center console INFINITI QX56 2006 Factory Owner's Manual
[x] Cancel search | Manufacturer: INFINITI, Model Year: 2006, Model line: QX56, Model: INFINITI QX56 2006Pages: 3383, PDF Size: 51.76 MB
Page 2255 of 3383
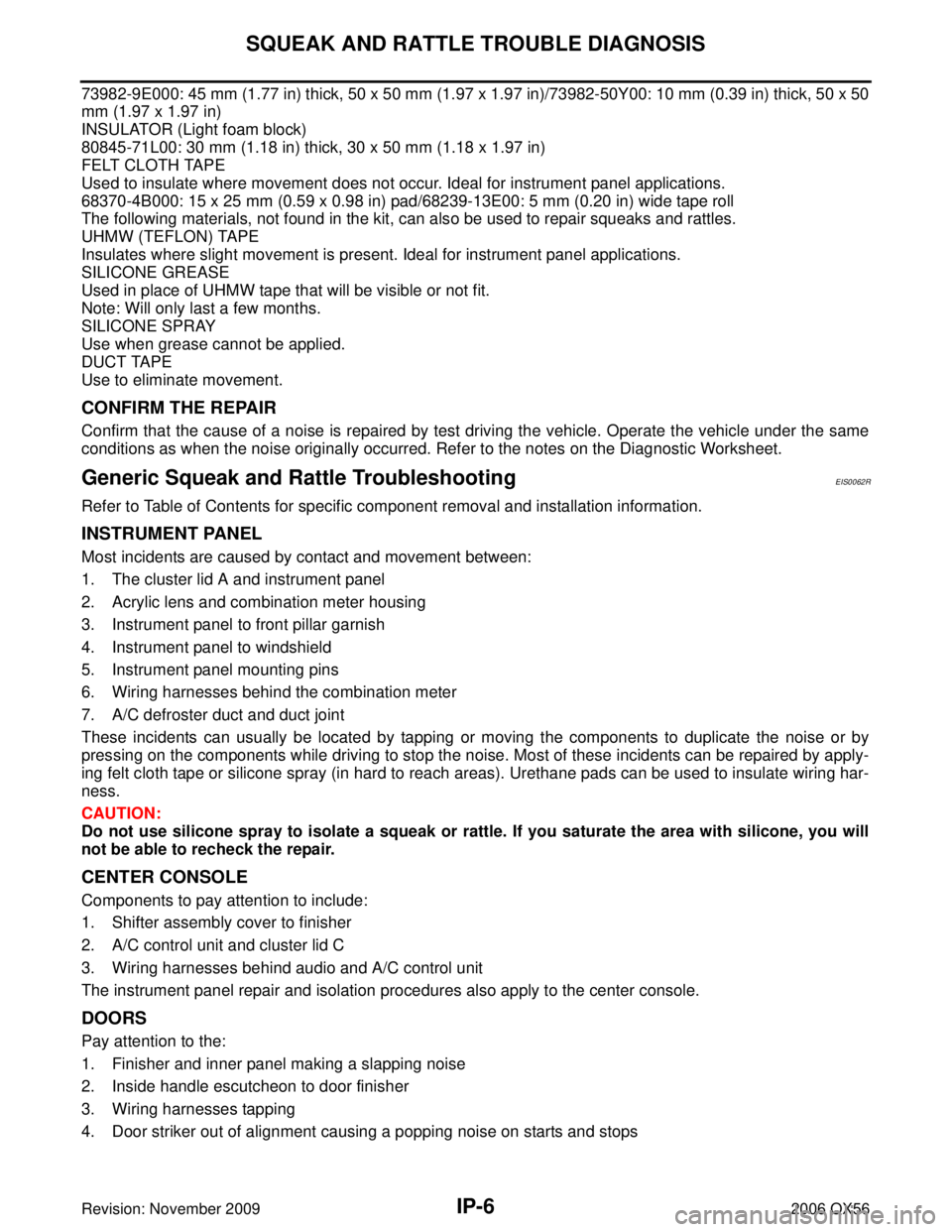
IP-6
SQUEAK AND RATTLE TROUBLE DIAGNOSIS
Revision: November 20092006 QX56
73982-9E000: 45 mm (1.77 in) thick, 50 x 50 mm (1.97 x 1.97 in)/73982-50Y00: 10 mm (0.39 in) thick, 50 x 50
mm (1.97 x 1.97 in)
INSULATOR (Light foam block)
80845-71L00: 30 mm (1.18 in) thick, 30 x 50 mm (1.18 x 1.97 in)
FELT CLOTH TAPE
Used to insulate where movement does not occur. Ideal for instrument panel applications.
68370-4B000: 15 x 25 mm (0.59 x 0.98 in) pad/68239-13E00: 5 mm (0.20 in) wide tape roll
The following materials, not found in the kit, can also be used to repair squeaks and rattles.
UHMW (TEFLON) TAPE
Insulates where slight movement is present. Ideal for instrument panel applications.
SILICONE GREASE
Used in place of UHMW tape that will be visible or not fit.
Note: Will only last a few months.
SILICONE SPRAY
Use when grease cannot be applied.
DUCT TAPE
Use to eliminate movement.
CONFIRM THE REPAIR
Confirm that the cause of a noise is repaired by test driving the vehicle. Operate the vehicle under the same
conditions as when the noise originally occurred. Refer to the notes on the Diagnostic Worksheet.
Generic Squeak and Rattle TroubleshootingEIS0062R
Refer to Table of Contents for specific component removal and installation information.
INSTRUMENT PANEL
Most incidents are caused by contact and movement between:
1. The cluster lid A and instrument panel
2. Acrylic lens and combination meter housing
3. Instrument panel to front pillar garnish
4. Instrument panel to windshield
5. Instrument panel mounting pins
6. Wiring harnesses behind the combination meter
7. A/C defroster duct and duct joint
These incidents can usually be located by tapping or moving the components to duplicate the noise or by
pressing on the components while driving to stop the noise. Most of these incidents can be repaired by apply-
ing felt cloth tape or silicone spray (in hard to reach areas). Urethane pads can be used to insulate wiring har-
ness.
CAUTION:
Do not use silicone spray to isolate a squeak or rattle. If you saturate the area with silicone, you will
not be able to recheck the repair.
CENTER CONSOLE
Components to pay attention to include:
1. Shifter assembly cover to finisher
2. A/C control unit and cluster lid C
3. Wiring harnesses behind audio and A/C control unit
The instrument panel repair and isolation procedures also apply to the center console.
DOORS
Pay attention to the:
1. Finisher and inner panel making a slapping noise
2. Inside handle escutcheon to door finisher
3. Wiring harnesses tapping
4. Door striker out of alignment causing a popping noise on starts and stops
Page 2260 of 3383
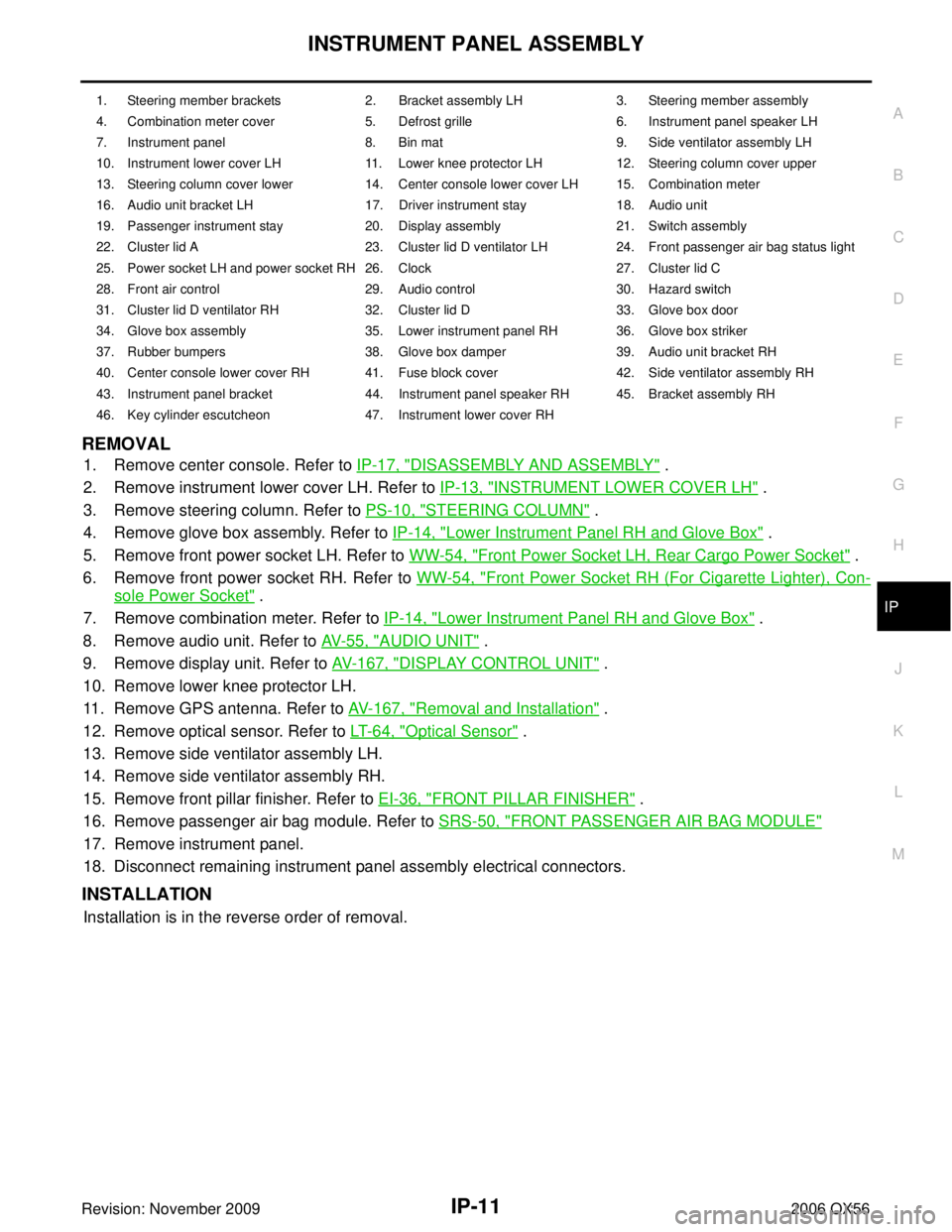
INSTRUMENT PANEL ASSEMBLYIP-11
C
DE
F
G H
J
K L
M A
B
IP
Revision: November 2009 2006 QX56
REMOVAL
1. Remove center console. Refer to IP-17, "DISASSEMBLY AND ASSEMBLY" .
2. Remove instrument lower cover LH. Refer to IP-13, "
INSTRUMENT LOWER COVER LH" .
3. Remove steering column. Refer to PS-10, "
STEERING COLUMN" .
4. Remove glove box assembly. Refer to IP-14, "
Lower Instrument Panel RH and Glove Box" .
5. Remove front power socket LH. Refer to WW-54, "
Front Power Socket LH, Rear Cargo Power Socket" .
6. Remove front power socket RH. Refer to WW-54, "
Front Power Socket RH (For Cigarette Lighter), Con-
sole Power Socket" .
7. Remove combination meter. Refer to IP-14, "
Lower Instrument Panel RH and Glove Box" .
8. Remove audio unit. Refer to AV- 5 5 , "
AUDIO UNIT" .
9. Remove display unit. Refer to AV- 1 6 7 , "
DISPLAY CONTROL UNIT" .
10. Remove lower knee protector LH.
11. Remove GPS antenna. Refer to AV- 1 6 7 , "
Removal and Installation" .
12. Remove optical sensor. Refer to LT- 6 4 , "
Optical Sensor" .
13. Remove side ventilator assembly LH.
14. Remove side ventilator assembly RH.
15. Remove front pillar finisher. Refer to EI-36, "
FRONT PILLAR FINISHER" .
16. Remove passenger air bag module. Refer to SRS-50, "
FRONT PASSENGER AIR BAG MODULE"
17. Remove instrument panel.
18. Disconnect remaining instrument panel assembly electrical connectors.
INSTALLATION
Installation is in the reverse order of removal.
1. Steering member brackets2. Bracket assembly LH3. Steering member assembly
4. Combination meter cover 5. Defrost grille6. Instrument panel speaker LH
7. Instrument panel 8. Bin mat9. Side ventilator assembly LH
10. Instrument lower cover LH 11. Lower knee protector LH12. Steering column cover upper
13. Steering column cover lower 14. Center console lower cover LH 15. Combination meter
16. Audio unit bracket LH 17. Driver instrument stay18. Audio unit
19. Passenger instrument stay 20. Display assembly21. Switch assembly
22. Cluster lid A 23. Cluster lid D ventilator LH24. Front passenger air bag status light
25. Power socket LH and power socket RH 26. Clock 27. Cluster lid C
28. Front air control 29. Audio control30. Hazard switch
31. Cluster lid D ventilator RH 32. Cluster lid D33. Glove box door
34. Glove box assembly 35. Lower instrument panel RH 36. Glove box striker
37. Rubber bumpers 38. Glove box damper39. Audio unit bracket RH
40. Center console lower cover RH 41. Fuse block cover 42. Side ventilator assembly RH
43. Instrument panel bracket 44. Instrument panel speaker RH 45. Bracket assembly RH
46. Key cylinder escutcheon 47. Instrument lower cover RH
Page 2261 of 3383
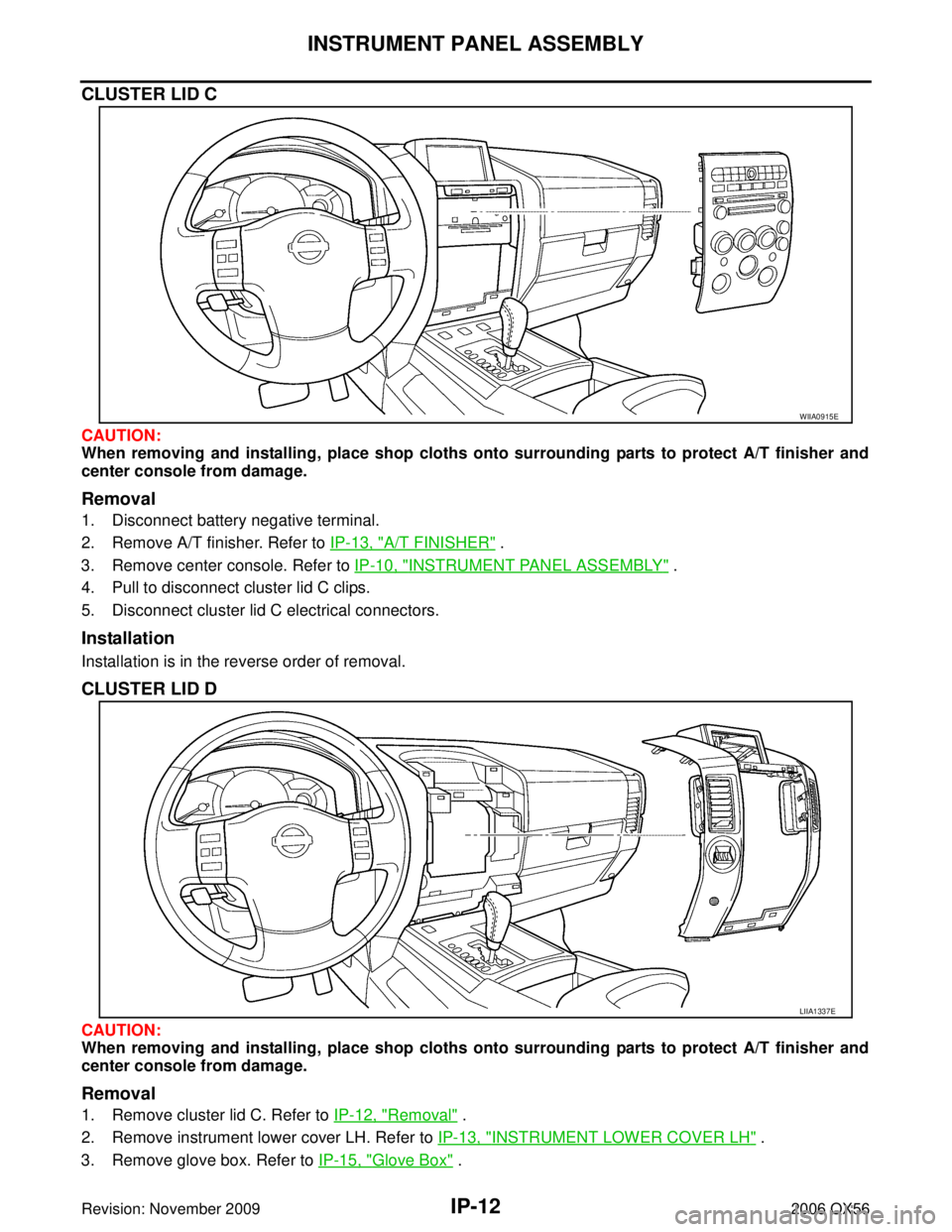
IP-12
INSTRUMENT PANEL ASSEMBLY
Revision: November 20092006 QX56
CLUSTER LID C
CAUTION:
When removing and installing, place shop cloths onto surrounding parts to protect A/T finisher and
center console from damage.
Removal
1. Disconnect battery negative terminal.
2. Remove A/T finisher. Refer to IP-13, "
A/T FINISHER" .
3. Remove center console. Refer to IP-10, "
INSTRUMENT PANEL ASSEMBLY" .
4. Pull to disconnect cluster lid C clips.
5. Disconnect cluster lid C electrical connectors.
Installation
Installation is in the reverse order of removal.
CLUSTER LID D
CAUTION:
When removing and installing, place shop cloths onto surrounding parts to protect A/T finisher and
center console from damage.
Removal
1. Remove cluster lid C. Refer to IP-12, "Removal" .
2. Remove instrument lower cover LH. Refer to IP-13, "
INSTRUMENT LOWER COVER LH" .
3. Remove glove box. Refer to IP-15, "
Glove Box" .
WIIA0915E
LIIA1337E
Page 2265 of 3383
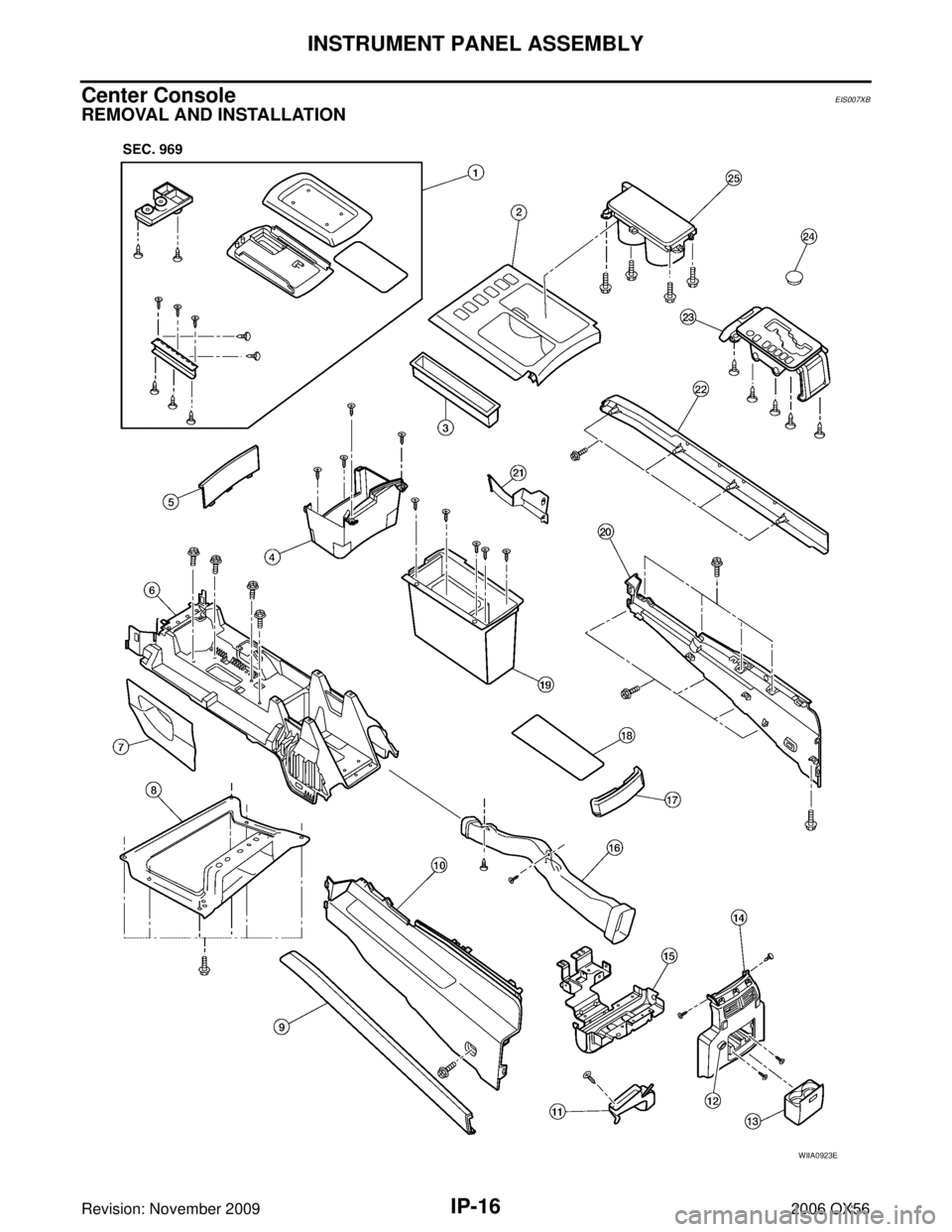
IP-16
INSTRUMENT PANEL ASSEMBLY
Revision: November 20092006 QX56
Center ConsoleEIS007XB
REMOVAL AND INSTALLATION
WIIA0923E
Page 2266 of 3383
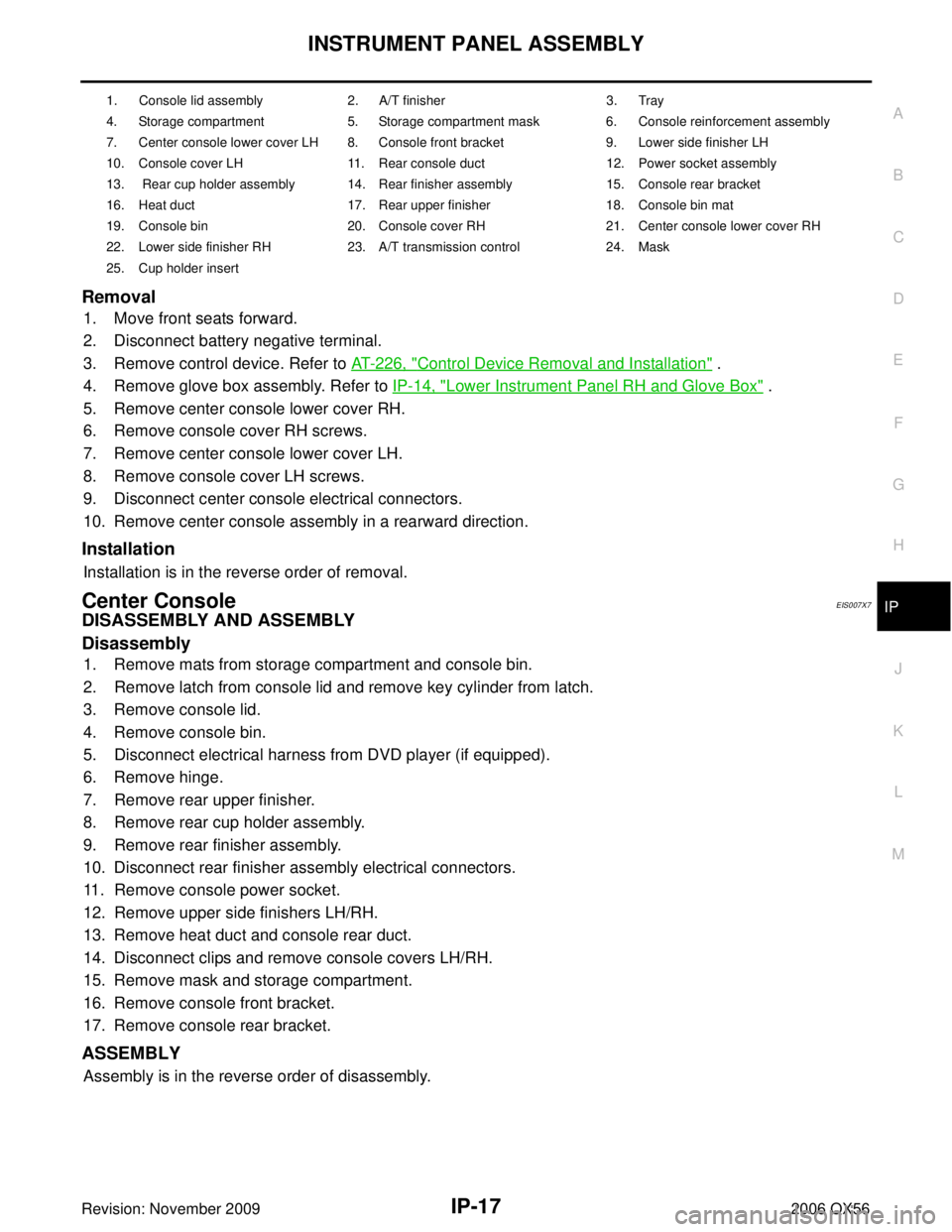
INSTRUMENT PANEL ASSEMBLYIP-17
C
DE
F
G H
J
K L
M A
B
IP
Revision: November 2009 2006 QX56
Removal
1. Move front seats forward.
2. Disconnect battery negative terminal.
3. Remove control device. Refer to AT- 2 2 6 , "
Control Device Removal and Installation" .
4. Remove glove box assembly. Refer to IP-14, "
Lower Instrument Panel RH and Glove Box" .
5. Remove center console lower cover RH.
6. Remove console cover RH screws.
7. Remove center console lower cover LH.
8. Remove console cover LH screws.
9. Disconnect center console electrical connectors.
10. Remove center console assembly in a rearward direction.
Installation
Installation is in the reverse order of removal.
Center ConsoleEIS007X7
DISASSEMBLY AND ASSEMBLY
Disassembly
1. Remove mats from storage compartment and console bin.
2. Remove latch from console lid and remove key cylinder from latch.
3. Remove console lid.
4. Remove console bin.
5. Disconnect electrical harness from DVD player (if equipped).
6. Remove hinge.
7. Remove rear upper finisher.
8. Remove rear cup holder assembly.
9. Remove rear finisher assembly.
10. Disconnect rear finisher assembly electrical connectors.
11. Remove console power socket.
12. Remove upper side finishers LH/RH.
13. Remove heat duct and console rear duct.
14. Disconnect clips and remove console covers LH/RH.
15. Remove mask and storage compartment.
16. Remove console front bracket.
17. Remove console rear bracket.
ASSEMBLY
Assembly is in the reverse order of disassembly.
1. Console lid assembly 2. A/T finisher 3. Tray
4. Storage compartment 5. Storage compartment mask 6. Console reinforcement assembly
7. Center console lower cover LH 8. Console front bracket 9. Lower side finisher LH
10. Console cover LH 11. Rear console duct 12. Power socket assembly
13. Rear cup holder assembly 14. Rear finisher assembly 15. Console rear bracket
16. Heat duct 17. Rear upper finisher 18. Console bin mat
19. Console bin 20. Console cover RH 21. Center console lower cover RH
22. Lower side finisher RH 23. A/T transmission control 24. Mask
25. Cup holder insert
Page 2635 of 3383
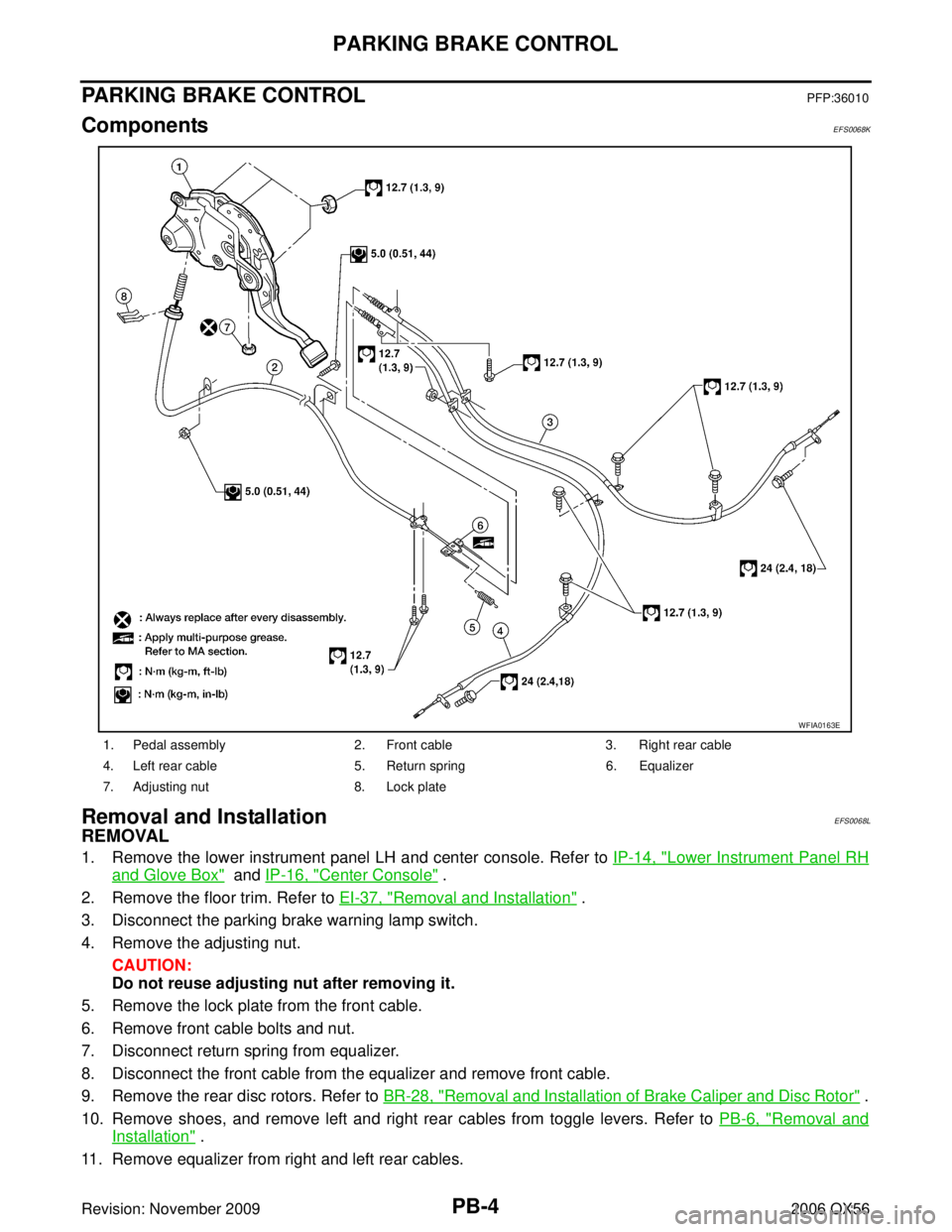
PB-4
PARKING BRAKE CONTROL
Revision: November 20092006 QX56
PARKING BRAKE CONTROLPFP:36010
ComponentsEFS0068K
Removal and InstallationEFS0068L
REMOVAL
1. Remove the lower instrument panel LH and center console. Refer to IP-14, "Lower Instrument Panel RH
and Glove Box" and IP-16, "Center Console" .
2. Remove the floor trim. Refer to EI-37, "
Removal and Installation" .
3. Disconnect the parking brake warning lamp switch.
4. Remove the adjusting nut. CAUTION:
Do not reuse adjusting nut after removing it.
5. Remove the lock plate from the front cable.
6. Remove front cable bolts and nut.
7. Disconnect return spring from equalizer.
8. Disconnect the front cable from the equalizer and remove front cable.
9. Remove the rear disc rotors. Refer to BR-28, "
Removal and Installation of Brake Caliper and Disc Rotor" .
10. Remove shoes, and remove left and right rear cables from toggle levers. Refer to PB-6, "
Removal and
Installation" .
11. Remove equalizer from right and left rear cables.
1. Pedal assembly 2. Front cable 3. Right rear cable
4. Left rear cable 5. Return spring 6. Equalizer
7. Adjusting nut 8. Lock plate
WFIA0163E
Page 2776 of 3383
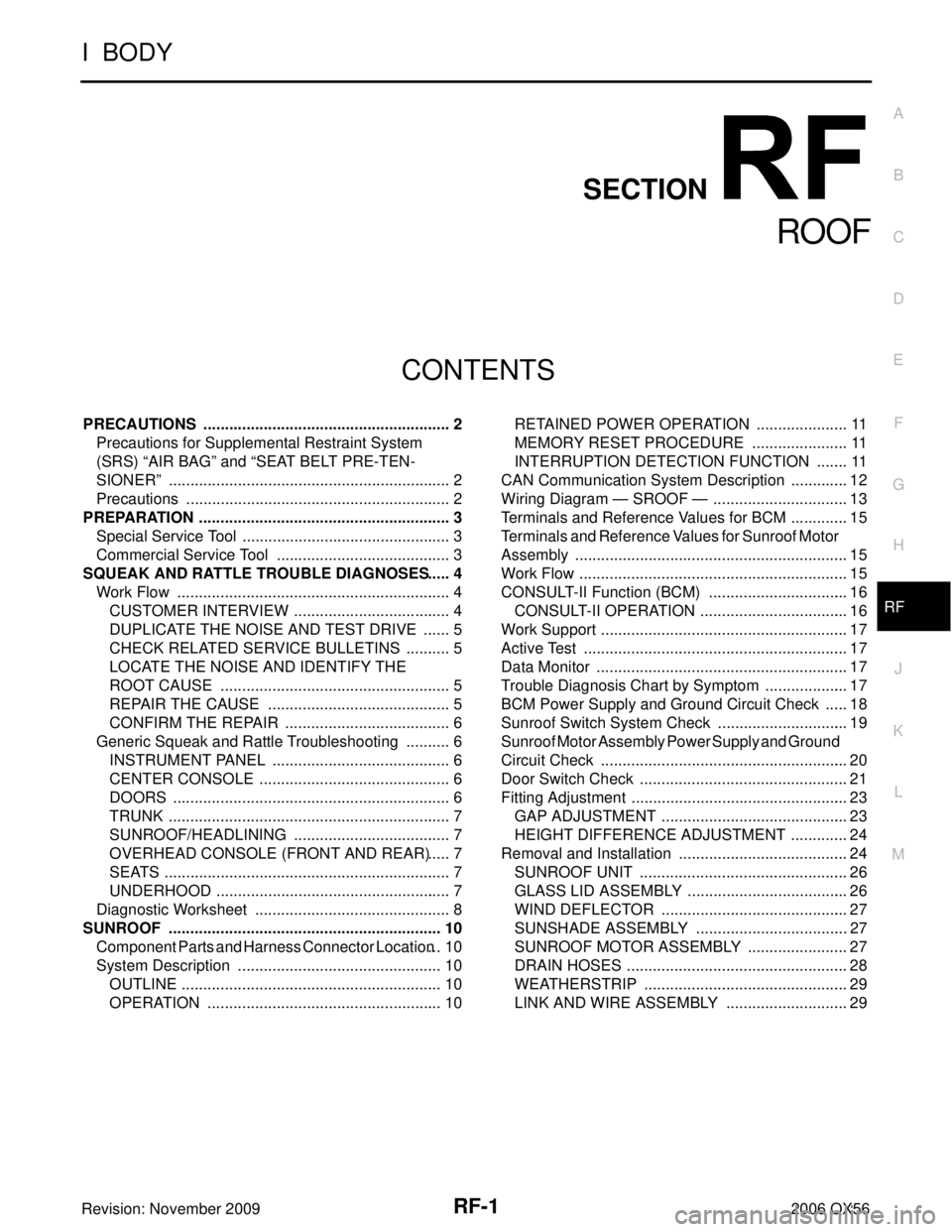
RF-1
ROOF
I BODY
CONTENTS
C
DE
F
G H
J
K L
M
SECTION
A
B
RF
Revision: November 2009 2006 QX56
PRECAUTIONS .....................................................
..... 2
Precautions for Supplemental Restraint System
(SRS) “AIR BAG” and “SEAT BELT PRE-TEN-
SIONER” ............................................................. ..... 2
Precautions ......................................................... ..... 2
PREPARATION ...................................................... ..... 3
Special Service Tool ............................................ ..... 3
Commercial Service Tool .................................... ..... 3
SQUEAK AND RATTLE TROUBLE DIAGNOSES ..... 4
Work Flow ................................................................ 4 CUSTOMER INTERVIEW ................................ ..... 4
DUPLICATE THE NOISE AND TEST DRIVE .. ..... 5
CHECK RELATED SERVICE BULLETINS ...... ..... 5
LOCATE THE NOISE AND IDENTIFY THE
ROOT CAUSE ................................................. ..... 5
REPAIR THE CAUSE ...................................... ..... 5
CONFIRM THE REPAIR .................................. ..... 6
Generic Squeak and Rattle Troubleshooting ...... ..... 6
INSTRUMENT PANEL ..................................... ..... 6
CENTER CONSOLE ........................................ ..... 6
DOORS ............................................................ ..... 6
TRUNK ............................................................. ..... 7
SUNROOF/HEADLINING ................................ ..... 7
OVERHEAD CONSOLE (FRONT AND REAR) ..... 7
SEATS .............................................................. ..... 7
UNDERHOOD .................................................. ..... 7
Diagnostic Worksheet ......................................... ..... 8
SUNROOF ............................................................. ... 10
Component Parts and Harness Connector Location ... 10
System Description ............................................. ... 10
OUTLINE .......................................................... ... 10
OPERATION .................................................... ... 10RETAINED POWER OPERATION ...................
... 11
MEMORY RESET PROCEDURE .................... ... 11
INTERRUPTION DETECTION FUNCTION ..... ... 11
CAN Communication System Description ........... ... 12
Wiring Diagram — SROOF — ................................ 13
Terminals and Reference Values for BCM ........... ... 15
Terminals and Reference Values for Sunroof Motor
Assembly ............................................................. ... 15
Work Flow ............................................................... 15
CONSULT-II Function (BCM) .............................. ... 16
CONSULT-II OPERATION ................................ ... 16
Work Support ....................................................... ... 17
Active Test .............................................................. 17
Data Monitor ........................................................... 17
Trouble Diagnosis Chart by Symptom ................. ... 17
BCM Power Supply and Ground Circuit Check ... ... 18
Sunroof Switch System Check ............................ ... 19
Sunroof Motor Assembly Power Supply and Ground
Circuit Check ....................................................... ... 20
Door Switch Check ................................................. 21
Fitting Adjustment ................................................ ... 23
GAP ADJUSTMENT ......................................... ... 23
HEIGHT DIFFERENCE ADJUSTMENT ........... ... 24
Removal and Installation ..................................... ... 24
SUNROOF UNIT .............................................. ... 26
GLASS LID ASSEMBLY ................................... ... 26
WIND DEFLECTOR ......................................... ... 27
SUNSHADE ASSEMBLY .................................... 27
SUNROOF MOTOR ASSEMBLY ..................... ... 27
DRAIN HOSES ................................................. ... 28
WEATHERSTRIP ............................................. ... 29
LINK AND WIRE ASSEMBLY .......................... ... 29
Page 2781 of 3383
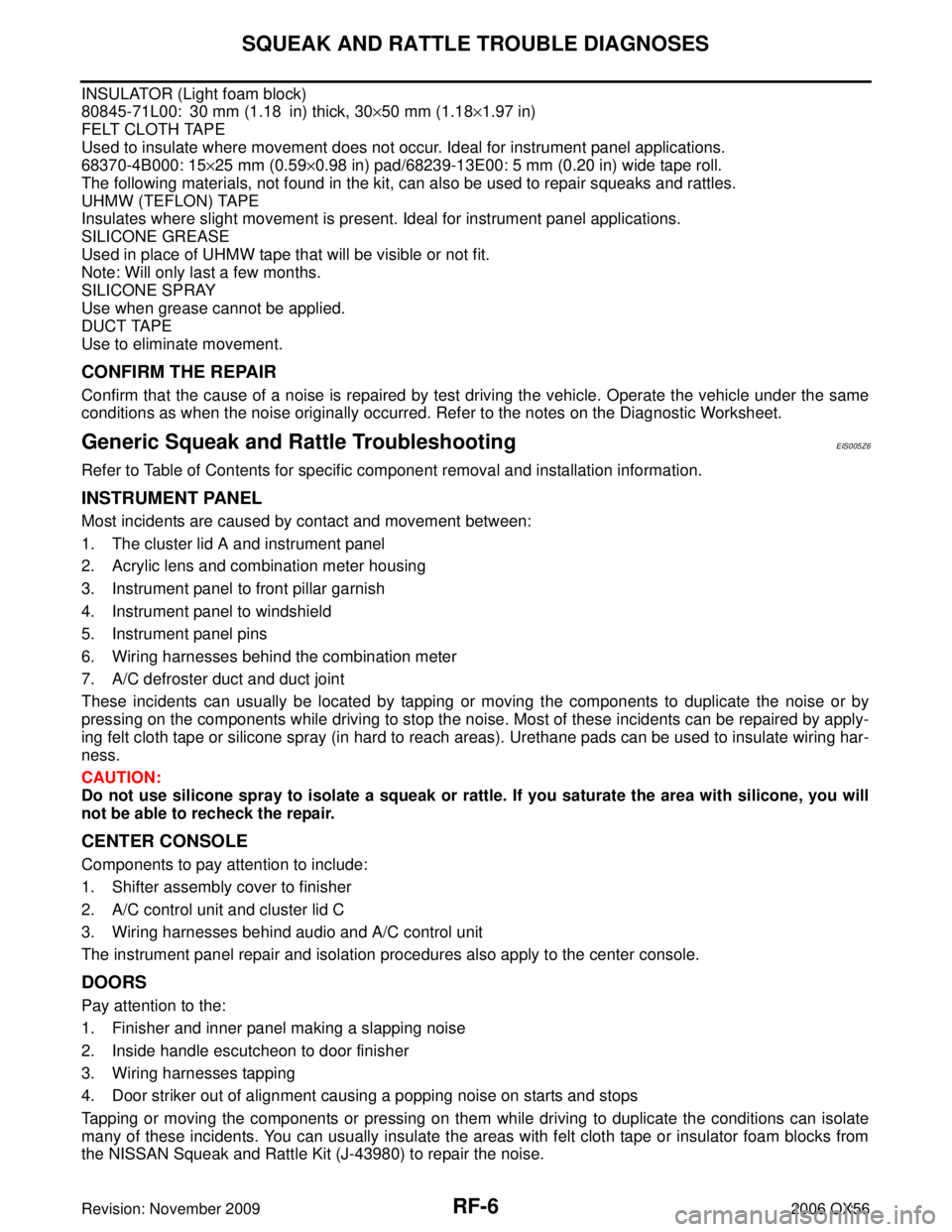
RF-6
SQUEAK AND RATTLE TROUBLE DIAGNOSES
Revision: November 20092006 QX56
INSULATOR (Light foam block)
80845-71L00: 30 mm (1.18 in) thick, 30×50 mm (1.18 ×1.97 in)
FELT CLOTH TAPE
Used to insulate where movement does not occur. Ideal for instrument panel applications.
68370-4B000: 15 ×25 mm (0.59 ×0.98 in) pad/68239-13E00: 5 mm (0.20 in) wide tape roll.
The following materials, not found in the kit, can also be used to repair squeaks and rattles.
UHMW (TEFLON) TAPE
Insulates where slight movement is present. Ideal for instrument panel applications.
SILICONE GREASE
Used in place of UHMW tape that will be visible or not fit.
Note: Will only last a few months.
SILICONE SPRAY
Use when grease cannot be applied.
DUCT TAPE
Use to eliminate movement.
CONFIRM THE REPAIR
Confirm that the cause of a noise is repaired by test driving the vehicle. Operate the vehicle under the same
conditions as when the noise originally occurred. Refer to the notes on the Diagnostic Worksheet.
Generic Squeak and Rattle TroubleshootingEIS005Z6
Refer to Table of Contents for specific component removal and installation information.
INSTRUMENT PANEL
Most incidents are caused by contact and movement between:
1. The cluster lid A and instrument panel
2. Acrylic lens and combination meter housing
3. Instrument panel to front pillar garnish
4. Instrument panel to windshield
5. Instrument panel pins
6. Wiring harnesses behind the combination meter
7. A/C defroster duct and duct joint
These incidents can usually be located by tapping or moving the components to duplicate the noise or by
pressing on the components while driving to stop the noise. Most of these incidents can be repaired by apply-
ing felt cloth tape or silicone spray (in hard to reach areas). Urethane pads can be used to insulate wiring har-
ness.
CAUTION:
Do not use silicone spray to isolate a squeak or rattle. If you saturate the area with silicone, you will
not be able to recheck the repair.
CENTER CONSOLE
Components to pay attention to include:
1. Shifter assembly cover to finisher
2. A/C control unit and cluster lid C
3. Wiring harnesses behind audio and A/C control unit
The instrument panel repair and isolation procedures also apply to the center console.
DOORS
Pay attention to the:
1. Finisher and inner panel making a slapping noise
2. Inside handle escutcheon to door finisher
3. Wiring harnesses tapping
4. Door striker out of alignment causing a popping noise on starts and stops
Tapping or moving the components or pressing on them while driving to duplicate the conditions can isolate
many of these incidents. You can usually insulate the areas with felt cloth tape or insulator foam blocks from
the NISSAN Squeak and Rattle Kit (J-43980) to repair the noise.
Page 2802 of 3383
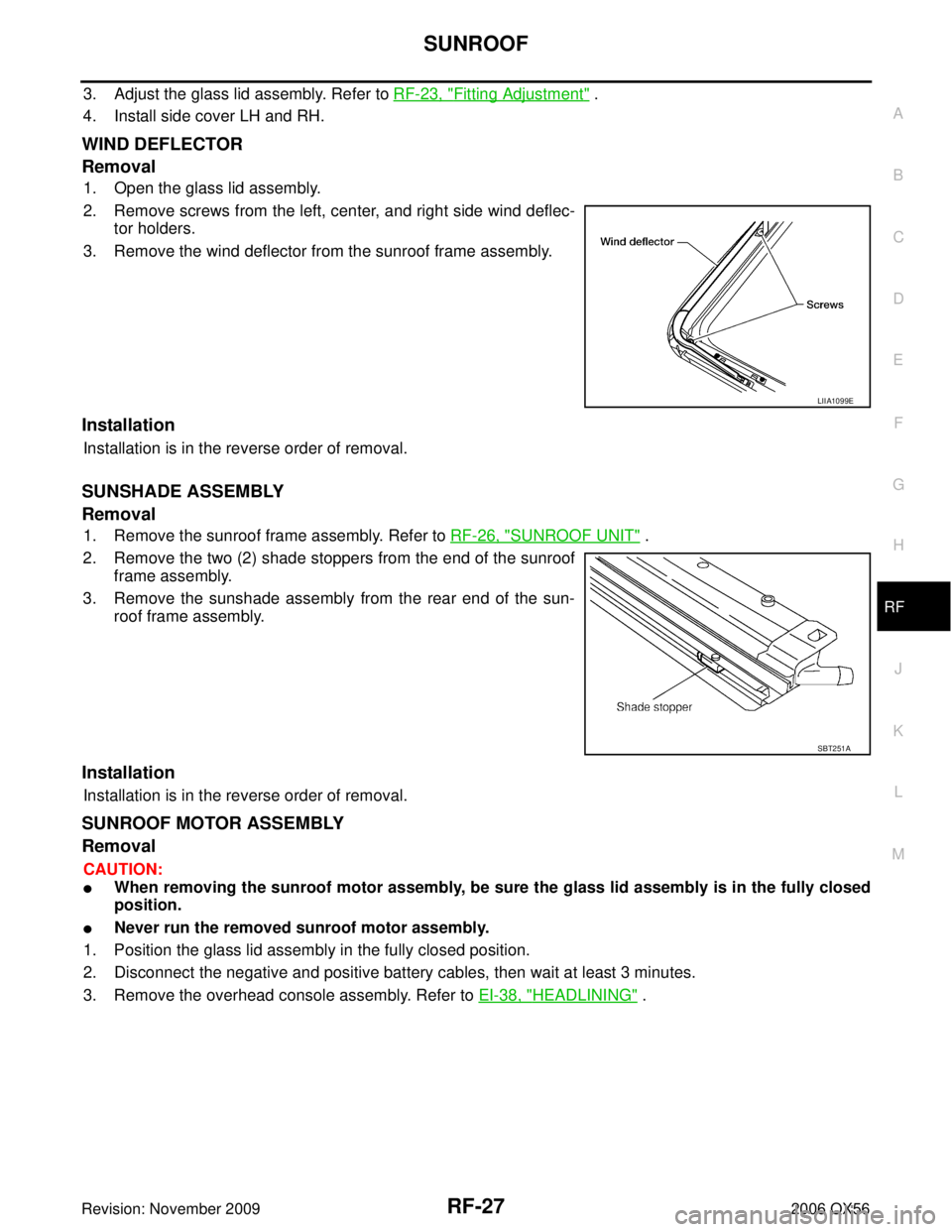
SUNROOFRF-27
C
DE
F
G H
J
K L
M A
B
RF
Revision: November 2009 2006 QX56
3. Adjust the glass lid assembly. Refer to RF-23, "Fitting Adjustment" .
4. Install side cover LH and RH.
WIND DEFLECTOR
Removal
1. Open the glass lid assembly.
2. Remove screws from the left, center, and right side wind deflec- tor holders.
3. Remove the wind deflector from the sunroof frame assembly.
Installation
Installation is in the reverse order of removal.
SUNSHADE ASSEMBLY
Removal
1. Remove the sunroof frame assembly. Refer to RF-26, "SUNROOF UNIT" .
2. Remove the two (2) shade stoppers from the end of the sunroof frame assembly.
3. Remove the sunshade assembly from the rear end of the sun- roof frame assembly.
Installation
Installation is in the reverse order of removal.
SUNROOF MOTOR ASSEMBLY
Removal
CAUTION:
When removing the sunroof motor assembly, be sure the glass lid assembly is in the fully closed
position.
Never run the removed sunroof motor assembly.
1. Position the glass lid assembly in the fully closed position.
2. Disconnect the negative and positive battery cables, then wait at least 3 minutes.
3. Remove the overhead console assembly. Refer to EI-38, "
HEADLINING" .
LIIA1099E
SBT251A
Page 2932 of 3383
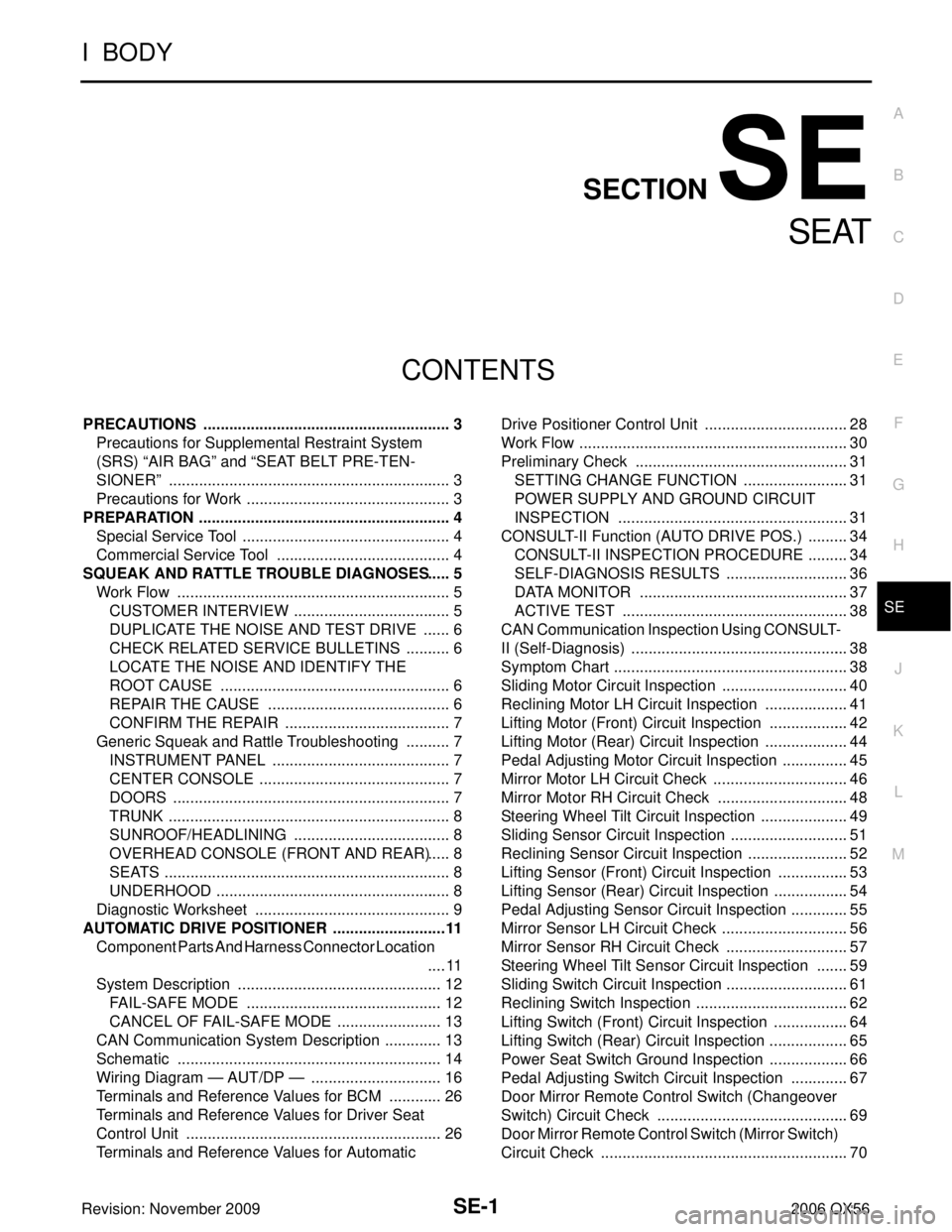
SE-1
SEAT
I BODY
CONTENTS
C
DE
F
G H
J
K L
M
SECTION
A
B
SE
Revision: November 2009 2006 QX56
PRECAUTIONS .....................................................
..... 3
Precautions for Supplemental Restraint System
(SRS) “AIR BAG” and “SEAT BELT PRE-TEN-
SIONER” ............................................................. ..... 3
Precautions for Work ........................................... ..... 3
PREPARATION ...................................................... ..... 4
Special Service Tool ............................................ ..... 4
Commercial Service Tool .................................... ..... 4
SQUEAK AND RATTLE TROUBLE DIAGNOSES ..... 5
Work Flow ................................................................ 5 CUSTOMER INTERVIEW ................................ ..... 5
DUPLICATE THE NOISE AND TEST DRIVE .. ..... 6
CHECK RELATED SERVICE BULLETINS ...... ..... 6
LOCATE THE NOISE AND IDENTIFY THE
ROOT CAUSE ................................................. ..... 6
REPAIR THE CAUSE ...................................... ..... 6
CONFIRM THE REPAIR .................................. ..... 7
Generic Squeak and Rattle Troubleshooting ...... ..... 7
INSTRUMENT PANEL ..................................... ..... 7
CENTER CONSOLE ........................................ ..... 7
DOORS ............................................................ ..... 7
TRUNK ............................................................. ..... 8
SUNROOF/HEADLINING ................................ ..... 8
OVERHEAD CONSOLE (FRONT AND REAR) ..... 8
SEATS .............................................................. ..... 8
UNDERHOOD .................................................. ..... 8
Diagnostic Worksheet ......................................... ..... 9
AUTOMATIC DRIVE POSITIONER ....................... ....11
Component Parts And Harness Connector Location .... 11
System Description ............................................. ... 12
FAIL-SAFE MODE ........................................... ... 12
CANCEL OF FAIL-SAFE MODE ...................... ... 13
CAN Communication System Description ........... ... 13
Schematic ........................................................... ... 14
Wiring Diagram — AUT/DP — ............................ ... 16
Terminals and Reference Values for BCM .......... ... 26
Terminals and Reference Values for Driver Seat
Control Unit ......................................................... ... 26
Terminals and Reference Values for Automatic Drive Positioner Control Unit ...............................
... 28
Work Flow ............................................................... 30
Preliminary Check ............................................... ... 31
SETTING CHANGE FUNCTION ...................... ... 31
POWER SUPPLY AND GROUND CIRCUIT
INSPECTION ................................................... ... 31
CONSULT-II Function (AUTO DRIVE POS.) ....... ... 34
CONSULT-II INSPECTION PROCEDURE ....... ... 34
SELF-DIAGNOSIS RESULTS .......................... ... 36
DATA MONITOR .............................................. ... 37
ACTIVE TEST ..................................................... 38
CAN Communication Inspection Using CONSULT-
II (Self-Diagnosis) ................................................ ... 38
Symptom Chart ....................................................... 38
Sliding Motor Circuit Inspection ........................... ... 40
Reclining Motor LH Circuit Inspection ................. ... 41
Lifting Motor (Front) Circuit Inspection ................ ... 42
Lifting Motor (Rear) Circuit Inspection ................. ... 44
Pedal Adjusting Motor Circuit Inspection ............. ... 45
Mirror Motor LH Circuit Check ................................ 46
Mirror Motor RH Circuit Check ............................ ... 48
Steering Wheel Tilt Circuit Inspection .................. ... 49
Sliding Sensor Circuit Inspection ......................... ... 51
Reclining Sensor Circuit Inspection ..................... ... 52
Lifting Sensor (Front) Circuit Inspection .............. ... 53
Lifting Sensor (Rear) Circuit Inspection ............... ... 54
Pedal Adjusting Sensor Circuit Inspection ........... ... 55
Mirror Sensor LH Circuit Check ........................... ... 56
Mirror Sensor RH Circuit Check ............................. 57
Steering Wheel Tilt Sensor Circuit Inspection ..... ... 59
Sliding Switch Circuit Inspection .......................... ... 61
Reclining Switch Inspection ................................. ... 62
Lifting Switch (Front) Circuit Inspection ............... ... 64
Lifting Switch (Rear) Circuit Inspection ................ ... 65
Power Seat Switch Ground Inspection ................ ... 66
Pedal Adjusting Switch Circuit Inspection ........... ... 67
Door Mirror Remote Control Switch (Changeover
Switch) Circuit Check ............................................. 69
Door Mirror Remote Control Switch (Mirror Switch)
Circuit Check ....................................................... ... 70