oil ISUZU TF SERIES 2004 Workshop Manual
[x] Cancel search | Manufacturer: ISUZU, Model Year: 2004, Model line: TF SERIES, Model: ISUZU TF SERIES 2004Pages: 4264, PDF Size: 72.63 MB
Page 1209 of 4264
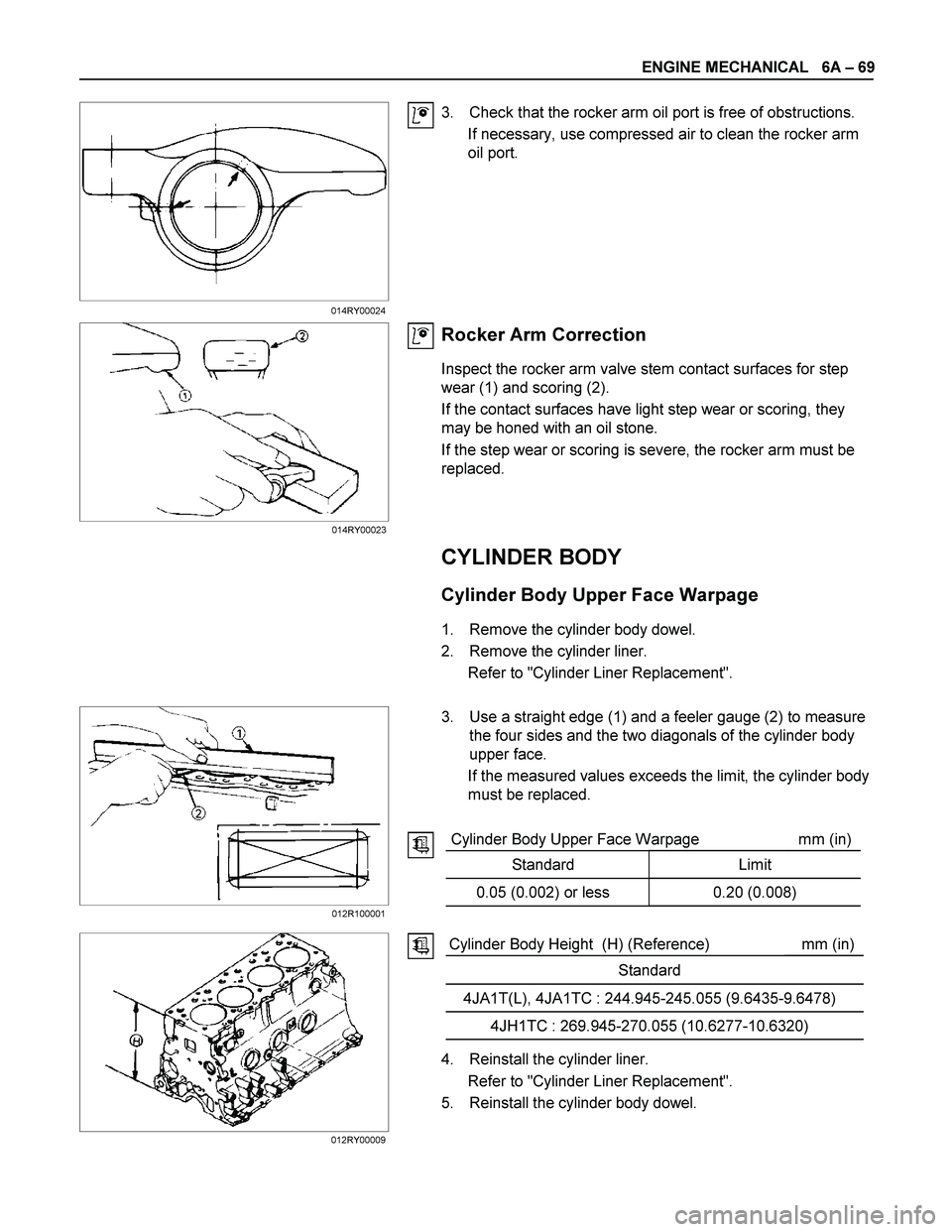
ENGINE MECHANICAL 6A – 69
3. Check that the rocker arm oil port is free of obstructions.
If necessary, use compressed air to clean the rocker arm
oil port.
Rocker Arm Correction
Inspect the rocker arm valve stem contact surfaces for step
wear (1) and scoring (2).
If the contact surfaces have light step wear or scoring, they
may be honed with an oil stone.
If the step wear or scoring is severe, the rocker arm must be
replaced.
CYLINDER BODY
Cylinder Body Upper Face Warpage
1. Remove the cylinder body dowel.
2. Remove the cylinder liner.
Refer to "Cylinder Liner Replacement".
3. Use a straight edge (1) and a feeler gauge (2) to measure
the four sides and the two diagonals of the cylinder body
upper face.
If the measured values exceeds the limit, the cylinder body
must be replaced.
Cylinder Body Upper Face Warpage mm (in)
Standard Limit
0.05 (0.002) or less 0.20 (0.008)
Cylinder Body Height (H) (Reference) mm (in)
Standard
4JA1T(L), 4JA1TC : 244.945-245.055 (9.6435-9.6478)
4JH1TC : 269.945-270.055 (10.6277-10.6320)
4. Reinstall the cylinder liner.
Refer to "Cylinder Liner Replacement".
5. Reinstall the cylinder body dowel.
014RY00024
012R100001
012RY00009014RY00023
Page 1213 of 4264
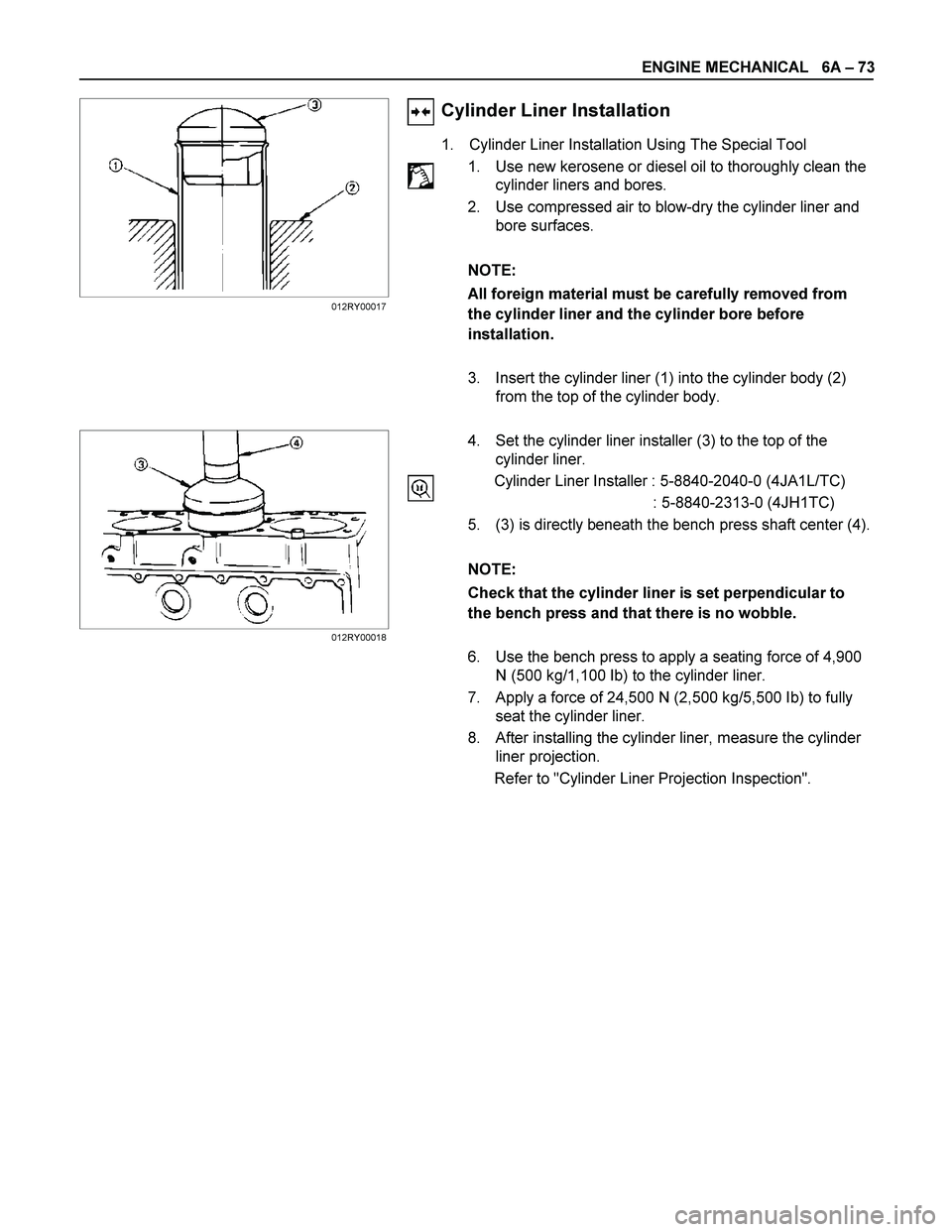
ENGINE MECHANICAL 6A – 73
Cylinder Liner Installation
1. Cylinder Liner Installation Using The Special Tool
1. Use new kerosene or diesel oil to thoroughly clean the
cylinder liners and bores.
2. Use compressed air to blow-dry the cylinder liner and
bore surfaces.
NOTE:
All foreign material must be carefully removed from
the cylinder liner and the cylinder bore before
installation.
3. Insert the cylinder liner (1) into the cylinder body (2)
from the top of the cylinder body.
4. Set the cylinder liner installer (3) to the top of the
cylinder liner.
Cylinder Liner Installer : 5-8840-2040-0 (4JA1L/TC)
: 5-8840-2313-0 (4JH1TC)
5. (3) is directly beneath the bench press shaft center (4).
NOTE:
Check that the cylinder liner is set perpendicular to
the bench press and that there is no wobble.
6. Use the bench press to apply a seating force of 4,900
N (500 kg/1,100 Ib) to the cylinder liner.
7. Apply a force of 24,500 N (2,500 kg/5,500 Ib) to fully
seat the cylinder liner.
8. After installing the cylinder liner, measure the cylinder
liner projection.
Refer to "Cylinder Liner Projection Inspection".
012RY00017
012RY00018
Page 1215 of 4264
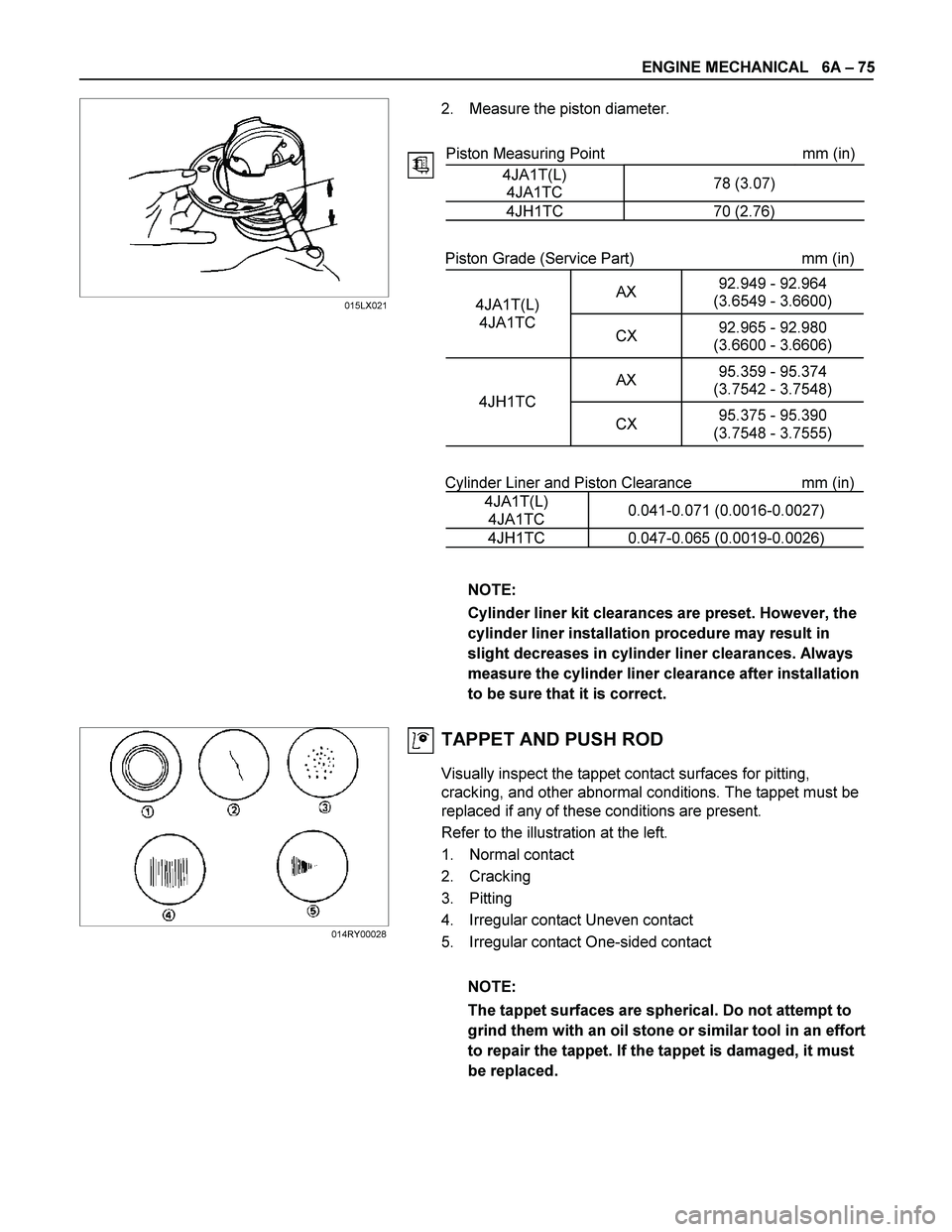
ENGINE MECHANICAL 6A – 75
2. Measure the piston diameter.
Piston Measuring Point mm (in)
4JA1T(L)
4JA1TC 78 (3.07)
4JH1TC 70 (2.76)
Piston Grade (Service Part) mm (in)
AX 92.949 - 92.964
(3.6549 - 3.6600)
4JA1T(L)
4JA1TC
CX 92.965 - 92.980
(3.6600 - 3.6606)
AX 95.359 - 95.374
(3.7542 - 3.7548)
4JH1TC
CX 95.375 - 95.390
(3.7548 - 3.7555)
Cylinder Liner and Piston Clearance mm (in)
4JA1T(L)
4JA1TC 0.041-0.071 (0.0016-0.0027)
4JH1TC 0.047-0.065 (0.0019-0.0026)
NOTE:
Cylinder liner kit clearances are preset. However, the
cylinder liner installation procedure may result in
slight decreases in cylinder liner clearances. Always
measure the cylinder liner clearance after installation
to be sure that it is correct.
TAPPET AND PUSH ROD
Visually inspect the tappet contact surfaces for pitting,
cracking, and other abnormal conditions. The tappet must be
replaced if any of these conditions are present.
Refer to the illustration at the left.
1. Normal contact
2. Cracking
3. Pitting
4. Irregular contact Uneven contact
5. Irregular contact One-sided contact
NOTE:
The tappet surfaces are spherical. Do not attempt to
grind them with an oil stone or similar tool in an effort
to repair the tappet. If the tappet is damaged, it must
be replaced.
015LX021
014RY00028
Page 1217 of 4264
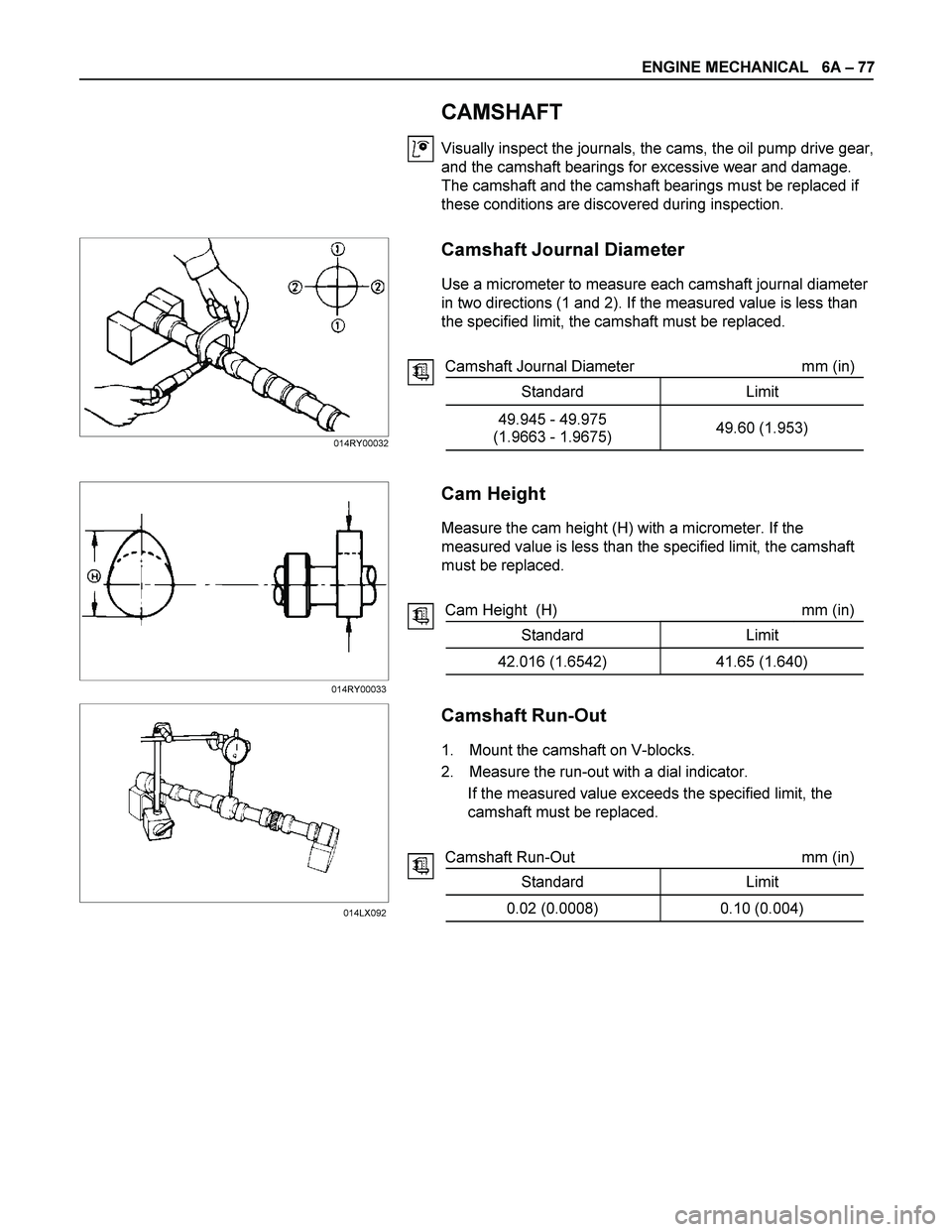
ENGINE MECHANICAL 6A – 77
CAMSHAFT
Visually inspect the journals, the cams, the oil pump drive gear,
and the camshaft bearings for excessive wear and damage.
The camshaft and the camshaft bearings must be replaced if
these conditions are discovered during inspection.
Camshaft Journal Diameter
Use a micrometer to measure each camshaft journal diameter
in two directions (1 and 2). If the measured value is less than
the specified limit, the camshaft must be replaced.
Camshaft Journal Diameter mm (in)
Standard Limit
49.945 - 49.975
(1.9663 - 1.9675) 49.60 (1.953)
Cam Height
Measure the cam height (H) with a micrometer. If the
measured value is less than the specified limit, the camshaft
must be replaced.
Cam Height (H) mm (in)
Standard Limit
42.016 (1.6542) 41.65 (1.640)
Camshaft Run-Out
1. Mount the camshaft on V-blocks.
2. Measure the run-out with a dial indicator.
If the measured value exceeds the specified limit, the
camshaft must be replaced.
Camshaft Run-Out mm (in)
Standard Limit
0.02 (0.0008) 0.10 (0.004)
014RY00032
014RY00033
014LX092
Page 1218 of 4264
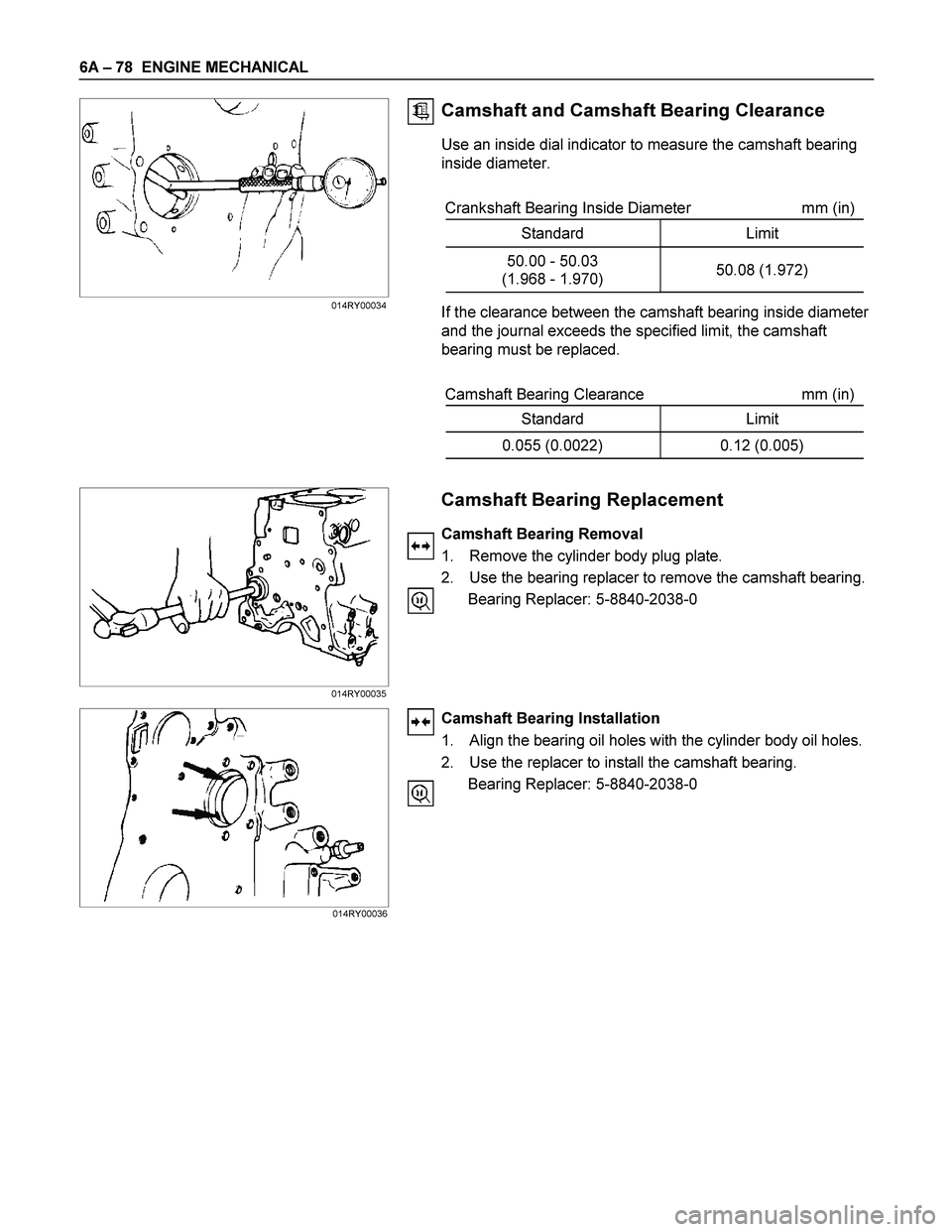
6A – 78 ENGINE MECHANICAL
Camshaft and Camshaft Bearing Clearance
Use an inside dial indicator to measure the camshaft bearing
inside diameter.
Crankshaft Bearing Inside Diameter mm (in)
Standard Limit
50.00 - 50.03
(1.968 - 1.970) 50.08 (1.972)
If the clearance between the camshaft bearing inside diameter
and the journal exceeds the specified limit, the camshaft
bearing must be replaced.
Camshaft Bearing Clearance mm (in)
Standard Limit
0.055 (0.0022) 0.12 (0.005)
Camshaft Bearing Replacement
Camshaft Bearing Removal
1. Remove the cylinder body plug plate.
2. Use the bearing replacer to remove the camshaft bearing.
Bearing Replacer: 5-8840-2038-0
Camshaft Bearing Installation
1. Align the bearing oil holes with the cylinder body oil holes.
2. Use the replacer to install the camshaft bearing.
Bearing Replacer: 5-8840-2038-0
014RY00034
014RY00035
014RY00036
Page 1219 of 4264
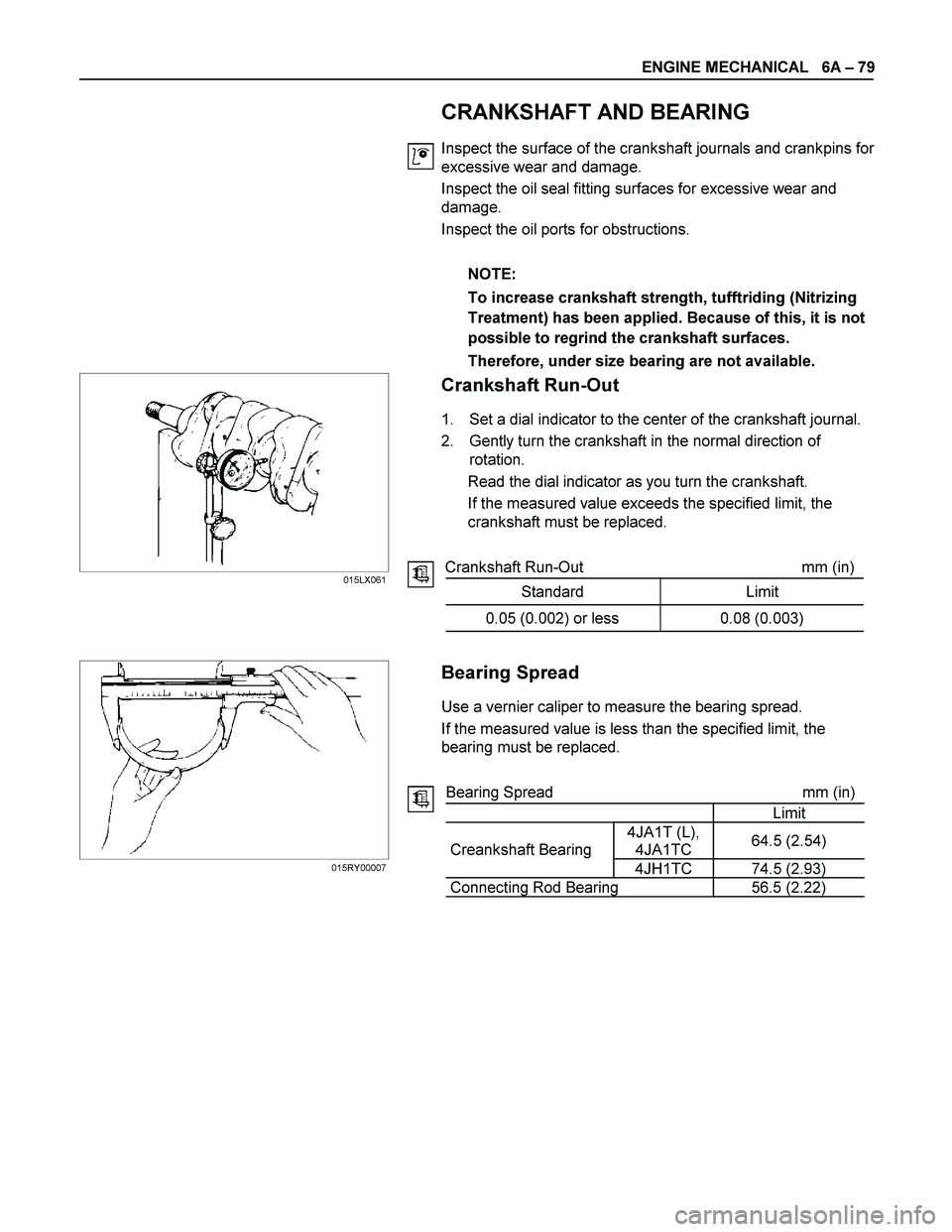
ENGINE MECHANICAL 6A – 79
CRANKSHAFT AND BEARING
Inspect the surface of the crankshaft journals and crankpins for
excessive wear and damage.
Inspect the oil seal fitting surfaces for excessive wear and
damage.
Inspect the oil ports for obstructions.
NOTE:
To increase crankshaft strength, tufftriding (Nitrizing
Treatment) has been applied. Because of this, it is not
possible to regrind the crankshaft surfaces.
Therefore, under size bearing are not available.
Crankshaft Run-Out
1. Set a dial indicator to the center of the crankshaft journal.
2. Gently turn the crankshaft in the normal direction of
rotation.
Read the dial indicator as you turn the crankshaft.
If the measured value exceeds the specified limit, the
crankshaft must be replaced.
Crankshaft Run-Out mm (in)
Standard Limit
0.05 (0.002) or less 0.08 (0.003)
Bearing Spread
Use a vernier caliper to measure the bearing spread.
If the measured value is less than the specified limit, the
bearing must be replaced.
Bearing Spread mm (in)
Limit
4JA1T (L),
4JA1TC 64.5 (2.54)
Creankshaft Bearing
4JH1TC 74.5 (2.93)
Connecting Rod Bearing 56.5 (2.22)
015LX061
015RY00007
Page 1222 of 4264
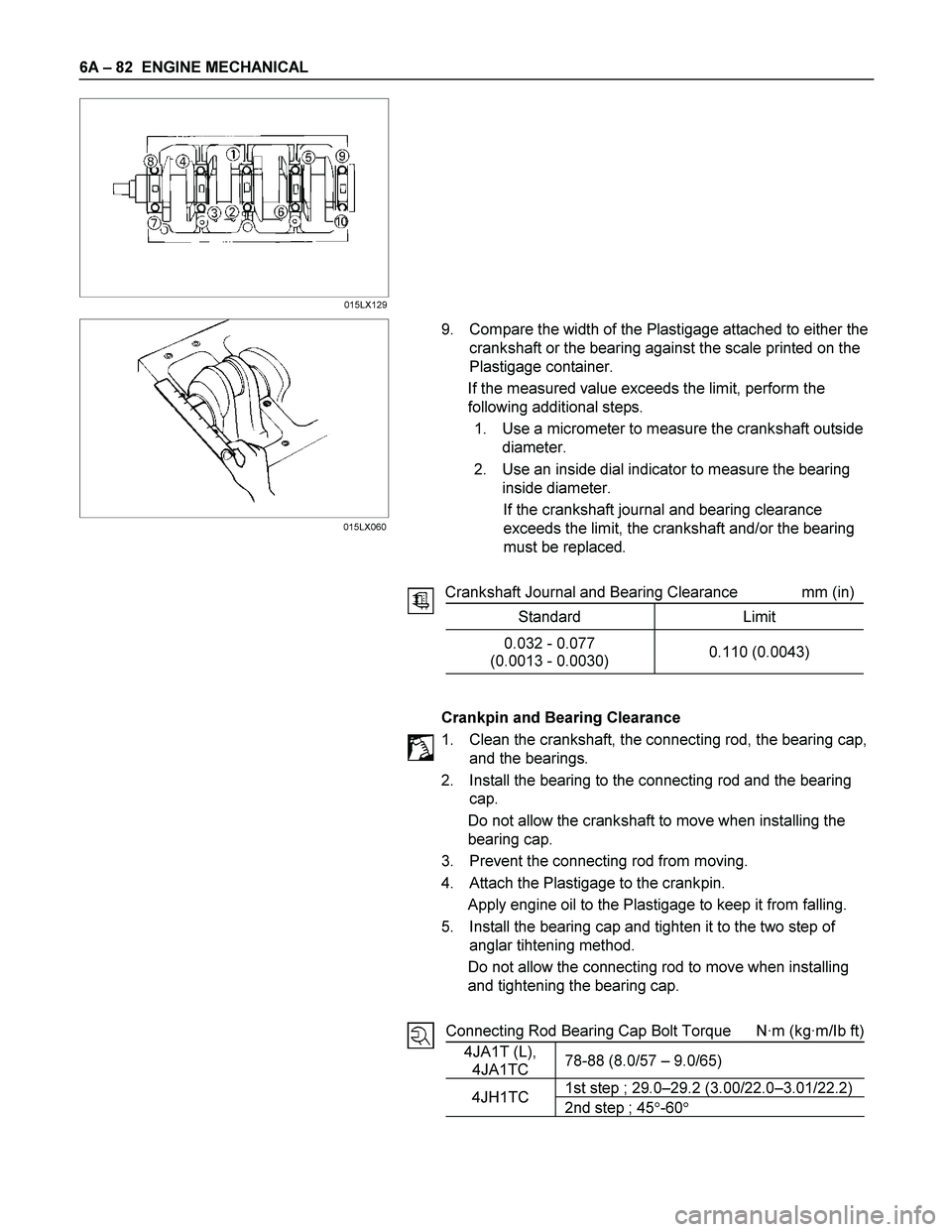
6A – 82 ENGINE MECHANICAL
9. Compare the width of the Plastigage attached to either the
crankshaft or the bearing against the scale printed on the
Plastigage container.
If the measured value exceeds the limit, perform the
following additional steps.
1. Use a micrometer to measure the crankshaft outside
diameter.
2. Use an inside dial indicator to measure the bearing
inside diameter.
If the crankshaft journal and bearing clearance
exceeds the limit, the crankshaft and/or the bearing
must be replaced.
Crankshaft Journal and Bearing Clearance mm (in)
Standard Limit
0.032 - 0.077
(0.0013 - 0.0030) 0.110 (0.0043)
Crankpin and Bearing Clearance
1. Clean the crankshaft, the connecting rod, the bearing cap,
and the bearings.
2. Install the bearing to the connecting rod and the bearing
cap.
Do not allow the crankshaft to move when installing the
bearing cap.
3. Prevent the connecting rod from moving.
4. Attach the Plastigage to the crankpin.
Apply engine oil to the Plastigage to keep it from falling.
5. Install the bearing cap and tighten it to the two step of
anglar tihtening method.
Do not allow the connecting rod to move when installing
and tightening the bearing cap.
Connecting Rod Bearing Cap Bolt Torque N·m (kg·m/Ib ft)
4JA1T (L),
4JA1TC 78-88 (8.0/57 – 9.0/65)
1st step ; 29.0–29.2 (3.00/22.0–3.01/22.2)4JH1TC
2nd step ; 45-60
015LX129
015LX060
Page 1227 of 4264
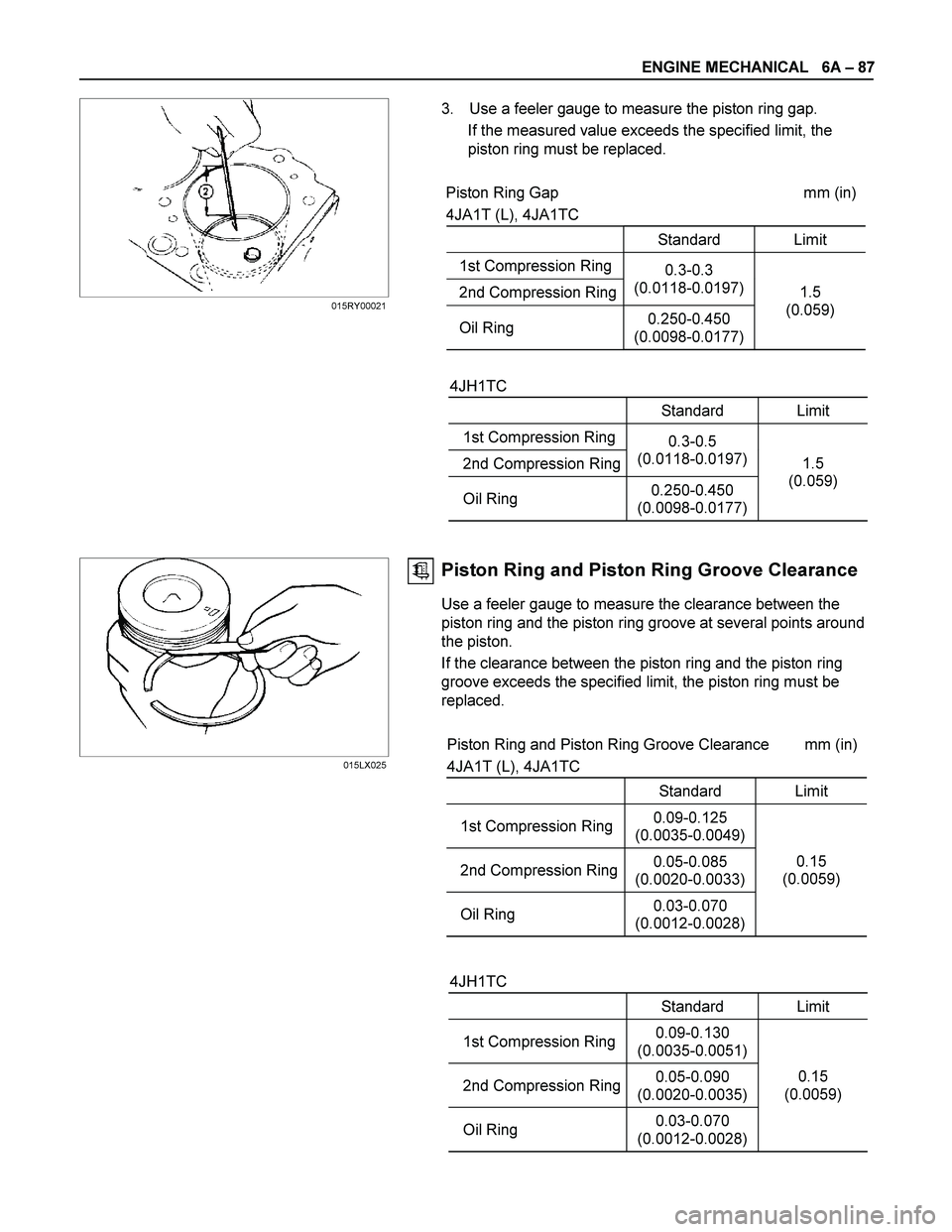
ENGINE MECHANICAL 6A – 87
3. Use a feeler gauge to measure the piston ring gap.
If the measured value exceeds the specified limit, the
piston ring must be replaced.
Piston Ring Gap mm (in)
4JA1T (L), 4JA1TC
Standard Limit
1st Compression Ring
2nd Compression Ring0.3-0.3
(0.0118-0.0197)
Oil Ring 0.250-0.450
(0.0098-0.0177) 1.5
(0.059)
4JH1TC
Standard Limit
1st Compression Ring
2nd Compression Ring0.3-0.5
(0.0118-0.0197)
Oil Ring 0.250-0.450
(0.0098-0.0177) 1.5
(0.059)
Piston Ring and Piston Ring Groove Clearance
Use a feeler gauge to measure the clearance between the
piston ring and the piston ring groove at several points around
the piston.
If the clearance between the piston ring and the piston ring
groove exceeds the specified limit, the piston ring must be
replaced.
Piston Ring and Piston Ring Groove Clearance mm (in)
4JA1T (L), 4JA1TC
Standard Limit
1st Compression Ring0.09-0.125
(0.0035-0.0049)
2nd Compression Ring0.05-0.085
(0.0020-0.0033)
Oil Ring 0.03-0.070
(0.0012-0.0028) 0.15
(0.0059)
4JH1TC
Standard Limit
1st Compression Ring0.09-0.130
(0.0035-0.0051)
2nd Compression Ring0.05-0.090
(0.0020-0.0035)
Oil Ring 0.03-0.070
(0.0012-0.0028) 0.15
(0.0059)
015RY00021
015LX025
Page 1231 of 4264
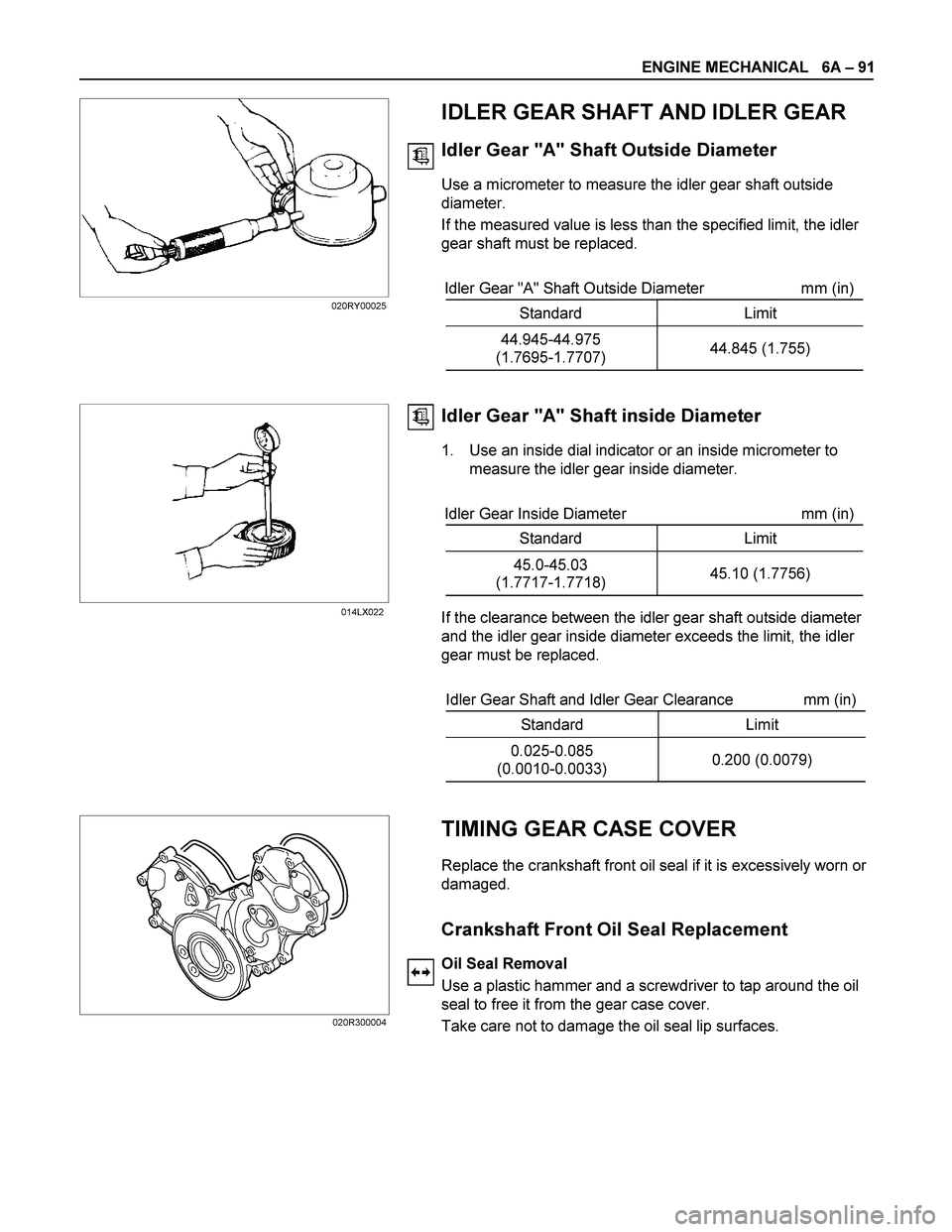
ENGINE MECHANICAL 6A – 91
IDLER GEAR SHAFT AND IDLER GEAR
Idler Gear "A" Shaft Outside Diameter
Use a micrometer to measure the idler gear shaft outside
diameter.
If the measured value is less than the specified limit, the idler
gear shaft must be replaced.
Idler Gear "A" Shaft Outside Diameter mm (in)
Standard Limit
44.945-44.975
(1.7695-1.7707) 44.845 (1.755)
Idler Gear "A" Shaft inside Diameter
1. Use an inside dial indicator or an inside micrometer to
measure the idler gear inside diameter.
Idler Gear Inside Diameter mm (in)
Standard Limit
45.0-45.03
(1.7717-1.7718) 45.10 (1.7756)
If the clearance between the idler gear shaft outside diameter
and the idler gear inside diameter exceeds the limit, the idler
gear must be replaced.
Idler Gear Shaft and Idler Gear Clearance mm (in)
Standard Limit
0.025-0.085
(0.0010-0.0033) 0.200 (0.0079)
TIMING GEAR CASE COVER
Replace the crankshaft front oil seal if it is excessively worn or
damaged.
Crankshaft Front Oil Seal Replacement
Oil Seal Removal
Use a plastic hammer and a screwdriver to tap around the oil
seal to free it from the gear case cover.
Take care not to damage the oil seal lip surfaces.
020RY00025
014LX022
020R300004
Page 1232 of 4264
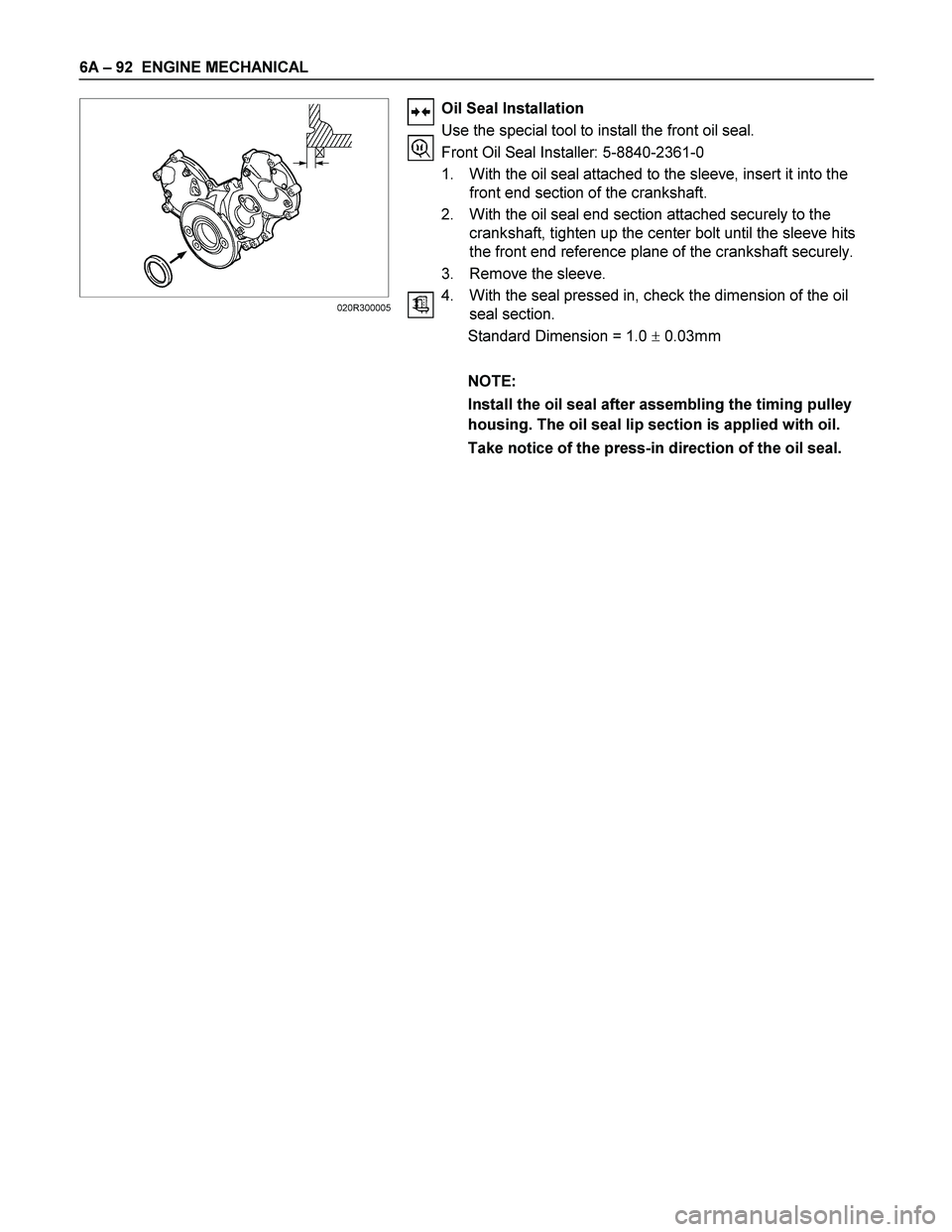
6A – 92 ENGINE MECHANICAL
Oil Seal Installation
Use the special tool to install the front oil seal.
Front Oil Seal Installer: 5-8840-2361-0
1. With the oil seal attached to the sleeve, insert it into the
front end section of the crankshaft.
2. With the oil seal end section attached securely to the
crankshaft, tighten up the center bolt until the sleeve hits
the front end reference plane of the crankshaft securely.
3. Remove the sleeve.
4. With the seal pressed in, check the dimension of the oil
seal section.
Standard Dimension = 1.0 0.03mm
NOTE:
Install the oil seal after assembling the timing pulley
housing. The oil seal lip section is applied with oil.
Take notice of the press-in direction of the oil seal.
020R300005