length INFINITI QX56 2004 Factory Owner's Guide
[x] Cancel search | Manufacturer: INFINITI, Model Year: 2004, Model line: QX56, Model: INFINITI QX56 2004Pages: 3371, PDF Size: 78.5 MB
Page 2776 of 3371
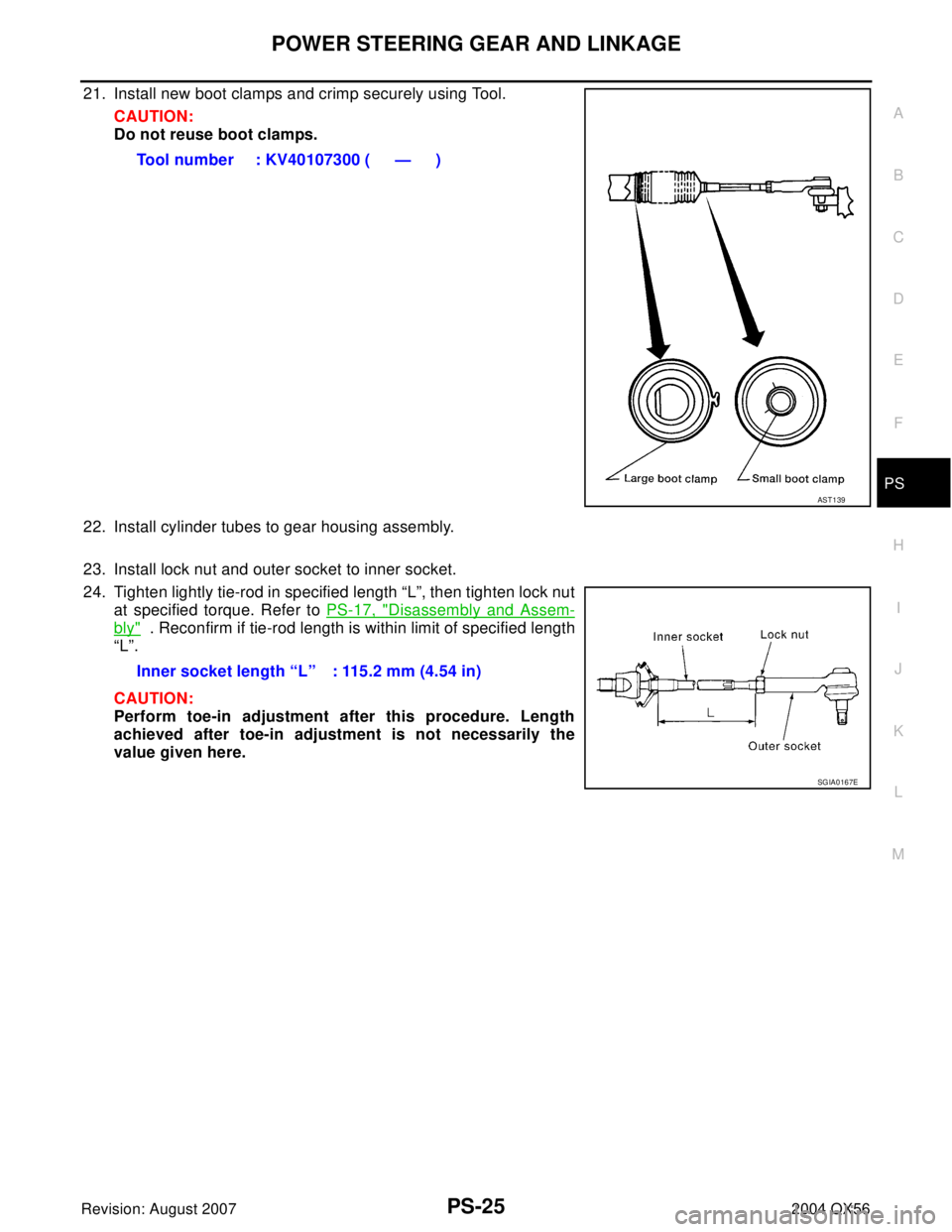
POWER STEERING GEAR AND LINKAGE
PS-25
C
D
E
F
H
I
J
K
L
MA
B
PS
Revision: August 20072004 QX56
21. Install new boot clamps and crimp securely using Tool.
CAUTION:
Do not reuse boot clamps.
22. Install cylinder tubes to gear housing assembly.
23. Install lock nut and outer socket to inner socket.
24. Tighten lightly tie-rod in specified length “L”, then tighten lock nut
at specified torque. Refer to PS-17, "
Disassembly and Assem-
bly" . Reconfirm if tie-rod length is within limit of specified length
“L”.
CAUTION:
Perform toe-in adjustment after this procedure. Length
achieved after toe-in adjustment is not necessarily the
value given here.Tool number : KV40107300 ( — )
AST 1 39
Inner socket length “L” : 115.2 mm (4.54 in)
SGIA0167E
Page 2784 of 3371
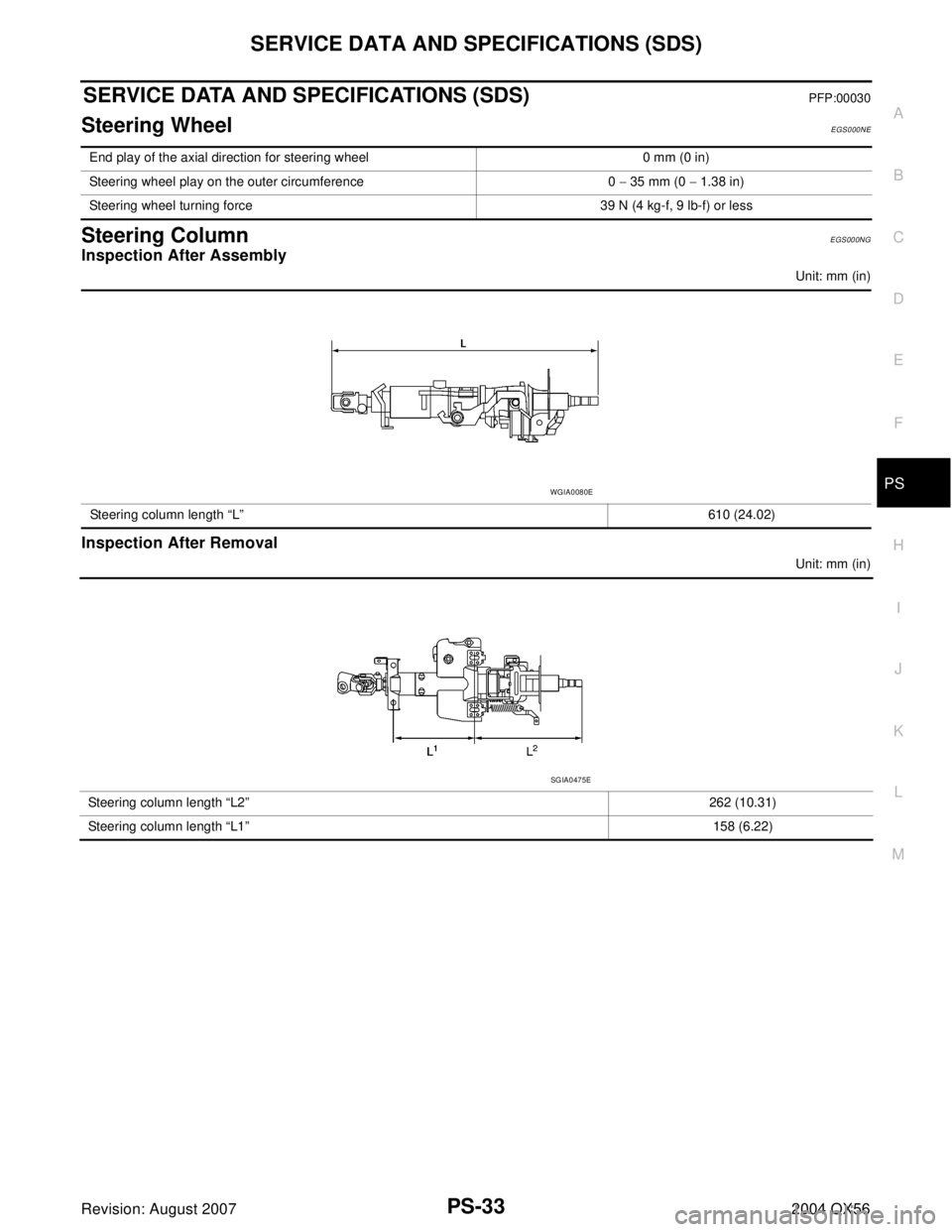
SERVICE DATA AND SPECIFICATIONS (SDS)
PS-33
C
D
E
F
H
I
J
K
L
MA
B
PS
Revision: August 20072004 QX56
SERVICE DATA AND SPECIFICATIONS (SDS)PFP:00030
Steering WheelEGS000NE
Steering ColumnEGS000NG
Inspection After Assembly
Unit: mm (in)
Inspection After Removal
Unit: mm (in) End play of the axial direction for steering wheel 0 mm (0 in)
Steering wheel play on the outer circumference 0 − 35 mm (0 − 1.38 in)
Steering wheel turning force 39 N (4 kg-f, 9 lb-f) or less
Steering column length “L”610 (24.02)
WGIA0080E
Steering column length “L2”262 (10.31)
Steering column length “L1” 158 (6.22)
SGIA0475E
Page 2785 of 3371
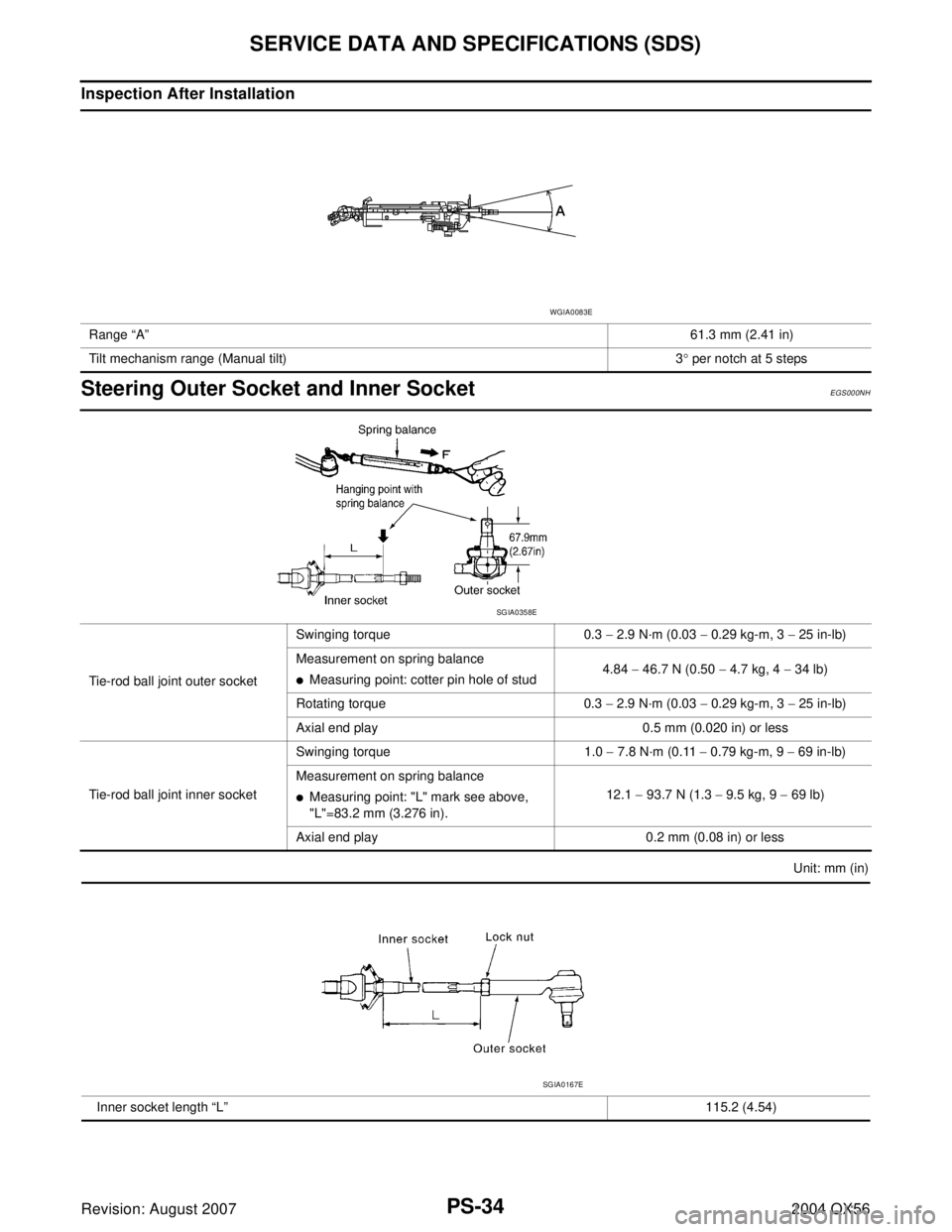
PS-34
SERVICE DATA AND SPECIFICATIONS (SDS)
Revision: August 20072004 QX56
Inspection After Installation
Steering Outer Socket and Inner SocketEGS000NH
Unit: mm (in) Range “A”61.3 mm (2.41 in)
Tilt mechanism range (Manual tilt) 3° per notch at 5 steps
WGIA0083E
Tie-rod ball joint outer socketSwinging torque 0.3 − 2.9 N·m (0.03 − 0.29 kg-m, 3 − 25 in-lb)
Measurement on spring balanceMeasuring point: cotter pin hole of stud4.84 − 46.7 N (0.50 − 4.7 kg, 4 − 34 lb)
Rotating torque 0.3 − 2.9 N·m (0.03 − 0.29 kg-m, 3 − 25 in-lb)
Axial end play 0.5 mm (0.020 in) or less
Tie-rod ball joint inner socketSwinging torque 1.0 − 7.8 N·m (0.11 − 0.79 kg-m, 9 − 69 in-lb)
Measurement on spring balance
Measuring point: "L" mark see above,
"L"=83.2 mm (3.276 in).12.1 − 93.7 N (1.3 − 9.5 kg, 9 − 69 lb)
Axial end play 0.2 mm (0.08 in) or less
SGIA0358E
Inner socket length “L” 115.2 (4.54)
SGIA0167E
Page 2798 of 3371
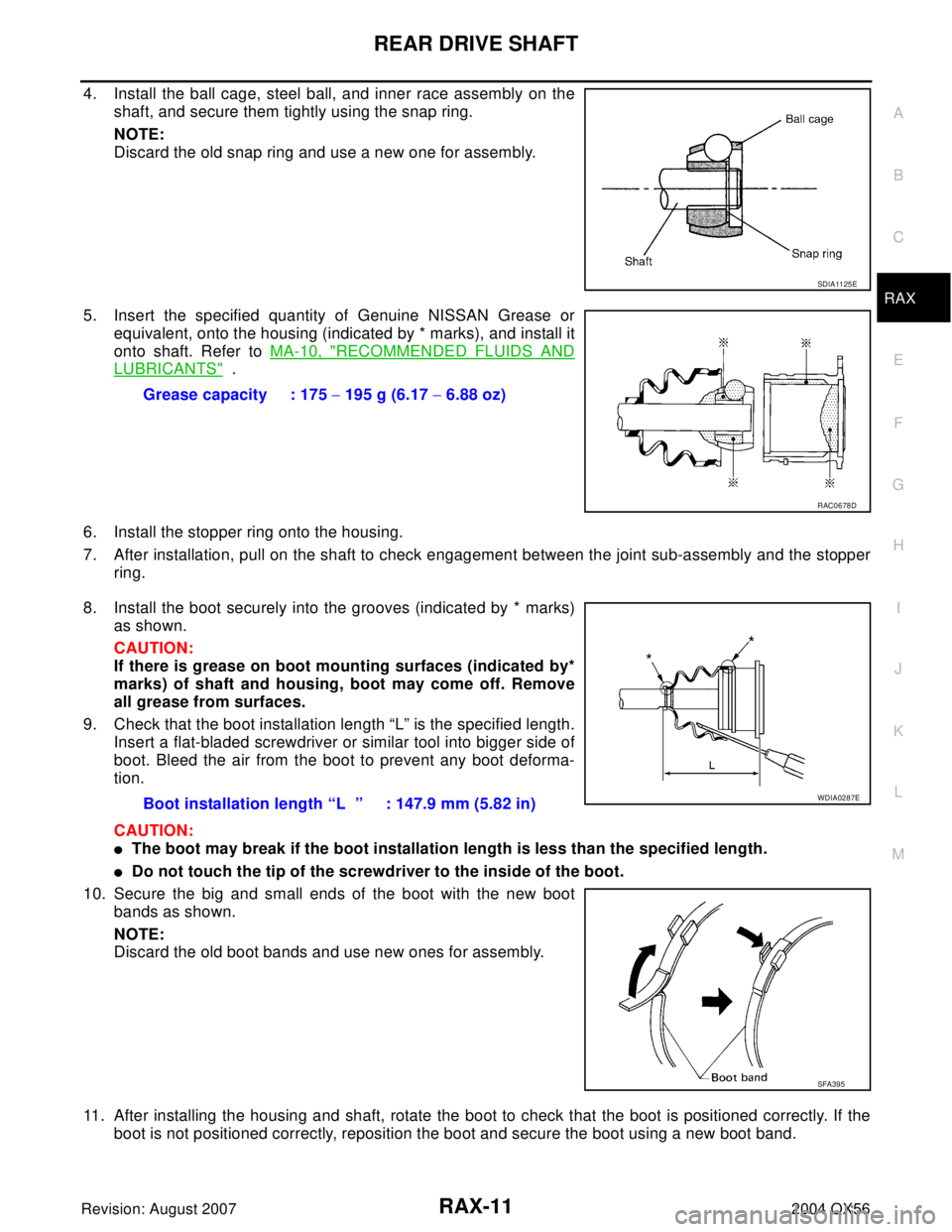
REAR DRIVE SHAFT
RAX-11
C
E
F
G
H
I
J
K
L
MA
B
RAX
Revision: August 20072004 QX56
4. Install the ball cage, steel ball, and inner race assembly on the
shaft, and secure them tightly using the snap ring.
NOTE:
Discard the old snap ring and use a new one for assembly.
5. Insert the specified quantity of Genuine NISSAN Grease or
equivalent, onto the housing (indicated by * marks), and install it
onto shaft. Refer to MA-10, "
RECOMMENDED FLUIDS AND
LUBRICANTS" .
6. Install the stopper ring onto the housing.
7. After installation, pull on the shaft to check engagement between the joint sub-assembly and the stopper
ring.
8. Install the boot securely into the grooves (indicated by * marks)
as shown.
CAUTION:
If there is grease on boot mounting surfaces (indicated by*
marks) of shaft and housing, boot may come off. Remove
all grease from surfaces.
9. Check that the boot installation length “L” is the specified length.
Insert a flat-bladed screwdriver or similar tool into bigger side of
boot. Bleed the air from the boot to prevent any boot deforma-
tion.
CAUTION:
The boot may break if the boot installation length is less than the specified length.
Do not touch the tip of the screwdriver to the inside of the boot.
10. Secure the big and small ends of the boot with the new boot
bands as shown.
NOTE:
Discard the old boot bands and use new ones for assembly.
11. After installing the housing and shaft, rotate the boot to check that the boot is positioned correctly. If the
boot is not positioned correctly, reposition the boot and secure the boot using a new boot band.
SDIA11 25 E
Grease capacity : 175 − 195 g (6.17 − 6.88 oz)
RAC0678D
Boot installation length “L ” : 147.9 mm (5.82 in)WDIA0287E
SFA39 5
Page 2799 of 3371
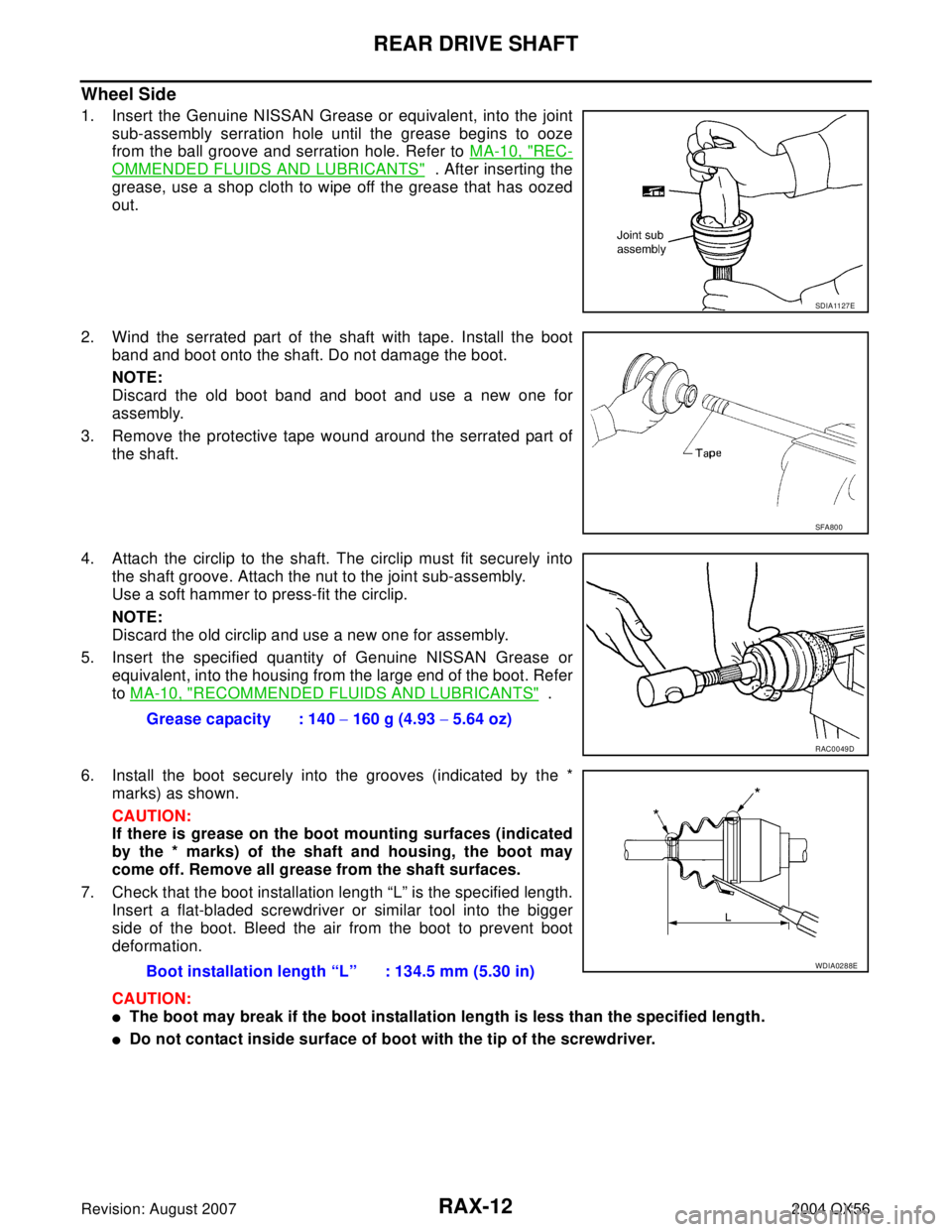
RAX-12
REAR DRIVE SHAFT
Revision: August 20072004 QX56
Wheel Side
1. Insert the Genuine NISSAN Grease or equivalent, into the joint
sub-assembly serration hole until the grease begins to ooze
from the ball groove and serration hole. Refer to MA-10, "
REC-
OMMENDED FLUIDS AND LUBRICANTS" . After inserting the
grease, use a shop cloth to wipe off the grease that has oozed
out.
2. Wind the serrated part of the shaft with tape. Install the boot
band and boot onto the shaft. Do not damage the boot.
NOTE:
Discard the old boot band and boot and use a new one for
assembly.
3. Remove the protective tape wound around the serrated part of
the shaft.
4. Attach the circlip to the shaft. The circlip must fit securely into
the shaft groove. Attach the nut to the joint sub-assembly.
Use a soft hammer to press-fit the circlip.
NOTE:
Discard the old circlip and use a new one for assembly.
5. Insert the specified quantity of Genuine NISSAN Grease or
equivalent, into the housing from the large end of the boot. Refer
to MA-10, "
RECOMMENDED FLUIDS AND LUBRICANTS" .
6. Install the boot securely into the grooves (indicated by the *
marks) as shown.
CAUTION:
If there is grease on the boot mounting surfaces (indicated
by the * marks) of the shaft and housing, the boot may
come off. Remove all grease from the shaft surfaces.
7. Check that the boot installation length “L” is the specified length.
Insert a flat-bladed screwdriver or similar tool into the bigger
side of the boot. Bleed the air from the boot to prevent boot
deformation.
CAUTION:
The boot may break if the boot installation length is less than the specified length.
Do not contact inside surface of boot with the tip of the screwdriver.
SDIA11 27 E
SFA80 0
Grease capacity : 140 − 160 g (4.93 − 5.64 oz)
RAC0049D
Boot installation length “L” : 134.5 mm (5.30 in)WDIA0288E
Page 2801 of 3371
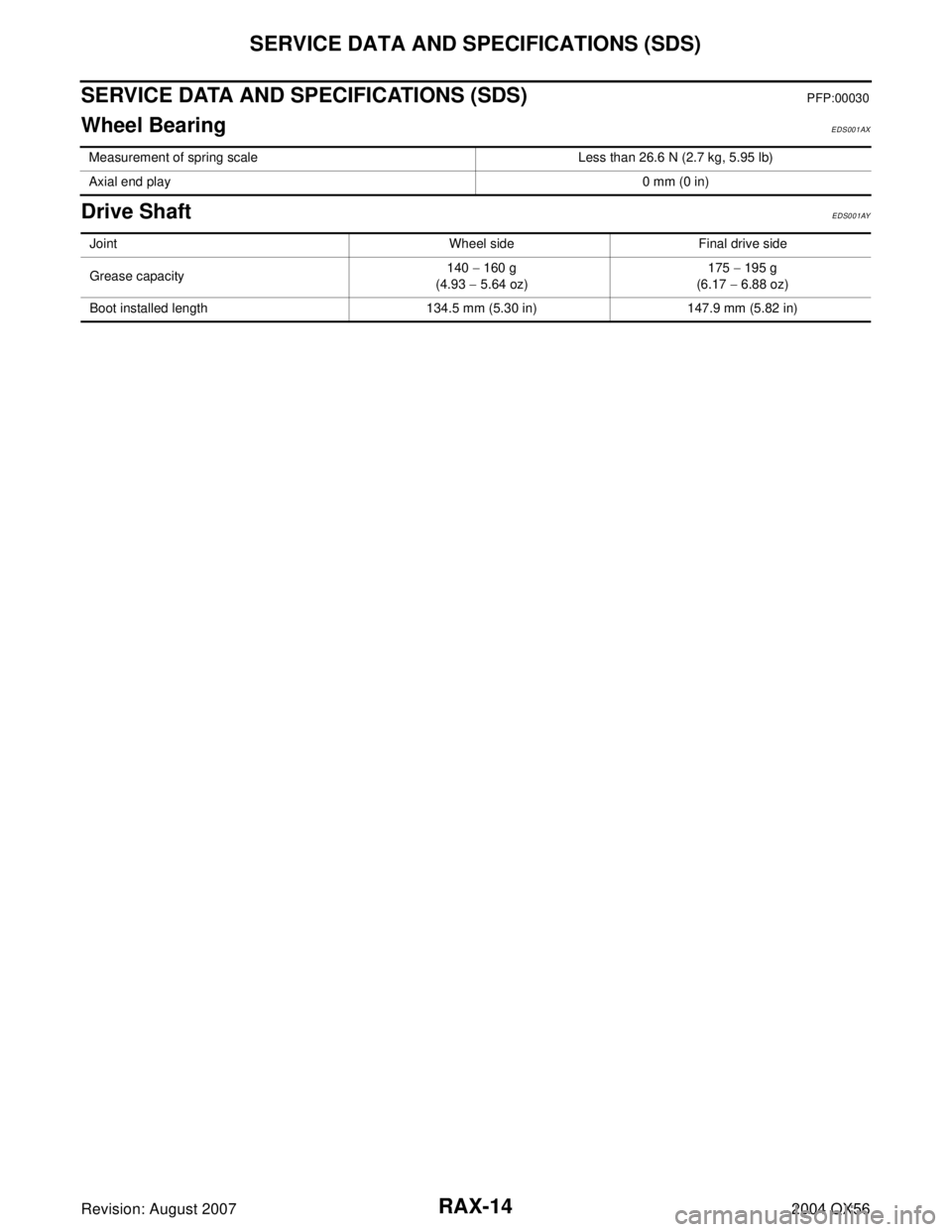
RAX-14
SERVICE DATA AND SPECIFICATIONS (SDS)
Revision: August 20072004 QX56
SERVICE DATA AND SPECIFICATIONS (SDS)PFP:00030
Wheel BearingEDS001AX
Drive ShaftEDS001AY
Measurement of spring scale Less than 26.6 N (2.7 kg, 5.95 lb)
Axial end play0 mm (0 in)
Joint Wheel side Final drive side
Grease capacity140 − 160 g
(4.93 − 5.64 oz)175 − 195 g
(6.17 − 6.88 oz)
Boot installed length 134.5 mm (5.30 in) 147.9 mm (5.82 in)
Page 2917 of 3371
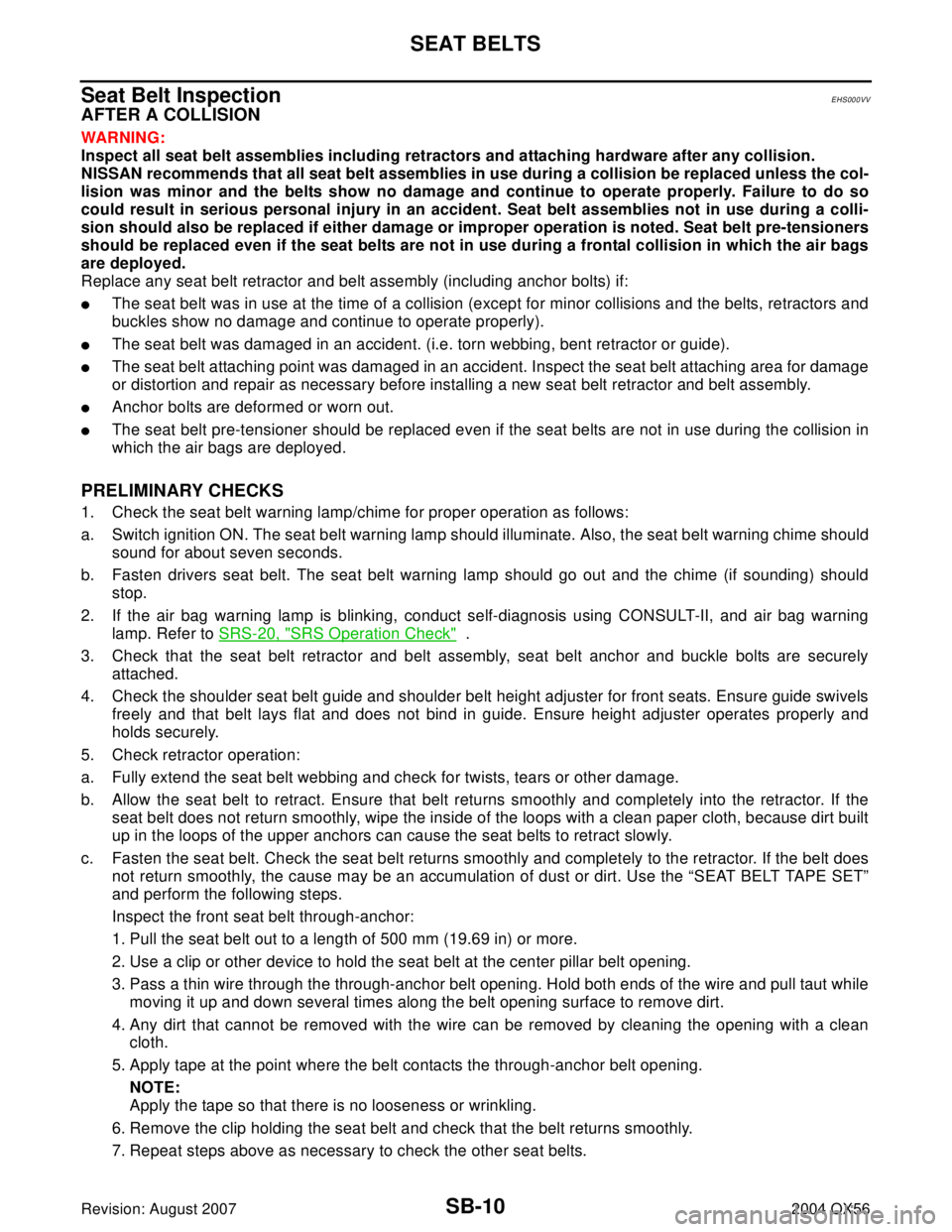
SB-10
SEAT BELTS
Revision: August 20072004 QX56
Seat Belt InspectionEHS000VV
AFTER A COLLISION
WAR NIN G:
Inspect all seat belt assemblies including retractors and attaching hardware after any collision.
NISSAN recommends that all seat belt assemblies in use during a collision be replaced unless the col-
lision was minor and the belts show no damage and continue to operate properly. Failure to do so
could result in serious personal injury in an accident. Seat belt assemblies not in use during a colli-
sion should also be replaced if either damage or improper operation is noted. Seat belt pre-tensioners
should be replaced even if the seat belts are not in use during a frontal collision in which the air bags
are deployed.
Replace any seat belt retractor and belt assembly (including anchor bolts) if:
The seat belt was in use at the time of a collision (except for minor collisions and the belts, retractors and
buckles show no damage and continue to operate properly).
The seat belt was damaged in an accident. (i.e. torn webbing, bent retractor or guide).
The seat belt attaching point was damaged in an accident. Inspect the seat belt attaching area for damage
or distortion and repair as necessary before installing a new seat belt retractor and belt assembly.
Anchor bolts are deformed or worn out.
The seat belt pre-tensioner should be replaced even if the seat belts are not in use during the collision in
which the air bags are deployed.
PRELIMINARY CHECKS
1. Check the seat belt warning lamp/chime for proper operation as follows:
a. Switch ignition ON. The seat belt warning lamp should illuminate. Also, the seat belt warning chime should
sound for about seven seconds.
b. Fasten drivers seat belt. The seat belt warning lamp should go out and the chime (if sounding) should
stop.
2. If the air bag warning lamp is blinking, conduct self-diagnosis using CONSULT-II, and air bag warning
lamp. Refer to SRS-20, "
SRS Operation Check" .
3. Check that the seat belt retractor and belt assembly, seat belt anchor and buckle bolts are securely
attached.
4. Check the shoulder seat belt guide and shoulder belt height adjuster for front seats. Ensure guide swivels
freely and that belt lays flat and does not bind in guide. Ensure height adjuster operates properly and
holds securely.
5. Check retractor operation:
a. Fully extend the seat belt webbing and check for twists, tears or other damage.
b. Allow the seat belt to retract. Ensure that belt returns smoothly and completely into the retractor. If the
seat belt does not return smoothly, wipe the inside of the loops with a clean paper cloth, because dirt built
up in the loops of the upper anchors can cause the seat belts to retract slowly.
c. Fasten the seat belt. Check the seat belt returns smoothly and completely to the retractor. If the belt does
not return smoothly, the cause may be an accumulation of dust or dirt. Use the “SEAT BELT TAPE SET”
and perform the following steps.
Inspect the front seat belt through-anchor:
1. Pull the seat belt out to a length of 500 mm (19.69 in) or more.
2. Use a clip or other device to hold the seat belt at the center pillar belt opening.
3. Pass a thin wire through the through-anchor belt opening. Hold both ends of the wire and pull taut while
moving it up and down several times along the belt opening surface to remove dirt.
4. Any dirt that cannot be removed with the wire can be removed by cleaning the opening with a clean
cloth.
5. Apply tape at the point where the belt contacts the through-anchor belt opening.
NOTE:
Apply the tape so that there is no looseness or wrinkling.
6. Remove the clip holding the seat belt and check that the belt returns smoothly.
7. Repeat steps above as necessary to check the other seat belts.
Page 2918 of 3371
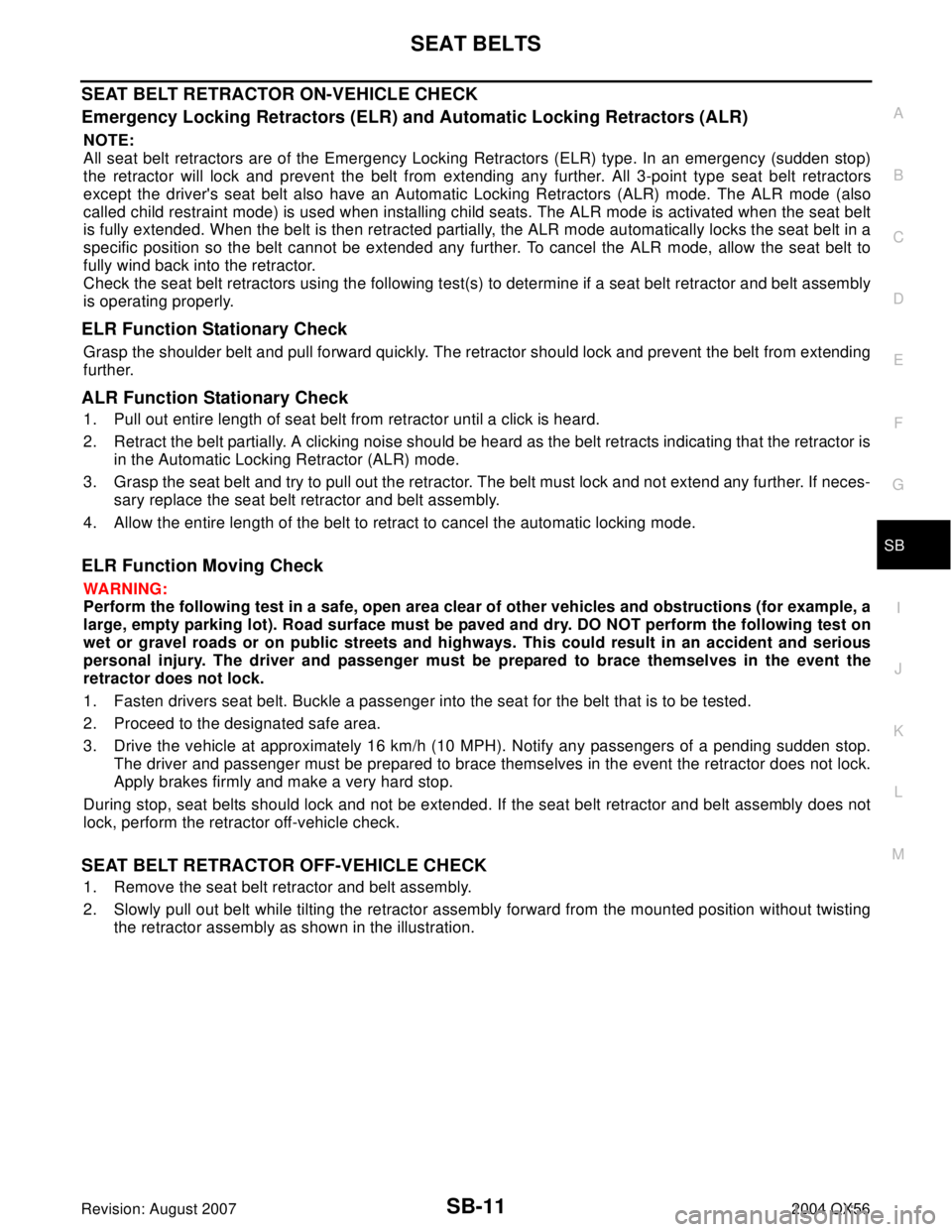
SEAT BELTS
SB-11
C
D
E
F
G
I
J
K
L
MA
B
SB
Revision: August 20072004 QX56
SEAT BELT RETRACTOR ON-VEHICLE CHECK
Emergency Locking Retractors (ELR) and Automatic Locking Retractors (ALR)
NOTE:
All seat belt retractors are of the Emergency Locking Retractors (ELR) type. In an emergency (sudden stop)
the retractor will lock and prevent the belt from extending any further. All 3-point type seat belt retractors
except the driver's seat belt also have an Automatic Locking Retractors (ALR) mode. The ALR mode (also
called child restraint mode) is used when installing child seats. The ALR mode is activated when the seat belt
is fully extended. When the belt is then retracted partially, the ALR mode automatically locks the seat belt in a
specific position so the belt cannot be extended any further. To cancel the ALR mode, allow the seat belt to
fully wind back into the retractor.
Check the seat belt retractors using the following test(s) to determine if a seat belt retractor and belt assembly
is operating properly.
ELR Function Stationary Check
Grasp the shoulder belt and pull forward quickly. The retractor should lock and prevent the belt from extending
further.
ALR Function Stationary Check
1. Pull out entire length of seat belt from retractor until a click is heard.
2. Retract the belt partially. A clicking noise should be heard as the belt retracts indicating that the retractor is
in the Automatic Locking Retractor (ALR) mode.
3. Grasp the seat belt and try to pull out the retractor. The belt must lock and not extend any further. If neces-
sary replace the seat belt retractor and belt assembly.
4. Allow the entire length of the belt to retract to cancel the automatic locking mode.
ELR Function Moving Check
WA RN ING:
Perform the following test in a safe, open area clear of other vehicles and obstructions (for example, a
large, empty parking lot). Road surface must be paved and dry. DO NOT perform the following test on
wet or gravel roads or on public streets and highways. This could result in an accident and serious
personal injury. The driver and passenger must be prepared to brace themselves in the event the
retractor does not lock.
1. Fasten drivers seat belt. Buckle a passenger into the seat for the belt that is to be tested.
2. Proceed to the designated safe area.
3. Drive the vehicle at approximately 16 km/h (10 MPH). Notify any passengers of a pending sudden stop.
The driver and passenger must be prepared to brace themselves in the event the retractor does not lock.
Apply brakes firmly and make a very hard stop.
During stop, seat belts should lock and not be extended. If the seat belt retractor and belt assembly does not
lock, perform the retractor off-vehicle check.
SEAT BELT RETRACTOR OFF-VEHICLE CHECK
1. Remove the seat belt retractor and belt assembly.
2. Slowly pull out belt while tilting the retractor assembly forward from the mounted position without twisting
the retractor assembly as shown in the illustration.
Page 2949 of 3371
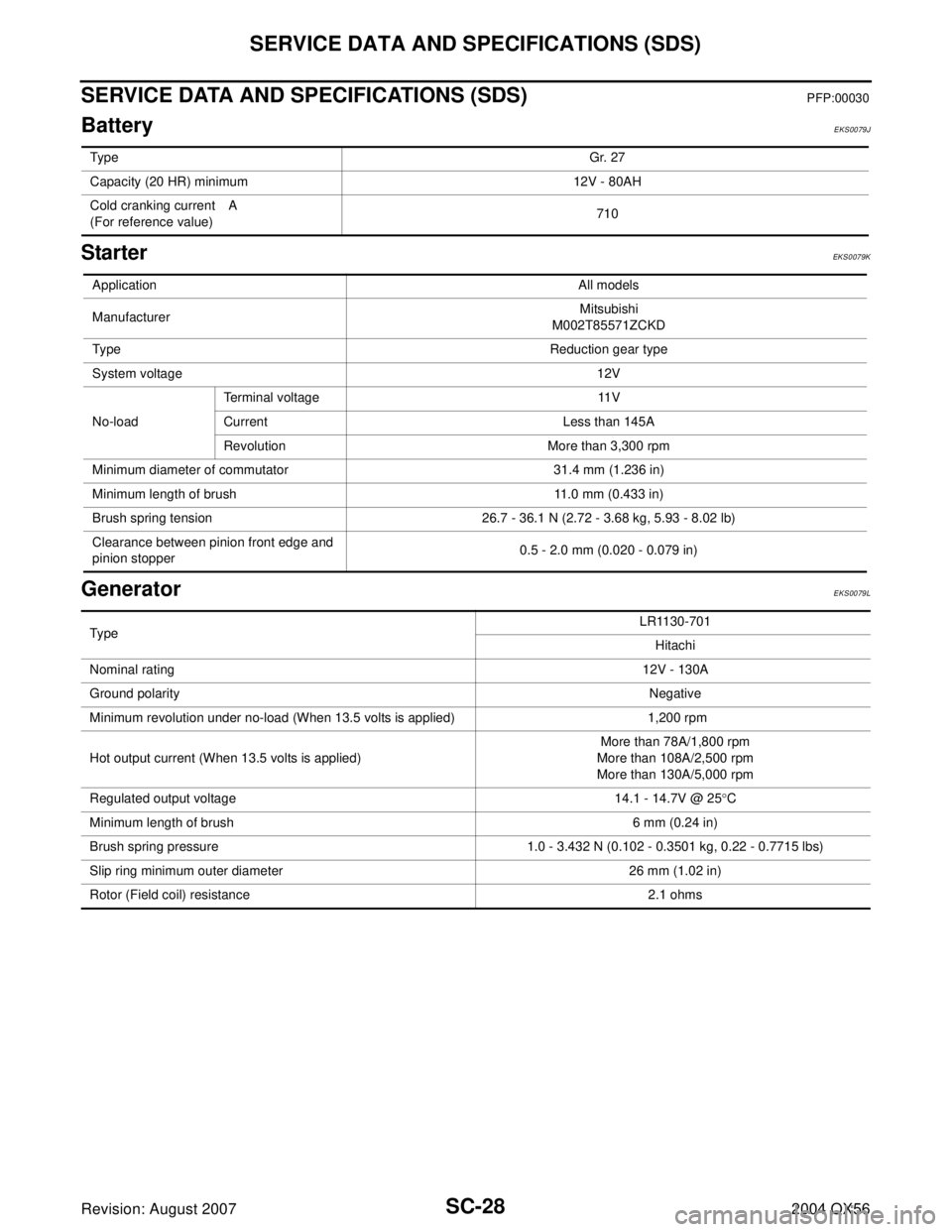
SC-28
SERVICE DATA AND SPECIFICATIONS (SDS)
Revision: August 20072004 QX56
SERVICE DATA AND SPECIFICATIONS (SDS)PFP:00030
BatteryEKS0079J
StarterEKS0079K
GeneratorEKS0079L
Typ eGr. 27
Capacity (20 HR) minimum 12V - 80AH
Cold cranking current A
(For reference value)710
ApplicationAll models
ManufacturerMitsubishi
M002T85571ZCKD
Ty peReduction gear type
System voltage 12V
No-loadTerminal voltage 11V
Current Less than 145A
Revolution More than 3,300 rpm
Minimum diameter of commutator 31.4 mm (1.236 in)
Minimum length of brush 11.0 mm (0.433 in)
Brush spring tension 26.7 - 36.1 N (2.72 - 3.68 kg, 5.93 - 8.02 lb)
Clearance between pinion front edge and
pinion stopper0.5 - 2.0 mm (0.020 - 0.079 in)
Ty peLR1130-701
Hitachi
Nominal rating12V - 130A
Ground polarityNegative
Minimum revolution under no-load (When 13.5 volts is applied) 1,200 rpm
Hot output current (When 13.5 volts is applied)More than 78A/1,800 rpm
More than 108A/2,500 rpm
More than 130A/5,000 rpm
Regulated output voltage 14.1 - 14.7V @ 25°C
Minimum length of brush 6 mm (0.24 in)
Brush spring pressure 1.0 - 3.432 N (0.102 - 0.3501 kg, 0.22 - 0.7715 lbs)
Slip ring minimum outer diameter 26 mm (1.02 in)
Rotor (Field coil) resistance 2.1 ohms
Page 3234 of 3371
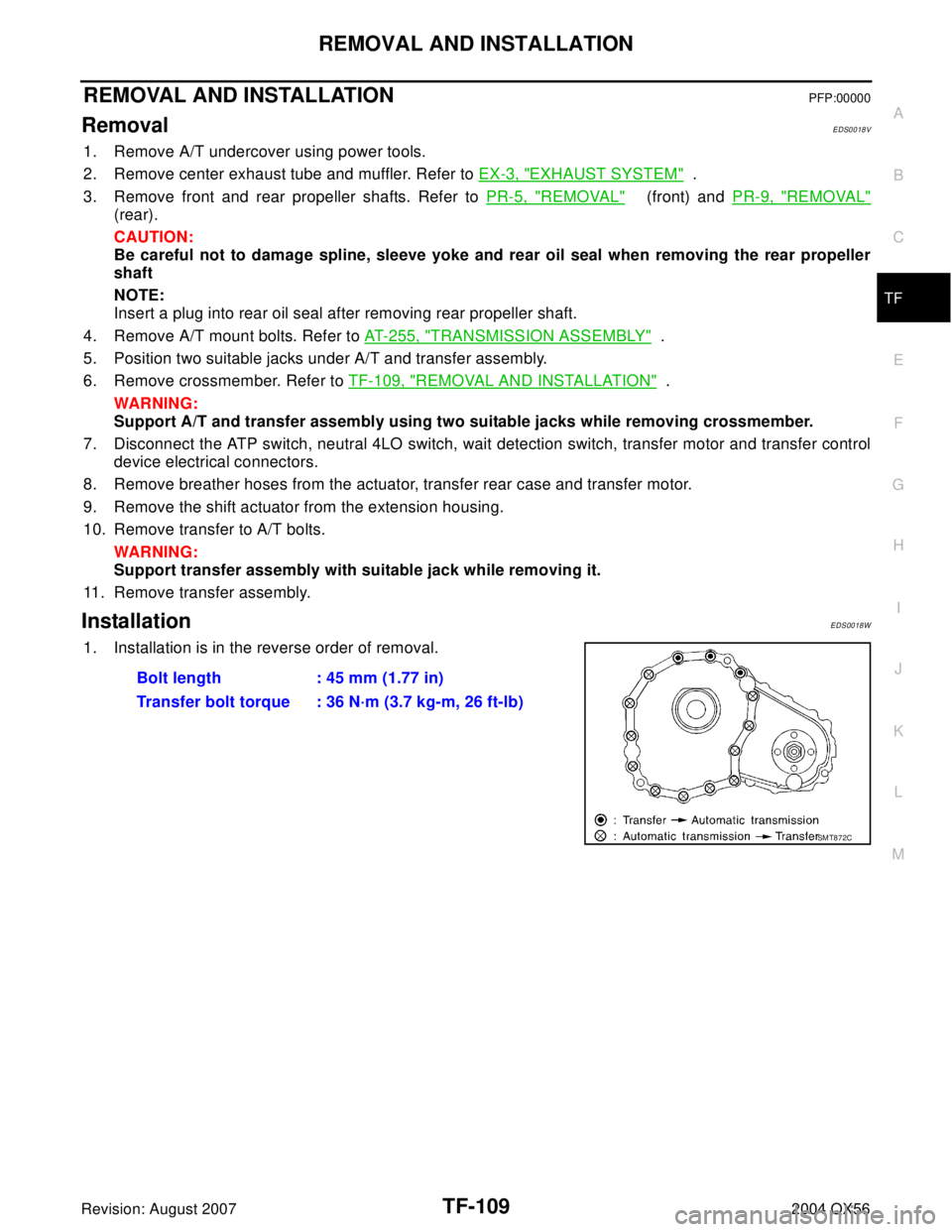
REMOVAL AND INSTALLATION
TF-109
C
E
F
G
H
I
J
K
L
MA
B
TF
Revision: August 20072004 QX56
REMOVAL AND INSTALLATIONPFP:00000
RemovalEDS0018V
1. Remove A/T undercover using power tools.
2. Remove center exhaust tube and muffler. Refer to EX-3, "
EXHAUST SYSTEM" .
3. Remove front and rear propeller shafts. Refer to PR-5, "
REMOVAL" (front) and PR-9, "REMOVAL"
(rear).
CAUTION:
Be careful not to damage spline, sleeve yoke and rear oil seal when removing the rear propeller
shaft
NOTE:
Insert a plug into rear oil seal after removing rear propeller shaft.
4. Remove A/T mount bolts. Refer to AT-255, "
TRANSMISSION ASSEMBLY" .
5. Position two suitable jacks under A/T and transfer assembly.
6. Remove crossmember. Refer to TF-109, "
REMOVAL AND INSTALLATION" .
WAR NIN G:
Support A/T and transfer assembly using two suitable jacks while removing crossmember.
7. Disconnect the ATP switch, neutral 4LO switch, wait detection switch, transfer motor and transfer control
device electrical connectors.
8. Remove breather hoses from the actuator, transfer rear case and transfer motor.
9. Remove the shift actuator from the extension housing.
10. Remove transfer to A/T bolts.
WAR NIN G:
Support transfer assembly with suitable jack while removing it.
11. Remove transfer assembly.
InstallationEDS0018W
1. Installation is in the reverse order of removal.
Bolt length : 45 mm (1.77 in)
Transfer bolt torque : 36 N·m (3.7 kg-m, 26 ft-lb)
SMT872C