check engine ISUZU AXIOM 2002 Service Workshop Manual
[x] Cancel search | Manufacturer: ISUZU, Model Year: 2002, Model line: AXIOM, Model: ISUZU AXIOM 2002Pages: 2100, PDF Size: 19.35 MB
Page 697 of 2100
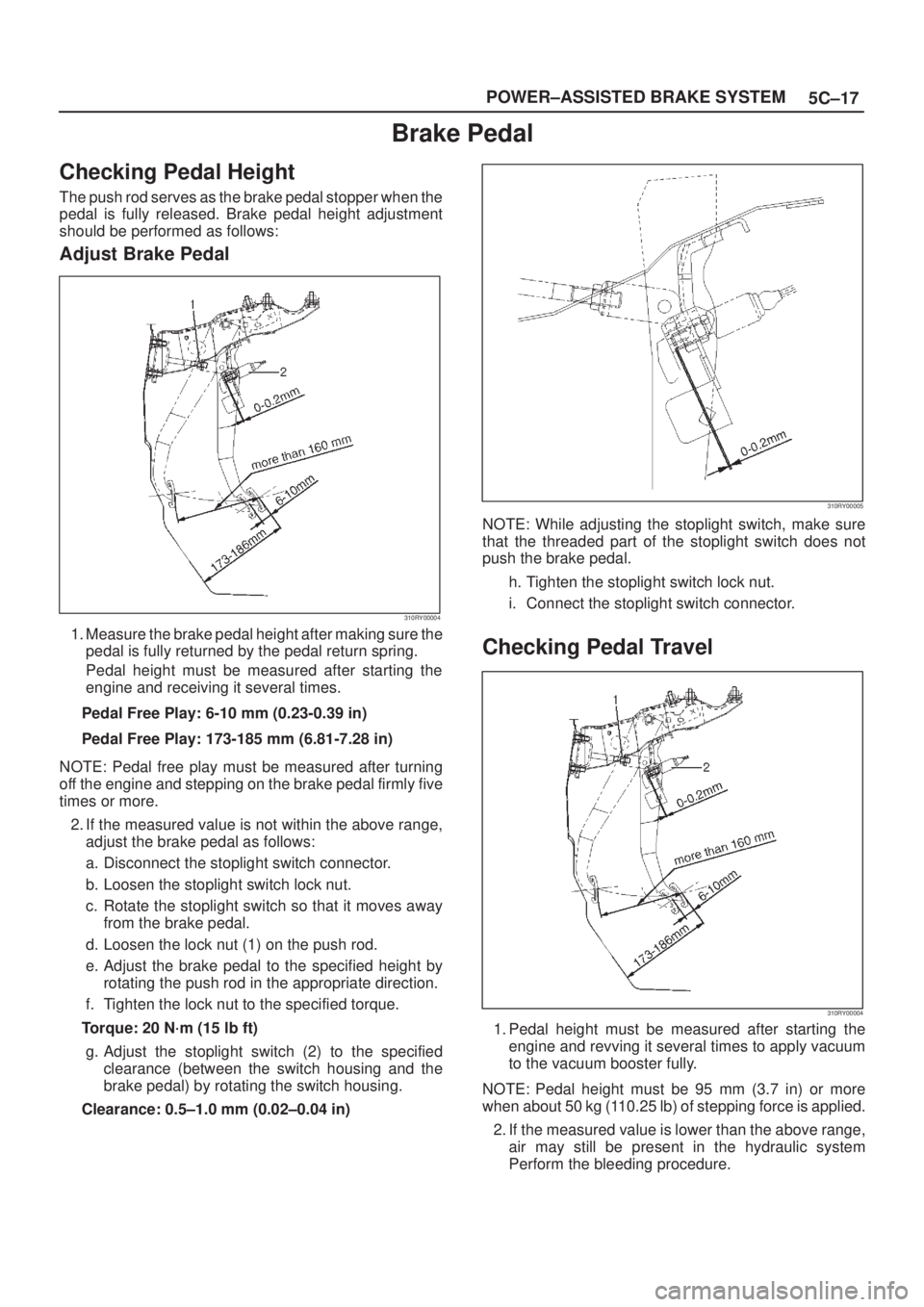
5C±17 POWER±ASSISTED BRAKE SYSTEM
Brake Pedal
Checking Pedal Height
The push rod serves as the brake pedal stopper when the
pedal is fully released. Brake pedal height adjustment
should be performed as follows:
Adjust Brake Pedal
310RY00004
1. Measure the brake pedal height after making sure the
pedal is fully returned by the pedal return spring.
Pedal height must be measured after starting the
engine and receiving it several times.
Pedal Free Play: 6-10 mm (0.23-0.39 in)
Pedal Free Play: 173-185 mm (6.81-7.28 in)
NOTE: Pedal free play must be measured after turning
off the engine and stepping on the brake pedal firmly five
times or more.
2. If the measured value is not within the above range,
adjust the brake pedal as follows:
a. Disconnect the stoplight switch connector.
b. Loosen the stoplight switch lock nut.
c. Rotate the stoplight switch so that it moves away
from the brake pedal.
d. Loosen the lock nut (1) on the push rod.
e. Adjust the brake pedal to the specified height by
rotating the push rod in the appropriate direction.
f. Tighten the lock nut to the specified torque.
Torque: 20 N´m (15 lb ft)
g. Adjust the stoplight switch (2) to the specified
clearance (between the switch housing and the
brake pedal) by rotating the switch housing.
Clearance: 0.5±1.0 mm (0.02±0.04 in)
310RY00005
NOTE: While adjusting the stoplight switch, make sure
that the threaded part of the stoplight switch does not
push the brake pedal.
h. Tighten the stoplight switch lock nut.
i. Connect the stoplight switch connector.
Checking Pedal Travel
310RY00004
1. Pedal height must be measured after starting the
engine and revving it several times to apply vacuum
to the vacuum booster fully.
NOTE: Pedal height must be 95 mm (3.7 in) or more
when about 50 kg (110.25 lb) of stepping force is applied.
2. If the measured value is lower than the above range,
air may still be present in the hydraulic system
Perform the bleeding procedure.
Page 706 of 2100
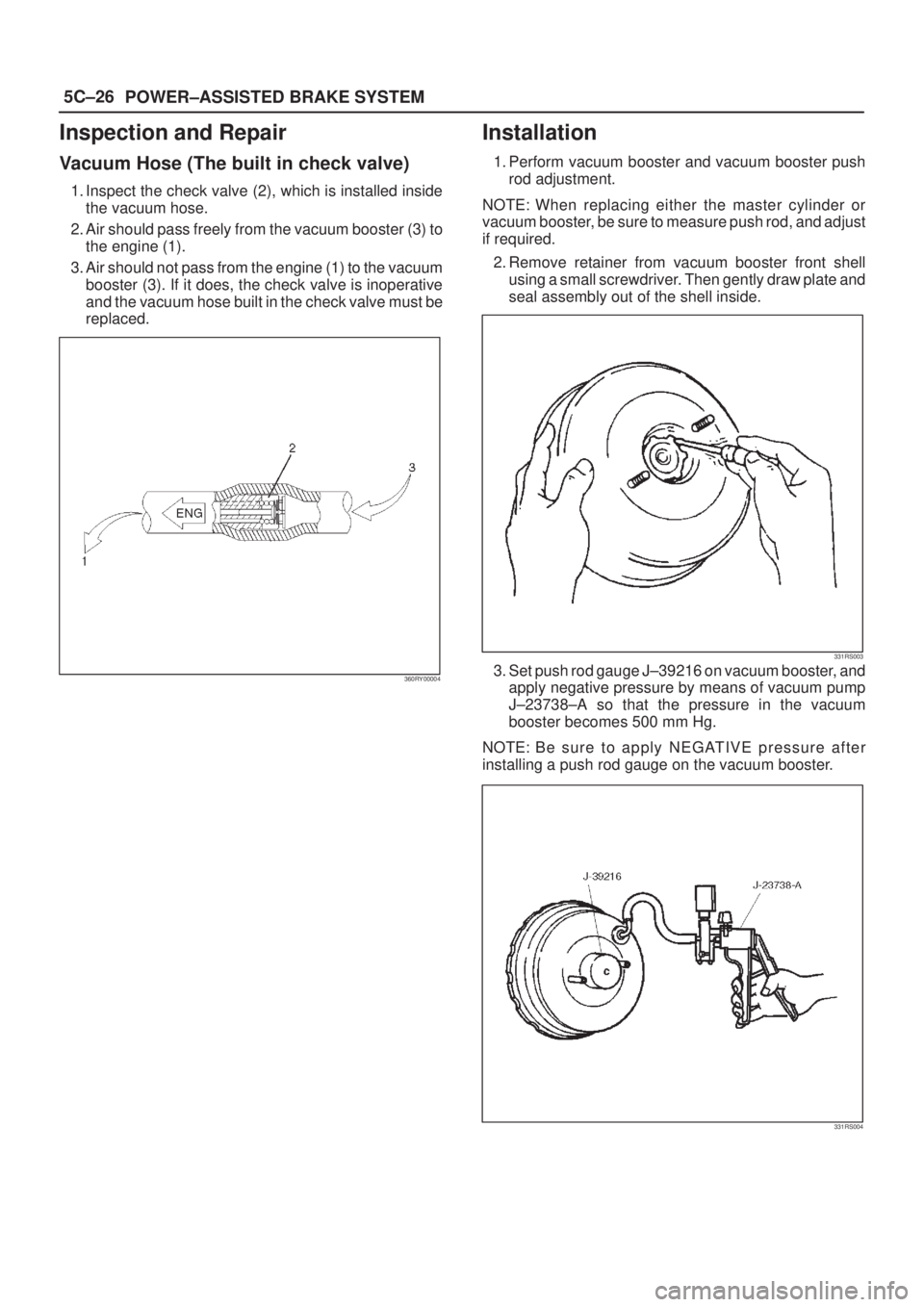
5C±26
POWER±ASSISTED BRAKE SYSTEM
Inspection and Repair
Vacuum Hose (The built in check valve)
1. Inspect the check valve (2), which is installed inside
the vacuum hose.
2. Air should pass freely from the vacuum booster (3) to
the engine (1).
3. Air should not pass from the engine (1) to the vacuum
booster (3). If it does, the check valve is inoperative
and the vacuum hose built in the check valve must be
replaced.
360RY00004
Installation
1. Perform vacuum booster and vacuum booster push
rod adjustment.
NOTE: When replacing either the master cylinder or
vacuum booster, be sure to measure push rod, and adjust
if required.
2. Remove retainer from vacuum booster front shell
using a small screwdriver. Then gently draw plate and
seal assembly out of the shell inside.
331RS003
3. Set push rod gauge J±39216 on vacuum booster, and
apply negative pressure by means of vacuum pump
J±23738±A so that the pressure in the vacuum
booster becomes 500 mm Hg.
NOTE: Be s u r e t o apply NEGATIVE pressure after
installing a push rod gauge on the vacuum booster.
331RS004
Page 746 of 2100
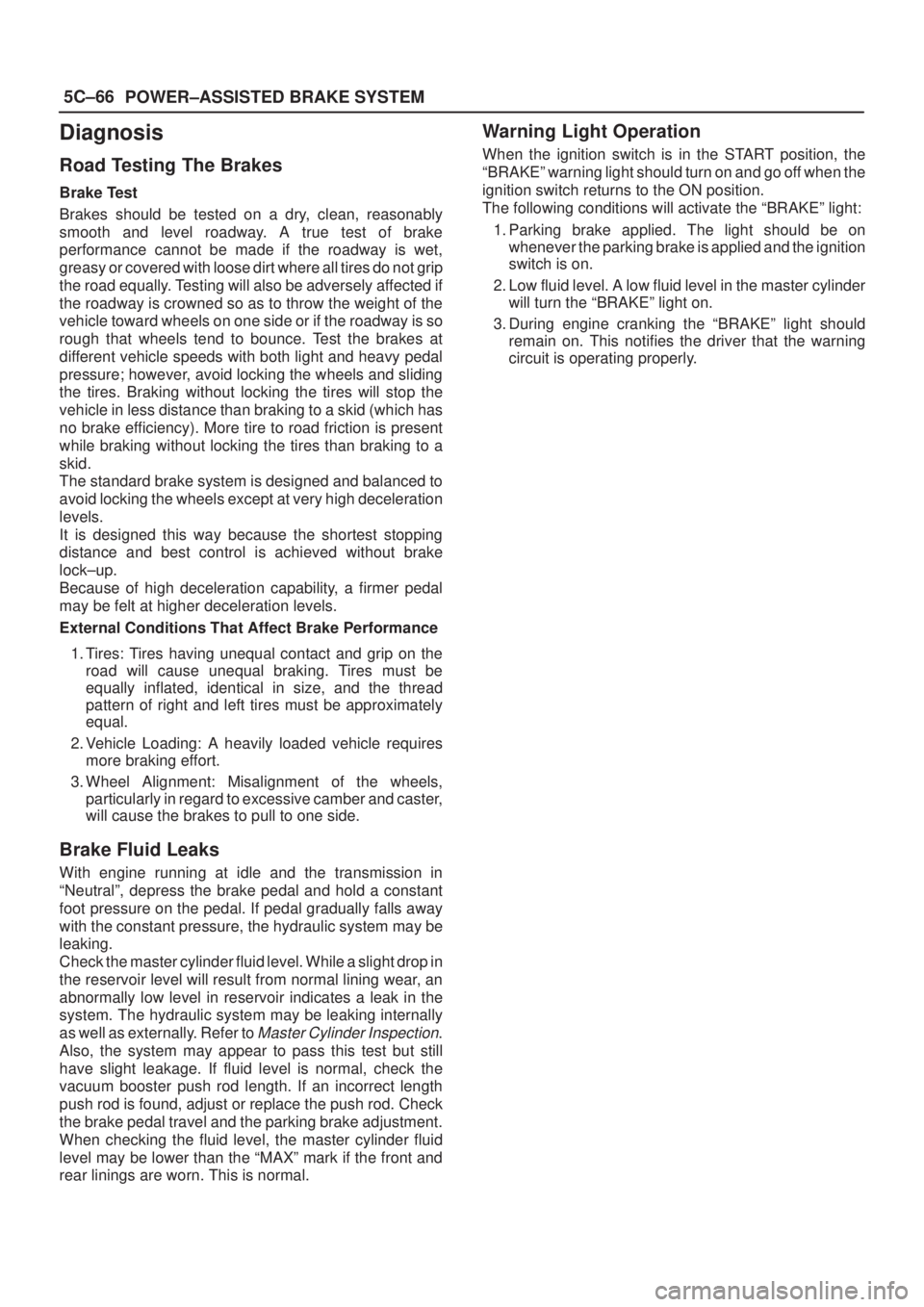
5C±66
POWER±ASSISTED BRAKE SYSTEM
Diagnosis
Road Testing The Brakes
Brake Test
Brakes should be tested on a dry, clean, reasonably
smooth and level roadway. A true test of brake
performance cannot be made if the roadway is wet,
greasy or covered with loose dirt where all tires do not grip
the road equally. Testing will also be adversely affected if
the roadway is crowned so as to throw the weight of the
vehicle toward wheels on one side or if the roadway is so
rough that wheels tend to bounce. Test the brakes at
different vehicle speeds with both light and heavy pedal
pressure; however, avoid locking the wheels and sliding
the tires. Braking without locking the tires will stop the
vehicle in less distance than braking to a skid (which has
no brake efficiency). More tire to road friction is present
while braking without locking the tires than braking to a
skid.
The standard brake system is designed and balanced to
avoid locking the wheels except at very high deceleration
levels.
It is designed this way because the shortest stopping
distance and best control is achieved without brake
lock±up.
Because of high deceleration capability, a firmer pedal
may be felt at higher deceleration levels.
External Conditions That Affect Brake Performance
1. Tires: Tires having unequal contact and grip on the
road will cause unequal braking. Tires must be
equally inflated, identical in size, and the thread
pattern of right and left tires must be approximately
equal.
2. Vehicle Loading: A heavily loaded vehicle requires
more braking effort.
3. Wheel Alignment: Misalignment of the wheels,
particularly in regard to excessive camber and caster,
will cause the brakes to pull to one side.
Brake Fluid Leaks
With engine running at idle and the transmission in
ªNeutralº, depress the brake pedal and hold a constant
foot pressure on the pedal. If pedal gradually falls away
with the constant pressure, the hydraulic system may be
leaking.
Check the master cylinder fluid level. While a slight drop in
the reservoir level will result from normal lining wear, an
abnormally low level in reservoir indicates a leak in the
system. The hydraulic system may be leaking internally
as well as externally. Refer to
Master Cylinder Inspection.
Also, the system may appear to pass this test but still
have slight leakage. If fluid level is normal, check the
vacuum booster push rod length. If an incorrect length
push rod is found, adjust or replace the push rod. Check
the brake pedal travel and the parking brake adjustment.
When checking the fluid level, the master cylinder fluid
level may be lower than the ªMAXº mark if the front and
rear linings are worn. This is normal.
Warning Light Operation
When the ignition switch is in the START position, the
ªBRAKEº warning light should turn on and go off when the
ignition switch returns to the ON position.
The following conditions will activate the ªBRAKEº light:
1. Parking brake applied. The light should be on
whenever the parking brake is applied and the ignition
switch is on.
2. Low fluid level. A low fluid level in the master cylinder
will turn the ªBRAKEº light on.
3. During engine cranking the ªBRAKEº light should
remain on. This notifies the driver that the warning
circuit is operating properly.
Page 750 of 2100
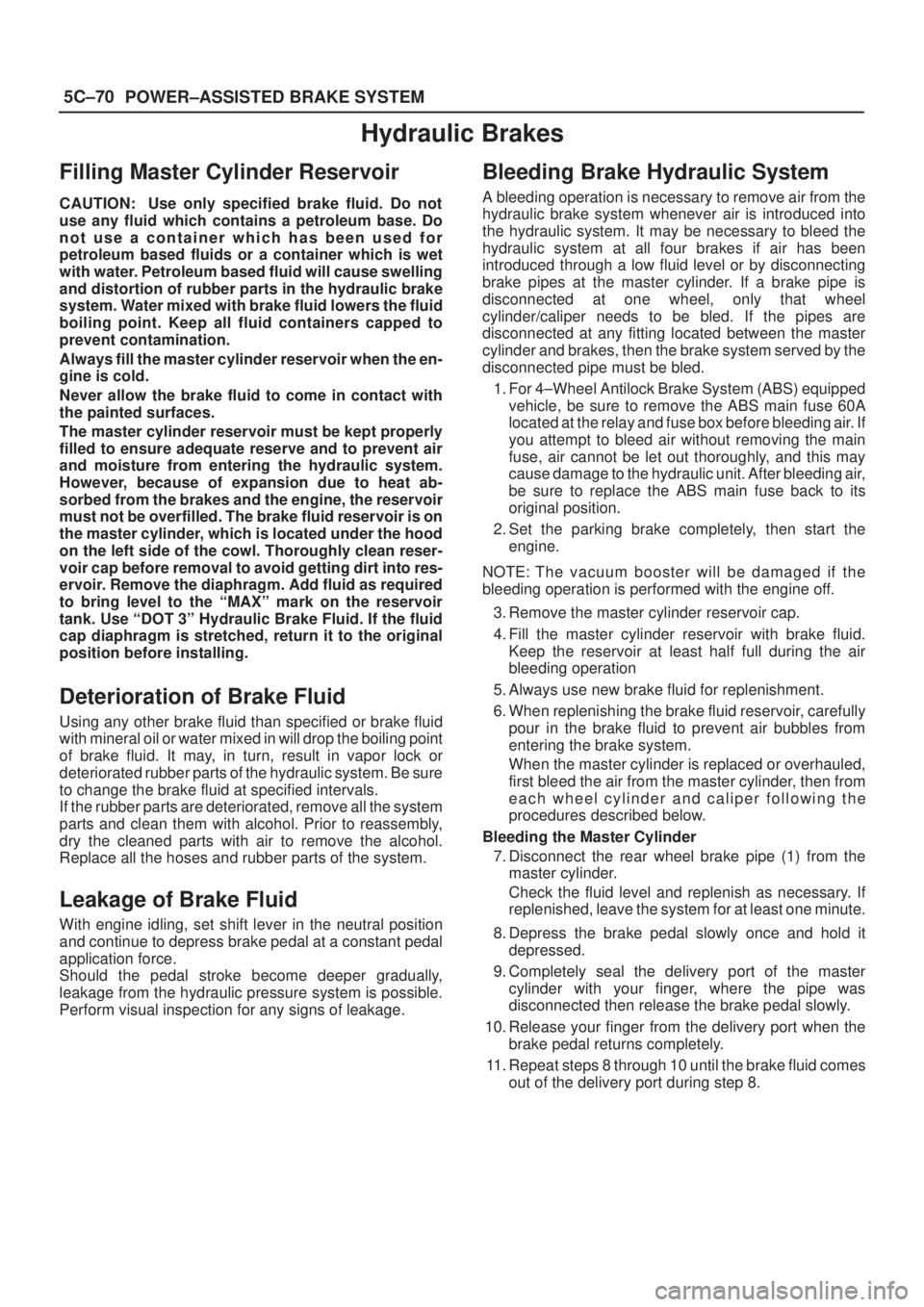
5C±70
POWER±ASSISTED BRAKE SYSTEM
Hydraulic Brakes
Filling Master Cylinder Reservoir
CAUTION: Use only specified brake fluid. Do not
use any fluid which contains a petroleum base. Do
not use a container which has been used for
petroleum based fluids or a container which is wet
with water. Petroleum based fluid will cause swelling
and distortion of rubber parts in the hydraulic brake
system. Water mixed with brake fluid lowers the fluid
boiling point. Keep all fluid containers capped to
prevent contamination.
Always fill the master cylinder reservoir when the en-
gine is cold.
Never allow the brake fluid to come in contact with
the painted surfaces.
The master cylinder reservoir must be kept properly
filled to ensure adequate reserve and to prevent air
and moisture from entering the hydraulic system.
However, because of expansion due to heat ab-
sorbed from the brakes and the engine, the reservoir
must not be overfilled. The brake fluid reservoir is on
the master cylinder, which is located under the hood
on the left side of the cowl. Thoroughly clean reser-
voir cap before removal to avoid getting dirt into res-
ervoir. Remove the diaphragm. Add fluid as required
to bring level to the ªMAXº mark on the reservoir
tank. Use ªDOT 3º Hydraulic Brake Fluid. If the fluid
cap diaphragm is stretched, return it to the original
position before installing.
Deterioration of Brake Fluid
Using any other brake fluid than specified or brake fluid
with mineral oil or water mixed in will drop the boiling point
of brake fluid. It may, in turn, result in vapor lock or
deteriorated rubber parts of the hydraulic system. Be sure
to change the brake fluid at specified intervals.
If the rubber parts are deteriorated, remove all the system
parts and clean them with alcohol. Prior to reassembly,
dry the cleaned parts with air to remove the alcohol.
Replace all the hoses and rubber parts of the system.
Leakage of Brake Fluid
With engine idling, set shift lever in the neutral position
and continue to depress brake pedal at a constant pedal
application force.
Should the pedal stroke become deeper gradually,
leakage from the hydraulic pressure system is possible.
Perform visual inspection for any signs of leakage.
Bleeding Brake Hydraulic System
A bleeding operation is necessary to remove air from the
hydraulic brake system whenever air is introduced into
the hydraulic system. It may be necessary to bleed the
hydraulic system at all four brakes if air has been
introduced through a low fluid level or by disconnecting
brake pipes at the master cylinder. If a brake pipe is
disconnected at one wheel, only that wheel
cylinder/caliper needs to be bled. If the pipes are
disconnected at any fitting located between the master
cylinder and brakes, then the brake system served by the
disconnected pipe must be bled.
1. For 4±Wheel Antilock Brake System (ABS) equipped
vehicle, be sure to remove the ABS main fuse 60A
located at the relay and fuse box before bleeding air. If
you attempt to bleed air without removing the main
fuse, air cannot be let out thoroughly, and this may
cause damage to the hydraulic unit. After bleeding air,
be sure to replace the ABS main fuse back to its
original position.
2. Set the parking brake completely, then start the
engine.
NOTE: The vacuum booster will be damaged if the
bleeding operation is performed with the engine off.
3. Remove the master cylinder reservoir cap.
4. Fill the master cylinder reservoir with brake fluid.
Keep the reservoir at least half full during the air
bleeding operation
5. Always use new brake fluid for replenishment.
6. When replenishing the brake fluid reservoir, carefully
pour in the brake fluid to prevent air bubbles from
entering the brake system.
When the master cylinder is replaced or overhauled,
first bleed the air from the master cylinder, then from
each wheel cylinder and caliper following the
procedures described below.
Bleeding the Master Cylinder
7. Disconnect the rear wheel brake pipe (1) from the
master cylinder.
Check the fluid level and replenish as necessary. If
replenished, leave the system for at least one minute.
8. Depress the brake pedal slowly once and hold it
depressed.
9. Completely seal the delivery port of the master
cylinder with your finger, where the pipe was
disconnected then release the brake pedal slowly.
10. Release your finger from the delivery port when the
brake pedal returns completely.
11. Repeat steps 8 through 10 until the brake fluid comes
out of the delivery port during step 8.
Page 751 of 2100
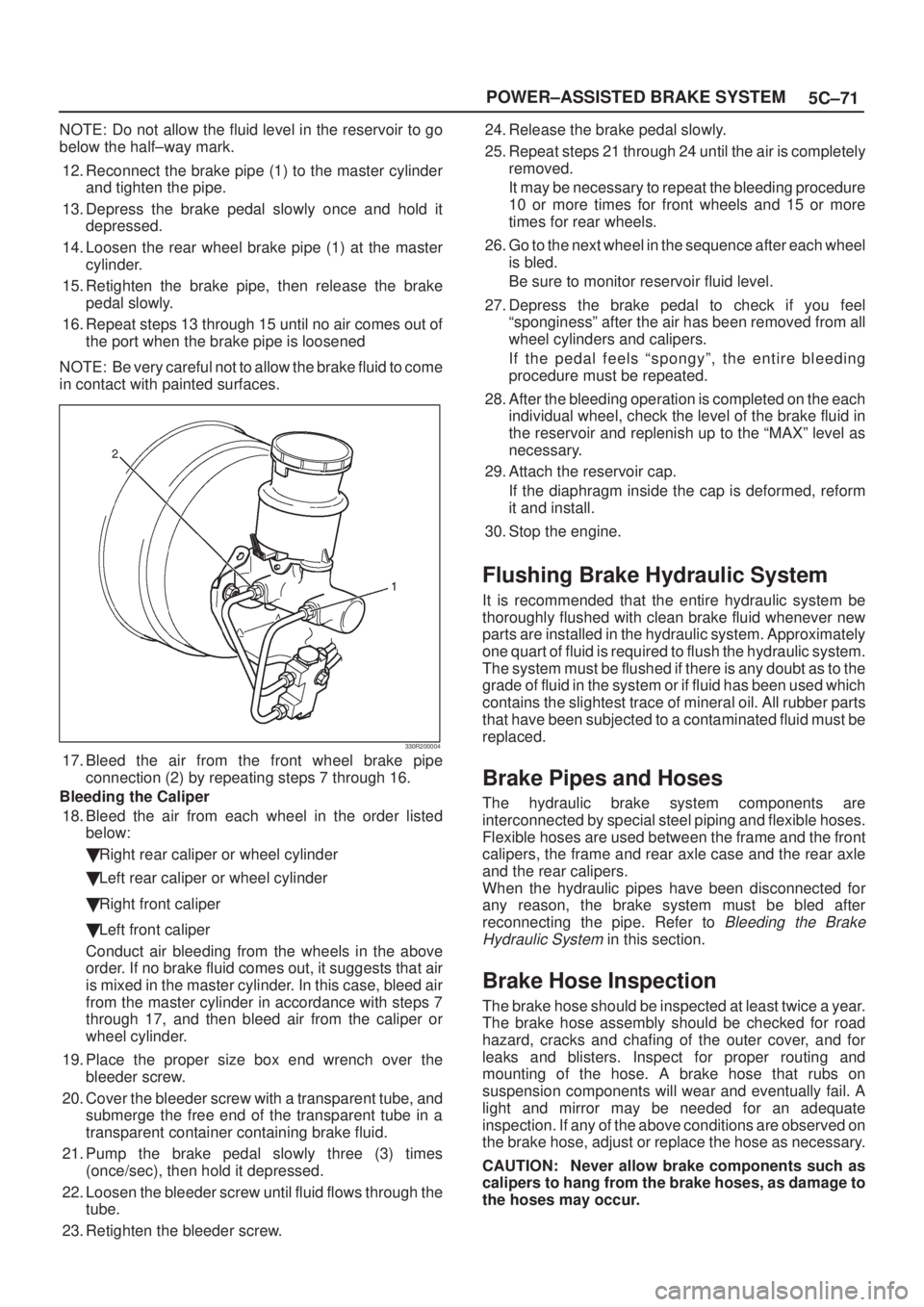
5C±71 POWER±ASSISTED BRAKE SYSTEM
NOTE: Do not allow the fluid level in the reservoir to go
below the half±way mark.
12. Reconnect the brake pipe (1) to the master cylinder
and tighten the pipe.
13. Depress the brake pedal slowly once and hold it
depressed.
14. Loosen the rear wheel brake pipe (1) at the master
cylinder.
15. Retighten the brake pipe, then release the brake
pedal slowly.
16. Repeat steps 13 through 15 until no air comes out of
the port when the brake pipe is loosened
NOTE: Be very careful not to allow the brake fluid to come
in contact with painted surfaces.
330R200004
17. Bleed the air from the front wheel brake pipe
connection (2) by repeating steps 7 through 16.
Bleeding the Caliper
18. Bleed the air from each wheel in the order listed
below:
Right rear caliper or wheel cylinder
Left rear caliper or wheel cylinder
Right front caliper
Left front caliper
Conduct air bleeding from the wheels in the above
order. If no brake fluid comes out, it suggests that air
is mixed in the master cylinder. In this case, bleed air
from the master cylinder in accordance with steps 7
through 17, and then bleed air from the caliper or
wheel cylinder.
19. Place the proper size box end wrench over the
bleeder screw.
20. Cover the bleeder screw with a transparent tube, and
submerge the free end of the transparent tube in a
transparent container containing brake fluid.
21. Pump the brake pedal slowly three (3) times
(once/sec), then hold it depressed.
22. Loosen the bleeder screw until fluid flows through the
tube.
23. Retighten the bleeder screw.24. Release the brake pedal slowly.
25. Repeat steps 21 through 24 until the air is completely
removed.
It may be necessary to repeat the bleeding procedure
10 or more times for front wheels and 15 or more
times for rear wheels.
26. Go to the next wheel in the sequence after each wheel
is bled.
Be sure to monitor reservoir fluid level.
27. Depress the brake pedal to check if you feel
ªsponginessº after the air has been removed from all
wheel cylinders and calipers.
If the pedal feels ªspongyº, the entire bleeding
procedure must be repeated.
28. After the bleeding operation is completed on the each
individual wheel, check the level of the brake fluid in
the reservoir and replenish up to the ªMAXº level as
necessary.
29. Attach the reservoir cap.
If the diaphragm inside the cap is deformed, reform
it and install.
30. Stop the engine.
Flushing Brake Hydraulic System
It is recommended that the entire hydraulic system be
thoroughly flushed with clean brake fluid whenever new
parts are installed in the hydraulic system. Approximately
one quart of fluid is required to flush the hydraulic system.
The system must be flushed if there is any doubt as to the
grade of fluid in the system or if fluid has been used which
contains the slightest trace of mineral oil. All rubber parts
that have been subjected to a contaminated fluid must be
replaced.
Brake Pipes and Hoses
The hydraulic brake system components are
interconnected by special steel piping and flexible hoses.
Flexible hoses are used between the frame and the front
calipers, the frame and rear axle case and the rear axle
and the rear calipers.
When the hydraulic pipes have been disconnected for
any reason, the brake system must be bled after
reconnecting the pipe. Refer to
Bleeding the Brake
Hydraulic System
in this section.
Brake Hose Inspection
The brake hose should be inspected at least twice a year.
The brake hose assembly should be checked for road
hazard, cracks and chafing of the outer cover, and for
leaks and blisters. Inspect for proper routing and
mounting of the hose. A brake hose that rubs on
suspension components will wear and eventually fail. A
light and mirror may be needed for an adequate
inspection. If any of the above conditions are observed on
the brake hose, adjust or replace the hose as necessary.
CAUTION: Never allow brake components such as
calipers to hang from the brake hoses, as damage to
the hoses may occur.
Page 757 of 2100
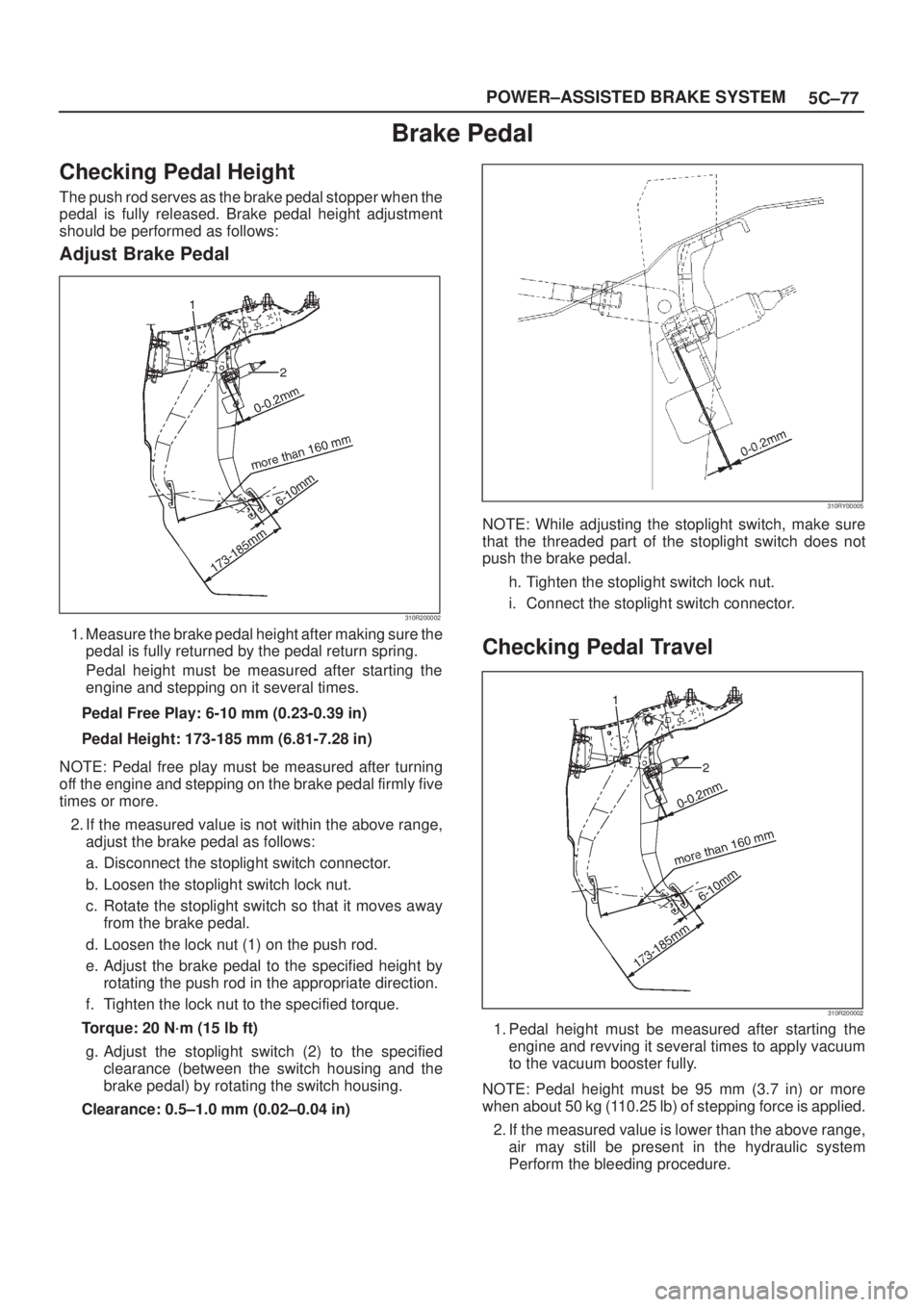
5C±77 POWER±ASSISTED BRAKE SYSTEM
Brake Pedal
Checking Pedal Height
The push rod serves as the brake pedal stopper when the
pedal is fully released. Brake pedal height adjustment
should be performed as follows:
Adjust Brake Pedal
310R200002
1. Measure the brake pedal height after making sure the
pedal is fully returned by the pedal return spring.
Pedal height must be measured after starting the
engine and stepping on it several times.
Pedal Free Play: 6-10 mm (0.23-0.39 in)
Pedal Height: 173-185 mm (6.81-7.28 in)
NOTE: Pedal free play must be measured after turning
off the engine and stepping on the brake pedal firmly five
times or more.
2. If the measured value is not within the above range,
adjust the brake pedal as follows:
a. Disconnect the stoplight switch connector.
b. Loosen the stoplight switch lock nut.
c. Rotate the stoplight switch so that it moves away
from the brake pedal.
d. Loosen the lock nut (1) on the push rod.
e. Adjust the brake pedal to the specified height by
rotating the push rod in the appropriate direction.
f. Tighten the lock nut to the specified torque.
Torque: 20 N´m (15 lb ft)
g. Adjust the stoplight switch (2) to the specified
clearance (between the switch housing and the
brake pedal) by rotating the switch housing.
Clearance: 0.5±1.0 mm (0.02±0.04 in)
310RY00005
NOTE: While adjusting the stoplight switch, make sure
that the threaded part of the stoplight switch does not
push the brake pedal.
h. Tighten the stoplight switch lock nut.
i. Connect the stoplight switch connector.
Checking Pedal Travel
310R200002
1. Pedal height must be measured after starting the
engine and revving it several times to apply vacuum
to the vacuum booster fully.
NOTE: Pedal height must be 95 mm (3.7 in) or more
when about 50 kg (110.25 lb) of stepping force is applied.
2. If the measured value is lower than the above range,
air may still be present in the hydraulic system
Perform the bleeding procedure.
Page 766 of 2100
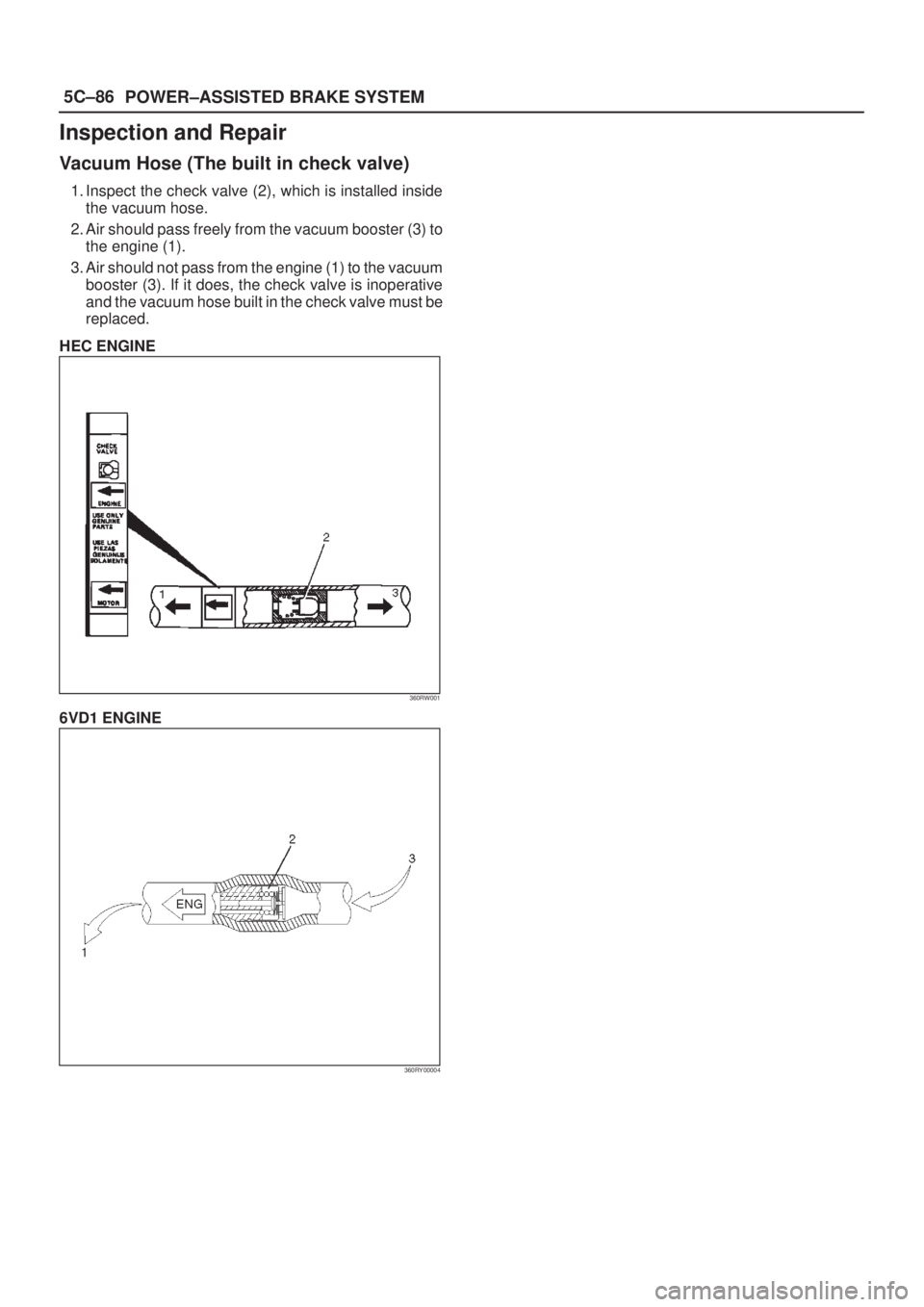
5C±86
POWER±ASSISTED BRAKE SYSTEM
Inspection and Repair
Vacuum Hose (The built in check valve)
1. Inspect the check valve (2), which is installed inside
the vacuum hose.
2. Air should pass freely from the vacuum booster (3) to
the engine (1).
3. Air should not pass from the engine (1) to the vacuum
booster (3). If it does, the check valve is inoperative
and the vacuum hose built in the check valve must be
replaced.
HEC ENGINE
360RW001
6VD1 ENGINE
360RY00004
Page 814 of 2100
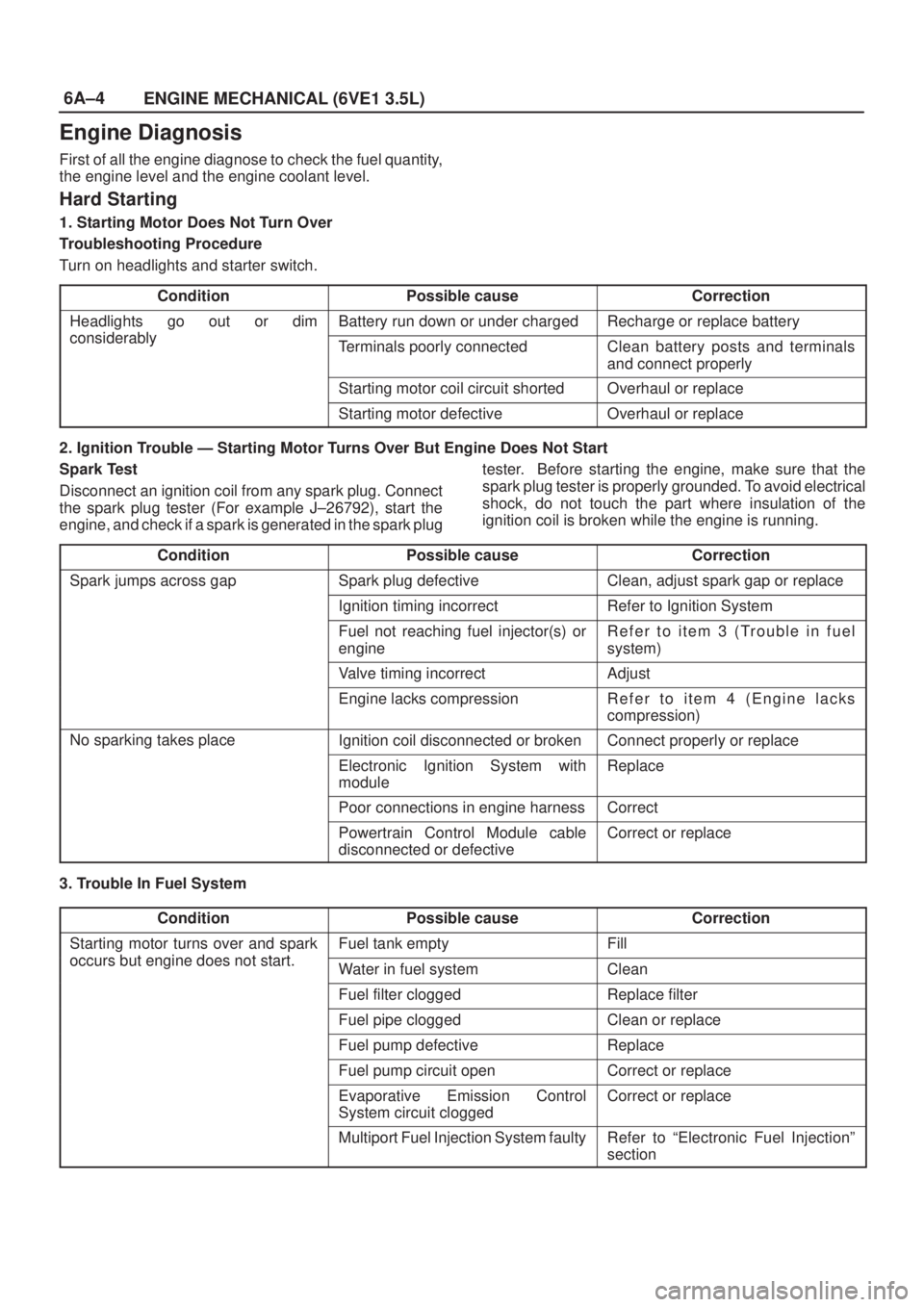
6A±4
ENGINE MECHANICAL (6VE1 3.5L)
Engine Diagnosis
First of all the engine diagnose to check the fuel quantity,
the engine level and the engine coolant level.
Hard Starting
1. Starting Motor Does Not Turn Over
Troubleshooting Procedure
Turn on headlights and starter switch.
Condition
Possible causeCorrection
Headlights go out or dim
considerably
Battery run down or under chargedRecharge or replace battery
considerablyTerminals poorly connectedClean battery posts and terminals
and connect properly
Starting motor coil circuit shortedOverhaul or replace
Starting motor defectiveOverhaul or replace
2. Ignition Trouble Ð Starting Motor Turns Over But Engine Does Not Start
Spark Test
Disconnect an ignition coil from any spark plug. Connect
the spark plug tester (For example J±26792), start the
engine, and check if a spark is generated in the spark plugtester. Before starting the engine, make sure that the
spark plug tester is properly grounded. To avoid electrical
shock, do not touch the part where insulation of the
ignition coil is broken while the engine is running.
Condition
Possible causeCorrection
Spark jumps across gapSpark plug defectiveClean, adjust spark gap or replace
Ignition timing incorrectRefer to Ignition System
Fuel not reaching fuel injector(s) or
engineRefer to item 3 (Trouble in fuel
system)
Valve timing incorrectAdjust
Engine lacks compressionRefer to item 4 (Engine lacks
compression)
No sparking takes placeIgnition coil disconnected or brokenConnect properly or replace
Electronic Ignition System with
moduleReplace
Poor connections in engine harnessCorrect
Powertrain Control Module cable
disconnected or defectiveCorrect or replace
3. Trouble In Fuel System
Condition
Possible causeCorrection
Starting motor turns over and spark
occurs but engine does not start
Fuel tank emptyFill
occurs but engine does not start.Water in fuel systemClean
Fuel filter cloggedReplace filter
Fuel pipe cloggedClean or replace
Fuel pump defectiveReplace
Fuel pump circuit openCorrect or replace
Evaporative Emission Control
System circuit cloggedCorrect or replace
Multiport Fuel Injection System faultyRefer to ªElectronic Fuel Injectionº
section
Page 815 of 2100
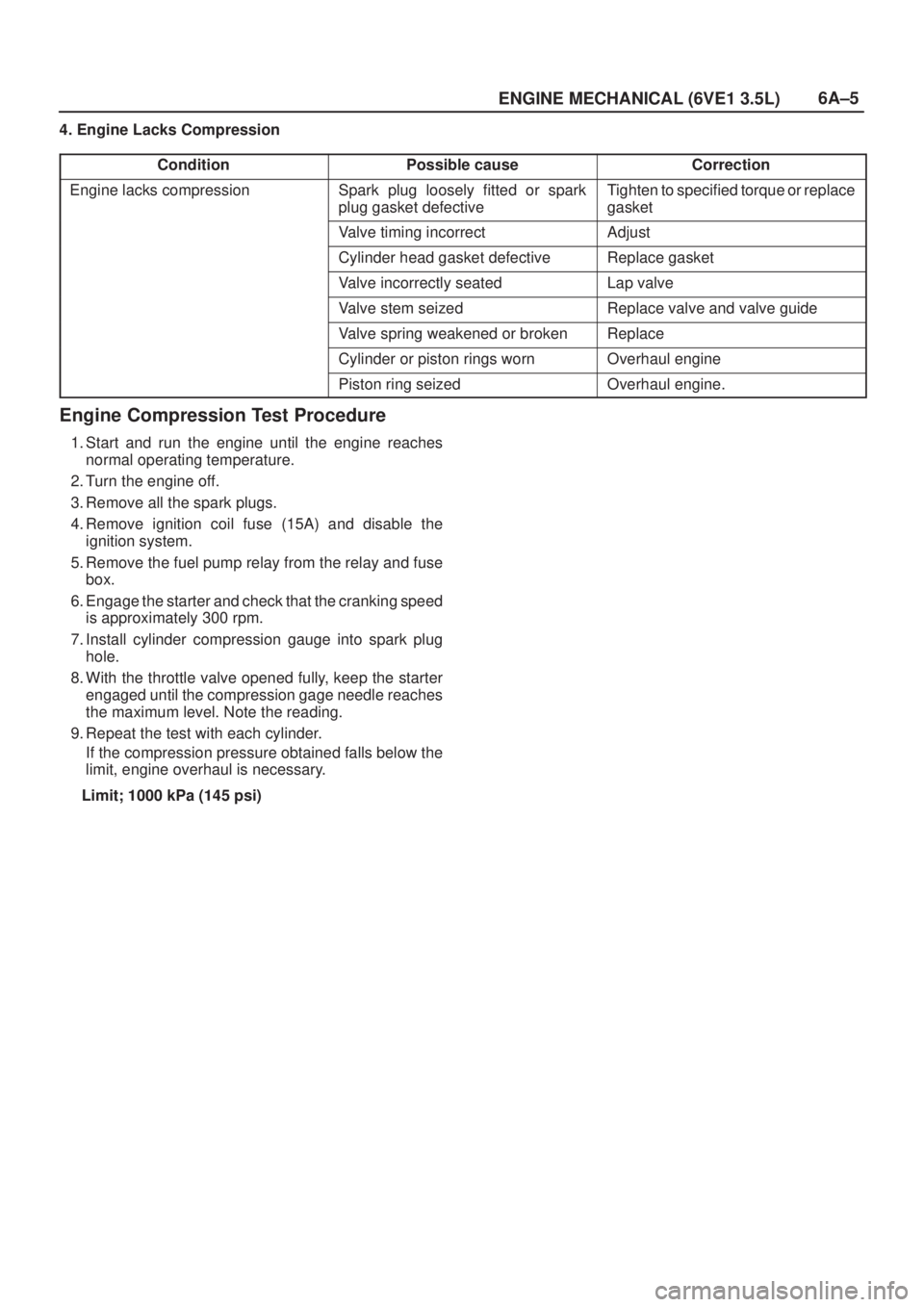
6A±5
ENGINE MECHANICAL (6VE1 3.5L)
4. Engine Lacks Compression
Condition
Possible causeCorrection
Engine lacks compressionSpark plug loosely fitted or spark
plug gasket defectiveTighten to specified torque or replace
gasket
Valve timing incorrectAdjust
Cylinder head gasket defectiveReplace gasket
Valve incorrectly seatedLap valve
Valve stem seizedReplace valve and valve guide
Valve spring weakened or brokenReplace
Cylinder or piston rings wornOverhaul engine
Piston ring seizedOverhaul engine.
Engine Compression Test Procedure
1. Start and run the engine until the engine reaches
normal operating temperature.
2. Turn the engine off.
3. Remove all the spark plugs.
4. Remove ignition coil fuse (15A) and disable the
ignition system.
5. Remove the fuel pump relay from the relay and fuse
box.
6. Engage the starter and check that the cranking speed
is approximately 300 rpm.
7. Install cylinder compression gauge into spark plug
hole.
8. With the throttle valve opened fully, keep the starter
engaged until the compression gage needle reaches
the maximum level. Note the reading.
9. Repeat the test with each cylinder.
If the compression pressure obtained falls below the
limit, engine overhaul is necessary.
Limit; 1000 kPa (145 psi)
Page 818 of 2100
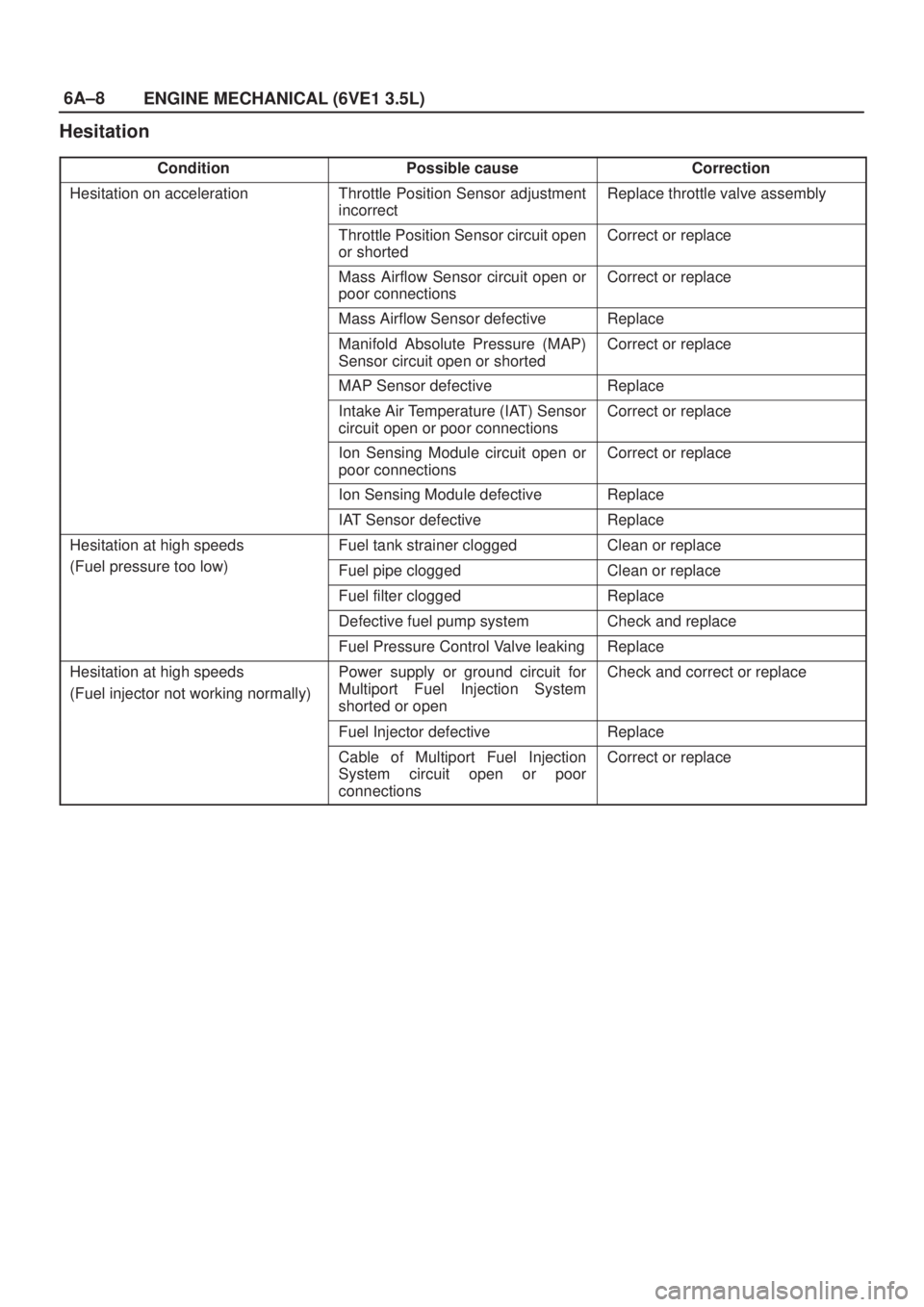
6A±8
ENGINE MECHANICAL (6VE1 3.5L)
Hesitation
ConditionPossible causeCorrection
Hesitation on accelerationThrottle Position Sensor adjustment
incorrectReplace throttle valve assembly
Throttle Position Sensor circuit open
or shortedCorrect or replace
Mass Airflow Sensor circuit open or
poor connectionsCorrect or replace
Mass Airflow Sensor defectiveReplace
Manifold Absolute Pressure (MAP)
Sensor circuit open or shortedCorrect or replace
MAP Sensor defectiveReplace
Intake Air Temperature (IAT) Sensor
circuit open or poor connectionsCorrect or replace
Ion Sensing Module circuit open or
poor connectionsCorrect or replace
Ion Sensing Module defectiveReplace
IAT Sensor defectiveReplace
Hesitation at high speedsFuel tank strainer cloggedClean or replace
(Fuel pressure too low)Fuel pipe cloggedClean or replace
Fuel filter cloggedReplace
Defective fuel pump systemCheck and replace
Fuel Pressure Control Valve leakingReplace
Hesitation at high speeds
(Fuel injector not working normally)Power supply or ground circuit for
Multiport Fuel Injection System
shorted or openCheck and correct or replace
Fuel Injector defectiveReplace
Cable of Multiport Fuel Injection
System circuit open or poor
connectionsCorrect or replace