air filter INFINITI M35 2007 Factory Service Manual
[x] Cancel search | Manufacturer: INFINITI, Model Year: 2007, Model line: M35, Model: INFINITI M35 2007Pages: 4647, PDF Size: 93.69 MB
Page 4 of 4647

QUICK REFERENCE CHART M35/M45
* : Fuel, engine coolant and engine oil full. Spare tire, jack, hand tools and mats in designated positions.
REAR WHEEL ALIGNMENT (Unladen*)ELS0003Y
* : Fuel, engine coolant and engine oil full. Spare tire, jack, hand tools and mats in designated positions.
BRAKEELS0003Z
* : Under force of 490 N ( 50 kg, 110 lb ) with engine running.
REFILL CAPACITIESELS00040
Wheel
turning
angle (Full
turn)Inside
Degree minute
(Decimal degree)Minimum 36°20′ (36.3°)39°45′ (39.8°)
Nominal 39°20′ (39.3°)42°45′ (42.8°)
Maximum 40°20′ (40.3°)43°45′ (43.8°)
Outside
Degree minute
(Decimal degree)Nominal 33° 25′ (33.4°)33° 20′ (33.3°)32° 30′ (32.5°) Axle2WD AWD
Tire 245/45R18 245/40R19 245/45R18
Axle2WD AWD
Tire 245/45R18 245/40R19 245/45R18
Camber
Degree minute (Decimal degree)Minimum –1° 10′ (–1.17°)–1° 20′ (–1.33°)–0° 40′ (–0.67°)
Nominal –0° 40′ (–0.67°)–0° 50′ (–0.83°)–0° 10′ (–0.17°)
Maximum –0° 10′ (–0.17°)–0° 20′ (–0.33°) 0° 20′ (0.33° )
Total toe-inDistanceMinimum 0.1 mm (0.004 in)
Nominal 2.8 mm (0.110 in)
Maximum 5.5 mm (0.217 in)
Angle
(left wheel or right wheel )
Degree minute
(Decimal degree)Minimum 0′ (0°)
Nominal 7′ (0.12°)
Maximum 14′ (0.23°)
Front brake Repair limit thickness 2.0 mm (0.079 in)
Wear limit 26.0 mm (1.024 in)
Rear brake Repair limit thickness 2.0 mm (0.079 in)
Wear limit 14.0 mm (0.551 in)
Brake pedal height 157 - 167 mm (6.18 - 6.57 in)
Depressed pedal height* 90 mm (3.54 in) or more
UNITLiter US measure
Fuel tank76 20 gal
Coolant ( With reservoir tank )VQ35DE 8.9 9 - 3/8 qt
VK45DE 10.4 11 qt
Engine (VQ35DE)Drain and refill
With oil filter change 4.7 5 qt
Without oil filter change 4.4 4 - 5/8 qt
Dry engine (Overhaul) 5.4 5 - 3/4 qt
Engine (VK45DE)Drain and refill
With oil filter change 5.5 5 - 3/4 qt
Without oil filter change 4.9 5 - 1/8 qt
Dry engine (Overhaul) 6.7 7 - 1/8 qt
2007
Page 95 of 4647
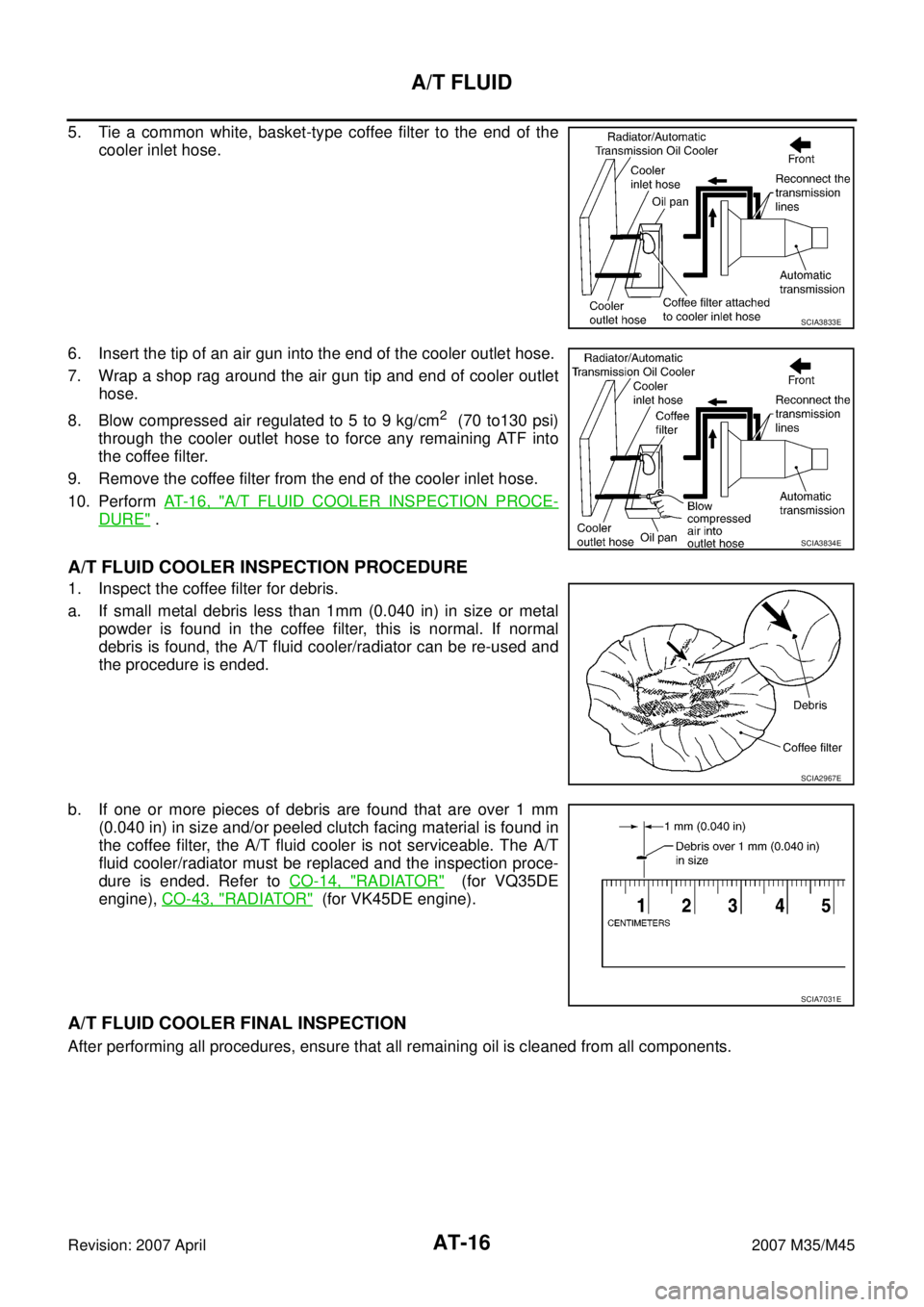
AT-16
A/T FLUID
Revision: 2007 April2007 M35/M45
5. Tie a common white, basket-type coffee filter to the end of the
cooler inlet hose.
6. Insert the tip of an air gun into the end of the cooler outlet hose.
7. Wrap a shop rag around the air gun tip and end of cooler outlet
hose.
8. Blow compressed air regulated to 5 to 9 kg/cm
2 (70 to130 psi)
through the cooler outlet hose to force any remaining ATF into
the coffee filter.
9. Remove the coffee filter from the end of the cooler inlet hose.
10. Perform AT- 1 6 , "
A/T FLUID COOLER INSPECTION PROCE-
DURE" .
A/T FLUID COOLER INSPECTION PROCEDURE
1. Inspect the coffee filter for debris.
a. If small metal debris less than 1mm (0.040 in) in size or metal
powder is found in the coffee filter, this is normal. If normal
debris is found, the A/T fluid cooler/radiator can be re-used and
the procedure is ended.
b. If one or more pieces of debris are found that are over 1 mm
(0.040 in) in size and/or peeled clutch facing material is found in
the coffee filter, the A/T fluid cooler is not serviceable. The A/T
fluid cooler/radiator must be replaced and the inspection proce-
dure is ended. Refer to CO-14, "
RADIATOR" (for VQ35DE
engine), CO-43, "
RADIATOR" (for VK45DE engine).
A/T FLUID COOLER FINAL INSPECTION
After performing all procedures, ensure that all remaining oil is cleaned from all components.
SCIA3833E
SCIA3834E
SCIA2967E
SCIA7031E
Page 454 of 4647
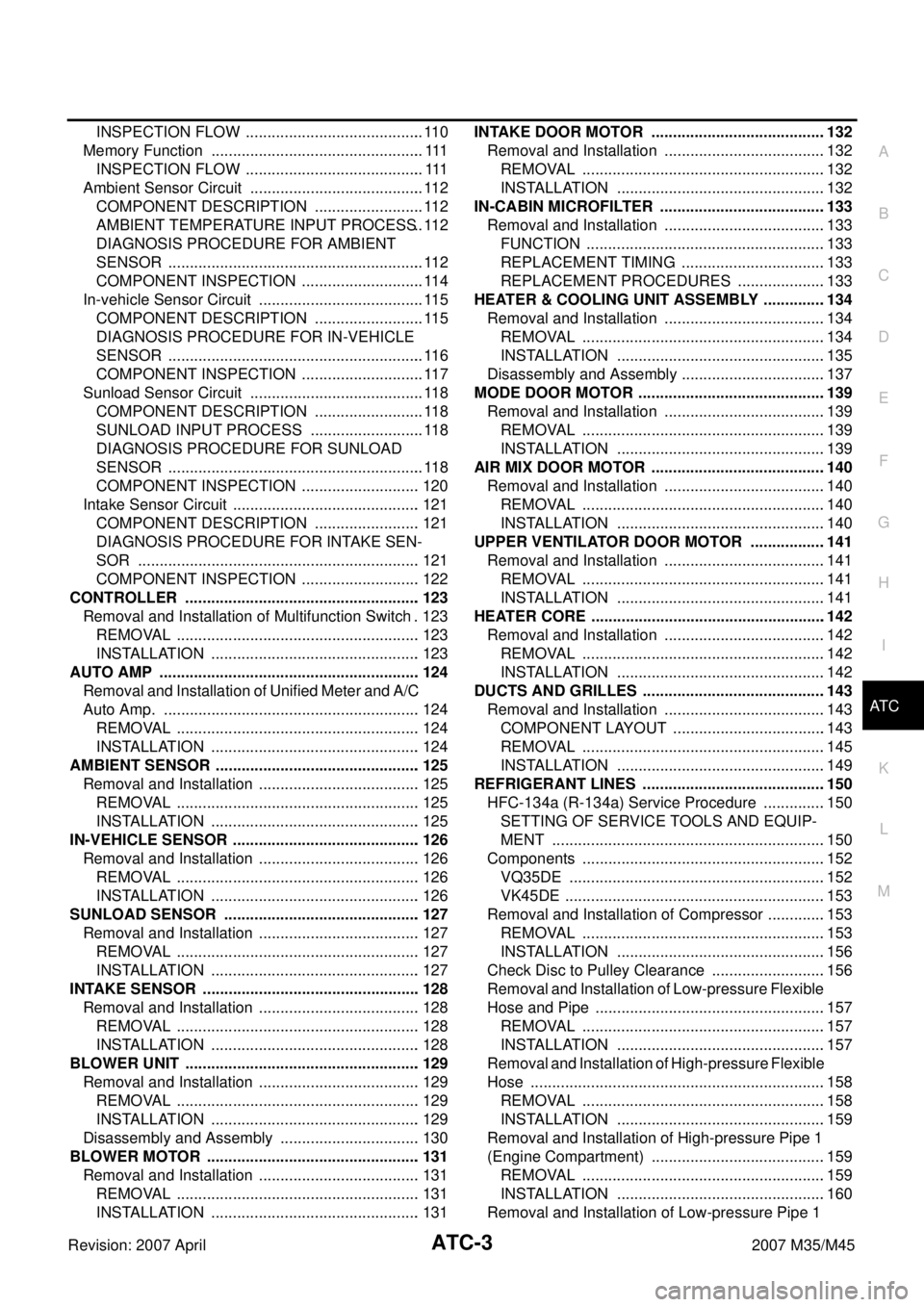
ATC-3
C
D
E
F
G
H
I
K
L
MA
B
AT C
Revision: 2007 April2007 M35/M45 INSPECTION FLOW .......................................... 110
Memory Function ................................................. . 111
INSPECTION FLOW ......................................... . 111
Ambient Sensor Circuit ......................................... 112
COMPONENT DESCRIPTION .......................... 112
AMBIENT TEMPERATURE INPUT PROCESS .. 112
DIAGNOSIS PROCEDURE FOR AMBIENT
SENSOR ............................................................ 112
COMPONENT INSPECTION ............................. 114
In-vehicle Sensor Circuit ....................................... 115
COMPONENT DESCRIPTION .......................... 115
DIAGNOSIS PROCEDURE FOR IN-VEHICLE
SENSOR ............................................................ 116
COMPONENT INSPECTION ............................. 117
Sunload Sensor Circuit ......................................... 118
COMPONENT DESCRIPTION .......................... 118
SUNLOAD INPUT PROCESS ........................... 118
DIAGNOSIS PROCEDURE FOR SUNLOAD
SENSOR ............................................................ 118
COMPONENT INSPECTION ............................ 120
Intake Sensor Circuit ............................................ 121
COMPONENT DESCRIPTION ......................... 121
DIAGNOSIS PROCEDURE FOR INTAKE SEN-
SOR .................................................................. 121
COMPONENT INSPECTION ............................ 122
CONTROLLER ....................................................... 123
Removal and Installation of Multifunction Switch . 123
REMOVAL ......................................................... 123
INSTALLATION ................................................. 123
AUTO AMP ............................................................. 124
Removal and Installation of Unified Meter and A/C
Auto Amp. ............................................................ 124
REMOVAL ......................................................... 124
INSTALLATION ................................................. 124
AMBIENT SENSOR ................................................ 125
Removal and Installation ...................................... 125
REMOVAL ......................................................... 125
INSTALLATION ................................................. 125
IN-VEHICLE SENSOR ............................................ 126
Removal and Installation ...................................... 126
REMOVAL ......................................................... 126
INSTALLATION ................................................. 126
SUNLOAD SENSOR .............................................. 127
Removal and Installation ...................................... 127
REMOVAL ......................................................... 127
INSTALLATION ................................................. 127
INTAKE SENSOR ................................................... 128
Removal and Installation ...................................... 128
REMOVAL ......................................................... 128
INSTALLATION ................................................. 128
BLOWER UNIT ....................................................... 129
Removal and Installation ...................................... 129
REMOVAL ......................................................... 129
INSTALLATION ................................................. 129
Disassembly and Assembly ................................. 130
BLOWER MOTOR .................................................. 131
Removal and Installation ...................................... 131
REMOVAL ......................................................... 131
INSTALLATION ................................................. 131INTAKE DOOR MOTOR .........................................132
Removal and Installation ......................................132
REMOVAL .........................................................132
INSTALLATION .................................................132
IN-CABIN MICROFILTER .......................................133
Removal and Installation ......................................133
FUNCTION ........................................................133
REPLACEMENT TIMING ..................................133
REPLACEMENT PROCEDURES .....................133
HEATER & COOLING UNIT ASSEMBLY ...............134
Removal and Installation ......................................134
REMOVAL .........................................................134
INSTALLATION .................................................135
Disassembly and Assembly ..................................137
MODE DOOR MOTOR ............................................139
Removal and Installation ......................................139
REMOVAL .........................................................139
INSTALLATION .................................................139
AIR MIX DOOR MOTOR .........................................140
Removal and Installation ......................................140
REMOVAL .........................................................140
INSTALLATION .................................................140
UPPER VENTILATOR DOOR MOTOR ..................141
Removal and Installation ......................................141
REMOVAL .........................................................141
INSTALLATION .................................................141
HEATER CORE .......................................................142
Removal and Installation ......................................142
REMOVAL .........................................................142
INSTALLATION .................................................142
DUCTS AND GRILLES ...........................................143
Removal and Installation ......................................143
COMPONENT LAYOUT ....................................143
REMOVAL .........................................................145
INSTALLATION .................................................149
REFRIGERANT LINES ...........................................150
HFC-134a (R-134a) Service Procedure ...............150
SETTING OF SERVICE TOOLS AND EQUIP-
MENT ................................................................150
Components .........................................................152
VQ35DE ............................................................152
VK45DE .............................................................153
Removal and Installation of Compressor ..............153
REMOVAL .........................................................153
INSTALLATION .................................................156
Check Disc to Pulley Clearance ...........................156
Removal and Installation of Low-pressure Flexible
Hose and Pipe ......................................................157
REMOVAL .........................................................157
INSTALLATION .................................................157
Removal and Installation of High-pressure Flexible
Hose .....................................................................158
REMOVAL .........................................................158
INSTALLATION .................................................159
Removal and Installation of High-pressure Pipe 1
(Engine Compartment) .........................................159
REMOVAL .........................................................159
INSTALLATION .................................................160
Removal and Installation of Low-pressure Pipe 1
Page 584 of 4647
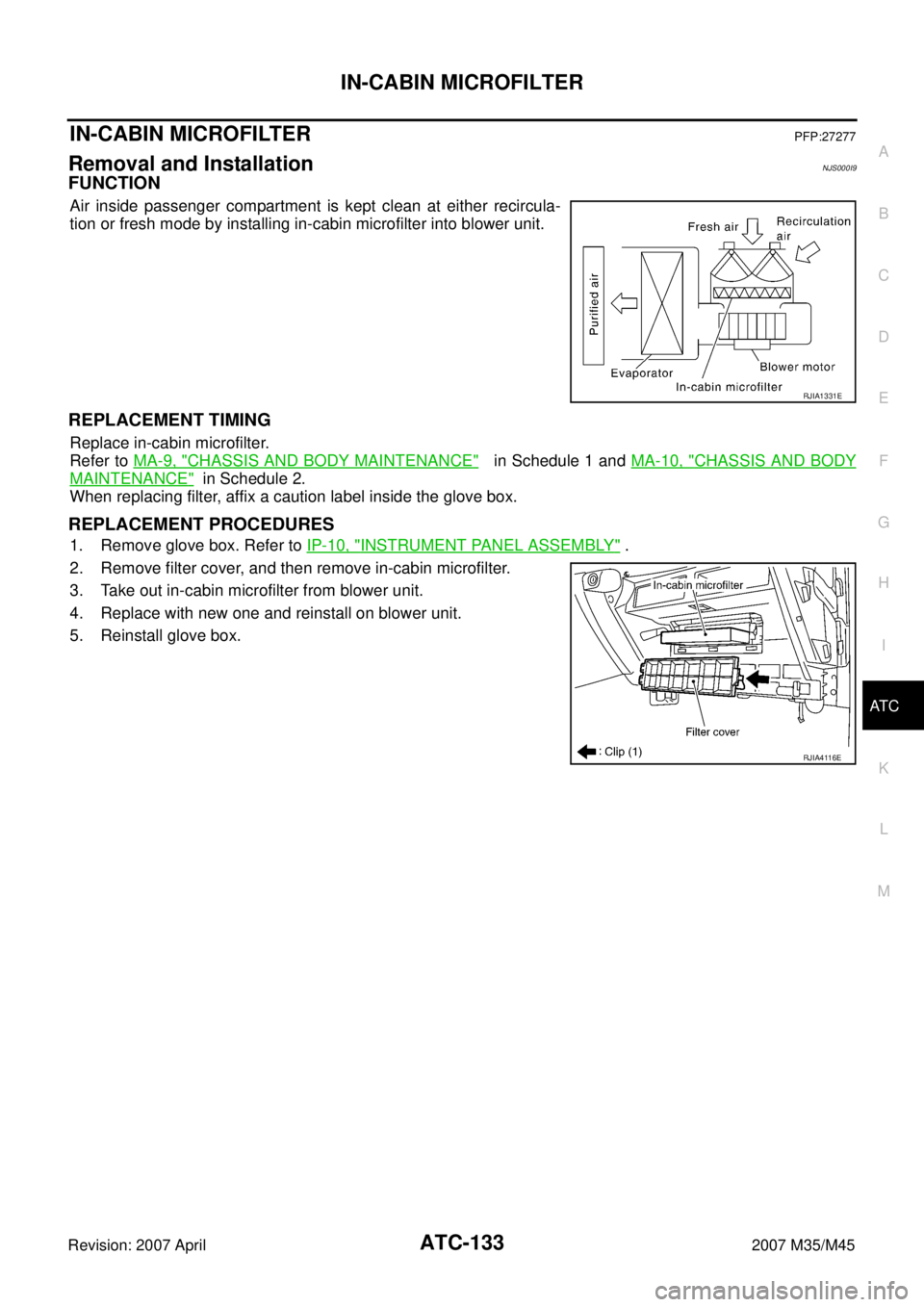
IN-CABIN MICROFILTER
ATC-133
C
D
E
F
G
H
I
K
L
MA
B
AT C
Revision: 2007 April2007 M35/M45
IN-CABIN MICROFILTERPFP:27277
Removal and InstallationNJS000I9
FUNCTION
Air inside passenger compartment is kept clean at either recircula-
tion or fresh mode by installing in-cabin microfilter into blower unit.
REPLACEMENT TIMING
Replace in-cabin microfilter.
Refer to MA-9, "
CHASSIS AND BODY MAINTENANCE" in Schedule 1 and MA-10, "CHASSIS AND BODY
MAINTENANCE" in Schedule 2.
When replacing filter, affix a caution label inside the glove box.
REPLACEMENT PROCEDURES
1. Remove glove box. Refer to IP-10, "INSTRUMENT PANEL ASSEMBLY" .
2. Remove filter cover, and then remove in-cabin microfilter.
3. Take out in-cabin microfilter from blower unit.
4. Replace with new one and reinstall on blower unit.
5. Reinstall glove box.
RJIA1331E
RJIA4116E
Page 1618 of 4647
![INFINITI M35 2007 Factory Service Manual BASIC SERVICE PROCEDURE
EC-89
[VQ35DE]
C
D
E
F
G
H
I
J
K
L
MA
EC
Revision: 2007 April2007 M35/M45
Without CONSULT-II
1. Remove fuel pump fuse (1) located in IPDM E/R (2).
2. Start engine.
3. After en INFINITI M35 2007 Factory Service Manual BASIC SERVICE PROCEDURE
EC-89
[VQ35DE]
C
D
E
F
G
H
I
J
K
L
MA
EC
Revision: 2007 April2007 M35/M45
Without CONSULT-II
1. Remove fuel pump fuse (1) located in IPDM E/R (2).
2. Start engine.
3. After en](/img/42/57024/w960_57024-1617.png)
BASIC SERVICE PROCEDURE
EC-89
[VQ35DE]
C
D
E
F
G
H
I
J
K
L
MA
EC
Revision: 2007 April2007 M35/M45
Without CONSULT-II
1. Remove fuel pump fuse (1) located in IPDM E/R (2).
2. Start engine.
3. After engine stalls, crank it two or three times to release all fuel
pressure.
4. Turn ignition switch OFF.
5. Reinstall fuel pump fuse after servicing fuel system.
FUEL PRESSURE CHECK
CAUTION:
Before disconnecting fuel line, release fuel pressure from fuel line to eliminate danger.
NOTE:
Prepare pans or saucers under the disconnected fuel line because the fuel may spill out. The fuel
pressure cannot be completely released because Y50 models do not have fuel return system.
Use Fuel Pressure Gauge Kit (J-44321) to check fuel pressure.
1. Release fuel pressure to zero. Refer to EC-88, "
FUEL PRESSURE RELEASE" .
2. Install the inline fuel quick disconnected fitting between fuel
damper and fuel injector tube.
3. Connect the fuel pressure test gauge (quick connector adapter
hose) to the inline fuel quick disconnected fitting.
4. Turn ignition switch ON and check for fuel leakage.
5. Start engine and check for fuel leakage.
6. Read the indication of fuel pressure gauge.
7. If result is unsatisfactory, go to next step.
8. Check the following.
Fuel hoses and fuel tubes for clogging
Fuel filter for clogging
Fuel pump
Fuel pressure regulator for clogging
If OK, replace fuel pressure regulator.
If NG, repair or replace.
PBIB2697E
At idling:
Approximately 350 kPa (3.57 kg/cm2 , 51 psi)
PBIB1571E
Page 1676 of 4647
![INFINITI M35 2007 Factory Service Manual TROUBLE DIAGNOSIS - SPECIFICATION VALUE
EC-147
[VQ35DE]
C
D
E
F
G
H
I
J
K
L
MA
EC
Revision: 2007 April2007 M35/M45
5. CHANGE ENGINE OIL
1. Stop the engine.
2. Change engine oil.
NOTE:
This symptom may INFINITI M35 2007 Factory Service Manual TROUBLE DIAGNOSIS - SPECIFICATION VALUE
EC-147
[VQ35DE]
C
D
E
F
G
H
I
J
K
L
MA
EC
Revision: 2007 April2007 M35/M45
5. CHANGE ENGINE OIL
1. Stop the engine.
2. Change engine oil.
NOTE:
This symptom may](/img/42/57024/w960_57024-1675.png)
TROUBLE DIAGNOSIS - SPECIFICATION VALUE
EC-147
[VQ35DE]
C
D
E
F
G
H
I
J
K
L
MA
EC
Revision: 2007 April2007 M35/M45
5. CHANGE ENGINE OIL
1. Stop the engine.
2. Change engine oil.
NOTE:
This symptom may occur when a large amount of gasoline is mixed with engine oil because of driving
conditions (such as when engine oil temperature does not rise enough since a journey distance is too
short during winter). The symptom will not be detected after changing engine oil or changing driving con-
dition.
>>INSPECTION END
6. CHECK FUEL PRESSURE
Check fuel pressure. (Refer to EC-88, "
Fuel Pressure Check" .)
OK or NG
OK >> GO TO 9.
NG (Fuel pressure is too high)>>Replace fuel pressure regulator, refer to EC-89, "
FUEL PRESSURE
CHECK" . GO TO 8.
NG (Fuel pressure is too low)>>GO TO 7.
7. DETECT MALFUNCTIONING PART
1. Check the following.
–Clogged and bent fuel hose and fuel tube
–Clogged fuel filter
–Fuel pump and its circuit (Refer to EC-675, "FUEL PUMP" .)
2. If NG, repair or replace the malfunctioning part. (Refer to EC-89, "
FUEL PRESSURE CHECK" .)
If OK, replace fuel pressure regulator.
>> GO TO 8.
8. CHECK “A/F ALPHA-B1”, “A/F ALPHA-B2”
1. Start engine.
2. Select “A/F ALPHA-B1”, “A/F ALPHA-B2” in “DATA MONITOR (SPEC)” mode, and make sure that the
each indication is within the SP value.
OK or NG
OK >>INSPECTION END
NG >> GO TO 9.
9. PERFORM POWER BALANCE TEST
1. Perform “POWER BALANCE” in “ACTIVE TEST” mode.
2. Make sure that the each cylinder produces a momentary engine
speed drop.
OK or NG
OK >> GO TO 12.
NG >> GO TO 10.
PBIB0133E
Page 1846 of 4647
![INFINITI M35 2007 Factory Service Manual DTC P0171, P0174 FUEL INJECTION SYSTEM FUNCTION
EC-317
[VQ35DE]
C
D
E
F
G
H
I
J
K
L
MA
EC
Revision: 2007 April2007 M35/M45
4. CHECK FUEL PRESSURE
1. Release fuel pressure to zero. Refer to EC-88, "
FU INFINITI M35 2007 Factory Service Manual DTC P0171, P0174 FUEL INJECTION SYSTEM FUNCTION
EC-317
[VQ35DE]
C
D
E
F
G
H
I
J
K
L
MA
EC
Revision: 2007 April2007 M35/M45
4. CHECK FUEL PRESSURE
1. Release fuel pressure to zero. Refer to EC-88, "
FU](/img/42/57024/w960_57024-1845.png)
DTC P0171, P0174 FUEL INJECTION SYSTEM FUNCTION
EC-317
[VQ35DE]
C
D
E
F
G
H
I
J
K
L
MA
EC
Revision: 2007 April2007 M35/M45
4. CHECK FUEL PRESSURE
1. Release fuel pressure to zero. Refer to EC-88, "
FUEL PRESSURE RELEASE" .
2. Install fuel pressure gauge and check fuel pressure. Refer to EC-89, "
FUEL PRESSURE CHECK" .
OK or NG
OK >> GO TO 6.
NG >> GO TO 5.
5. DETECT MALFUNCTIONING PART
Check the following.
Fuel pump and circuit (Refer to EC-675, "FUEL PUMP" .)
Fuel pressure regulator (Refer to EC-89, "FUEL PRESSURE CHECK" .)
Fuel lines (Refer to FL-3, "FUEL SYSTEM" .)
Fuel filter for clogging
>> Repair or replace.
6. CHECK MASS AIR FLOW SENSOR
With CONSULT-II
1. Install all removed parts.
2. Check “MASS AIR FLOW” in “DATA MONITOR” mode with CONSULT-II.
With GST
1. Install all removed parts.
2. Check mass air flow sensor signal in Service $01 with GST.
OK or NG
OK (With CONSULT-II)>>GO TO 7.
OK (Without CONSULT-II)>>GO TO 8.
NG >> Check connectors for rusted terminals or loose connections in the mass air flow sensor circuit or
grounds. Refer to EC-193, "
DTC P0101 MAF SENSOR" .
7. CHECK FUNCTION OF FUEL INJECTOR
With CONSULT-II
1. Start engine.
2. Perform “POWER BALANCE” in “ACTIVE TEST” mode with
CONSULT-II.
3. Make sure that each circuit produces a momentary engine
speed drop.
OK or NG
OK >> GO TO 10.
NG >> Perform trouble diagnosis for FUEL INJECTOR, refer to
EC-669, "
FUEL INJECTOR" . At idling: Approximately 350 kPa (3.57 kg/cm
2 , 51 psi)
2.0 - 6.0 g·m/sec: at idling
7.0 - 20.0 g·m/sec: at 2,500 rpm
2.0 - 6.0 g·m/sec: at idling
7.0 - 20.0 g·m/sec: at 2,500 rpm
PBIB0133E
Page 1884 of 4647
![INFINITI M35 2007 Factory Service Manual DTC P0300 - P0306 MULTIPLE CYLINDER MISFIRE, NO. 1 - 6 CYLINDER MIS-
FIRE
EC-355
[VQ35DE]
C
D
E
F
G
H
I
J
K
L
MA
EC
Revision: 2007 April2007 M35/M45
8. CHECK SPARK PLUG
Check the initial spark plug fo INFINITI M35 2007 Factory Service Manual DTC P0300 - P0306 MULTIPLE CYLINDER MISFIRE, NO. 1 - 6 CYLINDER MIS-
FIRE
EC-355
[VQ35DE]
C
D
E
F
G
H
I
J
K
L
MA
EC
Revision: 2007 April2007 M35/M45
8. CHECK SPARK PLUG
Check the initial spark plug fo](/img/42/57024/w960_57024-1883.png)
DTC P0300 - P0306 MULTIPLE CYLINDER MISFIRE, NO. 1 - 6 CYLINDER MIS-
FIRE
EC-355
[VQ35DE]
C
D
E
F
G
H
I
J
K
L
MA
EC
Revision: 2007 April2007 M35/M45
8. CHECK SPARK PLUG
Check the initial spark plug for fouling, etc.
OK or NG
OK >> Replace spark plug(s) with standard type one(s). For
spark plug type, refer to EM-45, "
SPARK PLUG (PLATI-
NUM-TIPPED TYPE)" .
NG >> 1. Repair or clean spark plug.
2. GO TO 9.
9. CHECK FUNCTION OF IGNITION COIL-III
1. Reconnect the initial spark plugs.
2. Crank engine for about 3 seconds, and recheck whether spark is generated between the spark plug and
the grounded portion.
OK or NG
OK >>INSPECTION END
NG >> Replace spark plug(s) with standard type one(s). For spark plug type, refer to MA-20, "
Changing
Spark Plugs (Platinum-Tipped Type)" .
10. CHECK COMPRESSION PRESSURE
Check compression pressure. Refer to EM-102, "
CHECKING COMPRESSION PRESSURE" .
OK or NG
OK >> GO TO 11.
NG >> Check pistons, piston rings, valves, valve seats and cylinder head gaskets.
11 . CHECK FUEL PRESSURE
1. Install all removed parts.
2. Release fuel pressure to zero. Refer to EC-88, "
FUEL PRESSURE RELEASE" .
3. Install fuel pressure gauge and check fuel pressure. Refer to EC-89, "
FUEL PRESSURE CHECK" .
OK or NG
OK >> GO TO 13.
NG >> GO TO 12.
12. DETECT MALFUNCTIONING PART
Check the following.
Fuel pump and circuit (Refer to EC-675, "FUEL PUMP" .)
Fuel pressure regulator (Refer to EC-89, "FUEL PRESSURE CHECK" .)
Fuel lines (Refer to FL-3, "FUEL SYSTEM" .)
Fuel filter for clogging
>> Repair or replace.
SEF156I
Spark should be generated.
At idling: Approximately 350 kPa (3.57 kg/cm
2 , 51 psi)
Page 2320 of 4647
![INFINITI M35 2007 Factory Service Manual BASIC SERVICE PROCEDURE
EC-791
[VK45DE]
C
D
E
F
G
H
I
J
K
L
MA
EC
Revision: 2007 April2007 M35/M45
Without CONSULT-II
1. Remove fuel pump fuse (1) located in IPDM E/R (2).
2. Start engine.
3. After e INFINITI M35 2007 Factory Service Manual BASIC SERVICE PROCEDURE
EC-791
[VK45DE]
C
D
E
F
G
H
I
J
K
L
MA
EC
Revision: 2007 April2007 M35/M45
Without CONSULT-II
1. Remove fuel pump fuse (1) located in IPDM E/R (2).
2. Start engine.
3. After e](/img/42/57024/w960_57024-2319.png)
BASIC SERVICE PROCEDURE
EC-791
[VK45DE]
C
D
E
F
G
H
I
J
K
L
MA
EC
Revision: 2007 April2007 M35/M45
Without CONSULT-II
1. Remove fuel pump fuse (1) located in IPDM E/R (2).
2. Start engine.
3. After engine stalls, crank it 2 or 3 times to release all fuel pres-
sure.
4. Turn ignition switch OFF.
5. Reinstall fuel pump fuse after servicing fuel system.
FUEL PRESSURE CHECK
CAUTION:
Before disconnecting fuel line, release fuel pressure from fuel line to eliminate danger.
NOTE:
Prepare pans or saucers under the disconnected fuel line because the fuel may spill out. The fuel
pressure cannot be completely released because Y50 models do not have fuel return system.
Use Fuel Pressure Gauge Kit (J-44321) to check fuel pressure.
1. Release fuel pressure to zero. Refer to EC-790, "
FUEL PRESSURE RELEASE" .
2. Install the inline fuel quick disconnect fitting A between fuel
damper (1) and fuel tube.
3. Connect the fuel pressure gauge B (quick connect adapter
hose) to the inline fuel quick disconnect fitting.
4. Turn ignition switch ON and check for fuel leakage.
5. Start engine and check for fuel leakage.
6. Read the indication of fuel pressure gauge.
7. If result is unsatisfactory, go to next step.
8. Check the following.
Fuel hoses and fuel tubes for clogging
Fuel filter for clogging
Fuel pump
Fuel pressure regulator for clogging
If OK, replace fuel level sensor unit, fuel filter and fuel pump assembly.
If NG, repair or replace.
PBIB2697E
At idling:
Approximately 350 kPa (3.57 kg/cm2 , 51 psi)
PBIB2720E
Page 2332 of 4647
![INFINITI M35 2007 Factory Service Manual TROUBLE DIAGNOSIS
EC-803
[VK45DE]
C
D
E
F
G
H
I
J
K
L
MA
EC
Revision: 2007 April2007 M35/M45
Air Air duct
55555 5EM-177
Air cleanerEM-177
Air leakage from air duct
(Mass air flow sensor — electric
INFINITI M35 2007 Factory Service Manual TROUBLE DIAGNOSIS
EC-803
[VK45DE]
C
D
E
F
G
H
I
J
K
L
MA
EC
Revision: 2007 April2007 M35/M45
Air Air duct
55555 5EM-177
Air cleanerEM-177
Air leakage from air duct
(Mass air flow sensor — electric](/img/42/57024/w960_57024-2331.png)
TROUBLE DIAGNOSIS
EC-803
[VK45DE]
C
D
E
F
G
H
I
J
K
L
MA
EC
Revision: 2007 April2007 M35/M45
Air Air duct
55555 5EM-177
Air cleanerEM-177
Air leakage from air duct
(Mass air flow sensor — electric
throttle control actuator)
5555EM-177
Electric throttle control actuatorEM-179
Air leakage from intake manifold/
Collector/GasketEM-179
Cranking Battery
111111
11SC-4
Generator circuitSC-20
Starter circuit 3SC-8
Signal plate 6EM-252
PNP switch 4AT- 11 3
Engine Cylinder head
55555 55 5EM-235
Cylinder head gasket 4 3
Cylinder block
66666 66 64
EM-252
Piston
Piston ring
Connecting rod
Bearing
Crankshaft
Va l v e
mecha-
nismTiming chain
55555 55 5EM-203
CamshaftEM-215
Intake valve timing controlEM-215
Intake valve
3EM-235
Exhaust valve
Exhaust Exhaust manifold/Tube/Muffler/
Gasket
55555 55 5EM-183
,
EX-3
Three way catalyst
Lubrica-
tionOil pan/Oil strainer/Oil pump/Oil
filter/Oil gallery
55555 55 5EM-187
,
LU-31
, LU-
30
Oil level (Low)/Filthy oilLU-27
SYMPTOM
Reference
page
HARD/NO START/RESTART (EXCP. HA)
ENGINE STALL
HESITATION/SURGING/FLAT SPOT
SPARK KNOCK/DETONATION
LACK OF POWER/POOR ACCELERATION
HIGH IDLE/LOW IDLE
ROUGH IDLE/HUNTING
IDLING VIBRATION
SLOW/NO RETURN TO IDLE
OVERHEATS/WATER TEMPERATURE HIGH
EXCESSIVE FUEL CONSUMPTION
EXCESSIVE OIL CONSUMPTION
BATTERY DEAD (UNDER CHARGE)
Warranty symptom code AA AB AC AD AE AF AG AH AJ AK AL AM HA