Head light INFINITI QX56 2007 Factory Workshop Manual
[x] Cancel search | Manufacturer: INFINITI, Model Year: 2007, Model line: QX56, Model: INFINITI QX56 2007Pages: 3061, PDF Size: 64.56 MB
Page 2295 of 3061
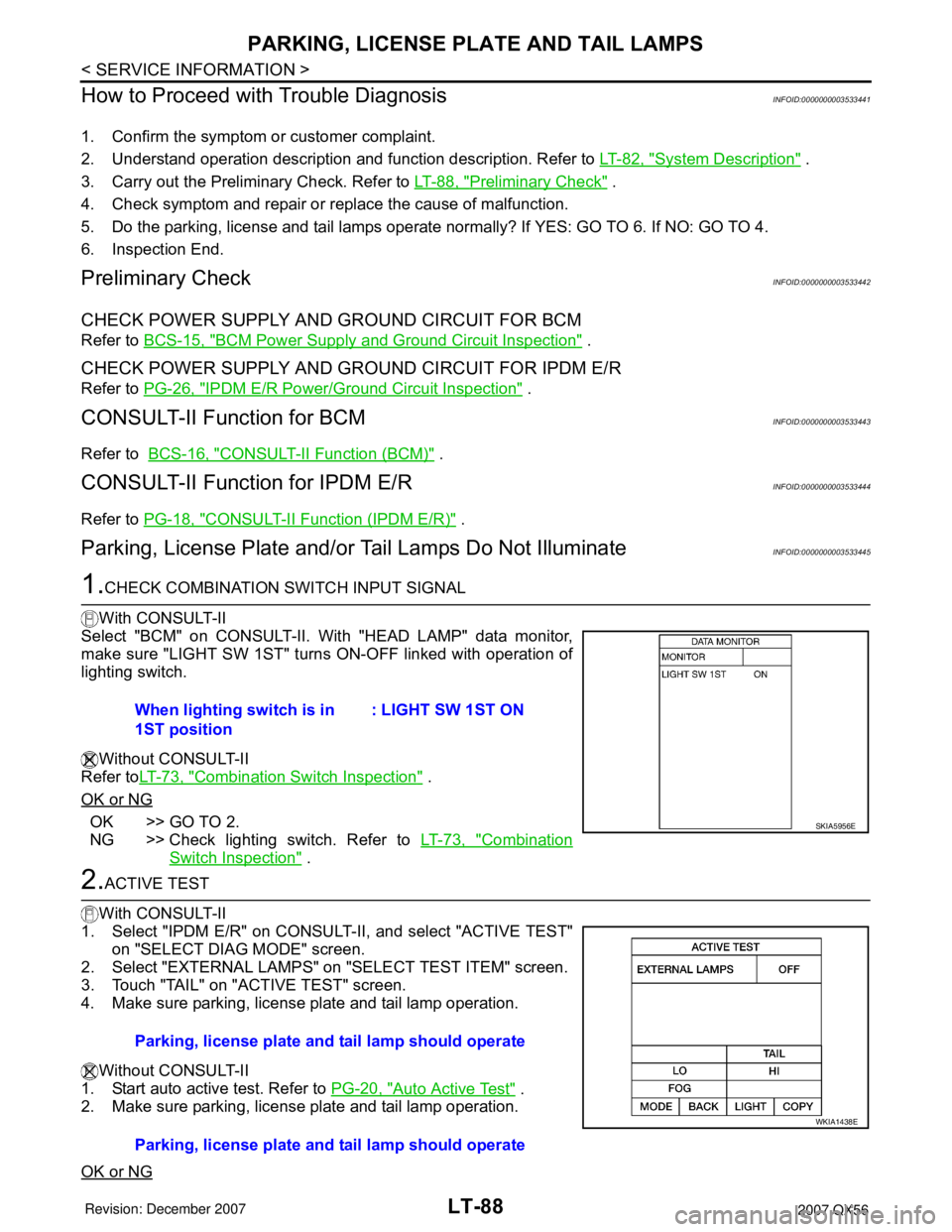
LT-88
< SERVICE INFORMATION >
PARKING, LICENSE PLATE AND TAIL LAMPS
How to Proceed with Trouble Diagnosis
INFOID:0000000003533441
1. Confirm the symptom or customer complaint.
2. Understand operation description and function description. Refer to LT-82, "
System Description" .
3. Carry out the Preliminary Check. Refer to LT-88, "
Preliminary Check" .
4. Check symptom and repair or replace the cause of malfunction.
5. Do the parking, license and tail lamps operate normally? If YES: GO TO 6. If NO: GO TO 4.
6. Inspection End.
Preliminary CheckINFOID:0000000003533442
CHECK POWER SUPPLY AND GROUND CIRCUIT FOR BCM
Refer to BCS-15, "BCM Power Supply and Ground Circuit Inspection" .
CHECK POWER SUPPLY AND GROUND CIRCUIT FOR IPDM E/R
Refer to PG-26, "IPDM E/R Power/Ground Circuit Inspection" .
CONSULT-II Function for BCMINFOID:0000000003533443
Refer to BCS-16, "CONSULT-II Function (BCM)" .
CONSULT-II Function for IPDM E/RINFOID:0000000003533444
Refer to PG-18, "CONSULT-II Function (IPDM E/R)" .
Parking, License Plate and/or Tail Lamps Do Not IlluminateINFOID:0000000003533445
1.CHECK COMBINATION SWITCH INPUT SIGNAL
With CONSULT-II
Select "BCM" on CONSULT-II. With "HEAD LAMP" data monitor,
make sure "LIGHT SW 1ST" turns ON-OFF linked with operation of
lighting switch.
Without CONSULT-II
Refer toLT-73, "
Combination Switch Inspection" .
OK or NG
OK >> GO TO 2.
NG >> Check lighting switch. Refer to LT-73, "
Combination
Switch Inspection" .
2.ACTIVE TEST
With CONSULT-II
1. Select "IPDM E/R" on CONSULT-II, and select "ACTIVE TEST"
on "SELECT DIAG MODE" screen.
2. Select "EXTERNAL LAMPS" on "SELECT TEST ITEM" screen.
3. Touch "TAIL" on "ACTIVE TEST" screen.
4. Make sure parking, license plate and tail lamp operation.
Without CONSULT-II
1. Start auto active test. Refer to PG-20, "
Auto Active Test" .
2. Make sure parking, license plate and tail lamp operation.
OK or NG
When lighting switch is in
1ST position: LIGHT SW 1ST ON
SKIA5956E
Parking, license plate and tail lamp should operate
Parking, license plate and tail lamp should operate
WKIA1438E
Page 2302 of 3061
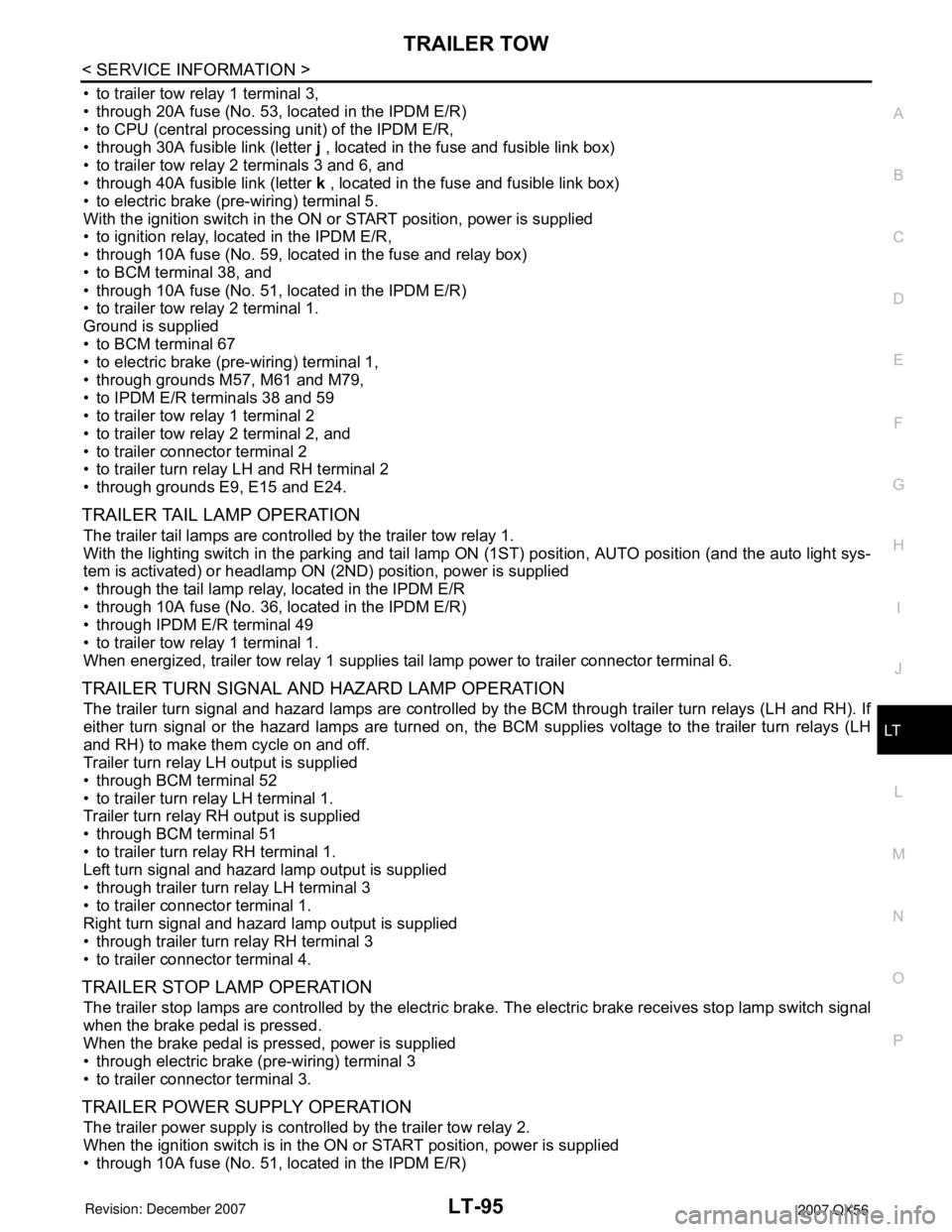
TRAILER TOW
LT-95
< SERVICE INFORMATION >
C
D
E
F
G
H
I
J
L
MA
B
LT
N
O
P
• to trailer tow relay 1 terminal 3,
• through 20A fuse (No. 53, located in the IPDM E/R)
• to CPU (central processing unit) of the IPDM E/R,
• through 30A fusible link (letter j , located in the fuse and fusible link box)
• to trailer tow relay 2 terminals 3 and 6, and
• through 40A fusible link (letter k , located in the fuse and fusible link box)
• to electric brake (pre-wiring) terminal 5.
With the ignition switch in the ON or START position, power is supplied
• to ignition relay, located in the IPDM E/R,
• through 10A fuse (No. 59, located in the fuse and relay box)
• to BCM terminal 38, and
• through 10A fuse (No. 51, located in the IPDM E/R)
• to trailer tow relay 2 terminal 1.
Ground is supplied
• to BCM terminal 67
• to electric brake (pre-wiring) terminal 1,
• through grounds M57, M61 and M79,
• to IPDM E/R terminals 38 and 59
• to trailer tow relay 1 terminal 2
• to trailer tow relay 2 terminal 2, and
• to trailer connector terminal 2
• to trailer turn relay LH and RH terminal 2
• through grounds E9, E15 and E24.
TRAILER TAIL LAMP OPERATION
The trailer tail lamps are controlled by the trailer tow relay 1.
With the lighting switch in the parking and tail lamp ON (1ST) position, AUTO position (and the auto light sys-
tem is activated) or headlamp ON (2ND) position, power is supplied
• through the tail lamp relay, located in the IPDM E/R
• through 10A fuse (No. 36, located in the IPDM E/R)
• through IPDM E/R terminal 49
• to trailer tow relay 1 terminal 1.
When energized, trailer tow relay 1 supplies tail lamp power to trailer connector terminal 6.
TRAILER TURN SIGNAL AND HAZARD LAMP OPERATION
The trailer turn signal and hazard lamps are controlled by the BCM through trailer turn relays (LH and RH). If
either turn signal or the hazard lamps are turned on, the BCM supplies voltage to the trailer turn relays (LH
and RH) to make them cycle on and off.
Trailer turn relay LH output is supplied
• through BCM terminal 52
• to trailer turn relay LH terminal 1.
Trailer turn relay RH output is supplied
• through BCM terminal 51
• to trailer turn relay RH terminal 1.
Left turn signal and hazard lamp output is supplied
• through trailer turn relay LH terminal 3
• to trailer connector terminal 1.
Right turn signal and hazard lamp output is supplied
• through trailer turn relay RH terminal 3
• to trailer connector terminal 4.
TRAILER STOP LAMP OPERATION
The trailer stop lamps are controlled by the electric brake. The electric brake receives stop lamp switch signal
when the brake pedal is pressed.
When the brake pedal is pressed, power is supplied
• through electric brake (pre-wiring) terminal 3
• to trailer connector terminal 3.
TRAILER POWER SUPPLY OPERATION
The trailer power supply is controlled by the trailer tow relay 2.
When the ignition switch is in the ON or START position, power is supplied
• through 10A fuse (No. 51, located in the IPDM E/R)
Page 2328 of 3061
![INFINITI QX56 2007 Factory Workshop Manual ILLUMINATION
LT-121
< SERVICE INFORMATION >
C
D
E
F
G
H
I
J
L
MA
B
LT
N
O
P
• to BCM terminal 38, and
• through 10A fuse [No. 14, located in the fuse block (J/B)]
• to combination meter terminal INFINITI QX56 2007 Factory Workshop Manual ILLUMINATION
LT-121
< SERVICE INFORMATION >
C
D
E
F
G
H
I
J
L
MA
B
LT
N
O
P
• to BCM terminal 38, and
• through 10A fuse [No. 14, located in the fuse block (J/B)]
• to combination meter terminal](/img/42/57029/w960_57029-2327.png)
ILLUMINATION
LT-121
< SERVICE INFORMATION >
C
D
E
F
G
H
I
J
L
MA
B
LT
N
O
P
• to BCM terminal 38, and
• through 10A fuse [No. 14, located in the fuse block (J/B)]
• to combination meter terminal 24.
Ground is supplied
• to BCM terminal 67
• to combination meter terminal 17
• through grounds M57, M61 and M79, and
• to IPDM E/R terminals 38 and 59
• through grounds E9, E15 and E24.
ILLUMINATION OPERATION BY LIGHTING SWITCH
With the lighting switch in the 1ST or 2ND position (or if the auto light system is activated), the BCM receives
input signal requesting the illumination lamps to illuminate. This input signal is communicated to the IPDM E/R
across the CAN communication lines. The CPU of the IPDM E/R controls the tail lamp relay coil, which, when
energized, directs power
• through 10A fuse (No. 36, located in the IPDM E/R)
• through IPDM E/R terminal 49
• to illumination control switch terminal 1
• to power liftgate switch terminal 3
• to front room/map lamp assembly (console box illumination) terminal 7
• to hazard switch terminal 3
• to rear sonar system OFF switch terminal 3
• to glove box lamp terminal 1
• to door mirror remote control switch terminal 16
• to display control unit terminal 14
• to power window and door lock/unlock switch RH terminal 5 (early production)
• to main power window and door lock/unlock switch LH terminal 16 (early production)
• to 4WD shift switch terminal 7 (with 4-wheel drive)
• to front air control terminal 23
• to rear power vent window switch terminal 5
• to DVD player terminal 12 (with DVD entertainment system)
• to NAVI control unit terminal 61
• to pedal adjusting switch terminal 5
• to electric brake (pre-wiring) terminal 4 (with trailer tow)
• to front and rear heated seat switch LH and RH terminal 5
• to A/T device terminal 11
• to VDC OFF switch terminal 3
• to tow mode switch terminal 3
• to headlamp aiming switch terminal 3
• to clock terminal 3, and
• through 10A fuse (No. 37, located in the IPDM E/R)
• through IPDM E/R terminal 57
• to AV switch terminal 3
• to audio unit terminal 8
• to rear air control terminal 1 and
• to rear audio remote control unit terminal 6.
The illumination control switch controls illumination intensity by varying the ground to the following
• through illumination control switch terminal 2
• to power liftgate switch terminal 4
• to front room/map lamp assembly (console box illumination) terminal 8
• to AV switch terminal 4
• to hazard switch terminal 4
• to audio unit terminal 7
• to rear sonar system OFF switch terminal 4
• to power window and door lock/unlock switch RH terminal 1 (early production)
• to main power window and door lock/unlock switch LH terminal 12 (early production)
• to 4WD switch terminal 8 (with 4-wheel drive)
• to front air control terminal 24
• to rear power vent window switch terminal 6
• to DVD player terminal 10 (with DVD entertainment system)
• to pedal adjusting switch terminal 6
• to A/T device terminal 12
Page 2329 of 3061
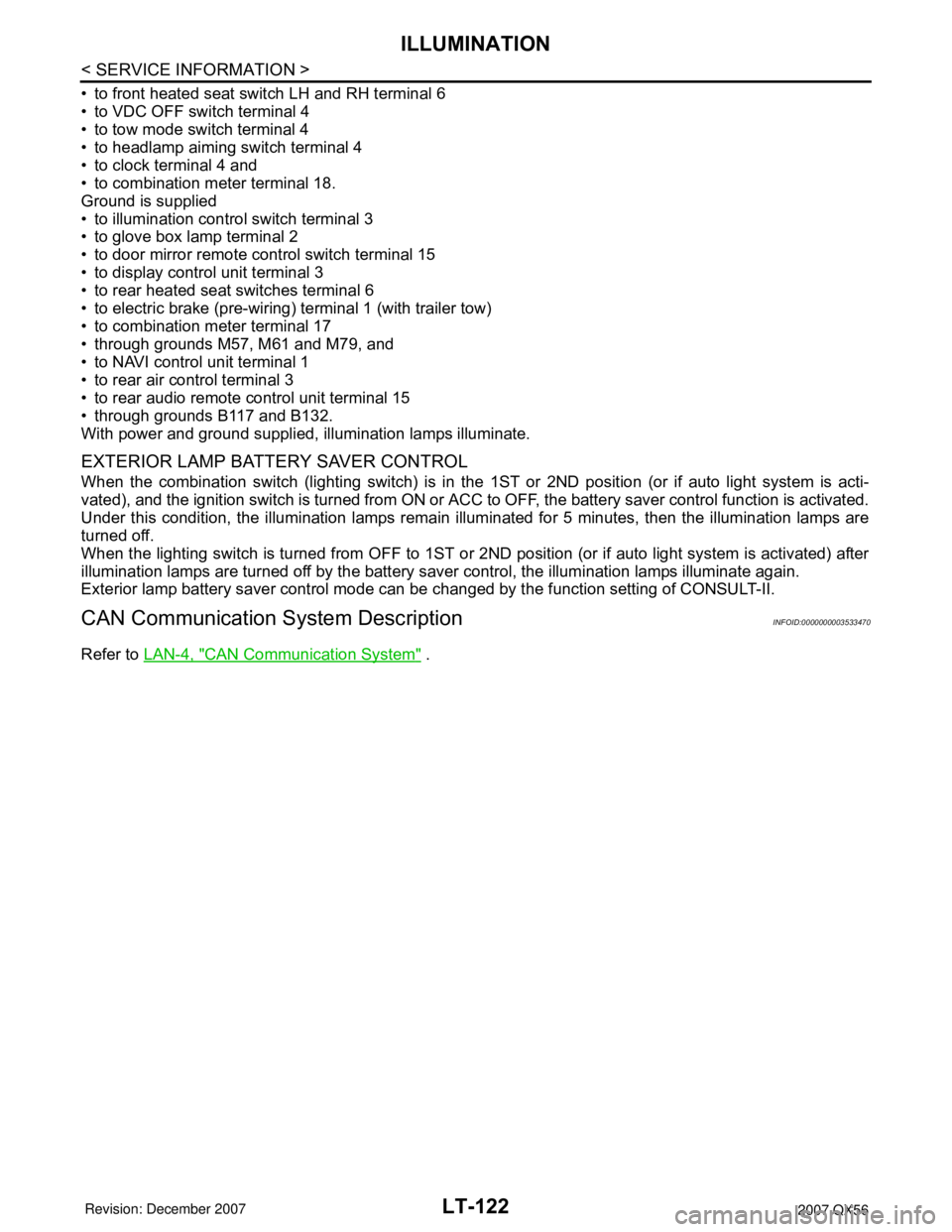
LT-122
< SERVICE INFORMATION >
ILLUMINATION
• to front heated seat switch LH and RH terminal 6
• to VDC OFF switch terminal 4
• to tow mode switch terminal 4
• to headlamp aiming switch terminal 4
• to clock terminal 4 and
• to combination meter terminal 18.
Ground is supplied
• to illumination control switch terminal 3
• to glove box lamp terminal 2
• to door mirror remote control switch terminal 15
• to display control unit terminal 3
• to rear heated seat switches terminal 6
• to electric brake (pre-wiring) terminal 1 (with trailer tow)
• to combination meter terminal 17
• through grounds M57, M61 and M79, and
• to NAVI control unit terminal 1
• to rear air control terminal 3
• to rear audio remote control unit terminal 15
• through grounds B117 and B132.
With power and ground supplied, illumination lamps illuminate.
EXTERIOR LAMP BATTERY SAVER CONTROL
When the combination switch (lighting switch) is in the 1ST or 2ND position (or if auto light system is acti-
vated), and the ignition switch is turned from ON or ACC to OFF, the battery saver control function is activated.
Under this condition, the illumination lamps remain illuminated for 5 minutes, then the illumination lamps are
turned off.
When the lighting switch is turned from OFF to 1ST or 2ND position (or if auto light system is activated) after
illumination lamps are turned off by the battery saver control, the illumination lamps illuminate again.
Exterior lamp battery saver control mode can be changed by the function setting of CONSULT-II.
CAN Communication System DescriptionINFOID:0000000003533470
Refer to LAN-4, "CAN Communication System" .
Page 2424 of 3061
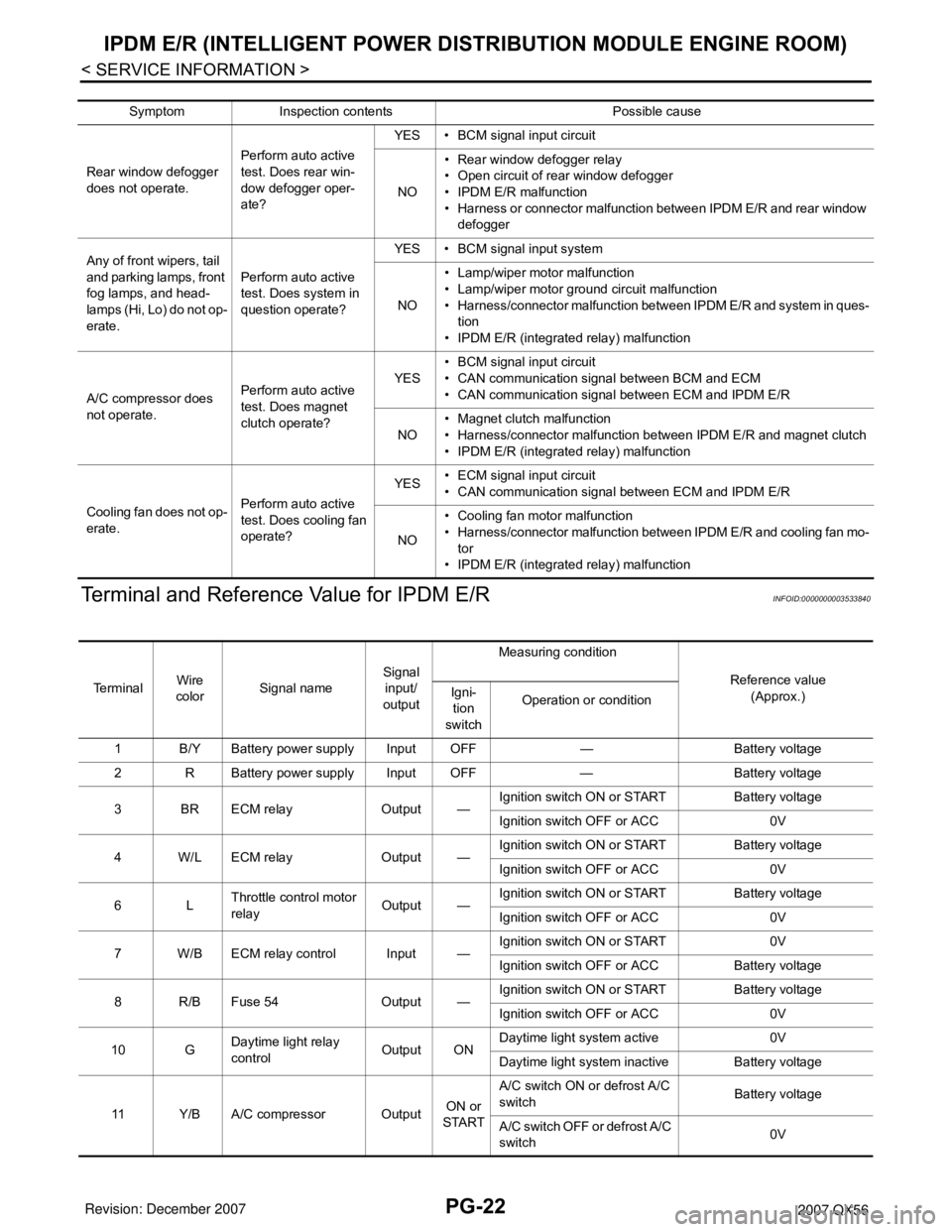
PG-22
< SERVICE INFORMATION >
IPDM E/R (INTELLIGENT POWER DISTRIBUTION MODULE ENGINE ROOM)
Terminal and Reference Value for IPDM E/R
INFOID:0000000003533840
Symptom Inspection contents Possible cause
Rear window defogger
does not operate.Perform auto active
test. Does rear win-
dow defogger oper-
ate?YES • BCM signal input circuit
NO• Rear window defogger relay
• Open circuit of rear window defogger
•IPDM E/R malfunction
• Harness or connector malfunction between IPDM E/R and rear window
defogger
Any of front wipers, tail
and parking lamps, front
fog lamps, and head-
lamps (Hi, Lo) do not op-
erate.Perform auto active
test. Does system in
question operate?YES • BCM signal input system
NO• Lamp/wiper motor malfunction
• Lamp/wiper motor ground circuit malfunction
• Harness/connector malfunction between IPDM E/R and system in ques-
tion
• IPDM E/R (integrated relay) malfunction
A/C compressor does
not operate.Perform auto active
test. Does magnet
clutch operate?YES• BCM signal input circuit
• CAN communication signal between BCM and ECM
• CAN communication signal between ECM and IPDM E/R
NO• Magnet clutch malfunction
• Harness/connector malfunction between IPDM E/R and magnet clutch
• IPDM E/R (integrated relay) malfunction
Cooling fan does not op-
erate.Perform auto active
test. Does cooling fan
operate?YES• ECM signal input circuit
• CAN communication signal between ECM and IPDM E/R
NO• Cooling fan motor malfunction
• Harness/connector malfunction between IPDM E/R and cooling fan mo-
tor
• IPDM E/R (integrated relay) malfunction
Te r m i n a lWire
colorSignal nameSignal
input/
outputMeasuring condition
Reference value
(Approx.) Igni-
tion
switchOperation or condition
1 B/Y Battery power supply Input OFF — Battery voltage
2 R Battery power supply Input OFF — Battery voltage
3 BR ECM relay Output —Ignition switch ON or START Battery voltage
Ignition switch OFF or ACC 0V
4 W/L ECM relay Output —Ignition switch ON or START Battery voltage
Ignition switch OFF or ACC 0V
6LThrottle control motor
relayOutput —Ignition switch ON or START Battery voltage
Ignition switch OFF or ACC 0V
7 W/B ECM relay control Input —Ignition switch ON or START 0V
Ignition switch OFF or ACC Battery voltage
8 R/B Fuse 54 Output —Ignition switch ON or START Battery voltage
Ignition switch OFF or ACC 0V
10 GDaytime light relay
controlOutput ONDaytime light system active 0V
Daytime light system inactive Battery voltage
11 Y/B A/C compressor OutputON or
STARTA/C switch ON or defrost A/C
switchBattery voltage
A/C switch OFF or defrost A/C
switch0V
Page 2425 of 3061
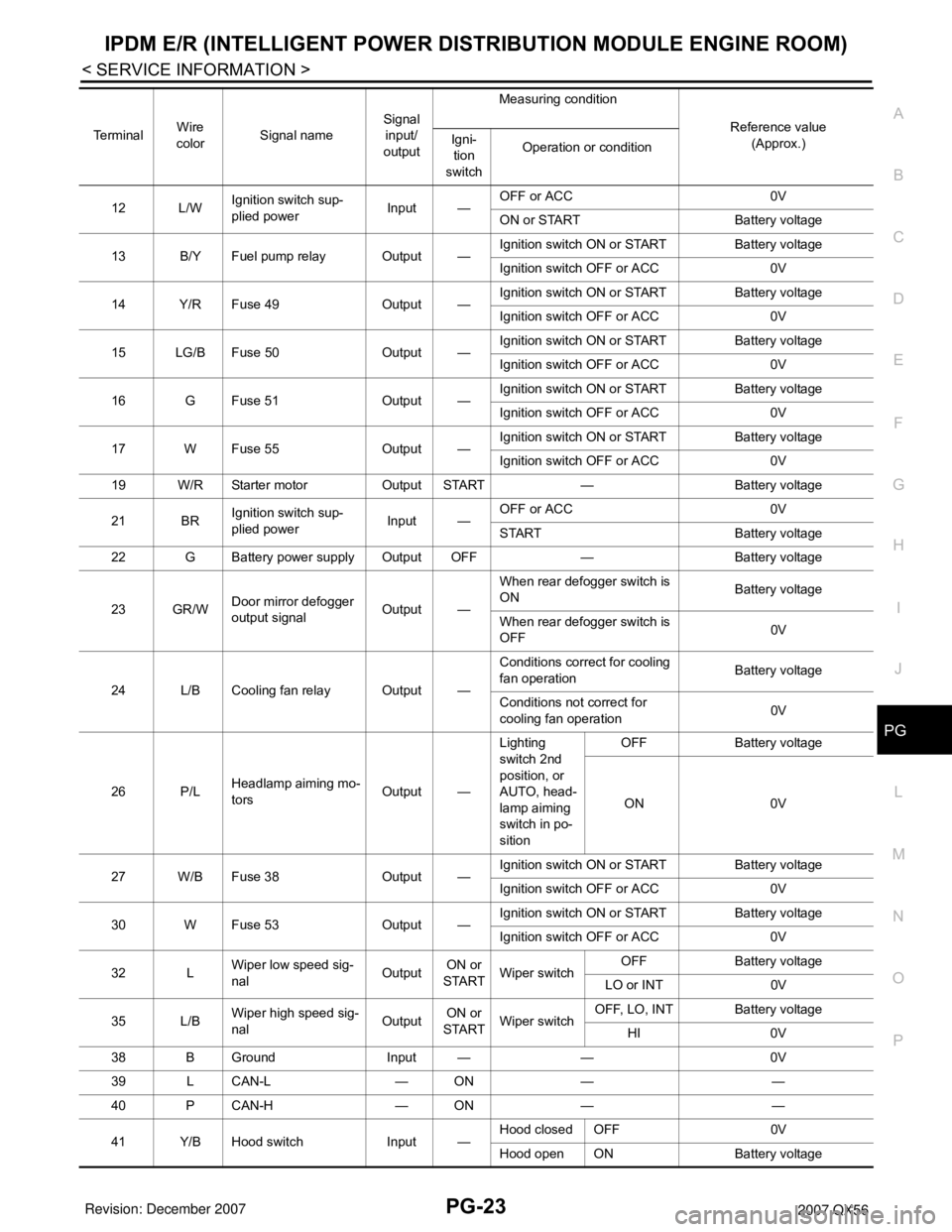
IPDM E/R (INTELLIGENT POWER DISTRIBUTION MODULE ENGINE ROOM)
PG-23
< SERVICE INFORMATION >
C
D
E
F
G
H
I
J
L
MA
B
PG
N
O
P
12 L/WIgnition switch sup-
plied powerInput —OFF or ACC 0V
ON or START Battery voltage
13 B/Y Fuel pump relay Output —Ignition switch ON or START Battery voltage
Ignition switch OFF or ACC 0V
14 Y/R Fuse 49 Output —Ignition switch ON or START Battery voltage
Ignition switch OFF or ACC 0V
15 LG/B Fuse 50 Output —Ignition switch ON or START Battery voltage
Ignition switch OFF or ACC 0V
16 G Fuse 51 Output —Ignition switch ON or START Battery voltage
Ignition switch OFF or ACC 0V
17 W Fuse 55 Output —Ignition switch ON or START Battery voltage
Ignition switch OFF or ACC 0V
19 W/R Starter motor Output START — Battery voltage
21 BRIgnition switch sup-
plied powerInput —OFF or ACC 0V
START Battery voltage
22 G Battery power supply Output OFF — Battery voltage
23 GR/WDoor mirror defogger
output signalOutput —When rear defogger switch is
ONBattery voltage
When rear defogger switch is
OFF0V
24 L/B Cooling fan relay Output —Conditions correct for cooling
fan operationBattery voltage
Conditions not correct for
cooling fan operation0V
26 P/LHeadlamp aiming mo-
torsOutput —Lighting
switch 2nd
position, or
AUTO, head-
lamp aiming
switch in po-
sitionOFF Battery voltage
ON 0V
27 W/B Fuse 38 Output —Ignition switch ON or START Battery voltage
Ignition switch OFF or ACC 0V
30 W Fuse 53 Output —Ignition switch ON or START Battery voltage
Ignition switch OFF or ACC 0V
32 LWiper low speed sig-
nalOutputON or
STARTWiper switchOFF Battery voltage
LO or INT 0V
35 L/BWiper high speed sig-
nalOutputON or
STARTWiper switchOFF, LO, INT Battery voltage
HI 0V
38 B Ground Input — — 0V
39 L CAN-L — ON — —
40 P CAN-H — ON — —
41 Y/B Hood switch Input —Hood closed OFF 0V
Hood open ON Battery voltage Te r m i n a lWire
colorSignal nameSignal
input/
outputMeasuring condition
Reference value
(Approx.) Igni-
tion
switchOperation or condition
Page 2426 of 3061
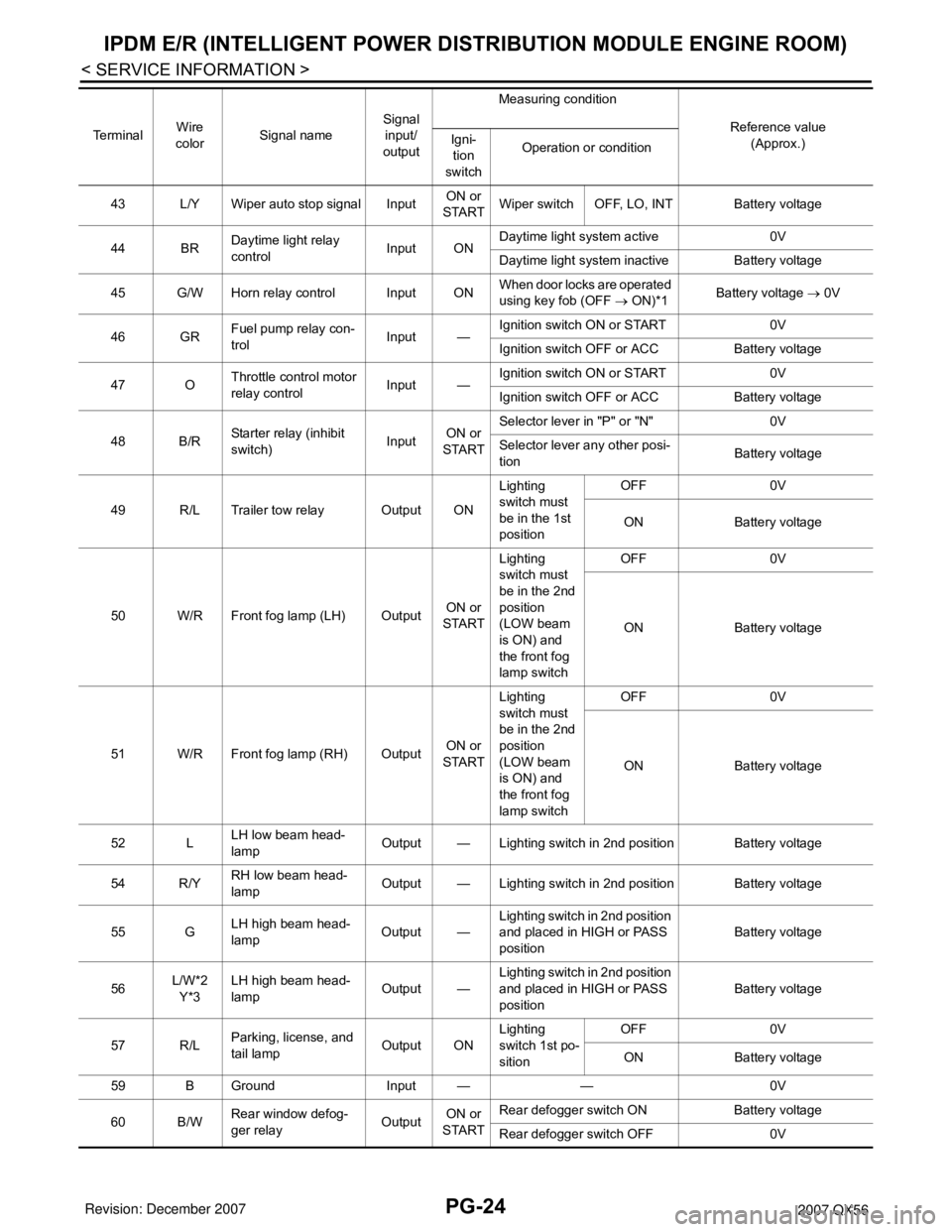
PG-24
< SERVICE INFORMATION >
IPDM E/R (INTELLIGENT POWER DISTRIBUTION MODULE ENGINE ROOM)
43 L/Y Wiper auto stop signal InputON or
STARTWiper switch OFF, LO, INT Battery voltage
44 BRDaytime light relay
controlInput ONDaytime light system active 0V
Daytime light system inactive Battery voltage
45 G/W Horn relay control Input ONWhen door locks are operated
using key fob (OFF → ON)*1Battery voltage → 0V
46 GRFuel pump relay con-
trolInput —Ignition switch ON or START 0V
Ignition switch OFF or ACC Battery voltage
47 OThrottle control motor
relay controlInput —Ignition switch ON or START 0V
Ignition switch OFF or ACC Battery voltage
48 B/RStarter relay (inhibit
switch)InputON or
STARTSelector lever in "P" or "N" 0V
Selector lever any other posi-
tionBattery voltage
49 R/L Trailer tow relay Output ONLighting
switch must
be in the 1st
positionOFF 0V
ON Battery voltage
50 W/R Front fog lamp (LH) OutputON or
STARTLighting
switch must
be in the 2nd
position
(LOW beam
is ON) and
the front fog
lamp switchOFF 0V
ON Battery voltage
51 W/R Front fog lamp (RH) OutputON or
STARTLighting
switch must
be in the 2nd
position
(LOW beam
is ON) and
the front fog
lamp switchOFF 0V
ON Battery voltage
52 LLH low beam head-
lampOutput — Lighting switch in 2nd position Battery voltage
54 R/YRH low beam head-
lampOutput — Lighting switch in 2nd position Battery voltage
55 GLH high beam head-
lampOutput —Lighting switch in 2nd position
and placed in HIGH or PASS
positionBattery voltage
56L/W*2
Y*3LH high beam head-
lampOutput —Lighting switch in 2nd position
and placed in HIGH or PASS
positionBattery voltage
57 R/LParking, license, and
tail lampOutput ONLighting
switch 1st po-
sitionOFF 0V
ON Battery voltage
59 B Ground Input — — 0V
60 B/WRear window defog-
ger relayOutputON or
STARTRear defogger switch ON Battery voltage
Rear defogger switch OFF 0V Te r m i n a lWire
colorSignal nameSignal
input/
outputMeasuring condition
Reference value
(Approx.) Igni-
tion
switchOperation or condition
Page 2462 of 3061
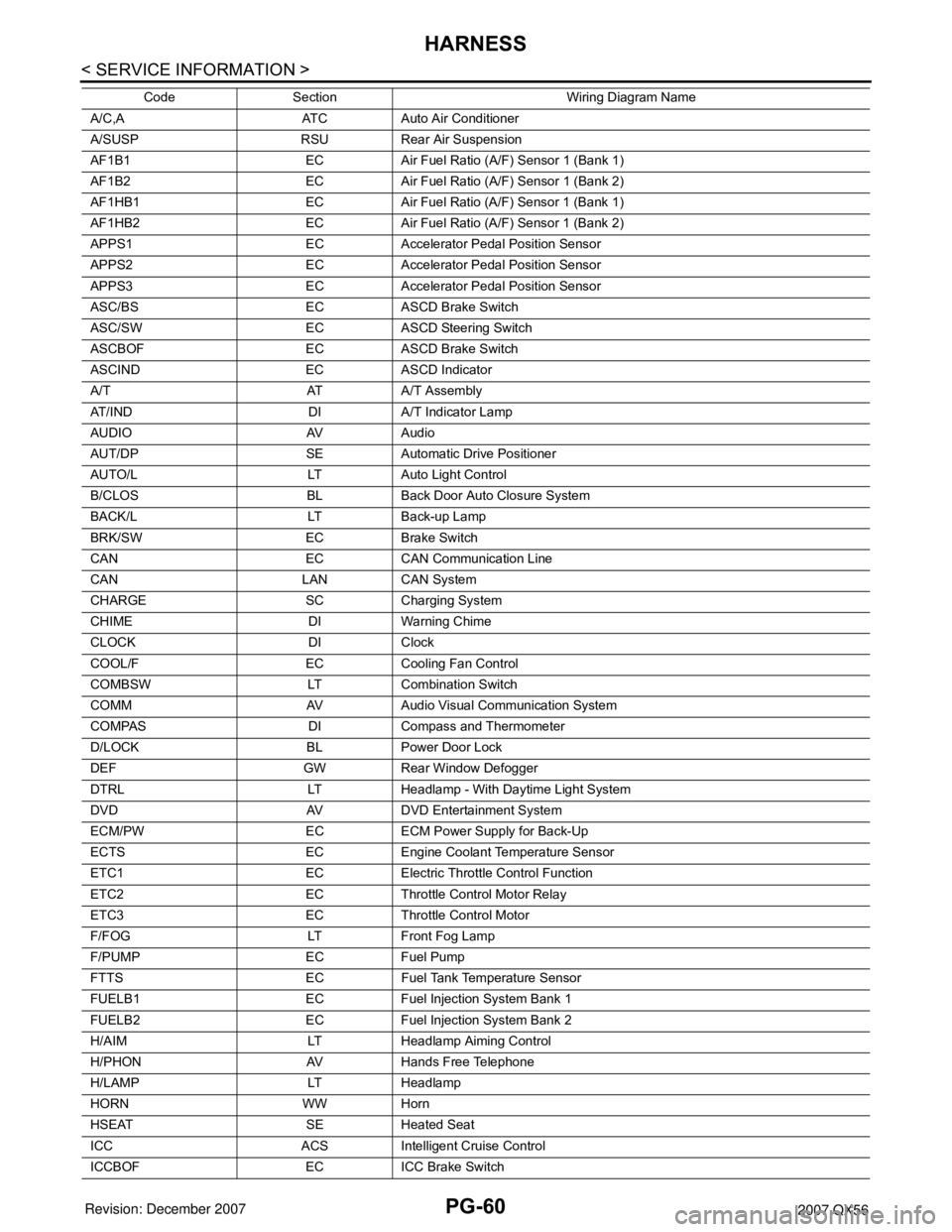
PG-60
< SERVICE INFORMATION >
HARNESS
Code Section Wiring Diagram Name
A/C,A ATC Auto Air Conditioner
A/SUSP RSU Rear Air Suspension
AF1B1 EC Air Fuel Ratio (A/F) Sensor 1 (Bank 1)
AF1B2 EC Air Fuel Ratio (A/F) Sensor 1 (Bank 2)
AF1HB1 EC Air Fuel Ratio (A/F) Sensor 1 (Bank 1)
AF1HB2 EC Air Fuel Ratio (A/F) Sensor 1 (Bank 2)
APPS1 EC Accelerator Pedal Position Sensor
APPS2 EC Accelerator Pedal Position Sensor
APPS3 EC Accelerator Pedal Position Sensor
ASC/BS EC ASCD Brake Switch
ASC/SW EC ASCD Steering Switch
ASCBOF EC ASCD Brake Switch
ASCIND EC ASCD Indicator
A/T AT A/T Assembly
AT/IND DI A/T Indicator Lamp
AUDIO AV Audio
AUT/DP SE Automatic Drive Positioner
AUTO/L LT Auto Light Control
B/CLOS BL Back Door Auto Closure System
BACK/L LT Back-up Lamp
BRK/SW EC Brake Switch
CAN EC CAN Communication Line
CAN LAN CAN System
CHARGE SC Charging System
CHIME DI Warning Chime
CLOCK DI Clock
COOL/F EC Cooling Fan Control
COMBSW LT Combination Switch
COMM AV Audio Visual Communication System
COMPAS DI Compass and Thermometer
D/LOCK BL Power Door Lock
DEF GW Rear Window Defogger
DTRL LT Headlamp - With Daytime Light System
DVD AV DVD Entertainment System
ECM/PW EC ECM Power Supply for Back-Up
ECTS EC Engine Coolant Temperature Sensor
ETC1 EC Electric Throttle Control Function
ETC2 EC Throttle Control Motor Relay
ETC3 EC Throttle Control Motor
F/FOG LT Front Fog Lamp
F/PUMP EC Fuel Pump
FTTS EC Fuel Tank Temperature Sensor
FUELB1 EC Fuel Injection System Bank 1
FUELB2 EC Fuel Injection System Bank 2
H/AIM LT Headlamp Aiming Control
H/PHON AV Hands Free Telephone
H/LAMP LT Headlamp
HORN WW Horn
HSEAT SE Heated Seat
ICC ACS Intelligent Cruise Control
ICCBOF EC ICC Brake Switch
Page 2498 of 3061
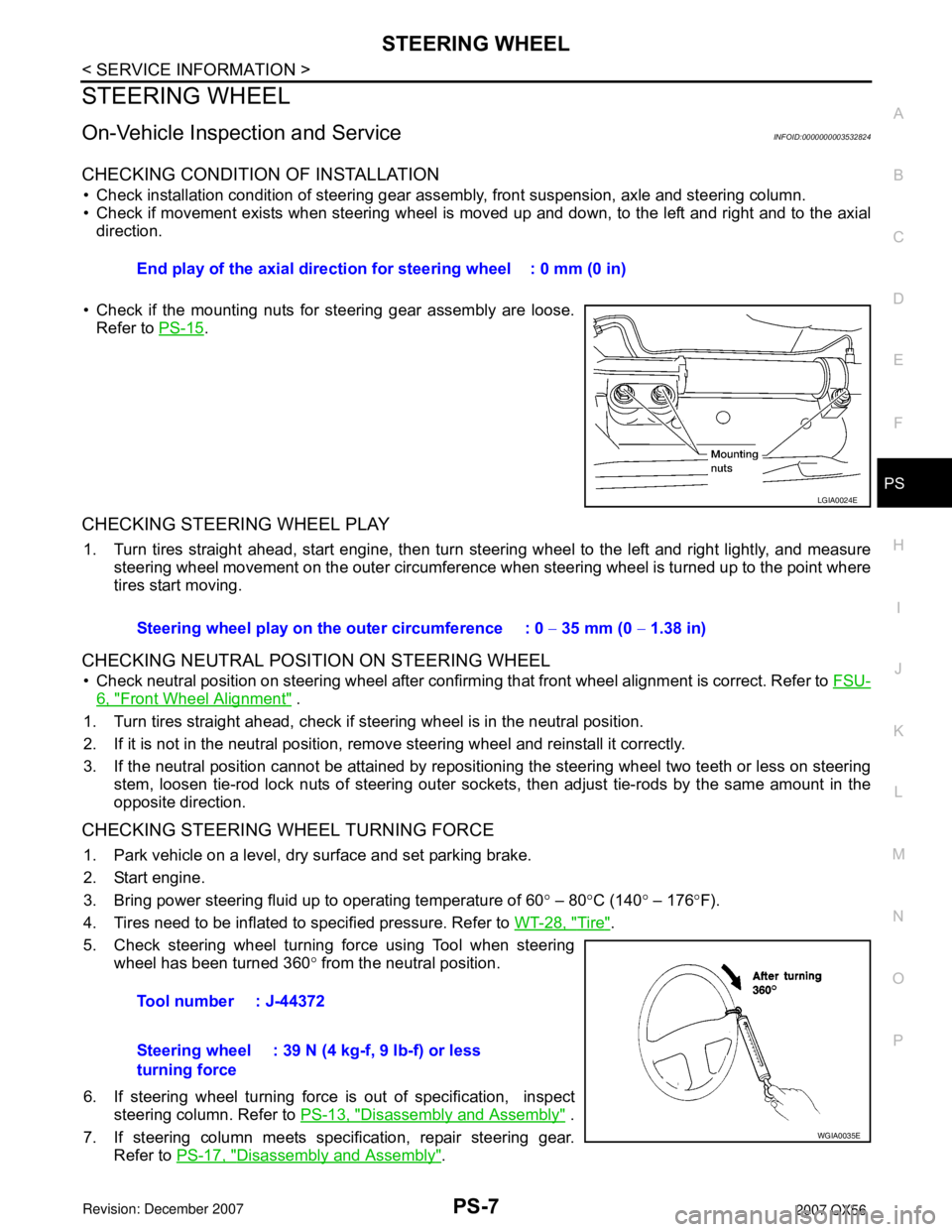
STEERING WHEEL
PS-7
< SERVICE INFORMATION >
C
D
E
F
H
I
J
K
L
MA
B
PS
N
O
P
STEERING WHEEL
On-Vehicle Inspection and ServiceINFOID:0000000003532824
CHECKING CONDITION OF INSTALLATION
• Check installation condition of steering gear assembly, front suspension, axle and steering column.
• Check if movement exists when steering wheel is moved up and down, to the left and right and to the axial
direction.
• Check if the mounting nuts for steering gear assembly are loose.
Refer to PS-15
.
CHECKING STEERING WHEEL PLAY
1. Turn tires straight ahead, start engine, then turn steering wheel to the left and right lightly, and measure
steering wheel movement on the outer circumference when steering wheel is turned up to the point where
tires start moving.
CHECKING NEUTRAL POSITION ON STEERING WHEEL
• Check neutral position on steering wheel after confirming that front wheel alignment is correct. Refer to FSU-
6, "Front Wheel Alignment" .
1. Turn tires straight ahead, check if steering wheel is in the neutral position.
2. If it is not in the neutral position, remove steering wheel and reinstall it correctly.
3. If the neutral position cannot be attained by repositioning the steering wheel two teeth or less on steering
stem, loosen tie-rod lock nuts of steering outer sockets, then adjust tie-rods by the same amount in the
opposite direction.
CHECKING STEERING WHEEL TURNING FORCE
1. Park vehicle on a level, dry surface and set parking brake.
2. Start engine.
3. Bring power steering fluid up to operating temperature of 60° – 80°C (140° – 176°F).
4. Tires need to be inflated to specified pressure. Refer to WT-28, "
Tire".
5. Check steering wheel turning force using Tool when steering
wheel has been turned 360° from the neutral position.
6. If steering wheel turning force is out of specification, inspect
steering column. Refer to PS-13, "
Disassembly and Assembly" .
7. If steering column meets specification, repair steering gear.
Refer to PS-17, "
Disassembly and Assembly". End play of the axial direction for steering wheel : 0 mm (0 in)
LGIA0024E
Steering wheel play on the outer circumference : 0 − 35 mm (0 − 1.38 in)
Tool number : J-44372
Steering wheel
turning force: 39 N (4 kg-f, 9 lb-f) or less
WGIA0035E
Page 2539 of 3061
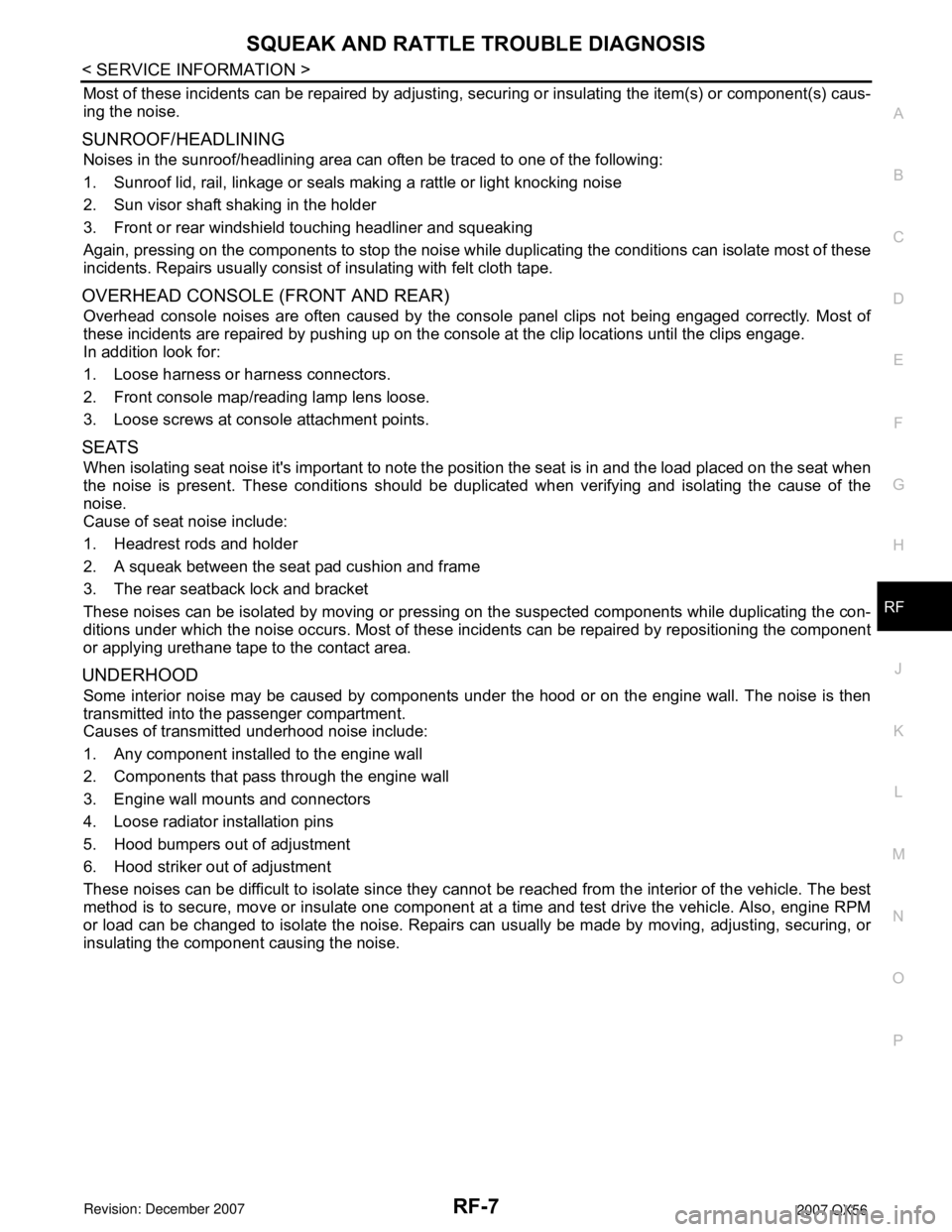
SQUEAK AND RATTLE TROUBLE DIAGNOSIS
RF-7
< SERVICE INFORMATION >
C
D
E
F
G
H
J
K
L
MA
B
RF
N
O
P
Most of these incidents can be repaired by adjusting, securing or insulating the item(s) or component(s) caus-
ing the noise.
SUNROOF/HEADLINING
Noises in the sunroof/headlining area can often be traced to one of the following:
1. Sunroof lid, rail, linkage or seals making a rattle or light knocking noise
2. Sun visor shaft shaking in the holder
3. Front or rear windshield touching headliner and squeaking
Again, pressing on the components to stop the noise while duplicating the conditions can isolate most of these
incidents. Repairs usually consist of insulating with felt cloth tape.
OVERHEAD CONSOLE (FRONT AND REAR)
Overhead console noises are often caused by the console panel clips not being engaged correctly. Most of
these incidents are repaired by pushing up on the console at the clip locations until the clips engage.
In addition look for:
1. Loose harness or harness connectors.
2. Front console map/reading lamp lens loose.
3. Loose screws at console attachment points.
SEATS
When isolating seat noise it's important to note the position the seat is in and the load placed on the seat when
the noise is present. These conditions should be duplicated when verifying and isolating the cause of the
noise.
Cause of seat noise include:
1. Headrest rods and holder
2. A squeak between the seat pad cushion and frame
3. The rear seatback lock and bracket
These noises can be isolated by moving or pressing on the suspected components while duplicating the con-
ditions under which the noise occurs. Most of these incidents can be repaired by repositioning the component
or applying urethane tape to the contact area.
UNDERHOOD
Some interior noise may be caused by components under the hood or on the engine wall. The noise is then
transmitted into the passenger compartment.
Causes of transmitted underhood noise include:
1. Any component installed to the engine wall
2. Components that pass through the engine wall
3. Engine wall mounts and connectors
4. Loose radiator installation pins
5. Hood bumpers out of adjustment
6. Hood striker out of adjustment
These noises can be difficult to isolate since they cannot be reached from the interior of the vehicle. The best
method is to secure, move or insulate one component at a time and test drive the vehicle. Also, engine RPM
or load can be changed to isolate the noise. Repairs can usually be made by moving, adjusting, securing, or
insulating the component causing the noise.