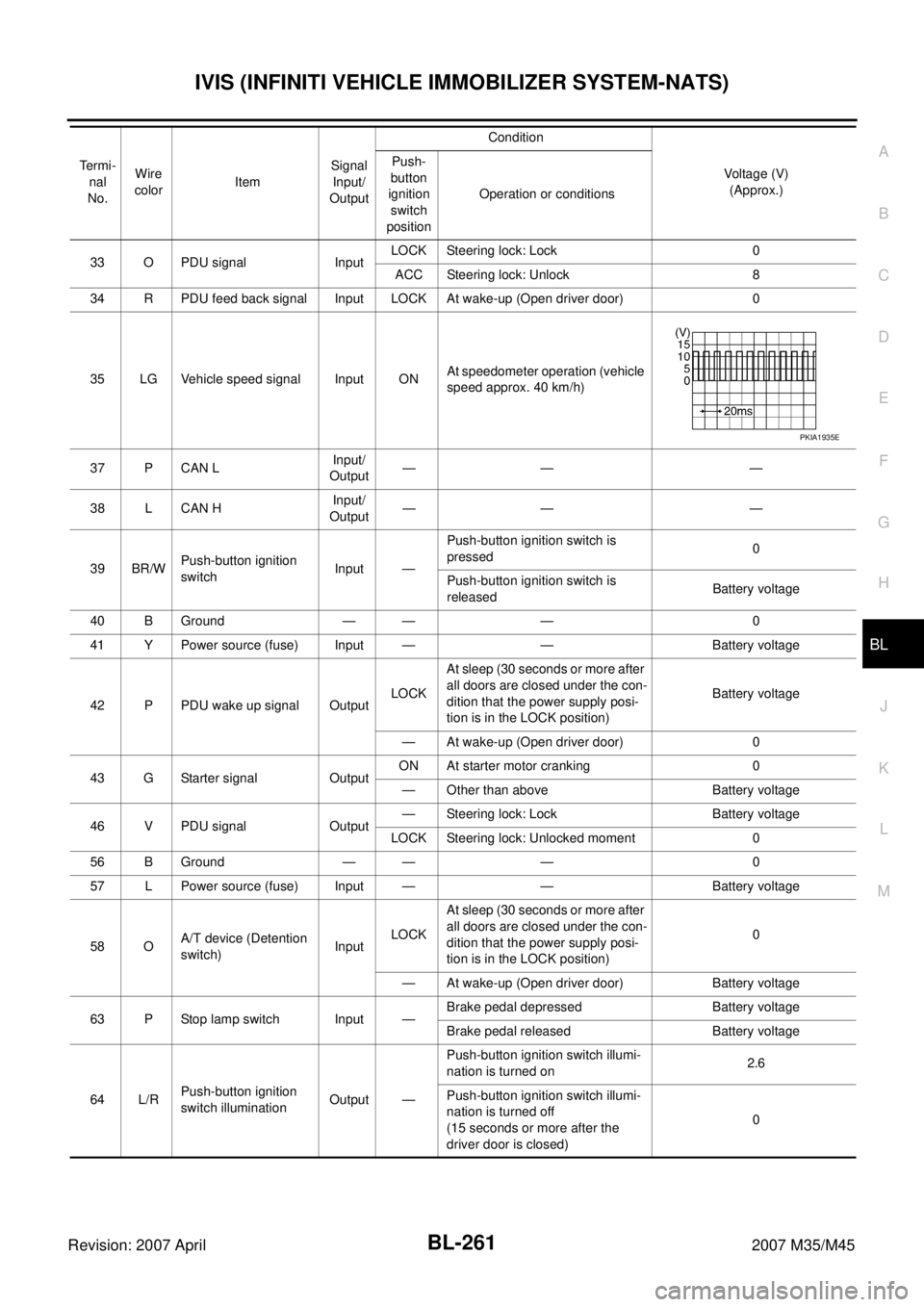
IVIS (INFINITI VEHICLE IMMOBILIZER SYSTEM-NATS)
BL-261
C
D
E
F
G
H
J
K
L
MA
B
BL
Revision: 2007 April2007 M35/M45
33 O PDU signal InputLOCK Steering lock: Lock 0
ACC Steering lock: Unlock 8
34 R PDU feed back signal Input LOCK At wake-up (Open driver door) 0
35 LG Vehicle speed signal Input ONAt speedometer operation (vehicle
speed approx. 40 km/h)
37 P CAN LInput/
Output—— —
38 L CAN HInput/
Output—— —
39 BR/WPush-button ignition
switchInput —Push-button ignition switch is
pressed0
Push-button ignition switch is
releasedBattery voltage
40 B Ground — — — 0
41 Y Power source (fuse) Input — — Battery voltage
42 P PDU wake up signal OutputLOCKAt sleep (30 seconds or more after
all doors are closed under the con-
dition that the power supply posi-
tion is in the LOCK position)Battery voltage
— At wake-up (Open driver door) 0
43 G Starter signal OutputON At starter motor cranking 0
— Other than above Battery voltage
46 V PDU signal Output— Steering lock: Lock Battery voltage
LOCK Steering lock: Unlocked moment 0
56 B Ground — — — 0
57 L Power source (fuse) Input — — Battery voltage
58 OA/T device (Detention
switch)InputLOCKAt sleep (30 seconds or more after
all doors are closed under the con-
dition that the power supply posi-
tion is in the LOCK position)0
— At wake-up (Open driver door) Battery voltage
63 P Stop lamp switch Input —Brake pedal depressed Battery voltage
Brake pedal released Battery voltage
64 L/RPush-button ignition
switch illuminationOutput —Push-button ignition switch illumi-
nation is turned on2.6
Push-button ignition switch illumi-
nation is turned off
(15 seconds or more after the
driver door is closed)0 Te r m i -
nal
No.Wire
colorItemSignal
Input/
OutputCondition
Voltage (V)
(Approx.) Push-
button
ignition
switch
positionOperation or conditions
PKIA1935E
Page 1195 of 4647
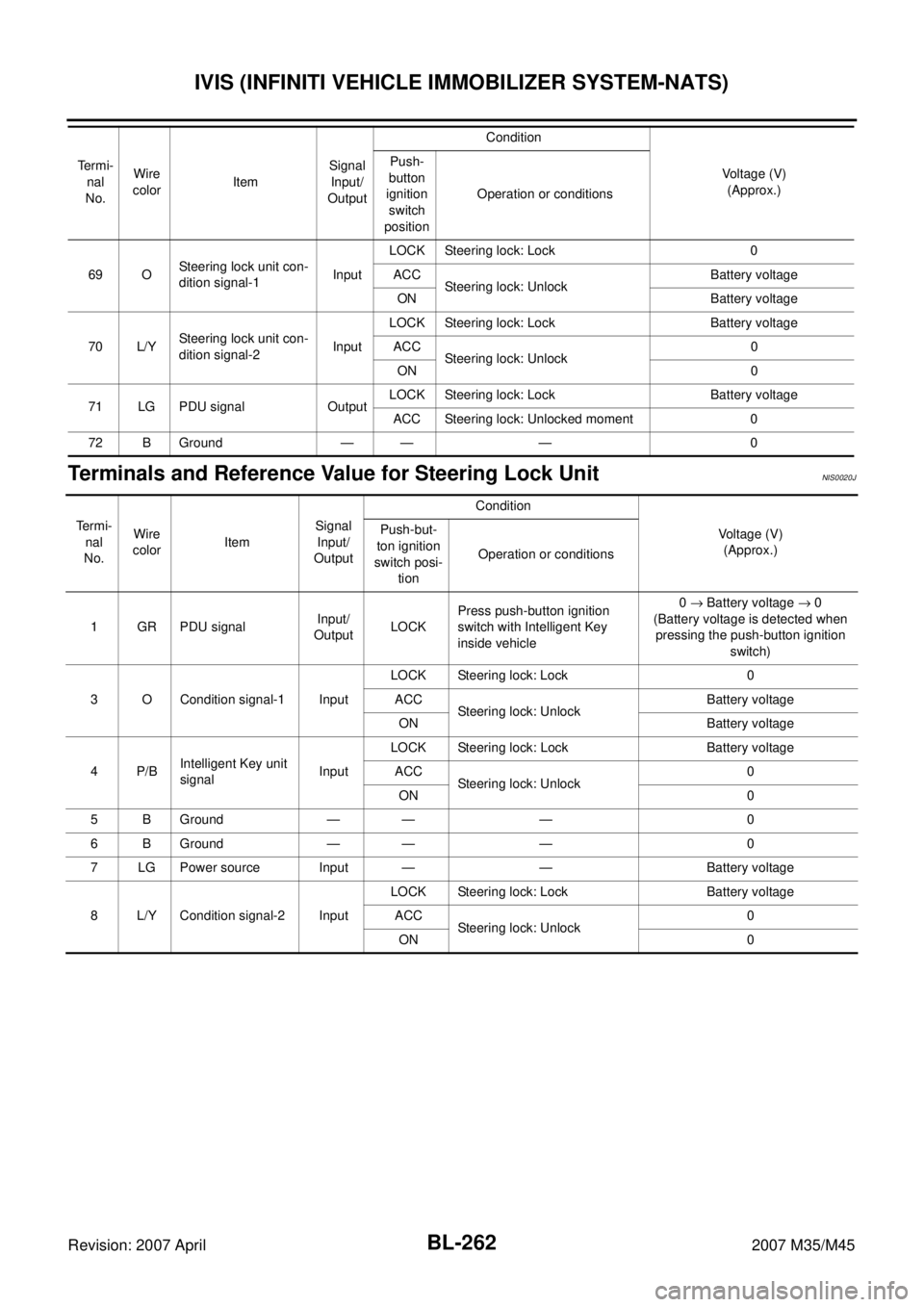
BL-262
IVIS (INFINITI VEHICLE IMMOBILIZER SYSTEM-NATS)
Revision: 2007 April2007 M35/M45
Terminals and Reference Value for Steering Lock UnitNIS0020J
69 OSteering lock unit con-
dition signal-1InputLOCK Steering lock: Lock 0
ACC
Steering lock: UnlockBattery voltage
ON Battery voltage
70 L/YSteering lock unit con-
dition signal-2InputLOCK Steering lock: Lock Battery voltage
ACC
Steering lock: Unlock0
ON 0
71 LG PDU signal OutputLOCK Steering lock: Lock Battery voltage
ACC Steering lock: Unlocked moment 0
72 B Ground — — — 0 Termi-
nal
No.Wire
colorItemSignal
Input/
OutputCondition
Voltage (V)
(Approx.) Push-
button
ignition
switch
positionOperation or conditions
Termi-
nal
No.Wire
colorItemSignal
Input/
OutputCondition
Voltage (V)
(Approx.) Push-but-
ton ignition
switch posi-
tionOperation or conditions
1 GR PDU signalInput/
OutputLOCKPress push-button ignition
switch with Intelligent Key
inside vehicle0 → Battery voltage → 0
(Battery voltage is detected when
pressing the push-button ignition
switch)
3 O Condition signal-1 InputLOCK Steering lock: Lock 0
ACC
Steering lock: UnlockBattery voltage
ON Battery voltage
4P/BIntelligent Key unit
signalInputLOCK Steering lock: Lock Battery voltage
ACC
Steering lock: Unlock0
ON 0
5 B Ground — — — 0
6 B Ground — — — 0
7 LG Power source Input — — Battery voltage
8 L/Y Condition signal-2 InputLOCK Steering lock: Lock Battery voltage
ACC
Steering lock: Unlock0
ON 0
Page 1197 of 4647
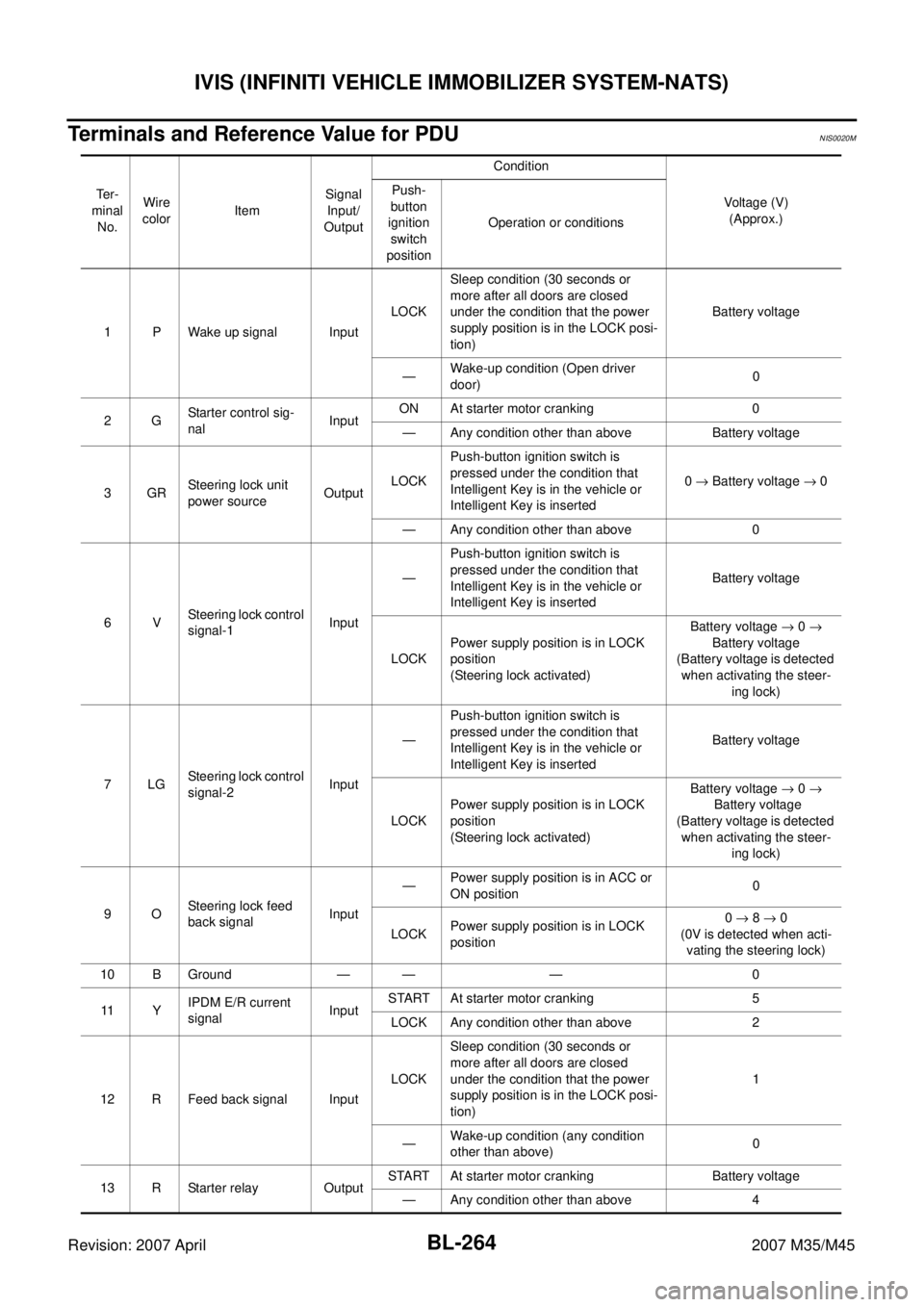
BL-264
IVIS (INFINITI VEHICLE IMMOBILIZER SYSTEM-NATS)
Revision: 2007 April2007 M35/M45
Terminals and Reference Value for PDUNIS0020M
Te r -
minal
No.Wire
colorItemSignal
Input/
OutputCondition
Voltage (V)
(Approx.) Push-
button
ignition
switch
positionOperation or conditions
1 P Wake up signal InputLOCKSleep condition (30 seconds or
more after all doors are closed
under the condition that the power
supply position is in the LOCK posi-
tion)Battery voltage
—Wake-up condition (Open driver
door)0
2GStarter control sig-
nalInputON At starter motor cranking 0
— Any condition other than above Battery voltage
3GRSteering lock unit
power sourceOutputLOCKPush-button ignition switch is
pressed under the condition that
Intelligent Key is in the vehicle or
Intelligent Key is inserted0 → Battery voltage → 0
— Any condition other than above 0
6VSteering lock control
signal-1Input—Push-button ignition switch is
pressed under the condition that
Intelligent Key is in the vehicle or
Intelligent Key is insertedBattery voltage
LOCKPower supply position is in LOCK
position
(Steering lock activated)Battery voltage → 0 →
Battery voltage
(Battery voltage is detected
when activating the steer-
ing lock)
7LGSteering lock control
signal-2Input—Push-button ignition switch is
pressed under the condition that
Intelligent Key is in the vehicle or
Intelligent Key is insertedBattery voltage
LOCKPower supply position is in LOCK
position
(Steering lock activated)Battery voltage → 0 →
Battery voltage
(Battery voltage is detected
when activating the steer-
ing lock)
9OSteering lock feed
back signalInput—Power supply position is in ACC or
ON position0
LOCKPower supply position is in LOCK
position0 → 8 → 0
(0V is detected when acti-
vating the steering lock)
10 B Ground — — — 0
11 YIPDM E/R current
signalInputSTART At starter motor cranking 5
LOCK Any condition other than above 2
12 R Feed back signal InputLOCKSleep condition (30 seconds or
more after all doors are closed
under the condition that the power
supply position is in the LOCK posi-
tion)1
—Wake-up condition (any condition
other than above)0
13 R Starter relay OutputSTART At starter motor cranking Battery voltage
— Any condition other than above 4
Page 1291 of 4647
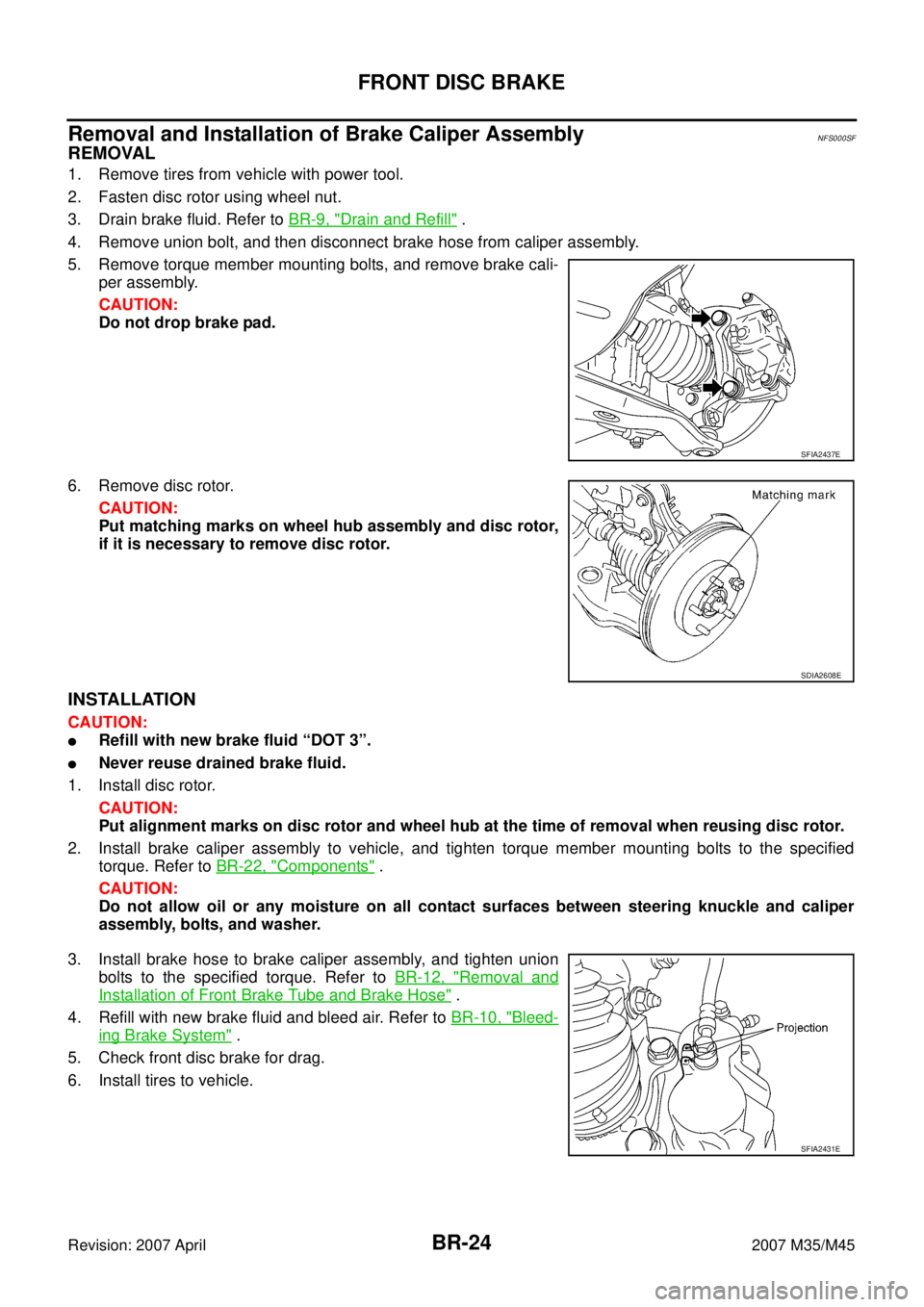
BR-24
FRONT DISC BRAKE
Revision: 2007 April2007 M35/M45
Removal and Installation of Brake Caliper AssemblyNFS000SF
REMOVAL
1. Remove tires from vehicle with power tool.
2. Fasten disc rotor using wheel nut.
3. Drain brake fluid. Refer to BR-9, "
Drain and Refill" .
4. Remove union bolt, and then disconnect brake hose from caliper assembly.
5. Remove torque member mounting bolts, and remove brake cali-
per assembly.
CAUTION:
Do not drop brake pad.
6. Remove disc rotor.
CAUTION:
Put matching marks on wheel hub assembly and disc rotor,
if it is necessary to remove disc rotor.
INSTALLATION
CAUTION:
Refill with new brake fluid “DOT 3”.
Never reuse drained brake fluid.
1. Install disc rotor.
CAUTION:
Put alignment marks on disc rotor and wheel hub at the time of removal when reusing disc rotor.
2. Install brake caliper assembly to vehicle, and tighten torque member mounting bolts to the specified
torque. Refer to BR-22, "
Components" .
CAUTION:
Do not allow oil or any moisture on all contact surfaces between steering knuckle and caliper
assembly, bolts, and washer.
3. Install brake hose to brake caliper assembly, and tighten union
bolts to the specified torque. Refer to BR-12, "
Removal and
Installation of Front Brake Tube and Brake Hose" .
4. Refill with new brake fluid and bleed air. Refer to BR-10, "
Bleed-
ing Brake System" .
5. Check front disc brake for drag.
6. Install tires to vehicle.
SFIA2437E
SDIA2608E
SFIA2431E
Page 1302 of 4647
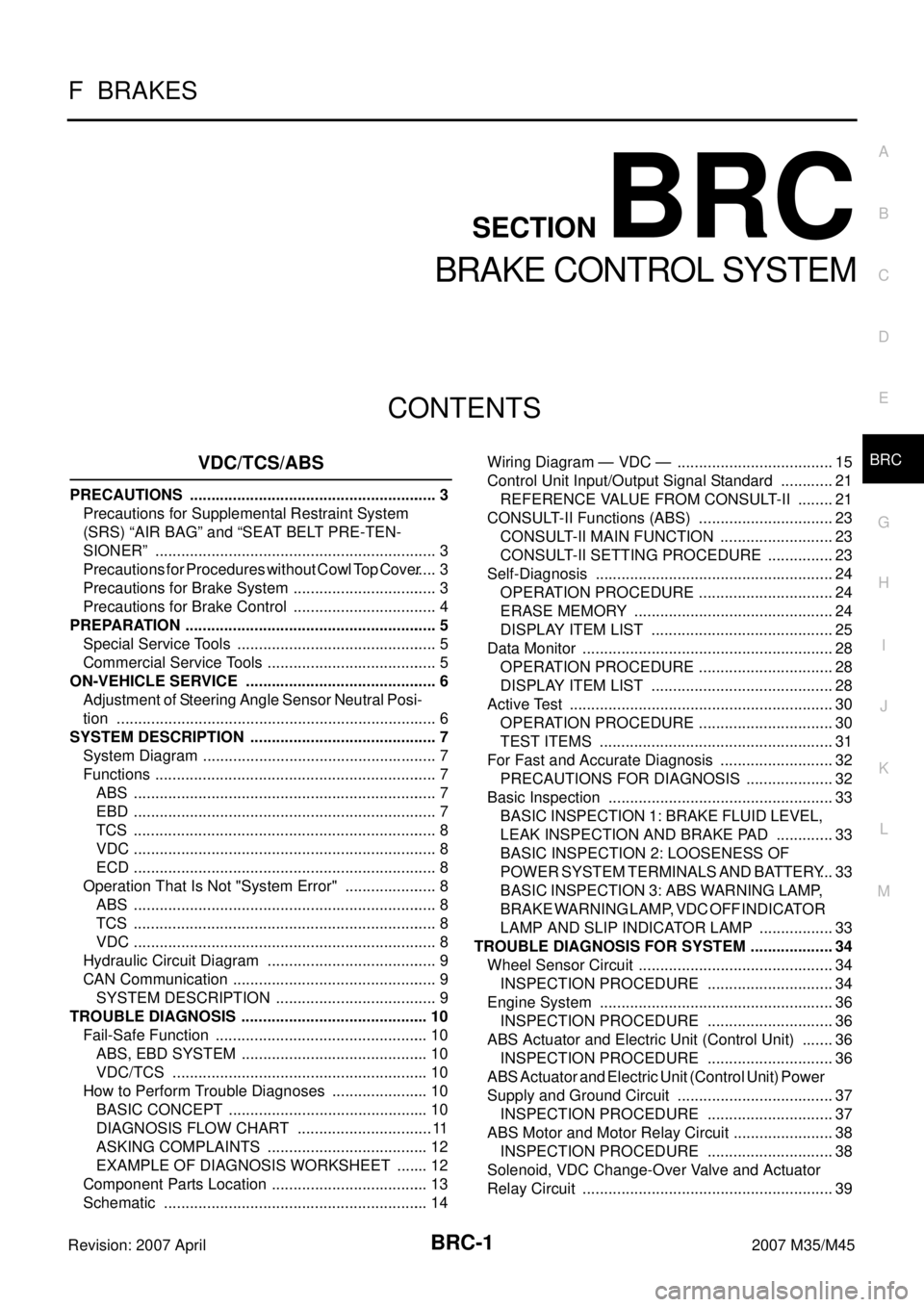
BRC-1
BRAKE CONTROL SYSTEM
F BRAKES
CONTENTS
C
D
E
G
H
I
J
K
L
M
SECTION BRC
A
B
BRC
Revision: 2007 April2007 M35/M45
BRAKE CONTROL SYSTEM
VDC/TCS/ABS
PRECAUTIONS .......................................................... 3
Precautions for Supplemental Restraint System
(SRS) “AIR BAG” and “SEAT BELT PRE-TEN-
SIONER” .................................................................. 3
Precautions for Procedures without Cowl Top Cover ..... 3
Precautions for Brake System .................................. 3
Precautions for Brake Control .................................. 4
PREPARATION ........................................................... 5
Special Service Tools ............................................... 5
Commercial Service Tools ........................................ 5
ON-VEHICLE SERVICE ............................................. 6
Adjustment of Steering Angle Sensor Neutral Posi-
tion ........................................................................... 6
SYSTEM DESCRIPTION ............................................ 7
System Diagram ....................................................... 7
Functions .................................................................. 7
ABS ....................................................................... 7
EBD ....................................................................... 7
TCS ....................................................................... 8
VDC ....................................................................... 8
ECD ....................................................................... 8
Operation That Is Not "System Error" ...................... 8
ABS ....................................................................... 8
TCS ....................................................................... 8
VDC ....................................................................... 8
Hydraulic Circuit Diagram ........................................ 9
CAN Communication ................................................ 9
SYSTEM DESCRIPTION ...................................... 9
TROUBLE DIAGNOSIS ............................................ 10
Fail-Safe Function .................................................. 10
ABS, EBD SYSTEM ............................................ 10
VDC/TCS ............................................................ 10
How to Perform Trouble Diagnoses ....................... 10
BASIC CONCEPT ............................................... 10
DIAGNOSIS FLOW CHART ................................ 11
ASKING COMPLAINTS ...................................... 12
EXAMPLE OF DIAGNOSIS WORKSHEET ........ 12
Component Parts Location ..................................... 13
Schematic .............................................................. 14Wiring Diagram — VDC — ..................................... 15
Control Unit Input/Output Signal Standard ............. 21
REFERENCE VALUE FROM CONSULT-II ......... 21
CONSULT-II Functions (ABS) ................................ 23
CONSULT-II MAIN FUNCTION ........................... 23
CONSULT-II SETTING PROCEDURE ................ 23
Self-Diagnosis ........................................................ 24
OPERATION PROCEDURE ................................ 24
ERASE MEMORY ............................................... 24
DISPLAY ITEM LIST ........................................... 25
Data Monitor ........................................................... 28
OPERATION PROCEDURE ................................ 28
DISPLAY ITEM LIST ........................................... 28
Active Test .............................................................. 30
OPERATION PROCEDURE ................................ 30
TEST ITEMS ....................................................... 31
For Fast and Accurate Diagnosis ........................... 32
PRECAUTIONS FOR DIAGNOSIS ..................... 32
Basic Inspection ..................................................... 33
BASIC INSPECTION 1: BRAKE FLUID LEVEL,
LEAK INSPECTION AND BRAKE PAD .............. 33
BASIC INSPECTION 2: LOOSENESS OF
POWER SYSTEM TERMINALS AND BATTERY ... 33
BASIC INSPECTION 3: ABS WARNING LAMP,
BRAKE WARNING LAMP, VDC OFF INDICATOR
LAMP AND SLIP INDICATOR LAMP .................. 33
TROUBLE DIAGNOSIS FOR SYSTEM .................... 34
Wheel Sensor Circuit .............................................. 34
INSPECTION PROCEDURE .............................. 34
Engine System ....................................................... 36
INSPECTION PROCEDURE .............................. 36
ABS Actuator and Electric Unit (Control Unit) ........ 36
INSPECTION PROCEDURE .............................. 36
ABS Actuator and Electric Unit (Control Unit) Power
Supply and Ground Circuit ..................................... 37
INSPECTION PROCEDURE .............................. 37
ABS Motor and Motor Relay Circuit ........................ 38
INSPECTION PROCEDURE .............................. 38
Solenoid, VDC Change-Over Valve and Actuator
Relay Circuit ........................................................... 39
Page 1327 of 4647
![INFINITI M35 2007 Factory Owners Guide BRC-26
[VDC/TCS/ABS]
TROUBLE DIAGNOSIS
Revision: 2007 April2007 M35/M45
C1120 FR LH IN ABS SOLWhen the control unit detects a malfunction in the front left inlet sole-
noid circuit.
BRC-39, "
Sole-
no INFINITI M35 2007 Factory Owners Guide BRC-26
[VDC/TCS/ABS]
TROUBLE DIAGNOSIS
Revision: 2007 April2007 M35/M45
C1120 FR LH IN ABS SOLWhen the control unit detects a malfunction in the front left inlet sole-
noid circuit.
BRC-39, "
Sole-
no](/img/42/57024/w960_57024-1326.png)
BRC-26
[VDC/TCS/ABS]
TROUBLE DIAGNOSIS
Revision: 2007 April2007 M35/M45
C1120 FR LH IN ABS SOLWhen the control unit detects a malfunction in the front left inlet sole-
noid circuit.
BRC-39, "
Sole-
noid, VDC
Change-Over
Valve and Actua-
tor Relay Circuit"
C1121 FR LH OUT ABS SOLWhen the control unit detects a malfunction in the front left outlet sole-
noid circuit.
C1122 FR RH IN ABS SOLWhen the control unit detects a malfunction in the front right inlet sole-
noid circuit.
C1123 FR RH OUT ABS SOLWhen the control unit detects a malfunction in the front right outlet sole-
noid circuit.
C1124 RR LH IN ABS SOLWhen the control unit detects a malfunction in the rear left inlet solenoid
circuit.
C1125 RR LH OUT ABS SOLWhen the control unit detects a malfunction in the rear left outlet sole-
noid circuit.
C1126 RR RH IN ABS SOLWhen the control unit detects a malfunction in the rear right inlet sole-
noid circuit.
C1127 RR RH OUT ABS SOLWhen the control unit detects a malfunction in the rear right outlet sole-
noid circuit.
C1130 ENGINE SIGNAL 1
Major engine components are malfunctioning.BRC-36, "
Engine
System"
C1131 ENGINE SIGNAL 2
C1132 ENGINE SIGNAL 3
C1133 ENGINE SIGNAL 4
C1136 ENGINE SIGNAL 6
C1137 RAS CIRCUIT When RAS control unit is malfunctioning.BRC-47, "
RAS
Control Unit Cir-
cuit (With RAS)"
C1142 PRESS SEN CIRCUIT Pressure sensor signal line is open or shorted, or pressure sensor is
malfunctioning.BRC-40, "
Pres-
sure Sensor Cir-
cuit"
C1143 ST ANG SEN CIRCUIT Neutral position of steering angle sensor is dislocated, or the steering
angle sensor is malfunctioning.BRC-41, "
St e e r -
ing Angle Sensor
Circuit"
C1144 ST ANG SEN SIGNAL Neutral position correction of steering angle sensor is not finished.BRC-6, "
Adjust-
ment of Steering
Angle Sensor
Neutral Position"
C1145 YAW RATE SENSOR Yaw rate sensor is malfunctioning, or the yaw rate sensor signal line is
open or shorted.BRC-44, "Ya w
Rate/Side G
Sensor Circuit"C1146 SIDE G-SEN CIRCUITSide G sensor is malfunctioning, or circuit of side G sensor is open or
shorted.
C1147 USV LINE [FL-RR]VDC switch-over solenoid valve (USV1) on the primary side is open cir-
cuit or shorted, or the control line is open or shorted to the power supply
or the ground.
BRC-39, "
Sole-
noid, VDC
Change-Over
Valve and Actua-
tor Relay Circuit"
C1148 USV LINE [FR-RL]VDC switch-over solenoid valve (USV2) on the secondary side is open
circuit or shorted, or the control line is open or shorted to the power
supply or the ground.
C1149 HSV LINE [FL-RR]VDC switch-over solenoid valve (HSV1) on the primary side is open cir-
cuit or shorted, or the control line is open or shorted to the power supply
or the ground.
C1150 HSV LINE [FR-RL]VDC switch-over solenoid valve (HSV2) on the secondary side is open
circuit or shorted, or the control line is open or shorted to the power
supply or the ground.
C1153 EMERGENCY BRAKEWhen ABS actuator and electric unit (control unit) is malfunctioning.
(Pressure increase is too much or too little)BRC-36, "
ABS
Actuator and
Electric Unit
(Control Unit)"
Code Display item Malfunction detecting condition Check item
Page 1328 of 4647
![INFINITI M35 2007 Factory Owners Guide TROUBLE DIAGNOSIS
BRC-27
[VDC/TCS/ABS]
C
D
E
G
H
I
J
K
L
MA
B
BRC
Revision: 2007 April2007 M35/M45
Note 1: After completing repairs of shorted sensor circuit, when ignition switch is turned ON, ABS wa INFINITI M35 2007 Factory Owners Guide TROUBLE DIAGNOSIS
BRC-27
[VDC/TCS/ABS]
C
D
E
G
H
I
J
K
L
MA
B
BRC
Revision: 2007 April2007 M35/M45
Note 1: After completing repairs of shorted sensor circuit, when ignition switch is turned ON, ABS wa](/img/42/57024/w960_57024-1327.png)
TROUBLE DIAGNOSIS
BRC-27
[VDC/TCS/ABS]
C
D
E
G
H
I
J
K
L
MA
B
BRC
Revision: 2007 April2007 M35/M45
Note 1: After completing repairs of shorted sensor circuit, when ignition switch is turned ON, ABS warning lamp turns on. Make sure that
ABS warning lamp turns off while driving vehicle at 30 km/h (19 MPH) or more for approximately 1 minute according to self-diagnosis
procedure. In addition, if wheel sensor 2 is displayed for wheels, check wheel sensor circuit and also check control unit power voltage.
Note 2: When malfunctions are detected in several systems, including CAN communication circuit [U1000], troubleshoot CAN communi-
cation circuit. Refer to BRC-48, "
CAN Communication Circuit" . C1155 BR FLUID LEVEL LOWBrake fluid level is low or communication line between the ABS actuator
and electric unit (control unit) and brake fluid level switch is open or
shorted. BRC-46, "
Brake
Fluid Level
Switch Circuit"
C1156 ST ANG SEN COM CIR CAN communication circuit or steering angle sensor is malfunctioning.BRC-48, "
CAN
Communication
Circuit"
C1170 VARIANT CODING In a case where VARIANT CODING is different.BRC-36, "
ABS
Actuator and
Electric Unit
(Control Unit)"
C1185 ACC CONT ICC sensor integrated unit internal malfunction.BRC-48, "
ICC
Sensor Inte-
grated Unit Cir-
cuit (With ICC)"
U1000 CAN COMM CIRCUITWhen ABS actuator and electric unit (control unit) is not transmitting or
receiving CAN communication signal for 2 seconds or more.BRC-48, "
CAN
Communication
Circuit"
(Note 2)
U1100 ACC COMM CIRCUITWhen there is a malfunction in the CAN communication circuit or ICC
sensor integrated unit.BRC-48, "
CAN
Communication
Circuit"
Code Display item Malfunction detecting condition Check item