Ins INFINITI QX56 2004 Factory Service Manual
[x] Cancel search | Manufacturer: INFINITI, Model Year: 2004, Model line: QX56, Model: INFINITI QX56 2004Pages: 3371, PDF Size: 78.5 MB
Page 3273 of 3371
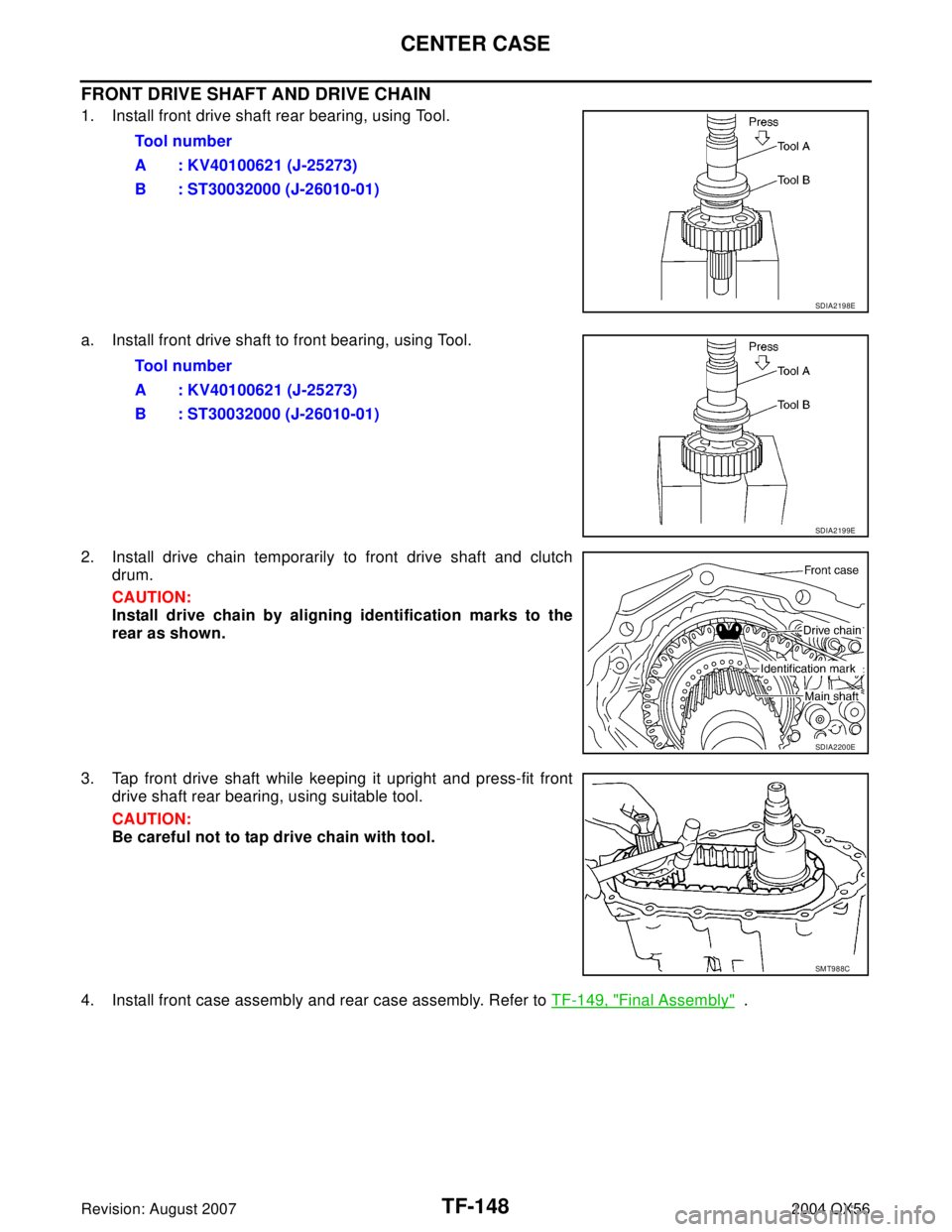
TF-148
CENTER CASE
Revision: August 20072004 QX56
FRONT DRIVE SHAFT AND DRIVE CHAIN
1. Install front drive shaft rear bearing, using Tool.
a. Install front drive shaft to front bearing, using Tool.
2. Install drive chain temporarily to front drive shaft and clutch
drum.
CAUTION:
Install drive chain by aligning identification marks to the
rear as shown.
3. Tap front drive shaft while keeping it upright and press-fit front
drive shaft rear bearing, using suitable tool.
CAUTION:
Be careful not to tap drive chain with tool.
4. Install front case assembly and rear case assembly. Refer to TF-149, "
Final Assembly" . Tool number
A : KV40100621 (J-25273)
B : ST30032000 (J-26010-01)
SDIA2198E
Tool number
A : KV40100621 (J-25273)
B : ST30032000 (J-26010-01)
SDIA2199E
SDIA2200E
SMT988C
Page 3274 of 3371
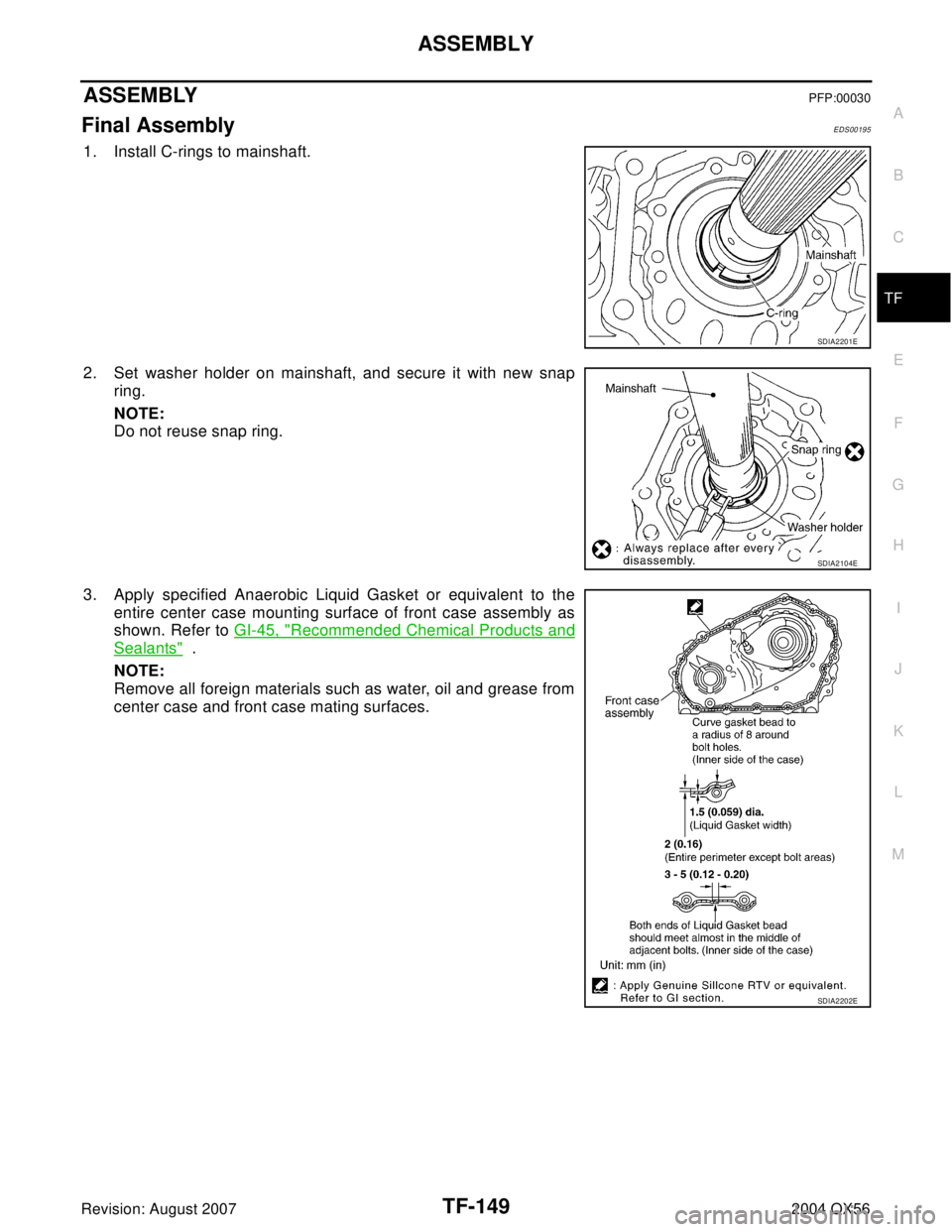
ASSEMBLY
TF-149
C
E
F
G
H
I
J
K
L
MA
B
TF
Revision: August 20072004 QX56
ASSEMBLYPFP:00030
Final AssemblyEDS00195
1. Install C-rings to mainshaft.
2. Set washer holder on mainshaft, and secure it with new snap
ring.
NOTE:
Do not reuse snap ring.
3. Apply specified Anaerobic Liquid Gasket or equivalent to the
entire center case mounting surface of front case assembly as
shown. Refer to GI-45, "
Recommended Chemical Products and
Sealants" .
NOTE:
Remove all foreign materials such as water, oil and grease from
center case and front case mating surfaces.
SDIA2201E
SDIA2104E
SDIA2202E
Page 3275 of 3371
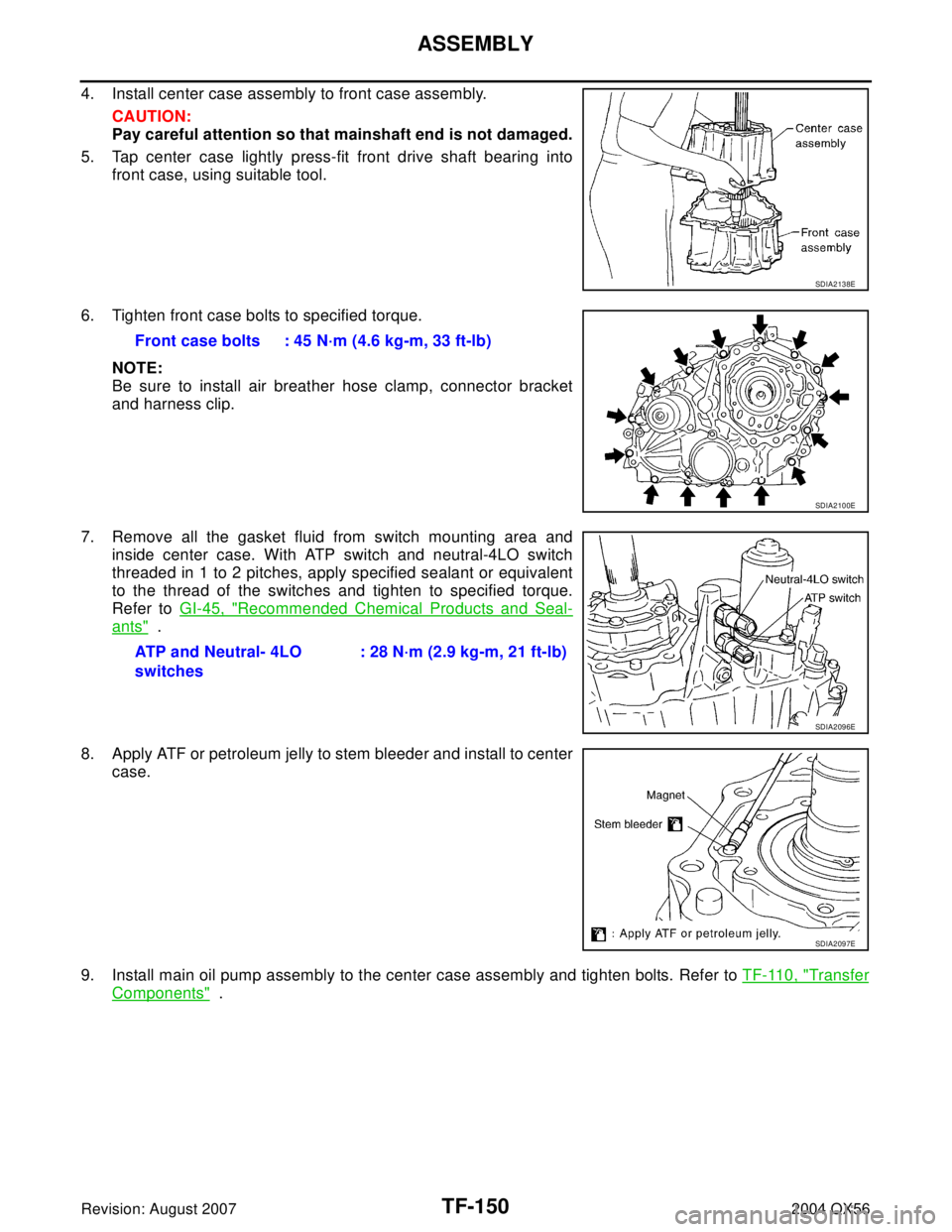
TF-150
ASSEMBLY
Revision: August 20072004 QX56
4. Install center case assembly to front case assembly.
CAUTION:
Pay careful attention so that mainshaft end is not damaged.
5. Tap center case lightly press-fit front drive shaft bearing into
front case, using suitable tool.
6. Tighten front case bolts to specified torque.
NOTE:
Be sure to install air breather hose clamp, connector bracket
and harness clip.
7. Remove all the gasket fluid from switch mounting area and
inside center case. With ATP switch and neutral-4LO switch
threaded in 1 to 2 pitches, apply specified sealant or equivalent
to the thread of the switches and tighten to specified torque.
Refer to GI-45, "
Recommended Chemical Products and Seal-
ants" .
8. Apply ATF or petroleum jelly to stem bleeder and install to center
case.
9. Install main oil pump assembly to the center case assembly and tighten bolts. Refer to TF-110, "
Transfer
Components" .
SDIA2138E
Front case bolts : 45 N·m (4.6 kg-m, 33 ft-lb)
SDIA2100E
ATP and Neutral- 4LO
switches: 28 N·m (2.9 kg-m, 21 ft-lb)
SDIA2096E
SDIA2097E
Page 3276 of 3371
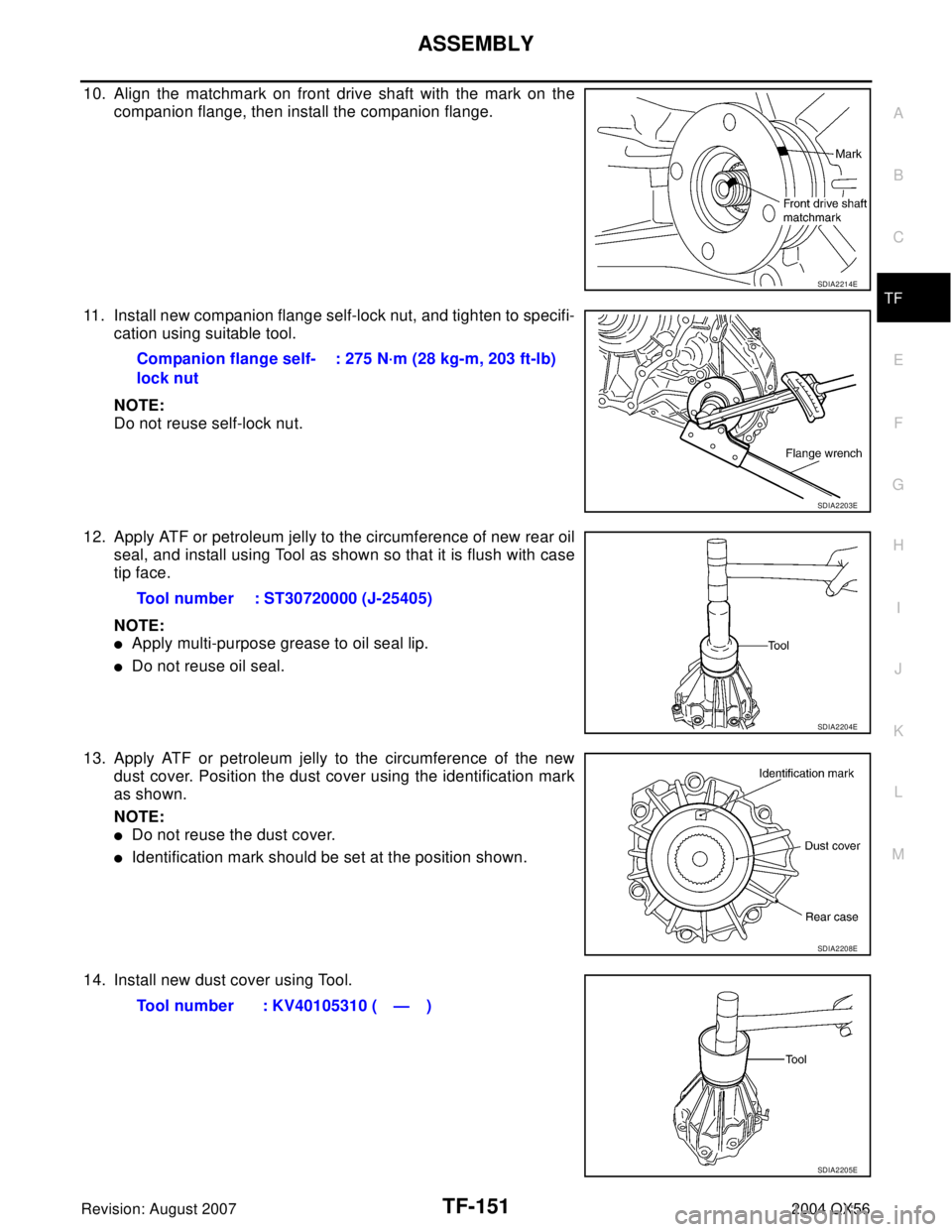
ASSEMBLY
TF-151
C
E
F
G
H
I
J
K
L
MA
B
TF
Revision: August 20072004 QX56
10. Align the matchmark on front drive shaft with the mark on the
companion flange, then install the companion flange.
11. Install new companion flange self-lock nut, and tighten to specifi-
cation using suitable tool.
NOTE:
Do not reuse self-lock nut.
12. Apply ATF or petroleum jelly to the circumference of new rear oil
seal, and install using Tool as shown so that it is flush with case
tip face.
NOTE:
Apply multi-purpose grease to oil seal lip.
Do not reuse oil seal.
13. Apply ATF or petroleum jelly to the circumference of the new
dust cover. Position the dust cover using the identification mark
as shown.
NOTE:
Do not reuse the dust cover.
Identification mark should be set at the position shown.
14. Install new dust cover using Tool.
SDIA2214E
Companion flange self-
lock nut: 275 N·m (28 kg-m, 203 ft-lb)
SDIA2203E
Tool number : ST30720000 (J-25405)
SDIA2204E
SDIA2208E
Tool number : KV40105310 ( — )
SDIA2205E
Page 3277 of 3371
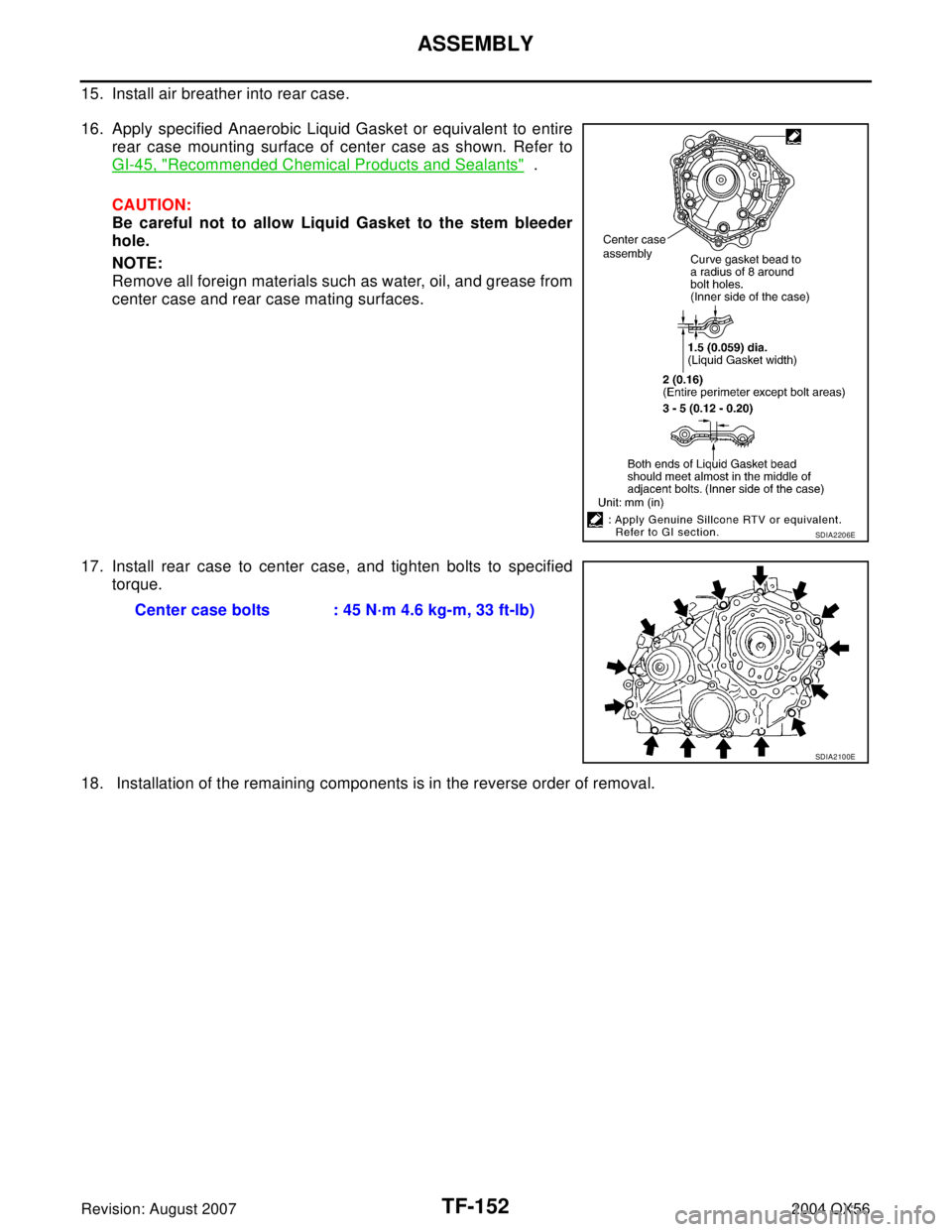
TF-152
ASSEMBLY
Revision: August 20072004 QX56
15. Install air breather into rear case.
16. Apply specified Anaerobic Liquid Gasket or equivalent to entire
rear case mounting surface of center case as shown. Refer to
GI-45, "
Recommended Chemical Products and Sealants" .
CAUTION:
Be careful not to allow Liquid Gasket to the stem bleeder
hole.
NOTE:
Remove all foreign materials such as water, oil, and grease from
center case and rear case mating surfaces.
17. Install rear case to center case, and tighten bolts to specified
torque.
18. Installation of the remaining components is in the reverse order of removal.
SDIA2206E
Center case bolts : 45 N·m 4.6 kg-m, 33 ft-lb)
SDIA2100E
Page 3278 of 3371

SERVICE DATA AND SPECIFICATIONS (SDS)
TF-153
C
E
F
G
H
I
J
K
L
MA
B
TF
Revision: August 20072004 QX56
SERVICE DATA AND SPECIFICATIONS (SDS)PFP:00030
General SpecificationsEDS0031B
Inspection and AdjustmentEDS0031C
CLEARANCE BETWEEN INNER GEAR AND OUTER GEAR
Unit: mm (in)
CLUTCH
Unit: mm (in)
PINION GEAR END PLAY
Unit: mm (in)
CLEARANCE BETWEEN SHIFT FORK AND SLEEVE
Unit: mm (in)
SELECTIVE PARTS
Sub-oil Pump
Unit: mm (in)
*: Always check with the Parts Department for the latest parts information.
Main Oil Pump
Unit: mm (in) Applied modelVK56DE
Transfer modelATX14B
Fluid capacity (Approx.)
(US qt, lmp qt)3.0 (3-1/8, 2-5/8)
Gear ratioHigh 1.000
Low 2.596
Number of teethPlanetary
gearSun gear 57
Internal gear 91
Front drive sprocket 38
Front drive shaft 38
Item Specification
Sub-oil pump 0.015 - 0.035 (0.0006 - 0.0014)
Main oil pump 0.015 - 0.035 (0.0006 - 0.0014)
Item Limit value
Drive plate1.4 (0.055)
Item Standard
Pinion gear end play 0.1 - 0.7 (0.004 - 0.028)
Item Standard
Shift fork and sleeve Less than 0.36 (0.0142)
Gear thicknessPart number*
Inner gear Outer gear
9.27 - 9.28 (0.3650 - 0.3654) 31346 0W462 31347 0W462
9.28 - 9.29 (0.3654 - 0.3657) 31346 0W461 31347 0W461
9.29 - 9.30 (0.3657 - 0.3661) 31346 0W460 31347 0W460
Gear thicknessPart number*
Inner gear Outer gear
8.27 - 8.28 (0.3256 - 0.3260) 31346 7S112 31347 7S112
8.28 - 8.29 (0.3260 - 0.3264) 31346 7S111 31347 7S111
8.29 - 8.30 (0.3264 - 0.3268) 31346 7S110 31347 7S110
Page 3280 of 3371
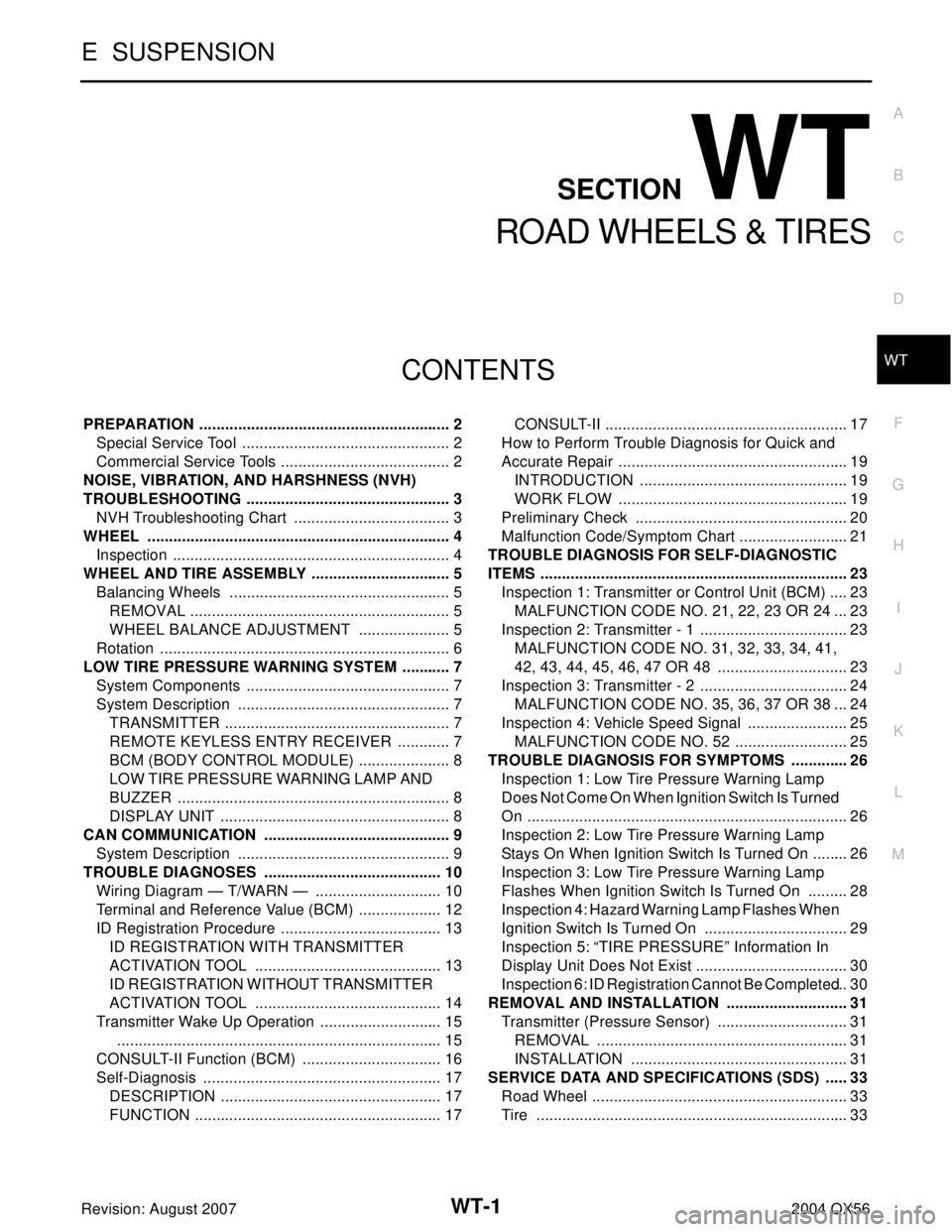
WT-1
ROAD WHEELS & TIRES
E SUSPENSION
CONTENTS
C
D
F
G
H
I
J
K
L
M
SECTION WT
A
B
WT
Revision: August 20072004 QX56 PREPARATION ........................................................... 2
Special Service Tool ................................................. 2
Commercial Service Tools ........................................ 2
NOISE, VIBRATION, AND HARSHNESS (NVH)
TROUBLESHOOTING ................................................ 3
NVH Troubleshooting Chart ..................................... 3
WHEEL ....................................................................... 4
Inspection ................................................................. 4
WHEEL AND TIRE ASSEMBLY ................................. 5
Balancing Wheels .................................................... 5
REMOVAL ............................................................. 5
WHEEL BALANCE ADJUSTMENT ...................... 5
Rotation .................................................................... 6
LOW TIRE PRESSURE WARNING SYSTEM ............ 7
System Components ................................................ 7
System Description .................................................. 7
TRANSMITTER ..................................................... 7
REMOTE KEYLESS ENTRY RECEIVER ............. 7
BCM (BODY CONTROL MODULE) ...................... 8
LOW TIRE PRESSURE WARNING LAMP AND
BUZZER ................................................................ 8
DISPLAY UNIT ...................................................... 8
CAN COMMUNICATION ............................................ 9
System Description .................................................. 9
TROUBLE DIAGNOSES .......................................... 10
Wiring Diagram — T/WARN — .............................. 10
Terminal and Reference Value (BCM) .................... 12
ID Registration Procedure ...................................... 13
ID REGISTRATION WITH TRANSMITTER
ACTIVATION TOOL ............................................ 13
ID REGISTRATION WITHOUT TRANSMITTER
ACTIVATION TOOL ............................................ 14
Transmitter Wake Up Operation ............................. 15
............................................................................ 15
CONSULT-II Function (BCM) ................................. 16
Self-Diagnosis ........................................................ 17
DESCRIPTION .................................................... 17
FUNCTION .......................................................... 17CONSULT-II ......................................................... 17
How to Perform Trouble Diagnosis for Quick and
Accurate Repair ...................................................... 19
INTRODUCTION ................................................. 19
WORK FLOW ...................................................... 19
Preliminary Check .................................................. 20
Malfunction Code/Symptom Chart .......................... 21
TROUBLE DIAGNOSIS FOR SELF-DIAGNOSTIC
ITEMS ........................................................................ 23
Inspection 1: Transmitter or Control Unit (BCM) ..... 23
MALFUNCTION CODE NO. 21, 22, 23 OR 24 ... 23
Inspection 2: Transmitter - 1 ................................... 23
MALFUNCTION CODE NO. 31, 32, 33, 34, 41,
42, 43, 44, 45, 46, 47 OR 48 ............................... 23
Inspection 3: Transmitter - 2 ................................... 24
MALFUNCTION CODE NO. 35, 36, 37 OR 38 ... 24
Inspection 4: Vehicle Speed Signal ........................ 25
MALFUNCTION CODE NO. 52 ........................... 25
TROUBLE DIAGNOSIS FOR SYMPTOMS .............. 26
Inspection 1: Low Tire Pressure Warning Lamp
Does Not Come On When Ignition Switch Is Turned
On ........................................................................... 26
Inspection 2: Low Tire Pressure Warning Lamp
Stays On When Ignition Switch Is Turned On ......... 26
Inspection 3: Low Tire Pressure Warning Lamp
Flashes When Ignition Switch Is Turned On .......... 28
Inspection 4: Hazard Warning Lamp Flashes When
Ignition Switch Is Turned On .................................. 29
Inspection 5: “TIRE PRESSURE” Information In
Display Unit Does Not Exist .................................... 30
Inspection 6: ID Registration Cannot Be Completed ... 30
REMOVAL AND INSTALLATION ............................. 31
Transmitter (Pressure Sensor) ............................... 31
REMOVAL ........................................................... 31
INSTALLATION ................................................... 31
SERVICE DATA AND SPECIFICATIONS (SDS) ...... 33
Road Wheel ............................................................ 33
Tire ......................................................................... 33
Page 3283 of 3371
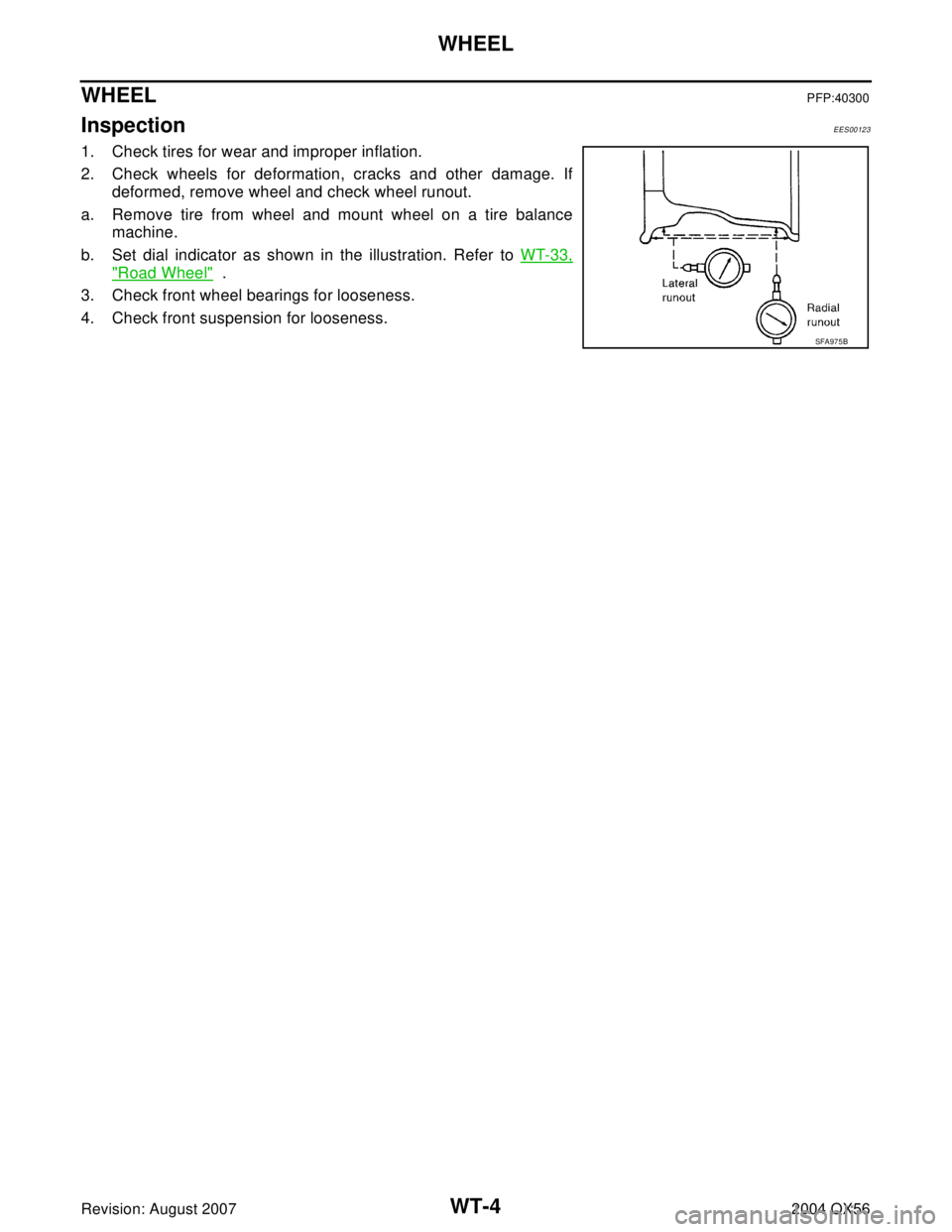
WT-4
WHEEL
Revision: August 20072004 QX56
WHEELPFP:40300
InspectionEES00123
1. Check tires for wear and improper inflation.
2. Check wheels for deformation, cracks and other damage. If
deformed, remove wheel and check wheel runout.
a. Remove tire from wheel and mount wheel on a tire balance
machine.
b. Set dial indicator as shown in the illustration. Refer to WT-33,
"Road Wheel" .
3. Check front wheel bearings for looseness.
4. Check front suspension for looseness.
SFA975B
Page 3284 of 3371
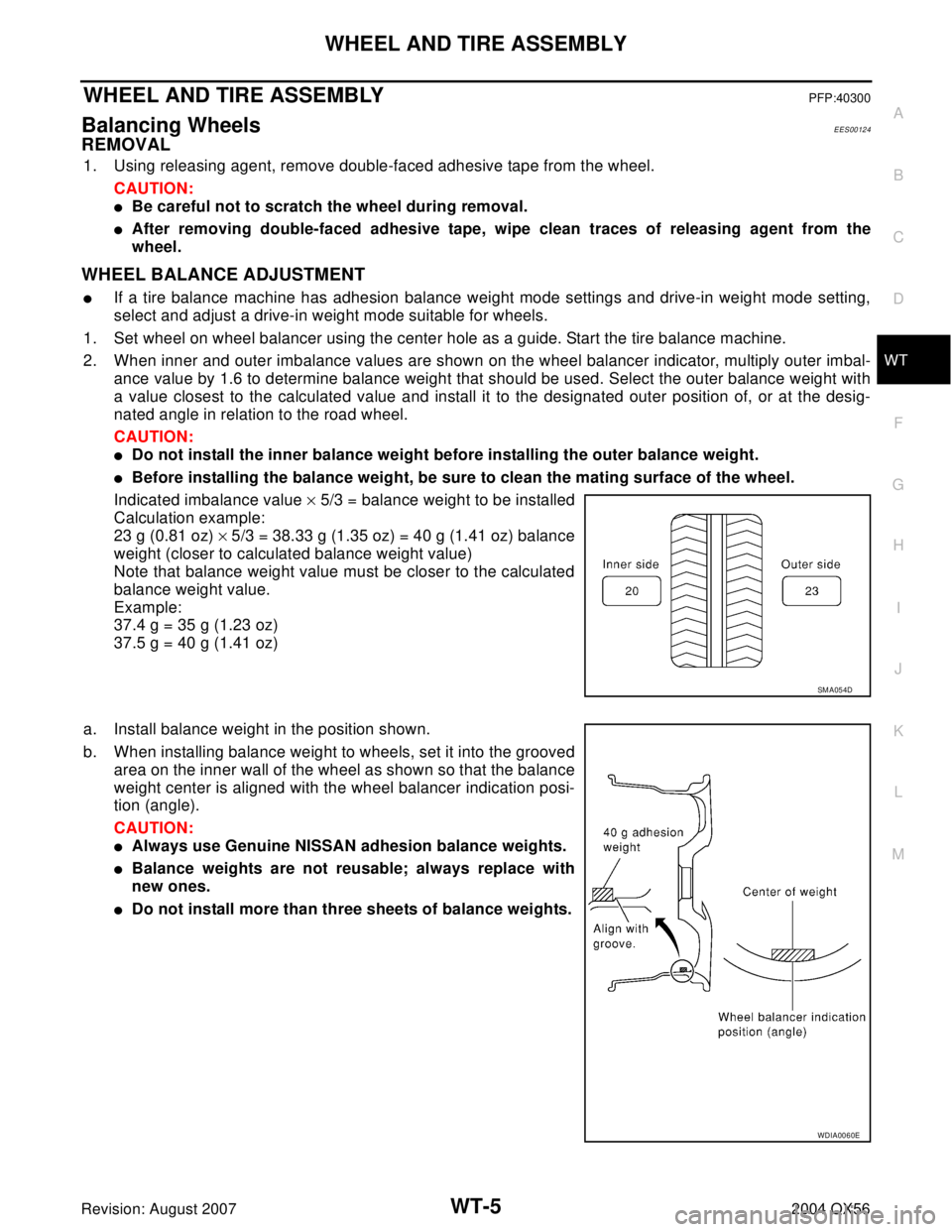
WHEEL AND TIRE ASSEMBLY
WT-5
C
D
F
G
H
I
J
K
L
MA
B
WT
Revision: August 20072004 QX56
WHEEL AND TIRE ASSEMBLYPFP:40300
Balancing WheelsEES00124
REMOVAL
1. Using releasing agent, remove double-faced adhesive tape from the wheel.
CAUTION:
Be careful not to scratch the wheel during removal.
After removing double-faced adhesive tape, wipe clean traces of releasing agent from the
wheel.
WHEEL BALANCE ADJUSTMENT
If a tire balance machine has adhesion balance weight mode settings and drive-in weight mode setting,
select and adjust a drive-in weight mode suitable for wheels.
1. Set wheel on wheel balancer using the center hole as a guide. Start the tire balance machine.
2. When inner and outer imbalance values are shown on the wheel balancer indicator, multiply outer imbal-
ance value by 1.6 to determine balance weight that should be used. Select the outer balance weight with
a value closest to the calculated value and install it to the designated outer position of, or at the desig-
nated angle in relation to the road wheel.
CAUTION:
Do not install the inner balance weight before installing the outer balance weight.
Before installing the balance weight, be sure to clean the mating surface of the wheel.
Indicated imbalance value × 5/3 = balance weight to be installed
Calculation example:
23 g (0.81 oz) × 5/3 = 38.33 g (1.35 oz) = 40 g (1.41 oz) balance
weight (closer to calculated balance weight value)
Note that balance weight value must be closer to the calculated
balance weight value.
Example:
37.4 g = 35 g (1.23 oz)
37.5 g = 40 g (1.41 oz)
a. Install balance weight in the position shown.
b. When installing balance weight to wheels, set it into the grooved
area on the inner wall of the wheel as shown so that the balance
weight center is aligned with the wheel balancer indication posi-
tion (angle).
CAUTION:
Always use Genuine NISSAN adhesion balance weights.
Balance weights are not reusable; always replace with
new ones.
Do not install more than three sheets of balance weights.
SM A05 4D
WDIA0060E
Page 3285 of 3371
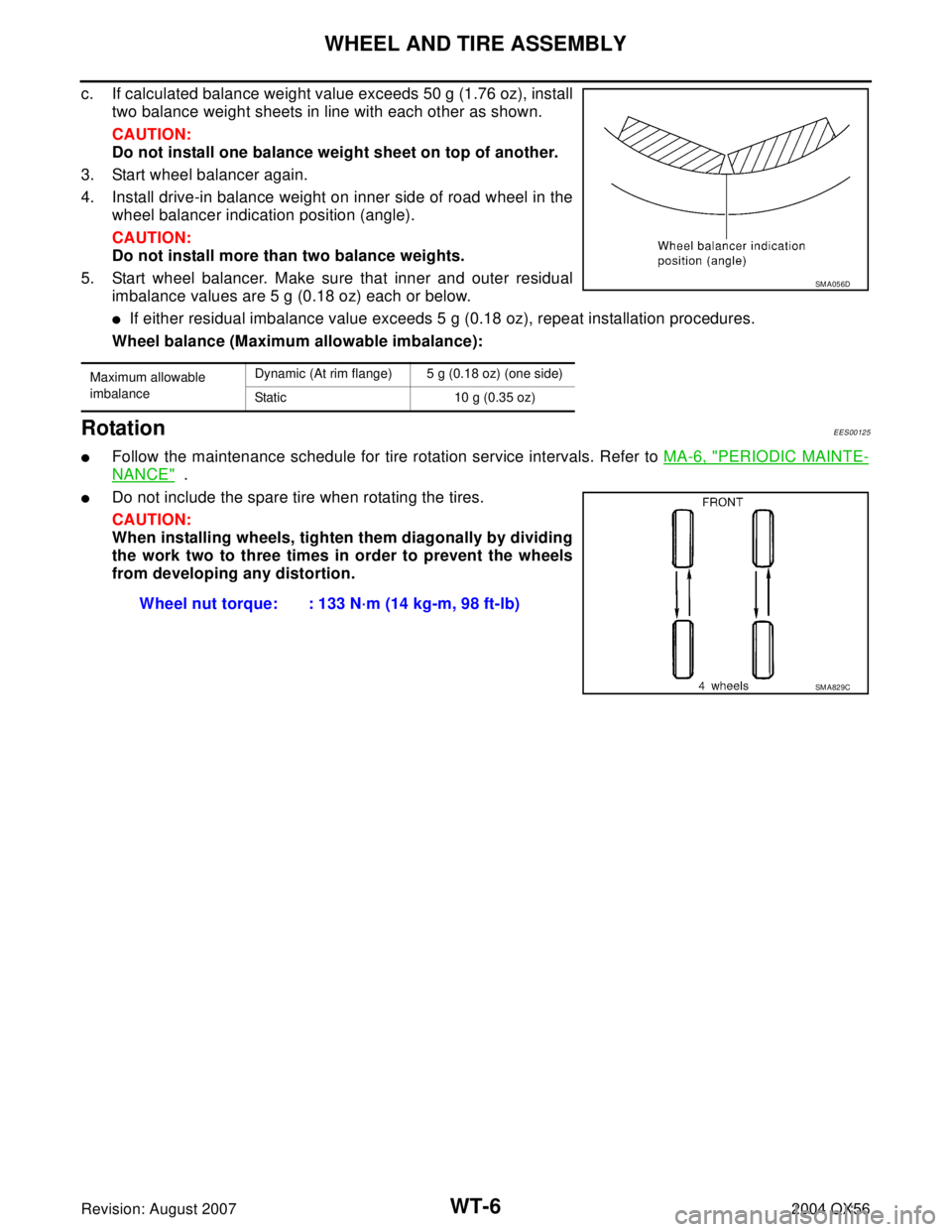
WT-6
WHEEL AND TIRE ASSEMBLY
Revision: August 20072004 QX56
c. If calculated balance weight value exceeds 50 g (1.76 oz), install
two balance weight sheets in line with each other as shown.
CAUTION:
Do not install one balance weight sheet on top of another.
3. Start wheel balancer again.
4. Install drive-in balance weight on inner side of road wheel in the
wheel balancer indication position (angle).
CAUTION:
Do not install more than two balance weights.
5. Start wheel balancer. Make sure that inner and outer residual
imbalance values are 5 g (0.18 oz) each or below.
If either residual imbalance value exceeds 5 g (0.18 oz), repeat installation procedures.
Wheel balance (Maximum allowable imbalance):
RotationEES00125
Follow the maintenance schedule for tire rotation service intervals. Refer to MA-6, "PERIODIC MAINTE-
NANCE" .
Do not include the spare tire when rotating the tires.
CAUTION:
When installing wheels, tighten them diagonally by dividing
the work two to three times in order to prevent the wheels
from developing any distortion.
Maximum allowable
imbalanceDynamic (At rim flange) 5 g (0.18 oz) (one side)
Static 10 g (0.35 oz)
SM A05 6D
Wheel nut torque: : 133 N·m (14 kg-m, 98 ft-lb)
SM A82 9C