torque INFINITI QX4 2005 Factory Service Manual
[x] Cancel search | Manufacturer: INFINITI, Model Year: 2005, Model line: QX4, Model: INFINITI QX4 2005Pages: 3419, PDF Size: 80.18 MB
Page 2153 of 3419
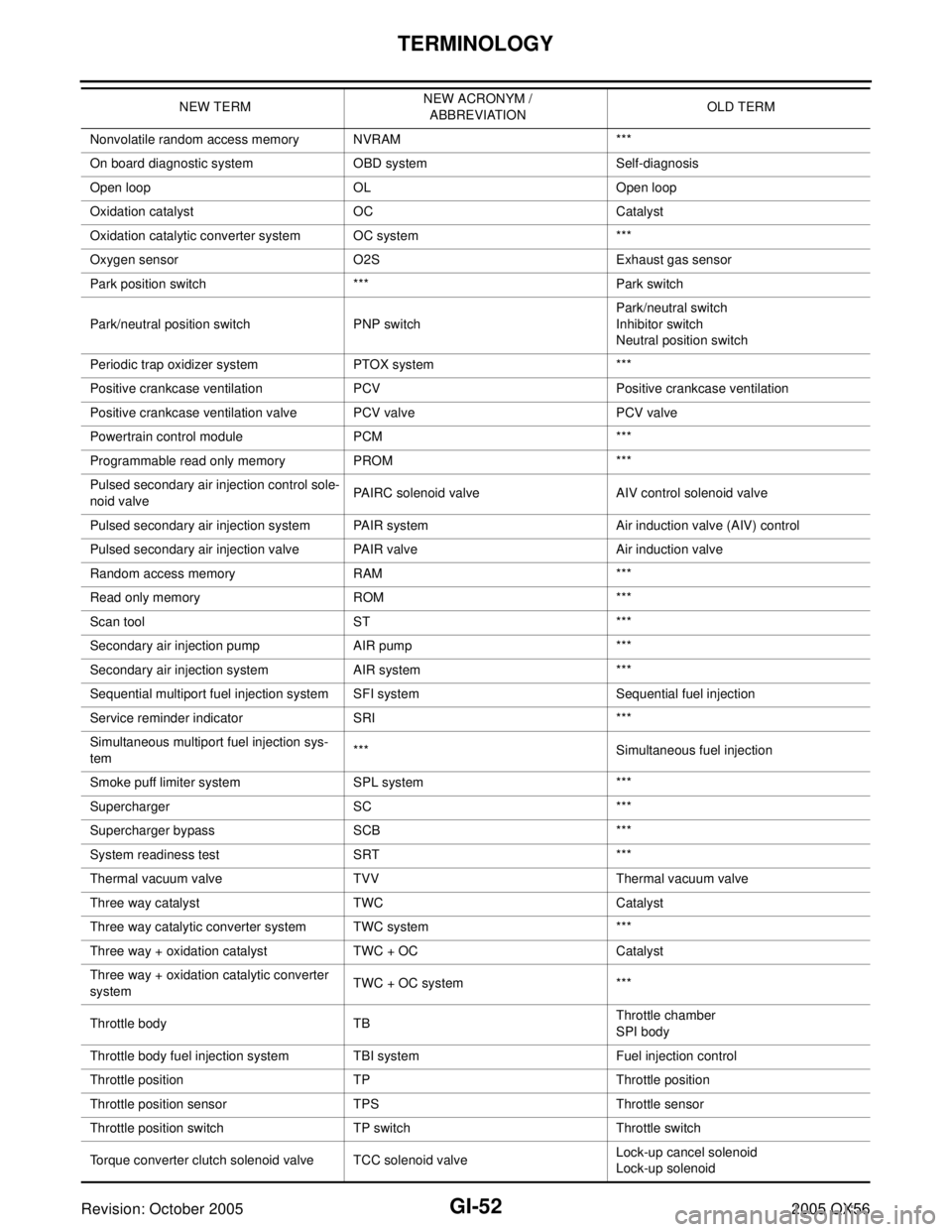
GI-52
TERMINOLOGY
Revision: October 20052005 QX56
Nonvolatile random access memory NVRAM ***
On board diagnostic system OBD system Self-diagnosis
Open loop OL Open loop
Oxidation catalyst OC Catalyst
Oxidation catalytic converter system OC system ***
Oxygen sensor O2S Exhaust gas sensor
Park position switch *** Park switch
Park/neutral position switch PNP switchPark/neutral switch
Inhibitor switch
Neutral position switch
Periodic trap oxidizer system PTOX system ***
Positive crankcase ventilation PCV Positive crankcase ventilation
Positive crankcase ventilation valve PCV valve PCV valve
Powertrain control module PCM ***
Programmable read only memory PROM ***
Pulsed secondary air injection control sole-
noid valvePAIRC solenoid valve AIV control solenoid valve
Pulsed secondary air injection system PAIR system Air induction valve (AIV) control
Pulsed secondary air injection valve PAIR valve Air induction valve
Random access memory RAM ***
Read only memory ROM ***
Scan tool ST ***
Secondary air injection pump AIR pump ***
Secondary air injection system AIR system ***
Sequential multiport fuel injection system SFI system Sequential fuel injection
Service reminder indicator SRI ***
Simultaneous multiport fuel injection sys-
tem*** Simultaneous fuel injection
Smoke puff limiter system SPL system ***
Supercharger SC ***
Supercharger bypass SCB ***
System readiness test SRT ***
Thermal vacuum valve TVV Thermal vacuum valve
Three way catalyst TWC Catalyst
Three way catalytic converter system TWC system ***
Three way + oxidation catalyst TWC + OC Catalyst
Three way + oxidation catalytic converter
systemTWC + OC system ***
Throttle body TBThrottle chamber
SPI body
Throttle body fuel injection system TBI system Fuel injection control
Throttle position TP Throttle position
Throttle position sensor TPS Throttle sensor
Throttle position switch TP switch Throttle switch
Torque converter clutch solenoid valve TCC solenoid valveLock-up cancel solenoid
Lock-up solenoid NEW TERMNEW ACRONYM /
ABBREVIATIONOLD TERM
Page 2228 of 3419
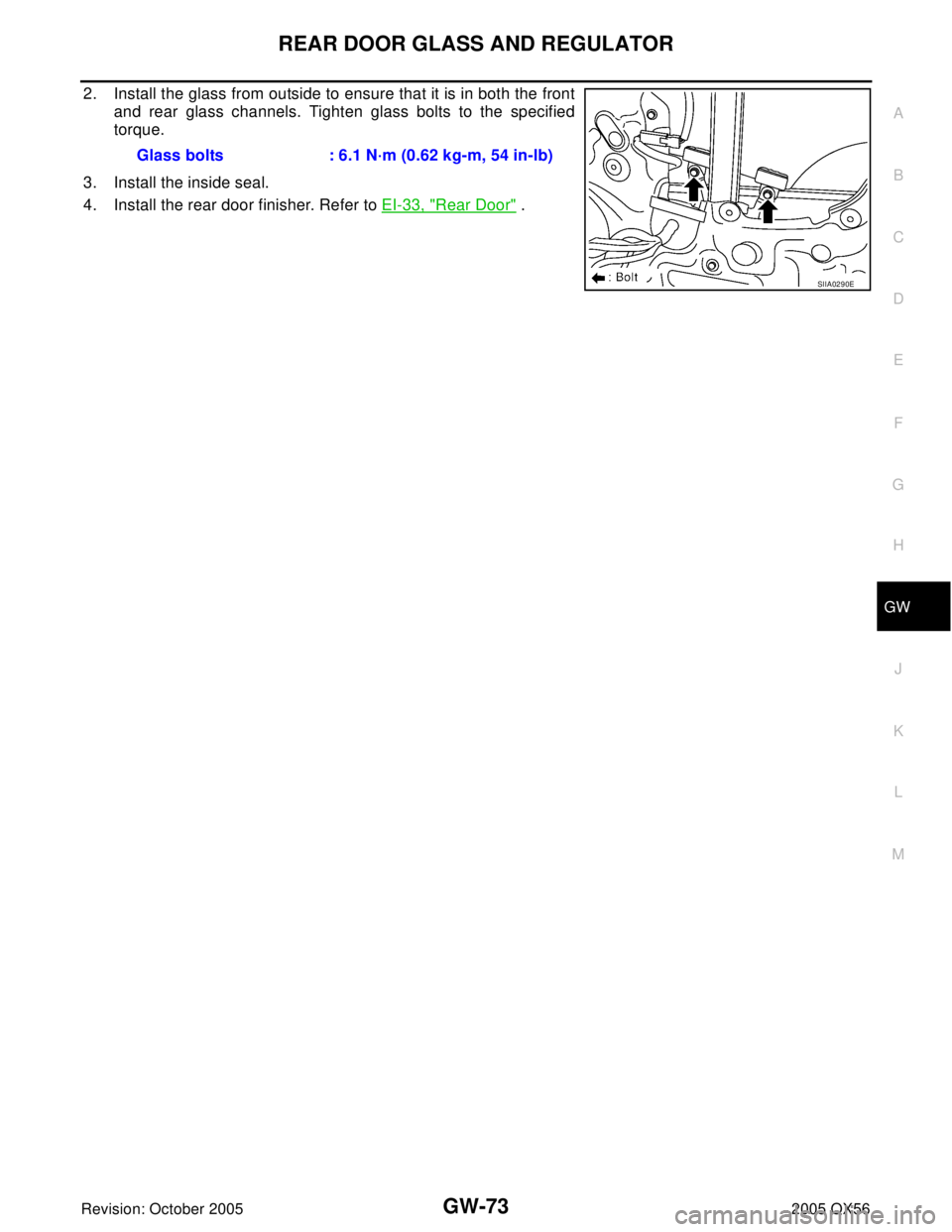
REAR DOOR GLASS AND REGULATOR
GW-73
C
D
E
F
G
H
J
K
L
MA
B
GW
Revision: October 20052005 QX56
2. Install the glass from outside to ensure that it is in both the front
and rear glass channels. Tighten glass bolts to the specified
torque.
3. Install the inside seal.
4. Install the rear door finisher. Refer to EI-33, "
Rear Door" . Glass bolts : 6.1 N·m (0.62 kg-m, 54 in-lb)
SIIA0290E
Page 2229 of 3419
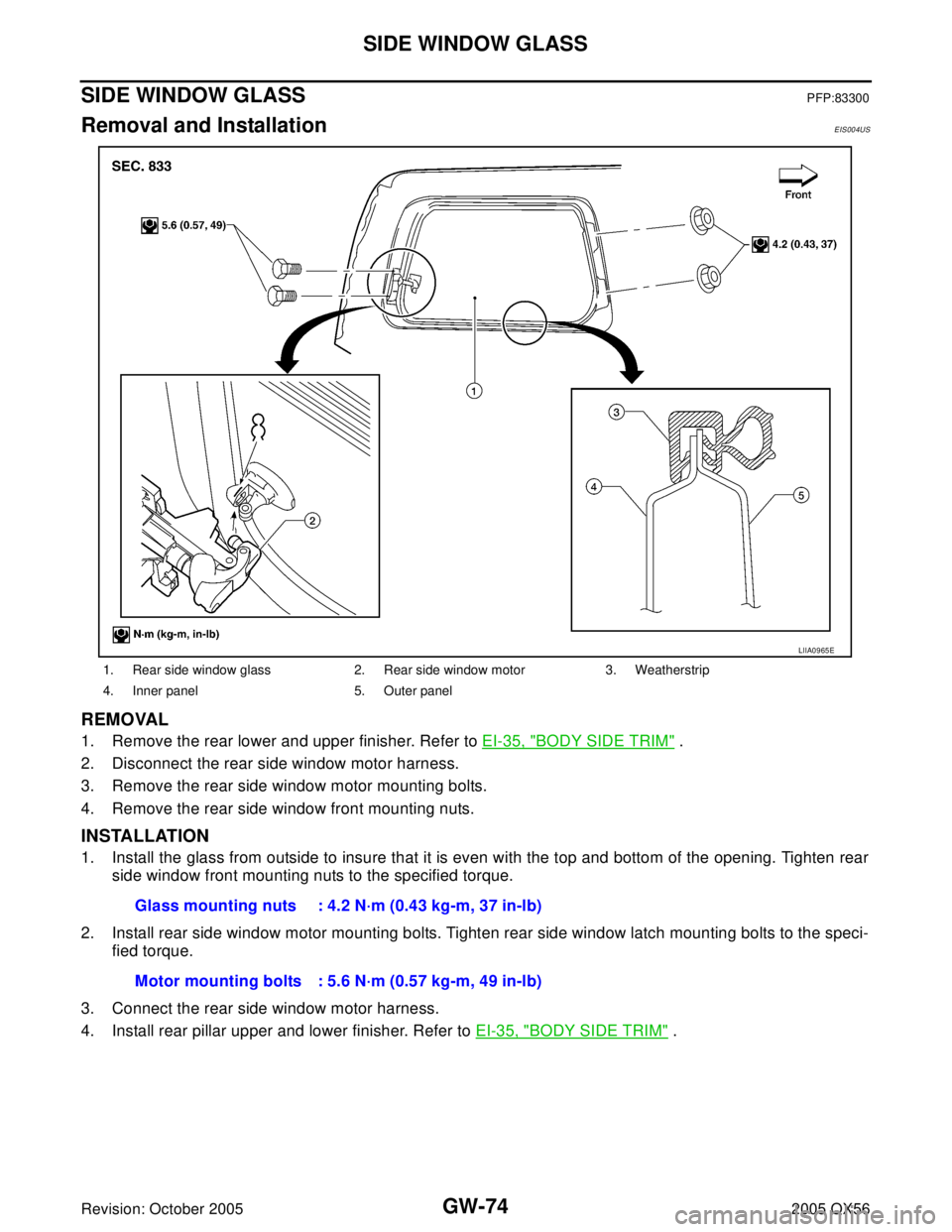
GW-74
SIDE WINDOW GLASS
Revision: October 20052005 QX56
SIDE WINDOW GLASSPFP:83300
Removal and InstallationEIS004US
REMOVAL
1. Remove the rear lower and upper finisher. Refer to EI-35, "BODY SIDE TRIM" .
2. Disconnect the rear side window motor harness.
3. Remove the rear side window motor mounting bolts.
4. Remove the rear side window front mounting nuts.
INSTALLATION
1. Install the glass from outside to insure that it is even with the top and bottom of the opening. Tighten rear
side window front mounting nuts to the specified torque.
2. Install rear side window motor mounting bolts. Tighten rear side window latch mounting bolts to the speci-
fied torque.
3. Connect the rear side window motor harness.
4. Install rear pillar upper and lower finisher. Refer to EI-35, "
BODY SIDE TRIM" .
1. Rear side window glass 2. Rear side window motor 3. Weatherstrip
4. Inner panel 5. Outer panel
LIIA0965E
Glass mounting nuts : 4.2 N·m (0.43 kg-m, 37 in-lb)
Motor mounting bolts : 5.6 N·m (0.57 kg-m, 49 in-lb)
Page 2261 of 3419
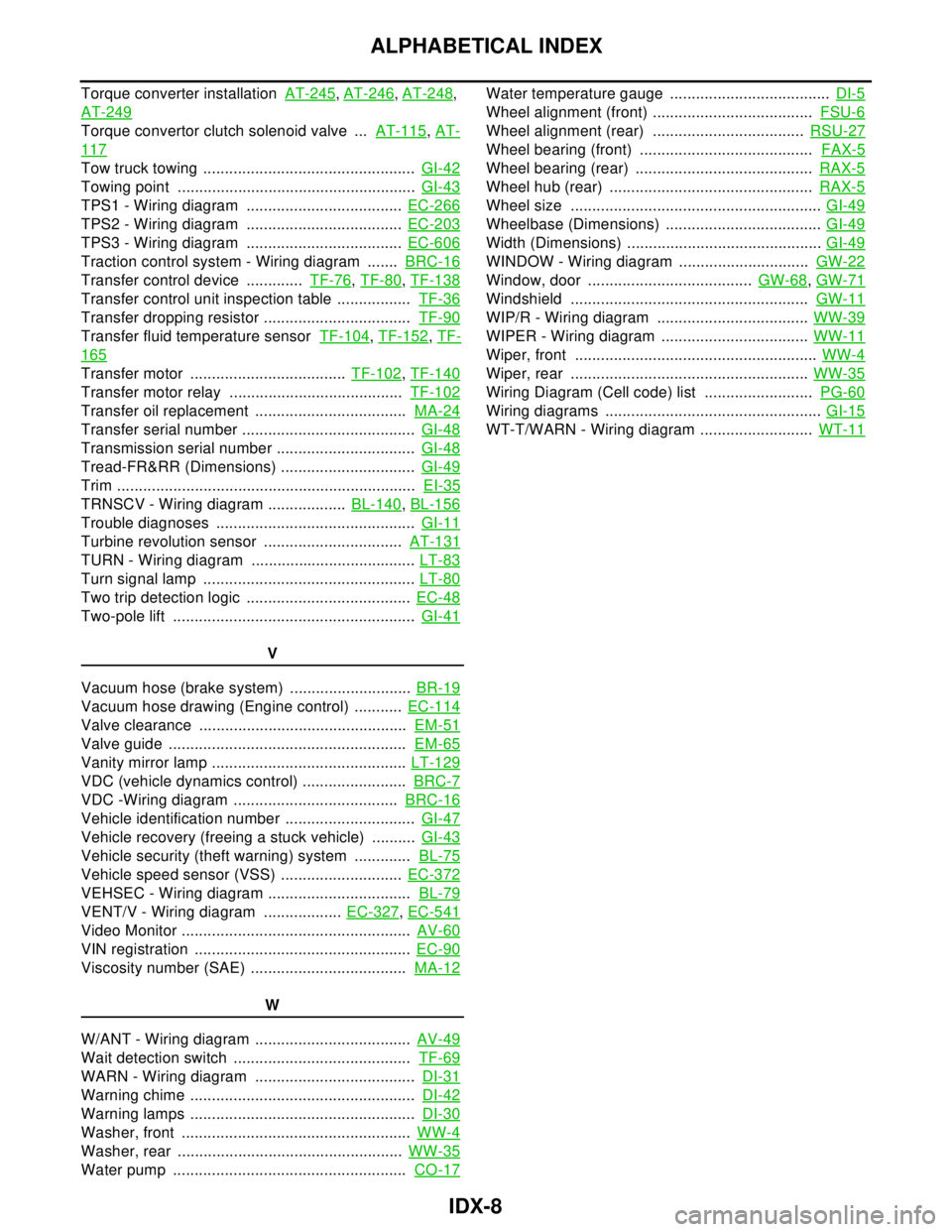
IDX-8
ALPHABETICAL INDEX
Torque converter installation AT-245, AT-246, AT-248,
AT-249
Torque convertor clutch solenoid valve ... AT-115, AT-
117
Tow truck towing ................................................. GI-42
Towing point ....................................................... GI-43
TPS1 - Wiring diagram .................................... EC-266
TPS2 - Wiring diagram .................................... EC-203
TPS3 - Wiring diagram .................................... EC-606
Traction control system - Wiring diagram ....... BRC-16
Transfer control device ............. TF-76, TF-80, TF-138
Transfer control unit inspection table ................. TF-36
Transfer dropping resistor .................................. TF-90
Transfer fluid temperature sensor TF-104, TF-152, TF-
165
Transfer motor .................................... TF-102, TF-140
Transfer motor relay ........................................ TF-102
Transfer oil replacement ................................... MA-24
Transfer serial number ........................................ GI-48
Transmission serial number ................................ GI-48
Tread-FR&RR (Dimensions) ............................... GI-49
Trim ..................................................................... EI-35
TRNSCV - Wiring diagram .................. BL-140, BL-156
Trouble diagnoses .............................................. GI-11
Turbine revolution sensor ................................ AT-131
TURN - Wiring diagram ...................................... LT-83
Turn signal lamp ................................................. LT-80
Two trip detection logic ...................................... EC-48
Two-pole lift ........................................................ GI-41
V
Vacuum hose (brake system) ............................ BR-19
Vacuum hose drawing (Engine control) ........... EC-114
Valve clearance ................................................ EM-51
Valve guide ....................................................... EM-65
Vanity mirror lamp ............................................. LT-129
VDC (vehicle dynamics control) ........................ BRC-7
VDC -Wiring diagram ...................................... BRC-16
Vehicle identification number .............................. GI-47
Vehicle recovery (freeing a stuck vehicle) .......... GI-43
Vehicle security (theft warning) system ............. BL-75
Vehicle speed sensor (VSS) ............................ EC-372
VEHSEC - Wiring diagram ................................. BL-79
VENT/V - Wiring diagram .................. EC-327, EC-541
Video Monitor ..................................................... AV-60
VIN registration .................................................. EC-90
Viscosity number (SAE) .................................... MA-12
W
W/ANT - Wiring diagram .................................... AV-49
Wait detection switch ......................................... TF-69
WARN - Wiring diagram ..................................... DI-31
Warning chime .................................................... DI-42
Warning lamps .................................................... DI-30
Washer, front ..................................................... WW-4
Washer, rear .................................................... WW-35
Water pump ...................................................... CO-17
Water temperature gauge ..................................... DI-5
Wheel alignment (front) ..................................... FSU-6
Wheel alignment (rear) ................................... RSU-27
Wheel bearing (front) ........................................ FAX-5
Wheel bearing (rear) ......................................... RAX-5
Wheel hub (rear) ............................................... RAX-5
Wheel size .......................................................... GI-49
Wheelbase (Dimensions) .................................... GI-49
Width (Dimensions) ............................................. GI-49
WINDOW - Wiring diagram .............................. GW-22
Window, door ...................................... GW-68, GW-71
Windshield ....................................................... GW-11
WIP/R - Wiring diagram ................................... WW-39
WIPER - Wiring diagram .................................. WW-11
Wiper, front ........................................................ WW-4
Wiper, rear ....................................................... WW-35
Wiring Diagram (Cell code) list ......................... PG-60
Wiring diagrams .................................................. GI-15
WT-T/WARN - Wiring diagram .......................... WT-11
Page 2625 of 3419
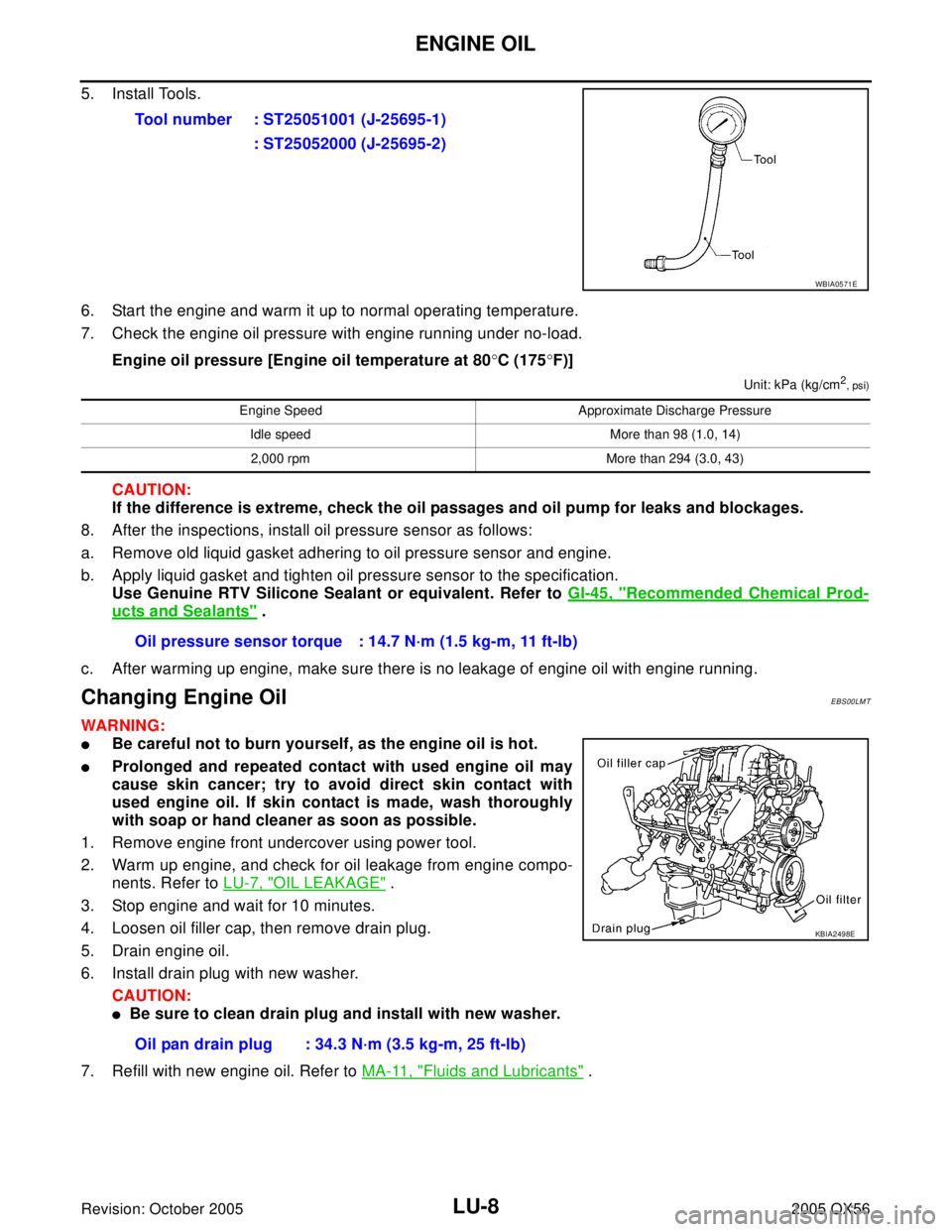
LU-8Revision: October 2005
ENGINE OIL
2005 QX56
5. Install Tools.
6. Start the engine and warm it up to normal operating temperature.
7. Check the engine oil pressure with engine running under no-load.
Engine oil pressure [Engine oil temperature at 80°C (175°F)]
Unit: kPa (kg/cm2
, psi)
CAUTION:
If the difference is extreme, check the oil passages and oil pump for leaks and blockages.
8. After the inspections, install oil pressure sensor as follows:
a. Remove old liquid gasket adhering to oil pressure sensor and engine.
b. Apply liquid gasket and tighten oil pressure sensor to the specification.
Use Genuine RTV Silicone Sealant or equivalent. Refer to GI-45, "
Recommended Chemical Prod-
ucts and Sealants" .
c. After warming up engine, make sure there is no leakage of engine oil with engine running.
Changing Engine OilEBS00LMT
WAR NIN G:
Be careful not to burn yourself, as the engine oil is hot.
Prolonged and repeated contact with used engine oil may
cause skin cancer; try to avoid direct skin contact with
used engine oil. If skin contact is made, wash thoroughly
with soap or hand cleaner as soon as possible.
1. Remove engine front undercover using power tool.
2. Warm up engine, and check for oil leakage from engine compo-
nents. Refer to LU-7, "
OIL LEAKAGE" .
3. Stop engine and wait for 10 minutes.
4. Loosen oil filler cap, then remove drain plug.
5. Drain engine oil.
6. Install drain plug with new washer.
CAUTION:
Be sure to clean drain plug and install with new washer.
7. Refill with new engine oil. Refer to MA-11, "
Fluids and Lubricants" . Tool number : ST25051001 (J-25695-1)
: ST25052000 (J-25695-2)
WBIA0571E
Engine Speed Approximate Discharge Pressure
Idle speed More than 98 (1.0, 14)
2,000 rpm More than 294 (3.0, 43)
Oil pressure sensor torque : 14.7 N·m (1.5 kg-m, 11 ft-lb)
Oil pan drain plug : 34.3 N·m (3.5 kg-m, 25 ft-lb)
KBIA2498E
Page 2756 of 3419
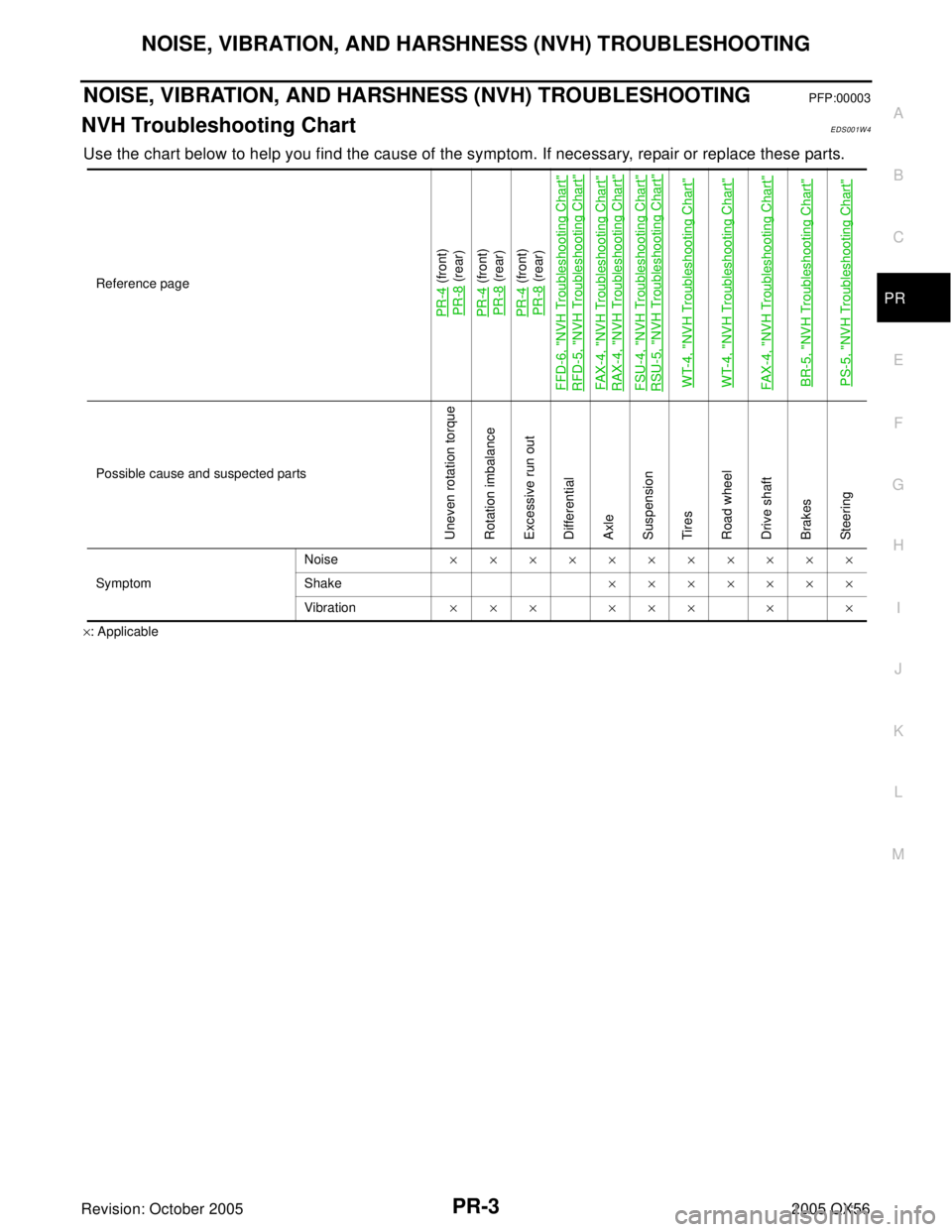
NOISE, VIBRATION, AND HARSHNESS (NVH) TROUBLESHOOTING
PR-3
C
E
F
G
H
I
J
K
L
MA
B
PR
Revision: October 20052005 QX56
NOISE, VIBRATION, AND HARSHNESS (NVH) TROUBLESHOOTINGPFP:00003
NVH Troubleshooting ChartEDS001W4
Use the chart below to help you find the cause of the symptom. If necessary, repair or replace these parts.
×: ApplicableReference page
PR-4
(front)
PR-8 (rear)
PR-4 (front)
PR-8 (rear)
PR-4 (front)
PR-8 (rear)
FFD-6, "
NVH Troubleshooting Chart
"
RFD-5, "
NVH Troubleshooting Chart
"
FAX -4, "
NVH Troubleshooting Chart
"
RAX-4, "
NVH Troubleshooting Chart
"
FSU-4, "
NVH Troubleshooting Chart
"
RSU-5, "
NVH Troubleshooting Chart
"
WT-4, "
NVH Troubleshooting Chart
"
WT-4, "
NVH Troubleshooting Chart
"
FAX -4, "
NVH Troubleshooting Chart
"
BR-5, "
NVH Troubleshooting Chart
"
PS-5, "
NVH Troubleshooting Chart
"
Possible cause and suspected parts
Uneven rotation torque
Rotation imbalance
Excessive run out
Differential
Axle
Suspension
Tire s
Road wheel
Drive shaft
Brakes
Steering
SymptomNoise×××××××××××
Shake×××××××
Vibration××× ××× × ×
Page 2770 of 3419
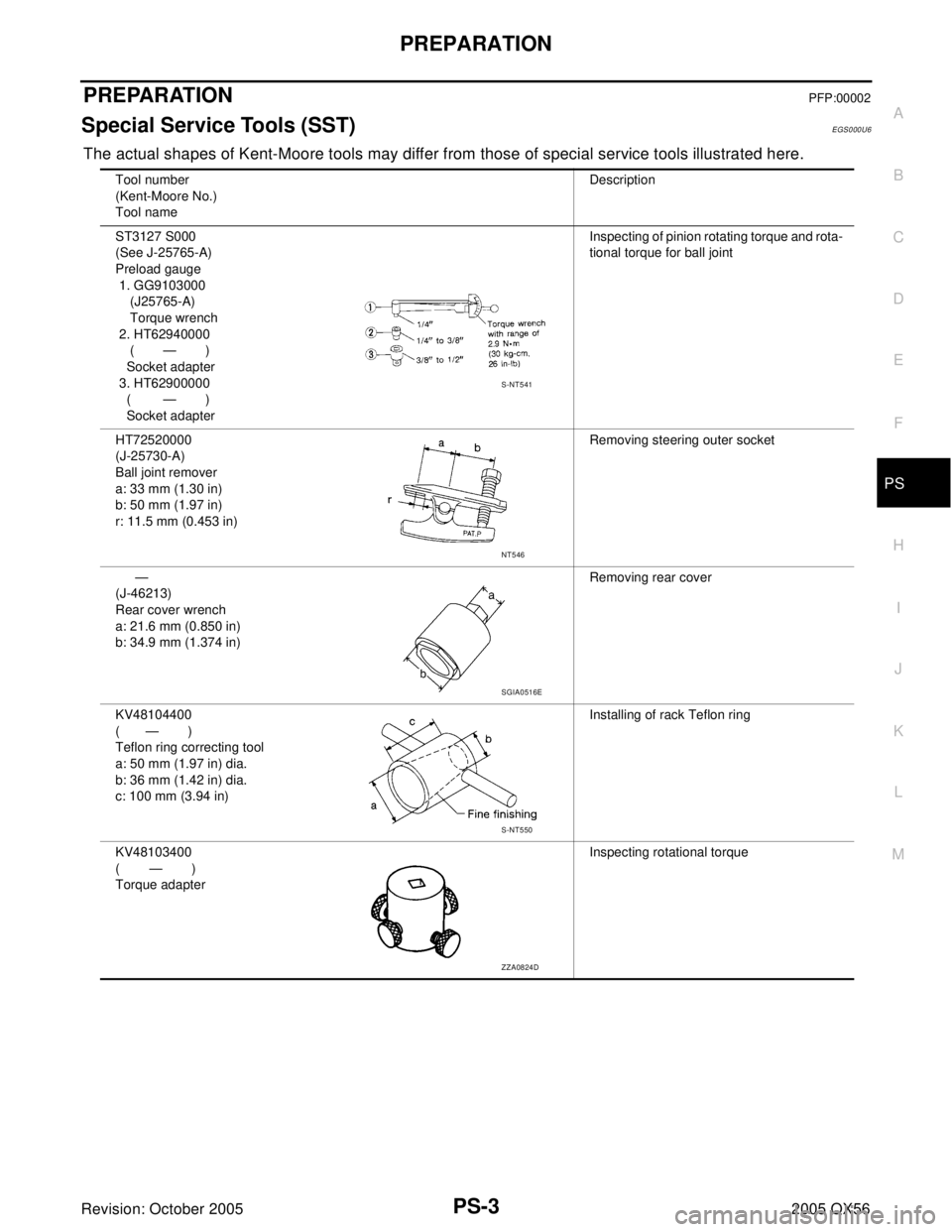
PREPARATION
PS-3
C
D
E
F
H
I
J
K
L
MA
B
PS
Revision: October 20052005 QX56
PREPARATIONPFP:00002
Special Service Tools (SST)EGS000U6
The actual shapes of Kent-Moore tools may differ from those of special service tools illustrated here.
Tool number
(Kent-Moore No.)
Tool nameDescription
ST3127 S000
(See J-25765-A)
Preload gauge
1. GG9103000
(J25765-A)
Torque wrench
2. HT62940000
( — )
Socket adapter
3. HT62900000
( — )
Socket adapterInspecting of pinion rotating torque and rota-
tional torque for ball joint
HT72520000
(J-25730-A)
Ball joint remover
a: 33 mm (1.30 in)
b: 50 mm (1.97 in)
r: 11.5 mm (0.453 in)Removing steering outer socket
—
(J-46213)
Rear cover wrench
a: 21.6 mm (0.850 in)
b: 34.9 mm (1.374 in)Removing rear cover
KV48104400
( — )
Teflon ring correcting tool
a: 50 mm (1.97 in) dia.
b: 36 mm (1.42 in) dia.
c: 100 mm (3.94 in)Installing of rack Teflon ring
KV48103400
( — )
Torque adapterInspecting rotational torque
S-NT541
NT546
SGIA0516E
S-NT550
ZZA0824D
Page 2772 of 3419
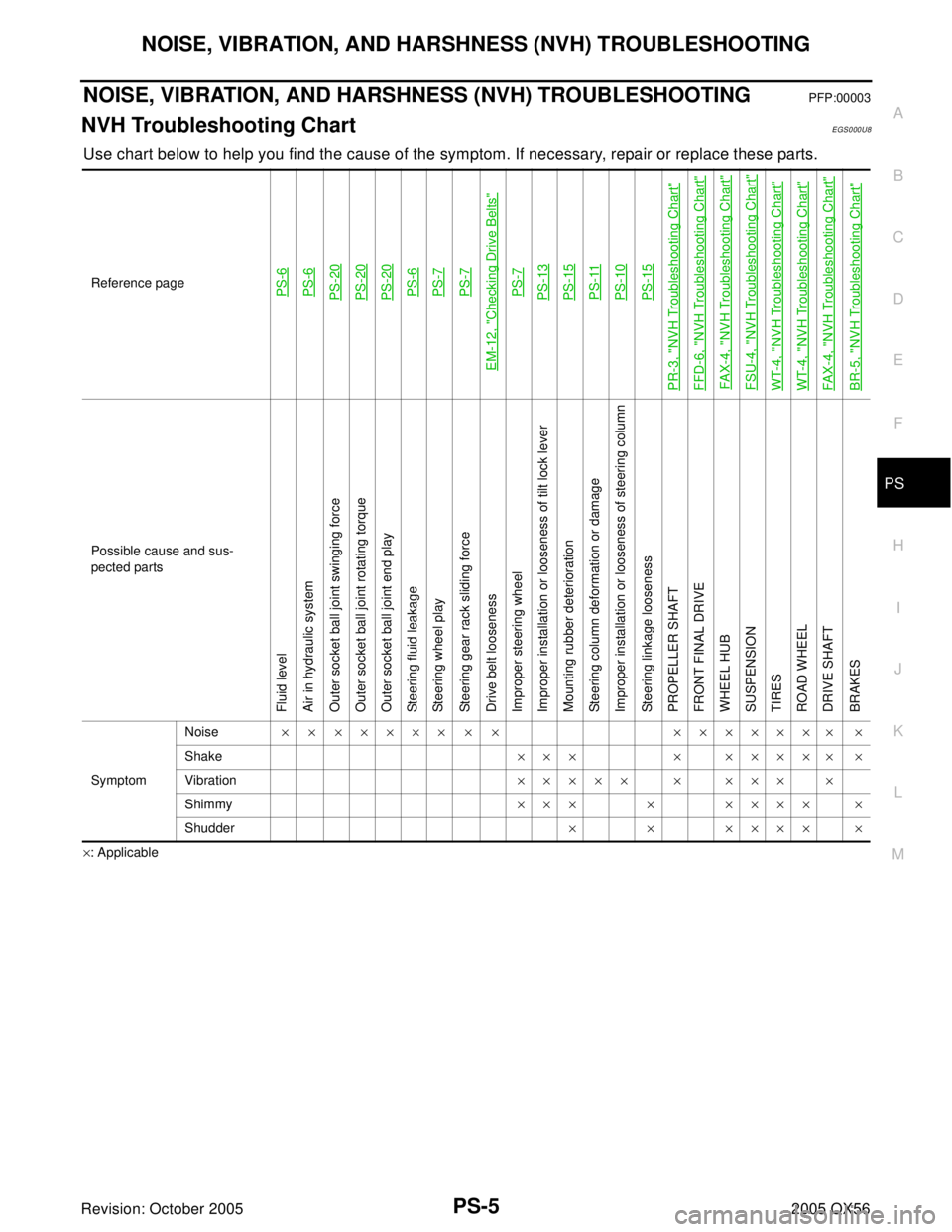
NOISE, VIBRATION, AND HARSHNESS (NVH) TROUBLESHOOTING
PS-5
C
D
E
F
H
I
J
K
L
MA
B
PS
Revision: October 20052005 QX56
NOISE, VIBRATION, AND HARSHNESS (NVH) TROUBLESHOOTINGPFP:00003
NVH Troubleshooting ChartEGS000U8
Use chart below to help you find the cause of the symptom. If necessary, repair or replace these parts.
×: ApplicableReference page
PS-6PS-6PS-20PS-20PS-20PS-6PS-7PS-7
EM-12, "
Checking Drive Belts
"
PS-7PS-13PS-15PS-11PS-10PS-15
PR-3, "
NVH Troubleshooting Chart
"
FFD-6, "
NVH Troubleshooting Chart
"
FA X-4, "
NVH Troubleshooting Chart
"
FSU-4, "
NVH Troubleshooting Chart
"
WT-4, "
NVH Troubleshooting Chart
"
WT-4, "
NVH Troubleshooting Chart
"
FAX -4, "
NVH Troubleshooting Chart
"
BR-5, "
NVH Troubleshooting Chart
"
Possible cause and sus-
pected parts
Fluid level
Air in hydraulic system
Outer socket ball joint swinging force
Outer socket ball joint rotating torque
Outer socket ball joint end play
Steering fluid leakage
Steering wheel play
Steering gear rack sliding force
Drive belt looseness
Improper steering wheel
Improper installation or looseness of tilt lock lever
Mounting rubber deterioration
Steering column deformation or damage
Improper installation or looseness of steering column
Steering linkage looseness
PROPELLER SHAFT
FRONT FINAL DRIVE
WHEEL HUB
SUSPENSION
TIRES
ROAD WHEEL
DRIVE SHAFT
BRAKES
SymptomNoise× × ××××× × × ××××××× ×
Shake××× × ××××× ×
Vibration××××× × ××× ×
Shimmy××× × ×××× ×
Shudder× × ×××× ×
Page 2787 of 3419
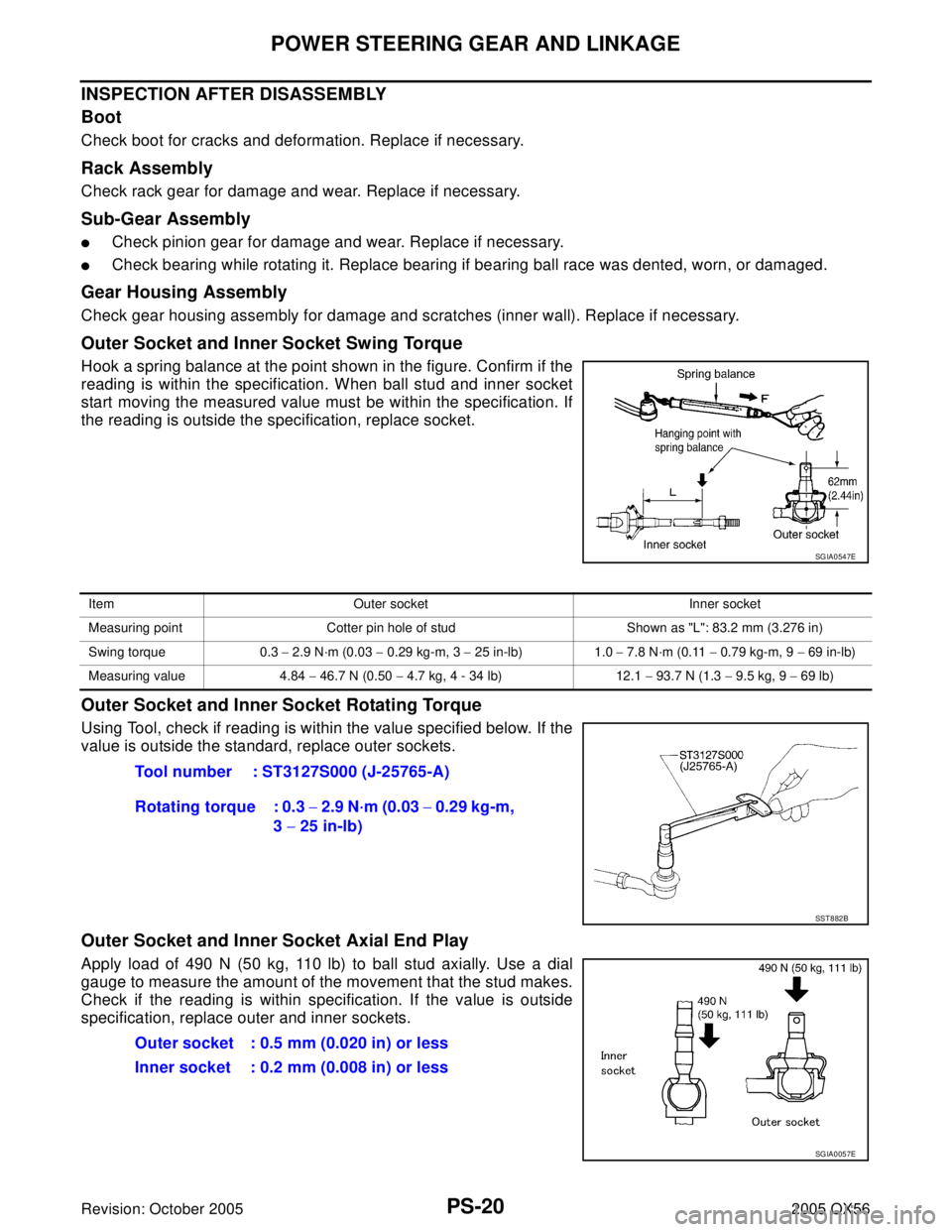
PS-20
POWER STEERING GEAR AND LINKAGE
Revision: October 20052005 QX56
INSPECTION AFTER DISASSEMBLY
Boot
Check boot for cracks and deformation. Replace if necessary.
Rack Assembly
Check rack gear for damage and wear. Replace if necessary.
Sub-Gear Assembly
Check pinion gear for damage and wear. Replace if necessary.
Check bearing while rotating it. Replace bearing if bearing ball race was dented, worn, or damaged.
Gear Housing Assembly
Check gear housing assembly for damage and scratches (inner wall). Replace if necessary.
Outer Socket and Inner Socket Swing Torque
Hook a spring balance at the point shown in the figure. Confirm if the
reading is within the specification. When ball stud and inner socket
start moving the measured value must be within the specification. If
the reading is outside the specification, replace socket.
Outer Socket and Inner Socket Rotating Torque
Using Tool, check if reading is within the value specified below. If the
value is outside the standard, replace outer sockets.
Outer Socket and Inner Socket Axial End Play
Apply load of 490 N (50 kg, 110 lb) to ball stud axially. Use a dial
gauge to measure the amount of the movement that the stud makes.
Check if the reading is within specification. If the value is outside
specification, replace outer and inner sockets.
SGIA0547E
Item Outer socket Inner socket
Measuring point Cotter pin hole of stud Shown as "L": 83.2 mm (3.276 in)
Swing torque 0.3 − 2.9 N·m (0.03 − 0.29 kg-m, 3 − 25 in-lb) 1.0 − 7.8 N·m (0.11 − 0.79 kg-m, 9 − 69 in-lb)
Measuring value 4.84 − 46.7 N (0.50 − 4.7 kg, 4 - 34 lb) 12.1 − 93.7 N (1.3 − 9.5 kg, 9 − 69 lb)
Tool number : ST3127S000 (J-25765-A)
Rotating torque : 0.3 − 2.9 N·m (0.03 − 0.29 kg-m,
3 − 25 in-lb)
SST 8 82 B
Outer socket : 0.5 mm (0.020 in) or less
Inner socket : 0.2 mm (0.008 in) or less
SGIA0057E
Page 2790 of 3419
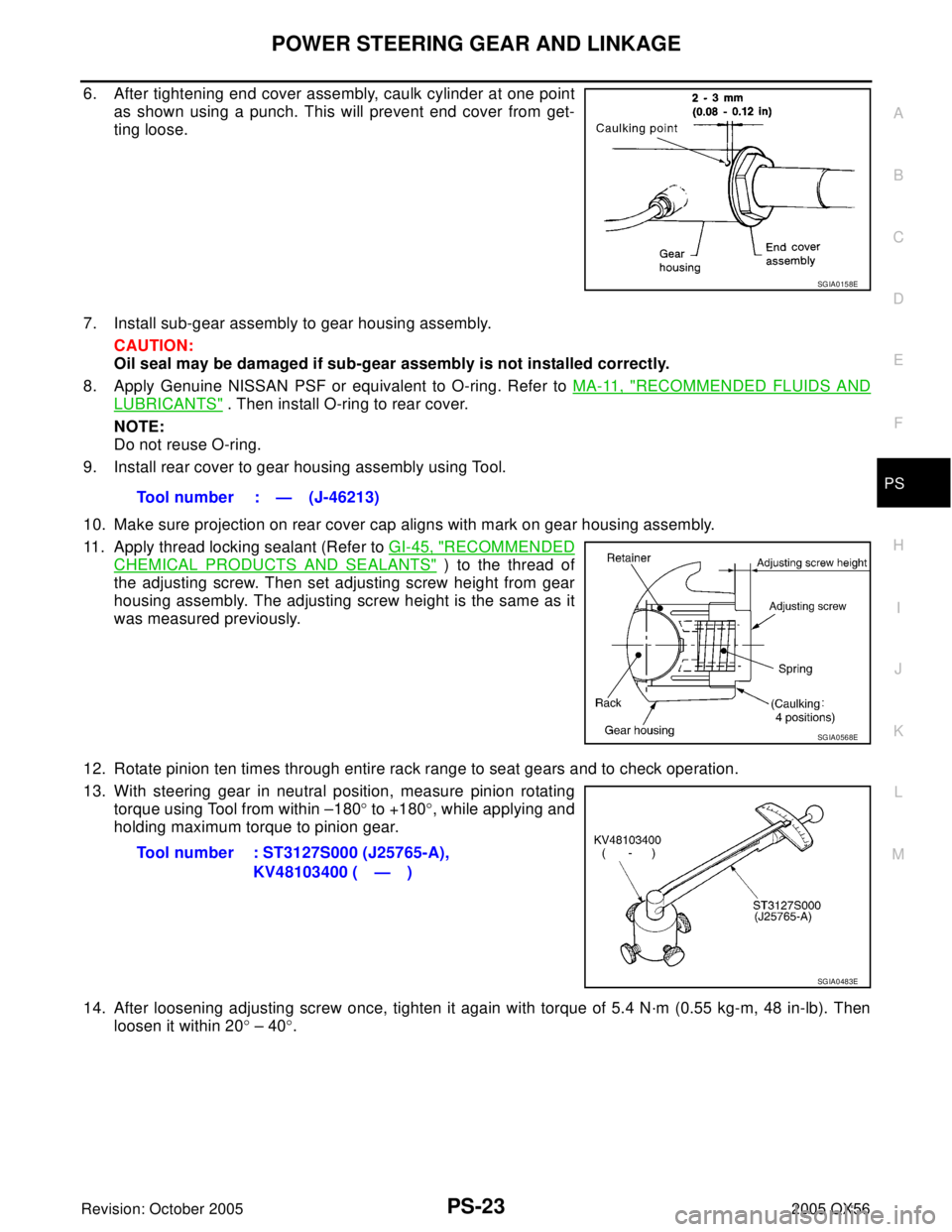
POWER STEERING GEAR AND LINKAGE
PS-23
C
D
E
F
H
I
J
K
L
MA
B
PS
Revision: October 20052005 QX56
6. After tightening end cover assembly, caulk cylinder at one point
as shown using a punch. This will prevent end cover from get-
ting loose.
7. Install sub-gear assembly to gear housing assembly.
CAUTION:
Oil seal may be damaged if sub-gear assembly is not installed correctly.
8. Apply Genuine NISSAN PSF or equivalent to O-ring. Refer to MA-11, "
RECOMMENDED FLUIDS AND
LUBRICANTS" . Then install O-ring to rear cover.
NOTE:
Do not reuse O-ring.
9. Install rear cover to gear housing assembly using Tool.
10. Make sure projection on rear cover cap aligns with mark on gear housing assembly.
11. Apply thread locking sealant (Refer to GI-45, "
RECOMMENDED
CHEMICAL PRODUCTS AND SEALANTS" ) to the thread of
the adjusting screw. Then set adjusting screw height from gear
housing assembly. The adjusting screw height is the same as it
was measured previously.
12. Rotate pinion ten times through entire rack range to seat gears and to check operation.
13. With steering gear in neutral position, measure pinion rotating
torque using Tool from within –180° to +180°, while applying and
holding maximum torque to pinion gear.
14. After loosening adjusting screw once, tighten it again with torque of 5.4 N·m (0.55 kg-m, 48 in-lb). Then
loosen it within 20° – 40°.
SGIA0158E
Tool number : — (J-46213)
SGIA0568E
Tool number : ST3127S000 (J25765-A),
KV48103400 ( — )
SGIA0483E