height INFINITI QX56 2006 Factory User Guide
[x] Cancel search | Manufacturer: INFINITI, Model Year: 2006, Model line: QX56, Model: INFINITI QX56 2006Pages: 3383, PDF Size: 51.76 MB
Page 909 of 3383
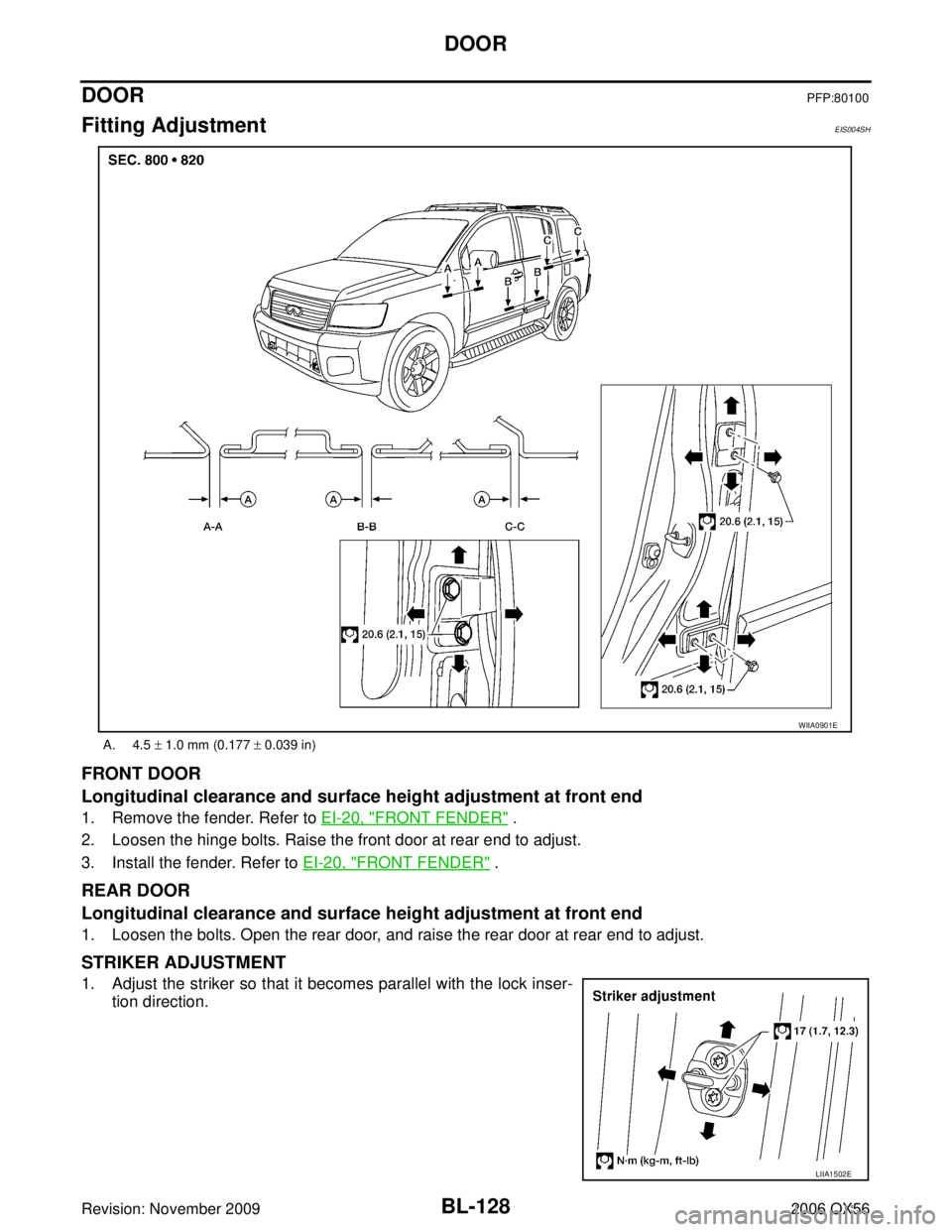
BL-128
DOOR
Revision: November 20092006 QX56
DOORPFP:80100
Fitting AdjustmentEIS004SH
FRONT DOOR
Longitudinal clearance and surface height adjustment at front end
1. Remove the fender. Refer to EI-20, "FRONT FENDER" .
2. Loosen the hinge bolts. Raise the front door at rear end to adjust.
3. Install the fender. Refer to EI-20, "
FRONT FENDER" .
REAR DOOR
Longitudinal clearance and surface height adjustment at front end
1. Loosen the bolts. Open the rear door, and raise the rear door at rear end to adjust.
STRIKER ADJUSTMENT
1. Adjust the striker so that it becomes parallel with the lock inser-
tion direction.
A. 4.5 ± 1.0 mm (0.177 ± 0.039 in)
WIIA0901E
LIIA1502E
Page 997 of 3383
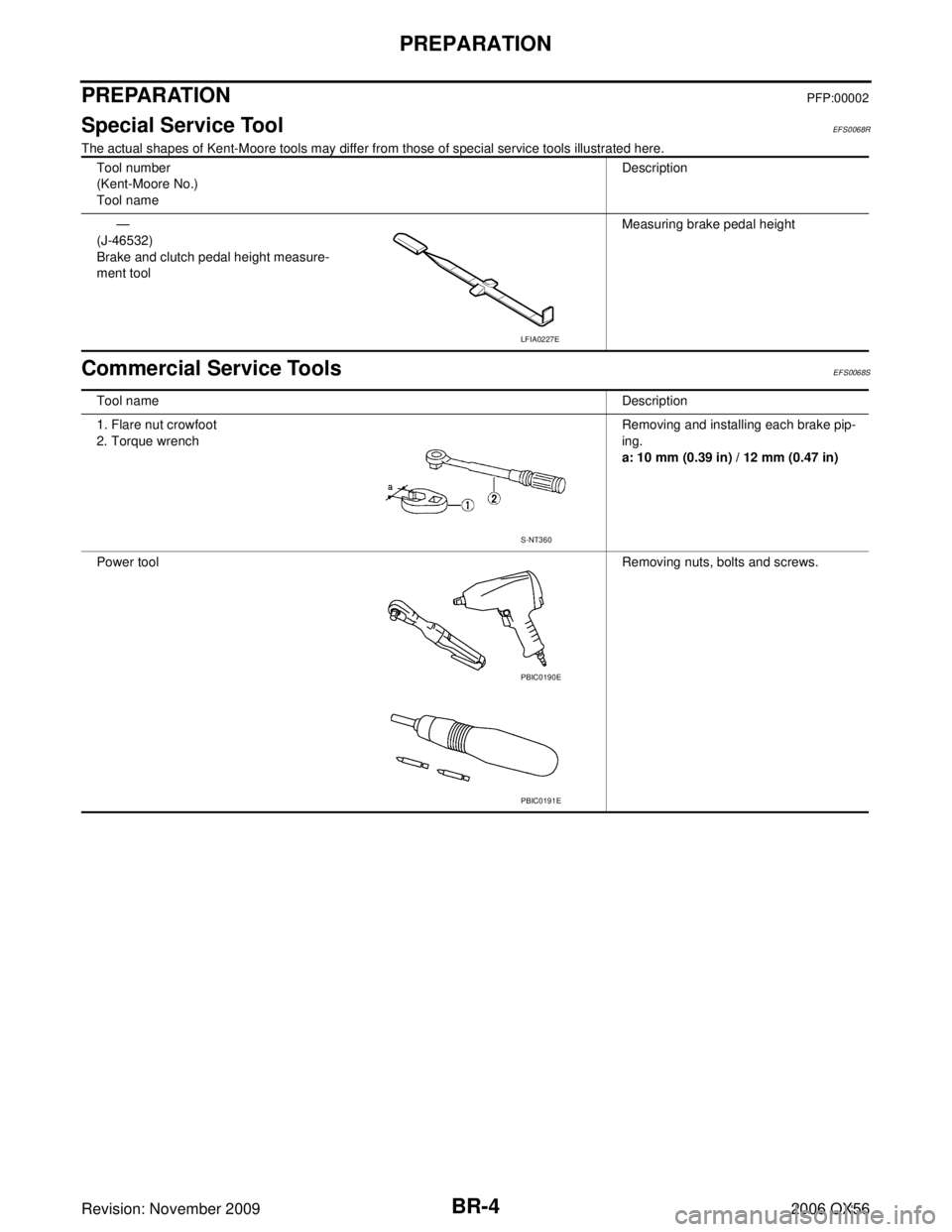
BR-4
PREPARATION
Revision: November 20092006 QX56
PREPARATIONPFP:00002
Special Service ToolEFS0068R
The actual shapes of Kent-Moore tools may differ from those of special service tools illustrated here.
Commercial Service ToolsEFS0068S
Tool number
(Kent-Moore No.)
Tool nameDescription
—
(J-46532)
Brake and clutch pedal height measure-
ment tool Measuring brake pedal height
LFIA0227E
Tool name
Description
1. Flare nut crowfoot
2. Torque wrench Removing and installing each brake pip-
ing.
a: 10 mm (0.39 in) / 12 mm (0.47 in)
Power tool Removing nuts, bolts and screws.
S-NT360
PBIC0190E
PBIC0191E
Page 999 of 3383
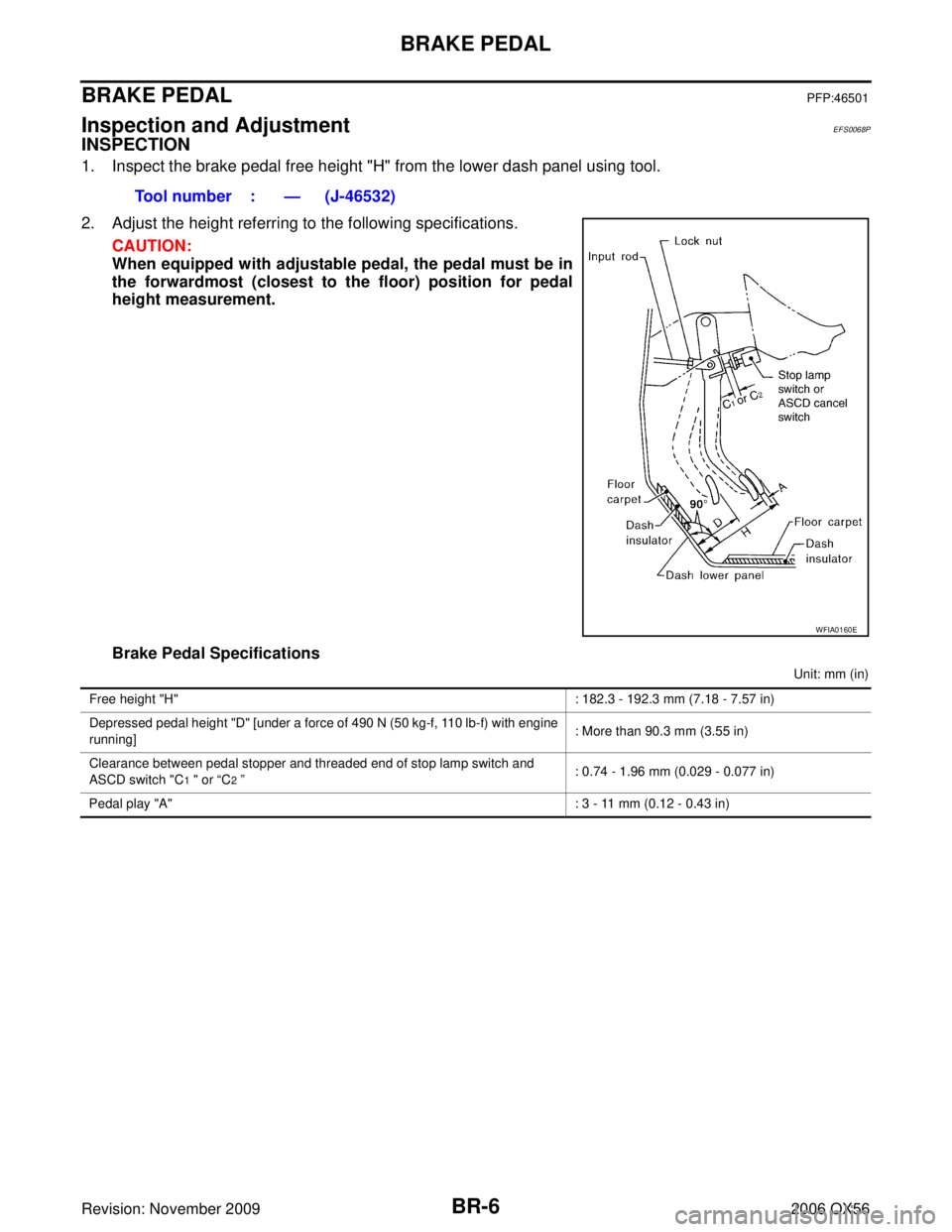
BR-6
BRAKE PEDAL
Revision: November 20092006 QX56
BRAKE PEDALPFP:46501
Inspection and Adjustment EFS0068P
INSPECTION
1. Inspect the brake pedal free height "H" from the lower dash panel using tool.
2. Adjust the height referring to the following specifications.
CAUTION:
When equipped with adjustable pedal, the pedal must be in
the forwardmost (closest to the floor) position for pedal
height measurement.
Brake Pedal Specifications
Unit: mm (in)
Tool number : — (J-46532)
WFIA0160E
Free height "H" : 182.3 - 192.3 mm (7.18 - 7.57 in)
Depressed pedal height "D" [under a force of 490 N (50 kg-f, 110 lb-f) with engine
running] : More than 90.3 mm (3.55 in)
Clearance between pedal stopper and threaded end of stop lamp switch and
ASCD switch "C
1 " or “ C2 ” : 0.74 - 1.96 mm (0.029 - 0.077 in)
Pedal play "A" : 3 - 11 mm (0.12 - 0.43 in)
Page 1000 of 3383
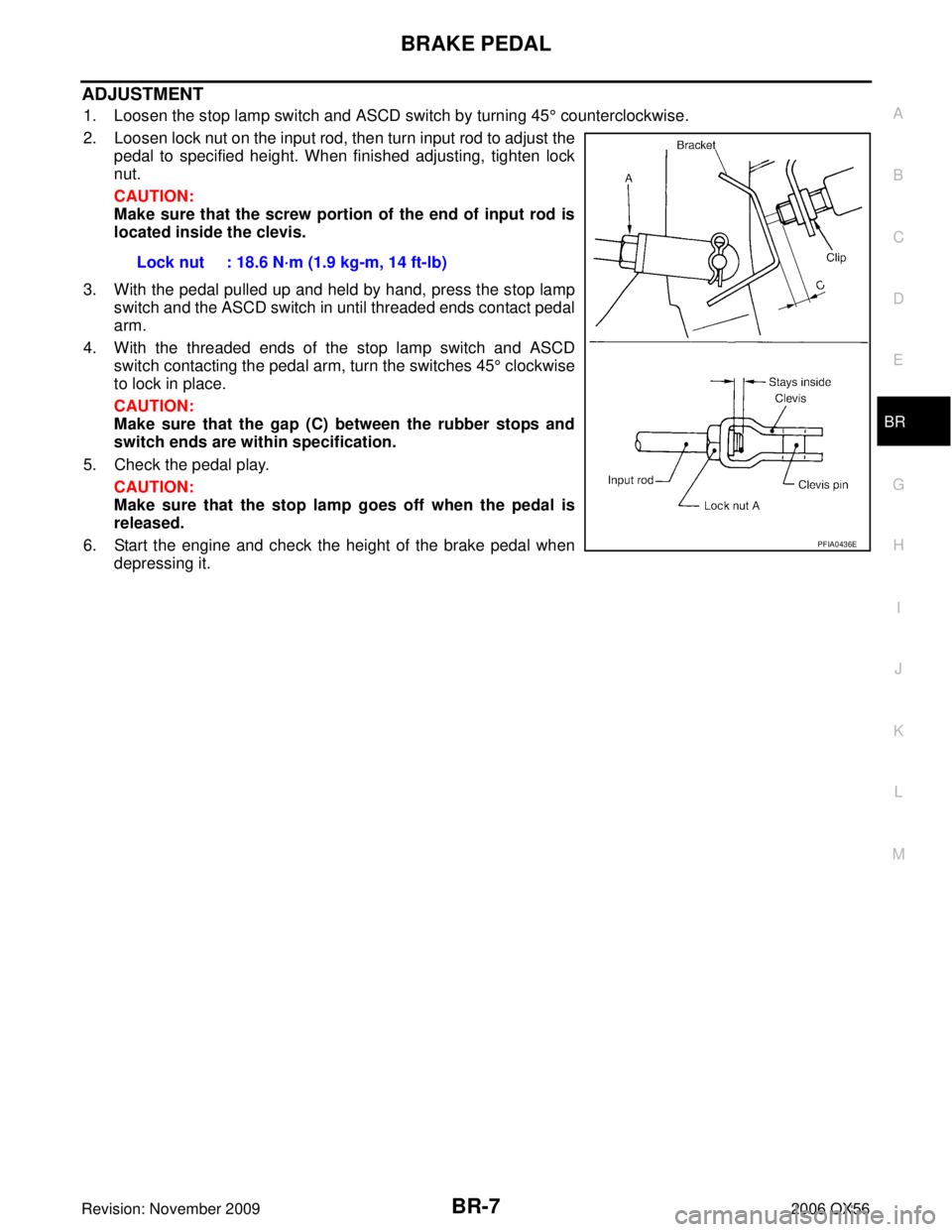
BRAKE PEDALBR-7
C
DE
G H
I
J
K L
M A
B
BR
Revision: November 2009 2006 QX56
ADJUSTMENT
1. Loosen the stop lamp switch and ASCD switch by turning 45° counterclockwise.
2. Loosen lock nut on the input rod, then turn input rod to adjust the pedal to specified height. When finished adjusting, tighten lock
nut.
CAUTION:
Make sure that the screw portion of the end of input rod is
located inside the clevis.
3. With the pedal pulled up and held by hand, press the stop lamp switch and the ASCD switch in until threaded ends contact pedal
arm.
4. With the threaded ends of the stop lamp switch and ASCD switch contacting the pedal arm, turn the switches 45 ° clockwise
to lock in place.
CAUTION:
Make sure that the gap (C) between the rubber stops and
switch ends are within specification.
5. Check the pedal play. CAUTION:
Make sure that the stop lamp goes off when the pedal is
released.
6. Start the engine and check the height of the brake pedal when depressing it.Lock nut : 18.6 N·m (1.9 kg-m, 14 ft-lb)
PFIA0436E
Page 1012 of 3383
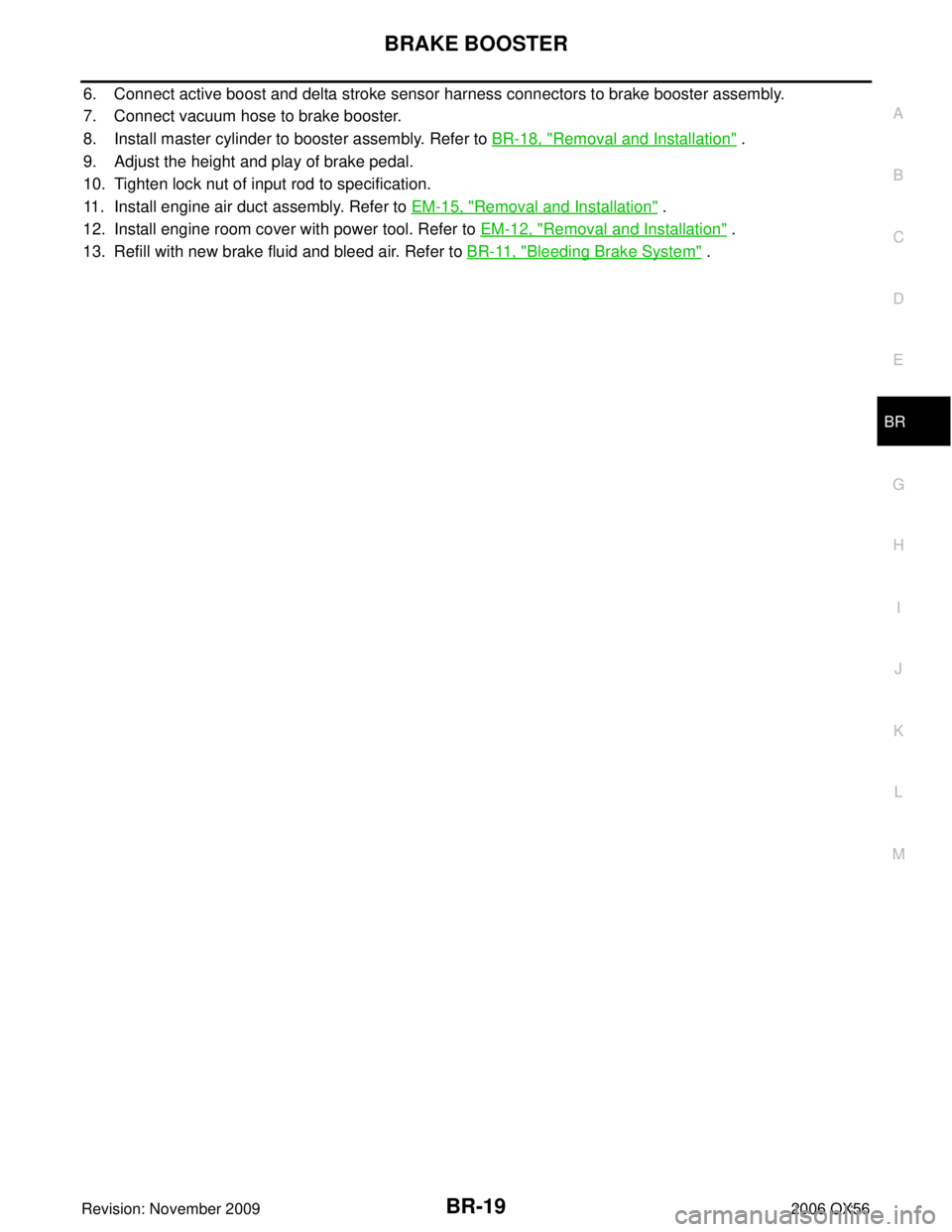
BRAKE BOOSTERBR-19
C
DE
G H
I
J
K L
M A
B
BR
Revision: November 2009 2006 QX56
6. Connect active boost and delta stroke sensor harness connectors to brake booster assembly.
7. Connect vacuum hose to brake booster.
8. Install master cylinder to booster assembly. Refer to BR-18, "
Removal and Installation" .
9. Adjust the height and play of brake pedal.
10. Tighten lock nut of input rod to specification.
11. Install engine air duct assembly. Refer to EM-15, "
Removal and Installation" .
12. Install engine room cover with power tool. Refer to EM-12, "
Removal and Installation" .
13. Refill with new brake fluid and bleed air. Refer to BR-11, "
Bleeding Brake System" .
Page 1025 of 3383

BR-32
SERVICE DATA AND SPECIFICATIONS (SDS)
Revision: November 20092006 QX56
SERVICE DATA AND SPECIFICATIONS (SDS)PFP:00030
General SpecificationsEFS004WQ
Unit: mm (in)
Brake PedalEFS004WR
Brake BoosterEFS004WS
Check ValveEFS004WT
Front Disc BrakeEFS004WU
Front brake Brake modelCLZ31VCAD41VA
Rotor outer diameter × thickness 320 × 26 (12.60 × 1.02) 350 x 30 (13.78 x 1.181)
Pad Length × width × thickness 111 . 0
× 73.5 × 11.88 (4.73 ×
2.894 × 0.468) 151.6 x 56.5 x 12 (5.968 x
2.224 x 0.47)
Cylinder bore diameter 51 (2.01)51 (2.01)
Rear brake Brake model AD14VE
Rotor outer diameter × thickness 320 × 14 (12.60 × 0.55)
Pad Length × width × thickness 83.0 × 33.0 × 8.5 (3.268 × 1.299 × 0.335)
Cylinder bore diameter 48 (1.89)
Control valve Valve model Electric brake force distribution
Brake booster Booster model
C215T
Diaphragm diameter 215 (8.46)
Recommended brake fluid Genuine NISSAN Super Heavy Duty Brake Fluid or equivalent
Brake pedal height (from dash lower panel top surface) 182.3 − 192.3 mm (7.18 − 7.57 in)
Depressed pedal height [under a force of 490 N (50 kg-f, 110 lb-f)
with engine running] More than 90.3 mm (3.55 in)
Clearance between stopper rubber and the threaded end of stop
lamp switch 0.74
− 1.96 mm (0.029 − 0.077 in)
Pedal play 3 − 11 mm (0.12 − 0.43 in)
Output rod installation standard dimension 15.6 − 15.9 mm (0.614 − 0.626 in)
Vacuum leakage
[at vacuum of – 66.7 kPa(– 500 mmHg, – 19.69 inHg)] Within 1.3 kPa (10 mmHg, 0.39 inHg) of vacuum for 15 seconds
Brake model
CLZ31VCAD41VA
Brake pad Standard thickness (new)
11.88 mm (0.468 in)12 mm (0.47 in)
Repair limit thickness 1.0 mm (0.039 in)1.0 mm (0.039 in)
Disc rotor Standard thickness (new)
26.0 mm (1.024 in) 30.0 mm (1.181 in)
Repair limit thickness 24.5 mm (0.965 in) 28.5 mm (1.122 in)
Maximum uneven wear (measured at 8 positions) 0.015 mm (0.0006 in)
Runout limit (with it attached to the vehicle) 0.03 mm (0.001 in)
Page 1373 of 3383
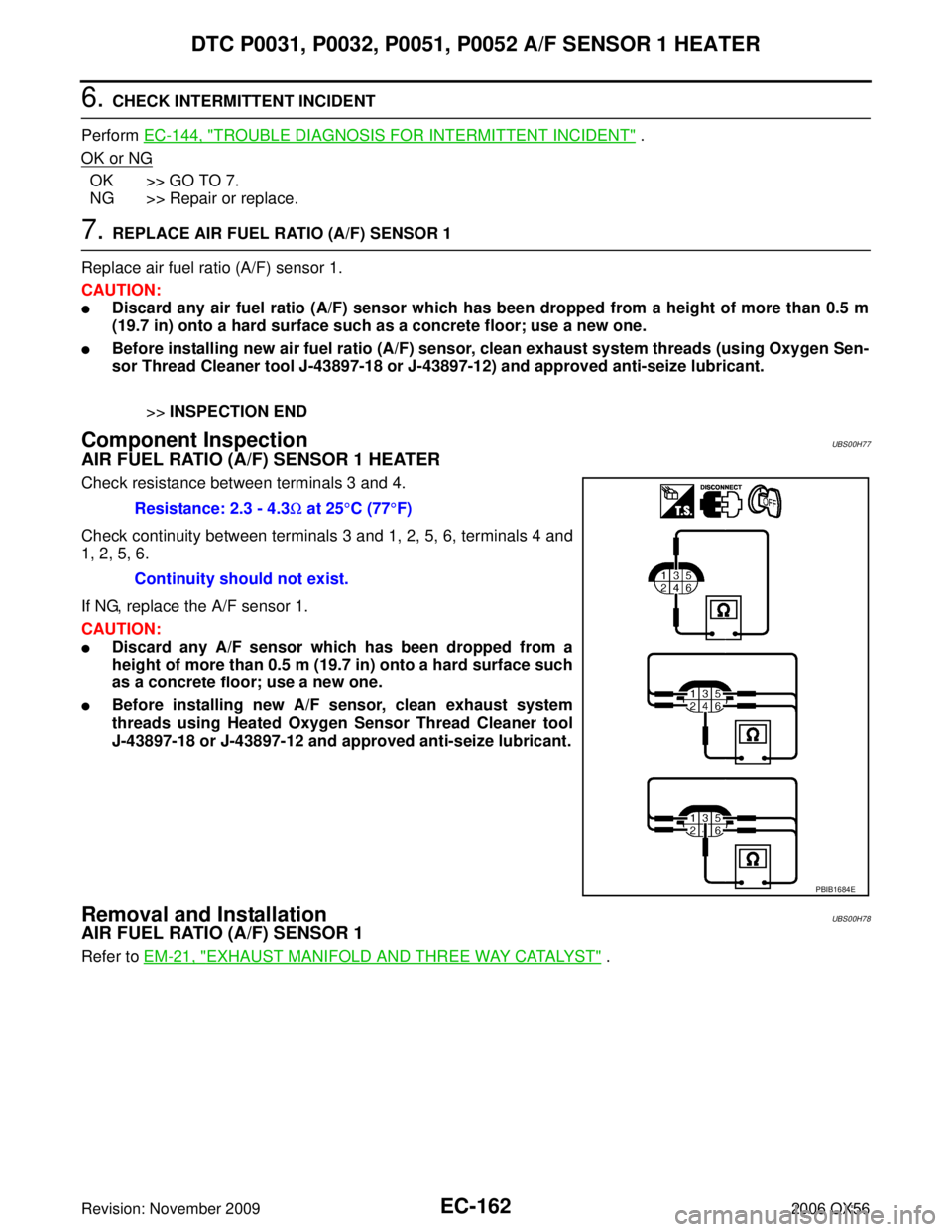
EC-162Revision: November 2009
DTC P0031, P0032, P0051, P0052 A/F SENSOR 1 HEATER
2006 QX56
6. CHECK INTERMITTENT INCIDENT
Perform EC-144, "
TROUBLE DIAGNOSIS FOR INTERMITTENT INCIDENT" .
OK or NG
OK >> GO TO 7.
NG >> Repair or replace.
7. REPLACE AIR FUEL RATIO (A/F) SENSOR 1
Replace air fuel ratio (A/F) sensor 1.
CAUTION:
Discard any air fuel ratio (A/F) sensor which has been dropped from a height of more than 0.5 m
(19.7 in) onto a hard surface such as a concrete floor; use a new one.
Before installing new air fuel ratio (A/F) sensor, clean exhaust system threads (using Oxygen Sen-
sor Thread Cleaner tool J-43897-18 or J-43897-12) and approved anti-seize lubricant.
>>INSPECTION END
Component InspectionUBS00H77
AIR FUEL RATIO (A/F) SENSOR 1 HEATER
Check resistance between terminals 3 and 4.
Check continuity between terminals 3 and 1, 2, 5, 6, terminals 4 and
1, 2, 5, 6.
If NG, replace the A/F sensor 1.
CAUTION:
Discard any A/F sensor which has been dropped from a
height of more than 0.5 m (19.7 in) onto a hard surface such
as a concrete floor; use a new one.
Before installing new A/F sensor, clean exhaust system
threads using Heated Oxygen Sensor Thread Cleaner tool
J-43897-18 or J-43897-12 and approved anti-seize lubricant.
Removal and Installation UBS00H78
AIR FUEL RATIO (A/F) SENSOR 1
Refer to EM-21, "EXHAUST MANIFOLD AND THREE WAY CATALYST" .
Resistance: 2.3 - 4.3Ω
at 25°C (77 °F)
Continuity should not exist.
PBIB1684E
Page 1381 of 3383
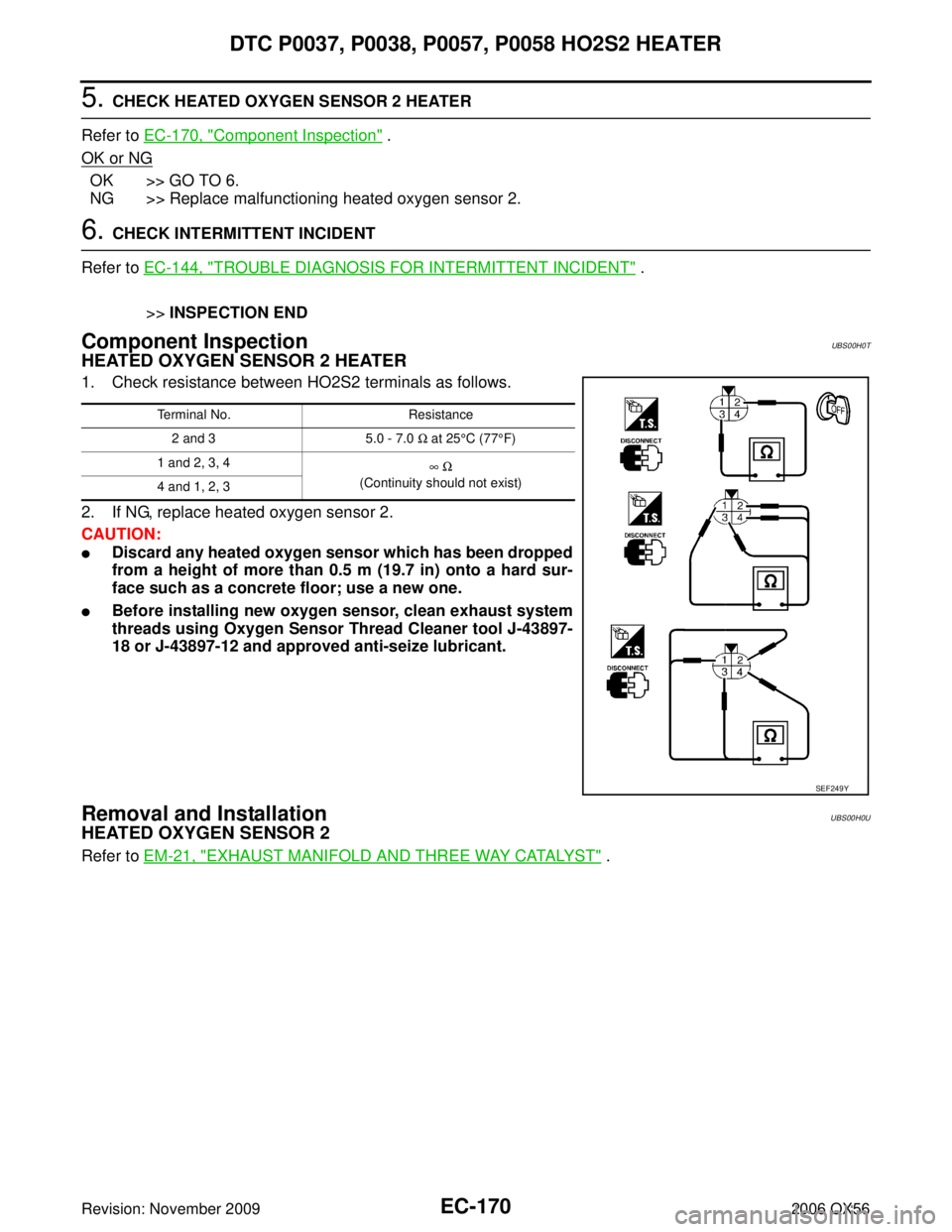
EC-170Revision: November 2009
DTC P0037, P0038, P0057, P0058 HO2S2 HEATER
2006 QX56
5. CHECK HEATED OXYGEN SENSOR 2 HEATER
Refer to EC-170, "
Component Inspection" .
OK or NG
OK >> GO TO 6.
NG >> Replace malfunctioning heated oxygen sensor 2.
6. CHECK INTERMITTENT INCIDENT
Refer to EC-144, "
TROUBLE DIAGNOSIS FOR INTERMITTENT INCIDENT" .
>> INSPECTION END
Component InspectionUBS00H0T
HEATED OXYGEN SENSOR 2 HEATER
1. Check resistance between HO2S2 terminals as follows.
2. If NG, replace heated oxygen sensor 2.
CAUTION:
Discard any heated oxygen sensor which has been dropped
from a height of more than 0.5 m (19.7 in) onto a hard sur-
face such as a concrete floor; use a new one.
Before installing new oxygen sensor, clean exhaust system
threads using Oxygen Sensor Thread Cleaner tool J-43897-
18 or J-43897-12 and approved anti-seize lubricant.
Removal and InstallationUBS00H0U
HEATED OXYGEN SENSOR 2
Refer to EM-21, "EXHAUST MANIFOLD AND THREE WAY CATALYST" .
Terminal No. Resistance
2 and 3 5.0 - 7.0 Ω at 25°C (77 °F)
1 and 2, 3, 4 \b Ω
(Continuity should not exist)
4 and 1, 2, 3
SEF249Y
Page 1432 of 3383
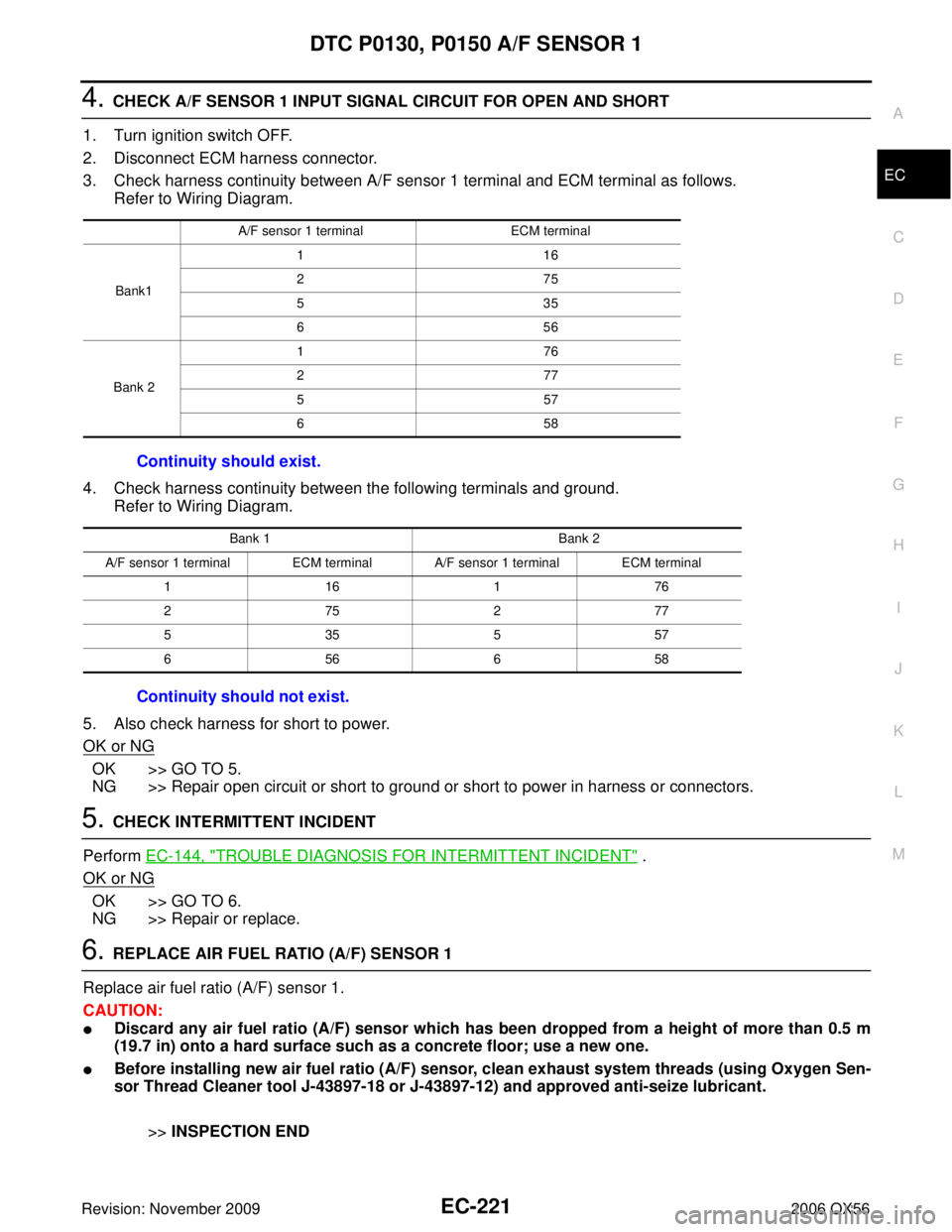
DTC P0130, P0150 A/F SENSOR 1EC-221
C
DE
F
G H
I
J
K L
M A
EC
Revision: November 2009 2006 QX56
4. CHECK A/F SENSOR 1 INPUT SIGNAL CIRCUIT FOR OPEN AND SHORT
1. Turn ignition switch OFF.
2. Disconnect ECM harness connector.
3. Check harness continuity between A/F sensor 1 terminal and ECM terminal as follows. Refer to Wiring Diagram.
4. Check harness continuity between the following terminals and ground. Refer to Wiring Diagram.
5. Also check harness for short to power.
OK or NG
OK >> GO TO 5.
NG >> Repair open circuit or short to ground or short to power in harness or connectors.
5. CHECK INTERMITTENT INCIDENT
Perform EC-144, "
TROUBLE DIAGNOSIS FOR INTERMITTENT INCIDENT" .
OK or NG
OK >> GO TO 6.
NG >> Repair or replace.
6. REPLACE AIR FUEL RATIO (A/F) SENSOR 1
Replace air fuel ratio (A/F) sensor 1.
CAUTION:
Discard any air fuel ratio (A/F) sensor which has been dropped from a height of more than 0.5 m
(19.7 in) onto a hard surface such as a concrete floor; use a new one.
Before installing new air fuel ratio (A/F) sensor, clean exhaust system threads (using Oxygen Sen-
sor Thread Cleaner tool J-43897-18 or J-43897-12) and approved anti-seize lubricant.
>>INSPECTION END
A/F sensor 1 terminal ECM terminal
Bank1 11
6
27 5
53 5
65 6
Bank 2 17
6
27 7
55 7
65 8
Continuity should exist.
Bank 1 Bank 2
A/F sensor 1 terminal ECM terminal A/F sensor 1 terminal ECM terminal 11 617 6
27 527 7
53 555 7
65 665 8
Continuity should not exist.
Page 1441 of 3383
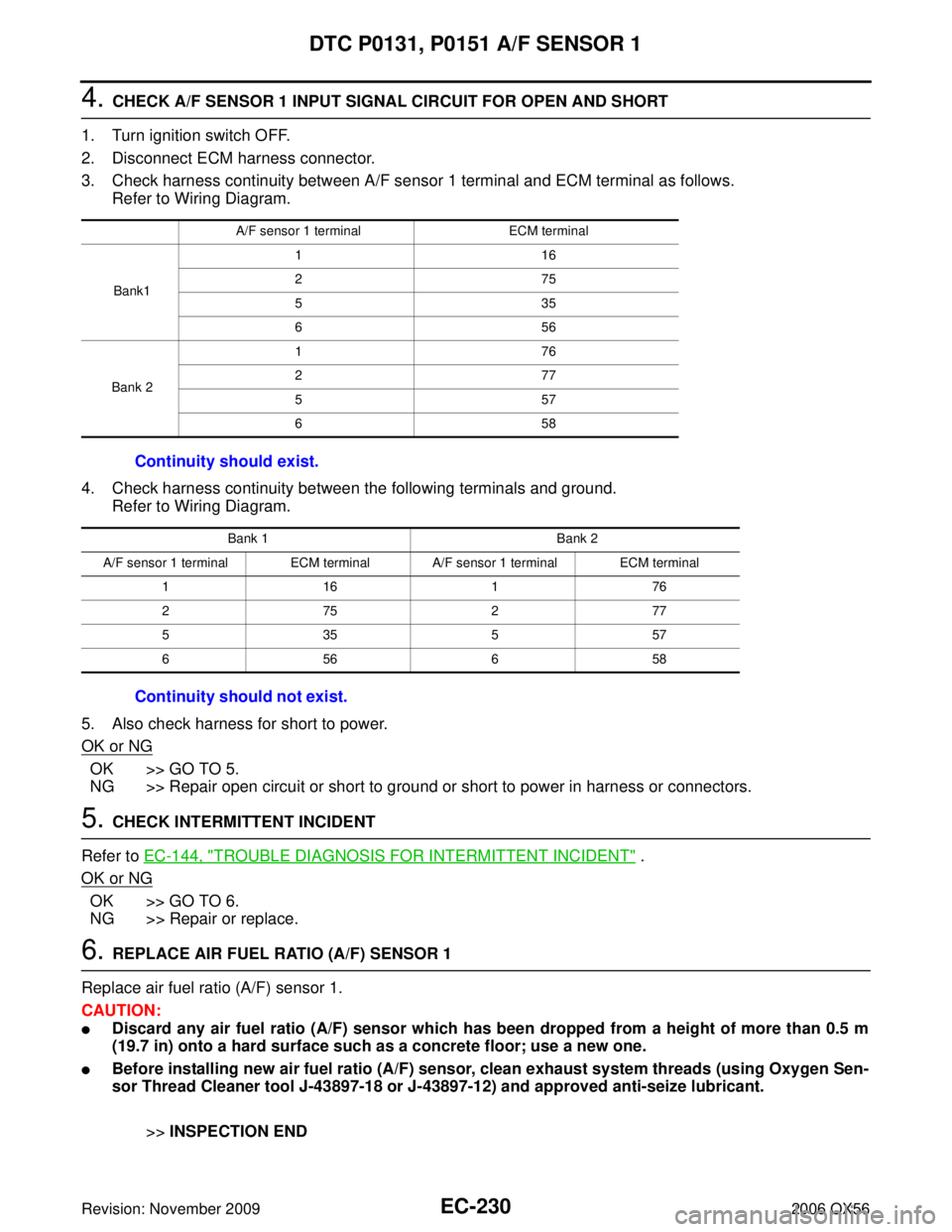
EC-230Revision: November 2009
DTC P0131, P0151 A/F SENSOR 1
2006 QX56
4. CHECK A/F SENSOR 1 INPUT SIGNAL CIRCUIT FOR OPEN AND SHORT
1. Turn ignition switch OFF.
2. Disconnect ECM harness connector.
3. Check harness continuity between A/F sensor 1 terminal and ECM terminal as follows. Refer to Wiring Diagram.
4. Check harness continuity between the following terminals and ground. Refer to Wiring Diagram.
5. Also check harness for short to power.
OK or NG
OK >> GO TO 5.
NG >> Repair open circuit or short to ground or short to power in harness or connectors.
5. CHECK INTERMITTENT INCIDENT
Refer to EC-144, "
TROUBLE DIAGNOSIS FOR INTERMITTENT INCIDENT" .
OK or NG
OK >> GO TO 6.
NG >> Repair or replace.
6. REPLACE AIR FUEL RATIO (A/F) SENSOR 1
Replace air fuel ratio (A/F) sensor 1.
CAUTION:
Discard any air fuel ratio (A/F) sensor which has been dropped from a height of more than 0.5 m
(19.7 in) onto a hard surface such as a concrete floor; use a new one.
Before installing new air fuel ratio (A/F) sensor, clean exhaust system threads (using Oxygen Sen-
sor Thread Cleaner tool J-43897-18 or J-43897-12) and approved anti-seize lubricant.
>>INSPECTION END
A/F sensor 1 terminal ECM terminal
Bank1 11
6
27 5
53 5
65 6
Bank 2 17
6
27 7
55 7
65 8
Continuity should exist.
Bank 1 Bank 2
A/F sensor 1 terminal ECM terminal A/F sensor 1 terminal ECM terminal 11 617 6
27 527 7
53 555 7
65 665 8
Continuity should not exist.