engine coolant ISUZU TF SERIES 2004 Workshop Manual
[x] Cancel search | Manufacturer: ISUZU, Model Year: 2004, Model line: TF SERIES, Model: ISUZU TF SERIES 2004Pages: 4264, PDF Size: 72.63 MB
Page 2420 of 4264
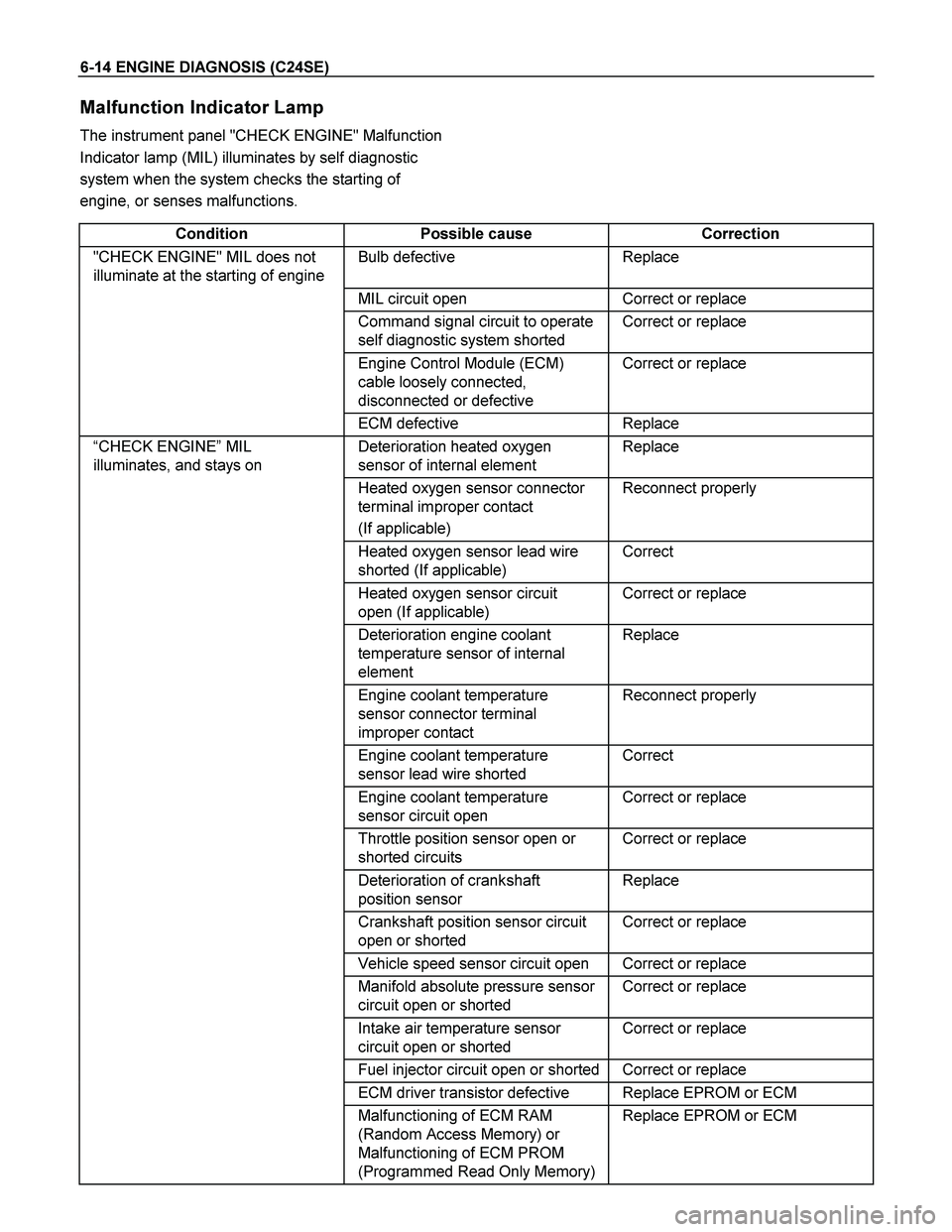
6-14 ENGINE DIAGNOSIS (C24SE)
Malfunction Indicator Lamp
The instrument panel "CHECK ENGINE" Malfunction
Indicator lamp (MIL) illuminates by self diagnostic
system when the system checks the starting of
engine, or senses malfunctions.
Condition Possible cause Correction
"CHECK ENGINE" MIL does not
illuminate at the starting of engine Bulb defective Replace
MIL circuit open Correct or replace
Command signal circuit to operate
self diagnostic system shorted Correct or replace
Engine Control Module (ECM)
cable loosely connected,
disconnected or defective Correct or replace
ECM defective Replace
“CHECK ENGINE” MIL
illuminates, and stays on Deterioration heated oxygen
sensor of internal element Replace
Heated oxygen sensor connector
terminal improper contact
(If applicable) Reconnect properly
Heated oxygen sensor lead wire
shorted (If applicable) Correct
Heated oxygen sensor circuit
open (If applicable) Correct or replace
Deterioration engine coolant
temperature sensor of internal
element Replace
Engine coolant temperature
sensor connector terminal
improper contact Reconnect properly
Engine coolant temperature
sensor lead wire shorted Correct
Engine coolant temperature
sensor circuit open Correct or replace
Throttle position sensor open or
shorted circuits Correct or replace
Deterioration of crankshaft
position sensor Replace
Crankshaft position sensor circuit
open or shorted Correct or replace
Vehicle speed sensor circuit open Correct or replace
Manifold absolute pressure sensor
circuit open or shorted Correct or replace
Intake air temperature sensor
circuit open or shorted Correct or replace
Fuel injector circuit open or shorted Correct or replace
ECM driver transistor defective Replace EPROM or ECM
Malfunctioning of ECM RAM
(Random Access Memory) or
Malfunctioning of ECM PROM
(Programmed Read Only Memory)Replace EPROM or ECM
Page 2422 of 4264
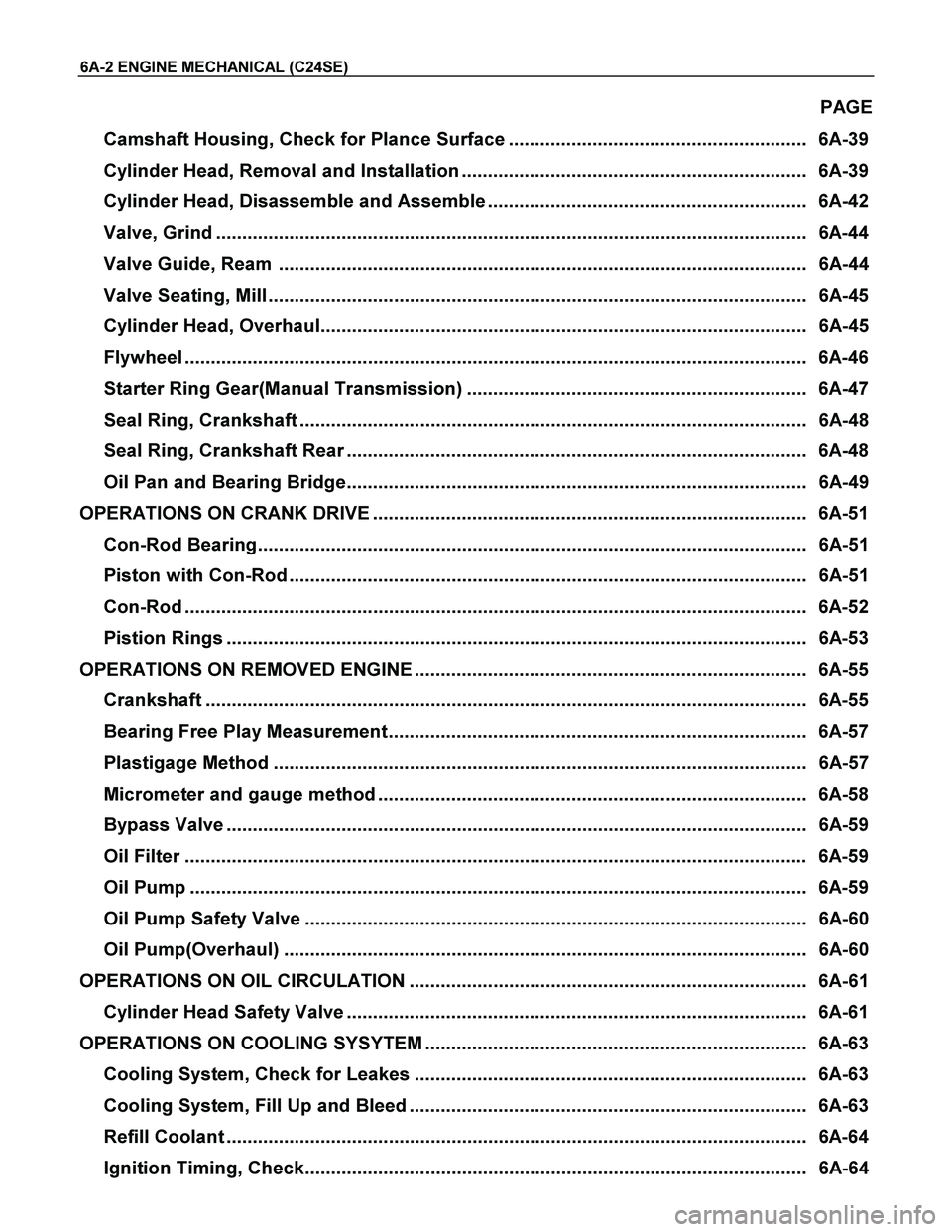
6A-2 ENGINE MECHANICAL (C24SE)
PAGE
Camshaft Housing, Check for Plance Surface ......................................................... 6A-39
Cylinder Head, Removal and Installation .................................................................. 6A-39
Cylinder Head, Disassemble and Assemble ............................................................. 6A-42
Valve, Grind ................................................................................................................. 6A-44
Valve Guide, Ream ..................................................................................................... 6A-44
Valve Seating, Mill ....................................................................................................... 6A-45
Cylinder Head, Overhaul............................................................................................. 6A-45
Flywheel ....................................................................................................................... 6A-46
Starter Ring Gear(Manual Transmission) ................................................................. 6A-47
Seal Ring, Crankshaft ................................................................................................. 6A-48
Seal Ring, Crankshaft Rear ........................................................................................ 6A-48
Oil Pan and Bearing Bridge........................................................................................ 6A-49
OPERATIONS ON CRANK DRIVE ................................................................................... 6A-51
Con-Rod Bearing......................................................................................................... 6A-51
Piston with Con-Rod ................................................................................................... 6A-51
Con-Rod ....................................................................................................................... 6A-52
Pistion Rings ............................................................................................................... 6A-53
OPERATIONS ON REMOVED ENGINE ........................................................................... 6A-55
Crankshaft ................................................................................................................... 6A-55
Bearing Free Play Measurement ................................................................................ 6A-57
Plastigage Method ...................................................................................................... 6A-57
Micrometer and gauge method .................................................................................. 6A-58
Bypass Valve ............................................................................................................... 6A-59
Oil Filter ....................................................................................................................... 6A-59
Oil Pump ...................................................................................................................... 6A-59
Oil Pump Safety Valve ................................................................................................ 6A-60
Oil Pump(Overhaul) .................................................................................................... 6A-60
OPERATIONS ON OIL CIRCULATION ............................................................................ 6A-61
Cylinder Head Safety Valve ........................................................................................ 6A-61
OPERATIONS ON COOLING SYSYTEM ......................................................................... 6A-63
Cooling System, Check for Leakes ........................................................................... 6A-63
Cooling System, Fill Up and Bleed ............................................................................ 6A-63
Refill Coolant ............................................................................................................... 6A-64
Ignition Timing, Check................................................................................................ 6A-64
Page 2431 of 4264
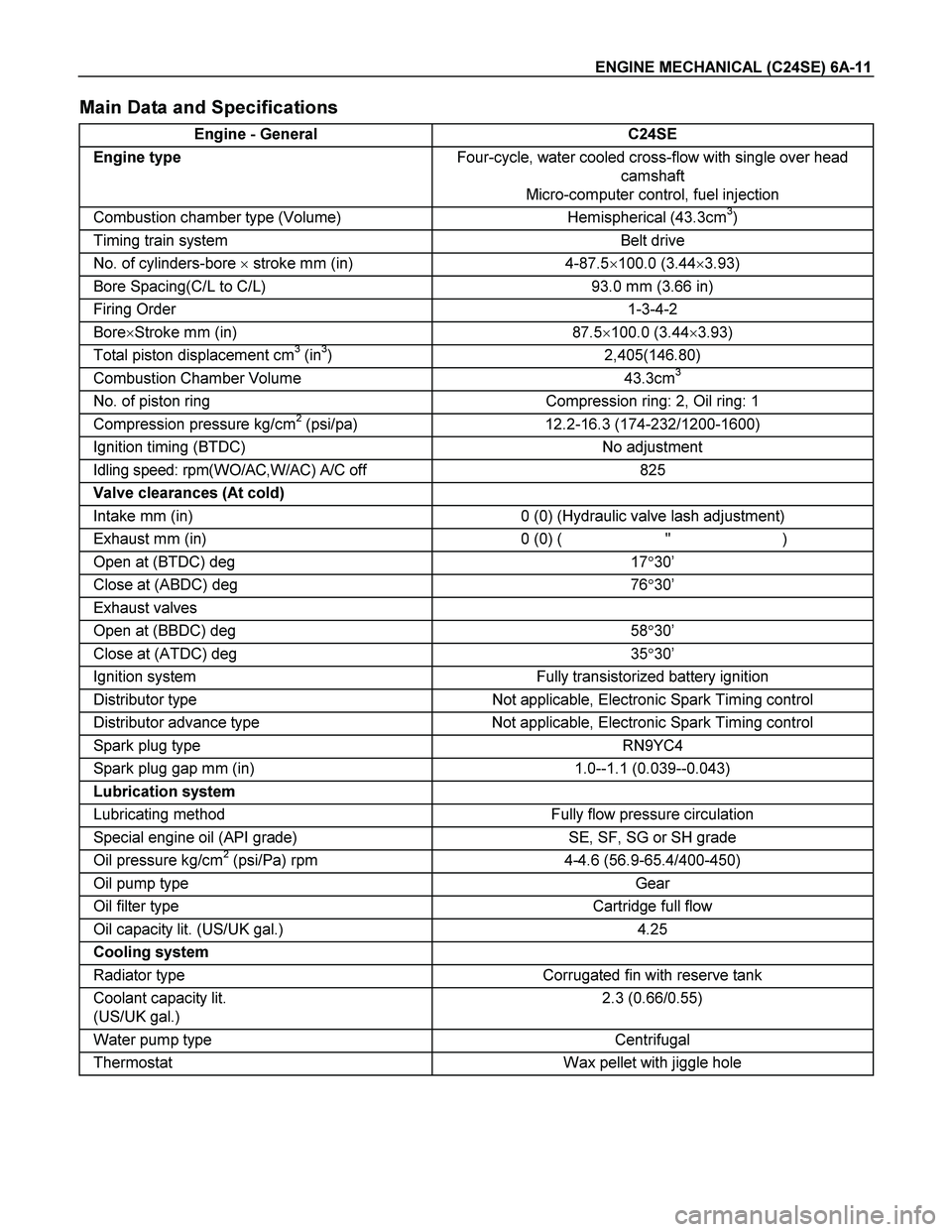
ENGINE MECHANICAL (C24SE) 6A-11
Main Data and Specifications
Engine - General C24SE
Engine type Four-cycle, water cooled cross-flow with single over head
camshaft
Micro-computer control, fuel injection
Combustion chamber type (Volume) Hemispherical (43.3cm3)
Timing train system Belt drive
No. of cylinders-bore stroke mm (in) 4-87.5100.0 (3.443.93)
Bore Spacing(C/L to C/L) 93.0 mm (3.66 in)
Firing Order 1-3-4-2
BoreStroke mm (in) 87.5100.0 (3.443.93)
Total piston displacement cm3 (in3) 2,405(146.80)
Combustion Chamber Volume 43.3cm3
No. of piston ring Compression ring: 2, Oil ring: 1
Compression pressure kg/cm2 (psi/pa) 12.2-16.3 (174-232/1200-1600)
Ignition timing (BTDC) No adjustment
Idling speed: rpm(WO/AC,W/AC) A/C off 825
Valve clearances (At cold)
Intake mm (in) 0 (0) (Hydraulic valve lash adjustment)
Exhaust mm (in) 0 (0) ( " )
Open at (BTDC) deg 1730’
Close at (ABDC) deg 7630’
Exhaust valves
Open at (BBDC) deg 5830’
Close at (ATDC) deg 3530’
Ignition system Fully transistorized battery ignition
Distributor type Not applicable, Electronic Spark Timing control
Distributor advance type Not applicable, Electronic Spark Timing control
Spark plug type RN9YC4
Spark plug gap mm (in) 1.0--1.1 (0.039--0.043)
Lubrication system
Lubricating method Fully flow pressure circulation
Special engine oil (API grade) SE, SF, SG or SH grade
Oil pressure kg/cm2 (psi/Pa) rpm 4-4.6 (56.9-65.4/400-450)
Oil pump type Gear
Oil filter type Cartridge full flow
Oil capacity lit. (US/UK gal.) 4.25
Cooling system
Radiator type Corrugated fin with reserve tank
Coolant capacity lit.
(US/UK gal.) 2.3 (0.66/0.55)
Water pump type Centrifugal
Thermostat Wax pellet with jiggle hole
Page 2433 of 4264
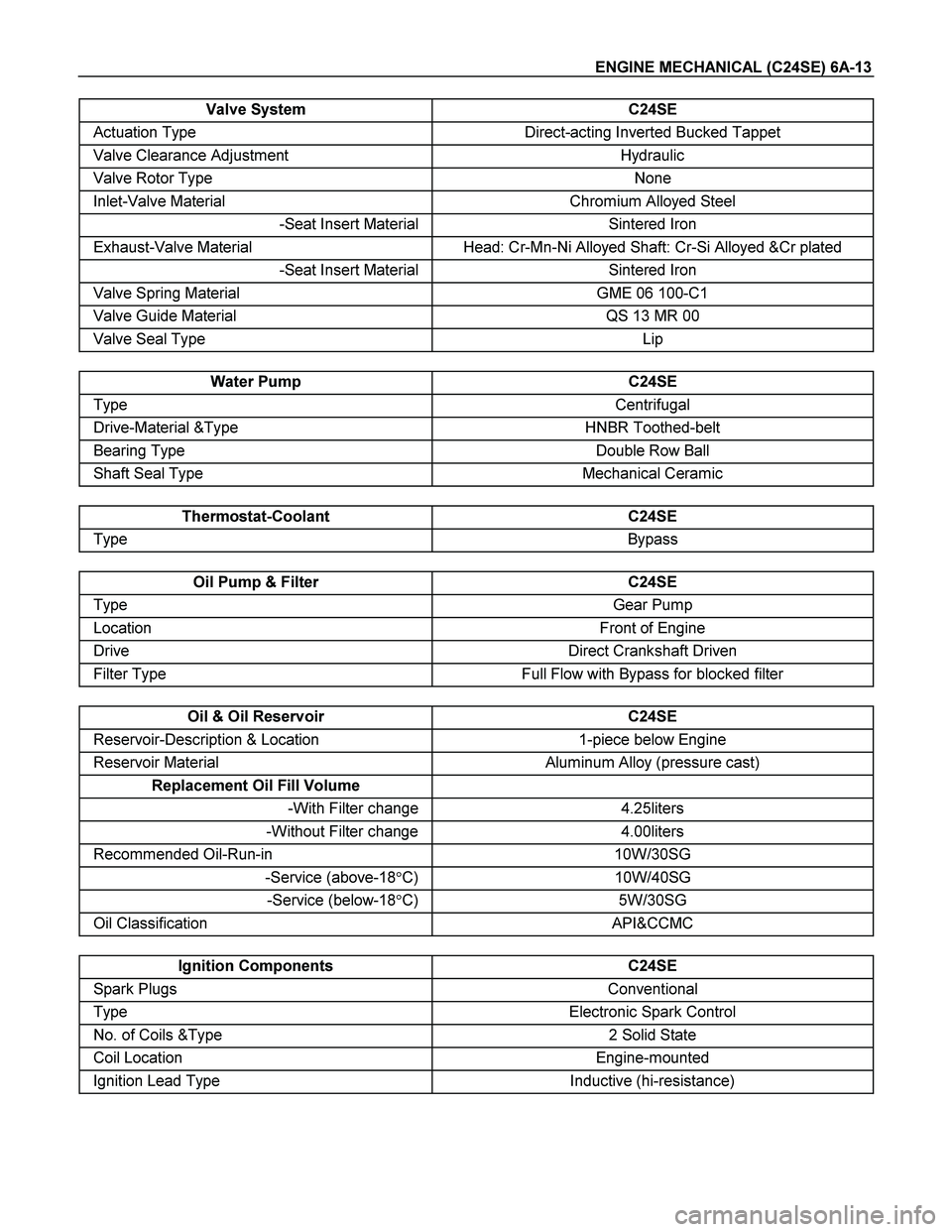
ENGINE MECHANICAL (C24SE) 6A-13
Valve System C24SE
Actuation Type Direct-acting Inverted Bucked Tappet
Valve Clearance Adjustment Hydraulic
Valve Rotor Type None
Inlet-Valve Material Chromium Alloyed Steel
-Seat Insert Material Sintered Iron
Exhaust-Valve Material Head: Cr-Mn-Ni Alloyed Shaft: Cr-Si Alloyed &Cr plated
-Seat Insert Material Sintered Iron
Valve Spring Material GME 06 100-C1
Valve Guide Material QS 13 MR 00
Valve Seal Type Lip
Water Pump C24SE
Type Centrifugal
Drive-Material &Type HNBR Toothed-belt
Bearing Type Double Row Ball
Shaft Seal Type Mechanical Ceramic
Thermostat-Coolant C24SE
Type Bypass
Oil Pump & Filter C24SE
Type Gear Pump
Location Front of Engine
Drive Direct Crankshaft Driven
Filter Type Full Flow with Bypass for blocked filter
Oil & Oil Reservoir C24SE
Reservoir-Description & Location 1-piece below Engine
Reservoir Material Aluminum Alloy (pressure cast)
Replacement Oil Fill Volume
-With Filter change 4.25liters
-Without Filter change 4.00liters
Recommended Oil-Run-in 10W/30SG
-Service (above-18C) 10W/40SG
-Service (below-18C) 5W/30SG
Oil Classification API&CCMC
Ignition Components C24SE
Spark Plugs Conventional
Type Electronic Spark Control
No. of Coils &Type 2 Solid State
Coil Location Engine-mounted
Ignition Lead Type Inductive (hi-resistance)
Page 2447 of 4264
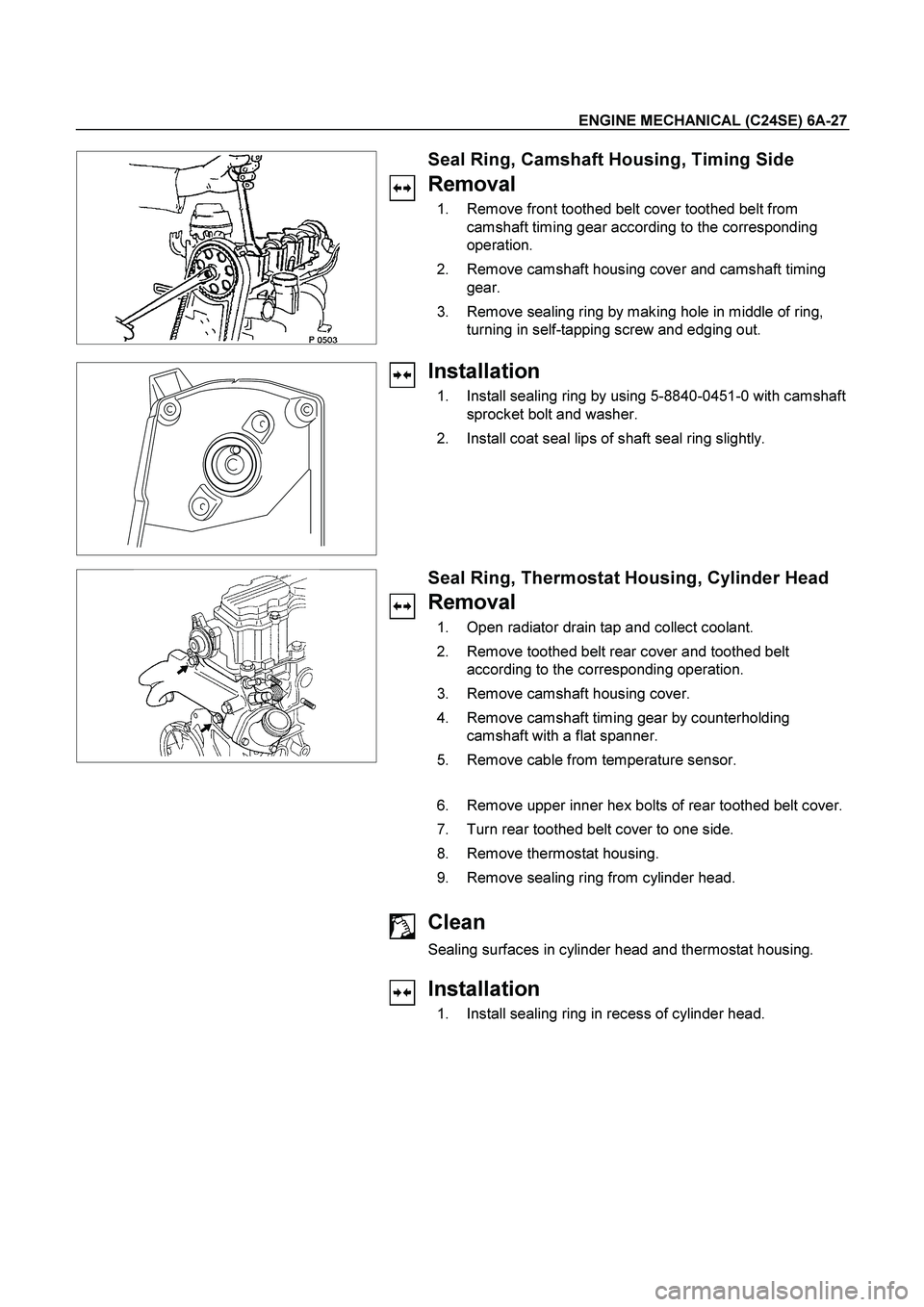
ENGINE MECHANICAL (C24SE) 6A-27
Seal Ring, Camshaft Housing, Timing Side
Removal
1. Remove front toothed belt cover toothed belt from
camshaft timing gear according to the corresponding
operation.
2. Remove camshaft housing cover and camshaft timing
gear.
3. Remove sealing ring by making hole in middle of ring,
turning in self-tapping screw and edging out.
Installation
1. Install sealing ring by using 5-8840-0451-0 with camshaft
sprocket bolt and washer.
2. Install coat seal lips of shaft seal ring slightly.
Seal Ring, Thermostat Housing, Cylinder Head
Removal
1. Open radiator drain tap and collect coolant.
2. Remove toothed belt rear cover and toothed belt
according to the corresponding operation.
3. Remove camshaft housing cover.
4. Remove camshaft timing gear by counterholding
camshaft with a flat spanner.
5. Remove cable from temperature sensor.
6. Remove upper inner hex bolts of rear toothed belt cover.
7. Turn rear toothed belt cover to one side.
8. Remove thermostat housing.
9. Remove sealing ring from cylinder head.
Clean
Sealing surfaces in cylinder head and thermostat housing.
Installation
1. Install sealing ring in recess of cylinder head.
Page 2455 of 4264
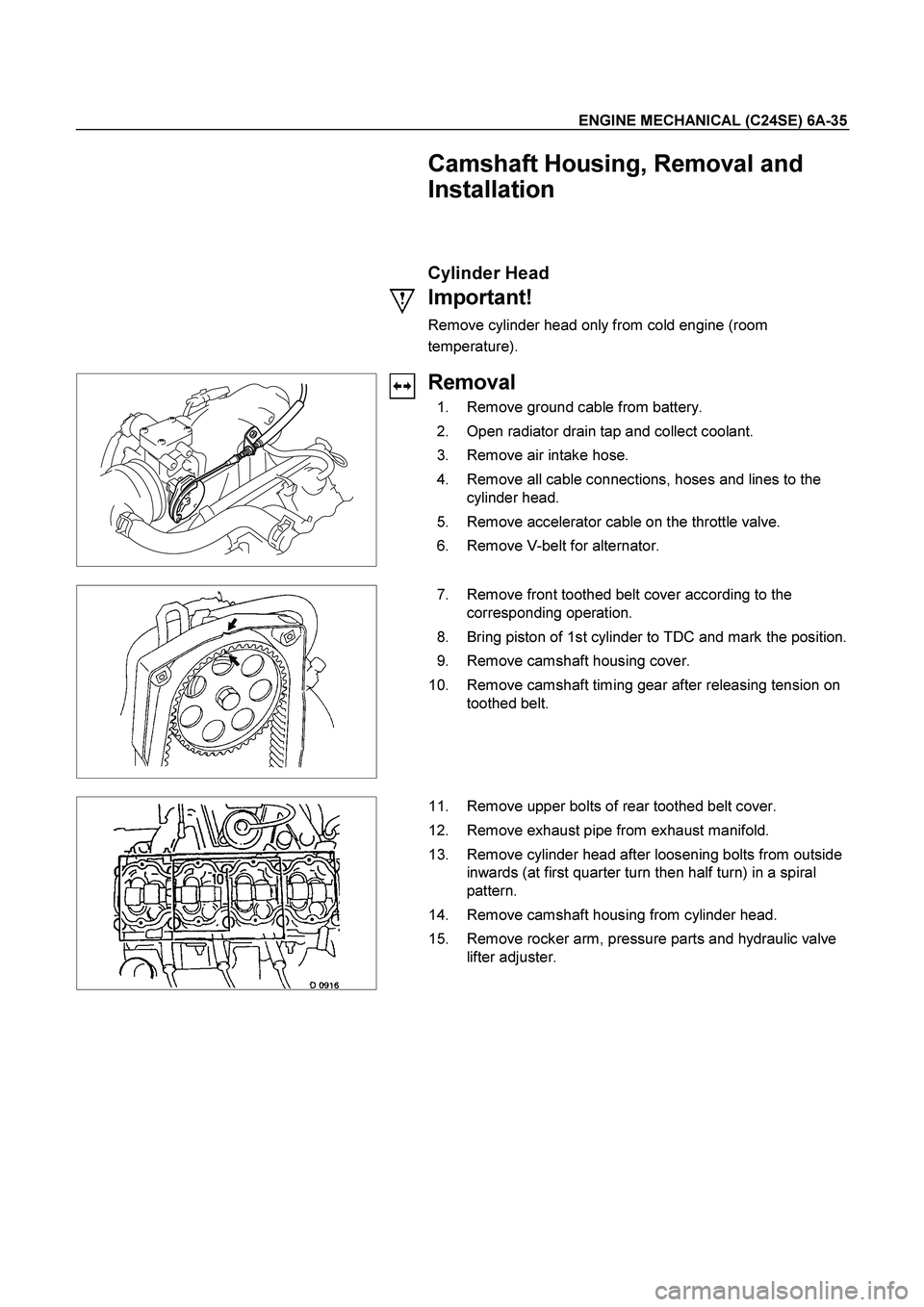
ENGINE MECHANICAL (C24SE) 6A-35
Camshaft Housing, Removal and
Installation
Cylinder Head
Important!
Remove cylinder head only from cold engine (room
temperature).
Removal
1. Remove ground cable from battery.
2. Open radiator drain tap and collect coolant.
3. Remove air intake hose.
4. Remove all cable connections, hoses and lines to the
cylinder head.
5. Remove accelerator cable on the throttle valve.
6. Remove V-belt for alternator.
7. Remove front toothed belt cover according to the
corresponding operation.
8. Bring piston of 1st cylinder to TDC and mark the position.
9. Remove camshaft housing cover.
10. Remove camshaft timing gear after releasing tension on
toothed belt.
11. Remove upper bolts of rear toothed belt cover.
12. Remove exhaust pipe from exhaust manifold.
13. Remove cylinder head after loosening bolts from outside
inwards (at first quarter turn then half turn) in a spiral
pattern.
14. Remove camshaft housing from cylinder head.
15. Remove rocker arm, pressure parts and hydraulic valve
lifter adjuster.
Page 2483 of 4264
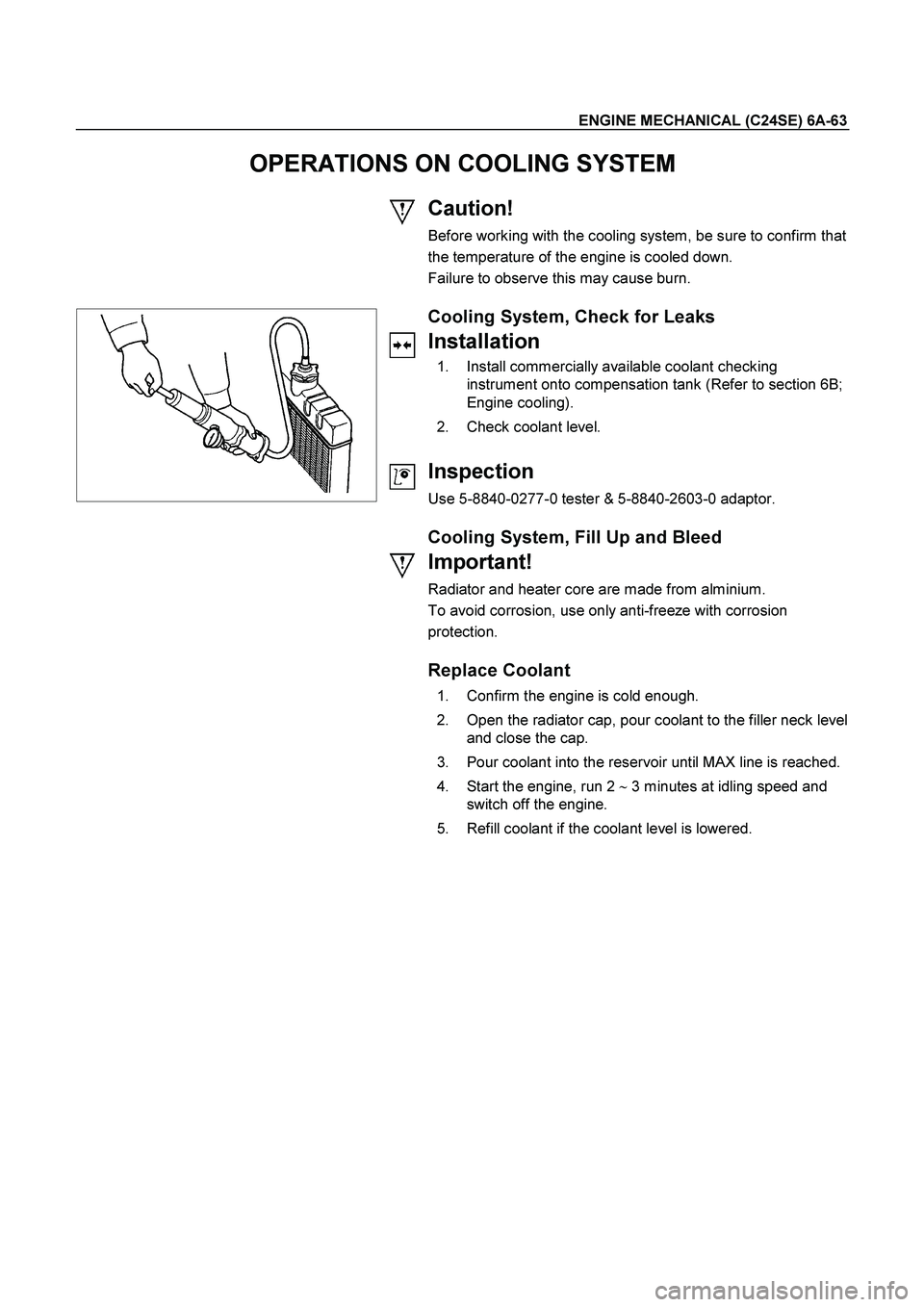
ENGINE MECHANICAL (C24SE) 6A-63
OPERATIONS ON COOLING SYSTEM
Caution!
Before working with the cooling system, be sure to confirm that
the temperature of the engine is cooled down.
Failure to observe this may cause burn.
Cooling System, Check for Leaks
Installation
1. Install commercially available coolant checking
instrument onto compensation tank (Refer to section 6B;
Engine cooling).
2. Check coolant level.
Inspection
Use 5-8840-0277-0 tester & 5-8840-2603-0 adaptor.
Cooling System, Fill Up and Bleed
Important!
Radiator and heater core are made from alminium.
To avoid corrosion, use only anti-freeze with corrosion
protection.
Replace Coolant
1. Confirm the engine is cold enough.
2. Open the radiator cap, pour coolant to the filler neck level
and close the cap.
3. Pour coolant into the reservoir until MAX line is reached.
4. Start the engine, run 2
3 minutes at idling speed and
switch off the engine.
5. Refill coolant if the coolant level is lowered.
Page 2484 of 4264
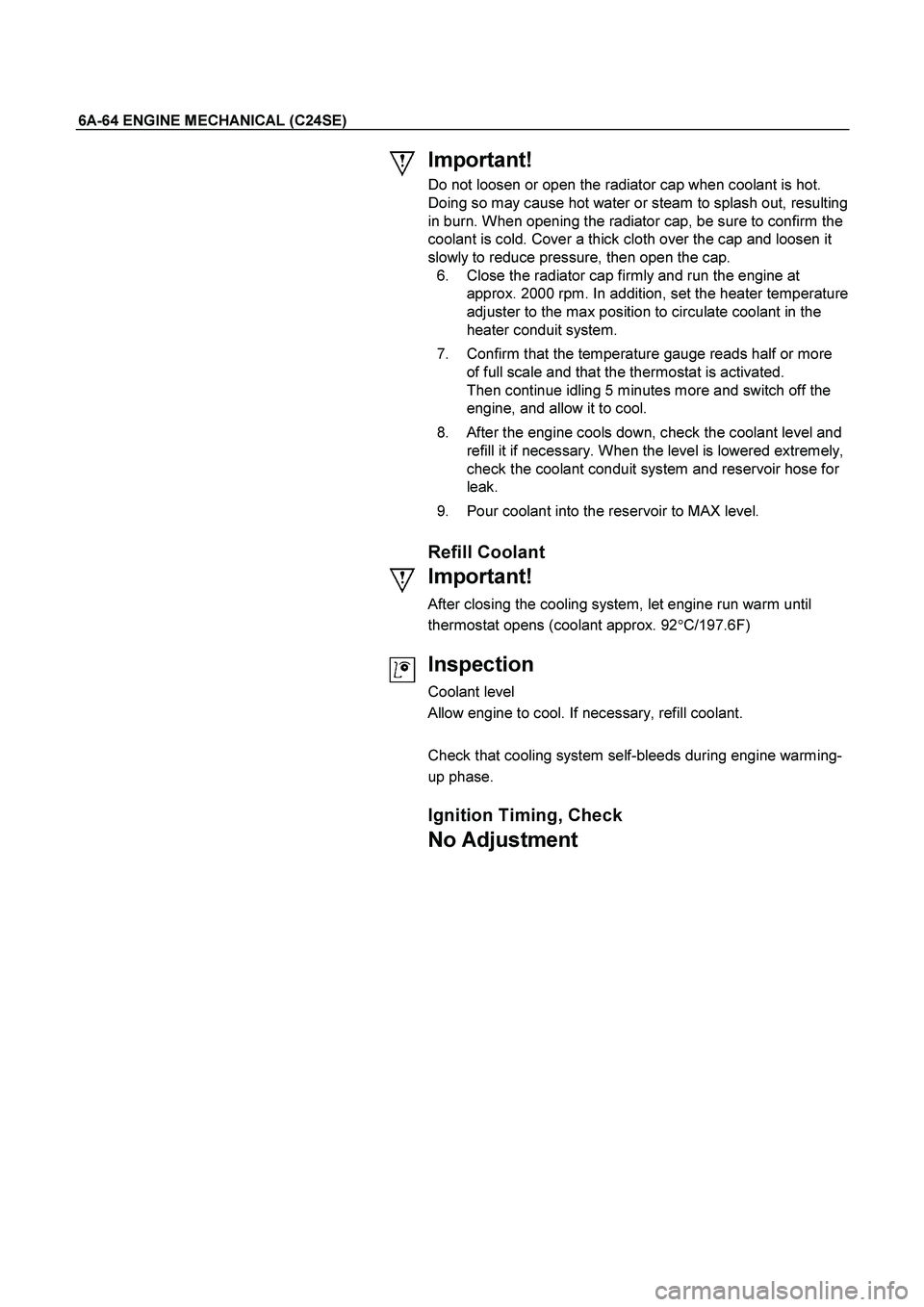
6A-64 ENGINE MECHANICAL (C24SE)
Important!
Do not loosen or open the radiator cap when coolant is hot.
Doing so may cause hot water or steam to splash out, resulting
in burn. When opening the radiator cap, be sure to confirm the
coolant is cold. Cover a thick cloth over the cap and loosen it
slowly to reduce pressure, then open the cap.
6. Close the radiator cap firmly and run the engine at
approx. 2000 rpm. In addition, set the heater temperature
adjuster to the max position to circulate coolant in the
heater conduit system.
7. Confirm that the temperature gauge reads half or more
of full scale and that the thermostat is activated.
Then continue idling 5 minutes more and switch off the
engine, and allow it to cool.
8. After the engine cools down, check the coolant level and
refill it if necessary. When the level is lowered extremely,
check the coolant conduit system and reservoir hose for
leak.
9. Pour coolant into the reservoir to MAX level.
Refill Coolant
Important!
After closing the cooling system, let engine run warm until
thermostat opens (coolant approx. 92C/197.6F)
Inspection
Coolant level
Allow engine to cool. If necessary, refill coolant.
Check that cooling system self-bleeds during engine warming-
up phase.
Ignition Timing, Check
No Adjustment
Page 2486 of 4264
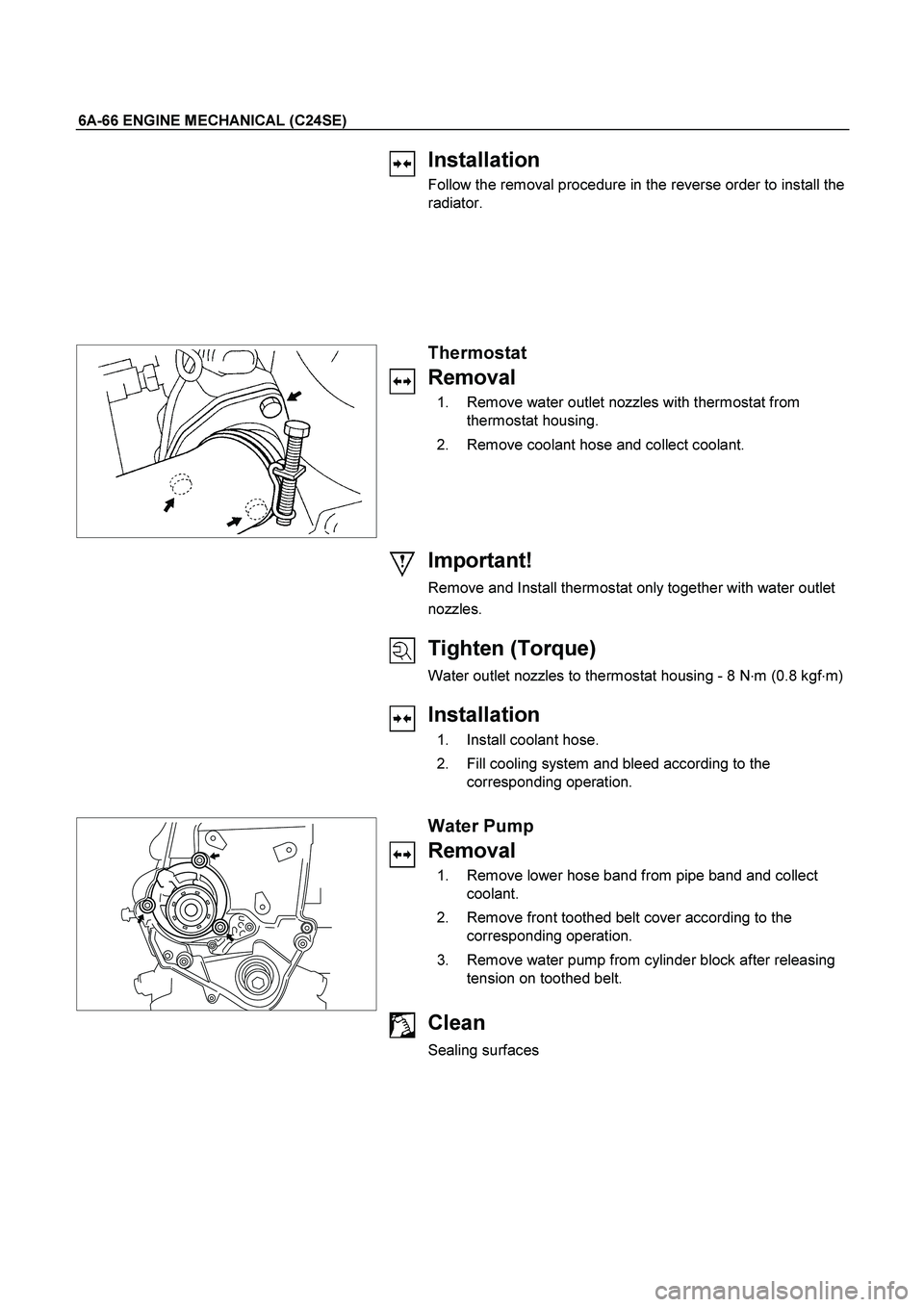
6A-66 ENGINE MECHANICAL (C24SE)
Installation
Follow the removal procedure in the reverse order to install the
radiator.
Thermostat
Removal
1. Remove water outlet nozzles with thermostat from
thermostat housing.
2. Remove coolant hose and collect coolant.
Important!
Remove and Install thermostat only together with water outlet
nozzles.
Tighten (Torque)
Water outlet nozzles to thermostat housing - 8 N
m (0.8 kgf
m)
Installation
1. Install coolant hose.
2. Fill cooling system and bleed according to the
corresponding operation.
Water Pump
Removal
1. Remove lower hose band from pipe band and collect
coolant.
2. Remove front toothed belt cover according to the
corresponding operation.
3. Remove water pump from cylinder block after releasing
tension on toothed belt.
Clean
Sealing surfaces
Page 2487 of 4264
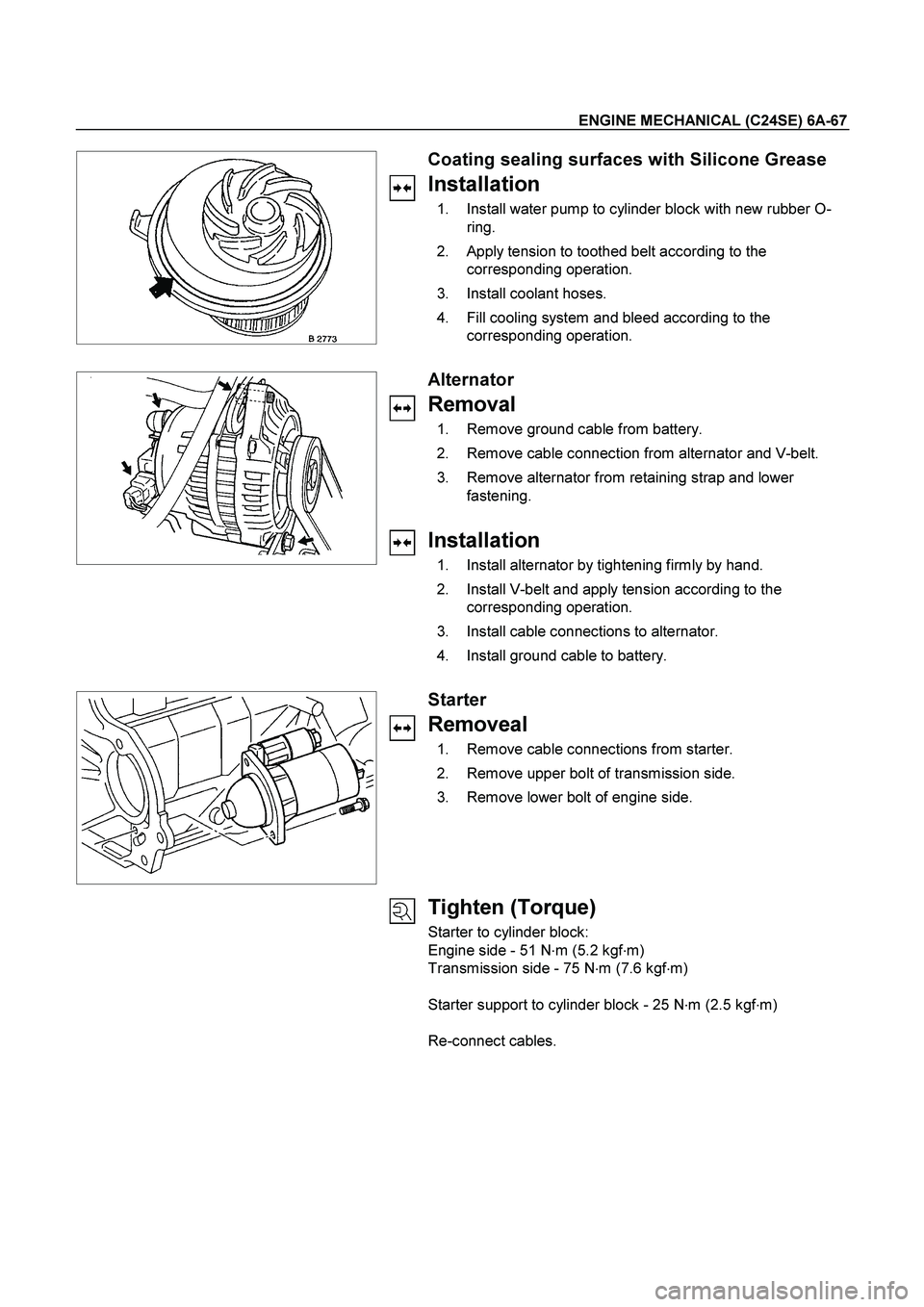
ENGINE MECHANICAL (C24SE) 6A-67
Coating sealing surfaces with Silicone Grease
Installation
1. Install water pump to cylinder block with new rubber O-
ring.
2. Apply tension to toothed belt according to the
corresponding operation.
3. Install coolant hoses.
4. Fill cooling system and bleed according to the
corresponding operation.
Alternator
Removal
1. Remove ground cable from battery.
2. Remove cable connection from alternator and V-belt.
3. Remove alternator from retaining strap and lower
fastening.
Installation
1. Install alternator by tightening firmly by hand.
2. Install V-belt and apply tension according to the
corresponding operation.
3. Install cable connections to alternator.
4. Install ground cable to battery.
Starter
Removeal
1. Remove cable connections from starter.
2. Remove upper bolt of transmission side.
3. Remove lower bolt of engine side.
Tighten (Torque)
Starter to cylinder block:
Engine side - 51 N
m (5.2 kgf
m)
Transmission side - 75 N
m (7.6 kgf
m)
Starter support to cylinder block - 25 N
m (2.5 kgf
m)
Re-connect cables.