turn signal INFINITI QX56 2009 Factory Service Manual
[x] Cancel search | Manufacturer: INFINITI, Model Year: 2009, Model line: QX56, Model: INFINITI QX56 2009Pages: 4171, PDF Size: 84.65 MB
Page 27 of 4171
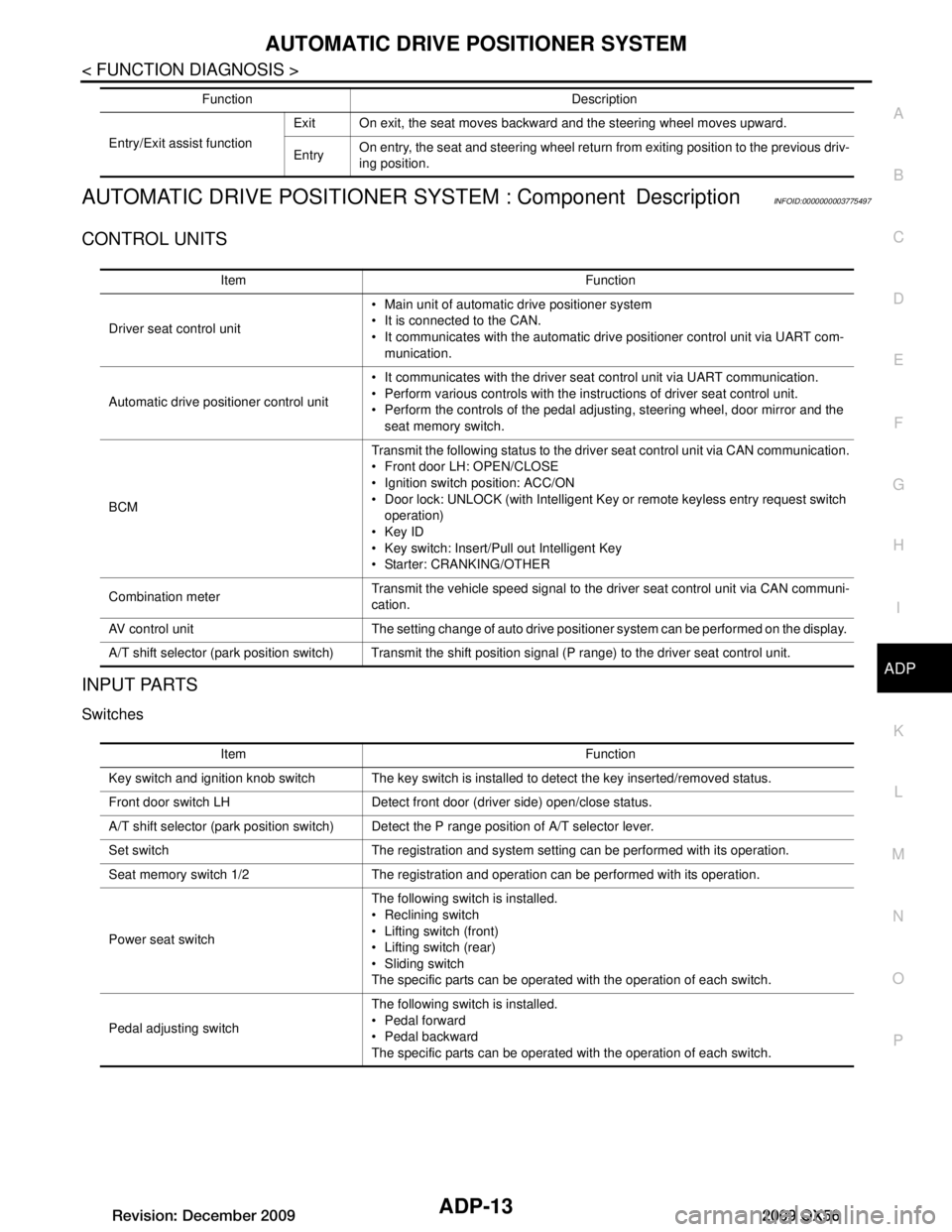
AUTOMATIC DRIVE POSITIONER SYSTEMADP-13
< FUNCTION DIAGNOSIS >
C
DE
F
G H
I
K L
M A
B
ADP
N
O P
AUTOMATIC DRIVE POSITIONER SYSTEM : Component DescriptionINFOID:0000000003775497
CONTROL UNITS
INPUT PARTS
Switches
Entry/Exit assist functionExit On exit, the seat moves backward and the steering wheel moves upward.
Entry
On entry, the seat and steering wheel return from exiting position to the previous driv-
ing position.
Function Description
Item Function
Driver seat control unit Main unit of automatic drive positioner system
It is connected to the CAN.
It communicates with the automatic drive positioner control unit via UART com-
munication.
Automatic drive positioner control unit It communicates with the driver seat control unit via UART communication.
Perform various controls with the instructions of driver seat control unit.
Perform the controls of the pedal adjusting, steering wheel, door mirror and the
seat memory switch.
BCM Transmit the following status to the driver seat control unit via CAN communication.
Front door LH: OPEN/CLOSE
Ignition switch position: ACC/ON
Door lock: UNLOCK (with Intelligent Key or remote keyless entry request switch
operation)
Key ID
Key switch: Insert/Pull out Intelligent Key
Starter: CRANKING/OTHER
Combination meter Transmit the vehicle speed signal to the driver seat control unit via CAN communi-
cation.
AV control unit The setting change of auto drive positioner system can be performed on the display.
A/T shift selector (park position switch) Transmit the shift position signal (P range) to the driver seat control unit.
Item Function
Key switch and ignition knob switch The key switch is installed to detect the key inserted/removed status.
Front door switch LH Detect front door (driver side) open/close status.
A/T shift selector (park position switch) Detect the P range position of A/T selector lever.
Set switch The registration and system setting can be performed with its operation.
Seat memory switch 1/2 The registration and operation can be performed with its operation.
Power seat switch The following switch is installed.
Reclining switch
Lifting switch (front)
Lifting switch (rear)
Sliding switch
The specific parts can be operated with the operation of each switch.
Pedal adjusting switch The following switch is installed.
Pedal forward
Pedal backward
The specific parts can be operated with the operation of each switch.
Revision: December 20092009 QX56
Page 29 of 4171
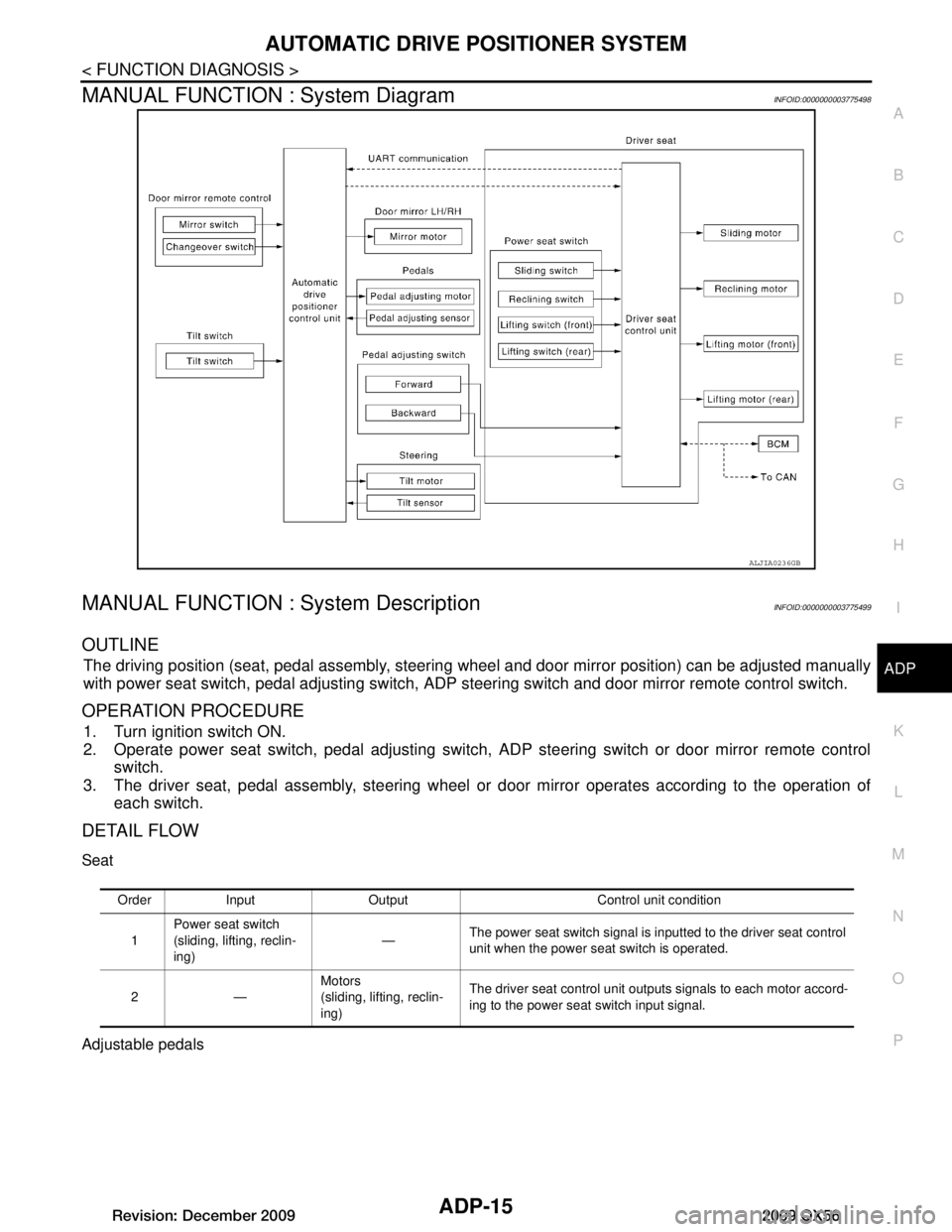
AUTOMATIC DRIVE POSITIONER SYSTEMADP-15
< FUNCTION DIAGNOSIS >
C
DE
F
G H
I
K L
M A
B
ADP
N
O P
MANUAL FUNCTION : System DiagramINFOID:0000000003775498
MANUAL FUNCTION : System DescriptionINFOID:0000000003775499
OUTLINE
The driving position (seat, pedal assembly, steering wheel and door mirror position) can be adjusted manually
with power seat switch, pedal adjusting switch, ADP st eering switch and door mirror remote control switch.
OPERATION PROCEDURE
1. Turn ignition switch ON.
2. Operate power seat switch, pedal adjusting switch, ADP steering switch or door mirror remote control
switch.
3. The driver seat, pedal assembly, steering wheel or door mirror operates according to the operation of each switch.
DETAIL FLOW
Seat
Adjustable pedals
ALJIA0236GB
Order Input Output Control unit condition
1 Power seat switch
(sliding, lifting, reclin-
ing)
—
The power seat switch signal is inputted to the driver seat control
unit when the power seat switch is operated.
2— Motors
(sliding, lifting, reclin-
ing)The driver seat control unit outputs signals to each motor accord-
ing to the power seat switch input signal.
Revision: December 20092009 QX56
Page 50 of 4171
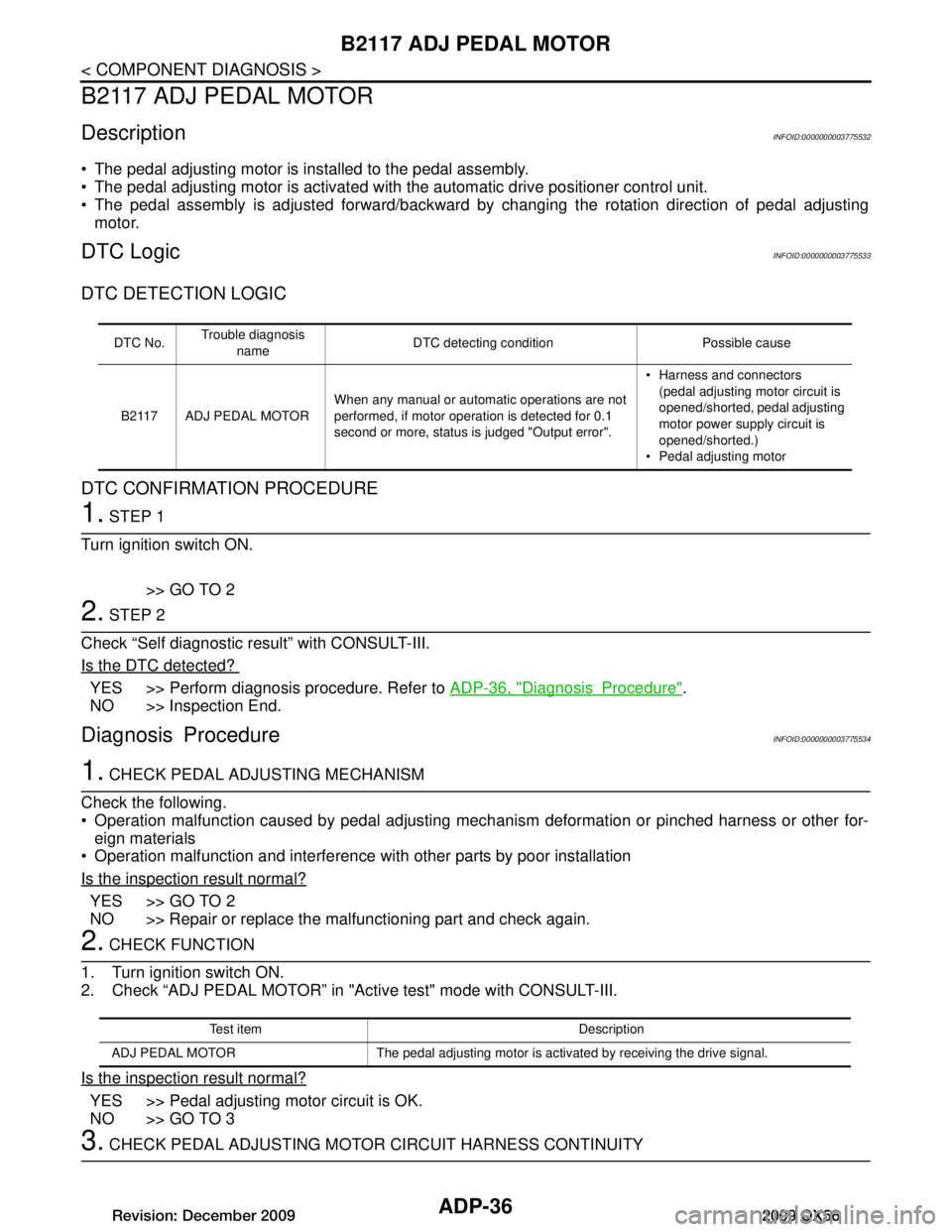
ADP-36
< COMPONENT DIAGNOSIS >
B2117 ADJ PEDAL MOTOR
B2117 ADJ PEDAL MOTOR
DescriptionINFOID:0000000003775532
The pedal adjusting motor is installed to the pedal assembly.
The pedal adjusting motor is activated with the automatic drive positioner control unit.
The pedal assembly is adjusted forward/backward by changing the rotation direction of pedal adjustingmotor.
DTC LogicINFOID:0000000003775533
DTC DETECTION LOGIC
DTC CONFIRMATION PROCEDURE
1. STEP 1
Turn ignition switch ON.
>> GO TO 2
2. STEP 2
Check “Self diagnostic result” with CONSULT-III.
Is the DTC detected?
YES >> Perform diagnosis procedure. Refer to ADP-36, "Diagnosis Procedure".
NO >> Inspection End.
Diagnosis ProcedureINFOID:0000000003775534
1. CHECK PEDAL ADJUSTING MECHANISM
Check the following.
Operation malfunction caused by pedal adjusting mech anism deformation or pinched harness or other for-
eign materials
Operation malfunction and interference wit h other parts by poor installation
Is the inspection result normal?
YES >> GO TO 2
NO >> Repair or replace the malfunctioning part and check again.
2. CHECK FUNCTION
1. Turn ignition switch ON.
2. Check “ADJ PEDAL MOTOR” in "Active test" mode with CONSULT-III.
Is the inspection result normal?
YES >> Pedal adjusting motor circuit is OK.
NO >> GO TO 3
3. CHECK PEDAL ADJUSTING MOTOR CIRCUIT HARNESS CONTINUITY
DTC No. Trouble diagnosis
name DTC detecting condition Possible cause
B2117 ADJ PEDAL MOTOR When any manual or automatic operations are not
performed, if motor operation is detected for 0.1
second or more, status is judged "Output error". Harness and connectors
(pedal adjusting motor circuit is
opened/shorted, pedal adjusting
motor power supp ly circuit is
opened/shorted.)
Pedal adjusting motor
Test item Description
ADJ PEDAL MOTOR The pedal adjusting motor is activated by receiving the drive signal.
Revision: December 20092009 QX56
Page 51 of 4171
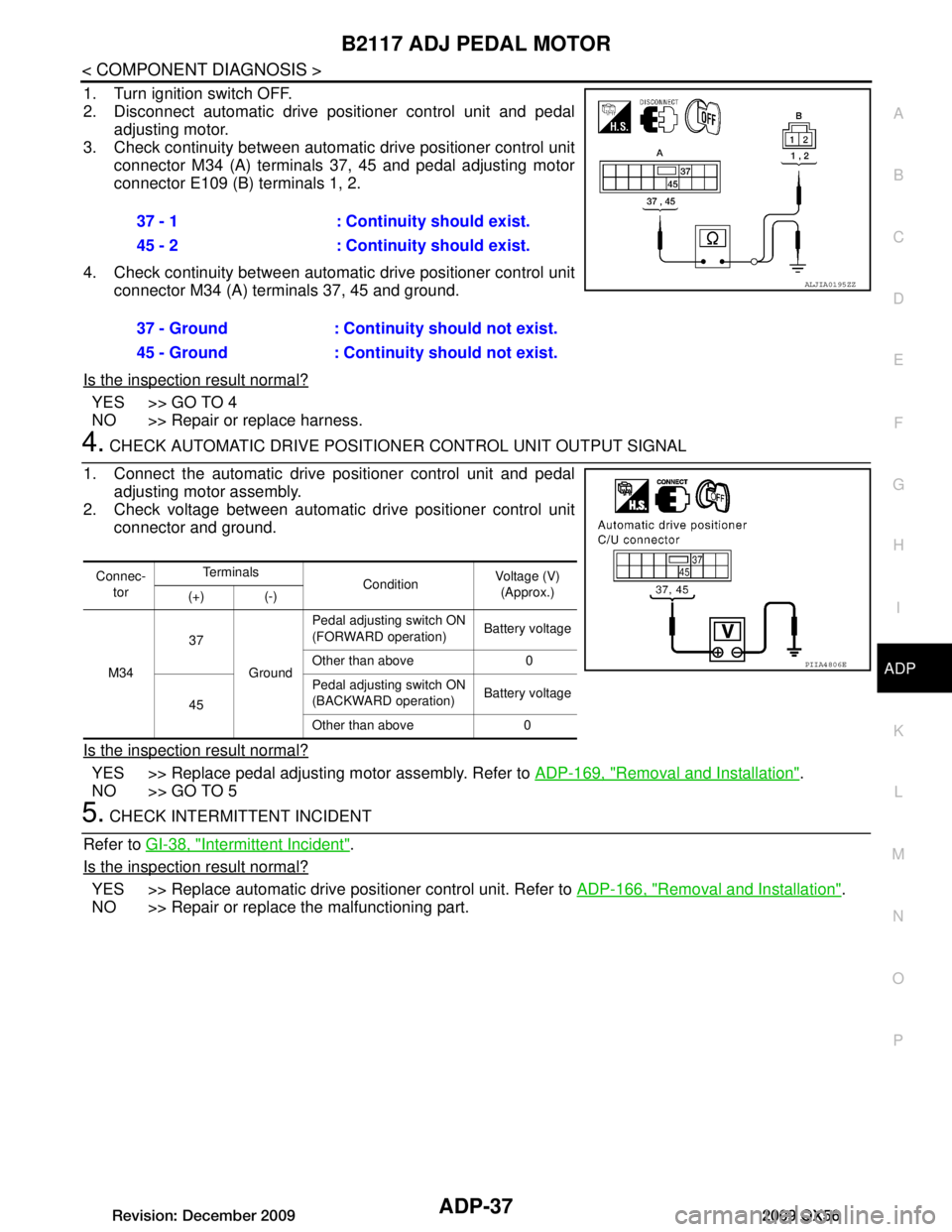
B2117 ADJ PEDAL MOTORADP-37
< COMPONENT DIAGNOSIS >
C
DE
F
G H
I
K L
M A
B
ADP
N
O P
1. Turn ignition switch OFF.
2. Disconnect automatic drive positioner control unit and pedal adjusting motor.
3. Check continuity between automat ic drive positioner control unit
connector M34 (A) terminals 37, 45 and pedal adjusting motor
connector E109 (B) terminals 1, 2.
4. Check continuity between automat ic drive positioner control unit
connector M34 (A) terminals 37, 45 and ground.
Is the inspection result normal?
YES >> GO TO 4
NO >> Repair or replace harness.
4. CHECK AUTOMATIC DRIVE POSITION ER CONTROL UNIT OUTPUT SIGNAL
1. Connect the automatic drive positioner control unit and pedal adjusting motor assembly.
2. Check voltage between automatic drive positioner control unit
connector and ground.
Is the inspection result normal?
YES >> Replace pedal adjusting motor assembly. Refer to ADP-169, "Removal and Installation".
NO >> GO TO 5
5. CHECK INTERMITTENT INCIDENT
Refer to GI-38, "Intermittent Incident"
.
Is the inspection result normal?
YES >> Replace automatic drive posit ioner control unit. Refer to ADP-166, "Removal and Installation".
NO >> Repair or replace the malfunctioning part. 37 - 1 : Continuity should exist.
45 - 2 : Continuity should exist.
37 - Ground : Continuity should not exist.
45 - Ground : Continuity should not exist.
ALJIA0195ZZ
Connec-
tor Te r m i n a l s
ConditionVoltage (V)
(Approx.)
(+) (-)
M34 37
Ground Pedal adjusting switch ON
(FORWARD operation)
Battery voltage
Other than above 0
45 Pedal adjusting switch ON
(BACKWARD operation)
Battery voltage
Other than above 0
PIIA4806E
Revision: December 20092009 QX56
Page 52 of 4171
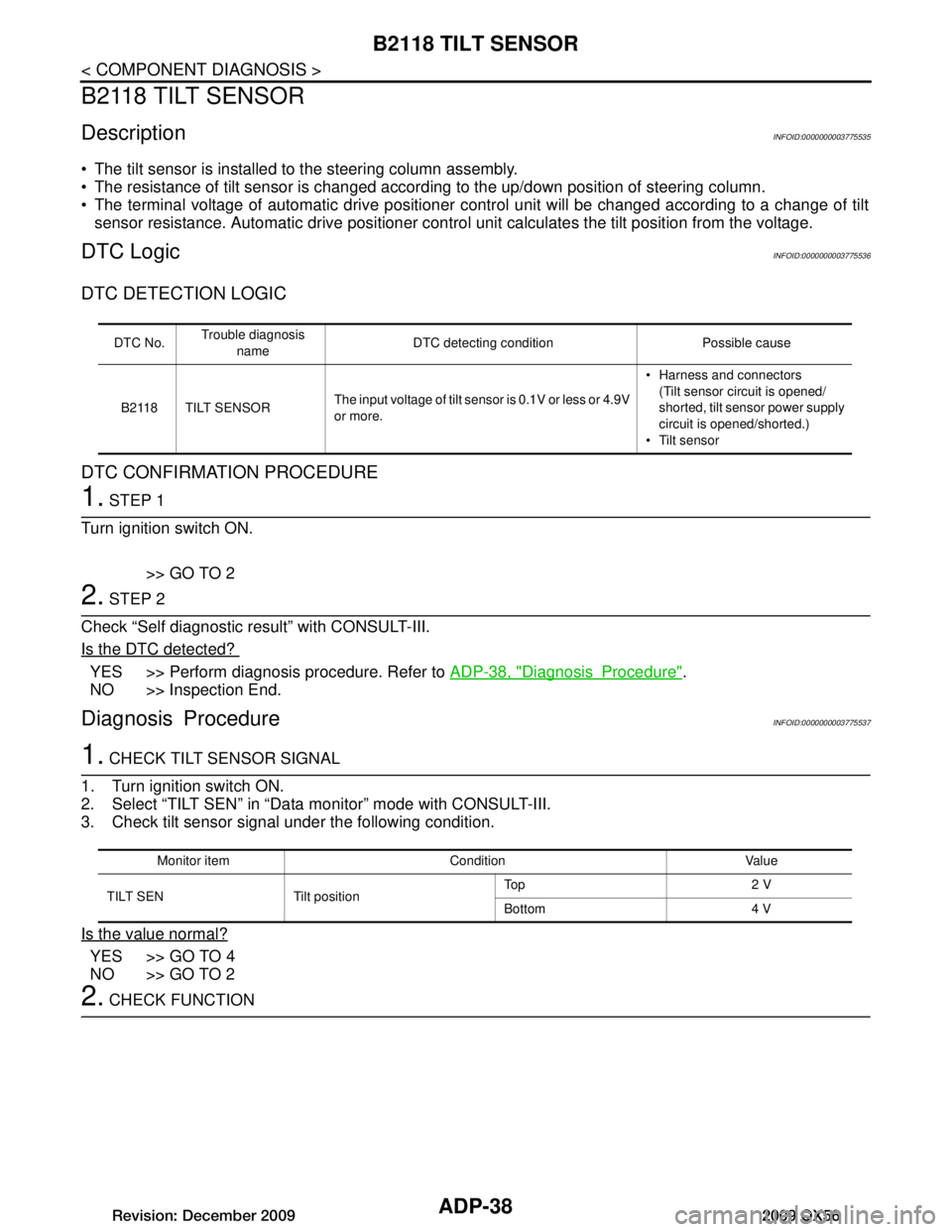
ADP-38
< COMPONENT DIAGNOSIS >
B2118 TILT SENSOR
B2118 TILT SENSOR
DescriptionINFOID:0000000003775535
The tilt sensor is installed to the steering column assembly.
The resistance of tilt sensor is changed according to the up/down position of steering column.
The terminal voltage of automatic drive positioner c ontrol unit will be changed according to a change of tilt
sensor resistance. Automatic drive positioner contro l unit calculates the tilt position from the voltage.
DTC LogicINFOID:0000000003775536
DTC DETECTION LOGIC
DTC CONFIRMATION PROCEDURE
1. STEP 1
Turn ignition switch ON.
>> GO TO 2
2. STEP 2
Check “Self diagnostic result” with CONSULT-III.
Is the DTC detected?
YES >> Perform diagnosis procedure. Refer to ADP-38, "Diagnosis Procedure".
NO >> Inspection End.
Diagnosis ProcedureINFOID:0000000003775537
1. CHECK TILT SENSOR SIGNAL
1. Turn ignition switch ON.
2. Select “TILT SEN” in “Data m onitor” mode with CONSULT-III.
3. Check tilt sensor signal under the following condition.
Is the value normal?
YES >> GO TO 4
NO >> GO TO 2
2. CHECK FUNCTION
DTC No. Trouble diagnosis
name DTC detecting condition Possible cause
B2118 TILT SENSOR The input voltage of tilt sensor is 0.1V or less or 4.9V
or more. Harness and connectors
(Tilt sensor circuit is opened/
shorted, tilt sensor power supply
circuit is opened/shorted.)
Tilt sensor
Monitor item Condition Value
TILT SEN Tilt position To p 2 V
Bottom 4 V
Revision: December 20092009 QX56
Page 54 of 4171
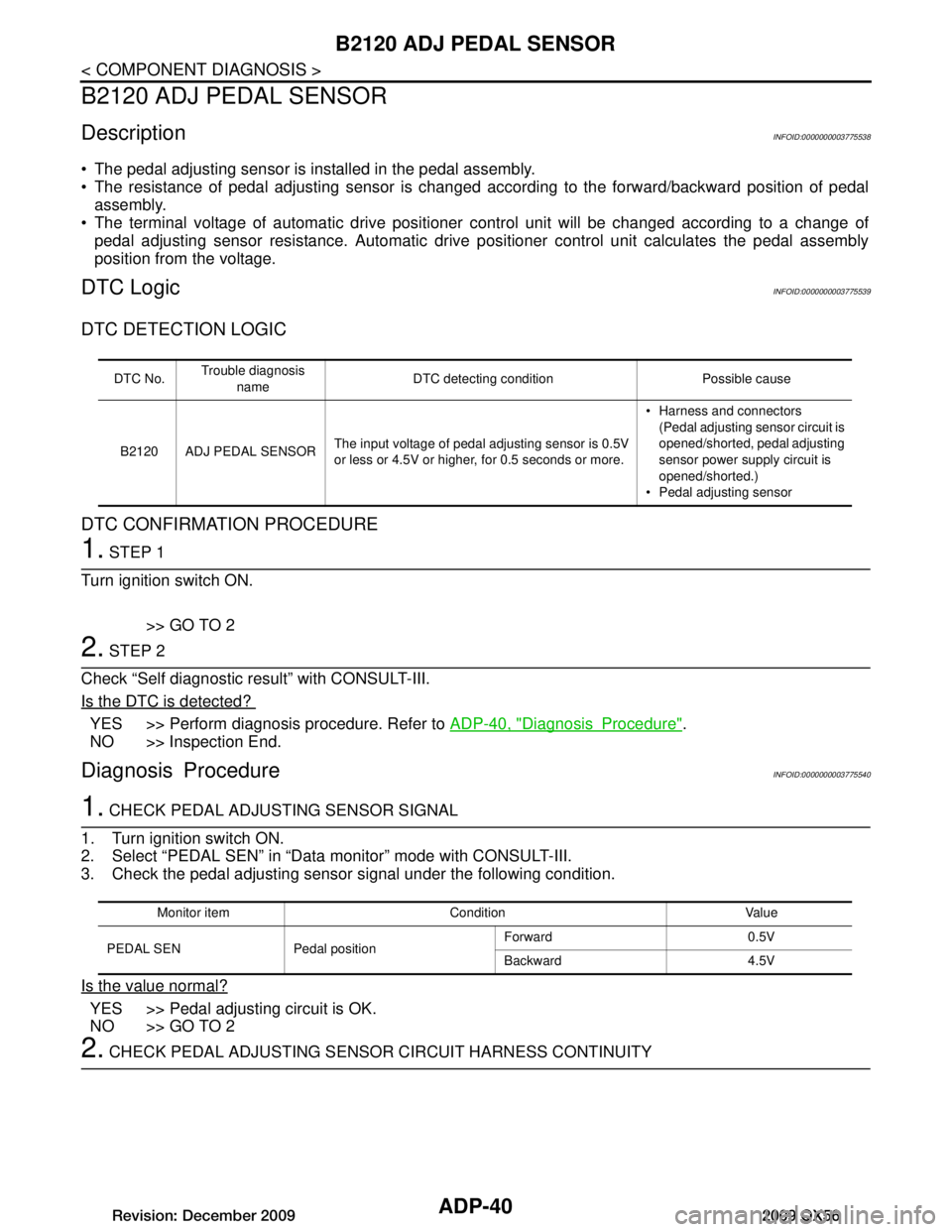
ADP-40
< COMPONENT DIAGNOSIS >
B2120 ADJ PEDAL SENSOR
B2120 ADJ PEDAL SENSOR
DescriptionINFOID:0000000003775538
The pedal adjusting sensor is installed in the pedal assembly.
The resistance of pedal adjusting sensor is changed according to the forward/backward position of pedalassembly.
The terminal voltage of automatic drive positioner control unit will be changed according to a change of
pedal adjusting sensor resistance. Automatic drive pos itioner control unit calculates the pedal assembly
position from the voltage.
DTC LogicINFOID:0000000003775539
DTC DETECTION LOGIC
DTC CONFIRMATION PROCEDURE
1. STEP 1
Turn ignition switch ON.
>> GO TO 2
2. STEP 2
Check “Self diagnostic result” with CONSULT-III.
Is the DTC is detected?
YES >> Perform diagnosis procedure. Refer to ADP-40, "Diagnosis Procedure".
NO >> Inspection End.
Diagnosis ProcedureINFOID:0000000003775540
1. CHECK PEDAL ADJUSTING SENSOR SIGNAL
1. Turn ignition switch ON.
2. Select “PEDAL SEN” in “Dat a monitor” mode with CONSULT-III.
3. Check the pedal adjusting sensor signal under the following condition.
Is the value normal?
YES >> Pedal adjusting circuit is OK.
NO >> GO TO 2
2. CHECK PEDAL ADJUSTING SENSO R CIRCUIT HARNESS CONTINUITY
DTC No.Trouble diagnosis
name DTC detecting condition Possible cause
B2120 ADJ PEDAL SENSOR The input voltage of pedal adjusting sensor is 0.5V
or less or 4.5V or higher, for 0.5 seconds or more. Harness and connectors
(Pedal adjusting sensor circuit is
opened/shorted, pedal adjusting
sensor power supply circuit is
opened/shorted.)
Pedal adjusting sensor
Monitor item Condition Value
PEDAL SEN Pedal position Forward 0.5V
Backward 4.5V
Revision: December 20092009 QX56
Page 56 of 4171
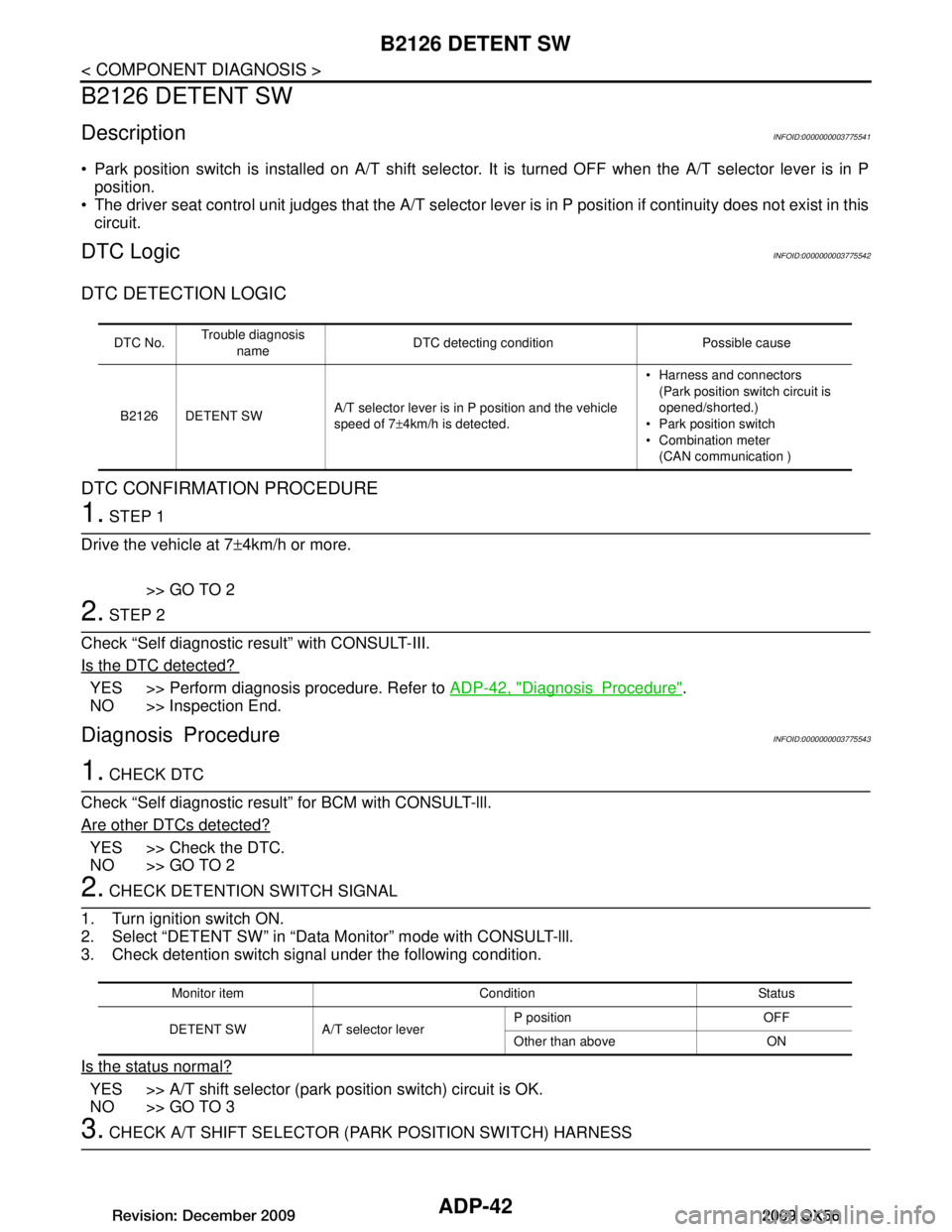
ADP-42
< COMPONENT DIAGNOSIS >
B2126 DETENT SW
B2126 DETENT SW
DescriptionINFOID:0000000003775541
Park position switch is installed on A/T shift selector. It is turned OFF when the A/T selector lever is in P
position.
The driver seat control unit judges that the A/T selector le ver is in P position if continuity does not exist in this
circuit.
DTC LogicINFOID:0000000003775542
DTC DETECTION LOGIC
DTC CONFIRMATION PROCEDURE
1. STEP 1
Drive the vehicle at 7 ±4km/h or more.
>> GO TO 2
2. STEP 2
Check “Self diagnostic result” with CONSULT-III.
Is the DTC detected?
YES >> Perform diagnosis procedure. Refer to ADP-42, "Diagnosis Procedure".
NO >> Inspection End.
Diagnosis ProcedureINFOID:0000000003775543
1. CHECK DTC
Check “Self diagnostic result” for BCM with CONSULT-lll.
Are other DTCs detected?
YES >> Check the DTC.
NO >> GO TO 2
2. CHECK DETENTION SWITCH SIGNAL
1. Turn ignition switch ON.
2. Select “DETENT SW” in “Data Monitor” mode with CONSULT-lll.
3. Check detention switch signal under the following condition.
Is the status normal?
YES >> A/T shift selector (park position switch) circuit is OK.
NO >> GO TO 3
3. CHECK A/T SHIFT SELECTOR (PARK POSITION SWITCH) HARNESS
DTC No. Trouble diagnosis
name DTC detecting condition Possible cause
B2126 DETENT SW A/T selector lever is in P position and the vehicle
speed of 7
±4km/h is detected. Harness and connectors
(Park position switch circuit is
opened/shorted.)
Park position switch
Combination meter (CAN communication )
Monitor item Condition Status
DETENT SW A/T selector lever P position OFF
Other than above ON
Revision: December 20092009 QX56
Page 58 of 4171
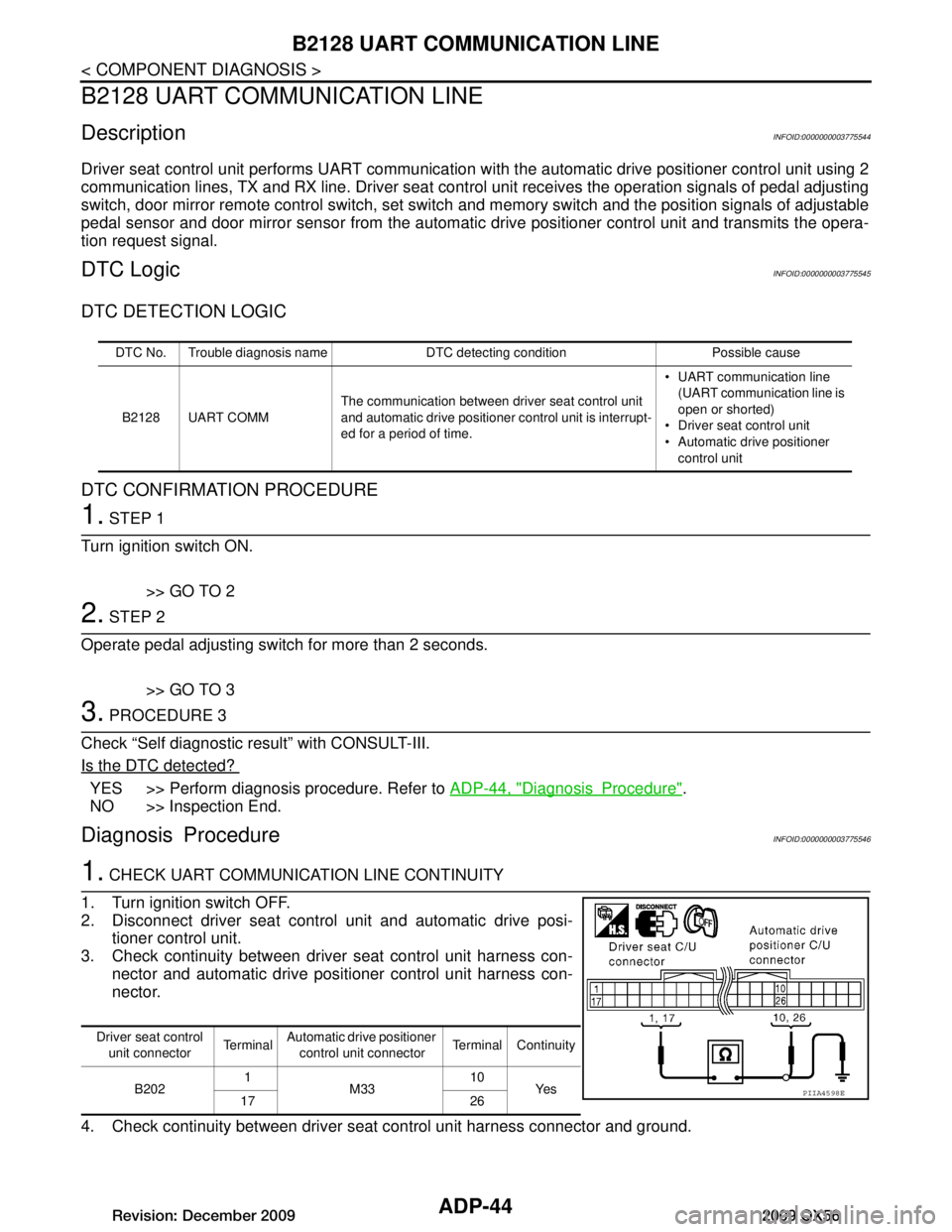
ADP-44
< COMPONENT DIAGNOSIS >
B2128 UART COMMUNICATION LINE
B2128 UART COMMUNICATION LINE
DescriptionINFOID:0000000003775544
Driver seat control unit performs UART communication with the automatic drive positioner control unit using 2
communication lines, TX and RX line. Driver seat cont rol unit receives the operation signals of pedal adjusting
switch, door mirror remote control switch, set switch and memory switch and the position signals of adjustable
pedal sensor and door mirror sensor from the automatic drive positioner control unit and transmits the opera-
tion request signal.
DTC LogicINFOID:0000000003775545
DTC DETECTION LOGIC
DTC CONFIRMATION PROCEDURE
1. STEP 1
Turn ignition switch ON.
>> GO TO 2
2. STEP 2
Operate pedal adjusting switch for more than 2 seconds.
>> GO TO 3
3. PROCEDURE 3
Check “Self diagnostic result” with CONSULT-III.
Is the DTC detected?
YES >> Perform diagnosis procedure. Refer to ADP-44, "Diagnosis Procedure".
NO >> Inspection End.
Diagnosis ProcedureINFOID:0000000003775546
1. CHECK UART COMMUNICA TION LINE CONTINUITY
1. Turn ignition switch OFF.
2. Disconnect driver seat contro l unit and automatic drive posi-
tioner control unit.
3. Check continuity between driver seat control unit harness con- nector and automatic drive positi oner control unit harness con-
nector.
4. Check continuity between driver seat control unit harness connector and ground.
DTC No. Trouble diagnosis name DTC detecting condition Possible cause B2128 UART COMM The communication between driver seat control unit
and automatic drive positioner control unit is interrupt-
ed for a period of time. UART communication line
(UART communication line is
open or shorted)
Driver seat control unit
Automatic drive positioner control unit
Driver seat control unit connector Te r m i n a lAutomatic drive positioner
control unit connector Terminal Continuity
B202 1
M33 10
Ye s
17 26
PIIA4598E
Revision: December 20092009 QX56
Page 60 of 4171

ADP-46
< COMPONENT DIAGNOSIS >
POWER SUPPLY AND GROUND CIRCUIT
POWER SUPPLY AND GROUND CIRCUIT
BCM
BCM : Diagnosis ProcedureINFOID:0000000004055989
1. CHECK FUSES AND FUSIBLE LINK
Check that the following fuses and fusible link are not blown.
Is the fuse blown?
YES >> Replace the blown fuse or fusible link after repairing the affected circuit.
NO >> GO TO 2
2. CHECK POWER SUPPLY CIRCUIT
1. Turn ignition switch OFF.
2. Disconnect BCM.
3. Check voltage between BCM harness connector and ground.
Is the measurement value normal?
YES >> GO TO 3
NO >> Repair or replace harness.
3. CHECK GROUND CIRCUIT
Check continuity between BCM harness connector and ground.
Does continuity exist?
YES >> Inspection End.
NO >> Repair or replace harness.
DRIVER SEAT CONTROL UNIT
Terminal No. Signal name Fuses and fusible link No.
57 Battery power supply 22 (15A)
70 F (50A)
11 Ignition ACC or ON 4 (10A)
38 Ignition ON or START 59 (10A)
Connector Te r m i n a l s
Power
source Condition
Voltage (V) (Ap-
prox.)
(+) (-)
M18 11 Ground
ACC
power
supply Ignition
switch
ACC or ON Battery voltage
38 Ground Ignition
power
supply Ignition
switch ON or START Battery voltage
M20 57 Ground
Battery
power
supply Ignition
switch
OFF Battery voltage
70 Ground Battery
power
supply Ignition
switch OFF Battery voltage
LIIA2415E
BCM
GroundContinuity
Connector Terminal
M20 67 Yes
LIIA0915E
Revision: December 20092009 QX56
Page 63 of 4171
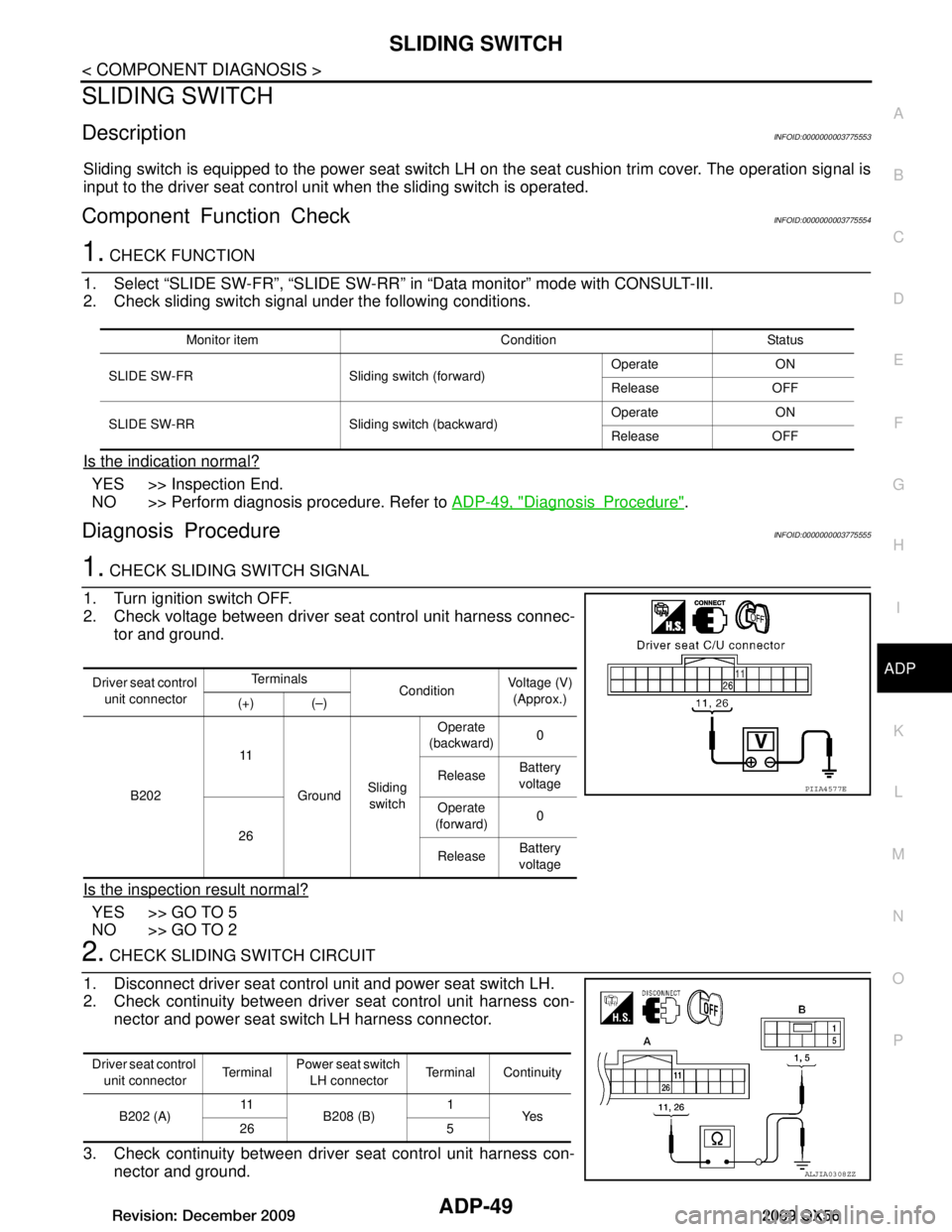
SLIDING SWITCHADP-49
< COMPONENT DIAGNOSIS >
C
DE
F
G H
I
K L
M A
B
ADP
N
O P
SLIDING SWITCH
DescriptionINFOID:0000000003775553
Sliding switch is equipped to the power seat switch LH on the seat cushion trim cover. The operation signal is
input to the driver seat control unit when the sliding switch is operated.
Component Function CheckINFOID:0000000003775554
1. CHECK FUNCTION
1. Select “SLIDE SW-FR”, “SLIDE SW-RR” in “Data monitor” mode with CONSULT-III.
2. Check sliding switch signal under the following conditions.
Is the indication normal?
YES >> Inspection End.
NO >> Perform diagnosis procedure. Refer to ADP-49, "Diagnosis Procedure"
.
Diagnosis ProcedureINFOID:0000000003775555
1. CHECK SLIDING SWITCH SIGNAL
1. Turn ignition switch OFF.
2. Check voltage between driver s eat control unit harness connec-
tor and ground.
Is the inspection result normal?
YES >> GO TO 5
NO >> GO TO 2
2. CHECK SLIDING SWITCH CIRCUIT
1. Disconnect driver seat control unit and power seat switch LH.
2. Check continuity between driver seat control unit harness con-
nector and power seat switch LH harness connector.
3. Check continuity between driver seat control unit harness con-
nector and ground.
Monitor item Condition Status
SLIDE SW-FR Sliding switch (forward) Operate ON
Release OFF
SLIDE SW-RR Sliding switch (backward) Operate ON
Release OFF
Driver seat control
unit connector Te r m i n a l s
ConditionVoltage (V)
(Approx.)
(+) (–)
B202 11
Ground Sliding
switch Operate
(backward) 0
Release Battery
voltage
26 Operate
(forward) 0
Release Battery
voltage
PIIA4577E
Driver seat control
unit connector Te r m i n a l
Power seat switch
LH connector Terminal Continuity
B202 (A) 11
B208 (B) 1
Ye s
26 5
ALJIA0308ZZ
Revision: December 20092009 QX56